Lithium-ion battery recycling: a source of per- and polyfluoroalkyl substances (PFAS) to the environment?
Received
8th December 2022
, Accepted 23rd April 2023
First published on 27th April 2023
Abstract
Recycling of lithium-ion batteries (LIBs) is a rapidly growing industry, which is vital to address the increasing demand for metals, and to achieve a sustainable circular economy. Relatively little information is known about the environmental risks posed by LIB recycling, in particular with regards to the emission of persistent (in)organic fluorinated chemicals. Here we present an overview on the use of fluorinated substances – in particular per- and polyfluoroalkyl substances (PFAS) – in state-of-the-art LIBs, along with recycling conditions which may lead to their formation and/or release to the environment. Both organic and inorganic fluorinated substances are widely reported in LIB components, including the electrodes and binder, electrolyte (and additives), and separator. Among the most common substances are LiPF6 (an electrolyte salt), and the polymeric PFAS polyvinylidene fluoride (used as an electrode binder and a separator). Currently the most common LIB recycling process involves pyrometallurgy, which operates at high temperatures (up to 1600 °C), sufficient for PFAS mineralization. However, hydrometallurgy, an increasingly popular alternative recycling approach, operates under milder temperatures (<600 °C), which could favor incomplete degradation and/or formation and release of persistent fluorinated substances. This is supported by the wide range of fluorinated substances detected in bench-scale LIB recycling experiments. Overall, this review highlights the need to further investigate emissions of fluorinated substances during LIB recycling and suggests that substitution of PFAS-based materials (i.e. during manufacturing), or alternatively post-treatments and/or changes in process conditions may be required to avoid formation and emission of persistent fluorinated substances.
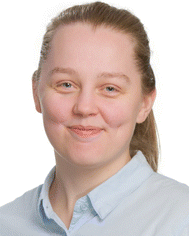 Amanda Rensmo | Amanda Rensmo obtained a MSc in Chemical Engineering from Uppsala University (Sweden) with the master thesis titled “Per- and Polyfluoroalkyl Substance (PFAS) Emissions from Recycling Processes of Lithium-Ion Batteries” through the project SCOPE-LIB in collaboration with Rise and Stockholm University. She also holds a BSc in Chemistry and Physics from Hope College (Michigan, USA) where she performed research on the battery capacity for Prussian Blue Analogues. Currently, she is working at the consultancy firm WSP (Sweden) in several investigations with an energy focus, particularly on batteries and hydrogen gas. |
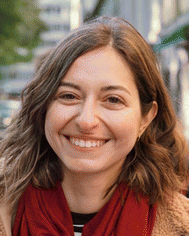 Eleni Savvidou | Eleni Savvidou is a PhD student in the Department of Environmental Science at Stockholm University, Sweden. She obtained a BSc in Chemistry from Ulm University (Germany) and a MSc in Environmental Science – Environmental Toxicology and Chemistry from Stockholm University (Sweden). Her research focuses on identifying PFAS in different consumer products and processes using a fluorine mass balance approach and other analytical techniques, and the investigation of potential alternatives for these use cases. |
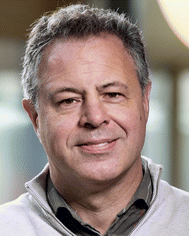 Ian T. Cousins | Ian Cousins is a Professor in the Department of Environmental Science at Stockholm University, Sweden. He holds a BSc (Hons) in Chemistry from the University of York (UK), an MSc in Environmental Management from the University of Surrey (UK) and a PhD in Environmental Science from Lancaster University (UK). He was formerly an Environmental Chemist at the Water Research Centre plc (UK) and a postdoctoral fellow at Trent University (Canada). His research program comprises a combination of experimental and modelling approaches to investigate the sources, transport, fate and exposure of contaminants, with a recent focus on PFAS. |
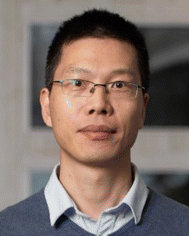 Xianfeng Hu | Xianfeng Hu is a senior researcher in the department of metallurgy at Swedish Research Institute for Mining Metallurgy and Materials (Swerim, Luleå site, Sweden). He holds a BSc in materials science and engineering from Henan University of Science and Technology (China), a MSc in materials science and engineering from Xi'an Jiaotong University (China), and a PhD degree in process metallurgy from Luleå University of Technology (Sweden). His research program focuses on the pyrometallurgy extraction of valuable metals from primary and secondary resources, and development of new metallurgical processes. |
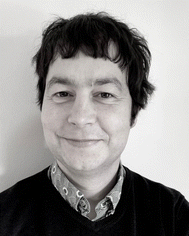 Steffen Schellenberger | Steffen Schellenberger is a researcher at the RISE Research Institutes of Sweden. He holds a degree in chemical engineering (MSc equivalent) from the Universities of Applied Sciences in Esslingen, Germany, and a PhD in Environmental Science from Stockholm University, Sweden. He formerly worked in R&D of new chemicals at MERCK, Germany. His current research focuses on the development and characterization of environmentally friendly chemicals in materials and products as well as the substitution of hazardous chemicals such as PFAS. |
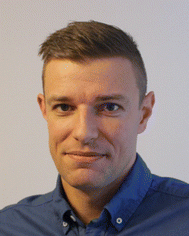 Jonathan P. Benskin | Jonathan Benskin is a Professor in the Department of Environmental Science at Stockholm University, Sweden. He holds a BSc in Chemistry from the University of Victoria (Canada), and a PhD in Medical Sciences from the University of Alberta (Canada). He was formerly an NSERC Industrial Fellow and Principle Scientist at AXYS Analytical Services Ltd and a Visiting Scientist at the Institute of Ocean Sciences (Fisheries and Oceans Canada). His research program focuses on understanding the occurrence, fate, and behaviour of emerging organic contaminants, in particular PFAS, using novel analytical tools. |
Environmental significance
Per- and polyfluoroalkyl substances (PFAS) are a large class of highly persistent organic substances, many of which are bioaccumulative and toxic. One of the many uses of PFAS is in lithium-ion batteries (LIBs). Recycling of LIBs is a rapidly growing industry, yet the potential for PFAS emission during this process remains unclear. Here we present an overview on the use of PFAS and other fluorinated substances in state-of-the-art LIBs, along with the recycling conditions which may lead to their formation and/or release to the environment. This review highlights the paucity of information on emission of fluorinated substances during LIB recycling, despite widespread use of PFAS and other fluorinated chemicals in LIBs.
|
Introduction
Electric vehicles (EVs) are expected to become the principal modes of transportation manufactured by the largest car brands by the year 2050.1,2 This shift in market demand has increased the need for batteries, in particular lithium-ion batteries (LIBs).3–5 However, transition metals (e.g. Co, Ni, and Mn) required for manufacturing of LIBs are in finite supply.6,7 One solution for addressing this shortage is recycling,8 which is expected to be among the main sources for Fe, Al and Cu by 2050.9 While recovery of critical raw materials (in particular metals) via recycling will help to mitigate resource depletion and associated environmental impacts,1,6,10 sustainable recycling infrastructure must first be developed, to avoid exposure of humans and the environment to hazardous substances.4
Compared to other battery types, LIBs are a relatively new technology, with SONY entering the market in 1991 with the first commercial LIB.11 Thus, it is only recently that a sufficient number of aged and unusable batteries are available to make recycling economically viable. Recycling of LIBs has increased rapidly over the last decade and in 2019 the European Union (EU) proposed that 70% of LIBs should be recycled by 2030.4,5,12,13 Large investments have been made by the EU in several LIB recycling projects.6 In contrast, on a global scale, only about 5–7% of all LIBs are currently collected for recycling, while the remainder are most often disposed of in landfills.9,14 In fact, many consumer products containing LIBs are discarded within six years of use.15,16 To facilitate increased EV production, the share of LIBs that are redirected from waste to recycling streams must increase.4
Recycled batteries are of interest for their valuable transition metals (Ni and Co) resulting in an industrial process designed specifically for recovery of these substances.17–20 Recycling separates various LIB components into different fractions. Depending on the recycling conditions and composition of the original LIBs, this process may lead to emission of gas and/or liquid containing harmful chemicals.6,21 One such class of chemicals used widely in the LIB industry are per- and polyfluoroalkyl substances (PFAS). PFAS make up a large group of anthropogenic substances which have been manufactured since the 1950s and are defined as containing at least one perfluoromethyl or perfluoromethylene group, with some exceptions noted.22 Many PFAS display unusual properties (e.g. thermal and chemical stability, ability to reduce the surface tension of liquids and surfaces, combined oil and water repellency, and dielectric properties), which has led to their widespread use across different areas, including in firefighting foams, water/stain resistance, and plastic extrusion.23 The European Chemicals Agency estimated that the total number of commercially-relevant PFAS exceeds 10
000 substances, which are used in >1400 products or processes.24,25
Interest in PFAS has intensified drastically over the last 20 years since the first detection of perfluorooctane sulfonate (PFOS) in the blood of non-occupationally exposed humans26 and wildlife globally.27 All PFAS are considered persistent, or break down to persistent end products,28 and many are bioaccumulative in wildlife29–31 and humans.32 Some PFAS have also been linked to ecotoxicological33 and adverse human health effects,34 including altered immune and thyroid function, liver disease, lipid and insulin dysregulation, kidney disease, adverse reproductive and developmental outcomes, and cancer.34 Research up to now has mainly focused on studying the emissions, transport and fate, and effects of a relatively small number of legacy PFAS; however, novel PFAS are continuously introduced onto the global market and are detectable in the environment, including remote wildlife.35
While prior studies10,36 have considered multiple environmental impacts of LIBs, there is a paucity of information on the potential emission of PFAS. The purpose of this review is to summarize the state of knowledge on the use of fluorinated substances in LIBs, and the potential for PFAS to be released to the environment during LIB recycling. Within this broad objective, we aim to (a) review and summarize the use of fluorinated chemicals in LIBs; (b) assess the potential for PFAS release and/or mobilization during recycling; and (c) identify knowledge gaps in understanding the risks associated with PFAS released during LIB recycling.
Scope of literature review
Since much of the technology used in LIBs and in LIB recycling is proprietary, this review cannot be considered exhaustive. Nevertheless, it provides a broad overview of the potential use and emissions of fluorinated substances from LIBs based on literature available as of November, 2022. To this end, our search focused on three databases (Web of Science [Clarivate], Scopus [Elsevier] and Google Scholar), using keywords presented in Table 1. For each database, the same search structure was adopted, utilizing key words for up to 3 different categories (i.e. “LIBs”, “Fluoropolymer”, and “Process/Industry”). Other restrictions were used to keep the total number of abstracts obtained from each database below 400. As LIBs may have different chemistries, we did not restrict our search to one particular cathode material. However, to avoid novel, yet commercially irrelevant materials, we did not include solid state batteries, ionic or gel electrolytes and silicon anodes in our search. Review articles and those published most recently, as well as state-of-the-art and commercial techniques were given the highest priority for inclusion in this review.
