DOI:
10.1039/C4GC02237H
(Paper)
Green Chem., 2015,
17, 2208-2216
Chameleon behaviour of iodine in recovering noble-metals from WEEE: towards sustainability and “zero” waste†
Received
15th November 2014
, Accepted 12th January 2015
First published on 12th January 2015
Abstract
An effective and sustainable method for the selective leaching of metals from the non-ferrous metal fraction of Waste Electric and Electronic Equipment (WEEE) is described here. This method consists of a sequence of steps which involve the selective leaching of the different metals from the shredded sample by using environmentally friendly lixiviants in water. In particular: (1) a refluxing citric acid (3 M) solution which dissolves Sn, Zn, Pb, Ni, and other base metals; (2) NH3 in combination with an IO3−/I− mixture which allows one to oxidize Cu and Ag, and to separate them by selective AgI precipitation; (3) an I−/I2 mixture (5.3
:
1 molar ratio) which is capable of leaching quantitatively Au metal from the solid residue. Each step is followed by a further treatment for: (i) high-rate metal and reagent recovery, in the case of NMs; (ii) inertization, in the case of heavy metals. The “chameleon” behaviour of iodine, which shows versatile redox/complexing/precipitating capabilities, allows one to achieve, on the one hand, a selective noble-metal (NM) leaching and, on the other hand, a simple and effective reagent and metal recovery. The comparison of the above described method with a similarly effective one previously patented by some of the same authors, allows one to point out that a significant improvement in sustainability is achieved in terms of lixiviant employment, which is of low cost, easily available and recyclable, and able to work in water solutions, while maintaining or improving its environmentally friendly character.
1. Introduction
Waste of Electric and Electronic Equipment (WEEE) represents the most promising secondary source of raw materials, in particular metals, in our contemporary world. Due to the large amount, growing accumulation rates and peculiar composition of WEEE, governments world-wide have promulgated specific directives in order to promote sustainable waste management and to face the increasing demand for the planet's limited resources.1,2 Accordingly, the new world-wide waste management strategy is addressed at converting “trash” into “resource” by creating value from waste, through reuse, recycling, waste-to-energy and recovery, while allowing only safe and sustainable processes or methods. Noble metals (NMs) have wide application in the manufacture of electronic equipment, working as contact materials due to their high chemical stability and good conducting properties.3 As a consequence, WEEE may contain noble, and in addition other, critical metals4 in amounts comparable to, or even higher than those in, their ores. It happens in Printed Circuits Boards (PCB) or other Hi-Tech scraps, on account of which these are called “urban mines”. Although pyrometallurgical processes have been typically employed to recover NMs from WEEE,5 in the last few decades several studies have been addressed to investigate known or new hydrometallurgical processes, with the view to limiting economical and environmental costs. Regarding the hydrometallurgical processes for gold reclamation from ores and for refining NM slags and ashes, it must, however, be recalled that the well-known “Cyanidation”§ and “aqua-regia”¶ processes are still the most widely employed, despite their being based on the use of highly toxic and/or aggressive chemicals.5,6 The effectiveness of these processes is relatable to the joint presence of complexing and oxidizing agents. In the above-mentioned cases CN− and Cl− act as complexing agents capable of lowering the high NM reduction potential through the formation of stable metal-complexes, and O2 and NO3− act as oxidants. On these bases, alternative leaching mixtures, such as thiourea or thiosulfate solutions in the presence of oxidizing reagents, have been proposed for gold etching, but they have not found large-scale applications mainly due to the large consumption of non-recyclable reagents.5,6 More recently mixtures of thionyl chloride and organic solvents/reagents such as pyridine, N,N-dimethylformamide and imidazole, named “organic aqua-regia”, have raised great interest for their capability to dissolve gold and other NMs at high dissolution rates under mild conditions.7 This method was applied for etching Au metallization on a circuit board. The enhanced reactivity of “organic aqua-regia” was ascribed to the formation of donor–acceptor adducts between the reagents and considered unique when compared to the so-far available etching reagents. However, the harmful nature of the employed reagents/solvents, makes it unappealing for safe and friendly use.8 Moreover, we note that similar etching properties towards NMs have been recognized since the late 90s11 in donor/acceptor (dihalogens, mainly I2) mixtures, which may form adducts, remain stable9 or undergo further transformation in organic solvents.10 In particular in our laboratory the etching properties of dihalogen mixtures with donors bearing two vicinal thionic groups, such as cyclic-dithioxamides [e.g. N,N′-dimethylperhydrodiazepine-2,3-dithione (Me2dazdt) and N,N′-dimethylpiperazine-2,3-dithione (Me2pipdt)] have been extensively investigated.11a,12 It is found that Me2dazdt/I2 mixtures, in particular the Me2dazdt·2I2 adduct, in organic solvents dissolve Au13 and Pd14 selectively under mild conditions, while they are inactive towards Pt, which, in turn, can be dissolved by Me2pipdt/I2 mixtures in the above cited solvents.15 Remarkably, organic solutions of Me2dazdt·2I2 have been used successfully on a laboratory scale for gold recovery from both WEEE (ink-jet cartridges, smart cards, PCBs and selected shredded R4 WEEE)16 and microelectronic devices in deprocessing procedures for failure analysis.17 Moreover the use of organic solvents allows one to avoid a detrimental wetting of electric contacts. Thus the effectiveness and homogeneity of etching, combined