DOI:
10.1039/C6RA17899E
(Paper)
RSC Adv., 2016,
6, 91111-91120
Sustainable valorization of flue gas CO2 and wastewater for the production of microalgal biomass as a biofuel feedstock in closed and open reactor systems
Received
13th July 2016
, Accepted 17th September 2016
First published on 19th September 2016
Abstract
As a green process development initiative, the potential of valorization of wastes, like domestic wastewater and coal-fired flue gas CO2, by Scenedesmus sp. was examined in closed and open reactor systems. The green microalga, when cultivated in the photobioreactor, produced 35.6% lipid and 10.4% carbohydrate with 46.1% increase in biomass productivity (185.7 ± 7.3 mg L−1 d−1) at an optimal flue gas CO2 concentration of 2.5% as compared to the control (0.03%, CO2). The culture also showed significant remediation of ammonium, nitrate, phosphate and COD by about 95%, 66%, 72%, and 93%, respectively. The raceway pond culture supplemented with 2.5% flue gas CO2 produced 24.1% lipid and 19.2% carbohydrate with 36% rise in biomass productivity (97.1 ± 2.7 mg L−1 d−1) when compared to the control. Fatty acid profiling showed a higher percentage of C16/C18. Thus, this study realized the goal and implemented the mandate of developing green and sustainable processes for converting inexpensive, but polluting wastes like flue gas and wastewater, into biofuel feedstock through microalgal cultivation.
1. Introduction
Microalgae attracts huge interest among researchers as a possible feedstock for the production of eco-friendly biofuel, because of its superiority over other energy crops and having other environmental benefits.1,2 Microalgae offer many advantages of having higher growth rate, biomass and lipid productivity, photosynthetic efficiency, CO2 biofixation rate and the capability for bioremediation of wastewater.3,4 Some researchers also reported that microalgae could be successfully used for simultaneously upgrading biogas production systems and facilitating anaerobic digester slurry treatment.5 However, the chief problem for microalgal based biofuel is its production cost and having different expenditure during microalgae cultivation mostly the huge requirement of freshwater, inorganic nutrients and synthetic CO2.6 Therefore, to make biofuel production commercially successful, it is essential to make the process of generating microalgal feedstock economically feasible.
Due to rapid industrialization, the concentration of CO2 in the atmosphere has risen to an alarming level of 400 ppm. Nearly 22% flue gas emission is mainly because of coal-fired power plants, which cause severe damage to our eco-system.7 Microalgae-based CO2 bio-fixation is an economical and eco-friendly approach to mitigate CO2 emissions and simultaneously, produce algal biomass for biofuel production. As documented earlier, approximately 1.8 kg of CO2 is required to generate 1 kg of microalgae biomass.8 Exhaust flue gases mainly from coal-fired power plants can be captured as an economical CO2 source for the cultivation of microalgae.9 This method of using coal-fired flue gas as the carbon source for microalgal cultivation concurrently diminish the biomass production cost and also counterbalance carbon dioxide emissions to the atmosphere.10 Weissman and Goebel showed that there is substantial economic benefit that may be accrued by extracting CO2 from flue gas instead of purchasing carbon dioxide.11 Typically, the coal-fired flue gas contains CO2 concentrations ranging from 10 to 15% (v/v), which may be a good resource of carbon for the growth of microalgae.12 However, it is necessary to supply optimal concentration of flue gas CO2 to achieve favorable microalgal biomass growth.
On the other hand, the continual release of domestic wastewaters into the aquatic ecosystem causes water pollution.13 Microalgal based wastewater treatment is an eco-friendly and sustainable option over conventional technologies, due to their nutrient removal capability at the tertiary stage of treatment, while potentially generating algal biomass for biofuel production using nutrient rich wastewater.14,15 Wastewater utilization as a nutrient source would not only eliminate the use of fertilizer, but also offset the production costs of large-scale algal cultivation. Woertz et al., demonstrated that algae are efficient means for wastewater treatment with nutrients removal capacity of more than 99% for ammonium and orthophosphate when supplemented with carbon dioxide.16 Some previous studies have indicated that domestic wastewater is a good nutrient source for microalgal production of biomass as the biofuels feedstock.9,17
Therefore, the combination of microalgal culture systems with coal-fired flue gas as the source of carbon and wastewater as the nutrient source could be a useful strategy to cut down the input expenditure of freshwater, synthetic CO2 and nutrients required for cultivation process of microalgae, and simultaneously facilitate in CO2 mitigation and wastewater treatment.18 This combined use of flue gas and wastewater helps to create environmental and economic credits by opposing the use of pure CO2 and synthetic nutrients for algal growth. An analysis by Lundquist et al., establishes that the process can generate enough revenue stream to make the process economical.19
Cultivation of microalgae in open raceway ponds are greatly prized as they are inexpensive to construct and its convenient operation regardless of their lesser biomass yields in comparison to closed photobioreactors.12 Microalga, Scenedesmus sp., is considered as a potential source of lipid for biodiesel production.20 Also, some species of Scenedesmus have been able to grow and sustain with supplementation of flue gas as the source of carbon.21 However, there are few reports on the integrated system for microalgae cultivation using coal-fired flue gas CO2 and domestic wastewater in closed and open culture systems.
Considering the urgent need for green and cost-effective process development on the basis of performance evaluation of the closed and open culture systems, while valorizing polluting wastes, the present study was undertaken to establish an integrated system for flue gas CO2 fixation, wastewater remediation and biomass feedstock generation for sustainable biofuel application. Primarily, this study evaluates the effect of using different concentration of real coal-fired flue gas CO2 in domestic wastewater for biomass growth, lipid and carbohydrate production, CO2 bio-fixation rate and nutrient removal efficiency of Scenedesmus sp. in the photobioreactor. Consequently, the suitability of growing microalgae in open raceway pond using coal-fired flue gas and domestic wastewater was demonstrated as a feasible strategy for algae biomass production.
