DOI:
10.1039/D5TA03489B
(Review Article)
J. Mater. Chem. A, 2025,
13, 22271-22294
Progress in porous metal chalcogenides for electrocatalytic water splitting
Received
2nd May 2025
, Accepted 9th June 2025
First published on 11th June 2025
Abstract
Industry and everyday existence are undergoing an energy structure revolution, and hydrogen is a crucial clean alternative energy source. Both academics and businesses envision water electrolysis as a key procedure for green hydrogen generation in the future. In recent years, porous metal chalcogenides (PMChs), including metal sulfides, metal selenides, and metal tellurides, have gained significant interest as electrocatalysts for electrochemical water splitting due to their distinctive structure, characteristics, and potential applications. The PMChs exhibit extensive surface areas, varied compositions, and improved electronic conductivity, rendering them exceptionally suitable for electrochemical energy conversion devices with outstanding performance. This review showcases the production of diverse PMChs by several typical methods such as hydrothermal, spray pyrolysis, electrodeposition, liquid-phase deposition, template-based, and template-free synthesis. The article also comprehensively analyzes the most recent developments in the sulfides, selenides, and tellurides for electrocatalytic water splitting (EWS). The innovative design, production, and electrochemical performance of the porous sulfide, selenide, and telluride-based metal chalcogenides are demonstrated and evaluated. Finally, the existing challenges and potential opportunities of PMChs in EWS applications are presented. We anticipate that this timely assessment will encourage more comprehensive research and generate more significant interest, thereby enhancing the advancement of potential PMChs.
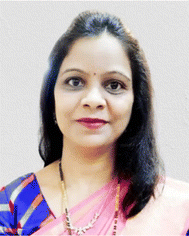 Pradnya M. Bodhankar | Dr Pradnya M. Bodhankar is an Assistant Professor at the Vishwaniketan's Institute of Management Entrepreneurship and Engineering Technology, India. Dr Bodhankar obtained her PhD from the University of Mumbai, India. The primary emphasis of her ongoing research is the development of metal/metal oxide-based electrocatalysts with precise control over their shape and size for electrochemical water-splitting and advanced energy storage battery materials. In addition, Dr Bodhankar has held the position of Women Scientist (WOS-A) at the Department of Physics at the University of Mumbai, funded by a grant from the Department of Science and Technology (DST) in India. Dr Bodhankar has authored over 10 peer-reviewed journal articles, including highly cited and most downloaded review articles, which have accumulated over 500 citations in a short period. |
 Pradip B. Sarawade | Dr Pradip B. Sarawade has been an Assistant Professor at the Dept. of Physics, University of Mumbai, since September 2014. Before moving to Mumbai University, he served at KAUST, a catalysis center in Saudi Arabia, from 2011 to 2014. Before joining the KAUST catalysis center, he worked as a Postdoctoral Research Fellow at the Department of Chemical Engineering, Hanyang University, South Korea, from 2010–2011 and as a research scientist at E&B Nanotech Co. Ltd South Korea from 2006–2010. He obtained his PhD in Materials Science from Hanyang University, South Korea, in 2009. His research interest encompasses the development of nanomaterials like silica aerogel with enhancing specific surface area, porosity, and mechanical strength for thermal protection applications. He has co-authored more than 105 peer-reviewed publications in high-quality journals with citations of more than 3500 with an h-index of 32 and 5 patents in nanomaterials, including a book on Silica Aerogels. He is a recognized teacher at the University of Mumbai, and he guides students seeking an MSc (by research) and PhD Degrees in Physics, Chemistry, Nanosciences, and Nanotechnology. |
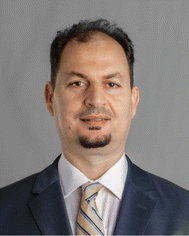 Abdulkarem I. Amhamed | Dr Abdulkarem Amhamed is the CO2 Cluster Program Director, Principal Scientist, and Chartered Chemical Engineer with 25 years of experience in the oil and gas industry, including Industry 4.0 and sustainable process design. He holds a Doctorate in Chemical Engineering from Bradford University, UK, and an MSc from the University of Salford, UK. Currently, Dr Amhamed leads the CO2 Cluster and Clean Fuel Program at Qatar Environment and Energy Research Institute, HBKU, Qatar Foundation. Under his leadership, the program secured $6.4 million in funding from the Qatar National Research Fund's National Priorities Research Program Cluster Track (NPRP-C) for five years. Dr Amhamed has held several senior research and management positions in both academia and industry, including serving as the Strategic Research Project Lead for a $15 million collaboration between Qatar Energy and UOP Honeywell, USA, and as the General Managing Director of ESSO Company, Libya. Dr Amahmed has authored over 70 peer-reviewed journal articles, accumulating over 1300 citations and achieving an h-index of 18 within a short period since joining the R&D division at HBKU. He also holds more than 19 patents as an inventor or co-inventor. |
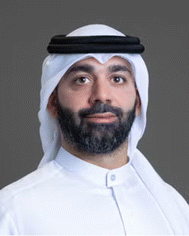 Tareq Al-Ansari | Dr Tareq Al-Ansari is an Associate Professor at the College of Science and Engineering, head of the sustainable development division, and acting executive director of the Qatar Environment and Energy Research Institute. He acquired a BEng. in Mechanical Engineering from the University College London and an MPhil in Engineering for Sustainable Development from the University of Cambridge. He completed his PhD in Sustainable Development and Environmental Engineering at Imperial College London. Dr Tareq Al-Ansari has authored over 150 peer-reviewed journal articles, garnering more than 12 000 citations, with an h-index of 57. His contributions also include technical reports, book chapters, and active involvement in sustainability-focused research initiatives. Dr Al-Ansari supervises PhD students through collaborative academic and industry programs and is committed to nurturing the next generation of researchers. |
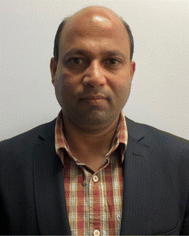 Nawshad Haque | Dr Nawshad Haque is a Principal Research Scientist in the Energy Business Unit at the Commonwealth Scientific and Industrial Research Organization (CSIRO) Australia and leads the Technoeconomics for Decarbonisation Team. Dr Haque also leads the India-Australia Minerals Scholar Network on Critical Minerals and Green Steel research to develop talents, which was announced as part of the joint Prime Minister's statements for both nations. Dr Haque is currently an elected Fellow of the Australian Institute of Energy, Australasian Institute of Mining and Metallurgy, and a member of TMS. Dr Haque has co-supervised over 20 CSIRO sponsored 20 PhD students and over 60 vacation scholarship projects to completion, many on technoeconomic and life cycle assessment. Dr Haque has published over 130 peer-reviewed journal articles, attracting more than 7500 citations with an h-index of 42 and an i10-index of 97, technical reports, and several book chapters. In addition, he mentors postdoctoral fellows and supervises PhD students through university and industry collaborations. Dr Haque has over 23 years of R&D experience since having a PhD in Chemical Engineering from the University of Sydney, Australia. |
 Dattatray S. Dhawale | Dr Dattatray S. Dhawale is a Senior Research Scientist in the Energy Business Unit at the Commonwealth Scientific and Industrial Research Organization (CSIRO), Australia's leading science agency. Dr Dhawale is a prolific, well-cited, and multiple-fellowship-winning scientist. Dr Dhawale's achievements have been honored by several prestigious fellowships, such as Brain Korea-21 (Hanyang University, South Korea), MANA NIMS Japan, Lindau Nobel Laureate Meeting, Germany, etc. Dr Dhawale led several multidisciplinary projects from idea conception to delivery. His research focuses on developing nanomaterials for next-generation electrochemical technologies for producing and utilizing clean and green fuels like hydrogen, ammonia, and CO2 reforming to decarbonize the various energy sectors. Dr Dhawale has published over 80 peer-reviewed journal articles, attracting more than 6600 citations with an h-index of 45 and an i10-index of 67, four patents, technical reports, and several book chapters. Dr Dhawale supervises PhD students through the CSIRO Industry PhD scholarship (iPhD) program and brings together an industry partner and a university for impact-driven research. In addition, he mentors postdoctoral fellows and CSIRO-sponsored vacation students. |
1. Introduction
In the past century, global energy consumption has consistently and significantly risen due to worldwide progress and the growth of the global population. It is estimated that energy demand will increase from 16 terawatts (TW) in 2010 to 23 TW in 2030, and it may even reach 30 TW by 2050.1 Coal, oil, and natural gas are examples of nonrenewable fossil fuels that account for more than 80% of the world's total energy consumption.2 The quick combustion of conventional fuels dramatically contributes to the generation of CO2, climate change, and environmental damage. Activistically implementing clean and renewable energy systems is imperative to achieve sustainable economic growth and maintain environmental equilibrium.3 Thus, expediting the development of renewable and environmentally friendly alternatives that may effectively address the existing issues and ensure sustainable long-term progress is essential. Given that water is the only by-product of combustion, molecular hydrogen gas (H2) is a fuel that is very desirable since it possesses an extraordinary energy density and does not contribute to pollution. This makes it an ideal energy transporter and a promising contender for future low-carbon energy systems.4 Electrochemical water splitting (EWS) is a promising technology for producing green hydrogen gas as an energy source, although there are already instances of sustainable energy sources being utilized.5 The electrocatalytic half-reactions, including the oxygen evolution reaction (OER) and hydrogen evolution reaction (HER), are crucial processes in electrochemical water splitting and have been extensively researched in recent decades. The most advanced electrocatalysts for these electrochemical processes consist of noble metal and transition metal-based compounds such as Pt, IrO2, RuO2, and so on.6–11 Nevertheless, the overpriced expense of the valuable electrocatalysts significantly limits their practical use. Hence, the quest for cost-effective, enduring, and affordable electrocatalysts continues to be a significant hurdle.12,13
Over the last several decades, there has been a growing interest in exploring transition metal chalcogenides (TMChs), more notably sulfides and selenides, as possible electrode materials for energy storage and conversion applications.14 This is because they can have stoichiometric compositions that can be adjusted, unique crystal structures, a large number of redox sites, and a comparatively better electrical conductivity compared to other catalysts and transition metal oxides.15–17 Also, metal chalcogenides have more electrochemical reversibility than metal oxides because they have faster charge transfer kinetics. Moreover, certain metal chalcogenides such as MoS2, CoS2, CoSe2, FeSe2, etc., have shown potential as electrocatalysts for HER and OER as they exhibit low overpotentials and small Tafel slopes.18–20 Recently, porous metal chalcogenides (PMChs) have demonstrated effective electrocatalysis for both HER and OER, exhibiting enhanced activity due to their substantial internal reactive surface areas and efficient mass and electron transport through extensive pathways.21–23
PMChs are inorganic compounds that resemble oxide-based porous materials. The chalcogen elements—sulfur (S), selenium (Se), and tellurium (Te)—are categorized in group 16 of the periodic table, alongside oxygen (O). By altering the composition, pore dimensions, and morphology, one may proficiently adjust the properties of PMChs, encompassing conductivity and selectivity.24 Various synthetic methodologies, such as template-assisted synthesis, self-assembly, and hydrothermal reactions, have been utilized to generate a unique porous architecture with a substantial surface area within the metal chalcogenide framework.25,26 Furthermore, porous metal chalcogenides possess a wide range of optoelectronic properties, which vary from being insulators to genuine metals.27,28 These properties include adjustable and significant bandgaps, high electron mobility, and a highly polarizable surface that exhibits Lewis's basicity.28,29 It is important to note that these qualities distinguish them from their metal-oxide counterparts. Furthermore, thorough examinations of the composition, structure, morphology, and dimensionality of porous metal chalcogenides have revealed their inherent and versatile high chemical reactivity, rendering them highly appealing for various applications, including adsorption, electrocatalysis, energy storage, and solar-to-chemical energy conversion.30–33
This review provides progress on porous metal chalcogenides (MSx/MSey/MTez, where M represents Fe, Co, Ni, Sn, Mo, W, Sb, Mn, Zn, Cu, Ti, Ta, V, Bi, Nb, or their combinations) that are actively being explored for electrochemical water splitting reactions, namely for the HER and the OER. We begin by describing the importance of porosity and focusing on the electrocatalyst fabrication techniques and reaction mechanisms of the HER and the OER. The synthetic methods of PMChs are summarized, and their electrochemical performances are highlighted. In conclusion, the difficulties and perspectives that have been encountered in the development of PMChs for EWS are brought to light.
2. Importance of porosity
Porous materials are an essential group of substances with empty spaces, known as pores, inside their structure. The pores exhibit a diverse variety of sizes, including micropores (<2 nm), mesopores (2–50 nm), and macropores (>50 nm).34 Nanoporous materials refer to materials that have pore widths less than 100 nm.35 Nanoporous metals have numerous unique characteristics that render them highly desirable as electrocatalysts.36 The metallic structure is interconnected, forming an intensely conductive network that enables the efficient movement of electrons. Furthermore, the intricate internal curvature of the structure might expose a multitude of distinct crystal facets on the surfaces of the ligaments. This can result in advantageous reaction sites influenced by the particular reaction conditions and surface composition.37 Moreover, the manufacturing approach can be applied to monometallic and bimetallic catalysts featuring highly porous structures and large surface areas.36,38,39 This allows for versatility in creating and manipulating specific catalytic sites.36 Additionally, manifolds and limited spaces inside the nanoporous structure provide a compelling approach to regulating the movement of reactants and/or products. This results in an increased preference for desirable products and reduced undesired ones. From a fundamental standpoint, the monolithic structure of nanoporous metals presents a distinct chance to separate support effects and investigate the genuine source of catalytic activity.40,41
Porous materials have garnered considerable attention in a range of chemical engineering processes because they have the potential to act as catalysts42,43 Porous materials have also been widely used in electrocatalysis, a heterogeneous process that occurs at the interface.44,45 This is because porous materials possess unique physical and chemical features that are distinct from those of ordinary materials.42,46 As shown in Fig. 1, porous materials are adaptable in the field of electrocatalysis thanks to their ability to provide a high number of surface sites and facilitate mass diffusion during the process.
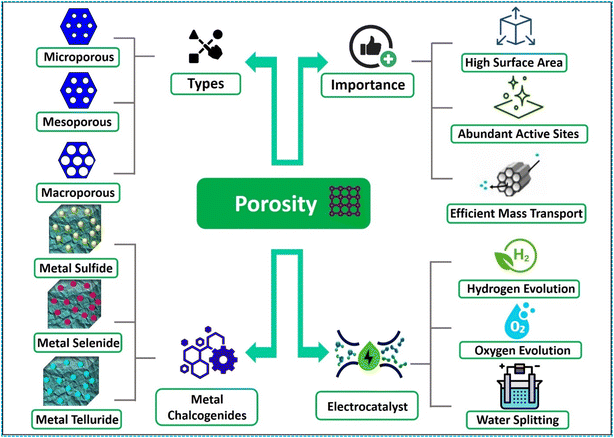 |
| Fig. 1 Concept map of importance of porosity in electrochemical water splitting reactions. | |
Porous counterparts can reduce the resistance to mass transfer and raise the specific current densities in HER and OER compared to bulk materials.47,48 Over the past few years, researchers have made great strides in developing procedures for preparing a wide variety of porous structures.49,50
2.1 BET surface area analysis
The Brunauer–Emmett–Teller (BET) method, developed in 1938, measures surface areas of porous structures by analyzing gas molecule adsorption.51,52 It's an extension of the Langmuir theory for multi-layer adsorption.53 BET's simplicity and conclusiveness make it a standard tool for calculating surface areas of new porous materials, like metal chalcogenides. BET study involves injecting inert gas at boiling temperature onto porous solids, obtaining micropore volume and pore size distribution (PSD) using t-plot and Barrett–Joyner–Halenda (BJH) techniques.54 Adsorption isotherms are classified into six types by IUPAC, providing insights into texture and pore structure explained in detail in Fig. 2 and 3.34 By measuring N2 multilayer adsorption, BET evaluates specific surface areas, making it a valuable tool for material characterization.
