DOI:
10.1039/D5SC03065J
(Review Article)
Chem. Sci., 2025,
16, 13149-13172
Recent advances in MOF composites for photocatalysis
Received
27th April 2025
, Accepted 26th June 2025
First published on 27th June 2025
Abstract
Metal–organic frameworks (MOFs), characterized by their tunable porosity, high surface area, and structural diversity, have emerged as promising materials for photocatalysis. To address inherent limitations of pristine MOFs such as restricted light absorption, rapid charge recombination, and insufficient active sites, MOF composites have emerged and been widely applied in photocatalysis. This review focuses on the classifications of MOF composites, emphasizing component selection and synergistic effect. Then recent environmental and energy-related photocatalytic applications are systematically discussed, including contaminant degradation, water splitting, CO2 reduction, and N2 fixation. Finally, the further trends and challenges of MOF composites for photocatalysis are proposed. We hope that this review can provide a forward-looking perspective on MOF composites as next-generation photocatalysts and offer actionable strategies to promote the resolution of energy crisis and environmental pollution.
 Chenxi Zhang | Chenxi Zhang graduated from Nankai University with BSc and PhD degrees under the supervision of Prof. Shuangxi Liu in 2014 and 2019, respectively. During 2017 to 2018, he went to the University of Namur as a joint PhD student under the supervision of Prof. Bao-Lian Su. From 2019 to 2021, he worked as a joint postdoctoral researcher at the University of Science and Technology of China and Shenzhen University under the supervision of Prof. Hai-Long Jiang and Prof. Chuanxin He. He is currently an assistant research fellow at the College of Chemistry, Tianjin Normal University. His research interest focuses on photocatalysis. |
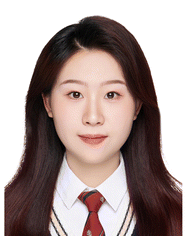 Yanhong Wu | Yanhong Wu graduated from Tianjin Normal University with a BSc degree in Chemistry in 2023. She is currently a master’s student at the College of Chemistry, Tianjin Normal University. Her scientific interest focuses on photocatalysis. |
 Dandan Li | Dandan Li received her PhD degree from Anhui University in 2016 and then worked at USTC as a postdoctoral researcher under the guidance of Prof. Hai-Long Jiang from 2016 to 2018. She is currently an associate professor at Anhui University. Her research work is focused on the development of multiphoton harvesting MOFs for photocatalysis and biological applications. |
 Hai-Long Jiang | Hai-Long Jiang earned his PhD (2008) from the Fujian Institute of Research on the Structure of Matter, CAS. He subsequently worked at the National Institute of Advanced Industrial Science and Technology (AIST, Japan), first as an AIST Fellow and later as a JSPS Fellow during 2008–2011. After a postdoctoral stint at Texas A&M University (USA), he joined USTC as a full professor in 2013 and was appointed as a chair professor in 2022. He is a Fellow of both the Chinese Chemical Society (FCCS) and Royal Society of Chemistry (FRSC) and has been annually named as a highly cited researcher by Clarivate Analytics since 2017. His research group (http://mof.ustc.edu.cn/) engages in microenvironment modulation (MEM) of catalytic centers based on reticular materials. |
1. Introduction
The escalating global energy crisis and environmental pollution demand urgent innovations in sustainable technology.1 Photocatalysis, a change in the rate or initiation of a chemical reaction under ultraviolet, visible or infrared radiation in the presence of a light-absorbing photocatalyst that participates in reactant transformations, has emerged as a promising strategy to address these challenges by clean fuel production,2–5 contaminant degradation,6,7 and value-added chemical harvest.8–10 At its core, photocatalysis relies on three sequential steps (Fig. 1): step 1, light absorption and charge carrier excitation; step 2, photogenerated charge carrier separation and migration; step 3, surface catalytic reactions.11 To enhance the overall efficiency, it is imperative to optimize each step by accordingly designing and synthesizing efficient photocatalysts. Although conventional inorganic semiconductors, such as TiO2, CdS, and g-C3N4, have been extensively studied, their intrinsic limitations (e.g. the narrow light absorption range, rapid recombination and the restricted migration path of photogenerated charge carriers, and insufficient surface active sites) hinder their practical application.12–14 These bottlenecks necessitate the development of advanced photocatalysts.
 |
| Fig. 1 Schematic diagram of the three steps in photocatalysis. | |
As a relatively new class of porous crystalline materials, metal–organic frameworks (MOFs) are constructed from metal ions or clusters and organic ligands.15–20 MOFs have been widely studied in photocatalysis due to their high porosity, large specific surface area, flexible structure, easy functionalization, and diverse active sites.21–24 Despite the above structural advantages, pristine MOFs often suffer from the limited light response range, inadequate charge mobility, and instability under certain reaction conditions, which lead to unsatisfactory photocatalytic performance.25 To overcome these constraints, MOF composites with functional components unlock the potential for further development in photocatalysis. Leveraging the synergistic effects, MOF composites can amplify light harvesting, suppress the recombination of charge carriers, and create additional active sites.
Currently, considerable research interest has been directed towards MOF composites in photocatalysis, as reflected in the substantial growth of related review articles. Although these reviews contribute significantly to the development of this field, they primarily focus on specific photocatalytic reactions. This review will systematically categorize MOF composites in photocatalysis based on component types and functions and spotlight the synergistic mechanisms of MOFs and components.26–28 Then, the latest advances of MOF composites in photocatalytic reactions (e.g. contaminant degradation, water splitting, CO2 reduction, and N2 fixation) will be discussed.
Finally, critical challenges in future research will be analyzed. By correlating material design with mechanism insight, this review aims to inspire the further development of MOF composites in photocatalysis, fostering sustainable chemical production and environmental amelioration.
2. Classifications of MOF composites
To date, researchers have integrated various materials with MOFs to optimize their properties and develop novel photocatalysts, including metal/MOF, semiconductor/MOF, reticular material/MOF, and other material/MOF. The following sections provide a comprehensive overview of these MOF composites, with particular emphasis on the functional roles of constituent components in photocatalytic processes.
2.1 Metal/MOF
Integrating metals with MOFs is one of the most efficient strategies to improve photocatalytic activity. Consequently, the application of the resulting metal/MOF composites in photocatalysis is quite extensive.29 According to the roles that metals play in photocatalysis, they can be broadly categorized into the following four types.
2.1.1 Introduction of the localized surface plasmon resonance (LSPR) effect.
In metal nanostructures with high electron mobility (e.g. Au, Ag, and Cu), the LSPR effect emerges when incident light frequency matches the intrinsic oscillation frequency of valence electrons, inducing coherent electron oscillations and strong electromagnetic field amplification near metal surfaces. The LSPR effect can enhance photocatalytic performance by generating hot carriers and localized electromagnetic fields, which improves light absorption and reduces the recombination of charge carriers.30
In metal/MOF photocatalysts, the LSPR effect occupies an important position.31–37 Chen et al. encapsulated plasmonic Au nanoparticles (NPs) within UiO-66/polytetrafluoroethylene (PTFE) membranes for photocatalytic N2 fixation under visible light and ambient conditions (Fig. 2a).32 The hot electrons generated on Au NPs due to the LSPR effect were injected into N2 molecules, leading to the activation and subsequent conversion of N2 into NH3. The designed gas–membrane–solution interface guaranteed the stability and dispersity of Au NPs, promoting the enhancement of mass transfer of N2 and H+ and reaction efficiency. This strategy offers a promising approach for photocatalytic N2 fixation and may extend to other gas molecules. Choi and coworkers integrated UiO-67 with covalently anchored Re-complex to prevent deactivation via dimerization (Fig. 2b).35 By systematically tuning Re-complex density per unit cell, Re3-MOF exhibited optimal activity due to balanced proximity between active sites. By coating on plasmonic Ag nanocubes, Re3-MOF was spatially localized within the electromagnetic field due to the LSPR effect. Accordingly, the composite demonstrated 7-fold amplified activity and 48-hour stability in photocatalytic CO2 reduction to CO under visible light. This work bridges tunable catalyst design within porous frameworks with plasmonic nanostructure integration for enhanced artificial photosynthesis. Xiao et al. developed a Cu/Cu@UiO-66 material by integrating plasmonic Cu NPs on the surface and encapsulating Cu quantum dots (QDs) within UiO-66 via an advanced double-solvent approach (ADSA).37 The surface Cu NPs induced the LSPR effect to broaden the light absorption range to the visible region, while the internal Cu QDs formed Schottky junctions with UiO-66 to facilitate charge separation, which synergistically enhanced light utilization and suppressed electron–hole recombination. The ultralow Cu loading minimized metal usage while achieving improved photocatalytic efficiency and stability in selective oxidation of benzylic alcohol.
 |
| Fig. 2 (a) Schematic diagram of Au@UiO-66/PTFE membrane.32 Copyright 2021, American Chemical Society. (b) The structure of Ag⊂Re3-MOF for plasmon-enhanced photocatalytic CO2 conversion.35 Copyright 2016, American Chemical Society. | |
Apart from coinage metals, other metals also participate in photocatalytic reactions due to their LSPR effect.38 Zhang et al. synthesized a Bi/BiO2−X-Bi2O2CO3/BiOCl@Bi-MOF composite. The Bi-MOF provided active sites, while Bi metal improved light absorption via the LSPR effect.39 The heterojunction material followed the indirect Z-scheme, which promoted charge separation and made it possible to degrade chlortetracycline (CTC) under visible light irradiation. The design emphasizes the importance of component interaction in photocatalysis.
2.1.2 Formation of the Schottky junction.
For n-type semiconductors, their work functions are generally lower, or, equivalently, their Fermi levels are higher than those of metals. Upon intimate contact, the electrons on semiconductors migrate to metals to reach the equilibrium state, resulting in the formation of the Schottky junction.40–43 The consumed electrons lead to the upward bending energy band and the depletion layer in semiconductors. The Schottky barrier is created at the interface, which favors electron capture and suppresses charge recombination. It should be noted that in the Schottky junction, the work function of the metal is required to be higher than that of the semiconductor and the flow of electrons from the metal to the semiconductor is prohibited. These characteristics are distinctly different from those of common semiconductor-cocatalyst systems in photocatalysts.
Although MOFs are not strictly semiconductors, they can form Schottky junctions with metal NPs like semiconductors as well, providing a conceptual framework for understanding interfacial charge transfer in these systems. With their previous research in mind,44–46 the Jiang group loaded Pt NPs on MOF supports (ZIF-8, UiO-66, and MIL-125) that exhibited no visible-light response, respectively.47 Despite being a redox-inert support with a d10 ZnII configuration, ZIF-8 induced a higher Schottky barrier than redox-active UiO-66 with ZrIV and MIL-125 with TiIV, which facilitated electron donation from the MOF to Pt while blocking reverse electron transfer upon visible light irradiation. Along with the Pt interband excitation, the electron density was modulated, thereby enhancing the generation of reactive oxygen species O2˙− for benzylamine oxidation over Pt/ZIF-8. In contrast, the redox-active supports permitted electron backflow, which was not conducive to the reaction (Fig. 3a). This work challenges conventional concepts and demonstrates the superiority of inert supports in optimizing metal–support electronic interactions for photocatalysis.
 |
| Fig. 3 (a) The electron transfer process and mechanism of Pt/MOFs. The green and cyan bands represent inert and active MOFs.47 Copyright 2022, John Wiley and Sons. (b) The construction of a highly efficient MOF-based Schottky junction.48 Copyright 2021, John Wiley and Sons. | |
Taking the novel Schottky junction PtPd (100)@UiO-66-NH2 as an example, Wang et al. proposed three parameters, Vtransfer, Dtransfer, and Vconsume, which represent the electron transfer rate, the electron transfer distance, and the electron consume rate, respectively (Fig. 3b).48 Through dual electron pathways, the PtPd alloy enhanced Vtransfer, while encapsulation within UiO-66-NH2 reduced Dtransfer by shortening the charge migration route. Exposing (100) facets of PtPd amplified Vconsume by boosting H2O activation efficiency. Drawing support from the collaborative optimization of the above three strategies, the photocatalytic H2 evolution rate of PtPd (100)@UiO-66-NH2 was remarkably improved with a 300 W Xe lamp compared to conventional Pt/UiO-66-NH2.
2.1.3 Fabrication of the Z-scheme.
Mimicking natural photosynthesis, the Z-scheme photocatalysis has emerged as a highly promising system.49–52 This two-step photoexcitation system employs two photocatalysts with staggered bandgap structures. Under light excitation, photogenerated electrons from photocatalyst II (PC II) recombine with photogenerated holes from photocatalyst I (PC I) via redox mediators or direct interfacial contact, leaving electrons on PC I and holes on PC II (Fig. 4a).53 As a consequence, strong redox potentials are preserved for oxidation and reduction reactions, and the charge carriers are spatially separated. However, utilizing metal as one of the photocatalysts in a Z-scheme system is highly unusual. The Jiang group encapsulated atomically precise MAg24 nanoclusters (M = Ag, Pd, Pt, Au) into UiO-66-NH2via electrostatic assembly.54 As revealed by in situ X-ray photoelectron spectroscopy (XPS) and femtosecond time-resolved transient absorption spectroscopy (fs-TAS), heteroatom doping at the cluster core modulated charge dynamics by constructing a Z-scheme charge transfer pathway, prolonging carrier lifetimes while suppressing recombination (Fig. 4b). The metal nanoclusters were confined by UiO-66-NH2, improving the stability of the composites. Among the catalysts, AuAg24@UiO-66-NH2 demonstrated optimal activity and excellent stability in photocatalytic H2 production under visible light irradiation. This work pioneered a novel metal@MOF Z-scheme photocatalytic system, highlighting the critical role of atomic-level heteroatom engineering.
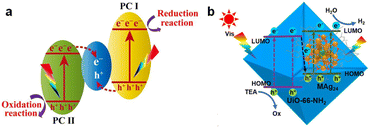 |
| Fig. 4 (a) Schematic diagram of a Z-scheme photocatalytic system.53 Copyright 2018, Elsevier. (b) Photocatalytic mechanism of the Z-scheme heterojunction in MAg24@UiO-66-NH2 for H2 production.54 Copyright 2024, John Wiley and Sons. | |
2.1.4 Cocatalysts.
In photocatalysis, cocatalysts are widely employed to enhance charge separation and provide active sites for surface redox reactions, among which metals are one of the most common types due to their low overpotential, high electrical conductivity, and efficient electron capture ability.55–57 In metal/MOF composites, metals often serve as cocatalysts.58–66 The Jiang group investigated the role of cocatalyst microenvironment modulation with Pt NPs embedded in UiO-66-NH2.61 The interfacial surfactant polyvinylpyrrolidone (PVP) on Pt NPs hindered electron transfer between the MOF photosensitizer and cocatalyst. Controlled removal of PVP enhanced electrical conductivity, accelerated interfacial electron kinetics, and suppressed charge recombination, thereby improving photocatalytic H2 evolution. Surface-clean Pt@UiO-66-NH2 exhibited superior activity compared to the PVP-capped counterparts (Fig. 5a), which was further improved by introducing ferrocene carboxylic acid as the electron mediator. This work highlights the critical influence of interfacial microenvironments on cocatalyst functionality.
 |
| Fig. 5 (a) Schematic diagram of the photocatalytic performance of Pt@UiO-66-NH2.61 Copyright 2021, John Wiley and Sons. (b) The synthesis process of Ru1/d-UiO-66.72 Copyright 2024, John Wiley and Sons. | |
Single-atom (SA) metal cocatalysts, characterized by isolated metal atoms anchored on supports, maximize atomic utilization efficiency. Unlike conventional cocatalysts with aggregated metal NPs, the unsaturated coordination environments and highly exposed active sites of SA cocatalysts reduce energy barriers and enhance charge transfer kinetics, boosting photocatalytic activity.67–71 Ren et al. anchored Ru SAs onto defective UiO-66, establishing electron–metal–support interactions (EMSI) via covalent bonds.72 The EMSI facilitated rapid charge transfer between Ru SAs and UiO-66, optimizing the local electron density for N2 activation. Density Functional Theory (DFT) analysis revealed that Ru donated d-orbital electrons to N2 π*-antibonding orbitals, weakening the N
N triple bond. Defective UiO-66 nodes stabilized Ru SAs, preventing aggregation while redistributing electrons (Fig. 5b). The optimized Ru1/d-UiO-66 exhibited enhanced photocatalytic ammonia synthesis via a distal reaction pathway under a 300 W Xe lamp. This work demonstrates the critical role of the Ru SA cocatalyst in mediating EMSI effect and activating inert N2 through tailored electronic modulation.
2.2 Semiconductor/MOF
As pioneering materials in photocatalysis, semiconductors have unequivocally demonstrated their performance through decades of scientific validation. In semiconductor/MOF composites, semiconductors can significantly broaden the light absorption range and effectively enhance charge carrier separation efficiency, contributing to the improvement of photocatalytic performance.
2.2.1 Semiconductors as photosensitizers.
Due to the lack of inherent light absorption ability, certain MOFs require the introduction of photosensitizers to facilitate photocatalytic reactions.73,74 Jiang et al. integrated TiO2 into tailored molecular compartments within MIL-101-based MOFs to optimize photocatalytic CO2 reduction.75 Acting as the light-harvesting antenna, TiO2 in specific mesopores named after compartments II can synergistically interact with metal clusters embedded in MOFs, facilitating efficient electron transfer and charge separation (Fig. 6a and b). According to XPS, X-ray absorption spectroscopy (XAS), and electron paramagnetic resonance (EPR) investigations, the secondary building units (SBUs) of the MOF received electrons from TiO2 to generate Cr2+ under light irradiation, which reverted to Cr3+ and evolved CO/CH4 upon CO2 introduction, identifying the metal containing SBUs as catalytic sites (Fig. 6c). Under a 300 W Xe lamp irradiation, the photogenerated holes on TiO2 oxidized H2O and evolved O2 without sacrificial agent. The compartmentalized spatial control of TiO2 highlights the influence of precise positioning in MOF composites.
 |
| Fig. 6 Raw and filtered (a) high-angle annular dark-field (HAADF) images and (b) integrated differential phase contrast (iDPC) images of 42%-TiO2-in-MIL-101-Cr taken from [110] incidence. Blue, red, and orange outlines represent compartments I, compartments II, and the unit cells, respectively. The scale bars are 5 nm. (c) Photocatalytic mechanism of TiO2-in-MOF compartments composed of Cr clusters.75 Copyright 2020, Springer Nature. | |
2.2.2 Construction of type II heterojunction/Z-scheme/S-scheme.
Type II heterojunction, Z-scheme, and S-scheme systems are typical examples of heterojunctions and are familiar in semiconductor/MOF photocatalysts. Xu and coworkers investigated heterojunction engineering with size-controlled CdS QDs integrated with Cd-TCPP MOF nanosheets.76 The quantum confinement effect modulated the conduction band position of CdS relative to Cd-TCPP, governing the electron injection rate across the heterojunction. Larger CdS QDs with lower conduction band potentials promoted efficient hot electron transfer while hindering light absorption. Consequently, optimal photocatalytic activity occurred at intermediate QD sizes. The type II heterojunction in CdS/Cd-TCPP enhanced H2 production by optimizing interfacial electron transfer dynamics (Fig. 7a). This work establishes size-dependent bandgap engineering to regulate charge carrier dynamics in heterojunction photocatalysts.
 |
| Fig. 7 (a) Photocatalytic mechanism of the type II heterojunction in CdS/Cd-TCPP for H2 production.76 Copyright 2022, Elsevier. (b) Photocatalytic mechanism of the Z-scheme heterojunction in MXene@g-C3N4/MIL-101(Fe) for ENR degradation.77 Copyright 2025, Elsevier. (c) Photocatalytic mechanism of the S-scheme heterojunction in Ni@MOF/BVO for CO2 reduction.78 Copyright 2022, John Wiley and Sons. | |
Very recently, Lin et al. synthesized a MXene@g-C3N4/MIL-101(Fe) heterojunction with high surface area and abundant reactive sites for visible-light-driven photocatalytic degradation of enrofloxacin (ENR).77 With MXene nanosheets as electron mediators, an indirect Z-scheme mechanism was established to achieve directional electron transfer from MIL-101(Fe) to g-C3N4 (Fig. 7b). The redox-active sites were spatially separated, thereby suppressing charge recombination. Scavenger-assisted photocatalytic degradation experiments and EPR spectral analysis demonstrated h+ and O2˙− as the key reactive species. The role of the Z-scheme in optimizing charge dynamics and interfacial reactions was elucidated, offering a promising way for designing MOF-based photocatalysts.
