DOI:
10.1039/D5TC00259A
(Paper)
J. Mater. Chem. C, 2025, Advance Article
Plant-derived cellulose nanocrystals as a pre-alignment layer for ferroelectric mesogens in display applications†
Received
20th January 2025
, Accepted 6th June 2025
First published on 9th June 2025
Abstract
The alignment of mesogens is a critical determinant of the efficacy of liquid crystal display (LCD) devices. Conventional LCDs utilize the rubbed polyimide technique for mesogenic alignment on substrates, which is prone to static charges and impurities that can degrade device performance. Herein, we introduce an innovative bio-based environmentally benign pre-alignment layer for LCDs by employing cellulose nanocrystals (CNCs) derived from plant sources for the first time. Leveraging the self-assembling properties of CNCs, thin films were fabricated on indium tin oxide (ITO) coated glass substrates using the evaporation-induced vertical deposition technique. The surface morphology of the prepared CNC layer was characterized using scanning electron microscopy (SEM), atomic force microscopy (AFM), and profilometry. In addition, a systematic comparison of the surface energies of the developed CNC pre-alignment layer against other surfaces such as bare ITO-glass, nylon-coated ITO-glass, and a rubbed polyimide surface on ITO-glass was conducted. Furthermore, the alignment of a ferroelectric mesogen (ZLI3654) was evaluated using the LC cells fabricated using the CNC pre-alignment layer and compared with the conventional devices. It is seen that the augmented surface energy of the self-assembled CNC layer on ITO coated glass enhances adhesive properties, leading to a robust mesogenic alignment. The quality of mesogenic alignment over CNC layers and the resultant device performance are intricately tied to the concentration of the CNC coating. Comparative analysis with conventional display devices reveals that the CNC-aligned device exhibits electro-optical performance on par with its traditional counterpart, all while maintaining optical transparency. This investigation delves into the fundamental aspects of mesogenic alignment over CNC layers, offering insights for developing advanced LCD devices through a rubbing-free, environmentally benign, and facile alignment technique.
Introduction
Liquid crystals (LCs) are widely acknowledged as versatile functional materials with applications spanning electro-optic devices, display and non-display technologies, information systems, energy solutions, separation processes, and healthcare innovations.1–14 Among the LC family, ferroelectric liquid crystals (FLCs), a subclass of chiral smectic phases with tilted structures, exhibit spontaneous polarization due to their low symmetry and chirality. Known for their fast response, low threshold voltage, and memory effect, FLCs have attracted considerable interest for both fundamental studies and display and non-display applications.15–17 These materials exhibit substantial birefringence and manifest heightened responsiveness to external stimuli such as temperature, electric field, and magnetic field, rendering them particularly apt for integration into display devices. In display applications, the surface alignment of LCs assumes paramount significance. The orientation of mesogens across the solid surface is governed by the interplay of surface interactions and the geometric characteristics of the sample cell. Various methods can be employed to establish the desired alignment layers for LC molecules. However, the technique of mechanically rubbed polyimide stands out as the predominant approach, finding widespread utilization for aligning mesogens in the context of flat-panel displays.18–20 This technique involves slender polymer layer deposition onto the substrate, subsequently undergoing a rubbing process facilitated by a velvet cloth. During this rubbing procedure, the polyimide molecules experience stress, inducing anisotropic orientation of the layer atop the substrate. Additionally, the chosen rubbing direction imparts in-plane anisotropy to the system. The anisotropic molecular forces operative between the rubbed polyimide surface and the LCs contribute significantly to the surface alignment of the latter. However, it is noteworthy that the rubbing process engenders the generation of dust particles and the accumulation of static electricity, both of which exert consequential effects throughout the manufacturing processes of LCDs. Consequently, the scientific community has evinced interest in alternatives that obviate the need for rubbing in mesogen alignment. Various novel techniques have been reported in pursuit of this objective. Some of the well-recognized techniques are the use of UV-light-induced alignment layers for UV-curable polymers, Langmuir–Blodgett layers, and photo-aligned layers, polarized light alignment, pulse laser ablation, and flow-induced molecular orientation of liquid crystalline polymers.7,21–29 Moreover, the presence of ionic impurities is a major obstacle limiting the performance of LC devices. The ions in the host matrix govern electrical conductivity in LC devices.30 Different physical phenomena associated with the ions and electrical conductivity are comprehensively studied.31–39 These ions can emanate through different sources, such as ionic dissociation of residual impurities, ionic contamination during the synthesis of LCs, the manufacturing process of the device, chemical decomposition, and self-dissociation of LCs due to aging.39–41 The presence of these ions adversely affects the performance of LC devices, such as image sticking, image flickering, and slow response, thereby questioning the applicability of LC devices. The research community has devised different ways to remove these ionic impurities from the LC matrix. The ionic contamination during the synthesis of LCs can be removed by employing advanced methods such as recrystallization, vacuum sublimation, zone refining, and chromatography.42,43 Nowadays, ion-capturing agents such as porous particles, oxide nanoparticles, and metal–organic frameworks are suggested to trap the ions in the LC medium. For now, layers, nanoparticles, and microparticles are the popular ion-trapping agents used in LC devices.44–48 Usually, the optical transmittance of the layers is compromised when the alignment layers are used as ion-trapping agents. Hence, highly transparent pre-alignment layers that are rubbing-free with excellent ion absorption properties are well appreciated.
A great deal of work has been carried out to obtain alignment layers based on the rubbed polyimide technique, and plenty of mechanisms were put forward to explain them. Rubbing generates microgrooves or scratches on the polymer surface, resulting in long-range elastic effects on the surface.18,49 Some other studies suggested that the aligned polymer chains, as a result of rubbing, serve as a template for LC alignment.50–53 However, rubbing can produce alignment of polyimide molecules very close to the layer surface, nearly 10 nm from the outer layer.54 Moreover, molecular dynamics simulation of the interface between rubbed polyimide and LCs successfully gives surface alignment of LCs over the rubbed surface.55 Investigations were carried out to study the alignment of mesogens over Langmuir Blodgett (LB) layers. Polyimide materials were the conventional choice for preparing LB layers due to their adaptability in practical applications. Nevertheless, a novel and simplest approach was reported to develop LB layers for LC alignment using polymeric acid and poly-diisopropyl fumarate (PDiPF).21,22 Linearly polarized UV light initiates anisotropic photoreactions in side-chain LC polymers. These photo-crosslinked layers are used to align low molecular-weight LCs.56 Using nanoimprint lithography and UV-curing methods, a hybrid layer is developed with gallium oxide (GaO) and a UV-curing polymer for the alignment of mesogens. The refractive index anisotropy and van der Waals forces within the hybrid layer enable uniform and homogeneous alignment of LC molecules.26 A similar approach is exploited to produce 1-D nanostructures on a thin layer using a hybrid mixture of tin oxide and a UV-curable polymer. A uniform and homogeneous alignment of mesogens is produced due to anisotropic characteristics and geometric restrictions of the fabricated nanostructures over the layer.57 A rubbing-free alignment layer is developed using a UV pulsed laser ablation technique, and planar alignment of mesogens was accomplished. The dipolar interactions and van der Waals forces among LC molecules and the substrates are responsible for the alignment.58 The flow-induced molecular orientation of liquid crystalline polymers (LCP) can give alignment layers without rubbing, where the anisotropic structure of molecular orientation is exploited. A monolayer graphene film deposited on a glass substrate is utilized as a substitute for traditional ITO and polymer films. This graphene film, employed in the fabrication of the LC cell, demonstrates remarkable optical transmittance (∼95%) across the 450–800 nm wavelength range, along with an electrical sheet resistance of 328.77 Ω per square. The alignment of FLC mesogens on the graphene monolayer is facilitated by π–π electron interactions between the benzene rings of the FLC molecules and the honeycomb lattice structure of graphene.59 The surface alignment of LC molecules over the layers coated with hydroxypropyl cellulose (HPC) is widely investigated. The concentration of HCP, coating speed, and coating thickness play a vital role in forming anisotropic molecular orientations at the surface of the layers.29
Among the various pre-alignment techniques, the rubbed polyimide approach is still used to fabricate custom LC devices for both display and non-display applications, as well as for basic research.60,61 However, most of the polymers used as pre-alignment layers are petroleum-derivatives such as nylon 6,6 and are hazardous to the environment causing pollution. In this context, the search for a natural and biodegradable alternative as an alignment layer material is highly desirable. Plant-derived cellulose nanocrystals (CNC) show spindle-like morphology, which is expected to give homogeneous alignment to the mesogens via self-assembly.62,63 Apart from renewability, biocompatibility, and biodegradability, the physical properties of CNCs, such as high specific surface area, liquid crystalline behavior, and optical transparency, are well understood.64 Such an eco-friendly material as an alignment layer is expected to resolve two major drawbacks of the conventional polyimide alignment technique. Firstly, the CNCs show high optical transmittance and self-assembly behavior, which can provide alignment layers upon coating without additional rubbing. Hence, it removes the chances of dust and static charges, adversely affecting LC device performance. Secondly, it is an environmentally friendly material that hardly generates any chemical waste and is easy to handle. Additionally, the conventional rubbed-polyimide methods entail spin coating the polymer solution, thermally curing the film, and then rubbing the substrate to create microgrooves using a velvet cloth. On the other hand, vertical deposition is an evaporation induced fabrication method, which is utilized for preparing periodically ordered structures of colloids, especially for photonic crystals.65 This deposition technique not only assembles the colloidal particles in a periodic manner but also generates micro-sized domains due to the capillary forces and convex flow.65,66 The self-assembled CNC on an ITO substrate can be effectively utilized as a pre-alignment layer for the LC mesogens for advanced device applications. In this context, we have chosen CNCs as the pre-alignment layer by using the vertical deposition approach and the promising qualities of CNC layers are anticipated to address the current issues. Moreover, the high colloidal stability of the aqueous solution of CNCs is perfect for vertical deposition without any sedimentation. To the best of our knowledge, this technique has never been applied to provide a pre-alignment layer for the mesogens using CNCs.
