DOI:
10.1039/C4RA13961E
(Paper)
RSC Adv., 2015,
5, 3352-3357
Hybrid annealing method synthesis of Li[Li0.2Ni0.2Mn0.6]O2 composites with enhanced electrochemical performance for lithium-ion batteries
Received
6th November 2014
, Accepted 4th December 2014
First published on 4th December 2014
Abstract
A lithium rich composite cathode electrode material Li[Li0.2Ni0.2Mn0.6]O2 was synthesized using the hybrid annealing method. Compared with the traditional annealing method, the hybrid annealing method added a cool treatment to the annealing process. Based on detailed characterizations from X-ray diffraction (XRD), transmission electron microscopy (TEM), scanning electron microscopy (SEM) and electrochemical impedance spectroscopy (EIS), it is suggested that a good layer structure (axis ratio of c/a > 5.0), appropriate particle size of about 100 nm, and high lithium ion diffusion coefficient around 3.98 × 10−24 cm2 s−1 are attained when the annealing temperature drops to 100 °C. Because of the above reasons the sample showed a high discharge capacity and excellent cycle stability. The first discharge capability and capacity retention after 60 cycles are 287.3 mA h g−1 and 96.1%, respectively. The reasons for the electrochemical enhancement are systematically investigated.
1. Introduction
The present dominant commercial cathode material LiCoO2 has a practical discharge capacity value of 140 mA h g−1 at low rates (C/10 or lower rates), only 50% of the theoretical capacity, as limited by its structural stability.1–3 To overcome the critical disadvantages of the commercially used LiCoO2 such as expensiveness,4 limited energy and power density,5 toxicity, etc., an alternative cathode with a layered structure is urgently needed to meet the rapid development of electric vehicles (EVs) and hybrid electric vehicles (HEVs).6 Therefore, the further development of cathode materials is necessary in order to attain high discharge capacities and good cycling stabilities. At present, olivine structure LiFePO4,7,8 spinel structure LiMn2O4,9,10 and layered structure LiNixMnyCozO2 (x + y + z = 1)11–15 are the alternatives with the double advantages of lower toxicity and cost. Nevertheless, these cathode materials have to face the challenge of greatly enhancing electrochemical performance.16
With these considerations in mind, more and more interests have been focused on the lithium-rich xLi2MnO3·(1 − x)LiMO2 (M = Mn, Ni, and Co, etc.) cathode materials because of their capacity as high as 250 mA h g−1 (close to their theoretical capacity), low cost, chemical stability and environmental friendliness.17,18 However, several problems still block the commercial application of the xLi2MnO3·(1 − x)LiMO2 cathode materials. On the one hand, such Li-rich layered oxides with manganese element in high valence state have a serious surface destruction due to the decomposition of electrolyte and the Jahn–Teller effect especially at the highly delithiated state up to 4.7 V. Therefore, this phenomenon is general and leads to a steady capacity decrease during cycling.19 On the other hand, the large irreversible capacity loss in the first cycle leads to a first Coulomb efficiency decrease.20 So far, the investigations have mainly focused on the surface modification to improve these disadvantages.21–24 However, the electrochemical performance of cathode materials is closely related to its structure which is influenced heavily by preparation conditions.25 Hence, researchers have paid much attention to the synthesis and optimization of the material with co-precipitation method, solid state method, sol–gel method, etc.26–30 Controlling and improving the experimental conditions (for example pH, annealing temperature, and time of mixing) are necessary to obtain a good electrochemical performance final product. As we all known, the reported optimized electrochemical performance is that the first discharge capacity is about 250 mA h g−1 (0.1 C), the retained discharge capacity is about 200 mA h g−1 after 40 cycles.31–33 In the traditional two-step annealing method, the precursor is annealed at 500 °C for 4 h and annealed subsequently at 900 °C for 12 h in air, and then the products were obtained after being slowly cooled to room temperature.34 This method can result in micron-sized large spherical aggregates, and thus hinder Li-ion transport.35 All these reasons may give rise to low discharge capacity and poor cycling stability.
