DOI:
10.1039/C7GC00014F
(Perspective)
Green Chem., 2017,
19, 2748-2761
Green chemistry and polymers made from sulfur
Received
3rd January 2017
, Accepted 27th February 2017
First published on 3rd March 2017
Abstract
Polymers are among the most important mass-produced materials on the planet, yet they are largely derived from a finite supply of petrochemicals. To ensure the sustainable production of polymers and functional materials, alternative feedstocks are required. This Perspective examines this challenge in the context of an emerging class of polymers made from elemental sulfur. Because sulfur is a by-product of the petroleum industry, converting it into useful polymers and related materials is an advance in waste valorisation. Additionally, co-polymerisation of sulfur with renewable monomers represents an additional contribution to sustainability. These reactions are often solvent free and benefit from full atom economy, futher augmenting their Green Chemistry credentials. Applications of these materials will be discussed, with a spotlight on environmental benefits. A forward looking assessment of the opportunities for using sulfur polymers in Green Chemistry is also included.
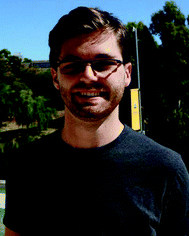 Max J. H. Worthington | Max J. H. Worthington completed his BSc in Chemistry with a first class Honours degree at Flinders University in 2015. He is currently a PhD student at Flinders University where he is investigating renewable polymers for applications in environmental remediation, biochemistry, and agriculture. His research in sulfur polymers that capture mercury pollution has garnered wide attention, with profiles in international news and documentaries, and several on-going collaborations with both industry and environmental agencies. |
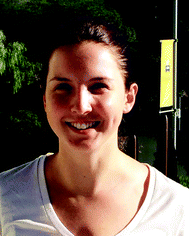 Renata L. Kucera | Renata L. Kucera is a third-year undergraduate at Flinders University. With the support of summer research scholarships from Flinders University and the National Environmental Science Programme, Renata has discovered several new polymers made by the co-polymerisation of sulfur and unsaturated industrial waste. Her current research interests span Green Chemistry, synthesis and sustainable polymers. |
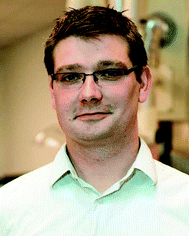 Justin M. Chalker | Dr Justin M. Chalker earned a B.S. in Chemistry and a B.A. in the History and Philosophy of Science at The University of Pittsburgh in 2006. At Pittsburgh, he contributed to the total synthesis of several natural products under the direction of Theodore Cohen. Supported by a Rhodes Scholarship and a National Science Foundation Graduate Research Fellowship, Justin then completed his D.Phil. at the University of Oxford under the supervision of Prof. Benjamin Davis where he developed several tools for the site-selective modification of proteins. In 2012, Justin started his independent career as an assistant professor at The University of Tulsa where he established a diverse research program in organic chemistry, biochemistry and material science. In these projects, contributions to sustainability, environmental protection and human wellbeing are priorities. In 2015, Justin moved to Flinders University in Adelaide, Australia where he is a Lecturer in Synthetic Chemistry and recipient of an Australian Research Council Discovery Early Career Researcher Award. In 2016, Justin was named Tall Poppy of the Year for South Australia in recognition of his achievements in research, teaching and science communication. |
Introduction
The impact of synthetic polymers and functional materials on human life is profound. Such materials ensure access to clean air and water,1,2 medical devices that improve quality of life,3,4 sustainable power generation and energy storage,5,6 building materials for transportation and infrastructure,7 high-tech devices for communication and information processing,8,9 fibres for functional textiles,10,11 and a host of other far-reaching capabilities.12–14 Our everyday routines and economies also rely heavily on synthetic polymers, especially plastics. With approximately 322 million tonnes of plastics produced in 2015,15 polymers are among the most widely produced synthetic materials on Earth. To ensure sustainable access to these materials, it is imperative that the synthesis of polymers aligns with the principles of Green Chemistry.16,17 Given that the vast majority of synthetic polymers are derived from finite resources such as petroleum feedstocks,18 a grand challenge in polymer chemistry is to identify sustainable building blocks that provide monomers already in use or polymers that are functional equivalents to existing macromolecules. To this end, the Green Chemistry and polymer communities have made some admirable gains. Through the use of safer solvents,19 greener and catalytic processing,16,20 starting materials derived from renewable biomass,21,22 re-purposing agricultural and industrial waste as a starting material,20,23,24 using CO2 as a monomer18 or converting it into a traditional olefin monomer,25 and designing new strategies for recycling and bio-degradation,26,27 the Green Chemistry metrics over the lifetime of synthetic macromolecules have improved. Simultaneously, the introduction of new polymers that address these concerns also improves the outlook for sustainability and environmental benefit. In this Perspective, we discuss one of these classes of new materials—polymers made from sulfur—and the many ways in which they are green in their preparation and use. While this class of materials alone will not solve the problem of polymer sustainability, it may contribute in several important ways. Accordingly, this Perspective examines how polymers made from sulfur can be derived from waste and renewable sources, and how the resulting materials can be used in applications that benefit the environment (Fig. 1).
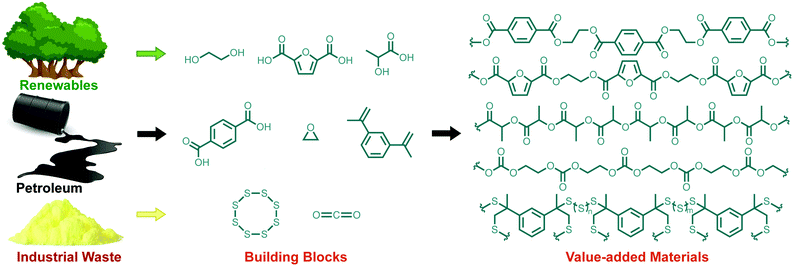 |
| Fig. 1 Polymers are largely derived from a finite resource: petroleum. However, the future of polymer synthesis will depend on sourcing monomers from alternative feedstocks such as renewable biomass, agricultural waste, and industrial by-products such as CO2 and sulfur. This Perspective examines the opportunities in Green Chemistry afforded by the use of sulfur as a building block for functional materials that benefit the environment. The tree and oil barrel graphics were licensed from 123RF.com with image credit to lilu330 and dvarg, respectively. Copyright 123RF.com. | |
Sulfur: a widely available and underused building block
Sulfur has been used for many centuries in applications as diverse as medicine, fabric bleaching, construction of lamp wicks, gun powder formulation and then more recently in the vulcanisation of latex.28,29 In these cases, sulfur was sourced largely through geological deposits.28 With the growing concerns for acid rain, however, the desulfurisation of crude oil shifted the major share of sulfur production to the petroleum sector from 1970 to 1990.29 By removing sulfur from crude oil and natural gas, SO2 emissions from combustion of petroleum-derived fuels are curtailed, preventing acid rain.29 In the desulfurisation process, the sulfur atoms in H2S and organosulfur compounds are ultimately converted to elemental sulfur.30 Although elemental sulfur is not toxic,31 it is a flammable solid32 so finding productive uses for this stockpiled material is important. With approximately 70 million tonnes produced each year from petroleum refining,28,33 elemental sulfur is widely available and inexpensive (∼$120 USD per tonne).33 A significant portion of sulfur is used in the industrial production of sulfuric acid, and in the United States 90% of all sulfur consumption is tied to the synthesis of H2SO4.29 On a smaller scale, sulfur is used directly in the production of rubber34 and fertiliser.28 Modern synthetic chemistry has also benefitted from the versatile chemistry of elemental sulfur.35–37 Still, there is a net excess of several millions of tonnes of sulfur produced each year in petrochemical refining.29 This excess sulfur is accumulated and stored in megaton deposits, often open to the environment (Fig. 2). Finding large-scale uses for this sulfur, such as conversion to useful polymers, would be an important advance. And while any product made from this sulfur should rightly be classified as petroleum-derived, there are also well-established methods to access this abundant element directly from geological sources, should this prove necessary in the future.38 In the first instance, however, it is best to take advantage of the excess waste sulfur generated by the petroleum industry. In doing so, this by-product is repurposed for value-added applications—a clear opportunity to develop novel sulfur chemistry.
