Electrochemical silver dissolution and recovery as a potential method to disinfect drinking water for underprivileged societies
Received
24th November 2015
, Accepted 23rd December 2015
First published on 23rd December 2015
Abstract
Limited access to disinfected drinking water is a critical challenge in developing countries. Ionic silver has biocidal capabilities and silver ionization is an established method for cooling water disinfection. However, silver ionization cannot be used in drinking water treatment because of its inherent human health risks. In this proof-of-concept study, a laboratory scale electrochemical reactor was developed where ionic silver is released via oxidation of metallic silver and subsequently recovered through cathodic reduction. Complete inactivation of Escherichia coli was demonstrated in 30 min at an application of 1.2 V. A high silver concentration (>1 mg L−1) was achieved in less than two minutes of water residence time within the disinfection reactor. The effluent silver concentration was linearly proportional to the electric current, allowing reliable estimation of silver concentration and corresponding disinfection performance by measuring electric current using an electrical multimeter. The disinfected water was further treated in a separate silver recovery cell. The silver concentration dropped down to safe levels for continued human consumption (0.1 mg L−1) via spontaneous cathodic silver reduction coupled with anodic oxidation of metallic aluminum. The estimated energy requirement was 6.1 kJ to treat 1 m3 of water; thus, solar panels or bicycle generators can provide sufficient energy for disinfection. The electrochemical disinfection and subsequent silver recovery methods have a strong potential as a prospective method to supply safe drinking water in underprivileged and remote societies.
Water impact
Rapid inactivation of E. coli was demonstrated in electrochemical disinfection. Residual silver concentration was effectively reduced to the safe level for human consumption in a separate experiment. A bicycle generator or photovoltaic solar panel can provide energy for water disinfection. The findings support that the disinfection method has a potential to provide safe drinking water to people in underprivileged communities.
|
1. Introduction
Limited access to safe drinking water is a serious and constant challenge in underdeveloped and remote societies.1–3 Water-related diseases from contaminated drinking water, hygiene, and sanitation have caused an estimated 3.6 million deaths per annum.4 Water treatment using various disinfection methods, such as chlorination, ozonation, and ultraviolet (UV) light radiation, can effectively inactivate microorganisms including human pathogens; however, people in underprivileged societies cannot afford sufficient energy or infrastructure to produce the disinfection chemicals and operate the reactors for drinking water treatment.5 Thus, the main goal of this study was to develop an affordable disinfection method for people in underprivileged societies.
Silver was used for water disinfection and antimicrobial therapy in ancient civilizations and the biocidal capacity of ionic silver has been demonstrated in a number of modern scientific studies.6–11 Silver ionization, which has a strong biocidal capacity, has been used to control Legionella pathogens in cooling water systems and hosipitals.12–14 However, silver applications in drinking water treatment have been limited by the potential health risks of continued silver consumption and the high cost of silver. Silver concentrations should be 0.1 mg L−1 or lower for continued human consumption to avoid potential adverse health risks.15,16 However, a silver concentration at 0.1 mg L−1 or lower can substantially decrease the disinfection efficiency,17 indicating that silver concentration should be sufficiently high (e.g., 1 mg L−1 or higher) for reliable and rapid inactivation of microorganisms. In addition, the high concentration needed for effective disinfection requires a large amount of silver, making the method expensive and economically unfeasible. Applications of nano-sized silver particles have been extensively investigated as an alternative method for water disinfection and treatment.10,11,18,19 Such nano-sized particles dramatically increase the effective surface area, and thus improve the biocidal capacity of silver. However, nano-sized silver particles can cause potential human health risks and they can accumulate in organisms along the food chain if they are released in natural water systems.20–22 Thus, this study focused on using millimetre sized silver granules as the source of silver ions for water disinfection.
Here we have suggested and examined an innovative disinfection method where silver ions are released and simultaneously recovered via two electrode reactions (Fig. 1A): one discharges silver ions into the solution through the oxidation of metallic silver at the anode (forward reaction of eqn (1)) whereas the other retrieves the dissolved silver by a reduction reaction at the cathode (reverse reaction of eqn (1)). It should be emphasized that during conventional silver ionization, silver ions are dispersed into untreated water with no means of recovery. The cathodic reduction reaction differentiates this system from typical silver ionization techniques.
