DOI:
10.1039/D4MH01414F
(Communication)
Mater. Horiz., 2025,
12, 1323-1333
Optimizing dielectric, mechanical, and thermal properties of epoxy resin through molecular design for multifunctional performance†
Received
9th October 2024
, Accepted 22nd November 2024
First published on 2nd December 2024
Abstract
Epoxy resins are widely used as dielectric materials in electrical and electronic systems. However, the trend of miniaturization of electronic devices and increasing power output of electrical equipment have created new challenges for dielectric materials, necessitating low dielectric constants, high breakdown strength, and high electrical resistivity. This study introduces three molecular modifications to epoxy resin systems using facile synthesis procedures, including modifiers with bulky groups and crosslinking potential to reduce the dielectric constant while enhancing mechanical and thermal reliability, along with deep traps to increase breakdown strength. The modified epoxy resins exhibit significant improvements. Notably, epoxy/amine resin grafted with only 0.5 wt% maleic anhydride demonstrates a 30% decrease in dielectric constant, a 17-fold increase in volume resistivity, an increase in dielectric breakdown strength from 61.5 to 73.4 kV mm−1, and a rise in tensile strength from 69.7 to 75.4 MPa. Other modifiers also show enhancements in dielectric, mechanical, thermal, and water uptake properties. Fourier-transform infrared spectroscopy (FTIR), scanning electron microscopy (SEM), and energy-dispersive X-ray spectroscopy (EDX) are employed to reveal the chemical structure of the modified epoxy resin and the distribution of modifiers. Results confirm successful grafting and exceptional dispersion without agglomeration. This study demonstrates that small amounts of chemical modifiers can significantly enhance epoxy resin performance. The resulting materials can meet the requirements for next-generation dielectric materials while maintaining low production costs.
New concepts
Current methods for enhancing epoxy resin (EP) properties, such as filler incorporation, often face challenges like nanoparticle agglomeration, which limits its performance improvement. In this study, we introduce a novel molecular design approach for EP, utilizing a deep charge trap mechanism, to simultaneously enhance its dielectric, mechanical, and thermal properties. By incorporating chemical modifiers such as maleic anhydride (MA), allyl chloroacetate (AC), and 2-amino-5-chloro-2′-fluorobenzophenone (ACF), we achieve significant reductions in dielectric loss while enhancing the resistivity, dielectric breakdown strength, mechanical robustness, and thermal stability. Our work offers new insights into molecular-level modifications in EP, demonstrating that even small amounts of chemical modifiers can optimize multifunctional performance. This scalable, cost-effective approach provides a promising alternative for next-generation dielectric materials in electrical and electronic applications, presenting a fresh perspective beyond conventional nanofiller strategies.
|
1 Introduction
The utility of epoxy resin (EP) has been ubiquitous in industries that require high-performing materials due to its versatility from chemical and processing perspectives. The outstanding properties of EP, such as high modulus, high strength, good adhesion, and high chemical resistance, among others, are highly desirable in diverse applications, including construction, automotive sectors, and aerospace industries.1–3 These exceptional qualities have made EP indispensable for a wide range of applications that demand robustness and durability. However, despite the numerous advantages of traditional EP, the continuing miniaturization of electronic devices and the increasing power output of electrical equipment have created new challenges that require materials with low dielectric constant, high breakdown strength, and high electrical resistivity4,5 Traditional EP often fails to meet the stringent requirements of advanced dielectric materials for these emerging applications. As a result, the development of innovative modification approaches for EP has gained considerable interest within the scientific and industrial communities.
To address the need for improved dielectric properties in EP, researchers have devised strategies involving the incorporation of nanofillers.6,7 These nanoparticles, when dispersed within the epoxy matrix, introduce numerous deep traps capable of capturing injected charges and suppressing space charge accumulation. However, the effectiveness of this suppression mechanism heavily depends on achieving uniform nanoparticle dispersion throughout the polymer matrix.8 While the addition of fillers can potentially enhance dielectric properties, it may adversely impact the processability and mechanical performance of the resulting polymer composites. Moreover, the presence of fillers can lead to a mismatch between the filler and polymer matrix, causing electric distortion and potentially degrading critical properties such as breakdown strength, dielectric loss, and electrical resistivity.9 Consequently, increasing attention has been directed toward molecular modification techniques, which offer the advantage of being free from the agglomeration problems associated with filler incorporation.
The effects of modifications on the thermal stability of EP have been extensively studied. Lin and Pearce10,11 investigated the thermal properties of DGEBA (diglycidyl ether of bisphenol A)–DGEBF (diglycidyl ether of 9,9-bis(4-hydroxyphenyl)fluorene) and DGEBA–DGEPP (diglycidyl ether of phenolphthalein) copolymers. Their findings revealed that the DGEBA–DGEBF copolymer exhibited superior heat and flame resistance compared to the DGEBA–DGEPP copolymer, attributable to its higher aromatic ring content. Fourier-transform infrared (FTIR) data suggested that the possible degradation mechanisms for these EP involve the Wieland rearrangement, Claisen rearrangement, and Norrish-type reactions. Chen et al. prepared five different EPs cured with TMB (trimethoxy boroxine) and DDS (diaminodiphenylsulfone) hardeners.12 The results indicated that polymers with high aromaticity and/or cyclic ring structures in the chain backbone generally exhibited enhanced heat resistance. Furthermore, the morphology and structure of organosilicon polymer-modified EP were investigated by incorporating an organosilicon polymer (denoted as ETOP) as a modifier to blend with bisphenol A-type EP.13 The study demonstrated that the cross-linked epoxy-rich matrix possessed a higher glass transition temperature (Tg) than pure EP at higher ETOP content. This observation was attributed to the participation of epoxide groups on ETOP molecules in the cross-linking reaction of the matrix, thereby increasing the cross-link density and enhancing the Tg.
