Long-term performance of a 200 liter modularized microbial fuel cell system treating municipal wastewater: treatment, energy, and cost†
Received
19th January 2016
, Accepted 3rd February 2016
First published on 4th February 2016
Abstract
Microbial fuel cells (MFCs) have been intensively studied at a bench scale and the further development of this technology requires system scaling up and understanding of their performance under non-laboratory conditions. In this study, a 200 L modularized MFC system consisting of 96 MFC modules was developed and operated in a local wastewater treatment plant for treating primary effluent. During more than 300 days' operation, the MFC system removed more than 75% of the total chemical oxygen demand and 90% of the suspended solids, despite significant fluctuations in treatment performance affected by wastewater quality and operational factors. It achieved 68% removal of ammonia nitrogen, but phosphorous and the nitrate accumulated due to nitrification needs further disposal. The frequency of the catholyte recirculation exerted a strong effect on the energy consumption of the MFC system. Through both parallel and serial electric connections, the MFC system generated power of ∼200 mW that was extracted by a power management system to drive a 60 W DC pump for catholyte recirculation. Over 60% of the material cost of the MFCs was due to the cation exchange membrane, and the capital cost of the MFC system could be comparable to that of small wastewater treatment facilities. The results of this study encourage the further development of MFC technology with reduced costs and improved performance towards sustainable wastewater treatment.
Water impact
Development of microbial fuel cells (MFCs) will help to achieve sustainable wastewater treatment by recovering bioenergy and reducing energy consumption. Modularizing MFC reactors could be a feasible approach to scale up the system. Long-term examination of MFC systems with actual wastewater under non-laboratory conditions is critical to understanding their real-world performance, operational parameters, costs, and the challenges for further development.
|
1. Introduction
Microbial fuel cells (MFCs) have been intensively studied in the past decade with great advancements in system development, microbiology, electrochemistry, and materials.1 The potential advantages of MFC technology, including direct production of electric energy, low production of sludge, and low energy consumption, make it promising as an alternative approach for sustainable wastewater treatment.2 Applications of MFC technology have expanded beyond electricity generation with versatile functions such as nutrient removal and recovery,3 promoting algal biomass production,4 and metal removal and recovery.5 Appropriate modification of MFC systems creates various derivatives for desalination,6 hydrogen production,7 and synthesis of organic compounds.8
Despite great progress in the research of this technology, there are still challenges for MFCs to be used for practical applications. Among those challenges, system scaling up appears to be very important and a major obstacle.9 The declining performance of electricity generation or power output has been observed in larger systems due to weak mixing and poor design of electrode configuration.10 Bench-scale MFCs with a small liquid capacity (<50 mL) usually generate relatively high power densities (>500 Wm−3) whereas MFCs larger than 2 L generally produce a power density less than 30 Wm−3, although energy recovery could have different implications and requires further assessment.11 In general, there are two strategies for scaling up MFCs, enlarging the single reactor and stacking multiple reactors into one system (modularization). Increasing the size of an MFC reactor is necessary for its development; however, a full scale application of MFCs will be unlikely to have a single reactor, because it will unavoidably enlarge the distance between the anode and the cathode electrodes, thereby increasing the internal resistance and decreasing electricity generation. On the other hand, modularization of MFC reactors through hydraulic and/or electrical connection seems to be more promising for creating a large-scale system.
Several laboratory studies have shown encouraging results for the technical feasibility of operating multiple MFC reactors through stacking. Like chemical fuel cells, stackable MFC reactors connected in series or parallel are able to achieve the desired voltage or current output, as well as an increased liquid volume capacity.12–15 For example, an MFC stack consisting of 40 identical 20 mL MFC units could achieve an open circuit voltage (OCV) of 13.03 V and was capable of self-maintenance under specially designed laboratory conditions.16 Systems based on modularized MFC units have been developed as well to realize the demands of a large volumetric capacity. An MFC system was designed to contain multiple MFC units installed inside a large container, which allowed the MFC modules in one single chamber to function independently with a different electric connection while the liquid capacity of the system was not limited by the structure of MFCs.17 The modularized MFC system could be simplified by using alternating graphite fiber brush array anode modules and dual cathode modules.18 The success of stacking bench-scale MFCs has encouraged the scaling up of the MFC modules towards a large-scale system. A 90 L MFC system following a similar design of a previous system17 could achieve sufficient energy from brewery wastewater treatment to support its operation.19 The largest size of an individual MFC module in the literature is 250 L, and several such MFC modules were stacked to treat municipal wastewater.20 Nevertheless, there is a strong demand for more studies of modularized MFC systems.