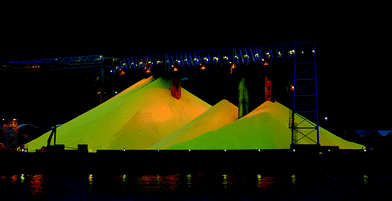 |
| Fig. 2 A stockpile of sulfur produced from the hydrodesulfurisation process in petroleum refining. Approximately 70 million tonnes of sulfur were produced in 2015 by the petroleum industry. Image credit: Gord McKenna, made available through a Creative Commons license: https://www.flickr.com/photos/gord99/5170487123/. | |
Polymers and materials made from sulfur
Given the wide availability of sulfur, there has been a resurgence in using it as a starting material for polymers and materials.38–41 In order to make polymers directly from sulfur, however, there are several challenges. The main limitation has been the instability of polysulfides42 made by the ring-opening polymerisation (ROP) of sulfur (Fig. 3).35,43 When elemental sulfur is heated above its floor temperature (159 °C), S–S bond homolysis provides thiyl radicals that attack and open the ring of another molecule of S8.43,44 The polymerisation is then propagated by repeated ring-opening and S–S bond formation between S8 and the growing polysulfide chain (Fig. 3). However, the reaction is reversible and the terminal thiyl radicals of the polysulfide can depolymerise and expel S8 or other cyclic sulfur species. Backbiting is one mechanism by which this depolymerisation may occur (Fig. 3), providing thermodynamically favoured S8 in preference to terminal thiyl radicals.43 To provide stable polysulfide polymers, the thiyl radicals must be quenched before depolymerisation. Pyun, Sung, Char and collaborators have shown that trapping the thiyl radicals with polyenes can provide a stable polymer made predominately from elemental sulfur.45 As outlined in Fig. 3, addition of the linear polymeric sulfur to polyenes results in branching of the polymeric chains. In the termination events, the thiyl radicals are thought to be quenched by at least two different mechanisms. In one case, intramolecular recombination of thiyl radicals would provide stable polysulfide loops (Fig. 3).45 In cases where H-atoms are available (e.g. allylic and benzylic hydrogen atoms from the alkene co-monomer), H-atom abstraction may convert the thiyl radical to a thiol (Fig. 3).38,46 Notably, the H-atom abstraction pathway would result in chain transfer processes that ultimately lead to increased branching at the alkene co-monomer (Fig. 3). In any case, by quenching the thiyl radicals in the polysulfide polymer, the depolymerisation is suppressed and a stable macromolecule is obtained. In classic vulcanisation, elemental sulfur is used in relatively small quantities to cross-link latex or other preformed polymers. In the so-called inverse vulcanisation in Fig. 3 (coined by Pyun, Sung, Char and collaborators),45 the alkene co-monomer is used in relatively small amounts and links together and branches the polysulfide polymers. Through inverse vuncanisation, polymers containing very high sulfur content can be obtained (typically 50–90% sulfur by mass). Of relevance to Green Chemistry, inverse vulcanisation does not require exogenous solvents or reagents in the synthesis. The sulfur and alkene are used as co-monomers and the reaction medium. Furthermore, the reaction is entirely atom economical, with all of the starting material incorporated into the product.
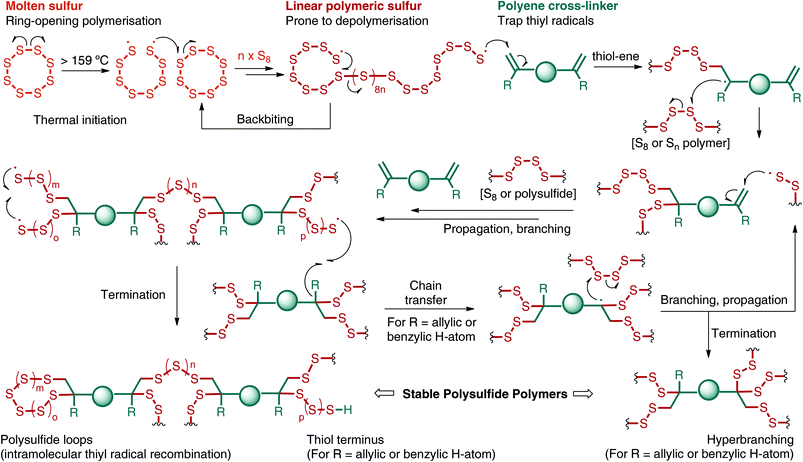 |
| Fig. 3 Mechanistic aspects of inverse vulcanisation. Sulfur is heated to a temperature at which S–S bonds undergo homolysis and generate thiyl radicals. These thiyl radicals react with sulfur (S8 or polysulfides) and alkene co-monomers. Without an alkene cross-linker, the terminal thiyl radicals are unstable and decompose (through backbiting, for instance) to reform S8. Addition of the thiyl radical to the alkene, followed by radical termination, provides stable polysulfide polymers. The termination may result in polysulfide loops by intramolecular thiyl radical recombination. Where H-atoms are available (as allylic or benzylic H-atoms, for instance) thiyl groups can be converted into thiols and chain transfer results in increased branching. | |
In Pyun's seminal report, he and his collaborators used 1,3-diisopropylbenzene (DIB, 1) as the organic cross-linker. In the event, sulfur was heated to 185 °C to initiate ring-opening polymerisation. Addition of DIB (typically at a feed ratio of 10–50 wt%) resulted in cross-linking and vitrification within minutes (Fig. 4a). The resulting red polymeric glass is referred to as poly(sulfur-random-1,3-diisopropenylbenzene), or poly(S-r-DIB). Because of the high sulfur content (typically targeted at 50–90 wt% sulfur) and the polysulfide structure of the backbone of the polymer, poly(S-r-DIB) has several interesting chemical, material, and optical properties. For instance, the poly(S-r-DIB) polysulfides are redox active and useful as next generation cathode materials for lithium–sulfur batteries, as Pyun and co-workers demonstrated in their original45 and subsequent studies.47–51 The high sulfur content also imparts a high refractive index and an IR region of transparency that is convenient for night vision, thermal imaging and other optical applications.52–54 Furthermore, the S–S crosslinks of the polysulfide are dynamic, which allows for straightforward repair of the polysulfide by thermal annealing.53,55
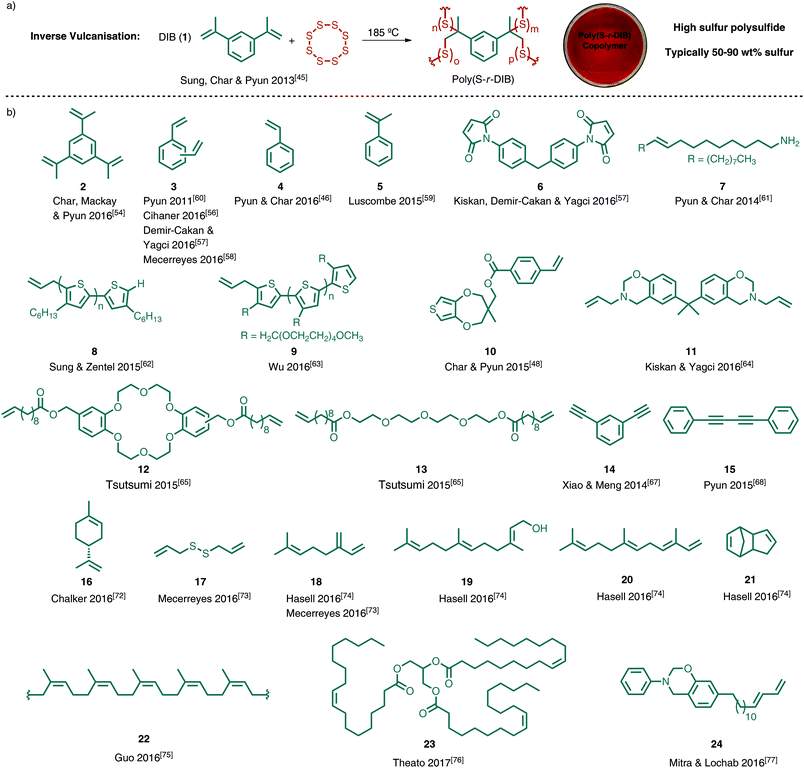 |
| Fig. 4 (a) Inverse vulcanisation of 1,3-diisopropenylbenzene (DIB) provides the polysulfide poly(sulfur-random-1,3-diisopropenylbenzene), or poly(S-r-DIB).45 The polymer can be processed, moulded and cured in a variety of architectures. The image of the poly(S-r-DIB), cured in a petri dish, was adapted with permission from ref. 55. Copyright 2014 American Chemical Society. (b) A selection of unsaturated cross-linkers used for inverse vulcanisation and related reactions used to access polysulfide polymers. The corresponding authors and the associated citations are indicated for reference. | |
These creative contributions from Pyun and co-workers have since inspired further exploration of inverse vulcanisation with a variety of unsaturated cross-linkers to obtain polysulfides with complementary properties (Fig. 4). Pyun and associates showed, for instance, that inverse vulcanisation using triene 2, provides a polysulfide with improved thermomechanical properties in the form of a higher glass transition temperature (over 100 °C) than the first generation poly(S-r-DIB) which possessed a Tg of 43–49 °C.54 In other studies, inverse vulcanisation with divinylbenzene (DVB, 3),56–58 styrene (4),46 and α-methylstyrene (5),59 demonstrated that traditional and widely available monomers for radical polymerisation can also be converted into polysulfides. In the case of DVB, the synthesis of the corresponding polysulfides was informed by early studies in the Pyun laboratory in 2011 when sulfur was used as a reaction medium to prepare gold nanoparticles and related composites. In this prescient study, sulfur was cross-linked with DVB.60 The more recent DVB polysulfides, prepared by inverse vulcanisation, could be fashioned into a highly IR transparent thin film,56 or used as a cathode material for Li–S batteries.58 The co-polymerisation of sulfur, DVB, and bis-maleimide 6 also provided a novel cathode material for Li–S cells.57 In the case of styrene, important mechanistic aspects of the polymerisation were revealed in the inverse vulcanisation. Specifically, chain transfer reactions can occur after thiyl radicals abstract the benzylic hydrogen atom available after styrene is incorporated into the polysulfide (see Fig. 3 for related processes). The chain transfer results in branching—despite styrene having only one alkene—and provides a stable polysulfide that is resistant to depolymerisation.46 The resulting polymers were further tested for their potential as cathodes. For α-methylstyrene, the resulting polysulfide was used as a reaction medium for CdS nanoparticle synthesis. This was possible because the polysulfide derived from 5 was a liquid at the temperature of the CdS synthesis (200 °C). The CdS nanoparticles formed could then be isolated by centrifugation after dissolving the polysulfide in chloroform.59 These studies by Luscombe built upon prior work in nanoparticle composite preparation by Pyun60 and Char61 in which liquid sulfur and polysulfides formed from DVB60 or oleylamine (7)61 provided a matrix for the synthesis of gold and PbS nanoparticles.
