DOI:
10.1039/C5RA27256D
(Paper)
RSC Adv., 2016,
6, 13418-13425
Enhanced thermal stability and flame retardancy of polyurethane foam composites with polybenzoxazine modified ammonium polyphosphates
Received
20th December 2015
, Accepted 20th January 2016
First published on 25th January 2016
Abstract
The influence of polybenzoxazine modified ammonium polyphosphate (BMAPP) on the thermal behavior and flame retardancy of a rigid polyurethane foam (PU) are investigated via thermogravimetric analysis (TG), TG coupled with infrared spectroscopy (TG-FTIR), UL-94 vertical burning testing and limit oxygen index (LOI). The TG testing results indicate that BMAPP can enhance the thermal stability of PU, both under air and nitrogen conditions. The initial degradation temperature of the BMAPP/PU composites is 264 °C in air, which is 22 °C and 30 °C higher than that of ammonium polyphosphate (APP)/PU composites and neat PU, respectively. The reason might be attributed to the better dispersion and compatibility of BMAPP particles in PU compared with APP, which can prevent the PU chain from degrading at low temperatures. The LOI value results demonstrate that BMAPP has higher flame retardancy in PU than APP. Residue analysis implies that polybenzoxazine is partially converted into Si–O as char residue during combustion.
Introduction
Polyurethane is a kind of polymer with a basic repetitive unit being a urethane bond (NHCOO). It can be produced from a polyaddition reaction between polyfunctional alcohols (polyol polyether or polyol polyester) and polyisocyanate to form urethane linkages.1 Rigid polyurethane foam (PU) is a typical material of polyurethane widely used in buildings and insulated appliances, such as refrigerators, tank and pipe insulation, etc.2,3 However, neat PU is considerably flammable because it consists of a large number of aliphatic segments and possesses a porous cellular structure, which increases the surface contact area between the materials and the air. Upon ignition, PU rapidly burns, releases a large amount of heat, and then reaches the peak of the burning intensity in a short time.4–6 Thermal degradation of materials is the initial step of solid combustion processes and the pyrolysis products that contain gaseous fuel support the combustion.7,8 Therefore, it is meaningful to improve flame retardancy and to study the thermal degradation characteristics and the volatile products of PU.
The selection of appropriate flame retardants for PU is important to preserve the other excellent properties of the foams. Basically, flame retardants can be either reactive or additive. The addition type includes: ammonium polyphosphate (APP), triethyl phosphate, triphenyl phosphate, expandable graphite, tricresyl phosphate, melamine cyanurate, dimethyl methylphosphonate, and alkylphosphinates. Reactive flame retardant usually contain phosphorus, nitrogen and hydroxyl.9 Among the additive flame retardants, APP is synthesized from the inorganic salt of polyphosphoric acid and ammonia, and is currently getting the attention among the industries. APP is able to function as a flame retardant in the condensed or polymer phase through intumescence. During intumescence, a material swells when it is exposed to heat or fire to form a porous carbonaceous foam which acts as a barrier to prevent heat, air and pyrolysis products from entering the surface of the material.10–12 APP is known to be preferred over other flame retardants due to its smaller loadings, a lower cost and excellent processability.13–15 In addition, APP is halogen-free, which is considered to be eco-friendly and safe for the environment and ecosystem.16–19
In spite of many advantages, higher efficiency and water resistant APP is expected to be obtained. Recently, many studies have been reported regarding APP. F Shukor’s group20 has reported the effect of ammonium polyphosphate on flame retardancy, thermal stability and mechanical properties of alkali treated kenaf fiber filled PLA biocomposites. Shao et al.21 have prepared ethylenediamine-modified APP via ion exchange reaction. Hu et al.22 have found that APP microencapsulated with ethyl cellulose shows better flame retardancy in poly(butylene succinate) than APP. In order to improve flame retardancy and overcome the shortcomings, in this study, polybenzoxazine is selected to modify APP polybenzoxazine is synthesized from the copolymerization of bisphenol A, formaldehyde and 3-triethoxysilylpropylamine. The thermal behavior and flame retardancy of polybenzoxazine modified ammonium polyphosphate (BMAPP)/PU composites are investigated.