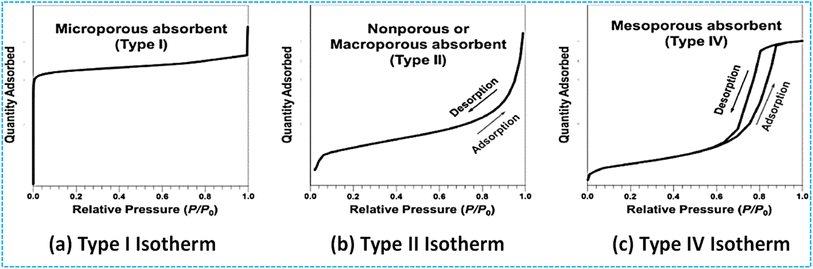 |
| Fig. 2 The typical isotherm shapes include (a) microporous, characterized by a type I isotherm profile, (b) non-porous and macroporous, represented by a type II isotherm profile, and (c) mesoporous, which follows a type IV isotherm profile. Reproduced from ref. 34 with permission from IUPAC, copyright 1985. | |
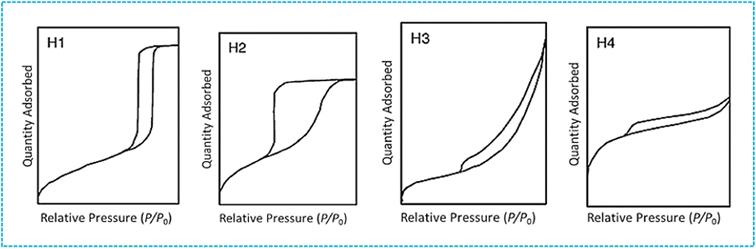 |
| Fig. 3 The four distinct hysteresis shapes of adsorption isotherm are typically observed in subcritical N2 adsorption studies. Reproduced from ref. 34 with permission from IUPAC, copyright 1985. | |
2.2 Mesoporous materials as electrocatalysts
Mesoporous materials are identified by pore diameters ranging from 2 to 50 nm.55 Mesoporous materials possess extensive accessible surface areas and adjustable pore diameters, significantly enhancing mass transport and the dispersion of electrons and reactants. Consequently, mesoporous materials exhibit exceptional promise in electrocatalysis, photocatalysis, and energy storage and conversion.56 The International Union of IUPAC defines a mesoporous material as having either an ordered or disordered mesostructure. In crystalline inorganic materials, the structure of mesoporous substances considerably restricts the number of lattice units, hence drastically altering the solid-state chemistry. The battery performance of mesoporous electroactive materials markedly differs from that of their bulk counterparts.57
Adsorption-based techniques, particularly the BET method, are employed to determine porosity and surface area because of their capacity to quantify porosity within the range of 0.4–50 nm and their measuring simplicity and cost-effectiveness. The type of isotherm (Fig. 3) can also reveal the sort, scale, and form of the pores in the material.58
Several porous catalysts play significant roles in the process of water splitting.59–61 Recently, metal porous chalcogenides have emerged as a viable option to replace precious metal catalysts due to their affordability, ease of production, and inherent electronic structure for the process of water splitting.62–64 The notable features of metal chalcogenides, derived from their diverse composition and electronic structure, include customizable active sites, rendering them excellent candidates for the development of exceptionally effective electrocatalysts.65,66 Various metal chalcogenides materials have been shown to create functional hybrid nanoarchitectures using different optimization strategies, including controlling the morphology (1D, 2D, 3D, and other forms), regulating the structure (porous structure, phase regulation, amorphous structure), optimizing the electronic structure (defects, vacancies, nanointerfaces, stress regulation), and forming heterostructures with other nanomaterials (oxides, hydroxides, carbon materials, noble metals), among others.67–69 For instance, 3D materials with mesoporous and hollow structures enhance the expression of active sites, facilitate adsorption for intermediates, and enable the release and storage of gases, rendering them promising materials across numerous fields.70,71 The application of 3D nanostructures in electrocatalysis significantly enhances reaction efficiency due to higher contact surface area, diminished electron transfer resistance, augmented active sites, and improved connectivity between the electrolyte and catalysts. Simultaneously, the mesoporous and hollow architectures can facilitate the release of evolved gases and enhance catalytic efficacy.17,21,72
It is important to note that even though metal chalcogenides have an excellent electrocatalytic performance for water splitting, it is essential to meticulously examine the alterations in morphology, structure, valence state, elemental composition, and electronic characteristics such as conductivity, bandgap, and density of states following the electrocatalytic reaction. This is because the surface of the electrocatalysts will inevitably undergo oxidation during the OER, and reduction reactions will also occur under the conditions of the HER. Hence, it is imperative to conduct a comprehensive investigation in order to verify the alterations in the electrocatalytic performance of porous metal chalcogenides that have undergone surface modification.
3. Fundamentals of electrocatalytic water splitting
Electrolysis of water uses electrical energy to separate water molecules into hydrogen and oxygen. Electrolytic water is composed of the HER and the OER. Depending on the electrolyte that is utilized, the reaction mechanism of the HER and OER can be slightly different.
3.1 Hydrogen evolution reaction (HER)
The electrochemical HER is a cathodic half-reaction that can occur through either the Volmer–Heyrovsky pathway or the Volmer–Tafel pathway in both acidic and alkaline conditions, as seen in Fig. 4.73 The Volmer reaction is the initial and often occurring phase, in which an electron combines with a proton that has gathered on the catalyst's surface, resulting in the formation of an adsorbed hydrogen (MH) atom intermediate. In addition, the Volmer reaction is accompanied by either the amalgamation of an adsorbed MH atom with an electron and a proton (known as the Volmer–Heyrovsky pathway) or combining two MH atoms (known as the Volmer–Tafel pathway). M represents the active sites of the catalyst. The production of the MH intermediate is implicated in both the Volmer–Heyrovsky and Volmer–Tafel pathways. The hydrogen adsorption capacity is the primary aspect considered while constructing electrocatalysts.
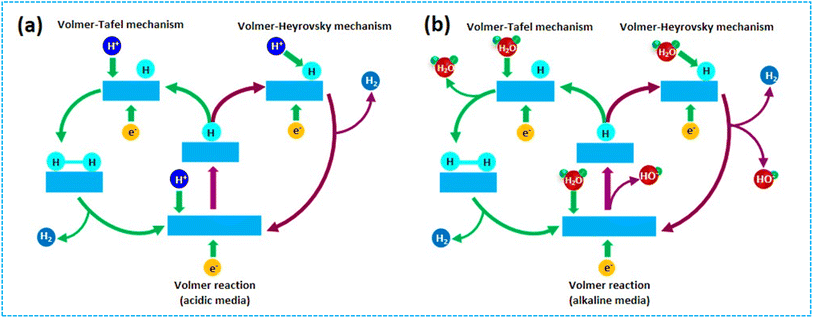 |
| Fig. 4 Schematic representation of HER mechanism in (a) acidic and (b) alkaline media. | |
Acidic conditions:
| Volmer reaction: H+ + e− → MH | (1) |
| Tafel reaction: MH + MH → H2(g) | (2) |
| Heyrovsky reaction: MH + H+ + e− → H2(g) | (3) |
Alkaline conditions:
| Volmer reaction: H2O(l) + e− → OH− + MH | (4) |
| Tafel reaction: MH + MH → H2(g) | (5) |
| Heyrovsky reaction: MH + H2O(l) + e− → OH− + H2(g) | (6) |
Individual steps can serve as rate-determining reactions that dictate the HER rate within various reaction processes. Enhancing the speed of these reactions is crucial for optimizing the overall water-splitting.
3.2 Oxygen evolution reaction (OER)
OER, is a chemical process that involves the transfer of four electrons. The standard potential of OER is 1.23 V vs. RHE. Kinetically, the simultaneous transmission of several electrons is not beneficial.
Acidic conditions:
| M + H2O(l) → MOH + H+ + e− | (7) |
| MO + H2O2(l) → MOOH + H+ + e− | (10) |
| MOOH → M + O2(g) + H+ + e− | (11) |
Alkaline conditions:
| MOH + OH− → MO + H2O(l) + e− | (13) |
| MOOH + OH− → M + O2(g) + H2O(l) + e− | (16) |
Within the OER process, every individual step must surpass a substantial variation in potential, leading to the slow kinetics of OER. The reaction mechanism is illustrated in Fig. 5. To achieve efficient water electrolysis, it is imperative to tune the anode catalyst and minimize the overpotential of the OER.
 |
| Fig. 5 Schematic representation of OER mechanism in (a) acidic and (b) alkaline media. | |
The OER refers to the half-reaction involved in the process of water splitting. The processes occurring at the cathode and anode during the water-splitting reaction exhibit distinct characteristics in both acidic and alkaline environments. Several research groups have suggested various processes for the OER at the anode electrode, either in acidic conditions (eqn (7)–(11)) or alkaline settings (eqn (12)–(16)). There are both differences and commonalities among these proposed mechanisms. The majority of the hypothesized pathways share common intermediates, such as MOH and MO. However, the main distinction is in the reaction that produces oxygen. There are two distinct methods for producing oxygen from a MO intermediate, as shown in Fig. 5. The initial pathway necessitates the direct amalgamation of 2MO to yield O2(g). The alternative path entails the synthesis of the MOOH intermediate, which subsequently undergoes decomposition to produce O2(g). This second route is represented by the black line in Fig. 5. While distinctions exist, there is widespread agreement that the electrocatalysis of OER constitutes a heterogeneous process, wherein the bonding interactions (M–O) among the intermediates (MOH, MO, and MOOH) are crucial to the overall electrocatalytic efficacy. An electrocatalyst is a catalyst that aids in electrochemical reactions. The material may be modified either at the electrode's surface or function as the electrode itself. In general, the primary role of the electrocatalyst is to attract the reactant onto its surface, resulting in the formation of an adsorbed intermediate. This process aids in transferring charge between the electrode and the reactant.
3.3 Criteria for electrochemical water splitting performance evaluation
Electrocatalytic activity can be assessed using several fundamental characteristics, including overpotential (η), Tafel slope, exchange current density, electrochemical impedance spectroscopy, electroactive surface area, turnover frequency (TOF), and stability. The catalyst was evaluated using linear scan voltammetry (LSV). Typically, the overpotential value at 10 mA cm−2 is lower, indicating a lower voltage for hydrogen production by water decomposition.
3.3.1 Overpotential (η).
Overpotential (η) is a crucial factor for assessing the performance of electrocatalysts in water splitting. It is among the most significant criteria to consider in evaluating their performance. Overpotential, in theory, is the discrepancy between the real potential and the thermodynamic value at a certain current density (eqn (17)).74 The theoretical potentials for HER and OER are 0 volts and 1.23 volts, respectively, as stated previously. However, in practice, the slow reaction rates of the HER and OER necessitate the use of a larger applied potential to overcome the inherent energy barrier throughout the catalytic process. | η = Eapplied − E0 − iR | (17) |
where, Eapplied represents the actual applied potential, E0 is the theoretical equilibrium value, and iR denotes the ohmic correction under similar conditions.
The electrocatalytic activity of a catalyst is typically evaluated using three overpotential values obtained from the polarisation curve at current densities of 1 mA cm−2 (η1), 10 mA cm−2 (η10), and 100 mA cm−2 (η100). The initiation of the reaction is often indicated as η1. The standard for comparing the performance of electrocatalysts is always represented by the value of η10. This is to get a photoelectrochemical water splitting efficiency of 12.3%.75 However, it is important to mention that the overpotential is highly influenced by the amount of active material loaded on the electrode. Therefore, to make a fair comparison of the activity of different electrocatalysts, it is advised that the amount of loading mass be normalized based on the surface area of the electrode.76 In addition, a value of 100 for η is a crucial factor to consider when evaluating practical applications.
3.3.2 Tafel slope (b).
The Tafel slope (b) is a crucial metric indicating the water-splitting activity level. The Tafel slope measures the rate at which the current density increases as the overpotential increases. It is used to analyze the kinetics of an electrocatalyst. In general, there is a logarithmic relationship between overpotential and current density. According to the Tafel equation (eqn (18)), the Tafel slope can be linearly fitted on the Tafel plot with the expression: | η = a + b log j | (18) |
where η represents the overpotential, b represents the Tafel slope, and j represents the current density.77 The Tafel diagram provides us with another significant quantity known as the exchange current density (jo). When the value of η is zero, the corresponding current density (j) is referred to as the exchange current density (jo). Generally, a high turnover frequency (jo) and a lower Tafel slope indicate better catalytic activity.
3.3.3 Turnover frequency (TOF).
The term “TOF” refers to the number of molecules that transform to produce the desired product at each active site during a specific period. It exposes the inherent activity of electrocatalysts. The TOF values can be determined using eqn (19).78 |  | (19) |
where j represents the current density in the polarisation curve, A is the surface area of the working electrode, α is the number of electrons generated per molar of the target product in the HER or OER reaction, F is the Faraday constant, and n is the number of moles of the active materials. Calculating the TOF value accurately is particularly challenging due to the unequal catalytic activity of atoms inside a catalyst. Nevertheless, TOF remains a valuable metric for comparing similar catalysts.
3.3.4 Stability.
Stability is an essential consideration in assessing the longevity of a catalyst for real-world use. Typically, two approaches are employed to determine the stability of electrocatalysts.79 Firstly, a cyclic voltammetry measurement is conducted by comparing the polarisation curve of the catalyst before and after 1000 cycles of cyclic voltammetry. In general, if the overpotential closely aligns with the initial polarisation curve, it indicates a high level of stability. Another approach involves the utilization of chronoamperometry or chronopotentiometry for measurement purposes. The rate of change in electrical potential over a certain period can be quantified at a designated level of electric current, where a high degree of preservation indicates exceptional stability.
4. Synthesis of porous metal chalcogenides
Porous metal chalcogenides (PMChs) are a series of high-performance water-splitting catalysts that are based on earth-abundant metals.80,81 Recently, it has been discovered that these catalysts are readily available and highly active.14,24,82 The notable attributes of metal chalcogenides, such as their regulated shape and many active sites, contribute to their high reactivity, making them an excellent choice for constructing hybrid nanomaterials. Typically, metal chalcogenides can be synthesized via solid-phase chemical synthesis, wet-chemical synthesis, or a chemical vapor deposition (CVD) – based epitaxial growth technique. In developing multifunctional metal chalcogenides and hybrid nanostructures derived from these compounds, numerous strategies can be employed to modify their physical and chemical properties, providing a wide range of applications.
