DOI:
10.1039/C4RA16082G
(Paper)
RSC Adv., 2015,
5, 16870-16877
Chemical vapor infiltration tailored hierarchical porous CNTs/C composite spheres fabricated by freeze casting and their adsorption properties
Received
10th December 2014
, Accepted 15th January 2015
First published on 20th January 2015
Abstract
Carbon nanotubes (CNTs) are one of the most promising candidates as adsorbents in many fields due to their unique structural characteristics. In this paper, hierarchical porous CNTs/carbon (CNTs/C) composite spheres were prepared and their strength and adsorption of vitamin B12 (VB12) were investigated. The initial porous CNT spheres were fabricated by freeze casting followed by freeze drying. Afterwards, the primary porous CNT spheres were further reinforced and tailored by chemical vapor infiltration (CVI) and steam activation. Consequently, the composite CNTs/C spheres with hierarchical porous structure and high strength were successfully fabricated. SEM and polarized light microscopy observations showed that, in addition to macro-sized radial through-pores in the spheres, many micro-sized pores were distributed uniformly in the wall of the radial tunnel-like through-pores. Mercury porosimetry and BET tests indicated that the width of the radial lamellar channels was about 5–15 μm, and the average diameter of the mesopores was about 3.8 nm. Adsorption of VB12 for these hierarchical porous CNTs/C spheres could reach 51.48 mg g−1, which is about 3.7 and 3.4 times those of traditional activated carbon beads and macroporous resin beads, respectively.
1. Introduction
Carbon nanotubes (CNTs) have aroused great enthusiasm and persistent exploration of applications in many fields over the past few years after they were discovered in 1991.1 Owing to their relatively high specific surface area and easily modified surface, CNTs have attracted researchers' interests as a promising new sorbent for heavy metals2–4 in wastewater treatment or for oil slick in rivers or seas.5,6 Particularly, based on their meso-porous structure in as-prepared or functionalized powdered CNTs, researchers have investigated their use for clearing middle molecular toxins in blood as a novel sorbent in hemoperfusion.7 Both powdered CNTs and CNTs/carbon composite beads exhibited better performance than traditional sorbents such as active carbon beads and macroporous resin beads.8,9
Evidently, powdered CNTs have many limitations in practical applications as sorbents, for example, it is difficult to separate and recycle them from mixtures, which probably might cause secondary pollution. Particularly, free CNTs must be strictly prohibited in hemoperfusion. Therefore, the biggest challenge for taking the advantage of CNTs as sorbents is to develop advanced technologies to fabricate CNT-based bulk materials. Accordingly, considerable attention has been paid to the research about syntheses of CNT bulk materials in different shapes such as CNT-fibers,10 CNT-foams11,12 and 3D-blocks.13,14 When compared with the aforementioned bulk materials, spherical shaped materials should be more competitive as sorbents or catalyst carriers due to their considerably lower packing density, higher surface area to volume ratio and smaller fluid resistance. Actually, Chao Ye et al. prepared CNTs/phenolic-resin-derived activated carbon beads by spheroidizing small grains of CNTs/phenolic resin in an autoclave and found that the adsorption of vitamin B12 (VB12, which was designated as the reference or representative of middle molecular toxins) for the composite beads with 22.5% CNTs was 2.3 times that of a commercial macroporous resin.8 Yuemei Lu et al. increased the ratio of CNTs from 22.5% to 45% in the composite carbon beads by reversed phase suspension polymerization and achieved a high adsorption of low density lipoprotein (LDL) up to 10.46 mg g−1.9 Furthermore, increasing the ratio of CNTs in the composite spheres could improve the adsorption capacity of the CNT-based sorbent, although it is a big challenge. In addition, another concern is that the adsorption capacity of the CNTs far beneath the surface of the composite beads was limited because they are deeply buried and the diffusing channels are limited because in the nearly solid beads, the passageway is mainly developed by steam activation. Undoubtedly, it is difficult to get enough access from the surface to inner core of the spheres.
Herein, the authors have proposed a novel strategy to synthesize CNTs/carbon (CNTs/C) composite spheres with high CNT ratio, hierarchical porous structure and high adsorption capacity by combining freezing casting, chemical vapor infiltration (CVI) technology and steam activation. Freezing casting is a segregation-induced templating of a second phase by solidifying the solvent, which involves preparing a stable suspension, pouring the suspension into a mould, freezing the suspension and then sublimating the solvent crystals.15–17 It is a promising technique to fabricate porous materials with complex pore structures and it has been widely explored in preparing porous ceramic18,19 and biological materials.20,21 In this work, freeze casting has been adopted to prepare primary CNT spheres with radially aligned channels from the core to the surface, and then the brittle pure CNT spheres were strengthened by the CVI process, during which pyrocarbon was produced to connect or “weld” the adjacent yet discrete CNTs to form integral CNTs/C spheres with high strength. Before the adsorption of VB12, steam activation was fulfilled to improve the hydrophilicity and further tailor the pore structure of the composite spheres.