Table 1 Literature review keywords within various databases, utilizing the Boolean command AND between each search word if not otherwise stated, where * serves as the truncation operator
Database |
LIBs |
Fluoropolymer |
Process/industry |
Other restrictions |
Results |
PVDF searched for as: PVdF OR PVDF OR P(VDF) OR P(VdF).
|
Web of science |
Lithium ion batter* OR LIB |
Fluoropolymer |
|
Binder OR additive OR separator OR electrolyte |
10 |
|
Lithium ion batter* OR LIB |
Fluorinated |
|
Binder OR additive OR separator OR electrolyte |
362 |
|
|
|
Battery recycling |
HF |
4 |
|
Lithium ion batter* |
PVDFa |
Recycling |
Products |
4 |
|
Lithium ion batter* |
PVDFa |
Recycling |
HF |
7 |
|
|
PVDFa |
Decomposition OR degradation |
Thermal treatment |
10 |
Google Scholar |
LIB |
Fluorinated organics |
Commercial AND state-of-the-art |
Additives |
12 |
|
Lithium ion |
Fluorinated organics |
State-of-the-art |
Additives |
2 |
|
Lithium ion |
Fluoropolymer |
State-of-the-art |
Additives NOT = (PVDF AND FEC) |
90 |
SCOPUS |
Lithium ion batter* OR lib |
|
Recycling OR recycle |
LIMIT TO = (fluorine compounds) |
34 |
|
Lithium ion batter* OR lib |
|
Recycling OR recycle |
LIMIT TO = (heat treatment) |
38 |
|
Lithium ion batter* OR lib |
|
Recycling OR recycle |
LIMIT TO = (recycling process AND hydrometallurgy) |
13 |
|
Lithium ion batter* OR lib |
|
Recycling OR recycle |
LIMIT TO = electric vehicles (evs) AND battery industry |
78 |
|
Lithium ion batter* OR lib |
|
Recycling OR recycle |
LIMIT TO = (recycling technology) |
63 |
Fluorinated lithium-ion battery components
LIBs are electrochemical cells in which chemical energy is converted into electrical energy (and vice versa). Their principle of operation is the same as other battery chemistries (e.g. lead-acid), but the voltage difference between the two electrodes in a LIB is much larger (i.e. 3–4 V), providing improved performance in terms of energy and power density.4,37 The battery consists of a positive electrode (cathode) and a negative electrode (anode), both of which are surrounded by electrolyte and separated by a permeable membrane (the separator; Fig. 1). The electrodes consist of electroactive materials but also a binder material which imparts structural integrity while improving interconnectivity within the electrode, adhesion to the current collector, and formation of the solid electrolyte interface (SEI) during the first battery cycles.38–40 Fluorinated substances were identified in electrodes and binder, electrolyte (main components and additives), and separator, and are described in detail below.
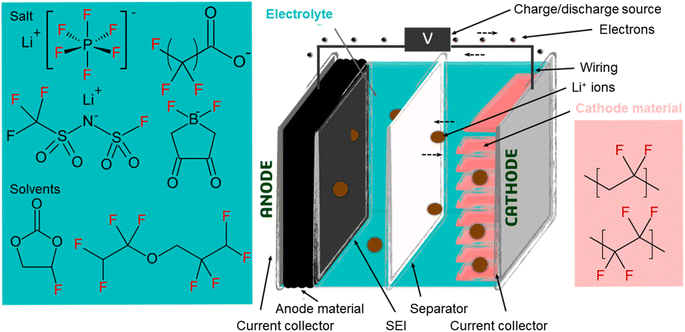 |
| Fig. 1 Simplified schematic of a lithium-ion battery, adapted from Bresser et al. (2015),38 including examples of fluorinated species included in many batteries, some of which are classified as PFAS under the OECD definition. | |
Electrodes
Anodes usually consist of graphite combined with styrene-butadiene rubber and carboxymethyl cellulose binders, but polyvinylidene fluoride (PVDF; Fig. 2A) may also be used.38–42 Cathodes, in comparison, consist mostly of an electroactive material (e.g. lithium nickel manganese cobalt oxide (NMC) or lithium iron phosphate (LFP)) along with a binder (1–8 wt%), which is often fluorinated.20,38,39,43 The binder is generally considered an inactive part of the battery, but it can influence formation of the SEI as well as the conductivity and the overall performance of the battery.40,44 Fluorinated binders offer higher stability due to their resistance to oxidation compared to non-fluorinated binders.39 They can also prevent self-discharge by inhibiting some electrochemical reactions and thus improve the energy density as well as lifespan of the battery.45 Binder material may exist as either a homopolymer (e.g. PVDF; most common) or copolymer (e.g. polyvinylidene fluoride co-hexafluoropropylene [PVDF-HFP] or polyvinylidene fluoride co-trifluoroethylene [PVDF-TrFE]; Fig. 2A).39,40,45–49 Other fluorochemical binders include polytetrafluoroethylene (PTFE),20 fluoroacrylate polymers (noted only by the general name in the scientific literature or a patent under the trade name TRD202A),50,51 or fluorinated ethylene propylene (FEP), which is less common commercially (Fig. 2A).23 In order to avoid side reactions between the cathode materials and the electrolytes (which could pose a safety risk), surface fluorination of the electroactive materials is commonly performed using, for example, AlF3.11,38,52–58
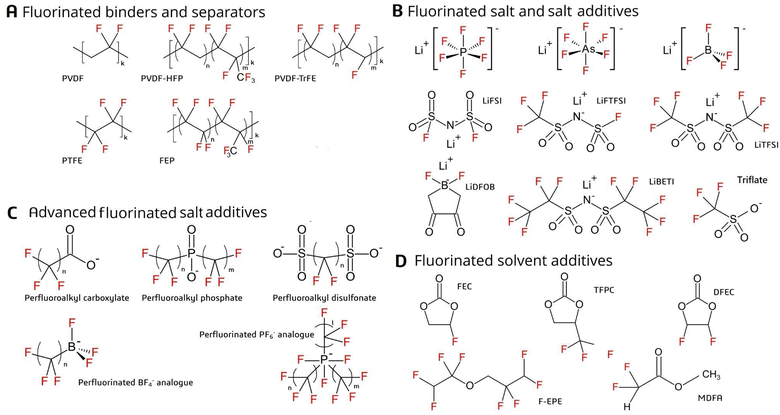 |
| Fig. 2 Examples of fluorinated substances found in LIB components with their CAS numbers in parentheses. (A) Fluorinated binders and separators: polyvinylidene fluoride (PVDF, 24937-79-9), polyvinylidene fluoride co-hexafluoropropylene (PVDF-HFP, 9011-17-0), polyvinylidene fluoride co-trifluoroethylene (PVDF-TrFE, 28960-88-5), polytetrafluoroethylene (PTFE, 9002-84-0), and fluorinated ethylene propylene (FEP, 25067-11-2); (B) fluorinated salt and salt additives: LiPF6 (21324-40-3), LiAsF6 (29935-35-1), LiBF4 (14283-07-9), lithium bis(fluorosulfonyl)imide (LiFSI, 171611-11-3), lithium fluorosulfonyl-trifluorosulfonyl imide (LiFTFSI, 192998-62-2), lithium bis(trifluoromethylsulfonyl)imide (LiTFSI, 90076-65-6), lithium difluoro(oxalate)borate (LiDFOB, 409071-16-5) and lithium bis(perfluoroethanesulfonyl)imide (LiBETi, 132843-44-8), triflate (37181-39-8); (C) advanced fluorinated salt additives: including for example lithium tri(pentafluoroethyl)triphosphate (LiFAP); (D) fluorinated solvent additives: fluoroethylene carbonate (FEC, 114435-02-8), difluoroethylene carbonate (DFEC, 171730-81-7), trifluoropropylene carbonate (TFPC, 167951-80-6), methyl difluoroacetate (MDFA, 433-53-4) and tetrafluoroethyl tetrafluoropropylether (F-EPE, 16627-68-2). Subscripts k, l, m, n refer to various lengths of backbone repeating units for binders, separators and salt additives. | |
Separator
Within the battery, separation of the two electrodes by a semipermeable barrier is necessary in order to extract electrical energy.59 The separator should be porous and allow for wetting; thus, fiber-structured materials are often used.37 While the battery separator is usually polypropylene or polyethylene, fluoropolymers such as PVDF or its copolymer PVDF-HFP have also been used (Fig. 2A).9,39,45,52,59–62
Electrolyte
The electrolyte is comprised of salt(s) (Fig. 2B) dissolved in solvent(s). Examples of the latter include ethylene or propylene carbonates.37,38,63 LiSO3CF3 (triflate) has been used as a main salt in batteries since the 1970s,11 but today, LiPF6 is the principal electrolyte salt used in commercial batteries due to its high ionic conductivity and potential to passivate the Al current collector (Fig. 2B).52,64,65 Less common salts include LiAsF6, LiBF4, lithium bis(trifluoromethylsulfonyl)imide (LiTFSI), lithium bis(perfluoroethanesulfonyl)-imide (LiBETI), lithium difluoro(oxalate)borate (LiDFOB), lithium bis(fluorosulfonyl)imide (LiFSI), and lithium fluorosulfonyl-trifluorosulfonyl imide (LiFTFSI) (Fig. 2B).6,11,38,52,63,64,66–71
Electrolyte additives
Additives in the electrolyte include co-solvents or minor salts (i.e. in addition to the main salt or solvent), which may account for 5–10 wt% of the electrolyte (Fig. 2B). These substances are important to improve battery properties, including SEI formation, conductivity, flame retardance, and reduced gas build-up within the LIB cells.3,4,11,37,38,72–75 For example, LiFSI (an additive) is often used together with LiPF6 (a main salt).68 Other examples of additives include imides substituted with electron withdrawing groups (e.g. –COCF3 or –SO2CF3), such as TFSI− (Fig. 2B).11,38
New additive salts (i.e. advanced alternatives), which have until now been mostly used for lab-scale experiments, include perfluoroalkyl carboxylates (PFCAs), perfluoroalkyl phosphinates and perfluoroalkyl disulfonates (Fig. 2C).11,43,71 There are also examples of perfluorinated analogues of the PF6− and BF4− anions, of which lithium tri(pentafluoroethyl)triphosphate (LiFAP) has shown promising results for increasing the flash point of the electrolyte solvent (Fig. 2C),11,52,76 among other properties. Organoborate, organophosphate and organoaluminate analogues may also include perfluorinated carbon atoms, which could improve resistance to hydrolysis; however, these advanced salts are not expected to occur on the market in large amounts.11 The potential of these salts to be widely commercialized in the future still remains doubtful, given their high cost and uncertainties over conductive performance.11,52
Additive solvents can consist of a fluorinated derivative of the main electrolyte solvent (Fig. 2D). Examples include fluorinated carbonates (e.g. fluoroethylene carbonate), carboxylates (e.g. methyl difluoroacetate) and ethers (e.g. tetrafluoroethyl tetrafluoropropylether) (Fig. 2D).11,43,52,71,74,76–81 In addition to reducing flammability, fluorine substitution in solvents increases oxidation potential and, consequently, anodic stability under high temperature and voltage.76,77 However, the electrolyte solvent should also be capable of solvating lithium ions, which becomes increasingly difficult with fluorination. Thus, partially (i.e. mono- or di-)fluorinated organic solvents are expected in future batteries used in, for example, EVs.11
Future battery components
The future outlook of battery usage predicts LIBs with higher energy densities, where the current LiPF6 salt and other functional components may be unsuitable.3,11 To address this limitation, new materials must be developed. In addition to accommodating LIBs with higher energy densities, future salts should display improved thermal stability, SEI-formation, low-temperature operation and compatibility with emerging solvents. Moreover, general electrolyte conditions such as high ionic conductivity, salt solubility, and stability are required.11 At very high voltages, cathode electrolyte interface (CEI)-forming salts are required which may increase the number of additives in one electrolyte.76,82 Fluorinated electrolyte species (i.e. both salt and solvent) fulfill many of these requirements, suggesting that these substances may be strong candidates for future battery components.11,71,78 However, challenges remain for fluorinated binder materials such as PVDF, which may not meet adhesion and mechanical strength requirements under high voltages. Multilayer binders of the aforementioned polymers or other materials have been proposed,44 which may complicate the recycling procedure.