The Jing group immobilized single Ni(II) sites on 2D NTU-9 MOF, which was then assembled with BiVO4via H-bonds to obtain a Ni@MOF/BVO composite.78 The heterojunction exhibited nearly 100% CO selectivity in photocatalytic reduction of CO2, which was ascribed to the S-scheme charge transfer mechanism and the local microenvironment (LME) around Ni sites according to in situ diffuse reflectance infrared transform spectra (DRIFTS) and DFT calculation. The S-scheme mechanism facilitated electron migration from BVO to MOF and subsequently to single Ni(II) sites, optimizing charge separation while retaining strong redox potentials (Fig. 7c). Featuring Ti(IV)-oxo nodes and vicinal carboxylic moieties, the LME around Ni sites promoted CO2 adsorption via H-bonding, proton-assisted reduction, and CO desorption, ensuring high CO selectivity (99.2%). This work emphasizes the well-designed S-scheme mechanism and single-atom catalysts with tailored coordination environments for efficient artificial photosynthesis.
2.3 Reticular material/MOF
Reticular materials, exemplified by MOFs and covalent-organic frameworks (COFs), constitute a distinctive type of crystalline porous material. Although formed via coordination bonds and covalent bonds respectively, MOFs and COFs share many similarities, such as well-defined structures and high tunability.79 The strategically designed MOF/MOF or COF/MOF composites exhibit enhanced light absorption capabilities and superior charge separation efficiency, resulting in markedly improved photocatalytic activity.
2.3.1 Reticular materials as photosensitizers.
Certain MOFs or COFs exhibit excellent light absorption properties, which can complement MOFs that lack good light absorption but possess other advantages. Liu et al. synthesized a MOF-on-MOF composite (MIL-125@ZIF-8) through a site-selective epitaxial-growth strategy.80 By minimizing lattice mismatch between {110} facets of MIL-125 and {001} facets of ZIF-8, spatially selective integration was achieved at the corner or side surface (Fig. 8a). In photocatalytic orange II degradation, ZIF-8 grown on the corner surfaces outperformed that on the side surfaces. The performance of MIL-125@ZIF-8 was remarkably enhanced owing to adsorption of dye molecules by ZIF-8 and light-harvesting property of MIL-125 (Fig. 8b), highlighting the importance of the synergistic effect of light absorption and reactant adsorption.
 |
| Fig. 8 (a) Schematic diagram of site-selective epitaxial-growth of ZIF-8 on MIL-125. (b) Photocatalytic mechanism of orange II degradation over ZIF-8@MIL-125.80 Copyright 2020, Royal Society of Chemistry. (c) Photocatalytic mechanism of ZIF-8@iCOF.81 Copyright 2023, American Chemical Society. | |
Similar condition also exists in ZIF-8@ionic COF (ZIF-8@iCOF) with a core–shell structure, in which iCOF acts as light antenna and generates excitons.81 ZIF-8 effectively enhanced the intersystem crossing (ISC) of iCOF, facilitating the transfer of excitons to the lower-energy triplet excited state to produce singlet oxygen (1O2) (Fig. 8c). Under white light irradiation (50 mW cm−2) for 15 min, the photocatalytic bactericidal efficiency of ZIF-8@iCOF was 99.99999%. The results provide an insightful strategy for regulating the light absorption performance of MOFs.
2.3.2 Construction of type II heterojunction/Z-scheme/S-scheme.
The rational construction of heterojunctions with reticular materials has emerged as a promising strategy to promote charge carrier separation and migration efficiency. In particular, the structural tailorability of MOFs and COFs allows for precise adjustment of bandgaps and energy levels to achieve optimal band alignment.
The Jiang group explored microenvironment modulation with sandwich-structured UiO-66-NH2@Pt@UiO-66-X photocatalysts.82 By changing the functional groups (-X) of the UiO-66-X shell, both charge separation in the UiO-66-NH2 core and proton reduction efficiency of the Pt mediator were synergistically regulated. According to the results of temperature-dependent photoluminescence (PL) spectra and electrochemical hydrogen evolution reaction (HER) measurements, exciton binding energy (Eb) and overpotential of UiO-66-NH2@Pt@UiO-66-X were obtained to estimate the efficiencies of charge separation (η2) and the surface reaction (η3) (Fig. 9a). As a consequence, UiO-66-NH2@Pt@UiO-66-H showed optimal activity under irradiation of >380 nm owing to the equilibrium between η2 and η3, highlighting microenvironment engineering as a critical strategy for coordinating photocatalytic processes.
 |
| Fig. 9 (a) Photocatalytic H2 production rate, Eb and overpotential in the HER of UiO-66-NH2@Pt@UiO-66-X.82 Copyright 2023, John Wiley and Sons. (b) Photocatalytic mechanism of the S-scheme heterojunction in NH2-MIL-125/TpBpy-COF for overall water splitting.84 Copyright 2025, John Wiley and Sons. | |
Huang and coworkers proposed a novel method to fabricate a hierarchical core–shell PCN-222-Ni@UiO-67-NH2 (P@U) heterostructure through distinct nucleation kinetics of two Zr-MOFs.83 Due to the structural advantages of both parent MOFs such as high crystallinity, large porosity, and good stability, the composite exhibited enhanced photoresponse, optimized band alignment, and improved charge carrier separation at the interface. Without sacrificial agents, the HCOOH production rate of P@U was 146.0 μmol g−1 h−1, which was 2.7 times that of sole PCN-222-Ni and 8.1 times that of sole UiO-67-NH2 under visible light. The EPR and in situ DRIFTS characterizations proved the rationality of the Z-scheme mechanism in P@U. This approach transcends conventional molecular-level optimization, emphasizing hierarchical control as a critical pathway for advanced catalyst development, which is beneficial for effective charge separation and HCOOH production.
Very recently, Chu et al. presented a covalently-linked MOF/COF S-scheme heterojunction NH2-MIL-125/TpBpy-COF for photocatalytic overall water splitting.84 By controlling MOF crystal facets, the anisotropic exposure of (001) and (111) facets in NH2-MIL-125(Ti) enhanced the interfacial internal electric field, optimizing charge transfer via the S-scheme pathway (Fig. 9b). The robust built-in electric field facilitated spatial separation of photogenerated charge carriers while preserving strong redox potentials. The visible-light-driven overall water splitting H2 and O2 evolution rates of NH2-MIL-125/TpBpy-COF were 331.6 and 165.7 μmol g−1 h−1, which achieved the highest reported activity among COF-based photocatalysts. The work demonstrates crystal facet engineering as a reasonable strategy to strengthen S-scheme heterojunction efficiency in composite reticular materials.
2.4 Other material/MOF
Beyond the aforementioned systems, it is feasible to expand MOF composites with other materials, which will be discussed as follows.
2.4.1 Upconversion nanoparticles (UCNPs)/MOF.
Featuring anti-Stokes emission, UCNPs can convert long-wavelength light to short-wavelength light.85,86 In UCNPs/MOF composites, the light absorption range of MOF is effectively broadened by UCNPs and the photocatalytic performance is enhanced. For instance, taking NaYF4:Yb, Tm, Er and UiO-66-NH2 as a core and shell respectively, the Jiang group successfully synthesized UCNPs-Pt@MOF/Au composites.87 Due to the SPR and upconversion effects of Au and UCNPs, the composite photocatalyst can absorb all three regions, i.e. ultraviolet, visible, and near-infrared (NIR) regions of full solar spectrum (Fig. 10a). By adjusting the thickness of MOF and the loading amount of Au, the optimal photocatalyst presented a photocatalytic H2 production activity of 280 μmol g−1 h−1, and the electron transfer mechanism was clearly elucidated.
 |
| Fig. 10 (a) The light absorption region of UCNPs-Pt@MOF/Au.87 Copyright 2018, John Wiley and Sons. (b) Schematic diagram of photocatalytic hydrogen production over MIL-125-NH2 and metal oxides/MIL-125-NH2.93 Copyright 2022, John Wiley and Sons. | |
In addition to H2 production, many reports on photocatalytic degradation with UCNPs/MOF under NIR light irradiation can be found as well.88–92
2.4.2 Metal oxide/MOF.
Beyond serving as semiconductors, metal oxides possess the ability to regulate the charge properties of MOFs. The Jiang group integrated MIL-125-NH2 and two metal oxides (MoO3 or V2O5).93 Unlike common semiconductors, these metal oxides possess appropriate work functions and energy levels. They neither participated in the formation of heterojunction nor acted as cocatalysts, but induced band bending in MIL-125-NH2, which can be evidenced by a Kelvin probe force microscope (KPFM) and surface photovoltage (SPV) spectra and promoted the separation of photogenerated charge carriers. Therefore, the photocatalytic activities of the MOF composites were 56 and 42 times higher than that of pristine MOF under irradiation of >380 nm (Fig. 10b). More importantly, this is the first report on band bending in MOFs, demonstrating the semiconductor-like properties of MOFs.
2.4.3 Metal phosphide/MOF.
As good electronic conductors and active sites, metal phosphides are widely recognized as excellent cocatalysts.94–97 These unique characteristics make metal phosphides different from common semiconductors. After integrating with MOFs, metal phosphides also demonstrate unique properties in photocatalysis. The Jiang group incorporated small, monodisperse Ni2P with UiO-66-NH2 for the first time.98 The characterization revealed the electron transfer mechanism between Ni2P and UiO-66-NH2, demonstrating the kinetic advantage of Ni2P over Pt (Fig. 11a). Despite leading in thermodynamics, the photocatalytic H2 production rate of Pt@UiO-66-NH2 was still inferior to that of Ni2P@UiO-66-NH2 under irradiation of >380 nm, which was the integrated result between thermodynamics and dynamics. In composites with other MOFs such as MIL-125-NH2
99 and UiO-66,100,101 metal phosphides also exhibited good photocatalytic H2 production performance.
 |
| Fig. 11 (a) The transient absorption kinetics of Ni2P@UiO-66-NH2 and Pt@UiO-66-NH2.98 Copyright 2020, John Wiley and Sons. (b) Photocatalytic mechanism of the Z-scheme heterojunction in MIL101/CDs-C3N4 for ENR degradation.106 Copyright 2024, John Wiley and Sons. | |
2.4.4 Carbon material/MOF.
In photocatalysis, carbon materials can play various roles.102,103 Samy et al. employed carbon nanotubes (CNTs) as photocatalysts and combined them with MOF-808 to obtain a heterogeneous photocatalyst for the degradation of carbamazepine and diazinon under the irradiation of 286 nm.104 In the rational estimation, the cost of this photocatalytic system was 2.523 $ per m3, laying a solid foundation for its comprehensive application. Liu and coworkers synthesized a C60@NU-901 composite for photocatalytic H2 production under a 300 W Xe lamp.105 The significant host–guest interactions between the components contributed to the formation of built-in electric fields and efficient charge separation, resulting in a remarkably improved activity. Zhou et al. fabricated a MIL-101/CDs-C3N4 composite for photocatalytic oxidative desulfurization under irradiation of >400 nm by a thermal polymerization-hydrothermal strategy.106 The plane-averaged differential charge density plot demonstrated the formation of a Z-scheme heterojunction between MIL-101(Fe) and g-C3N4 (Fig. 11b). The carbon quantum dots (CDs) can capture electrons from g-C3N4, facilitating the separation of charge carriers. Using graphene oxide (GO) as the template and electron mediator, Wang et al. developed a series of ultrathin metal–organic layers (MOLs)@GO samples.107 With the help of the photosensitizer, Co-MOL@GO achieved a record-high CO evolution rate (18.0 mmol g−1 h−1), which was 2.4 times higher than that of sole Co-MOL. The result demonstrated the importance of GO, the electron mediator. The aforementioned reports suggest that upon compositing with MOFs, different forms of carbon exhibit diverse functions in distinct photocatalytic reactions.
2.4.5 Halide perovskite/MOF.
Unlike common semiconductors, halide perovskites are intolerant to H2O, which is essential in most photocatalytic reactions.108 Therefore, encapsulating halide perovskites with MOFs for physical isolation is a feasible strategy. Kong et al. and Wu et al. fabricated CsPbBr3@ZIF-67 and MAPbI3@PCN-221(Fex) respectively, achieving photocatalytic reduction of CO2 to CH4 and CO.109,110 Inspired by the thylakoid membrane, Huang and coworkers mimicked natural photosystem I (PS I) and introduced CsPbI3 into Rh-functionalized ZIF-62 MOF glass to construct a novel artificial photosynthesis system.111 Through liquid-phase sintering at 325 °C under argon protection, the light absorption range was broadened to 600–800 nm and the surface defects of CsPbI3 were passivated. In addition, an alloyed interface between the components was formed, benefiting the extraction and transfer of photogenerated charge carriers. Under visible light irradiation, the coenzyme nicotinamide adenine dinucleotide (NADH) was first regenerated over the composite catalyst. Then the derived protons and electrons were transferred to formate dehydrogenase (FDH), reducing CO2 to HCOOH (Fig. 12a). The HCOOH production rate of the tandem reaction was ∼0.12 mmol h−1 within 1 hour and ∼0.07 mmol h−1 within 5 hours with nearly 100% selectivity (Fig. 12b). This work highlights the synergistic role of MOFs and halide perovskites, offering a novel design for sustainable solar-driven chemical synthesis.
 |
| Fig. 12 (a) Photocatalytic mechanism of the artificial PS I system. (b) Time course of photocatalytic HCOOH production.111 Copyright 2024, American Chemical Society. (c) Photocatalytic mechanism of UZT/CFMX for H2 production.117 Copyright 2022, John Wiley and Sons. | |
2.4.6 MXene/MOF.
MXenes refer to transition metal carbides, nitrides, or carbonitrides with two-dimensional structures.112–114 Thanks to their low Fermi level and high electrical conductivity, MXenes often serve as efficient cocatalysts in photocatalysis.115 The Huang group synthesized Ti3C2@MIL-125-NH2 by an in situ growth method, in which Ti3C2 acted as the Ti source.116 In photocatalytic H2 production under AM 1.5G light, the cocatalyst Ti3C2 facilitated the transfer of excited electrons on MIL-125-NH2 through Ti–N bonds, promoting the reduction of H+ to H2. Shi et al. constructed a novel UiO-66-NH2(Zr/Ti)/carboxyl-functionalized MXene (UZT/CFMX) photocatalyst via the carboxyl-assisted coordination strategy.117 The heterojunction suppressed the recombination of charge carriers and mediated H2O activation through carbon (from the carboxyl group)-oxygen (from H2O) interaction (Fig. 12c). Therefore, additional pathways for photocatalytic water splitting were created. The synergistic interactions optimized the interfacial reaction dynamics and collectively boosted the photocatalytic activity under 350–780 nm irradiation. The semiconductor characteristics of MXenes also allow the construction of heterostructures between them and MOFs.118 For instance, a 0D/2D Ti3C2 quantum dots/two-dimensional nickel-MOF (Ti3C2-QDs/Ni-MOF) heterojunction composite was reported by Qin and coworkers for photocatalytic N2 fixation under a 300 W Xe lamp.119 The internal electric field formed between the components accelerated the migration of photogenerated electrons, and Ti3C2-QDs significantly promoted the physical adsorption of N2, which was the prerequisite for the reaction.
3. Applications of MOF composites in photocatalysis
This section will systematically examine representative applications of MOF composites in photocatalysis, including contaminant degradation, water splitting, CO2 reduction, and N2 fixation. To capture the most recent developments, our coverage focuses on reports published after 2020.
3.1 Contaminant degradation
Water pollution has emerged as a critical global challenge, which poses a severe threat to the environment and human health due to the persistence and toxicity of contaminants.120–123 Photocatalysis, a sustainable technology utilizing light energy to drive redox reactions, offers a promising solution for contaminant degradation by converting hazardous substances into harmless products.124–127 Combining the exceptional adsorption capability of MOFs with the functionality of nanomaterials, MOF composites have attracted attention for contaminant degradation recently (Table 1),128–131 including volatile organic compounds (VOCs), dyes, antibiotics, and heavy metals.