In this study, ultra-fine CNCs were extracted from banana pseudo-stem fibers via acid hydrolysis. Subsequent to the extraction, pre-alignment layers in the form of thin films were prepared on ITO coated glass substrates utilizing the evaporation induced vertical deposition technique. The surface morphology of these pre-alignment layers was meticulously examined using diverse techniques, including SEM, polarized optical microscopy (POM), AFM, and profilometry. The surface energy of the CNC coating on ITO was quantitatively assessed through a two-liquid method, and comparative analyses were performed with respect to the bare ITO surface and surfaces coated with nylon and rubbed polyimide. The FLC material ZLI3654 was introduced into the fabricated cells, and the alignment of mesogens was examined using polarizing optical microscopy. The investigation extended to assessing the impact of distinct pre-alignment layers on electro-optical properties, transmittance, and molecular relaxation. An exhaustive analysis of electrical conductivity and optical transmittance was conducted. The device performance was systematically evaluated at varying concentrations of the CNC solution (which lead to the different thicknesses of the CNC layer on ITO) to ascertain the optimum value. Comparative analyses were performed with devices lacking alignment layers and those fabricated using the conventional rubbed polyimide technique.
Results and discussion
Characterization of cellulose nanocrystals (CNCs)
Cellulose nanocrystals (CNCs) were extracted from banana pseudo-stem fibers by mercerization and bleaching followed by acid hydrolysis using 64% H2SO4. The CNC colloid formed was found to be highly stable as revealed by the zeta potential value −49.3 mV and longer shelf life. CNCs are prepared by hydrolyzing cellulosic materials in H2SO4, a process that introduces sulphate groups onto their surface. These negatively charged sulphate groups generate electrostatic repulsion between CNC particles, resulting in stable aqueous suspensions. Structural and chemical characteristics of CNCs were analyzed by WAXS and FTIR, and the results were compared with that of the holocellulose from banana fiber, respectively (Fig. S1, ESI†). Fig. S1a (ESI†) shows the diffraction pattern corresponding to cellulose II, which has resulted from the pretreatment of holocellulose (cellulose I). After the CNC formation, the peak corresponding to the (110) plane is augmented to a higher extent due to the increase in the crystallinity, which is the characteristic property of the CNC formed by acid hydrolysis. Reagents like strong acids rupture the hydrogen bonds between fibrils and highly disordered amorphous regions caused by the penetration of the hydronium (H3O+) ions, followed by hydrolytic cleavage. However, the highly ordered crystalline region remained intact and resulted in crystals with a low aspect ratio. The estimated CrI value for holocellulose from banana fiber is about 59% and for CNCs it is 80.9% respectively, which confirms the phase purity of CNCs from holocellulose and is comparable with the reported values.67–69 The corresponding FTIR spectra were recorded and are shown in Fig. S1b (ESI†), which displays the characteristic peaks of cellulose functionalities. In the FTIR spectra of holocellulose, the peaks at 1242, 1500 and 1700 cm−1 corresponding to the lignin and hemicellulose were not observed. This confirms the removal of lignin and hemicellulose contents by the pretreatment and bleaching processes. Fig. S2 (ESI†) depicts the thermal stability of CNCs from room temperature to 700 °C. Initial small weight loss (5–7%) from room temperature to 150 °C represents the absorbed water loss generally visible in the TGA curves of nanocellulose.70 Second major weight loss started at 200 °C, attributed to the degradation of cellulose, which originated from glycosidic bond breakage and depolymerisation of cellulose followed by the last carbonisation process.71,72 Based on the TGA results of CNCs, it is confirmed that CNCs are thermally stable up to a temperature 200 °C. Even though the FLC display devices generally operate at room temperature, CNC pre-alignment layers provide favourable thermal stability for their operation.
Additionally, the piezoelectric response of the CNC film was confirmed through both domain switching observed via PFM and the output performance of a piezoelectric nanogenerator (PENG) fabricated using CNC films.73,74 For the PFM analysis, a DC voltage of −3 V was applied to an 8 × 8 μm2 area of the CNC film coated on ITO-glass substrates. The resulting amplitude and phase responses are shown in Fig. S3a and c (ESI†), respectively. The appearance of several white islands in these images indicates domain contrast arising from the weak piezoelectric response of the material. Upon applying a +3 V DC voltage to the same region, the white areas transitioned to black, signifying a reversal in domain orientation represented in Fig. S3b and d (ESI†) respectively in amplitude and phase diagrams. The absence of a P–E hysteresis loop further confirms that the observed domain switching originates from piezoelectric rather than ferroelectric behaviour. To further validate the piezoelectric performance, a PENG device was fabricated using the CNC film. The open-circuit voltage and short-circuit current outputs under different applied forces are presented in Fig. S4 (ESI†). The device generated a peak-to-peak open-circuit voltage of 300 mV, as shown in Fig. S4a (ESI†), and a short-circuit current of 40 nA under an applied force of 20 N, as illustrated in Fig. S4b (ESI†). The relatively low open-circuit voltage and short-circuit current outputs further reflect the limited piezoelectric performance of the CNC film, consistent with the weak domain contrast observed in PFM analysis.