To improve the prospects of polysulfides as cathode materials, several polymers have been prepared by inverse vulcanisation that contain polythiophene cross-linkers that overcome the high resistivity of sulfur. For example, polythiophenes such as 8 and 9 contain alkene end groups that can be cross-linked by inverse vulcanisation.62,63 An alternative approach features monomer 10 in which the inverse vulcanisation is carried out first, with a second-stage electrochemical oxidation of the polysulfide providing the target polythiophene polymer.48 This tandem and orthogonal polymerisation strategy is notable not only for its entry to polythiophenes after inverse vulcanisation, but also for the manner in which it installs complementary and distinct polymer backbones. Such sequential cross-linking has also been studied by Kiskan and Yagci using monomer 11. In this report, inverse vulcanisation of 11 was followed by ring-opening polymerisation of the oxazine to provide polysulfide phenolic networks reinforced by both polysulfide branching and polybenzoxazine cross-linking.64
Dienes 12 and 13 were also used to form polysulfides, with further testing as cathode materials in Mg–S and Li–S cells.65,66 The polyether groups were proposed to increase ion mobility of the magnesium or lithium ions. Other studies toward novel cathode materials also revealed that poly-alkynes are suitable monomers for the synthesis of polysulfides. Alkyne 14 provides highly crosslinked polysulfides in which thiyl radicals of the growing polysulfide can add multiple times to the alkyne carbons.67 In the case of di-yne 15, addition of sulfur to the alkynes ultimately provides a thiophene derivative that is cross-linked through polysulfide linkages.68
It should also be noted that while alkene and alkyne cross-linkers are highlighted in Fig. 4, other functional groups react with sulfur in which alternative mechanisms are operative in the inverse vulcanisation. For instance, Park has illustrated how polythiols such as trithiocyanuric acid can be used to prepare sulfur-rich polymers by reaction with elemental sulfur.69 Coskun and Choi have also explored aromatic thiol cross-linkers in inverse vulcanisation.70 The same laboratories also described a unique cross-linking mechanism in which thiyl radicals of the polysulfide chain insert into aromatic C–H bonds.70,71 These materials were tested further as cathodes for Li–S batteries.69–71
In the survey of unsaturated cross-linkers for inverse vulcanisation discussed so far, many are relatively valuable fine chemicals. Other than the monomers 3–5, which are available in bulk quantities because of their use in traditional polymerisations, alkenes 1–15 in Fig. 4 are comparatively expensive, require multiple steps to prepare, or are simply not available in the multi-kilogram quantities required for bulk polymer synthesis. These features may be irrelevant for high-end applications where monomer cost and raw material supply are not primary considerations. Also, it is entirely possible that increasing demand for these cross-linkers, and their polysulfides, could lead to bulk production and lower cost. These future prospects aside, there is still a mismatch in scale and supply of these co-monomers when compared to sulfur, which is available in multi-million tonne quantities. It is therefore worthwhile to consider other co-monomers for inverse vulcanisation that are available on large scale as either industrial by- or co-products or renewable feedstocks from biological sources. In considering such co-monomers for inverse vulcanisation, the excess sulfur produced industrially can be productively consumed. This strategy also draws strong links to the principles of Green Chemistry by using industrial by-products and renewable feedstocks as the sole materials in the synthesis of valuable polymers. Monomers 16–24 were explicitly chosen for use in inverse vulcanisation because they address this overarching goal of sustainability.72–78 The resulting polysulfides have also been employed in applications that benefit the environment, such as environmental remediation and sustainable energy technologies. These polysulfides, and their applications in Green Chemistry, are discussed in more detail in the next two sections.
Polysulfides for environmental protection and remediation
Using sulfur as a monomer aligns with several principles of Green Chemistry in that its polymerisation benefits from excellent atom economy and does not require solvent. Furthermore, because sulfur is a by-product of the petroleum industry, using it as a starting material is an advance in waste valorisation. The environmental benefits are compounded when sulfur is co-polymerised with a renewable olefin and the resulting polymer is used in pollution monitoring and remediation. Specifically, the high sulfur content of these polysulfides is expected to impart affinity for soft Lewis acids, such as certain heavy metals. But, in contrast to elemental sulfur, the polysulfide polymers have the capacity to be processed into forms that confer mechanical, chemical and thermal properties that are complementary or superior to elemental sulfur.
Our lab contributed in this regard with the development of a polysulfide made from elemental sulfur and D-limonene (Fig. 5a).72 The D-limonene monoterpene (16) is found in the zest of citrus fruit and is produced on the order of 70
000 tonnes per year in the citrus industry through steam distillation of the non-edible peel.79 By simply reacting sulfur with D-limonene using an inverse vulcanisation protocol, a polysulfide wax was formed that was effective in capturing palladium and mercury salts.72
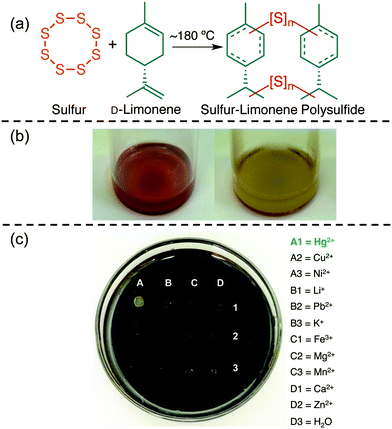 |
| Fig. 5 (a) A polysulfide made from elemental sulfur and D-limonene. (b) The limonene polysulfide changes colour from dark red to yellow upon binding to mercury(II) and removing it from water. (c) The chromogenic response to mercury(II) is selective among the metals screened in the study. These images are reproduced with permission from the authors and ref. 72 under a Creative Common License. | |
Palladium is a valuable catalyst in a variety of organic transformations,80,81 and its recovery from waste streams is desirable. More recently palladium has been identified as a pollutant leached from catalytic converters by automobile exhaust.82 The capture of palladium therefore confers both economic and environmental benefits, so it is valuable to know that polysulfides can be used to recover this transition metal.
Mercury is a highly toxic metal that is encountered in a variety of industrial activities such as oil and gas refining, coal combustion and artisanal and small-scale gold mining.83 Exposure to mercury can lead to serious health problems, including debilitating neurological and embryotoxic effects.84 The remediation of mercury pollution is therefore essential in protecting the environment and human health. For these reasons, it was encouraging that the limonene polysulfide was effective in removing highly toxic mercury(II) from water.72 The mercury removal was even suitable for remediating pond water littered with silt and other debris.72 Upon capture of the mercury(II), the polysulfide underwent a colour change from dark red to yellow—revealing an additional (and unexpected) sensing capability of the material (Fig. 5b). The chromogenic response was selective for mercury(II) among the metals investigated in this report (Fig. 5c).72
The Green Chemistry aspects in this limonene polysulfide synthesis are worth noting. The synthesis does not require exogenous reagents or solvents, it requires only limonene and sulfur.72 Like the majority of inverse vuncanisations, the synthesis of the limonene polysulfide is highly atom-economical, though some small molecule by-products such as p-cymene were produced.72 Furthermore, both co-monomers can be considered by- or co-products of industrial processes, so this is an example of a value-added material made entirely from re-purposed waste.