Table 1 MOF composites for photocatalytic contaminant degradation
Photocatalysts |
Contaminants |
Light source |
Activity |
Ref. |
UCNP/NH2-MIL-125 |
CH3CHO |
Visible light |
96% in 30 min |
92
|
Natural solar light |
88% in 30 min |
Near-infrared light |
80% in 30 min |
MPA-m/U66N-m |
CH3COCH3 |
350–780 nm |
95% in 60 min |
132
|
La-Bi2WO6-BiFeWOx-WO3@MOF |
Phenol |
≥420 nm |
98.62% in 80 min |
133
|
Nicotine |
92.41% in 80 min |
Benzopyrene |
81.74% in 80 min |
Nitrosamine |
98.23% in 80 min |
MIL-101(Fe)/ZnFe2O4 |
Phenol |
300 mW LED light |
99.3% in 6 min |
134
|
MIL-101(Fe)/CQDs@g-C3N4 |
Sulfur |
>400 nm |
98.04% in 180 min |
106
|
cMIL-125@ZIF-8 |
Orange II |
>420 nm |
∼97.3% in 120 min |
80
|
MIL-68@COF-V |
Rhodamine 6G |
Visible light |
97.6% in 25 min |
135
|
Tetracycline |
96.5% in 15 min |
Phenols |
95.3% in 40 min |
Tm@Yb@Y/NMF |
Rhodamine B |
300 W lamp |
77% in 50 min |
91
|
Bi2MoO6/MIL-88B(Fe) |
Rhodamine B |
420–760 nm |
99.5% in 120 min |
136
|
Bisphenol A |
54.0% in 120 min |
Sr-NDI@9,10-ME |
Rhodamine B |
≥420 nm |
95.31% in 15 min |
137
|
TiO2@In-TCBPE |
Rhodamine B |
300 W lamp |
100% in 13 min |
138
|
MOF-1/GO/Fe3O4 |
Methylene blue |
Visible light |
95% in 80 min |
139
|
β-NaYF4:Yb,Tm/MIL-100(Fe) |
Methylene blue |
Full-spectrum |
96.7% in 75 min |
90
|
ZIF-8@AgNWs |
Methylene blue |
300–1100 nm |
94% in 60 min |
140
|
MoS2@MIL-88(Fe) |
Methylene blue |
400–800 nm |
98.5% in 60 min |
141
|
Rhodamine B |
97.4% in 60 min |
MOF-5@rGO |
Methylene blue |
300–1900 nm |
95% in 20 min |
142
|
Rhodamine B |
97% in 20 min |
Methylene orange |
92% in 20 min |
CNTs/MOF-808 |
Carbamazepine |
286 nm |
91.6% in 90 min |
104
|
Diazinon |
254 nm |
99.7% in 60 min |
PDINH/MIL-88A(Fe) |
Chloroquine phosphate |
Visible light |
95.7% in 30 min |
143
|
Bi/BiO2−X–Bi2O2CO3/BiOCl@Bi-MOF |
Chlortetracycline |
190–1100 nm |
94.6% in 90 min |
39
|
Co/Mn-MOF-74@gC3N4 |
Doxycycline hydrochloride |
>420 nm |
94% in 60 min |
144
|
MXene@g-C3N4/MIL-101(Fe) |
Enrofloxacin |
465 ± 40 nm |
99% in 60 min |
77
|
PCN-222/PCN-134 |
Nizatidine |
Simulated visible light |
90.81% in 120 min |
145
|
γ-Fe2O3-MIL-53(Fe)-GO |
Norfloxacin |
420–780 nm |
92.8% in 90 min |
146
|
UiO-66/NH2-MIL-125/g-C3N4 |
Ofloxacin |
>420 nm |
99.1% in 50 min |
147
|
MIL-88A(Fe)/LaFeO3 |
Ofloxacin |
300 ± 50 mW LED light |
98.4% in 10 min |
148
|
In-MOF/BiOF |
Perfluorooctanoate |
500 W Hg lamp |
100% in 180 min |
149
|
TpMA@NH2-MIL-125 |
Propylparaben |
>400 nm |
99% in 120 min |
150
|
Ag/AgCl/MOF-303 |
Sulfamethoxazole |
>420 nm |
99% in 40 min |
151
|
MIL-125-NH2@CoFe PBA |
Tetracycline |
≥420 nm |
86.9% in 120 min |
152
|
NH2-UiO-66@DAT-HOF |
Tetracycline |
>400 nm |
∼72% in 60 min |
153
|
MIL-125(Ti)@Ti-Ce-MOF |
Tetracycline |
AM 1.5G |
97.8% in 30 min |
154
|
MIL-125-NH2/TiO2/Ti3C2 |
Tetracycline hydrochloride |
>420 nm |
83% in 60 min |
155
|
ZnIn2S4@PCN-224 |
Tetracycline hydrochloride |
>420 nm |
99.9% in 60 min |
156
|
UiO-66-(COOH)2/MoS2/ZnIn2S4 |
Cr(VI) |
500 W lamp |
0.06850 min−1 |
157
|
NH2-MIL-88B(Fe)/CDs |
Cr(VI) |
Visible light |
95% in 45 min |
158
|
Methylene blue |
92% in 90 min |
UiO-66-NH2@HDU-25 |
Cr(VI) |
>420 nm |
∼99% in 30 min |
159
|
Au/MIL-101(Fe)/BiOBr |
Cr(VI) |
>420 nm |
100% in 20 min |
160
|
Norfloxacin |
81.8% in 75 min |
CdS-ZnS-ZIF-8 |
Cr(VI) |
420–760 nm |
99% in 10 min |
161
|
MIL-88A(Fe)@ZnIn2S4 |
Cr(VI) |
500 W lamp |
100% in 9 min |
162
|
Sulfamethoxazole |
99.6% in 60 min |
MOF525@BDMTp |
U(VI) |
Xe lamp |
73.6% in 120 min |
163
|
Chlorpyrifos |
99.8% in 150 min |
POM@Cu-MOFs |
U(VI) |
Visible light |
99.4% in 60 min |
164
|
Shah et al. integrated NH2-BDC stabilized NaYbF4:Tm3+ (UCNP) and NH2-MIL-125(Ti) to form UCNP/NMIL(Ti).92 Under visible/solar/NIR light, UCNP/NMIL(Ti) can degrade 96%/88%/80% of VOC CH3CHO in 30 min with apparent rate constants 3.4/2.5/2.4-fold those of UCP@NMIL(Ti), in which NaYbF4:Tm3+ was stabilized with EDTA instead of NH2-BDC. The results undoubtedly proved the significance of the ligand-sharing synthetic method. The degradation efficiency exhibited a positive correlation with relative humidity (0–100% RH), suggesting rapid conversion of H2O to ˙OH radicals (Fig. 13a). Moreover, the excellent photocatalytic performance can be attributed to abundant oxygen vacancies, coordinatively unsaturated metal sites, broad light absorption range, and high charge carrier separation efficiency. This work provides new possibilities for exploring novel synthetic strategies.
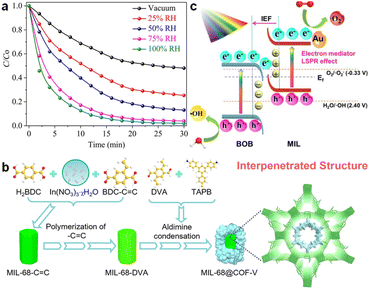 |
| Fig. 13 (a) Photocatalytic CH3CHO degradation rate curves over UCNP/NMIL(Ti) under visible light with different RH%.92 Copyright 2022, Elsevier. (b) The construction process of MIL-68@COF-V.135 Copyright 2024, John Wiley and Sons. (c) Photocatalytic mechanism of the plasmonic S-scheme heterojunction in Au/MIL/BOB.160 Copyright 2024, Elsevier. | |
Zhou and coworkers introduced a novel C–C covalent linkage strategy to construct a core–shell MIL-68@COF-V composite (Fig. 13b).135 Unlike imine-linked MIL-68-NH2@COF-V, MIL-68@COF-V possessed adjustable shell thickness and the interpenetrated structure, resulting in enhanced light absorption and charge carrier separation. Under visible light, MIL-68@COF-V exhibited a comprehensive degradation effect on dye (rhodamine 6G), antibiotic (tetracycline), and VOC (phenol), far exceeding MIL-68-NH2@COF-V. Furthermore, the in situ growth MIL-68@COF-V film degraded 97.6% of rhodamine 6G in 25 min, 96.5% of tetracycline in 15 min, and 95.3% of phenol in 40 min, with apparent rate constants 1.61–2.86 times as high as those of the powder composite. This work highlights the potential of C–C covalently linked MOF@COF heterostructures through rational structure design and scalable film fabrication.
Simultaneous photocatalytic degradation of heavy metals and antibiotics faces limitations in terms of active sites, charge separation, and redox ability. In the work reported by Li et al., a novel plasmonic S-scheme heterojunction Au/MIL-101(Fe)/BiOBr (Au/MIL/BOB) was constructed via a solvothermal-photoreduction method (Fig. 13c).160 Compared to pristine BiOBr, the visible-light-driven photocatalytic degradation apparent rate constants of the optimized catalyst were enhanced by 53.3 and 2 times for Cr(VI) and norfloxacin (NOR), respectively. The synergistic effect in the Cr(VI)-NOR system effectively increased the carrier utilization. Due to the LSPR effect of Au NPs, the light absorption of Au/MIL/BOB was promoted. The MOF-based S-scheme structure facilitated the separation of charge carriers and the exposure of active sites, while maintaining high redox ability. The rational design of Au/MIL/BOB demonstrates great potential in wastewater purification.
3.2 Water splitting
As a sustainable and eco-friendly energy source, H2 has garnered significant attention in recent years.165 Photocatalytic water splitting has emerged as a competitive approach for H2 production,166,167 with MOF composites demonstrating remarkable potential in this field.168,169 A summary of MOF composites for photocatalytic water splitting is presented below (Table 2). It should be noted that based on reaction products, photocatalytic water splitting with MOF composites can be categorized into two types: H2 production exclusively with sacrificial agents and overall water splitting H2 and O2 production simultaneously without sacrificial agents. Most research in the table still focuses on H2 production, while progress in overall water splitting remains relatively limited, with activity yet to be improved. This is primarily due to the difficulty in overcoming the slow kinetics of the water oxidation reaction.
Table 2 MOF composites for photocatalytic water splitting
Photocatalysts |
SAa |
Cocatalysts |
Light source |
Products |
Activity |
AQEb |
Ref. |
Sacrificial agents.
Apparent quantum efficiency.
2,3-Dihydro-1,3-dimethyl-2-phenyl-1H-benzimidazole.
Triisopropanolamine.
|
PtPd cubes@UiO-66-NH2 |
Trolamine |
— |
300 W lamp |
H2 |
6.97 μmol h−1 |
— |
48
|
Au/PFC-9 |
Trolamine |
— |
400–800 nm |
H2 |
130 μmol g−1 h−1 |
0.009%@400 nm |
33
|
AuPt@UiO-66 |
Triethylamine |
— |
300 W lamp |
H2 |
340.2 μmol g−1 h−1 |
5.01%@550 nm |
65
|
CoMo6S24@NU1K |
Trolamine |
— |
=390 nm |
H2 |
360 μmol g−1 h−1 |
— |
170
|
MoO3/MIL-125-NH2 |
Triethylamine |
— |
>380 nm |
H2 |
399.0 μmol g−1 h−1 |
0.41%@380 nm |
93
|
Ni2P@UiO-66-NH2 |
Triethylamine |
— |
>380 nm |
H2 |
409.1 μmol g−1 h−1 |
— |
98
|
TiO2@NH2-MIL-125(Ti) |
Trolamine |
— |
AM 1.5G |
H2 |
440 μmol g−1 h−1 |
— |
171
|
Cu-NH2-MIL-125 |
Triethylamine |
— |
=420 nm |
H2 |
490 μmol g−1 h−1 |
6.6%@420 nm |
172
|
Pt-Fc@UiO-66-NH2 |
Trolamine |
— |
>380 nm |
H2 |
514.8 μmol g−1 h−1 |
— |
61
|
Au@NH2-UiO-66/CdS |
Lactic acid |
— |
>420 nm |
H2 |
664.9 μmol g−1 h−1 |
5.1%@400 nm |
173
|
Pd@Pt/UiO-66-NH2 |
Triethylamine |
— |
>380 nm |
H2 |
1200.5 μmol g−1 h−1 |
— |
46
|
Zr-MOF-S@CdS |
Lactic acid |
Pt |
≥420 nm |
H2 |
1861.7 μmol g−1 h−1 |
— |
174
|
Cs2.5H0.5PW12O40@UiO-66-NH2(Hf-Zr) |
Trolamine |
— |
>420 nm |
H2 |
1822 μmol g−1 h−1 |
— |
175
|
Cu-MOL/Ni-MOL |
Ascorbic acid |
— |
≥400 nm |
H2 |
2027 μmol g−1 h−1 |
2.75%@420 nm |
176
|
UiO-66-NH2(Zr/Ti)/MXene |
Trolamine |
Pt |
350–780 nm |
H2 |
2187 μmol g−1 h−1 |
— |
117
|
NH2-MIL-125(Ti)@ZnIn2S4/CdS |
CH3OH |
— |
>400 nm |
H2 |
2.367 mmol g−1 h−1 |
— |
177
|
CdS/Ni-MOF |
Lactic acid |
— |
>420 nm |
H2 |
2508 μmol g−1 h−1 |
13.03%@450 nm |
178
|
p-TCN@U6-3 |
Trolamine |
— |
>420 nm |
H2 |
2628 μmol g−1 h−1 |
— |
179
|
UiO-66-NH2@Pt@UiO-66-H |
Triethylamine |
— |
>380 nm |
H2 |
2708.2 μmol g−1 h−1 |
— |
82
|
CdS/Cd-TCPP |
Trolamine |
— |
≥420 nm |
H2 |
3150 μmol g−1 h−1 |
— |
76
|
AuAg24@UiO-66-NH2 |
Triethylamine |
— |
>380 nm |
H2 |
3.6 mmol g−1 h−1 |
0.53%@380 nm |
54
|
Ni-Sb9@UiO-Ir-C6 |
BIHc |
— |
>420 nm |
H2 |
4.3 mmol g−1 h−1 |
— |
180
|
Ti3C2@MIL-NH2 |
Trolamine, CH3OH |
— |
AM 1.5G |
H2 |
4383.1 μmol g−1 h−1 |
3.14%@420 nm |
116
|
Pt(1.5)/MIL-125-NH-CH2OH |
Trolamine |
— |
>420 nm |
H2 |
4496.4 μmol g−1 h−1 |
— |
62
|
S-NRs/NMOF-Ni |
Lactic acid |
— |
300 W lamp |
H2 |
4500 μmol g−1 h−1 |
11.83%@365 nm |
181
|
Ni-MOF-74/BiVO4/P |
Trolamine |
— |
≥420 nm |
H2 |
4908 μmol g−1 h−1 |
— |
182
|
ZnIn2S4-NiO@MOF |
Trolamine |
— |
≥420 nm |
H2 |
4970.9 μmol g−1 h−1 |
5.91%@405 nm |
183
|
CoPOH/MIL |
Triethylamine |
— |
>385 nm |
H2 |
6.6 mmol g−1 h−1 |
11.4%@390 nm |
184
|
NH2-UiO-66@TFPT-DETH |
Sodium ascorbate |
Pt |
≥420 nm |
H2 |
7178 μmol g−1 h−1 |
1.11%@420 nm |
185
|
CdS/P415-NH2 |
Na2S and Na2SO3 |
— |
>420 nm |
H2 |
138 μmol g−1 min−1 |
8.2%@420 nm |
186
|
NU-1000@ZnIn2S4 |
Trolamine |
— |
≥400 nm |
H2 |
8.53 mmol g−1 h−1 |
5.9%@380 nm |
187
|
CdS@MOF-808 |
Triethylamine |
— |
>420 nm |
H2 |
10.41 mmol g−1 h−1 |
3.28%@400 nm |
188
|
ZnCo2S4/MOF-199 |
Trolamine |
— |
>420 nm |
H2 |
11.6 mmol g−1 h−1 |
4.92%@420 nm |
189
|
HKUST-1/TiO2 |
CH3OH |
— |
300 W lamp |
H2 |
13.25 mmol g−1 h−1 |
— |
190
|
MTV-Ti-MOF/COF |
Ascorbic acid |
Pt |
>420 nm |
H2 |
13.98 mmol g−1 h−1 |
5.9%@515 nm |
191
|
NH2-MIL-125(Ti)/Zn0.5Cd0.5S/NiS |
Trolamine |
Pt |
>420 nm |
H2 |
14 876.7 μmol g−1 h−1 |
24.2%@420 nm |
192
|
20% H2N-Cu-MOF/TpPa-1-COF |
Ascorbic acid |
Pt |
≥420 nm |
H2 |
15.3 mmol g−1 h−1 |
0.72%@420 nm |
193
|
Pt-SAs@Pd-PCN-222-NH2 |
TIPAd |
— |
≥420 nm |
H2 |
16 591 μmol g−1 h−1 |
— |
194
|
UiO-66-(COOH)2/MoS2/ZnIn2S4 |
Na2S and Na2SO3 |
— |
300 W lamp |
H2 |
18.794 mmol g−1 h−1 |
— |
157
|
CdS@PCN-222(Pt) |
Lactic acid |
— |
≥420 nm |
H2 |
29.5 mmol g−1 h−1 |
9.9%@420 nm |
195
|
C60@NU-901 |
Ascorbic acid |
Pt |
300 W lamp |
H2 |
22.3 mmol g−1 h−1 |
0.45%@420 nm |
105
|
ZCS-0.5/MOF-545Co |
Lactic acid |
— |
=420 nm |
H2 |
29.6 mmol g−1 h−1 |
— |
196
|
Au@UiOS@ZnIn2S4 |
Na2S and Na2SO3 |
— |
420–780 nm |
H2 |
39.16 mmol g−1 h−1 |
30.1%@365 nm |
197
|
UiOS-Cu-CdS/ZnS |
Na2S and Na2SO3 |
— |
320–780 nm |
H2 |
42.55 mmol g−1 h−1 |
20.2%@400 nm |
198
|
CuSL-CuBr |
Triethylamine |
— |
420–800 nm |
H2 |
50.28 mmol g−1 h−1 |
0.47%@500 nm |
199
|
ZnIn2S4@PCN-224 |
Na2S and Na2SO3 |
Pt |
>420 nm |
H2 |
68.2 mmol g−1 h−1 |
6.45%@420 nm |
156
|
Liposome-MOF |
— |
Pt, Ir |
400 and 450 nm |
H2 and O2 |
H2: 11.6 μmol g−1 h−1; O2: 6.4 μmol g−1 h−1 |
(1.5 ± 1)%@436 nm |
200
|
Pt@NH2-UiO-66@MnOx |
— |
— |
≥400 nm |
H2 and O2 |
H2: 19.6 μmol g−1 h−1; O2: 10.1 μmol g−1 h−1 |
— |
60
|
Fe2NiCbz-P33 |
— |
— |
≥420 nm |
H2 and O2 |
H2: 170.2 μmol g−1 h−1; O2: 85.1 μmol g−1 h−1 |
∼1.3%@595 nm |
201
|
NH2-MIL-125(Ti)/TpBpy-COF |
— |
Au, MnOx |
>420 nm |
H2 and O2 |
H2: 331.6 μmol g−1 h−1; O2: 165.7 μmol g−1 h−1 |
6.06%@450 nm |
84
|
CdS@ZIF |
— |
— |
≥400 nm |
H2 and O2 |
H2: 346.8 μmol g−1 h−1; O2: 173.4 μmol g−1 h−1 |
1.77%@400 nm |
202
|
A hierarchical ZnIn2S4@PCN-224 composite was integrated by Jin et al. through a facile solvothermal method.156 The optimized composite demonstrated an exceptional visible-light-driven photocatalytic water splitting H2 production rate, achieving 5.68 mmol g−1 h−1 without cocatalyst. With Pt cocatalyst loaded by the in situ growth method, the H2 production rate boosted to 68.2 mmol g−1 h−1, surpassing those of most MOF composites. Structural and mechanistic analyses revealed that the enhanced activity stemmed from the effective Z-scheme heterojunction in ZnIn2S4@PCN-224, which facilitated spatial separation of electron–hole pairs while maintaining strong redox potentials (Fig. 14a). Hierarchical architecture not only enhanced charge carrier dynamics, but also provided abundant active sites.
 |
| Fig. 14 (a) Photocatalytic mechanism of the Z-scheme heterojunction in ZnIn2S4@PCN-224.156 Copyright 2021, Elsevier. (b) Photocatalytic mechanism of CdS@ZIF.202 Copyright 2023, John Wiley and Sons. | |
Ng and coworkers exploited the multifunctional interface between CdS and ZIF-8 (CdS@ZIF) to achieve overall water splitting under irradiation of ≥400 nm.202 In the absence of sacrificial agent and cocatalyst, the optimal H2 and O2 production rates of CdS@ZIF were 346.8 and 173.4 μmol g−1 h−1 with an ideal stoichiometric ratio of 2
:
1. The interface can enrich the photogenerated electrons on CdS to promote H2 production and delocalize photogenerated holes to ZIF to boost O2 production (Fig. 14b). Mechanistic analyses revealed that the intelligently designed interface enhanced the intrinsic catalytic activity of CdS and improved the intrinsic catalytic activity of CdS and improved the transfer and utilization efficiency of charge carriers.