Self-assembly of CNCs – a rubbing-free pre-alignment method
Fig. 1 depicts the synthesis procedure for CNCs and subsequent vertical deposition on an ITO coated glass substrate. The spindle-like shape and surface chemistry of sulphonated CNCs promote unique self-assembly behaviour, including the formation of lyotropic chiral nematic liquid crystalline phases in water. Remarkably, this chiral nematic ordering is retained even after drying, enabling the formation of well-structured solid films. In suspension, CNC molecules organize locally to minimize electrostatic interactions.69,75,76 At the interface between isotropic and anisotropic phases, anchoring forces are minimal, allowing CNCs to adopt various orientations. However, when deposited on smooth, impenetrable surfaces such as indium tin oxide (ITO), CNCs exhibit planar anchoring, where the director aligns parallel to the surface but may orient in any in-plane direction.76,77 To ensure uniform film formation, proper care was taken during the coating process. We note that a lack of uniform and unidirectional flow during deposition could compromise layer homogeneity. Therefore, ITO substrates were carefully dipped into CNC aqueous suspensions, and controlled solvent evaporation was employed to achieve homogeneous, self-assembled CNC layers. A stock solution of 0.5 wt% CNCs is utilized for the evaporation induced vertical deposition of CNCs over plasma-treated ITO coated glass substrates. Different amounts of CNCs (100, 150, 200, 250, and 300 μL) from the stock solutions were used for vertical deposition, and the samples were termed CNC100, CNC150, CNC200, CNC250, and CNC300, respectively. The typical spindle -like morphology of CNCs was confirmed by AFM analysis, which shows an average width of 15 ± 2 nm and an average length of 160 ± 50 nm (inset of Fig. 2f).
 |
| Fig. 1 Preparation of CNCs from banana fiber by acid hydrolysis, schematic illustration of evaporation induced vertical deposition of CNC on an ITO substrate, and the fabricated display device. | |
 |
| Fig. 2 The height profile of the nylon-rubbed layer and C200 across the microchannels. Schematic representation of the pre-aligned layers undergoing profilometric scanning is shown in the inset. SEM image of (b) a rubbed polyimide layer over ITO; rubbing direction is indicated by an arrow, and (c) self-assembled layers of CNCs over an ITO substrate. AFM image of (d) nylon coated, (e) rubbed polyimide, and (f) CNC coated (inset shows the spindle-like structure of CNCs) on ITO coated glass. | |
Surface morphology of pre-alignment layers
The surface morphology of the pre-alignment layer plays a critical role in determining the orientation of LC molecules, which in turn influences the overall performance of the device. To investigate this, several characterization techniques such as surface profilometry, POM, AFM, and SEM were employed. These methods were used to analyse various pre-alignment layers, including bare nylon, rubbed polyimide, and CNC coatings on ITO-coated glass substrates. POM in reflection mode, without the use of polarizers, enabled the examination of large-area alignment surfaces (Fig. S5, ESI†). After spin coating and thermal curing, the nylon surface without any rubbing appeared smooth and uniform (Fig. S5a, ESI†), lacking any directional features. This smooth surface may result in the random alignment of mesogens. However, when the nylon layer was rubbed with a velvet cloth, a series of well-defined directional channels formed on the surface (Fig. S5b, ESI†). These micro-sized channels are known to facilitate the alignment of mesogenic molecules along their length.78 Similarly, the CNC-coated surface exhibited parallel lines (Fig. S5c, ESI†), comparable to those seen on the rubbed nylon layer. These lines are characteristic of CNC-based assemblies prepared via the evaporation-induced vertical deposition method. They are visually distinguishable and serve as micro-channels that support homogeneous LC alignment.
Surface profilometric analysis was employed to confirm the presence of micro-sized channels and to quantitatively measure the thickness of the pre-alignment layers. A schematic of the profilometry setup is provided in the inset of Fig. 2a. To perform the measurement, a reference line (indicated in red) was scratched onto the surface of each pre-alignment layer using a needle, aligned parallel to the direction of the microchannels. The profilometer tip then scanned the surface along the direction marked by the brown line, which is perpendicular to the reference line, recording height variations. During scanning, periodic surface height variations were consistently observed across the sample CNC200, as shown in Fig. 2a. These periodic profiles correspond to the presence of microchannels in the pre-alignment layers. Similar height variations were also detected in the rubbed nylon layer in Fig. 2a, confirming the formation of directional microchannels. The analysis was extended to CNC-based films with varying concentrations, and the average thickness values are summarized in Table S1 (ESI†). The results revealed a clear trend of increasing film thickness with higher CNC content. It is important to highlight that the CNC layers, formed through a rubbing-free, evaporation-induced vertical deposition method, successfully produced microchannels comparable to those generated by conventional rubbing of polyamide layers. This demonstrates the effectiveness of CNC-based self-assembled films as a viable alternative for alignment layers in liquid crystal devices.
The SEM analysis was used to investigate the alignment layers' surface morphology on the ITO coated glass substrate. The SEM image of the rubbed nylon layer developed through the rubbed polyimide process is displayed in Fig. 2b. The arrow points in the direction of the rubbing, and it is easy to observe the microgrooves that have been created. The mechanism underlying these microchannels, which create homogeneous mesogenic alignment across the substrates, is widely recognized. The SEM images of a thoroughly dried CNC coating unambiguously validate a uniform and consistent layered or microchannel morphology of width around 50 ± 10 μm across the layer, shown in Fig. 2c.
The detailed analysis of the surface morphology of the alignment layers was done using the AFM technique in tapping mode. Fig. 2d depicts an AFM image of the nylon polymer layer without any rubbing process over the ITO surface. The random orientation of the polymer produces irregularities over the surface and is clearly visible. These random orientations of polymer chains would result in poor mesogenic alignment, discussed later in this article. In contrast, the application of the rubbed polyimide technique induces the formation of microchannels on the coating surfaces, as elucidated in Fig. 2e. These microgrooves, a consequence of the rubbing process, play a pivotal role in facilitating a unidirectional flow of mesogens within the material. In the case of CNC coating on ITO, the microchannels of width 50 ± 10 μm that are visible in SEM images will not be observed in AFM since that exceeds the maximum area of 20 × 20 μm2 can be covered by one scan. At a maximum 20 × 20 μm2 area of coverage (Fig. 2f), the CNC coating was found to have uniform height, whereas, at higher magnification, the characteristic spindle-like structures of CNC were able to be disclosed, as shown in the inset of Fig. 2f.
Surface anchoring energy of pre-alignment layers
The surface anchoring energy plays a vital role in governing the alignment of mesogens over different coatings. A renowned two-liquid method is utilized to quantify the surface anchoring energies of ITO surfaces coated with different pre-alignment layers. To measure the contact angles and, subsequently, the surface energy of the surfaces, diiodomethane (MI) is used as the non-polar solution, while water is utilized as the polar solution.79–82 Fig. 3 displays the contact angles associated with different pre-alignment layers. It is noted that the raw ITO surface exhibits the greater contact angles and least surface energy of 39.89 mJ m−2. This surface would give the FLC mesogens a cohesive, repelling quality as they align. The CNC-coated surface shows the least contact angles with a higher surface energy of 62.70 mJ m−2 and it would aid in better alignment of the mesogenic layers. The sequence in which the adhesive properties of the surfaces grow is as follows: ITO surface < nylon layer without rubbing < nylon layer with rubbing < CNC layer. The microgrooves created through rubbing and the microchannels generated owing to the self-assembly of CNC decrease the contact angles and increase the wettability of the surfaces. However, the ITO surfaces are coated with a distinct CNC thickness, giving almost the same surface energy, and are presented in Table 1. All the CNC-coated surfaces have surface energy greater than the conventional rubbed polyamide surface and bare-ITO surface, reflected in the FLC's aligning capability over them.
 |
| Fig. 3 Contact angle measurement of different surfaces using the polar solution, water, and non-polar solution, diiodomethane. | |
Table 1 Contact angles and surface energy of different layers using two-liquid methods
Alignment surface |
Contact angle |
Surface energy (mJ m−2) |
Water (°) |
Diiodomethane (MI) (°) |
ITO surface (no alignment layer) |
80 |
41 |
39.89 |
Nylon layer without rubbing |
73 |
38 |
42.74 |
Nylon layer with rubbing |
62 |
27 |
50.6 |
CNC100 |
37 |
35 |
61.21 |
CNC150 |
38 |
34 |
60.84 |
CNC200 |
35 |
32 |
62.70 |
CNC250 |
46 |
32 |
56.71 |
CNC300 |
37 |
33 |
61.53 |
Mesogenic alignment over different pre-alignment layers
The alignment of mesogens across various surfaces was analyzed through polarized optical microscopy, and the outcomes are presented in Fig. 4. Fig. 4a and b depict the bright and dark states of mesogens on ITO plates lacking any surface modifications. Notably, the images reveal characteristic focal conical structures of FLCs with evident light leakage in the dark state. This suboptimal mesogenic alignment is attributed to the absence of microchannels and the relatively lower surface energy inherent to the ITO surface. Fig. 4c and d illustrate the mesogenic alignment over nylon-coated layers without rubbing. Despite the interference of light resulting in colored states, the bright and dark states exhibit a limited contrast ratio due to poor distinguishability. The deficiency in microchannels, coupled with the dispersed orientation of polymer chains within the pre-alignment layer, exerts minimal influence on the LC mesogens, culminating in a multi-domain LC alignment. Fig. 4e and f depict bright and dark states of mesogens aligned over the surface treated with nylon followed by rubbing. The mesogens are appropriately aligned along the rubbed direction, and the bright and dark states are well distinguished with a well-defined contrast ratio. Among the CNC pre-aligned layers, CNC200 is characterized by monodomain alignment of mesogens with a minimum light leakage in the dark state, whose bright and dark states are seen respectively in Fig. 4g and h. The micro-channels present in the pre-alignment layer due to the self-assembly of CNC properly aid the LC mesogens in getting aligned over the film. Additionally, the higher surface energy offered by the layer enhances the wettability and provides less resistance against mesogenic flow. However, the light leakage in the dark state is contributed by the scattering centers present in the pre-aligned layer due to the aggregation of CNCs. The light leakage and the contrast ratio of the CNC pre-aligned samples depend on the degree of thickness or the concentration of the CNC coating.