2. Experimental
2.1 Materials
Multi-walled carbon nanotubes (MWCNTs, with a diameter of 10–20 nm and a length of 5–15 μm) were purchased from CNano Technology Ltd. and pre-treated with mixed acid (H2SO4
:
HNO3 = 3
:
1) in a reflux condenser for 30 min. Chitosan, which was used as the binder of the initial CNT spheres (degree of deacetylation = 80–95%), and VB12 were obtained from Sinopharm Chemical Reagent Beijing Co. Ltd. Acetic acid (A.R., Beijing Chemical Works) was used to dissolve chitosan. As the contrast, two types of typical commercial sorbents, activated carbon (AC) spheres and macroporous resin (MR) spheres were purchased from Aier Hemoperfutor Factory, PR China.
2.2 Preparation of CNTs/C composite spheres
The fabrication process included four steps (Fig. 1): (i) mixing the acid pretreated CNTs and chitosan (100
:
3 in weight ratio) and then dissolving them in 1% acetic acid solution, followed by magnetic stirring and further ultrasonic dispersing for 2 hours. (ii) Then, dripping the uniform suspension into liquid nitrogen dropwise with an injector. Note that the suspension drop immediately turned into solid beads during the quenching process, and after being freeze-dried for 24 h, porous but fragile CNT spheres with a little chitosan binder were obtained. (iii) Strengthening the weak spheres in a furnace by the CVI process. During this process, pyrocarbon deposited in the interstitial space in the CNTs once the mixed gas of C3H6 (1 m3 h−1) and N2 (1 m3 h−1) infiltrated into the beads at 940 °C. Moreover, although the initial sponge-like freeze-dried CNT spheres were reinforced and some macropores were modified by CVI, some of the nano-sized pores might be blocked slightly and they became a little hydrophobic after CVI; therefore, the following step was necessary. (iv) Activating the CVI reinforced CNTs/C spheres with steam (0.55 mL min−1) by peristaltic pump at 900 °C for different times. In this process, the pore structure was further tailored and hydrophilic hierarchical porous CNTs/C composite spheres were acquired.
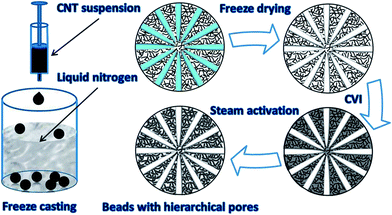 |
| Fig. 1 Schematic illustration of the fabrication process of hierarchical porous CNTs/C composite spheres. | |
2.3 Characterization
The morphology and microstructure of the samples were investigated with polarized light microscopy (PLM) and scanning electron microscopy (SEM) (MERLIN VP Compact, JSM-7001F). Macropores were measured by Mercury porosimetry (AUTO PORE IV 9520) and the pressure range varied between 3.31 × 10−3 and 4.14 × 102 MPa. The specific surface area, meso- and micro-pores were determined by nitrogen adsorption–desorption at 77 K (Quadrasorb SI-MP) after outgassing at 250 °C for 2 h. The BET equation was used to calculate the total specific surface area. The pore distribution and surface area of mesopores were calculated by the BJH method. The mechanical properties of the spheres were tested in a material testing instrument (Instron 4943) with a 10 N load cell.
The spheres with a uniform diameter of 2.5 mm were placed on the bottom stage, and then the top stage was driven down to compress the samples. The loading rate was 0.05 mm min−1.
2.4 Adsorption of VB12
The adsorption property of the CNTs/C hierarchical porous spheres was evaluated by investigating their adsorption of VB12, which is the representative of middle molecular toxins. Specifically, 15 mg of the CNTs/C spheres were added into 50 mL of VB12 solution (80 mg L−1) and the adsorption was carried out in the water bath (37 ± 1 °C) of a reciprocating shaker at the speed of 150 times per minute for 2 h. An aliquot of the solution was sampled periodically to detect the concentration variation of VB12 using a UV-Vis spectrophotometer at a wavelength of 361 ± 1 nm, and the adsorption capacities were calculated as follows:
where QA (mg g−1) was the adsorption capacity of VB12, C0 and Ct (mg L−1) were the concentration of VB12 before and after adsorption, respectively, and V (mL) is the volume of the solution and m (mg) is the weight of the spheres.