The above reports illustrate the high value of component selection and mechanism research in MOF composites.
3.3 CO2 reduction
As a kind of greenhouse gas, CO2 exacerbates global warming, extreme weather, and ocean acidification, which threatens ecosystems and biodiversity.203–205 Photocatalysis is a promising strategy to reduce CO2 to fuels or chemicals and achieve sustainable carbon cycling.206,207 Among various photocatalysts, MOF composites have demonstrated exceptional potential due to their prominent CO2 capture capabilities.208,209 The following is a summary of the research reports on photocatalytic CO2 reduction with MOF composites (Table 3).
Table 3 MOF composites for photocatalytic CO2 reduction
Photocatalysts |
Photosensitizers |
SAa |
Light source |
Products |
Selectivity |
Activity |
AQEb |
Ref. |
Sacrificial agents.
Apparent quantum efficiency.
Triisopropanolamine.
2,3-Dihydro-1,3-dimethyl-2-phenyl-1H-benzimidazole.
|
Cu2O@Cu3(BTC)2 |
— |
— |
>400 nm |
CH4 |
— |
0.09 μmol h−1 |
— |
211
|
MOF-FA1-W/TiO2/Au |
— |
— |
300–800 nm |
CH4 |
— |
17.2 μmol g−1 h−1 |
— |
212
|
CdS/Ni-MOF |
— |
— |
300 W lamp |
CO |
— |
1.87 μmol g−1 h−1 |
0.05%@365 nm |
213
|
Co-MOF/Cu2O |
— |
— |
>420 nm |
CO |
∼100% |
3.83 μmol g−1 h−1 |
— |
214
|
TTCOF/NH2-UiO-66(Zr) |
— |
— |
≥420 nm |
CO |
98% |
6.56 μmol g−1 h−1 |
0.21%@420 nm |
215
|
ZnIn2S4/MOF-808 |
— |
— |
Xe lamp |
CO |
— |
8.21 μmol g−1 h−1 |
— |
216
|
CD@NH2-UiO-66 |
— |
Trolamine |
>420 nm |
CO |
— |
16.6 μmol g−1 h−1 |
— |
217
|
Co-MOF-3 |
[Ru(bpy)3]Cl2 |
Trolamine |
≥400 nm |
CO |
100% |
27.1 μmol g−1 h−1 |
— |
218
|
Pt@NH2-UiO-66@Cu-TCPP |
— |
Triethylamine |
>400 nm |
CO |
∼100% |
40.2 μmol g−1 h−1 |
— |
219
|
Cs3Bi2Br9/MOF 525 Co |
— |
— |
AM 1.5G |
CO |
99.50% |
61.2 μmol g−1 h−1 |
0.07%@420 nm |
220
|
NH2-UiO-66-Fc |
— |
Trolamine |
400–780 nm |
CO |
100% |
90.65 μmol g−1 h−1 |
0.92%@350 nm |
221
|
[Co2#@Cu-CAT]-CsPbBr3 QDs |
— |
— |
>400 nm |
CO |
— |
133.4 μmol g−1 h−1 |
— |
222
|
Cu NWs@HKUST-1 |
— |
— |
>420 nm |
CO |
92% |
176.2 μmol g−1 h−1 |
— |
223
|
[Emim]BF4@PCN-250-Fe2Co |
— |
— |
>420 nm |
CO |
100% |
313.3 μmol g−1 h−1 |
2.9%@420 nm |
224
|
Zr-MBA-Ru/Re-MOF |
— |
— |
400–800 nm |
CO |
99% |
440 μmol g−1 h−1 |
0.11%@450 nm |
225
|
In-MOF/GO |
— |
— |
>420 nm |
CO |
100% |
762.5 μmol g−1 h−1 |
— |
226
|
Co-MOL@GO |
[Ru(phen)3](PF6)2 |
Trolamine |
=450 nm |
CO |
95% |
18.0 mmol g−1 h−1 |
— |
107
|
PCN-250-Fe2Mn |
[Ru(bpy)3]Cl2 |
TIPAc |
>420 nm |
CO |
82.17% |
21.51 mmol g−1 h−1 |
2.6%@450 nm |
227
|
TiO2/UiO-66 |
— |
— |
300 W lamp |
CO |
90.4% |
1.9 μmol g−1 h−1 |
— |
228
|
CH4 |
17.9 μmol g−1 h−1 |
Zn-MOF/BiVO4 |
— |
— |
>420 nm |
CO |
— |
4.31 μmol g−1 h−1 |
— |
229
|
CH4 |
0.62 μmol g−1 h−1 |
Co-MOF/g-C3N4 |
— |
— |
>420 nm |
CO |
— |
6.75 μmol g−1 h−1 |
— |
230
|
CH4 |
5.47 μmol g−1 h−1 |
CsPbBr3/CuTCPP |
— |
— |
300 W lamp |
CO |
— |
11.8 μmol g−1 h−1 |
0.05%@420 nm |
231
|
CH4 |
2.95 μmol g−1 h−1 |
Ru/MOF-74/C3N4 |
— |
— |
300 W lamp |
CO |
— |
11.8 μmol g−1 h−1 |
7.8%@365 nm |
232
|
CH4 |
7.3 μmol g−1 h−1 |
Cu-BTB-Fe |
— |
Lactic acid |
350–780 nm |
CO |
69.24% |
14.29 μmol g−1 h−1 |
— |
233
|
CH4 |
32.20 μmol g−1 h−1 |
NH2-MIL-68@TP-TA |
— |
— |
300 W lamp |
CO |
— |
25 μmol g−1 h−1 |
— |
234
|
CH4 |
11.67 μmol g−1 h−1 |
Ag/NH2-MIL-125(Ti) (T3-Ag) |
— |
Trolamine |
AM 1.5G |
CO |
— |
26.7 μmol g−1 h−1 |
0.02%@450 nm |
235
|
CH4 |
90.5% |
63.3 μmol g−1 h−1 |
Au@PCN-222 |
— |
— |
≥420 nm |
CO |
— |
29.1 μmol g−1 h−1 |
0.24%@450 nm |
34
|
CH4 |
2.5 μmol g−1 h−1 |
Ni@NTU-9/BiVO4 |
— |
— |
300 W lamp |
CO |
99.20% |
44.5 μmol g−1 h−1 |
— |
78
|
CH4 |
0.625 μmol g−1 h−1 |
Au-NC@MOF |
— |
CH3OH |
300–800 nm |
CO |
— |
57.6 μmol g−1 h−1 |
— |
236
|
CH4 |
1.8 μmol g−1 h−1 |
g-C3N4-RGO-NH2-MIL-125(Ti) |
— |
— |
Visible light |
CO |
96.53% |
95.9 μmol g−1 h−1 |
0.41%@450 nm |
237
|
CH4 |
3.47% |
3.45 μmol g−1 h−1 |
Zr-PS3-FeTCPP0.43 |
— |
Triethylamine |
500 W lamp |
CO |
54.64% |
247.8 μmol g−1 h−1 |
2.2%@360 nm |
238
|
CH4 |
32.28% |
42%-TiO2-in-MIL-101-Cr-NO2 |
— |
— |
300 W lamp |
CO |
91% |
11 mmol g−1 h−1 |
11.3%@350 nm |
75
|
CH4 |
1.1 mmol g−1 h−1 |
g-C3N4/Ma-MbTCPP |
— |
Triethylamine |
360–800 nm |
CO |
29% |
12.3 μmol g−1 h−1 |
— |
239
|
CH4 |
27% |
11.6 μmol g−1 h−1 |
C2H6 |
44% |
18.5 μmol g−1 h−1 |
Au@UiO-67-bpy-Cu |
— |
Trolamine |
>400 nm |
CH3OH |
96% |
118.4 μmol g−1 h−1 |
— |
240
|
TiO2@Cu-BTC-MOF |
— |
Triethylamine |
W lamp |
CH3OH |
— |
4000 μmol g−1 h−1 |
— |
241
|
(CsPbI3)0.25(4%Rh-agZIF-62)0.75 |
— |
Trolamine |
>400 nm |
HCOOH |
— |
0.12 mM h−1 |
— |
111
|
NH2-MIL-125(Ti)–Cu |
— |
Trolamine |
>420 nm |
HCOOH |
— |
30.1 μmol g−1 h−1 |
1.18%@380 nm |
242
|
Cu NCs@UiO-66-NH2 |
— |
Trolamine |
250–385 nm |
HCOOH |
86% |
128 μmol g−1 h−1 |
— |
243
|
PCN-222-Ni@UiO-67-NH2 |
— |
— |
≥420 nm |
HCOOH |
73.2% |
146 μmol g−1 h−1 |
— |
83
|
CA@PCN-222 |
— |
Trolamine |
400–800 nm |
HCOO− |
— |
280.4 μmol g−1 h−1 |
— |
244
|
(PW12,Cp*Rh)@UiO-67 |
[Ru(bpy)3]Cl2 |
Trolamine |
>415 nm |
HCOO− |
— |
357.1 μmol g−1 h−1 |
— |
245
|
Cu2O@POM12@HKUST-4 |
— |
BIHd |
300 W lamp |
HCOOH |
100% |
522.6 μmol g−1 h−1 |
— |
246
|
M68N@In-TCPP |
— |
— |
Sunlight |
HCOOH |
85.4% |
397.5 μmol g−1 h−1 |
0.16%@400 nm |
210
|
CO |
61.2 μmol g−1 h−1 |
Cu2O@Cu-MOF/TiO2 |
— |
— |
320–780 nm |
CH4 |
90% |
366.0 μmol g−1 h−1 |
— |
247
|
CO |
4.5% |
18.17 μmol g−1 h−1 |
C2H6 |
5.5% |
22.71 μmol g−1 h−1 |
Zn2GeO4/ZIF-67 |
— |
— |
350 W lamp |
CH3OH |
31.27% |
5.15 μmol g−1 h−1 |
0.913%@420 nm |
248
|
C2H5OH |
24.73% |
4.08 μmol g−1 h−1 |
Cu SAs/UiO-66-NH2 |
— |
Trolamine |
>400 nm |
CH3OH |
— |
5.33 μmol g−1 h−1 |
— |
249
|
C2H5OH |
4.22 μmol g−1 h−1 |
g-C3N4/CuO@MIL-125(Ti) |
— |
— |
300 W lamp |
CO |
3.4% |
60.0 μmol g−1 h−1 |
3.10%@420 nm |
250
|
CH3OH |
18.9% |
332.4 μmol g−1 h−1 |
CH3CHO |
20.3% |
177.2 μmol g−1 h−1 |
C2H5OH |
57.4% |
501.9 μmol g−1 h−1 |
Ce-UiO-66-bpydc-MOF |
— |
— |
400–800 nm |
CH3COOH |
99.50% |
128 μmol g−1 h−1 |
0.93%@450 nm |
251
|
According to the carbon chain length, CO2 reduction products can be primarily categorized into single-carbon (C1) products (e.g. CO, CH4, CH3OH, and HCOOH) and multi-carbon (C2+) products (e.g. C2H6 and CH3COOH). One example of each category will be given below.
Very recently, Cai and coworkers presented an In-based MOF heterostructure In-NH2-MIL-68@In-TCPP (M68N@In-TCPP) via one-pot synthesis.210 The core–shell architecture integrated the MOFs through competitive linker nucleation with In nodes, forming coherent interfaces that enhanced structural stability and charge transfer. DFT calculations suggested that CO2 molecules were favorable for adsorption at In–N sites of the In-TCPP shell, and H2O molecules were preferably activated at the InO4(OH)2 sites of the M68N shell (Fig. 15a and b). The S-scheme mechanism promoted directed charge separation via built-in electric fields between the components, facilitating the spatial separation of charge carriers. Under concentrated sunlight, M68N@In-TCPP created an unparalleled yield of HCOOH (397.5 μmol g−1 h−1) with a selectivity of 85.4%, which was higher than those of reported MOF-based photocatalysts. Notably, H2O2 (321.2 μmol g−1 h−1) was also detected, achieving the utilization of photogenerated holes without photosensitizers, noble metals, or sacrificial agents. This work demonstrates a well-designed approach for solar-driven CO2-to-chemical conversion, highlighting the potential of MOF composites in sustainable energy and carbon-neutral technology through reactant affinity engineering.
 |
| Fig. 15 DFT calculations of the charge difference density of (a) CO2 adsorption at In–N sites and (b) H2O adsorption at InO4(OH)2 sites. Magenta, red, light blue, brown, and pink spheres represent In, O, N, C, and H atoms, respectively.210 Copyright 2025, Springer Nature. (c) CO2 adsorption–desorption isotherms of Ce-MOF and Ce-MOF-RuII-bpy at 298 K.251 Copyright 2023, Royal Society of Chemistry. | |
Karmakar et al. reported a visible-light-driven photocatalytic system with post-synthetic modified Ce-UiO-66-bpydc grafted with [Ru(bpy)2Cl2].251 The obtained Ce-MOF-RuII-bpy promoted efficient metal-to-ligand charge transfer (MLCT) and leveraged the vacant low-lying 4f orbital of CeIV to facilitate rapid electron transport, as verified by TAS and X-ray structure absorption near edge spectroscopy (XANES). Under visible light (400–800 nm) irradiation, Ce-MOF-RuII-bpy achieved exceptional selectivity (99.5%) for double-carbon (C2) product generation in aqueous media while suppressing the formation of C1 and H2 byproducts. Ce-MOF-RuII-bpy demonstrated a significantly enhanced activity with a CH3COOH production rate of 128 μmol g−1 h−1, representing a 7.4-fold improvement over Ce-MOF. In CO2 adsorption measurements, the modified MOF achieved a saturation capacity of 37 cm3 g−1, which exceeded that of the pristine MOF by 1.9 times (Fig. 15c), indicating the significance of CO2 adsorption capability in determining catalytic performance. According to DFT calculations, CeIII was identified as the active site for CO2 reduction. The in situ DRIFTS and Gibbs free energy analysis revealed the C–C coupling pathway for CH3COOH synthesis. The synergistic effect of an appropriate photosensitizer, pore confinement of Ce-MOF, and unsaturated Ce sites with a low-lying orbital contributed to the impressive high selectivity toward the C2 product, which provides new insights into MOF composites in photocatalytic CO2 reduction.
3.4 N2 fixation
Nitrogen plays an indispensable role in modern agriculture and industry. Paradoxically, N2, which constitutes 78% of the atmosphere, exists as a thermodynamically stable triple-bonded molecule. Therefore, chemically inert N2 needs to be fixed and converted to NH3 or other nitrogenous compounds.252,253 Photocatalytic N2 fixation is considered a promising strategy for N2 fixation.254 Recent advances demonstrate the emerging potential of MOF composites in photocatalytic N2 fixation owing to their structural tunability and active site accessibility (Table 4).255
Table 4 MOF composites for photocatalytic N2 fixation
Photocatalysts |
SAa |
Light source |
Products |
Activity |
AQEb |
Ref. |
Sacrificial agents.