2. Materials and methods
2.1. Microalgae, inoculum preparation and culture conditions
The green microalga, Scenedesmus sp. of chlorophycean class, was procured from the Indian Agricultural Research Institute (IARI), New Delhi, was utilized in this study. The modified bold's basal medium (BBM) was used for inoculum preparation.22 The 2% (Vinoculum/Vmedia) microalga was inoculated into a column photobioreactor with working volume of 0.5 L. Microalgal cells were cultured under photoperiod of 14
:
10 (light
:
dark cycle) illumination using white fluorescent tubes at light intensity of 3500 Lux at 25 ± 2 °C and with the influx of filter-sterilized air (0.03% CO2) with a flow rate of 0.5 vvm. The initial pH of the culture medium was 6.8. Microalgal cells after the mid exponential phase (i.e. on the 3rd day), were harvested by centrifugation and suspended in freshly sterilized wastewater to develop the inoculums with high biomass density. For further experiments, the inoculum showing the optical density of 0.1 at 750 nm that corresponded to the biomass of 0.04 g L−1 with 2% (v/v) size. All chemicals used in this study are of analytical grade and procured from Merck, India. All analysis was executed in triplicates and expressed as the mean ± standard deviation (SD).
2.2. Wastewater sampling and analysis
The domestic wastewater (DWW) was collected from IIT campus (IIT Kharagpur, India). The wastewater was first centrifuged at 4000 rpm for 15 min, and then the supernatant was autoclave at 121 °C for 20 min for sterilization before use as the culture medium for cultivation of microalgae. The supernatant culture medium was properly diluted and examine for BOD, COD, NH4+, NO3−, NO2− and PO43− by adopting the standard protocols of American public health association (APHA).23 The heavy metal contents of the wastewater samples were analyzed by ICP-MS. The characteristics of the wastewater were described in Table 1.
Table 1 Characteristics of domestic wastewater used in the experiments. Data were presented as the average of three replicates ± standard deviation (SD)
Parameters |
Concentration |
N–NH4 (mg L−1) |
38.6 ± 1.5 |
N–NO3 (mg L−1) |
17.1 ± 0.5 |
N–NO2 (mg L−1) |
0.34 ± 0.02 |
P–PO4 (mg L−1) |
9.24 ± 0.31 |
BOD (mg L−1) |
39.3 ± 2.1 |
COD (mg L−1) |
142.2 ± 5.2 |
Cr (μg L−1) |
60.2 ± 8.7 |
Ni (μg L−1) |
58.9 ± 3.5 |
Zn (μg L−1) |
347.2 ± 21.2 |
Cd (μg L−1) |
3.97 ± 0.42 |
Pb (μg L−1) |
68.9 ± 5.4 |
pH |
8.15 ± 0.05 |
2.3. Flue gas analysis
The flue gas was generated and collected through the indigenously designed in situ flue gas generator by burning coal.24 The flue gas generator was comprised of the three-chambered double layered jacket to lower the temperature of flue gas. The raw flue gas was collected from the top of the stack and then allowed to pass through a vacuum precipitator to eliminate the particulate matter. Subsequently, the flue gas was transferred to gas storage cylinder through compressor pump prior to supplying it to the algal culture system. The coal-fired flue gas comprised of carbon dioxide 12 ± 1% (v/v), carbon-monoxide 0.55% (v/v), oxygen 8.24% (v/v), nitrogen oxides 61 ppm, sulfur oxides 0.3% (v/v), other hydrocarbons 9 ppm. An online flue gas analyzer was used to know the constituents of the flue gas (Model: FGA 53X; make: INDUS Scientific, Mumbai, India).
2.4. Cultivation of microalgae
The experiments were performed in two phases. In the first phase, the experiment was performed to select an optimum flue gas CO2 concentration (%) according to biomass and lipid yield after 7 days of cultivation of Scenedesmus sp. using domestic wastewater. The second phase of the study was carried out in open raceway pond in batch experiments to determine the performance of algal biomass production. The concentrations of the flue gas CO2 was varied to 2.5%, 5% and 10% by mixing with air, and the ambient air (0.03% CO2) supply was used as the control. During incubation, 5 mL of culture was collected everyday for analytical study.
2.4.1. Cultivation of microalgae in photobioreactor. Microalga, Scenedesmus sp. of 2% inoculums size was grown in the domestic wastewater in the photobioreactor for 7 days in a batch mode. Different concentration of flue gas was aerated in the cultures at 0.5 vvm. Scenedesmus sp. was cultured at 25 ± 2 °C in a column photobioreactor (33 cm length, 4.5 cm inner diameter) with 500 mL of working volume. All cultures were supplied with a light intensity of 3500 Lux through cool white fluorescent tubes with a photoperiod of 14
:
10 h light and dark cycle. The intensity of supplied light was measured using a quantum meter (HTC LX 102 Lux Meter). The initial pH of the culture solution was maintained at 6.8 and the pH of the culture medium was measured using a pH meter (Deluxe pH Meter, Model LT-10).
2.4.2. Cultivation of microalgae with raceway pond. Subsequently, Scenedesmus sp. was cultivated in two outdoor raceway pond at Kharagpur (22.3302° N, 87.3237° E) with working volume of 60 L. To carry out the raceway pond experiment, the optimal flue gas CO2 concentration obtained from PBR studies i.e. flue gas with 2.5% CO2 and pure air as control was used. The outdoor raceway ponds used in this study were 110 cm length channels, had a channel width of one channel is 15 cm and 30 cm deep. The average depth of the working volume was 15 cm. The raceway pond is having the illuminated surface area of 0.3 m2. It was agitated for 24 h by a paddle wheel and rotated at a speed of 15 rpm, such that the linear velocity of the culture was 0.3 m s−1. The raceway pond was operated in batch mode for 7 days, and then biomass of Scenedesmus sp. was harvested. Inoculums preparation was done using a photobioreactor placed indoor with artificial light for the period of 3 days and inoculums size of 2% was used for the experiment. Evaporation losses were from 5 to 10% per day of the entire culture medium and were accordingly replenished with freshwater every morning. Solar intensities varied between 300 lx (early morning i.e. 6 AM and late evening i.e. 6 PM) to 48
000 lx (mid-day i.e. 12 AM). The light intensity was determined by a digital light meter (HTC, India; Model no. 102).
2.5. Growth of microalgae
The biomass yield (YB, g L−1) of microalga, Scenedesmus sp. was determined spectrophotometrically from the optical density of the culture through previously established biomass versus optical density calibration curve.20 The specific growth rate (μ, d−1) was calculated according to our previous study.20 The experiments were executed in triplicates, and the average values were reported.