Experimental
Materials
APP (phase II, the degree of polymerization > 1000) was supported by Polyrocks chemical Co., Ltd., China. Bisphenol A, 4,4′-diphenylmethane diisocyanate (MDI), and dicyandiamide was purchased from Aladdin Industrial Corporation (China). Formaldehyde was obtained from polyether polyols (4110, hydroxyl value = 410–450 mg KOH per g) and was provided by Guangzhou Ruiyin Trading Co., Ltd., China. N-Pentane was supplied by TianjingFuchen Chemical Reagent Factory (Tianjin, China). Dibutyltin dilaurate was purchased from Shanghai Lingfeng Chemical Reagent Co. Ltd., China.
Synthesis of BMAPP
Formaldehyde (6.48 g, 37%) was mixed with 30 ml of toluene under mechanical stirring in a flask. 3-Triethoxysilylpropylamine (8.84 g) was dropped into the flask. Subsequently, 4.56 g of bisphenol A and 25 ml of toluene were slowly added into the mixture. The solution was heated at 85 °C for 5 hours. After that, 150 ml toluene and 60 g APP were successively put into the flask. After being keept for another 10 min, 10 ml of formic acid was added. Then the mixture was kept under stirring at 85 °C for 12 hour. Finally, the suspension was filtered and rinsed with toluene. The obtained powder was dried at 120 °C. The reactive formula is depicted in Scheme 1.
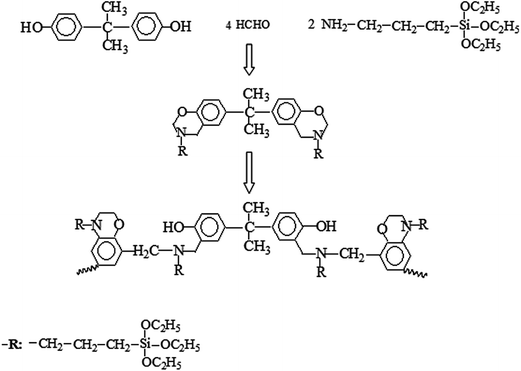 |
| Scheme 1 Reactive formula of polybenzoxazine. | |
Preparation of PU composites
The polyether polyol (20.00 g) was mixed with the other ingredients: the foaming agent (N-pentane) (2.60 g), the catalyst (dibutyltin dilaurate) (0.11 g), and the flame retardant (APP or BMAPP), which were stirred for homogenization and then MDI (20.20 g) was added into the mixture under continuous stirring. When it began to foam, the mixture was immediately poured into the mould. The container was then placed on a flat surface for 5 h at 70 °C.
Measurements
Scanning electron microscopy (SEM) and energy dispersive spectroscopy (EDS). The SEM and EDS results of the samples were recorded on a Hitachi S3400N scanning electron microscope (SEM) and X-ray energy dispersive spectroscope (EDS, Bruker), respectively.
UL-94 vertical burning test. The vertical test was carried out on a CFZ-3-type instrument (Jiangning Analysis Instrument Company, China) according to the UL-94 test standard. The specimens used were of dimensions 120 × 15 × 8 mm3.
Limiting oxygen index (LOI). LOI was measured according to ISO4589. The apparatus used was an oxygen index meter (JF-3, Jiangning Analysis Instrument Company, China). The samples used for the test were of dimensions 100 × 10 × 10 mm3.
Water leaching rate. About 8 g of flame retardants (marked Wa) were packaged with the same filter papers (marked Wc). The specimens were put in about 2 l of distilled water and the temperature was kept at different temperatures for 36 h. The water was then removed and the specimens were dried to constant mass at 80 °C (marked Wt). The water leaching rate of the specimens can be expressed as:
Water leaching rate = (Wt − Wc)/(Wa − Wc) × 100% |
Thermogravimetric analysis (TG). Each sample was examined under an air flow (30 ml min−1) on a DTG-60H apparatus (Shimadzu Company) at a heating rate of 10 °C min−1. The mass of all samples was kept within 3–5 mg in an open Al pan.
