DOI:
10.1039/C5RA21583H
(Paper)
RSC Adv., 2016,
6, 1-7
Improving the mechanical properties of cellulose diacetate fibers via using an ionic liquid as processing solvent†
Received
16th October 2015
, Accepted 11th December 2015
First published on 15th December 2015
Abstract
The solutions of cellulose diacetates (CDA) in ionic liquids, 1-butyl-3-methylimidazolium chloride ([BMIM]Cl), 1-butyl-3-methylimidazolium tetrafluoroborate ([BMIM]BF4), 1-butyl-3-methylimidazolium hexafluorophosphate ([BMIM]PF6) and 1-butyl-3-methylimidazolium formate ([BMIM]COOH), have been investigated to identify the solvent for optimal CDA fiber performance. The CDA/[BMIM]Cl and CDA/[BMIM]BF4 solutions both behave as typical shear-thinning fluids that are beneficial for fiber spinning. The CDA/[BMIM]Cl solution exhibits higher flowability and spinnability than the CDA/[BMIM]BF4 solution. CDA fibers with compact morphology and smooth surface have been fabricated from the [BMIM]Cl solution. The tensile strength of the resulting CDA fibers (3.00 cN per dtex) is significantly improved over that of commercial CDA fibers (1.44 cN per dtex), even when the commercial fibers (3.83 dtex) are thinner than the new CDA fibers (5.20 dtex). The present method to fabricate CDA fibers with improved mechanical properties can be directly used for the production of fabric yarns and garments.
Introduction
Cellulose acetates (CAs) are commercially important cellulose derivatives in which the hydroxyl groups in the anhydroglucose units of cellulose are substituted by acetyl groups.1 The most commonly used CAs are cellulose diacetate (CDA) with an average degree of substitution (DS) ranging from 2.2 to 2.7 acetyl groups per glucose unit and cellulose triacetate (CTA) with an average DS above 2.7.2 As regenerated cellulose fibers, CDA fibers have played an irreplaceable role in the family of natural and synthetic fibers for decades. Compared with other regenerated cellulose fibers, CDA fibers combine the merits of synthetic fibers and cellulose fibers, including softness and suppleness with a silk-like handle, a pleasant feel on the skin, excellent draping qualities, natural crease resistance, low moisture absorption and distinct filtering effect. It has been widely applied in textiles, for medical care and filter materials.3 Furthermore, CDA fibers are environmentally friendly widely available from natural and renewable sources, and has been the subject of extensive current researches.3–7
CDA fibers are commercially manufactured by dry spinning. During the formation process of CDA fibers, large quantities of acetone are needed, which incurs both environmental and health concerns as acetone is highly volatile and flammable. The use of acetone also lowers the production throughput. Furthermore, the produced CDA fibers from using acetone have relatively low mechanical strength, typically in the range of 1.06–1.23 cN per dtex.3 This has limited the application scope in textiles. In most textile processing, CDA fibers prepared using acetone as solvent are blended with other fibers such as rayon, silk, polyester, nylon, and so on to enhance the yarn process performance. A new environmental friendly process to fabricate CDA fibers with enhanced mechanical properties is highly demanded.
Room temperature ionic liquids (ILs) have been extensively investigated in the last decade as process solvents thanks to their non-flammability, negligible vapor pressure, outstanding solubility, chemical and thermal stability.8–12 As a potential “green” solvent, ILs have been broadly investigated for cellulose dissolution in recent years.13–17 The interactions between the anions of ILs containing 1-butyl-3-methylimidazolium ([BMIM]+) cations and hydroxyl groups were considered to break the hydrogen bonding between adjacent cellulose chains and thus result in dissolution of the cellulose in the ILs. Moreover, the ILs could alter the spinnability of the cellulose/IL solutions. The cellulose fibers fabricated from the IL solution were reported to exhibit comparable mechanical properties to lyocell fibers.18 In this paper, ILs are investigated as processing solvents for commercially most important cellulose fibers, CDA fibers. The solubility of CDA in various ILs was first examined, and the ILs with good solubility were selected to study the rheological behaviors of the CDA/IL solutions. It is further demonstrated that CDA fibers spun from [BMIM]Cl can exhibit significantly improved mechanical properties.