4.1 Porous metal sulfides
Transition metal sulfide materials are becoming increasingly popular in electrochemical energy storage and conversion due to their favorable electrical characteristics and affordable cost.83,84 Mesoporous metal sulfides are the most intriguing of all metal sulfides. Mesoporous materials offer several benefits, including extremely high surface areas, adjustable mesopores, and large pore volumes. These characteristics enhance the active surface, facilitate the movement of guest species through the material, and alleviate structural strain caused by volume expansion resulting from redox reactions.85 Significant actions have been undertaken to synthesize mesoporous metal sulfides.86–89 The early efforts have been made using soft templating methods, sol–gel, and aerogel.90–92 The most generally used method for producing well-structured mesoporous metal sulfides is nanocasting, which employs mesoporous silica as a rigid template.88,93 Using thermally stable hard templates enables the successful production of highly crystalline mesoporous metal sulfides.
A rapid one-step flame combustion deposition approach was devised by Wang et al.94 The method involved fabricating mesoporous metal sulfides directly on nickel foam without the use of a binder or template (Fig. 6a). The first-row transition metal sulfides, which include Co9S8, Ni3S4, NiCo2S4, and FeS, were successfully synthesized using a three-dimensional architecture, a large specific surface area (about 110 m2 g−1), and interconnected pore networks. This study presented a novel and scalable approach to acquire mesoporous metal sulfides that exhibit exceptional electrochemical performance.94 The synthesis of mesoporous transition metal dichalcogenides greatly relies on this practical approach, which is of fundamental significance. Zhang et al.95 have synthesized a distinctive three-dimensional catalyst consisting of interconnected porous networks of NiCo disulfide that were grown on carbon cloth (CC).95 This was achieved by a simple hydrothermal technique followed by a low-temperature sulfuration process. The process of creating a network of linked pores in (Ni0.33Co0.67)S2 nanowires (NWs) on a carbon cloth substrate is depicted in Fig. 6b. The nitrogen adsorption–desorption isotherm plot of (Ni0.33Co0.67)S2 NWs exhibits a type IV isotherm, indicative of mesopore existence. Comparing the BJH pore size distribution curves reveals that the average pore size of NiCo precursor NNs is 1.2 nm, but that of (Ni0.33Co0.67)S2 NWs is 9.1 nm, further confirming their mesoporous nature. The specific surface area of the (Ni0.33Co0.67)S2 nanowires, as measured by the BET method, was 24.61 m2 g−1. This value was considerably higher than the specific surface area of the NiCo precursor nanoneedles, which was 5.57 m2 g−1. The presence of a mesoporous structure and a larger surface area resulted in the exposure of a significant number of active sites. This leads to an increase in the contact area between the electrode and electrolyte, hence enhancing the rate of electron diffusion.95 Ma et al.96 have successfully created three CoSx compounds, specifically Co9S8, Co3S4, and CoS2 hollow nanospheres (HNSs), by accurately changing the molar ratio of carbon disulfide to cobalt acetate in a facile solution-based approach.96Fig. 6c displayed a schematic representation of the preparation process. The Co9S8, Co3S4, and CoS2 hollow nanospheres were synthesized using a simple wet-chemical process. The CS2 served as both a sulfur supply and an oil-droplet template in the reaction. Usually, three ethylenediamine (EN) molecules react with a cobalt ion (Co2+) to produce a complex solution called [Co(EN)3]2+. Subsequently, when this solution is mixed with an aqueous solution and carbon disulfide (CS2), it forms an oil/water system. Subsequently, EN interacts with the CS2 oil phase, resulting in the liberation of H2S at the interface between oil and water. Subsequently, hydrogen sulfide (H2S) can undergo a reaction with [Co(EN)3]2+ to generate nuclei of cobalt sulfide. The excess CS2 evaporated, and the hollow nanospheres, constructed from nanosheets, were ultimately obtained. The CoS2 HNSs exhibit a markedly greater BET surface area (71.2 m2 g−1) compared to the other two comparatives, hence offering an increased number of electroactive sites and enhancing electrolyte penetration in the catalytic process.96
 |
| Fig. 6 (a) Schematic representation of the reactive spray deposition process for mesoporous metal sulfides. Reproduced from ref. 94 with permission from American Chemical Society, copyright 2019. (b) Schematic representation of the fabrication process for (Ni0.33Co0.67)S2 NWs/CC. Reproduced from ref. 95 with permission from American Chemical Society, copyright 2018. (c) Schematic representation of the synthetic methodologies of Co9S8, Co3S4, and CoS2 HNSs, respectively. Reproduced from ref. 96 with permission from Royal Society of Chemistry, copyright 2018. (d) Schematic illustration of the synthesis procedures for porous (Ni0.75Fe0.25)Se2 nanosheets on CFC. Reproduced from ref. 97 with permission from American Chemical Society, copyright 2016. (e) Schematic illustration of the synthesis of p-CoSe2 on carbon cloth. Reproduced from ref. 98 with permission from American Chemical Society, copyright 2018. (f) Schematic illustration for the synthesis of o-CoTe2|P@HPC/CNTs composite. Reproduced from ref. 99 with permission from American Chemical Society, copyright 2020. | |
4.2 Porous metal selenides
Among the group of transition metal chalcogenides, metal selenides (Se) have recently been identified as a distinct family of compounds for water electrolysis. They possess particular characteristics that set them apart from their sulfide counterparts, commonly called “star chalcogenides”. The 3d orbital of Se can bond with metal atoms since its energy level is close to the 3s and 3p orbitals. The electron structure of transition metal selenides promotes increased metallicity, which enhances electron transport and facilitates chemical reactions. In addition, porous metal selenides provide several benefits, including easy preparation, exceptional catalytic activity, and outstanding stability. These qualities make them very suitable for the electrochemical breakdown of water, making them perfect candidates for this process. Wang et al.97 presented a study where they described a simple technique for creating porous (Ni0.75Fe0.25)Se2 nanosheets on flexible and conductive CFC support material (Fig. 6d).97 Initially, the ultrathin NiFe-based nanosheet precursor was created using a standard solvothermal method. Subsequently, the porous (Ni0.75Fe0.25)Se2 nanosheets with a high surface area of 60.3 m2 g−1 were obtained by directly subjecting the precursor to a secondary hydrothermal procedure, including selenisation. The fabricated porous (Ni0.75Fe0.25)Se2 nanosheets showed superior electrochemical performance (overpotential of 255 mV at 35 mA cm2 and a low Tafel slope of 47.2 mV dec−1) compared to the nanosheet precursors based on Ni, NiFe, and porous NiSe2. The excellent performance of the (Ni0.75Fe0.25)Se2 nanosheets can be due to their porous nanostructure, high electronic conductivity, and extensive electro-active surface area resulting from the integration of Fe and the process of selenisation.97 Although recent improvements have been made in creating transition metal selenide nanostructures, making a porous nanosheet electrode without a binder with more active sites is still challenging. Wan et al.98 described the vapor selenisation of a pre-synthesized α-Co(OH)2 nanosheet array precursor, resulting in the self-templating production of a porous CoSe2 nanosheet array on carbon cloth (p-CoSe2/CC).98 As depicted in Fig. 6e, the synthetic procedures can be separated into two distinct stages: (i) the α-Co(OH)2 nanosheets are grown on CC by electrodeposition at 25 °C. (ii) The α-Co(OH)2/CC is converted to p-CoSe2/CC by reacting with selenium vapor at a temperature of 450 °C. The material demonstrated a significant active surface area, rapid diffusion of produced gas, and robust structural stability during electrochemical water-splitting reactions (Table 1).98
Table 1 Synthesis methods, porosity, BET surface area and pore size of porous metal chalcogenides
Porous metal chalcogenides |
Synthesis method |
Morphology |
Porosity |
BET surface area (m2 g−1) |
Pore size (nm) |
Ref. |
NiS/Ni/NC |
Ball-milling |
Sponge-like |
Meso- |
921.2 |
4 |
100
|
CoSx |
Anodization |
Wrinkled-like |
Meso- |
35.6 |
5 |
101
|
MoS2/CoMo2S4 |
Soft template |
Spherical |
Meso- |
53 |
7 |
102
|
FeS2 |
Sol–gel |
Spherical |
Meso- |
128 |
3.8 |
21
|
Co9S8 |
Reactive spray deposition |
Coral-reef-like |
Meso- |
120 |
4.8 |
94
|
Ni3S4 |
118 |
5.3 |
NiCo2S4 |
113 |
5.6 |
FeS |
101 |
6.3 |
Ni0.76Fe0.24Se |
Hydrothermal |
3D-rose-like |
Meso- |
14.3 |
5.2 |
22
|
Cu0.4Ni0.3Co0.3Se2@N-C n-box |
Template-assisted refluxing method |
Hollow nanobox |
Meso- |
72.1 |
2.5 |
103
|
Ni0.5Mo0.5OSe |
Hydrothermal |
Nanosheets |
Nano- |
286 |
2.36 |
104
|
Co/Fe/Se-400 |
Solvothermal |
2D lamellar structure |
Micro- |
178.72 |
2.40 |
105
|
CoZn–Se |
Liquid-phase deposition |
Nanoflakes |
Porous |
20.4 |
7.9 |
106
|
O-Co0.5Mo0.5Se2 |
Hydrothermal |
Nanoflakes |
Nano- |
302 |
3.59 |
107
|
Ni-MOF-Fe-Se-400 |
Solvothermal |
Nanosheet and mesoporous tubes |
Meso- |
86.86 |
3 |
108
|
CoTe2@CdTe |
Hydrothermal |
Nanowire array |
Meso- |
18.28 |
31.1 |
109
|
CoTe |
Hydrothermal |
Nanoflakes |
Porous |
53.4 |
— |
110
|
NiNCs-1T-Mn-VTe2 |
Hydrothermal |
Nanosheet |
Meso- |
92 |
24.3 |
111
|
CoTe2/MnTe2 |
Hydrothermal |
Nanorods |
Porous |
134.9 |
6.8 |
112
|
V-CoTe2/MoTe2@CC |
Hydrothermal |
Nanodendrites |
Meso- |
279.5 |
5.5 |
113
|
NdTe-HS/NF |
Hydrothermal |
Hollow shell |
Meso- |
43 |
— |
114
|
4.3 Porous metal tellurides
Transition metal tellurides (TMTs) have gained significant interest as emerging catalysts due to the unique properties of tellurium (Te). In comparison to other chalcogens like selenium (Se), sulfur (S), and oxygen (O), tellurium (Te) has a lower electronegativity and a more metallic nature.115 These characteristics contribute to improved electrical conductivity and a stronger covalent bond between the metal and chalcogen atoms in TMTs. The covalent character in the system can result in a beneficial electronic band structure. This makes it easier to establish the boundaries of the valence band and the conduction band with the oxidation and reduction potentials of water that are present. In addition to this, it enhances the redox reactions that occur within the transition metal center, which ultimately results in an improvement in the electrocatalytic performance.23,116,117 Chen et al.99 found that vacancy occupation triggers a phase change from hexagonal to orthorhombic CoTe2, significantly increasing OER catalytic activity. To create h-CoTe2@HPC/CNTs, hexagonal CoTe2 nanoparticles with high Te-vacancy content were pyrolyzed and then tellurized in core–shell ZnCo-zeolitic imidazolate frameworks. CoTe2 underwent a polymorphic transition from hexagonal to orthorhombic structure through anion P-doping (Fig. 6f). This resulted in the creation of HPC/CNTs-confined orthorhombic P-doped CoTe2 nanoparticles (o-CoTe2|P@HPC/CNTs). Hierarchically porous carbon was designed to maximize surface area and prevent nanoparticle agglomeration. The BET surface area and pore volume of o-CoTe2|P@HPC/CNTs were calculated as 262 m2 g−1 and 0.362 cm3 g−1, respectively. Large BET surface area and well-distributed pores can expose active areas and speed up mass diffusion during electrochemical reactions.99 Xue et al.118 fabricated NiTe nanoarrays arranged in a cross-columnar pattern supported on a nickel foam substrate.118 Etching nickel foam using sodium tellurite as a source of tellurium and hydrazine hydrate as the reducing agent was the method that was utilized in the fabrication of the NiTe nanoarrays on NF. This process generated tellurium ions in a hydrothermal system at a temperature of 180 °C for a duration of 24 hours. Afterward, an ion exchange method was employed to create NiTe/NiS heterojunctions. This involved immersing the NiTe nanoarrays in a sodium sulfide solution at a temperature of 160 °C for a duration of 8 hours. Remarkably, the NiTe/NiS nanoarrays, demonstrated exceptional stability and displayed remarkable activity in the OER at extremely low overpotentials.118 Xu et al.119 aimed to create a new Ni3Te2–CoTe composite electrocatalyst in their study, considering the benefits of the hybridization approach.119 The Ni3Te2–CoTe composite was synthesized on carbon fabric using a one-step hydrothermal method. Adding CoTe in Ni3Te2–CoTe/CC enhanced the exposure of Ni3Te2, contributing to a superior catalytic performance. The results indicated that Ni3Te2–CoTe/CC has the potential to be a suitable option for many applications requiring OER. Furthermore, the findings demonstrated that using material hybridization as a straightforward and efficient approach to improve the electrochemical performance of an electrode was a significant finding.119
5. Electrocatalytic water splitting performance of porous metal chalcogenides
Electrocatalysis is gaining importance in sustainable technologies as the demand for alternative energy sources, especially in green energy conversion and clean fuel production sectors, continues to rise.120–122 Electrocatalytic water-splitting, powered by renewable energy, is highly regarded as a significant achievement in the future energy sector.123,124 This process utilizes water, a renewable resource, to produce H2, which has a high energy content of 143 MJ kg−1 and is a clean energy carrier with zero carbon emissions.125,126 A variety of metal chalcogenides, such as CoS2, FeS2, NiS2, MoS2, CoTe, NiSe, etc., have been effectively produced as porous structures with diverse morphologies, crystal phases, and pore size distributions.20,21,127–135 In this section, we examine the electrochemical energy uses of common porous metal chalcogenides. These materials are appealing due to their notable characteristics, such as strong mechanical properties, high stability against heat and chemicals, compatibility with the environment, versatile surface chemistry, and diverse architecture. Additionally, they possess a significant number of oxygen vacancies and defects. The article also demonstrates the appropriate configuration of micropores, mesopores, and macropores, which can serve as chemical reaction regions.