LIB recycling processes
LIB recycling may involve pyrometallurgical, hydrometallurgical, or direct recycling processes (Fig. 3), of which pyrometallurgical recycling with or without down-stream hydrometallurgical processing are among the most common practices today.20,83,84 Hydrometallurgy-dominant recycling processes are generally considered superior in terms of immediate recovery of battery-grade materials and compliance with the upcoming EU battery regulation; consequently, these processes are anticipated to dominate the industry in the near future.6,14,17,20,72,85–87 Within the LIB recycling research field, there is also great interest in recovery of battery components without decomposition (i.e. direct recycling). However, this process has not yet been commercialized86 or it is limited to handling in-house LIB production scrap on a very small scale. The following section describes each of the major LIB recycling approaches in detail, along with their potential for PFAS emissions.
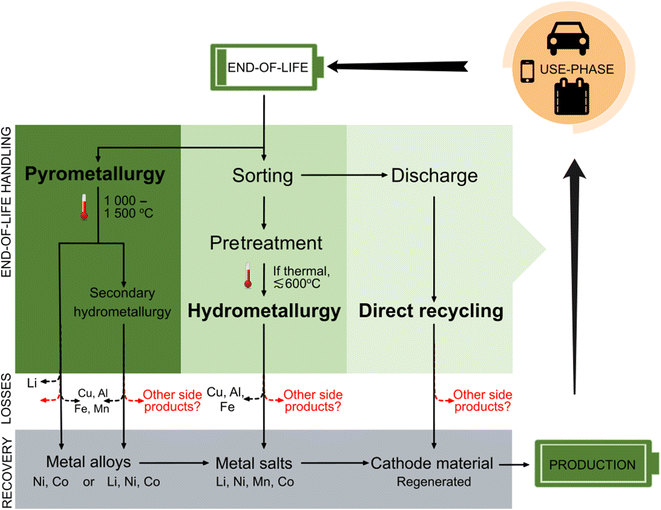 |
| Fig. 3 Overview of handling, material losses, and material recovery for the three major LIB recycling processes: pyrometallurgy, hydrometallurgy and direct recycling. Temperatures are ≅ ambient when not stated. Dashed arrows indicate fractions that are not possible to recycle using a given process. Figure adapted from Kushnir, 2015 86 and Lv et al., 2018.83 | |
Pyrometallurgical recycling process
Pyrometallurgical recycling is a high-temperature smelting reduction process (up to 1600 °C), in which LIBs with or without pretreatment are added to a smelter or arc furnace together with slag formers. During this process, electrode-active materials are reduced by graphite in the LIBs. The high temperatures serve to incinerate organic components (such as volatile organic compounds, binder material etc.).17,20,87,88 The end product is a metal alloy consisting of Ni, Co, Fe and Cu, while Li, Mn, and Al are usually lost to slag. When followed by a hydrometallurgical process, Li in the slag can be recovered.9,13,17,59 In an optimized pyrometallurgical process it is also possible to concentrate and recover lithium in the flue dust.89 While the high temperatures applied during pyrometallurgy favor decomposition of PFAS and other organofluorine components, the large quantity of hazardous gas generated from this process (including hydrofluoric acid), along with intense energy use and production of metal alloys (which require further handling) represent significant drawbacks. Other disadvantages of the pyrometallurgical recycling process lie in the production of a metal alloy instead of battery precursor materials, and the generation of carbon dioxide caused by carbothermic reduction and graphite burning.17,20,85,86
Pretreatment + hydrometallurgical recycling
A multi-step pretreatment process is required to prepare LIBs for hydrometallurgy. While procedures for pretreatment are still under development, this method typically involves sorting followed by a combination of deactivation, dismantling, and binder removal. Of these steps, deactivation is particularly important for reducing the risks of overheating (and by extension, production of toxic and flammable gasses) within the battery cell during recycling.85 LIB deactivation is often initiated by discharging the battery in a salt solution (NaCl or Na2SO4),15,20 which risks production of HF gas.20,85 Alternatively, discharge may be achieved through an electrical circuit9 which enables recovery of the residual energy, although this has yet to be commercialized.15,85 The second part of deactivation is the electrolyte recovery, which involves thermal treatment (at temperatures around 160 °C)9,90 or solvents (e.g. N-methyl-2-pyrrolidone87) for extraction. Since the conduction salt LiPF6 in LIB electrolytes may release HF (and other substances) when in contact with air, this treatment step is run under an inert atmosphere together with a gas scrubber.7,60 Due to electrolyte decomposition during the use-phase and absorption processes at the electrodes, 100% electrolyte recovery is not possible.72 Increased yields of electrolyte with supercritical CO2 extraction methods are currently a new field of research which allows milder process conditions and minimizes impurities.85 It is also possible to combine the different treatments for electrolyte evaporation, such as elevated temperature for solvent extraction or solvents with supercritical CO2.72,90
Following deactivation, LIB components such as separators, wiring, plastic covers and steel cases are dismantled.6,91 These components have established recycling streams,86 while anodes and cathodes that contain the main fraction of rare metals undergo further processing.91 Thereafter, dismantled LIBs are crushed and ground to release the electroactive compounds for hydrometallurgical recycling.6 This mechanical treatment can also be applied directly, without a deactivation or dismantling step, by applying a controlled atmosphere, which may also increase the yield of the desired metal salts.6,20,85 Granules of the crushed materials (mainly electrodes) are sorted into fractions by various sorting methods (e.g. sieving).91
The fine powder of the shredded LIB materials (i.e. “black mass”17) requires further processing to liberate the desired transition metals. The binder removal step is aimed at removing the remaining organic components in the battery before the black mass is subjected to a leaching process. The separation of the electroactive material in the electrode (e.g. lithium oxides) from the organic binder matrix (e.g. PVDF), which is coated to the aluminum and copper current collectors, is performed by thermal treatment, solvent dissolution or a combination of both.5,55,87,91 In literature, thermal treatments are often described to run at approximately 400–600 °C, which is above the temperature required for binder degradation but below that of active materials decomposition.55,87,91 This process may occur either in the presence of oxygen (incineration) or under vacuum atmosphere (pyrolysis).17,54,60,85 Still, literature disagrees on the optimal temperature for binder removal, which ranges from 500–650 °C (below melting temperature of Al)20,54,60,88 or ≥700 °C (complete calcination temperature with phase transition).55,92 To ensure decomposition of PVDF, it is arguably better to have as high temperatures as possible; however, high temperatures are generally avoided for hydrometallurgy due to reasons mentioned above, such as reduced metal yield and increased energy consumption as well as the possibility of Al melting around the binder material. Thus, it is reasonable to assume that the applied conditions in industry would be as low as possible while still burning off the binder (e.g. around or slightly above 500 °C). Removal of PVDF in the binder by solvent dissolution most commonly uses N-methyl-2-pyrrolidone as it is also the solvent for the production of the binder slurry in upstream battery production.87
After binder removal, the material is ready for hydrometallurgical processing, which is initiated via an acid leaching process involving inorganic acids (e.g. sulfuric acid, nitric acid or hydrochloric acid),14 followed by a series of additional processing/refining steps such as precipitation, solvent extraction, ion exchange and/or electrolysis.5,9,17,88,91 The metals isolated from this process, often in the form of salts, are used up-stream in production of cathode materials for new batteries.9 Overall, hydrometallurgical LIB recycling has several advantages, including improved yields for metal recovery and lower energy demands, but requires extensive pretreatment steps to liberate the cathode active materials for the leaching process.17,88,91
Direct recycling
At the end of a lithium-ion battery's service life, the chemistry has been altered, for example by a lack of lithium ions or crystal structure failure (among others).9,87 Direct recycling is an emerging approach which involves replenishing depleted lithium in a used LIB.88 The method is thus selective and non-destructive and the cathode regains its electrochemical properties, thus by-passing steps in both the downstream and upstream production compared to pyro- or hydrometallurgy.7,87,88 This process is still under development and to the best of our knowledge has not yet implemented on a commercial scale.9
Possible fluorochemical emissions from LIB recycling
While the use of fluorinated substances in LIBs is well known, there is a paucity of information on the fate of these substances (or the potential formation of new substances) during recycling.18 Ultimately, the identity of substances emitted during recycling will depend on battery chemistries and recycling conditions.6,92 As such, mapping of fluorinated components and potential transformation products is urgently needed. In this section, we consider the fate of fluorinated ingredients used in the major fluorochemical-containing LIB components (i.e. electrolyte and binder) during recycling, and thereafter summarize the literature investigating overall emissions during LIB recycling. While a discussion of hazards associated with these substances is beyond the scope of this review, we note that most fluorinated species formed during recycling are likely to be persistent, and this property alone justifies concern over environmental emissions.28
Electrolyte emissions
Decomposition of the electrolyte salt, solvent or a combination thereof during LIB recycling can lead to formation of a wide range of organic and inorganic fluorinated species, such as organophosphates and organofluorophosphates (e.g. mono- and difluoroethylphoshpates).3,72,93 Among electrolyte salts, lithium hexafluorophosphate (LiPF6) was reported to decompose to PO2F2−, HPO3, POF3, PF5, LiF and HF or F− (Fig. 4) under conditions relevant to recycling, but also during aging and abuse situations (e.g. EV accidents).3,6,21,53,64,72,85,90,92,94,95 Of these products, HF is of particular concern due to its toxicity and corrosive nature. Decomposition of electrolyte solvents may also lead to formation of gaseous products (e.g. hydrocarbons and COF2)85,94 and/or react with decomposed electrolyte salts. For example, reactions between PF5 and organic carbonates at elevated temperatures and in the presence of a catalyst such as lithium metal or oxygen are widely reported.3,21,72,92,93,96 One ex situ study simulating thermal runaway at 89 °C (where only the positive electrode materials were present) reported formation of bis-(2-fluoroethyl)-ether, which is presumably formed from reaction between the electrolyte solvent and salt (Fig. 4).96 This was further supported by detection of an ethylene fluoride fragment identified in a separate study by nuclear magnetic resonance (Fig. 4).97 Unfortunately, emission of fluorinated products are only mentioned intermittently in the scientific literature and with limited accompanying information on reaction pathways or analytical methods.