In this work, we prepared Li[Li0.2Ni0.2Mn0.6]O2, i.e., xLi2MnO3·(1 − x)LiNi0.5Mn0.5O2 (x = 0.5), through a co-precipitation method and proposed a hybrid annealing method to improve its first discharge capacity and cycling performance, which is completely different from the traditional annealing method such as optimize annealing temperature or time. First the precursor was annealed at 500 °C for 3 h, and then the annealing temperature dropped from 500 °C to 100 °C. Subsequently, annealed at 900 °C for 6 h in air and then cooled to room temperature. The sample shows the first discharge capacity is 287.3 mA h g−1 (0.1 C) and capacity retention ratios is 96.1% after 60 cycles. The Li[Li0.2Ni0.2Mn0.6]O2 prepared by the hybrid annealing method exhibits a excellent electrochemical performance because of the cool treatment mainly affects the formation of the good layered structure which contributes to enhance the value of lithium ion diffusion coefficient (DLi+).
2. Experimental
2.1. A novel synthesis for Li[Li0.2Ni0.2Mn0.6]O2
Li[Li0.2Ni0.2Mn0.6]O2 was synthesized from mixed nickel–manganese carbonate and lithium carbonate precursors by a co-precipitation method. The preparation procedure can be briefly described as follows: firstly, a 0.2 mol L−1 aqueous solution of nickel sulfate and manganese sulfate (Ni
:
Mn = 1
:
3) was added to a 1 mol L−1, equivolume, aqueous solution of sodium carbonate, from which green precipitates formed instantly; the mixed solution was aged for 12 h. The co-precipitation and aging procedures were carried out under constant stirring (250 rpm) at 80 °C. Secondly, The (Ni0.25Mn0.75)CO3 precipitate was filtered, washed, dried at 100 °C overnight, and thereafter intimately mixed with Li2CO3. Thirdly, the mixture was decomposed at 500 °C for 3 h in air. Then, the samples annealing temperature dropped from 500 °C to 200 °C, 100 °C and 20 °C, respectively, annealed subsequently at 900 °C for 6 h in air. Finally, the products were obtained after being slowly cooled to room temperature. The final products were named as T200, T100 and T20, respectively. The sample without cool treatment in the process of annealing was named as T500.
2.2. Structural characterization
Crystallite structures were determined by X-ray diffraction (XRD) using a Rigaku D/MAX 2400 diffractometer (Japan) with Cu Kα radiation (λ = 0.15418 nm) operating at 40 kV and 150 mA. The microstructure and morphology of the materials were characterized using a transmission electron microscope (TEM, JEOL, JEM-2010, Japan) operating at an accelerating voltage of 5.0 kV and a field emission scanning electron microscope (SEM, JEOL, JSM-6701F, Japan) working at an accelerating voltage of 200 kV.
2.3. Electrochemical performance tests
The electrodes were fabricated using a mixture of the prepared materials (85 wt%), acetylene black (10 wt%), and polyvinylidene fluoride (PVDF 5 wt%) in N-methyl-2-pyrrolidone (NMP) to form a slurry. The slurry was spread onto Al foil and dried in an oven at 50 °C overnight. The electrode area was 0.64 cm2 and the loading of active materials was about 2.5 mg cm−2. The electrochemical performance was tested by assembling CR2032 coin cells, using Li metal as the negative electrode. The electrolyte solution was 1 mol L−1 LiPF6 in EC–DEC (1
:
1 vol%). Charge/discharge performance was tested by LAND CT2001A battery testing system at a current density of 20 mA g−1 (0.1 C rate) and a voltage range of 2.0 V–4.8 V. The electrochemical impedance spectroscopy (EIS) was measured using an electrochemical workstation (CHI 660C) and the applied frequency was from 100 kHz to 10 mHz.