Experimental
Materials and methods
CDA powder was provided by Xi'an Huida Chemical Industry Co., Ltd. (degree of polymerization was 473, DS = 2.46). It was dried in vacuum oven at 80 °C for 12 h before use. Commercial CDA fibers were purchased from Hangzhou Xinxie Fiber Co., Ltd, China. [BMIM]BF4, [BMIM]PF6, and [BMIM]COOH were purchased from Shanghai Chengjie Chemical CO., LTD, China. [BMIM]Cl was synthesized according to the literature.19 The molecular structures for these ILs are shown in Fig. 1. Water content of [BMIM]Cl was less than 0.2 wt% as measured by Karl Fischer titration (ZSD-2 with a precision of 0.05 wt%, Shanghai Anting Electric Instruments Co. Ltd., China). The commercial ILs were used without further purification. The 1HNMR spectra and the photograph of the ILs are shown in Fig. S1 and S2,† respectively.
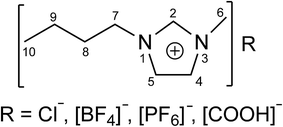 |
| Fig. 1 Molecular structures of the ILs used in this work. | |
Rheological measurements were performed on a rotational rheometer (Phsica MCR 301, Anton Paar Instrument Corporation, Austria) with a parallel plate (PP-25, diameter: 25 mm). The Fourier transform infrared (FT-IR) spectra of the CDA/IL solutions were recorded on a Nicolet Nexus 670 (Thermo Fisher, USA) with wavenumbers ranging from 500 cm−1 to 4000 cm−1. The mechanical testing of fibers was performed on an XQ-1 tensile tester (China Textile University, Shanghai, China) at an extension rate of 4 mm min−1. Each series of samples was measured more than 20 times to get the statistical data. The mechanical testing was conducted at room temperature and 65% relative humidity. The morphology of the fibers was characterized by a JSM-5600LV scanning electron microscope (JEOL Co., Tokyo, Japan). The sample surface was coated with sputtered gold before SEM imaging. WAXD measurements were performed on a D/MAX-2000 diffractometer (Rigaku, Tokyo, Japan) with the Cu Kα radiation at 40 kV and 35 mA. The powder samples were scanned from 5 to 60°, and the data were analyzed with Peakfit software (version 4.12, Seasolve Co., San Jose, CA). The crystallinity and crystalline orientation factor were calculated according to the method reported in literatures.20,21
Dissolution of CDA in ILs and fiber spinning process
Dried CDA powder was mixed with ILs in a flask and mechanically stirred for 4 h at 30 and 90 °C, and then dried in a vacuum oven at 80 °C for 48 h to remove bubbles generated during the dissolution process. The mixture turned homogeneous and transparent. The solubility was calculated based on the amounts of dissolved CDA and the ILs.
The preparation of spinning dope was carried out in a special vertical kneader system and the spinning experiments were performed on a model dry-jet-wet spinning equipment made in our laboratory. In a typical spinning procedure, a CDA/[BMIM]Cl mixture containing 12 wt% CDA pre-dried in vacuum at 90 °C was placed in the vertical kneader system and stirred for about 2 h until a homogeneous spinning dope was obtained. The spinning dope was dried in vacuum at 80 °C for 12 h to remove bubbles generated in the stirring process. It was then transferred to a spinning tank, extruded through a spinneret orifice, passed through a 60 mm-long air gap, and immersed in a coagulation bath of water to precipitate CDA into filaments form. The coagulation bath was filled with water and kept at 15 °C. The obtained filaments were immediately drawn, washed in a water bath, and finally rolled up. The temperature of the washing bath was 60 °C. The spinning temperature was 70 °C, and spinneret orifice with a diameter of 0.1 mm and 0.08 mm was used.