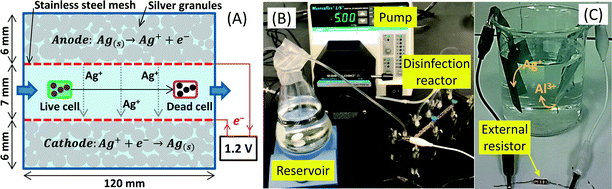 |
| Fig. 1 (A) Reactions expected in the electrochemical disinfection reactor. (B) Experimental setup for the disinfection experiment. (C) Silver recovery cell using aluminum foil. | |
As silver ions travel from the anode to the cathode, the space between the two electrodes becomes an active disinfection zone where microorganisms are inactivated. Because the silver ions are recovered at the cathode as metallic silver, the disinfected water has a low silver concentration. In addition, the residual silver ions in the disinfected water can be further recovered by coupling the silver reduction reaction (reverse reaction of eqn (1)) with an aluminum oxidation reaction (forward reaction of eqn (2)), allowing safe human consumption of the treated water.
Aluminum is a commonly used chemical in drinking water treatment for flocculation of suspended particles in water and excessive Al3+ will be naturally removed by aluminum hydroxide precipitation.23 Also, the electric energy requirement is expected to be low because the first redox couple (forward and backward reactions of eqn (1)) is thermodynamically neutral and the second set of the redox reactions (backward reaction of eqn (1) and forward reaction of eqn (2)) is driven spontaneously.24 Compared to currently available disinfection methods (e.g., chlorination, ozonation, and UV radiation), this electrochemical silver disinfection method is expected to require an almost negligible amount of electric energy for microbial inactivation. Thus, a large amount of water can be treated using photovoltaic solar panels or bicycle generators, providing safe drinking water to people in underprivileged societies. The specific objectives of this study are to: (1) demonstrate effective microbial inactivation using the electrochemical silver disinfection method; (2) establish a correlation between the electric current and resulting silver concentration for the estimation of disinfection performance; (3) demonstrate further recovery of silver from the treated water using the second set of electrode reactions; and (4) quantify the energy requirement for this disinfection method.
2. Experimental methods
2.1 Electrochemical disinfection reactor
The disinfection reactor was constructed using three thin low-density poly(ethylene) blocks covered with poly(acrylic) plates (McMaster-Carr, NJ, USA). Each block was drilled to make a narrow inner chamber (length 12 cm, width 0.8 cm). The middle chamber (0.7 cm thick) was used for water flow and the upper and lower chambers (0.6 cm thick) were filled with silver casting grain granules (99.9% purity, granule size between 1.6 and 6.4 mm, Alfa Aesar, MA, USA) to be used as the anode and cathode (Fig. 1A). Approximately 34.2 g of the silver granules were sandwiched between a poly(acrylic) end plate and a piece of stainless steel mesh (SS-306, 200 × 200 mesh, McMaster-Carr, NJ, USA). The upper layer of the silver granules was used as the anode and the lower layer was the cathode. The silver granules were tightly sandwiched so that the whole layer behaved as an electrical continuum and the stainless steel mesh was used as the current collector. In a separate experiment, corrosion of the stainless steel mesh was not observed (1.2 V application for 24 h). The effective reactor volume was approximately 11.2 mL whereas the empty volume was 17.7 mL without the silver granules.
2.2
Escherichia coli preparation
Escherichia coli RS2g was used to examine the disinfection capacity. The microbial strain was enriched in a nutrient broth at 37 °C to an approximate concentration of 108 colony forming units (CFU) mL−1. The nutrient broth was prepared with 10 g HiVeg lysate, 5 g yeast extract, 10 g sodium chloride, 10 mg rifampicin, and 100 mg kanamycin in 1 L of deionized water.25 The bacterial cells were separated from the nutrient solution in a centrifuge at 8500 rpm for 10 min (Allegra 25R, Beckman Coulter Life Sciences, Germany). The centrifuged cells were then suspended in autoclaved 1 mM phosphate buffer solution (0.15 mM monopotassium phosphate and 0.85 mM disodium phosphate). These centrifugation and suspension steps were repeated twice for further removal of nutrients. The suspended solution was diluted to ~105 CFU mL−1 using 1 mM phosphate buffer solution before it was used in the silver disinfection experiment.
2.3 Reactor operation for disinfection test
Prior to the disinfection test, 70% (v/v) ethyl alcohol was pumped at 5 mL min−1 (Masterflex L/S pump, Cole-Parmer Instrument Company, IL, USA) through the reactor for 20 min to control microbial contamination.26 The ethyl alcohol was then replaced by deionized water which was pumped for another 30 min to remove residual ethanol from the reactor. After this cleaning process, the reactor was emptied and the prepared E. coli solution (~105 CFU mL−1) was pumped at 5 mL min−1 for 15 min and the effluent was discarded. This rinsing step with the E. coli solution is necessary to minimize the bacterial loss by adsorption on the silver granules and reactor surfaces during the disinfection experiment. The main part of the disinfection experiment was performed for 30 min by circulating 200 mL of the E. coli solution between a reservoir and the disinfection reactor at 5 mL min−1 (Fig. 1B). The reservoir was gently stirred using a magnetic stirrer.