Improving the toughness of EP is another active area of research, aimed at enhancing the ability of these materials to deform plastically and resist crack propagation. Misaki et al.14 investigated the fracture properties of p,p′-diaminodiphenyl methane-cured EP modified with various aromatic and aliphatic glycidyl compounds. Their findings revealed that while most of these compounds promoted an increase in fracture toughness, the heat resistance of the modified EP was compromised to some extent by the incorporation of glycidyl compounds. Additionally, they observed an inverse relationship between cross-linked density of the resins and their impact strength and fracture toughness. Remarkably, the addition of 10 wt% of a terpolymer resulted in a substantial (140%) increase in the fracture toughness of the modified EP.
While extensive research efforts have been dedicated to modifying EP to improve their thermal and mechanical properties, relatively few studies are focused on enhancing their dielectric characteristics. With the rapid development in energy storage and conversion, flexible electronics, smart sensing, and 5G/6G communication, there is an urgent need for EP with tailorable dielectric properties.9 Some research demonstrates that the introduction of polar groups in resin enhances the dielectric breakdown strength, which can be attributed to the formation of deep traps that capture charges.15,16 Meanwhile, the existence of bulky groups benefits the reduction of dielectric constants.17
Inspired by these previous findings, this study synthesized three types of molecularly modified EP using various strategies, such as introducing polar groups to increase the breakdown voltage, incorporating bulky groups, and promoting crosslinking to reduce the dielectric constant and loss. Fourier-transform infrared spectroscopy (FTIR), scanning electron microscopy (SEM), and energy-dispersive X-ray spectroscopy (EDX) were employed to reveal the chemical structure of the modified EP and the distribution of modifiers. Dielectric, mechanical, and thermal stability tests were conducted to evaluate the performance of the modified EP. The findings of this study provide an efficient way to simultaneously enhance the dielectric, mechanical, and thermal properties of EP, making the molecularly modified EP a promising candidate for a new generation of dielectric materials applied in the electrical and electronic industry.
2 Results and discussion
2.1 Chemical change during modification process
2.1.1 Allyl chloroacetate-epoxy resin (EP-AC).
The Fourier-transform infrared (FTIR) spectra of EP-AC are shown in Fig. 1(a). The right section displays the spectra for post-cured EP-AC with different AC contents. The characteristic C
O peak18 at 1743 cm−1 is observed in all EP-AC samples and increases with higher AC content, confirming the existence of AC in the EP system. To ensure that AC is chemically bonded to the polymer chain, further analysis was conducted. The chemical bonds in EP containing 1.5 wt% AC (EP-AC-1.5) were characterized before and after heat curing, as illustrated in the left section of Fig. 1(a). The reduction in the intensity of the C
C peak19 at 1648 cm−1 suggests the consumption of C
C bonds in AC and their integration into the EP chain. The consistent C
C intensities across different AC concentrations further support this conclusion. The proposed reaction mechanism, shown in Fig. 1(d), suggests that the C
C bond in AC reacts with –NH– groups in the epoxy/amine resin.
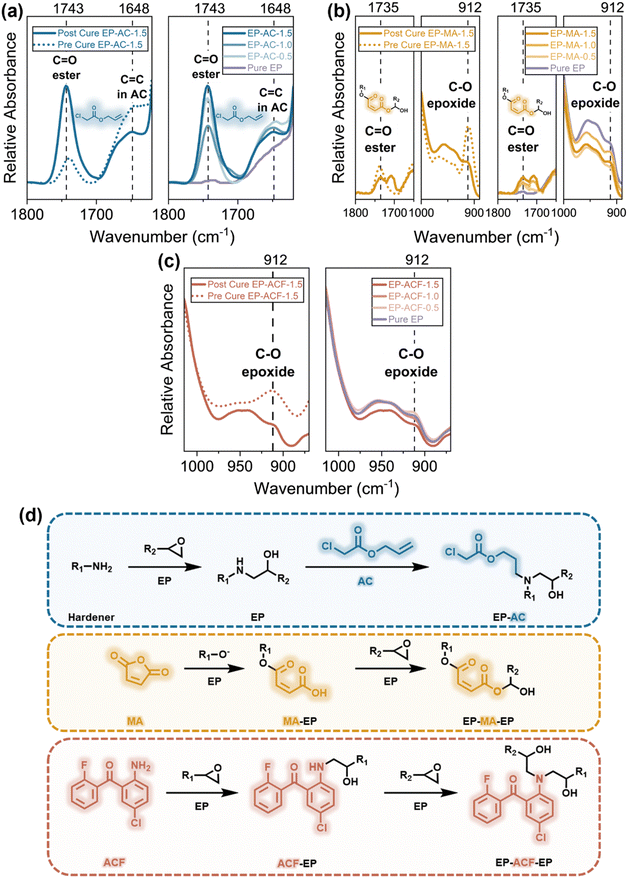 |
| Fig. 1 Chemical changes during the molecular modification of EP. (a)–(c) FTIR spectra of EP modified with AC, MA, and ACF, respectively, before and after thermal post-curing, and with varying modifier dosages after complete curing. (d) Proposed mechanisms for the chemical grafting of the three modifiers onto the EP chain. | |