3. Results and discussion
3.1. Structure analysis of Li[Li0.2Ni0.2Mn0.6]O2
X-ray diffraction (XRD) is employed to determine the crystallographic phases of the samples (Fig. 1a). All the strong diffraction peaks can be indexed as the O3 type layered structure based on a hexagonal α-NaFeO2 with space group R
m.36 The additional weak peaks with short-ranged superstructure reflections around 2θ = 20–25° can be attributed to the existence of monoclinic Li2MnO3 phase (JCPDS card no. 27-1252) (C2/m) and the ordering of Li, Ni, and Mn atoms in the transition metal layers.22,37,38 The details of the atomic arrangement in the transition metal layers of these materials have not confirmed yet.39 With the annealing temperature dropping, the splitting of the pair reflections (018)/(110) and (006)/(012) become more obvious, indicating the good structural compatibility between Li2MnO3 and LiNi0.5Mn0.5O2.40,41 It is reported that the c/a axis ratio is an indicator of the hexagonal ordering.42 So, the axis ratio of c/a is taken as an important structural parameter to examine the influences of the cool treatment temperature on the lithium de-intercalation in the lattice of the samples. The higher axis ratio of c/a makes the material a better hexagonal ordering. With the annealing temperature dropping from 500 °C to 20 °C, the axis ratios of c/a are 4.9524 (T500), 4.9791 (T200), 5.0215 (T100), and 4.9897 (T20) (Table 1). The trends of c/a axis ratio evolution are represented in Fig. 1b, which indicates the improved layered structure by cool treatment. Therefore, T100 has good hexagonal ordering, high crystallinity, and good layered structure.
 |
| Fig. 1 (a) X-ray diffraction (XRD) patterns and (b) axis ratio of c/a trends evolution of the samples synthesized at different cool treatment temperatures: T500, T200, T100, and T20. | |
Table 1 Lattice parameters of the samples synthesized at different cool temperatures
Samples |
a (Å) |
c (Å) |
c/a |
V (Å3) |
T500 |
2.8568 |
14.1486 |
4.9524 |
300.0215 |
T200 |
2.8566 |
14.2236 |
4.9791 |
301.5633 |
T100 |
2.8537 |
14.3301 |
5.0215 |
303.1962 |
T20 |
2.8566 |
14.2539 |
4.9897 |
302.2057 |
3.2. Morphology of Li[Li0.2Ni0.2Mn0.6]O2
The size and morphology of the samples are characterized by scanning electron microscopy (SEM). The particle sizes of all the samples are hugely different (Fig. 2). The particle gradually formed inerratic prismatic structure with the annealing temperature dropping. T500 has a slightly big particle size, with an average particle size of 650 nm. The surface morphology is rough and the particle boundary is not clear (Fig. 2a). As can be seen from the Fig. 2b and c, T200 and T100 show nearly the same particle size, mainly distributed around 100–150 nm. The surface morphology is smoother than T500. The particle size of T100 (∼100 nm) is the smallest among all the samples. T20 has a slightly big particle size and the mean size is about 450 nm (Fig. 2d). It is thus concluded that the cool treatment has a great influence on the particle size. As the annealing temperature dropping, the particle distribution becomes more uniform and smaller. Therefore, the T100 has fine microstructure and small particle size, which can increase sufficient contact area of the material with the electrolyte and provide a large area for electrochemical reaction.
 |
| Fig. 2 Scanning electron microscopy (SEM) images of the samples synthesized at different cool treatment temperatures: (a) T500, (b) T200, (c) T100, and (d) T20. | |
The morphology and structure of the T100 are further studied by TEM and the results are given in Fig. 3. It is shown from TEM images that the grain sizes of the T100 are in the range of 100–200 nm (Fig. 3a), consistent with the above SEM observations. Fig. 3b displays high resolution transmission electron microscopy (HRTEM) image of T100. The high-resolution TEM image of T100 displays clear lattice fringes with a width of 2.34 Å corresponding to the (101) plane. Therefore, from the structural analyses, it is certain that there is a high crystallinity for the sample.
