DOI:
10.1039/C5RA18328F
(Paper)
RSC Adv., 2016,
6, 163-173
The role of shear conditions on floc characteristics and membrane fouling in coagulation/ultrafiltration hybrid process – the effect of flocculation duration and slow shear force
Received
8th September 2015
, Accepted 4th December 2015
First published on 21st December 2015
Abstract
The impact of shear conditions during coagulation on the ultrafiltration permeate flux in a coagulation–ultrafiltration (C–UF) process was investigated. Different flocculation durations and slow shear forces were used to determine the impact of shear conditions on the C–UF process. Floc characteristics, including the average size, fractal dimension and flocs size distribution under different coagulation conditions were studied. Moreover, the normalized flux and reversibility of membrane fouling were also analyzed to investigate membrane fouling. The results indicated that flocs formed at a shorter flocculation duration with small fractal dimensions and easily developed a cake layer with larger pores and a fluffy structure on the membrane surface. However, a higher frequency of small-sized flocs still remained at a flocculation time of 5 min, which was attributed to inadequate collision among particles, which could cause severe membrane fouling. As a result, slow stirring for an appropriately short time (10 min) and the reduction of low shear force (G = 8 s−1) are conducive for forming flocs with a loose and porous structure without the occurrence of more small particles in water, which seemed to effectively improve the membrane permeability.
1. Introduction
In drinking-water treatment processes, membrane technology is an attractive alternative for providing high-quality water that can satisfy the requirements of stricter water quality regulations.1 However, fouling is one of the main disadvantages of membrane ultrafiltration processes, with the result that a decline in flux results in higher water treatment costs and the deterioration of the membrane.2 Different pre-treatments before ultrafiltration have been widely applied as methods to reduce membrane fouling, such as coagulation, adsorption and oxidation. A combination of powder active carbon (PAC) adsorption and UF has been reported to more effectively mitigate membrane fouling.3 Oxidation before ultrafiltration can decrease the density of organic matter in effluents and remove oxidation intermediates, which could reduce the severity of membrane fouling by the removal of foulants on the membrane surface.4,5
Pre-coagulation before UF, especially by “in-line” chemical coagulation, can significantly reduce membrane fouling.6,7 The effects of pre-coagulation on membrane permeability are mainly related to the coagulation conditions, including the types and dosages of the coagulants and the mixing mode.8,9 Pikkarainen et al.10 have stated that Fe- and Al-based coagulants caused similar hydraulic resistance properties in membrane filtration, but Fe-based coagulants would result in strong coloration on the surface of the water. Choi and Dempsey11 investigated the influence of alum concentration on membrane fouling in polyethersulfone flat-sheet ultrafiltration and found that “in-line” coagulation can improve the hydraulic removal of filter cake. Flocs that are formed under charge neutralization conditions lead to lower hydraulic resistance than those formed under sweep floc conditions.12 Significantly, the properties of aggregates formed under different coagulation conditions could affect membrane fouling.13–15 It should be worthwhile to note that the structure of particle aggregates is also closely related to the flocculation duration and shear conditions involved in the coagulation/flocculation process.
In various mechanical aquatic systems, particles and flocs in suspension are highly dependent on varying flocculation durations and flow conditions. In a pre-coagulation/ultrafiltration process, the circulation of suspensions induced by different coagulation conditions most likely influences the characteristics of flocs and also the structure of the cake layer on the membrane surface. Rossini et al. investigated the influence of a rapid mixing time on the final efficiency of coagulation and found that a short duration of rapid mixing was helpful in producing lower residual turbidity.16 Wahlberg et al.17 have shown in their work that activated sludge flocculated by mechanical means rapidly grew by 99% within 10 minutes under batch conditions. Under the same conditions, the properties and configurations of flocs formed during the whole flocculation process could extensively change with different flocculation times. However, little attention has been paid to the effect of flocculation duration on the performance of a coagulation–UF process. Biggs and Lant18 considered that the larger the shear force was, the smaller was the average size of flocs that aggregated under steady-state conditions. Other works have reported that the morphology of flocs was strongly dependent on how the shear rate (G) was applied when a polymeric flocculant was used.19,20 He et al. have investigated the evolution of the size and structure of flocs under a low shear force.21 Klimpel and Hogg22 thought that a higher mixing speed caused a large fractal dimension of the floc structure. Up to now, previous studies were mainly focused on the relationship between the characteristics of flocs and conventional coagulation/flocculation processes. However, there was a lack of a sufficiently comprehensive and thorough understanding of the relationship between the characteristics of flocs formed under different pre-coagulation conditions and the subsequent membrane behaviors and fouling mechanisms in a coagulation–ultrafiltration process. Our previous paper investigated the influence of the breakage process of flocs on membrane fouling in a coagulation/ultrafiltration process, which concentrated on the effect of the additional coagulants polyaluminum chloride and polyacrylamide. Other articles specialized in the comparison of the characteristics of flocs formed by different coagulants as well as their distinct effects on membrane fouling.23,24 Little research has been carried out on the effects of different flocculation durations and low shear forces during coagulation and membrane performance.
This work aimed to investigate the impact of different flocculation durations and low shear forces on a coagulation process in order to provide a better mechanistic understanding of the changes in properties of aggregates on membrane fouling in the subsequent ultrafiltration process. A series of modified flocculation tests were conducted at different flocculation durations and slow mixing speeds prior to UF. The main investigation focused on the size, structure and surface characteristics of flocs in pre-coagulation combined with a UF membrane process. The reversibility of membrane fouling was also investigated.
2. Methods and materials
2.1 Suspension
Kaolin clay (Tianjin, China) and humic acid (Shanghai, China) were used to test a water sample. A suspension of kaolin clay was prepared by dissolving 50.0 g kaolin clay in 1 L deionized water with continuous magnetic stirring for 24 h. After sedimentation for 1 h, 800 mL of supernatant was used as the stock suspension of kaolin clay.