3. Results and discussion
3.1 Morphology and microstructure
It is well known that water turns into ice once the temperature drops below its freezing point. Generally, this process is rather slow in nature, whereas in this study when the suspension of CNTs was dripped into liquid nitrogen, the droplets would solidify in no time, and therefore they could maintain their spherical shape. After freeze drying, spongy CNT spheres with a diameter of 2.5–3 mm were obtained (Fig. 2a). Moreover, the diameter of the spheres could be adjusted by changing the syringe needles or changing the viscosity of the suspension. Although a little binder was added to prevent the spheres from collapsing after being freeze dried, the fluffy spheres were still quite fragile; therefore, CVI was introduced to reinforce the initial spheres because pyrocarbon would deposit preferentially in the interstitial space in the CNTs under negative pressure. As a result, the CNTs would be connected or “welded”. Note that the CVI time was controlled to prevent blockage of the pores. Actually, the surface of the spheres was full of holes after CVI (Fig. 2b and d) and the cross section showed a radial plate-like structure (Fig. 2c). Based on polarized light microscopy images (Fig. 2e), it could be discerned that the cross section was composed of radial laminar pores, which were developed directionally from the surface to the inner core. The wall thickness of the pores was about 1 μm and the width of the laminar pores was about 5–15 μm (inset of Fig. 2e). However, it must be pointed out that the alignment of laminar structure varied a little, particularly in the outer layer of the spheres, i.e., some zones were built with laminar pores perfectly parallel to each other (Fig. 2h), whereas others were composed of domains in which the orientation of the pore walls were different (Fig. 2f). Adjacent to the outer layer, laminar pores were well aligned radially from the center. This radial microstructure could have something to do with the ice crystal growth during solidification process, because the growth rate along different lattice planes was not equivalent (inset of Fig. 2g). This is discussed in the next section.
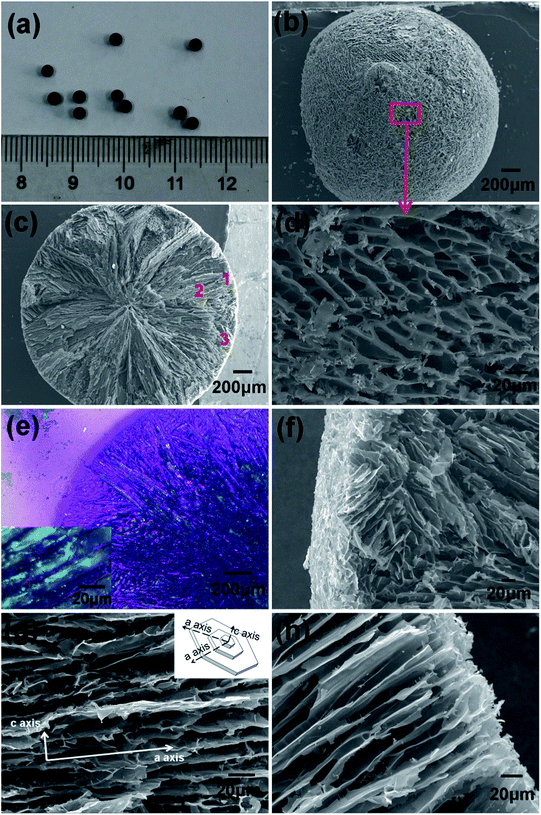 |
| Fig. 2 Optical image of CNTs/C composite spheres (a) and SEM images of the surface (b), cross section (c), magnified surface morphology (d); PLM image of the cross section (e); magnified image of the microstructure of framed area 1 (f); framed area 2 (g) and framed area 3 (h). (Note: inset in (e) is the magnified detailed view of laminar structure and that in (g) is the schematic crystal lattice of ice.) | |
Different from traditional activated carbon beads, in which mainly micropores were developed by activation in the surface layer and almost no passageway to the center existed, the CNTs/C spheres have lot of radial pores, which could play as the through channels for the diffusivity of solutions. In addition, abundant mesopores exist in the spheres, which are crucial for the adsorption of middle molecular matters. Generally, before the CVI process, the mesopores in the fluffy CNT spheres mainly resulted from the loose aggregation or stacking of CNTs in the walls of the tunnels (Fig. 3a),7 and they would be further quantified by N2 adsorption tests.