Result and discussion
Dissolution of CDA in ILs
ILs have been used to dissolve different polymers and exhibited different selective solubility.9,12,22 To establish a suitable spinning method for CDA, IL selection becomes important. ILs containing [BMIM]+ with various anions were selected in the present study to examine the solubility of CDA since these ILs had been reported applicable for cellulose fiber formation. The solubility of CDA in [BMIM]Cl, [BMIM]BF4, [BMIM]PF6, and [BMIM]COOH was tested at 30 °C and 90 °C. The data listed in Table 1 show that CDA is not soluble in [BMIM]COOH, but soluble in [BMIM]BF4 (up to 19 wt% at 90 °C), [BMIM]Cl (up to 17 wt% at 90 °C), and [BMIM]PF6 (up to 14 wt% at 90 °C). These results are different from cellulose reported in literature.13 Cellulose has good solubility in [BMIM]COOH and [BMIM]Cl, but does not dissolve in [BMIM]BF4 or [BMIM]PF6. It is generally accepted that the dissolution of cellulose in [BMIM]+-containing ILs is resulted from the coordination between hydroxyl groups of cellulose and the anions of ILs such as [COOH]− and Cl−, that is, hydrogen bonding between the hydroxyl groups in cellulose and anions plays the key factor in the cellulose dissolution in ILs.13,22 In [BMIM]BF4 and [BMIM]PF6, the hydrogen bonding cannot be formed between the hydroxyl groups and the [BF4]− and [PF6]− anions. Thus, these two ILs cannot dissolve cellulose.23–25 When many hydroxyl groups were substituted by acetyl groups as in CDA, the hydrogen bonding between the hydroxyl groups of CDA and anions in ILs is obviously weakened. In general, CDA is soluble in proton accepting solvents, such as ketones, esters or heterocyclic bases, which interact with the hydroxyl group in CDA, resulting in the dissolution of CDA in these solvents. Acidic solvents or proton donors, such as cresols, chlorinated hydrocarbons and formic acid, which interact primarily with the acetyl groups of CDA, are also good solvents for CDA. Therefore, the dissolution of CDA in [BMIM]+-containing ILs may mainly originates from the hydrogen bonding between H–C in the imidazolium ring and acetyl groups.9,26,27 We argue the dissolution mechanism of CDA in ILs as follows: the ion pairs in ILs dissociate to individual anions and [BMIM]+ ions; the individual [BMIM]+ ions coordinate with the acetyl groups of CDA, which act as proton acceptors and form hydrogen bonds with H in [BMIM]+ ions, leading to dissolution of CDA in ILs. In this mechanism, the acidity of the H atoms in [BMIM]+ is important in the dissolution of CDA, and the H–C adjacent to imino N can have sufficient acidity thanks to strong electron-pulling of the imino N atoms. This mechanism also predicts that the solvatochromic polarity of ILs is important to influencing the solubility. As reported in literatures, the solvatochromic polarity of the four ILs used here followed the order: [BMIM]COOH > [BMIM]Cl > [BMIM]BF4 > [BMIM]PF6.28–31 For [BMIM]COOH, the strong solvatochromic polarity makes the anion be strongly bounded to the cation. Therefore, the H in [BMIM]+ is less acidic, and the formation of hydrogen bonds with acetyl groups is reduced. That is the reason why CDA is insoluble in [BMIM]COOH. The hydrogen bonding between H–C in imidazolium ring and acetyl groups was confirmed by FTIR spectrum of the CDA/[BMIM]Cl solution. As shown in Fig. 2, the absorption peaks of acetyl groups in CDA are observed at 1747 cm−1, 1371 cm−1 and 1236 cm−1, which can be assigned to the vibration of C
O, C–O and C–H respectively.32 The absorption peaks of imidazolium ring in [BMIM]Cl are observed at 3141 cm−1 and 3064 cm−1, which correspond to the vibration of C(4,5)–H and C(2)–H, respectively.33 There are no significant absorption peaks emerging or vanishing for CDA after being dissolved in [BMIM]Cl, which indicates that no chemical reaction has occurred during the dissolution. However, the absorption peaks of acetyl groups shift slightly to 1741 cm−1, 1382 cm−1 and 1238 cm−1. Meanwhile, the characteristic absorption peaks of C(4,5)–H and C(2)–H in imidazolium ring shift to 3149 cm−1 and 3097 cm−1 in CDA/[BMIM]Cl solution. These observations indicate that strong interactions occur between CDA acetyl groups and H atom in [BMIM]+, and it can be deduced that the acetyl groups in CDA act as proton acceptors and form hydrogen bonds with H in imidazolium ring of [BMIM]Cl.
