DOI:
10.1039/B811536B
(Review Article)
Energy Environ. Sci., 2009,
2, 19-34
Vertically-aligned nanostructures of ZnO for excitonic solar cells: a review
Received
7th July 2008
, Accepted 29th September 2008
First published on 25th November 2008
Abstract
This work is a brief account of the most recent developments observed in the application of ZnO nanostructured materials in excitonic solar cells (organic, hybrid and dye sensitized solar cells). Special emphasis is made to one-dimensional (1D), vertically-aligned nanostructures (nanowires NW, nanorods NR) of ZnO semiconductor oxide and the extensive research work invested in recent years for its application as an electron acceptor material in solar cells. Our aim is to give the reader a broad overview of this semiconductor oxide and to understand the causes, advantages and disadvantages, for its application in a well-aligned nanostructure form. We briefly describe the most applied methodologies for its synthesis as well as the effect on surface area, electron transport and charge recombination when it is applied as an electron transport material in excitonic solar cells (XSCs). The importance of low-cost and easy-scalable synthesis techniques, as well as stability issues on these solar cells are discussed. Finally, we include a brief analysis of the possible future trends for the application of this interesting semiconductor oxide in XSCs.
Irene Gonzalez-Valls | Irene Gonzalez-Valls studied chemistry at the University of Barcelona where she received her laureate degree in organic chemistry in 2006. She obtained a Masters degree in organic chemistry at Prof. Roeland J. M. Nolte's laboratory (Netherlands). She is currently pursuing PhD studies at the Nanoscience and Nanotechnology Research Centre (CIN2, CSIC-ICN). Her research is devoted to the synthesis of well-ordered nanostructured oxides for excitonic solar cells applying hydrothermal, electrochemical and nanofabrication techniques. |
Monica Lira-Cantu | Dr Monica Lira-Cantu received her PhD in 1997 at the Institute of Materials Science of Barcelona (ICMAB) working on the application of hybrid organic–inorganic materials for lithium batteries. From 1999 to 2001 she worked as a research scientist at ExxonMobil Research & Engineering (USA) and returned to Spain in 2002. She is currently a permanent research scientist at the Nanoscience and Nanotechnology Research Center (CIN2, CSIC-ICN) in Barcelona (Spain). Her research interests are the synthesis and application of nanostructured materials for excitonic solar cells and sensors |
Broader context
Excitonic solar cells (organic, hybrid and dye sensitized) are the best examples of efficient and environmental friendly energy-conversion devices. The possibility of being fabricated by low-cost and easy-scalable solution processing techniques has driven the technology into the marketplace. Nanostructured materials are key constituents of these solar cells. The improvement in photovoltaic efficiency is achievable by the application of advanced structures built at a nanoscale: nanoparticles, nanorods, nanocables, nanosheets, core-shell, among many others. ZnO has become a promising semiconductor oxide when applied as an electron transport material. It presents properties closely related to the best semiconductor oxide used up to date, TiO2, but contrary to the former, it is possible to obtain ZnO in a wide variety of nano-forms by low-cost and scalable synthesis methods. Yet another breakthrough in ZnO-based photovoltaics seems possible if nanostructures could be obtained in a controlled, well-ordered and reproducible manner. This review describes the evolution and future potential for the application of nanostructured ZnO in next-generation excitonic solar cells.
|
Introduction
In our need for highly efficient, low cost and CO2-free sources of energy, the conversion of sunlight into electricity has materialized as one of the most encouraging alternatives. Among the different emerging photovoltaic options, XSCs are promising candidates for achieving the basic criteria for large scale commercialization: they are highly efficient devices that employ low-cost materials and offer the possibility of being fabricated by large-scale and inexpensive (solution processing) techniques.1,2 The most important examples of XSCs are Organic Solar Cells (OSC), Hybrid Solar Cells (HSC) and Dye Sensitized Solar Cells (DSC) and their main difference with respect to conventional inorganic solar cells (ISC) resides in their photoconversion mechanism. In ISCs the absorption of light leads to the direct formation of free electron–hole pairs in the bulk of the material and the direct production of charge carriers.1,2 In XSCs, the presence of organic semiconductors implies that the absorption of photons from sunlight produces an exciton, a tightly bound electron–hole pair, which must be split for charge generation. Exciton dissociation takes place at the interface between the constituent semiconductors. Thus, XSCs encompass photovoltaic systems largely dependent on interfacial processes. The reliance on the crystallinity of the materials for photovoltaic response indicates that while highly crystalline and chemically pure materials are required for ISCs (e.g.silicon), less pure and therefore less expensive compounds can be applied in XSCs (e.g. TiO2).2,3 Although ISCs have the advantage of high efficiency (∼20%) and long lifetime (25 y), state-of-the-art XSCs have improved enormously in the past few years demonstrating efficiencies as high as 11.3% and lifetimes of 10
000 h for DSC4,5,126,158 and about 5–6% efficiency for OSC.5 These promising results have encouraged many research groups, as well as industrial partners, to investigate different ways to improve XSCs performance, especially device efficiency and lifetime.
In this review, an introduction to the application of ZnO nanostructured electrodes is given, particularly vertically-aligned nanostructures like nanowires (NW), nanorods (NR), nanotips or similar. We discuss XSCs where inorganic semiconductor oxides, such as ZnO, act as the electron transport material, i.e.HSC and DSC but not OSCs.2,6 We summarize the most applied techniques used for ZnO fabrication and review the advantages and disadvantages observed during its application. We discuss the need for higher solar cell stability and the development of synthesis techniques that are easily scalable and produce well-aligned, ordered and reproducible nanostructures at the nanosize scale. Finally, we give a brief description of the possible future development in XSCs.
Excitonic solar cells: organic (OSC), hybrid (HSC) and dye sensitized solar cells (DSC)
Classification
In XSCs the transformation of photons of light into electrical energy takes place in three basic steps: (1) Photon absorption and exciton formation, (2) Charge separation or exciton dissociation and (3) Charge transport. The active materials (donors and acceptors) required for these processes to take place can be organic or inorganic semiconductors. If we classify XSCs by the type of semiconductor material applied, then we can identify three general types: OSCs, HSCs and DSCs. In OSCs both materials are purely organic semiconductors, for example the blend between two conducting organic polymers or a mixture between C60 derivative and a conjugated polymer.5,29 In the case of HSC, the device is characterized for the presence of, at least, one phase of an inorganic semiconductor (e.g.CdSe, TiO2) and a second phase of a conducting organic polymer. Although DSC can be classified also as HSC (due to the application of organic and inorganic materials), here we consider DSC as a different type of XSC, due to the presence of a liquid electrolyte.† The inorganic materials in XSCs can be in any form (nanoparticles, nanorods, tetrapods, nanosheets, etc).
The application of organic semiconductors in XSC presents some drawbacks, like low electronic mobility of, for example, conducting organic polymers, with values typically around 10−4cm2V−1s−1.7 Thus, HSCs have been shown to enhance performance by the introduction of electron transport and charge transfer materials.7,8,11 The formation of a donor–acceptor junction yields a charge-separation state that should be within the organic semiconductor diffusion length, this is, about 20 nm.8 To enhance organic solar cell performance Hegeer and Friend et al., proposed the bulk-heterojunction concept.9,10 In this concept an intimate mixture in the nanoscale range between the n-type (C60 derivatives) and p-type (polymer) materials allows for a large-area donor–acceptor interface for efficient exciton dissociation.11 The electron is accepted by the material with greater electron affinity and the hole by the material with lower ionization potential.12 Conducting organic polymers act as the hole transport material (HTM) in these systems, although other organic semiconductors can be applied. The concept has been extended to other n–p type systems, where inorganic materials are applied as electron acceptors such as inorganic semiconductors and semiconductor oxides. These types of solar cells known as HSC are easily recognized by the direct physical contact between the electron transport material (ETM) and the hole transport material (HTM), or the inorganic and organic semiconductors, respectively. In HSC, the donor and the acceptor semiconductors are found in a direct physical contact so the exciton dissociation takes place efficiently at the interfaces. Thus, one of the active materials has the dual function of light-harvesting and charge carrier transport (hole or electron) while the other phase is only responsible for (the opposite) charge carrier transport. Although a similar mechanism for exciton dissociation is observed in the DSC,3 there is an important difference. The light-harvesting and charge transport is carried out by different active materials: in DSC a Dye is absorbed on the surface of a nanostructured semiconductor oxide, usually nanoparticles of TiO2, and is responsible for light absorption. Upon excitation an electron is injected into the conduction band of the oxide and transported through the nanoparticle network; an organic hole conductor (liquid redox electrolyte) is responsible for the regeneration of the Dye. The spatial separation between the light-harvesting compound (Dye) and the charge carrier material in DSC seems to be the key to their higher efficiency and longer lifetime.13,14 Nevertheless, it is not clear yet the advantages and disadvantages in terms efficiency and lifetime proposed for this separation.15
There are many inorganic semiconductors applied as nanostructured materials for XSCs; semiconductor oxides such as TiO2,16–24,74,113 Nb2O5,22–25ZnO,23,25–28,108 SnO2,30 CeO2 or CeO2-TiO2,23,25 or inorganic semiconductors applied in HSCs; CdSe,31copper indium disulfide CuInS2,32–35CuInSe2 and CuInTe2,35 PbS,36–40 GsAs,41,42PbSe,43 or HgTe nanocrystals,44,46 among others. As will be explained, ZnO has recently emerged as a promising candidate due to its semiconducting properties which are very similar to the most used semiconductor oxide, TiO2, but are especially due to the possibility of obtaining ZnO nanostructures by easy and low-cost techniques.45
In a HSC where the light-harvesting compound is an organic semiconductor (e.g. a conducting organic polymer) the application of vertically-aligned oxide nanostructures arise from the need to overcome problems observed at the bulk heterojunction. In the former type of heterojunction, an inorganic semiconductor oxide nanoparticle is dispersed within the conjugated polymer matrix. The resulting oxide nanoparticle/polymer blend must be annealed to improve nanoparticle connection and to favor electron pathway through the electrode. Nevertheless, these devices are still limited by incomplete exciton dissociation due to the isolation of some nanoparticles from each other after thermal treatment. The later eliminates the possibility of efficient electron transport reducing overall device efficiency. A nanostructured thin film made of vertical-aligned nanowires provides a higher interfacial area between the donor and the acceptor material (polymer/oxide, respectively) with highly-efficient electron transport pathways. In the case of DSCs, the replacement of the nanoparticle electrode by vertically-aligned nanostructures has also emerged as a possible way to obtain faster electron transport thus improving solar cell efficiency. Moreover, the urge to replace problematic liquid electrolytes in DSC by solid hole-conductors with slower kinetics6 impels the application of faster electron transport materials like the vertically-aligned nanostructures. Fig. 1 shows a schematic representation of a XSC applying vertically-aligned ZnO nanostructured electrode. The hole conductor can be a conducting organic polymer in HSC and solid-state dye sensitized solar cells (ss-DSC), and a redox liquid electrolyte in the case of DSC.
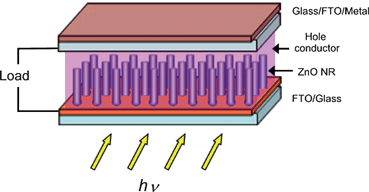 |
| Fig. 1 Schematic representation of an XSC applying ZnO nanowires as the electron transport material. In a DSC the ZnO nanowires are loaded with an adsorbed layer of a light-harvesting Dye and the hole conductor is typically a liquid electrolyte with a I−/I3−redox couple. In a HSC the hole conductor and light-harvesting compound is a conjugated polymer. | |
Zinc oxide (ZnO) is well-known for its multiple properties; it exhibits semiconducting, piezoelectric or pyroelectric properties, among many others. It can be obtained in a wide variety of nanostructures; nanoparticles, core-shell nanoparticles, tetrapods, hierarchical structures, nanoflower, nanosheets, vertically-aligned nanosheets, nanowires, nanorods, nanotips, nanotubes or, more recently, branched nanostructures have been reported.47 Thus, it is not surprising to find ZnO in many devices: optoelectronics, sensors, biomedical, electrochemical, etc. The control of its structures at nanosize level provides novel and enhanced electrical, mechanical, chemical and optical properties that help us to understand the many processes occurring in new generation solar cells49 Its development has followed a trend based on the need to improve efficiency by increasing surface area (enhancing the interface between semiconductor constituents), or the application of single-crystalline nanostructures that are able to reduce electron hopping steps and enhance electron mobility.48 Large amounts of information and reviews about ZnO properties, synthesis, characterization and applications are available in the literature,47–50 so we have limited this section to a general overview about some of the most interesting aspects of this oxide, especially those related to its application in solar cells.