2.1.2 Maleic anhydride-epoxy resin (EP-MA).
As shown in Fig. 1(b), there is an increase in the ester bond peak at 1735 cm−1 and a decrease in the epoxide peak at 912 cm−1 as MA content increases.18,20,21 This indicates the consumption of epoxide groups, along with the formation of ester bonds. The same trend is also evident in the comparison of specimens before and after heat curing, directly indicating the grafting process of MA onto the EP chain. The proposed chemical reaction mechanism is shown in Fig. 1(d). Each MA molecule contains two reactive sites that can react with epoxy groups, contributing to crosslinking.
2.1.3 2-Amino-5-chloro-2′-fluorobenzophenone-epoxy resin (EP-ACF).
ACF contains amine groups, which are similar to the curing sites of the amine hardener in this EP system. One ACF molecule can potentially bond with two epoxy rings, thereby enhancing crosslinking. The FTIR spectra of EP-ACF with varying ACF content are shown in Fig. 1(c). A decrease in the epoxide peak20,21 at 912 cm−1 is observed as ACF content increases, indicating greater consumption of epoxy rings by ACF. Therefore, it can be concluded that the amine groups in ACF react with epoxy rings, as illustrated in the reaction mechanism in Fig. 1(d).
2.1.4 Curing behavior of modified EP.
Differential scanning calorimetry (DSC) was used to investigate the degree of curing for all modified EP with the highest dosage of 1.5 wt%. The DSC curve comparisons for uncured and cured EP with 1.5 wt% modifiers are illustrated in Fig. S3 (ESI†). The DSC curves for uncured specimens displayed distinct exothermic peaks, indicating ongoing curing. In contrast, the cured specimens (under the conditions described in Section 3.2.2) showed flat curves with no exothermic activity, indicating that curing was effectively complete for all three modified epoxy resins.
2.2 Microstructural analysis of chemically modified epoxy resin
Energy-dispersive X-ray analysis (EDX) was conducted to assess the dispersion of the modifiers. The elemental mappings for various elements in the modified EP with 1.5 wt% modifier content are shown in Fig. 2(a)–(d). The mappings demonstrate a homogeneous distribution of elements, including those specific to the modifiers, confirming the uniform dispersion of the modifiers in the EP matrix. Specifically, Fig. 2(b)–(d) illustrate well-dispersed elemental signals for carbon (C), nitrogen (N), oxygen (O), and modifier-specific elements like chlorine (Cl) and fluorine (F). This indicates effective incorporation of the modifiers on molecular level without any agglomeration. It ensures a uniform composition throughout the EP matrix, addressing issues such as agglomeration and uneven dispersion commonly seen in filler-incorporated composites.
 |
| Fig. 2 EDX elemental mapping of the fracture surfaces for (a) Pure EP, and EP modified with 1.5 wt% of (b) AC, (c) MA and (d) ACF. | |
2.3 Improvement in dielectric properties
2.3.1 Dielectric constant and dielectric loss.
The dielectric spectra of EP modified with AC, MA, and ACF at varying concentrations were analyzed using the capacitance method at room temperature. Fig. 3(a)–(c) illustrates the dielectric constant and dielectric loss spectra across multiple frequencies. Fig. 3(d) compares the dielectric spectra of the three modified EP at their optimal modifier contents: 1.0 wt% for EP-AC, 0.5 wt% for EP-MA, and 1.5 wt% for EP-ACF. Generally, all modified EP exhibit lower dielectric constants and dielectric losses compared to pure EP, suggesting that the bulky groups and enhanced crosslinking introduced by the modifiers can improve the dielectric performance. Additionally, both the dielectric constant and loss decrease with increasing frequency.
 |
| Fig. 3 Dielectric properties of modified EP. (a)–(c) Dielectric constant and dielectric loss spectra for EP modified with varying concentrations (0, 0.5, 1.0, and 1.5 wt%) of (a) AC, (b) MA, and (c) ACF. (d) Comparison of dielectric constant and dielectric loss spectra for the three modifiers at their optimal concentrations. Comparison of (e) dielectric constant and (f) dielectric loss for AC, MA, and ACF-modified EP at various dosages tested under 50 Hz. | |
The dielectric constant and loss at a fixed frequency of 50 Hz are compared in Fig. 3(e) and (f). All modified EP, regardless of the modifier concentration, exhibit a lower dielectric constant than pure EP. Each type of molecular modification has a distinct impact on the dielectric properties of the epoxy resin:
1. EP-ACF
ACF introduces bulky aromatic groups, which create steric hindrance and restrict dipole alignment under an electric field. In addition, ACF promotes crosslinking within the polymer matrix, forming a more rigid structure and limiting charge carrier movement. These combined effects lead to a 27% reduction in dielectric constant and a 42% reduction in dielectric loss for EP-ACF-1.5 compared to pure EP.