Thermogravimetric analysis-Fourier transform infrared spectra (TG-FTIR). TG-FTIR was performed using the Netzsch TG209F3 thermo-analyzer that was linked to the Bruker TENSOR 27 FTIR spectrophotometer. About 5.0 mg of the sample was put in an alumina crucible and heated from 40 to 800 °C. The heating rate was 10 °C min−1 (air atmosphere, flow rate of 30 ml min−1).
Results and discussions
Characterization of BMAPP by SEM and EDS
In order to study the surface morphology of APP and BMAPP, SEM photographs and EDS surface elemental compositions are presented in Fig. 1 and Table 1. It can be seen that APP particles show a smooth surface, after modification; the surface of BMAPP is comparatively rough, obviously, the polybenzoxazine resin is attached on the particles. Particulate aggregation can be observed on the surface. Under mild polymerization conditions, chain growth can terminate at the dimer length due to hydrogen bond formation at the growth front, which might lead to the resultant aggregation.23 EDS results show that the elemental compositions of APP are 7.06% (C), 53.56% (O), 20.25% (N) and 19.34% (P) respectively. As for BMAPP, due to the presence of polybenzoxazine, the amount of the C element is increased to 42.96%; what’s more, the Si element is observed and its proportion is 1.33%. The above results indicate that polybenzoxazine exists on the surface of BMAPP.
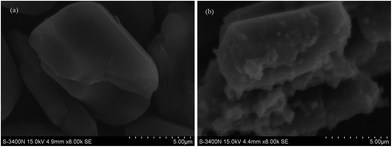 |
| Fig. 1 SEM photographs of (a) APP and (b) BMAPP. | |
Table 1 Surface elemental compositions of APP and BMAPP
Sample |
C (at%) |
O (at%) |
N (at%) |
P (at%) |
Si (at%) |
APP |
7.06 |
53.36 |
20.25 |
19.34 |
0 |
BMAPP |
42.96 |
34.30 |
13.08 |
8.33 |
1.33 |
WLR of BMAPP
The defined WLR is used here to evaluate the water resistance of APP and BMAPP. It can be seen on Fig. 2 that the WLR of APP is 99.5% at 30 °C, and it increases to 100% at higher temperatures. After modification, the WLR values of BMAPP demonstrate a drastic decrement, which is only 5.8% at 30 °C. It can be inferred that APP can be easily attacked by moisture or water. In contrast, due to the presence of a hydrophobic polybenzoxazine coating, the water resistance of BMAPP is significantly improved.
 |
| Fig. 2 Water leaching rate of APP and BMAPP. | |
Thermal degradation of BMAPP
TG and DTG curves of APP and BMAPP under an air atmosphere are given in Fig. 3(a) and (b). The related temperatures at which 5% (Tid) mass losses and the maximum decomposition rate (Tmax) occurred are listed.
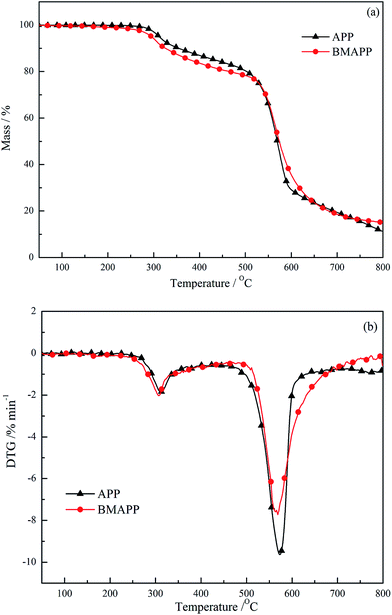 |
| Fig. 3 TG and DTG curves of APP and BMAPP under air atmosphere. | |
The decomposition of APP consists of two steps, the corresponding Tmax are 308 and 572 °C. The weight loss up to the onset temperature (Tid) of APP mainly evolves in the elimination of ammonia and the formation of a highly cross-linked polyphosphoric acid (PPA), which occurs at 311 °C. The second degradation stage has a mass loss of approximately 65% in the temperature range of 500–700 °C, which corresponds to PPA evaporation and/or dehydration to P4O10. Finally at 800 °C, the solid residue of APP is 11.4%.