2.5.1. Determination of kinetic parameters of algal growth. The logistic kinetic model was used to determine the growth kinetics of Scenedesmus sp. The model is a substrate independent equation and can precisely explain the entire growth profile (lag, exponential, and stationary phase) of algae.6 The logistic model is described by eqn (1). |
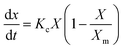 | (1) |
Integrating this equation, we get eqn (2),
|
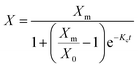 | (2) |
where,
t correspond to time,
X is the microalgal biomass concentration (g L
−1),
X0 is the initial concentration of algal biomass,
Xm is the maximum concentration of algal biomass, and
Kc is the apparent specific growth rate (d
−1). These constants were determined by fitting experimental data in
eqn (2) using the curve fitting tool in MATLAB.
2.6. Determination of carbon dioxide biofixation rate
The CO2 fixation efficiency by microalgae was calculated everyday in terms of the amount of CO2 that was captured by the microalga. Moreover, the carbon dioxide consumption rate (PCO2, mg L−1 d−1) was derived by using the following equation:where PB denotes the biomass productivity (mg L−1 d−1). This equation is derived from the typical molecular formula of microalgal biomass, CO0.48H1.83N0.11P0.01 which was used in this study where it assumes that one gram of produced microalgal biomass is equivalent to about 1.88 g of captured carbon dioxide.8,25
2.7. Analytical procedures and nutrient removal
The nutrient concentrations during the batch experiment were evaluated for the samples collected on 7 days of incubation time. The samples collected from different culture conditions were centrifuged at 3500 rpm, and the upper aqueous layer was then filtered through 0.22 mm membrane filter (Millipore). After filtration, the filtrate was appropriately diluted and analyzed for COD, PO43−, NH4+, NO3−, and NO2−. The standard protocols of American Public Health Association (APHA) were used to characterize the different nutrient concentration of wastewater. The removal percentage and removal rate of nutrients were calculated according to previously described method of our previous study.20
2.8. Analysis of lipid, carbohydrate content and fatty acid composition
Initially, the microalgal cell was harvested by centrifugation and then lyophilized. The modified method reported by Bligh and Dyer was used for extraction of total lipids from lyophilized microalgae culture, and lipids were quantified gravimetrically.26 The fatty acids methyl esters (FAMEs) were analyzed using a method described in our previous studies.
The concentration of carbohydrate was determined by using the phenol-sulfuric acid method.27 Each experiment was carried out in triplicate, and the average values were reported.
2.9. CHNS analysis
The microalgal biomass harvested from stationary growth stage by centrifugation was dried in a vacuum freeze-dryer. Carbon, hydrogen, nitrogen and sulfur percentages of microalgae biomass were determined using a CHNS analyzer (Elementar, vario Macro cube). The percent of oxygen was estimated by subtracting the relative percent of C, H, N, S from 100.
2.10. Statistical analysis
All the experiments were performed in triplicate, and the results of the study were expressed as the mean ± standard deviation (SD) of the three replicates. Standard deviations have been incorporated in the figures in the form of error bars. The Student's t-test was used to evaluate the difference between groups of discrete variables. A value of p < 0.05 was considered as statistically significant.
3. Result and discussion
3.1. Biomass growth and CO2 bio-fixation rate of Scenedesmus sp. with different flue gas CO2 concentrations in domestic wastewater
The growth performance of Scenedesmus sp. in the presence of varying flue gas CO2 (2.5%, 5% and 10% v/v) concentration in domestic wastewater was carried out in photobioreactor (Fig. 1a). In all culture conditions, the growth curve showed the shorter lag phase of one day, indicating the suitability of flue gas CO2 and wastewater as growth substrates for microalgae cultivation. Culture supplemented with flue gas containing 2.5% CO2 supported higher microalgae growth after 7 days of incubation, resulting in the biomass yield of 1.3 g L−1, on dry cell weight (DCW) basis, which was 1.46 times higher compared to the control, culture supplied with air (0.03% CO2, v/v). The biomass yields in culture supplied with flue gas CO2 were higher than the ambient air, implying that the flue gas as a carbon source facilitated the growth of microalgae. According to Jacob et al., flue gas containing 15–20% of CO2 (v/v) can be used for microalgae growth.28 However, the microalga biomass growth declined on supplementation with higher concentrations of flue gas CO2 (5% and 10%), which showed intolerance at higher CO2 concentration. It is well documented that the supply of high CO2 concentration reduces the conversion efficiency of light energy during the photosynthesis process.29 Moreover, the presence of hazardous flue gas components like SOx, NOx in higher flue gas concentration has shown adverse influence on microalgal growth.24 Table 2 summarizes various kinetic parameters like specific growth rate, doubling time, biomass yield, biomass productivity and CO2 fixation rate of Scenedesmus sp. in different flue gas concentrations. The culture supplemented with 2.5% flue gas CO2 showed the maximum specific growth rate of 0.501 ± 0.021 d−1, doubling time of 1.39 ± 0.05 d, biomass productivity of 185.7 ± 7.3 mg L−1 d−1 and CO2 fixation rate of 349.1 ± 13.8 g L−1 d−1.