2. EP-MA
MA reacts with up to two epoxide groups, promoting crosslinking that limits dipole mobility and reduces polarization. Consequently, EP-MA-0.5 exhibits a dielectric constant up to 30% lower than pure EP. The increased crosslink density also reduces dielectric loss by limiting charge carrier movement, resulting in a 10% reduction compared to pure EP. Due to competition with the hardener and the high molar concentration of MA, the optimal dosage by weight must be carefully selected.
3. EP-AC
The grafting of AC molecules onto the epoxy resin chain increases molecular weight, enhancing the rigidity of the polymer chain and hindering dipole movement. This results in a 20% reduction in the dielectric constant for EP-AC-1.0 compared to pure EP. The increased rigidity also contributes to a 12% reduction in dielectric loss.
Among the three modifications, ACF is the most effective due to the presence of bulky aromatic groups and crosslinking sites, which significantly hinder dipole alignment and restrict charge carrier movement. Consequently, ACF effectively reduces both the dielectric constant and dielectric loss. MA follows ACF in its effectiveness, as it promotes crosslinking when the optimal dosage is selected, increasing the rigidity of the polymer matrix and reducing dipole mobility. AC, by grafting onto the polymer chain, increases the molecular weight and provides some reduction in dielectric properties, although its effect is less pronounced compared to ACF and MA.
In summary, all three modifications are able to reduce the dielectric constant and loss of epoxy resin through different strategies. Among them, ACF is the most effective, followed by MA and AC. These reductions in dielectric constant and loss significantly enhance the performance of EP in electrical and electronic applications by minimizing power dissipation and signal delays.22,23
2.3.2 Volume resistivity.
Volume resistivity of the modified EP was measured using an electrometer at ambient temperature. As shown in Fig. 4(a), all modified EP exhibit significant improvement in resistivity compared to pure epoxy. This enhancement is attributed to the polar groups in the modifiers, which form deep traps that capture charge carriers and reduce their mobility.24,25 Notably, EP-MA-0.5 achieves the highest resistivity at 1.1 × 1015 Ω cm, which is 17 times higher than that of pure EP, as shown in Fig. 4(b). EP-AC-1.5 follows with a resistivity of 4.7 × 1014 Ω cm, a 7-fold increase compared to pure EP. EP-ACF-1.0 shows a smaller improvement, with a 5-fold increase in resistivity, due to the lower density of polar groups in ACF. Interestingly, peak resistivity values are observed in both EP-ACF and EP-MA systems. When excessive ACF or MA is present, they compete with the hardener for epoxy rings, resulting in defects that reduce electrical durability. These defects are primarily structural irregularities caused by incomplete or disrupted crosslinking, leading to shorter or more branched polymer chains and microstructural heterogeneities.26,27 Additionally, excess modifier and unreacted hardener act as impurities within the thermoset network, increasing the polymer free volume, compromising uniformity and creating localized weak points that further degrade performance.28 Therefore, identifying the optimal modifier content is crucial.
 |
| Fig. 4 Volume resistivity and dielectric breakdown. (a) Volume resistivity for pure EP and AC, MA, and ACF modified EP with various concentrations. (b) Comparison of volume resistivity for the modified EP with the optimal modifier concentrations. (c) Characteristic AC breakdown strengths when failure probability is at 63.2%. (d) Failure probability of pure and modified EP at optimal concentrations under various electrical stresses, analyzed using Weibull statistics. | |
2.3.3 Dielectric breakdown strength.
The dielectric breakdown strength of the modified EP was tested under AC voltage in insulating oil at ambient temperature. Two-parameter Weibull statistical analysis was employed to determine the failure probability of specimens under varying electrical stress.
The characteristic dielectric breakdown strength (α) for each group is summarized in Fig. 4(c), indicating that all modifiers can effectively improve dielectric durability. Fig. 4(d) illustrates the failure probability of pure EP and all modified EP at optimal concentrations. EP-MA-0.5 shows the highest breakdown strength at 73.9 kV mm−1, which is 120% of that of pure EP (61.5 kV mm−1). The ester bond in MA, particularly the carbonyl (C
O) groups, introduces charge traps in the polymer.29,30 The presence of deep traps introduced by MA is confirmed through first principles calculations, as shown in Fig. S5 (ESI†). Due to the high concentration of C
O groups in MA, the density of charge traps is significantly increased in EP-MA. These deep traps effectively reduce charge mobility and impede space charge accumulation, thereby enhancing the dielectric properties and electrical resistivity of the modified polymer. Improved breakdown strength can also be seen in EP-AC-1.5 at 73.4 kV mm−1 and EP-ACF-1.0 at 64.0 kV mm−1.