 |
| Fig. 4 The bright and dark states of mesogens over different surfaces (in (e), the rubbing direction in the nylon polymer layer is indicated by an arrow). | |
The mesogenic alignment across CNC coatings of varying thicknesses is illustrated in Fig. 5. A noteworthy observation is the homogeneous alignment achieved across all concentrations, attributed to the microchannels formed through the self-assembly of CNCs and the heightened surface energy. The circled area in Fig. 5a highlights CNC aggregation within the pre-aligned layers, with the number of aggregates escalating with increasing CNC concentration and coating thickness. These aggregates impede the smooth alignment of LC molecules, resulting in the emergence of light-leaking centers. Notably, among the CNC pre-alignment layers, CNC200 exhibits minimal light leakage in its dark state, while CNC300 demonstrates an enhanced contrast ratio.
 |
| Fig. 5 The alignment of mesogens over CNC layers made with different thicknesses; (a) and (b) represent the bright and dark states of CNC100 (CNC aggregation is shown inside (a) with the white circles), (c) and (d) represent the bright and dark states of CNC150, (e) and (f) represent the bright and dark states of CNC250, (g) and (h) represent bright and dark states of CNC300. | |
Role of pre-alignment layers in the molecular relaxation of FLCs
Molecular relaxation is a crucial factor in the fundamental and practical features of LC devices. The role of molecular relaxation in alignment layers and at various interfaces has been previously reported.83,84 Fig. 6 displays the dielectric absorption curve (loss factor, tan
δ) and dispersion curves of the samples. At room temperature, every sample below 100 Hz has a low-frequency relaxation peak, as seen in Fig. 6a. These relaxation peaks were reported in FLC materials and accounted for the ionization–recombination-assisted diffusion of slow ions in the medium85 or interfacial polarization (Maxwell–Wagner mode) between the alignment layer and the FLC material.86 Another explicit relaxation peak is observed for all the samples near 1 kHz frequency, and it is regarded as the Goldstone mode (GM), which is the signature of all FLCs in the Sm C* phase. The phase fluctuations in the azimuthal orientation of the director contribute to the GM.87–89 It is observed that the GM relaxation peak intensity depends on the type of alignment layer, and it increases in the order given by nylon layer without rubbing < no alignment layer < CNC layer < nylon layer with rubbing. These data highlight that, compared to other samples, the mesogens above the CNC layer and the nylon-rubbed layer jointly contributed to the bulk relaxation process of GM because of their superior alignment and monodomain character. A slight change in the GM peak location indicated that the alignment layers were influencing the mesogens' free rotation in their own way. Fig. 6b shows that over the whole frequency range, there is very little difference in the permittivity values of the samples. Nevertheless, it is noteworthy that the conventional LC device exhibits the highest permittivity value, reaching 44 at 100 Hz. Notably, the permittivity values of the CNC200 device display only marginal deviation from those of the traditional LC device.
 |
| Fig. 6 Room temperature (a) dielectric absorption curves and (b) dielectric dispersion curve of the samples in different alignment layers. Temperature-dependent dielectric relaxation of the samples over different surfaces; (c) ITO layer without alignment, (d) nylon layer without rubbing, (e) nylon rubbed layer, and (f) CNC200 layer. | |
The molecular relaxation process significantly influences parameters such as the temperature, sample geometry, and alignment type.85,89,90 Temperature-dependent absorption curves of the sample aligned without any specific alignment layer (over ITO plates) are presented in Fig. 6c. Apart from low-frequency relaxation peaks, two additional relaxation modes are visible in the spectrum, and both are temperature-dependent. A light relaxation mode is presented near the GM mode at 45 °C, called partially unwound helical mode (p-UHM), and is well studied.61,91 Another bulk relaxation mode is observed around 10 kHz at 59 °C, called soft mode (SM).88 It is a characteristic mode in FLCs during the transition from the SmC* → SmA* phase. Both these modes are present in the sample aligned on a nylon polyimide rubbed layer (Fig. 6e) and the CNC200 aligned layer (Fig. 6f) at different temperatures. However, in the mesogens aligned over the nylon layer without rubbing, the magnitude of GM relaxation peak is seen to be much reduced (Fig. 6d). Additionally, a little shift in the transition temperature is noted.
Effect of pre-alignment layers on the electro-optical properties of FLCs
A thorough investigation is conducted into the effects of various alignment layers on the electro-optical characteristics, and the findings are reported in Fig. 7. Using the dynamics of polarization reversal in FLCs, the digital pulse approach was utilized to evaluate the spontaneous polarization (Ps) and switching time. The techniques for measuring Ps using a triangle wave are well documented in the literature.92–94 Fig. 7a shows that at lower voltages, the nature of alignment layers determines the value of Ps. On the other hand, Ps rises with applied voltages, and among the samples, there is only a slight variation in the saturated values (at 20 Vpp). The sample with the nylon-rubbed layer has a high Ps value over the whole voltage range compared to the other samples. However, because of its thicker pre-alignment layer, the Ps value of CNC200 is somewhat lower than that of the nylon-rubbed layer. The ferroelectric nature of the samples is confirmed by measuring the PE loop of the samples, which is shown in Fig. 7b. Since the shape of the PE loop depends on the frequency of the applied signal, the electrical signals of 100 Hz were utilized for measurements.95,96 The variation in coercive field values, remanent polarization, and saturated values of spontaneous polarization does not vary frequently from one layer to another. Notably, the CNC pre-alignment layer has a minimal impact on the P–E hysteresis behavior of the FLC sample. Its role in this application is primarily structural facilitating uniform LC alignment via its self-assembling behavior rather than functional in terms of contributing to the device's ferroelectric response. The time which is required for the mesogens to change their polarizing state is defined as the switching time. Its variation against the applied field is presented in Fig. 7c. It is observed that switching time decreases with applied voltages for all the samples. Additionally, its value depends on the nature of the pre-alignment layer. The switching time is minimum for the nylon pre-alignment layer without any rubbing and maximum for the CNC200 pre-alignment layer. This increase in switching time might be a consequence of retardation in polarization reversal of the mesogens close to the cellulose alignment layers. The switching time of the CNC-based pre-alignment layer device was compared with other plant-derived alignment layers. A switching time of 13 ms has been reported for a self-assembled alignment layer based on chlorophyll extracted from plants and doped into the liquid crystal.97 In contrast, our device demonstrated a significantly faster switching response of approximately 0.75 ms at 20 Vpp, highlighting its superior performance. A comparison of electro-optical performances of our device with the available plant derived ecofriendly alignment layers is presented in Table 2.