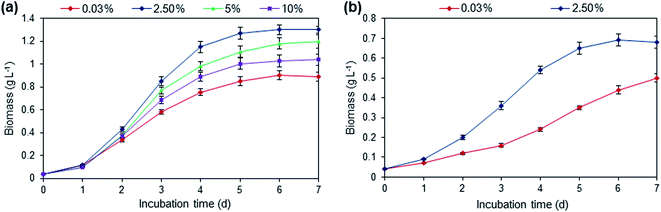 |
| Fig. 1 Growth curve of Scenedesmus sp. using photobioreactor (a) and raceway pond (b) in domestic wastewater supplemented with coal-fired flue gas CO2. The initial biomass concentration was approximately 0.04 g L−1. The cultures of microalgae were cultivated at 50 μmol m−2 s−1. The flue gas was provided at 0.5 vvm. The cultures were incubated for 7 days, and the culture were sampled every 24 h for determinations of biomass growth. Data were presented as the average of three replicates ± standard deviation (SD). | |
Table 2 The specific growth rate, biomass yield, biomass productivity and CO2 consumption rate for Scenedesmus sp. with different flue gas CO2 compositions in domestic wastewater for 7 days. Data were presented as the average of three replicates ± standard deviation (SD)
Flue gas CO2 (%) |
Specific growth rate μ (d−1) |
Doubling time T (d) |
Biomass yield YB, (g L−1) |
Biomass productivity PB, (mg L−1 d−1) |
CO2 fixation rate FRCO2, (mg L−1 d−1) |
Photobioreactor |
0.03% |
0.443 ± 0.017 |
1.56 ± 0.07 |
0.89 ± 0.03 |
127.1 ± 5.1 |
239.1 ± 9.5 |
2.5% |
0.501 ± 0.021 |
1.39 ± 0.05 |
1.31 ± 0.12 |
185.7 ± 7.3 |
349.1 ± 13.8 |
5% |
0.486 ± 0.019 |
1.43 ± 0.03 |
1.21 ± 0.11 |
171.4 ± 6.8 |
322.3 ± 12.8 |
10% |
0.465 ± 0.018 |
1.49 ± 0.06 |
1.04 ± 0.04 |
148.6 ± 5.9 |
279.3 ± 11.1 |
![[thin space (1/6-em)]](https://www.rsc.org/images/entities/char_2009.gif) |
Raceway pond |
0.03% |
0.361 ± 0.011 |
1.92 ± 0.07 |
0.51 ± 0.02 |
71.4 ± 3.1 |
134.3 ± 5.9 |
2.5% |
0.405 ± 0.013 |
1.71 ± 0.05 |
0.68 ± 0.02 |
97.1 ± 2.7 |
182.6 ± 5.2 |
To examine the possibility of cultivation of microalga, Scenedesmus sp., in outdoor culture condition at higher volume with the utilization of wastewater and coal-fired flue gas were studied. In this stage, algal cells were grown in outdoor raceway pond using domestic wastewater and optimal flue gas concentration (2.5%, v/v), obtained from the previous photobioreactor study. As a control experiment, microalga was also cultured with ambient air in open raceway pond. The growth curve of Scenedesmus sp. cultured in raceway pond showed nearly 2 days of lag phase for culture supplied with flue gas whereas lag phase of 3 days was observed for control experiment (Fig. 1b). As shown in Fig. 1b, microalgae cultivated in raceway pond supplemented with flue gas had better growth than that of the control. The stationary phase of algal growth was observed after 5 days of incubation in raceway pond with flue gas supplementation. Clearly, microalgae cultivated in raceway pond with flue gas showed better biomass growth and productivity compared to culture with air aeration (Table 2). This higher biomass yield with flue gas supplementation in raceway pond was mainly due to the presence of CO2 as the carbon source in the aqueous culture. The supply of CO2 tends to increase the dissolved carbon in the culture solution.25 As shown in Table 2, raceway pond aerated with flue gas showed the maximum specific growth rate of 0.405 d−1, doubling time of 1.71 d, biomass yield of 0.68 g L−1, biomass productivity of 97.1 mg L−1 d−1 and CO2 fixation rate of 182.63 g L−1 d−1. In the case of ambient air aeration, in raceway pond, the algal culture resulted in a lower performance of growth and CO2 fixation after 7 days of incubation. This indicates that Scenedesmus sp. had a good tolerance to flue gas and can be cultivated in the open system. Table 3 shows the comparative results of various reported studies with respect to flue gas carbon dioxide including the present study.12,20,30,31
Table 3 Comparative results of various reported studies with respect to flue gas carbon dioxide
Microalgae |
CO2% & vvm |
Culture medium |
Culture type |
Cultivation time (d) |
Biomass concentration (g L−1) |
Biomass productivity (mg L−1 d−1) |
Growth rate (d−1) |
Reference |
Chlorella sorokiniana |
4% flue gas (oil industry) & 0.33 |
Modified TAP |
Photobioreactor (airlift) |
8 |
1.1 |
150 |
0.44 |
Kumar et al.30 |
Scenedesmus sp. |
2.5% (CO2 enriched gas) & 0.5 |
Domestic wastewater |
Photobioreactor (airlift) |
7 |
1.37 |
196 |
0.51 |
Nayak et al.20 |
C. sorokiniana |
12% flue gas |
Centrate media |
Photobioreactors |
4 |
0.33 |
— |
1.68 |
Lizzul et al.31 |
Nannochloropsis oceanica |
13% coal-fired flue gas |
Industrial medium |
Raceway pond |
15 |
0.34 |
— |
0.051 |
Zhu et al.12 |
Scenedesmus sp. |
2.5% (coal flue gas CO2) & 0.5 |
Domestic wastewater |
Photobioreactor (airlift) |
7 |
1.3 |
185.7 |
0.501 |
This study |
Scenedesmus sp. |
2.5% (coal flue gas CO2) & 0.5 |
Domestic wastewater |
Open raceway pond |
7 |
0.68 |
97.1 |
0.405 |
This study |
To enhance the economics of the process, it is essential to decrease the cost associated with utilization of synthetic CO2 and inorganic nutrient (mainly nitrogen and phosphorus) for microalgae cultivation. The above results suggested that the use of 2.5% coal-fired flue gases with domestic wastewater substituted from costly pure CO2 as a source of carbon with freshwater and inorganic nutrient for autotrophic growth of microalga, Scenedesmus sp. reduces the cost for biomass production of microalgae and enhances the feasibility of the process.
The experimental growth data of optimal flue gas conditions (2.5% CO2, v/v) obtained from photobioreactor and raceway pond were fitted with the logistic model. The logistic kinetic constants X0, Xm, and Kc with flue gas 2.5% CO2 in photobioreactor were 0.036 g L−1, 1.306 g L−1, 1.402 d−1 (r2 = 0.99). However, in outdoor raceway pond, logistic constants X0, Xm, and Kc were 0.032 g L−1, 0.708 g L−1, and 1.051 d−1 (r2 = 0.98), respectively. Model fitting with experimental data resulted in the regression coefficient (r2) higher than 0.98. The model demonstrated reasonably good fit with the experimental results (Fig. 2a and b).