In this study, a 200 L modularized MFC system consisting of 96 tubular MFC modules (2 L/each) was examined for long-term (one year) performance treating municipal wastewater (primary effluent) under non-laboratory conditions. The research was built on the prior efforts of developing tubular MFCs with long-term operation21–22 and focused on two key aspects of the scaling up of MFC-based treatment systems, liquid capacity for wastewater treatment and energy recovery from MFCs. The performance of the contaminant removal and electricity generation was evaluated. Development of the power management system and energy extraction from this system has been previously reported,23 and herein the application of the extracted energy to power a recirculation pump was evaluated. A preliminary analysis of the material and capital costs of this MFC system was conducted.
2. Materials and methods
2.1 Construction and operation of the MFC system
The MFC system consisted of 96 tubular MFC modules, which were placed as 12 × 8 arrays with 12 MFCs in each row and 8 rows in total (Fig. 1A and B). Each tubular MFC module was constructed with a cation exchange membrane (CEM, Ultrex CMI7000, Membranes International, Inc., Glen Rock, NJ) with a liquid volume of 2 L based on the method used in a previous study.21 A carbon brush was used as the anode electrode while carbon cloth coated with nitrogen doped activated carbon powder24 was used as the cathode electrode, which was wrapped outside the membrane tube. The 8 rows (R1–8) were divided into four sets (S1–4), each of which contained 2 rows. Within a set, 24 MFCs in 2 rows were hydraulically connected through plug-flow feeding. Thus, there were in total four feeding ports to the MFC system. The anode effluents from the four sets were collected in a rectangular tank with a surface area of 4 m2 (2 × 2 m) and a depth of 0.5 m, which was placed under the MFC modules. The depth of water in the tank was controlled by an overflow port to achieve an effective liquid volume of about 100 L. Some of the water in the collection tank was pumped to the top of the MFC array as the catholyte.
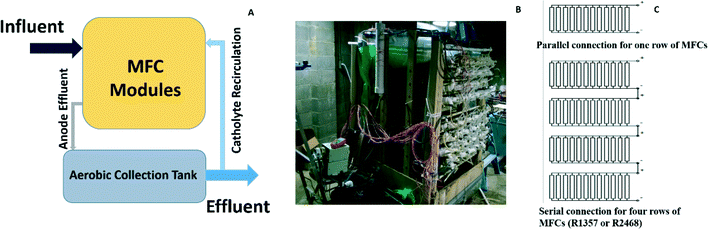 |
| Fig. 1 The MFC system: (A) the schematic showing the MFC modules and a collection tank; (B) the MFC setup in a local wastewater treatment plant; and (C) the electric connections. | |
The MFC system was installed in a local wastewater treatment plant (Pepper's Ferry Regional Wastewater Treatment Authority, Radford, VA) and started by feeding the primary effluent continuously at a hydraulic retention time (HRT) of 6 h into the MFC anode chambers. When the performance of the MFC system became relatively stable, the HRT was adjusted to 12 h for the MFC anode chambers; because the MFC effluent stayed for 6 h in the collection tank before discharge, the overall HRT for the MFC system (consisting of the MFCs and the collection tank) was 18 h. The catholyte was recirculated by a submersible pump (FLOTEC 1/4 HP, 79.5 L min−1) with a frequency of 300 s on per 30 min operational cycle unless specified in the section 3.3.
2.2 Electrical connection
For the electricity connection, the 12 MFCs in each row were connected in parallel with an external circuit across a resistor of 3.3 ohm, and then R1, R3, R5, and R7 were connected in series (“R1357”) while R2, R4, R6, and R8 were connected in series (“R2468”), both of which had a 15 ohm resistor as the external load (Fig. 1C). The 15 ohm load was selected because it was close to the internal resistance of the system determined from the polarization tests.23 The reason why the adjacent rows were not connected in series was to avoid short circuit connections.
To study energy extraction and application in the MFC system, the MFCs were connected to a boost converter (BQ 25504, Texas Instruments, TX) to charge the 50-F capacitors to 5 V (BCAP0050-P270, Maxwell, CA), and then the output voltage was boosted to 12 V through another DC–DC converter (3–34 V to 4–35 V, DROK, China) as shown in Fig. 6A. The MOSFET switches were controlled by a microcontroller to adjust charging/discharging mode. When the voltage of the capacitors was less than 5 V, the charging circuit was activated until the voltage reached 5 V. Then, the capacitors were connected with the 12 V booster to drive the DC pump. The discharging was stopped when the capacitors' voltage dropped to 4 V, which activated the charging circuit again to transfer energy from the MFCs to the capacitors for the next discharging cycle. The energy produced from the MFCs was used to power a 12 V DC pump (Micro Car Diaphragm Water Pump, 60 W, 5 L min−1, AUBIG) for catholyte recirculation.