The TG and DTG curves of BMAPP show different mass loss behaviors, as seen from the additional DTG peak maxima at 311 and 568 °C. Due to the decomposition of polybenzoxazine, the Tid of BMAPP is reduced by about 15 °C compared with that of APP and resulting in BMAPP decomposing faster than APP at the first stage. When the temperature is above 530 °C, BMAPP appears more stable than APP, which is probably the consequence of the formation of a thermally stable precursor char from polybenzoxazine. Polybenzoxazine obtain a high charred yield (40–80%) at 800 °C according to the literature,24–27 which contributes to blocking the heat transfer. As a result, the rate of weight loss of BMAPP is lower than that of APP at the second degradation stage; what’s more, 3.8% of a higher solid residue is left from BMAPP compared to APP at 800 °C (Table 2).
Table 2 TG and DTG data of APP and BMAPP under air atmosphere
Sample |
Tid (°C) |
Tmax (°C) |
Solid residue (wt%) |
APP |
311 |
308, 572 |
11.4 |
BMAPP |
296 |
311, 568 |
15.2 |
Flame retardancy of BMAPP in PU
Limiting oxygen index (LOI) and UL-94 flame retardancy rating of the composites are summarized in Fig. 4. Incorporation of APP into PU improves the flame retardancy based on the LOI value and UL-94 rating. The LOI value of APP/PU composites increased from 16.5% to 24.0% as the APP loading increased from 0 and to 16.7 wt%. The UL-94 rating of APP/PU specimen is promoted to V-0 by adding 16.7 wt% APP. A similar tendency for the LOI and UL-94 rating are found for the BMAPP filled specimens. However, the LOI values of the BMAPP/PU composites are higher than those of the APP/PU samples with the same APP content, which illustrates that BMAPP has relatively better flame retardancy in PU. Presumably, this better flame retardancy of BMAPP can be attributed to better dispersion and a more stable and higher amount of residue.
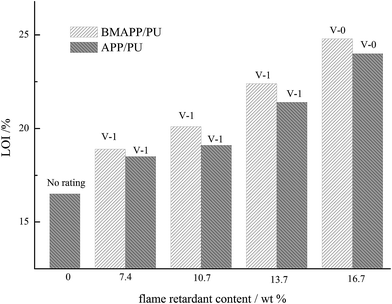 |
| Fig. 4 LOI value and UL-94 rating of PU composites. | |
Thermal behavior of PU composites
Thermal behaviors of the selected samples under air and N2 atmosphere are shown in Fig. 5 and 6, respectively. Table 3 and 4 accordingly collate the relevant data.