 |
| Fig. 3 Transmission electron microscopy (TEM) image (a) and the high-resolution TEM image (b) of the T100. | |
3.3. Electrochemical test
Fig. 4a shows the first charge–discharge curves of the samples at a current rate of 0.1 C between 2.0 V and 4.7 V. During the first charge to 4.7 V, the electrochemical reaction happens in two charging regions: a smoothly sloping voltage region from 3.8 V to 4.5 V, which is ascribed to the removal of lithium from the electrode structure accompanied with the oxidation of nickel ions from Ni2+ to Ni4+, and the voltage plateau region above 4.5 V, which could be ascribed to the activation of Li2MnO3.19,43 This activation of Li2MnO3 process has been considered to be associated with the irreversible removal of Li2O from the electrode material.44 With the annealing temperature dropping from 500 °C to 100 °C, the first discharge capacity gradually increased, 201.8 mA h g−1 (T500), 217.3 mA h g−1 (T200), 287.3 mA h g−1 (T100), and the first Coulomb efficiency also gradually increased, 65% (T500), 66.2% (T200), 75% (T100). These results indicate that the cool treatment is beneficial for achieving a high discharge capacity. However, when the annealing temperature further decreases to 20 °C, the electrochemical performance becomes poor. The first discharge capacity and first Coulomb efficiency are only 214.4 mA h g−1 and 63.8%, respectively. Therefore, it is believed that the cool treatment temperature plays an important role to obtain the high discharge capacity and first Coulomb efficiency values. The cycle performance of the samples at different cool treatment temperatures is further discussed, as indicated in Fig. 4b. For T500 and T200, the cycling stability become poor with the cycle number increasing. After 60 cycles for T100, the discharge capacity and the capacity retention ratios are 276.2 mA h g−1 and 96.1%. The T20 exhibits a relatively high cycle stability, but with a low discharge capacity. Obviously T100 displays the most excellent electrochemical performance among all of the samples.
 |
| Fig. 4 (a) First charge–discharge curves and (b) cycle performance at 0.1 C (20 mA g−1) for T500, T200, T100, and T20; inset shows Coulombic efficiency for T100. | |
The rate capability of T100 exhibits a remarkable improvement compared to the T500. The first charge–discharge curves of the T500 and T100 are presented in Fig. 5a, measured at 0.5 C. The first discharge capacities of the T500 and T100 are 152.7 mA h g−1 and 182.6 mA h g−1, respectively. Fig. 5b shows the cyclic performances of T500 and T100 at 0.5 C between 2.0 V and 4.7 V. While the T500 delivers a capacity of 111.5 mA h g−1 with capacity retention of 73.8% after 200 cycles, the T100 exhibits a capacity of 178.4 mA h g−1 with capacity retention of 97.6% after 200 cycles. The results indicate that rate capability and cyclic stability of Li[Li0.2Ni0.2Mn0.6]O2 are improved effectively by cool treatment.
 |
| Fig. 5 (a) First charge–discharge curves and (b) cycle performance at 0.5 C (100 mA g−1) for T500 and T100. | |
Electrochemical impedance spectroscopy (EIS) measurements were conducted to provide further information on the effect of cool treatment on electrode kinetics and lithium-ion diffusion coefficient in Li-ion battery materials.45 Impedance spectra for the samples produced at different cool treatment temperatures were investigated to get insight into the electrochemical process. All the Nyquist plots show two semicircles in the high and middle frequency regions and a slope in the low frequency region (Fig. 6a). The semicircles in the high and middle frequency regions correspond to lithium ion diffusion through the surface layer and charge transfer reaction, respectively, while the slope in the low frequency region is attributed to lithium ion diffusion in the bulk material.46 These Nyquist plots are fitted with the equivalent electrical circuit inserting in Fig. 6a, where Re stands for internal resistance of the cell, Rsf and Csl represent the resistance and the capacitance of solid electrolyte interface (SEI) film. Rct and Cdl correspond to charge transfer resistance and double layer capacitance. W is the Warburg impedance related to the solid state lithium ions diffusion inside the active materials.47
 |
| Fig. 6 (a) Electrochemical impedance spectroscopy (EIS) of different samples measured, and (b) profiles of the real parts of impedance (Zr) νs. ω−1/2 from 0.1 to 0.01 Hz and corresponding linear fitting curves for T500, T200, T100, and T20. | |
The lithium ion diffusion coefficient (DLi+) is calculated from the straight sloping line in low frequency region in terms of the following eqn (1),48,49
|
 | (1) |
where
R is the ideal gas constant,
T is the absolute temperature,
F is the Faraday constant,
A is the surface area of the electrode,
C is the concentration of Li
+ in the material, and
σ is the Warburg factor which has the relationship with
Zr (
Zr is the real part of impedance) in the following
eqn (2),
From eqn (2), the Warburg factor (σ) can be obtained from the linear fitting of (Zr) νs. ω−1/2 in the low frequency range of 0.1–0.01 Hz (Fig. 6b).