2.3 Measurements and analysis
The voltage of the MFCs was recorded every 10 min using a digital multimeter (2700, Keithley Instruments, Inc., Cleveland, OH, USA). The temperature of the wastewater influent/effluent and the room where the MFC system was set up was monitored using a temperature sensor (DS18B20, Dallas Semiconductor, Dallas, TX) through a microcontroller (Arduino Uno, Italy). The concentration of the chemical oxygen demand (COD) was measured using a COD digester and a colorimeter according to the manufacturer's instructions (Hach Company, Loveland, CO, USA). The total suspended solids (TSS) was measured using standard methods.25 The concentrations of ammonia, nitrate, and phosphorous were measured using a colorimeter (DR 890, Hach Company). The theoretical energy consumption of the feeding pump (influent) and the recirculation pump was estimated as:26 | 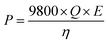 | (1) |
where P is the power demand (W), Q is the flow rate (m3 s−1), E is the hydraulic head loss (m), and η is the pump efficiency (0.5–0.9).
The energy stored/released from the capacitors was calculated as:
| 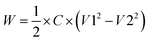 | (2) |
where
C is the capacity of the capacitor,
V1 is the voltage before discharging, and
V2 is the voltage after discharging.
3. Results and discussion
3.1 Electricity generation
The MFC system was started by feeding primary effluent and gradually reducing the external resistance for 30 days before data collection began. Between days 30 and 74, the electricity generation was monitored based on rows, each of which contained 12 MFC modules in parallel connection (Fig. 2). In general, the odd-number rows (e.g., R3 and R5) produced more electricity than the even-number ones, likely due to the concentration gradients between the two rows. For example, R3 and R4 were hydraulically connected as a plug-flow reactor with the wastewater being fed into the first MFC module of R3 and the effluent being discharged from the last MFC module of R4; in that way, the organic concentration in the MFCs of R3 should be generally higher than that in those of R4. However, one exception is that R1 generated the lowest current density of ∼2 A m−3 (∼50 mA), which could be related to the operational issue that those MFC reactors were dried after inoculation for such a long time that a layer of inactive materials (e.g., dead cells) could form on the surface of the carbon brush electrode and prevent its contact with electrochemically-active bacteria after the second inoculation. Similar results were observed from the previous study that the maximal power production was obtained from serially connected rows in the absence of R1 (R357 > R1357).23 Serious corrosion of copper wires that were used for connecting the electric circuits was observed and resulted in a significant decrease in electricity generation; after the replacement of the corroded copper wire with titanium wire and additional insulation treatment, the current was boosted significantly especially in R3, R5, and R7, which produced electricity of over 6 A m−3 individually (150 mA) (Fig. 2).
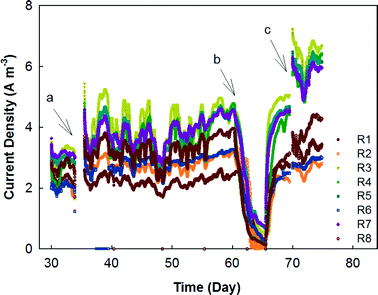 |
| Fig. 2 The current densities of the 8 rows of MFCs with a parallel electric connection in each row. Arrow “a” indicates a power outage, arrow “b” indicates an unexpected stop in the feeding, and the arrow “c” represents the replacement of copper wire with titanium wire. | |
In the next stage, the electrical connection of the MFC system was modified with R1, 3, 5, and 7 being electrically connected in series as group 1 (G1), while R2, 4, 6, and 8 were electrically connected in series as group 2 (G2). The external resistance for each group was adjusted to 15 ohm based on previous tests for maximum power output,23 and the current generation of those two groups is shown in Fig. 3. As expected, G2 produced less electricity most of the time because of its lower organic concentration (Fig. 3A). The profile of the temperature of the wastewater (influent and effluent) and the room is shown in Fig. 3B. It seems that both G1 and G2 were affected by the temperature and the current generation consistently followed a similar trend of temperature variation. The serial connection did not increase the current density, and because of the increased external resistance (adjusted for the maximum power output), the average current density from G1 was lower than 0.8 A m−3 (80 mA) and G2 generated 0.5 A m−3 (50 mA).