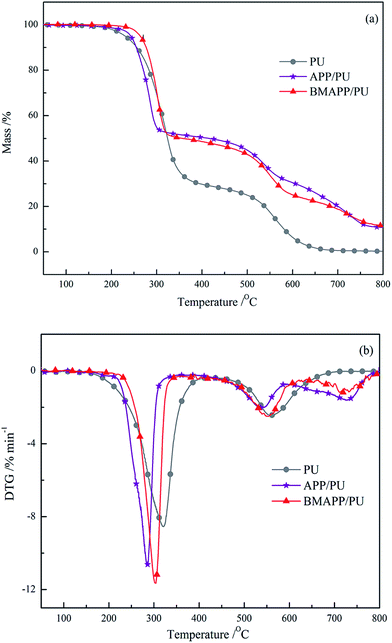 |
| Fig. 5 TG (a) and DTG (b) curves of PU, APP/PU (16.7 wt%) and BMAPP/PU (16.7 wt%) composites under an air atmosphere. | |
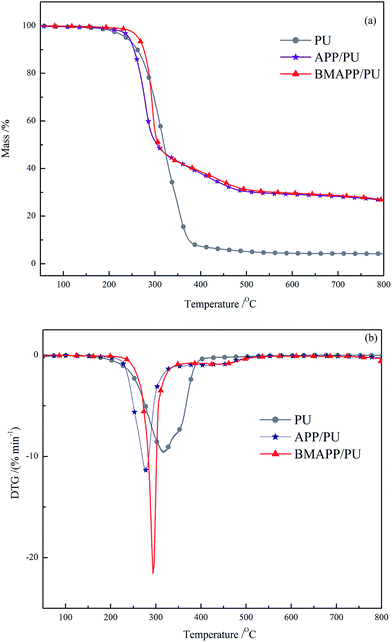 |
| Fig. 6 TG (a) and DTG (b) curves of PU, APP/PU (16.7 wt%) and BMAPP/PU (16.7 wt%) composites under an N2 atmosphere. | |
Table 3 TG and DTG data of PU composites under an air atmosphere
Sample |
Tid (°C) |
Tmax (°C) |
Solid residue (wt%) |
PU |
230 |
319, 561 |
0.22 |
APP/PU |
242 |
281, 537, 728 |
9.86 |
BMAPP/PU |
264 |
304, 556, 724 |
11.6 |
Table 4 TG and DTG data of PU composites under an N2 atmosphere
Sample |
Tid (°C) |
Tmax (°C) |
Solid residue (wt%) |
PU |
238 |
318 |
4.2 |
APP/PU |
243 |
276 |
26.6 |
BMAPP/PU |
264 |
294 |
26.8 |
The thermal degradation behaviours of PU, APP/PU and BMAPP/PU under an air atmosphere are completely different. Based on the DTG curves, PU degrades in a two-step process. Tid of pure PU is 230 °C, due to the addition of APP, Tid of APP/PU is increased to 242 °C. This phenomenon indicates that the flame retardant can enhance the thermal behavior. For BMAPP/PU, Tid is sharply improved by 34 °C as the TG curves depicted; it can be inferred that BMAPP has a significant effect on the improvement of the thermal stability under an air atmosphere. The reason might be attributed to the better dispersion and compatibility of BMAPP particles in PU compared with APP, which can prevent the PU chain from degrading at low temperatures.
At the first decomposition stage above Tid, APP/PU decomposes faster than PU because of the catalysis of polyphosphoric acids (PPAs) that are released from APP. Due to the presence of polybenzoxazine on the surface, the temperature of release of the PPAs is improved for BMAPP, which leads to a lower mass loss for BMAPP/PU than for APP/PU below 320 °C. As the temperature increases, polybenzoxazine degrades into a solid residue; BMAPP would degrade into PPA, which contributes to a slightly higher mass loss for BMAPP/PU compared with APP/PU above 324 °C up to 716 °C. At 800 °C, the residue yield of PU, APP/PU, BMAPP/PU are 0.22%, 9.86% and 11.6%, respectively.
Under an N2 atmosphere, PU, APP/PU and BMAPP/PU all show one degradation stage, and the corresponding Tmax are 318, 276 and 294 °C. Similarly to the thermal behavior under an air atmosphere, the Tid of BMAPP/PU is 26 °C higher than that of PU and 21 °C higher than that of APP/PU, which implies that the modification of APP can improve the thermal stability of BMAPP/PU. The thermal behaviors of APP/PU and BMAPP/PU are similar when the temperature is above 311 °C. Finally, at 800 °C, the residues left of PU, APP/PU and BMAPP/PU are 4.2%, 26.6% and 26.8%, respectively.
Char residue analysis
The char layer is a critical factor in flame retardant performance during combustion. Therefore, it is necessary to evaluate the char layers so as to further investigate the mechanism. The char residue of the composites after the LOI test are collected and then characterized via EDS, FTIR and SEM. The EDS results are depicted in Table 5, it can be observed that the char residue of the APP/PU composite contains 64.31 wt% C, 17.19 wt% O, 12.50 wt% P, and 5.99 wt% N. As for BMAPP/PU, due to the presence of polybenzoxazine, the P content of BMAPP is lower than that of APP, which leads to the percentage of P presenting a slight decrement. In addition, 0.58 wt% Si is detected. The SEM images of the residue are depicted in Fig. 7, cells can be obviously observed on Fig. 7(a); in contrast, the residue of PU/BMAPP after the LOI test is compact, the cells are collapsed and presented as an overburden layer, which is beneficial for the improvement of flame retardancy.