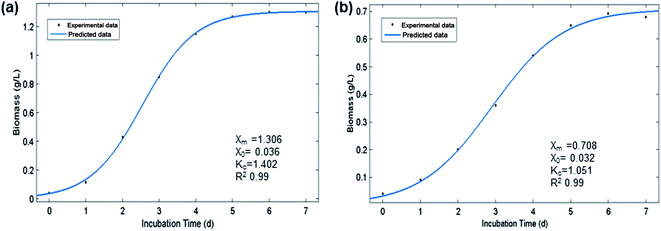 |
| Fig. 2 Experimental data and model prediction for biomass growth of Scenedesmus sp. supplemented with 2.5% flue gas CO2 in photobioreactor (a) and raceway pond (b) using the logistic equation. Solid lines indicate the predicted values and the experimental values are shown by the symbols (closed circle). Data were presented as the average of three replicates ± standard deviation (SD). | |
3.2. Influence of different coal-fired flue gas CO2 concentration on pH change in aqueous culture media
Fig. 3a shows the pH change in the culture media during microalgae cultivation in photobioreactor aerated with different concentration of coal-fired flue gas CO2. The culture supplemented with 2.5% flue gas CO2 was found suitable for biomass growth with the pH value ranging from 6.9 to 7.6, which was found within the optimal range for Scenedesmus sp. for better growth than other culture conditions (Fig. 3a). The pH value ranging from 7 to 8 have been reported favorable for the growth of freshwater microalgae.32 In all culture conditions, the gradual increase in pH was observed with incubation time, and this change of pH towards more alkalinity was due to the growth of microalgae where utilization of carbon and formation of OH− ion occur in the process of photosynthesis.25 The highest pH value of nearly 8.5 was observed in culture aerated with ambient air (0.03% of CO2). Although the microalgae showed biomass growth in the wide range of pH from 6.6 to 8.5, while the highest biomass productivity was recorded at pH 7.6. Similar result was observed by Maraskolhe et al. where the Scenedesmus sp. could be grown in the wide ranges of pH.33 In open raceway pond study, the pH value ranged from 6.9 to 7.9 in culture supplemented with the flue gas, while the pH value for culture supplemented with only air varied from 7.8 to 8.6 (Fig. 3b).
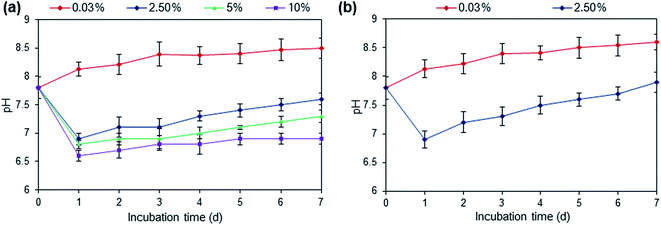 |
| Fig. 3 The pH value of Scenedesmus sp. using photobioreactor (a) and raceway pond (b) in domestic wastewater supplemented with coal-fired flue gas CO2. The initial pH value was approximately 7.8. The microalgal cells were cultivated at 50 μmol m−2 s−1. The flue gas was provided at 0.5 vvm. The cultures were grown for 7 days, and the microalgal cells culture were sampled every 24 h for growth determinations. Data were presented as the average of three replicates ± standard deviation (SD). | |
3.3. Nutrient removal capacity under varying flue gas CO2 addition
The removal capacity of various parameters such as NH4+, NO3−, PO43− and COD by Scenedesmus sp. was determined in domestic wastewater on the 7th day of incubation time (Table 4). Similar to biomass growth data, the maximum nutrients removal capacity of microalgae was also observed under the most favorable 2.5% CO2 concentration in the flue gas and strongly correlated with the microalgal growth (Table 4). The concentration (mg L−1) ratio of N/P in domestic wastewater was found to be 6.1, and this ratio can change according to the place and time of collection in a domestic treatment plant. It is reported that the N/P ratio in the range of 6.8–10 is considered most favorable for freshwater microalgae.15 The nutrient removal percentage of NH4+, NO3−, PO43− and COD were found to be 95.3%, 66.1%, 71.9%, and 93.1%, respectively, was observed in 2.5% CO2 flue gas when carried out in the photobioreactor. Whereas the nutrient removal rate of 5.26 ± 0.22 mg L−1 d−1, 1.61 ± 0.03 mg L−1 d−1, 0.95 ± 0.02 mg L−1 d−1 and 18.9 ± 0.4 mg L−1 d−1, was found for NH4+, NO3−, PO43− and COD respectively. However, the control experiment with ambient air showed the least nutrient removal capacity for all the nutrients. The nutrient removal efficiency was observed to be directly correlated with the biomass growth performance of microalgae. In raceway pond, the nutrients removal percentage by microalgae was found to be 75.4 ± 2.9%, 49.7 ± 3.3%, 55.6 ± 2.7% and 49.4 ± 3.1% for NH4+, NO3−, PO43− and COD, respectively, whereas the removal rate was found to be 4.16 ± 0.11 mg L−1 d−1, 1.21 ± 0.01 mg L−1 d−1, 0.73 ± 0.02 mg L−1 d−1 and 10.1 ± 0.4 mg L−1 d−1, respectively (Table 4). It was observed that the removal percentage and removal rate was found to be more with ammonium in comparison to nitrate. In the literature, it was also reported that ammonium is among the most common forms of nitrogen that can be readily absorbed by most microalgal species.34
Table 4 Removal efficiency of NH4+, NO3−, PO43−, and COD. Data were presented as the average of three replicates ± standard deviation (SD)
Flue gas CO2 (%) |
Nutrient removal (%) |
Nutrient removal rate (mg L−1 d−1) |
NH4+ |
NO3− |
PO43− |
COD |
NH4+ |
NO3− |
PO43− |
COD |
Photobioreactor |
0.03% |
84.7 ± 3.3 |
50.3 ± 2.1 |
60 ± 2.7 |
71.2 ± 3.7 |
4.67 ± 0.31 |
1.23 ± 0.01 |
0.79 ± 0.02 |
14.5 ± 0.3 |
2.5% |
95.3 ± 3.7 |
66.1 ± 3.1 |
71.9 ± 2.9 |
93.1 ± 3.3 |
5.26 ± 0.22 |
1.61 ± 0.03 |
0.95 ± 0.02 |
18.9 ± 0.4 |
5% |
91.9 ± 3.2 |
58.5 ± 2.9 |
66.4 ± 2.1 |
90.1 ± 3.2 |
5.07 ± 0.24 |
1.43 ± 0.04 |
0.88 ± 0.04 |
18.3 ± 0.7 |
10% |
84.9 ± 2.7 |
54.9 ± 2.8 |
62.1 ± 3.1 |
83.8 ± 3.9 |
4.69 ± 0.31 |
1.34 ± 0.06 |
0.82 ± 0.01 |