with safe and friendly use, make these reagents a very promising alternative to the less selective and inhomogeneous ones commonly employed for this kind of application. On the other hand, their relatively high cost, market unavailability and use of an organic solvent for leaching may limit their appeal for large scale applicability in WEEE recovery processes. With the view to overcoming these limitations for a better match with industrial requirements of technical, economical and environmental sustainability and based on our knowledge of donor–acceptor systems and iodine chemistry,18 we have exploited the versatility of this “chameleonic” element to design a process for NM recovery from WEEE, where only water is used as the solvent and elemental sustainability is pursued as much as possible. The versatility of iodine is relatable to its redox properties which allow several species in different oxidation states, exhibiting a variety of properties, to be reversibly formed. For example, I2 can behave as an oxidizing agent towards reducing species, such as elemental metals, forming I−. This capability, shown in organic solvents,19 can be preserved in water, where I2 is almost insoluble, employing an I3− ion (formed through I−–I2 donor–acceptor interactions) which shows similar oxidation properties.20 The iodide ion may be employed as a donor towards suitable metal ions to form stable metal complexes or also as a precipitating agent to form salts of low solubility. These properties are largely applied to lower the reduction potential of metals favouring metal oxidation, as occurs in the case of gold,21 or for selective ion separation. On the other hand, I− can be quite easily oxidized back to I2, and this capability can be useful to recover the reagent at the end of the leaching process.22 Finally, I2 produces IO3−/I− mixtures through a disproportion reaction. Thus a further tuning of the oxidating/complexing/precipitating properties of the reagents is achieved on simple pH variation.21 The versatility of the “chameleonic” iodine, combined with its low environmental impact and elemental sustainability, make I2-based lixiviants very appealing for employment in “green” metal recovering processes, as described in this paper.23 We report here an effective and sustainable hydrometallurgical method for NM recovery from WEEE. The obtained results are thoroughly discussed in comparison with those obtained for our previous patented method to point out the advantages/disadvantages of the two methods. The full characterization of the used real sample is also presented here to highlight the characteristics of the test specimen.
2. Experimental
2.1 Materials and methods
Reagents and solvents were purchased from Sigma-Aldrich (except citric acid anhydrous FU-E 330 from ACEF, Italy) and used without further purification.
The real sample is used as provided by a company which treats WEEE by applying a conventional mechanical process24 and consists of a milled mixture of metals (average particle size: 0.4 mm) which represents the non-ferrous metallic fraction output of the de-processing plant. In this plant the incoming material consists of PCBs and selected small electronic equipment, e.g. mobile phones, notebooks, etc., and this is submitted to the crushing, separation from residual hazardous components, shredding and mechanical separation (magnetic and eddy current separation) of ferrous and non-ferrous metals, and of plastics.
2.2 Characterization of the test specimen
The test specimen has been fully characterized by Inductively Coupled Plasma-Atomic Emission Spectroscopy (ICP-AES) and by X-ray-based techniques such as Scanning Electron Microscopy interfaced with X-ray microanalysis (SEM-EDS), X-ray Photoelectron Spectroscopy (XPS), Wide-angle X-ray Diffraction (WA-XRD), and X-ray Fluorescence (XRF).
2.2.1 ICP-AES characterization.
0.5 g aliquots were sub-sampled from the original solid mixture, then introduced in TFM vessels containing a mixture of HNO3 (65%, 2 mL), HCl (37%, 6 mL), H2O2 (30%, 0.5 mL) and treated in a Milestone Ethos 1 Microwave digester, equipped with an HPR1000/10S high pressure segmented rotor, an ATC-400CE automatic temperature control and a Terminal 640 with easyCONTROL software. The treatment was performed applying a microwave program consisting of two steps lasting 10 and 20 minutes, respectively, at a temperature of 200 °C and microwave power up to 1000 W. The samples were prepared for the analysis by diluting the digested solutions with 1% HCl–HNO3 blank and then the metals were determined using an ICP-AES Varian Liberty 200 Spectrometer, with respect to 5-point calibration plots in the 1–50 ppm range for copper and in the 1–10 ppm range for the other metals. Three independent experiments were used to determine the average values which are reported in Table 1.
Table 1 Average metal content of the specimen sample
Test specimen |
Metal |
Composition (%, w/w) |
|
Cu |
79 |
Sn |
10 |
Pb |
7 |
Zn |
2 |
Ni |
0.5 |
Ag |
0.06 |
Au |
0.01 |
Others (Al, Cr, Mn, Fe, Co) |
1 |
2.2.2 Morphological, dimensional and compositional analysis.
Morphological characterization of the sample was obtained by metallographic and electronic microscopy, by means of the Zeiss Axioskop 40 Metallographic Microscope equipped with a 100× objective and a Canon PowerShot G5 to collect images, and of SEM (ESEM Quanta FEI 200, equipped with EDS detector), respectively. The dimensional characterization has been obtained by using particle sieves and SEM images. Finally, compositional information has been collected, on representative aliquots of the sample, by means of EDS microanalysis, XPS analysis (Theta Probe spectrometer, Thermo Electron Corporation, using monochromatic Al Kα source and sample deposited on discs of double adhesive graphite fitted on the sample holder), WA-XRD (Panalytical Empyrean diffractometer equipped with a graphite monochromator on the diffracted beam and an X'Celerator linear detector. The scans were collected within the range of 10°–90° (2θ) using CuKα radiation), and XRF (ASSING S.p.A., mod. ASX-DUST) measurements.