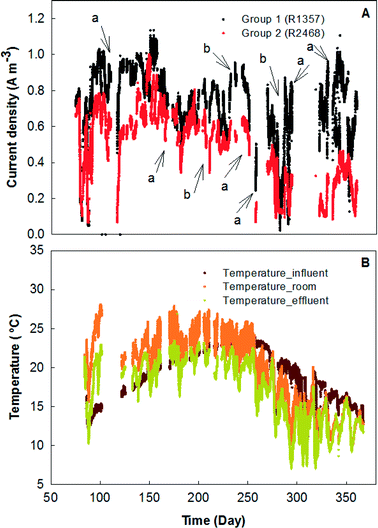 |
| Fig. 3 The current density MFCs connected in series in two groups (A) and the temperature records (B). In Fig. 3A, arrow “a” indicates a power outage, and arrow “b” indicates an unexpected stop of the feeding caused by the stopping of the influent pump and the malfunction of the floating switch. | |
3.2 Treatment performance
The MFC system could effectively remove organic and nitrogen compounds, and the treatment was via a two-step pathway, anaerobic treatment in the MFC anodes and aerobic treatment on the MFC cathodes/in the collection tank. The MFC system removed 76.8% of total COD (TCOD) and 55.5% of soluble COD (SCOD). The organic concentrations in the primary effluent (which was the feeding solution for the MFC system) varied significantly over time, and the TCOD concentration in the primary effluent was 155 ± 37 mg L−1 and the SCOD concentration was 73 ± 23 mg L−1. The effluent TCOD concentrations from the four groups were 98 ± 29, 89 ± 29, 99 ± 30, and 103 ± 26 mg L−1, respectively, and the SCOD concentrations were 76 ± 26, 79 ± 22, 82 ± 23, and 85 ± 25 mg L−1, respectively (Fig. 4A). Thus, the MFC anodes reduced 37.6% of TCOD at a HRT of 12 h, but SCOD was accumulated a little likely due to the release of soluble organics from particular COD content (influent solid) through hydrolysis. When the anode effluents flowed over the cathode electrodes and through the collection tank, additional removal of organic compounds occurred, via aerobic treatment that removed 39.2% of TCOD and 59.5% of SCOD, resulting in a TCOD of 36 ± 15 mg L−1 and SCOD of 33 ± 11 mg L−1 in the final effluent from the collection tank. The removal of the total suspended solids occurred mainly in the MFC anodes, which decreased the TSS concentration from 72.9 ± 16.6 mg L−1 to 12.4 ± 8.9 mg L−1, and the cathode/collection tank further reduced the TSS concentration to 6.3 ± 4.1 mg L−1 in the final effluent (Fig. 4A). During the operation of this MFC system over 300 days, no excessive sludge was wasted while the final effluent TSS was maintained at a low level of less than 10 mg L−1 (which met the discharging limit), likely benefiting from the low growth rate in the MFC anodes and biomass decay in the collection tank.
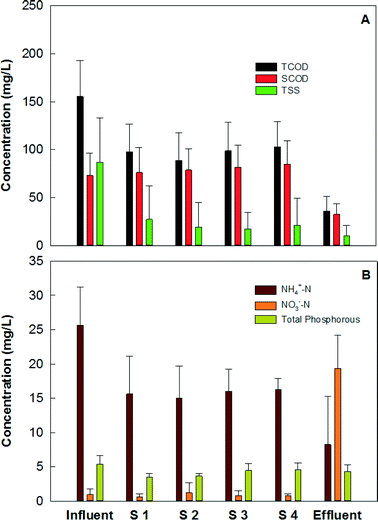 |
| Fig. 4 The performance of the MFC treatment: (A) COD and TSS; and (B) nitrogen and total phosphorous. S1–4 represent four sets of MFC reactors, each of which contained two rows of MFCs fed in the same hydraulic loop. | |
The removal of nutrients, especially ammonium nitrogen, is expected via multiple approaches such as ammonium ion transport across the cation exchange membrane and nitrification/denitrification on the cathode.3 The primary effluent contained an ammonium concentration of 25.7 ± 5.5 mg N L−1, which was reduced to 8.2 ± 7.0 mg N L−1 (Fig. 4B), resulting in an average removal efficiency of 68%. Because the anode effluents would flow through the cathode, the ammonium ion transport across the cation exchange membrane could not be distinguished. The removal of ammonium nitrogen was likely by nitrification, which resulted in the accumulation of nitrate (18.3 ± 6.0 mg N L−1) in the final effluent (Fig. 4B). The nitrification also led to a pH of 7.6 ± 0.4 in the final effluent from the collection tank (Table S1, ESI†), which would not favor ammonium removal or even recovery through forming ammonia gas.27–28 There was a small amount of nitrite in the effluent with an average concentration of 0.9 ± 1.0 mg L−1. Unlike nitrogen removal, the MFC system did not perform well in removing phosphorous. Biomass uptake could be the major mechanism accounting for the reduced concentration, and there was about 20% uptake during the 18-hour residential time, resulting in a final concentration of 4.3 ± 1.0 mg L−1 (Fig. 4B).