During the disinfection experiment, two different voltage conditions (0.6 and 1.2 V) were applied and the resulting electric current was recorded every 30 s using potentiostat (MGP-2, Bio-Logic, France). In addition to the two applied voltage conditions, two control experiments were conducted. In one control test, the E. coli solution was circulated between the reservoir and reactor without any voltage applications (Open circuit). In the other control experiment, the E. coli solution was kept in the reservoir without the circulation (No silver). All experiments were conducted in an air-conditioned laboratory at 22.1 ± 0.7 °C.
2.4 Plate counting
Agar plates were prepared with 15 g agar, 5 g yeast extract, 10 mg rifampicin, 100 mg kanamycin, 10 g HiVeg lysate, and 10 g sodium chloride in 1 L of deionized water.25 The added antibiotics (rifampicin and kanamycin) are necessary to selectively culture E. coli RS2g.
During the silver disinfection experiment, a sample (0.2 mL) was taken from the reservoir at 0, 10, 20, and 30 min. The sample was serially diluted depending on the expected amount of viable cells. For example, samples at 0 min were diluted by a factor of 10 and 100, whereas samples at 30 min with 1.2 V application were not diluted. The diluted or undiluted samples (0.1 mL) were seeded on the agar plates and the seeded plates were incubated at 37 °C for 24 h.
2.5 Reactor operation for current–silver correlation
The continuous flow experiment was conducted using 1 mM phosphate buffer solution without the E. coli strain to correlate the electric current and concentration of ionic silver present in the effluent from the electrochemical disinfection reactor. The applied voltage was increased stepwise every 22 min from the open circuit, to 0.3, 0.6, 0.9 and 1.2 V, while 1 mM phosphate buffer solution was continuously pumped through the electrochemical disinfection reactor at 5 mL min−1 (no recirculation). At the end of each applied voltage condition, the effluent was collected and acidified using nitric acid (1% v/v) and was then analyzed for silver using inductive coupled plasma-optical emission spectrometry (ICP-OES) (VistaPRO, Varian Inc., Australia). The pH and conductivity of the effluent samples were also determined (SevenMulti, Mettler Toledo Group, Switzerland). There were no discernable changes in pH and conductivity from the influent and the pH ranged from 7.2 and 7.4 and the conductivity was also stationary between 222 and 237 μS cm−1.
In a separate continuous flow operation, samples in the water flow chamber of the reactor were taken through predrilled holes located at 3, 6, and 9 cm from the inlet point. These samples were acidified and analyzed with ICP-OES to determine the silver concentration in the reactor.
2.6 Silver recovery test using aluminum foil
The silver recovery cell was prepared using a glass beaker with a 5 × 4 cm2 piece of household aluminum foil as the anode and a 5 × 4 cm2 piece of stainless steel mesh (SS-306, 200 × 200 mesh, McMaster-Carr, USA) as the cathode (Fig. 1C). The prepared electrodes were located a few centimeters from each other in the silver recovery cell without mixing conditions. The two electrodes were connected externally through a resistor (1000, 4700, or 9700 Ω). The potential drop across the external resistor was monitored every 30 s using a MGP-2 potentiostat (BioLogic, France) to determine the electric current generated in the silver recovery cell using Ohm's law. The silver recovery cell was filled with 200 mL of silver solution. The silver solution was collected from the electrochemical silver reactor (applied voltage = 1.2 V; flow rate = 5 mL min−1) and stored in a glass container for 16 h prior to the silver recovery experiment. During the silver recovery experiment, a 4 mL sample was taken every 3 h for the first 12 h and then another sample was collected at 24 h. The samples were acidified and the silver concentration was determined using ICP-OES (VistaPRO, Varian Inc., Australia).
2.7 Silver recovery efficiency
Coulombic efficiency is the charge-based ratio between the amount of silver recovered and the total charge transferred via the electrode reactions in the silver recovery cell: | 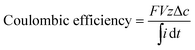 | (3) |
where, F is the Faraday constant, V is the volume of solution (0.2 L), z is the charge of ionic silver (+1), Δc is the change in ionic silver concentration during the silver recovery test (mol L−1), and i is the electric current (A).
3. Results and discussion
3. 1. Disinfection effectiveness
E. coli RS2g was successfully inactivated in the electrochemical system and the disinfection performance was substantially enhanced with an applied voltage. When 1.2 V was applied, viable E. coli colonies were not detected after 30 min, indicating complete inactivation of the microorganism (Table 1). When the applied voltage was decreased to 0.6 V, the electrochemical disinfection system showed 99.6% and 99.8% removal after the 30 min treatment (Table 1). For the open circuit condition (no electric current), a partial inactivation of E. coli was demonstrated with an observed 60.3% and 79.5% removal in 30 min (Table 1). This partial removal without electric current can be explained by the silver ions becoming dissolved via non-electrode reactions because no distinct decreases in CFU were observed during the no-silver control experiment (Table 1). It should be noted that the total surface area of the silver granules was substantially large (~63 cm2), allowing active silver dissolution via non-electrode reactions.