Building upon the use of polysulfides in mercury capture, Hasell and co-workers85 studied both the limonene polysulfide72 and Pyun's poly(S-r-DIB) co-polymer45 in the removal of mercury(II) chloride from water. Their team found the active surface of the limonene polysulfide, due to its soft waxy nature, can actually be regenerated by the mechanical force of stirring.85 More impressively, the authors disclosed a method to form polysulfide foams from the polymers using supercritical carbon dioxide.85 The foam dramatically increases the surface area and the polymer's ability to capture mercury(II) from water (Fig. 6). For instance, a foam prepared from Pyun's poly(S-r-DIB) was able to reduce the concentration of mercury(II) in water from 2000 ppb to ∼80 ppb after a 3 hour incubation. Translation to a continuous process was also demonstrated where the polysulfide foam was packed into a column as a solid adsorbent for water purification.85
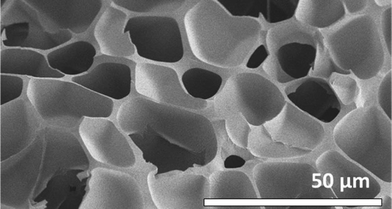 |
| Fig. 6 A porous version of poly(S-r-DIB) was prepared by foaming with supercritical CO2. This material was effective in removing mercury salts from water. The image was adapted from ref. 85 with permission from the Royal Society of Chemistry. | |
The Hasell laboratory has since extended these foams to polysulfides made from the reaction of sulfur with the low cost, industrially produced monomer dicyclopentadiene (21) and renewable terpenes such as myrcene (18), farnesol (19) and farnesene (20).74 Again the high surface area imparted by supercritical carbon dioxide foaming or using sodium chloride as a porogen allowed efficient sequestration of inorganic mercury from water. In this study, the authors deliberately explored renewable alkene cross-linkers so the preparation of the polysulfides is imminently scalable and sustainable—a necessary requirement for applications in environmental protection and remediation.
Another effective method for imparting high surface area to polysulfide polymers is electrospinning.86,87 Theato and co-workers recently demonstrated for the first time that polysulfides prepared by inverse vulcanisation, such as poly(S-r-DIB), are compatible with electrospinning.88 Using a carrier polymer such as high molecular weight poly(methyl methacrylate) proved important in accessing uniform fibres with diameters on the order of 1 micron (Fig. 7).88
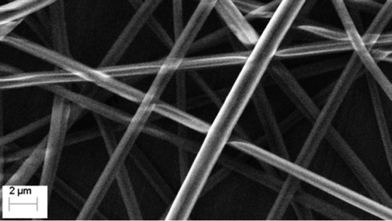 |
| Fig. 7 Electrospinning a blend of poly(S-r-DIB) and poly(methyl methacrylate) provides uniform fibres with very high surface area. The fibres showed excellent performance in capturing water soluble mercury. Adapted from ref. 88 under a Creative Commons License. | |
The high surface area of these fibres was beneficial in mercury uptake studies in which an impressive 98% of mercury(II) could be removed in just a few seconds from water containing 20 ppm HgCl2. The authors also demonstrated a higher affinity of the polysulfide fibres for Hg2+ than for other metals ions examined (Cd2+, Co2+, Cu2+, Fe3+, Pb2+, and Zn2+).88 The rapid binding to mercury and high distribution coefficients (Kd) on the order of 105 mL g−1 bode well for applications of electrospun polysulfides in water filtration devices.
The polysulfide polymers prepared by inverse vulcanisation can be further converted to porous carbon materials.89 The Hasell laboratory showed that heating the polysulfides at 750 °C in a furnace under a flow of argon leads to the thermal extrusion of sulfur and sulfurous by-products—some of which, the authors note, could be recycled and re-used. The remaining carbonised product is porous and doped with between 7 and 14% sulfur—a value independent of the amount of sulfur in the original polysulfide.89 The authors further characterised the gas sorption properties for their porous carbonaceous materials made from both Pyun's poly(S-r-DIB) and Chalker's sulfur-limonene polysulfide.89 Remarkably, these porous materials were complementary in their gas adsorption selectivity. The carbon derived from the poly(S-r-DIB), for instance, was microporous and readily adsorbed nitrogen and carbon dioxide. In contrast, the porous carbon derived from the sulfur-limonene polysulfide occluded nitrogen, but readily adsorbed hydrogen and carbon dioxide.89 Porous materials are widely used in a variety of industrial separations and environmental applications,90 such as gas separations,91 carbon dioxide sequestration,92,93 oil spill cleanup,94 waste treatment,95,96 and water purification.97 The authors also explicitly point out that the synthesis of polysulfides by inverse vulcanisation is atom-economical, solvent free, and makes use of industrial by-products such as sulfur and limonene.89 Therefore, Hasell's work constitutes an important advance not only in waste valorisation and sustainable material synthesis, but also how such materials can be tailored for environmentally focussed end uses.
Polysulfides for sustainable energy production and storage
Sustainable energy production and storage are two of the greatest challenges facing our species.98,99 And while it is still an exploratory period for polysulfides, several studies using these high sulfur content materials have revealed promising results in energy generation and battery research.
Liu, Gardner and Kloo, for instance, recently demonstrated that polysulfides prepared by inverse vulcanisation work as hole-transport materials in solid-state dye-sensitised solar cells.100 Using poly(S-r-DIB) at 50% sulfur by weight, the authors demonstrated a power conversion efficiency of 1.5%. While this result is modest in comparison to high-performance dye-sensitised solar cells, the very low cost of the sulfur polymer will likely lead to further studies to improve its performance in generating power from sunlight.
Polysulfides prepared by inverse vulcanisation have also been used in the photochemical generation of hydrogen fuel. Zhang and co-workers prepared poly(S-r-DIB) as nanowires and explored their use in the photochemical splitting of water with visible light to generate hydrogen, a clean-burning fuel.101 The nanowires were prepared using an anodic aluminium oxide membrane as a template, in which poly(S-r-DIB) was synthesised and cured. The template was removed by etching with sodium hydroxide, providing the polysulfide nanowires. The photocatalytic activity of these polysulfide nanowires was superior to bulk sulfur, a feature attributed in part to their high surface area. This study is an important report of the ways in which inexpensive sulfur can be converted into a valuable catalyst that can harness visible light for the generation of clean fuels.
In a third area of energy research featuring polysulfides, polymers prepared by inverse vulcanisation have been intensely studied as next-generation cathode materials for batteries. Because many forms of sustainable energy production are intermittent (e.g. solar and wind power), high performance energy storage is required.99 Because Li–S cells have a theoretical capacity and power density that exceeds current Li-ion technology, and sulfur is very inexpensive, there has been intense interest in developing practical Li–S cells.102,103 The original report on inverse vulcanisation by Pyun and associates explored, among other things, the use of their poly(S-r-DIB) polymers as cathode materials.45 One of the main objectives was to determine if their sulfur–DIB co-polymers could address the rapid capacity loss and short cycle lifetimes of typical Li–S cells. Indeed the authors found that poly(S-r-DIB) at 90 wt% sulfur and 10 wt% DIB displayed superior capacity to sulfur over hundreds of cycles.38,45,47,49 Specific capacities on the order of 1000 mA h g−1 over 100 cycles are especially encouraging.47 A key to this success is the polysulfide's ability to suppress lithium sulfide deposits on the cathode and protect it against mechanical wear.38
Since these reports,45,47,49 many more studies have emerged in which inverse vulcanisation and related processes are used to prepare cathode materials and other composites with high sulfur content.46,48,50,51,57,58,62,63,65–71,73,75–78,104–109 Rather than reiterate these achievements here, we instead highlight some recent efforts where renewable alkenes were used in the inverse vulcanisation. In this way, the cathode materials can be prepared entirely from waste and renewable resources, thereby raising their Green Chemistry profile. Theato, for example, prepared polysulfides from plant trigycerides (linseed oil, sunflower oil, and olive oil) and sulfur in an inverse vulcanisation procedure.76 A simplified structure of the triglyceride monomer (23) is shown in Fig. 4. And while oleic acid is shown as the fatty acid in 23, it should be noted that polyunsaturated linoleic acid is also a major component of these triglycerides.76 The resulting material was a polysulfide rubber containing embedded particles of free sulfur. The materials were studied as cathode materials for “green Li–S batteries.”76 Encouragingly, the authors discovered high initial specific capacities (880 mA h g−1) and established a benchmark in capacity retention for these green materials over 100 cycles (63%). In a similar effort, Mecerreyes and co-workers explored the inverse vulcanisation of the renewable alkenes diallyl disulfide and myrcene, derived from alliums and thyme, respectively.73 Subsequent electrochemical tests demonstrated the use of the polysulfides as cathode materials for Li–S batteries.73 Initial capacities of 770 mA h g−1 and 790 mA h g−1 were measured for the diallyl disulfide and myrcene polysulfides, respectively, with a capacity retention of about 80%.