3.3 Effects of catholyte recirculation
Catholyte recirculation is considered to be a major energy consumer for MFCs operated similarly to the present MFC system,29 and thus from days 185 to 215, the catholyte recirculation was examined at various frequencies to study its effects on the performance of electricity production and wastewater treatment. The tests changed both the pumping duration and operation intervals, which could be expressed as “s on per min” as shown in Fig. 5. For example, “60/60” means that the recirculation pump was on for 60 s of every 60 min operation. Initially, the frequency of the catholyte recirculation was kept at 300 s per 30 min, which led to an average current generation of 0.73 A m−3 (73 mA) from G1 and 0.64 A m−3 (64 mA) from G2. When the operation cycle was set at 60 min, the current density of G1 decreased from 0.72 ± 0.02 to 0.53 ± 0.05 A m−3 as the recirculating duration decreased from 60 to 10 s (Fig. 5A). When the operation cycle was shortened to 30 min but the total recirculation time (10 s) in one hour was kept the same as the previous 60 min cycle, the current density of G1 was recovered close to the original level, indicating the importance of the catholyte recirculation that provides water for cathode reactions. The frequent catholyte recirculation may relieve the loss of water molecules caused by evaporation and shorter cycle intervals are expected to be beneficial in maintaining the moisture of the cathode electrode. It seemed that 5 s of pumping was sufficient to generate moderate current when the operation cycle was between 30 and 45 min, but either decreasing the recirculation time (from 5 s to 3 s) or longer cycle intervals (such as 10 s on per 60 min) apparently suppressed the current production (Fig. 5).
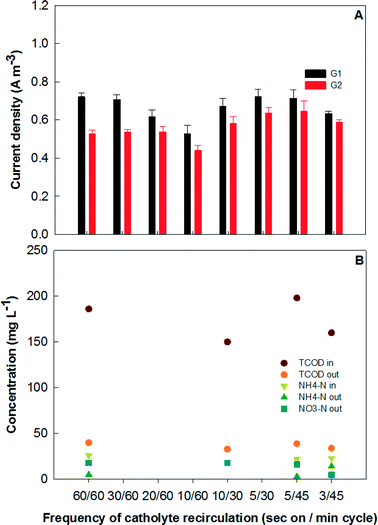 |
| Fig. 5 The effects of catholyte recirculation frequency on (A) electricity production and (B) treatment performance. | |
An analysis of the energy balance for the MFC system is presented in Table 1 based on the normalized energy recovery (NER) from the MFCs11 and energy consumption by the feeding and recirculation pumping per cubic meter of treated wastewater. Clearly, less frequent catholyte recirculation is critical to achieve a positive net energy balance from the system, but an appropriate cycle interval was also required to maintain a relatively high energy production. For example, when the recirculation duration was kept as 10 s in a 60 min operation cycle, the total energy balance was negative, indicating that the recirculation pumping consumed more energy than was produced. However, when the recirculation duration was kept as 5 s for an operation cycle of 30–45 min, the electrical energy produced was theoretically sufficient to cover the consumption for both the feeding and recirculation pumping. It was shown that a frequency of 5 s on per 30 min, 5 s on per 45 min, and 3 s on per 45 min would achieve a positive net energy balance of 0.005, 0.006, and 0.003 kW h m−3, respectively.
Table 1 Energy production and consumption in the MFC system with various catholyte recirculation frequencies. The energy consumption of the feeding and recirculation pump was based on the theoretical calculation using eqn (1). The head losses of the feeding pump and the recirculation pump were 3 m and 2 m, respectively
Recirculation frequency (s on per min) |
Current (A m−3) |
Energy recovery from MFCs (kW h m−3) |
Feeding pump (kW h m−3) |
Recirculation pump (kW h m−3) |
Net energy (kW h m−3) |
G1 |
G2 |
G1 |
G2 |
60/60 |
0.72 |
0.53 |
0.009 |
0.005 |
0.009 |
0.018 |
−0.013 |
30/60 |
0.71 |
0.54 |
0.009 |
0.005 |
0.009 |
−0.004 |
20/60 |
0.62 |
0.54 |
0.007 |
0.005 |
0.006 |
−0.003 |
10/60 |
0.53 |
0.44 |
0.005 |
0.003 |
0.003 |
−0.004 |
10/30 |
0.67 |
0.58 |
0.008 |
0.006 |
0.006 |
−0.001 |
5/30 |
0.72 |
0.64 |
0.009 |
0.007 |
0.003 |
0.005 |
5/45 |
0.71 |
0.64 |
0.009 |
0.007 |
0.002 |
0.006 |
3/45 |
0.63 |
0.59 |
0.007 |
0.006 |
0.001 |
0.003 |
Contaminant removal was affected by recirculation as well. As shown in Fig. 5B, the final effluent COD appeared to be very close to the average summarized in Fig. 4A for most frequencies, but the ammonia in the effluent increased to 14 mg L−1 and the corresponding nitrate was only 5 mg L−1 with a recirculation frequency as low as 5 s on per 45 min cycle. The short recirculation duration possibly decreased the oxygen reaeration and mixing in the collection tank, which inhibited the activity of ammonia oxidation. Because of the frequent malfunction of the influent (due to the power shutting off or other unexpected reasons), sometimes the operation of the MFC system could be shut down automatically with no cathode recirculation, resulting in little nitrification and the effluent ammonia was as high as 19 mg L−1. Therefore, the catholyte recirculation in the present MFC system is important for its impact on energy consumption, electricity production, and ammonium removal.
