A balance-in-a-box: an integrated paper-based weighing balance for infant birth weight determination†
Received
8th October 2016
, Accepted 21st November 2016
First published on 29th November 2016
Abstract
The birth weight of babies is generally used as a health state indicator but is not often recorded in resource-poor settings due to limited access to medical clinics. In this work we develop a low-cost and lightweight “balance-in-a-box” that could allow remote communities to have access to a weighing balance. The “balance-in-a-box” is a cardboard mailing box which is reconstructed to form the balance tray, with a novel piezoresistive pressure sensor underneath, a paper-based readout system and battery integrated with copper tape to form an electrical circuit. The readout system comprises multiple segments of electrochromic Prussian blue/polyaniline on conductive gold nanoparticle films connected by graphite resistive separators. The color of each segment is voltage dependent and is directly correlated to the weight applied to the pressure sensor. It is shown that by varying the properties of the readout system (total resistance, individual resistance values of the graphite separators and number of gold nanoparticle segments) that it is possible to tune the critical weight values in which the gold nanoparticle segments change color. Overall, this work demonstrates that babies can be classified as very low birth weight (<1.5 kg), low birth weight (1.5 to 2.5 kg) or healthy (>2.5 kg) using a simple, integrated paper-based system that can be deployed to resource-poor settings where babies are at greatest risk of being underweight and requiring health care treatment.
1. Introduction
A reduction of low birth weight infants is one of the major Millennium Development Goals adopted by the United Nations.1 The World Health Organisation (WHO) has defined low birth weight as less than 2.5 kg, which can be subcategorised into very low birth weight (less than 1.5 kg) and extremely low birth weight (less than 1 kg).2,3 These low birth weight infants are 20 times more likely to die than heavier babies and face a greater risk of inhibited growth, impaired cognitive development and developing chronic diseases later in life.2–5 In 2000, a WHO study found that more than 20 million infants worldwide were low birth weight. Of these 20 million infants, over 95% were from developing countries.2 Low birth weight in developing regions can be due to several factors such as poor maternal health and nutrition during pregnancy, pregnancy complications, as well as a high prevalence of malaria, diarrhoea and respiratory infections.2,3
Birth weight has long been used as an indicator to determine the chance of a newborn's survival, growth and long-term health.2–4 By monitoring the weight of the newborn baby as soon as possible after birth, appropriate care and planning can be initiated for low birth weight babies to help increase the chance of survival. In developing countries, more than 50% of newborns are not weighed at birth since the majority are not delivered in health facilities, nor with the help of a skilled attendant.2–4 The main reasons for not seeking health care services are due to poverty, poor quality of care such as overcrowding and lack of qualified paramedical personnel, and long distance from home.4,6 Thus, a low-cost weighing balance that can be used in remote areas and operated easily may assist in monitoring the weight of a baby after birth.
Weight can be measured using pressure sensing devices based on capacitance,7–9 piezoresistivity,10–13 piezoelectricity14–16 or optics.17–19 Among these, piezoresistive sensors based on composite materials offer the advantages of being simple, flexible, low-cost, compact and lightweight.20 Generally, a conductive filler such as carbon black, graphite or metallic particles is mixed within a soft insulating matrix (e.g. silicone rubber) to exhibit piezoresistivity.12,21–25 This piezoresistive effect is attributed to the variation in the tunneling resistance when the distance between the conductive filler changes upon application of pressure/force.23,26 By choosing the proper type and amount of the metallic filler, the piezoresistive properties of the composite can be tuned.26 Recently, our group27 developed a piezoresistive pressure sensor using irregularly shaped copper particles and carbon paste embedded in polydimethylsiloxane (PDMS). The irregularly shaped protrusions of the copper particles provided regions of local field enhancement resulting in extreme pressure sensitivity whereas the addition of carbon allowed the overall electrical conductivity to be increased. As piezoresistive pressure sensors produce changes in electrical resistance, sensors of this type are usually coupled to an electronic readout system (e.g. a computer), which may not be suitable if the sensor is to be used in remote areas where access to electronic infrastructure is limited.
Recently, paper has gained a lot of interest as a platform for developing a wide range of paper-based electronic devices and displays28–47 since it is lightweight, inexpensive, disposable and can be easily miniaturized. Our group has developed a low-cost, lightweight paper-based electrochromic readout system that is compatible with piezoresistive pressure sensors.27,45 The paper-based readout system consisted of segments of gold nanoparticle films coated with electrochromic polyaniline and Prussian blue in which the segments were connected via graphite resistive separators. This paper-based readout system could measure a change in electrical resistance of a piezoresistive composite and convert the resistance into a voltage signal. The change in the voltage across the readout system affected the color of the electrochromic material on each segment of the gold nanoparticle film and could be used as an indicator of the pressure applied, for applications such as compression therapy.27 By using the pressure sensor as the means to measure weight, and a paper-based electrochromic readout system as the transducer, it may also be possible to develop a weighing device that meets the criteria of lightweight, compact and low-cost.