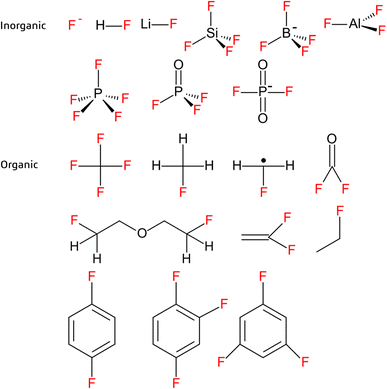 |
| Fig. 4 Examples of inorganic (top) and organic (bottom) fluorinated substances reported in the literature from LIB recycling experiments.1,3,6,13,16,21,47,53,55,64,72,85,92,94–98,101–103 | |
Binder emissions
As the most frequently used binder material, PVDF (homopolymer or copolymer) is the focus of most of the existing literature on binder removal during recycling. Binder removal conditions have been studied for PVDF in cathodes, where a temperature of at least 400 °C was required for degradation to be initiated (PVDF decomposes in the range of 350–600 °C).54,60,88 Investigations into the thermolysis of pure fluoropolymers indicate formation of a large and diverse suite of transformation products, only some of which have been identified.98–100 Examples include hydrofluoric acid, difluorobenzene and trifluorobenzene, fluorinated alkanes, vinylidene fluoride (VDF) (and related PVDF degradation products) as well as undefined oligomers and polymerized species (Fig. 4).1,13,16,47,92,101–103 Given these observations, and considering the extensive use of fluorinated substances (including fluoropolymers) in LIBs, it is reasonable to expect that an equally diverse range of transformation products may form during LIB recycling.
The mechanism of PVDF thermolysis proceeds via a dehydrofluorination reaction which removes one fluorine atom and one hydrogen atom in the PVDF chain, forming a carbon–carbon double bond.46,92,98,104 This is also called “unzipping” if it occurs throughout the main carbon chain.13,105 It is proposed that the mechanism begins with removal of one hydrogen from the main carbon chain, forming a radical which then removes one fluorine atom forming a double bond. Unsaturated bonds are possible in a polyenic sequence which can then form other molecules by polyaromatization. They could also cross-link, forming cyclic organofluorines.104 The presence of Li can also induce dehydrofluorination, producing a lithiated unsaturated polymer, which may lead to formation of unsaturated organolithium fluoropolymers under conditions relevant to LIB recycling.15,44,46 For example, PVDF can react with metallic Li or lithiated graphite forming unsaturated fluorine compounds.106 Another process of degradation is by scission at the carbon–carbon bond forming halogenated or oxygenated compounds, as well as radicals.98,105 The scission can occur throughout the full polymer, resulting in the monomer VDF (Fig. 4).98
Apart from elevated temperatures, another recycling method for binders is solvent dissolution. Sarkar et al. (2021)47 observed that while pure PVDF was readily soluble in organic solvents such as tetrahydrofuran, the polymer became insoluble when it occurred as a film on Al substrates. Alternatively, concentrated sulfuric acid used in the main process of leaching during the hydrometallurgical stage may introduce unsaturated bonds, leading to break down of PVDF.14
Fluorochemical emissions measured during LIB recycling experiments
Only a handful of studies have begun to characterize product formation during LIB recycling and most have focused on gases. For example, in a benchtop study on combined mechanical and thermal treatment of LIBs, Hu et al. (2022)94 reported an increase in both the number and concentration of gaseous fluorinated substances formed with increasing treatment temperature. Detection of CHF, CH3F, CF4, COF2, CH2F˙ radical and SiF4 were attributed to decomposition of the binder, while the detected POF3 and PF5 likely appeared as a result of decomposition of LiPF6 (Fig. 4).94 Other studies have detected products such as SiF4, LiBF4, and AlF3, the latter of which may be attributed to HF corroding the Al current collector (Fig. 4).6,53,55,95 In general, the solids formed at elevated temperatures in LIB recycling are not well investigated as they often are considered as byproducts in the process, mentioned as residue, organic oil, char or tar.13,15,16,21,60,92,94 Characterization of these products is clearly needed to get a complete picture of emission of fluorinated substances (including PFAS) during LIB recycling.
Occurrence of LIB-derived PFAS in the environment
The use of PFAS in LIBs is primarily associated with PVDF in the binder material. Despite increasing fluoropolymer production in recent years,107 PVDF has not yet been identified in environmental samples. However, other fluoropolymer microparticles, such as the aforementioned binder material polytetrafluoroethylene (PTFE), have been reported in Mediterranean fish and remote Arctic Ocean sediment samples demonstrating a global presence.108,109 PTFE, followed by PVDF, have the highest global production volumes among fluoropolymers.107 The increasing use of PVDF in the renewable energy sector is likely to lead to increasing emissions and increasing likelihood of its detection in environmental samples. This is also expected for processing aids/emulsifiers which are necessary for the production of fluoropolymers.110–112 For example, PTFE has been manufactured using ammonium salts of PFOA and hexafluoropropylene oxide dimer acid (HFPO-DA; “GenX”), both of which are highly persistent and widespread contaminants of the global environment. While these substances occur at very low concentrations in fluoropolymers and are unlikely to contribute significantly to fluorochemical emissions during LIB recycling, their emission during the production of fluoropolymers has been shown to be considerable.113–115 The ammonium salt of perfluorononanoic acid (PFNA) was historically used as a processing aid in emulsion polymerization process for manufacturing PVDF, and released to the environment in large quantities.116 Due to regulatory pressure on long-chain PFAAs such as PFOA and PFNA, Solvay replaced them with other alternative PFAS (cyclic or polymeric functionalized perfluoropolyethers) for its PTFE and PVDF manufacture.117 In recent years, some of the major global manufacturers (namely Solvay, Arkema and Gujarat Fluorochemicals)118 have switched to using non-fluorinated processing aids (NFPAs) as substitutes for PFAS. While the use of NFPAs eliminates the concerns regarding releases of fluorinated surfactants such as PFNA etc. to the environment during manufacture of PVDF, a wide range of other fluorinated organic substances (i.e. fluorinated gases, residual monomers and oligomers, and fluorinated byproducts) will still be released, and these emissions should be closely monitored and regulated.119 Although new NFPAs exist for PVDF synthesis, emissions of PFAS-based emulsifiers might still occur from producers that have not changed their processes. Analysis of river water downstream of fluoropolymer manufacturing sites (including PVDF) detected high levels of PFAS contaminations in the recent past.113,120
PFAS used in electrolytes belong to a larger group of substances known as ionic liquids (ILs).121 Although not noted as an electrolyte, Zahn et al. (2016)122 identified the first fluorinated ionic liquid, trifluoromethane sulfonic acid (TFMSA), to be recognized as an environmental contaminant. TMFSA was detected in a variety of water compartments implying high persistence and mobility in the water cycle. Later, Neuwald et al. (2020)123 further identified another ionic liquid, categorized in this review article as an advanced electrolyte additive, tri(pentafluoroethyl)triphosphate (FAP), in μg L−1 levels in several German surface waters. Both TFMSA and FAP were first tentatively identified using tandem mass spectrometry experiments and their identities later confirmed with reference standards. Neuwald et al. (2021)121 used a suspect screening approach to identify 65 substances including substances noted above as possible compounds in LIB electrolyte, namely; PF6−, BF4−, bis(trifluoromethylsulfonyl)imide LiTFSI, bis(fluorosulfonyl)imide (LiFSI) and tris(trifluoromethylsulfonyl) methanide. They again identified TFMSA and FAP in these new samples. The inorganic ions FSI−, PF6− and BF4− are not PFAS22 but four of the identified fluorinated ionic liquids, namely; TFMSA, FAP and bis(trifluoromethylsulfonyl)imide and tris(trifluoromethylsulfonyl) methanide, meet the PFAS definition.22 These four fluorinated ILs could potentially be used in LIB electrolytes, but are likely to have other uses as well. For example, trifluoromethanesulfonic acid (TFMSA) and tris(trifluoromethanesulfonyl)methanide are mainly used as catalysts for chemical synthesis.124–126 FAP is used in electrochemical devices, including the above mentioned use in LIBs, and as a new media for application in modern technologies and chemical synthesis.127,128 Bis(trifluoromethylsulfonyl)imide and similar ILs have mostly been investigated for their use as corrosion inhibitors.129
While beyond the scope of this study, electronics associated with LIBs may also represent an important source of PFAS to the environment. Apart from the presence of fluorinated substances in LIBs such as electrodes and binder, electrolyte (and additives), and separator, this indicates that PFAS emissions in LIB recycling may also derive from the electronic components of LIBs as well as the devices which use LIBs. Indeed, a non-target investigation of wastewater from three US electronics fabrication facilities revealed >130 homologues spanning 41 PFAS classes, with perfluorobutane sulfonate (PFBS) occurring at concentrations of up to 8000 ng L−1.130 Further information on the use of PFAS in electronic products along with exposure risks during e-waste handling can be found in the recent review by Tansel (2022).131
Literature review outcomes
The following key findings from this review are summarized below:
• Information pertaining to the occurrence of PFAS in LIBs or their potential for emission to the environment during recycling is limited. This may be due to the confidential nature of LIB components and/or because the LIB recycling industry is still in its infancy.
• A wide range of organic and inorganic fluorinated substances (including PFAS) were reported in LIB components, including the electrodes and binder, electrolyte (and additives), and separator.
• Emission of fluorinated substances (including PFAS) may occur directly from LIB components, but also from formation during the recycling process.
• Hydrometallurgical recycling processes (including pretreatment steps) generally involve lower temperatures than pyrometallurgy. These lower temperatures may favor incomplete mineralization of PFAS and/or production of novel fluorinated substances.
• As LIB technology develops to meet increasing performance demands, an increasing number of fluorinated substances could be expected to be incorporated into LIBs. This development is uncertain due to the broad restriction proposal for PFAS in the EU.
• LIB recycling processes are undergoing constant refinement in response to economic incentives and regulatory measures but also to increase product yields. These changes (which will likely favor a hydrometallurgical process in the future) are expected to have an impact on the types of fluorinated substances formed and/or emitted during LIB recycling.
Future outlook and implications for policy makers, scientists, and industry
On 13 January 2023, authorities in Denmark, Germany, the Netherlands, Norway and Sweden submitted a restriction proposal for ∼10
000 PFAS to the European Chemicals Agency (ECHA).25 The proposal aims to reduce PFAS emissions into the environment and make consumer products and industrial processes safer for society. Notably, the proposal highlighted that PFAS-free alternatives for LIBs are currently unavailable, and that in order to meet the goals of the European Green Deal initiative, LIB production will continue to grow. While this implies that the European Commission (together with member states) will likely grant derogations for the continued use of PFAS in LIBs, industry will be strongly incentivized to look for alternatives, since derogations are not permanent and are proposed to be 5 or 12 years for applications within the energy sector which includes LIBs.25 Moreover, during the derogation period, manufacturers are expected to actively innovate towards eliminating uses of PFAS in their products and processes. In parallel to the PFAS restriction proposal, the latest EU proposal for battery regulation requires manufacturers to share information showing how vehicle batteries can be dismantled, transported and recycled safely, including reporting of environmental and/or human health impacts associated with battery components.4 Given this impending regulation, the EU battery recycling industry and associated actors in the product supply chain (e.g., automobile manufacturers) need to (a) identify and substitute current PFAS-containing LIB components with PFAS-free alternatives, and (b) identify, and mitigate any emission of PFAS which may occur during recycling.