3.4 Energy production and utilization
Energy extraction from MFCs has been investigated to power small electronics such as sensors, low-voltage batteries/capacitors, and small DC motors.30 In this study, the feasibility of energy utilization on-site using a charging/discharging strategy was examined. More details about the energy extraction and power management system from this MFC system have been previously reported.23 To power a 12 V water pump, the energy extracted from the MFC system was stored in 5 V capacitors, which were used as power sources to drive the water pump through a 3–12 V boost converter. An example of the voltage variation in the MFC system and the capacitors is shown in Fig. 6. It required 50–60 min to charge the capacitors from 4 to 5 V, while a 1 V drop could provide the energy to run the water pump for the catholyte recirculation for about 5 s.
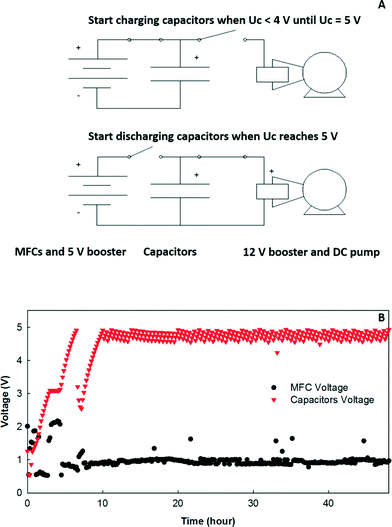 |
| Fig. 6 Electricity extraction and application: (A) schematic of the power management system showing charging/discharging; and (B) an example of the voltage variation in the MFC system output and the capacitors. | |
To better understand the energy use, consumption based on theoretical calculations (eqn (1)) and actual utilization according to the power requirement of the pumps were estimated (Table 2). When the AC pump was used and the recirculation frequency was 5 s on per 30 min, the theoretical energy consumption by the recirculation and feeding pumping in one operational cycle was 91.6 and 272 J, while G1 produced 146.5 J based on the average current density generation, which was about 40% of the total energy consumption. However, the actual energy requirements for recirculation based on the power input (1/4 HP, 186 W) and the operational time was 931 J, and then G1 could provide only 12.2% of the total requirements (including both recirculation and feeding). When the AC pump was replaced by the DC pump, the theoretical energy input for the recirculation was only 9.1 J with a frequency of 5/60 while the actual energy consumption was 300 J. The energy produced from G1 could provide 52.9% and 34.7% of the theoretic and actual consumption of the DC pump for both recirculation and feeding, respectively. When the energy of G2 was included, the total energy production from both G1 and G2 could support 78.4% of the theoretical energy consumption. In actual application, only the energy from G1 was used, and the energy generated in one operational cycle could support about 5 s operation of the DC pump. The relatively high energy input for the feeding pump (influent) was caused by high hydraulic head loss (about 3 m) due to the small tubing and connectors used in the system. If the head loss can be reduced to 0.5 m, the total theoretical energy input for the feeding pump would be around 90 J for each cycle using a DC pump.
Table 2 Analysis of power/energy input and output of the MFC system
|
|
Recirculation |
Feedingb |
MFCs (G1) |
MFCs (G2) |
Theorya |
Actual |
Averagec |
Averagec |
Theoretical power and energy was calculated based on eqn (1), assuming the pump efficiency was 90%.
The power and energy required for feeding was estimated using eqn (1) with an efficiency of 90%.