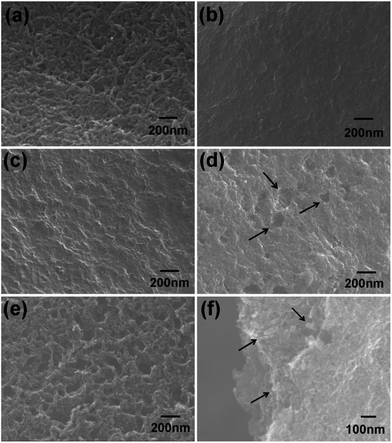 |
| Fig. 3 SEM images of the channel walls of the freeze-dried spheres (a), after CVI for 4 h (b), after being activated by steam for 30 min (c), for 45 min (d), for 60 min (e) and CNTs in fractured surface of the channel walls (f). | |
The hierarchical pore structure of the spheres could be favorable for adsorption; however, the maximum load of the sponge spheres was only 0.135 N. Basically, pyrocarbon is preferentially deposited in the nano-sized interstitial space between two carbon nanotubes. Hence, theoretically, an appropriate ratio of pyrocarbon could just connect adjacent CNTs to strengthen the fragile spheres yet it would not block the initial pores. After CVI for 4 h, the channel walls were coated homogeneously with pyrolytic carbon (Fig. 3b). Although the pyrocarbon film could significantly increase the strength of the spheres to 2.231 N, some of the meso- and micro-pores were blocked. Thus, further activation was necessary for recovering and tailoring the pore structure. 30 min of activation made the wall surface rough, (Fig. 3c) and afterwards some etched pits of about 50–100 nm in diameter were produced when extending the activation to 45 min (Fig. 3d). On further increasing the activation time to 60 min, more pits appeared and some were enlarged (Fig. 3e). In addition, CNTs were exposed again (Fig. 3e and f), and predictably the specific surface area and pore volume were greatly improved in the hierarchical porous CNTs/C spheres.
3.2 Pore structure evolution
Usually, the pore structure of traditionally activated carbon beads is developed mostly at the stage of activation. In contrast, the hierarchical porous structure of CNTs/C spheres was primarily determined by freeze casting, and then tailored further by CVI and steam activation, during which pore structure and strength were modified as required. Thus, a deep understanding of the pore structure evolution was favorable to take the full advantage of the adsorption capacity of CNTs to the greatest extent.
More specifically, at the initial stage of freeze casting, once the CNT suspension was dropped into the liquid nitrogen, the temperature of the thin surface layer instantly decreased to −196 °C and the temperature at the center remained at room temperature. This process could be simulated by finite element analyses (Fig. 4a), and then in less than 3 seconds, the outer layer was frozen (Fig. 4b). Because the degree of supercooling in the outer layer was considerably higher than that necessary for freezing water, a large amount of ice nuclei were simultaneously generated. Correspondingly, this homogeneous nucleation brought about a randomly aligned polycrystalline structure. Whenever the outer layer transformed into ice, the heat inside could only be conducted radially via ice and the temperature gradient decreased greatly. Then, the radial aligned temperature distribution could definitely lead to radial ice crystals.
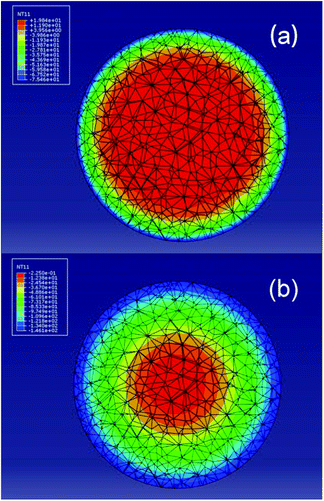 |
| Fig. 4 Finite element simulation diagram of the temperature distribution along the cross section after the suspension of CNTs being dropped in liquid nitrogen for 0.47 s (a) and 2.61 s (b). | |
There are 15 known crystalline phases of ice, and the hexagonal lattice shown in Fig. 2g is the most common structure. According to the research of Deville et al., the chemical potential of the ice crystal is different in different crystal planes. The facets parallel to the c axis have a higher chemical potential than the ones parallel to the a axis, and thus the ice growth rate along the a axis is 102 to 103 times faster than that along the c axis. Accordingly, when the temperature gradient was parallel to the a axis of the crystal, the crystal had kinetically favorable conditions to grow into a lamellar structure.22–25 Of course, between the thin outer layer of randomly aligned domains and the inner layer with a regular radial structure, there should be a transitional zone, which connects the two parts (Fig. 2e). After being freeze dried, the ice crystals sublimed, and the evolved pores were the exact mirror image of the ice crystals. Overall, the pore structure (Fig. 2) was fairly consistent with the abovementioned theoretical analyses.