ZnO properties
Despite the fact that TiO2 is the most used semiconductor oxide in XSCs, ZnO is being intensely investigated because of its similarities with the former, i.e. it is a wide band gap semiconductor oxide (3.37 eV) with a conduction band edge located at approximately the same level as TiO2. The electron mobility of ZnO has been proven to be higher than TiO2.51,52 The longer electron lifetimes observed for ZnO means lower charge recombination which is beneficial for solar cell performance. An important advantage of ZnO over TiO2 is that it can be synthesized applying a wide range of synthesis techniques;47–50 to obtain a great variety of different morphologies and nanostructured electrodes, especially vertically-aligned nanostrucutres.62 Some of these methodologies have been shown to be easily scalable and suitable for many substrates,45 which makes ZnO very attractive for fabricating complete solar cell devices by applying low-cost solution processing techniques. Surprisingly, the highest efficiency XSCs applying ZnO have only reached 6–7%53,161 which is less than the 11.3% obtained with the best DSC applying TiO2.4 Thus it is important to have carefully control parameters, such as dye or polymer concentration, pH or sensitization with time, in order to improve solar cell efficiency.
Dye immersion time and ZnO solubility.
In DSC, the reasons for the lower efficiency of XSC applying ZnO are not yet clear but it seems to be related to the stability of the oxide surface and surface area density. In DSC, some authors have reported that, contrary to TiO2, low dye absorption time is required for higher solar cell efficiency60,80,81 which indicates some basic differences in surface chemistry between these two oxides. Keis et al. reported the difference between dye-sensitization on TiO2 and ZnO.52 In TiO2 there is strong adsorption of the carboxyl groups to the surface which favors monolayer growth and usually 20–24 h immersion time needed. In ZnO, however, the sensitization process follows more complicated steps: diffusion of the dye, adsorption on the ZnO surface, dissolution of Zn surface atoms and formation of [Dye–Zn2+] complex.52 Moreover, the acidity of the –COOH binding groups from the Dye affects the chemical stability of the ZnO, which dissolves and precipitates as a [Dye–Zn2+] complex, responsible for the poor electron injection from the Dye.51,52 The formation of this complex has not been observed for TiO2. In ZnO the surface is predominantly positively charged at a pH below the point of zero charge (pzc) and negatively charged above it. The pH for the dye loading process is usually around 5 but in ZnO proceeds at about 9.52 Other groups have also reported the effect that ZnO treatments in basic media (KOH) has on the absorption–desorption of dye molecules.157,159–161 Problems related to the instability of the ZnO surface, in the presence of conducting polymers, have not been addressed yet for HSC. For example, Janssen et al. reported that the stabilization of polymers increases with increasing nanoparticle loading in blends made by polymers/ZnO.116,125 This stabilization is clearly observed when blends are applied and is the basic principle for some devices.155,156 Nevertheless, Krebs et al. reported that the application of polymers containing –COOH groups result in the stabilization of the polymer/ZnO nanoparticles, enhancing the lifetime of the solar cell up to hundreds of hours.119 In HSC these studies are very recent and in-depth research efforts are needed to understand this behavior.
Wettability.
Another example considers one of the main problems observed in XSCs when applying high surface area electrodes: wettability. The organic semiconductor (dye, polymer or similar) must penetrate and reach the whole surface area of the electron transport oxide for good charge transport, a task that is sometimes problematic during solar cell fabrication. The possibility of overcoming these problems may be found within the ZnO surface itself, which is known to present high sensitivity towards conditions of humidity or UV irradiation22–24 which affect its interaction with dyes, polymers or other organic semiconductors.52,54,80,81 Some laboratories have reported properties of superhydrophobicity and superhydrophilicity on ZnO under different conditions. These properties can be reversibly switched by the alternation of UV irradiation and dark storage. The effect has been reported to be related to the interaction between surface photosensitivity and the nanostructure of the oxide and should be analyzed for its relation to solar cell activity.55 These sometimes contradictory results, indicate that ZnO presents many other properties, which are still under investigation or not yet analyzed under conditions of sunlight irradiation or in the interaction with components of the solar cell.
Synthesis methods: requirements to obtain optimal nanostructures
The synthesis of 1D ZnO nanostructures have been recently reviewed for semiconductor oxides in general56 and for ZnO nanostructures in particular.57,58Nanostructures of ZnO can be found as simple nanoparticles or as nanorods, nanobelts, branched nanorods, nanowires, ultranarrow nanobelts, hierarchical nanostructures, nanocombs, nansoprings, nanospirals, nanorings, core-shell nanostructures, nanocages, nanoflowers, among many others.54,56 There are many possible methods of fabricating ZnO nanomaterials and the observed properties depend to a great extent on the preparation conditions. It is also difficult to establish the optimal synthesis methodology for solar cell applications because the efficiency of a XSC depends on many aspects and not only on ZnO nanostructure, like thin film thickness, nanostructure dimension or surface area and also on overall device preparation such as the polymer or dye applied, back contacts, active area, etc. Up to date, the most attractive synthesis technique for obtaining well-aligned nanostructures of ZnO for photovoltaic applications is the hydrothermal method (HT). Although more expensive and less straight-forward techniques have been applied, including high-temperature vapor-phase deposition techniques (physical and chemical vapor-phase deposition),69 metal organic vapor deposition (MOCVD), chemical vapor deposition (CVD), atomic layer deposition (ALD), among others (see Table 1 and 2).
Table 1 Application of vertically-aligned nanostructures of ZnO in dye sensitized solar cells (DSCs). HT: Hydrothermal, SP: Spray Pyrolysis, S: Sputtering, PCEM: Pulsed Current Electrolysis Method, TM: Template, MOCVD: Metal Organic Vapor Deposition, VD: Vapor Deposition, CVD: Chemical Vapor Deposition, TD: Thermal Decomposition, ALD: Atomic Layer Deposition, CBD: Chemical Bath Deposition, EQ: Electrochemical Deposition
Nanorod (NR) or nanowire (NW) dimensions |
Synthesis |
Dye
|
Light intensity |
J
sc
|
V
oc
|
FF
|
η
|
Ref. |
Ø (nm) |
L(µm)
|
method |
|
(mW/cm2) |
(mA/cm2) |
(V) |
(%) |
(%) |
|
150 |
1.8 |
MOCVD
|
porphyrin- |
— |
— |
— |
— |
0.1 |
82
|
based |
3.5 |
HT + VD |
N719 |
100 |
1.17 |
0.76 |
25 |
0.22 |
83
|
8 |
HT
|
N719 |
100 |
1.3 |
0.67 |
32 |
0.3 |
65
|
110 |
4–5 |
HT
|
N3 |
23.6 |
0.49 |
0.34 |
45 |
0.32 |
84
|
190 |
7 |
HT
|
N719 |
100 |
1.5 |
0.8 |
40 |
0.38 |
85
|
|
3.2 |
MOCVD
|
N719 |
100 |
2.04 |
0.662 |
41 |
0.55 |
86
|
70–100 |
5 |
CVD
|
N719 |
100 |
1.2 |
0.82 |
61 |
0.60 |
87
|
500 |
10 |
HT
|
N719 |
100 |
1.94 |
0.45 |
70 |
0.62 |
88
|
60 |
1 |
HT + TD |
Rose bengal |
2 |
0.049 |
0.55 |
55 |
0.7 |
89
|
50 |
4.6 |
CVD
|
Mercurochrome
|
100 |
3.30 |
0.516 |
49 |
0.83 |
90
|
130–200 |
16–17 |
HT
|
N719 |
100 |
5.3–5.85 |
0.61–0.71 |
36–38 |
1.2–1.5 |
59
|
∼150 |
4.5 |
ALD + TM |
N719 |
90 |
3.3 |
0.739 |
64 |
1.6 |
91
|
150 |
2.6 |
HT
|
N719 |
100 |
2.88 |
0.6 |
54 |
0.94 |
93
|
150 |
4.0 |
HT
|
N719 |
100 |
3.97 |
0.59 |
54 |
1.27 |
93
|
150 |
5.1 |
HT
|
N719 |
100 |
4.84 |
0.61 |
48 |
1.42 |
93
|
150 |
10.8 |
HT
|
N719 |
100 |
5.37 |
0.64 |
49 |
1.69 |
93
|
100–120 |
14 |
HT
|
N719 |
100 |
6.79 |
0.54 |
50 |
1.7 |
94
|
200 |
11 |
HT
|
N719 |
100 |
5.5 |
0.65 |
53 |
1.9 |
95
|
30–70 |
0.24 |
HT
|
N3 |
42 |
1.02 |
0.52 |
39 |
0.5 |
96
|
30–70 |
0.85 |
HT
|
N3 |
42 |
1.96 |
0.56 |
42 |
1.1 |
96
|
30–70 |
1.1 |
HT
|
N3 |
42 |
3.46 |
0.57 |
38 |
1.8 |
96
|
30–70 |
1.9 |
HT
|
N3 |
42 |
5.18 |
0.55 |
36 |
2.4 |
96
|
Others:
Nanoparticles
(NP), doped NP, Mixed NP + NW (Mix), Branched NW (
b-NW
),
Nanosheets
(NS), Terrace NW (
t-NW
),
Nanotube
(NT), Porous single crystal (PSC).