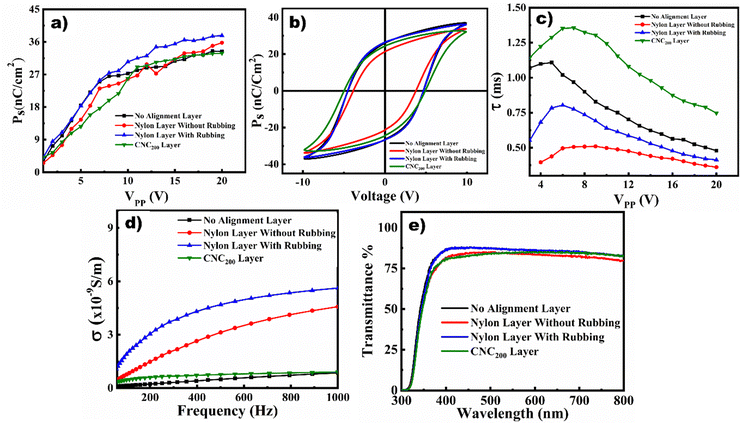 |
| Fig. 7 Electro-optical response of the devices made out of different alignment layers; (a) spontaneous polarization, (b) P–E hysteresis loop, (c) switching time, (d) electrical conductivity of different alignment layers at room temperature, and (e) optical transmittance of alignment layers in the visible domain of the electromagnetic spectrum. | |
Table 2 Comparison of the properties of the CNC pre-alignment layer against other plant derived environmentally friendly pre-alignment layers
Alignment material |
Mechanism of film preparation |
Type of alignment |
Optical transparency of film and other parameters |
Ref. |
Poly(methyl methacrylate) derivative films containing plant-based and renewable cardanol moieties |
Spin coating |
Vertical/homeotropic |
(a) 92% at 550 nm; similar to a bare glass substrate |
105 |
UV-curing |
(b) Voltage holding ratio (VHR) – 99% |
No rubbing |
(c) Residual DC voltage (RDC) – 20 mV |
Plant-based polysaccharide derivatives, such as guar gum |
Spin coating |
Planar and vertical |
(a) Transmittance – 99% at 550 nm |
106 |
Heat curing |
Rubbed layers |
Rubbing |
Chlorophyll extracted from plants doped into LCs |
Material doped into LCs |
Vertical alignment |
(a) Threshold voltage – 2.35 V |
97 |
Self-assembly |
(b) Response time 11 ms and 13 ms |
(c) VHR – 94% |
(d) RDC – 192 mV |
Plant based vanillin derivative-substituted polystyrene films |
Spin coating |
Planar and vertical |
(a) Transmittance is higher than 94% in the visible range of 400–800 nm |
107 |
(b) VHR – 98.9% |
(c) RDC – 15 mV |
Plant-based and renewable, eugenol-modified polystyrene layer |
Spin coating |
Random planar and vertical |
(a) Transmittance −99% at 550 nm |
108 |
(b) VHR – 99% |
(c) RDC – 10 mV |
Renewable and plant-based isoeugenol-substituted polystyrene films |
Spin coating |
Random planar and vertical |
(a) High temperature stability (100 °C) |
109 |
(b) Stability against a UV energy of 15 J cm−2 |
Renewable and phytochemical-based chavicol containing polymer film |
Spin coating |
Random planar and vertical |
(a) Stability against a UV energy of 15 J cm−2 |
110 |
Plant derived cellulose nanocrystals |
Vertical deposition |
Planar alignment |
(a) Stable even at high temperatures (up to 200 °C) |
This work |
Self-assembly |
(b) Enhancement in transmittance (88%), compared to bare ITO glass (82%) |
(c) Low electrical conductivity |
The electrical conductivity of the device with different alignment layers at room temperature is studied using the impedance spectroscopic technique in a frequency domain of 0.1 kHz to 1 kHz, and the results are manifested in Fig. 7d. The device with the nylon layer with rubbing as the pre-alignment layer shows the highest conductivity in the entire frequency domain, which recommends generating static charges during the rubbing process. Nevertheless, the incorporation of the CNC layer leads to a marked reduction in device conductivity, primarily attributed to the rubbing-free vertical deposition technique employed in the fabrication of the pre-alignment layers. Additionally, plenty of reports suggest that alignment layers can capture the ions within the layer.98–100 In the case of CNCs, the inherent negative charge of the self-assembled layers might contribute to the adsorption of the excess ions in FLCs, thereby reducing the conductivity owing to ionic movements. The ion trapping by the CNC layers is highly dependent on their thickness, and the best outcome is produced at a CNC200 concentration of the coating solution. Optical transmittance is one of the fundamental requirements of LC devices. The light transmittance of pre-alignment layers before filling FLC materials is presented in Fig. S6 (ESI†). The accuracy of the measuring instrument is verified by measuring the transmittance of air, which shows 100% transmittance. The transmittance of ITO-glass at 600 nm is approximately 82% relative to air. In comparison, the CNC layer exhibits a higher optical transmittance of 88%. Coating the ITO-glass with CNC alignment layers does not degrade its light transmittance; instead, it slightly enhances it which makes it suitable for LC device applications. The role of pre-alignment layers in the light transmittance of the LC devices after filling the FLCs is displayed in Fig. 7e. The ITO layer, nylon layers with and without rubbing, and CNC200 layer show similar transmittance in the entire visible spectrum domain. Notably, CNC pre-alignment layers offer excellent optical transparency, showing no compromise in light transmittance when compared to traditional alignment materials. Unlike the conventional rubbed polyimide technique, CNCs enable a rub-free alignment process that effectively mitigates the influence of ionic impurities, one of the major drawbacks of rubbed alignment methods. Furthermore, the electro-optical performance of CNC-based devices closely matches that of devices using traditional rubbed polyimide layers. In addition, CNC layers demonstrate a faster switching response than other environmentally friendly, plant-derived alignment layers reported to date. These distinctive advantages position CNCs as a strong candidate to replace conventional polymer-based alignment layers in LC devices.
Experimental section
Materials
Chemically extracted banana pseudo-stem fibers from agricultural wastes are utilized as cellulose sources. Sodium hydroxide (NaOH), sodium chlorite (NaClO2), and sulfuric acid (H2SO4, 98%) were purchased from Sigma Aldrich, India. Deionized (DI) water (Milli-Q purifier system, Merck, Germany) was utilized as water for all experiments. The FLC material used in this work is ZLI3654, procured from E. Merk, Darmstadt.
Materials preparation
Synthesis of cellulose nanocrystals (CNCs). Extraction of cellulose fibers from banana pseudo-stem fibers was conducted by mercerization followed by bleaching. A detailed experimental procedure can be found elsewhere.101 The dried holocellulose can be stored under ambient conditions and further utilized for CNC synthesis. The synthesis of highly crystalline CNCs was done using well-established H2SO4 hydrolysis.102 In more detail, about 3 g of cellulose fibers were treated with 60 mL, 64% H2SO4 for 2 h at 45 °C in a water bath. After 2 h, the reaction is quenched and neutralized by adding about 5–6 times amount of water into the reaction mixture. Entire solution is centrifuged and concentrated at 10
000 rpm for 10 minutes. Removal of excess precursor acid was ensured by the dialysis for 4–5 days. Finally, a stock colloidal suspension of 0.5 wt% CNC was made and preserved at 4 °C for further use.
Fabrication of a display device. The desired concentrations of CNC solution (100, 150, 200, 250, and 300 μL are pipetted out from the stock colloidal suspension of CNCs and made up to 4 mL) are prepared, and patterned ITO coated glass is dipped in the solution placed over a water bath. Prior to this, the ITO plates are subjected to plasma treatment for ten minutes in order to compensate for their hydrophobic nature and inhibit adhesion. The solution is allowed to evaporate at a controlled temperature of 55 °C. The self-assembly of CNC generates pre-alignment layers on the substrates once the solution is evaporated. The pre-aligned substrates were assembled to form an LC cell, where a mylar spacer of 6 μm is used to define the thickness. The electrical connections were made by using copper wires for further characterization. Additionally, two similar devices were fabricated: one without any alignment layer and one with a conventional rubbed polyimide technique. The FLC material ZLI3654 was introduced onto the cell through capillary action by heating it at 120 °C, well above the isotropic temperature of the sample, and then cooling down to room temperature.