To determine the size and distribution of the radial macro-channels, a mercury (Hg) intrusion method was adopted to analyze the CNTs/C spheres. The results in Fig. 5 indicate that the median pore diameter is 9.20 μm and most of the macro-pores have a diameter of 6–12 μm, which is quite consistent with the observations made by SEM and PLM (Fig. 2). Reasonably, the size, morphology and distribution of the macro-channels could be designed and fabricated under control and this interesting work is being carried on and would be discussed in the future.
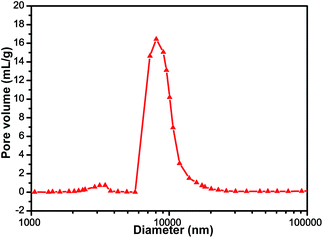 |
| Fig. 5 Macro-pore test of the freeze dried CNT spheres by mercury porosimetry. | |
As absorbents for middle molecular matter, mesopores that were rare in traditional activated carbon beads were indispensible. In this work, the initial mesopores among intertwined CNTs might be slightly blocked during the CVI process, and then in the following activation process, the pore structure could be tailored and developed further. The pore structure evolution was monitored by BET tests (Fig. 6, Table 1).
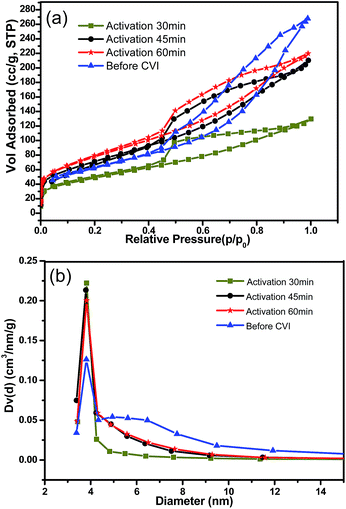 |
| Fig. 6 Pore structure character analyzed by N2 adsorption–desorption isotherms (a) and pore size distribution of the porous spheres (b). | |
Table 1 Pore diameters, volumes and BET specific surface areas of CNTs/C spheres, AC and MR beads
Samples |
Average pore diameter (nm) |
Mesopore volume (cm3 g−1) |
Total pore volume (cm3 g−1) |
Mesopore specific surface area (m2 g−1) |
Total BET surface area (m2 g−1) |
Original CNT spheres |
3.781 |
0.217 |
0.255 |
193.747 |
218 |
Activated CNTs/C (30) |
3.820 |
0.133 |
0.153 |
115.629 |
174 |
Activated CNTs/C (45) |
3.791 |
0.240 |
0.297 |
188.973 |
257 |
Activated CNTs/C (60) |
3.820 |
0.253 |
0.287 |
195.774 |
280 |
AC beads |
1.418 |
0.255 |
0.557 |
63.620 |
810 |
MR beads |
1.439 |
0.241 |
0.702 |
119.78 |
961 |
It should be noted that, as shown in Fig. 6a, the N2 adsorption–desorption isotherm of the freeze dried spheres have the typical character of type IV curves, which is in accordance with the mesoporous structure of loosely stacking CNTs.7 Although CVI reinforced the fragile freeze dried spheres, it might also cause the blockage of some of the meso- and micro-pores, whereas after further activation by steam, the filmy pyrocarbon was etched away and some micropores may have developed into mesopores. Therefore, the total pore volume would be increased with the extension of the activation time (Fig. 6a). After being activated for 60 min, the pore volume and specific surface area of the sample were higher than that of the initial freeze dried CNT spheres. In contrast, the total BET specific surface area and total volume were considerably higher for AC beads and MR beads, but the mesopore volumes of these two were approximately equal to that of the activated CNTs/C spheres. Nevertheless, the average pore diameters of the AC beads and MR beads were only about 1.4 nm, which was considerably lower than that of the CNTs/C spheres. In addition, it should be expectable that a higher proportion of mesopores could be acquired by modifying the ratio of pyrocarbon to CNTs and controlling the degree of steam activation process in the following work. For adsorbents, in addition to pore volume, pore size and distribution were the other key factors as well. It was interesting that the pore size distribution of both the original spheres and the activated ones were quite similar (Fig. 6b). The average pore diameters of all the samples were almost equal to 3.8 nm. Probably, the unchanged average pore size might be ascribed to the possibility that the mesopores in the stacked CNTs were kept all the way even though the pore evolution in the fabrication process was complicated.