2.4 Mechanical properties
The mechanical properties of the modified EP including tensile strength, Young's modulus, and hardness, were characterized. Tensile strengths for all groups are shown in Fig. 5(a). Among the modifiers, AC is the most effective, increasing the tensile strength of EP-AC-1.5 from 69.7 MPa (pure EP) to 77.7 MPa. The tensile strength improves with increasing AC content, which can be attributed to the high concentration of ester bonds in AC, leading to a more stable mechanical structure.3,31,32 ACF and MA modifications also enhance the mechanical strength, with both achieving the tensile strength of 75.4 MPa at their optimal concentrations. The Young's modulus values are displayed in Fig. 5(b), revealing significant improvements due to these molecular modifications. Specifically, EP-AC-1.5 demonstrates the highest modulus at 787 MPa, followed by EP-ACF-1.5 at 735 MPa and EP-MA-1.5 at 695 MPa, while the modulus for pure EP is 618 MPa. The hardness of the modified EP was also evaluated and illustrated in Fig. 5(c). All three modifications benefit the hardness of the EP due to the enhanced crosslinking within the polymer network. MA produces the greatest improvement in hardness, followed by ACF and AC.
 |
| Fig. 5 Mechanical properties of modified EP. (a) Tensile strength, (b) Young's modulus, and (c) hardness for modified EP at various modifier concentration. (d) SEM images of fracture surfaces for pure and modified EP. | |
2.5 Thermal properties
The Tg of the modified epoxy resins was measured via DMA to assess the thermal properties. As shown in Fig. 6(a), all three types of modifications result in increased Tg at their optimal modifier content. EP-AC-1.5 exhibits the highest Tg at 140 °C, while the Tg of pure EP is 130 °C. The next one is EP-ACF-1.5 with a Tg at 136 °C, followed by EP-MA-0.5 at 131 °C. The increase in Tg can be attributed to the enhanced crosslinking within the polymer network33 and extended chain length.34 Additionally, the rigid benzene rings in ACF also contribute to the increased Tg due to the steric hindrance effect.35,36
 |
| Fig. 6 (a) Tg of modified EP at various modifier concentrations. (b) Water absorption of modified epoxy resins with 1.5 wt% modifier content. | |
Notably, Tg for EP-MA decreases as MA content increases. This weakening effect, due to excessive MA, is also observed in tensile strength and dielectric durability. This is caused by competition between MA and the amine hardener, reducing crosslinking efficiency and increasing the polymer free volume.26 Reduced crosslinking is confirmed by the curing dynamics study. The released heat during the curing reaction decreases with increasing MA concentration, as shown in Fig. S4 (ESI†). Therefore, the optimal dosage of modifiers must be carefully selected.
2.6 Water absorption
Water absorption behavior is critical for dielectric materials if the equipment is designed to operate in humid environments, as moisture can adversely affect dielectric properties due to the high polarity of water molecules.37
While the introduction of polar groups into epoxy resins benefits properties such as resistivity and dielectric breakdown strength, these same polar groups also increase water absorption,38 which is adverse to the dielectric performance of the material. Accelerated water absorption tests were conducted in boiling water for all three types of modified resins with the highest modifier dosage (1.5 wt%). As illustrated in Fig. 6(b), EP-MA-1.5 shows higher water absorption than pure EP due to the incorporation of ester bonds. This highlights the trade-off between enhanced dielectric properties and reduced hydrophobicity. Bulky groups such as benzene and fluorinated groups incorporated by ACF are expected to mitigate this adverse impact. The addition of benzene helps hinder water diffusion, while fluorinated groups reduce the polarizability of the polymer.39 As a result, EP-ACF not only shows lower water absorption than pure epoxy resin but also maintains high resistivity and strong dielectric properties. These combined benefits make EP-ACF an ideal candidate for dielectric applications in humid environments.
Experimental section
Materials
EP solution ARALDITE® LY 5052 and amine hardener ARADUR® 5052 CH were provided by Huntsman Advanced Materials Americas LLC. The chemical structure of this epoxy resin is illustrated in Fig. S1 (ESI†). The three modifiers, allyl chloroacetate (AC), 2-amino-5-chloro-2′-fluorobenzophenone (ACF), and maleic anhydride (MA), were supplied by Sigma-Aldrich Pte Ltd. Their chemical structures and physical states are listed in Table 1. Methanol provided by Aik Moh Chemicals Pte Ltd was used as the solvent.
Table 1 Modifier properties and pre-treatment procedures
Modifiers |
Chemical structure |
Physical state at RTa |
Improvement strategy |
Treatment prior to blending with liquid EP |
RT = room temperature.
|
Allyl chloroacetate (AC) |
|
Colourless liquid |
Polar group |
Premix with hardener |
Maleic anhydride (MA) |
|
White solid |
Polar group + crosslinking |
Dissolve in methanol, mix with hardener, stir for 10 minutes to evaporate the solvent |
2-Amino-5-chloro-2′-fluorobenzophenone (ACF) |
|
Yellow powder |
Polar group + bulky group + crosslinking |
Grind to fine powder, then premix with hardener |
3.2 Sample preparation
3.2.1 Preparation of pure epoxy resin.
Epoxy/amine resin specimens were prepared by mixing the uncured EP solution with the amine-containing hardener at a fixed weight ratio of 1
:
0.38. A Thinky Mixer ARE-310 was utilized for planetary mixing at 2000 rpm and centrifugal defoaming at 2200 rpm. The clear and bubble-free mixture was then gently poured into stainless-steel or silicone molds with specific cavities for curing. The EP was cured at room temperature for 24 hours, followed by post-curing at 100 °C for 4 hours. This unmodified epoxy resin is defined as pure EP. The specimens were stored in a dry box at 40% relative humidity.