Table 1 Solubility (wt%) of CDA in various ILs
Sample |
Temperature |
[BMIM]COOH |
[BMIM]Cl |
[BMIM]BF4 |
[BMIM]PF6 |
CDA (wt%) |
30 °C |
Insoluble |
13 |
14 |
10 |
90 °C |
Insoluble |
17 |
19 |
14 |
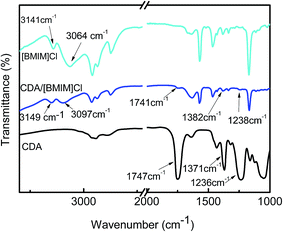 |
| Fig. 2 FTIR spectra of CDA, [BMIM]Cl and CDA/[BMIM]Cl solution. | |
Steady shear rheological behaviors of CDA/IL solutions
Rheological properties of polymer solution are very important in guiding solution spinning. The good solvents [BMIM]Cl and [BMIM]BF4 were selected to further investigate the rheological behaviors of the resulting solutions. Fig. 3 displays the steady-shear viscosity curves of CDA/[BMIM]Cl and CDA/[BMIM]BF4 solutions at different temperatures with the CDA mass concentration 12 wt%. Both solutions exhibit typical shear-thinning behavior, which is similar to cellulose/ILs solution.34 CDA chains would be un-tangled and un-orientated in the direction of shearing, resulting in the decrease of viscosity with increase of shear rate. It is also clear that the apparent viscosity of both solutions decreased with the increase of temperature because CDA molecules tend to move more easily at higher temperatures. Of the two solutions, the CDA/[BMIM]Cl solution has higher apparent shear viscosity than the CDA/[BMIM]BF4 solution at the same temperature, which may be caused by the higher viscosity of [BMIM]Cl.
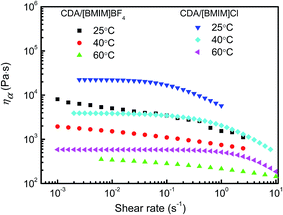 |
| Fig. 3 Viscosity–shear rate curves of 12 wt% CDA/[BMIM]Cl and CDA/[BMIM]BF4 solutions at specified temperatures. | |
Dynamic rheological behaviors
Strain sweep was performed to determine the linear viscoelastic region of the CDA/[BMIM]Cl and CDA/[BMIM]BF4 solutions. The dynamic frequency sweep was executed with angular frequencies from 628 to 0.1 rad s−1 in the linear viscoelastic region. The test temperature was raised from 25 °C to 100 °C. Master curves of both CDA/IL solutions were drawn based on the time–temperature superposition principle (Fig. 4). It is apparent that the time–temperature superposition principle works perfectly in both CDA/IL solutions, which indicates that the liquid state characteristics of the solutions are well retained, and there is no obvious structural transformation over the whole temperature range. This stability in a wide temperature range is desirable for spinning solutions.
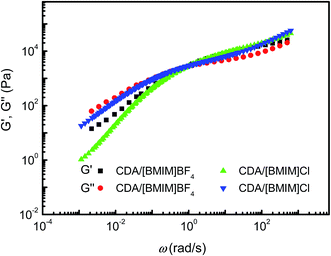 |
| Fig. 4 Master time–temperature superposition curves of 12 wt% CDA/[BMIM]Cl and CDA/[BMIM]BF4 solutions at 25 °C. | |
The loss modulus G′ is larger than the storage modulus G′ in the low-frequency region, which indicates that the CDA/IL solutions behave as a viscous fluid. With the increase of the angular frequency (ω), the G′–ω and G′–ω curves intercross around 100 rad s−1, indicating an entangled polymer solution and strong interactions among CDA chains.