Apparatus and measurements. The thickness of the pre-alignment layers based on nylon (rubbed) and CNCs on the ITO coated glass substrate were quantified employing a stylus profilometer (DektakXT, Bruker) at room temperature. Subsequently, the surface morphology of the pre-alignment layers was investigated using scanning electron microscopy (Zeiss EVO 50) and atomic force microscopy (AFM) operating in tapping mode (Bruker). The basic chemical and structural characterization of CNCs isolated by acid hydrolysis was conducted using Fourier transform infrared (FTIR) analysis (PerkinElmer). Wide-angle X-ray scattering (WAXS) measurements were carried out using an XEUSS SAXS/WAXS system. Both measurements were done in the solid state and compared with the initial holocellulose source. Conversion of CNCs from holocellulose is evaluated by estimating the crystallinity index (CrI) from the XRD patterns of both CNCs and holocellulose. Since we used cellulose II formed by the NaOH pretreatment of the naturally occurring cellulose I,
where I110 – intensity of the peak corresponding to the 110 plane and IAM – intensity of the amorphous region.103,104Zeta potential analysis of the CNC colloid was studied using dynamic light scattering (DLS) using Zetasizer Nano ZS and Malvern 200 equipment. The thermal stability of the CNC was evaluated using a thermogravimetric analyzer (TGA, TA Q50) in the range from room temperature to 700 °C at a rate of 10 °C min−1 under a nitrogen atmosphere. Piezoresponse force microscopy (PFM) of the CNC film was performed using a FlexAFM system (Nanosurf). A source measuring unit (Keithley 2450) and a current preamplifier (SR570, Stanford Research) were used for the electrical characterization of the piezoelectric nanogenerator (PENG) device based on the CNC film. The optical characterization of nylon rubbed and CNC pre-alignment coatings on ITO glass and mesogenic alignment was conducted employing a polarizing optical microscope (Leica DM2700P) fitted with a charge-coupled device (CCD) camera at ambient temperature. Measurement of electro-optical properties of the FLC device (film) utilized the direct pulse technique, with input wave patterns (square and triangular waves from 1 Vpp to 20 Vpp; peak to peak voltage) generated through an arbitrary function generator (Tektronix AFG1062) and output signals captured using a digital phosphor oscilloscope (Tektronix DPO2004B). Electrical conductivity and dielectric spectroscopic analyses were carried out using an LCR meter (HIOKI 3532-50 LCR Hi TESTER) spanning a frequency domain of 100 Hz to 1 MHz and using an impedance analyzer (Wayne Kerr 6540 A) with a frequency range of 20 Hz to 1 MHz, utilizing a measuring voltage of 0.5 Vpp. Temperature control during experiments was facilitated by a JULABO F-25 HE temperature controller, offering a temperature stability of ±0.01 °C. The sample cells were thermally isolated for temperature-dependent investigations. For the analysis of P–E hysteresis loops of the FLC film, a ferroelectric tester (aixACCT-TF2000E) was employed. A triangular wave of 10Vpp with a current of 10 μA is applied at a frequency of 100 Hz to analyze the hysteresis loops. Optical transmission of the pre-alignment layer CNC films and FLC films was measured using a UV-vis-NIR spectrophotometer (Shimadzu, UV-3600) equipped with an integrating sphere attachment, with polytetrafluoroethylene (PTFE) serving as the reference material. Photoluminescence spectra were acquired using a FluroLog-3 instrument (Horiba) equipped with a 450 W xenon arc lamp.
Conclusions
This article proposes an alternative approach to achieve alignment of FLCs for display applications. An environmentally friendly pre-alignment layer for FLC display devices has been developed employing CNC pre-alignment layers via a vertical deposition technique and its performance has been evaluated against a traditional rubbed polyimide technique. LC devices incorporating various pre-alignment layers, including conventional rubbed polyimide and CNC layers, were fabricated and systematically compared. Devices with CNC layers exhibited highly robust mesogenic alignment, with the quality of alignment being sensitive to the thickness of the CNC layer. The spindle-like structure and self-assembling properties of CNCs, coupled with the vertical deposition method, enabled the formation of microchannels on the substrate. These microchannels effectively guided mesogens, ensuring homogeneous alignment across the developed layer. Surface energy measurements revealed that CNC alignment layers possessed higher surface energy compared to conventional counterparts, significantly enhancing mesogenic alignment. Additionally, the alignment layers influenced dielectric relaxation and transition temperatures of the mesogens. The electro-optical properties of CNC-based devices, including spontaneous polarization, switching time, and polarization–electric (PE) hysteresis, were comparable to those of devices using conventional rubbed polyimide layers, without compromising optical transparency. Moreover, CNC alignment layers demonstrated the ability to capture excess ions in the medium, resulting in reduced device conductivity. This study highlights the potential of CNCs as an alignment layer for next-generation LCD applications. Surface functionalization of CNCs offers further advantages, such as improved wettability, higher density distribution, and enhanced orientation, paving the way for significant advancements in pre-alignment layer design and overall LC device performance.
Author contributions
Abhilash T. K. contributed to the fabrication and characterization of the FLC device, as well as to the manuscript preparation. Hasna M. Abdul Hakkeem contributed to the synthesis, vertical deposition, characterization of CNCs and manuscript writing. Saju Pillai and Achu Chandran provided valuable insights during the experiments and offered constructive feedback to enhance the quality of the manuscript.
Data availability
The data supporting this article have been included in the manuscript itself and also as part of the ESI.†
Conflicts of interest
There are no conflicts to declare.
Acknowledgements
The authors express their sincere gratitude to the Director of CSIR-NIIST for unwavering motivation and support. Special appreciation is extended to Dr Bhoje Gowd, Dr Swapna Nair, Ajaikrishnan U, and Dr Surendran K P for their invaluable assistance in characterization. The author ATK acknowledges financial support from UGC. The author Achu Chandran acknowledges the funding support from the Science & Engineering Research Board (SERB), India, project no. CRG/2023/004068, Department of Science and Technology (DST), India under project no. DST/TDT/DDP-07/2021 and Council of Scientific and Industrial Research (CSIR), New Delhi, through Fast Track Translation Project, FTT040506.
Notes and references
- J. Sakuda, E. Hosono, M. Yoshio, T. Ichikawa, T. Matsumoto, H. Ohno, H. Zhou and T. Kato, Adv. Funct. Mater., 2015, 25, 1206–1212 CrossRef CAS.
- D. Högberg, B. Soberats, S. Uchida, M. Yoshio, L. Kloo, H. Segawa and T. Kato, Chem. Mater., 2014, 26, 6496–6502 CrossRef.
- K.-H. Kim and J.-K. Song, NPG Asia Mater., 2009, 1, 29–36 CrossRef.
- D. Pauluth and K. Tarumi, J. Mater. Chem., 2004, 14, 1219 RSC.
- K. Yin, E.-L. Hsiang, J. Zou, Y. Li, Z. Yang, Q. Yang, P.-C. Lai, C.-L. Lin and S.-T. Wu, Light: Sci. Appl., 2022, 11, 161 CrossRef CAS.
- N. Tamaoki, Adv. Mater., 2001, 13, 1135–1147 CrossRef CAS.
- A. K. Srivastava, W. Zhang, J. Schneider, A. L. Rogach, V. G. Chigrinov and H.-S. Kwok, Adv. Mater., 2017, 29, 1701091 CrossRef PubMed.
- M. Zhou, T. J. Kidd, R. D. Noble and D. L. Gin, Adv. Mater., 2005, 17, 1850–1853 CrossRef CAS.
- B. M. Carter, B. R. Wiesenauer, E. S. Hatakeyama, J. L. Barton, R. D. Noble and D. L. Gin, Chem. Mater., 2012, 24, 4005–4007 CrossRef CAS.
- S. Sivakumar, K. L. Wark, J. K. Gupta, N. L. Abbott and F. Caruso, Adv. Funct. Mater., 2009, 19, 2260–2265 CrossRef CAS.
- H. Tan, X. Li, S. Liao, R. Yu and Z. Wu, Biosens. Bioelectron., 2014, 62, 84–89 CrossRef CAS.
- D. Hartono, X. Bi, K.-L. Yang and L.-Y. L. Yung, Adv. Funct. Mater., 2008, 18, 2938–2945 CrossRef CAS.
- S. J. Woltman, G. D. Jay and G. P. Crawford, Nat. Mater., 2007, 6, 929–938 CrossRef CAS PubMed.
- P. J. M. Wyatt, J. Bailey, M. Nagaraj and J. C. Jones, Nat. Commun., 2021, 12, 4717 CrossRef CAS PubMed.