5.1 Porous metal sulfides for EWS
Until now, nickel sulfide has been well-researched and suggested to be effective in electrocatalytic water splitting in an alkaline media.136,137 To further enhance the catalytic activity, NiS2 has been combined with a highly efficient electrocatalyst, such as MoS2, resulting in increased catalytic activity.138 Lonkar et al.138 have suggested an eco-friendly method for synthesizing MoS2-wrapped NiS2 nanohybrids that were evenly distributed on conductive graphene sheets. Fig. 7a depicts the scheme for creating mesoporous MoS2–NiS2/G nanohybrids using solid-state synthesis. These nanohybrids were utilized as a bifunctional electrocatalyst for the process of overall water splitting (Fig. 7b). The combination of MoS2–NiS2/graphene has resulted in an increased surface area (105 m2 g−1), many electro-active sites, and a customized conductive network. This has led to improved efficiency in the process of water splitting. The nanohybrid demonstrated excellent catalytic efficiency for the HER with remarkably low overpotentials in both acidic (152 mV) and alkaline (141 mV) environments at a current density of 10 mA cm−2. Similarly, a low OER overpotential of 320 mV was attained in an alkaline environment. The resulting nanohybrid has developed into a highly effective electrocatalyst with dual functions, allowing efficient water splitting. It achieves a final cell voltage of 1.58 V and demonstrates excellent activity and stability (Fig. 7c). As shown in Fig. 7d, hydrogen and oxygen evolved significantly at the cathode and the anode electrodes. MoS2–NiS2/G possesses outstanding electrocatalytic performance, which can be attributed to the presence of a heterogeneous nanostructure composed of MoS2 and NiS2. In addition to being supported by a conductive graphene framework, this nanostructure was loaded with defect-rich synergistic interfaces. This arrangement provides a large number of active sites and ensures high-rate and long-life stability, as shown in Fig. 7e.138 Previous research has shown that porous cobalt sulfides, such as Co9S8, CoS2, CoS, etc., exhibit superior catalytic activity for both the HER and the OER in an alkaline media.127,139–141 Additionally, these sulfides demonstrate exceptional chemical stability and electrical conductivity. Moreover, earlier research has shown that the free energy of adsorption for hydrogen and oxygen-containing substances decreases when cobalt atoms are added to the edge sites of other transition metal chalcogenides.142,143 Furthermore, the transfer of charge inside the electrocatalyst material through linkages, as well as between the electrocatalyst interface and species containing H and O, is enhanced synergistically, thereby showing a considerable increase in the catalyzing activity of HER and OER.142 Further, the combination of porous cobalt and nickel sulfide shows potential for use in electrocatalytic water splitting.
 |
| Fig. 7 (a) Schematic showing of the fabrication of the MoS2–NiS2/G nanohybrid, (b) the cathode and anode LSV curves of the MoS2–NiS2/G‖MoS2–NiS2/G two-electrode system in 1 M KOH, (c) chronopotentiometry and chrono-amperometry curves at a constant current density of 10 mA cm−2 and potential for overall water splitting, (d) an optical photograph illustrating the production of hydrogen and oxygen bubbles resulting from the overall water splitting process on MoS2–NiS2/G, functioning as both the anode and cathode and (e) schematic illustration of the overall water splitting using MoS2–NiS2/G as a bifunctional electrocatalyst for simultaneous HER and OER. Reproduced from ref. 138 with permission from Royal Society of Chemistry, copyright 2020. (f) Table of contents graphic of 3D binder-free NiCoSe2@PCM as a high-efficiency bifunctional electrocatalyst for overall water splitting. Reproduced from ref. 149 with permission from Elsevier, copyright 2021. (g) Schematic illustration for the design and fabrication of the O-Co1−xMoxSe2 (0 ≤ x ≤ 1) nanostructures, (h) schematic representation for the construction of water splitting device, (i) polarization curves of O-Co0.5Mo0.5Se2‖O-Co0.5Mo0.5Se2 and Pt/C‖RuO2 devices at a fixed scan rate of 10 mV s−1. Reproduced from ref. 107 with permission from Wiley, copyright 2020. (j) Schematic of the construction of the NiNCs-1T-Mn-VTe2 NS and its utilization as a superior electrocatalyst for overall water splitting, (k) LSV measurements curves of NiNCs-1T-Mn-VTe2, (l) digital NiNCs-1T-Mn-VTe2 image of the device during the electro-catalytic water splitting showing the appearance of H2 reaction and O2 gas bubbles on the surface of the cathode and anode. Reproduced from ref. 111 with permission from Elsevier, copyright 2022. | |
Moreover, increasing the intrinsic activity towards HER and OER can be accomplished by utilizing a porous heterostructured nanoelectrocatalyst, which provides a potential technique.144–147 For instance, Hu et al.148 created freestanding heterogeneous CoS2/CoS nanosheets using a one-step sintering procedure. These nanosheets were made using a unique hierarchical tremella-like metal–organic framework (MOF) and exhibited a high specific surface area of 45.35 m2 g−1. A cost-effective OER electrocatalyst has been developed, which produces satisfactory electrocatalytic efficiencies with a low overpotential of 269 mV at a current density of 10 mA cm−2, a Tafel slope of 52 mV dec−1, and a good stability in alkaline solution that is comparable to that of RuO2 counterparts.148 Ran et al.21 described a simple synthetic procedure for creating mesoporous FeS2 as an electrocatalyst for the HER without using a hard template. After a sulphurization process in an H2S environment, the sol–gel method was used to successfully generate the mesoporous FeS2 materials with a high surface area (128 m2 g−1).
An impressive HER catalytic performance was attained with a low overpotential of 96 mV at a current density of 10 mA cm−2 and a Tafel slope of 78 mV per decade in alkaline circumstances (pH 13). According to theoretical estimates, the exposed (210) facets are responsible for the mesoporous FeS2's exceptional catalytic activity. The mesoporous FeS2 material may offer a viable substitute for Pt-based electrocatalysts for water splitting.21 Yang et al.150 described a three-dimensional (3D) porous CoS2/FeS-MOF with tunable Co/Fe molar ratios for HER and OER (CoS2/FeS-MOF@NF). The built symmetric electrolyzer CoS2/FeS-MOF@NF-1 achieves a low cell voltage of 1.5 V at 10 mA cm−2 and long-term stability for 24 hours.150
Another research proposes a design methodology for effective high-current-density OER electrocatalysts utilizing sustainable wood fiber materials.151 The researchers enclosed Co9 S8/CoS heterojunction nanoparticles within a sulfur and nitrogen co-doped carbon (SNC) matrix and uniformly attached them onto the S-doped carbonized wood fibers (SCWF) substrate to create microleaf arrays. The heterojunction interface effect in (Co9S8/CoS)@SNC can enhance the scaling relationship of the intermediate and remarkably improve catalytic performance for the OER. The distinctive structural characteristics of microleaf arrays inhibit active particle agglomeration and offer an extensive specific surface area of 252.05 m2 gm−1 for the reaction. The electrocatalyst performs superior high-current-density oxygen evolution, exhibiting a low overpotential (274 mV @ 1000 mA cm−2) and Tafel slope (48.84 mV dec−1).151
From the above discussion, it is clear that porous metal sulfides have shown promising potential as efficient electrocatalysts for water splitting, particularly in HER and OER in alkaline media. Combining these metal sulfides like MoS2 and graphene can enhance their performance. Key findings include MoS2-wrapped NiS2 nanohybrids on graphene sheets exhibiting excellent bifunctional electrocatalytic activity, porous cobalt sulfides demonstrating superior catalytic activity and chemical stability, and heterostructured nanoelectrocatalysts such as CoS2/CoS nanosheets and CoS2/FeS-MOF enhancing intrinsic activity towards HER and OER. These findings underscore the potential of porous metal sulfides as effective electrocatalysts for water splitting.
5.2 Porous metal selenides for EWS
Selenide and sulfur are part of the same major group and exhibit numerous similarities in their properties. Metal selenides are exceptional electrocatalytic materials characterized by superior electrical conductivity and great physical density. Furthermore, the s and p orbitals of selenide can undergo hybridization with the d orbitals of metals, resulting in selenide exhibiting superior crystalline characteristics and catalytic efficacy. TMSe is anticipated to serve as a catalyst that can substitute precious metals due to its elevated catalytic activity, narrow band gap, excellent stability, and inexpensive cost.152,153
Porous metal selenides have several benefits, including facile synthesis, exceptional catalytic activity, and outstanding stability, which render them very suitable for water electrochemical water-splitting.154 Jiang et al.155 created a structure consisting of nanoporous Co0.85Se with single-atom platinum (Pt/np-Co0.85Se) to investigate the underlying factors contributing to the activity of the HER. The presence of atomic Pt in Co0.85Se optimizes the surface active sites, resulting in lower energy barriers and enhanced hydrogen adsorption/desorption. The combined action of Pt atoms and np-Co0.85Se resulted in an initial overpotential that was close to zero. The Tafel slope exhibited a remarkably low value of 35 mV dec−1, while the turnover frequency reached an impressive value of 3.93 s−1 at −100 mV in a neutral solution. The diffusion of Pt ions into Co vacancies of nano-sized Co0.85Se ligaments is facilitated by the bicontinuous nanoporous structure with a large surface area (15.1 m2 g−1), creating the uniform Pt-doped np-Co0.85Se single-atom, which facilitated more efficient mass-transfer processes. These results surpassed those of commercial Pt/C.155
The creation of hierarchical nanostructures with very efficient and long-lasting multifunctional catalysts holds great importance in the realm of emerging water-splitting energy technologies. In this regard, Prabhakaran and colleagues107 have shown a method for creating a 3D hierarchical structure of oxygenated cobalt molybdenum selenide (O-Co1−xMoxSe2) using nanoarchitectures. Following a facile and cost-effective hydrothermal method, these structures were fabricated using a one-of-a-kind ion exchange procedure (Fig. 7g).107 At a relative pressure of 0.45 to 1.0, all materials displayed type IV isotherms with a hysteresis loop, indicating mesoporous characteristics. Above all, O-Co0.5Mo0.5Se2 NSs had a huge specific surface area (SSA) of roughly 302 m2 g−1, significantly greater than that of O-CoSe2 (≈71 m2 g−1), O-MoSe2 (≈135 m2 g−1), O-Co0.75Mo0.25Se2 (≈186 m2 g−1), and O-Co0.25Mo0.75Se2 (≈225 m2 g−1). Furthermore, the O-Co0.5Mo0.5Se2 NSs exhibit a mesoporous nature with an average pore size of around 3.59 nm. The oxygen released during the selenium process at 180 °C using a regulated ion-exchange approach is responsible for successfully developing the mesopores in the O-Co0.5Mo0.5Se2 NSs. Due to its abundant electro-active sites and nanoporous networks, as well as its plentiful oxygen vacancies, the O-Co0.5Mo0.5Se2 catalyst demonstrates efficient catalysis of the HER and OER (Fig. 7h). It achieves a low overpotential of approximately 102 and 189 mV, respectively, at a current density of 10 mA cm−2. Additionally, it exhibits exceptional durability. The O-Co0.5Mo0.5Se2‖O-Co0.5Mo0.5Se2 water-splitting device requires a voltage of around 1.53 V at a current density of 10 mA cm−2 (Fig. 7i), which was significantly better than the benchmark Pt/C‖RuO2 (approximately 1.56 V).107
Preparing improved three-dimensional electrodes and optimizing their morphology is crucial for increasing the electrocatalytic activity of catalysts. The catalytic activity is enhanced by directly depositing selenide onto a conductive substrate, reducing the resistance between the catalyst and the current collector. Nanofiber (NF) is frequently used as a substrate to create Ni–Co–Se nanostructures.156,157 It simultaneously acts as both the framework and the source of Ni. The Ni0.89Co0.11Se2 mesoporous nanosheet networks, developed by Liu et al.,157 exhibit exceptional catalytic capabilities for the HER and demonstrate remarkable stability throughout a broad pH range due to their distinctive morphology and electronic structure. The observation of a type IV isotherm with a hysteresis loop confirmed the mesoporous structure of the Ni0.89Co0.11Se2 nanosheets. The specific surface area of Ni0.89Co0.11Se2 nanosheets was determined to be 37.32 m2 g−1, and their mean pore size was 4.8 nm, ranging from 2 to 20 nm.157 Poorahong et al.149 have also fabricated a three-dimensional, binder-free bimetallic nickel–cobalt selenide nanosheet structure anchored on a macroporous conductive carbon membrane (NiCoSe2@PCM). A distinctive interconnecting macroporous phase change material was synthesized using cryogelation, freeze-drying, and subsequent carbonization. The PCM serves as a framework for the development of a NiCoSe2 catalyst (Fig. 7f). Uniform and compact nanosheets composed of few-layer NiCoSe2 were synthesized on the surface of the PCM, eliminating the necessity for a transfer step or a conductive addition. The porous characteristic, as evidenced by the type IV isotherm, resulted in a high BET surface area of 38.2 m2 g−1. The NiCoSe2 nanosheets, oriented perpendicularly, exhibit exceptional electrochemical catalytic activity, demonstrated by a low overpotential of 0.116 V (at 10 mA cm−2) and a Tafel slope of 66 mV dec−1 for the HER, as well as an overpotential of 1.37 V (at 10 mA cm−2) with a Tafel slope of 60 mV dec−1 for the OER. Remarkable stability with no degradation in current density was noted during a 23 hour testing duration. Bifunctional NiCoSe2@PCM was used to construct a two-electrode electrolyzer, achieving 10 mA cm−2 at a low voltage of 1.73 V.
Wang et al.158 have fabricated porous NiCo diselenide nanosheets on carbon cloth for water splitting. The NiCo diselenide nanosheets have a moderate BET-specific surface area (165 m2 g−1), which is about six times greater than that of Ni diselenide nanosheets (28 m2 g−1) but somewhat less than that of Co diselenide nanoplates (172 m2 g−1). The size distribution of nanopores on the surface of metal diselenide nanosheets may be related to the variation in BET surface area. Ni diselenide nanosheets have pores that are roughly 35 nm in size, which is more significant than that of Co diselenide nanoplates (5 nm) and NiCo diselenide nanosheets (8 nm). The NiCo diselenide/CC composites exhibited high HER activity with a small Tafel slope of 31.6 mV dec−1 and a low overpotential of 108 mV at 10 mA cm−2. They also have superior OER capability with a small Tafel slope of 42.3 mV dec−1 and an OER current density of 10 mA cm−2 at a low potential of 258 mV. Their HER/OER activity remained steady even after 50 hours of polarization. The three-dimensional structure of the nanosheets facilitates the movement of charge and electrons, hence enhancing the availability of catalytic active sites.158
Recent studies have shown that metal selenides, specifically cobalt selenide (Co0.85Se) and nickel–cobalt selenide (NiCoSe2), can be effective water-splitting electrocatalysts. Co0.85Se exhibits exceptional HER activity with low overpotential and Tafel slope, while O-Co1−xMoxSe2 nanostructures demonstrate efficient HER and OER catalysis. NiCoSe2 nanosheets anchored on conductive substrates show excellent electrochemical catalytic activity for HER and OER. The enhanced performance of these metal selenides can be attributed to their high surface area, mesoporous structure, abundant electro-active sites, and optimized electronic structure (Table 2).