Apparent quantum efficiency.
|
Nano-SH-MOF@H-C3N4 |
— |
>420 nm |
NH3 |
0.12 μg mL−1 h−1 |
0.12%@500 nm |
256
|
Ru@MIL-125/MnOx |
— |
>420 nm |
NH3 |
10.43 μmol g−1 h−1 |
0.17%@500 nm |
257
|
CeO2/UNH(Ce) |
— |
250 W Hg light |
NH3 |
47.55 μmol L−1 h−1 |
— |
258
|
Pmo10V2@MIL-88A |
Na2SO3 |
300 W Xe lamp |
NH3 |
50.82 μmol g−1 h−1 |
0.29%@380 nm |
259
|
Ru1/d-UiO-66 |
— |
300 W Xe lamp |
NH3 |
53.28 μmol g−1 h−1 |
0.34%@300 nm |
72
|
Ru/DUT-67(Zr) |
— |
300 W Xe lamp |
NH3 |
61.1 μmol g−1 h−1 |
1.07%@280 nm |
260
|
Ti3C2-QD/Ni-MOF |
Na2SO3 |
300 W Xe lamp |
NH3 |
88.79 μmol g−1 h−1 |
— |
119
|
GSCe |
— |
=365 nm |
NH3 |
110.24 μmol L−1 h−1 |
9.25%@365 nm |
261
|
Au@PCN-221(Fe) |
— |
300 W Xe lamp |
NH3 |
129.2 μmol g−1 h−1 |
0.33%@365 nm |
262
|
UiO-66/PDA/CNNS |
K2SO3 |
300 W Xe lamp |
NH3 |
147.8 μmol g−1 h−1 |
0.86%@380 nm |
263
|
Ru@Mo-MOF-tri |
— |
>400 nm |
NH3 |
637 μmol g−1 h−1 |
— |
264
|
Mo72Fe30@UiO-66 |
— |
300 W Xe lamp |
HNO3 |
702.4 μg g−1 h−1 |
0.072%@380 nm |
265
|
MIL-125-NH2@Co-HHTP |
— |
AM 1.5 G |
NH3 |
2.1 mmol g−1 h−1 |
16.2%@365 nm |
266
|
Ru/MOF-74/C3N4 |
CH3OH |
300 W Xe lamp |
NH3 |
8.1 mmol g−1 h−1 |
— |
232
|
Au@UiO-66/PTFE membranes |
— |
>400 nm |
NH3 |
18.9 mmol g−1 h−1 |
1.54%@520 nm |
32
|
Ding et al. developed a Ru-anchored MOF-74/C3N4 composite via in situ synthesis (Fig. 16a).232 With the dual validation of Nessler's agent and an ammonium ion composite electrode, a superior NH3 yield of 8.1 mmol g−1 h−1 was detected over Ru/MOF-74/C3N4 under a 300 W Xe lamp, which is 3 times that of MOF-74/C3N4 and 6 times that of pure C3N4. The new energy level in the bandgap of MOF-74 introduced by Ru SAs and the type-II heterojunction mechanism inhibited electron–hole recombination while suppressing competing hydrogen evolution. DFT calculations demonstrated that Ru SAs can effectively decrease the energy barrier and Gibbs free energy in N2 fixation. Pristine MOF-74 had no adsorption ability for N2, which was consistent with the result that MOF-74 exhibited no obvious activity.
 |
| Fig. 16 (a) The synthesis process of a Ru-anchored MOF-74/C3N4 composite.232 Copyright 2023, Elsevier. (b) Schematic illustration of the efficient storage and conversion of N2 to HNO3 by Mo72Fe30@UiO-66.265 Copyright 2023, John Wiley and Sons. | |
Apart from NH3, NO3− is also an important product in N2 fixation. Li and coworkers designed a dual-active-site photocatalyst by integrating polyoxometalate (POM) Mo72Fe30 with UiO-66 for photocatalytic N2 fixation under a 300 W Xe lamp (Fig. 16b).265 The coordination microenvironment was modified to create unsaturated metal clusters with Lewis-acidic d-orbitals in UiO-66, promoting N2 adsorption through 3σg orbital electron acceptance. The temperature-programmed desorption (TPD) characterization showed that Mo72Fe30@UiO-66 possessed one more desorption peak than UiO-66, indicating the better N2 adsorption capacity of Mo72Fe30@UiO-66. Acting as electron sponges, Mo72Fe30 provided electrons to UiO-66, while holes accumulated on Mo72Fe30 for N2 activation. According to the ion chromatograph results, the optimized HNO3 yield of Mo72Fe30@UiO-66 was 702.4 μg g−1 h−1, the better N2 adsorption capacity of Mo72Fe30@UiO-66. Acting as an electron sponge, Mo72Fe30 provided electrons without sacrificial agent, 7 times and 24 times higher than that of UiO-66 and that of Mo72Fe30.
As demonstrated by the above two examples, the pivotal factor in photocatalytic N2 fixation is N2 adsorption, where MOFs exhibit exceptional advantage. Through rational structural engineering, the N2 adsorption capacity of MOF composites can be precisely modulated, which effectively facilitates the subsequent catalytic process.
4. Conclusion and prospects
The rapid development of MOF composites for photocatalysis has gained significant momentum due to the unique flexibility and compatibility of MOFs. Integrating MOFs with other functional materials, such as metal NPs, semiconductors, and reticular materials, has transcended the limitations of pristine MOFs and further expanded the potential of MOF-based photocatalysts. These systems leverage synergistic effects that enhance light absorption, charge separation, and surface catalytic efficiency, effectively addressing some of the intrinsic limitations of pristine MOFs. Consequently, MOF composites have demonstrated performance across a variety of photocatalytic applications, including contaminant degradation, water splitting, CO2 reduction, and N2 fixation. The ability to engineer the electronic properties and catalytic sites within MOF composites allows for fine-tuning of the photocatalytic activity and selectivity.
Although MOF composites have demonstrated remarkable potential in photocatalysis, significant hurdles remain in translating these materials from laboratory research to practical applications. For metal/MOF composites, key challenges involve suppressing nanoparticle sintering and establishing robust metal–support interactions, as uncontrolled aggregation or residual surfactants can significantly compromise catalytic activity. Future research should focus on atomic-level precision synthesis to tailor the size, composition, and spatial distribution of metal clusters within MOFs, thereby enhancing metal–MOF coupling for improved performance.
The integration of semiconductors with MOFs often faces challenges such as rapid charge recombination and unfavorable band alignment. To address these issues, carefully engineered semiconductor/MOF heterojunctions (e.g., type II, Z-scheme, or S-scheme) can significantly enhance charge separation and photocatalytic efficiency. Furthermore, selecting semiconductors with complementary electronic properties and precisely tuning their band structures, through linker functionalization or strategic doping, offers a promising strategy to suppress recombination losses while extending light absorption across a broader spectral range.
One major challenge in developing reticular material/MOF composites has been the difficulty of establishing strong covalent bonding between COFs and MOFs at their interfaces, primarily due to distinct chemical natures. This limitation results in weak interfacial connections that significantly hinder efficient charge-carrier transfer and separation. A key solution is post-synthetic functionalization of the MOF or COF to introduce complementary reactive groups that form covalent linkages. Similar strategies include growing a COF directly on the MOF surface or using layer-by-layer assembly to create intimate, well-anchored interfaces. Looking ahead, atomic-level assembly of two-dimensional MOF and COF layers (2D/2D heterostructures) is a promising frontier-precisely stacking MOF nanosheets with COF sheets to engineer the interface on the atomic scale.
Other material/MOF composites offer unique opportunities but also present distinct challenges that demand customized solutions. For UCNPs/MOF systems, the primary limitation stems from the low quantum yield of UCNPs, severely constraining their near-infrared light utilization efficiency. Moreover, several critical issues hinder the photocatalytic performance of various MOF-based composites: the poor electronic conductivity of metal oxide/MOF systems, the intricate synthesis procedures required for metal phosphide/MOF hybrids, the limited thermal stability of metal sulfide/MOF composites, and the inadequate cycling durability of carbon material/MOF photocatalysts. Developing cost-effective strategies to integrate emerging functional materials (e.g., MXenes, COFs, and 2D materials) with MOFs represents a promising direction for future research in this field.
In addition to the aforementioned potential approaches for achieving each of the strategies, innovative strategies are needed to unlock the full potential of MOF composites in photocatalysis.
4.1 Structural control and precise design
Presently, the combination of MOFs and other components into composites, in many cases, lacks elaborate structural control.267 Fabrication of MOF composites at molecular and even atomic scales, such as precise location control of the guest species,268 would be significant not only for fundamental structure–property understanding but also for optimized photocatalytic performance. Future advancements in this field can focus on atomic-level positioning of active sites. Developing synthetic strategies to precisely anchor catalytic species (e.g., single atoms, clusters, or co-catalysts) at specific locations within MOFs (e.g., nodes, linkers, or pore cavities) could enhance charge transfer and active-site accessibility. For hierarchical structuring of MOF composites, beyond simple hybridization, future designs should consider multi-scale structural engineering, including controlled spatial distribution of components (e.g., core–shell, Janus, or spatially graded architectures) to optimize light absorption, charge separation, and reactant diffusion.
4.2 Exploring the roles of the components
As the structure–function relationships of MOF composites grow increasingly complex, exploring the interplay between various factors influencing their performance is crucial for designing enhanced MOF-based photocatalysts. Distinct from traditional inorganic semiconductors, the well-defined structures of MOFs offer significant advantages in precisely unveiling the photocatalytic mechanism. In previous reports, a series of standardized characterization techniques have been employed to comprehensively evaluate the properties of MOF composites, such as powder X-ray diffraction for crystallographic structure determination, electron microscopy for morphological characterization, N2 adsorption–desorption analysis for porosity and specific surface area evaluation, diffuse reflectance ultraviolet-visible spectroscopy for light absorption range measurement, X-ray photoelectron spectroscopy for surface elemental composition and electronic transfer analysis, and photoluminescence spectroscopy for charge carrier separation efficiency assessment. The multi-technique approach ensures fundamental understanding of the structural and functional characteristics of MOF composites. Moreover, with theoretical calculations269 and advanced characterization techniques such as TAS,200 XAS,270 KPFM,218 and in situ DRIFTS,226 MOF composites can be accurately characterized, encompassing quantifying interfacial stresses in interface interactions and accurate tracing of electron flow to clarify the charge transfer mechanisms in MOF composites. This deeper insight into their structural and functional intricacies will lead to more foundational understanding of photocatalytic processes.
4.3 Microenvironment modulation around catalytic sites
Thanks to the atomically precise tunability of MOF structures and inspired by enzymatic catalysis, MOFs offer an ideal platform for microenvironment modulation around catalytic centers,271 which presents a significant opportunity to enhance photocatalytic performance. However, current investigations into this topic are still limited and need to be strengthened. Future studies should focus on developing advanced synthetic strategies to systematically modify SBUs and organic linkers to create tailored microenvironments, such as confined hydrophobic pockets or charged domains, favoring specific photocatalytic reactions. Machine learning and DFT calculations are utilized to predict optimal microenvironment configurations for specific reactions, accelerating the discovery of high-performance MOF photocatalysts.
4.4 Developing MOF composites for tandem photocatalytic reactions
Achieving high selectivity and catalytic efficiency in photocatalytic reactions remains a significant challenge, particularly in complex, multi-step processes.272 MOF composites, integrating multiple functional components can mimic natural enzymatic systems where cascade reactions occur in a confined environment. By precisely controlling the spatial distribution and electronic interactions between different active sites, these composites could enable synergistic effects, such as enhanced charge separation, substrate channeling, and intermediate stabilization. The development of multi-component MOF composites,273 where different active sites work in concert to catalyze sequential reactions, can further improve catalytic efficiency and expand the scope of possible reactions.
4.5 Enhancing stability
Although MOF composites for photocatalysis hold immense promise, their stability during catalytic reactions is a major concern.274 The degradation of MOF structures under prolonged light irradiation, in harsh chemical environments, or under thermal fluctuations can significantly reduce their photocatalytic efficiency and recyclability. Moreover, the decomposition of MOF composites may generate potential false positive catalytic results.22 Although isotopic labeling can be used to identify product sources, it has limitations such as incomplete detection of molecular ion signatures, discrepancies between ion flow and molecular ion peak intensities, and inconsistent proportionality between 13C and 16O isotopic fragments. To address this challenge, future research should focus on multiple strategies to enhance the robustness of MOF composites: incorporating protective coatings (e.g., carbon layers, polymers, or inorganic shells) can shield MOFs from degradation while maintaining photocatalytic activity; developing dynamic MOF composites capable of self-repairing minor structural damage (e.g., via reversible ligand exchange or guest-induced healing) could extend their operational lifespan. Additionally, many MOF-based photocatalysts rely on sacrificial agents (e.g., triethanolamine and triethylamine) to enhance charge separation, but these additives may accelerate MOF decomposition. To address this limitation, overall redox photocatalysis has emerged as a promising strategy, in which reduction and oxidation reactions are coupled within a single system, increasing the durability of the catalyst and the economic value by avoiding the use of sacrificial agents.275,276
4.6 Scalable and sustainable synthesis
While significant progress has been made in synthesizing MOF composites to promote photocatalytic performance, many of the methods developed are not easily scalable or cost-effective for large-scale production.277 Conventional solvothermal synthesis often requires prolonged reaction times, high energy consumption, and large quantities of organic solvents, which raises economic and ecological concerns. To address these limitations, techniques such as microwave-assisted synthesis, continuous flow production, electrochemical routes, and mechanochemical methods can be optimized for the scalable production of MOF composites.278,279 By advancing these scalable synthesis techniques, the field can move toward economically viable and environmentally friendly production of MOF composites, unlocking their full potential for real-world photocatalytic applications.
4.7 Exploring novel MOF composites
The discovery and exploration of new MOF composites, particularly those with unique structures or properties, can open up new avenues for photocatalysis. In this regard, large language models (LLMs),280,281 machine learning (ML),282 artificial intelligence (AI),283 and high-throughput screening protocols284 can accelerate the development of novel MOFs with desirable photocatalytic properties. Additionally, exploring unconventional MOF structures, such as those with mixed-metal nodes,285 flexible frameworks,286 or hierarchical porosity,287 can lead to the development of materials with unprecedented photocatalytic performance. Mixed-metal nodes may introduce synergistic electronic effects, improving charge carrier dynamics, while flexible MOFs could enable adaptive guest interactions for enhanced substrate activation. Hierarchical porosity, combining micro- and mesopores, can facilitate mass transport and expose more active sites, crucial for large-molecule photocatalytic reactions.
More than that, a persistent challenge in MOF-based photocatalysis research lies in the prevalence of conceptual ambiguities and oversimplified mechanistic interpretations, frequently arising from inadequate experimental evidence and incomplete mechanistic understanding. To establish reliable structure–activity relationships, comprehensive characterization of MOF composites must employ advanced spectroscopic methods. Essential spectroscopic tools include in situ DRIFTS for monitoring surface-bound intermediates, EPR spectroscopy for identifying radical species and paramagnetic centers, and time-resolved photoluminescence (TRPL) for quantifying excited-state lifetimes and charge-carrier dynamics. These techniques, particularly when complemented by transient absorption spectroscopy, offer direct insights into charge-transfer mechanisms and trap-state distributions that govern photocatalytic activity. Moreover, to prevent mechanistic oversimplification, we strongly recommend correlating observations from multiple orthogonal techniques, including EPR, in situ DRIFTS, and UV-vis spectroscopy, with theoretical band-structure calculations. Such a multimodal approach provides more reliable evidence than performance enhancement alone for identifying active species. Particularly crucial are in situ and operando measurements under actual catalytic conditions, which enable direct correlation between observed intermediates and functional behaviour.
In summary, the journey towards optimizing MOF composites for photocatalysis is a multifaceted endeavor, requiring collaboration across chemistry, materials science, and engineering. With continued innovation in material design, mechanistic insights, and scalable fabrication, MOF composites are poised to revolutionize photocatalysis, contributing to sustainable energy solutions and environmental remediation. The future promises an era where MOF composites shine even brighter in photocatalysis.
Data availability
No primary research results, software, or code have been included, and no new data were generated or analyzed as part of this review.
Author contributions
Chenxi Zhang: conceptualization, funding acquisition, visualization, writing – original draft, writing – review & editing. Yanhong Wu: investigation, visualization, writing – review & editing. Dandan Li: conceptualization, funding acquisition, writing – review & editing. Hai-Long Jiang: conceptualization, funding acquisition, project administration, supervision, writing – review & editing.
Conflicts of interest
There are no conflicts to declare.
Acknowledgements
This work was supported by the National Key Research and Development Program of China (2021YFA1500400), the National Natural Science Foundation of China (U22A20401, 22331009, 22302147, W2512006, 22171001, and 22475001), the Strategic Priority Research Program of the Chinese Academy of Sciences (XDB0450302 and XDB0540000), and the Natural Science Foundation of Anhui Province (2408085Y010).
References
- J. Gong, C. Li and M. R. Wasielewski, Chem. Soc. Rev., 2019, 48, 1862–1864 RSC.
- A. Wagner, C. D. Sahm and E. Reisner, Nat. Catal., 2020, 3, 775–786 CrossRef CAS.
- Z. Wang, T. Hisatomi, R. Li, K. Sayama, G. Liu, K. Domen, C. Li and L. Wang, Joule, 2021, 5, 344–359 CrossRef CAS.
- K. Sun, Y. Huang, F. Sun, Q. Wang, Y. Zhou, J. Wang, Q. Zhang, X. Zheng, F. Fan, Y. Luo, J. Jiang and H.-L. Jiang, Nat. Chem., 2024, 16, 1638–1646 CrossRef CAS PubMed.
- S. E. Braslavsky, A. M. Braun, A. E. Cassano, A. V. Emeline, M. I. Litter, L. Palmisano, V. N. Parmon and N. Serpone, Pure Appl. Chem., 2011, 83, 931–1014 CrossRef CAS.
- R. Su, Y. Zhu, B. Gao and Q. Li, Water Res., 2024, 251, 121119 CrossRef CAS PubMed.
- S. Thakur, A. Ojha, S. K. Kansal, N. K. Gupta, H. C. Swart, J. Cho, A. Kuznetsov, S. Sun and J. Prakash, Adv. Powder Mater., 2024, 3, 100233 CrossRef.
- F. Wang and H. Duan, Chem Catal., 2022, 2, 644–646 CrossRef CAS.
- H. Jiao, C. Wang, L. Xiong and J. Tang, Acc. Mater. Res., 2022, 3, 1206–1219 CrossRef CAS.
- H.-G. Jin, P.-C. Zhao, Y. Qian, J.-D. Xiao, Z.-S. Chao and H.-L. Jiang, Chem. Soc. Rev., 2024, 53, 9378–9418 RSC.
- Q. Wang and K. Domen, Chem. Rev., 2020, 120, 919–985 CrossRef CAS PubMed.
- C. Xu, P. Ravi Anusuyadevi, C. Aymonier, R. Luque and S. Marre, Chem. Soc. Rev., 2019, 48, 3868–3902 Search PubMed.
- A. Meng, L. Zhang, B. Cheng and J. Yu, Adv. Mater., 2019, 31, 1807660 CrossRef.
- J. Shi, J. Zhang, L. Yang, M. Qu, D.-C. Qi and K. H. L. Zhang, Adv. Mater., 2021, 33, 2006230 CrossRef CAS.
- H. Furukawa, K. E. Cordova, M. O'Keeffe and O. M. Yaghi, Science, 2013, 341, 1230444 CrossRef.
- H.-C. J. Zhou and S. Kitagawa, Chem. Soc. Rev., 2014, 43, 5415–5418 RSC.
- G. Cai, P. Yan, L. Zhang, H.-C. Zhou and H.-L. Jiang, Chem. Rev., 2021, 121, 12278–12326 CrossRef CAS.
- R.-J. Wei, P.-Y. You, H. Duan, M. Xie, R.-Q. Xia, X. Chen, X. Zhao, G.-H. Ning, A. I. Cooper and D. Li, J. Am. Chem. Soc., 2022, 144, 17487–17495 CrossRef CAS.
- B.-T. Liu, S.-H. Gong, X.-T. Jiang, Y. Zhang, R. Wang, Z. Chen, S. Zhang, K. O. Kirlikovali, T.-F. Liu, O. K. Farha and R. Cao, Nat. Synth., 2023, 2, 873–879 CrossRef CAS.
- W. Gong, X. Chen, M. Wahiduzzaman, H. Xie, K. O. Kirlikovali, J. Dong, G. Maurin, O. K. Farha and Y. Cui, J. Am. Chem. Soc., 2024, 146, 2141–2150 CrossRef CAS PubMed.