|
Structure |
Dimensions |
Synthesis |
Dye
|
Light |
J
sc
|
V
oc
|
FF
|
η
|
Ref. |
method |
intensity |
(mA/cm2) |
(V) |
(%) |
(%) |
b-NR
|
100 nm NR 20 nm |
MOCVD
|
N719 |
100 |
1.62 |
0.74 |
38 |
0.5 |
64
|
branches |
t-NR
|
|
CBD + HT |
N719 |
|
8.0 |
0.42 |
27 |
0.9 |
104
|
b-NR
|
|
MOCVD
|
N719 |
100 |
3 |
|
|
1.1 |
103
|
Mix |
30–300 nm |
HT
|
Mercurochrome
|
100 |
6.28 |
0.61 |
62 |
2.37 |
99
|
Mix |
30–300 nm NW |
HT
|
Mercurochrome
|
100 |
9.06 |
0.58 |
60 |
3.2 |
100
|
15 nm NP |
NS |
|
|
N-719
|
100 |
13.8 |
0.56 |
44 |
3.3 |
97
|
NS |
|
Pyrolysis
|
N-719
|
100 |
11.2 |
0.58 |
|
3.9 |
102
|
NT
|
210 nm pore |
ALD + TM |
N-719
|
100 |
3.3 |
0.73 |
64 |
1.6 |
92
|
329 nm spacing |
NP |
20 nm |
Commercial |
N-719
|
100 |
6.0 |
0.701 |
49 |
1.8 |
171
|
NT
|
11 nm |
CBD + Pyrolysis |
N-719
|
100 |
12.6 |
0.67 |
48 |
4.1 |
98
|
NT
|
11 nm |
CBD + Pyrolysis |
N-719
|
14 |
1.5 |
0.60 |
72 |
4.6 |
98
|
NP |
|
|
N-719
|
100 |
1.3 |
0.56 |
68 |
5 |
53
|
TiO2/NR |
NR: 100 nm L |
Sol–gel |
N3 |
|
11.4 |
0.76 |
50 |
5.8 |
105
|
25 nm W |
Pop-corn |
100 nm aggregates of |
Hydrolysis
|
N3 |
100 |
18.7 |
0.63 |
45.1 |
5.4 |
172–173
|
10–15 nm nanoparticles |
(6.2) |
Doped NP |
26–60 nm |
Sol–gel |
N-719
|
10 |
6.49 |
0.79 |
37 |
6 |
101
|
NP |
20–30 nm |
Commercial |
N-719
|
100 |
18.11 |
0.62 |
58 |
6.58 |
157
|
PSC
|
— |
EQ |
D-149
|
100 |
— |
— |
— |
7.2 |
159–161
|
Table 2 Some examples of HSC applying ZnO nanostructures as the electron transport material and conducting polymers as the hole transport material. HT: Hydrothermal, SP: Spray Pyrolysis, S: Sputtering, PCEM: Pulsed Current Electrolysis Method, TM: Template, DF: Dense Film, NP: Nanoparticles, NR: Nanorods
Type of ZnO |
Synthesis technique |
Organic component |
Substrate |
Light intensity |
J
sc
|
V
oc
|
FF
|
η
|
Ref. |
|
D (nm) |
L (µm) |
(mW/cm2) |
(mA/cm2) |
(V) |
(%) |
(%) |
|
NP |
— |
— |
SP, S |
MEH–PPV |
ITO |
100 |
50 nA |
0.41 |
— |
— |
109
|
0.28 |
Mesoporous/NP |
— |
— |
TM |
P3HT |
ITO |
100 |
0.44 |
0.46 |
— |
— |
118
|
NP |
— |
— |
HT
|
P3HT |
ITO |
100 |
9.55 |
0.31 |
42 |
— |
120
|
P3HT/Perylene |
NP |
— |
— |
HT
|
P3MHOCT |
ITO |
100 |
0.7 |
0.65 |
56 |
0.05 |
119
|
NR
|
110 |
1.25 |
HT
|
P3HT + |
ITO |
100 |
1.73 |
0.30 |
38.9 |
0.20 |
107
|
interfacial modifier |
DF
|
— |
— |
HT
|
Dye/P3HT |
ITO |
100 |
0.5 |
0.22 |
— |
0.03 |
108
|
P3HT/P3HT |
NP |
70/150 |
— |
HT
|
Dye/P3HT |
ITO |
100 |
2.0 |
0.17 |
— |
0.05 |
108
|
P3HT/P3HT |
NR
|
60/100 |
0.5/1 |
HT
|
Dye/P3HT |
ITO |
100 |
3.2 |
0.22 |
— |
0.20 |
108
|
P3HT/P3HT |
NP (55%) |
|
|
HT
|
PPAT
|
ITO |
100 |
0.79 |
0.71 |
54 |
0.30 |
121
|
NR
|
100 |
0.25–0.5 |
HT
|
P3HT |
ITO |
100 |
2.2 |
0.44 |
56 |
0.53 |
110
|
NP (55%) |
— |
— |
HT
|
PPHT
|
ITO |
100 |
0.38 |
0.64 |
54 |
0.12 |
122
|
NP (55%) |
— |
— |
HT
|
Dye/PPHT |
ITO |
100 |
1.45 |
0.62 |
61 |
0.55 |
122
|
NR
|
50 |
0.18 |
PCE |
P3HT |
Au-coated ITO |
100 |
0.30 |
0.335 |
40 |
0.04 |
106
|
NR
|
50 |
0.18 |
PCE |
P3HT/TiO2 |
Au-coated ITO |
100 |
1.96 |
0.38 |
39 |
0.29 |
106
|
NR ZnO/TiO2 |
50 |
0.18 |
PCE |
P3HT/TiO2 |
Au-coated ITO |
100 |
2.20 |
0.40 |
35 |
0.31 |
106
|
NR ZnO/TiO2 |
50 |
0.18 |
PCE |
P3HT/TiO2–Pyr |
Au-coated ITO |
100 |
2.67 |
0.49 |
45 |
0.59 |
106
|
NP |
4.9 |
— |
HT
|
P3HT |
ITO |
100 |
2.38 |
0.70 |
60 |
0.9 |
116
|
NP |
— |
— |
HT
|
P3HT |
ITO |
100 |
3.5 |
0.83 |
50 |
1.4 |
114
|
NP |
4–6 |
— |
HT
|
MDMO–PPV |
ITO |
85 |
3.46 |
0.845 |
42 |
1.47 |
115
|
NP |
4.9 |
— |
HT
|
MDMO–PPV |
ITO |
71 |
2.40 |
0.814 |
59 |
1.6 |
125
|
3.9 |
— |
0.80 |
50 |
NP |
10 |
— |
HT
|
P3HT |
ITO |
100 |
6.1 |
0.75 |
52 |
2.4 |
163
|
NR
|
20–40 |
0.3 |
HT
|
P3HT/PCBM |
ITO |
100 |
9.6 |
0.57 |
50 |
2.7 |
112
|
In general, the hydrothermal technique is based on a two-step method involving the coating of a substrate with ZnO nanoparticles (seeds) of less than 10 nm in diameter. Every ZnO seed works as a nucleation site for the formation of ZnO nanowires under mid-wet conditions.70 The synthesis conditions, like zinc concentration in solution, growth time or growth temperature, determine the final nanorod dimension and quality. Also, the stability of precursor ZnO seeds (nanoparticles) or the substrates to be applied are important factors affecting the final ZnO nanostructures with reproducible results. As an example, Fig. 2 shows a graph of the variation of nanorods length and diameter depending on the additives added during synthesis. In this case, the authors applied an additive, polyethylenimine (PEI)59 and searched for large surface area electrodes so that a higher amount of Dye absorption can be obtained when applied in a DSC. Nanorods as long as 30 µm were observed when PEI additive was used, without additive the length of the nanorods was not more than 5 µm, and their diameters also increased with time (see Fig. 2). Yet, the longest nanorods, 20–25 µm, show only 1/5 of the surface area of an electrode made of nanoparticles. The best photovoltaic efficiency was not higher than 1.5%, applying nanorods of 16–17 µm in length and between 120–300 nm in diameter.59
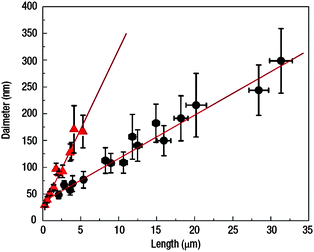 |
| Fig. 2 Effect of polyethylenimine additive on the dimensions of ZnO nanorods. ● indicate synthesis with PEI and ▲ without PEI.59 | |
The resulting vertically-aligned nanorods present an aspect similar to those shown in Fig. 3a. In this case, however, the authors applied chemical bath deposition technique to grow ZnO nanorods at 95 °C, a method closely related to the hydrothermal technique described above. The NRs obtained in this case, had thinner diameters, about 50 nm, closer in value to the electron diffusion length (∼20 nm) of organic semiconductors. The obtained ZnO nanostructures can be characterized by scanning electron microscopy (SEM), transmission electron microscopy (TEM), high-resolution TEM (HRTEM), powder X-ray diffraction (XRD), etc. HRTEM analyses demonstrates the synthesis of a high-crystalline ZnO structure (Fig. 3b) as required for high electron mobility.48
As can be observed in Table 1 and 2, vertically-aligned nanostructures of ZnO have been extensively applied in XSCs. Nevertheless, in terms of vertical and well-ordered alignment, the current synthesis methodologies applied for their fabrication produce irreproducible nanostructures with dimensions that are too far away from ideal electrode characteristics. Synthesis conditions must be controlled carefully, a minimal change in synthesis condition or even in the roughness of the underlying substrate can affect nanorods dimension.61,162 For example, images in Fig. 4 were obtained with careful control of the synthesis conditions applied, from concentration of reactants to growth time and temperature, as well as additives. The only difference between the ZnO nanorods in these images is the distance from the substrate to the bottom of the reaction flask used during synthesis which was 10 times larger for the nanorods observed in Fig 4b. NRs with almost the same length were obtained (500 nm) in both cases, but the surface density and NR diameter were different in each case.61
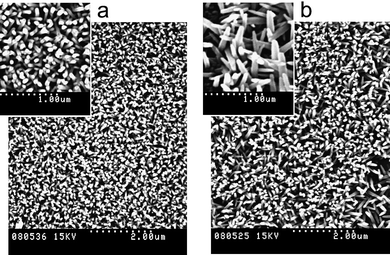 |
| Fig. 4 Top view of arrays of vertically-aligned ZnO nanorods synthesized by the hydrothermal method on indium tin oxide (ITO) substrates.45 Distance from the substrate to the bottom of the reaction flask was 10 times larger for (b) with respect to (a). Nanorod diameter: (a) ∼75 nm and (b) ∼150 nm.61 | |
Another example is the effect of ambient humidity on the degree of alignment in ZnO nanorod arrays. Lee, et al, report that close-packed ZnO nanorod arrays with [001] axis perpendicular to the substrate can be obtained only when seeded at ∼20% relative humidity (RH) at room temperature (RT). When the seeding RH was raised to ∼60%, the polydispersity in the diameter and length of the ZnO nanorods increased. Thus, these authors report an optimal seeding humidity of 30–40% for the synthesis of ordered ZnO nanorod arrays.162
Table 1 and 2 show the dimensions of vertically-aligned ZnO nanostructures applied in XSCs (DSCs and HSCs) and the photovoltaic performance observed in each case. The tables are arranged by increasing efficiency and for comparison a few examples of XSCs applying ZnO electrodes made of colloidal nanoparticles are included. We observed that the highest solar cell efficiency obtained corresponds to solar cells applying ZnO nanorods with very thin diameters (30–70 nm) and lengths up to 1.9 µm.96 Nevertheless, highest efficiency is still observed for electrodes made of colloidal nanoparticles, in DSC the best efficiency is 6% and for HSC 2.4%. An innovative synthesis method developed by Prof. Yoshida's group has been applied to obtain porous single crystal ZnO. Although the obtained ZnO nanostructure is not made from nanowires or nanorods of ZnO, the as-prepared material presents interconnected and vertically-aligned channels of crystalline ZnO. The voids left behind during synthesis present the exact required nanosize for dye loading. The technique is based on a one-step electrochemical self-assembly where the oxide is electrodeposited in the presence of organic dye molecules which are de-loaded after synthesis to give porous thin films of crystalline ZnO. The ZnO electrodes prepared by this technique and analyzed in DSCs resulted in a 7.2% efficiency,161 the highest reported efficiency to date from applying ZnO in XSCs.159–161 Moreover, the versatility of the technique permits the fabrication of ZnO thin films at low temperature and applying flexible substrates.
Surface area and design of ZnO nanostructure.
The key to high efficiency when applying porous single crystal as described above, is related to the optimal distance obtained between ZnO and the Dye. Thus, it is not difficult to realize that in order to overcome all the aforementioned issues and to obtain maximum photovoltaic performance, vertically-aligned nanostructured thin films of ZnO must be optimized in 3D by selecting the height, diameter and spacing between nanorods as schematically represented in Fig. 6. The ideal nanostructure is not easy or straightforward to obtain. The fact that electron diffusion length is in the range of 20 nm suggests that the best well-aligned nanostructure could have vertical nanostructures of about 20–40 nm in diameter and space between them of about 40 nm. Thus, a dense array of long and thin single-crystalline nanowires electrode would be ideal. Besides electrical properties, the nanostructure of the electrode is of crucial importance to obtain higher surface and higher electron transport. Thus in a more sophisticated nanostructure, a vertically-aligned branched-nanowire network (see Fig. 5c) could, in principle, benefit even more for both a larger surface area for light-harvesting compound loading (polymer or Dye) and more efficient electron transport.64,67–79 In addition, some groups report that the use of vertical nanostructures may not be optimal for light-harvesting because some photons can fall on the gap of adjacent nanorods and the light loss could be significant. In vertically-aligned ZnO branched nanorods (Fig. 5c) the improvement could be double: higher surface area and increased interaction with light, maintaining good electron transport.68 Another possibility based on the porous single crystal concept described previously159–161 where nanoporosity is in the exact nanosize range required for dye loading (or re-loading), ensuring ideal oxide–dye interaction. Moreover, the nanostructure represents an up-standing and well-crystalline ZnO nanostructure which is not completely vertical (See Fig. 5d) thus improving surface area for charge collection.
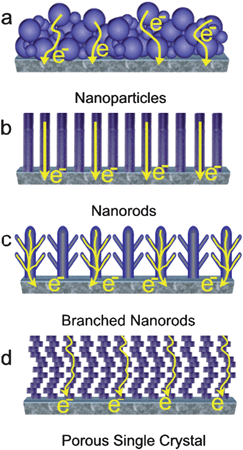 |
| Fig. 5 Schematic representation of the possible electron path taking place on different nanostructured electrodes made with (a) nanoparticles , (b) nanorods , (c) branched nanorods and (d) porous single crystal. | |
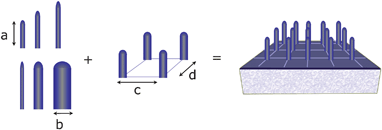 |
| Fig. 6 Schematic representation of a vertically-aligned electrode where the height, diameter and spacing between nanorods can be modified to suit the best properties for electron transport and dye/polymer absorption. | |
Thus a careful design of the nanostructured electrode made of vertically-aligned nanorods should be made in order to fulfill the best requirements for the type of solar cell where will be applied. For example, one of the most problematic issues observed in XSCs is Dye or polymer infiltration (wettability), a solvent-soluble Dye could reach the whole surface area of the nanostructured electrode more easily than a viscous polymer solution which has to penetrate into dense packed nanowire network. Research work on wettability of ZnO nanostructures seems to be missing from the literature.