Table 5 Surface elemental compositions of the char residues collected from the composites (16.7 wt%) after the LOI test
Residue |
C |
O |
P |
N |
Si |
APP/PU/wt% |
64.31 |
17.19 |
12.50 |
5.99 |
0 |
BMAPP/PU/wt% |
60.64 |
21.07 |
10.37 |
7.35 |
0.58 |
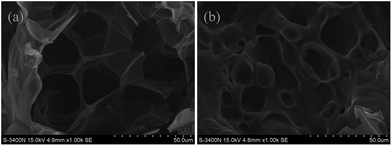 |
| Fig. 7 SEM images of the char residue of (a) APP/PU (16.7 wt%) and (b) BMAPP/PU (16.7 wt%). | |
Fig. 8 plots the FTIR spectra of the char residues of the composites. The earmark absorptions at 993, 1164, 1402 and 1635 cm−1 imply the presence of P–O–C, C–O–C, C–N, unsaturated –C
O, etc.16,28 However, an additional FTIR peak at 1085 cm−1 can be observed for the residue of BMAPP/PU, which might be assigned to the absorption of Si–O. The EDS and FTIR results indicate that polybenzoxazine, which is coated on the surface of BMAPP, is partially converted into the residue presented as Si–O during combustion.
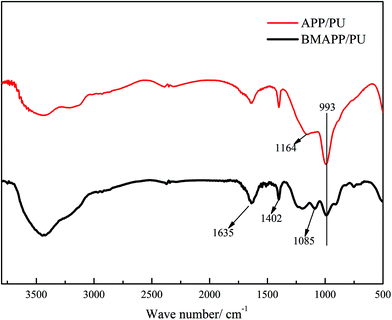 |
| Fig. 8 FTIR spectra of the char residues collected from the composites (16.7 wt%) after the LOI test. | |
TG-FTIR analysis of the BMAPP/PU composites
The thermal degradation characteristics of BMAPP/PU under both an air and nitrogen gaseous atmosphere are studied using TG-FTIR. Fig. 9 displays the three-dimensional spectrum and the volatile products detected by FTIR under air atmosphere. The broad range of peaks at 3500–3700 cm−1 can be assigned to absorptions of H2O. It can be detected from above 400 °C. The peaks in the region around 2200–2400 cm−1 are caused by CO2. It can be observed that the absorption intensity of the CO2 volatile products is fluctuating. From about 350 °C to 450 °C, the absorption intensity of CO2 is weakened. Compounds containing aromatic rings are confirmed by the peaks in the range of 1731–1450 cm−1.7,29,30
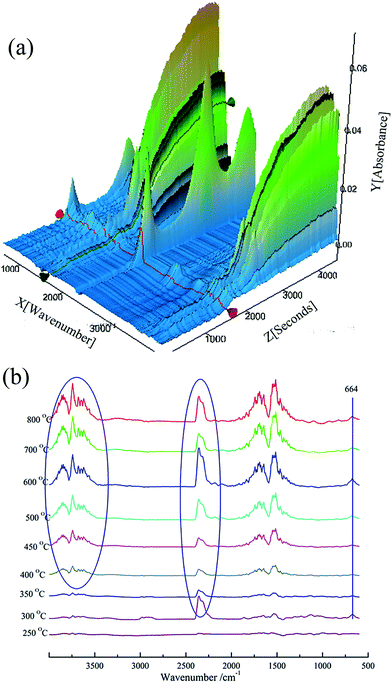 |
| Fig. 9 3D TG-FTIR spectrum (a) of the gas phase of BMAPP/PU (16.7 wt%) and the FTIR spectra (b) of the gas products at different temperatures during thermal degradation under an air atmosphere. | |
As for the pyrolysis of BMAPP/PU under an N2 atmosphere, the results are shown in Fig. 10. The main volatile products from BMAPP/PU under a nitrogen gaseous atmosphere are compounds containing aromatic rings and H2O, which corresponds to the peaks at 3500–3700 cm−1 and 1731–1450 cm−1. These absorptions can be observed from 250 °C and the absorption intensity gradually weakens. At around 300 °C, the peaks at 2352 and 667 cm−1 arise, which involves the production of CO2.