Table 1 Amount of viable E. coli cells (mean ± standard deviation (SD) in CFU mL−1) during electrochemical disinfection. (Water volume = 200 mL; recirculation flow rate = 5 mL min−1; 22 °C; duplicated experiments performed independently; N = 2)
|
1.2 V application |
0.6 V application |
Open circuit |
No silver |
No detection of viable colonies.
|
0 min |
441 500 ± 330 219 |
149 000 ± 41 012 |
253 100 ± 247 346 |
344 000 ± 5657 |
10 min |
6685 ± 1393 |
16 780 ± 4455 |
323 050 ± 419 951 |
386 500 ± 251 023 |
20 min |
170 ± 226 |
13 295 ± 9355 |
303 200 ± 309 430 |
302 000 ± 65 054 |
30 min |
0a |
390 ± 127 |
93 000 ± 108 894 |
505 500 ± 65 761 |
3.2 Ionic silver concentration
Ionic silver (Ag+) released from the electrode reactions was the active disinfectant in the electrochemical system. In the abiotic experiment under continuous flow conditions, the silver concentration from the reactor increased as the applied voltage increased (Fig. 2A). The open circuit condition resulted in 0.15 mg L−1 of silver in the effluent, indicating that the silver granules naturally dissolved to give silver when there are no reactions at the electrode, which explains the partial inactivation of the bacteria under open circuit conditions (Table 1). There was no statistically significant change in the effluent silver concentration for the increased applied voltage up to 0.6 V (Fig. 2A). The relatively low silver concentration (0.2 mg L−1) at the 0.6 V application explains the incomplete disinfection capacity (99.6% and 99.8%). It should be noted that the drinking water treatment regulations in developed countries commonly require at least log 3 removal of bacteria (i.e., 99.9% inactivation), therefore, the 0.6 V application does not provide adequate removal of bacteria for drinking water standards.27 When the applied voltage was increased above 0.6 V to 1.2 V, the silver concentration in the effluent increased sharply to 1.15 mg L−1 (Fig. 2A). As a result, the 1.2 V application achieved the complete inactivation of the E. coli strain in 30 min (Table 1). The comparison between the inactivation results (Table 1) and silver concentration (Fig. 2A) indicates that the silver concentration should be 1 mg L−1 or higher for the effective disinfection of E. coli (i.e., log 3 or higher removal in 30 min). When the silver concentration at 1.2 V application (1.15 mg L−1) is normalized by the total surface area of the silver granules, 0.012 mg L−1 of Ag+ was produced per cm2 of the silver granule surface (average silver granule diameter = 4 mm; total mass of silver granules in the reactor = 68.4 g; metallic silver density = 10.49 g cm−3).
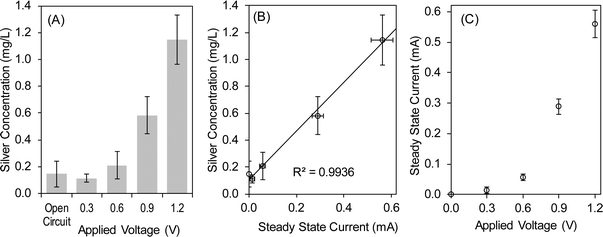 |
| Fig. 2 (A) Effluent silver concentration from the electrochemical disinfection reactor. (B) Linear correlation between the electric current and silver concentration. (C) Correlation between the electric current and applied voltage. (The steady-state current was obtained by averaging measured current values over the last 10 min of 22 min continuous flow operation.) (Error bar = 2 × SD; N = 3). | |
The silver concentration in the effluent was linearly proportional to the electric current (Fig. 2B). This clear linear trend indicates that the effluent silver concentration can be estimated by measuring the electric current in the electrochemical disinfection reactor. Measurement of the silver concentration needs expensive analytical instruments (e.g., ICP, atomic adsorption, or photocolorimetry) and various chemicals for sample preparation, making it practically impossible to measure the silver concentration in water used by underprivileged communities.28 However, the silver concentration needs to be determined to estimate the disinfection efficiency in the Chick–Watson model:23
|  | (4) |
where,
X is the viable microbial population,
k is the rate constant for disinfection,
c is the disinfectant concentration, and
n is the coefficient of dilution. The linear trend between the silver concentration and electric current will allow the reliable estimation of the silver concentration and the resulting disinfection effectiveness by measuring the current using an electric multimeter.
If the applied potential exceeds 1.23 V, the water electrolysis reactions start contributing to the electric current and result in an overestimation of silver concentration as well as disinfection effectiveness. Therefore, it is recommended that the electrochemical silver reactor be operated below the threshold voltage for water electrolysis (1.23 V).