- A. Chandran, J. Prakash, K. K. Naik, A. K. Srivastava, R. Dąbrowski, M. Czerwiński and A. M. Biradar, J. Mater. Chem. C, 2014, 2, 1844 RSC.
- R. B. Meyer, L. Liebert, L. Strzelecki and P. Keller, J. Phys. Lett., 1975, 36, 69–71 CrossRef.
- N. A. Clark and S. T. Lagerwall, Appl. Phys. Lett., 1980, 36, 899–901 CrossRef CAS.
- D. W. Berreman, Phys. Rev. Lett., 1972, 28, 1683–1686 CrossRef CAS.
- N. A. J. M. van Aerle and A. J. W. Tol, Macromolecules, 1994, 27, 6520–6526 CrossRef CAS.
- J. M. Geary, J. W. Goodby, A. R. Kmetz and J. S. Patel, J. Appl. Phys., 1987, 62, 4100–4108 CrossRef CAS.
- M. Chizaki, H. Abe, H. Iwa, R. Tomokiyo, K. Shigehara, N. Amaya, N. Kaiya, Y. Iimura and S. K. Shunsuke Kobayashi, Jpn. J. Appl. Phys., 1995, 34, 2411 CrossRef CAS.
- T. Sasaki and H. F. Nishikawa, Jpn. J. Appl. Phys., 1992, 31, L632 CrossRef CAS.
- O. Yaroshchuk and Y. Reznikov, J. Mater. Chem., 2012, 22, 286–300 RSC.
- W. M. Gibbons, P. J. Shannon, S.-T. Sun and B. J. Swetlin, Nature, 1991, 351, 49–50 CrossRef CAS.
- M. Schadt, K. Schmitt, V. Kozinkov and V. Chigrinov, Jpn. J. Appl. Phys., 1992, 31, 2155 CrossRef CAS.
- D. H. Kim, D. W. Lee, J. Y. Oh, J. Won and D.-S. Seo, ACS Appl. Nano Mater., 2022, 5, 1435–1445 CrossRef CAS.
- J. H. Lee, D. H. Kim, J. Won, D. W. Lee, J. Y. Oh, Y. Liu, Y.-P. Park, H.-C. Jeong and D.-S. Seo, Mater. Chem. Phys., 2021, 269, 124771 CrossRef CAS.
- N. Mori, M. Morimoto and K. Nakamura, Macromolecules, 1999, 32, 1488–1492 CrossRef CAS.
- N. Mori, M. Morimoto and K. Nakamura, Adv. Mater., 1999, 11, 1049–1051 CrossRef CAS.
- V. G. Chigrinov, ISBN 9780890068984.
- Y. Garbovskiy and I. Glushchenko, Crystals, 2015, 5, 501–533 CrossRef CAS.
- A. R. Karaawi, M. V. Gavrilyak, V. A. Boronin, A. M. Gavrilyak, J. V. Kazachonok and F. V. Podgornov, Liq. Cryst., 2020, 47, 1507–1515 CrossRef CAS.
- S. K. Gupta, D. P. Singh and R. Manohar, Adv. Mater. Lett., 2015, 6, 68–72 CrossRef.
- D. A. Corder, D. R. Evans and J. R. Tyrer, Meas. Sci. Technol., 1997, 8, 1034–1040 CrossRef CAS.
- N. Pushpavathi, K. L. Sandhya and R. Pratibha, Liq. Cryst., 2019, 46, 666–673 CrossRef CAS.
- A. Sawada and S. Naemura, Jpn. J. Appl. Phys., Part 2, 2002, 41, 6–9 CrossRef.
- A. Sawada, K. Tarumi and S. Naemura, Jpn. J. Appl. Phys., Part 1, 1999, 38, 1418–1422 CrossRef CAS.
- A. Sawada, K. Tarumi and S. Naemura, Jpn. J. Appl. Phys., Part 1, 1999, 38, 1423–1427 CrossRef CAS.
- M. Sierakowski, Mol. Cryst. Liq. Cryst. Sci. Technol., Sect. A, 2002, 375, 659–677 CrossRef CAS.
- H.-Y. Hung, C.-W. Lu, C.-Y. Lee, C.-S. Hsu and Y.-Z. Hsieh, Anal. Methods, 2012, 4, 3631 RSC.
- R. Kravchuk, O. Koval’chuk and O. Yaroshchuk, Mol. Cryst. Liq. Cryst., 2002, 384, 111–119 CrossRef CAS.
- J. L. Haberfeld, E. C. Hsu and J. F. Johnson, Mol. Cryst. Liq. Cryst., 1973, 24, 1–5 CrossRef CAS.
- P. Keller and L. Liebert, Liquid Crystals, Solid State Physics Supplement 14, Academic Press, New York, 1978, pp. 20–75 Search PubMed.
- Y. Garbovskiy and I. Glushchenko, Appl. Phys. Lett., 2015, 107, 041106 CrossRef.
- C.-T. Huang, K.-T. Liao, C.-H. Lin, J.-S. Hsu and W. Lee, Appl. Phys. Express, 2013, 6, 121701 CrossRef.
- W. Lee, C.-T. Huang, K.-T. Liao, J.-S. Hsu and C.-H. Lin, Mol. Cryst. Liq. Cryst., 2014, 601, 88–96 CrossRef CAS.
- T.-Y. Tasi, P.-C. Wu, K.-T. Liao, H.-Y. Huang, C.-H. Lin, J.-S. Hsu and W. Lee, Opt. Mater. Express, 2015, 5, 639 CrossRef.
- Y. Huang, P. J. Bos and A. Bhowmik, J. Appl. Phys., 2010, 108, 064502 CrossRef.
- Y.-M. Zhu, L. Wang, Z.-H. Lu, Y. Wei, X. X. Chen and J. H. Tang, Appl. Phys. Lett., 1994, 65, 49–51 CrossRef CAS.
- J. A. Castellano, Mol. Cryst. Liq. Cryst., 1983, 94, 33–41 CrossRef CAS.
- N. A. J. M. Van Aerle, M. Barmentlo and R. W. J. Hollering, J. Appl. Phys., 1993, 74, 3111–3120 CrossRef CAS.
- J. M. Geary, J. W. Goodby, A. R. Kmetz and J. S. Patel, J. Appl. Phys., 1987, 62, 4100–4108 CrossRef CAS.
- N. A. J. M. van Aerle and A. J. W. Tol, Macromolecules, 1994, 27, 6520–6526 CrossRef CAS.
- M. F. Toney, T. P. Russell, J. A. Logan, H. Kikuchi, J. M. Sands and S. K. Kumar, Nature, 1995, 374, 709–711 CrossRef CAS.
- N. F. A. Van Der Vegt, F. Müller-Plathe, A. Geleßus and D. Johannsmann, J. Chem. Phys., 2001, 115, 9935–9946 CrossRef CAS.
- N. Kawatsuki, H. Takatsuka and T. Y. Ono, Jpn. J. Appl. Phys., 1997, 36, 6464 CrossRef CAS.
- J. H. Lee, D. H. Kim, J. Won, D. W. Lee, J. Y. Oh, Y. Liu, Y. P. Park, H. C. Jeong and D. S. Seo, Mater. Chem. Phys., 2021, 269, 124771 CrossRef CAS.
- Q. Luo, S. Xiong, H. Wu, Z. Sun and N. Ming, Mol. Cryst. Liq. Cryst. Sci. Technol., Sect. A, 1996, 289, 69–76 CrossRef CAS.
- A. Chandran, T. Joshi, I. Sharma, K. M. Subhedar, D. S. Mehta and A. M. Biradar, J. Mol. Liq., 2019, 279, 294–298 CrossRef CAS.
- A. Chandran, J. Prakash, K. K. Naik, A. K. Srivastava, R. D
browski, M. Czerwiński and A. M. Biradar, J. Mater. Chem. C, 2014, 2, 1844–1853 RSC. - A. Chandran, A. Choudhary, L. K. Gangwar, T. K. Abhilash, B. S. Athira and A. M. Biradar, J. Mol. Liq., 2021, 340, 117194 Search PubMed.
- C. Liu, B. Li, H. Du, D. Lv, Y. Zhang, G. Yu, X. Mu and H. Peng, Carbohydr. Polym., 2016, 151, 716–724 CrossRef CAS PubMed.