2.3 Characterization of the recovered metals
The recovered metals have been weighed and then characterized by ICP-AES after acid dissolution (concentrated HNO3 for Cu and Ag; aqua-regia for Au), as described above. Copper recovered by cementation, has been also characterized by SEM-EDS.
2.4 Electrowinning experiments
Metals copper, silver and gold have been recovered from the leaching solutions by electrodeposition. The electrowinning apparatus was formed by two metallic electrodes (Pt-wire for the anode and Cu-layer for the cathode) connected, to their perspective ends, with an external electron supply (Thurlby Thandar Instruments, mod. PL 310) which drives the process.
3. Results and discussion
3.1 Description of the test specimen of WEEE
The sample which was submitted to leaching consists of a non-ferrous metallic fraction obtained as the output of a mechanical de-processing plant, where a selection of PCBs and small electronic equipment are shredded and submitted to pre-treatments in order to separate the incoming mixture into homogeneous particle flows with a high concentration of the target materials: aluminium, ferrous metals, vitreous-plastic materials and non-ferrous metals. Table 1 summarizes the metal content of the non-ferrous metal fraction determined by ICP-AES spectrometry, as described in the Experimental section.
Fig. 1a and b show the morphology of the sample by metallographic and scanning electron microscopy, respectively.
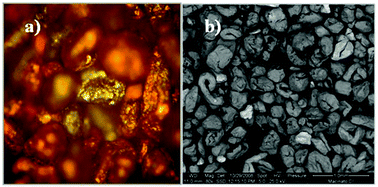 |
| Fig. 1 Top-view micrographs of the test specimen by: (a) metallographic (magnification 100×); and (b) scanning electron (magnification 80×) microscopy. | |
An average particles size of approximately 0.4 mm has been determined by using particle sieves and SEM images. The average metal composition obtained by SEM-EDS on three different aliquots of the test specimen, as well as the qualitative XRD and XRF characterization, agree with the chemical composition reported in Table 1. Punctual SEM-EDS and XPS determinations on the surface of selected grains of the sample show the presence of oxidized metals. Details of the chemical–physical characterization are reported in ESI.†
3.2 Selective leaching and recovery of metals from the WEEE specimen sample
The employed method (named Method A) was applied on a laboratory scale, starting from 10 g of the sample and is based on a sequence of three main steps which allow the selective removal of base metals and copper and silver, leaving as residue the WEEE fraction enriched in gold, as summarized in Fig. 2.
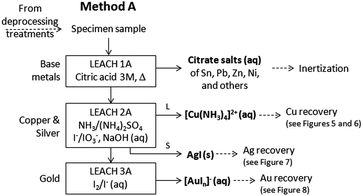 |
| Fig. 2 Schematic diagram of the leaching steps of Method A. L, S = liquid and solid fractions. | |
3.2.1 Leach 1A: Base metals’ dissolution and inertization.
Citric acid, a weak natural acid solid at room temperature, has been employed for the dissolution of base metals (Leach 1A, Fig. 2) in spite of more harmful acids such as HNO3 or H2SO4, typically employed in WEEE treatments.25 In Fig. 3 the weight loss with time of 10 g of the test specimen on reaction with citric acid 3 M under different leaching conditions (room temperature (a); under reflux (b); room temperature and addition of 27.3 mL H2O2 35% (c)); is reported.
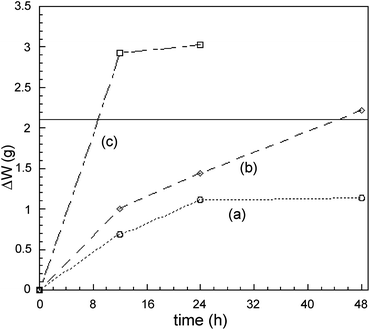 |
| Fig. 3 Weight loss of 10 g of test specimen in the given time (hours) by treatment with citric acid 3 M at: (a) room temperature (⋯○⋯); (b) refluxing (–◊–); (c) by H2O2 35% addition (─ ·□─ ·). The solid line represents the expected amount of base metals in the sample (2.1 g). | |
As shown, a quantitative base metal dissolution is achieved under the (b) and (c) conditions in the observation time. Approximately 48 hours are required to complete the treatment (b). The colour of the solution changes from colourless to greenish and no precipitate is formed. As expected, faster leaching, approximately 8 h, accompanied with a loss in selectivity, is obtained in the presence of H2O2 (c). In fact a partial copper dissolution (about 12% in 24 h) is observed as suggested qualitatively by the dark green-blue colour of the solution and quantitatively by the weight loss of the sample which exceeds, in the time, the expected base metal amounts. Moreover on standing, the leaching solution forms a Cu(C2O4)·H2O precipitate, which was identified by the WA-XRD spectrum, shown in Fig. 4.