Table 2 Electrochemical parameters of porous metal chalcogenides
Porous metal chalcogenides |
Porosity |
Electrolyte |
OER η (mV) @ 10 mA cm−2/Tafel slope |
HER η (mV) @ 10 mA cm−2/Tafel slope |
Stability (h) |
TOF (s−1) @ 300 mV |
Ref. |
Ni3S2/MnS–O |
Porous |
1 M KOH |
228/46 |
116/41 |
50 |
— |
159
|
Ni0.7Fe0.3S2 |
Porous |
1 M KOH |
198/56 |
155/109 |
13.8 |
— |
160
|
h-CoxSy |
Meso- |
1 M KOH |
320/98 |
295/145 |
18 |
0.45 |
161
|
N–Ni3S2/NF |
Porous |
1 M KOH |
—/70 |
110 |
8 |
— |
162
|
MoS2/Mo |
Macro- |
0.5 M H2SO4 |
— |
168/48 |
17 |
— |
19
|
FeS2 |
Meso- |
0.1 M KOH |
— |
96/78 |
25 |
— |
21
|
MoS2–NiS2/G |
Meso- |
0.5 M H2SO4 |
— |
152/53 |
20 |
— |
138
|
1 M KOH |
320/82 |
141/77 |
NiS2 |
Meso- |
0.5 M H2SO4 |
— |
174/63 |
10 |
— |
136
|
NiS |
Meso- |
1 M KOH |
320/59 |
148/82 |
MoNiFeS |
Micro- |
1 M KOH |
190 @ 40/74.2 |
247 @ 40/164 |
50 |
— |
163
|
Zn0.5Al0.5S@N-MC |
Meso- |
1 M KOH |
340/23 |
— |
50 |
— |
164
|
NiCoPS@SC |
Meso- |
1 M KOH |
329/87 |
— |
12 |
— |
165
|
MoNiS3−xOx |
Porous |
1 M KOH |
— |
231 @ 1 A/65.5 |
48 |
— |
166
|
P-CoNi2S4 |
Porous |
1 M KOH |
282/40 |
135/65 |
100 |
— |
147
|
MoS2@Zn0.76Co0.24S |
Meso- |
1 M KOH |
90 @ 20/57 |
169/39.7 |
48 |
— |
167
|
Ni0.76Fe0.24Se |
Meso- |
1 M KOH |
197/56 |
— |
16.6 |
— |
22
|
Pt/np-Co0.85Se |
Nano- |
1 M PBS |
— |
55/35 |
40 |
3.93 @ 100 mV |
155
|
CuCo2Se4@Au |
Porous |
1 M KOH |
320 @ 50/66.5 |
125/- |
8 |
0.041 |
168
|
Ni0.89Co0.11Se2 MNSN/NF |
Meso- |
1 M KOH |
— |
85/52 |
30 |
— |
157
|
O-Co0.5Mo0.5Se2 |
Nano- |
1 M KOH |
189/62 |
102/59 |
36 |
— |
107
|
N–NiSe2/NF |
Meso- |
0.5 M H2SO4 |
— |
102/ |
20 |
— |
169
|
1 M PBS |
— |
206 |
1 M KOH |
— |
86/69 |
Fe-doped MOF CuCoSe@HCNF |
Meso- |
1 M KOH |
260 @ 20/57 |
70/59 |
50 |
— |
170
|
Ni0.85Se/RGO |
Porous |
1 M KOH |
320 @ 30/91 |
169/65 |
20 |
0.049 |
82
|
Co–ZnSe |
Porous |
1 M KOH |
320/66 |
— |
15 |
0.022 |
106
|
NiSe2–MoSe2@NC/CC |
Porous |
1 M KOH |
280/84.4 |
91/63.6 |
70 |
— |
171
|
CuTe-NS/NiF |
Porous |
0.5 M KOH |
— |
250/36 |
65 |
0.912 @ 350 mV |
23
|
NiNCs-1T-Mn-VTe2 |
Meso- |
1 M KOH |
258 @ 40/65.1 |
61/71.5 |
50 |
— |
172
|
Co–Te NF |
Porous |
1 M KOH |
241/201 |
90/143 |
15.5 |
1.03 |
134
|
Hollow NiTe2 |
Meso- |
0.5 M H2SO4 |
— |
85/59 |
30 |
— |
173
|
Fe-Co1.11Te2@NCNTF-2 |
Porous |
1 M KOH |
297/92 |
107/73 |
18 |
0.02 |
174
|
CoTe2@NCNTFs |
Meso- |
1 M KOH |
330/82.8 |
204/58.04 |
30 |
— |
175
|
Fe-Co1.11Te2@NCNTF |
Porous |
1 M KOH |
297/97.7 |
107/73 |
18 |
0.035 |
174
|
5.3 Porous metal tellurides for EWS
Porous metal tellurides (PMTs) have gained significant attention as new catalysts due to the unique properties of tellurium.176–178 When compared to other chalcogens, such as selenium (Se) and sulfur (S), tellurium (Te) appears to have a lower electronegativity and a more robust metallic property.115 This leads to increased electrical conductivity and a higher level of covalency in the metal–chalcogen links in PMTs. The presence of covalent character in the system can result in a beneficial electronic band structure. This makes it easier to align the edges of the valence band and the conduction band with the oxidation and reduction potentials of water that are present. In addition to this, it stimulates the redox reactions that occur within the transition metal center, which ultimately results in an improvement in the electrocatalytic performance.23
In reality, the gradual shift in the electronic band structure of oxides and the remainder of the chalcogenide series (sulfides, selenides, and tellurides) may explain the trend in catalytic activity between oxides and the rest of the chalcogenide series. This is because the margins of the valence and conduction bands coincide with the water oxidation–reduction levels.179 As the electronegativity of the chalcogen atom falls further down the series, the degree of covalency in the metal–chalcogen bond increases. Previous research has shown that a higher degree of covalency in metal–anion bonding increases the efficiency of OER catalysis, so it is reasonable to expect the chalcogenide series to improve catalytic efficiency even more.116 Because Te's electronegativity (2.1) is lower than Se's (2.55), nickel tellurides will have a higher degree of covalency than selenides. Indeed, a qualitative band structure investigation revealed that tellurides have a better band alignment with water oxidation levels than selenides. Gao et al.115 synthesized innovative hierarchical CoTe2 and CoTe nanofleeces for effective OER catalysts using phase-selective methods. The hierarchical CoTe2 and CoTe nanofleeces exhibited BET surface areas of 97 and 75 m2 g−1, respectively, which are relatively high for transition metal chalcogenide materials. The elevated surface area is ascribed to the minuscule branched nanofleeces, which possess typical diameters of approximately 10 nm. At a modest overpotential of 357 mV, hierarchical CoTe2 nanostructures have been claimed to be capable of achieving a current density of 10 mA cm−2 for the oxygen evolution reaction.115
Pan et al.111 have developed nickel nanoclusters (NiNCs) that are combined with manganese (Mn) and inserted into and mixed with 1T VTe2 nanosheets (NiNCs-1T-Mn-VTe2 NS) to achieve EWS at extremely low potentials (Fig. 7j). The N2 adsorption–desorption isotherm results indicated that NiNCs-1T-Mn-VTe2 NS possesses the largest surface area of 92 m2 g−1, with an average pore diameter of 24.3 nm. The efficacy of EWS is greatly enhanced by Mn doping and intercalation in 1T VTe2 (1T Mn VTe2), as it improves the performances of both the OER and the HER. Combining NiNCs with 1T Mn VTe2 results in the formation of a very efficient electrochemical catalyst, known as NiNCs-1T-Mn-VTe2 NS, to split water at extremely low potentials. The NiNCs-1T Mn VTe2 NS exhibited remarkable performance, achieving a current density of 10 mA cm2 with an HER overpotential of only 61 mV and a current density of 40 mA cm2 with an OER overpotential of 258 mV. The NiNCs-1T Mn VTe2 NS(+) device necessitated a cell potential of 1.51 V to achieve a current density of 10 mA cm2 (Fig. 7k and l).111
The aforementioned study indicates that porous metal tellurides, particularly hierarchical CoTe2 and CoTe nanofleeces, together with nickel nanoclusters integrated with manganese-doped VTe2 nanosheets (NiNCs-1T-Mn-VTe2 NS), serve as efficient electrocatalysts for water splitting. These nanostructures possess a high surface area and exhibit efficient catalytic activity for the OER, whereas NiNCs-1T-Mn-VTe2 NS has outstanding performance in electrochemical water splitting, attaining low overpotentials for both reactions. The improved performance is due to elevated surface area, porosity, regulated doping and heterostructuring, diminished charge transfer resistance, and augmented electrical conductivity.
All the above-mentioned porous metal chalcogenides, including sulfides, selenides, and tellurides, exhibit discrete performances toward electrochemical water-splitting. The porous metal chalcogenide catalysts exhibit low overpotentials, achieve high current densities, and deliver high intrinsic activities. In addition, heterostructured chalcogenides with controlled doping can also help increase electrical conductivity by reducing charge transfer resistance. Despite the noticeable progress in a porous metal chalcogenides catalyst, the practical applications are still under development.
The correlation between the BET surface area and the HER and OER overpotential at 10 mA cm−2 of porous metal chalcogenides-based electrocatalysts is presented in Fig. 8. This analysis reveals a significant trend where high surface area porous metal chalcogenides exhibit substantially reduced overpotential values. Notably, the electrocatalysts Ni0.5Mo0.5OSe, O-Co0.5Mo0.5Se2, and V-CoTe2/MoTe2@CC, which possess high BET surface areas, demonstrate remarkably low overpotential values. This correlation suggests that the high surface area of these materials plays a crucial role in enhancing their electrocatalytic performance. Several benefits are associated with porous metal chalcogenides with a high surface area. These benefits include an increase in the number of active sites, an improvement in mass transport, and an enhancement in electrical conductivity. These characteristics allow for improved electron transport during electrochemical processes, reducing the constraints imposed by diffusion and enhancing the reaction's kinetics. The decreased overpotential values of these chalcogenides provide evidence that they have the potential to function as effective electrocatalysts for applications involving water splitting. Further optimization of their surface area, composition, and structure could lead to even more excellent performance and the development of energy storage and conversion technologies that are more efficient and sustainable.
 |
| Fig. 8 The summary of the BET surface area, HER, and OER overpotential at 10 mA cm−2 of the various porous metal chalcogenides. The data were initially reported as follows: VTe/CNTs,180 NiFeSe@NiSe/O@CC,181 Ni0.5Mo0.5OSe,104 MoS2/CoMo2S4,182 Cu0.4Ni0.3Co0.3Se2@N-C,103 O-Co0.5Mo0.5Se2,107 Ni3S2/MnS–O,159 CoTe NF,110 V-CoTe2/MoTe2@CC,113 MoS2–NiS2/G,138 h-CoxSy,161 Ni0.76Fe0.24Se.22 | |
6. Performance of porous metal chalcogenides for overall water splitting
Water electrolyzers require an active catalyst to facilitate the HER and OER processes. Using a single OER and HER bifunctional electrocatalyst not only makes the entire system design easier but also reduces the cost of the system. One of the most challenging tasks is to drive the electrolyzer while maintaining a low cell voltage to achieve a high current density. To improve the overall water-splitting activity, it is of utmost significance to combine the advantages of HER and OER electrocatalysts to design OER-HER bifunctional heterostructures that are both long-lasting and effective.
In this regard, Pathak et al.113 used a hydrothermal approach to synthesize a vanadium-doped cobalt/molybdenum precursor. During this process, the precursor was transformed into the matching telluride (Fig. 9a), which had the morphology of nanodendrites growing across 2D nanosheets (Fig. 9b and c). Fig. 9d confirms that the N2 adsorption isotherms of V-CoTe2/MoTe2@CC and CoTe2/MoTe2@CC exhibited typical type-IV isotherms. These isotherms had surface areas of 279.5 m2 g−1 and 225.2 m2 g−1, respectively. BET studies demonstrated that the introduction of V doping into the material resulted in the formation of defects, lattice expansion, and surface roughening, all of which contributed to a considerable increase in the BET surface area. Furthermore, the BJH pore size distribution profiles of V-CoTe2/MoTe2@CC and CoTe2/MoTe2@CC demonstrate that the bulk of mesopores are approximately 5.5 nm and 5.1 nm, respectively. When it comes to aqueous alkaline electrolytes, the vast majority of mesopores are compatible with electrical mobility.
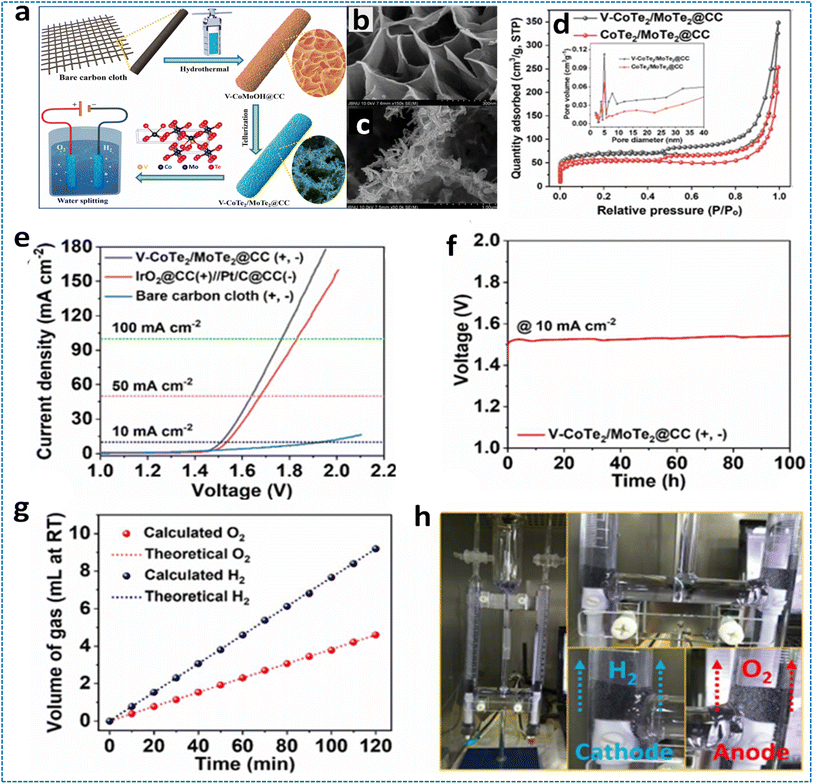 |
| Fig. 9 (a) Schematic representation of the preparation of V-CoTe2/MoTe2@CC and its application for water splitting, (b) FESEM image of as-prepared V–CoMoOH@CC, (c) FESEM image of V-CoTe2/MoTe2@CC, (d) N2 adsorption isotherms (inset: BJH pore size distribution profile), (e) polarization curves of V-CoTe2/MoTe2@CC(+, −), IrO2@CC(+)//Pt/C@CC(−) and bare CC(+, −) devices, (f) chronopotentiometric stability test result at 10 mA cm−2, (g) theoretical and experimental volumes of H2 and O2, (h) digital image of a laboratory-made H-cell set up for the measurement of faradaic efficiency (insets: enlarged photos showing the cathode and anode), generated at 10 mA cm−2 by the V-CoTe2/MoTe2@CC electrodes at varying times in an H-cell. Reproduced from ref. 113 with permission from Royal Society of Chemistry, copyright 2024. | |
Importantly, comprehensive characterization shows how vanadium doping may be used to control the electrical characteristics of bimetallic tellurides. This is accomplished by causing lattice expansions and exposing ample active sites for the HER and OER. As a consequence of this, the V-CoTe2/MoTe2@CC material has remarkable performance in terms of both the HER (η10 = 79 mV, Tafel slope = 58.9 mV dec−1) and the OER (η10 = 249 mV, Tafel slope = 57.7 mV dec−1). In terms of overall water splitting, the V-CoTe2/MoTe2@CC(+, −) semiconductor beats the state-of-the-art IrO2@CC(+)//Pt/C@CC(−) semiconductor (Fig. 9e). CoTe2 and MoTe2 are responsible for the synergistic effects that manifest themselves as a result of the modified lattice that is caused by vanadium dopants and the coexistence of several active sites.