Renewable monomers 22 and 24 have also been reported recently in inverse vulcanisation, with further electrochemical testing. Polyisoprene 22, for instance, can be converted to a polysulfide very similar to vulcanised rubber, but with higher sulfur content necessary for use as a cathode.75 Importantly 22 is a renewable polyene. similarly, 24 is interesting in that it is derived in part from an agricultural waste material, cardanol, and therefore provides an advance in waste valorisation as well as a contribution to sustainable power storage materials.77,78
The merger of waste sulfur and renewable plant oils to access polysulfides is an important effort in sustainable synthesis. Furthermore, the polysulfides are useful in a variety of applications that benefit the environment. In particular, these materials have been demonstrated to be effective in power generation and storage, photocatalysis for the production of clean fuels, and sequestration of heavy metal pollution. These green applications are summarised in Fig. 8.
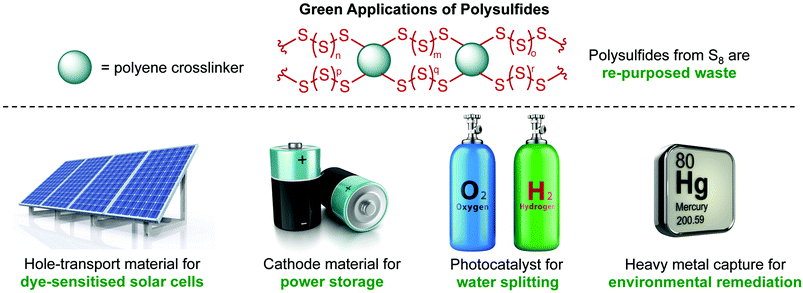 |
| Fig. 8 Polysulfides prepared by inverse vulcanisation have been explored in diverse areas of sustainability including power generation, power storage, photocatalytic water splitting, and environmental remediation. Graphics of solar panels, batteries, gas cylinders, and mercury symbol were licensed from 123RF.com, with image credit to Michael Rosskothen, mrgao, Oleksandr Marynchenko, and 3dalia, respectively. Copyright 123RF.com. | |
Green chemistry outlook for sulfur polymers
The sustainable synthesis of polymers and functional materials is critical for our future. Among the diverse efforts toward this goal, polymers made from sulfur have emerged as a new class of materials useful in several applications. Because sulfur can be considered a by-product of the petroleum industry, the preparation of high sulfur polymers is an innovative example of waste valorisation. Furthermore, the syntheses of sulfur polymers typically benefit from high atom economy and often require no solvent—two ways in which they align with priorities of Green Chemistry. Further benefits to the environment come from preparing these polymers through the co-polymerisation of sulfur and renewable alkenes such as terpenes and triglycerides. Additionally, several recent reports were discussed in which these polysulfide materials were used to capture heavy metal pollution, and generate and store power. In this way, the synthesis and application of polymers made from sulfur provides a broad platform for sustainable science and technology. In order to realise the full benefit of these features, however, there are several challenges on the horizon. We outline these challenges and opportunities to help motivate future research in the Green Chemistry of polymers made from sulfur.
Controlled polymerisation of sulfur at low temperature
The microstructure of polysulfides prepared by inverse vulcanisation can be controlled in part by simply varying the feed ratio of sulfur to alkene.38 Higher levels of sulfur result in longer stretches of catenated sulfur atoms (higher sulfur rank), while lower levels provide shorter stretches of sulfur atoms between the alkene co-monomer (lower sulfur rank). This feature allows some control over the level of crystallinity, as higher levels of sulfur in the polysulfide result in more crystalline polymers. Nonetheless, inverse vulcanisation still provides a statistical distribution of polysulfide microstructures. It could be advantageous, perhaps, to devise alternative polymerisation conditions in which the sulfur rank, cross-linking, molecular weight and polydispersity can be better controlled. Such control would benefit fundamental studies in how specific polysulfide structures affect their function. In Green Chemistry, for instance, control over the polysulfide structure would allow the preparation of materials with optimised electrochemical properties for power generation and storage, or optimal structures for binding a particular heavy metal pollutant. While devising methods for the controlled polymerisation of sulfur are a task for future research, there have been some notable efforts to use reversible addition–fragmentation chain transfer (RAFT) to control the rate of inverse vulcanisation.108 This strategy also provides a polysulfide with dormant RAFT groups ligated to the polymer, presenting further opportunities for post-synthetic functionalisation.108 These early steps in controlling the polymerisation of sulfur will help guide future efforts to exact more control of polysulfide structure.
Limited control of inverse vulcanisation is due, in part, to high temperatures employed in the polymerisation (typically 160 to 200 °C). These temperatures likely lead to random and equilibrated microstructures, due to thermal scission and recombination of S–S bonds in the polysulfide backbone. The high temperatures could also lead to side reactions such as undesired H-atom abstraction, chain transfer, or oxidation. When limonene is used as the alkene cross-linker, for instance, its oxidation by sulfur to p-cymene was an undesired side reaction.72 The high temperatures used for inverse vulcanisation also necessitate energy input that violates a principle of Green Chemistry. It is therefore worth identifying alternative methods for polymerising sulfur at lower temperatures. In doing so, energy input would be reduced, side reactions may be suppressed, and it is likely that more control could be exerted over the polymerisation. To achieve this aim in radical polymerisation of sulfur, it is likely that alternative methods of initiation will be required, as well as a suitable solvent or form of sulfur that is miscible with the co-monomer or reaction medium. It may be the case that entirely different mechanisms of polymerisation are required. For instance, ionic condensation polymerisation of polysulfides and haloalkanes proceeds efficiently at 30 °C.110
The ability to carry out polymerisations of sulfur at lower temperature will also allow a far greater range of alkene cross-linkers to be used in the reaction. Using the standard inverse vulcanisation protocol, the alkene typically requires a relatively high boiling point. In Fig. 4, for instance, most of the alkenes have a boiling point higher than 160 °C. Of these co-monomers, styrene has the lowest boiling point at 145 °C. If the radical polymerisation of sulfur can be carried out at lower temperatures, alkenes with lower boiling points could then be readily employed as co-monomers. As the material properties of the polysulfide also depend on the alkene, this is an important way in which complementary materials can be accessed. Even the relatively small panel of alkenes in Fig. 4 illustrate this point: inverse vulcanisation with 1 provides a glass,45 while 16 provides a wax72 and 23 a rubber.76
Green solvents for polysulfide synthesis and processing
While inverse vulcanisation can be executed under solvent free conditions (i.e. the unsaturated cross-linker is reacted with molten sulfur and polysulfide pre-polymers), it is worth considering what green solvents are available for both polysulfide synthesis and processing. In the relatively few solution-phase syntheses of polysulfides by inverse vulcanisation, non-green organic solvents such as o-dichlorobenzene,63 pyridine111 and carbon disulfide67 have been used because of their relatively high boiling points and ability to solvate sulfur. Likewise, in experiments that required manipulation of polysulfide polymers in solution (such as casting polysulfides into thin films or electrospinning polysulfide solutions), non-green solvents such as dimethylformamide,69,88 acetonitrile,77 tetrahydrofuran,61,77,88 and 1,2-dichlorobenzene,52 were used. It is therefore worthwhile to identify safe, sustainable and biodegradable solvents suitable for the synthesis and manipulation of sulfur polymers. The limited solubility of sulfur and sulfur-rich polymers, as well as the high reaction temperatures typically used in inverse vulcanisation, make this a largely unmet challenge.
Notably, a few reports have integrated green solvents into the processes involving sulfur polymers. Pyun, Char and co-workers, for instance, have made progress in interfacial condensation polymerisations in water, studying inorganic polysulfides (NaS-[S]n-SNa, derived from sodium sulfide and elemental sulfur) and their reaction with 1,2,3-trichloropropane.110 The polymer products presented as nanoparticles containing above 75% sulfur by mass. While this polymerisation is mechanistically distinct from inverse vulcanisation, it is a clear demonstration of converting elemental sulfur into polymers in a safe and relatively green aqueous solvent. Importantly, even though the polymer particles were not soluble in water, they could be processed as dispersions.
For polysulfide processing, super critical carbon dioxide has been explored by Hasell and co-workers in the preparation of polysulfide foams, as described previously and shown in Fig. 6.74,85 In addition to establishing a route to high surface area polysulfides, Hasell's work illustrated that super critical carbon dioxide can innervate and swell polysulfides—perhaps providing a lead for further studies in solvating polysulfide melts or pre-polymers. As supercritical carbon dioxide is recognised as a relatively green solvent for polymer processing,112 its use in the manipulation of polysulfides is encouraging.
Outside of these few studies, the integration of green solvents with sulfur polymer synthesis and processing is limited. There is clearly an opportunity for further progress in identifying green solvents for sulfur polymer chemistry.
Toxicity of polysulfides
A central tenet of Green Chemistry is the design of safer chemicals. While elemental sulfur is non-toxic, little is known about the toxicity of polysulfide polymers. For the polysulfide prepared using sulfur and limonene,72 it was shown by our team and collaborators that nothing toxic was leached from the material into water, as indicated by cell viability assays of HepG2 and Huh7 liver cells. This result was used as motivation to explore these polysulfides for water purification in both natural waterways and in municipal water systems—research that is ongoing in our lab. Other than these relatively simple tests, there have not been additional toxicity studies on polymers prepared by inverse vulcanisation. It is likely that the toxicological profile will vary based on the organic cross-linker and its products of biodegradation. As this information becomes available, it will help guide the use of these polymers in environmental and biological applications.