A 10 g sample of humic acid (Jufeng, Shanghai, China) was dispersed in 0.1 mM L−1 NaOH and mixed for 24 h with a magnetic stirrer. The suspension was filtered using a 0.45 μm fiber filter membrane. The pH of the filtered solution was adjusted to 7.5 using 0.01 mol L−1 NaOH or HCl and the solution diluted to 1000 mL in a measuring flask.25 The solution was stored in the dark.
Harbin tap water, China, has an alkalinity of 15 mg L−1 as CaCO3 and a pH of around 7.2. A small dose of humic acid was added to the testing water to reduce disturbances due to divalent metal ions such as Ca2+ and Mg2+ in the tap water.26 For flocculation tests, the stock solution was diluted in the tap water, containing 100 mg L−1 clay and 2 mg L−1 humic acid. The initial turbidity was about 90 NTU. During the experimental program, the temperature of the solution was 22 ± 2 °C.
2.2 Coagulants
Polyaluminum chloride (PACl) (28% quality, calculated as Al2O3), the basicity of which was 72.3%, was prepared at a concentration of 1% by dissolving 5 g reagent in 500 mL deionized water.27 This coagulant solution was stored for 24 h for the flocculation tests and directly pipetted into the testing water without further dilution.
2.3 Apparatus
A modified version of the jar test process was used in this research. A non-intrusive optical sampling technique was applied to capture digital images of particles from the moment of addition of the coagulant, which were then analyzed to determine particle size distributions and geometrical properties and for calculations of the fractal dimension.28 This basic procedure has been widely used by our research fellows.21,26,29 Because there was no sample handling during measurements, there was no concern about destroying the characteristics of the floc. This coagulation setup, which was introduced in detail in our previous studies,30,31 included an in situ recognition system, a rectangular stirred tank (homemade) and an R1342 model impeller (IKA, Germany). A schematic diagram of this setup is shown in Fig. 1.
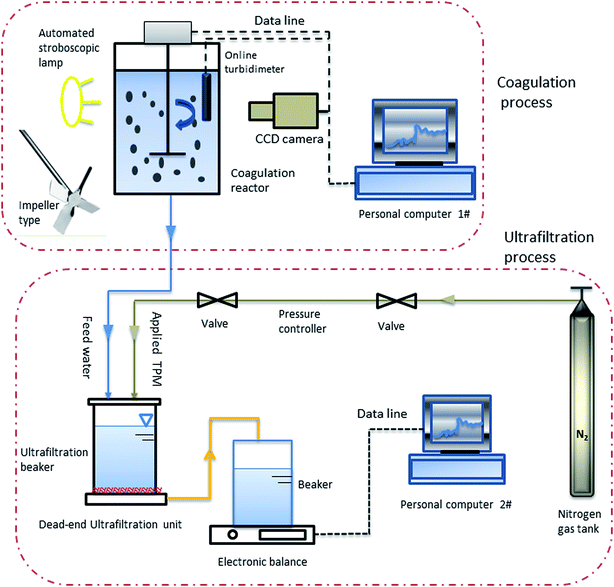 |
| Fig. 1 Schematic of pre-coagulation/ultrafiltration experiments. | |
2.4 Coagulation procedure
On adding an optimal dose of PACl (around 0.08 mM Al) to the reactor, the sample of testing water was mixed rapidly at 400 rpm (G ≈ 175 s−1) for 60 s.21 This was followed by slow stirring at 90 rpm (G ≈ 20 s−1) for different flocculation durations to allow flocs to grow. After 30 min of sedimentation, the turbidity of the supernatant was measured by an online turbidimeter (100AW, WTW, Germany). After stirring at 400 rpm for 60 s to break the flocs, the stirring speed was returned to 90 rpm for 15 min to allow flocs to regrow. To investigate the effect of different slow mixing speeds, the rapid mixing speed was set at 400 rpm for 60 s, then at shear rates from 8 to 20 s−1 for 15 min, at 400 rpm for 60 s to break the flocs and finally reduced to 90 rpm for the flocs to regrow.
2.5 Analysis of floc morphology
The size, dp, of the irregular shape of a floc can be calculated in terms of the equivalent diameter by: |
 | (1) |
where Ap is the projected area of the floc. Then, the average size and size distribution of flocs in more than 20 images taken within a minute were used to determine the size of flocs at the corresponding instant.21
For a 2D projected image of a particle, the value of the fractal dimension (Df) indicates the surface morphology of the aggregate in a two-dimensional projection according to:
where
P is the perimeter of the aggregate and
Df is the two-dimensional fractal dimension of the object. Values range from
Df = 1, which indicates the projected area of a linear structure, to
Df = 2 for a circular structure. As the area of an object becomes larger, the perimeter increases more quickly than for Euclidean objects, which means that the boundary of the object becomes more convoluted and its shape more irregular. In our study, flocs in more than 10 images taken within a minute were used to calculate the value of
Df at the corresponding instant.
2.6 Ultrafiltration procedure
A dead-end batch ultrafiltration unit with a cylindrical beaker of 400 mL capacity (Amicon 8400, Millipore, US) was used for ultrafiltration experiments and a schematic diagram is also shown in Fig. 1. An ultrafiltration membrane (Mosu, Shanghai, China) with a molecular weight cut-off (MWCO) of 100 kDa was used for ultrafiltration after it was “wetted” to its optimal operating conditions. The membrane material was polyethersulfone (PES) and the effective membrane area was 50.24 cm2. The membrane pore size was about 0.005–0.01 μm. A fresh piece of membrane was used in every ultrafiltration experiment. The effluent solution from coagulation (after different flocculation durations and the use of a slow stirring speed) was gently decanted from the coagulation tank without sedimentation to the dead-end filtration unit and filtered through the ultrafiltration membrane. A constant pressure of 0.15 MPa was kept with nitrogen gas. The instantaneous mass of cumulative permeate was measured by an electronic balance (SI-2002, Denver Instrument, China) and recorded via a personal computer equipped with a data acquisition system.