Remarkably, the potential of the V-CoTe2/MoTe2@CC(+, −) full-cell device was demonstrated by continuously executing the chronopotentiometry (CP) test for a duration of 100 hours at a current density of 10 mA cm−2 in a solution of 1.0 M KOH (Fig. 9f). The faradaic efficiency of the electrode materials was also investigated by measuring the volume of hydrogen and oxygen produced at a current density of 10 mA cm−2 at various time intervals using a laboratory-made hydrogen cell. The volume of hydrogen and oxygen produced was monitored every ten minutes for up to one hundred and twenty minutes. This was done to precisely match the theoretical values (Fig. 9g) and provide strong evidence of a one hundred percent faradaic efficiency for the HER and the OER. The digital photos that are displayed in Fig. 9h show the H-cell electrolyzer that was manufactured in the laboratory, as well as the H2 and O2 bubbles that were produced at the cathode and anode, respectively.113Fig. 10 compares the overall water-splitting cell voltage and stability of the bifunctional mesoporous metal chalcogenide electrocatalysts. Several PMCh catalysts have exhibited superior performance in terms of their capacity to operate at low cell potential for overall water splitting. However, the issue of durability remains a concern. Fig. 10 depicts the V-CoTe2/MoTe2@CC catalyst, which is the most suitable choice for overall water splitting and practical application, demonstrating excellent performance and durability. Therefore, developing efficient bifunctional catalysts with long-lasting performance capable of being included in renewable technologies continues to be difficult.
 |
| Fig. 10 Overall water-splitting cell voltage and stability of the bifunctional mesoporous metal chalcogenide electrocatalysts. The data were initially reported as follows: Ni/NiS/NC,100 Ni3S2/MnS,159 CoSx,101 MoS2–NiS2/G,138 (Ni0.33Co0.67)S2/CC,95 Ni0.85Se/RGO,82 O-Co0.5Mo0.5Se2,107 Fe-Co1.11Te2@NCTF,174 V-CoTe2/MoTe2@CC,113 Fe-CuCoSe@HCNFs,170 and NiSe/Ni/NC.183 | |
In a nutshell, mesoporous metal chalcogenide materials exhibit exceptional efficacy in electrochemical water splitting owing to their distinctive structural and electrical characteristics. These materials possess larger pores (2–50 nm) compared to microporous materials, facilitating enhanced mass transfer of reactants and products during electrochemical processes. They possess an increased surface area, offering additional active sites for electrochemical reactions. Increased pore size diminishes diffusion constraints, facilitating easier access of reactants to active sites. Thus, mesoporous materials have enhanced electronic conductivity due to their reduced pore sizes. They demonstrate excellent stability compared to macroporous materials, which are susceptible to collapse or deterioration during electrochemical reactions. The pore structure can be adjusted to boost performance, and integrating metal and chalcogenide ions can improve the material's efficacy in water splitting.
7. Challenges and future research directions
A major challenge in utilizing PMChs for electrochemical water-splitting is the low electrical conductivity, restricted active areas, and inadequate stability under extreme operating conditions. Over time, PMChs often experience deterioration, resulting in reduced catalytic activity. Moreover, a substantial impediment must be addressed for the scalability of PMChs synthesis. Many researchers have investigated diverse techniques to tackle these challenges. Persistent efforts have demonstrated that these tactics will likely improve charge transfer and catalytic activity of PMChs. Nonetheless, additional research is required to resolve concerns of irreversible surface restoration. Surface modification can enhance the production of electrocatalytic hydroxyl oxide. Conversely, these hydroxyl oxides frequently dissolve in the electrolyte, leading to the corrosion of the catalyst or the degradation of its structure. Thus, achieving and sustaining the appropriate equilibrium during water splitting is essential for preserving the catalyst's efficacy. Fig. 11 depicts the major challenges and feasible solutions for the utilization of PMChs in electrochemical water-splitting applications.
 |
| Fig. 11 Schematic representation of the key challenges in utilizing porous metal chalcogenides for electrocatalytic water splitting and the corresponding feasible solutions. | |
(1) Porous metal chalcogenides are primarily manufactured using transition metals such as Co, Ni, Fe, etc. Additional metals such as indium (In), zinc (Zn), strontium (Sr), and others can be utilized in the synthesis of PMChs to augment their electrochemical capabilities further.
(2) Out of several cost-effective and easy synthesis methods, the hydrothermal reaction remains the most commonly employed technology. This simple synthesis approach requires very gentle reaction conditions compared to other procedures. Nevertheless, it presents challenges in monitoring crystal growth, limiting its applicability to laboratory settings and posing a significant obstacle to commercial use. Therefore, it is recommended that researchers develop a controlled and expandable synthetic method to produce different types of PMChs, as it is crucial for the widespread use of PMChs in industrial applications.
(3) The use of theoretical calculations employing Density Functional Theory (DFT) has been acknowledged as a potent method for obtaining significant insights into manipulating catalyst electronic structure and predicting the efficacy of new catalysts. Theoretical calculations offer insights into the crystal structure, electrical state, and chemical composition of PMChs. In addition, DFT provides valuable information on the process of introducing impurities (doping) and how the materials interact with polarizable molecular charge. These foundational understandings provide us with profound insight into the functioning mechanism of PMChs, as well as their activity and stability during electrolysis.
(4) The design of high-performance electrocatalysts is crucial for advancing energy storage and conversion technologies. Porous metal chalcogenides have shown great promise due to their unique structure and properties, but rational design remains a significant challenge. To address this, researchers recommend exploring the application of artificial intelligence (AI) and machine learning (ML) techniques to drive the design of porous metal chalcogenide electrocatalysts. By leveraging AI/ML algorithms, researchers can rapidly screen and optimize these materials' composition, structure, and properties to achieve enhanced electrocatalytic performance. By integrating AI/ML techniques into the design of porous metal chalcogenide electrocatalysts, researchers can unlock new opportunities for advancing energy storage and conversion technologies. The application of AI/ML techniques are expected to improve electrocatalytic performance significantly, reduce the time and resources required for experimental synthesis and testing, and provide a deeper understanding of structure–property relationships.
(5) Using porous metal chalcogenides as electrocatalysts for electrochemical water splitting is promising for producing clean hydrogen fuel. However, further improvements are needed to achieve high efficiency and stability. Tandem electrolysis, which involves using two or more electrochemical cells connected in series, can enhance the efficiency and stability of the water-splitting process. Tandem electrolysis can improve efficiency by optimizing voltage and current density for each cell, reducing the risk of electrode degradation and enhancing stability. It also allows for greater flexibility in designing water-splitting systems by enabling the use of different electrocatalysts and operating conditions. Porous metal chalcogenides offer high surface areas, enabling enhanced electrochemical reaction rates and efficiency, making them suitable for tandem electrolysis.
(6) Porous metal chalcogenides' distinctive structure and characteristics make them highly promising electrocatalysts for electrochemical water splitting. However, additional enhancements are required to reach a state of great utility. Therefore, it may be feasible to implement hybrid processes that integrate photocatalysis with bio-electrochemical systems or other water splitting methods. Increased efficiency, stability, sustainability, and cost-effectiveness are possible advantages of hybrid processes. The increased surface areas of porous metal chalcogenides allow for more efficient and rapid electrochemical reactions. Their tunable properties can be fine-tuned to optimize particular hybrid processes by manipulating their structure, morphology, and composition. Porous metal chalcogenides are well-suited for hybrid processes due to their long-term stability and performance in electrochemical applications. Building and optimizing hybrid processes that integrate different water splitting methods with electrocatalysts based on porous metal chalcogenides, creating new porous metal chalcogenide materials with enhanced hybrid process capabilities, and finally, commercializing and scaling up hybrid processes utilizing porous metal chalcogenides are all areas that could benefit from further research in the future.
8. Conclusions
Pursuing cost-effective, highly efficient, and stable electrocatalysts is crucial for promoting energy conversion through electrocatalytic reactions. PMCh electrocatalysts have emerged as a promising option for catalyzing electrochemical reactions. These catalysts possess porous structure, inherent activity, a regulated electronic structure, and a specific composition, making them highly effective in achieving this objective. The distinctive characteristics of porous metal chalcogenide nanomaterials, including optimal atomic configuration, superior electrical conductivity, easily modifiable structure, and scalability in synthesis, have significant implications for research across various domains. Innovative materials, various synthetic processes, and improved methodologies have been developed to synthesize porous metal chalcogenide nanocrystals to provide more active and stable metal sulfide-based nanomaterials. Furthermore, hybrid engineering with metal chalcogenides facilitates the creation of innovative functional composites with various materials, including metals, oxides, nitrides, chalcogenides, and carbides.
This article provides a detailed analysis of the progress in developing PMCh electrocatalysts. These catalysts have enhanced performance in terms of HER and OER, leading to better overall efficiency in water splitting. This paper comprehensively explains the rational methods used to build PMCh electrocatalysts to achieve improved efficiency in overall water splitting and related processes. The paper also discussed several synthesis methods for creating porous structures with distinct morphologies. Despite several investigations conducted using experimental techniques, PMChs continue to provide significant promise in advancing the efficiency of the water-splitting process.
Recent research has investigated the potential of PMCh as a catalyst for enhancing performance in water electrolysis. Although there are significant obstacles to overcome, it is anticipated that the current research endeavors in manufacturing, in situ characterization, theoretical computation, modeling, and experimentation will lead to advancements in PMCh electrocatalysts that can be implemented on an industrial scale.
Data availability
All data for this manuscript are available and obtained from the corresponding author.
Conflicts of interest
The authors declare that they have no known competing financial interests or personal relationships that could have appeared to influence the work reported in this paper.
References
- N. S. Lewis and D. G. Nocera, Proc. Natl. Acad. Sci. U. S. A., 2006, 103, 15729–15735 CrossRef CAS PubMed.
- E. A. Quadrelli, G. Centi, J.-L. Duplan and S. Perathoner, ChemSusChem, 2011, 4, 1194–1215 CrossRef CAS PubMed.
- P. Poizot and F. Dolhem, Energy Environ. Sci., 2011, 4, 2003–2019 RSC.
- S. Sikiru, T. L. Oladosu, T. I. Amosa, J. O. Olutoki, M. Ansari, K. J. Abioye, Z. U. Rehman and H. Soleimani, Int. J. Hydrogen Energy, 2024, 56, 1152–1182 CrossRef CAS.
- X. Li, L. Zhao, J. Yu, X. Liu, X. Zhang, H. Liu and W. Zhou, Nano-Micro Lett., 2020, 12, 1–29 CrossRef CAS PubMed.
- S. Anantharaj, P. E. Karthik, B. Subramanian and S. Kundu, ACS Catal., 2016, 6, 4660–4672 CrossRef CAS.
- K. A. Stoerzinger, O. Diaz-Morales, M. Kolb, R. R. Rao, R. Frydendal, L. Qiao, X. R. Wang, N. B. Halck, J. Rossmeisl and H. A. Hansen, ACS Energy Lett., 2017, 2, 876–881 CrossRef CAS.
- P. M. Bodhankar, P. B. Sarawade, G. Singh, A. Vinu and D. S. Dhawale, J. Mater. Chem. A, 2021, 9, 3180–3208 RSC.
- P. M. Bodhankar, D. S. Dhawale, S. Giddey, R. Kumar and P. B. Sarawade, Sustainable Energy Fuels, 2022, 6, 5491–5502 RSC.
- P. M. Bodhankar, P. B. Sarawade, P. Kumar, A. Vinu, A. P. Kulkarni, C. D. Lokhande and D. S. Dhawale, Small, 2022, 18, 2107572 CrossRef CAS PubMed.
- P. M. Bodhankar, A. Chunduri, N. Patel, D. S. Dhawale, A. Vinu, H. Aljohani and P. B. Sarawade, Sustainable Energy Fuels, 2021, 5, 1120–1128 RSC.
- Y. Jin, H. Wang, J. Li, X. Yue, Y. Han, P. K. Shen and Y. Cui, Adv. Mater., 2016, 28, 3785–3790 CrossRef CAS PubMed.
- W. Li, H. Yao, K. Yan, G. Zheng, Z. Liang, Y.-M. Chiang and Y. Cui, Nat. Commun., 2015, 6, 7436 CrossRef CAS PubMed.
- Y. Liu, Y. Guo, Y. Liu, Z. Wei, K. Wang and Z. Shi, Energy Fuels, 2023, 37, 2608–2630 CrossRef CAS.
- D. Gao, B. Xia, C. Zhu, Y. Du, P. Xi, D. Xue, J. Ding and J. Wang, J. Mater. Chem. A, 2018, 6, 510–515 RSC.
- L. Yang, L. Huang, Y. Yao and L. Jiao, Appl. Catal., B, 2021, 282, 119584 CrossRef CAS.
- H. Xu, J. Cao, C. Shan, B. Wang, P. Xi, W. Liu and Y. Tang, Angew. Chem., 2018, 130, 8790–8794 CrossRef.
- W. Wang, H. Cao, W. Li, J. Wu, E. Sheng, Z. Chen, W.-C. Cheong and K. Wu, Mater. Lett., 2020, 272, 127828 CrossRef CAS.
- Z. Pu, Q. Liu, A. M. Asiri, Y. Luo, X. Sun and Y. He, Electrochim. Acta, 2015, 168, 133–138 CrossRef CAS.
- Y. Jiang, S. Gao, J. Liu, G. Xu, Q. Jia, F. Chen and X. Song, Nanoscale, 2020, 12, 11573–11581 RSC.
- R. Miao, B. Dutta, S. Sahoo, J. He, W. Zhong, S. A. Cetegen, T. Jiang, S. P. Alpay and S. L. Suib, J. Am. Chem. Soc., 2017, 139, 13604–13607 CrossRef CAS PubMed.
- J. Yu, G. Cheng and W. Luo, Nano Res., 2018, 11, 2149–2158 CrossRef CAS.
- Q. U. Khan, M. W. Ishaq, N. Begum, K. Khan, U. Khan, A. T. Khan, M. A. U. Din, M. Idrees and L. Zhu, Int. J. Hydrogen Energy, 2021, 46, 18729–18739 CrossRef CAS.
- J. Yin, J. Jin, H. Lin, Z. Yin, J. Li, M. Lu, L. Guo, P. Xi, Y. Tang and C. H. Yan, Adv. Sci., 2020, 7, 1903070 CrossRef CAS PubMed.
- I. Vamvasakis, K. S. Subrahmanyam, M. G. Kanatzidis and G. S. Armatas, ACS Nano, 2015, 9, 4419–4426 CrossRef CAS PubMed.