- J.-D. Xiao and H.-L. Jiang, Acc. Chem. Res., 2019, 52, 356–366 CrossRef CAS PubMed.
- K. Sun, Y. Qian and H.-L. Jiang, Angew. Chem., Int. Ed., 2023, 62, e202217565 CrossRef CAS PubMed.
- W. Wang, D. Chen, F. Li, X. Xiao and Q. Xu, Chem, 2024, 10, 86–133 CAS.
- A. Dhakshinamoorthy, Z. Li, S. Yang and H. Garcia, Chem. Soc. Rev., 2024, 53, 3002–3035 RSC.
- J. Guo, Y. Wan, Y. Zhu, M. Zhao and Z. Tang, Nano Res., 2021, 14, 2037–2052 CrossRef CAS.
- Y. Qian, F. Zhang and H. Pang, Adv. Funct. Mater., 2021, 31, 2104231 CrossRef CAS.
- D. Chen, Y.-T. Zheng, N.-Y. Huang and Q. Xu, EnergyChem, 2024, 6, 100115 CrossRef CAS.
- A. Hayat, S. Rauf, B. Al Alwan, A. El Jery, N. Almuqati, S. Melhi, M. A. Amin, Y. Al-Hadeethi, M. Sohail, Y. Orooji and W. Lv, Mater. Today Energy, 2024, 41, 101542 CrossRef CAS.
- Q. Yang, Q. Xu and H.-L. Jiang, Chem. Soc. Rev., 2017, 46, 4774–4808 RSC.
- S. Li, P. Miao, Y. Zhang, J. Wu, B. Zhang, Y. Du, X. Han, J. Sun and P. Xu, Adv. Mater., 2021, 33, 2000086 CrossRef CAS.
- B. Zhang, X. Cao, J. Wen, S. Guo, X. Duan and X.-M. Zhang, Coord. Chem. Rev., 2024, 518, 216113 CrossRef CAS.
- L.-W. Chen, Y.-C. Hao, Y. Guo, Q. Zhang, J. Li, W.-Y. Gao, L. Ren, X. Su, L. Hu, N. Zhang, S. Li, X. Feng, L. Gu, Y.-W. Zhang, A.-X. Yin and B. Wang, J. Am. Chem. Soc., 2021, 143, 5727–5736 CrossRef CAS.
- Q.-Q. Huang, Z.-B. Fang, K. Pang, W.-K. Qin, T.-F. Liu and R. Cao, Adv. Funct. Mater., 2022, 32, 2205147 Search PubMed.
- T. Huang, J. Han, Z. Li, Y. Hong, X. Gu, Y. Wu, Y. Zhang and S. Liu, Angew. Chem., Int. Ed., 2025, 64, e202500269 CrossRef CAS PubMed.
- K. M. Choi, D. Kim, B. Rungtaweevoranit, C. A. Trickett, J. T. D. Barmanbek, A. S. Alshammari, P. Yang and O. M. Yaghi, J. Am. Chem. Soc., 2017, 139, 356–362 CrossRef CAS PubMed.
- Q. Liu, C. Zeng, L. Ai, Z. Hao and J. Jiang, Appl. Catal., B, 2018, 224, 38–45 CrossRef CAS.
- L. Xiao, Q. Zhang, P. Chen, L. Chen, F. Ding, J. Tang, Y.-J. Li, C.-T. Au and S.-F. Yin, Appl. Catal., B, 2019, 248, 380–387 CrossRef CAS.
- M. Sayed, J. Yu, G. Liu and M. Jaroniec, Chem. Rev., 2022, 122, 10484–10537 Search PubMed.
- Y. Zhang, F. Ma, M. Ling, H. Zheng, Y. Wu and L. Li, Chem. Eng. J., 2023, 464, 142762 CrossRef CAS.
- H. Wang, L. Zhang, Z. Chen, J. Hu, S. Li, Z. Wang, J. Liu and X. Wang, Chem. Soc. Rev., 2014, 43, 5234–5244 RSC.
- S. Bai, J. Jiang, Q. Zhang and Y. Xiong, Chem. Soc. Rev., 2015, 44, 2893–2939 RSC.
- Y.-Z. Chen, Z. U. Wang, H. Wang, J. Lu, S.-H. Yu and H.-L. Jiang, J. Am. Chem. Soc., 2017, 139, 2035–2044 Search PubMed.
- P. Kumari, N. Bahadur, L. Kong, L. A. O'Dell, A. Merenda and L. F. Dumée, Mater. Adv., 2022, 3, 2309–2323 RSC.
- J.-D. Xiao, Q. Shang, Y. Xiong, Q. Zhang, Y. Luo, S.-H. Yu and H.-L. Jiang, Angew. Chem., Int. Ed., 2016, 55, 9389–9393 Search PubMed.
- J.-D. Xiao, L. Han, J. Luo, S.-H. Yu and H.-L. Jiang, Angew. Chem., Int. Ed., 2018, 57, 1103–1107 Search PubMed.
- Y. Pan, Y. Qian, X. Zheng, S.-Q. Chu, Y. Yang, C. Ding, X. Wang, S.-H. Yu and H.-L. Jiang, Natl. Sci. Rev., 2021, 8, nwaa224 Search PubMed.
- Z.-X. Sun, K. Sun, M.-L. Gao, Ö. Metin and H.-L. Jiang, Angew. Chem., Int. Ed., 2022, 61, e202206108 CrossRef CAS.
- Y. Wang, W. Zhang, D. Li, J. Guo, Y. Yu, K. Ding, W. Duan, X. Li, H. Liu, P. Su, B. Liu and J. Li, Adv. Sci., 2021, 8, 2004456 Search PubMed.
- W. Zhang, A. R. Mohamed and W.-J. Ong, Angew. Chem., Int. Ed., 2020, 59, 22894–22915 Search PubMed.
- J. Abdul Nasir, A. Munir, N. Ahmad, T. u. Haq, Z. Khan and Z. Rehman, Adv. Mater., 2021, 33, 2105195 CrossRef CAS PubMed.
- G. Liao, C. Li, S.-Y. Liu, B. Fang and H. Yang, Trends Chem., 2022, 4, 111–127 Search PubMed.
- S. Chen, C. Li, K. Domen and F. Zhang, Joule, 2023, 7, 2445–2467 CrossRef CAS.
- Q. Xu, L. Zhang, J. Yu, S. Wageh, A. A. Al-Ghamdi and M. Jaroniec, Mater. Today, 2018, 21, 1042–1063 CrossRef CAS.
- H. Wang, X. Zhang, W. Zhang, M. Zhou and H.-L. Jiang, Angew. Chem., Int. Ed., 2024, 63, e202401443 CrossRef CAS PubMed.
- J. Yang, D. Wang, H. Han and C. Li, Acc. Chem. Res., 2013, 46, 1900–1909 Search PubMed.
- B. Qiu, M. Du, Y. Ma, Q. Zhu, M. Xing and J. Zhang, Energy Environ. Sci., 2021, 14, 5260–5288 RSC.
- W. Gao, H. Li, J. Hu, Y. Yang, Y. Xiong, J. Ye, Z. Zou and Y. Zhou, Chem. Sci., 2024, 15, 14081–14103 Search PubMed.
- Z. Li, J.-D. Xiao and H.-L. Jiang, ACS Catal., 2016, 6, 5359–5365 CrossRef CAS.
- X. Ma, L. Wang, Q. Zhang and H.-L. Jiang, Angew. Chem., Int. Ed., 2019, 58, 12175–12179 CrossRef CAS.
- J. Zhang, T. Bai, H. Huang, M.-H. Yu, X. Fan, Z. Chang and X.-H. Bu, Adv. Mater., 2020, 32, 2004747 CrossRef CAS.
- M. Xu, D. Li, K. Sun, L. Jiao, C. Xie, C. Ding and H.-L. Jiang, Angew. Chem., Int. Ed., 2021, 60, 16372–16376 CrossRef CAS.
- X. Huang, X. Li, Q. Luan, K. Zhang, Z. Wu, B. Li, Z. Xi, W. Dong and G. Wang, Nano Res., 2021, 14, 4250–4257 CrossRef CAS.
- Y.-N. Gong, J.-H. Mei, J.-W. Liu, H.-H. Huang, J.-H. Zhang, X. Li, D.-C. Zhong and T.-B. Lu, Appl. Catal., B, 2021, 292, 120156 CrossRef CAS.
- S. Wang, K. Gao, Y. Cui, S. Li, H. Zhang, B. Zhang, J. Wu, H. Hou and S. Zang, Nano Res., 2023, 16, 4715–4722 CrossRef CAS.
- Y. Wang, B. Niu, Z. Zhang, J. Li, H. Sheng, W. Xu, J. Cheng, Z. Hao, D. Duan and J. Li, Nano Lett., 2024, 24, 12628–12633 CrossRef CAS.
- L. Yuan, P. Du, C. Zhang, Y. Xi, Y. Zou, J. Li, Y. Bi, T. Bao, C. Liu and C. Yu, Appl. Catal., B, 2025, 364, 124855 CrossRef CAS.
- Z.-H. Xue, D. Luan, H. Zhang and X. W. Lou, Joule, 2022, 6, 92–133 CrossRef CAS.
- H. Liu, M. Cheng, Y. Liu, J. Wang, G. Zhang, L. Li, L. Du, G. Wang, S. Yang and X. Wang, Energy Environ. Sci., 2022, 15, 3722–3749 RSC.
- P. Zhou, M. Luo and S. Guo, Nat. Rev. Chem., 2022, 6, 823–838 CrossRef CAS PubMed.
- K. Kong, H. Zhang, A. Han, F. Li and D. Wang, Energy Environ. Sci., 2024, 17, 7649–7680 RSC.
- S.-M. Wu and P. Schmuki, Adv. Mater., 2025, 37, 2414889 CrossRef CAS PubMed.
- G. Ren, J. Zhao, Z. Zhao, Z. Li, L. Wang, Z. Zhang, C. Li and X. Meng, Angew. Chem., Int. Ed., 2024, 63, e202314408 Search PubMed.
- Y. Pan, D. Li and H.-L. Jiang, Chem.–Eur. J., 2018, 24, 18403–18407 CrossRef CAS PubMed.
- H.-Q. Xu, S. Yang, X. Ma, J. Huang and H.-L. Jiang, ACS Catal., 2018, 8, 11615–11621 CrossRef.
- Z. Jiang, X. Xu, Y. Ma, H. S. Cho, D. Ding, C. Wang, J. Wu, P. Oleynikov, M. Jia, J. Cheng, Y. Zhou, O. Terasaki, T. Peng, L. Zan and H. Deng, Nature, 2020, 586, 549–554 Search PubMed.
- W. Xu, J. Wang, H. Yu, P. Liu, G.-R. Zhang, H. Huang and D. Mei, Appl. Catal., B, 2022, 308, 121218 CrossRef CAS.
- Z.-F. Lin, T.-H. Wang, P. Venkatesan and R.-A. Doong, Chem. Eng. J., 2025, 505, 159411 CrossRef CAS.
- L. Zhao, J. Bian, X. Zhang, L. Bai, L. Xu, Y. Qu, Z. Li, Y. Li and L. Jing, Adv. Mater., 2022, 34, 2205303 CrossRef CAS PubMed.
- K. Sun, Y. Qian, D. Li and H.-L. Jiang, Adv. Mater., 2024, 2411118 Search PubMed.
- C. Liu, L. Lin, Q. Sun, J. Wang, R. Huang, W. Chen, S. Li, J. Wan, J. Zou and C. Yu, Chem. Sci., 2020, 11, 3680–3686 RSC.
- Y. Li, L. Liu, T. Meng, L. Wang and Z. Xie, ACS Nano, 2023, 17, 2932–2942 Search PubMed.
- S. Wang, Z. Ai, X. Niu, W. Yang, R. Kang, Z. Lin, A. Waseem, L. Jiao and H.-L. Jiang, Adv. Mater., 2023, 35, 2302512 Search PubMed.
- H.-B. Huang, Z.-B. Fang, R. Wang, L. Li, M. Khanpour, T.-F. Liu and R. Cao, Small, 2022, 18, 2200407 Search PubMed.
- X. Chu, S. Liu, B.-B. Luan, Y. Zhang, Y. Xi, L.-H. Shao, F.-M. Zhang and Y.-Q. Lan, Angew. Chem., Int. Ed., 2025, 64, e202422940 CrossRef CAS PubMed.
- X. Chen, X. Zhang and Y. Zhao, Chem. Soc. Rev., 2025, 54, 152–177 Search PubMed.
- X. Li, H. Wu, S. Yin, C. Yu, Y. Shao, D. Zhou and P. She, Chem. Synth., 2025, 5, 29 CrossRef CAS.
- D. Li, S.-H. Yu and H.-L. Jiang, Adv. Mater., 2018, 30, 1707377 CrossRef PubMed.
- M. Li, Z. Zheng, Y. Zheng, C. Cui, C. Li and Z. Li, ACS Appl. Mater. Interfaces, 2017, 9, 2899–2905 Search PubMed.
- M. Li, J. Wang, Y. Zheng, Z. Zheng, C. Li and Z. Li, Inorg. Chem. Front., 2017, 4, 1757–1764 RSC.
- H. Zhang, W. Zhang, S. Gao, X. Lu, D. Zhang, X. Zhang and M. Wang, Appl. Phys. A, 2022, 128, 499 CrossRef CAS.
- H. Ren, R. Bai, F. Huang, J. Zhang and L. Wang, Cryst. Growth Des., 2022, 22, 4864–4873 CrossRef CAS.
- S. J. Shah, W. Li, Y. Tang, Y. Hu, S. Jiang, H. He, R. Wang, Z. Zhao and Z. Zhao, Appl. Catal., B, 2022, 315, 121555 CrossRef CAS.
- C. Zhang, C. Xie, Y. Gao, X. Tao, C. Ding, F. Fan and H.-L. Jiang, Angew. Chem., Int. Ed., 2022, 61, e202204108 CrossRef CAS PubMed.
- A. Ray, S. Sultana, L. Paramanik and K. M. Parida, J. Mater. Chem. A, 2020, 8, 19196–19245 RSC.
- L.-f. Hong, R.-t. Guo, Y. Yuan, X.-y. Ji, Z.-d. Lin, Z.-s. Li and W.-g. Pan, ChemSusChem, 2021, 14, 539–557 CrossRef CAS PubMed.
- Y. Yang, C. Zhou, W. Wang, W. Xiong, G. Zeng, D. Huang, C. Zhang, B. Song, W. Xue, X. Li, Z. Wang, D. He, H. Luo and Z. Ouyang, Chem. Eng. J., 2021, 405, 126547 CrossRef CAS.
- C. Li, D. Zhu, S. Cheng, Y. Zuo, Y. Wang, C. Ma and H. Dong, Chin. Chem. Lett., 2022, 33, 1141–1153 CrossRef CAS.
- K. Sun, M. Liu, J. Pei, D. Li, C. Ding, K. Wu and H.-L. Jiang, Angew. Chem., Int. Ed., 2020, 59, 22749–22755 CrossRef CAS PubMed.
- S. Kampouri, T. N. Nguyen, C. P. Ireland, B. Valizadeh, F. M. Ebrahim, G. Capano, D. Ongari, A. Mace, N. Guijarro, K. Sivula, A. Sienkiewicz, L. Forró, B. Smit and K. C. Stylianou, J. Mater. Chem. A, 2018, 6, 2476–2481 RSC.
- L. Wu, Y. Tong, L. Gu, Z. Xue and Y. Yuan, Sustainable Energy Fuels, 2018, 2, 2502–2506 Search PubMed.
- Y. Zhang and Z. Jin, Phys. Chem. Chem. Phys., 2019, 21, 8326–8341 RSC.
- S. Cao and J. Yu, J. Photochem. Photobiol., C, 2016, 27, 72–99 CrossRef CAS.
- Y. Xu, S. Li, M. Chen, J. Zhang and F. Rosei, Trends Chem., 2022, 4, 984–1004 CrossRef CAS.
- M. Samy, M. G. Ibrahim, M. Fujii, K. E. Diab, M. ElKady and M. Gar Alalm, Chem. Eng. J., 2021, 406, 127152 Search PubMed.
- L. Liu, H. Meng, Y. Chai, X. Chen, J. Xu, X. Liu, W. Liu, D. M. Guldi and Y. Zhu, Angew. Chem., Int. Ed., 2023, 62, e202217897 Search PubMed.
- X. Zhou, T. Wang, D. He, P. Chen, H. Liu, H. Lv, H. Wu, D. Su, H. Pang and C. Wang, Angew. Chem., Int. Ed., 2024, 63, e202408989 Search PubMed.
- J.-W. Wang, L.-Z. Qiao, H.-D. Nie, H.-H. Huang, Y. Li, S. Yao, M. Liu, Z.-M. Zhang, Z.-H. Kang and T.-B. Lu, Nat. Commun., 2021, 12, 813 CrossRef CAS PubMed.
- J. Hou, Z. Wang, P. Chen, V. Chen, A. K. Cheetham and L. Wang, Angew. Chem., Int. Ed., 2020, 59, 19434–19449 CrossRef CAS.
- Z.-C. Kong, J.-F. Liao, Y.-J. Dong, Y.-F. Xu, H.-Y. Chen, D.-B. Kuang and C.-Y. Su, ACS Energy Lett., 2018, 3, 2656–2662 CrossRef CAS.
- L.-Y. Wu, Y.-F. Mu, X.-X. Guo, W. Zhang, Z.-M. Zhang, M. Zhang and T.-B. Lu, Angew. Chem., Int. Ed., 2019, 58, 9491–9495 CrossRef CAS PubMed.
- W. Huang, B. Chan, Y. Yang, P. Chen, J. Wang, L. Casey, C. Atzori, T. Schulli, O. Mathon, H. G. Hackbarth, N. M. Bedford, D. Appadoo, X. Li, T. Lin, R. Lin, J. Lee, Z. Wang, V. Chen, A. K. Cheetham, L. Wang and J. Hou, J. Am. Chem. Soc., 2025, 147, 3195–3205 CrossRef CAS PubMed.
- A. VahidMohammadi, J. Rosen and Y. Gogotsi, Science, 2021, 372, eabf1581 CrossRef CAS.
- X. Li, Z. Huang, C. E. Shuck, G. Liang, Y. Gogotsi and C. Zhi, Nat. Rev. Chem., 2022, 6, 389–404 CrossRef PubMed.
- K. R. G. Lim, M. Shekhirev, B. C. Wyatt, B. Anasori, Y. Gogotsi and Z. W. Seh, Nat. Synth., 2022, 1, 601–614 CrossRef CAS.
- X. Zhuang, S. Zhang, Y. Tang, F. Yu, Z. Li and H. Pang, Coord. Chem. Rev., 2023, 490, 215208 CrossRef CAS.