17 ± 0.3 |
![[thin space (1/6-em)]](https://www.rsc.org/images/entities/char_2009.gif) |
Raceway pond |
0.03% |
71.2 ± 3.4 |
32.2 ± 3.7 |
53.4 ± 2.5 |
46.5 ± 3.6 |
3.93 ± 0.23 |
0.79 ± 0.02 |
0.71 ± 0.01 |
9.5 ± 0.3 |
2.5% |
75.4 ± 2.9 |
49.7 ± 3.3 |
55.6 ± 2.7 |
49.4 ± 3.1 |
4.16 ± 0.11 |
1.21 ± 0.01 |
0.73 ± 0.02 |
10.1 ± 0.4 |
3.4. Total lipid accumulation under varying flue gas CO2 addition
Fig. 4a shows the total lipid content and lipid productivity after harvesting microalgae on 7th day of cultivation in the photobioreactor. Microalga, Scenedesmus sp. grown in domestic wastewater supplemented with 2.5, 5 and 10% CO2 showed total lipid content and lipid productivity ranging from 25.1 to 35.6% and 31.9 to 66.1 mg L−1 d−1, respectively, on dry cell weight basis. As indicated in Fig. 4a the highest lipid content of 35.6% and lipid productivity of 66.1 mg L−1 d−1 were observed in culture supplemented with 2.5% flue gas CO2 and this might be mainly due to the deprivation of nitrogen and phosphorus in the culture medium on the 7th day of incubation. Previously reported studies have also indicated that depletion of nitrogen and phosphorus resulted in enhanced lipid content in microalgae.35 It is also suggested that CO2 concentration could also affect the lipid content in microalgae.36 The microalgae incubated in open raceway pond, supplemented with coal-fired flue gas showed lipid content of 24.1% and lipid productivity of 23.4 mg L−1 d−1 on 7th day whereas with air aeration resulted in lipid content of 18.8% and lipid productivity of 13.4 mg L−1 d−1 on the 7th day of incubation (Fig. 4b). The high lipid productivity of microalgae cultivated in wastewater with flue gas have been proven advantageous, besides previous studies have also suggested potential synergy in the utilization of nutrient from wastewater and carbon source from flue gas for cost-effective biofuel production.34,35
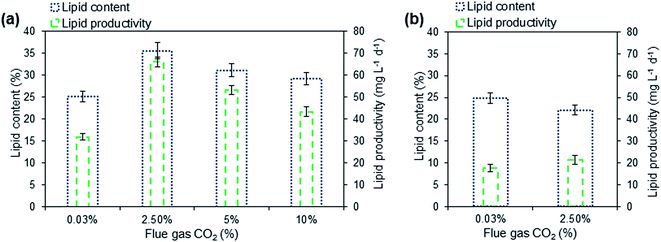 |
| Fig. 4 Lipid productivity and lipid percentage for Scenedesmus sp. using photobioreactor (a) and raceway pond (b) with different concentration of coal-fired flue gas CO2 in domestic wastewater for 7 days. Data were presented as the average of three replicates ± standard deviation (SD). | |
3.5. FAME profile under varying flue gas CO2 addition
The quality of biodiesel can be analyzed and characterized by the FAME profile of microalgal oil.37 Moreover, the compositions of the fatty acids profile in microalgae alter with different culture conditions (Table 5). Major fatty acid components like C16:0, C18:0, C16:1, C18:1, C18:2 and C18:3 accounted for nearly 80.4–86.8% of the total fatty acids by Scenedesmus sp. in photobioreactor aerated with different flue gas CO2. These fatty acid components are known to be beneficial for biodiesel application.32 In the photobioreactor study, the amount of saturated (SFA), monounsaturated (MUFA) and polyunsaturated (PUFA) fatty acids of the total fatty acids in the microalga ranged from 48.2 to 52.4%, 20.7 to 25% and 26 to 30%, respectively. In raceway pond study, culture supplemented with flue gas showed high SFA of 52.3%, and UFA of 47.7% which is beneficial for high-quality biodiesel (Table 5). Additionally, the balanced ratio of saturated (SFA) and unsaturated (UFA) fatty acids, which were found in all culture conditions, is beneficial for biodiesel application.6 Thus, the fatty acid profiles obtained from Scenedesmus sp. lipid in all the culture conditions were found to be suitable for biodiesel application, thereby making it a potential candidate as the biofuel feedstock.
Table 5 Changes in fatty acid profile of Scenedesmus sp. cultivated under different condition. Data were presented as the average of three replicates
Fatty acids |
Photobioreactor |
Raceway pond |
0.03% |
2.5% |
5% |
10% |
0.03% |
2.5% |
C16:0 |
29.2 |
31.7 |
27.2 |
25.2 |
29.8 |
33.1 |
C16:1 |
7.1 |
6.3 |
6.4 |
6.5 |
6.3 |
6.1 |
C18:0 |
4.1 |
4.3 |
5.8 |
7.1 |
5.2 |
6.7 |
C18:1 |
14.5 |
18.7 |
16.1 |
14.2 |
13.4 |
16.8 |
C18:2 |
17.4 |
18.9 |
16.3 |
19.2 |
16.2 |
18.1 |
C18:3 |
8.1 |
6.9 |
10.1 |
9.5 |
6.1 |
5.9 |
Total SFA |
52.4 |
48.2 |
50.2 |
49.3 |
57.7 |
52.3 |
Total MUFA |
21.6 |
25 |
22.5 |
20.7 |
19.7 |
22.9 |
Total PUFA |
26 |
26.8 |
27.3 |
30 |
22.6 |
24.8 |
Total UFA |
47.6 |
51.8 |
49.8 |
50.7 |
42.3 |
47.7 |
C16–C18 |
80.4 |
86.8 |
81.9 |
81.7 |
77 |
86.7 |
3.6. CHNS analysis of Scenedesmus sp. under varying flue gas CO2 addition
Table 6 shows the CHNS analysis of lyophilized Scenedesmus sp. biomass under different culture conditions. The biomass composition with respect to major elements like carbon, hydrogen, nitrogen and oxygen ranged between 49.6% to 52.1%, 6.1% to 7.2%, 6.2% to 6.8% and 34.1% to 37.8%, respectively. The C/N composition of microalgal biomass varied from 7.4 to 8.4. The lowest C/N ratio of 7.4 was found in the control experiment, whereas, the highest C/N of 8.4 was found in culture aerated with 2.5% flue gas CO2. In general, superior C/N of lyophilized biomass shows elevated lipid accumulation. In raceway pond, C/N ratio in culture supplemented with flue gas was found to be 8.1 as opposed to 7.8 for the culture bubbled with pure air.