In this paper, we demonstrate a semi-quantitative readout system that enables an infant's weight to be classified as normal, low or very low birth weight with 2.5 kg and 1.5 kg as the critical weight values in which the readout system changes color. The research herein demonstrates that it is possible to alter the critical weight value by changing the resistive properties of the readout system (total resistance and individual resistance values of the graphite separators) while maintaining the composition of the piezoresistive pressure sensor. A quantitative readout system for weight is also demonstrated by increasing the number of gold nanoparticle film segments. The weighing balance is constructed within a cardboard mailing box, thus termed a “balance-in-a-box”. By integrating all the components inside a cardboard mailing box, and using the box as a pre-calibrated tray for the baby, the weighing balance can simply be mailed to the designated home or delivery unit without the use of any additional packaging materials.
2. Experimental
2.1. Materials & apparatus
All solutions were prepared in Milli-Q water (>18.2 MΩ cm from Millipore) unless otherwise stated. All chemicals were of analytical grade, used as received unless otherwise stated, and were purchased from Sigma Aldrich (Sydney, Australia): hydrochloric acid, sodium dodecyl sulphate, cyclohexane, propylene carbonate, acetonitrile, lithium perchlorate, poly(methyl methacrylate) (PMMA), potassium ferricyanide, tetraoctylammonium bromide, toluene, sodium borohydride, sodium carbonate, hydrogen tetrachloroaurate and dimethylamino pyridine (DMAP). Aniline solution was purchased from BDH chemicals Ltd., Radnor, PA, USA. Ferric chloride (FeCl3) and ferric chloride hexahydrate (FeCl3·6H2O) were from Ajax, Scoresby, Australia. Ag/AgCl ink (AGCL-675 C) and carbon ink (C-774) were purchased from Conductive Compounds, Hudson, NH, United States. Whatman® filter paper (No. 1) was obtained from Sigma Aldrich. Nail polish (satin sheet, Face of Australia) was purchased from Priceline (Sydney, Australia). A calligraphy pen (width 0.2 cm, Automatic Pen No. 1) was purchased from Will's Quills (Sydney, Australia). Graphite pencils were from Faber-Castell (Sydney, Australia). Polydimethylsiloxane (Pinkysil silicone, 20 shore, skin-compatible) was purchased from Barnes, Australia. Metallic copper powder (∼200 mesh) was purchased from Australian Metal Powders Supplies Pty Ltd. (Sydney, Australia). The mailing box (BX 19, 387 × 282 × 68 mm) was purchased from Australia Post (Sydney, Australia). A wooden block (90 × 60 mm, weight ∼27 g) was made from CSIRO workshop (Sydney, Australia). 3M double sided tape was purchased from Officeworks (Sydney, Australia).
2.2. Synthesis of gold nanoparticles coated with DMAP
Gold nanoparticles were prepared following the Brust method48 and transferred to the aqueous phase using DMAP using the method by Gittins and Caruso.49 The gold nanoparticles have a typical diameter of 6 ± 2 nm.
2.3. Synthesis of gel electrolyte, Prussian blue and polyaniline
A gel electrolyte was prepared by adding 1.2 g of PMMA into 1 M LiClO4 in propylene carbonate at 130 °C. Prussian blue was prepared by mixing equal volumes of 40 mM FeCl3 and 40 mM K3Fe(CN)6 in 10 mM HCl. The polyaniline mixture (emeraldine salt state) was synthesized following the method by Kelly et al.50 Briefly, 0.721 g of sodium dodecyl sulphate was dissolved in 50 mL of Milli-Q water. The solution was stirred until all the solid particles were dissolved. Next, 2.28 mL of this solution was removed and replaced with 2.28 mL of concentrated aniline solution. The solution was stirred for another 45 min. Following this process, 25 mL of 0.5 M FeCl3·6H2O solution was added and stirred for another 2.5 h. The synthesis of polyaniline was completed by adding 15 mL of 1 M HCl into the solution. The solid paste of the as-synthesized polyaniline mixture (emeraldine salt state) was collected prior to use.
2.4. Fabrication and assembly of the readout system
The general fabrication of the readout system has been reported earlier45 with modifications described herein. Squares (7 mm wide × 7 mm long, spaced 2 mm apart) were drawn lightly with a pencil on paper with the aid of a 3D printed stencil. Following this, the paper was then coated with nail polish to prevent the gold nanoparticles from penetrating though the paper matrix. The gold nanoparticle films were then formed on paper using a method described previously.49 Briefly, ∼80 μL of 1% w/v DMAP-gold nanoparticles in ethanol was applied using a calligraphy pen to fill these squares. The paper was then transferred onto a hot plate and dried at 80 °C until it appeared golden. The resistance of the gold nanoparticle films was reduced by a sintering process using a camera flash unit (Canon Speedlite 550 EX with Fresnel lens removed) positioned 1.1 cm away from the gold nanoparticle film (energy density of 2.1 J cm−2, flash duration of approximately 1 ms and twice flashing process).51 The typical resistance of the gold nanoparticle film after sintering was 2–6 Ω. For the readout system that consisted of ten gold nanoparticle segments (with nine graphite resistive separators), the length of the gold nanoparticle films was decreased to 3 mm. After creating these conductive gold nanoparticle films, graphite films (width 7 mm, length 2 mm) were drawn using a graphite pencil to connect each of these conductive gold nanoparticle segments. Approximately four traces of graphite were used and the resistance was adjusted to the desired value with an eraser or extra graphite traces. To fabricate the readout system with two and nine graphite resistive separators, 3B and 7B graphite pencils were used, respectively. For the readout system with different resistances in each of the graphite separators, 3B and 4B pencils were used.