The possibility of obtaining highly porous ZnO nanomaterials with crystalline structure as already reported, suggests that there is room for improvement on solar cell efficiency. Nevertheless, all the synthesis methods found in the literature to obtain ZnO nanostructures applied in XSCs show irreproducible results. The latter means that similar but no identical ZnO nanostructures can be obtained from synthesis to synthesis. The best reproducible nanostructures have been observed for synthesis methods requiring several steps or more elaborated methodologies like the application of templates or vapor-phase synthesis techniques. A recent review by M. Zacharias62 describes various growth processes, with special emphasis on the vapor–liquid–solid (VLS) process, which offers the possibility for the control of the positions of the nanostructures in 3D.62 The authors describe techniques like vapor–liquid–solid (VLS), vapor–solid (VS), solution growth (SG), and describe the benefits of applying nanolithography (NL) techniques like photolithography (PhL), e-beam lithography (eBL), nanospheres lithography (NSp), masks and templates based on porous alumina (TM), nanoimprint lithography (NIL), etc.62 Many of these nanostructures are obtained on metallic substrates like Au, or on semiconductors not compatible with XSC configurations but could be adapted to the application of substrates compatible with XSC components.
Vertically-aligned ZnO nanostructures for high efficient electron transport
An efficient nanostructured electrode for XSC should present high electron transport and low recombination rate. The effective electron diffusion length depends on the application of an optimal electrode thickness, and is represented by
where Dn is the diffusion coefficient for the electron within the electrode and the τn is the survival time of the electron with respect to the regenerator (a Dye in a DSC and a polymer in a XSC).63 Analysis applying the intensity modulated photocurrent spectroscopy (IMPS) technique together with the analysis of photocurrent decay can determine the values of electron diffusion and transport time (τd). In both cases the solar cell is illuminated with a laser whose intensity is varied as a function of time and the transient response of the solar cell photoresponse is measured. The minimum angular frequency observed in the imaginary plot of modulated photocurrent vs frequency can be applied to obtain the electron transport time: τd =ω,min−1.63
For electrodes made with colloidal nanoparticles, it has been observed that charge transport and recombination accelerate when increasing light intensity and their ratio (τd/τn) remains constant. In the case of vertically aligned electrodes a similar intensity-dependent behavior was observed for recombination and the electron transport was observed to be independent of light. The measured recombination/transport times ratio was observed to be about 64, or 18 times that observed with the nanoparticle electrode, as seen in Fig. 7.63 Other interesting results have been observed when comparing the carrier density of nanostructured and dense thin film electrodes of ZnO. Some models demonstrated that ZnO nanowires present high donor density of 6.2 × 1019 cm−3, and the effect of annealing temperature has been proved to reduce this value by two orders of magnitude.117
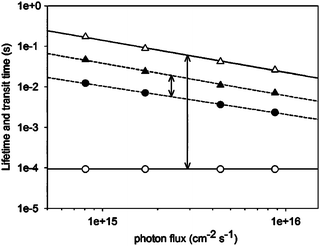 |
| Fig. 7 Electron lifetime (△) and average transit time (●) over a range of illumination intensities. ↕ highlight the difference between τn and τd for nanoparticle (▲) and nanorod (○) devices.63 | |
Thus, improving the interfacial processes where exciton generation and separation take place will translate into higher solar cell efficiency. Other reports demonstrate that electron transport in semiconductor oxides made of nanoparticles proceed by a trap-limited diffusion process due to the random pathway the electrons must follow through the thin film. The electron must pass through a series of interparticle hopping steps, estimated in 103–106 particles, in order to reach the collection electrode.64,65 Although the electron transport through a nanoparticle thin film is high, the electron must overcome several grain boundary and dead ends with a high probability for recombination before reaching the electrode current collector.65,66 Despite their slow nature, electron collection is favored over recombination in DSCs due to the slower kinetics observed for the liquid electrolyte. Galoppini et al. analysed electron transport in DSCs by always applying films of 2 µm thickness synthesized by the MOCVD technique and comparing them with a thin film made of nanoparticles.83 Results demonstrated that the electron transport of the ZnO nanoparticle electrode was similar to a thin film made of TiO2nanoparticles (transport time of ∼10 ms) but the electron transport increased about 2 orders of magnitude when a thin film of ZnO vertically-aligned nanowires was used (∼ 30 µs).66,67 The same authors reported the electron mobility for ZnO thin film, which has been measured to be about 400 cm2V−1 s−1, and electron mobility several orders of magnitude higher for ZnO nanowires (>20 cm2V−1 s−1).66
If we consider that the electron collection efficiency is a measure of the competition between electron transport and recombination rate, a well-aligned nanostructured semiconductor oxide could provide a faster and direct electrical pathway for the collection of electrons as shown in Fig. 5b. The latter has been proved by Hupp67 who compared the dynamics of charge transport and recombination of two ZnO electrodes, one made by ZnO colloidal nanoparticles and the other as vertically-aligned nanorods. Fig. 7 shows the dependence of electron recombination with light intensity for both types of electrodes.67
Photovoltaic properties of vertically-aligned ZnO nanostructures in excitonic solar cells
The properties of vertically-aligned nanostructures has been the subject of extended research work and several reviews can be found in the literature.71 Particularly TiO2, as one of the most widely used semiconductor oxides in Hybrid and Dye sensitized solar cells, has been recently reviewed.72 Moreover, reviews on other type of nanowires and nanotubes of different inorganic semiconductors like ZnO, CdS, CdSe, CdTe, CuO can also be found.73–76,78
In this section we consider XSCs where sole ZnO nanostructures are used as the ETM. Thus, XSCs applying ZnO in addition to other compounds that could enhance electron injection (like PCBM, TiO2 or similar) are not included.
Application in dye sensitized solar cells
The first application of ZnO in DSC goes back to 1969 with the work reported by Gerisher et al. applying a single crystal oxide as the electrode.76 Since then, several attempts to improve solar cell efficiency have been observed. In 1980, electrodes made of ZnO disks were applied in DSC obtaining 2.5% efficiency.77 Currently, the application of ZnO nanostructured electrodes made of colloidal nanoparticles has achieved up to 6.58% efficiency,157 Efforts to improve the DSC conversion efficiency by increasing surface area was made by the application of ZnO nanostructures like nanoflower (η = 1.9%),95nanosheets (η = 3.9%),102 hierarchically structured (3.5%),146 or its application together with other oxides as mesoporous SnO2–ZnO (6.34%),131 core–shell ZnO–TiO2 (9.8%)148 or more recently doped-ZnO nanoparticles (η = 6%).101 The highest efficiency reported up to date is 7.2% applying porous single crystal.161Table 1 summarizes photovoltaic properties observed for DSC applying ZnO vertically-aligned nanostructures (nanorods, nanowires, nanotubes) and other related structures.
The first principle to consider in relation to efficiency is the size and spacing of the nanostructures which must be in the range of the exciton diffusion length, between 5 and 20 nm. Thus the optimum nanostructure will be the one with a perfectly ordered array of crystalline ZnO nanowires oriented normal to the electrode surface. The nanowires must also be thin (up to 40 nm in diameter) and with spacing between them of about 20–40 nm. The length of the nanowires will define the amount of absorbed dye within the nanostructure and, as a consequence, the solar cell efficiency, thus a 10–20 µm nanowire length is desirable.81 Dimensions of vertically-aligned nanowires vary greatly depending on the synthesis technique used, the later influences to a great extent the photovoltaic properties of the DSC. We have observed that vertically-aligned nanostructures of ZnO applied as electron acceptors in DSC are limited to only a few synthesis methods, hydrothermal, MOCVD, CVD, atomic layer deposition or a combination of them as seen in Table 1.
From Table 1 we can also extract the different ZnO nanorods lengths applied by different laboratories. NRs length and diameter are directly related to the surface area available for Dye loading which directly affect the solar cell efficiency.90 Baxter and Aydil et al. carried out a detailed study of the effect of NRs length and diameter on photovoltaic response.65 The authors applied hydrothermal techniques using seeded substrates of ZnO nanoparticles of about 5–10 nm in diameter (the application of no-seeded substrates results in ZnO NR of larger diameter). During synthesis the nanorods were grown from ZnO seeded substrates and the solution was replaced several times to enhance nanorod growth. Each time the growth solution was changed one synthesis cycle is completed. Their study revealed a linear growth of the NRs with the number of cycles. Lengths which varied from 2, 5 or 8 µm were obtained after 2, 4 or 8 four-hour-cycles, respectively (Fig. 8).
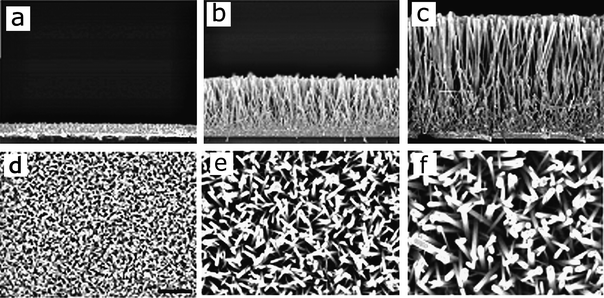 |
| Fig. 8 Cross-sectional (upper row) and top view (lower row) SEM images of ZnO nanowire arrays grown for ((a), (d)) one, ((b), (e)) four, and ((c), (f)) eight 4 h synthesis cycles. Scale bars are 2 µm for ((a)–(c)) and 1 µm for ((d)–(f)).65 | |
In the case of the diameter, the results indicate an initial linear diameter growth with number of cycles but the growth was observed to take place at a slower rate, going from 50 nm up to 150 nm (aspect ratios from 10 to 60), when going from 1 to 8 cycles. As a result of the surface area increase with NR length, the efficiency observed for DSC with 1 µm length and 50 nm diameter (1 synthesis cycle) was observed to be 0.04% which increased up to 0.18% for a NR of 8 µm in length and 155 nm in diameter, as shown in Fig. 9. The best conversion efficiency obtained by the authors was 0.3%.
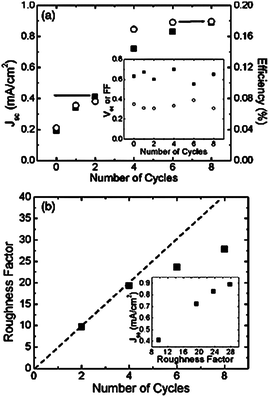 |
| Fig. 9 (a) Current density (■) and efficiency (○) as a function of number of growth cycles. Inset shows open circuit voltage (Voc) in volts (■) and fill factor (○) vsgrowth cycles. (b) Roughness factor of the nanowire arrays as a function of the number of growth cycles. The dotted line helps to show the sub-linear dependence of the roughness factor on the number of growth cycles.65 | |
Although the photovoltaic performance of DSCs depends on multiple parameters, the above example demonstrates the importance of the synthesis technique applied for the fabrication of the electron transport electrode. To our knowledge, the highest conversion efficiency obtained to date applying only vertically-aligned ZnO nanostructures has been reported by Guo et al.96 The authors applied nanorods of ZnO with diameters between 30–70 nm and lengths up to 1.9 µm. The authors carried out a detailed study of synthesis conditions for the ZnO nanorods, growth time and temperature, and its influence on DSC efficiency. Their findings revealed a direct improvement of solar cell efficiency with increasing NR growth temperature, η = 0.5% when growth temperature was 40 °C, η = 1.1% at 60 °C, η = 1.8% at 80 °C and η = 2.4% at 95 °C. The improvement in efficiency was attributed to the length of the ZnO nanorods, that increased from 240 nm up to 1.9 µm when the temperature was raised. The latter affects the total amount of dye loading on the electrode and as a consequence higher amount of photons can be converted into electrical energy. As we can observe from Table 1 the NR applied by these authors are especially thin (the smallest diameter of all), and are closely related to the electron diffusion length values (10–20 nm) required for efficient exciton dissociation.