Structural viscosity index
Structural viscosity index (Δη) is a very important and common experimental parameter to evaluate the spinnability of spinning dope. It is useful to represent the structural degree of polymer in solution and speculate the entanglement degree of polymer chain in fluids. Δη can be described by the following equation:35 Δη = −[d(lg
ηa)/dγ1/2] × 100, where ηa refers to apparent viscosity and γ shear rate. For non-Newtonian fluids, the values of Δη are positive and smaller Δη reflects better spinnability of fluids.
The relationships of log
ηa versus γ1/2 of 12 wt% CDA/[BMIM]Cl and CDA/[BMIM]BF4 solutions at different temperatures are given in Fig. 5. Fitting curves of the experimental data in linear formula are also shown. It can be seen that the plots of experimental data exhibit good linear relationship. The Δη (inset in Fig. 5) for CDA/IL solutions at different temperatures can be calculated according to the slopes of the corresponding linear fitting curves. With increasing temperature, Δη values of both CDA/IL solutions drop sharply, indicating that the flowability and spinnability of both CDA/IL solutions can be significantly improved by increasing temperature. The decreasing Δη can be attributed to the decrease of entanglement and easier movements of CDA chains in solution with increasing temperature. The Δη values of CDA/[BMIM]Cl fall more steeply that those of the CDA/[BMIM]BF4 solution suggesting that flowability and spinnability of the CDA/[BMIM]Cl solution is more sensitive to temperature. The Δη values of the CDA/[BMIM]BF4 solution are larger than those of CDA/[BMIM]Cl solution at the same temperature. It is inferred that [BMIM]Cl is more effective in overcoming the entanglements of CDA chains than [BMIM]BF4 for its stronger solvability and polarity. Thus, the CDA/[BMIM]Cl solution exhibits better flowability and spinnability,36 and would be more suitable to fabricate CDA fibers.
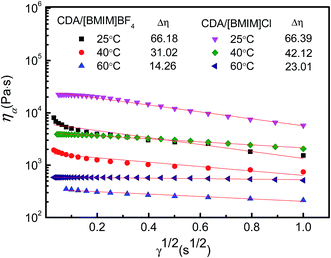 |
| Fig. 5 Relationships of lg ηa versus γ1/2 of 12 wt% CDA/[BMIM]Cl and CDA/[BMIM]BF4 solutions at specified temperatures. | |
Further investigation has been done on structural viscosity index for 12 wt% CDA/[BMIM]Cl solution at a higher temperature range from 70 °C to 100 °C (Fig. 6). The values of Δη were calculated as 5.91, 3.93, 2.57 and 1.64 at 70 °C, 80 °C, 90 °C and 100 °C, respectively, which means that the CDA/[BMIM]Cl solution behaves like a Newton fluid, and the influence of temperature on the flowability and spinnability is less evident at temperatures over 70 °C. In consideration of the risk of potential partial degradation at elevated temperatures, the spinning temperature was set at 70 °C for the CDA spinning process.
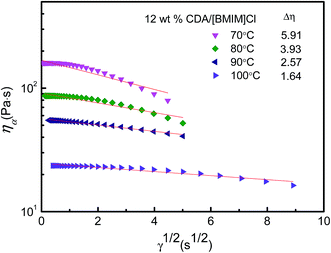 |
| Fig. 6 Relationships of lg ηa versus γ1/2 of 12 wt% CDA/[BMIM]Cl solution from 70 °C to 100 °C. | |
Mechanical properties of CDA fibers
Fiber spinning was conducted using a 12 wt% CDA/[BMIM]Cl solution and dry-wet spinning process. The CDA fibers 1–3 and CDA fiber 4 were obtained through a spinneret orifice with a diameter of 0.1 mm and 0.08 mm, respectively. The fineness, tensile strength and elongation at break of all fiber samples are summarized in Table 2. A commercial CDA fiber was also tested for comparison. From the data, the fineness for CDA fibers 1–3 decreases from 20.80 dtex to 9.28 dtex with the increase of draft radio from 4.8 to 11.8. The tensile strength improves from 1.24 cN per dtex to 1.80 cN per dtex, whereas the elongation at break decreases from 10.34 to 8.00. Compared with that of the commercial CDA fibers (1.44 cN per dtex), the as-fabricated CDA fibers have comparable or higher tensile strength despite of the greater fineness. The tensile strength of CDA fibers from the IL solution is also greater than that reported in literature (1.06–1.23 cN per dtex).3 When a spinning equipment with a smaller orifice was used, CDA fiber 4 with higher tensile strength (3.00 cN per dtex) was obtained. This indicates that the tensile strength of CDA fibers from the [BMIM]Cl solution could potentially be improved by adjusting the spinning conditions. Further work along this line is in progress.