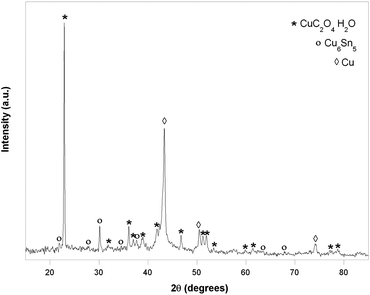 |
| Fig. 4 WA-XRD spectrum and peaks assignment for Cu(C2O4)·H2O precipitate obtained from the leaching of 10 g of test specimen by citric acid 3M at room temperature and H2O2 35% addition. | |
This behaviour could be explained by invoking Fenton chemistry.26 In fact, the metal's dissolution generates the required M(n−1)+/Mn+/H2O2 mixture able to activate the radical reactions which start from the formation of the OH˙ radical.|| Under the described conditions, a reproducible partial degradation of citric acid to oxalic acid through C–C bond breaking occurs. Further studies are in progress to clarify the mechanism of the reaction. After leaching, metals can be recovered from the aqueous solutions in the form of citrate salts or through conventional treatments with suitable precipitating reagents. The excess of citric acid is recovered directly from the resulting solution by solvent evaporation and/or by solvent extraction. In the described conditions, Ag and Au, remain unreacted.
On the basis of the results described above for Leach 1A, we can conclude that treatment (b) is most suitable to maximize selectivity and to avoid by-products, while treatment (c) may be preferred if faster but less selective processes are prioritised.
3.2.2 Leach 2A: copper and silver separation and recovery.
The solid residue from Leach 1A is treated with a mixture of ammonia (33%, 29 mL) and ammonium sulfate (25.6 g). To this mixture, a solution containing IO3− and I−, prepared through I2 (50 g) disproportion in 300 mL of NaOH 1.5 M, is slowly added dropwise. The solution becomes coloured by the formation of the blue [Cu(NH3)4]2+ complex. The reaction is stopped when no change in the colour of the solution is observed. To ascertain that complete copper dissolution is achieved, the procedure is repeated on the solid residue until a colourless solution appears. A quantitative copper dissolution is achieved in approximately 48 h. Meanwhile the precipitation of AgI occurs. Thus, as is predictable, the oxidation of the metals by iodate [E°(IO3−/I−) = +0.26 V]** is favoured by the presence of complexing (NH3) and precipitating (I−) reagents which affect the reduction potential through the formation and solubility constants (Kf and Ksp)** of related equilibria. In the employed ammonia excess, on the one hand, copper oxidation and the quantitative formation of the very stable [Cu(NH3)4]2+ complex, are achieved according to eqn (1) and (2): | Cu2+(aq) + 4NH3(aq) ⇌ [Cu(NH3)4]2+(aq) Kj = 1.1×1013 | (1) |
| [Cu(NH3)4]2+(aq) + 2e− ⇌ Cu(s)+4NH3(aq) E° = −0.05 V | (2) |
On the other hand, in the presence of IO3−/I−, the cited ammonia excess is not sufficient to favour silver complexation, and the quantitative AgI(s) precipitation occurs in agreement with the following equilibria (eqn (3)–(6)):
| AgI(s) ⇌ Ag+(aq) + I−(aq) Ksp = 1.2 × 10−16 | (3) |
| AgI(s) + 1e− ⇌ Ag(s) + I−(aq) E° = −0.152 V | (4) |
| Ag+(aq) + 2NH3(aq) ⇌ [Ag(NH3)2]+(aq) Kf = 1.6 × 107 | (5) |
| [Ag(NH3)2]2+(aq) + 1e− ⇌ Ag(s) + 2NH3(aq) E° = +0.373 V | (6) |
Finally, a comparison between the standard reduction potentials related to gold oxidation/complexation [E°([AuI2]−/Au) = +0.58 V, E°([AuI4]−/Au) = +0.56 V, at 298 K] and that reported for IO3−/I− redox couple suggests that gold dissolution should not occur, as found.
Accordingly, a selective copper and silver separation, leaving gold unreacted, is achieved.
Cu0 recovery from Leach 2A solution.
Both chemical and electrochemical reductions, well-known as “cementation” and “electrowinning”, have been applied for copper recovery from a solution containing [Cu(NH3)4]2+(aq). Accordingly, a Zn(s) excess, in the form of powder, is added to the Leach 2A blue solution, which undergoes decolouration as a consequence of copper reduction. The unreacted Zn(s) excess has been removed by washing the solid residue with diluted HCl. A quantitative copper recovery (8.1 ± 0.3 g on 10 g of test specimen), with purity >90% and in the form of uniform particles of approximately 500 nm, has been obtained through cementation, as shown in the SEM micrograph reported in Fig. 5.
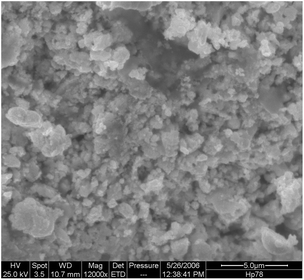 |
| Fig. 5 SEM micrograph of copper recovered by cementation with Zn. Average particles size = ∼500 nm. | |
NH3 and I2 can be selectively recovered from the resulting solution. NH3(aq) is recovered by bubbling the vapours produced by distillation into water, meanwhile an abundant precipitation of Zn(OH)2 occurs when NH3(g) leaves the solution. This hydroxide can be recovered as it is or dissolved with HCl dil., and zinc is recovered from the chloridric solution by precipitation. After that, H2O2/H+ is added to the solution under warming, to oxidize iodide ions to I2. Under these conditions, purple vapours of I2 are formed and collected as solid on cooling. The copper cementation process, with the complete recovery of reagents and products for elemental sustainability, is summarized in Fig. 6.