In general, nanowires between 50 nm up to 300 nm average diameter and from 1 to 16 µm in length have been applied in DSC, as detailed in Table 1. Although DSC efficiency depends on different parameters like type of dye, type of electrolyte and especially the electrode morphology, we observed that solar cell efficiency is related to the diameter of the nanorods rather than their length. As mentioned before, the ZnO nanostructure most closely related to the optimal described previously, is probably the one that Prof. T. Yoshida has been developing for the last several years.159–161 This nanostructured thin film of ZnO is made by electrochemical deposition of Zn precursors and the application of dyes during the electrochemical synthesis.159–161 In a recent conference161 the group presented their latest results, 7.2% efficiency of a DSC based on a self-developed dye labeled D149. The ZnO nanostructure obtained is a porous single crystal (see Fig. 5d), obtained by the de-adsorption of the dye molecules from the ZnO–Dye nanomaterial after electrochemical synthesis. The de-adsorption of the dye permits the formation of nanoporosity with the exact nanosize required for dye re-loading, ensuring an ideal oxide–dye interaction.
Application in hybrid solar cells
The first reports of the application of ZnO in XSCs with relatively good efficiencies are very recent and may be attributed to Prof. J. A. Janssen. This group demonstrated in 2004 that solar cells applying blends of a conducting organic polymer and ZnO nanoparticles show efficiencies up to 1.6%.116,125 Recent reports from this group show an improvement on solar cell performance obtaining a current density, Jsc, of 6.1 mA cm−2, 0.75 V, 0.52 FF, and 2.4% efficiency,163 the highest efficiency reported to date for XSCs applying ZnO nanoparticles.
Many efforts to improve efficiency by the optimization of the nanoparticle/polymer blend or by the application of higher surface area electrodes (nanoparticles, nanorods, opals of ZnO, etc) have been observed by many groups. The first report of the application of ZnO as vertically-alignednanostructures in HSC was made in 2006.107,108,111 The ZnO nanostructure was applied in different configurations: in direct contact with a conducting organic polymer; as part of TiO2nanorods or nanowires; or, as part of a bulk-heterojunction solar cell made with a PCBM–P3HT blend; in all these systems ZnO has been observed to improve electron transport.
In HSC, the interest in the application of vertically-aligned ZnO nanostructures is based on the good performance observed when applying TiO2 vertically-aligned nanostructures in solar cells.74 Moreover, it offers the possibility of synthesizing ZnO nanorods applying a simple hydrothermal method that can be fabricated on a large scale and, almost, on any substrate.19,45,108 The photovoltaic response observed for HSC applying vertically-aligned ZnO nanostructures is listed in Table 2. We observed that the diameter of the ZnO nanorods applied by the different laboratories are between 80 and 150 nm, the most applied polymer is P3HT (one of the best and more stable of the commercially available polymers), the efficiencies reported are very similar between laboratories and, to our surprise, are not higher than 0.5%. Voc is relatively low, never higher than 0.44 V and, in general, the current density is reported to increase by four, when compared with devices in a planar configuration or applying nanoparticles.109,110 In addition, the longer the nanorod the higher the current density obtained from the solar cell.66 Olson and Ginley et al. studied HSCs applying the configuration ITO/ZnO NR/P3HT/Ag.66,110,111 The applied ZnO nanorods were synthesized with lengths between 250 and 500 nm, this increment in surface area was translated in an improved Jsc which changed from 1.29 to 2.17 mA cm−2. The low external quantum efficiency (EQE) values observed for the devices was attributed to the diameter (100 nm) and space between the NR that were not optimized to encompass the short electron diffusion length (3–5 nm) of the P3HT polymer. The reason for the low values of Voc (about 0.3 V) is not clear, the authors relate it to the presence of mid-gap states on the surface of the ZnO, or to high electron mobility within the ZnO NR which could increase recombination. Other results from the same author show the beneficial effect on Voc when treating the ZnO surface with surfactants at expense of Jsc.66 A recent report made by Plank and Schmidt-Mende et al. show the effect of ZnO layer thickness on the Voc and EQE values.109
The authors show that a thinner layer of ZnO presents an improvement in Voc from 0.28 V up to 0.41 V and EQE from 2% to 7.2% for a 650 nm and 130 nm layer thickness, respectively. In general, all the published works inform about the importance of the type of synthesis on photovoltaic performance. The possibility to control the diameter, spacing and length on the ZnO vertically-aligned nanostructure is a critical issue for all authors. It is also important to carry out studies on the control of polymer reorganization and morphology within the ZnO interface, which can affect the exciton dissociation and the unidirectional flow of electrons through components of the solar cell.116
All solid-state excitonic solar cells (ss-XSCs) applying ZnO: In between HSC and DSC.
Recent efforts to eliminate practical problems related to the liquid electrolyte in DSCs such as leakages, corrosion of electrodes, solvent evaporation, among others,129,130 have resulted in the development of XSCs in solid or quasi-solid state configurations. The ss-DSC concept was first reported around 1995136,145,147 and several compounds have been applied that include the application of p-type inorganic semiconductors,130polymer or gel electrolytes,129,132–135 ionic liquids,137–142 ionic liquid crystals,129,142,143 conducting organic polymers144,151–154 or redox molecules covalently linked to the dye and the TiO2 forming a triad,123,144,147 and several examples can be found in the literature. The most relevant are DSC applying TiO2 as ETM and spiro-OMeTAD or conducting organic polymers as solid-state HTM that have shown promising conversion efficiencies of 4% and 2.8%, respectively.151–154 The application of ZnO nanostructures in all solid-state XSCs have emerged from variations of the HSC or the DSC configurations. In a HSC there is a direct contact between the oxide and the polymer, thus dye has been introduced as the separator of HTM and ETM to improve electron injection and reduce recombination. In DSC configuration is HTM (usually a liquid electrolyte), the one that is replaced by solid hole conductors. Only a few examples of ss-XSC applying ZnO were found in the literature and are listed in Table 3. In these ss-XSCs the highest solar cell efficiencies are not higher than 0.55% but the research on these solar cells is in the early stages and more research results are expected in the following years.
Table 3 solid-state Exitonic Solar Cells (ss-XSC) applying ZnO nanostructures as the ETM and dyes as spatial separator between the HTM and ETM. TCO: Transparent conducting oxide like indium tin oxide, ITO, or fluor tin oxide, FTO. PDI: N,N′-didodecyl-3,4,9,10-perylene tetracarboxylic diimide. SAF: Safarine-O dye
|
J
sc
|
V
oc
|
η
|
FF
|
Ref. |
(mA/cm2) |
(V) |
(%) |
(%) |
From HSC |
Al/ZnO/PDIdye/(P3HT + ZnOnp)blend/PEDOT/ITO |
−9.55 |
0.35 |
— |
— |
120
|
|
|
|
|
|
|
|
ss-XSC |
Al/PPTH : SAFdye : ZnO/ITO |
1.45 |
0.62 |
0.55 |
0.61 |
122
|
|
|
|
|
|
|
|
From DSC |
ITO/ZnOdense/Z907dye/P3HT/PEDOT/Au |
−3.2 |
0.28 |
0.2 |
— |
108
|
In these few cases, all the authors agree on the beneficial effect observed on Jsc and whole solar cell performance when the dye is introduced between the HTM and ETM in a HSC. Nevertheless, in a DSC the effect is the contrary, replacement of the fast injection liquid electrolyte by a solid HTM results in a decrease in solar cell performance.
Stability of excitonic solar cells applying ZnO
Long-term stability tests performed on XSCs have reached several thousand hours under continuous illumination: from 1000 h up to 20
000 h for DSCs165 and from 4000 h166 to 10
000 h for OSCs.167,168 Recent publications on the stability test carried out to XSCs applying ZnO can be found, especially for HSC and ss-XSCs.
HSC stability.
In HSCs, an oxygen release and exchange mechanism has been recently reported for semiconductor oxides working in direct contact with light-harvesting and hole conducting polymers.22–24,124–125,127 This mechanism affects the performance of the solar cell under different atmospheres due to the semiconductor oxide requirement (“breathing”) of oxygen.22–24 The possibility to encapsulate these HSC or, to work under inert atmospheres is not an option due to the detrimental effect observed on photovoltaic properties in these environments. The latter suggests that XSCs applying semiconductor oxides cannot be applied under inert atmosphere environments, for example, in space-related applications.
The observed mechanism is linked to the semiconductor itself and has been observed in systems like ZnO electrodes applied in HSC made of dense thin films,22–25,128 hybrid nanocomposites made with nanoparticles124 and more recently on vertically-aligned ZnO nanostructured electrodes.66 This behavior is not exclusive to ZnO, it has also been observed in systems applying other semiconductor oxides (TiO2, Nb2O5, CeO2, etc22–24) in different configurations like TiO2/polymer nanocomposites,124 planar oxide/polymer HSC,22–24 and also in nanorods/polymer devices.124 Some initial reports applying ZnO nanoparticles indicate the stabilization of the oxide/polymer blend when increasing ZnO nanoparticle content. Nevertheless, the stabilization applies within ZnO/polymer nanoparticle blends and does not avoid the photo-oxidation (photobleaching) of the polymer under long-term irradiation conditions. The latter mechanism can not be avoided by the application of UV filters or inert atmospheres.24 Yet, much effort has been made to understand degradation mechanisms in XSCs, especially in OSCs22–25,119,168–170 and, very recently, efforts show the initial results of the effect of semiconductor oxides on organic polymers in HSCs.119 Krebs et al. has recently reported the long-term stability of a HSC made of ZnO nanoparticles and the polymer poly-(3-carboxydithiophene) (P3CT). The author modified the planar HSC configuration of ITO/ZnO/MEH–PPV/Ag22–24 applying ZnO as dense thin films, to ITO/ZnO/(P3CT–ZnO)blend/PEDOT:PSS/Ag using ZnO nanoparticles.119 While the lifetime of the first configuration was limited to only a few minutes (hours), the new configuration shows a lifetime of up to 500 h, in both cases without the use of a UV filter. There are many possible explanations for this lifetime improvement, among them are the higher stability of the polymer used and the electron withdrawing carboxylic acid groups which is more stable towards oxygen.119 Nevertheless, the time required for the solar cell to exchange oxygen and degrade the polymer could also be related to the total active surface area of the oxide. If the latter is true, in a HSC made of dense thin films of ZnO (about 30 nm thickness) the exchange of oxygen and the stabilization in the dark would take place in only a couple of hours,22–24 while in a nanostructured ZnO thin film made of nanoparticles the stabilization period could take several days, even months.110
ss-XSC stability.
Another possible alternative to overcome the degradation problem observed in HSCs could be the physical separation of the electron- and hole-transporting components as already suggested in published reports.123,124 This separation could avoid polymer degradation and improve lifetime in HSC applying semiconductor oxides as is observed in long-lasting DSCs. But, it could imply the possibility to enhance charge separation and avoid or retard recombination in this and all other types of bulk-heterojunction solar cells, as reported earlier.123,124 The latter has been proven by Ravirajan et al.,108 who fabricated a HSC applying ZnO in three different configurations: flat layer structure, vertically aligned nanorods and as nanoparticles. The authors applied the polymer in intimate contact with ZnO, but also added an amphiphilic molecular interface layer (a dye) in between the ZnO and the polymer. A transient absorption spectroscopy technique was used to obtain the photoinduced electron-transfer yield and the charge recombination kinetics. Comparison between the devices, ZnO coated and uncoated with dye showed that the dye-treated ZnO devices presented (a) longer lifetime of the hole polarons, (b) improvement of 50% in the charge transfer yield and (c) a slower half-life by a factor of 4–5. The authors observed an improvement in charge separation yield attributed to the “cascade” type of interface applied (ZnO/Dye/polymer) which blocked hole transfer. Another factor is the orientation of the dye, which is believed to attach its polar side group to the oxide while maintaining its nonpolar side towards the polymer, improving wettability. A direct charge transfer between ZnO and P3HT would promote recombination but it is effectively retarded by the application of a dye as a spatial separation between the hole and electron transfer materials. The latter work by Ravirajan et al.108 demonstrated the beneficial effect of separating the hole and the electron transport materials, and a few similar XSCs have been published since.149 The application of a dye (or any other sensitizer) as a spacer between the hole and electron transport material would resemble a DSC or more exactly, a solid-state DSC (ss-DSC).
Wang et al.120 carried out stability analyses of a solid-state XSC of the type Al/P3HT:ZnO:PDI/PEDOT/ITO where ZnO was used in the form of nanoparticles and the dye PDI was used to improve photovoltaic performance. As reported previously,108 the light absorption and exciton separation was greatly improved by the addition of the dye between the HTM and ETM. Nevertheless, stability analyses with the application of UV filter did not show any improvement in solar decay behavior.