The average power output was based on 300 days of data.
|
Power (W) |
AC pump |
−18.3 |
−186.3 |
−0.15 |
0.081 |
0.039 |
DC pump |
−1.8 |
−60 |
Energy consumption/production per cycle (J) |
AC pump (10 s/45 min) |
−91.6 |
−931.3 |
−272 |
146.5 |
70.5 |
DC pump (5 s/40 min) |
−9.1 |
−300 |
−544 |
293.0 |
141 |
3.5 Engineering cost analysis
A preliminary cost analysis was conducted here to estimate the total material cost of the 200 L MFC system and its capital cost. As shown in Table 3, the total material cost for making one tubular MFC module was about $23.2, and the CEM contributed over 60% of the total cost. Given the rapid advancement in material science, a low-cost ion exchange membrane could be expected and then the material cost of the proposed MFC modules would be greatly reduced. The capital cost of the MFC system used in this study was estimated to be $6064 (Table 4). Considering the challenges in scaling up MFCs, applying an MFC system for small scale wastewater treatment may be more feasible. Thus, the capital cost of the present MFC system was compared with small treatment systems normalized based on the treatment capacity (gpd – gallon per day). It should be noted that the capital cost of wastewater treatment systems varies significantly and is affected by many factors, and what is presented here acts as an example. The capital cost for a small wastewater treatment facility with a capacity of 10
000 gpd is $70 per gpd of treatment capacity.31 It was estimated that the capital cost of this 200 L MFC system was about $58 per gpd of treatment capacity. This comparison would not conclude that the MFC system is cheaper than the existing treatment system (a more comprehensive analysis will be needed), because the estimation of the MFC capital cost did not include that of pre- and post-treatment facilities. However, it indicates that the cost factor could be alleviated if an appropriate application niche (e.g., small systems for remote communities, isolated residential areas, hotel resorts, or military forward operating bases) is identified for MFC technology with the development of new cost-effective materials.
Table 3 Material cost of a single MFC module
Materials |
Cost ($) |
Cation exchange membrane |
14.48 |
Carbon cloth |
1.53 |
Carbon brush |
3.00 |
Activated carbon (catalyst) |
0.01 |
PTFE (binding agent) |
0.02 |
Titanium wire |
0.08 |
PVC tube |
0.14 |
Others |
4 |
Total |
23.18 |
Table 4 Total capital cost estimation of the 200 L MFC system
Items |
Cost ($) |
Assumption |
MFC system |
2226 |
|
Pumps |
800 |
|
Installation |
756 |
25% of equipment cost |
Land |
882 |
$39 930 per acre |
Direct cost (DC) |
4664 |
|
Engineering cost |
700 |
15% of DC |
Contingency |
700 |
15% of DC |
Indirect cost (IC) |
1399 |
|
Total capital cost (DC + IC) |
6064 |
|
Capital cost per gpd of capacity (200 L MFC system, 106 gpd) |
58 |
|
Capital cost per gpd of capacity (10 000 gpd WWTP)31 |
70 |
|
4. Conclusions
This study has demonstrated one of the very few field trials of large-scale MFC systems treating actual wastewater with a long-term operation. Although its performance was not as good as those reported from laboratory MFC systems, it did exhibit effective treatment of primary effluent through the integration of bioelectrochemical and aerobic treatment. Optimizing the coordination between MFC modules for the best performance will be a key challenge for modularized systems. Examination of the onsite application of the produced energy has revealed the gap between theoretical energy recovery and that of the real world. The capital cost of the MFC system could be comparable to that of small scale wastewater treatment facilities, with a potential for further reduction benefiting from the development of cost-effective membrane materials. It is expected that the results of this work will create interest in more studies of MFC systems at a comparable or larger scale by peer researchers to advance MFC technology towards sustainable wastewater treatment.
Acknowledgements
This study was financially supported by a grant from the National Science Foundation (#1348424). The authors thank Pepper's Ferry Regional Wastewater Treatment Authority for providing a testing site. They would also like to thank Dr. Fei Zhang, Mr. Bojun Xu, Mr. Joseph Stevens, Mr. Hwangbo Bae, Mr. Xiaojin Li, Mr. Shuai Luo, and Mr. Abdullah Alammar for their help with the experiment.
References
- B. Logan and K. Rabaey, Science, 2012, 337, 686–690 CrossRef CAS PubMed.
- W.-W. Li, H.-Q. Yu and Z. He, Energy Environ. Sci., 2014, 7, 911–924 CAS.
- P. Kelly and Z. He, Bioresour. Technol., 2014, 153, 351–360 CrossRef CAS PubMed.
- L. Xiao and Z. He, Renewable Sustainable Energy Rev., 2014, 37, 550–559 CrossRef CAS.
- H. Wang and Z. J. Ren, Water Res., 2014, 66, 219–232 CrossRef CAS PubMed.
- S. Sevdaa, H. Yuan, Z. He and I. M. Abu-Reesh, Desalination, 2015, 371, 9–17 CrossRef.
- H. Liu, H. Hu, J. Chignell and Y. Fan, Biofuels, 2010, 1, 129–142 CrossRef CAS.