Every ultrafiltration test comprised three periods and each period included three steps, and the operating sequences are shown in Fig. 2: (1) 400 mL coagulation effluent solution was filtered through the UF membrane; (2) the ultrafiltration membrane was turned over and the opposite face used, then backwashing was performed with 50 mL ultrapure water; (3) the ultrafiltration membrane was repositioned and the initial face used, then 100 mL ultrapure water was filtered to improve membrane flux after back washing. The flux of a membrane (J) is used as a critical indicator to determine membrane fouling. The initial membrane flux of ultrapure water is represented as Jp(0). The initial flux and final flux in each period are represented as Ji(n) and Jf(n), respectively. Here, n (1–3) is the cycle number. Based on this, the normalized permeate flux of the ultrafiltration process is represented as J/Jp(0). If the value of J/Jp(0) decreases, this means fouling of the membrane has become severe.
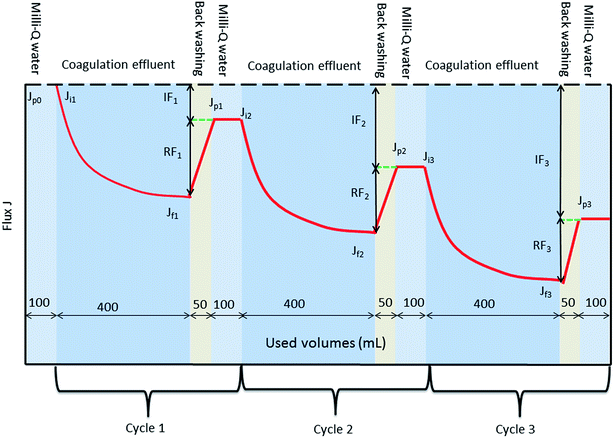 |
| Fig. 2 Schematic of ultrafiltration operating sequences. | |
If a pollutant on the membrane surface can be removed by a hydraulic backwash process, this pollutant is denoted as reversible fouling (RF), whereas the remaining contaminants on the surface of the membrane are named irreversible fouling (IF). The sum of both kinds of fouling is total fouling (TF). Jermann et al.32 reported that RF, IF and TF can be calculated by the following equations:
|
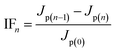 | (3) |
|
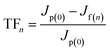 | (4) |
3. Results and discussion
3.1 Effect of flocculation duration on coagulation–ultrafiltration
3.1.1 Effect of flocculation duration on the evolution of floc characteristics. The flocculation duration is expected to have a major effect on the size and shape of flocs. In addition, the characteristics of flocs such as their size and compaction degree are very important for continuous membrane filtration. Therefore, the average size and fractal dimension (Df) of flocs were investigated and the results are shown in Fig. 3. The general shape of the curves is broadly similar in all cases. The average size of the flocs increased with the coagulation time during the floc aggregation process, regardless of the specific duration. When the stirring rate was increased to 400 rpm, there was a rapid reduction in average size as a result of floc breakage. After the breakage period, there were different degrees of recovery of average size, which shows that the agglomeration time has a significant impact on the reversibility of floc breakage. Specifically, with a shorter flocculation time flocs have a smaller average size at the end of the aggregation stage. A similar tendency in growth was found for a flocculation time of 10 min, when the average size of flocs was larger than that at 5 min. After coagulation for 15 and 20 min, the average size of flocs still continuously increased. However, both of these attained a maximum value nearly simultaneously after 10 min then fluctuated slightly on the plateau. It can be seen that there needed to be adequate time for suspended particles to aggregate into clusters, but the sizes of flocs do not persist with an increase in time. The traditional coagulation process is preferred as it retains large-sized flocs due to the following sedimentation unit. However, for the coagulation–ultrafiltration process, particles of a size that is larger than the membrane pore size could be rejected on the membrane surface and further removed by hydraulic or chemical backwashing.33 Therefore, there is no necessity to produce flocs of too large a size and a shorter flocculation time has more research significance.