After electrode fabrication, the as-synthesized polyaniline and Prussian blue were applied on top of the gold nanoparticle film by brushing the polyaniline paste followed by drying at 80 °C on a hot plate. Subsequently, Prussian blue solution was dropcast on top of the polyaniline layer. After further drying at 80 °C, the final film appeared green/blue. A reference electrode, Ag/AgCl ink, was painted (geometric area of 1.25 cm2) adjacent to the gold nanoparticle/graphite film and connected to one end of it. After the painting process, the ink was cured by placing the paper on a hot plate at 80 °C. The readout system was completed by placing LiClO4/PMMA gel electrolyte over both electrodes. A black wax crayon was drawn around the readout system and the back of the paper as a hydrophobic barrier to prevent the gel electrolyte from penetrating the paper.
2.5. Electrochemical testing of the readout system
The performance of the readout system was assessed by connecting the two ends of the gold nanoparticle/graphite film to a potentiostat (PARSTAT 2273 Advanced Electrochemical System Princeton Applied Research, Tennessee, United States). The end of the readout system that was connected to the Ag/AgCl electrode (referred as negative end (−) of the readout system) was connected to the negative terminal of the potentiostat (counter/reference electrode) whereas the other end of the readout system (referred as positive end (+) of the readout system) was connected to the positive terminal of the potentiostat (working electrode). The readout system was characterised by applying various voltages across the readout system between 0 and −1.5 V relative to Ag/AgCl electrode. The voltage gradient along the gold nanoparticle/graphite resistive film was measured using a Fluke 114 digital multimeter by placing the negative terminal probe of the multimeter to one end of the gold nanoparticle/graphite film while moving the other probe (positive terminal) away at increments of 0.1 cm towards the other end of the gold nanoparticle/graphite film. Analysis was performed by counting the number of gold nanoparticle segments that became transparent after 30 s (although the color change was observed within 10 s).
2.6. Fabrication of the pressure sensor
The carbon
:
copper
:
PDMS composite (C
:
Cu
:
PDMS) was prepared by gently mixing the carbon and copper powder in the PDMS at a weight ratio of 1.1
:
8
:
4 with addition of cyclohexane (2 mL) as a solvent. Afterwards, the mixture was poured into a rectangular mold (95 × 130 mm) before it was sandwiched between two metal plates in order to obtain a flat film (typical thickness of approximately 1.4 mm). The composite was left at room temperature for one hour before it was further cured in the oven for another hour. The final composite was cut in half prior to integration inside a mailing box.
2.7. Integration of the readout system, pressure sensor and coin battery inside a mailing box
The readout system, pressure sensor and a coin battery CR2032 (3 V) was integrated inside the mailing box (see Scheme 1). The mailing box served as a pre-calibrated tray for the baby as well as the package to deliver all of these components. The construction of the weighing balance is described herein.
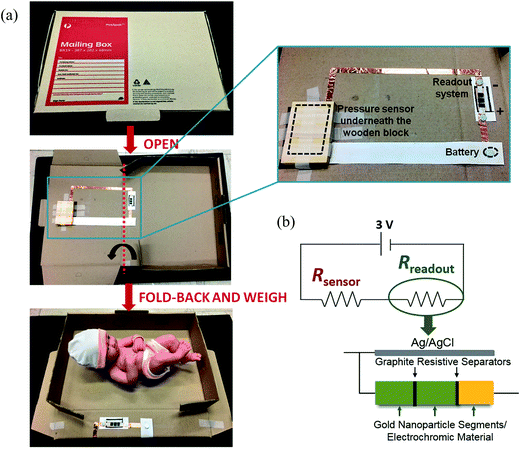 |
| Scheme 1 (a) Design of the “balance-in-a-box” comprising a paper-based readout system, a piezoresistive pressure sensor and a 3 V coin battery integrated within a mailing box. The pressure sensor was placed underneath the wooden block. Prior to weighing the baby, the mailing box was opened and folded back such that the pressure sensor was situated underneath the box and only the readout system and battery were facing the reader. The dashed red line represents the position where the flap is folded back. (b) Schematic diagram of the integrated pressure sensor (Rsensor), paper-based readout system (Rreadout) and 3 V coin battery (Vtotal). All the components were connected in series in the electrical circuit. The paper-based readout system consisted of three gold nanoparticle segments coated with an electrochromic material, connected via two graphite resistive separators and a printed Ag/AgCl electrode. | |
Initially, the mailing box was opened and on the inside top flap of the box (in the middle region), the C
:
Cu
:
PDMS pressure sensor (95 × 65 mm) was situated. In order for the pressure sensor to conduct an electrical signal, it was sandwiched between two metal electrodes. Two copper adhesive tapes were used, where one copper tape (area of 1800 mm2) was adhered directly to the cardboard and the second copper tape was attached to a piece of paper. The copper tape attached to the paper would lead to the positive end of the battery, whereas the copper tape that adhered directly to the cardboard would lead to the positive end of the readout system (i.e. the end of readout system that was connected to Ag/AgCl). To complete the electrical circuit, the negative end of the readout system was connected to the negative end of the battery using copper tape. The readout system and the battery were attached to the non-adhesive side of the copper tape using a neodymium magnet (diameter 10 mm). By using a magnet, the readout system can be replaced with a new one after use and the battery can be easily detached when the device is not in use. In order for weight to be distributed evenly over the pressure sensor, a wooden block (90 × 60 mm, weight 27 g) was used to elevate the tray. The pressure sensor and the wooden block were securely attached to the cardboard with sticky tape.