Table 2 Mechanical properties and crystallinity of CDA fibers
Sample |
Draft ratio |
Fineness (dtex) |
Tensile strength (cN per dtex) |
Elongation at break (%) |
Crystallinity |
Crystalline orientation factor |
1 |
4.8 |
20.80 |
1.24 |
10.34 |
26.56 |
0.645 |
2 |
10.4 |
10.64 |
1.78 |
8.61 |
37.78 |
0.649 |
3 |
11.8 |
9.28 |
1.80 |
8.00 |
45.04 |
0.653 |
4 |
7.4 |
5.20 |
3.00 |
9.67 |
48.14 |
0.664 |
Commercial CDA fiber |
— |
3.83 |
1.44 |
24.90 |
27.01 |
0.542 |
XRD analysis
XRD spectra of the CDA fibers are shown in Fig. 7. Two broad diffraction peaks are observed at about 10.3° and 17.6° in all CDA fibers, which are assigned to the crystallographic plane of (2 1 0) and (0 2 1), respectively.37,38 The diffraction intensity increases systematically from CDA fibers 1 to 4, with the commercial fibers slightly above that of the fiber 1. The degree of crystallinity data are tabulated in Table 2, showing the degree of crystallinity increases from 26.56 for fiber 1 to 48.14 for fiber 4. The crystalline orientation factors and tensile strengths of the fibers are also listed in Table 2. The crystalline orientation factor of CDA fibers 1–4 also increases from 0.645 to 0.664. It is known that the mechanical properties of fibers mainly rely on their crystallinity and orientation. With the increase of spinning tension in the spinning line, the CDA macromolecules align gradually in an orderly fashion along the drawing direction, resulting in an increasing orientation. At the same time, the crystallinity of the fibers increases as induced by the orientation, resulting in an increase in tensile strength of CDA fibers with the increase of draft ratio. All the CDA fibers fabricated from the [BMIM]Cl solution possess comparable or higher crystallinity and crystalline orientation factor as compared to the commercial CDA fibers, and thus the better mechanical properties. For CDA fiber 4, despite its smaller of draft radio than those for CDA fiber 2 and 3, the smallest fineness was obtained after a different spinneret orifice was adapted. Fiber 4 has the highest degree of crystallinity (48.14) and crystalline orientation factor (0.664), and consequently the greatest tensile strength up to 3.00 cN per dtex.
 |
| Fig. 7 XRD curves of CDA fibers using [BMIM]Cl as processing solvent and the commercial CDA fiber. | |
Morphology of CDA fiber
Fig. 8 shows the SEM images of CDA fiber 1 and commercial CDA fibers. The insets are photographs of the fibers. As shown in Fig. 8a, the CDA fiber 1 surface is very smooth, without any obvious flaws or crevices. Moreover, the CDA fibers have uniform and regular circle cross-sections (Fig. 9a). From the appearance and the comfortable feel, there is no big difference between the two fibers. The diameter of the commercial CDA fibers is less than 20 μm, as shown in Fig. 8b, much smaller than that of the CDA fibers processed from the [BMIM]Cl solution (close to 60 μm). The result is consistent with the fineness described in section above on mechanical properties. The cross-section SEM image of the commercial CDA fibers manufactured shown in Fig. 9b reveals a dog bone shape, which may be caused by the irregularly shaped spinneret orifice used in producing the commercial fibers.