Initial efforts to understand the effect of the long term stability of ss-DSCs, applying a Dye/TiO2electrode as the light-harvesting and electron transfer materials, respectively, and spiro-OMeTAD as the solid hole conductor, has been very recently presented by Fabregat-Santiago and Bisquert et al.164 The reported results show impedance models able to describe the main electrical parameters that determine the behavior of these ss-DSC, but more important is the report of the effect of different atmospheres (argon and air) on the photovoltaic and electrical properties of the ss-DSC. Initial results show better performance of the ss-DSC under oxygen-containing atmospheres, as reported previously for HSC.22–25 The latter implies that the presence of a dye is not enough for solar cell stability under different atmospheres as suggested earlier.15 The effect is currently under investigation by many research groups.
Future trends
Outstanding progress has been observed in recent years on the synthesis of vertically-aligned nanostructures of ZnO, nanorods, nanotubes or similar. The improvement in electron transport applying these nanostructures is a reality and current densities have been observed to improve by four when changing from nanoparticles to vertical nanostructures. The best solar cell performance applying nanostructures of ZnO in DSC now reaches 7.2% efficiency when applying vertical nanostructures made of porous single crystal ZnO, 6.58% when nanoparticles are used and 2.5% for vertically-aligned nanorods. In the case of HSC, the highest values are observed when ZnO nanoparticles are used, only 0.5% efficiency, for vertically-aligned nanostructures the efficiency is no higher than 0.2%. In the case of ss-XSC the observed efficiencies are even lower, as shown in Table 3. For comparison purposes Table 4 summarizes the best solar cell efficiencies observed to date for XSCs applying ZnO nanostructures. These low efficiencies seem to be related to many factors but especially to problems related to surface area, polymer infiltration, wettability and slow kinetics, in the case of solid hole conductors. In order to increase solar cell efficiency the surface area of the nanostructured ZnO electrode must be enhanced. In an effort to increase surface area and, at the same time, the interface between the semiconductor oxide and the corresponding organic semiconductor (Dye or conducting polymer), vertical nanostructures, such as branched nanorods or nanosheets, seem to be promising candidates for high efficiency XSCs. Particularly ZnO nanostructures, such as the porous single crystals reported by Yoshida161 (see Table 4), which present most of the characteristics needed for high electron transport and high solar cell efficiency: high density nanostructure, high surface area, low voids concentration between the nanostructure, and single-crystalline structure for electron transport without grain boundaries.
Table 4 Highest solar cell efficiencies reported for XSCs applying ZnO nanostructures
Working mechanisms
More recent developments relate to the application of doped ZnO materials to enhance light-harvesting properties. For example, a detailed study on the charge generation mechanism has been reported when applying Zn1−xMgxO (x = 0–0.4). Findings of new charge generation mechanisms in HSCs were reported and revealed to be completely different from the exciton dissociation mechanism observed to date of exciton dissociation at the interface in XSCs.150 In DSC, on the contrary, ZnO has been doped with Ga obtaining 6% efficiency, in this case the device was made by applying ionic liquid electrolytes.101
All-solid-state devices
Finally, a promising research trend is the possibility of developing XSCs as all-solid-state devices with high efficiencies, avoiding the application of problematic liquid electrolytes, and applying solution processing techniques for fabrication. We have identified two main research trends: the first is related to the application of solid hole conductors to replace the liquid electrolyte in DSC; the second is the application of a light-harvesting compound (e.g. a dye) between ZnO and the conducting polymer. Although efficiencies as high as 4% have been reported for ss-DSC applying solid hole conductors, such as spiro-OMeTAD, or almost 3% when applying conducting polymers,151–154 the electrode applied was made of TiO2 colloidal nanoparticles and not ZnO. The application of vertically-aligned nanostructures of ZnO in all-solid-state DSC is in its very early stages, and could possibly be attributed to J. Nelson.149 Although encouraging results have been obtained with these systems and research efforts seem to be directed towards this type of solar cell, it is necessary to understand their degradation mechanisms, or to find new methods for efficiency improvement.
Reproducibility and scalability
ZnO
nanostructures can be obtained by relatively easy hydrothermal techniques with the possibility of large scale production, but reproducibility of the nanostructure is still an issue. Techniques based on templates or nanolithography-based synthesis offer the possibility of reproducibility and the control of nanostructure dimensions in 3D (space between nanostructure, height, and thickness or diameter). A general trend seems to be towards the application of nanofabrication synthesis methods but the selected technique must be simple enough to avoid or reduce multi-step processes or the need for special equipment for the synthesis of ZnO nanostructures.
The development of high efficiency and long lasting XSCs applying nanostructured ZnO may depend upon an understanding of the basic working mechanism behind nanostructured ZnO and more importantly, its interaction with light-harvesting organic semiconductors, dyes or polymers.
Conclusions
This work provides a brief overview of the most recent research developments in the application of ZnO as a nanostructured material in excitonic solar cells. Vertically-aligned nanostructures have been exhaustively applied as electron transport material in DSC and HSC. Its application as vertical nanostructures goes beyond nanorods, nanotubes or nanowires and gets immersed into the application of higher surface area nanostructures, such as branched nanorods, nanosheets, nanowiskers or porous single crystals, among many others. The latter serves two purposes, it introduces a high surface area for higher interface between the light-harvesting material (dye or polymer) and increases the probability of photon absorption. Although many different synthesis techniques can be applied for the synthesis of ZnO nanostructures, only a few are promising candidates for low cost, solution processing fabrication and scalability, particularly the wet-chemical hydrothermal method. Nevertheless, reproducibility of the alignment and dimensions of the nanostructures has not been fully accomplished. A synthesis technique that is able to control the synthesis of these vertically-aligned nanostructures at the 3D level is required. The synthesis methodology most closely related to these properties may come from the application of nanofabrication techniques. Nevertheless, the aforementioned synthesis method must compete with the low cost and versatility of currently applied synthesis techniques.
Abbreviations
Acknowledgements
To the Canon Foundation in Europe (CFE) for the research fellowship awarded in 2006 to M. L-C to visit Japan. To the projects OTT2007-0423, OTT2007-0422 and OTT2007-1014 from the Spanish Ministry of Science and Innovation (MICINN) and CDTI. To the Consolider NANOSELECT project CSD2007-00041.
References
- C. J. Brabec, J. A. Hauch, P. Schilinsky and Ch. Waldauf, Mater. Res. Bull., 2005, 30, 50.
- B. A. Gregg, Mater. Res. Bull., 2005, 30, 20 CAS.
- M. Gratzel, Mater. Res. Bull., 2005, 30, 3.
- Y. Chiba, A. Islam, Y. Watanabe, R. Komiya, N. Koide and L. Han, Jpn. J. Appl. Phys., 2006, 45(25), L638 CrossRef CAS.
- J. Peet, J. Y. Kim, N. E. Coates, W. L. Ma, D. Moses, A. J. Heeger and G. C. Bazan, Nat. Mater., 2007, 6, 497 CrossRef CAS.
- J. Bisquert, J. Garcia-Canadas and I. Mora-Sero, Proc. SPIE-Int. Soc. Opt. Eng., 2004, 5215, 49 CAS.
- G. G. Wallace, C. O. Too, D. L. Officer and P. C. Dastoor, Mater. Res. Bull., 2005, 30, 46 CAS.
- K. M. Coakley, Y. Liu, C. Goh and M. D. McGehee, Mater. Res. Bull., 2005, 30, 37 CAS.
- J. J. M. Halls, C. A. Walsh, N. C. Greeenham, E. Marseglia, F. H. Friend, S. C. Moratti and A. B. Holmes, Nature, 1995, 376(6540), 498 CrossRef CAS.
- G. Yu, J. Gao, J. C. Hummelen, F. Wudl and A. J. Heeger, Science, 1995, 270, 1789 CrossRef CAS.
- R. A. J. Janssen, J. C. Hummelen and N. S. Sariciftci, Mater. Res. Bull., 2005, 30, 33 CAS.
- H. Spanggaard and F. C. Krebs, Sol. Energy Mater. Sol. Cells, 2004, 83, 125 CrossRef CAS.
- H. J. Snaith, S. M. Zakeeruddin, L. Schmidt-Mende, C. Klein and M. Gratzel, Angew. Chem., Int. Ed., 2005, 44, 6413 CrossRef.
- J. E. Moser, Nat. Mater., 2005, 4, 723 CrossRef CAS.
-
M. Lira-Cantu, P. Gomez-Romero in Hybrid Nanocomposites for Nanotechnology: Electronic, Optical, Magnetic and Bio/Medical Applications, ed. L. Merhari, 2008, Springer Verlag. ISBN 978-0-387-72398-3 Search PubMed.
- A. C. Arango, L. R. Johnson, V. N. Bliznyuk, Z. Schlesinger, S. A. Carter and H. H. Horhold, Adv. Mater., 2000, 12, 1689 CrossRef CAS.
- A. J. Breeze, Z. Schlesinger, S. A. Carter and P. J. Brock, Phys. Rev. B, 2001, 64, 125205 CrossRef.
- J. E. Kroeze, T. J. Savenije, M. J. W. Vermeulen and J. M. Warman, J. Phys. Chem. B, 2003, 107(31), 7696 CrossRef CAS.
- C. Y. Kwong, W. C. H. Choy, A. B. Djurisic, P. C. Chui, K. W. Cheng and W. K. Chan, Nanotechnology, 2004, 15, 1156 CrossRef CAS.
- L. H. Slooff, J. M. Kroon, J. Loos, M. M. Koetse and J. Sweelssen, Adv. Funct. Mater., 2005, 15(4), 689 CrossRef CAS.
- P. Ravirajan, S. A. Haque, J. R. Durrant, D. D. C. Bradley and J. Nelson, Adv. Funct. Mater., 2005, 15(4), 609 CrossRef CAS.
- M. Lira-Cantu, K. Norrman, J. W. Andreasen and F. C. Krebs, Chem. Mater., 2006, 18, 5684 CrossRef CAS.
- M. Lira-Cantu and F. C. Krebs, Sol. Energy Mater. Sol. Cells, 2006, 90, 2076 CrossRef CAS.
- M. Lira-Cantu, K. Norrman, J. W. Andreasen, N. Casan-Pastor and F. C. Krebs, J. Electrochem. Soc., 2007, 154(6), B508 CrossRef CAS.
-
M. Lira-Cantu, F. C. Krebs in Recent Research Developments in Applied Physics ed. S. G. Pandalai. Transworld Res. Network, Berlin, 2005, 8. ISBN 81-7895-187-8 Search PubMed.
- W. J. E. Beek, M. M. Wienk and R. A. J. Janssen, Adv. Mater., 2004, 16, 1009 CrossRef CAS.
- W. J. E. Beek, M. M. Wienk and R. A. J. Janssen, Adv. Funct. Mater., 2006, 16, 112.
- A. M. Peiro, P. Ravirajan, K. Govender, D. S. Boyle, P. O'Brien, D. D. C. Bradley, J. Nelson and J. R. Durrant, J. Mater. Chem., 2006, 16(21), 2088 RSC.
- B. R. Saunders and M. L. Turner, Adv. Colloid Interface Sci., 2008, 138, 1 CrossRef CAS.
- J. E. Kroeze and T. J. Savenije, Thin Solid Films, 2004, 451–45, 54 CrossRef.
- W. U. Huynh, J. J. Dittmer and A. P. Alivisatos, Science, 2002, 295(5564), 2425 CrossRef CAS.
- E. Arici, N. S. Sariciftci and D. Meissner, Adv. Funct. Mater., 2003, 13(2), 165 CrossRef CAS.
- S. Bereznev, I. Konovalov, A. Opik and J. Kois, Synth. Met., 2005, 152(1–3), 81 CrossRef CAS.
- E. Arici, H. Hoppe, F. Schaffler, D. Meissner, M. A. Malik and N. S. Sariciftci, Appl. Phys. A: Mater. Sci. Process., 2004, 79(1), 59 CrossRef CAS.
- K. P. Jayadevan and T. Y. Tseng, J. Nanosci. Nanotechnol., 2005, 5(11), 1768 CrossRef CAS.
- A. A. R. Watt, P. Meredith, J. D. Riches, S. Atkinson and H. Rubinsztein-Dunlop, Curr. Appl. Phys., 2004, 4(2–4), 320 CrossRef.
- S. A. McDonald, G. Konstantatos, S. G. Zhang, P. W. Cyr, E. J. D. Klem, L. Levina and E. H. Sargent, Nat. Mater., 2005, 4(2), 138 CrossRef CAS.