- Y. Li, Y. Liu, Z. Wang, P. Wang, Z. Zheng, H. Cheng, Y. Dai and B. Huang, Chem. Eng. J., 2021, 411, 128446 CrossRef CAS.
- L. Shi, C. Wu, Y. Wang, Y. Dou, D. Yuan, H. Li, H. Huang, Y. Zhang, I. D. Gates, X. Sun and T. Ma, Adv. Funct. Mater., 2022, 32, 2202571 CrossRef CAS.
- Z. Ajmal, A. Hayat, A. Qadeer, Y. Zhao, E. H. Ibrahim, M. u. Haq, K. Iqbal, M. Imran, M. Kuku, I. Hussain, H. Ali, Y. Orooji, J. L. Zhou and T. Ben, Coord. Chem. Rev., 2025, 523, 216226 CrossRef CAS.
- J. Qin, B. Liu, K.-H. Lam, S. Song, X. Li and X. Hu, ACS Sustainable Chem. Eng., 2020, 8, 17791–17799 CrossRef CAS.
- R. Das, C. D. Vecitis, A. Schulze, B. Cao, A. F. Ismail, X. Lu, J. Chen and S. Ramakrishna, Chem. Soc. Rev., 2017, 46, 6946–7020 RSC.
- S. Bolisetty, M. Peydayesh and R. Mezzenga, Chem. Soc. Rev., 2019, 48, 463–487 RSC.
- K. N. Heck, S. Garcia-Segura, P. Westerhoff and M. S. Wong, Acc. Chem. Res., 2019, 52, 906–915 CrossRef CAS PubMed.
- V. I. Parvulescu, F. Epron, H. Garcia and P. Granger, Chem. Rev., 2022, 122, 2981–3121 CrossRef CAS PubMed.
- H. Anwer, A. Mahmood, J. Lee, K.-H. Kim, J.-W. Park and A. C. K. Yip, Nano Res., 2019, 12, 955–972 CrossRef CAS.
- L. N. Pincus, A. W. Lounsbury and J. B. Zimmerman, Acc. Chem. Res., 2019, 52, 1206–1214 CrossRef CAS PubMed.
- J. Chakraborty, I. Nath and F. Verpoort, Chem. Soc. Rev., 2022, 51, 1124–1138 RSC.
- B. Weng, M. Zhang, Y. Lin, J. Yang, J. Lv, N. Han, J. Xie, H. Jia, B.-L. Su, M. Roeffaers, J. Hofkens, Y. Zhu, S. Wang, W. Choi and Y.-M. Zheng, Nat. Rev. Clean Technol., 2025, 1, 201–215 CrossRef.
- S. Rojas and P. Horcajada, Chem. Rev., 2020, 120, 8378–8415 CrossRef CAS.
- X. Zhao, J. Li, X. Li, P. Huo and W. Shi, Chin. J. Catal., 2021, 42, 872–903 CrossRef CAS.
- F. Ahmadijokani, A. Ghaffarkhah, H. Molavi, S. Dutta, Y. Lu, S. Wuttke, M. Kamkar, O. J. Rojas and M. Arjmand, Adv. Funct. Mater., 2024, 34, 2305527 CrossRef CAS.
- L. Lu, L. Li, M. Chu, C. Chen, B. Wang, J. Wang, Y. Shen, R. Ma, B. Li, L. Shen, H. Lin and B. Chen, Adv. Funct. Mater., 2025, 35, 2419433 CrossRef CAS.
- X. Yu, Y. Hu, X. Luan, S. Jalil Shah, L. Liu, C. Li, Y. Ren, L. Zhou, J. Li, J. Deng, K. Chai, Z. Zhao and Z. Zhao, Chem. Eng. J., 2023, 476, 146878 CrossRef CAS.
- J. Li, Y. Jing, S. Zhang, C. Rao, D. Luo, F. Xi, J. Wu, A. He, W. Shen and L. Zhang, Chem. Eng. J., 2024, 499, 156508 CrossRef CAS.
- X.-Y. Li, H.-Y. Chu, P. Wang, X.-H. Yi, L. Zhang and C.-C. Wang, Sep. Purif. Technol., 2025, 372, 133525 CrossRef CAS.
- S. Zhou, Y. Kuang, H. Yang, L. Gan, X. Feng, C. Mao, L. Chen, J. Zheng and G. Ouyang, Angew. Chem., Int. Ed., 2024, 63, e202412279 CrossRef CAS.
- K. Zhao, Z. Zhang, Y. Feng, S. Lin, H. Li and X. Gao, Appl. Catal., B, 2020, 268, 118740 CrossRef CAS.
- K. Liu, L. Wang, S. Li, H. Liu, D. Zhang, M. Jiang, W. Chen, F. Jiao, X. Zhang and W. Hu, Adv. Funct. Mater., 2023, 33, 2306871 CrossRef CAS.
- X. Liu, C. Li, J. Nan, R. Liang, H. Wang, R. Xu and Y. Zhang, Environ. Sci.: Nano, 2024, 11, 1533–1542 RSC.
- Y. Bai, S. Zhang, S. Feng, M. Zhu and S. Ma, Dalton Trans., 2020, 49, 10745–10754 RSC.
- Z. Tian, Z. Hou, X. Yang, L. Liu and W. Zhang, Adv. Eng. Mater., 2023, 25, 2201710 CrossRef CAS.
- M. Govarthanan, R. Mythili, W. Kim, S. Alfarraj and S. A. Alharbi, J. Hazard. Mater., 2021, 414, 125522 CrossRef CAS.
- Q. V. Thi, M. S. Tamboli, Q. Thanh Hoai Ta, G. B. Kolekar and D. Sohn, Mater. Sci. Eng., B, 2020, 261, 114678 CrossRef.
- X.-H. Yi, H. Ji, C.-C. Wang, Y. Li, Y.-H. Li, C. Zhao, A. Wang, H. Fu, P. Wang, X. Zhao and W. Liu, Appl. Catal., B, 2021, 293, 120229 CrossRef CAS.
- Q. Wen, D. Li, H. Li, M. Long, C. Gao, L. Wu, F. Song and J. Zhou, Sep. Purif. Technol., 2023, 313, 123518 CrossRef CAS.
- Y. Zhao, Y. Zhang, X. Cao, J. Li and X. Hou, Chem. Eng. J., 2023, 465, 143000 CrossRef CAS.
- Q. Wu, Y. Liu, H. Jing, H. Yu, Y. Lu, M. Huo and H. Huo, Chem. Eng. J., 2020, 390, 124615 CrossRef CAS.
- H. Sepehrmansourie, H. Alamgholiloo, N. Noroozi Pesyan and M. A. Zolfigol, Appl. Catal., B, 2023, 321, 122082 CrossRef CAS.
- R.-X. Mei, P. Wang, F.-X. Wang, Z.-C. Zhang, X.-H. Yi, Z.-Y. Jia, K.-X. Li and C.-C. Wang, Environ. Res., 2025, 279, 121863 CrossRef CAS.
- J. Wang, C.-S. Cao, J. Wang, Y. Zhang and L. Zhu, Appl. Catal., B, 2022, 304, 121013 CrossRef CAS.
- L. Tao, C. Zhou, W. Pan, R. Liu, C. Liao and G. Jiang, Appl. Catal., B, 2024, 357, 124298 CrossRef CAS.
- M.-Y. Sun, L. Zhang, Y. Li, C.-C. Wang, P. Wang, X. Ren and X.-H. Yi, Chin. Chem. Lett., 2025, 36, 110035 CrossRef CAS.
- L. Yuan, C. Zhang, Y. Zou, T. Bao, J. Wang, C. Tang, A. Du, C. Yu and C. Liu, Adv. Funct. Mater., 2023, 33, 2214627 CrossRef CAS.
- J. Wang, Y. Mao, R. Zhang, Y. Zeng, C. Li, B. Zhang, J. Zhu, J. Ji, D. Liu, R. Gao and Y. Ma, Adv. Sci., 2022, 9, 2204036 CrossRef CAS.
- T. Hu, P. Feng, H. Chu, X. Wang, F. Liu and W. Zhou, Adv. Funct. Mater., 2025, 35, 2416556 Search PubMed.
- Y. Wu, X. Li, Q. Yang, D. Wang, F. Yao, J. Cao, Z. Chen, X. Huang, Y. Yang and X. Li, Chem. Eng. J., 2020, 390, 124519 CrossRef CAS.
- P. Jin, L. Wang, X. Ma, R. Lian, J. Huang, H. She, M. Zhang and Q. Wang, Appl. Catal., B, 2021, 284, 119762 Search PubMed.
- F. Mu, Q. Cai, H. Hu, J. Wang, Y. Wang, S. Zhou and Y. Kong, Chem. Eng. J., 2020, 384, 123352 CrossRef CAS.
- L. Shao, Z. Yu, X. Li, X. Li, H. Zeng and X. Feng, Appl. Surf. Sci., 2020, 505, 144616 Search PubMed.
- W. Lu, C. Wang, W. Song, Z. Zhang, C. Xie and J. Wang, J. Mater. Chem. A, 2024, 12, 20149–20159 RSC.
- S. Li, K. Dong, M. Cai, X. Li and X. Chen, eScience, 2024, 4, 100208 Search PubMed.
- J. Wang, X. Li, B. Zhang and L. Bai, Inorg. Chem., 2023, 62, 1047–1053 Search PubMed.
- R. Yuan, J. Qiu, C. Yue, C. Shen, D. Li, C. Zhu, F. Liu and A. Li, Chem. Eng. J., 2020, 401, 126020 CrossRef CAS.
- X. Liu, Z.-H. Peng, L. Lei, R.-X. Bi, C.-R. Zhang, Q.-X. Luo, R.-P. Liang and J.-D. Qiu, Appl. Catal., B, 2024, 342, 123460 CrossRef CAS.
- Z. Dong, D. Zeng, Z. Li, J. Chen, Y. Wang, X. Cao, G. Yang, Z. Zhang, Y. Liu and F. Yang, Chem. Sci., 2024, 15, 19126–19135 RSC.
- C. Gunathilake, I. Soliman, D. Panthi, P. Tandler, O. Fatani, N. A. Ghulamullah, D. Marasinghe, M. Farhath, T. Madhujith, K. Conrad, Y. Du and M. Jaroniec, Chem. Soc. Rev., 2024, 53, 10900–10969 RSC.
- X. Tao, Y. Zhao, S. Wang, C. Li and R. Li, Chem. Soc. Rev., 2022, 51, 3561–3608 RSC.
- S. Nishioka, F. E. Osterloh, X. Wang, T. E. Mallouk and K. Maeda, Nat. Rev. Methods Primers, 2023, 3, 42 CrossRef CAS.
- S. Navalón, A. Dhakshinamoorthy, M. Álvaro, B. Ferrer and H. García, Chem. Rev., 2023, 123, 445–490 CrossRef.
- Y. Zhang, D. Ma, J. Li, C. Zhi, Y. Zhang, L. Liang, S. Mao and J.-W. Shi, Coord. Chem. Rev., 2024, 517, 215995 CrossRef CAS.
- J. Duan, H. Shabbir, Z. Chen, W. Bi, Q. Liu, J. Sui, L. Đorđević, S. I. Stupp, K. W. Chapman, A. B. F. Martinson, A. Li, R. D. Schaller, S. Goswami, R. B. Getman and J. T. Hupp, J. Am. Chem. Soc., 2023, 145, 7268–7277 CrossRef CAS PubMed.
- L. Sun, Y. Yuan, F. Wang, Y. Zhao, W. Zhan and X. Han, Nano Energy, 2020, 74, 104909 CrossRef CAS.
- X. Chen, S. Xiao, H. Wang, W. Wang, Y. Cai, G. Li, M. Qiao, J. Zhu, H. Li, D. Zhang and Y. Lu, Angew. Chem., Int. Ed., 2020, 59, 17182–17186 CrossRef CAS.
- Z. Li, J. Zi, X. Luan, Y. Zhong, M. Qu, Y. Wang and Z. Lian, Adv. Funct. Mater., 2023, 33, 2303069 CrossRef CAS.
- H. Hu, K. Zhang, G. Yan, L. Shi, B. Jia, H. Huang, Y. Zhang, X. Sun and T. Ma, Chin. J. Catal., 2022, 43, 2332–2341 CrossRef CAS.
- J. Dai, L. Yan, W. Yang, R. Li, Y. Dong and Y. Shen, Appl. Catal., B, 2025, 362, 124715 CrossRef CAS.
- Q.-P. Huang, C. Yang, Q. Yin, A.-A. Zhang, H.-X. Liu, L. Li, M.-M. Liu, Z.-B. Fang and T.-F. Liu, Angew. Chem., Int. Ed., 2025, e202502009 CAS.
- S. Zhang, M. Du, Z. Xing, Z. Li, K. Pan and W. Zhou, Appl. Catal., B, 2020, 262, 118202 CrossRef CAS.
- J. Guo, Y. Liang, L. Liu, J. Hu, H. Wang, W. An and W. Cui, Appl. Surf. Sci., 2020, 522, 146356 CrossRef CAS.
- J. Liu, Q. Li, X. Xiao, F. Li, C. Zhao, Q. Sun, P. Qiao, J. Zhou, J. Wu, B. Li, H. Bao and B. Jiang, J. Colloid Interface Sci., 2021, 590, 1–11 CrossRef CAS.
- S. Guo, C.-W. Pan, M. Hou, Y.-T. Hou, S. Yao, T.-B. Lu and Z.-M. Zhang, Angew. Chem., Int. Ed., 2025, 64, e202420398 CrossRef CAS.
- H. Yang, C. Yang, N. Zhang, K. Mo, Q. Li, K. Lv, J. Fan and L. Wen, Appl. Catal., B, 2021, 285, 119801 CrossRef CAS.
- H. Li, H. Gong and Z. Jin, Appl. Catal., B, 2022, 307, 121166 CrossRef CAS.
- H. Ma, Y. Liu, R. Xiong and J. Wei, Chin. Chem. Lett., 2022, 33, 1042–1046 CrossRef CAS.
- Y. Jung, C. W. Lee, B.-H. Lee, Y. Yu, J. Moon, H. S. Lee, W. Ko, J. Bok, K. Lee, J. Lee, M. S. Bootharaju, J. Ryu, M. Kim and T. Hyeon, J. Am. Chem. Soc., 2025, 147, 1740–1748 CrossRef CAS PubMed.
- Y. Chen, D. Yang, B. Shi, W. Dai, H. Ren, K. An, Z. Zhou, Z. Zhao, W. Wang and Z. Jiang, J. Mater. Chem. A, 2020, 8, 7724–7732 RSC.
- W. Hou, M. Chen, C. Chen, Y. Wang and Y. Xu, J. Colloid Interface Sci., 2021, 604, 310–318 CrossRef CAS PubMed.
- L. Liu, L. Zuo, X. Zhai, X. Xiao, H. Fan, B. Li and L. Wang, Appl. Catal., B, 2025, 361, 124686 CrossRef CAS.
- A. Ghosh, S. Karmakar, F. A. Rahimi, R. S. Roy, S. Nath, U. K. Gautam and T. K. Maji, ACS Appl. Mater. Interfaces, 2022, 14, 25220–25231 CrossRef CAS PubMed.
- X. Dai, S. Feng, C. Ma, L. Xu, L. Fan, Z. Ye and Y. Wang, Appl. Surf. Sci., 2023, 639, 158142 CrossRef CAS.
- A. Khan, M. Le Pivert, A. Ranjbari, D. Dragoe, D. Bahena-Uribe, C. Colbeau-Justin, C. Herrero, D. Rutkowska-Zbik, J. Deschamps and H. Remita, Adv. Funct. Mater., 2025, 2501736 CrossRef.
- C.-X. Chen, Y.-Y. Xiong, X. Zhong, P. C. Lan, Z.-W. Wei, H. Pan, P.-Y. Su, Y. Song, Y.-F. Chen, A. Nafady, Sirajuddin and S. Ma, Angew. Chem., Int. Ed., 2022, 61, e202114071 CrossRef CAS PubMed.
- C. Li, H. Lu, G. Ding, T. Ma, S. Liu, L. Zhang and G. Liao, Chin. J. Catal., 2024, 65, 174–184 CrossRef CAS.
- H. Hu, X. Zhang, K. Zhang, Y. Ma, H. Wang, H. Li, H. Huang, X. Sun and T. Ma, Adv. Energy Mater., 2024, 14, 2303638 CrossRef CAS.
- Q. Mo, L. Zhang, S. Li, H. Song, Y. Fan and C.-Y. Su, J. Am. Chem. Soc., 2022, 144, 22747–22758 CrossRef CAS PubMed.
- G.-W. Guan, S.-T. Zheng, M. Xia, K.-X. Li, Y.-S. Ouyang, G. Yang and Q.-Y. Yang, Chem. Eng. J., 2023, 464, 142530 CrossRef CAS.
- M. Chen, K. Umer, B. Li, Z. Li, K. Li, W. Sun and Y. Ding, J. Colloid Interface Sci., 2024, 653, 380–389 CrossRef CAS PubMed.
- S. Mao, J.-W. Shi, G. Sun, D. Ma, C. He, Z. Pu, K. Song and Y. Cheng, Appl. Catal., B, 2021, 282, 119550 CrossRef CAS.
- S. Mao, J.-W. Shi, G. Sun, Y. Zhang, X. Ji, Y. Lv, B. Wang, Y. Xu and Y. Cheng, Chem. Eng. J., 2021, 404, 126533 CrossRef CAS.
- Y.-J. Cheng, J.-Q. Zhao, X.-F. Ma, H.-L. Zheng, L. He, J. Zhang and Q. Lin, Adv. Mater., 2025, 2503756 CrossRef CAS PubMed.
- H. Hu, Z. Wang, L. Cao, L. Zeng, C. Zhang, W. Lin and C. Wang, Nat. Chem., 2021, 13, 358–366 CrossRef CAS PubMed.
- Q.-C. Lin, W.-M. Liao, J. Li, B. Ye, D.-T. Chen, X.-X. Zhou, P.-H. Li, M. Li, M.-D. Li and J. He, Angew. Chem., Int. Ed., 2025, 64, e202423070 CrossRef CAS PubMed.
- L. Shiuan Ng, T. Raja Mogan, J.-K. Lee, H. Li, C.-L. Ken Lee and H. Kwee Lee, Angew. Chem., Int. Ed., 2023, 62, e202313695 CrossRef CAS PubMed.
- M. B. Ross, P. De Luna, Y. Li, C.-T. Dinh, D. Kim, P. Yang and E. H. Sargent, Nat. Catal., 2019, 2, 648–658 CrossRef CAS.
- Y. Zhai, P. Han, Q. Yun, Y. Ge, X. Zhang, Y. Chen and H. Zhang, eScience, 2022, 2, 467–485 Search PubMed.