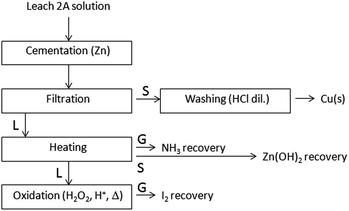 |
| Fig. 6 Schematic diagram of Cu(s) recovery by cementation on a Leach 2A solution. Reagent recovery/valorisation. S, L, G = solid, liquid and gaseous fractions. | |
With the view to obtaining the complete recovery of reagents and products, minimizing reagent consumption and avoiding by-products, alternative copper electrowinning has been performed as summarized in Fig. 7. In this case, preliminary NH3 and I2 removals from the Leach 2A solution, in the same way described for cementation, are performed. The resulting solution undergoes a conventional electrochemical metal deposition, obtaining a quantitative copper deposition (8.9 ± 1.5 g on 10 g of test specimen) on a copper electrode.
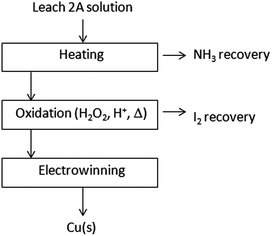 |
| Fig. 7 Schematic diagram of Cu(s) electrochemical recovery from a Leach 2A solution. Reagent recovery/valorisation. | |
Ag0 recovery.
As summarized in Fig. 8, the solid residue of the Leach 2A treatment is filtered on a glass Buchner funnel and then washed repeatedly on the frit with an aqueous solution of Na2S2O3 (0.5 g in 50 mL of H2O dist.), in order to dissolve AgI(s) and separate aqueous [Ag(S2O3)2]3− (Kf = 4.7 × 1013) from the metallic residue. Silver metal recovery in almost quantitative yields (6 ± 2 mg on 10 g of test specimen) is obtained by submitting the latter solution to the electrowinning process, where Ag(s) and S4O62−(aq) are produced at the cathode and anode, respectively. Ag0 can be also obtained by cementation with Zn (or other reducing metals such as Fe, Mg, etc.).27
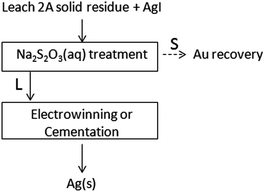 |
| Fig. 8 Schematic diagram of Ag(s) electrochemical/chemical recovery from a Leach 2A solid residue. | |
3.2.3 Leach 3A: gold dissolution and recovery.
The solid residue lasting from Leach 1A and 2A, containing mainly gold and inert plastic/vitreous materials, is treated for few minutes with a 10 mL water solution containing 0.46 g of KI (2.7 mmol) and 0.13 g of I2 (0.51 mmol) in a 5.3
:
1 molar ratio. Gold is dissolved and forms [AuIn]− complexes,22 according to reactions (7)–(10), due to the presence of the I3− reagent [E°(I3−/I−) = +0.54 V] whose oxidation capability is enhanced by the formation of complexes shown in eqn (7) and (9). | Au+(aq) + 2I−(aq) ⇌ [AuI2]−(aq) Kf = 7.9 × 1018 | (7) |
| [AuI2]−(aq) + 1e− ⇌ Au(s) + 2I−(aq) E° = +0.58 V | (8) |
| Au+(aq) + 4I−(aq) ⇌ [AuI4]−(aq) Kf = 5.0 × 1047 | (9) |
| [AuI4]−(aq) + 3e− ⇌ Au(s) + 4I−(aq) E° = +0.56 V | (10) |
After leaching, H2O2–HCl are added to the solution in order to oxidize iodide and recover I2 as described above. Metal gold, in 94–100% yields (0.97 ± 0.03 mg on 10 g of test specimen), is recovered from the chloridric solution by electrowinning (see Fig. 9).
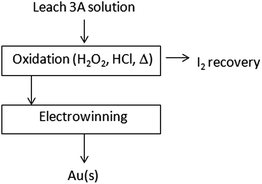 |
| Fig. 9 Schematic diagram of Au(s) electrochemical recovery from a Leach 3A solution. Reagent recovery/valorisation. | |
The gold recovery yields have been confirmed also by adding spikes of 2 and 5 mg (0.02 and 0.05%w/w, respectively) of gold powder to the incoming test specimen.
3.3 Two effective methods for WEEE recovery in comparison
As mentioned in the Introduction, Method A has been designed with the view to improving the matching of a previously patented method, very effective in NM recovery from WEEE,16 with industrial requirements of technical, economical and environmental sustainability. This method, here named Method B, is summarized in Fig. 10.
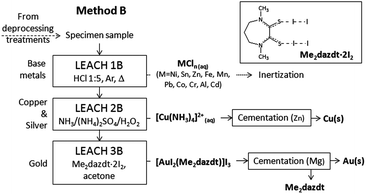 |
| Fig. 10 Schematic diagram of the previous patented method (Method B). | |
A comparison of the two methods is discussed below.
3.3.1 Leach 1.
In Leach 1B, HCl is employed as the lixiviant. This acid was preferred with respect to other commonly employed strong acids such as HNO3 or H2SO4 as it is more selective towards base metals (it does not contain species more oxidizing than H+) and less harmful in terms of toxic fumes and by-product production. Moreover, most of the base metal chloride salts show a high water solubility, which is an important factor to separate these metals from the milled mixture sample under treatment. The base metal dissolution in refluxing HCl (1
:
5, ∼2 M) is quite effective (24 h to dissolve base metals) but not fully selective due to a partial NM dissolution in the presence of O2, likely relatable to the complexing capability of Cl− towards these metals.21b By working under inert atmosphere (e.g. by Ar) conditions, a selective and quantitative base metal dissolution has been achieved. Base metals may be recovered from the chloridric solution with conventional treatments with suitable precipitating reagents.