- S. Zhang, P. W. Cyr, S. A. McDonald, G. Konstantatos and E. H. Sargent, Appl. Phys. Lett., 2005, 87(23), 233101 CrossRef.
- A. A. R. Watt, D. Blake, J. H. Warner, E. A. Thomsen, E. L. Tavenner, H. Rubinsztein-Dunlop and P. Meredith, J. Phys. D: Appl. Phys., 2005, 38(12), 2006 CrossRef CAS.
- L. L. Gao, B. Tong, G. J. Yao, Y. P. Dong, M. F. Zhang, J. Lam, W. Yip and B. Z. Tang, Acta Polym. Sin., 2005, 3, 313 Search PubMed.
- J. Ackermann, C. Videlot, A. El Kassimi, R. Guglielmetti and F. Fages, Adv. Funct. Mater., 2005, 15(5), 810 CrossRef CAS.
- J. Ackermann, C. Videlot and A. El Kassimi, Thin Solid Films, 2002, 403–404, 157 CrossRef CAS.
- D. H. Cui, J. Xu, T. Zhu, G. Paradee, S. Ashok and M. Gerhold, Appl. Phys. Lett., 2006, 88(18), 183111 CrossRef.
- S. Günes, H. Neugebauer, N. S. Sariciftci, H. Roither, M. Kovalenko, G. Pillwein and W. Heiss, Adv. Funct. Mater., 2006, 16(8), 1095 CrossRef.
- L. E. Greene, M. Law, J. Goldberger, F. Kim, J. C. Johnson, Y. Zhang, R. J. Saykally and P. Yang, Angew. Chem., Int. Ed. Engl., 2003, 42(26), 3031 CrossRef CAS.
- D. Milliron, I. Gur and A. P. Alivisatos, Mater. Res. Soc. Bull., 2005, 30, 41 Search PubMed.
- X. Wang, J. Song and Z. L. Wang, J. Mater. Chem., 2007, 17, 711 RSC.
- D. J. Milliron, S. M. Hughes, Y. Cui, L. Manna, J. B. Li, L. W. Wang and A. P. Alivisatos, Nature, 2004, 430(6996), 190 CrossRef CAS.
- Z. L. Wang, J. Phys.: Condens. Matter, 2004, 16, R829 CrossRef CAS.
- Z. L. Wang, Mater. Today, 2004, 26 CrossRef.
- M. Quintana, T. Edvinsson, A. Hagfeld and G. Boschloo, J. Phys. Chem. C, 2007, 111, 1035 CrossRef CAS.
- K. Keis, C. Bauer, G. Boschloo, A. Hagfeldt, K. Westermark, H. Rensmo and H. Siegbahn, J. Photochem. Photobiol., A, 2002, 148, 57 CrossRef CAS.
- K. Keis, E. Magnusson, H. Lindström, S.-E. Lindquist and A. Hagfeldt, Sol. Energy Mater. Sol. Cells, 2002, 73, 51 CrossRef.
- K. Hara, T. Horiguchi, T. Kinoshita, K. Sayama, H. Sugihara and H. Arakawa, Sol. Energy Mater. Sol. Cells, 2000, 64, 115 CrossRef CAS.
- X. Feng, L. Feng, M. Jin, J. Zhai, L. Jiang and D. Zhu, J. Am. Chem. Soc., 2004, 126, 62 CrossRef CAS.
- V. V. Kislyuk and O. P. Dimitriev, J. Nanosci. Nanotechnol., 2007, 8, 1.
- Y. W. Heo, D. P. Norton, L. C. Tien, Y. Kwon, B. S. Kang, F. Ren, S. J. Pearton and J. R. La Roche, Mater. Sci. Eng., R, 2004, 47, 1 CrossRef.
- I. ÜÖzgür, YaAlivov, C. Liu, A. Teke, M. A. Reshchikov, S. Doğan, V. Avrutin, S.-J. Cho and H. Morko., J. Appl. Phys., 2005, 98 Search PubMed 041301.
- M. Law, L. E. Greene, J. C. Johnson, R. Saykally and P. Yang, Nat. Mater., 2005, 4, 455 CrossRef CAS , permission to publish granted.
- J.-J. Wu, G.-R. Chen, H.-H. Yang, C.-H. Ku and J.-Y. Lai, Appl. Phys. Lett., 2007, 90, 213109 CrossRef.
-
I. Gonzalez-Valls, M. Lira-Cantu, unpublished results.
- H. J. Fan, P. Werner and M. Zacharias, Small, 2006, 2(6), 700 CrossRef CAS.
- A. B. F. Martinson, J. E. McGarrah, M. O. K. Parpia and J. T. Up, Phys. Chem. Chem. Phys., 2006, 8, 4655 RSC , permission to publish granted.
- J. B. Baxter and E. S. Aydil, Appl. Phys. Lett., 2005, 86, 053114 CrossRef.
- J. B. Baxter, A. M. Walker, K. van Ommering and E. S. Aydil, Nanotechnology, 2006, 17, S304 CrossRef CAS , permission to publish granted.
- D. C. Olson, Y.-J. Lee, M. S. White, N. Kopidakis, S. E. Shaheen, D. S. Ginley, J. A. Voight and J. W. P. Hsu, J. Phys. Chem. C, 2007, 111, 16640 CrossRef CAS.
- A. B. F. Martinson, J. E. McGarrah, M. O. K. Parpia and J. T. Hupp, Phys. Chem. Chem. Phys., 2006, 8, 4655 RSC.
- C. Y. Jiang, X. W. Sun, G. Q. Lo and D. L. Kwong, Appl. Phys. Lett., 2007, 90, 263501 CrossRef.
- H. Tang, L. Zhu, Z. Ye, H. He, Y. Zhang, M. Zhi, F. Yang, Z. Yang and B. Zhao, Mater. Lett., 2007, 61(4–5), 1170 CrossRef CAS.
- L. E. Greene, M. Law, D. H. Tan, M. Montano, J. Goldbergger, G. Somorjai and P. Yang, Nano Lett., 2005, 5(7), 1231 CrossRef CAS.
- C. Y. Yaing, X. W. Sun, K. W. Tan, G. Q. Lo, A. K. K. Kyat and D. L. Kwong, Appl. Phys. Lett., 2008, 92, 143101 CrossRef.
- Y. F. Hsu, Y. Y. Xi, C. T. Yip, A. B. Djurisic and W. C. Chan, J. Appl. Phys., 2008, 103, 083114 CrossRef.
- M. Law, J. Goldberger and P. Yang, Annu. Rev. Mater. Res., 2004, 34, 83 CrossRef CAS.
- G. K. Mor, O. K. Varghese, M. Palouse, K. Shankar and C. A. Grimes, Sol. Energy Mater. Sol. Cells, 2006, 90, 2011 CrossRef CAS.
- P. J. Pauzauskie and P. Yang, Mater. Today, 2006, 9(10), 36 CrossRef CAS.
- G.-C. Yi, Ch and W. I. WangPark, Semicond. Sci. Technol., 2005, 20, S22 CrossRef CAS.
- H. Gerischer and H. Tributsch, Ber. Bunsen-Ges. Phys. Chem., 1969, 73, 850.
- Z. Zhang, S. J. Wang and T. Yu, Wu. J. Solid State Chem., 2005, 178, 1864 Search PubMed.
- K. S. Kim, Y.-S. Kang, J.-H. Lee, Y.-J. Shin, N.-G. Park, K. S. Ryu and S. H. Chang, Bull. Korean Chem. Soc., 2006, 27(2), 295 CAS.
- T. P. Chou, Q. Zhang and G. Cao, J. Phys. Chem. C, 2007, 111, 18804 CrossRef CAS.
- S. Sakthivel, B. Neppolian, M. V. Shankar, B. Arabindoo, M. Palanichamy and V. Murugesan, Sol. Enery Mater. Sol. Cells, 2003, 77, 65 Search PubMed.
- E. Galoppini, J. Rochford, H. Chen, G. Saraf, Y. Lu, A. Hagfeldt and G. Boschloo, J. Phys. Chem. B, 2006, 110(33), 16159 CrossRef CAS.
- Y. F. Hsu, Y. Y. Xi, A. B. Djurisic and W. K. Chan, Appl. Phys. Lett., 2008, 92, 133507 CrossRef.
- H. Gao, G. Fang, M. Wang, N. Liu, L. Yuan, Ch. Li, L. Ai, J. Zhang, C. Zhou, S. Wu and X. Zhao, Mater. Res. Bull., 2008, 43(12), 3345 CrossRef CAS.
- C. Y. Jiang, X. W. Sun, K. W. Tan, G. Q. Lo, A. K. K. Kyaw and D. L. Kwong, Appl. Phys. Lett., 2008, 92, 143101 CrossRef.
- A. Du Pasquier, H. Chen and Y. Lu, Appl. Phys. Lett., 2006, 89, 253513 CrossRef.
- A.-J. Cheng, Y. Tzeng, Y. Zhou, M. Park, T. Wu, C. Shannon, D. Wang and W. Lee, Appl. Phys. Lett., 2008, 92, 092113 CrossRef.
- Y. Gao and M. Nagai, Langmuir, 2006, 22, 3936 CrossRef CAS.
- B. Pradhan, S. K. Batabyal and A. J. Pal, Sol. Energy Mater. Sol. Cells, 2007, 91, 769 CrossRef CAS.
- J.-J. Wu, G.-R. Chen, H.-H. Yang, Ch.-H. Ku and J.-Y. Lai, Appl. Phys. Lett., 2007, 90, 213109 CrossRef , permission to publish granted.
- A. B. F. Martinson, J. E. McGarrah, M. O. K. Parpia and J. T. Hupp, Phys. Chem. Chem. Phys., 2006, 8, 4655 RSC.
- A. B. F. Martinson, J. W. Elam, J. T. Hupp and M. J. Pellin, Nano Lett., 2007, 7(8), 2183 CrossRef CAS.
-
P. Charoensirithavorn, S. Yoshikawa. Proc. 2nd Int. Conf. Sustainable Energy and Environment (SEE 2006), Thailand, 2006 Search PubMed.
- Y. Gao, M. Nagai, T.-Ch. Chang and J.-J. Shyue, Cryst. Growth Des., 2007, 7(12), 2467 CrossRef CAS.
- C. Y. Jiang, X. W. Sun, G. Q. Lo and D. L. Kwong, Appl. Phys. Lett., 2007, 90, 263501 CrossRef.
- M. Guo, P. Diao, X. Wang and S. Cai, J. Solid State Chem., 2005, 178, 3210 CrossRef CAS.
- K. Kakiuchi and S. M.SaitoFujihara, Thin Solid Films, 2008, 516, 2026 CrossRef CAS.
- K. Kakiuchi, E. Hosono and S. Fujihara, J. Photochem. Photobiol., A, 2006, 179, 81 CrossRef CAS.
- C.-H. Ku, H.-H. Yang, G.-R. Chen and J.-J. Wu, Cryst. Growth Des., 2008, 8(1), 283 CrossRef CAS.
- C.-H. Ku and J.-J. Wu, Nanotechnology, 2007, 18, 505706 CrossRef.
- A. de Souza Gonçalves, M. R. Davolos, N. Masaki, S. Yanagida, A. Morandeira, J. R. Durrant, J. N. Freitas and A. F. Nogueira, Dalton Trans., 2008, 11, 1487 RSC.
- E. Hosono, S. Fujihara, I. Honma and H. Zhou, Adv. Mater., 2005, 17, 2091 CrossRef CAS.
- J. B. Baxter and E. S. Aydil, Sol. Energy Mater. Sol. Cells, 2006, 90, 607 CrossRef CAS.
- R. Zhang, S. Kumar, S. Zou and L. L. Kerr, Cryst. Growth Des., 2008, 8(2), 381 CrossRef CAS.
- S. Pang, T. Xie, Y. Zhang, X. Wei, M. Yang, D. Wang and Z. Du, J. Phys. Chem. C, 2007, 111, 18417 CrossRef CAS.
- Y.-Y. Lin, C.-W. Chen, T.-H. Chu, W.-F. Su, C.-C. Lin, C.-H. Ku, J.-J. Wu and C.-H. Chen, J. Mater. Chem., 2007, 17, 4571 RSC.
- A. M. Peiro, P. Ravirajan, K. Govender, D. S. Boyle, P. O'Brien, D. D. C. Bradley, J. Nelson and J. R. Durrant, J. Mater. Chem., 2006, 16, 2088 RSC.