Clearly, much work is needed by the research community as well as regulators and industry in order to quantify the scope of the problem regarding PFAS occurrence in LIBs, starting with estimates of the total volume of fluorochemicals used in LIBs to date. Only by developing such estimates can the relative importance of recycling-based emissions compared to other sources (e.g. municipal waste incineration) be determined. Once these inventories are performed, lab-based studies on the fate of fluorinated chemicals during LIB recycling are needed, as are investigations of solid, liquid and gaseous emissions from recycling facilities, using so-called “non-target” based analytical approaches. These data can be used to identify where emission reduction strategies should be introduced. Ultimately, such information is useful for life cycle toxicity assessment of LIBs, which will, in turn, facilitate comparisons among battery and recycling technologies.
Author contributions
Amanda Rensmo: writing – original draft, conceptualization, investigation, visualization; Eleni Savvidou: writing – review & editing, supervision; Ian Cousins: writing – review & editing, funding acquisition; Xianfeng Hu: writing – review & editing, funding acquisition; Steffen Schellenberger: writing – review & editing, conceptualization, funding acquisition, supervision; Jonathan Benskin: writing – review & editing, conceptualization, supervision.
Conflicts of interest
There are no conflicts of interest to declare.
Acknowledgements
Funding for this work was provided by the Swedish Energy Agency (SCOPE-LIBs project 48208-1), the Swedish Research Council FORMAS (grant number 2020-01978), and XPRES (Initiative for Excellence in Production Research). Mats Zackrisson (RISE), Martina Petranikova with Nils Zachmann and Nathalia Vieceli (Chalmers), Annika Ahlberg Tidblad (Volvo Cars) and Björn Hall (Stena Metall) along with colleagues within the SCOPE LIB, POPFREE and BASE industry collaborations are thanked for valuable input and fruitful discussions related to this work. Uppsala University is acknowledged for supporting the Master's thesis from which this article is based.
References
- G. Lombardo, B. Ebin, B.-M. Steenari, M. Alemrajabi, I. Karlsson and M. Petranikova, Comparison of the Effects of Incineration, Vacuum Pyrolysis and Dynamic Pyrolysis on the Composition of NMC-Lithium Battery Cathode-Material Production Scraps and Separation of the Current Collector, Resour. Conserv. Recycl., 2021, 164, 105142, DOI:10.1016/j.resconrec.2020.105142.
-
Global Electric Vehicle Outlook 2022, 2022, vol. 221, https://www.iea.org/reports/global-ev-outlook-2022/trends-in-electric-light-duty-vehicles, accessed 2022-12-02 Search PubMed.
- Y. P. Stenzel, F. Horsthemke, M. Winter and S. Nowak, Chromatographic Techniques in the Research Area of Lithium Ion Batteries: Current State-of-the-Art, Separations, 2019, 6(2), 26, DOI:10.3390/separations6020026.
- P. A. Christensen, P. A. Anderson, G. D. J. Harper, S. M. Lambert, W. Mrozik, M. A. Rajaeifar, M. S. Wise and O. Heidrich, Risk Management over the Life Cycle of Lithium-Ion Batteries in Electric Vehicles, Renew. Sustain. Energy Rev., 2021, 148, 111240, DOI:10.1016/j.rser.2021.111240.
-
A. Vezzini, 23 - Manufacturers, Materials and Recycling Technologies, in Lithium-Ion Batteries, ed. G. Pistoia, Elsevier, Amsterdam, 2014, pp. 529–551, DOI:10.1016/B978-0-444-59513-3.00023-6.
- J. Piątek, S. Afyon, T. M. Budnyak, S. Budnyk, M. H. Sipponen and A. Slabon, Sustainable Li-Ion Batteries: Chemistry and Recycling, Adv. Energy Mater., 2021, 11(43), 2003456, DOI:10.1002/aenm.202003456.
- J. Diekmann, C. Hanisch, T. Loellhoeffel, G. Schälicke and A. Kwade, Ecologically Friendly Recycling of Lithium-Ion Batteries - the LithoRec Process, ECS Trans., 2016, 73(1), 1, DOI:10.1149/07301.0001ecst.
-
M. F. Ashby, Materials and the environment: eco-informed material choice, Butterworth-Heinemann, Boston, 2013 Search PubMed.
- H. Pinegar and Y. R. Smith, Recycling of End-of-Life Lithium Ion Batteries, Part I: Commercial Processes, J. Sustain. Metall., 2019, 5(3), 402–416, DOI:10.1007/s40831-019-00235-9.
- D. A. Notter, M. Gauch, R. Widmer, P. Wäger, A. Stamp, R. Zah and H.-J. Althaus, Contribution of Li-Ion Batteries to the Environmental Impact of Electric Vehicles, Environ. Sci. Technol., 2010, 44(17), 6550–6556, DOI:10.1021/es903729a.
-
T. R. Jow, Electrolytes for Lithium and Lithium-Ion Batteries, Springer, New York, 2014 Search PubMed.
-
Proposal for a REGULATION OF THE EUROPEAN PARLIAMENT AND OF THE COUNCIL Concerning Batteries and Waste Batteries, Repealing Directive 2006/66/EC and Amending Regulation (EU) No 2019/1020; 2020, https://eur-lex.europa.eu/legal-content/EN/TXT/?uri=celex%3A52020PC0798, accessed 2022-11-15 Search PubMed.
- F. Tanaka, L. Gungaajav, O. Terakado, S. Kuzuhara and R. Kasuya, Dehydrofluorination Behavior of Poly(Vinylidene Fluoride) during Thermal Treatment Using Calcium Carbonate, Thermochim. Acta, 2021, 702, 178977, DOI:10.1016/j.tca.2021.178977.
- X. Fan, C. Song, X. Lu, Y. Shi, S. Yang, F. Zheng, Y. Huang, K. Liu, H. Wang and Q. Li, Separation and Recovery of Valuable Metals from Spent Lithium-Ion Batteries via Concentrated Sulfuric Acid Leaching and Regeneration of LiNi1/3Co1/3Mn1/3O2, J. Alloys Compd., 2021, 863, 158775, DOI:10.1016/j.jallcom.2021.158775.
- F. Diaz, Y. Wang, R. Weyhe and B. Friedrich, Gas Generation Measurement and Evaluation during Mechanical Processing and Thermal Treatment of Spent Li-Ion Batteries, Waste Manag., 2019, 84, 102–111, DOI:10.1016/j.wasman.2018.11.029.
- Y. Jie, S. Yang, Y. Li, F. Hu, D. Zhao, D. Chang, Y. Lai and Y. Chen, Waste Organic Compounds Thermal Treatment and Valuable Cathode Materials Recovery from Spent LiFePO4 Batteries by Vacuum Pyrolysis, ACS Sustainable Chem. Eng., 2020, 8(51), 19084–19095, DOI:10.1021/acssuschemeng.0c07424.
-
C. Ekberg and M. Petranikova, Chapter 7 - Lithium Batteries Recycling, in Lithium Process Chemistry, ed. A. Chagnes and J. Światowska, Elsevier, Amsterdam, 2015, pp. 233–267, DOI:10.1016/B978-0-12-801417-2.00007-4.
- M. Wang, Q. Tan, L. Liu and J. Li, A Facile, Environmentally Friendly, and Low-Temperature Approach for Decomposition of Polyvinylidene Fluoride from the Cathode Electrode of Spent Lithium-Ion Batteries, ACS Sustainable Chem. Eng., 2019, 7(15), 12799–12806, DOI:10.1021/acssuschemeng.9b01546.
- M. Wang, Q. Tan, L. Liu and J. Li, A Low-Toxicity and High-Efficiency Deep Eutectic Solvent for the Separation of Aluminum Foil and Cathode Materials from Spent Lithium-Ion Batteries, J. Hazard. Mater., 2019, 380, 120846, DOI:10.1016/j.jhazmat.2019.120846.
- E. Mossali, N. Picone, L. Gentilini, O. Rodrìguez, J. M. Pérez and M. Colledani, Lithium-Ion Batteries towards Circular Economy: A Literature Review of Opportunities and Issues of Recycling Treatments, J. Environ. Manage., 2020, 264, 110500, DOI:10.1016/j.jenvman.2020.110500.
- Y. Chen, N. Liu, Y. Jie, F. Hu, Y. Li, B. P. Wilson, Y. Xi, Y. Lai and S. Yang, Toxicity Identification and Evolution Mechanism of Thermolysis-Driven Gas Emissions from Cathodes of Spent Lithium-Ion Batteries, ACS Sustainable Chem. Eng., 2019, 7(22), 18228–18235, DOI:10.1021/acssuschemeng.9b03739.
- Z. Wang, A. M. Buser, I. T. Cousins, S. Demattio, W. Drost, O. Johansson, K. Ohno, G. Patlewicz, A. M. Richard, G. W. Walker, G. S. White and E. Leinala, A New OECD Definition for Per- and Polyfluoroalkyl Substances, Environ. Sci. Technol., 2021, 55(23), 15575–15578, DOI:10.1021/acs.est.1c06896.
- J. Glüge, M. Scheringer, I. T. Cousins, J. C. DeWitt, G. Goldenman, D. Herzke, R. Lohmann, C. A. Ng, X. Trier and Z. Wang, An Overview of the Uses of Per- and Polyfluoroalkyl Substances (PFAS), Environ. Sci.: Processes Impacts, 2020, 22(12), 2345–2373, 10.1039/D0EM00291G.
-
CompTox Chemicals Dashboard, https://comptox.epa.gov/dashboard/chemical-lists/pfasmaster, accessed 2022-11-15 Search PubMed.
-
All news - ECHA, https://echa.europa.eu/sv/-/echa-publishes-pfas-restriction-proposal, accessed 2023-02-24 Search PubMed.
- K. J. Hansen, L. A. Clemen, M. E. Ellefson and H. O. Johnson, Compound-Specific, Quantitative Characterization of Organic Fluorochemicals in Biological Matrices, Environ. Sci. Technol., 2001, 35(4), 766–770, DOI:10.1021/es001489z.
- J. P. Giesy and K. Kannan, Global Distribution of Perfluorooctane Sulfonate in Wildlife, Environ. Sci. Technol., 2001, 35(7), 1339–1342, DOI:10.1021/es001834k.
- I. T. Cousins, J. C. DeWitt, J. Glüge, G. Goldenman, D. Herzke, R. Lohmann, C. A. Ng, M. Scheringer and Z. Wang, The High Persistence of PFAS Is Sufficient for Their Management as a Chemical Class, Environ. Sci.: Processes Impacts, 2020, 22(12), 2307–2312, 10.1039/D0EM00355G.
- M. Houde, J. W. Martin, R. J. Letcher, K. R. Solomon and D. C. G. Muir, Biological Monitoring of Polyfluoroalkyl Substances: A Review, Environ. Sci. Technol., 2006, 40(11), 3463–3473, DOI:10.1021/es052580b.
- M. Houde, A. O. De Silva, D. C. G. Muir and R. J. Letcher, Monitoring of Perfluorinated Compounds in Aquatic Biota: An Updated Review, Environ. Sci. Technol., 2011, 45(19), 7962–7973, DOI:10.1021/es104326w.