As described, in Leach 1A the weaker citric acid is used to substitute hydrochloric acid. The quite low acidity of citric acid (pKa1 = 3.13; pKa2 = 4.76; pKa3 = 6.40) limits its effectiveness in metal dissolution, but the lower efficiency with respect to HCl can be overcome by increasing the acid concentration. Accordingly a quantitative dissolution of base metals is achieved by refluxing citric acid 3 M for about 48 h. Nevertheless, differently from HCl, leaching does not require an inert atmosphere thanks to its full selectivity towards base metals. The described behaviour coupled with the natural availability and low cost of citric acid, a solid and non-harmful reagent, makes Leach 1A preferable with respect to Leach 1B.
3.3.2 Leach 2.
An ammonia solution has been employed in Leach 2B to favour copper and silver dissolution, using as the oxidizing reagent H2O2 (28–35%), which is slowly added to the NH3–(NH4)2SO4 mixture. A fast and quantitative copper and silver dissolution occurs at room temperature. Meanwhile an effervescence due to the exothermic degradation of H2O2 to O2 catalyzed by metals is produced.
In Leach 2A, instead, copper and silver are oxidized through a milder one-step oxidating/complexing/precipitating reaction, with an alkaline IO3−/I− mixture, added to the ammonia solution. Fig. 11 shows a comparison of the weight loss in the time of a calibrated copper wire (500 mg, ∅ = 0.3 mm) for reaction with three different formulations of the Leach 2 solution, at room temperature and at the same NH3–(NH4)2SO4 concentration (4.4 × 10−3 M and 6.0 × 10−4 M, respectively).
 |
| Fig. 11 Weight loss of calibrated copper wires (500 mg, ∅ = 0.3 mm) in the given time (minutes) by treatment with NH3/(NH4)2SO4 (4.4 × 10−3 M and 6.0 × 10−4 M, respectively): (a) without additions (⋯○⋯); (b) with 30 mL NaOH 1.5 M/I2 (5 g) solution (–◊–); and (c) 2.7 mL H2O2 35% (─ ·□─ ·) additions. | |
Although the leaching with the IO3−/I− alkaline solution is less effective than that with H2O2, it shows the following advantages: (i) it allows a one-step dissolution/separation of copper and silver from the test specimen; (ii) it ensures a high atom economy, due to the recyclability of the employed reagents; (iii) metal-oxidations proceed more smoothly than in Leach 2B. These features make Leach 2A the treatment that better complies with the requirements of safety and sustainability which are the most important aspects in designing Method A.
3.3.3 Leach 3.
[Me2dazdt·2I2], described in the Introduction, has been employed as the leaching agent towards elemental gold in Leach 3B. This reagent is easy to handle, shows low toxicity and is effective under very mild conditions (room temperature and pressure, no protection from air and moisture). Its effectiveness in an organic solvent, in terms of reaction rate, homogeneity, and selectivity of gold dissolution, has been compared with an I−/I2 aqueous solution of the same concentration (5.0 × 10−3 mol dm−3) previously. As reported in ref. 11a and 17a, and summarized in ESI,† a comparison of calibrated gold wires and Si/SiO2/Ti/Au thin layers (thickness 300 μm/0.5 μm/15 nm/200 nm) showed that in both cases the diiodine adduct works better than the I−/I2 aqueous solution, making the former reactant the most suitable, in particular for gold removal from microelectronic devices (e.g. GaAs-based laser diodes, GaN-based LEDs and Al-silicon ICs) where effectiveness, selectivity and homogeneity of leaching are required to perform the end-of-life failure analysis.17b Regarding the [Me2dazdt·2I2] application in WEEE treatment, quantitative gold recovery is achieved from the test specimen under discussion, obtaining a 60%–100% ligand recovery also depending on the employed solvent (acetone or CH3CN respectively), by cementation with Mg(s).
On the other hand, the I−/I2 water solution, used in Leach 3A to oxidize gold, can improve its effectiveness by tuning the concentration and molar ratio of iodide–diiodine mixtures. In fact, a fast and quantitative gold leaching is obtained at room temperature by using 0.05 M and 0.27 M solutions for I2 and I−, respectively.
In conclusion, whether aqueous solvents are preferable and high selectivity and homogeneity of etching are not strictly required, such as in the case of WEEE recovery, I−/I2 mixtures in water seem more suitable for practical application with respect to the more effective [Me2dazdt·2I2] reagent in an organic solvent, since these reagents are more easily available and fully recyclable and have a lower cost.
4. Concluding remarks
In this paper an effective and sustainable method for the recovery of valuable metals from secondary sources has been described. In particular, the non-ferrous metallic fraction of a real sample of shredded WEEE has been investigated, fully characterized and submitted to a friendly closed-loop process for metal separation and valorisation with the view to evaluating all aspects related to technical, economical and environmental sustainability. A crucial role in the described method is played by iodine, whose versatile behavior has been successfully exploited for the selective dissolution–recovery of NMs. Moreover its non-harmful nature and ease of recovery increase its appeal as a “green” reagent.