Prior to measurement, the flap was folded back at the red dashed lines (as shown in Scheme 1) and secured to the bottom of the cardboard box (which now forms the tray) using a double-sided tape. By doing this, the pressure sensor would be situated underneath the tray and only the readout system and the battery would be visible to the reader. The performance of the integrated system was evaluated by adding various known weights on top of the box while counting the number of gold nanoparticle film segments that changed color after 30 s (although the color change was observed within 10 s).
3. Results and discussion
3.1. Principle of operation of the weight balance and readout system
As shown in Scheme 1b, the weight balance consists of a piezoresistive pressure sensor (Rsensor) integrated in series with a paper-based resistive readout system (Rreadout) and a coin cell battery (Vtotal). Changes in the resistance of the pressure sensor, as a result of load being applied to it, changes the voltage across the readout system (Vreadout). The relationship between Vreadout and Rsensor can be expressed as: | 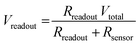 | (1) |
where the two resistors in the series circuit (pressure sensor and readout system) act as a voltage divider.
The readout system consists of an electrochromic coating of Prussian blue and polyaniline spread over multiple conductive gold nanoparticle film segments connected via graphite resistive separators. The consequence of the readout system being composed of alternating conductive segments and resistive separators is that the voltage drop which exists along the readout system has a staircase appearance with no significant voltage drop across the gold sections but with a significant drop across the resistive graphite separators. As the reduction voltage Vred of the electrochromic material is −0.6 V relative to Ag/AgCl,45 then the color of each of the Prussian blue/polyaniline/gold nanoparticle film segments will depend on the voltage across the readout system (as the result of changes in Rsensor) and subsequently the voltage of that particular segment (Vx). In the case where Vx is more positive than Vred then the segment will be in its original oxidised state (Prussian blue/emeraldine salt) and appear green/blue whereas in the case where Vx is more negative than Vred then the segment will be in its reduced state (Prussian white/leucoemeraldine) and be transparent (appear golden). The redox mechanism of the electrochromic Prussian blue/polyaniline has been reported earlier.45 Thus, the number of Prussian blue/polyaniline/gold nanoparticle segments in the readout system that change color from green/blue to transparent can be directly correlated with the resistance of the pressure sensor and the weight applied to it.
For infant health inferred through birth weight determination, babies that weigh less than 2.5 kg are considered low birth weight and those that weigh less than 1.5 kg are considered very low birth weight, with both requiring treatment. In the first instance, it would be sufficient to determine whether newborn babies fall within either of these categories by developing a semi-quantitative readout system that would change color at 1.5 kg and 2.5 kg. This requires identifying (1) a suitable composition of the pressure sensor, (2) a suitable resistance of the readout system that matches the operating dynamic range of the pressure sensor (3) and fine-tuning the resistance of each of the graphite resistive separators in the readout system such that the desired critical weight can be obtained.
3.2. Piezoresistive pressure sensor
In our previous study,27 we showed that the addition of carbon paste to a piezoresistive composite comprising irregularly shaped copper particles/PDMS increases the electrical conductivity of the composite such that less applied pressure/weight is necessary to obtain the same resistance value. The piezoresistive composite is highly sensitive to pressure changes which is a result of the irregularly shaped structure of the conductive copper particles which leads to field enhancement at the protrusions and a significant lowering of the electron tunnelling barrier.27 In the study reported herein, an optimised C
:
Cu
:
PDMS composition of 1.1
:
8
:
4 was selected. Such a composition is suitable for measuring high load/pressure (i.e. in the kilogram weight range).
A piezoresistive composite sheet (C
:
Cu
:
PDMS of 1.1
:
8
:
4) was constructed with dimensions 95 mm long, 65 mm wide and ∼1.4 mm thick and was sandwiched between two pieces of conductive copper tape and adhered to the inside flap of a cardboard mailing box. The cardboard box was folded back to form the scales and was elevated with a wooden block which was positioned over the piezoresistive composite sheet. This allows any weight that is placed on the cardboard scale to distribute evenly over the pressure sensor. The weighing balance was pre-calibrated with the initial weight of the mailing box (∼250 g) and hence, the weight presented in this study represents the actual weight of interest applied to the sensor.