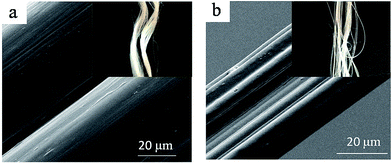 |
| Fig. 8 SEM images of CDA fiber 1 (a) and the commercial CDA fiber (b). Insets are optical photographs of the fibers. | |
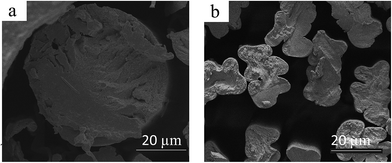 |
| Fig. 9 Cross-section SEM images of CDA fiber 1 (a) and the commercial CDA fiber (b). | |
Conclusions
In conclusions, the solubility of CDA in different ILs reveals a dissolution mechanism of CDA in the ILs based on H bonding between the acetyl groups on the CDA chains and the [BMIM]+ cations of the ILs. The anions affect the acidity of the H–C on the imidazole ring of the [BMIM]+ and thus the solubility. The solution in [BMIM]Cl shows the best flowability and spinnability. The CDA fibers have been successfully processed from the [BMIM]Cl solution with improved crystallinity and mechanical properties. The optimal tensile strength of CDA fibers can reach 3.00 cN per dtex with the fineness of 5.20 dtex, compared favorably with the fineness (3.83 dtex) and tensile strength (1.44 cN per dtex) of the commercial CDA fibers. We believe there is still a broad room to improve the properties of the CDA fibers by optimizing the spinning conditions. The added environmentally benignness of the IL should make this approach attractive for future textile applications.
Acknowledgements
This work was financially supported by the National Natural Science Foundation of China (51273041) and the Fundamental Research Funds for the Central Universities (2232014D3-36).
References
- D. Xu, Cellulose Derivatives, Chemical Industry Press, Beijing, 2001, p. 48 Search PubMed.
- P. Zugenmaier, Macromol. Symp., 2004, 208, 81–166 CrossRef CAS.
- R. C. Law, Macromol. Symp., 2004, 208, 255–266 CrossRef CAS.
- I. Munaweera, A. Aliev and K. J. Balkus Jr, ACS Appl. Mater. Interfaces, 2014, 6, 244–251 CAS.
- R. Nasser Jr and M. E. S. Taqueda, Ind. Eng. Chem. Res., 2008, 47, 8376–8383 CrossRef.
- D. A. Rubenstein, S. M. Venkitachalam, D. Zamfir, F. Wang, H. Lu, M. D. Frame and W. Yin, J. Biomater. Sci., Polym. Ed., 2010, 21, 1713–1736 CrossRef CAS PubMed.
- T. Matamá, R. Araújo, G. M. Gübitz, M. Casal and A. Cavaco-Paulo, Biotechnol. Prog., 2010, 26, 636–643 CrossRef PubMed.
- Y. Jeon, J. Sung, C. Seo, H. Lim, H. Cheong, M. Kang, B. Moon, Y. Ouchi and D. Kim, J. Phys. Chem. B, 2008, 112, 4735–4740 CrossRef CAS PubMed.
- H. Zhang, J. Wu, J. Zhang and J. He, Macromolecules, 2005, 38, 8272–8277 CrossRef CAS.
- C. G. Hanke, N. A. Atamas and R. M. Lynden-Bell, Green Chem., 2002, 4, 107–111 RSC.
- S. M. Urahata and M. C. C. Riberiro, J. Chem. Phys., 2004, 120, 1855–1863 CrossRef CAS PubMed.
- J. Li, J. Zhang, B. Han, Y. Wang and L. Gao, Chem. Phys., 2004, 121, 7408–7412 CAS.
- R. P. Swatloski, S. K. Spear, J. D. Holbrey and R. D. Rogers, J. Am. Chem. Soc., 2002, 124, 4974–4975 CrossRef CAS PubMed.
- T. Heinze, S. Dorn, M. Schöbitz, T. Liebert, S. Köhler and F. Meiste, Macromol. Symp., 2008, 262, 8–22 CrossRef CAS.
- T. Heinze, K. Schwikal and S. Barthel, Macromol. Biosci., 2005, 6, 520–525 CrossRef PubMed.