- P. Ravirajan, A. M. Peiro, M. K. Nazeeruddin, M. Graetzel, D. D. C. Bradley, J. R. Durrant and J. Nelson, J. Phys. Chem. B, 2006, 110, 7635 CrossRef CAS.
- N. O. V. Plank, M. E. Welland, J. L. MacManus-Driscoll and L. Schmidt-Mende, Thin Solid Films, 2008, 516(20), 7218–7222 CrossRef CAS.
- D. C. Olson, S. E. Shaheen, R. T. Collins and D. S. Ginley, J. Phys. Chem. C, 2007, 111, 16670 CrossRef CAS.
- D. C. Olson, J. Piris, R. T. Collins, S. E. Shaheen and D. S. Ginley, Thin Solid Films, 2006, 496, 26 CrossRef CAS.
- K. Takanezawa, K. Hirota, Q.-S. Wei, K. Tajima and K. Hashimoto, J. Phys. Chem. C, 2007, 111, 7218 CrossRef CAS.
- M. Wang and X. Wang, Sol. Energy Mater. Sol. Cells, 2007, 91, 1782 CrossRef CAS.
- D. J. D. Moet, L. J. A. Koster, B. De Boer and P. W. M. Blom, Chem. Mater., 2007, 19, 5856 CrossRef CAS.
- J.-P. Liu, S.-C. Qu, Y. Xu, Y.-H. Chen, X.-B. Zeng, Z.-J. Wang, H.-Y. Zhou and Z.-G. Wang, Chin. Phys. Lett., 2007, 24(5), 1350 CrossRef CAS.
- W. J. E. Beek, M. M. Wienk and R. A. J. Janssen, J. Mater. Chem., 2005, 15, 2985 RSC.
- I. Mora-Seró, F. Fabregat-Santiago, B. Denier, J. Bisquert, R. Tena-Zaera, J. Elias and C. Lévy-Clément, Appl. Phys. Lett., 2006, 89(20), 203117 CrossRef.
- M. Wang and X. Wang, Sol. Energy Mater. Sol. Cells, 2008, 92, 375.
- F. C. Krebs, Sol. Energy Mater. Sol. Cells, 2008, 92, 715 CrossRef CAS.
- M. Wang and X. Wang, Sol. Energy Mater. Sol. Cells, 2008, 92, 766 CrossRef CAS.
- G. D. Sharma, P. Suresh, S. Balaraju, S. K. Sharma and M. S. Roy, Synth. Met., 2008, 158(10), 400–410 CrossRef CAS.
- P. Suresh, P. Balaraju, S. K. Sharma, M. S. Roy and G. D. Sharma, Sol. Energy Mater. Sol. Cells, 2008, 92(8), 900–908 CrossRef CAS.
- J.-E. Moser, Nat. Mater., 2005, 4, 723 CrossRef CAS.
- L. Xiao-e, A. N. M. Green, S. A. Haque, A. Mills and J. R. Durtant, J. Photochem. Photobiol., A, 2004, 162(2–3), 253–259 CrossRef.
- W. J. E. Beek, M. M. Wienk and R. A. J. Janssen, Adv. Mater., 2004, 16(12), 1009 CrossRef CAS.
- J. M. Kroon, N. J. Bakker, H. J. P. Smit, P. Liska, K. R. Thampi, P. Wang, S. M. Zakeeruddin, M. Grätzel, A. Hinsch, S. Hore, U. Würfel, R. Sastrawan, J. R. Durrant, E. Palomares, H. Pettersson, T. Gruszecki, J. Walter, K. Skupien and G. E. Tulloch, Prog. Photovoltaics, 2006, 15(1), 1.
- J. E. Kroeze and T. J. Savenije, Thin Solid Films, 2004, 451–45, 54 CrossRef.
-
J. A. Ayllon and M. Lira-Cantu, Special Issue in Organic ElectronicsAppl. Phys. A: Mater. Sci. Proc., accepted Search PubMed.
- J. R. Durrant and S. A. Haque, Nat. Mater., 2003, 2, 362 CrossRef CAS.
- S. Yanagida, C. R. Chim., 2006, 9, 597 CrossRef CAS.
- S. Ito, Y. Makari, T. Kitamura, Y. Wada and S. Yanagida, J. Mater. Chem., 2004, 14, 385 RSC.
- M. Gratzel, J. Photochem. Photobiol., A, 2004, 164(1–3), 3 CrossRef CAS.
- L. Guo, S. Y. Dai, K. J. Wang, X. Q. Fang, C. W. Shi and X. Pan, Chem. J. Chin. Univ., 2005, 26(10), 1934 Search PubMed.
- W. Kubo, S. Kambe, S. Nakade, T. Kitamura, K. Hanabusa, Y. Wada and S. Yanagida, J. Phys. Chem. B, 2003, 107(18), 4374 CrossRef CAS.
- N. Mohmeyer, P. Wang, H. W. Schmidt, S. M. Zakeeruddin and M. Gratzel, J. Mater. Chem., 2004, 14(12), 1905 RSC.
- B. Li, L. Wang, B. Kang, P. Wang and Y. Qiu, Sol. Energy Mater. Sol. Cells, 2006, 90, 549–573 CrossRef CAS.
- H. Matsui, K. Okada, T. Kawashima, T. Ezure, N. Tanabe, R. Kawano and M. Watanabe, J. Photochem. Photobiol., A, 2004, 164(1–3), 129 CrossRef CAS.
- R. Kawano, H. Tokuda, T. Katakabe, H. Nakamoto, H. Kokubo, S. Imabayashi and M. Watanabe, Kob. Ronbu., 2006, 63(1), 31 Search PubMed.
- T. Oda, S. Tanaka and S. Hayase, Jpn. J. Appl. Phys., Part 1, 2006, 45(4A), 2780 CrossRef CAS.
- Y. Ogomi, T. Kato and S. Hayase, J. Photopolym. Sci. Technol., 2006, 19(3), 403 CrossRef CAS.
- L. Wang, S. B. Fang, Y. Lin, X. W. Zhou and M. Y. Li, Chem. Commun., 2005, 45, 5687 Search PubMed.
- A. F. Nogueira, C. Longo and M. A. De Paoli, Coord. Chem. Rev., 2004, 248, 1455 CrossRef CAS.
- Y. Saito, T. Azechi, T. Kitamura, Y. Hasegawa, Y. Wada and S. Yanagida, Coord. Chem. Rev., 2004, 248, 1469 CrossRef CAS.
- S. A. Haque, S. Handa, K. Peter, E. Palomares, M. Thelakkat and J. R. Durrant, Angew. Chem., Int. Ed., 2005, 44, 5740 CrossRef CAS.
- K. Murakoshi, R. Kogure, Y. Wada and S. Yanagida, Chem. Lett., 1997, 5, 471 CrossRef.
- T. P. Chou, Q. Zhang, G. E. Fryxell and G. Cao, Adv. Mater., 2004, 14, 385.
- F. Cao, G. Oskam and P. C. Searson, J. Phys. Chem., 1995, 99, 17071–17073 CrossRef CAS.
- Z.-S. Wang, C.-H. Huang, Y.-Y. Huang, Y.-J. Hou, P.-H. Xie, B.-W. Zhang and H.-M. Chang, Chem. Mater., 2001, 13, 678 CrossRef CAS.
- J. Boucle, P. Ravirajan and J. Nelson, J. Mater. Chem., 2007, 17, 3141 RSC.
- J. Piris, N. Kopidakis, D. C. Olson, S. E. Shaheen, D. S. Ginley and G. Rumbles, Adv. Funct. Mater., 2007, 17, 3849 CrossRef CAS.
- J. Xia, N. Masaki, M. Lira-Cantu, Y. Kim, K. Jiang and S. Yanagida, J. Phys. Chem. C, 2008, 112(30), 11569–11574 CrossRef CAS.
- J. Xia, M. Masaki, M. Lira-Cantu, Y. Kim, K. Jiang and S. Yanagida, J. Am. Chem. Soc., 2008, 130, 1258 CrossRef CAS.
- Y. Kim, Y.-E. Sung, M. J.-bXiaLira-Cantu, N. Masaki and S. Yanagida, J. Photochem.
Photobiol., A, 2008, 193(2–3), 77 CrossRef CAS.
- M. Lira-Cantu, F. Krebs, P. Gomez-Romero and S. Yanagida, Mater. Res. Soc. Symp. Proc., 2008, 1007, S14–04.
-
M. Lira-Cantu and F. C. Krebs, Wo. Pat., 2006120237, 2006.
-
F. C. Krebs and M. Lira-Cantu, Br. Pat., 2437362, 2007.
- M. Saito and S. Fujihara, Energy Environ. Sci., 2008, 1, 280–283 RSC.
- Efficiencies of 11.1% (certified) and 11.5% (not certified) correspond to Prof. Michael Grätzel group. Efficiency of 11.3% (not certified) reported by J. Desilvestro, et al., 23rd European Photovoltaic Solar Energy Conference and Exhibition, Valencia, Spain, 3 September, 2008 Search PubMed.
- T. Yoshida, M. Iwaya, H. Ando, T. Oekermann, K. Nonomura, D. Schlettwein, D. Wohrle and H. Minoura, Chem. Commun., 2004, 400–401 RSC.
- T. Yoshida, K. Terada, T. Sugiura and H. Minoura, Adv. Mater., 2000, 12(16), 1214–1217 CrossRef CAS.
-
T. Yoshida, 23rd European Photovoltaic Solar Energy Conference and Exhibition, Valencia, Spain, 3 September, 2008 Search PubMed.
- Y.-J. Lee, T. L. Sounart, D. A. Scrymgeour, J. A. Voigt and J. W. P. Hsu, J. Cryst. Growth, 2007, 3, 80–85 CrossRef.
-
S. D. Oosterhout, S. S. van Bavel, M. M. Wienk and R. J. Janssen. Abstr. Excitonic Solar Cell Conference, Warwick, UK, 9–12 September, 2008, p. 96 Search PubMed.
-
F. Fabrega-Santiago and B. Bisquert. Abstr. Excitonic Solar Cell Conference,Warwick, UK, 9–12 September, 2008, p. 38 Search PubMed.
- Lifetime of 20
000 h under continuous illumination at 1 sun and 65 °C have been reported for the DSCs of Dyesol by J. Desilvestro, et al., 23rd European Photovoltaic Solar Energy Conference and Exhibition, Valencia, Spain, 3 September, 2008 Search PubMed.
- Lifetime of 4000 h under continuous illumination at 1 sun and 65 °C have been reported for the OSC of Konarka by J. Poortmans, et al., 23rd European Photovoltaic Solar Energy Conference and Exhibition, Valencia, Spain, 3 September, 2008 Search PubMed.
- M. Jørgensen, K. Norrman and F. C. Krebs, Sol. Energy Mater. Sol. Cells, 2008, 92(7), 686–714 CrossRef.
- F. C. Krebs and K. Norrman, Prog. Potovoltaics, 2007, 15(8), 697–712 Search PubMed.
-
Prog. Photovoltaics, 2007, 15(8) Search PubMed.
-
Sol. Energy Mater. Sol. Cells, 2008, 92(7) Search PubMed.
- E. Guillen, F. Casanueva, J. A. Anta, A. Vega-Poot, G. Oskam, R. Alcantara, C. Fernandez-Lorenzo and J. Martın-Calleja, J. Photochem. Photobiol., A DOI:10.1016/j.jphotochem.2008.08.015.
- Q. Zhang, T. P. Chou, B. Russo, S. A. Jenekhe and G. Cao, Angew. Chem., Int. Ed., 2008, 47, 2402–2406 CrossRef CAS.
- G. Z. Cao, Photonics Spectra., 2008, 42(7), 60–61 Search PubMed.
Footnote |
† Excitonic solar cells can also be classified by the type of n–p junction. Thus, a bulk-heterojunction solar cell will be the one applying semiconductor materials (e.g. organic C60 derivatives like PCBM, or inorganic ZnO or CdSe nanoparticles) in direct physical contact with a conjugated polymer (see ref. 29). In DSC we find two types of junctions: a bulk heterojunction made by the TiO2nanoparticles and the light-harvesting Dye, and an electrochemical junction between the Dye/TiO2electrode and the redox electrolyte (see ref. 3). |
|
This journal is © The Royal Society of Chemistry 2009 |
Click here to see how this site uses Cookies. View our privacy policy here.