3.3 VB12 adsorption
As the representative of middle molecular toxins in hemoperfusion, VB12 was adopted to evaluate the adsorption capacity of new adsorbents. Currently, AC beads and MR beads have been applied in hemoperfusion for years. The adsorption of VB12 in 2 h at 37 °C for AC beads is 13.98 mg g−1 and that for MR beads is 15.25 mg g−1, which are a little higher than that for CNTs/C spheres activated for 30 min. With the increase of activation time, the adsorption capacity of CNTs/C spheres was greatly improved. The sample activated for 60 min had an adsorption of 51.48 mg g−1, which is 3.68 times greater than that of AC beads and 3.38 times greater than that of MR beads (Fig. 7a). Moreover, adsorption rate of CNTs/C spheres was considerably higher than that of AC beads and MR beads (Fig. 7b).
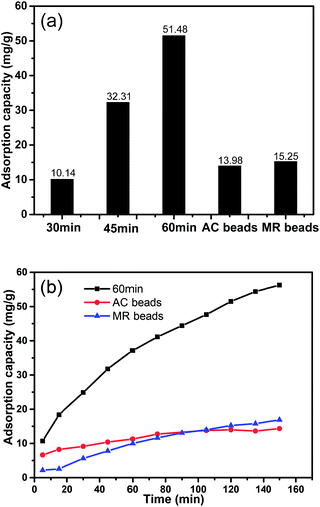 |
| Fig. 7 Adsorption capacity in 2 h (a) and adsorption rate (b) for VB12 by CNTs/C spheres, AC beads and MR beads. | |
Though the functional groups should be similar for CNTs/C spheres and AC beads due to the similar steam activation process, their pore structures were quite different from each other. Mesopores with a diameter of more than 2 nm might be one of the prerequisites for adsorbing VB12 when the size of VB12 is about 2.09 nm. Although the total pore volume and total BET specific surface area of AC beads and MR beads are rather higher than those of CNTs/C spheres, mesopore volumes of the two control samples were nearly equal to that of activated CNTs/C spheres. Therefore it should be reasonable to deduce that it was not the mesopores, but the micropores in AC beads and macropores in MR beads that contribute to the relatively high values of total pore volumes and total specific surface areas. Moreover, unfavorably, most of the pore diameters in AC beads and MR beads are lower than that of VB12.
Therefore, in addition to the advantages in mesopore diameter, mesopore volume and mesopore specific surface area for CNTs/C spheres listed in Table 1, the highly developed radial aligned macro-channels could also play another key role as the diffusing pathway for VB12 solution. In this case, VB12 could diffuse freely into the inner part of the spheres and accordingly, even CNTs in the inner zone could adsorb VB12. So most CNTs in the spheres could be taken fully utilized. In addition, the mesopores built within the walls of radial channels could accelerate the adsorption rate. Therefore, these hierarchical porous CNTs/C spheres could be a potential candidate in hemoperfusion or other related fields.
3.4 Mechanical properties
The initially freeze dried green CNT spheres were rather brittle and they tended to fall apart during the adsorption tests in the shaker due to the weak connection among CNTs. Evidently, the green CNT spheres were not suitable to be directly used as adsorbents for they might bring about secondary pollution. After CVI for 4 h, the mass gained was 45.63% and the breakage force of the CNTs/C spheres was greatly improved from 0.135 N for the green CNT spheres to 2.231 N. The maximum breakage load was 15.53 times higher than that of the green CNT spheres (Fig. 8). Inevitably, some micro- and meso-pores might be slightly blocked and that would be unfavorable for adsorption. To compromise this contradiction, steam activation should be used to acquire an optimal combination of strength and adsorption capacity.
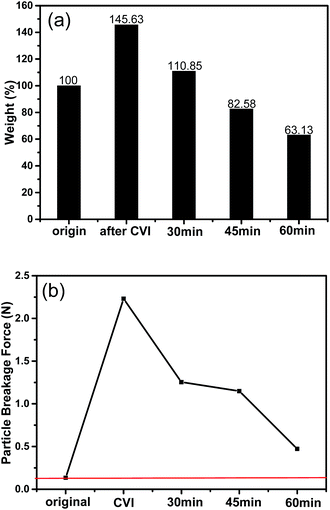 |
| Fig. 8 The mass variation of the spheres after CVI and being activated for different times (a) and breakage forces of the corresponding spheres (b). (Note: the mass of the initial CNT spheres were recorded as 100%, 30 min meant being activated for 30 min and so on.) | |
From Fig. 8a it could be figured out that after CVI, the mass gain is 45.63%, which indicates that the mass ratio of CNTs and pyrocarbon is about 2
:
1. During activation, the burn-offs become larger with increasing time, and the mass of the 30 min activated samples was still 10.85% higher than the green CNT spheres. However, it was difficult to discern whether the pyrocarbon or CNTs, or both are responsible for the mass loss. Nevertheless, after being activated for 45 min or more, the mass was lower than the initial spheres. Fortunately, the breakage forces were still considerably higher than those of the initial spheres (Fig. 8b), even for the 60 min activated ones, which underwent about 37% mass loss compared with the initial ones. This indicated that both CNTs and pyrocarbon would be etched if they are activated for certain time duration. Because the breakage force of the 45 min activated sample (1.148 N) was only a little lower than that of the 30 min activated one (1.254 N), the adsorption capacity of the former was 3.2 times that of the latter, and thus, probably, 45 min activation might be applicable.