- K. Rabaey, P. Girguis and L. K. Nielsen, Curr. Opin. Biotechnol., 2011, 22, 371–377 CrossRef CAS PubMed.
- B. E. Logan, Appl. Microbiol. Biotechnol., 2010, 85, 1665–1671 CrossRef CAS PubMed.
- B. E. Logan, M. J. Wallack, K.-Y. Kim, W. He, Y. Feng and P. E. Saikaly, Environ. Sci. Technol. Lett., 2015, 2, 206–214 CrossRef CAS.
- Z. Ge, J. Li, L. Xiao, Y. Tong and Z. He, Environ. Sci. Technol. Lett., 2014, 1, 137–141 CrossRef CAS.
- P. Aelterman, K. Rabaey, H. T. Pham, N. Boon and W. Verstraete, Environ. Sci. Technol., 2006, 40, 3388–3394 CrossRef CAS PubMed.
- L. Zhuang, Y. Zheng, S. Zhou, Y. Yuan, H. Yuan and Y. Chen, Bioresour. Technol., 2012, 106, 82–88 CrossRef CAS PubMed.
- A. Gálvez, J. Greenman and I. Ieropoulos, Bioresour. Technol., 2009, 100, 5085–5091 CrossRef PubMed.
- I. Ieropoulos, J. Greenman and C. Melhuish, Int. J. Energy Res., 2008, 32, 1228–1240 CrossRef CAS.
- P. Ledezma, A. Stinchcombe, J. Greenman and I. Ieropoulos, Phys. Chem. Chem. Phys., 2013, 15, 2278–2281 RSC.
- B. Wang and J. I. Han, Biotechnol. Lett., 2009, 31, 387–393 CrossRef CAS PubMed.
- W. He, X. Zhang, J. Liu, X. Zhu, Y. Feng and B. E. Logan, Environ. Sci.: Water Res. Technol., 2016, 2, 186–195 CAS.
- Y. Dong, Y. Qu, W. He, Y. Du, J. Liu, X. Han and Y. Feng, Bioresour. Technol., 2015, 195, 66–72 CrossRef CAS PubMed.
- Y. Feng, W. He, J. Liu, X. Wang, Y. Qu and N. Ren, Bioresour. Technol., 2014, 156, 132–138 CrossRef CAS PubMed.
- F. Zhang, Z. Ge, J. Grimaud, J. Hurst and Z. He, Environ. Sci. Technol., 2013, 47, 4941–4948 CrossRef CAS PubMed.
- F. Zhang, K. S. Jacobson, P. Torres and Z. He, Energy Environ. Sci., 2010, 3, 1347–1352 CAS.
- Z. Ge, L. Wu, F. Zhang and Z. He, J. Power Sources, 2015, 297, 260–264 CrossRef CAS.
- B. Zhang, Z. Wen, S. Ci, S. Mao, J. Chen and Z. He, ACS Appl. Mater.
Interfaces, 2014, 6, 7464–7470 CAS.
-
L. S. Clesceri, A. E. Greenberg and A. D. Eaton, Standard Methods for the Examination of Water and Wastewater, 20th edn, American Public Health Association, Washington, DC, 1998 Search PubMed.
- J. Kim, K. Kim, H. Ye, E. Lee, C. Shin, P. L. McCarty and J. Bae, Environ. Sci. Technol., 2011, 45, 576–581 CrossRef CAS PubMed.
- Y. Zhang and I. Angelidaki, Water Res., 2015, 85, 177–184 CrossRef CAS PubMed.
- P. Kuntke, K. M. Smiech, H. Bruning, G. Zeeman, M. Saakes, T. H. Sleutels, H. V. Hamelers and C. J. Buisman, Water Res., 2012, 46, 2627–2636 CrossRef CAS PubMed.
- K. S. Jacobson, P. Kelly and Z. He, Water Environ. Res., 2015, 87, 252–257 CrossRef CAS PubMed.
- H. Wang, J. D. Park and Z. J. Ren, Environ. Sci. Technol., 2015, 49, 3267–3277 CrossRef CAS PubMed.
- Comparison of costs for wastewater management systems, Barnstable County Wastewater Cost Task Force (http://www.ccwpc.org/images/educ_materials/wwreports/cape_cod_ww_costs–4-10.pdf), 2010.
Footnote |
† Electronic supplementary information (ESI) available: The supplementary materials contain a table of effluent pH and a figure of construction costs of wastewater treatment systems of different scales. See DOI: 10.1039/c6ew00020g |
|
This journal is © The Royal Society of Chemistry 2016 |
Click here to see how this site uses Cookies. View our privacy policy here.