The calculated results of lithium ion diffusion coefficient and the values of Re, Rsf, Rct, and Rtotal for T500, T200, T100, and T20 are shown in Table 2. As can be seen, it is obviously that T100 has the lowest Rsf and Rct, while T500 has the highest Rsf and Rct. In addition, the lithium ion diffusion coefficient of the T100 is 3.98 × 10−24 cm2 s−1, which is greater than the T500 of 6.82 × 10−25 cm2 s−1. Therefore, T100 exhibits the best electrochemical performance compared with other samples, which are consistent with above analyses results. Cool treatment decreases both Rsf and Rct, indicating an enhancement in the kinetics of lithium ion diffusion through surface layer and charge transfer reaction, which increase the electrochemical performance consequently. As a consequence, cool treatment contributes to decrease the Rsf and Rct and increase lithium ion diffusion coefficient, which also result in high discharge capacity, excellent cycling stability and high Coulombic efficiency.
Table 2 Fitted parameters for EIS obtained by Zswinpwin software of different samples
Samples |
Re (Ω) |
Rsf (Ω) |
Rct (Ω) |
Rtotal (Ω) |
DLi+ (cm2 s−1) |
T500 |
5.41 |
60.11 |
219.39 |
284.91 |
6.82 × 10−25 |
T200 |
5.66 |
52.28 |
180.83 |
238.77 |
1.65 × 10−24 |
T100 |
5.76 |
44.59 |
146.36 |
196.71 |
3.98 × 10−24 |
T20 |
5.19 |
47.13 |
201.87 |
254.19 |
3.01 × 10−24 |
To analysis the relation between structure and electrochemical performance of the electrode materials, the trends of c/a axis ratio and values of DLi+ evolution are shown in Fig. 7. With the axis ratio of c/a increasing, the value of DLi+ gradually increasing, T100 has the maximum value of c/a and DLi+, which indicates that the sample has a good layered structure and the maximum lithium ion diffusion coefficient. From above results, the cool treatment mainly affects the formation of the good layered structure which contributes to enhance the value of DLi+, and further influences electrochemical performance of the electrode materials.
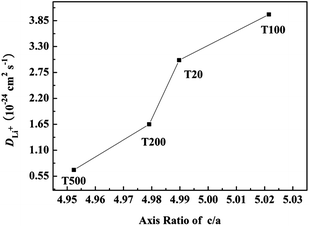 |
| Fig. 7 Axis ratio of c/a and DLi+ changes of T500, T200, T100 and T20. | |
4. Conclusions
In conclusion, Li[Li0.2Ni0.2Mn0.6]O2 electrode material is successfully synthesized by a novel hybrid annealing method. The resulting material delivers excellent performance (first discharge capacity is 287.3 mA h g−1 and capacity retention ratios is 96.1% after 60 cycles) as a cathode material for Li-ion batteries. The novel hybrid annealing method facilitates the formation of good layered structure which leads to high lithium ion diffusion coefficient, and then improves the electrochemical performance. This excellent property makes the Li[Li0.2Ni0.2Mn0.6]O2 be a potential practical application material of high energy Li-ion batteries.
Acknowledgements
This work was supported by the National Natural Science Foundation of China (no. 51362018, 21163010), the Key Project of Chinese Ministry of Education (no. 212183), and the Natural Science Funds for Distinguished Young Scholars of Gansu Province (no. 1111RJDA012).
References
- J. N. Reimers and J. R. Dahn, J. Electrochem. Soc., 1992, 139, 2091 CrossRef CAS PubMed.
- T. Ohzuku and A. Ueda, J. Electrochem. Soc., 1994, 141, 2972 CrossRef CAS PubMed.
- D. Luo, G. Li, C. Yu, S. l. Yang, J. Zheng, X. Guan and L. Li, J. Mater. Chem., 2012, 22, 22233 RSC.