4. Conclusion
In this work, CNTs/C composite spheres with special hierarchical porous structures were prepared successfully and in a novel way. The radial laminar channels from the center to the surface, which could act as the pathway for the solution diffusivity, were formed during a freeze casting process. The mesopores in the channel walls were tailored by subsequent CVI and steam activation processes. The width of the lamellar channels was about 5–15 μm and the average diameter of the mesopores was about 3.8 nm. In addition, the breakage load for the primary CNT spheres could be improved from 0.135 N to 2.231 N after the CVI reinforcing process, although it might decrease a little after activation. As a promising adsorbent, the adsorption capacity of the CNTs/C composite spheres for VB12 was about 51.48 mg g−1, which was 3.7 and 3.4 times greater than those of traditional AC beads and MR beads. Moreover, the adsorption rate was also higher than the other two reference samples. The excellent adsorption properties could be attributed to the hierarchical porous structure of the composite spheres. Furthermore, microstructure and finite element analyses indicated that the pore structure could be designed and modified in a more accurate way by controlling the suspension concentration, freeze casting, CVI duration and activation process and this requires further study.
Acknowledgements
The authors would like to thank Prof. Haiyan Zhao and Prof. Zhipeng Cai in Tsinghua University for their help in finite element analyses.
References
- S. Iijima, Helical microtubules of graphitic carbon, Nature, 1991, 354(6348), 56–58 CrossRef CAS.
- X. Peng, Z. Luan, Z. Di, Z. Zhang and C. Zhu, Carbon nanotubes-iron oxides magnetic composites as adsorbent for removal of Pb(II) and Cu(II) from water, Carbon, 2004, 43(4), 880–883 CrossRef PubMed.
- M. I. Kandaha and J.-L. Meunier, Removal of nickel ions from water by multi-walled carbon nanotubes, J. Hazard. Mater., 2007, 146(1–2), 283–288 CrossRef PubMed.
- S. S. Bayazita and I. Incib, Adsorption of Pb(II) ions from aqueous solutions by carbon nanotubes oxidized different methods, J. Ind. Eng. Chem., 2013, 19(6), 2064–2071 CrossRef PubMed.
- D. P. Hashim, N. T. Narayanan, J. M. Romo-Herrera, D. A. Cullen, M. G. Hahm, P. Lezzi, J. R. Suttle, D. Kelkhoff, E. Munoz-Sandoval, S. Ganguli, A. K. Roy, D. J. Smith, R. Vajtai, B. G. Sumpter, V. Meunier, H. Terrones, M. Terrones and P. M. Ajayan, Covalently bonded three-dimensional carbon nanotube solids via boron induced nanojunctions, Nature, 2012, 2(363), 1–8 Search PubMed.
- X. Gui, Z. Zeng, Z. Lin, Q. Gan, R. Xiang, Y. Zhu, A. Cao and Z. Tang, Magnetic and Highly Recyclable Macroporous Carbon Nanotubes for Spilled Oil Sorption and Separation, ACS Appl. Mater. Interfaces, 2013, 5(12), 5845–5850 CAS.
- C. Ye, Q.-M. Gong, F.-P. Lu and J. Liang, Adsorption of uraemic toxins on carbon nanotubes, Sep. Purif. Technol., 2007, 58(1), 2–6 CrossRef CAS PubMed.
- C. Ye, Q.-M. Gong, F.-P. Lub and J. Liang, Preparation of carbon nanotubes/phenolic-resin-derived activated carbon spheres for the removal of middle molecular weight toxins, Sep. Purif. Technol., 2008, 61(1), 9–14 CrossRef CAS PubMed.