Biodegradability of polysulfides
The persistence of polymers in the environment is cause for concern.113 A future line of research in the biodegradability of sulfur polymers is therefore worth considering. The mechanism of degradation will likely depend on both the polysulfide stability and the organic cross-linker. For instance, the S–S bonds of polysulfides are susceptible to reduction and photolysis, so polysulfide polymers might be degraded by reductases found in living organisms or after long-term exposure to sunlight. Additionally, by using cross-linkers that contain labile groups, biodegradability can be programmed into polysulfides. Polyenes 10, 12, 13, and 23, for instance, contain esters that can hydrolyse—perhaps slowly upon exposure to water or at the provocation of esterases. It remains to be seen whether these reactions are efficient, and if the products of degradation are ecologically innocuous, but the chemical lability of polysulfides could potentially be leveraged in the preparation of polymers with programmed lifetimes and biodegradability.
Recycling polysulfides
Consideration of polymer lifetime also prompts investigation of recycling methods. Unlike traditional polyolefins, which contain a very stable backbone of carbon–carbon bonds, polysulfides are comprised of relatively labile S–S bonds. It is therefore intriguing to consider ways in which polysulfides produced on an industrial scale could be depolymerised back to re-usable monomers or oligomers. Such a process does not necessarily have to provide S8 and the original alkene, but only a suitable precursor to other polysulfide polymers. Relatedly, polysulfides may be amendable to repair or restructuring by virtue of dynamic S–S bonds. Reports in thermal healing of fractured poly(S-r-DIB) bode well for such strategies.53,55
Commercial use and scalability
Commercial and industrial uptake of polysulfide materials prepared by inverse vulcanisation is required for wide impact in Green Chemistry. Otherwise, the applications in Fig. 8 will be confined to the research laboratory. One technical hurdle that will need to be overcome is the large-scale preparation of high-sulfur polysulfides (>50% sulfur) by inverse vulcanisation. As classic vulcanisation has long been used for the commercial production of rubber, factice, ebonite, and other sulfur-rich materials (typically containing up to 30% sulfur by mass),34 this challenge seems surmountable. Moreover, kilogram scale inverse vulcanisations have been reported.49 Yet, it is possible that commercial applications in energy and environmental protection would require hundreds of kilograms or even tonnes of polymer. In meeting such demand, the complex thermodynamics and changes in viscosity during inverse vulcanisation would make even pilot-scale batch processing a challenge. Therefore, it may be necessary to develop continuous processes for polysulfide production in which the scale of the reaction at any given time is relatively small, but sustained or parallel operation provides several kilograms of polymer or pre-polymer per hour. In one form, this may involve the direct polymerisation of sulfur and the alkene in an extruder. This reactive extrusion process would provide the polysulfides on a large scale and likely benefit from a superior safety profile when compared to batch methods.
Targeting problems of scale
In several parts of this Perspective it was argued that making polymers from elemental sulfur constitutes waste valorisation. The excess sulfur produced from petroleum refining demands such efforts. However, this excess sulfur problem will not be seriously addressed by inverse vulcanisation unless commercial production of polysulfides proves viable. It is therefore worthwhile considering sectors of the economy that would benefit from industrial production of polysulfides made from low-cost alkenes and elemental sulfur. Likewise, the potential benefits in Green Chemistry will only have impact if such polysulfides are deployed in applications and problems of immense scale. Several of these areas have been mentioned already, with power generation, power storage, water and air purification, and environmental remediation likely requiring industrial scale polysulfide production for serious impact. Other areas such as construction and agriculture may also benefit from an industrial supply of inexpensive polysulfides, so there are ample opportunities for future research to benefit these sectors. In our own efforts, we are aiming to devise new and versatile sulfur polymers—made entirely from renewables and industrial waste—that benefit the environment and align with values and priorities of Green Chemistry.
Acknowledgements
The authors thank Flinders University, the Australian Research Council, and the Australian National Environmental Science Program Emerging Priorities Funding for generous support of their research program.
References
- M. Ulbricht, Polymer, 2006, 47, 2217–2262 CrossRef CAS
.
- M. T. M. Pendergast and E. M. V. Hoek, Energy Environ. Sci., 2011, 4, 1946–1971 CAS
.
-
Biomaterials Science: An Introduction to Materials in Medicine, ed. B. D. Ratner, A. S. Hoffman, F. J. Schoen and J. E. Lemons, Elsevier, Amsterdam, 3rd edn, 2013 Search PubMed
.
- S. Agarwal, J. H. Wendorff and A. Greiner, Polymer, 2008, 49, 5603–5621 CrossRef CAS
.
- F. Vilela, K. Zhang and M. Antonietti, Energy Environ. Sci., 2012, 5, 7819–7832 CAS
.
- E. Serrano, G. Rus and J. García-Martínez, Renewable Sustainable Energy Rev., 2009, 13, 2373–2384 CrossRef CAS
.
-
A. Correia Diogo, in Materials for Construction and Civil Engineering: Science, Processing and Design, ed. M. C. Gonçalves and F. Margarido, Springer International Publishing, Switzerland, New York, 2015, pp. 447–499 Search PubMed
.
- P. Bujak, I. Kulszewicz-Bajer, M. Zagorska, V. Maurel, I. Wielgus and A. Pron, Chem. Soc. Rev., 2013, 42, 8895–8999 RSC
.
- E. P. Tomlinson, M. E. Hay and B. W. Boudouris, Macromolecules, 2014, 47, 6145–6158 CrossRef CAS
.
- W. Weng, P. Chen, S. He, X. Sun and H. Peng, Angew. Chem., Int. Ed., 2016, 55, 6140–6169 CrossRef CAS PubMed
.
- P. J. Rivero, A. Urrutia, J. Goicoechea and F. J. Arregui, Nanoscale Res. Lett., 2015, 10, 1–22 CrossRef CAS PubMed
.
- Z. L. Wang, ACS Nano, 2013, 7, 9533–9557 CrossRef CAS PubMed
.
- I. Armentano, M. Dottori, E. Fortunati, S. Mattioli and J. M. Kenny, Polym. Degrad. Stab., 2010, 95, 2126–2146 CrossRef CAS
.
- E. A. Jackson and M. A. Hillmyer, ACS Nano, 2010, 4, 3548–3553 CrossRef CAS PubMed
.
- Plastics—the Facts 2016. An analysis of European plastics, production, demand and waste data. PlasticsEurope and the European Association of Plastics Recycling and Recovery Organisations. 2016. http://www.plasticseurope.org/documents/document/20161014113313-plastics_the_facts_2016_final_version.pdf accessed 27 December 2016.
- P. Anastas and N. Eghbali, Chem. Soc. Rev., 2010, 39, 301–312 RSC
.
- M. A. R. Meier, J. O. Metzger and U. S. Schubert, Chem. Soc. Rev., 2007, 36, 1788–1802 RSC
.
- Y. Zhu, C. Romain and C. K. Williams, Nature, 2016, 540, 354–362 CrossRef CAS PubMed
.
- R. A. Sheldon, Green Chem., 2005, 7, 267–278 RSC
.
- R. A. Sheldon, J. Mol. Catal. A: Chem., 2016, 422, 3–12 CrossRef CAS
.
- D. Esposito and M. Antonietti, Chem. Soc. Rev., 2015, 44, 5821–5835 RSC
.
- A. Gandini, T. M. Lacerda, A. J. F. Carvalho and E. Trovatti, Chem. Rev., 2016, 116, 1637–1669 CrossRef CAS PubMed
.
-
J. H. Clark and A. S. Matharu, in Issues in Environmental Science and Technology: Waste as a Resource, ed. R. E. Hester and R. M. Harrison, Royal Society of Chemistry, 2013, 37, pp. 66–82 Search PubMed
.
- T. Mekonnen, P. Mussone and D. Bressler, Crit. Rev. Biotechnol., 2016, 36, 120–131 CrossRef CAS PubMed
.
- A. Goeppert, M. Czaun, J.-P. Jones, G. K. Surya Prakash and G. A. Olah, Chem. Soc. Rev., 2014, 43, 7995–8048 RSC
.
- R. S. Boethling, E. Sommer and D. DiFiore, Chem. Rev., 2007, 107, 2207–2227 CrossRef CAS PubMed
.
- R. A. Gross and B. Kalra, Science, 2002, 297, 803–807 CrossRef CAS PubMed
.
-
G. Kutney, Sulfur: History, Technology, Applications & Industry, ChemTec Publishing, Toronto, 2nd edn, 2013 Search PubMed
.
-
J. A. Ober, Materials Flow of Sulfur, Open-File Report 02–298. 2003, U.S. Department of the Interior, U.S. Geological Survey. https://pubs.usgs.gov/of/2002/of02-298/ accessed 27 December 2016.