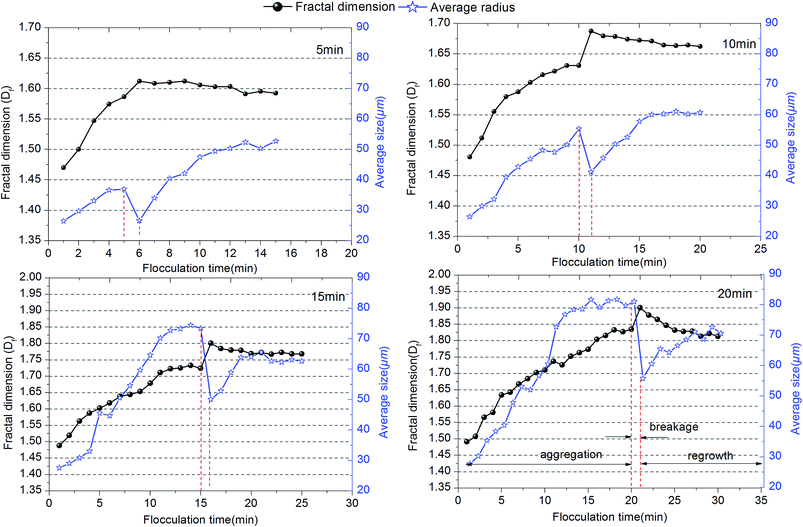 |
| Fig. 3 Variation of average size and fractal dimension of flocs for different flocculation durations. | |
Howe and Clark34 stated that the remaining dissolved organic matter (DOM) caused very little fouling of an ultrafiltration membrane after the colloidal fraction was removed. As a result, external membrane fouling by a cake layer should be investigated thoroughly. Cake layers consist of flocs formed during the coagulation process; hence, the structure of flocs directly influences membrane fouling.35 The fractal dimension of flocs has been widely used to evaluate the morphology of flocs.21,36 In this study, the evolution of the fractal dimension (Df) of flocs with different flocculation durations was investigated to identify the degree of floc compaction. The value of Df of flocs increased with the coagulation time during the floc aggregation process for different flocculation times, which suggests that much more compact flocs were developed. However, the value of the fractal dimension in the steady state increased with an increase in the flocculation time and followed the order of 20 min > 15 min > 10 min > 5 min. The large values of Df indicate that a higher degree of development and compaction of flocs began to be produced with an increase in flocculation time. Densely packed aggregates had a higher value of Df and were good at settling, whereas lower values of Df resulted from large, highly branched and loosely bound structures that are beneficial in reducing membrane fouling. From the results in Fig. 3, it can be seen that flocs formed at 5 min have the smallest fractal dimension, which appeared to be the best for alleviating membrane fouling. However, a shorter flocculation time would provide an incomplete reaction process for scattered particles to aggregate into large flocs. Thus, small particles, especially of the size of nanoscale primary particles, are still present in water systems, which may be one of the main factors that determine the density of the cake layer and increase membrane resistance. Therefore, as well as the size and fractal dimension of flocs, their particle size distribution is also a significant factor with an impact on membrane fouling.
3.1.2 Particles (flocs) size distribution at different flocculation durations. In order to investigate the coagulation–ultrafiltration process in more detail, the size distribution of flocs at different durations of flocculation was investigated. Four samples of flocs at different durations of slow stirring (5 min, 10 min, 15 min and 20 min) were taken at the end of the flocculation stage. Images of flocs were captured by the in situ recognition system and analyzed by the software, as described in Section 2. Fig. 4a shows the size distribution of flocs in the steady state at different flocculation durations. Firstly, the major peak for a flocculation duration of 5 min is to the left of all the other conditions, which implies that the frequency of small-sized flocs was notably reduced with an increase in flocculation time. However, at 10 min even the average size of flocs is not large enough and the probability of small particles is dramatically decreased. Considering durations of slow stirring of 15 and 20 min, the flocs reached a large size, which was expected as a longer duration of slow stirring would promote the aggregation of particles. For longer durations of slow stirring, the average size of flocs rapidly increased at the initial stage and then further increases in size were restricted, which resulted in a steady-state floc size and represents a dynamic balance between shear-induced aggregation and breakage.30 It can be speculated that a very long duration of slow stirring mainly contributes to further increasing the compactness of flocs, instead of affecting the size distribution of flocs. As a result, a longer flocculation duration seems more conducive to the traditional coagulation–sedimentation process. However, in contrast to the traditional coagulation process, which forms large and tight flocs, the main purpose was to decrease the amount of small particles and change the structure of the cake layer on the membrane surface. Cho et al. have also reported that a higher probability of small particles could intensify membrane fouling.37 Therefore, it can be seen that to appropriately shorten the flocculation duration has much more potential to retard membrane fouling.
 |
| Fig. 4 Effect of flocculation duration on (a) size distribution of flocs and (b) residual turbidity. | |
As shown in Fig. 4b, the residual turbidity after static sedimentation of flocs gradually decreased after 10 min and remained around 5 NTU with an increase in flocculation duration. Owing to the fact that residual turbidity after settling is mainly determined by small particles, especially nanoscale particles, the probability of small particles was compared with the residual turbidity.38 The lower was the proportion of small particles, the lower was the residual turbidity. A larger average size did correspond to a lower frequency of small particles and lower residual turbidity (Fig. 3 and 4). However, comparing durations of slow stirring of 10 min and 20 min, a twofold increase in flocculation duration did not dramatically lessen the amount of small particles and the residual turbidity (Fig. 4), but instead promoted the compactness of flocs (Fig. 3). As is well known, a higher density of flocs causes a void-free cake layer on the membrane surface and further promotes membrane fouling. Therefore, the flocculation duration can significantly influence the characteristics of flocs, such as their average size, structure and size distribution, which could further influence the efficiency of the subsequent ultrafiltration process.
3.1.3 Effect of flocculation duration on membrane flux. UF experiments were performed by filtering the pre-coagulation suspensions at different flocculation durations. The normalized permeate fluxes (J/Jp(0)) versus the filtration volume are shown in Fig. 5. In our previous study,15 the same raw water was used and the normalized permeate fluxes decreased dramatically from 1 to 0.4 in the end. In contrast, it was observed that pre-coagulation significantly increased the permeate fluxes, independently of the flocculation duration. Specifically, the improvement in the flux was followed with an increase in the flocculation time. At a duration of slow stirring of 5 min, the final value of J/Jp(0) was about 0.8, whereas the final normalized flux increased to 0.9 at a duration of slow stirring of 10 min. In contrast, this value tended to decrease with a further increase in the flocculation time. This somewhat implied that the flocculation time could influence the performance of ultrafiltration. Coagulation effluents, which are the feed water of ultrafiltration, contain different sizes of flocs formed at various flocculation durations. According to the results from Fig. 4, there are more small particles that remained in the coagulation effluent at a flocculation time of 5 min and these particles proved to be difficult to remove by sedimentation. Particles on a scale of several hundred nanometers are transported by a drag force and stay on the surface of the membrane to lead to membrane fouling. It seemed that membrane fouling mainly relied on the number of small particles in solution in water. However, the results showed that the flux ratio decreased with a decrease in the amount of small particles. The fractal dimension of flocs increased with an increase in the duration of slow stirring (Fig. 3), which meant a higher density of flocs was formed. Normally, the higher is the fractal dimension of flocs, the higher is the density of the cake layer developed by flocs.13 As a result, the cake layer on a membrane surface formed by flocs with lower density may have higher porosity and a looser structure. This cake layer acts as another filter shield and more fine colloids and other pollutants could be adsorbed into a cake layer with a porous structure, which further confirms that the characteristics of coagulated flocs play an important role in membrane filtration processes. For longer flocculation times, flocs with a higher effective density are preferable for the traditional coagulation process because of their better ability to settle in the subsequent settling unit. However, such aggregates are compressed easily by external pressure and build up a compact cake layer to cause higher specific resistance to the water flow. Based on the discussion above, a rather shorter duration of slow stirring (10 min) was much more adequate in improving the permeability of water through the cake layer on the membrane surface to reduce membrane fouling.