- L. P. Burkhard, Evaluation of Published Bioconcentration Factor (BCF) and Bioaccumulation Factor (BAF) Data for Per- and Polyfluoroalkyl Substances Across Aquatic Species, Environ. Toxicol. Chem., 2021, 40(6), 1530–1543, DOI:10.1002/etc.5010.
- E. M. Sunderland, X. C. Hu, C. Dassuncao, A. K. Tokranov, C. C. Wagner and J. G. Allen, A Review of the Pathways of Human Exposure to Poly- and Perfluoroalkyl Substances (PFASs) and Present Understanding of Health Effects, J. Expo. Sci. Environ. Epidemiol., 2019, 29(2), 131–147, DOI:10.1038/s41370-018-0094-1.
- G. T. Ankley, P. Cureton, R. A. Hoke, M. Houde, A. Kumar, J. Kurias, R. Lanno, C. McCarthy, J. Newsted, C. J. Salice, B. E. Sample, M. S. Sepúlveda, J. Steevens and S. Valsecchi, Assessing the Ecological Risks of Per- and Polyfluoroalkyl Substances: Current State-of-the Science and a Proposed Path Forward, Environ. Toxicol. Chem., 2021, 40(3), 564–605, DOI:10.1002/etc.4869.
- S. E. Fenton, A. Ducatman, A. Boobis, J. C. DeWitt, C. Lau, C. Ng, J. S. Smith and S. M. Roberts, Per- and Polyfluoroalkyl Substance Toxicity and Human Health Review: Current State of Knowledge and Strategies for Informing Future Research, Environ. Toxicol. Chem., 2021, 40(3), 606–630, DOI:10.1002/etc.4890.
- K. M. Spaan, C. van Noordenburg, M. M. Plassmann, L. Schultes, S. Shaw, M. Berger, M. P. Heide-Jørgensen, A. Rosing-Asvid, S. M. Granquist, R. Dietz, C. Sonne, F. Rigét, A. Roos and J. P. Benskin, Fluorine Mass Balance and Suspect Screening in Marine Mammals from the Northern Hemisphere, Environ. Sci. Technol., 2020, 54(7), 4046–4058, DOI:10.1021/acs.est.9b06773.
- S. Windisch-Kern, E. Gerold, T. Nigl, A. Jandric, M. Altendorfer, B. Rutrecht, S. Scherhaufer, H. Raupenstrauch, R. Pomberger, H. Antrekowitsch and F. Part, Recycling Chains for Lithium-Ion Batteries: A Critical Examination of Current Challenges, Opportunities and Process Dependencies, Waste Manag., 2022, 138, 125–139, DOI:10.1016/j.wasman.2021.11.038.
-
H. Berg, Batteries for Electric Vehicles: Materials and Electrochemistry, Cambridge University Press, Cambridge, 2015 Search PubMed.
-
D. Bresser, E. Paillard and S. Passerini, Chapter 6 - Lithium-Ion Batteries (LIBs) for Medium- and Large-Scale Energy Storage: Current Cell Materials and Components, in Advances in Batteries for Medium and Large-Scale Energy Storage, ed. C. Menictas, M. Skyllas-Kazacos and T. M. Lim, Woodhead Publishing Series in Energy, Woodhead Publishing, 2015, pp. 125–211, DOI:10.1016/B978-1-78242-013-2.00006-6.
-
R. Amin-Sanayei and W. He, Chapter 10 - Application of Polyvinylidene Fluoride Binders in Lithium-Ion Battery, in Advanced Fluoride-Based Materials for Energy Conversion, ed. T. Nakajima and H. Groult, Elsevier, 2015, pp. 225–235, DOI:10.1016/B978-0-12-800679-5.00010-5.
- A. Gören, C. M. Costa, M. M. Silva and S. Lanceros-Mendez, Influence of Fluoropolymer Binders on the Electrochemical Performance of C-LiFePO4 Based Cathodes, Solid State Ionics, 2016, 295, 57–64, DOI:10.1016/j.ssi.2016.07.012.
- S. F. Lux, F. Schappacher, A. Balducci, S. Passerini and M. Winter, Low Cost, Environmentally Benign Binders for Lithium-Ion Batteries, J. Electrochem. Soc., 2010, 157(3), A320, DOI:10.1149/1.3291976.
- P. P. Prosini, M. Carewska, C. Cento and A. Masci, Preparation of a Composite Anode for Lithium-Ion Battery Using a Commercial Water-Dispersible Non-Fluorinated Polymer Binder, Ionics, 2015, 21(9), 2401–2408, DOI:10.1007/s11581-015-1431-1.
- X. Mönnighoff, P. Murmann, W. Weber, M. Winter and S. Nowak, Post-Mortem Investigations of Fluorinated Flame Retardants for Lithium Ion Battery Electrolytes by Gas Chromatography with Chemical Ionization, Electrochim. Acta, 2017, 246, 1042–1051, DOI:10.1016/j.electacta.2017.06.125.
- F. Zou and A. Manthiram, A Review of the Design of Advanced Binders for High-Performance Batteries, Adv. Energy Mater., 2020, 10(45), 2002508, DOI:10.1002/aenm.202002508.
- C. M. Costa, M. M. Silva and S. Lanceros-Méndez, Battery Separators Based on Vinylidene Fluoride (VDF) Polymers and Copolymers for Lithium Ion Battery Applications, RSC Adv., 2013, 3(29), 11404–11417, 10.1039/C3RA40732B.
- A. D. Pasquier, F. Disma, T. Bowmer, A. S. Gozdz, G. Amatucci and J.-M. Tarascon, Differential Scanning Calorimetry Study of the Reactivity of Carbon Anodes in Plastic Li-Ion Batteries, J. Electrochem. Soc., 1998, 145(2), 472, DOI:10.1149/1.1838287.
- A. Sarkar, R. May, S. Ramesh, W. Chang and L. E. Marbella, Recovery and Reuse of Composite Cathode Binder in Lithium Ion Batteries, ChemistryOpen, 2021, 10(5), 545–552, DOI:10.1002/open.202100060.
- Z. Chen, L. Christensen and J. R. Dahn, A Study of the Mechanical and Electrical Properties of a Polymer/Carbon Black Binder System Used in Battery Electrodes, J. Appl. Polym. Sci., 2003, 90(7), 1891–1899, DOI:10.1002/app.12863.
- A. Taguet, B. Ameduri and A. Dufresne, Crosslinking and Characterization of Commercially Available Poly(VDF-Co-HFP) Copolymers with 2,4,4-Trimethyl-1,6-Hexanediamine, Eur. Polym. J., 2006, 42(10), 2549–2561, DOI:10.1016/j.eurpolymj.2006.04.012.
- S. N. Bryntesen, A. H. Strømman, I. Tolstorebrov, P. R. Shearing, J. J. Lamb and O. Stokke Burheim, Opportunities for the State-of-the-Art Production of LIB Electrodes—A Review, Energies, 2021, 14(5), 1406, DOI:10.3390/en14051406.
-
J. Paulsen, H. Hong and H. S. Ahn, Inventors. Umicore, assignee, Water-Based Cathode Slurry for a Lithium Ion Battery, US Pat., US20160218356A1, 2016 Search PubMed.
- J. Duan, X. Tang, H. Dai, Y. Yang, W. Wu, X. Wei and Y. Huang, Building Safe Lithium-Ion Batteries for Electric Vehicles: A Review, Electrochem. Energy Rev., 2020, 3(1), 1–42, DOI:10.1007/s41918-019-00060-4.
- S. Bertilsson, F. Larsson, M. Furlani, I. Albinsson and B.-E. Mellander, Lithium-Ion Battery Electrolyte Emissions Analyzed by Coupled Thermogravimetric/Fourier-Transform Infrared Spectroscopy, J. Power Sources, 2017, 365, 446–455, DOI:10.1016/j.jpowsour.2017.08.082.
- M. Petranikova, P. L. Naharro, N. Vieceli, G. Lombardo and B. Ebin, Recovery of Critical Metals from EV Batteries via Thermal Treatment and Leaching with Sulphuric Acid at Ambient Temperature, Waste Manag., 2022, 140, 164–172, DOI:10.1016/j.wasman.2021.11.030.
- S. Balachandran, K. Forsberg, T. Lemaître, N. Vieceli, G. Lombardo and M. Petranikova, Comparative Study for Selective Lithium Recovery via Chemical Transformations during Incineration and Dynamic Pyrolysis of EV Li-Ion Batteries, Metals, 2021, 11(8), 1240, DOI:10.3390/met11081240.
- F. Larsson, P. Andersson and B.-E. Mellander, Lithium-Ion Battery Aspects on Fires in Electrified Vehicles on the Basis of Experimental Abuse Tests, Batteries, 2016, 2(2), 9, DOI:10.3390/batteries2020009.
- J. Zhao, L. Liao, F. Shi, T. Lei, G. Chen, A. Pei, J. Sun, K. Yan, G. Zhou, J. Xie, C. Liu, Y. Li, Z. Liang, Z. Bao and Y. Cui, Surface Fluorination of Reactive Battery Anode Materials for Enhanced Stability, J. Am. Chem. Soc., 2017, 139(33), 11550–11558, DOI:10.1021/jacs.7b05251.
- L. Zhu, Y. Liu, W. Wu, X. Wu, W. Tang and Y. Wu, Surface Fluorinated LiNi0.8Co0.15Al0.05O2 as a Positive Electrode Material for Lithium Ion Batteries, J. Mater. Chem. A, 2015, 3(29), 15156–15162, 10.1039/C5TA02529J.
- S. Luiso and P. Fedkiw, Lithium-Ion Battery Separators: Recent Developments and State of Art, Curr. Opin. Electrochem., 2020, 20, 99–107, DOI:10.1016/j.coelec.2020.05.011.
- L. Zhu and M. Chen, Development of a Two-Stage Pyrolysis Process for the End-Of-Life Nickel Cobalt Manganese Lithium Battery Recycling from Electric Vehicles, Sustainability, 2020, 12(21), 9164, DOI:10.3390/su12219164.
- C. Arbizzani, F. De Giorgio and M. Mastragostino, Characterization Tests for Plug-in Hybrid Electric Vehicle Application of Graphite/LiNi0.4Mn1.6O4 Cells with Two Different Separators and Electrolytes, J. Power Sources, 2014, 266, 170–174, DOI:10.1016/j.jpowsour.2014.05.016.
- G. Kang and Y. Cao, Application and Modification of Poly(Vinylidene Fluoride) (PVDF) Membranes – A Review, J. Membr. Sci., 2014, 463, 145–165, DOI:10.1016/j.memsci.2014.03.055.
- S. Nowak and M. Winter, Review—Chemical Analysis for a Better Understanding of Aging and Degradation Mechanisms of Non-Aqueous Electrolytes for Lithium Ion Batteries: Method Development, Application and Lessons Learned, J. Electrochem. Soc., 2015, 162(14), A2500, DOI:10.1149/2.0121514jes.
- S. D. Muzio, A. Paolone and S. Brutti, Thermodynamics of the Hydrolysis of Lithium Salts: Pathways to the Precipitation of Inorganic SEI Components in Li-Ion Batteries, J. Electrochem. Soc., 2021, 168(10), 100514, DOI:10.1149/1945-7111/ac2aca.