3.3 Energy losses
The electric current in the silver reactor showed an exponential increase with the increase of applied voltage (Fig. 2C). In an electrolytic cell, the applied voltage is equal to the sum of the equilibrium potential, overpotential loss, and resistive potential loss. For the highest voltage application of 1.2 V, the ohmic resistance accounted for ~0.17 V of the energy loss (inter-electrode distance = 0.7 cm; solution conductivity = 230 μS cm−1; I = 0.56 mA; cross sectional area = 9.6 cm2). This estimation indicates that the majority of the applied voltage was consumed for the electrode overpotential and ohmic losses. The electrode overpotential loss can be reduced by increasing the surface area of the electrode. Although relatively coarse silver granules (1.6–6.4 mm in diameter) were used in this study, finer granules or other types of silver materials can be used to increase the electrode surface area.
The overall electrode reaction is thermodynamically neutral, that is, metallic silver at the anode is oxidized to ionic silver, which is then reduced to metallic silver at the cathode. Therefore, the equilibrium potential loss was created solely by the difference in ionic silver concentration between the anode and cathode surfaces, thus, this loss can be denoted as the concentration overpotential loss. The local concentration of ionic silver at the anode surface is higher than that at the cathode surface because ionic silver is created at the anode whereas it is removed at the cathode. This concentration difference can be minimized by inducing sufficient mixing conditions in the reactor. In this proof-of-concept study, the electrode silver granules were separated by a relatively fine stainless steel mesh (200 × 200 mesh), from the 0.7 cm wide inter-electrode space where the water flows easily without any obstacles. The estimated Reynolds number of 0.11 indicates a laminar flow regime in the reactor (flow velocity = 0.09 cm s−1; water viscosity at 22 °C = 0.95 Pa s), lacking hydrodynamic mixing.29 Based on this discussion, it is suggested that, in future studies and practical applications, the reactor be designed to induce mixing conditions using lumpy spacers or receive water directly to the anode region and discharge it from the cathode side. These suggested design changes will help reduce the overpotential and equilibrium potential losses in the silver disinfection reactor.
3.4 Residence time requirement
In a separate set of the continuous flow experiments, the silver concentration in the electrochemical silver reactor increased linearly in the direction of the water flow and reached its maximum value of 1.54 mg L−1 at 9 cm from the inlet point (Fig. 3). The water flow path in the reactor was 12 cm long and the mean hydraulic residence time was 2.2 min during the experiment (effective volume = 11.2 mL; flow rate = 5 mL min−1). Thus, less than 1.7 min of hydraulic residence time was actually required to attain the maximum silver concentration. This result indicates that the silver release reaction is achieved rapidly (less than 2 min) and thus the electrochemical silver reactor can be built with a compact size and readily transported to provide safe drinking water to people in remote communities.
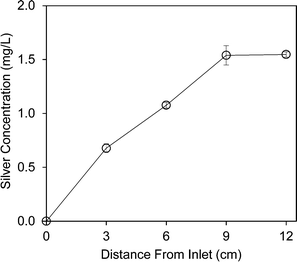 |
| Fig. 3 Silver concentration in the electrochemical disinfection reactor during continuous flow operation. (Applied voltage = 1.2 V; flow rate = 5 mL min−1; length of the flow path in the reactor = 12 cm; error bar = 2 × SD; N = 3). | |
3.5 Silver recovery using metallic aluminum
A guideline on drinking water quality by the World Health Organization (WHO) states that the silver concentration in drinking water should be 0.1 mg L−1 or lower for prolonged human consumption without potential adverse health risks.30 This guideline indicates that the water treated at 1.2 V is unsafe because of its high silver concentration of greater than 1 mg L−1. During the silver recovery experiment using the aluminum galvanic cell (Fig. 1C), the ionic silver concentration dropped to 0.1 mg L−1 in 12 h and the rate of silver recovery was not affected by the external resistance between 1000 and 9700 Ω (Fig. 4A). It should be noted that the solution used in this recovery experiment was the effluent from the electrochemical silver reactor (applied potential = 1.2 V; flow rate = 5 mL min−1) and kept in a glass container for about 16 h prior to this silver recovery test. The resulting aluminum release does not pose a health concern to humans. Aluminum salts (e.g., aluminum sulfate and poly aluminum chloride) are commonly added in drinking water treatment as a coagulant. In water, Al3+ is rapidly converted to aluminium hydroxide because it has a very low solubility limit at neutral pH ranges (~10−5 M).16 Thus, the aluminum oxidation reaction in the silver recovery cell does not pose human health risks. It should also be noted that the silver recovery cell was operated without mixing and the inter-electrode distance was approximately 2 cm. The hydrostatic condition and large inter-electrode distance (2 cm) imply that the slow recovery (requiring ~12 h) can be accelerated by providing mixing conditions or minimizing the inter-electrode distance.