Table 6 Elemental analysis of algal biomass of microalgae. Data were presented as the average of three replicates
Flue gas CO2% |
C (%, w/w) |
H (%, w/w) |
N (%, w/w) |
S (%, w/w) |
O (%, w/w) |
C/N |
Photobioreactor |
0.03% |
50.2 |
6.9 |
6.8 |
0.3 |
35.8 |
7.4 |
2.5% |
52.1 |
7.2 |
6.2 |
0.4 |
34.1 |
8.4 |
5% |
49.6 |
6.1 |
6.3 |
0.2 |
37.8 |
7.9 |
10% |
50.1 |
6.3 |
6.5 |
0.3 |
36.8 |
7.7 |
![[thin space (1/6-em)]](https://www.rsc.org/images/entities/char_2009.gif) |
Raceway pond |
0.03% |
51.4 |
6.6 |
6.6 |
0.3 |
35.1 |
7.8 |
2.5% |
52 |
7.2 |
6.4 |
0.5 |
33.9 |
8.1 |
3.7. Carbohydrate content under varying flue gas CO2 concentration
Due to the higher percentage of carbon found in the algal biomass, the carbohydrate content was estimated, which can be used as a substrate for bioethanol production. Carbohydrate is one of the major components in the algal biomass; mainly composed of starch and cellulose. The total carbohydrate content and carbohydrate productivity were determined on the 7th day of incubation (Fig. 5). The carbohydrate content of Scenedesmus sp. ranged from 10.4–13.6% based on their dry biomass when supplemented with flue gas CO2 concentration of 0.03% (ambient air), 2.5%, 5% and 10% in the photobioreactor. The content of carbohydrate was found to be lower in comparison to lipid and protein. With the increasing CO2 concentration the carbohydrate content also enhanced, thus, indicating the presence of CO2 influences the accumulation of carbohydrate in microalgae. Similar results were reported in microalgae where carbohydrate accumulation was enhanced under higher CO2 concentration.38 The maximum carbohydrate productivity of the Scenedesmus sp. was observed to be 20.2 mg L−1 d−1 in 10% flue gas CO2 supplementation in domestic wastewater (Fig. 5a).
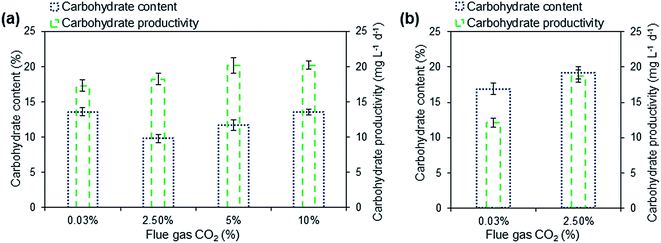 |
| Fig. 5 Carbohydrate productivity and carbohydrate percentage for Scenedesmus sp. using photobioreactor (a) and raceway pond (b) with different concentration of coal-fired flue gas CO2 in domestic wastewater for 7 days. Data were presented as the average of three replicates ± standard deviation (SD). | |
In open culture condition, the carbohydrate content and productivity were found to be higher than enclosed photobioreactor (Fig. 5b). The carbohydrate content of 21.9% was observed in raceway using ambient air, which was found to be slightly higher compared to culture aerated with flue gas of 19.2%. Whereas the carbohydrate productivity was found to be greater in flue gas supplementation (18.7 mg L−1 d−1) when compared to culture aerated with air aeration (15.6 mg L−1 d−1).
4. Conclusion
The microalga, Scenedesmus sp. demonstrated significant production of biomass, lipid, and carbohydrate as biofuel feedstock with efficient nutrient uptake from domestic wastewater, on supplementation of coal-fired flue gas CO2 (2.5%, v/v) in the closed photobioreactor. A subsequent study in open raceway pond, supplemented with 2.5% (v/v) flue gas CO2 in wastewater, showed enhanced biomass and lipid production by Scenedesmus sp. when compared to the control with air (0.03% CO2). Higher content of C16–C18 fatty acid implies good quality biofuel. Thus, green processes were developed and standardized as sustainable, eco-friendly and cost-effective strategies for biofuel production with simultaneous CO2 sequestration and wastewater valorization.
Acknowledgements
Authors thankfully acknowledge the financial support received from the Department of Science & Technology (DST), Government of India, for the project grant (No. DST/IS-STAC/CO2-SR-160/13(G); Date: 08.07.2013). The authors are also grateful to Indian Agricultural Research Institute, New Delhi for providing their microalgal strains.
References
- G. Subramanian, G. Yadav and R. Sen, RSC Adv., 2016, 6, 72897–72904 RSC.
- M. Nayak, J. Jena, S. Bhakta, S. S. Rath, C. Sarika, B. V. S. K. Rao, N. Pradhan, M. Thirunavoukkarasu, S. K. Mishra, P. K. Panda, R. B. N. Prasad, L. B. Sukla and B. K. Mishra, Int. J. Green Energy, 2011, 8, 669–683 CrossRef CAS.
- P. J. McGinn, K. E. Dickinson, S. Bhatti, J. Frigon, S. R. Guiot and S. J. B. O'Leary, Photosynth. Res., 2011, 109, 231–247 CrossRef CAS PubMed.