3.2.2 Preparation of chemically modified epoxy resin with AC, ACF and MA.
The three modifiers, AC, ACF, and MA, were incorporated into the EP at concentrations of 0.5, 1.0, and 1.5 wt%. The preparation method was similar to that of the neat EP, except that the modifier was pre-mixed with the low-viscosity hardener solution before blending with the liquid EP. This step ensured optimal dispersion and homogeneous grafting throughout the system. The pre-treatment of modifiers to facilitate dissolution into the hardener varied based on their physical state, as detailed in Table 1. Notably, for the hardener and MA-methanol solution, the methanol was fully evaporated before proceeding to the next step, as verified through weight checks and Fourier-transform infrared (FTIR) analysis. Once a homogeneous hardener-modifier mixture was obtained, the liquid EP was added, cast, and cured following the same procedure described in Section 3.2.1.
3.3 Chemical structure analysis
FTIR spectroscopy was employed to identify chemical reactions occurring during the modification process and to confirm the successful grafting of modifiers onto the polymer chain. The FTIR Frontier from PerkinElmer, equipped with attenuated total reflectance (ATR), was used. The light source spanned wavelengths from 4000–600 cm−1 (with ATR for solid samples) and 4000–500 cm−1 (without ATR for liquid samples), using 32 scan accumulations with a resolution of 4 cm−1. For solid specimens, the dimensions are a rectangular block with a length of 40 mm, width of 10 mm, and thickness of 2.5 mm.
To understand the chemical reactions during curing, changes in chemical bonds under different curing states were evaluated using FTIR. Specimens were analyzed after 24 hours of room temperature curing, representing an incomplete curing state (defined as pre cure), and after an additional 4 hours of curing at 100 °C, representing the complete curing state (defined as post cure).
3.4 Analysis of curing behavior
Differential scanning calorimetry (DSC) tests were conducted using DSC Q10 from TA Instruments. To assess the curing behavior, the uncured epoxy resin, hardener, and modifier were mixed following the pretreatment outlined in Section 3.2.2, with testing initiated within 10 minutes of mixing. The heating rate was 10 °C min−1, from 0 °C to 250 °C, and the heat released during curing was recorded. Duplicate tests were performed for each specimen type, and the curing heat values for specimens (H1 and H2) were confirmed to meet the inequality specified in BS ISO 14322.40 |  | (1) |
Cured specimens, prepared as described in Section 3.2.2 (24 hours at room temperature followed by 4 hours at 100 °C), were also analyzed by DSC under the same conditions (0 °C to 250 °C at 10 °C min−1). A few milligrams of film fragments were used for this test. The DSC curves of the cured specimens were compared with those of the uncured specimens to determine the degree of curing.
3.5 Dielectric spectroscopy and volume resistivity
Dielectric spectra of the EP were acquired using a Meggar IDAX 300 to assess the effects of chemical modifications on the dielectric constant and dielectric loss. Volume resistivity was measured with a 6517B Electrometer from Keithley Instruments, designed for high-resistivity samples. The tests were conducted using uniform disk samples with a thickness of 2 mm and a radius of 100 mm, and cylindrical electrodes with a guard ring, in accordance with IEC 62631.
3.6 Dielectric breakdown strength
The dielectric breakdown strength was measured using an AC high-voltage tester (Hipotronics 700 Series). Thin film specimens with a thickness of 200 μm were used to minimize the impact of defects. Step voltage was applied to the films via copper electrodes, with the initial voltage determined by a short-time test using a constant speed. Details can be found in ASTM D90. The data was analysed using a two-parameter Weibull distribution, as described by eqn (2), to evaluate the dielectric breakdown behaviour: |  | (2) |
where F is the probability of failure at a given electrical stress. E is the measured breakdown strength. α is the scale parameter representing the characteristic breakdown strength at 63.2% failure probability, and β is the shape parameter describing the data distribution. A higher α indicates stronger resistance to dielectric breakdown.
3.7 Mechanical properties
Tensile properties were characterized using a Shimadzu AGS-X mechanical tester, following ASTM D638 standards. A 20 kN load cell and a strain rate of 1 mm min−1 were used. Dog-bone-shaped test samples with a thickness of 2.5 mm, a width of 3.18 mm, and a gauge length of 7.62 mm were used. Details of dimension are provided in Fig. S2 and Table S1 in ESI.† Tensile strength and Young's modulus were determined from these tests. Hardness was measured using a MITECH MH180 Leeb Hardness Tester on the same specimen before tensile measurements.
3.8 Fractographic analysis
The morphology and element dispersion on the fracture surfaces of EP samples were analysed using a field emission scanning electron microscope (SEM) and energy-dispersive X-ray analysis (EDX). JEOL JSM 7800F Prime, equipped with an Oxford Ultim Max EDS detector, was used for this analysis. A platinum coating, along with conductive tapes, was applied to the sample surface to obtain high-quality images of non-conductive polymers.
3.9 Thermal stability
Dynamic mechanical analysis (DMA) was conducted to measure the glass transition temperature (Tg) of the EP. Rectangular specimen with a length of 40 mm, width of 10 mm, and thickness of 2.5 mm were used in this test. The three-point bending mode was used, with the temperature range extending from room temperature to 200 °C.