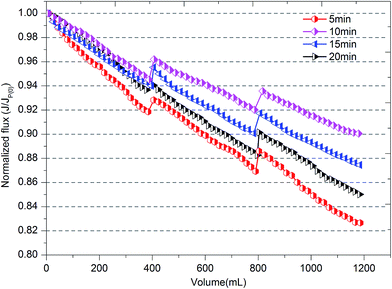 |
| Fig. 5 Normalized UF permeate flux profiles at different flocculation durations. | |
3.1.4 Effect of different flocculation durations on reversibility of membrane fouling. The previous literature has shown that particle sizes smaller than about 3 nm caused very little membrane fouling.39 In our study, the results meant that nanoscale particles that were retained on the membrane surface would not lead to internal membrane fouling, instead of external fouling. The part of external fouling that could be removed by hydraulic backwashing was considered as reversible fouling (RF), whereas the remaining part on the membrane surface was irreversible fouling (IF). Both RF and IF, which occurred during membrane filtration at different flocculation times, are shown in Fig. 6. Total fouling and irreversible fouling continued to increase with progressive cycles of filtration regardless of the flocculation duration, which indicated that foulants constantly accumulated on the membrane surface. For shorter flocculation times, the proportion of reversible fouling was larger than that for longer durations of slow stirring. From the results in Fig. 3, the fractal dimension of flocs is relatively smaller at shorter flocculation durations than that at longer durations of slow stirring, which suggests that a cake layer that is formed with a lower fractal dimension has relatively larger pores and a fluffy structure. A cake layer that was loose enough could be removed by hydraulic backwashing to reduce membrane fouling, whereas a relatively compact cake layer was still on the surface of the membrane, which resulted in a continuous increase in membrane resistance and decrease in flux. Especially for a duration of slow stirring of 5 min, decreases in the permeability of the cake layer resulted from incomplete aggregation of particles and a greater number of residual small particles. It was more difficult for smaller particles to be removed by backwashing, which further causes severe irreversible fouling. The higher level of irreversible membrane fouling may mainly be caused by the compact cake layer and number of small particles, which could be improved to appropriately shorten the flocculation duration.
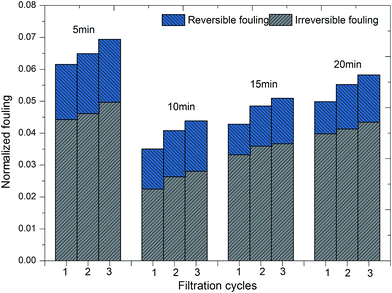 |
| Fig. 6 Effect of different flocculation durations on the reversibility of membrane fouling. | |
3.2 Effect of low shear force on coagulation–ultrafiltration process
3.2.1 Effect of low shear force on the evolution of floc characteristics. As well as the flocculation duration being very important for optimizing the coagulation/ultrafiltration hybrid process, the slow stirring force can also influence the efficiency of filtration. Fig. 7 shows the evolution of the size and structure of flocs under varying low shear forces (G < 20 s−1) at a flocculation time of 15 min. The average size of flocs before breakage firstly increased as the slow stirring speed increased. As is well known, there is a limit to the size of flocs under the given conditions of slow stirring.40 At a lower shear force (G = 8 s−1 and 10 s−1), the average size of flocs reached a rather larger steady-state size. It was expected that sufficient stirring time would promote the collision and aggregation of particles. At G = 15 s−1, the flocs evolved to the largest size at the steady state and then displayed a slight decline at a shear force of 20 s−1. With an increase in the shear rate, more sufficient collisions took place to make larger particles, while floc breakage could occur as well due to more frequent collisions of particles under more vigorous stirring, representing a dynamic balance between floc growth and breakage. Serra et al.41 found that the size of latex flocs formed under steady-state conditions was always reduced at larger shear rates (G > 20–30 s−1). Although the diameter of particles is inversely proportional to the specific resistance of cake, as stated in the well-known Carman–Kozeny equations,7 the resulting permeate flux is most likely affected by other factors.