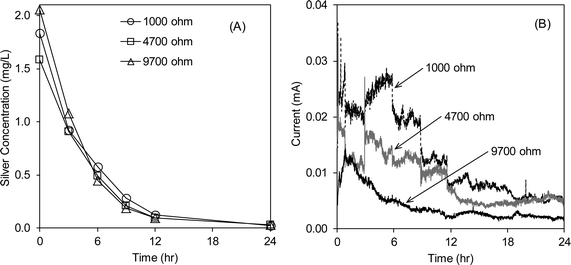 |
| Fig. 4 Silver recovery from 200 mL of silver solution using aluminum foil with various external resistors. (A) Silver concentration in the silver recovery cell. (B) Electric current during the silver recovery experiment. (The initial silver solution was the effluent from the electrochemical disinfection reactor at 1.2 V and 5 mL min−1). | |
In the silver recovery cell, the theoretical equilibrium potential at the aluminum anode ranges from −1.77 to −1.79 V versus standard hydrogen electrode (SHE) by the Nernst equation ({Al3+} = 0.01–0.1 mg L−1; 22 °C) whereas the cathode potential is between 0.45 and 0.52 V versus SHE ({Ag+} = 0.1–1.5 mg L−1; 22 °C), creating the open circuit potential of 2.22 to 2.31 V. This open circuit potential is large enough to drive the expected electrode reactions (backward reaction of eqn (1) and forward reaction of eqn (2)) without any expensive catalysts or external power supplies being required to recover the silver.
The electric current gradually decreased with time and the increasing external resistance from 1000 to 9700 Ω (Fig. 4B). The Coulombic efficiency values calculated using eqn (3) were 29% (1000 Ω), 36% (4700 Ω), and 102% (9700 Ω), and increased with the increasing external resistance. This result indicates that the majority of the cathode reaction was driven by the reduction of ionic silver with the large external resistance (9700 Ω), however, the smaller external resistances resulted in other reduction reactions at the stainless steel cathode, such as reduction of dissolved oxygen into water.
3.6 Energy requirement
The energy requirement for the electrochemical disinfection is small enough to be operated by solar panels or bicycle generators. During the experiment, 1.22 J of electric energy was consumed for the treatment of 0.2 L of the E. coli solution (1.2 V; 0.56 mA; 30 min), resulting in the energy requirement of 6.1 kJ per treatment of 1 m3 water. Commercial photovoltaic solar panels can produce electric power between 35 and 103 kJ h−1 per 1 m2 solar panel (total solar power assumed to be 411 kJ h−1; solar panel efficiency between 8.5% and 25%).31,32 This calculation indicates that a 1 m2 photovoltaic solar panel can provide enough energy to disinfect 5.7 to 16.9 m3 of water in 1 h. A bicycle generator is known to create electric power up to 1080 kJ h−1, which can be used to disinfect 177.2 m3 of water per hour.33 Because the reactor in this study was prepared as a proof-of-concept design, there is room to further reduce energy consumption in practical applications. For example, the inter-electrode distance (0.6 cm in this study) can be decreased and the electrode surface area can be increased by decreasing the silver granule size (1.6–6.4 mm in this study).
4. Conclusions
Limited access to clean and safe drinking water is a global challenge that millions of people currently face in developing countries. The disinfection system proposed and examined in this proof-of-concept study was targeted to prove that this system has the potential to provide safe drinking water to underprivileged societies without industrial infrastructure for centralized water treatment. In the laboratory scale experiments, it was demonstrated that the electrochemical reactor achieved complete inactivation of E. coli from >105 CFU mL−1 to zero viable cells in 30 min when 1.2 V was applied to the system. The rapid inactivation of E. coli was achieved using a substantially high residual silver concentration (above 1 mg L−1) and the high silver concentration was attained in less than 2 min of water residence within the reactor. A clear linear relationship between the silver concentration and electric current was established. Such a relationship is useful to estimate disinfection effectiveness by measuring electric current, not silver concentration. Note that silver analyses require expensive analytical instruments and sample preparation chemicals. In the silver recovery cell with aluminum oxidation, the high silver concentration was reduced in the silver recovery cell to the safe level for long-term human consumption (0.1 mg L−1). This silver recovery reaction was driven simultaneously without any electric energy demand and the energy requirement for the disinfection was substantially small so that a bicycle pedal generator or photovoltaic solar panel can provide sufficient energy for drinking water treatment. These conclusions support the fact that the demonstrated disinfection and recovery system has the potential to provide safe drinking water to people in underprivileged communities around the world. The system examined can supply clean water for a long time with only a small amount of metallic silver. It should be noted that the disinfection experiment was performed separately from the silver recovery experiment to avoid potential removal of E. coli cells by aluminum precipitants. In practical applications, the aluminum electrode can be incorporated in the disinfection reactor so that ionic silver can be recovered directly onto the silver electrodes, allowing an extended use of the silver electrodes for water purification.