- Y. Miao, P. Hynan, A. von Jouanne and A. Yokochi, Current Li-Ion Battery Technologies in Electric Vehicles and Opportunities for Advancements, Energies, 2019, 12(6), 1074, DOI:10.3390/en12061074.
- T. Zhang and E. Paillard, Recent Advances toward High Voltage, EC-Free Electrolytes for Graphite-Based Li-Ion Battery, Front. Chem. Sci. Eng., 2018, 12(3), 577–591, DOI:10.1007/s11705-018-1758-z.
- X. He, B. Yan, X. Zhang, Z. Liu, D. Bresser, J. Wang, R. Wang, X. Cao, Y. Su, H. Jia, C. P. Grey, H. Frielinghaus, D. G. Truhlar, M. Winter, J. Li and E. Paillard, Fluorine-Free Water-in-Ionomer Electrolytes for Sustainable Lithium-Ion Batteries, Nat. Commun., 2018, 9(1), 5320, DOI:10.1038/s41467-018-07331-6.
- F. Ahmed, I. Choi, T. Ryu, S. Yoon, M. M. Rahman, W. Zhang, H. Jang and W. Kim, Highly Conductive Divalent Fluorosulfonyl Imide Based Electrolytes Improving Li-Ion Battery Performance: Additive Potentiating Electrolytes Action, J. Power Sources, 2020, 455, 227980, DOI:10.1016/j.jpowsour.2020.227980.
- M. Bolloli, J. Kalhoff, F. Alloin, D. Bresser, M. L. Phung Le, B. Langlois, S. Passerini and J.-Y. Sanchez, Fluorinated Carbamates as Suitable Solvents for LiTFSI-Based Lithium-Ion Electrolytes: Physicochemical Properties and Electrochemical Characterization, J. Phys. Chem. C, 2015, 119(39), 22404–22414, DOI:10.1021/acs.jpcc.5b07514.
- J. Mun, J. Lee, T. Hwang, J. Lee, H. Noh and W. Choi, Lithium Difluoro(Oxalate)Borate for Robust Passivation of LiNi0.5Mn1.5O4 in Lithium-Ion Batteries, J. Electroanal. Chem., 2015, 745, 8–13, DOI:10.1016/j.jelechem.2015.02.034.
-
Z. Chen, Z. Zhang and K. Amine, Chapter 1 - High Performance Lithium-Ion Batteries Using Fluorinated Compounds, in Advanced Fluoride-Based Materials for Energy Conversion, ed. T. Nakajima and H. Groult, Elsevier, 2015, pp. 1–31, DOI:10.1016/B978-0-12-800679-5.00001-4.
- S. Nowak and M. Winter, The Role of Sub- and Supercritical CO2 as “Processing Solvent” for the Recycling and Sample Preparation of Lithium Ion Battery Electrolytes, Molecules, 2017, 22(3), 403, DOI:10.3390/molecules22030403.
- T. Hou, G. Yang, N. N. Rajput, J. Self, S.-W. Park, J. Nanda and K. A. Persson, The Influence of FEC on the Solvation Structure and Reduction Reaction of LiPF6/EC Electrolytes and Its Implication for Solid Electrolyte Interphase Formation, Nano Energy, 2019, 64, 103881, DOI:10.1016/j.nanoen.2019.103881.
- J. Im, J. Lee, M.-H. Ryou, Y. M. Lee and K. Y. Cho, Fluorinated Carbonate-Based Electrolyte for High-Voltage Li(Ni0.5Mn0.3Co0.2)O2/Graphite Lithium-Ion Battery, J. Electrochem. Soc., 2017, 164(1), A6381, DOI:10.1149/2.0591701jes.
- L. Xia, H. Miao, C. Zhang, G. Z. Chen and J. Yuan, Review—Recent Advances in Non-Aqueous Liquid Electrolytes Containing Fluorinated Compounds for High Energy Density Lithium-Ion Batteries, Energy Storage Mater., 2021, 38, 542–570, DOI:10.1016/j.ensm.2021.03.032.
- K. Deng, Q. Zeng, D. Wang, Z. Liu, G. Wang, Z. Qiu, Y. Zhang, M. Xiao and Y. Meng, Nonflammable Organic Electrolytes for High-Safety Lithium-Ion Batteries, Energy Storage Mater., 2020, 32, 425–447, DOI:10.1016/j.ensm.2020.07.018.
- M. He, C.-C. Su, C. Peebles and Z. Zhang, The Impact of Different Substituents in Fluorinated Cyclic Carbonates in the Performance of High Voltage Lithium-Ion Battery Electrolyte, J. Electrochem. Soc., 2021, 168(1), 010505, DOI:10.1149/1945-7111/abd44b.
- J. Xia, R. Petibon, A. Xiao, W. M. Lamanna and J. R. Dahn, Some Fluorinated Carbonates as Electrolyte Additives for Li(Ni0.4Mn0.4Co0.2)O2/Graphite Pouch Cells, J. Electrochem. Soc., 2016, 163(8), A1637, DOI:10.1149/2.0831608jes.
- O. Lavi, S. Luski, N. Shpigel, C. Menachem, Z. Pomerantz, Y. Elias and D. Aurbach, Electrolyte Solutions for Rechargeable Li-Ion Batteries Based on Fluorinated Solvents, ACS Appl. Energy Mater., 2020, 3(8), 7485–7499, DOI:10.1021/acsaem.0c00898.
- Y. M. Todorov, M. Aoki, H. Mimura, K. Fujii, N. Yoshimoto and M. Morita, Thermal and Electrochemical Properties of Nonflammable Electrolyte Solutions Containing Fluorinated Alkylphosphates for Lithium-Ion Batteries, J. Power Sources, 2016, 332, 322–329, DOI:10.1016/j.jpowsour.2016.09.119.
- T. Doi, R. J. Taccori, R. Fujii, T. Nagashima, T. Endo, Y. Kimura and M. Inaba, Non-Flammable and Highly Concentrated Carbonate Ester-Free Electrolyte Solutions for 5 V-Class Positive Electrodes in Lithium-Ion Batteries, ChemSusChem, 2021, 14(11), 2445–2451, DOI:10.1002/cssc.202100523.
- S. P. Kühn, K. Edström, M. Winter and I. Cekic-Laskovic, Face to Face at the Cathode Electrolyte Interphase: From Interface Features to Interphase Formation and Dynamics, Adv. Mater. Interfac., 2022, 9(8), 2102078, DOI:10.1002/admi.202102078.
- W. Lv, Z. Wang, H. Cao, Y. Sun, Y. Zhang and Z. Sun, A Critical Review and Analysis on the Recycling of Spent Lithium-Ion Batteries, ACS Sustainable Chem. Eng., 2018, 6(2), 1504–1521, DOI:10.1021/acssuschemeng.7b03811.
-
A New EU Regulatory Framework for Batteries. https://www.europarl.europa.eu/RegData/etudes/ATAG/2022/729285/EPRS_ATA(2022)729285_EN.pdf, accessed 2022-11-15.
- H. Pinegar and Y. R. Smith, Recycling of End-of-Life Lithium-Ion Batteries, Part II: Laboratory-Scale Research Developments in Mechanical, Thermal, and Leaching Treatments, J. Sustain. Metall., 2020, 6(1), 142–160, DOI:10.1007/s40831-020-00265-8.
-
D. Kushnir, Lithium Ion Battery Recycling Technology, Environmental Systems Analysis, Chalmers University, Göteborg, 2015, Report no.: 2015:18 Search PubMed.
- E. Fan, L. Li, Z. Wang, J. Lin, Y. Huang, Y. Yao, R. Chen and F. Wu, Sustainable Recycling Technology for Li-Ion Batteries and Beyond: Challenges and Future Prospects, Chem. Rev., 2020, 120(14), 7020–7063, DOI:10.1021/acs.chemrev.9b00535.
- S. Kim, J. Bang, J. Yoo, Y. Shin, J. Bae, J. Jeong, K. Kim, P. Dong and K. Kwon, A Comprehensive Review on the Pretreatment Process in Lithium-Ion Battery Recycling, J. Clean. Prod., 2021, 294, 126329, DOI:10.1016/j.jclepro.2021.126329.
- X. Hu, E. Mousa and G. Ye, Recovery of Co, Ni, Mn, and Li from Li-Ion Batteries by Smelting Reduction - Part II: A Pilot-Scale Demonstration, J. Power Sources, 2021, 483, 229089, DOI:10.1016/j.jpowsour.2020.229089.
- N. Zachmann, M. Petranikova and B. Ebin, Electrolyte Recovery from Spent Lithium-Ion Batteries Using a Low Temperature Thermal Treatment Process, J. Ind. Eng. Chem., 2022, 118, 351–361, DOI:10.1016/j.jiec.2022.11.020.
- Y. Yao, M. Zhu, Z. Zhao, B. Tong, Y. Fan and Z. Hua, Hydrometallurgical Processes for Recycling Spent Lithium-Ion Batteries: A Critical Review, ACS Sustainable Chem. Eng., 2018, 6(11), 13611–13627, DOI:10.1021/acssuschemeng.8b03545.
- G. Lombardo, B. Ebin, M. R. Foreman, B.-M. Steenari and M. Petranikova, Incineration of EV Lithium-Ion Batteries as a Pretreatment for Recycling – Determination of the Potential Formation of Hazardous by-Products and Effects on Metal Compounds, J. Hazard. Mater., 2020, 393, 122372, DOI:10.1016/j.jhazmat.2020.122372.
- Y. Yang, G. Huang, S. Xu, Y. He and X. Liu, Thermal Treatment Process for the Recovery of Valuable Metals from Spent Lithium-Ion Batteries, Hydrometallurgy, 2016, 165, 390–396, DOI:10.1016/j.hydromet.2015.09.025.
- X. Hu, E. Mousa, L. Ånnhagen, Z. Musavi, M. Alemrajabi, B. Hall and G. Ye, Complex Gas Formation during Combined Mechanical and Thermal Treatments of Spent Lithium-Ion-Battery Cells, J. Hazard. Mater., 2022, 431, 128541, DOI:10.1016/j.jhazmat.2022.128541.
- M. Grützke, V. Kraft, B. Hoffmann, S. Klamor, J. Diekmann, A. Kwade, M. Winter and S. Nowak, Aging Investigations of a Lithium-Ion Battery Electrolyte from a Field-Tested Hybrid Electric Vehicle, J. Power Sources, 2015, 273, 83–88, DOI:10.1016/j.jpowsour.2014.09.064.
- A. Hammami, N. Raymond and M. Armand, Runaway Risk of Forming Toxic Compounds, Nature, 2003, 424(6949), 635–636, DOI:10.1038/424635b.
- C. L. Campion, W. Li and B. L. Lucht, Thermal Decomposition of LiPF6-Based Electrolytes for Lithium-Ion Batteries, J. Electrochem. Soc., 2005, 152(12), A2327, DOI:10.1149/1.2083267.
-
J. T. Stapler, W. J. Barnes and W. E. Yelland, Thermal degradation of polyvinylidene fluoride and polyvinyl fluoride by oven pyrolysis, United States Army Natick Labs -Clothing and Organic Materials Lab, 1968 Search PubMed.
- D. A. Ellis, S. A. Mabury, J. W. Martin and D. C. G. Muir, Thermolysis of Fluoropolymers as a Potential Source of Halogenated Organic Acids in the Environment, Nature, 2001, 412(4), 321–324, DOI:10.1038/35085548.