4 Conclusions
In this study, epoxy/amine resin was successfully modified at the molecular level using strategies such as incorporating charge traps, adding bulky groups, and promoting crosslinking to enhance its dielectric, mechanical, and thermal properties. Based on the results from FTIR, dielectric spectroscopy, resistivity, breakdown tests, mechanical characterizations, DMA, SEM, and EDX, the following conclusions are drawn:
(1) All modified EP show reduced dielectric constant and loss compared to pure EP, primarily due to the introduction of bulky groups and crosslinking effects, minimizing dielectric polarization and molecular mobility. ACF is the most effective due to both bulky groups and crosslinking potential, followed by MA and AC.
(2) Volume resistivity and dielectric breakdown strength improve significantly in modified EPs, with EP-MA achieving 1.1 × 1015 Ω cm for resistivity and 74 kV mm−1 for breakdown strength. These improvements are due to deep traps formed by functional groups and increased crosslink density, hindering charge carrier movement and preventing electrical failure.
(3) Mechanical and thermal properties are enhanced, particularly in EP-AC-1.5, which shows increased tensile strength (78 MPa), Young's modulus (787 MPa), and Tg (140 °C). MA and ACF also demonstrate improved tensile strength, modulus, and thermal stability at optimal dosage.
(4) EP-ACF shows reduced water uptake compared to pure EP, due to bulky benzene and fluorinated groups that hinder water diffusion, making it suitable for humid environments.
(5) FTIR confirms the structural modification, with bulky groups and crosslinking sites to enhance dielectric, mechanical and thermal properties and polar groups to form charge traps, improving dielectric durability. SEM and EDX confirm homogeneous distribution.
(6) Optimizing modifier dosage is crucial for achieving desired properties. The uniform distribution and effectiveness of these modifications make the properties highly sensitive to modifier concentration. The recommended dosages are 0.5 wt% for MA and 1.5 wt% for AC and ACF.
Author contributions
Yuheng Deng: conceptualization, investigation, formal analysis, writing – original draft. Yen Wen Wong: investigation, validation. Letitia Kai Yue Teh: investigation, validation. Qi Wang: writing – review & editing. Weifeng Sun: conceptualization, computation. Wen Kwang Chern: resources, funding acquisition. Joo Tien Oh: supervision, funding acquisition. Zhong Chen: conceptualization, supervision, funding acquisition, writing – review & editing.
Data availability
Data supporting the findings of this study can be obtained from the corresponding author upon request.
Conflicts of interest
The authors declare no competing interests.
Acknowledgements
This research is supported by SP Group, the National Research Foundation, Singapore, the Energy Market Authority, under its Energy Programme (EMA-EP010-SNJL-002) and Nanyang Technological University.
References
- J. C. Capricho, B. Fox and N. Hameed, Polym. Rev., 2020, 60, 1–41 CrossRef CAS.
- N. R. Paluvai, S. Mohanty and S. K. Nayak, Polym.-Plast. Technol. Eng., 2014, 53, 1723–1758 CrossRef CAS.
- Y. Deng, Q. Wang, J. Ma, J. T. Oh and Z. Chen, Polym. Degrad. Stab., 2023, 215, 110455 CrossRef CAS.
- X. Huang, P. Jiang and T. Tanaka, IEEE Electr. Insul. Mag., 2011, 27, 8–16 Search PubMed.
- Q. Wang, Y. Deng, M. Yap, Y. Yang, J. Ma, W. K. Chern, J. Li and Z. Chen, Mater. Des., 2023, 235, 112409 CrossRef CAS.
- D. Q. Tan, Adv. Funct. Mater., 2020, 30, 1808567 CrossRef CAS.
-
Q. Wang, Y. Deng, J. Ma, M. Yap, Y. Yang, W. K. Chern and Z. Chen, in 2023 International Symposium on Electrical Insulating Materials (ISEIM), 2023, pp. 01–04.
- X.-D. Zhao, W.-F. Sun and H. Zhao, Polymers, 2019, 11, 592 CrossRef PubMed.
- J. Chen, Z. Pei, B. Chai, P. Jiang, L. Ma, L. Zhu and X. Huang, Adv. Mater., 2023, 2308670 CrossRef PubMed.
- S. C. Lin and E. M. Pearce, J. Polym. Sci., Part A: Polym. Chem., 1979, 17, 3095–3119 CAS.
- S. C. Lin, B. J. Bulkin and E. M. Pearce, J. Polym. Sci., Part A: Polym. Chem., 1979, 17, 3121–3148 CAS.
- C. S. Chen, B. J. Bulkin and E. M. Pearce, J. Appl. Polym. Sci., 1982, 27, 3289–3312 CrossRef CAS.
- T.-M. Lee, C.-C. M. Ma, C.-W. Hsu and H.-L. Wu, J. Appl. Polym. Sci., 2006, 99, 3491–3499 CrossRef CAS.
- T. Misaki, T. Hirohata, M. Yoshii and T. Hamasaki, J. Appl. Polym. Sci., 1989, 37, 2617–2625 CrossRef CAS.
- X.-D. Zhao, H. Zhao and W.-F. Sun, Polymers, 2020, 12, 62 CrossRef CAS PubMed.