Acknowledgements
This study was supported by Safe Drinking Water Pilot Project Grant (Canadian Foundation for Infectious Diseases), Discovery Grants (435547-2013, Natural Sciences and Engineering Research Council of Canada), Canada Research Chairs Program (950-2320518, Government of Canada), Leaders Opportunity Fund (31604, Canada Foundation for Innovation), and Ontario Research Fund-Research Infrastructure (31604, Ontario Ministry of Economic Development and Innovation). The authors thank Ms. Anna Robertson and Mr. Peter Koudys for their help on equipment operation and reactor construction.
References
- M. A. Shannon, P. W. Bohn, M. Elimelech, J. G. Georgiadis, B. J. Mariñas and A. M. Mayes, Science and technology for water purification in the coming decades, Nature, 2008, 452(7185), 301–310 CrossRef CAS PubMed.
- M. D. Sobsey, C. E. Stauber, L. M. Casanova, J. M. Brown and M. A. Elliot, Point of use household drinking water filtration: a practical, effective solution for providing sustained access to safe drinking water in the developing world, Environ. Sci. Technol., 2008, 42(12), 4261–4267 CrossRef CAS PubMed.
- K. S. Enger, K. L. Nelson, T. Clasen, J. B. Rose and J. N. S. Eisenberg, Linking quantitative microbial risk assessment and epidemiological data: informing safe drinking water trials in developing countries, Environ. Sci. Technol., 2012, 46(9), 5160–5167 CrossRef CAS PubMed.
-
A. Prüss-Üstün, R. Bos, F. Gore and J. Bartram, Safer water, better health, WHO, Geneva, 2008 Search PubMed.
- D. L. Sedlak and U. von Gunten, The chlorine dilemma, Science, 2011, 331(6013), 42–43 CrossRef CAS PubMed.
- J. A. Lemire, J. J. Harrison and R. J. Turner, Antimicrobial activity of metals: mechanisms, molecular targets and applications, Nat. Rev. Microbiol., 2013, 11(6), 371–384 CrossRef CAS PubMed.
- R. B. Thurman, C. P. Gerba and G. Bitton, The molecular mechanisms of copper and silver ion disinfection of bacteria and viruses, Environ. Sci. Technol., 1989, 18(4), 295–315 Search PubMed.
- J. A. Spadaro, T. J. Berger, S. D. Barranco, S. E. Chapin and R. O. Becker, Antibacterial effects of silver electrodes with weak direct current, Antimicrob. Agents Chemother., 1974, 6(5), 637–642 CrossRef CAS PubMed.
- A. D. Russel and W. B. Hygo, Antimicrobial activity and action of silver, Prog. Med. Chem., 1994, 31, 351–370 CrossRef.
- T. A. Dankovich, J. S. Levine, N. Potgeiter, E. Dillingham and J. A. Smith, Inactivation of bacteria from contaminated streams in Limpopo, South Africa by silver- or copper- nanoparticle paper filters, Environ. Sci.: Water Res. Technol., 2015 10.1039/c5ew00188a.
- O. Choi, K. K. Deng, N. J. Kim, L. Ross Jr., R. Y. Surampalli and Z. Hu, The inhibitory effects of silver nanoparticles, silver ions, and silver chloride colloids on microbial growth, Water Res., 2008, 42(12), 3066–3074 CrossRef CAS PubMed.
- J. E. Stout and V. L. Yu, Experiences of the first 16 hospitals using copper-silver ionization for Legionella control: implications for the evaluation of other disinfection modalities, Infect. Control Hosp. Epidemiol., 2003, 24(8), 562–568 Search PubMed.
- J. E. Stout, Y. E. Lin, A. M. Goetz and R. R. Muder, Controlling Legionella in hospital water systems: experience with the superheat-and-flush method and copper-silver ionization, Infect. Control Hosp. Epidemiol., 1998, 19(12), 911–914 CrossRef CAS PubMed.
- Z. Liu, J. E. Stout, L. Tedesco, M. Boldin, C. Hwang, W. F. Diven and V. L. Yu, Controlled evaluation of copper-silver ionization in eradicating Legionella pneumophila from a hospital water distribution system, J. Infect. Dis., 1994, 169(4), 919–922 CrossRef PubMed.
-
P. Gleick, Dirty Water: Estimated deaths from water-related diseases 2000–2020, Pacific Institute Research Report, 2002 Search PubMed.