- C. Gu, H.-M. Xu, S.-K. Han, M.-R. Gao and S.-H. Yu, Chem. Soc. Rev., 2021, 50, 6671–6683 RSC.
- T. D. C. Ha, H. Lee, I. Vamvasakis, G. S. Armatas, Y. Oh and M. G. Kim, EcoMat, 2023, 5, e12419 CrossRef CAS.
- S. Bag and M. G. Kanatzidis, J. Am. Chem. Soc., 2010, 132, 14951–14959 CrossRef CAS PubMed.
- S. Bag, I. U. Arachchige and M. G. Kanatzidis, J. Mater. Chem., 2008, 18, 3628–3632 RSC.
- Z. Hassanzadeh Fard, S. M. Islam and M. G. Kanatzidis, Chem. Mater., 2015, 27, 6189–6192 CrossRef CAS.
- J. Zhao, J. Wang, Z. Chen, J. Ju, X. Han and Y. Deng, APL Mater., 2021, 9, 050902 CrossRef CAS.
- C. H. Hendon, K. T. Butler, A. M. Ganose, Y. Román-Leshkov, D. O. Scanlon, G. A. Ozin and A. Walsh, Chem. Mater., 2017, 29, 3663–3670 CrossRef CAS PubMed.
- H. Mu, G. Lin, Y. Zhang, Y. Xiao and J. Liu, Colloids Surf., A, 2021, 623, 126734 CrossRef CAS.
- K. S. Sing, Pure Appl. Chem., 1985, 57, 603–619 CrossRef CAS.
- S. Polarz and B. Smarsly, J. Nanosci. Nanotechnol., 2002, 2, 581–612 CrossRef CAS PubMed.
- W. Luc and F. Jiao, ACS Catal., 2017, 7, 5856–5861 CrossRef CAS.
- G. Wittstock, M. Bäumer, W. Dononelli, T. Klüner, L. Lührs, C. Mahr, L. V. Moskaleva, M. Oezaslan, T. Risse, A. Rosenauer, A. Staubitz, J. Weissmüller and A. Wittstock, Chem. Rev., 2023, 123, 6716–6792 CrossRef CAS PubMed.
- S. De, J. Zhang, R. Luque and N. Yan, Energy Environ. Sci., 2016, 9, 3314–3347 RSC.
- A. Kumari, S. Kaushal and P. P. Singh, Mater. Today Energy, 2021, 20, 100667 CrossRef CAS.
- Z. Wei, J. Sun, Y. Li, A. K. Datye and Y. Wang, Chem. Soc. Rev., 2012, 41, 7994–8008 RSC.
- J. Zhang and C. M. Li, Chem. Soc. Rev., 2012, 41, 7016–7031 RSC.
- C. Perego and R. Millini, Chem. Soc. Rev., 2013, 42, 3956–3976 RSC.
- G. Singh, J. Lee, A. Karakoti, R. Bahadur, J. Yi, D. Zhao, K. AlBahily and A. Vinu, Chem. Soc. Rev., 2020, 49, 4360–4404 RSC.
- H. Chen, X. Liang, Y. Liu, X. Ai, T. Asefa and X. Zou, Adv. Mater., 2020, 32, 2002435 CrossRef PubMed.
- K. A. Adegoke and N. W. Maxakato, Coord. Chem. Rev., 2022, 457, 214389 CrossRef CAS.
- T. J. Barton, L. M. Bull, W. G. Klemperer, D. A. Loy, B. McEnaney, M. Misono, P. A. Monson, G. Pez, G. W. Scherer and J. C. Vartuli, Chem. Mater., 1999, 11, 2633–2656 CrossRef CAS.
- J. Qi, W. Zhang and R. Cao, ChemCatChem, 2018, 10, 1206–1220 CrossRef CAS.
- L. Kong, M. Zhong, W. Shuang, Y. Xu and X.-H. Bu, Chem. Soc. Rev., 2020, 49, 2378–2407 RSC.
- X.-Y. Yang, L.-H. Chen, Y. Li, J. C. Rooke, C. Sanchez and B.-L. Su, Chem. Soc. Rev., 2017, 46, 481–558 RSC.
- A. H. Lu and F. Schüth, Adv. Mater., 2006, 18, 1793–1805 CrossRef CAS.
- P. Sinha, A. Datar, C. Jeong, X. Deng, Y. G. Chung and L.-C. Lin, J. Phys. Chem. C, 2019, 123, 20195–20209 CrossRef CAS.
- S. Brunauer, P. H. Emmett and E. Teller, J. Am. Chem. Soc., 1938, 60, 309–319 CrossRef CAS.
-
K. S. Sing, Adsorption by Powders and Porous Solids, 2013, vol. 2, pp. 237–268 Search PubMed.
- U. Kuila and M. Prasad, Lead. Edge, 2013, 32, 1478–1485 CrossRef.
-
N. Rameli, K. Jumbri, R. Wahab, A. Ramli and F. Huyop, 2018.
- L. Zhang, L. Jin, B. Liu and J. He, Front. Chem., 2019, 7, 22 CrossRef CAS PubMed.
- A. Eftekhari, Microporous Mesoporous Mater., 2017, 243, 355–369 CrossRef CAS.
- J. Širc, R. Hobzova, N. Kostina, M. Munzarová, M. Juklíčková, M. Lhotka, Š. Kubinová, A. Zajícová and J. Michálek, J. Nanomater., 2012, 2012, 327369 CrossRef.
- F. Yu, H. Zhou, Y. Huang, J. Sun, F. Qin, J. Bao, W. A. Goddard III, S. Chen and Z. Ren, Nat. Commun., 2018, 9, 2551 CrossRef PubMed.
- A. Kumar and S. Bhattacharyya, ACS Appl. Mater. Interfaces, 2017, 9, 41906–41915 CrossRef CAS PubMed.
- S. Chen and S.-Z. Qiao, ACS Nano, 2013, 7, 10190–10196 CrossRef CAS PubMed.
- F. Jamal, A. Rafique, S. Moeen, J. Haider, W. Nabgan, A. Haider, M. Imran, G. Nazir, M. Alhassan and M. Ikram, ACS Appl. Nano Mater., 2023, 6, 7077–7106 CrossRef CAS.
- H. Liang, L. Li, F. Meng, L. Dang, J. Zhuo, A. Forticaux, Z. Wang and S. Jin, Chem. Mater., 2015, 27, 5702–5711 CrossRef CAS.
- Y. Hou, M. Qiu, T. Zhang, X. Zhuang, C. S. Kim, C. Yuan and X. Feng, Adv. Mater., 2017, 29, 1701589 CrossRef PubMed.
- S. Roy, A. Joseph, X. Zhang, S. Bhattacharyya, A. B. Puthirath, A. Biswas, C. S. Tiwary, R. Vajtai and P. M. Ajayan, Chem. Rev., 2024, 124, 9376–9456 CrossRef CAS PubMed.
- Y. Liu, P. Vijayakumar, Q. Liu, T. Sakthivel, F. Chen and Z. Dai, Nano-Micro Lett., 2022, 14, 43 CrossRef CAS PubMed.
- J. Yin, J. Jin, H. Lin, Z. Yin, J. Li, M. Lu, L. Guo, P. Xi, Y. Tang and C.-H. Yan, Adv. Sci., 2020, 7, 1903070 CrossRef CAS PubMed.
- Y. Zhang, Q. Zhou, J. Zhu, Q. Yan, S. X. Dou and W. Sun, Adv. Funct. Mater., 2017, 27, 1702317 CrossRef.
- K. Mensah-Darkwa, D. Nframah Ampong, E. Agyekum, F. M. de Souza and R. K. Gupta, Energies, 2022, 15, 4052 CrossRef CAS.
- L. Yu, J. F. Yang and X. W. Lou, Angew. Chem., 2016, 128, 13620–13624 CrossRef.
- B. Y. Guan, L. Yu, X. Wang, S. Song and X. W. Lou, Adv. Mater., 2016, 29, 1605051 CrossRef PubMed.
- W. Wang, L. Kuai, W. Cao, M. Huttula, S. Ollikkala, T. Ahopelto, A. P. Honkanen, S. Huotari, M. Yu and B. Geng, Angew. Chem., 2017, 129, 15173–15177 CrossRef.
- J. Zhu, L. Hu, P. Zhao, L. Y. S. Lee and K.-Y. Wong, Chem. Rev., 2019, 120, 851–918 CrossRef PubMed.
- Y. Yao, Z. Zhang and L. Jiao, Energy Environ. Mater., 2022, 5, 470–485 CrossRef CAS.
- F. Lyu, Q. Wang, S. M. Choi and Y. Yin, Small, 2019, 15, 1804201 CrossRef PubMed.
- Y. H. Budnikova, Dalton Trans., 2020, 49, 12483–12502 RSC.
- J. Tafel, Z. Phys. Chem., Stoechiom. Verwandtschaftsl., 1905, 50, 641–712 CrossRef CAS.
- X.-P. Li, C. Huang, W.-K. Han, T. Ouyang and Z.-Q. Liu, Chin. Chem. Lett., 2021, 32, 2597–2616 CrossRef CAS.
- X. Zou and Y. Zhang, Chem. Soc. Rev., 2015, 44, 5148–5180 RSC.
- A. Yadav, Y. Hunge and S.-W. Kang, Surf. Interfaces, 2021, 23, 101020 CrossRef CAS.
- H. Su, J. Jiang, S. Song, B. An, N. Li, Y. Gao and L. Ge, Chin. J. Catal., 2023, 44, 7–49 CrossRef CAS.
- G. Liu, C. Shuai, Z. Mo, R. Guo, N. Liu, X. Niu, Q. Dong, J. Wang, Q. Gao and Y. Chen, New J. Chem., 2020, 44, 17313–17322 RSC.
- Y. Guo, J. Tang, Z. Wang, Y.-M. Kang, Y. Bando and Y. Yamauchi, Nano Energy, 2018, 47, 494–502 CrossRef CAS.
- Y. Guo, T. Park, J. W. Yi, J. Henzie, J. Kim, Z. Wang, B. Jiang, Y. Bando, Y. Sugahara and J. Tang, Adv. Mater., 2019, 31, 1807134 CrossRef PubMed.
- W. Li, J. Liu and D. Zhao, Nat. Rev. Mater., 2016, 1, 1–17 Search PubMed.
- A. Fischereder, M. L. Martinez-Ricci, A. Wolosiuk, W. Haas, F. Hofer, G. Trimmel and G. J. Soler-Illia, Chem. Mater., 2012, 24, 1837–1845 CrossRef CAS.
- B. T. Yonemoto, G. S. Hutchings and F. Jiao, J. Am. Chem. Soc., 2014, 136, 8895–8898 CrossRef CAS PubMed.
- Y. Shi, Y. Wan, R. Liu, B. Tu and D. Zhao, J. Am. Chem. Soc., 2007, 129, 9522–9531 CrossRef CAS PubMed.
- C. R. Lubeck, T. J. Han, A. E. Gash, J. H. Satcher Jr and F. M. Doyle, Adv. Mater., 2006, 18, 781–784 CrossRef CAS.
- P. N. Trikalitis, K. K. Rangan, T. Bakas and M. G. Kanatzidis, Nature, 2001, 410, 671–675 CrossRef CAS PubMed.
- P. N. Trikalitis, K. K. Rangan and M. G. Kanatzidis, J. Am. Chem. Soc., 2002, 124, 2604–2613 CrossRef CAS PubMed.
- J. L. Mohanan, I. U. Arachchige and S. L. Brock, Science, 2005, 307, 397–400 CrossRef CAS PubMed.
- F. Gao, Q. Lu and D. Zhao, Adv. Mater., 2003, 15, 739–742 CrossRef CAS.
- Y. Wang, Y. Wu, A. Shirazi-Amin, P. Kerns, J. Fee, J. He, L. Jin, R. Maric and S. L. Suib, ACS Appl. Energy Mater., 2019, 2, 2370–2374 CrossRef CAS.
- Q. Zhang, C. Ye, X. L. Li, Y. H. Deng, B. X. Tao, W. Xiao, L. J. Li, N. B. Li and H. Q. Luo, ACS Appl. Mater. Interfaces, 2018, 10, 27723–27733 CrossRef CAS PubMed.
- X. Ma, W. Zhang, Y. Deng, C. Zhong, W. Hu and X. Han, Nanoscale, 2018, 10, 4816–4824 RSC.
- Z. Wang, J. Li, X. Tian, X. Wang, Y. Yu, K. A. Owusu, L. He and L. Mai, ACS Appl. Mater. Interfaces, 2016, 8, 19386–19392 CrossRef CAS PubMed.
- S. Wan, W. Jin, X. Guo, J. Mao, L. Zheng, J. Zhao, J. Zhang, H. Liu and C. Tang, ACS Sustain. Chem. Eng., 2018, 6, 15374–15382 CrossRef CAS.
- Z. Chen, M. Chen, X. Yan, H. Jia, B. Fei, Y. Ha, H. Qing, H. Yang, M. Liu and R. Wu, ACS Nano, 2020, 14, 6968–6979 CrossRef CAS PubMed.
- J. Ding, S. Ji, H. Wang, H. Gai, F. Liu, V. Linkov and R. Wang, Int. J. Hydrogen Energy, 2019, 44, 2832–2840 CrossRef CAS.
- H. Bian, T. Chen, Z. Chen, J. Liu, Z. Li, P. Du, B. Zhou, X. Zeng, J. Tang and C. Liu, Electrochim. Acta, 2021, 389, 138786 CrossRef CAS.
- Y. Guo, J. Tang, J. Henzie, B. Jiang, W. Xia, T. Chen, Y. Bando, Y.-M. Kang, M. S. A. Hossain, Y. Sugahara and Y. Yamauchi, ACS Nano, 2020, 14, 4141–4152 CrossRef CAS PubMed.
- H. Hosseini and M. Roushani, Chem. Eng. J., 2020, 402, 126174 CrossRef CAS.
- J. Balamurugan, T. T. Nguyen, D. H. Kim, N. H. Kim and J. H. Lee, Appl. Catal., B, 2021, 286, 119909 CrossRef CAS.
- Z.-t. Shang, T.-m. Li, B.-q. Hu, M. Liu, W.-t. Lu, F. Yu and Y. Zheng, Front. Energy, 2024, 18, 378–389 CrossRef CAS.
- G. Fang, Q. Wang, J. Zhou, Y. Lei, Z. Chen, Z. Wang, A. Pan and S. Liang, ACS Nano, 2019, 13, 5635–5645 CrossRef CAS PubMed.
- S. Prabhakaran, J. Balamurugan, N. H. Kim and J. H. Lee, Small, 2020, 16, 2000797 CrossRef CAS PubMed.
- K. Srinivas, F. Ma, Y. Liu, Z. Zhang, Y. Wu and Y. Chen, ACS Appl. Mater. Interfaces, 2022, 14, 52927–52939 CrossRef CAS PubMed.
- K. Chandra Majhi, P. Karfa and R. Madhuri, Electrochim. Acta, 2019, 318, 901–912 CrossRef CAS.