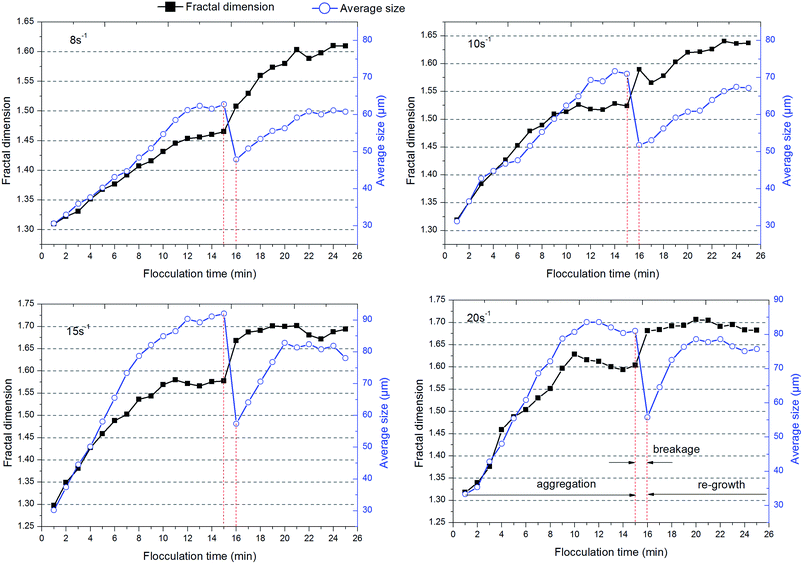 |
| Fig. 7 Variation of average size and fractal dimension of flocs for different low shear forces. | |
The fractal dimension of flocs, which is closely related to the structure of aggregates and efficiency of ultrafiltration, was measured at different shear rates and flocculation times and the results are also provided by Fig. 7. It was obvious that the fractal dimension of flocs increased as flocs formed under the different shear conditions that were adopted. Basically, dispersed particles rapidly aggregated as a result of the shear conditions at the start of the experiment and simultaneously some pores were formed in the interior of flocs. With the growth of flocs, the agglomeration of microclusters gradually plays a significant role in the development of flocs. Small, compact flocs could have the chance to enter into the inner holes of large flocs and then the fractal dimension of flocs would increase with the growth of flocs. Based on the results for the average size of flocs, a higher shear force leads to a greater probability of breaking of large flocs. Large shear rates (G = 15 and 20 s−1) are suitable for the conventional sedimentation process due to the better ability to settle of high-density flocs, whereas low shear forces (G = 8 s−1) seem to be more appropriate for the ultrafiltration process due to porosity and loose flocs. After the breakage stage, the fractal dimension of flocs is higher than that of flocs before breakage, which is consistent with previous studies.19,42 This is probably due to the fact that surface bonding around the periphery is destroyed owing to higher shear forces and some inner pores that had been hidden by aggregates were re-available for other small, compact clusters or particles, which improves the degree of compactness of flocs.
3.2.2 Effect of low shear force on particle size distribution. The size distribution of flocs under different shear forces is shown in Fig. 8. With an increase in the shear force, the probability of numbers of small particles was slightly decreased. However, the size distribution of flocs under higher applied shear (G = 20 s−1) shifted towards smaller sizes and the average size of flocs also decreased. It is most probable that particles were able to collide and aggregate into larger flocs with gentle stirring, whereas breakage possibly occurred under the larger shear force and led to the increase in the numbers of small particles. Because the frequency of small flocs was a little higher for the higher speed of slow mixing, it was expected that these would lead to higher residual turbidities. However, this was not the case, as the results show in Fig. 8b. When the shear force was 8 s−1, the residual turbidity was around 7 NTU. There was a steady decrease in residual turbidity as the speed of slow stirring increased to 20 s−1. The result may be that the density of flocs increases with an increase in the stirring speed, giving higher settling rates regardless of the smaller sizes of flocs.38 Higher shear rates during the slow stirring process could produce flocs with a higher effective density, which was beneficial for the sedimentation process. In contrast, flocs formed under a low shear force have a loose and porous structure without the presence of more small particles in water, which seemed to effectively improve the membrane permeability.
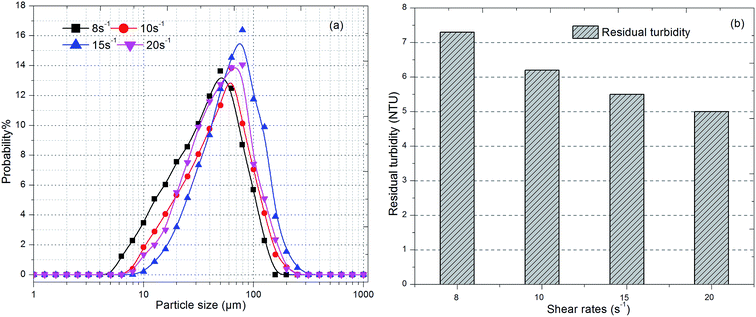 |
| Fig. 8 Effect of different low shear forces on (a) size distribution of flocs and (b) residual turbidity. | |
3.2.3 Effect of low shear force on membrane filtration. Coagulation under different shear forces was performed to investigate the effect of different conditions of slow stirring on ultrafiltration performance. The associated normalized permeate fluxes are plotted against filtration volume in Fig. 9. It was found that the declining trends in flux varied depending on the shear rates applied in the system. For raw water without coagulation, the final membrane flux was about 0.4 and this result could be found in our previous study.15 It was observed that pre-coagulation under a low shear force significantly increased the permeate fluxes. Specifically, the improvement in flux at a shear rate of 8 s−1 was the most effective because of the largest eventual permeate flux. The highest speed of slow stirring was found to contribute to the smallest improvement in membrane flux. On the basis of the discussion above, it was concluded that different floc morphologies formed under different shear forces could have an impact on the C–UF hybrid system in terms of membrane permeability. Even if the average size of flocs produced under a lower shear force is smaller than that under intensive conditions of slow stirring, the flocculation duration was enough for the collision and aggregation of dispersed particles, because the probability of small particles at the end of the flocculation process was not distinctly different. Therefore, there may be another factor that influences the efficiency of ultrafiltration as well as the particle size distribution. It is obvious from the results that an increase in shear force resulted in aggregates with a higher fractal dimension, which indicates a more compact floc structure. In a previous study it has been stated that aggregates with a loose structure produce less resistance in membrane ultrafiltration, whereas tight flocs that contributed to a cohesively structured cake layer could increase the resistance in UF and aggravate the declines in flux.43 A low shear force tends to form a fluffy cake layer and definitely helps alleviate declines in flux. Therefore, the application of a low shear force (G = 8 s−1) is more significant in terms of research and feasibility.