-
United States Environmental Protection Agency, Secondary drinking water regulations: guidance for nuisance chemicals, http://water.epa.gov/drink/contaminants/secondarystandards.cfm#tabletop Date of Access: August 18, 2015 Search PubMed.
- N. Silvestry-Rodriguez, K. R. Bright, D. C. Slack, D. R. Uhlmann and C. P. Gerba, Silver as a residual disinfectant to prevent biofilm formation in water distribution systems, Appl. Environ. Microbiol., 2008, 74(5), 1639–1641 CrossRef CAS PubMed.
- S. L. Loo, W. B. Krantz, A. G. Fane, Y. Gao, T. T. Lim and X. Hu, Bactericidal mechanisms revealed for rapid water disinfection by superabsorbent cryogels decorated with
silver nanoparticles, Environ. Sci. Technol., 2015, 49(4), 2310–2318 CrossRef CAS PubMed.
- D. T. Schoen, A. P. Schoen, L. Hu, H. S. Kim, S. C. Heilshorn and Y. Cui, High speed water sterilization using one-dimensional nanostructures, Nano Lett., 2010, 10(9), 3628–3632 CrossRef CAS PubMed.
- J. Tang, L. Xiong, S. Wang, J. Wang, L. Liu, J. Li, F. Yuan and T. Xi, Distribution, translocation and accumulation of silver nanoparticles in rats, J. Nanosci. Nanotechnol., 2009, 9(8), 4924–4932 CrossRef CAS PubMed.
- W.-Y. Kim, J. Kim, J. D. Park, H. Y. Ryu and I. J. Yu, Histological study of gender differences in accumulation of silver nanoparticles in kidneys of Fischer 344 rats, J. Toxicol. Environ. Health, Part A, 2009, 72(21–22), 1279–1284 CrossRef CAS PubMed.
- F. R. Khan, K. B. Paul, A. D. Dybowska, E. Valsami-Jones, J. R. Lead, V. Stone and T. F. Fernandes, Accumulation dynamics and acute toxicity of silver nanoparticles to Daphnia magna and Lumbriculus variegatus: implications for metal modeling approaches, Environ. Sci. Technol., 2015, 49(7), 4389–4397 CrossRef CAS PubMed.
-
M. M. Benjamin and D. F. Lawler, Water quality engineering: physical / chemical treatment processes, JohnWiley & Sons, Hoboken, NJ, 2013, pp. 488–535 Search PubMed.
-
A. J. Bard and L. R. Faulkner, Electrochemical methods: fundamentals and applications, John Wiley & Sons, Hoboken, NJ, 2001, pp. 44–86 Search PubMed.
- J. M. Passmore, D. L. Rudolph, M. M. F. Mesquita, E. E. Cey and M. B. Emelko, The utility of microspheres as surrogates for the transport of E. coli RS2g in partially saturated agricultural soil, Water Res., 2010, 44(4), 1235–1245 CrossRef CAS PubMed.
-
W. A. Rutala and D. J. Weber, Guideline for disinfection and sterilization in healthcare facilities, http://www.cdc.gov/hicpac/pdf/guidelines/Disinfection_Nov_2008.pdfp. 39 Date of Access: August 19 2015 Search PubMed.
-
Government of Ontario. Procedure for disinfection of drinking water in Ontario, https://dr6j45jk9xcmk.cloudfront.net/documents/1182/99-disinfection-of-drinking-water-en.pdfp. 4 Date of Access: August 19 2015 Search PubMed.
-
A. D. Eaton and M. A. H. Franson, Standard methods for the examination of water & wastewater, 18th edn, American Public Health Association, Washington, DC, 2005, pp. 3:13–3:93 Search PubMed.
-
E. J. Finnemore and J. B. Franzini, Fluid mechanics with engineering applications, 10th edn, McGraw Hill, New York, NY, 2006, pp. 234–241 Search PubMed.
-
World Health Organization, Guidelines for drinking-water quality, 3rd edn, 2008, http://www.who.int/water_sanitation_health/dwq/fulltext.pdfp. 434 Date of Access: August 19 2015 Search PubMed.
- Q. Schiermeier, H. Tollefson, T. Scully, A. Witze and O. Morton, Energy alternatives: electricity without carbon, Nature, 2008, 454, 816–823 CrossRef CAS PubMed.
- M. A. Green, K. Emery, Y. Hishikawa and W. Warta, Solar cell efficiency tables (version 35), Prog. Photovoltaics, 2010, 18, 144–150 CAS.
-
MNS Power Generating Systems, Roller style bicycle generator, http://pedalpowergenerator.com/shop-pedal-power/roller-style-bicycle-generator/ Date of Access: August 19 2015.
|
This journal is © The Royal Society of Chemistry 2016 |
Click here to see how this site uses Cookies. View our privacy policy here.