- L. Nisar, M. Sadaqat, A. Hassan, N.-U.-A. Babar, A. Shah, M. Najam-Ul-Haq, M. N. Ashiq, M. F. Ehsan and K. S. Joya, Fuel, 2020, 280, 118666 CrossRef CAS.
- U. N. Pan, D. R. Paudel, A. Kumar Das, T. I. Singh, N. H. Kim and J. H. Lee, Appl. Catal., B, 2022, 301, 120780 CrossRef CAS.
- Y. R. Rosyara, A. Muthurasu, K. Chhetri, I. Pathak, T. H. Ko, P. C. Lohani, D. Acharya, T. Kim, D. Lee and H. Y. Kim, ACS Appl. Mater. Interfaces, 2024, 16, 10238–10250 CrossRef CAS PubMed.
- I. Pathak, A. Muthurasu, D. Acharya, K. Chhetri, B. Dahal, Y. R. Rosyara, T. Kim, T. H. Ko and H. Y. Kim, J. Mater. Chem. A, 2024, 12, 17544–17556 RSC.
- K. M. Katubi, M. U. Nisa, S. Manzoor, Z. Ahmad, A. G. Abid, M. Abdullah, M. S. Al-Buriahi and M. N. Ashiq, Appl. Phys. A:Mater. Sci. Process., 2022, 128, 882 CrossRef CAS.
- Q. Gao, C. Q. Huang, Y. M. Ju, M. R. Gao, J. W. Liu, D. An, C. H. Cui, Y. R. Zheng, W. X. Li and S. H. Yu, Angew. Chem., Int. Ed., 2017, 56, 7769–7773 CrossRef CAS PubMed.
- J. Masud, P. C. Ioannou, N. Levesanos, P. Kyritsis and M. Nath, ChemSusChem, 2016, 9, 3128–3132 CrossRef CAS PubMed.
- F. A. Rasmussen and K. S. Thygesen, J. Phys. Chem. C, 2015, 119, 13169–13183 CrossRef CAS.
- Z. Xue, X. Li, Q. Liu, M. Cai, K. Liu, M. Liu, Z. Ke, X. Liu and G. Li, Adv. Mater., 2019, 31, 1900430 CrossRef PubMed.
- J. Xu, Y. Yin, H. Xiong, X. Du, Y. Jiang, W. Guo, Z. Wang, Z. Xie, D. Qu and H. Tang, Appl. Surf. Sci., 2019, 490, 516–521 CrossRef CAS.
- F. M. Sapountzi, J. M. Gracia, C. J. Weststrate, H. O. A. Fredriksson and J. W. Niemantsverdriet, Prog. Energy Combust. Sci., 2017, 58, 1–35 CrossRef.
- S. Wang, A. Lu and C.-J. Zhong, Nano Convergence, 2021, 8, 4 CrossRef CAS PubMed.
- P. J. Megía, A. J. Vizcaíno, J. A. Calles and A. Carrero, Energy Fuels, 2021, 35, 16403–16415 CrossRef.
- B. You and Y. Sun, Acc. Chem. Res., 2018, 51, 1571–1580 CrossRef CAS PubMed.
- S. Anwar, F. Khan, Y. Zhang and A. Djire, Int. J. Hydrogen Energy, 2021, 46, 32284–32317 CrossRef CAS.
- K. Mazloomi and C. Gomes, Renewable Sustainable Energy Rev., 2012, 16, 3024–3033 CrossRef CAS.
- Y. Wu, B. Xiao, K. Liu, S. Wang, Y. Hou, X. F. Lu and J. Zhang, Electrochem. Energy Rev., 2025, 8, 2 CrossRef CAS.
- Y. Hua, H. Jiang, H. Jiang, H. Zhang and C. Li, Electrochim. Acta, 2018, 278, 219–225 CrossRef CAS.
- K. Pan, Y. Zhai, J. Zhang and K. Yu, Materials, 2019, 12, 3364 CrossRef CAS PubMed.
- L. Tong, C. Song, Y. Liu, R. Xing, K. Sekar and S. Liu, Int. J. Hydrogen Energy, 2022, 47, 14404–14413 CrossRef CAS.
- L. Zhang, J. Rong, Y. Lin, Y. Yang, H. Zhu, X. Yu, X. Kang, C. Chen, H. M. Cheng and G. Liu, Adv. Funct. Mater., 2023, 33, 2307947 CrossRef CAS.
- B. Chen, P. Hu, F. Yang, X. Hua, F. F. Yang, F. Zhu, R. Sun, K. Hao, K. Wang and Z. Yin, Small, 2023, 19, 2207177 CrossRef CAS PubMed.
- A. Wang, K. Hu, Y. Liu, R. Li, C. Ye, Z. Yi and K. Yan, Int. J. Hydrogen Energy, 2019, 44, 6573–6581 CrossRef CAS.
- X. Wang, X. Huang, W. Gao, Y. Tang, P. Jiang, K. Lan, R. Yang, B. Wang and R. Li, J. Mater. Chem. A, 2018, 6, 3684–3691 RSC.
- L. Nisar, M. Sadaqat, A. Hassan, A. Shah, M. Najam-Ul-Haq, M. N. Ashiq, M. F. Ehsan and K. S. Joya, Fuel, 2020, 280, 118666 CrossRef CAS.
- F. Wang, Y. Li, T. A. Shifa, K. Liu, F. Wang, Z. Wang, P. Xu, Q. Wang and J. He, Angew. Chem., Int. Ed., 2016, 55, 6919–6924 CrossRef CAS PubMed.
- L. Pan, Z. Huijuan, L. Li, Z. Yan, D. Ju, X. Chaohe, H. Ning and W. Yu, ACS Appl. Mater. Interfaces, 2017, 9, 2500–2508 CrossRef PubMed.
- J.-T. Ren and Z.-Y. Yuan, ACS Sustain. Chem. Eng., 2017, 5, 7203–7210 CrossRef CAS.
- S. P. Lonkar, V. V. Pillai and S. M. Alhassan, Mater. Adv., 2020, 1, 794–803 RSC.
- Y. Yang, M. Yuan, H. Li, G. Sun and S. Ma, Electrochim. Acta, 2018, 281, 198–207 CrossRef CAS.
- X. Luo, Q. Zhou, S. Du, J. Li, J. Zhong, X. Deng and Y. Liu, ACS Appl. Mater. Interfaces, 2018, 10, 22291–22302 CrossRef CAS PubMed.
- Y. Li, X. Fu, W. Zhu, J. Gong, J. Sun, D. Zhang and J. Wang, Inorg. Chem. Front., 2019, 6, 2090–2095 RSC.
- P. Cai, J. Huang, J. Chen and Z. Wen, Angew. Chem., 2017, 129, 4936–4939 CrossRef.
- L. Lei, D. Huang, C. Zhang, R. Deng, S. Chen and Z. Li, J. Catal., 2020, 385, 129–139 CrossRef CAS.
- G. Zhao, K. Rui, S. X. Dou and W. Sun, Adv. Funct. Mater., 2018, 28, 1803291 CrossRef.
- X. Luo, P. Ji, P. Wang, R. Cheng, D. Chen, C. Lin, J. Zhang, J. He, Z. Shi, N. Li, S. Xiao and S. Mu, Adv. Energy Mater., 2020, 10, 1903891 CrossRef CAS.
- Y. Li, W. Wang, B. Huang, Z. Mao, R. Wang, B. He, Y. Gong and H. Wang, J. Energy Chem., 2021, 57, 99–108 CrossRef CAS.
- X. F. Lu, S. L. Zhang, W. L. Sim, S. Gao and X. W. Lou, Angew. Chem., 2021, 133, 23067–23073 CrossRef.
- X. Hu, P. Tan, R. Dong, M. Jiang, L. Lu, Y. Wang, H. Liu, Y. Liu, J. Xie and J. Pan, Energy Technol., 2021, 9, 2000961 CrossRef CAS.
- S. Poorahong, D. J. Harding, S. Keawmorakot and M. Siaj, J. Electroanal. Chem., 2021, 897, 115568 CrossRef CAS.
- Y. Yang, Q. Zhou, J. Yang, D. Qian, Y. Xiong, Z. Li and Z. Hu, Int. J. Hydrogen Energy, 2022, 47, 33728–33740 CrossRef CAS.
- B. Zhao, H. Luo, J. Liu, S. Chen, H. Xu, Y. Liao, X. F. Lu, Y. Qing and Y. Wu, Chin. Chem. Lett., 2025, 36, 109919 CrossRef CAS.
- Z. Wang, S. Liu, W. Duan, Y. Xing, Y. Hu and Y. Ma, Int. J. Hydrogen Energy, 2024, 60, 1414–1432 CrossRef CAS.
- X. Xia, L. Wang, N. Sui, V. L. Colvin and W. W. Yu, Nanoscale, 2020, 12, 12249–12262 RSC.
- M. Mushtaq, M. Koroma, S. Jiang, S. Mathi, M. Tu, Z. Khanam, Y.-W. Hu, J. Deng and M.-S. Balogun, J. Mater. Chem. A, 2025, 13, 5933–5944 RSC.
- K. Jiang, B. Liu, M. Luo, S. Ning, M. Peng, Y. Zhao, Y.-R. Lu, T.-S. Chan, F. M. de Groot and Y. Tan, Nat. Commun., 2019, 10, 1743 CrossRef PubMed.
- K. Xiao, L. Zhou, M. Shao and M. Wei, J. Mater. Chem. A, 2018, 6, 7585–7591 RSC.
- B. Liu, Y. F. Zhao, H. Q. Peng, Z. Y. Zhang, C. K. Sit, M. F. Yuen, T. R. Zhang, C. S. Lee and W. J. Zhang, Adv. Mater., 2017, 29, 1606521 CrossRef PubMed.
- X. Wang, Y. Zheng, J. Yuan, J. Shen, J. Hu, A.-j. Wang, L. Wu and L. Niu, Electrochim. Acta, 2017, 225, 503–513 CrossRef CAS.
- Y. Zhang, J. Fu, H. Zhao, R. Jiang, F. Tian and R. Zhang, Appl. Catal., B, 2019, 257, 117899 CrossRef CAS.
- J. Yu, G. Cheng and W. Luo, J. Mater. Chem. A, 2017, 5, 15838–15844 RSC.
- Z. Zhang, S. Li, X. Bu, Y. Dai, J. Wang, X. Bao and T. Wang, New J. Chem., 2021, 45, 17313–17319 RSC.
- P. Chen, T. Zhou, M. Zhang, Y. Tong, C. Zhong, N. Zhang, L. Zhang, C. Wu and Y. Xie, Adv. Mater., 2017, 29, 1701584 CrossRef PubMed.
- B. Ranjith, L. Gnanasekaran, P. C. Karthika, J. R. Rajabathar, H. A. Al-Lohedan, W. K. Kim, V. R. M. Reddy, M. Kapoor, S. Singh, M. Lavanyaj and G. Devendrapandi, Int. J. Hydrogen Energy, 2025, 112, 255–265 CrossRef.
- S. Shah, K. Jabbour, M. Abdullah, A. T. Alfagham, A. M. Elgorban, M. F. Ehsan and M. U. Nisa, J. Korean Ceram. Soc., 2025, 52, 1–10 Search PubMed.
- Y. Zhang, T. Yu, J. Zhou, D. Li, M. Feng, Z. Zhang, Q. Yao and Y. Zhou, Korean J. Chem. Eng., 2025, 42, 857–866 CrossRef CAS.
- C. Shi, J. Zhou, M. A. Boda, K. Zhao, Z. Yang, D. Yuan and Z. Yi, J. Mater. Chem. A, 2025, 13, 4538–4549 RSC.
- M. M. Meshesha, J. Gautam, D. Chanda, S. G. Jang and B. L. Yang, J. Colloid Interface Sci., 2023, 652, 272–284 CrossRef PubMed.
- X. Cao, J. E. Medvedeva and M. Nath, ACS Appl. Energy Mater., 2020, 3, 3092–3103 CrossRef CAS.
- F. Jing, Q. Lv, Q. Wang, K. Chi, Z. Xu, X. Wang and S. Wang, Electrochim. Acta, 2019, 304, 202–209 CrossRef CAS.
- S.-H. Chae, A. Muthurasu, T. Kim, J. S. Kim, M.-S. Khil, M. Lee, H. Kim, J. Y. Lee and H. Y. Kim, Appl. Catal., B, 2021, 293, 120209 CrossRef CAS.
- H. Zhou, D. Kong, N. Chu, H. Wang, J. Xu, Y. Wang and T. Xu, J. Colloid Interface Sci., 2025, 678, 968–976 CrossRef CAS PubMed.
- U. N. Pan, D. R. Paudel, A. K. Das, T. I. Singh, N. H. Kim and J. H. Lee, Appl. Catal., B, 2022, 301, 120780 CrossRef CAS.
- F. Zhang, T.-y. Eom, M. Cho, H.-J. Lee and H. Pang, J. Energy Storage, 2021, 42, 103098 CrossRef.
- B. He, X. C. Wang, L. X. Xia, Y. Q. Guo, Y. W. Tang, Y. Zhao, Q. L. Hao, T. Yu, H. K. Liu and Z. Su, ChemSusChem, 2020, 13, 5239–5247 CrossRef CAS PubMed.
- X. Wang, X. Huang, W. Gao, Y. Tang, P. Jiang, K. Lan, R. Yang, B. Wang and R. Li, J. Mater. Chem. A, 2018, 6, 3684–3691 RSC.
- K. S. Bhat, H. C. Barshilia and H. Nagaraja, Int. J. Hydrogen Energy, 2017, 42, 24645–24655 CrossRef CAS.
- M. Sadaqat, L. Nisar, F. Hussain, M. N. Ashiq, A. Shah, M. F. Ehsan, M. Najam-Ul-Haq and K. S. Joya, J. Mater. Chem. A, 2019, 7, 26410–26420 RSC.
- M. Nath, U. De Silva, H. Singh, M. Perkins, W. P. Liyanage, S. Umapathi, S. Chakravarty and J. Masud, ACS Appl. Energy Mater., 2021, 4, 8158–8174 CrossRef CAS.
- Y. Xu and M. A. Schoonen, Am. Mineral., 2000, 85, 543–556 CrossRef CAS.
- N. Bano, S. Manzoor, A. Sami, S. I. A. Shah, A. Junaid, M. Y. U. Rehman, R. A. Alshgari, M. F. Ehsan and M. N. Ashiq, J. Am. Ceram. Soc., 2024, 107, 4027–4041 CrossRef CAS.
- M. Singh, T. T. Nguyen, J. Balamurugan, N. H. Kim and J. H. Lee, Chem. Eng. J., 2022, 430, 132888 CrossRef CAS.
- Y. Guo, J. Tang, J. Henzie, B. Jiang, W. Xia, T. Chen, Y. Bando, Y.-M. Kang, M. S. A. Hossain and Y. Sugahara, ACS Nano, 2020, 14, 4141–4152 CrossRef CAS PubMed.
- J. Ding, P. Wang, S. Ji, H. Wang, D. J. Brett and R. Wang, Electrochim. Acta, 2019, 300, 93–101 CrossRef CAS.
|
This journal is © The Royal Society of Chemistry 2025 |
Click here to see how this site uses Cookies. View our privacy policy here.