- G. Subramanian, R. Dineshkumar and R. Sen, RSC Adv., 2016, 6, 51941–51956 RSC.
- C. Yan, L. Zhu and Y. Wang, Appl. Energy, 2016, 178, 9–18 CrossRef CAS.
- A. Karemore and R. Sen, RSC Adv., 2015, 5, 70929–70938 RSC.
- B. S. Vaz, J. A. V. Costa and M. G. Morais, Appl. Biochem. Biotechnol., 2016, 178, 418–429 CrossRef CAS PubMed.
- Y. Chisti, Biotechnol. Adv., 2007, 25, 294–306 CrossRef PubMed.
- F.-F. Li, Z.-H. Yang, R. Zeng, G. Yang, X. Chang, J.-B. Yan and Y.-L. Hou, Ind. Eng. Chem. Res., 2011, 50, 6496–6502 CrossRef.
- R. Dineshkumar, S. K. Dash and R. Sen, RSC Adv., 2015, 5, 73381–73394 RSC.
- J. C. Weissman and R. P. Goebel, Design and Analysis of Microalgal Open Pond Systems for the Purpose of Producing Fuels: A Subcontract Report, Sol. Energy Res. Inst., Golden, CO, USA, 1987 Search PubMed.
- B. H. Zhu, F. Q. Sun, M. Yang, L. Lu, G. P. Yang and K. H. Pan, Bioresour. Technol., 2014, 174, 53–59 CrossRef PubMed.
- T. Cai, S. Y. Park and Y. Lin, Renewable Sustainable Energy Rev., 2013, 19, 360–369 CrossRef CAS.
- A. L. Goncalves, J. C. M. Pires and M. Simoes, RSC Adv., 2016, 6, 22896–22907 RSC.
- L. D. Zhu and E. Hiltunen, Renewable Sustainable Energy Rev., 2016, 54, 1285–1290 CrossRef CAS.
- I. Woertz, A. Feffer, T. Lundquist and Y. Nelson, J. Environ. Eng., 2009, 135, 1115–1122 CrossRef CAS.
- R. A. I. Abou-Shanab, M.-K. Ji, H.-C. Kim, K.-J. Paeng and B.-H. Jeon, J. Environ. Eng., 2013, 115, 257–264 CAS.
- L. Jiang, S. Luo, X. Fan, Z. Yang and R. Guo, Appl. Energy, 2011, 88, 3336–3341 CrossRef CAS.
- T. J. Lundquist, I. C. Woertz, N. W. T. Quinn and J. R. Benemann, A realistic technology and engineering assessment of algae biofuel production, Energy Biosciences Institute, Univ. of California, Berkeley, 2010 Search PubMed.
- M. Nayak, A. Karemore and R. Sen, Algal Res., 2016, 16, 216–223 CrossRef.
- Z.-L. Sun, S.-Z. Xue, C.-H. Yan, W. Cong and D.-Z. Kong, RSC Adv., 2016, 6, 2703–2711 RSC.
- J. R. Stein, Handbook of phycological methods: culture methods and growth measurements, Cambridge Univ. Press, Cambridge, UK, 1973 Search PubMed.
- Standard Methods for the Examination of Water and Wastewater, ed. A. D. Eaton, L. S. Clesceri and A. E. Greenburg, APHA, Washington D.C., 21st edn, 1998 Search PubMed.
- G. Yadav, A. Karemore, S. K. Dash and R. Sen, Bioresour. Technol., 2015, 191, 399–406 CrossRef CAS PubMed.
- M. Nayak, S. S. Rath, M. Thirunavoukkarasu, P. K. Panda, B. K. Mishara and R. C. Mohanty, J. Microbiol. Biotechnol., 2013, 23, 1260–1268 CrossRef CAS PubMed.
- E. G. Bligh and W. J. Dyer, Can. J. Biochem. Physiol., 1959, 37, 911–917 CrossRef CAS PubMed.
- P. Rao and T. N. Pattabiraman, Anal. Biochem., 1989, 181, 18–22 CrossRef CAS PubMed.
- A. Jacob, A. Xia and J. D. Murphy, Appl. Energy, 2015, 148, 396–402 CrossRef CAS.
- J. C. M. Pires, M. C. M. Alvim-Ferraz, F. G. Martins and M. Simoes, Renewable Sustainable Energy Rev., 2012, 16, 3043–3053 CrossRef CAS.
- K. Kumar, D. Banerjee and D. Das, Bioresour. Technol., 2014, 152, 225–233 CrossRef CAS PubMed.
- A. M. Lizzul, P. Hellier, S. Purton, F. Baganz, N. Ladommatos and L. Campos, Bioresour. Technol., 2014, 151, 12–18 CrossRef CAS PubMed.
- D. Tang, W. Han, P. Li, X. Miao and J. Zhong, Bioresour. Technol., 2011, 102, 3071–3076 CrossRef CAS PubMed.
- V. R. Maraskolhe, A. R. Warghat, G. Charan and P. B. Nandhar, Afr. J. Agric. Res., 2012, 7, 2818–2823 Search PubMed.
- S. A. Razzak, M. M. Hossain, R. A. Lucky, A. S. Bassi and H. de Lasa, Renewable Sustainable Energy Rev., 2013, 27, 622–653 CrossRef CAS.
- M. K. Ji, R. A. I. Abou-Shanab, S. H. Kim, E. S. Salama, S. H. Lee, A. N. Kabra, Y. S. Lee, S. Hong and B. H. Jeon, Ecological Engineering, 2013, 58, 142–148 CrossRef.
- L. Brennan and P. Owende, Renewable Sustainable Energy Rev., 2010, 14, 557–577 CrossRef CAS.
- M. K. Ji, R. A. I. Abou-Shanab, S. H. Kim, E. S. Salama, S. H. Lee, A. N. Kabra, Y. S. Lee, S. Hong and B.-H. Jeon, Ecological Engineering, 2013, 58, 142–148 CrossRef.
- M. K. Ji, H. S. Yun, Y. T. Park, A. N. Kabra, I. H. Oh and J. Choi, J. Environ. Manage., 2015, 159, 115–120 CrossRef PubMed.
|
This journal is © The Royal Society of Chemistry 2016 |
Click here to see how this site uses Cookies. View our privacy policy here.