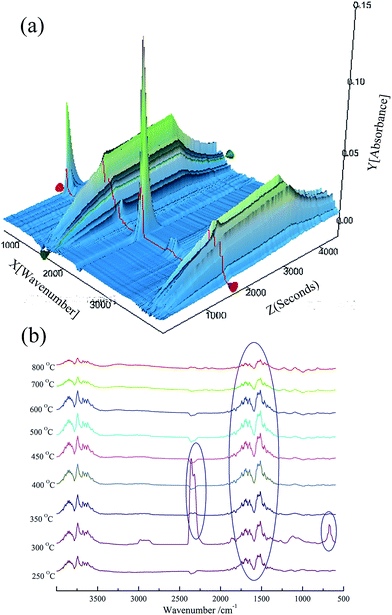 |
| Fig. 10 3D TG-FTIR spectrum (a) of the gas phase of BMAPP/PU (16.7 wt%) and the FTIR spectra (b) of the gas products at different temperatures during thermal degradation under an N2 atmosphere. | |
Conclusion
Polybenzoxazine is applied to modify APP in this paper and the resultant BMAPP is obtained. The influence of BMAPP on the thermal behavior and flame retardancy of a rigid polyurethane foam (PU) are remarkable. The LOI value results demonstrate that BMAPP has higher flame retardancy in PU than APP. The TG testing results indicate that BMAPP can enhance the thermal stability, both under air and nitrogen conditions. Due to the better dispersion and compatibility of BMAPP particles in PU compared with APP, the degradation of PU chains at low temperature can be prevented. Tid of BMAPP/PU is 264 °C under air conditions, which is 22 °C and 30 °C higher than that of the APP/PU composites and neat PU, respectively. The same as under air conditions, Tid of BMAPP/PU under an N2 atmosphere is 264 °C, while those of APP/PU and PU are 243 °C and 238 °C. The residue analysed via FTIR and EDS implies that polybenzoxazine, which is coated on the surface of BNAPP, is partially converted into Si–O as a char residue during combustion. The gas phase of BMAPP/PU is made of compounds containing aromatic rings, H2O and CO2 according to the TG-FTIR results.
Acknowledgements
The financial supports from the Guangdong Natural Science Foundation, China (No. 2015A030313798), Zhujiang Science & Technology New-star Program of Guangzhou, China (No. 2013J2200016) and Guangdong Special Support Program-Youth Top-notch Talent (No. 2014TQ01C400) are acknowledged.
References
- B. L. Xue, J. L. Wen and R. C. Sun, ACS Sustainable Chem. Eng., 2014, 2, 1474–1480 CrossRef CAS.
- C. Branca, C. D. Blasi, A. Casu, V. Morone and C. Costa, Thermochim. Acta, 2003, 399, 127–137 CrossRef CAS.
- K. I. Suresh, ACS Sustainable Chem. Eng., 2013, 1, 232–242 CrossRef CAS.
- L. Qian, F. Feng and S. Tang, Polymer, 2014, 55, 95–101 CrossRef CAS.
- L. Q. Fafei Feng, Polym. Compos., 2014, 35, 301–309 CrossRef.
- Y. L. Dennis Price, T. Richard Hull, G. John Milnes, B. K. Kandola and A. Richard Horrocks, Polym. Int., 2000, 49, 1153–1157 CrossRef.
- L. Jiao, H. Xiao, Q. Wang and J. Sun, Polym. Degrad. Stab., 2013, 98, 2687–2696 CrossRef CAS.