The initial resistance of the C
:
Cu
:
PDMS composite sheet with no additional weight being placed on the cardboard scale was approximately 70 kΩ. Note that in the absence of external pressure from the mailing box, the resistance was 60 MΩ. Upon adding weight on top of the C
:
Cu
:
PDMS composite, this compressed the PDMS polymer and reduced the distance between the conductive metal fillers resulting in a decrease in electrical resistance (Fig. 1). The dynamic range of the sensor was between 0.5 to 3.5 kg, which is suitable for weighing newborn infants. Although loads less than 0.5 kg could induce resistance changes, the uncertainty in these measurements was quite high due to the high pressure sensitivity in this range. In contrast, loads greater than 3.5 kg did not further reduce the resistance of the pressure sensor significantly.
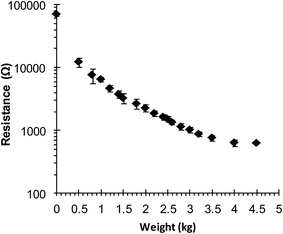 |
| Fig. 1 Influence of electrical resistance of the piezoresistive pressure sensor (C : Cu : PDMS with composition of 1.1 : 8 : 4) with weight application on a cardboard scale. The cardboard scale was pre-calibrated to take into account the weight of the mailing box (∼250 g). | |
3.3. General readout characterization
To provide a semi-quantitative reading on whether a weight loading is above or below a certain value, a readout system comprising three segments of conductive gold nanoparticle films connected via resistive graphite films was used. By having three segments of gold nanoparticle films coated with electrochromic material, each segment can allow a different weight range to be “read” by observing its color or by counting the number of segments that change color.
Since the output of the readout system is voltage, the effect of applying different voltages using a potentiostat directly across the readout system was firstly investigated (total resistance of readout system Rreadout = 1000 Ω). In reality, different voltages will be induced across the readout system when integrated with the piezoresistive pressure sensor and the coin cell battery. The readout system was first characterised by applying a constant voltage of −1.2 V across either end with a potentiostat. As can be seen in Fig. 2a, a staircase voltage drop was observed across the two graphite resistors whereas the gold nanoparticle film segments I, II and III were held at −1.2 V, −0.62 V, and 0 V, respectively. These values closely match the calculated values of −1.2 V, −0.6 V, and 0 V for segments I, II and III, respectively, revealing the consistency in the resistive graphite separators which have a resistance of approximately 500 Ω each. As the resistivity of the gold nanoparticle film is much less than that of the graphite film, the voltage drop is negligible along the gold nanoparticle film. In addition, the electrochromic Prussian blue/polyaniline film changed color from green/blue to transparent at segments I and II in which the voltage (Vx) was more negative than the reduction voltage of Prussian blue/polyaniline (Vred = −0.6 V relative to Ag/AgCl). Fig. 2b shows images of the readout system which were taken after applying voltages of 0 V, −0.6 V, −1 V, −1.2 V, −1.5 V and −1.8 V across the readout system. In this three-segment system, segment I is at the applied voltage, segment II is at half the applied voltage and segment III is at 0 V. Hence, as can be seen in Fig. 2b when −1.2 V was applied, segment II becomes transparent since it matches Vred = −0.6 V. Note that as one of the segments is always held at 0 V, it is not possible for all the segments to change color.
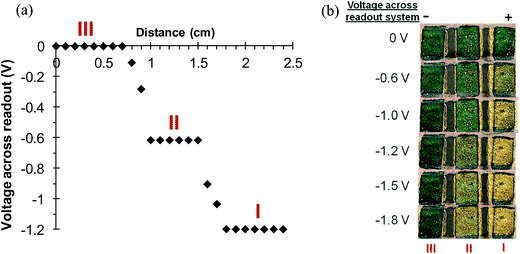 |
| Fig. 2 (a) Voltage drop along the gold nanoparticle film/graphite separators upon application of −1.2 V across the ends of the readout system. (b) Images of the readout system comprising three gold nanoparticle film segments/two graphite resistive separators formed using 3B pencil upon application of −0.6 V, −1 V, −1.2 V, −1.5 V and −1.8 V using a potentiostat. The positive end (+) of the readout system was connected to the working electrode whereas the negative end (−) of the readout system was connected to the counter/reference electrode. The red labels indicate the gold nanoparticle film segment number in the readout system. | |
3.4. Effect of total resistance of the readout system on the critical weight value
The objective of this work is to develop a readout system in which one segment becomes transparent when the weight is greater than 1.5 kg and two segments become transparent when the weight is greater than 2.5 kg. According to eqn (1), not only does the resistance of the pressure sensor Rsensor affect Vreadout but so does the total resistance of the readout system Rreadout. To illustrate this effect, three readout systems with different Rreadout values (500, 1000 and 1500 Ω) were studied. Fig. 3 compares how Rreadout affects the critical weight values for segments I and II which change color when Vreadout is −0.6 V and −1.2 V, respectively. When Rreadout = 1000 Ω, where the graphite separators (500 Ω each) were formed using a 3B graphite pencil, one obtains critical weight values of 1.35 kg and 2.5 kg for segments I and II, respectively. For higher values of Rreadout, both the critical weight values shift to lower values and vice versa. Although Rreadout = 1000 Ω is suitable for determining critical weights >2.5 kg at segment II, segment I does not change color at the desired weight of 1.5 kg. However, it can be seen that by changing the Rreadout, the critical weight reading in the readout system can be altered.