- A. S. Arico, P. Bruce, B. Scrosati, J. M. Tarascon and W. Van Schalkwijk, Nat. Mater., 2005, 4, 366 CrossRef CAS PubMed.
- J. B. Goodenough and Y. Kim, Chem. Mater., 2010, 22, 587 CrossRef CAS.
- M. Armand and J. M. Tarascon, Nature, 2008, 451, 652 CrossRef CAS PubMed.
- Y. Wang, E. Hosono, K. Wang and H. Zhou, Angew. Chem., Int. Ed., 2008, 47, 7461 CrossRef CAS PubMed.
- B. Wang, D. Wang, Q. Wang, T. Liu, C. Guo and X. Zhao, J. Mater. Chem. A, 2013, 1, 135 CAS.
- M. Hirayama, H. Ido, K. Kim, W. Cho, K. Tamura, J. I. Mizuki and R. Kanno, J. Am. Chem. Soc., 2010, 132, 15268 CrossRef CAS PubMed.
- J. Y. Luo, H. M. Xiong and Y. Y. Xia, J. Phys. Chem. C, 2008, 112, 12051 CAS.
- K. Kang, Y. S. Meng, J. Bŕeger, C. P. Grey and G. Ceder, Science, 2006, 311, 977 CrossRef CAS PubMed.
- T. E. Conry, A. Mehta, J. Cabana and M. M. Doeff, Chem. Mater., 2012, 24, 3307 CrossRef CAS.
- K. C. Jiang, S. Xin, J. S. Lee, J. Kim, X. L. Xiao and Y. G. Guo, Phys. Chem. Chem. Phys., 2012, 14, 2934 RSC.
- Y. Cho, S. Lee, Y. Lee, T. Hong and J. Cho, Adv. Energy Mater., 2011, 1, 821 CrossRef CAS.
- Y. Kim, ACS Appl. Mater. Interfaces, 2012, 4, 2329 CAS.
- C. C. Fu, G. S. Li, D. Luo, J. Zheng and L. P. Li, J. Mater. Chem. A, 2014, 2, 1471 CAS.
- S. H. Kang and M. M. Thackeray, Electrochem. Commun., 2009, 11, 748 CrossRef CAS PubMed.
- A. Ito, D. Li, Y. Sato, M. Arao, M. Watanabe, M. Hatano, H. Horie and Y. Ohsawa, J. Power Sources, 2010, 195, 567 CrossRef CAS PubMed.
- M. M. Thackeray, S. H. Kang, C. S. Johnson, J. T. Vaughey, R. Benedek and S. A. Hackney, J. Mater. Chem., 2007, 17, 3053 RSC.
- S. K. Martha, J. Nanda, G. M. Veith and N. J. Dudney, J. Power Sources, 2012, 199, 220 CrossRef CAS PubMed.
- Q. Y. Wang, J. Liu, A. V. Murugan and A. Manthiram, J. Mater. Chem., 2009, 19, 4965 RSC.
- J. Liu and A. Manthiram, J. Mater. Chem., 2010, 20, 3961 RSC.
- Y. S. Jung, A. S. Cavanagh, Y. F. Yan, S. M. George and A. Manthiram, J. Electrochem. Soc., 2011, 158, A1298 CrossRef CAS PubMed.
- F. Wu, N. Li, Y. F. Su, H. Q. Lu, L. J. Zhang, R. An, Z. Wang, L. Y. Bao and S. Chen, J. Mater. Chem., 2012, 22, 1489 RSC.
- J. Lin, D. B Mu, Y. Jin, B. Wu, Y. F. Ma and F. Wu, J. Power Sources, 2013, 230, 76 CrossRef CAS PubMed.
- Z. H. Lu and J. R. Dahn, J. Electrochem. Soc., 2002, 149, A815 CrossRef CAS PubMed.
- D. K. Lee, S. H. Park, K. Amine, H. J. Bang, J. Parakash and Y. K. Sun, J. Power Sources, 2006, 162, 1346 CrossRef CAS PubMed.