- D. Beyene, M. Chae, J. Dai, C. Danumah, F. Tosto, A. G. Demesa and D. C. Bressler, Materials, 2018, 11, 1272 CrossRef PubMed.
- S. Zhang, G. Sun, Y. He, R. Fu, Y. Gu and S. Chen, ACS Appl. Mater. Interfaces, 2017, 9, 16426–16434 CrossRef CAS PubMed.
- J.-M. Meijer, F. Hagemans, L. Rossi, D. V. Byelov, S. I. R. Castillo, A. Snigirev, I. Snigireva, A. P. Philipse and A. V. Petukhov, Langmuir, 2012, 28, 7631–7638 CrossRef CAS PubMed.
- S.-L. Kuai, X.-F. Hu, A. Haché and V.-V. Truong, J. Cryst. Growth, 2004, 267, 317–324 CrossRef CAS.
- L. R. F. Kusmono, M. W. Wildan and M. N. Ilman, Heliyon, 2020, 6, e05486 CrossRef PubMed.
- C. Vivian Abiaziem, A. Bassey Williams, A. Ibijoke Inegbenebor, C. Theresa Onwordi, C. Osereme Ehi-Eromosele and L. Felicia Petrik, J. Phys.: Conf. Ser., 2019, 1299, 012123 CrossRef.
- Y. Habibi, L. A. Lucia and O. J. Rojas, Chem. Rev., 2010, 110, 3479–3500 CrossRef CAS PubMed.
- H. M. A. Hakkeem, V. S. Ardra, A. De, A. Babu, M. Padmanabhan and S. Pillai, Int. J. Biol. Macromol., 2024, 273, 133140 CrossRef PubMed.
- H. A. Silvério, A. R. P. Leite, M. D. D. da Silva, R. M. N. de Assunção, A. C. Pero and D. Pasquini, Polym. Bull., 2022, 79, 2539–2557 CrossRef.
- Y. Ge, N. Lin, C. Du, T. Amann, H. Feng, C. Yuan and K. Li, Cellulose, 2023, 30, 3757–3771 CrossRef CAS.
- M. A. Signore, S. K. Padmanabhan, L. Velardi, A. Serra, M. Stoppa, L. Francioso and A. Licciulli, Appl. Surf. Sci., 2025, 692, 162734 CrossRef CAS.
- B. S. Athira, K. P. Surendran and A. Chandran, Chem. Eng. J., 2025, 506, 160056 CrossRef CAS.
- R. Prathapan, R. F. Tabor, G. Garnier and J. Hu, ACS Appl. Bio Mater., 2020, 3, 1828–1844 CrossRef CAS PubMed.
- R. M. Parker, G. Guidetti, C. A. Williams, T. Zhao, A. Narkevicius, S. Vignolini and B. Frka-Petesic, Adv. Mater., 2018, 30, 1704477 CrossRef PubMed.
- P.-X. Wang, W. Y. Hamad and M. J. MacLachlan, Nat. Commun., 2016, 7, 11515 CrossRef PubMed.
- Y. M. Zhu, L. Wang, Z. H. Lu, Y. Wei, X. X. Chen and J. H. Tang, Appl. Phys. Lett., 1994, 65, 49–51 CrossRef CAS.
- D. H. Kaelble, J. Adhes., 1970, 2, 66–81 CrossRef CAS.
- A. Chandran, T. Joshi, P. K. Khanna, D. S. Mehta, D. Haranath and A. M. Biradar, J. Appl. Phys., 2017, 122, 014101 CrossRef.
- D. K. Owens and R. C. Wendt, J. Appl. Polym. Sci., 1969, 13, 1741–1747 CrossRef CAS.
- F. Comte and D. Sage, Makromol. Chem., Macromol. Symp., 1989, 23, 299–305 CrossRef CAS.
- A. Chandran, A. Choudhary, P. Singh, D. Haranath and A. M. Biradar, Soft Matter, 2015, 11, 749–755 RSC.
- A. Chandran, P. K. Khanna, D. Haranath and A. M. Biradar, Phys. Rev. E, 2018, 97, 1–8 CrossRef.
- T. Joshi, A. Kumar, J. Prakash and A. M. Biradar, Liq. Cryst., 2010, 37, 1433–1438 CrossRef CAS.
- F. V. Podgornov, R. Wipf, B. Stühn, A. V. Ryzhkova and W. Haase, Liq. Cryst., 2016, 43, 1536–1547 CrossRef CAS.
- F. Kremer, V. Sven Uwe and E. W. Fischer, Liq. Cryst., 1991, 9, 145–150 Search PubMed.
- F. Gouda, K. Skarp and S. T. Lagerwall, Ferroelectrics, 1991, 113, 165–206 CrossRef CAS.
- A. M. Biradar, S. Wróbel and W. Haase, Phys. Rev. A:At., Mol., Opt. Phys., 1989, 39, 2693–2702 CrossRef CAS PubMed.
- H. Miyata, M. Maeda and I. Suzuki, Liq. Cryst., 1996, 20, 303–309 CrossRef CAS.
- A. Bawa, L. K. Gangwar, A. Dhingra, A. Choudhary, Rajesh, S. P. Singh, W. Haase and A. M. Biradar, Liq. Cryst., 2019, 46, 166–175 CrossRef CAS.
- S. S. Bawa, A. M. Biradar, K. Saxena and S. Chandra, Rev. Sci. Instrum., 1988, 59, 2023–2030 CrossRef CAS.
- K. Miyasato, S. Abe, H. Takezoe, A. Fukuda and E. Kuze, Jpn. J. Appl. Phys., 1983, 22, L661 CrossRef.
- S. S. Bawa, A. M. Biradar and S. Chandra, Phys. Status Solidi, 1987, 102, 829–834 Search PubMed.
- C. Reynaerts and A. de Vos, J. Phys. D: Appl. Phys., 1989, 22, 1504–1509 CrossRef CAS.
- C. Reynaerts and A. De Vos, Ferroelectrics, 1991, 113, 439–452 CrossRef CAS.
- G. Moon and J. H. Lee, Soft Matter, 2021, 17, 1834–1841 RSC.
- Y. Huang, P. J. Bos and A. Bhowmik, J. Appl. Phys., 2010, 108, 064502 CrossRef.
- Y. Huang, A. Bhowmik and P. J. Bos, Jpn. J. Appl. Phys., 2012, 51, 031701 CrossRef.
- Y. Huang, A. Bhowmik and P. J. Bos, J. Appl. Phys., 2012, 111, 024501 CrossRef.
- H. M. Abdul Hakkeem, A. Babu, S. Kumar Pal, A. Peer Mohamed, S. Kumar Ghosh and S. Pillai, Microchem. J., 2021, 168, 106393 CrossRef.
- R. Xiong, S. Yu, M. J. Smith, J. Zhou, M. Krecker, L. Zhang, D. Nepal, T. J. Bunning and V. V. Tsukruk, ACS Nano, 2019, 13, 9074–9081 CrossRef CAS PubMed.
- H. G. Ingersoll, J. Appl. Phys., 1946, 17, 924–939 CrossRef CAS.
- L. Segal, J. J. Creely, A. E. Martin and C. M. Conrad, Text. Res. J., 1959, 29, 786–794 CrossRef CAS.
- H. Kang, Y.-S. Choi, H. Hong, T. Ko, D. Kang and J.-C. Lee, Eur. Polym. J., 2014, 61, 13–22 CrossRef CAS.
- Y. Cho, J. Moon, D. E. Yang and H. Kang, Elastomers Compos., 2023, 58, 1–10 CAS.
- C. Ju, C. Park, T. Kim and H. Kang, RSC Adv., 2019, 9, 14188–14193 RSC.
- C. Ju, T. Kim and H. Kang, Polymers, 2018, 10, 201 CrossRef PubMed.
- D. Yang, K. Seo and H. Kang, Polymers, 2021, 13, 547 CrossRef CAS.
- J. Moon, K. Seo and H. Kang, Polymers, 2021, 13, 819 CrossRef CAS PubMed.
|
This journal is © The Royal Society of Chemistry 2025 |
Click here to see how this site uses Cookies. View our privacy policy here.