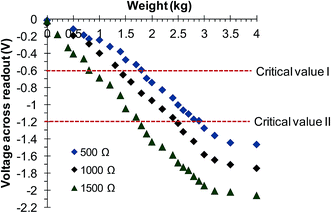 |
| Fig. 3 Voltage drop across three different readout systems (Rreadout = 500, 1000 and 1500 Ω) upon application of various weights to the piezoresistive pressure sensor. The critical weight value can be determined at segment I when Vreadout = −0.6 V (critical value I) and at segment II when Vreadout = −1.2 V (critical value II). | |
3.5. Effect of tuning the individual resistance values of the graphite separators
To demonstrate that changing the individual resistance values of the graphite separators R1 and R2 can shift the critical weight values of the readout system, R1 and R2 were tuned to 600 Ω and 400 Ω, respectively while maintaining the total resistance at 1000 Ω. N.B. R1 separates gold segments I and II and R2 separates gold segments II and III.
The readout system was assessed by applying −1.2 V across the readout system (see Fig. 4a). As described previously, when each of the graphite resistive separators were equal in their resistance (500 Ω), the second gold segment would be transparent as a result of the voltage at segment II being half the applied voltage (−0.6 V) and equal to the reduction voltage of the electrochromic material (see Fig. 2b). However, this was not the case when the resistance of the graphite separators was varied as the voltage at segment II depends on the fraction of R2 (400 Ω) to the total readout system resistance (1000 Ω). As shown in Fig. 4a, when −1.2 V was applied across the readout system the voltage at segment II was more positive than −0.6 V (i.e. −0.5 V) and thus did not change color. Instead, segment II started to change color when −1.5 V was applied across the readout system, equivalent to a weight of 3 kg, allowing segment II to be at −0.6 V (Fig. 4b). Fig. 4c shows the color change in the readout system upon application of various weights. Thus by having R1 = 600 Ω and R2 = 400 Ω, the critical values of segments I and II of this readout system were 1.35 kg and 3 kg, respectively (cf. 1.35 kg and 2.5 kg for R1 = R2 = 500 Ω, see Fig. S1 in ESI†). It is worth noting that although adjusting the resistance of each of the graphite separators while maintaining the total resistance can change the critical value for segment II, it does not change the critical value for segment I.
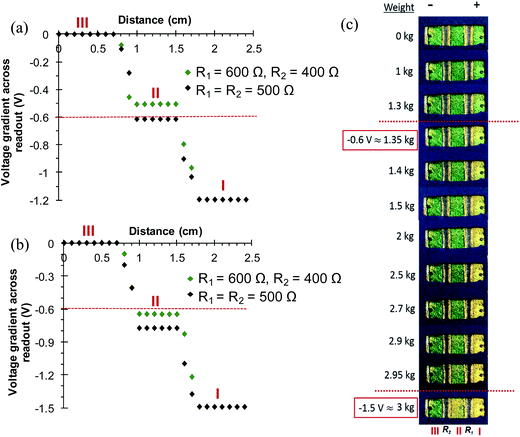 |
| Fig. 4 Effect of voltage at segment II of the readout system when R1 = R2 = 500 Ω (black data points) and when R1 = 600 Ω and R2 = 400 Ω (green points) with (a) −1.2 V and (b) −1.5 V across the readout system. (c) Images of the readout system with graphite resistive segments R1 = 600 Ω and R2 = 400 Ω upon application of various weights to the pressure sensor. To keep the terminology consistent for the battery and potentiostat, the positive end (+) of the readout system was connected to the negative terminal of the 3 V battery whereas the negative end (−) of the readout system was connected to the positive terminal of the battery. | |
3.6. A semi-quantitative readout system for reading critical values of 1.5 kg and 2.5 kg
The previous sections illustrated two methods to tune the critical weight value by (i) adjusting Rreadout and (ii) adjusting the individual resistance values of the graphite separators. Combining these two principles should allow one to develop a readout system in which segment I changes color at 1.5 kg and segment II changes color at 2.5 kg. The calculation proceeds by first tuning Rreadout so that segment I changes color when 1.5 kg is applied. Then the resistances of the graphite separators are adjusted so that segment I maintains its color change at 1.5 kg, while allowing segment II to change color at 2.5 kg.