- Y. Lu, Q. Gong, F. Lu and J. Liang, Preparation of sulfonated porous carbon nanotubes/activated carbon composite beads and their adsorption of low density lipoprotein, separation and purification technology, J. Mater. Sci.: Mater. Med., 2011, 22(8), 1855–1862 CrossRef CAS PubMed.
- M. Zhang, K. R. Atkinson and R. H. Baughman, Multifunctional Carbon Nanotube Yarns by Downsizing an Ancient Technology, Science, 2004, 306(5700), 1358–1361 CrossRef CAS PubMed.
- M. Zhang, S. Fang, A. A. Zakhidov, S. B. Lee, A. E. Aliev, C. D. Williams, K. R. Atkinson and R. H. Baughman, Strong, Transparent, Multifunctional, Carbon Nanotube Sheets, Science, 2005, 309(5738), 1215–1219 CrossRef CAS PubMed.
- R. K. Das, B. Liu, J. R. Reynolds and A. G. Rinzler, Engineered Macroporosity in Single-Wall Carbon Nanotube Films, Nano Lett., 2009, 9(2), 677–683 CrossRef CAS PubMed.
- J. Zou, J. Liu, A. S. Karakoti, A. Kumar, D. Joung, Q. Li, S. I. Khondaker, S. Seal and L. Zhai, Ultralight Multiwalled Carbon Nanotube Aerogel, ACS Nano, 2010, 4(12), 7293–7301 CrossRef CAS PubMed.
- X. Gui, J. Wei, K. Wang, A. Cao, H. Zhu, Y. Jia, Q. Shu and D. Wu, Carbon Nanotube Sponges, Adv. Mater., 2010, 22(5), 617–621 CrossRef CAS PubMed.
- S. Deville, Ice templating, freeze casting: beyond materials processing, J. Mater. Res., 2013, 28(17), 2202–2219 CrossRef CAS.
- E. Munch, J. Franco, S. Deville, P. Hunger, E. Saiz and A. P. Tomsia, Porous Ceramic Scaffolds with Complex Architectures, JOM, 2008, 60(6), 54–58 CrossRef CAS PubMed.
- S. Deville, E. Saiz and A. P. Tomsia, Ice-templated porous alumina structures, Acta Mater., 2007, 55(6), 1965–1974 CrossRef CAS PubMed.
- F. Bouville, E. Maire and S. Deville, Lightweight and stiff cellular ceramic structures by ice templating, J. Mater. Res., 2013, 29(2), 175–181 CrossRef.
- M.-H. Ho, P.-Y. Kuo, H.-J. Hsieh, T.-Y. Hsien, L.-T. Hou, J.-Y. Laid and Da-M. Wang, Preparation of porous scaffolds by using freeze-extraction and freeze-gelation methods, Biomaterials, 2004, 25(1), 129–138 CrossRef CAS.
- U. Soltmanna, H. Böttcher, D. Koch and G. Grathwohl, Freeze gelation: a new option for the production of biological ceramic composites (biocers), Mater. Lett., 2003, 57(19), 2861–2865 CrossRef.
- K. M. Pawelec, A. Husmann, S. M. Best and R. E. Cameron, A design protocol for tailoring ice-templated scaffold structure, J. R. Soc., Interface, 2014, 11(92), 1–9 CrossRef PubMed.
- W. L. Li, K. Lu and J. Y. Walz, Freeze casting of porous materials: review of critical factors in microstructure evolution, Int. Mater. Rev., 2012, 57(1), 37–60 CrossRef CAS PubMed.
- S. Deville, Freeze-Casting of Porous Ceramics: A Review of Current Achievements and Issues, Adv. Eng. Mater., 2008, 10(3), 155–169 CrossRef CAS.
- S. Deville, E. Maire, A. Lasalle, A. Bogner, C. Gauthier, J. Leloup and C. Guizard, In Situ X-Ray Radiography and Tomography Observations of the Solidification of Aqueous Alumina Particle Suspensions—Part I: Initial Instants, J. Am. Ceram. Soc., 2009, 92(11), 2489–2496 CrossRef CAS PubMed.
- S. Deville, E. Maire, A. Lasalle, A. Bogner, C. Gauthier, J. Leloup and C. Guizard, In Situ X-Ray Radiography and Tomography Observations of the Solidification of Aqueous Alumina Particle Suspensions—Part II: Initial Instants, J. Am. Ceram. Soc., 2009, 92(11), 2497–2503 CrossRef CAS PubMed.
|
This journal is © The Royal Society of Chemistry 2015 |
Click here to see how this site uses Cookies. View our privacy policy here.