- A. L. Myers, K. J. Jobst, S. A. Mabury and E. J. Reiner, Using Mass Defect Plots as a Discovery Tool to Identify Novel Fluoropolymer Thermal Decomposition Products, J. Mass Spectrom., 2014, 49(4), 291–296, DOI:10.1002/jms.3340.
- N. Awanis Hashim, Y. Liu and K. Li, Stability of PVDF Hollow Fibre Membranes in Sodium Hydroxide Aqueous Solution, Chem. Eng. Sci., 2011, 66(8), 1565–1575, DOI:10.1016/j.ces.2010.12.019.
- S.-S. Choi and Y.-K. Kim, Analysis of Pyrolysis Products of Poly(Vinylidene Fluoride-Co-Hexafluoropropylene) by Pyrolysis-Gas Chromatography/Mass Spectrometry, J. Fluorine Chem., 2014, 165, 33–38, DOI:10.1016/j.jfluchem.2014.06.004.
- G. Zhang, X. Yuan, Y. He, H. Wang, W. Xie and T. Zhang, Organics Removal Combined with in Situ Thermal-Reduction for Enhancing the Liberation and Metallurgy Efficiency of LiCoO2 Derived from Spent Lithium-Ion Batteries, Waste Manag., 2020, 115, 113–120, DOI:10.1016/j.wasman.2020.05.030.
- S.-S. Choi and Y.-K. Kim, Microstructural Analysis of Poly(Vinylidene Fluoride) Using Benzene Derivative Pyrolysis Products, J. Anal. Appl. Pyrolysis, 2012, 96, 16–23, DOI:10.1016/j.jaap.2012.02.014.
- A. J. de Jesus Silva, M. M. Contreras, C. R. Nascimento and M. F. da Costa, Kinetics of Thermal Degradation and Lifetime Study of Poly(Vinylidene Fluoride) (PVDF) Subjected to Bioethanol Fuel Accelerated Aging, Heliyon, 2020, 6(7), e04573, DOI:10.1016/j.heliyon.2020.e04573.
- N. Lingappan, L. Kong and M. Pecht, The Significance of Aqueous Binders in Lithium-Ion Batteries, Renew. Sustain. Energy Rev., 2021, 147, 111227, DOI:10.1016/j.rser.2021.111227.
- B. Améduri, The Promising Future of Fluoropolymers, Macromol. Chem. Phys., 2020, 221(8), 1900573, DOI:10.1002/macp.201900573.
- M. Bergmann, V. Wirzberger, T. Krumpen, C. Lorenz, S. Primpke, M. B. Tekman and G. Gerdts, High Quantities of Microplastic in Arctic Deep-Sea Sediments from the HAUSGARTEN Observatory, Environ. Sci. Technol., 2017, 51(19), 11000–11010, DOI:10.1021/acs.est.7b03331.
- G. Capillo, S. Savoca, G. Panarello, M. Mancuso, C. Branca, V. Romano, G. D'Angelo, T. Bottari and N. Spanò, Quali-Quantitative Analysis of Plastics and Synthetic Microfibers Found in Demersal Species from Southern Tyrrhenian Sea (Central Mediterranean), Mar. Pollut. Bull., 2020, 150, 110596, DOI:10.1016/j.marpolbul.2019.110596.
- K. Prevedouros, I. T. Cousins, R. C. Buck and S. H. Korzeniowski, Sources, Fate and Transport of Perfluorocarboxylates, Environ. Sci. Technol., 2006, 40(1), 32–44, DOI:10.1021/es0512475.
-
S. Schellenberger, The Missing Links: Towards an Informed Substitution of Durable Water Repellent Chemicals for Textiles, PhD thesis, Stockholm University, 2019 Search PubMed.
- L. Meng, B. Song, Y. Lu, K. Lv, W. Gao, Y. Wang and G. Jiang, The Occurrence of Per- and Polyfluoroalkyl Substances (PFASs) in Fluoropolymer Raw Materials and Products Made in China, J. Environ. Sci., 2021, 107, 77–86, DOI:10.1016/j.jes.2021.01.027.
- Y. Shi, R. Vestergren, L. Xu, X. Song, X. Niu, C. Zhang and Y. Cai, Characterizing Direct Emissions of Perfluoroalkyl Substances from Ongoing Fluoropolymer Production Sources: A Spatial Trend Study of Xiaoqing River, China, Environ. Pollut., 2015, 206, 104–112, DOI:10.1016/j.envpol.2015.06.035.
- M. Strynar, S. Dagnino, R. McMahen, S. Liang, A. Lindstrom, E. Andersen, L. McMillan, M. Thurman, I. Ferrer and C. Ball, Identification of Novel Perfluoroalkyl Ether Carboxylic Acids (PFECAs) and Sulfonic Acids (PFESAs) in Natural Waters Using Accurate Mass Time-of-Flight Mass Spectrometry (TOFMS), Environ. Sci. Technol., 2015, 49(19), 11622–11630, DOI:10.1021/acs.est.5b01215.
- W. A. Gebbink, L. van Asseldonk and S. P. J. van Leeuwen, Presence of Emerging Per- and Polyfluoroalkyl Substances (PFASs) in River and Drinking Water near a Fluorochemical Production Plant in the Netherlands, Environ. Sci. Technol., 2017, 51(19), 11057–11065, DOI:10.1021/acs.est.7b02488.
- Z. Wang, I. T. Cousins, M. Scheringer, R. C. Buck and K. Hungerbühler, Global Emission Inventories for C4–C14 Perfluoroalkyl Carboxylic Acid (PFCA) Homologues from 1951 to 2030, Part I: Production and Emissions from Quantifiable Sources, Environ. Int., 2014, 70, 62–75, DOI:10.1016/j.envint.2014.04.013.
- Z. Wang, I. T. Cousins, M. Scheringer and K. Hungerbühler, Fluorinated Alternatives to Long-Chain Perfluoroalkyl Carboxylic Acids (PFCAs), Perfluoroalkane Sulfonic Acids (PFSAs) and Their Potential Precursors, Environ. Int., 2013, 60, 242–248, DOI:10.1016/j.envint.2013.08.021.
- A. Tullo, The Fluoropolymer Industry’s Survival Plan, Chem. Eng. News, 2023, 101(8), 20–22, DOI:10.1021/cen-10108-feature2.
- R. Lohmann, I. T. Cousins, J. C. DeWitt, J. Glüge, G. Goldenman, D. Herzke, A. B. Lindstrom, M. F. Miller, C. A. Ng, S. Patton, M. Scheringer, X. Trier and Z. Wang, Are Fluoropolymers Really of Low Concern for Human and Environmental Health and Separate from Other PFAS?, Environ. Sci. Technol., 2020, 54(20), 12820–12828, DOI:10.1021/acs.est.0c03244.
- X. Song, R. Vestergren, Y. Shi, J. Huang and Y. Cai, Emissions, Transport, and Fate of Emerging Per- and Polyfluoroalkyl Substances from One of the Major Fluoropolymer Manufacturing Facilities in China, Environ. Sci. Technol., 2018, 52(17), 9694–9703, DOI:10.1021/acs.est.7b06657.
- I. Neuwald, M. Muschket, D. Zahn, U. Berger, B. Seiwert, T. Meier, J. Kuckelkorn, C. Strobel, T. P. Knepper and T. Reemtsma, Filling the Knowledge Gap: A Suspect Screening Study for 1310 Potentially Persistent and Mobile Chemicals with SFC- and HILIC-HRMS in Two German River Systems, Water Res., 2021, 204, 117645, DOI:10.1016/j.watres.2021.117645.
- D. Zahn, T. Frömel and T. P. Knepper, Halogenated Methanesulfonic Acids: A New Class of Organic Micropollutants in the Water Cycle, Water Res., 2016, 101, 292–299, DOI:10.1016/j.watres.2016.05.082.
- I. J. Neuwald, D. Zahn and T. P. Knepper, Are (Fluorinated) Ionic Liquids Relevant Environmental Contaminants? High-Resolution Mass Spectrometric Screening for per- and Polyfluoroalkyl Substances in Environmental Water Samples Led to the Detection of a Fluorinated Ionic Liquid, Anal. Bioanal. Chem., 2020, 412(20), 4881–4892, DOI:10.1007/s00216-020-02606-8.
- R. D. Howells and J. D. Mc Cown, Trifluoromethanesulfonic Acid and Derivatives, Chem. Rev., 1977, 77(1), 69–92, DOI:10.1021/cr60305a005.
-
H. Buchholz, K.-D. Franz, H. Mayr, M.-A. Funke and A. Zehetner, Use of Tris(Trifluoromethylsulfonyl)Methane, in Addition to Alkaline Metal Salts and Alkaline-Earth Metal Salts Thereof as Catalysts during c-c Bonding Syntheses and the Novel Magnesium Salt of Tris(Trifluoromethylsulfonyl)Methane, KR20010024410A, March 26 2001, https://patents.google.com/patent/KR20010024410A/en, accessed 2023-04-14.
- K. Ishihara, Y. Hiraiwa and H. Yamamoto, Homogeneous Debenzylation Using Extremely Active Catalysts: Tris(Triflyl)Methane, Scandium(III) Tris(Triflyl)Methide, and Copper(II) Tris(Triflyl)Methide, Synlett, 2000, 2000(01), 80–82, DOI:10.1055/s-2000-6436.
- N. V. Ignat'ev, U. Welz-Biermann, A. Kucheryna, G. Bissky and H. Willner, New Ionic Liquids with Tris(Perfluoroalkyl)Trifluorophosphate (FAP) Anions, J. Fluorine Chem., 2005, 126(8), 1150–1159, DOI:10.1016/j.jfluchem.2005.04.017.
-
N. Greinert, M. Uerdingen, L. Beylage, N. Ignatyev, J. H. Wilson, M. J. Goulding, R. Kemp, A. N. Smith, P. Bartlett, P. Barthen, W. Frank and R. S. Garcia, Particles for Electrophoretic Displays, WO2012072218A1, 2012.
- M. A. Assenine, B. Haddad, A. Paolone, S. A. Brandán, M. Goussem, D. Villemin, M. Boumediene, M. Rahmouni and S. Bresson, Synthesis, Thermal Properties, Vibrational Spectra and Computational Studies of Trioctylmethylammonium Bis(Trifluoromethylsulfonyl)Imide Ionic Liquid, J. Mol. Struct., 2021, 1232, 130085, DOI:10.1016/j.molstruc.2021.130085.
- P. Jacob, K. A. Barzen-Hanson and D. E. Helbling, Target and Nontarget Analysis of Per- and Polyfluoralkyl Substances in Wastewater from Electronics Fabrication Facilities, Environ. Sci. Technol., 2021, 55(4), 2346–2356, DOI:10.1021/acs.est.0c06690.
- B. Tansel, PFAS Use in Electronic Products and Exposure Risks during Handling and Processing of E-Waste: A Review, J. Environ. Manage., 2022, 316, 115291, DOI:10.1016/j.jenvman.2022.115291.
Footnote |
† S. S. and J. P. B. contributed equally and share last authorship. |
|
This journal is © The Royal Society of Chemistry 2023 |
Click here to see how this site uses Cookies. View our privacy policy here.