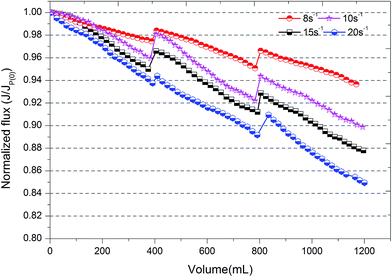 |
| Fig. 9 Normalized UF permeate flux profiles under different low shear forces. | |
3.2.4 Effect of low shear force on reversibility of membrane fouling. Both reversible fouling and irreversible fouling, which occurred at various speeds of slow stirring, are illustrated in Fig. 10. There were dramatic improvements in RF and IF with an increase in the shear force in the slow stirring procedure. This was probably because mild stirring conditions could cement small particles together to form floc aggregates, then a smaller quantity of small-sized substances were deposited in membrane pores. Besides, increased shear rates would force large-sized flocs to break at the end of the flocculation stage, which contributes to the deterioration of the structure of the flocs and the occurrence of more microparticles. This result may lead to small particles being trapped in the membrane pores and not easily removed by hydraulic backwashing. A higher fractal dimension indicates a higher effective density, which results in a faster settling velocity of flocs, which is preferable in a conventional coagulation–sedimentation process for water treatment but not in a coagulation–UF system. Flocs with a lower density could form a cake layer of higher porosity, whereas flocs with higher fractal dimensions resulted in more severe fouling in hybrid coagulation–UF systems due to relatively regularly shaped flocs being more easily compressed by external pressure.44,45 In our study, the structure of flocs formed under a low shear force became incompact and porous, which decreased irreversible fouling. Irreversible fouling was increased at a shear force of 20 s−1, even though the probability of small particles was lower than that at a shear rate of 8 s−1. The results indicated that the reversibility of fouling after hydraulic washes during multiple filtrations of coagulated water was mainly governed by the morphology of flocs and a low shear force in a slow mixing stage in the pre-coagulation process could effectively retard total and irreversible fouling in the ultrafiltration process.
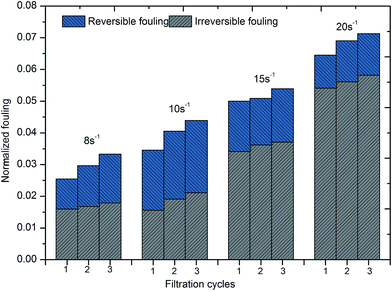 |
| Fig. 10 Effect of different low shear forces on the reversibility of membrane fouling. | |
4. Conclusions
The main conclusions of this work are as follows:
1. A coagulation/ultrafiltration process was conducted at different flocculation durations. A longer flocculation duration will produce flocs with a large average size and fractal dimension, whereas a shorter flocculation time forms small-sized flocs with a small fractal dimension. Flocs with a small fractal dimension have loose and porous properties, which easily lead to a cake layer with larger pores and a fluffy structure on the membrane surface. With a comprehensive consideration of the size distribution of flocs, a higher frequency of small-sized flocs still remained at a flocculation time of 5 min, attributing to inadequate collisions among particles, which would cause severe membrane fouling. Therefore, a rather shorter duration of slow stirring (10 min) was much more adequate in improving the permeability of water through the cake layer on the membrane surface to reduce membrane fouling.
2. A slow shear force was also an important factor that deserved to be investigated during the coagulation/ultrafiltration process. The average size of flocs increased as the speed of slow stirring increased, and the same was the case with the fractal dimension of flocs. However, the size distribution of flocs under higher applied shear (G = 20 s−1) shifted towards smaller size and the average size of flocs also decreased owing to breakage. As a result, flocs formed under a low shear force (G = 8 s−1) have a loose and porous structure without the presence of more small particles in water, which seemed to effectively improve the membrane permeability.
Acknowledgements
This study was supported by the National Science and Technology Major Project of Twelfth Five Years (Grant No. 2014ZX07201-012-2, Grant No. 2013ZX07201007-002), the National Natural Science Foundation of China (No. 51208140), the National Innovation Team supported by the National Science Foundation of China (Grant No. 50821002), and the State Key Laboratory of Urban Water Resource and Environment (Harbin Institute of Technology) (Grant No. 2012DX07). Comments and suggestions from anonymous reviewers are greatly acknowledged.
References
- W. Yu, L. Xu, J. Qu and N. Graham, J. Membr. Sci., 2014, 459, 157–168 CrossRef CAS.
- H. Jia, H. Zhang, J. Wang, H. Zhang and X. Zhang, RSC Adv., 2015, 5, 78738–78744 RSC.
- J. Haberkamp, A. S. Ruhl, M. Ernst and M. Jekel, Water Res., 2007, 41, 3794–3802 CrossRef CAS PubMed.
- T. Liu, Z. L. Chen, W. Z. Yu and S. J. You, Water Res., 2011, 45, 2111–2121 CrossRef CAS.
- H.-P. Xu, Y.-H. Yu, W.-Z. Lang, X. Yan and Y.-J. Guo, RSC Adv., 2015, 5, 13733–13742 RSC.
- R. H. Peiris, M. Jaklewicz, H. Budman, R. L. Legge and C. Moresoli, Water Res., 2013, 47, 3364–3374 CrossRef CAS.
- K. Listiarini, D. D. Sun and J. O. Leckie, J. Membr. Sci., 2009, 332, 56–62 CrossRef CAS.