- N. Usta, J. Appl. Polym. Sci., 2012, 124, 3372–3382 CrossRef CAS.
- J. I. Sohn, S. T. Lim, S. H. Park, H. J. Choi and M. S. Jhon, J. Mater. Sci., 2003, 38, 1485–1491 CrossRef CAS.
- Z. Zheng, X. Cui and H. Wang, Polym. Compos., 2015, 36, 1606–1619 CrossRef CAS.
- S. Nie, Y. Hu, L. Song, Q. He, D. Yang and H. Chen, Polym. Adv. Technol., 2008, 19, 1077–1083 CrossRef CAS.
- X. Chen, Y. Jiang and C. Jiao, J. Hazard. Mater., 2014, 266, 114–121 CrossRef CAS PubMed.
- K. S. Lim, S. T. Bee, L. T. Sin, T. T. Tee, C. T. Ratnam, D. Hui and A. R. Rahmat, Composites, Part B, 2016, 84, 155–174 CrossRef CAS.
- Z.-B. Shao, C. Deng, Y. Tan, L. Yu, M.-J. Chen, L. Chen and Y.-Z. Wang, J. Mater. Chem. A, 2014, 2, 13955–13965 CAS.
- X. Chen, Y. Jiang and C. Jiao, J. Therm. Anal. Calorim., 2014, 117, 1–10 CrossRef.
- F. Luo, K. Wu, M. Lu, S. Nie, X. Li and X. Guan, J. Therm. Anal. Calorim., 2015, 120, 1327–1335 CrossRef CAS.
- D. Saihia, I. Vromana, S. Girauda and S. Bourbigotb, React. Funct. Polym., 2005, 64, 127–138 CrossRef.
- K. Wu, Y. Zhang, W. Hu, J. Lian and Y. Hu, Compos. Sci. Technol., 2013, 81, 17–23 CrossRef CAS.
- S. Nie, X. Liu, K. Wu, G. Dai and Y. Hu, J. Therm. Anal. Calorim., 2013, 111, 425–430 CrossRef CAS.
- F. Shukor, A. Hassan, M. S. Islam, M. Mokhtar and M. Hasan, Mater. Des., 2014, 54, 425–429 CrossRef CAS.
- Z. B. Shao, C. Deng, Y. Tan, M. J. Chen, L. Chen and Y. Z. Wang, Polym. Degrad. Stab., 2014, 106, 88–96 CrossRef CAS.
- W. Hu, B. Wang, X. Wang, H. Ge, L. Song, J. Wang and Y. Hu, J. Therm. Anal. Calorim., 2014, 117, 27–38 CrossRef CAS.
- A. Chernykh, J. Liu and H. Ishida, Polymer, 2006, 47, 7664–7669 CrossRef CAS.
- S. Tiptipakorn, S. Damrongsakkul, S. Ando, K. Hemvichian and S. Rimdusit, Polym. Degrad. Stab., 2007, 92, 1265–1278 CrossRef CAS.
- S. B. Shen and H. Ishida, J. Polym. Sci., Part B: Polym. Phys., 1999, 37, 3257–3268 CrossRef CAS.
- S. Rimdusit, W. Tanthapanichakoon and C. Jubsilp, J. Appl. Polym. Sci., 2006, 99, 1240–1253 CrossRef CAS.
- C. Jubsilp, T. Takeichi and S. Rimdusit, Polym. Degrad. Stab., 2011, 96, 1047–1053 CrossRef.
- S. V. Levchik and E. D. Weil, Polym. Int., 2004, 53, 1585–1610 CrossRef CAS.
- K. Pielichowski and A. Leszczyńska, J. Therm. Anal. Calorim., 2004, 78, 631–637 CrossRef CAS.
- X. Chen, L. Huo, C. Jiao and S. Li, J. Anal. Appl. Pyrolysis, 2013, 100, 186–191 CrossRef CAS.
|
This journal is © The Royal Society of Chemistry 2016 |
Click here to see how this site uses Cookies. View our privacy policy here.