Based on eqn (1), to obtain a critical weight value of 1.5 kg (Rsensor = 3200 Ω) which can be observed at segment I (Vreadout = −0.6 V), the total resistance of the readout system needs to be Rreadout = 800 Ω when a 3 V battery is used. Subsequently, in order for segment II to change color at the critical weight value of 2.5 kg, the resistances of each of the graphite separators were determined to be R1 = 350 Ω and R2 = 450 Ω (see calculation in ESI†). Thus when segment II is at −0.6 V, this would be the result of −1.05 V being present across the readout system (Fig. 5a). The voltage drop across the readout system upon application of weight to the cardboard scale is shown in Fig. 5b. For weights between 0 and 1.45 kg, no segments changed color. For weights between 1.5 and 2.45 kg (Vreadout between −0.6 V and −1.05 V), segment I became transparent. When the weight exceeded 2.5 kg (Vreadout more negative than −1.05 V) segment I and II became transparent. Thus, the first and second segments of the gold nanoparticle film can provide a semi-quantitative reading with 1.5 kg and 2.5 kg as the critical weight values, respectively. Fig. 5c shows the integrated system with a weighted baby doll of 1.45 kg (very low birth weight, no segments changing color), 1.5 and 2.45 kg (both low birth weight, one segment changing color) and 2.5 kg (normal birth weight, two segments changing color). Note that between 2.45 kg to 2.5 kg, there is a transitioning of segment II from green/blue to transparent (see Fig. S2 in ESI†). Thus, the cardboard balance can distinguish within ±50 g whether an object is above or below the 2.5 kg threshold value. It is to be noted that movement of the baby may affect the weight resolution.
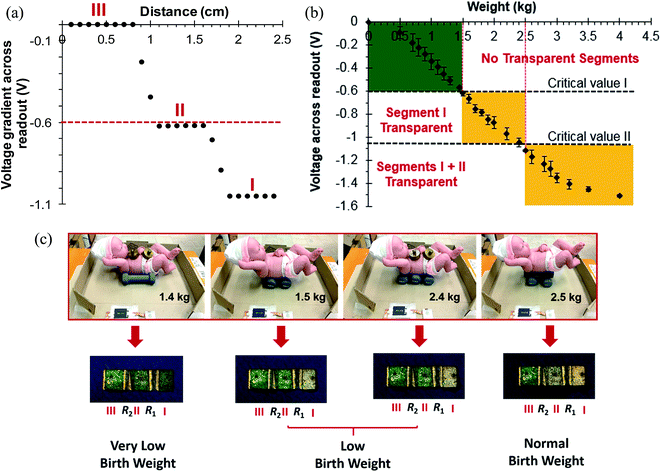 |
| Fig. 5 (a) Voltage gradient across the readout system (−1.05 V) as a result of a 2.5 kg baby being placed on the pressure sensor. The resistance of the graphite separators R1 and R2 were equal to 350 Ω and 450 Ω, respectively, which allowed segment II to be at Vred = −0.6 V. (b) Voltage drop across the readout system upon application of various weights to the cardboard weighing balance illustrating the critical weights in which the segments change color. (c) Images of the integrated “balance-in-a-box” which consisted of a C : Cu : PDMS pressure sensor, battery and paper-based readout system for infant birth weight determination. | |
The readout system was secured inside the mailing box, along the edge, such that when the box is folded back with the pressure sensor, the readout system remains visible to the user. Overall, the integration of all the components in a mailing box represents a “balance-in-a-box” that can be delivered to remote locations and be readily assembled for birth weight determination.
3.7. A quantitative weight balance
In the previous section, a semi-quantitative weight balance was demonstrated by having three segments of gold nanoparticle film which allowed two critical weight values to be determined and three different weight ranges to be differentiated. This allowed a baby's weight to be classified as normal, low, or very low birth weight. In order to improve the fidelity of the readout system, the number of gold nanoparticle film segments was increased to ten, with nine graphite resistive separators. The resistive separators were formed by using a higher grade of graphite pencil (7B) to maintain the total resistance of the readout system Rreadout at 1000 Ω, in order to make meaningful comparisons with the three-segment readout system. Fig. 6 shows the color changes observed on the ten-segment readout system upon application of specific weights whereas Table 1 summarises the number of transparent gold nanoparticle film segments that are observed and the weight ranges that correspond to that change for the three-segment and ten-segment readout systems. Although the dynamic range of each of the readout systems is the same, due to the use of the same type of pressure sensor (C
:
Cu
:
PDMS with composition of 1.1
:
8
:
4), the extra graphite resistive separators provided additional stepwise voltage changes across the readout system. Note that for the ten-segment system only seven segments became transparent when a baby doll with weight of 4.5 kg was placed. No further segments changed color since the upper weight range of 4.5 kg resulted in Vreadout being −1.7 V which resulted in segments VIII, IX and X being positive of −0.6 V.