-
E. Jüngst and W. Nehb, in Handbook of Heterogeneous Catalysis, ed. G. Ertl, H. Knozinger, F. Schüth and J. Weitkamp, Wiley-VCH Verlag GmbH & Co. KGaA, 2008, pp. 2609–2623 Search PubMed
.
- Reregistration Eligibility Document Facts: Sulfur. U.S. Environmental Protection Agency, Pesticides and Toxic Substances. May 1991. https://archive.epa.gov/pesticides/reregistration/web/pdf/0031fact.pdf accessed 27 December 2016.
- B. P. Kolodji, Process Saf. Prog., 1993, 12, 127–131 CrossRef CAS
.
- Mineral Commodity Summaries 2016. U.S. Department of the Interior, U.S. Geological Survey, 2016, 165-166. https://minerals.usgs.gov/minerals/pubs/mcs/ accessed 27 December 2016.
-
Rubber Basics, ed. R. B. Simpson, Rapra Technology Ltd., Shawbury, UK, 2002 Search PubMed
.
-
R. Mayer, in Organic Chemistry of Sulfur, ed. S. Oae, Plenum Press, New York, 1977, pp. 33–69 Search PubMed
.
- K. Wang, M. Groom, R. Sheridan, S. Zhang and E. Block, J. Sulfur Chem., 2013, 34, 55–66 CrossRef CAS
.
- O. Illa, M. Namutebi, C. Saha, M. Ostovar, C. C. Chen, M. F. Haddow, S. Nocquet-Thibault, M. Lusi, E. M. McGarrigle and V. K. Aggarwal, J. Am. Chem. Soc., 2013, 135, 11951–11966 CrossRef CAS PubMed
.
- J. J. Griebel, R. S. Glass, K. Char and J. Pyun, Prog. Polym. Sci., 2016, 58, 90–125 CrossRef CAS
.
- J. Lim, J. Pyun and K. Char, Angew. Chem., Int. Ed., 2015, 54, 3249–3258 CrossRef CAS PubMed
.
- A. Hoefling and P. Theato, Nachr. Chem., 2016, 64, 9–12 CrossRef CAS
.
- D. A. Boyd, Angew. Chem., Int. Ed., 2016, 55, 15486–15502 CrossRef CAS PubMed
.
- Here, we refer to polysulfides as materials that contain multiple stretches of sulfur atoms linked together through S–S bonds. We also take this definition to include materials where non-sulfur cross-linkers covalently connect networks of [S]n of various rank, where n ≥ 2. The key feature of polysulfide co-polymers in this context is the presence of multiple sulfur atoms that link together organic co-monomers.
- B. Meyer, Chem. Rev., 1976, 76, 367–388 CrossRef CAS
.
- S. J. Kennedy, J. C. Wheeler, C. Osuch and E. Wasserman, J. Phys. Chem., 1983, 87, 3961–3966 CrossRef CAS
.
- W. J. Chung, J. J. Griebel, E. T. Kim, H. Yoon, A. G. Simmonds, H. J. Ji, P. T. Dirlam, R. S. Glass, J. J. Wie, N. A. Nguyen, B. W. Guralnick, J. Park, Á. Somogyi, P. Theato, M. E. Mackay, Y.-E. Sung, K. Char and J. Pyun, Nat. Chem., 2013, 5, 518–524 CrossRef CAS PubMed
.
- Y. Zhang, J. J. Griebel, P. T. Dirlam, N. A. Nguyen, R. S. Glass, M. E. Mackay, K. Char and J. Pyun, J. Polym. Sci., Part A: Polym. Chem., 2016, 55, 107–116 CrossRef
.
- A. G. Simmonds, J. J. Griebel, J. Park, K. R. Kim, W. J. Chung, V. P. Oleshko, J. Kim, E. T. Kim, R. S. Glass, C. L. Soles, Y.-E. Sung, K. Char and J. Pyun, ACS Macro Lett., 2014, 3, 229–232 CrossRef CAS
.
- P. T. Dirlam, A. G. Simmonds, R. C. Shallcross, K. J. Arrington, W. J. Chung, J. J. Griebel, L. J. Hill, R. S. Glass, K. Char and J. Pyun, ACS Macro Lett., 2015, 4, 111–114 CrossRef CAS
.
- J. J. Griebel, G. Li, R. S. Glass, K. Char and J. Pyun, J. Polym. Sci., Part A: Polym. Chem., 2015, 53, 173–177 CrossRef CAS
.
- V. P. Oleshko, J. Kim, J. L. Schaefer, S. D. Hudson, C. L. Soles, A. G. Simmonds, J. J. Griebel, R. S. Glass, K. Char and J. Pyun, MRS Commun., 2015, 5, 353–364 CrossRef CAS
.
- P. T. Dirlam, J. Park, A. G. Simmonds, K. Domanik, C. B. Arrington, J. L. Schaefer, V. P. Oleshko, T. S. Kleine, K. Char, R. S. Glass, C. L. Soles, C. Kim, N. Pinna, Y.-E. Sung and J. Pyun, ACS Appl. Mater. Interfaces, 2016, 8, 13437–13448 CAS
.
- J. J. Griebel, S. Namnabat, E. T. Kim, R. Himmelhuber, D. H. Moronta, W. J. Chung, A. G. Simmonds, K.-J. Kim, J. van der Laan, N. A. Nguyen, E. L. Dereniak, M. E. Mackay, K. Char, R. S. Glass, R. A. Norwood and J. Pyun, Adv. Mater., 2014, 26, 3014–3018 CrossRef CAS PubMed
.
- J. J. Griebel, N. A. Nguyen, S. Namnabat, L. E. Anderson, R. S. Glass, R. A. Norwood, M. E. Mackay, K. Char and J. Pyun, ACS Macro Lett., 2015, 4, 862–866 CrossRef CAS
.
- T. S. Kleine, N. A. Nguyen, L. E. Anderson, S. Namnabat, E. A. LaVilla, S. A. Showghi, P. T. Dirlam, C. B. Arrington, M. S. Manchester, J. Schwiegerling, R. S. Glass, K. Char, R. A. Norwood, M. E. Mackay and J. Pyun, ACS Macro Lett., 2016, 5, 1152–1156 CrossRef CAS
.
- J. J. Griebel, N. A. Nguyen, A. V. Astashkin, R. S. Glass, M. E. MacKay, K. Char and J. Pyun, ACS Macro Lett., 2014, 3, 1258–1261 CrossRef CAS
.
- M. K. Salman, B. Karabay, L. C. Karabay and A. Cihaner, J. Appl. Polym. Sci., 2016, 133, 43655 CrossRef
.
- M. Arslan, B. Kiskan, E. C. Cengiz, R. Demir-Cakan and Y. Yagci, Eur. Polym. J., 2016, 80, 70–77 CrossRef CAS
.
- I. Gomez, D. Mecerreyes, J. A. Blazquez, O. Leonet, H. Ben Youcef, C. Li, J. L. Gómez-Cámer, O. Bundarchuk and L. Rodriguez-Martinez, J. Power Sources, 2016, 329, 72–78 CrossRef CAS
.
- T. R. Martin, K. A. Mazzio, H. W. Hillhouse and C. K. Luscombe, Chem. Commun., 2015, 51, 11244–11247 RSC
.
- W. J. Chung, A. G. Simmonds, J. J. Griebel, E. T. Kim, H. S. Suh, I.-B. Shim, R. S. Glass, D. A. Loy, P. Theato, Y.-E. Sung, K. Char and J. Pyun, Angew. Chem., Int. Ed., 2011, 50, 11409–11412 CrossRef CAS PubMed
.
- E. T. Kim, W. J. Chung, J. Lim, P. Johe, R. S. Glass, J. Pyun and K. Char, Polym. Chem., 2014, 5, 3617–3623 RSC
.
- B. Oschmann, J. Park, C. Kim, K. Char, Y.-E. Sung and R. Zentel, Chem. Mater., 2015, 27, 7011–7017 CrossRef CAS
.
- A. Chang, Q. Wu, X. Du, S. Chen, J. Shen, Q. Song, J. Xie and W. Wu, Chem. Commun., 2016, 52, 4525–4528 RSC
.
- M. Arslan, B. Kiskan and Y. Yagci, Macromolecules, 2016, 49, 767–773 CrossRef CAS
.
- K. Itaoka, I.-T. Kim, K. Yamabuki, N. Yoshimoto and H. Tsutsumi, J. Power Sources, 2015, 297, 323–328 CrossRef CAS
.
- K. Yamabuki, K. Itaoka, I.-t. Kim, N. Yoshimoto and H. Tsutsumi, Polymer, 2016, 91, 1–6 CrossRef CAS
.
- Z. Sun, M. Xiao, S. Wang, D. Han, S. Song, G. Chen and Y. Meng, J. Mater. Chem. A, 2014, 2, 9280–9286 CAS
.