Method A on the whole, which allows the recovery of NMs almost quantitatively by using “green” reagents under very mild conditions, represents, in our opinion, a very challenging and greener alternative to the methods currently in use for large scale NM recovery from real WEEE samples. It is remarkable that the investigated sample is representative of a complex mixture of WEEE consisting of very heterogeneous materials with a low content of NMs when compared, for example, with the corresponding milled sample obtainable from the “richer” PCBs. The satisfactory separation of a complex material like this and the quantitative recovery of the small amount of gold and silver contained in the test specimen, demonstrate the effectiveness of the method and suggest its wider applicability in terms of both process scale and selectable WEEE, with particular reference to PCBs, ink-jet printer cartridges and smart cards, that are widespread and typically richer in gold. Nevertheless, we note that if other NM removal applications are considered, the selection of the leaching solutions and the sequence of the steps should be tailored on a case-by-case basis depending on which aspect is prioritised (i.e., efficiency, homogeneity, rate, cost, recyclability and nature of reagents, product value, metal recovery, etc.), as demonstrated by the best results obtained by using [Me2dazdt·2I2] organic solutions with respect to the aqueous I−/I2 mixture in gold etching for the end-of-life failure analysis of microelectronic devices.
Acknowledgements
3R Metals Ltd, a spinoff of the University of Cagliari, and Sardegna Ricerche, who is the holder of the patent based on the reported Method B, are greatly acknowledged for financing and for the support to the research and technology transfer. The authors gratefully acknowledge Prof Emanuele Filiberto Trogu for his valuable contribution to the research. Finally, the authors acknowledge support by the X-ray photoelectron spectroscopy laboratory of Centro Grandi Strumenti of Università degli Studi di Cagliari (CGS), in particular Dr Marzia Fantauzzi and Prof Antonella Rossi for their help in collecting and discussing the XP-spectra, and Laboratorio di Microscopia, CRS4 – Parco tecnologico della Sardegna, in particular Dr Simona Podda for SEM-EDS characterization.
Notes and references
- Directive 2012/19/EC of the European Parliament and of the Council, Off. J. Eur. Union, 2012, L 197, 38 Search PubMed.
- Directive 2002/96/EC of the European Parliament and of the Council, Off. J. Eur. Union, 2002, L 37, 24 Search PubMed.
- L. H. Yamane, V. T. de Moraes, D. C. R. Espinosa and J. A. S. Tenório, Waste Manage., 2011, 31, 2553 CrossRef CAS PubMed.
- Report of the EC Ad-hoc Working Group on defining critical raw materials, May 2014, http://ec.europa.eu/enterprise/policies/raw-materials/files/docs/crm-report-on-critical-raw-materials_en.pdf.
-
(a) J. Cui and L. Zhang, J. Hazard. Mater., 2008, 158, 228 CrossRef CAS PubMed;
(b) Y. Zhou and K. Qiu, J. Hazard. Mater., 2010, 175, 823 CrossRef CAS PubMed.
-
(a)
P. A. Tasker, P. G. Plieger and L. C. West, in Comprehensive on Coordination Chemistry II, ed. M. D. Ward, J. A. McCleverty and T. J. Meyer, Elsevier, 2004, vol. 9, p. 759, and references cited therein; Search PubMed;
(b) S. Syed, Hydrometallurgy, 2012, 115–116, 30 CrossRef CAS PubMed;
(c) Y. J. Park and D. J. Fray, J. Hazard. Mater., 2009, 164, 1152 CrossRef CAS PubMed.
- W. Lin, R.-W. Zhang, S.-S. Jang, C.-P. Wong and J.-I. Hong, Angew. Chem., Int. Ed., 2010, 122, 8101 CrossRef.
- Our skepticism on the method based on organic aqua-regia, as a potential green chemistry technology was presented in C&N, April 4, 2011, p. 11 as a comment to News of the Week.
-
(a) F. Bigoli, P. Deplano, M. L. Mercuri, M. A. Pellinghelli, A. Sabatini, E. F. Trogu and A. Vacca, Can. J. Chem., 1995, 73, 380 CrossRef CAS;
(b) F. Bigoli, P. Deplano, A. Ienco, C. Mealli, M. L. Mercuri, M. A. Pellinghelli, G. Pintus, G. Saba and E. F. Trogu, Inorg. Chem., 1999, 38, 4626 CrossRef CAS PubMed.
-
(a) P. Deplano, S. M. Godfrey, F. Isaia, C. A. McAuliffe, M. L. Mercuri and E. F. Trogu, Chem. Ber., 1997, 130, 299 CrossRef CAS;
(b) F. Bigoli, P. Deplano, F. A. Devillanova, V. Lippolis, M. L. Mercuri, M. A. Pellinghelli and E. F. Trogu, Eur. J. Inorg. Chem., 1998, 137 CrossRef CAS.
-
(a) A. Serpe, F. Artizzu, M. L. Mercuri, L. Pilia and P. Deplano, Coord. Chem. Rev., 2008, 252, 1200 CrossRef CAS PubMed;
(b)
S. M. Godfrey and C. A. McAuliffe, in Modern Coordination Chemistry, ed. G. J. Leigh and N. Winterton, Royal Society of Chemistry, Cambridge, 2002, p. 79 Search PubMed.
-
(a) A. Serpe, F. Artizzu, L. Marchiò, M. L. Mercuri, L. Pilia and P. Deplano, Cryst. Growth Des., 2011, 11, 1278 CrossRef CAS;
(b) M. L. Mercuri, A. Serpe, L. Marchiò, F. Artizzu, D. Espa and P. Deplano, Inorg. Chem. Commun., 2014, 39, 47 CrossRef CAS PubMed.