- A. Velty and A. Corma, Chem. Soc. Rev., 2023, 52, 1773–1946 RSC.
- S. Fang, M. Rahaman, J. Bharti, E. Reisner, M. Robert, G. A. Ozin and Y. H. Hu, Nat. Rev. Methods Primers, 2023, 3, 61 CrossRef CAS.
- M. Li, Z. Han, Q. Hu, W. Fan, Q. Hu, D. He, Q. Chen, X. Jiao and Y. Xie, Chem. Soc. Rev., 2024, 53, 9964–9975 RSC.
- D. Li, M. Kassymova, X. Cai, S.-Q. Zang and H.-L. Jiang, Coord. Chem. Rev., 2020, 412, 213262 CrossRef CAS.
- P. M. Stanley, V. Ramm, R. A. Fischer and J. Warnan, Nat. Synth., 2024, 3, 307–318 CrossRef CAS.
- Z. Cai, H. Liu, J. Dai, B. Li, L. Yang, J. Wang and H. Zhu, Nat. Commun., 2025, 16, 2601 CrossRef CAS PubMed.
- H. Wu, X. Y. Kong, X. Wen, S.-P. Chai, E. C. Lovell, J. Tang and Y. H. Ng, Angew. Chem., Int. Ed., 2021, 60, 8455–8459 CrossRef CAS PubMed.
- M. Duflot, C. Marchal, V. Artero, K. C. Christoforidis and V. Keller, Adv. Energy Mater., 2025, 2500104 CrossRef CAS.
- M. Xu, C. Sun, X. Zhao, H. Jiang, H. Wang and P. Huo, Appl. Surf. Sci., 2022, 576, 151792 CrossRef CAS.
- W.-W. Dong, J. Jia, Y. Wang, J.-R. An, O.-Y. Yang, X.-J. Gao, Y.-L. Liu, J. Zhao and D.-S. Li, Chem. Eng. J., 2022, 438, 135622 CrossRef CAS.
- Q. Niu, S. Dong, J. Tian, G. Huang, J. Bi and L. Wu, ACS Appl. Mater. Interfaces, 2022, 14, 24299–24308 CrossRef CAS PubMed.
- M. Song, X. Song, X. Liu, W. Zhou and P. Huo, Chin. J. Catal., 2023, 51, 180–192 CrossRef CAS.
- S. Li, K. Ji, M. Zhang, C. He, J. Wang and Z. Li, Nanoscale, 2020, 12, 9533–9540 RSC.
- Y. Liu, C. Chen, J. Valdez, D. Motta Meira, W. He, Y. Wang, C. Harnagea, Q. Lu, T. Guner, H. Wang, C.-H. Liu, Q. Zhang, S. Huang, A. Yurtsever, M. Chaker and D. Ma, Nat. Commun., 2021, 12, 1231 CrossRef CAS PubMed.
- R. Jin, R. Li, M.-L. Ma, D.-Y. Chen, J.-Y. Zhang, Z.-H. Xie, L.-F. Ding, Y. Xie and J.-R. Li, Small, 2025, 2409759 CrossRef PubMed.
- N. Li, X.-P. Zhai, B. Ma, H.-J. Zhang, M.-J. Xiao, Q. Wang and H.-L. Zhang, J. Mater. Chem. A, 2023, 11, 4020–4029 RSC.
- L. Xia, W. Zhou, Y. Xu, Z. Xia, X. Wang, Q. Yang, G. Xie, S. Chen and S. Gao, Chem. Eng. J., 2023, 451, 138747 CrossRef CAS.
- K. Yuan, K. Tao, T. Song, Y. Zhang, T. Zhang, F. Wang, S. Duan, Z. Chen, L. Li, X. Zhang, D. Zhong, Z. Tang, T.-B. Lu and W. Hu, J. Am. Chem. Soc., 2024, 146, 6893–6904 CrossRef CAS PubMed.
- B. Li, X. Liu, B. Lei, H. Luo, X. Liu, H. Liu, Q. Gu, J.-G. Ma and P. Cheng, Adv. Sci., 2023, 10, 2302881 CrossRef CAS PubMed.
- Y. Wang, J.-X. Wei, H.-L. Tang, L.-H. Shao, L.-Z. Dong, X.-Y. Chu, Y.-X. Jiang, G.-L. Zhang, F.-M. Zhang and Y.-Q. Lan, Nat. Commun., 2024, 15, 8818 CrossRef CAS PubMed.
- S. Karmakar, S. Barman, F. A. Rahimi and T. K. Maji, Energy Environ. Sci., 2021, 14, 2429–2440 RSC.
- Z. Zhang, Y. Wang, Y. Xie, T. Tsukamoto, Q. Zhao, Q. Huang, X. Huang, B. Zhang, W. Song, C. Chen, H. Sheng and J. Zhao, Nat. Commun., 2025, 16, 274 CrossRef CAS PubMed.
- H. Dong, X. Zhang, Y. Lu, Y. Yang, Y.-P. Zhang, H.-L. Tang, F.-M. Zhang, Z.-D. Yang, X. Sun and Y. Feng, Appl. Catal., B, 2020, 276, 119173 CrossRef CAS.
- Y. Ma, Q. Tang, W.-Y. Sun, Z.-Y. Yao, W. Zhu, T. Li and J. Wang, Appl. Catal., B, 2020, 270, 118856 CrossRef CAS.
- Z. Zhao, J. Bian, L. Zhao, H. Wu, S. Xu, L. Sun, Z. Li, Z. Zhang and L. Jing, Chin. J. Catal., 2022, 43, 1331–1340 CrossRef CAS.
- Q. Chen, S. Li, H. Xu, G. Wang, Y. Qu, P. Zhu and D. Wang, Chin. J. Catal., 2020, 41, 514–523 CrossRef CAS.
- N. Li, X.-P. Zhai, W.-K. Yan, Y.-J. Zhang, Z.-T. Zhang, M.-J. Xiao, X.-D. Zhang, Q. Wang and H.-L. Zhang, Sol. RRL, 2021, 5, 2100558 CrossRef CAS.
- Z. Ding, X. Li, C. Kang, S. Yan, D. Zhao, H. Cai, S.-Y. Zhang and Y.-J. Zeng, Chem. Eng. J., 2023, 473, 145256 CrossRef.
- H. Yang, G. Liu, L. Zheng, M. Zhang, Z. Guan, T. Liu and J. Yang, Appl. Catal., B, 2024, 359, 124491 CrossRef.
- L. Wang, J. Mao, G. Huang, Y. Zhang, J. Huang, H. She, C. Liu, H. Liu and Q. Wang, Chem. Eng. J., 2022, 446, 137011 CrossRef.
- X.-M. Cheng, P. Wang, S.-Q. Wang, J. Zhao and W.-Y. Sun, ACS Appl. Mater. Interfaces, 2022, 14, 32350–32359 CrossRef PubMed.
- Y. Jiang, Y. Yu, X. Zhang, M. Weinert, X. Song, J. Ai, L. Han and H. Fei, Angew. Chem., Int. Ed., 2021, 60, 17388–17393 CrossRef CAS PubMed.
- R. R. Ikreedeegh and M. Tahir, J. Environ. Chem. Eng., 2021, 9, 105600 CrossRef CAS.
- Y. Yin, S. Feng, X. Xu, Y. Liu, Y. Li, L. Gao, X. Zhou, J. Dong, Y. Wu, J. Su, J.-L. Zuo, S. Yuan and J. Zhu, J. Am. Chem. Soc., 2025, 147, 16481–16493 CrossRef CAS PubMed.
- S. Xie, Y. Li, B. Sheng, W. Zhang, W. Wang, C. Chen, J. Li, H. Sheng and J. Zhao, Appl. Catal., B, 2022, 310, 121320 CrossRef CAS.
- E. Cepero-Rodríguez, A. Sousa-Castillo, L. V. Besteiro, B. Puértolas, M. Vázquez-González and M. A. Correa-Duarte, Adv. Energy Mater., 2024, 14, 2401887 CrossRef.
- P. Nagababu, Y. T. Prabhu, A. Kularkar, M. S. Subbalakshmi, J. Nagarkar and S. Rayalu, Emergent Mater., 2021, 4, 503–514 CrossRef CAS.
- M. A. Baluk, A. Pieczyńska, P. Mazierski, M. Kroczewska, K. Nikiforow, A. Mikolajczyk, J. Dołżonek, J. Łuczak and A. Zaleska-Medynska, Appl. Catal., B, 2024, 354, 124107 CrossRef CAS.
- S. Dai, T. Kajiwara, M. Ikeda, I. Romero-Muñiz, G. Patriarche, A. E. Platero-Prats, A. Vimont, M. Daturi, A. Tissot, Q. Xu and C. Serre, Angew. Chem., Int. Ed., 2022, 61, e202211848 CrossRef CAS PubMed.
- Z. Wei, S. Song, H. Gu, Y. Li, Q. Sun, N. Ding, H. Tang, L. Zheng, S. Liu, Z. Li, W. Chen, S. Li and S. Pang, Adv. Sci., 2023, 10, 2303206 CrossRef CAS PubMed.
- Y. Benseghir, A. Lemarchand, M. Duguet, P. Mialane, M. Gomez-Mingot, C. Roch-Marchal, T. Pino, M.-H. Ha-Thi, M. Haouas, M. Fontecave, A. Dolbecq, C. Sassoye and C. Mellot-Draznieks, J. Am. Chem. Soc., 2020, 142, 9428–9438 CrossRef CAS PubMed.
- Y.-J. Wang, X. Cheng, N.-N. Ma, W.-Y. Cheng, P. Zhang, F. Luo, W.-X. Shi, S. Yao, T.-B. Lu and Z.-M. Zhang, Angew. Chem., Int. Ed., 2025, 64, e202423204 CrossRef CAS PubMed.
- F. Dai, M. Zhang, J. Han, Z. Li, S. Feng, J. Xing and L. Wang, Nano Res., 2024, 17, 1259–1266 CrossRef CAS.
- R. Manna, S. Rahut and A. N. Samanta, Mater. Today Energy, 2023, 35, 101326 CrossRef CAS.
- G. Wang, C.-T. He, R. Huang, J. Mao, D. Wang and Y. Li, J. Am. Chem. Soc., 2020, 142, 19339–19345 CrossRef CAS.
- N. Li, X. Liu, J. Zhou, W. Chen and M. Liu, Chem. Eng. J., 2020, 399, 125782 CrossRef CAS.
- S. Karmakar, S. Barman, F. A. Rahimi, S. Biswas, S. Nath and T. K. Maji, Energy Environ. Sci., 2023, 16, 2187–2198 RSC.
- W. Guo, K. Zhang, Z. Liang, R. Zou and Q. Xu, Chem. Soc. Rev., 2019, 48, 5658–5716 RSC.
- L. Li, C. Tang, H. Jin, K. Davey and S.-Z. Qiao, Chem, 2021, 7, 3232–3255 CAS.
- L. Collado, A. H. Pizarro, M. Barawi, M. García-Tecedor, M. Liras and V. A. de la Peña O'Shea, Chem. Soc. Rev., 2024, 53, 11334–11389 RSC.
- X. Li, L. Tian, Q. Dong, Z. Wang, K. Ralphs, C. Esterhuysen, P. K. J. Robertson, D. W. Bahnemann, G. He and C. Wang, Coord. Chem. Rev., 2025, 534, 216543 CrossRef CAS.
- Z. Ding, S. Wang, S. Yan, Y.-J. Zeng and D.-H. Wang, ChemCatChem, 2023, 15, e202201605 CrossRef CAS.
- C. Wang, S. Wang, Y. Ping, Z. Zhao, D. Guo, D. Wang and X. Bu, Appl. Catal., B, 2024, 347, 123781 CrossRef CAS.
- S. Mansingh, S. Subudhi, S. Sultana, G. Swain and K. Parida, ACS Appl. Nano Mater., 2021, 4, 9635–9652 CrossRef CAS.
- X.-H. Li, H. Li, S.-L. Jiang, L. Yang, H.-Y. Li, Q.-L. Liu, W. Bai, Q. Zhang, C. Xiao and Y. Xie, ACS Catal., 2023, 13, 7189–7198 CrossRef CAS.
- J. Qiu, Q. Chen, C. Liu, Y. Chen, J. Wu, K. Jing, J. C. Yu, L. Wu and X. Fu, Appl. Catal., B, 2025, 366, 125034 CrossRef CAS.
- S. Liu, Z. Teng, H. Liu, T. Wang, G. Wang, Q. Xu, X. Zhang, M. Jiang, C. Wang, W. Huang and H. Pang, Angew. Chem., Int. Ed., 2022, 61, e202207026 CrossRef CAS PubMed.
- Q. Dong, X. Li, Y. Duan, X. He, X. Liang, F. Yu and C. Wang, Appl. Catal., B, 2025, 366, 125042 CrossRef CAS.
- H. Ren, J. Tan, Z. Zhao, Y. Shi, X. Xin, D. Yang and Z. Jiang, Catal. Sci. Technol., 2022, 12, 5540–5548 RSC.
- S. Wang, J.-J. Zhang, M.-Y. Zong, J. Xu, D.-H. Wang and X.-H. Bu, ACS Catal., 2022, 12, 7960–7974 CrossRef CAS.
- X. Li, L. Yang, Q. Liu, W. Bai, H. Li, M. Wang, Q. Qian, Q. Yang, C. Xiao and Y. Xie, Adv. Mater., 2023, 35, 2304532 CrossRef CAS PubMed.
- L. Yuan, C. Tang, P. Du, J. Li, C. Zhang, Y. Xi, Y. Bi, T. Bao, A. Du, C. Liu and C. Yu, Angew. Chem., Int. Ed., 2024, 63, e202412340 CrossRef CAS PubMed.
- Z. Han, Y. Yang, J. Rushlow, J. Huo, Z. Liu, Y.-C. Hsu, R. Yin, M. Wang, R. Liang, K.-Y. Wang and H.-C. Zhou, Chem. Soc. Rev., 2025, 54, 367–395 RSC.
- H. Zhang, C. Li, F. Lang, M. Li, H. Liu, D.-C. Zhong, J.-S. Qin, Z. Di, D.-H. Wang, L. Zeng, J. Pang and X.-H. Bu, Angew. Chem., Int. Ed., 2025, 64, e202418017 CrossRef PubMed.
- G. Hai and H. Wang, Coord. Chem. Rev., 2022, 469, 214670 CrossRef.
- S. Yang, B. Pattengale, S. Lee and J. Huang, ACS Energy Lett., 2018, 3, 532–539 CrossRef.
- L. Jiao, J. Wang and H.-L. Jiang, Acc. Mater. Res., 2021, 2, 327–339 CrossRef.
- C. Li, J. Wang, L. Tong, Y. Wang, P. Zhang, M. Zhu and H. Dong, Coord. Chem. Rev., 2024, 502, 215623 CrossRef.
- Y. Fan, H. Zheng, S. Labalme and W. Lin, J. Am. Chem. Soc., 2023, 145, 4158–4165 CrossRef PubMed.
- T. He, X.-J. Kong and J.-R. Li, Acc. Chem. Res., 2021, 54, 3083–3094 CrossRef PubMed.
- H. Liu, C. Xu, D. Li and H.-L. Jiang, Angew. Chem., Int. Ed., 2018, 57, 5379–5383 CrossRef PubMed.
- T. Uekert, C. M. Pichler, T. Schubert and E. Reisner, Nat. Sustain., 2021, 4, 383–391 CrossRef.
- A. M. Wright, M. T. Kapelewski, S. Marx, O. K. Farha and W. Morris, Nat. Mater., 2025, 24, 178–187 CrossRef PubMed.
- W. L. Teo, W. Zhou, C. Qian and Y. Zhao, Mater. Today, 2021, 47, 170–186 CrossRef.
- D. Chakraborty, A. Yurdusen, G. Mouchaham, F. Nouar and C. Serre, Adv. Funct. Mater., 2024, 34, 2309089 CrossRef.
- J. Van Herck, M. V. Gil, K. M. Jablonka, A. Abrudan, A. S. Anker, M. Asgari, B. Blaiszik, A. Buffo, L. Choudhury, C. Corminboeuf, H. Daglar, A. M. Elahi, I. T. Foster, S. Garcia, M. Garvin, G. Godin, L. L. Good, J. Gu, N. Xiao Hu, X. Jin, T. Junkers, S. Keskin, T. P. J. Knowles, R. Laplaza, M. Lessona, S. Majumdar, H. Mashhadimoslem, R. D. McIntosh, S. M. Moosavi, B. Mouriño, F. Nerli, C. Pevida, N. Poudineh, M. Rajabi-Kochi, K. L. Saar, F. Hooriabad Saboor, M. Sagharichiha, K. J. Schmidt, J. Shi, E. Simone, D. Svatunek, M. Taddei, I. Tetko, D. Tolnai, S. Vahdatifar, J. Whitmer, D. C. F. Wieland, R. Willumeit-Römer, A. Züttel and B. Smit, Chem. Sci., 2025, 16, 670–684 RSC.
- Z. Zheng, N. Rampal, T. J. Inizan, C. Borgs, J. T. Chayes and O. M. Yaghi, Nat. Rev. Mater., 2025, 10, 369–381 CrossRef.
- H. Mai, T. C. Le, D. Chen, D. A. Winkler and R. A. Caruso, Chem. Rev., 2022, 122, 13478–13515 CrossRef PubMed.
- A. Slattery, Z. Wen, P. Tenblad, J. Sanjosé-Orduna, D. Pintossi, T. den Hartog and T. Noël, Science, 2024, 383, eadj1817 CrossRef PubMed.
- Y. Hu, C. Yu, S. Wang, Q. Wang, M. Reinhard, G. Zhang, F. Zhan, H. Wang, D. Skoien, T. Kroll, P. Su, L. Li, A. Chen, G. Liu, H. Lv, D. Sokaras, C. Gao, J. Jiang, Y. Tao and Y. Xiong, Nat. Catal., 2025, 8, 126–136 CrossRef.
- J. Castells-Gil, N. Almora-Barrios, B. Lerma-Berlanga, N. M. Padial and C. Martí-Gastaldo, Chem. Sci., 2023, 14, 6826–6840 RSC.
- M. Bonneau, C. Lavenn, J.-J. Zheng, A. Legrand, T. Ogawa, K. Sugimoto, F.-X. Coudert, R. Reau, S. Sakaki, K.-i. Otake and S. Kitagawa, Nat. Chem., 2022, 14, 816–822 CrossRef CAS PubMed.
- K. Li, J. Yang and J. Gu, Acc. Chem. Res., 2022, 55, 2235–2247 CrossRef CAS.
|
This journal is © The Royal Society of Chemistry 2025 |
Click here to see how this site uses Cookies. View our privacy policy here.