- D. G. Raut, O. Sundman, W. Q. Su, P. Virtanen, Y. Sugano, K. Kordas and J. Mikkola, Carbohydr. Polym., 2015, 5, 18–25 CrossRef PubMed.
- B. Kosan, S. Dorn, F. Meister and T. Heinze, Macromol. Mater. Eng., 2010, 7, 676–681 CrossRef.
- T. Cai, H. Zhang, Q. Guo, H. Shao and X. Hu, J. Appl. Polym. Sci., 2010, 2, 1047–1053 CrossRef.
- S. Csihony, C. Fischmeister, C. Bruneau, I. Horváth and P. Dixneuf, New J. Chem., 2002, 26, 1667–1670 RSC.
- G. Cheng, P. Varanasi, C. Li, H. Liu, Y. B. Melnichenko, B. A. Simmons, M. S. Kent and S. Singh, Biomacromolecules, 2011, 12, 933–941 CrossRef CAS.
- G. Jiang, W. Huang, L. Li, X. Wang, F. Pang, Y. Zhang and H. Wang, Carbohydr. Polym., 2012, 87, 2012–2018 CrossRef CAS.
- R. Remsing, R. Swatloski, R. Rogers and G. Moyna, Chem. Commun., 2006, 28, 1271–1273 RSC.
- A. E. Bradley, C. Hardacre, J. D. Holbrey, S. Johnston, S. E. J. McMath and M. Nieuwenhuyzen, Chem. Mater., 2002, 2, 629–635 CrossRef.
- R. Bini, O. Bortolini, C. Chiappe, D. Pieraccini and T. Siciliano, J. Phys. Chem. B, 2007, 111, 598–604 CrossRef CAS.
- P. A. Z. Suarez, S. Einloft, J. E. L. Dullius, R. F. D. Souza and J. Dupont, J. Chim. Phys. Phys.-Chim. Biol., 1998, 95, 1626–1639 CrossRef CAS.
- H. Lee, T. P. Lodge and P. Timothy, J. Phys. Chem. Lett., 2010, 1, 1962–1966 CrossRef CAS.
- K. Kodama, R. Tsuda, K. Niitsuma, T. Tamura, T. Ueki, H. Kokubo and M. Watanabe, Polym. J., 2011, 43, 242–248 CrossRef CAS.
- K. Swiderski, A. Mclean, C. M. Gordon and D. H. Vaughan, Chem. Commun., 2004, 19, 2178–2179 RSC.
- S. H. Lee and S. B. Lee, Chem. Commun., 2005, 27, 3469–3471 RSC.
- Y. Fukaya, K. Hayashi, M. Wada and H. Ohno, Green Chem., 2008, 10, 44–46 RSC.
- R. Lungwitz, V. Strehmel and S. Spange, New J. Chem., 2010, 34, 1135–1140 RSC.
- Z. Li, N. Liu, Y. Yao, S. Chen, H. Wang and H. Wang, RSC Adv., 2015, 5, 901–907 RSC.
- A. Pinkert, K. N. Marsh, S. Pang and M. P. Staiger, Chem. Rev., 2009, 109, 6712–6728 CrossRef CAS.
- M. Gericke, K. Schlufter, T. Liebert, T. Heinze and T. Budtova, Biomacromolecules, 2009, 10, 1188–1194 CrossRef CAS.
- J. Cai, P. Fei, Z. Xiong, Y. Shi, K. Yan and H. Xing, Carbohydr. Polym., 2013, 92, 11–18 CrossRef CAS.
- Y. Zhang, X. Li, Y. Yang, A. Lan, X. He and M. Yu, RSC Adv., 2014, 4, 34584–34590 RSC.
- W. R. W. Daud and F. M. Djuned, Carbohydr. Polym., 2015, 5, 252–260 CrossRef.
- J. Mei, Y. Ou and J. Chen, J. Cellul. Sci. Technol., 2002, 10, 12–19 CAS.
Footnote |
† Electronic supplementary information (ESI) available. See DOI: 10.1039/c5ra21583h |
|
This journal is © The Royal Society of Chemistry 2016 |
Click here to see how this site uses Cookies. View our privacy policy here.