- F. Bigoli, P. Deplano, M. L. Mercuri, M. A. Pellinghelli, G. Pintus, A. Serpe and E. F. Trogu, Chem. Commun., 1998, 2351 RSC.
-
(a) A. Serpe, F. Bigoli, M. C. Cabras, P. Deplano, P. Fornasiero, M. Graziani, M. L. Mercuri, T. Montini, L. Pilia and E. F. Trogu, Chem. Commun., 2005, 1040 RSC;
(b)
P. Deplano, P. Fornasiero, M. Graziani, M. L. Mercuri, A. Serpe and E. F. Trogu, EU patent, EP1743044B1, 2005 Search PubMed.
- F. Bigoli, P. Deplano, M. L. Mercuri, M. A. Pellinghelli, G. Pintus, A. Serpe and E. F. Trogu, J. Am. Chem. Soc., 2001, 123, 1788 CrossRef CAS.
-
(a)
P. Deplano, M. L. Mercuri, L. Pilia, A. Serpe and M. Vanzi, EU patent, EP1964936, 2007 Search PubMed;
(b) A. Serpe, F. Artizzu, D. Espa, A. Rigoldi, M. L. Mercuri and P. Deplano, Green Process. Synth., 2014, 3, 141 CAS.
-
(a) L. Cau, P. Deplano, L. Marchió, M. L. Mercuri, L. Pilia, A. Serpe and E. F. Trogu, Dalton Trans., 2003, 1969 RSC;
(b) M. Vanzi, A. Bonfiglio, P. Salaris, P. Deplano, E. F. Trogu, A. Serpe, G. Salmini and R. De Palo, Microelectron. Reliab., 1999, 39, 1043 CrossRef.
- P. Deplano, J. R. Ferraro, M. L. Mercuri and E. F. Trogu, Coord. Chem. Rev., 1999, 188, 71 CrossRef CAS.
-
(a) Y. Nakao, J. Chem. Soc., Chem. Commun., 1992, 426 RSC;
(b) Y. Nakao and K. Sone, Chem. Commun., 1996, 897 RSC.
- W. Gottardi, Fresenius’ J. Anal. Chem., 1998, 362, 263 CrossRef CAS.
-
(a) M. Baghalha, Hydrometallurgy, 2012, 113–114, 42 CrossRef CAS PubMed;
(b) A. P. Abbott, G. Frisch, S. J. Gurman, A. R. Hillman, J. Hartley, F. Holyoak and K. S. Ryder, Chem. Commun., 2011, 47, 10031 RSC.
-
R. P. Homick and H. Sloan, US patent, US3957505, 1974 Search PubMed.
-
(a)
L. Jacques, patent, WO1998005569A1, 1996 Search PubMed;
(b) H. Zhang, C. A. Jeffery and M. I. Jeffrey, Hydrometallurgy, 2012, 125–126, 69 CrossRef CAS PubMed.
-
(a) K. Huang, J. Guo and Z. Xu, J. Hazard. Mater., 2009, 164, 399 CrossRef CAS PubMed;
(b) J. Wu, J. Li and Z. Xu, Environ. Sci. Technol., 2008, 42, 5272 CrossRef CAS.
-
(a) H. Yang, J. Liu and J. Yang, J. Hazard. Mater., 2011, 187, 393 CrossRef CAS PubMed;
(b) A. Behnamfard, M. M. Salarirad and F. Veglio, Waste Manage., 2013, 2354 CrossRef CAS PubMed;
(c) A. Mecucci and K. Scott, J. Chem. Technol. Biotechnol., 2002, 77, 449 CrossRef CAS.
-
(a) W. H. Koppenol, Free Radicals Biol. Med., 1993, 15, 645 CrossRef CAS, and references cited therein;
(b) K. Barbusiński, Ecol. Chem. Eng. S, 2009, 16, 347 Search PubMed.
- O. Kuntyi, G. Zozulya, I. Saldan, V. Kree, S. Korniy and B. Stel'makhovych, Cent. Eur. J. Chem., 2011, 9, 180 CrossRef CAS PubMed.
Footnotes |
† Electronic supplementary information (ESI) available: Chemical–physical characterization of the test specimen; Comparison between the reactivity of the Me2dazdt·2I2 acetone solution and the I2/I− water solution towards gold See DOI: 10.1039/c4gc02237h |
‡ Current address: Dipartimento di Fisica, Università di Cagliari, I-09042 Monserrato, Cagliari, Italy. |
§ Cyanidation is based on the use of cyanide salts in basic media with their subsequent adsorption on activated carbon and reduction of the complex by electro-winning. |
¶ Aqua-regia, the well known 3 : 1 mixture of concentrated hydrochloric and nitric acids, is highly aggressive and produces toxic fumes e.g. NOx. |
|| The nature of the oxidizing species obtained in the Fenton reaction is still a subject of discussion. In fact, this reaction, which was observed by H. J. H. Fenton over 110 years ago, is still very difficult to describe and understand.26b |
** All standard reduction potentials (E°) and equilibrium constants (Kf and KSP) are given at 298 K. |
|
This journal is © The Royal Society of Chemistry 2015 |
Click here to see how this site uses Cookies. View our privacy policy here.