- Y. Song, Y. Shen, H. Liu, Y. Lin, M. Li and C.-W. Nan, J. Mater. Chem., 2012, 22, 16491–16498 RSC.
- F. Fu, X. Zhou, M. Shen, D. Wang, X. Xu, S. Shang, Z. Song and J. Song, ACS Sustainable Chem. Eng., 2023, 11, 5973–5985 CrossRef CAS.
- T. H. Ha, J. Y. Jang, Y. B. Cho, H. M. Jeong and B. K. Kim, J. Appl. Polym. Sci., 2010, 116, 328–332 CrossRef CAS.
-
Interpreting Infrared, Raman, and Nuclear Magnetic Resonance Spectra, ed. R. A. Nyquist, Academic Press, San Diego, 2001, pp. 55–91 Search PubMed.
- G. Nikolic, S. Zlatkovic, M. Cakic, S. Cakic, C. Lacnjevac and Z. Rajic, Sensors, 2010, 10, 684–696 CrossRef CAS PubMed.
-
M. G. González, J. C. Cabanelas and J. Baselga, in Infrared Spectroscopy - Materials Science, Engineering and Technology, ed. T. Theophanides, InTech, 2012 Search PubMed.
- M. Zahidul Islam, Y. Fu, H. Deb, M. Khalid Hasan, Y. Dong and S. Shi, Eur. Polym. J., 2023, 200, 112543 CrossRef CAS.
- H. Sun, Y. Lv, C. Zhang, X. Zuo, M. Li, X. Yue and Z. Jiang, RSC Adv., 2018, 8, 7753–7760 RSC.
- S. Hu, X. Dong, W. Wang, S. Huang, J. Hu, Q. Li, J. He, Q. Shao, H. Yuan, H. Shi and W. Song, IEEE Trans. Dielectr. Electr. Insul., 2021, 28, 2004–2010 CAS.
- C. Zhang, J. Chang, H. Zhang, C. Li and H. Zhao, Polymers, 2019, 11, 1624 CrossRef CAS PubMed.
- C. Wang, H. Zhang, Y. Wang, C. Chen, Z. Zhang and Y. Wang, IEEE Trans. Dielectr. Electr. Insul., 2023, 30, 1178–1187 CAS.
- L. Wu, S. V. Hoa, Minh-Tan and Ton-That, J. Appl. Polym. Sci., 2006, 99, 580–588 CrossRef CAS.
- R. F. Minty, L. Yang and J. L. Thomason, Composites, Part A, 2018, 112, 64–70 CrossRef CAS.
- C. Yuan, Y. Zhou, Y. Zhu, S. Hu, J. Liang, Z. Luo, B. Gao, T. Zeng, Y. Zhang, J. Li, S. Huang, Z. Han, X. Yang, Y. Yang, P. Meng, J. Hu, J. He, H. Yuan and Q. Li, ACS Sustainable Chem. Eng., 2022, 10, 8685–8693 CrossRef CAS.
- J.-G. Gao, L.-W. Liu and W.-F. Sun, Polymers, 2023, 15, 231 CrossRef CAS PubMed.
- H. Lei, Q. Ma, Z. Wang, D. Zhang, X. Huang, M. Qin, H. Ma, W. Wang and Y. Cao, ACS Nano, 2023, 17, 16870–16878 CrossRef CAS PubMed.
-
Y. Deng, Q. Wang, J. Ma, Y. Yang, M. Yap, W. K. Chern, J. T. Oh and Z. Chen, in 2023 International Symposium on Electrical Insulating Materials (ISEIM), 2023, pp. 1–4.
- M. A. Sharaf and J. E. Mark, Rubber Chem. Technol., 1980, 53, 982–987 CrossRef CAS.
-
K. O’Driscoll and R. A. Sanayei, Chain-length dependence of the glass transition temperature, https://pubs.acs.org/doi/pdf/10.1021/ma00015a038, (accessed June 4, 2024).
- C. Zhang, H. Liang, D. Liang, Z. Lin, Q. Chen, P. Feng and Q. Wang, Angew. Chem., Int. Ed., 2021, 60, 4289–4299 CrossRef CAS PubMed.
- F. Dong, X. Yang, L. Guo, Y. Wang, H. Shaghaleh, Z. Huang, X. Xu, S. Wang and H. Liu, J. Mater. Chem. A, 2022, 10, 10139–10149 RSC.
- O. Teschke, G. Ceotto and E. F. de Souza, Phys. Chem. Chem. Phys., 2001, 3, 3761–3768 RSC.
- M. Jia, Y. Li, C. He and X. Huang, ACS Appl. Mater. Interfaces, 2016, 8, 26352–26358 CrossRef CAS PubMed.
- N. Song, K. Shi, H. Yu, H. Yao, T. Ma, S. Zhu, Y. Zhang and S. Guan, Eur. Polym. J., 2018, 101, 105–112 CrossRef CAS.
- BS ISO 14322:2018: Plastics - Epoxy resins - Determination of degree of crosslinking of crosslinked epoxy resins by differential scanning calorimetry (DSC).
|
This journal is © The Royal Society of Chemistry 2025 |
Click here to see how this site uses Cookies. View our privacy policy here.