- X. K. Huang, Q. S. Zhang, H. T. Chang, J. L. Gan, H. J. Yue and Y. Yang, J. Electrochem. Soc., 2009, 156, A162 CrossRef CAS PubMed.
- Y. J. Lee, M. G. Kim and J. Cho, Nano Lett., 2008, 8, 957 CrossRef CAS PubMed.
- M. G. Kim, M. Jo, Y. S. Hong and J. Cho, Chem. Commun., 2009, 218 RSC.
- Y. J. Liu, S. B. Liu, Y. P. Wang, L. Chen and X. H. Chen, J. Power Sources, 2013, 222, 455 CrossRef CAS PubMed.
- Y. J. Zhao, C. S. Zhao, H. L. Feng, Z. Q. Sun and D. G. Xia, Electrochem. Solid-State Lett., 2011, 14, A1 CrossRef CAS PubMed.
- Y. J. Kang, J. H. Kim, S. W. Lee and Y. K. Sun, Electrochim. Acta, 2005, 50, 4784 CrossRef CAS PubMed.
- Y. J. Liu, Y. Y. Gao, J. Lv and L. Chen, Mater. Res. Bull., 2013, 48, 4930 CrossRef CAS PubMed.
- C. J. Jafta, K. I. Ozoemena, M. K. Mathe and W. D. Roos, Electrochim. Acta, 2012, 85, 411 CrossRef CAS PubMed.
- Q. Q. Qiao, H. Z. Zhang, G. R. Li, S. H. Ye, C. W. Wang and X. P. Gao, J. Mater. Chem. A, 2013, 1, 5262 CAS.
- Y. S. Jung, A. S. Cavanagh, Y. F. Yan, S. M. George and A. Manthiram, J. Electrochem. Soc., 2011, 158, A1298 CrossRef CAS PubMed.
- J. M. Zheng, X. B. Wu and Y. Yang, Electrochim. Acta, 2011, 56, 3071 CrossRef CAS PubMed.
- Y. S. Meng, G. Ceder, C. P. Grey, W. S. Yoon, M. Jiang, J. Breger and Y. S. Horn, Chem. Mater., 2005, 17, 2386 CrossRef CAS.
- R. Santhanam, P. Jones, A. Sumana and B. Rambabu, J. Power Sources, 2010, 195, 7391 CrossRef CAS PubMed.
- J. Wang, B. Qiu, H. Cao, Y. Xia and Z. Liu, J. Power Sources, 2012, 218, 128 CrossRef CAS PubMed.
- K. M. Shaju, G. V. Subba Rao and B. V. R. Chowdari, Electrochim. Acta, 2002, 48, 145 CrossRef CAS.
- T. A. Arunkumar, Y. Wu and A. Manthiram, Chem. Mater., 2007, 19, 3067 CrossRef CAS.
- A. R. Armstrong, M. Holzapfel, P. Novak, C. S. Johnson, S.-H. Kang, M. M. Thackeray and P. G. Bruce, J. Am. Chem. Soc., 2006, 128, 8694 CrossRef CAS PubMed.
- D. Andre, M. Meiler, K. Steiner, C. Wimmer, T. Soczka-Guth and D. U. Sauer, J. Power Sources, 2011, 196, 5334 CrossRef CAS PubMed.
- J. Liu, Q. Y. Wang, B. Reeja-Jayan and A. Manthiram, Electrochem. Commun., 2010, 12, 750 CrossRef CAS PubMed.
- Z. Li, F. Du, X. F. Bie, D. Zhang, Y. M. Cai, X. R. Cui, C. Z. Wang, G. Chen and Y. J. Wei, J. Phys. Chem. C, 2010, 114, 22751 CAS.
- D. Luo, G. Li, X. Guan, C. Yu, J. Zheng, X. Zhang and L. Li, J. Mater. Chem. A, 2013, 1, 1220 CAS.
- X. Zhang, D. Luo, G. Li, J. Zheng, C. Yu, X. Guan, C. Fu, X. Huang and L. Li, J. Mater. Chem. A, 2013, 1, 9721 CAS.
|
This journal is © The Royal Society of Chemistry 2015 |
Click here to see how this site uses Cookies. View our privacy policy here.