- P. T. Dirlam, A. G. Simmonds, T. S. Kleine, N. A. Nguyen, L. E. Anderson, A. O. Klever, A. Florian, P. J. Costanzo, P. Theato, M. E. Mackay, R. S. Glass, K. Char and J. Pyun, RSC Adv., 2015, 5, 24718–24722 RSC
.
- H. Kim, J. Lee, H. Ahn, O. Kim and M. J. Park, Nat. Commun., 2015, 6, 7278 CrossRef CAS PubMed
.
- S. H. Je, T. H. Hwang, S. N. Talapaneni, O. Buyukcakir, H. J. Kim, J.-S. Yu, S.-G. Woo, M. C. Jang, B. K. Son, A. Coskun and J. W. Choi, ACS Energy Lett., 2016, 1, 566–572 CrossRef CAS
.
- S. N. Talapaneni, T. H. Hwang, S. H. Je, O. Buyukcakir, J. W. Choi and A. Coskun, Angew. Chem., Int. Ed., 2016, 55, 3106–3111 CrossRef CAS PubMed
.
- M. P. Crockett, A. M. Evans, M. J. H. Worthington, I. S. Albuquerque, A. D. Slattery, C. T. Gibson, J. A. Campbell, D. A. Lewis, G. J. L. Bernardes and J. M. Chalker, Angew. Chem., Int. Ed., 2016, 55, 1714–1718 CrossRef CAS PubMed
.
- I. Gomez, O. Leonet, J. Alberto Blazquez and D. Mecerreyes, ChemSusChem, 2016, 9, 3419–3425 CrossRef CAS PubMed
.
- D. J. Parker, H. A. Jones, S. Petcher, L. Cervini, J. M. Griffin, R. Akhtar and T. Hasell, J. Mater. Chem. A, 2017 10.1039/C6TA09862B
, in press.
- C. Fu, G. Li, J. Zhang, B. Cornejo, S. S. Piao, K. N. Bozhilov, R. C. Haddon and J. Guo, ACS Energy Lett., 2016, 1, 115–120 CrossRef CAS
.
- A. Hoefling, Y. J. Lee and P. Theato, Macromol. Chem. Phys., 2017, 218, 1600303 CrossRef
.
- S. Shukla, A. Ghosh, P. K. Roy, S. Mitra and B. Lochab, Polymer, 2016, 99, 349–357 CrossRef CAS
.
- A. Ghosh, S. Shukla, G. S. Khosla, B. Lochab and S. Mitra, Sci. Rep., 2016, 6, 25207 CrossRef CAS PubMed
.
-
R. J. Braddock, Handbook of Citrus By-Products and Processing Technology, Wiley, New York, 1999 Search PubMed
.
- K. C. Nicolaou, P. G. Bulger and D. Sarlah, Angew. Chem., Int. Ed., 2005, 44, 4442–4489 CrossRef CAS PubMed
.
- C. Torborg and M. Beller, Adv. Synth. Catal., 2009, 351, 3027–3043 CrossRef CAS
.
- C. Barbante, A. Veysseyre, C. Ferrari, K. van de Velde, C. Morel, G. Capodaglio, P. Cescon, G. Scarponi and C. Boutron, Environ. Sci. Technol., 2001, 35, 835–839 CrossRef CAS PubMed
.
- Global Mercury Assessment 2013. Sources, Emissions, Releases and Environmental Transport. United Nations Environment Programme, Chemicals Branch, Geneva, Switzerland, 2013. accessed 24 Oct 2016 from http://www.unep.org/PDF/PressReleases/GlobalMercuryAssessment2013.pdf.
- P. B. Tchounwou, W. K. Ayensu, N. Ninashvili and D. Sutton, Environ. Toxicol., 2003, 18, 149–175 CrossRef CAS PubMed
.
- T. Hasell, D. J. Parker, H. A. Jones, T. McAllister and S. M. Howdle, Chem. Commun., 2016, 52, 5383–5386 RSC
.
- A. Greiner and J. H. Wendorff, Angew. Chem., Int. Ed., 2007, 46, 5670–5703 CrossRef CAS PubMed
.
- S. Agarwal, A. Greiner and J. H. Wendorff, Adv. Funct. Mater., 2009, 19, 2863–2879 CrossRef CAS
.
- M. W. Thielke, L. A. Bultema, D. D. Brauer, B. Richter, M. Fischer and P. Theato, Polymers, 2016, 8, 266 CrossRef
.
- J. C. Bear, J. D. McGettrick, I. P. Parkin, C. W. Dunnill and T. Hasell, Microporous Mesoporous Mater., 2016, 232, 189–195 CrossRef CAS
.
- M. E. Davis, Nature, 2002, 417, 813–821 CrossRef CAS PubMed
.
- K. M. Steel and W. J. Koros, Carbon, 2003, 2003, 253–266 CrossRef
.
- Y.-S. Bae and R. Q. Snurr, Angew. Chem., Int. Ed., 2011, 50, 11586–11596 CrossRef CAS PubMed
.
- P. Nugent, Y. Belmabkhout, S. D. Burd, A. J. Cairns, R. Luebke, K. Forrest, T. Pham, S. Ma, B. Space, L. Wojtas, M. Eddaoudi and M. J. Zaworotko, Nature, 2013, 495, 80–84 CrossRef CAS PubMed
.
- M. O. Adebajo, R. L. Frost, J. T. Kloprogge, O. Carmody and S. Kokot, J. Porous Mater., 2003, 10, 159–170 CrossRef CAS
.
- J. M. Dias, M. C. M. Alvim-Ferraz, M. F. Almeida, J. Rivera-Utrilla and M. Sánchez-Polo, J. Environ. Manage., 2007, 85, 833–846 CrossRef CAS PubMed
.
- M. Hartmann, S. Kullmann and H. Keller, J. Mater. Chem., 2010, 20, 9002–9017 RSC
.
- M. A. Shannon, P. W. Bohn, M. Elimelech, J. G. Georgiadis, B. J. Mariñas and A. M. Mayes, Nature, 2008, 452, 301–310 CrossRef CAS PubMed
.
- S. Chu and A. Majumdar, Nature, 2012, 488, 294–303 CrossRef CAS PubMed
.
- M. Armand and J.-M. Tarascon, Nature, 2008, 451, 652–657 CrossRef CAS PubMed
.
- P. Liu, J. M. Gardner and L. Kloo, Chem. Commun., 2015, 51, 14660–14662 RSC
.
- S. Zhuo, Y. Huang, C. Liu, H. Wang and B. Zhang, Chem. Commun., 2014, 50, 11208–11210 RSC
.
- A. Manthiram, Y. Fu and Y.-S. Su, Acc. Chem. Res., 2013, 46, 1125–1134 CrossRef CAS PubMed
.
- J. W. Choi and D. Aurbach, Nat. Rev. Mater., 2016, 1, 16013 CrossRef CAS
.
- J. C. Bear, W. J. Peveler, P. D. McNaughter, I. P. Parkin, P. O'Brien and C. W. Dunnill, Chem. Commun., 2015, 51, 10467–10470 RSC
.
- B. Ding, Z. Chang, G. Xu, P. Nie, J. Wang, J. Pan, H. Dou and X. Zhang, ACS Appl. Mater. Interfaces, 2015, 7, 11165–11171 CAS
.
- J. Li, L. Yang, S. Yang and J. Y. Lee, Adv. Energy Mater., 2015, 5, 1501808 CrossRef
.
- Y. Wei, X. Li, Z. Xu, H. Sun, Y. Zheng, L. Peng, Z. Liu, C. Gao and M. Gao, Polym. Chem., 2015, 6, 973–982 RSC
.
- C. Almeida, H. Costa, P. Kadhirvel, A. M. Queiroz, R. C. S. Dias and M. R. P. F. N. Costa, J. Appl. Polym. Sci., 2016, 133, 43993 CrossRef
.
- B. Li, S. Li, J. Xu and S. Yang, Energy Environ. Sci., 2016, 9, 2025–2030 CAS
.
- J. Lim, U. Jung, W. T. Joe, E. T. Kim, J. Pyun and K. Char, Macromol. Rapid Commun., 2015, 36, 1103–1107 CrossRef CAS PubMed
.
- S. Yu, H. Kwon, H. R. Noh, B.-I. Park, N. K. Park, H.-J. Choi, S.-C. Choi and G. D. Kim, RSC Adv., 2015, 5, 36030–36035 RSC
.
- S. P. Nalawade, F. Picchioni and L. P. B. M. Janssen, Prog. Polym. Sci., 2006, 31, 19–43 CrossRef CAS
.
- A. A. Shah, F. Hasan, A. Hameed and S. Ahmed, Biotechnol. Adv., 2008, 26, 246–265 CrossRef CAS PubMed
.
|
This journal is © The Royal Society of Chemistry 2017 |
Click here to see how this site uses Cookies. View our privacy policy here.