- K. Kimura, T. Maeda, H. Yamamura and Y. Watanabe, J. Membr. Sci., 2008, 320, 356–362 CrossRef CAS.
- R. Bergamasco, L. C. Konradt-Moraes, M. F. Vieira, M. R. Fagundes-Klen and A. M. S. Vieira, Chem. Eng. J., 2011, 166, 483–489 CrossRef CAS.
- A. T. Pikkarainen and S. J. Judd, Water Res., 2005, 39, 1424 CrossRef CAS.
- K. Y. J. Choi and B. A. Dempsey, Water Res., 2004, 38, 4271–4281 CrossRef CAS.
- J. Moon, M. S. Kang, J. L. Lim, C. H. Kim and H. D. Park, Desalination, 2009, 247, 271–284 CrossRef CAS.
- W. Z. Yu, J. H. Qu and J. Gregory, Chem. Eng. J., 2015, 262, 676–682 CrossRef CAS.
- J.-L. Lin, C. Huang, C.-J. M. Chin and J. R. Pan, Water Res., 2008, 42, 4457–4466 CrossRef CAS PubMed.
- M. Yao, J. Nan, T. Chen, D. Zhan, Q. Li, Z. Wang and H. Li, J. Membr. Sci., 2015, 491, 63–72 CrossRef CAS.
- M. Rossini, J. G. Garrido and M. Galluzzo, Water Res., 1999, 33, 1817–1826 CrossRef CAS.
- E. J. Wahlberg, T. M. Keinath and D. S. Parker, Water Environ. Res., 1994, 66, 779–786 CrossRef CAS.
- C. A. Biggs and P. A. Lant, Water Res., 2000, 34, 2542–2550 CrossRef CAS.
- P. T. Spicer, S. E. Pratsinis, J. Raper, R. Amal, G. Bushell and G. Meesters, Powder Technol., 1998, 97, 26–34 CrossRef CAS.
- P. T. Spicer and S. E. Pratsinis, Water Res., 1996, 30, 1049–1056 CrossRef CAS.
- W. P. He, J. Nan, H. Y. Li and S. N. Li, Water Res., 2012, 46, 509–520 CrossRef CAS.
- R. C. Klimpel and R. Hogg, J. Colloid Interface Sci., 1986, 113, 121–131 CrossRef CAS.
- W. Xu, B. Gao, Y. Wang, Q. Zhang and Q. Yue, Chem. Eng. J., 2012, 181–182, 407–415 CrossRef CAS.
- W. Xu, B. Gao, R. Mao and Q. Yue, J. Hazard. Mater., 2011, 193, 249–256 CrossRef CAS.
- W. Yu, T. Liu, J. Gregory, L. Campos, G. Li and J. Qu, J. Membr. Sci., 2011, 385–386, 194–199 CrossRef CAS.
- M. Yao, J. Nan and T. Chen, Desalination, 2014, 354, 116–124 CrossRef CAS.
- W.-Z. Yu, H.-J. Liu, L. Xu, J.-H. Qu and N. Graham, J. Membr. Sci., 2013, 446, 50–58 CrossRef CAS.
- R. K. Chakraborti, K. H. Gardner, J. F. Atkinson and J. E. van Benschoten, Water Res., 2003, 37, 873–883 CrossRef CAS.
- J. Nan and W. He, Desalin. Water Treat., 2012, 41, 35–44 CrossRef.
- J. Nan, W. He, X. Song and G. Li, J. Environ. Sci., 2009, 21, 1059–1065 CrossRef CAS.
- W. He and J. Nan, Desalin. Water Treat., 2012, 41, 26–34 CrossRef.
- D. Jermann, W. Pronk, R. Kagi, M. Halbeisen and M. Boller, Water Res., 2008, 42, 3870–3878 CrossRef CAS.
- B. Ma, W. Yu, W. A. Jefferson, H. Liu and J. Qu, Water Res., 2015, 71, 140–149 CrossRef CAS.
- K. J. Howe and M. M. Clark, Environ. Sci. Technol., 2002, 36, 3571–3576 CrossRef CAS.
- F. Qu, H. Liang, J. Zhou, J. Nan, S. Shao, J. Zhang and G. Li, J. Membr. Sci., 2014, 449, 58–66 CrossRef CAS.
- P. Jarvis, B. Jefferson and S. A. Parsons, Water Res., 2006, 40, 2727–2737 CrossRef CAS.
- M. H. Cho, C. H. Lee and S. Lee, Desalination, 2006, 191, 386–396 CrossRef CAS.
- W.-Z. Yu, J. Gregory, L. Campos and G. Li, Chem. Eng. J., 2011, 171, 425–430 CrossRef CAS.
- B. Ma, W. Yu, H. Liu and J. Qu, Water Res., 2014, 51, 277–283 CrossRef CAS PubMed.
- F. E. Torres, W. B. Russel and W. R. Schowalter, J. Colloid Interface Sci., 1991, 142, 554–574 CrossRef CAS.
- T. Serra, J. Colomer and B. E. Logan, Water Res., 2008, 42, 1113–1121 CrossRef CAS.
- P. Jarvis, B. Jefferson and S. A. Parsons, Environ. Sci. Technol., 2005, 39, 2307–2314 CrossRef CAS.
- J. Wang, J. Guan, S. R. Santiwong and T. D. Waite, J. Membr. Sci., 2008, 321, 132–138 CrossRef CAS.
- Y. H. Choi, H. S. Kim and J. H. Kweon, Sep. Purif. Technol., 2008, 62, 529–534 CrossRef CAS.
- H. C. Kim, J. Membr. Sci., 2015, 475, 349–356 CrossRef CAS.
|
This journal is © The Royal Society of Chemistry 2016 |
Click here to see how this site uses Cookies. View our privacy policy here.