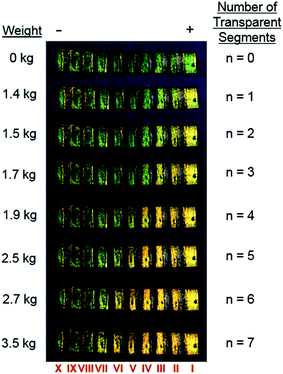 |
| Fig. 6 Images of the readout systems comprising ten gold nanoparticle film segments/nine graphite resistive separators upon application of different weights. | |
Table 1 Measurable weight ranges for a readout system comprising three and ten-segment gold nanoparticle films
Number of transparent segments |
Measurable weight range |
3-Segment system |
10-Segment system |
0 |
0–1.3 kg |
0–1.3 kg |
1 |
1.35–2.45 kg |
1.35–1.45 kg |
2 |
2.5–4.5 kg |
1.5–1.6 kg |
3 |
|
1.65–1.85 kg |
4 |
1.9–2.45 kg |
5 |
2.5–2.65 kg |
6 |
2.7–3.45 kg |
7 |
3.5–4.5 kg |
8 |
— |
9 |
— |
10 |
— |
Of particular note is that segment I becomes transparent for weight ranges between 1.35–2.45 kg and 1.35–1.45 kg for the three and ten-segment readout system, respectively. Thus as the number of segments increased from three to ten, the weight range narrowed from 1.1 kg, to 0.1 kg, respectively. Overall, there was an improved mass resolution over the entire 1.3–4.5 kg range for the ten-segment system. Moreover, one can observe that for a three-segment system, the 2.5–4.5 kg range is signified by one segment (i.e. segment II) changing color, but for the ten-segment system this can be separated into three distinct segments (2.5–2.65 kg for segment V, 2.7–3.45 kg for segment VI and 3.5–4.5 kg for segment VII). Although the mass resolution in each of the gold nanoparticle film segments is not equal, having multiple gold nanoparticle film segments can lead to an improvement in determining more accurate weights.
4. Conclusions
We have developed a “balance-in-a-box” consisting of a piezoresistive pressure sensor, coin battery and an electrochromic paper-based readout system integrated in an electrical circuit. The readout system could be used as a simple-to-interpret, low-cost indicator for if a baby is within the healthy weight range. By modifying the resistive properties of the readout system and increasing the number of conducting gold nanoparticle segments, the resolution of the readout system could be improved which in turn shifted the critical weight values in which the gold nanoparticle segments changed color. Ideally, if the weighing balance is to be shipped to the end-user, several extra readout systems, an electrolyte gel bottle, and instructions for use would be supplied in the box. Overall, such an integrated system could be used to address the challenge of recording the birth weight of babies in remote areas, where access to hospitals or medical clinics is limited. Moreover, this study has opened up a new opportunity that is not limited to weighing babies but other applications where semi-quantitative reading will suffice for performing analysis.
Acknowledgements
We would like to thank J. Myers for her help in synthesizing the gold nanoparticles.
References
-
United Nations, The Millennium Development Goals Report, 2015 Search PubMed.
-
UNICEF, WHO Low Birthweight: Country, Regional and Global Estimates, UNICEF, New York, 2004 Search PubMed.
- A. K. Blanc and T. Wardlaw, Monitoring Low Birth Weight: An Evaluation of International Estimates and an Updated Estimation Procedure, Bull. W. H. O., 2005, 83, 178–185d Search PubMed.
-
A. O. Lucas, B. J. Stoll and J. R. Bale, Improving Birth Outcomes: Meeting the Challenge in the Developing World, National Academies Press, Washington DC, 2003 Search PubMed.
- D. J. Barker, The Developmental Origins of Adult Disease, Eur. J. Epidemiol., 2003, 18, 733–736 CrossRef CAS PubMed.
- S. Karande, Consequences of Low Birth Eeight, Maternal Illiteracy and Poor Access to Medical Care in Rural India: Infantile Iatrogenic Cushing Syndrome, BMJ Case Rep., 2015 DOI:10.1136/bcr-2015-211387.
- J. Meyer, B. Arnrich, J. Schumm and G. Tröster, Design and Modeling of a Textile Pressure Sensor for Sitting Posture Classification, IEEE Sens. J., 2010, 10, 1391–1398 CrossRef CAS.
- P. Eswaran and S. Malarvizhi, MEMS Capacitive Pressure Sensors: A Review on Recent Development and Prospective, Int. J. Eng. Technol., 2013, 5, 2734–2746 Search PubMed.
- K. F. Lei, K.-F. Lee and M.-Y. Lee, Development of a Flexible PDMS Capacitive Pressure Sensor for Plantar Pressure Measurement, Microelectron. Eng., 2012, 99, 1–5 CrossRef CAS.
- X. Wang, Y. Gu, Z. Xiong, Z. Cui and T. Zhang, Silk-Molded Flexible, Ultrasensitive, and Highly Stable Electronic Skin for Monitoring Human Physiological Signals, Adv. Mater., 2014, 26, 1336–1342 CrossRef CAS PubMed.
- C. Pramanik, H. Saha and U. Gangopadhyay, Design Optimization of a High Performance Silicon MEMS Piezoresistive Pressure Sensor for Biomedical Applications, J. Micromech. Microeng., 2006, 16, 2060–2066 CrossRef CAS.
- S. Stassi, V. Cauda, G. Canavese and C. F. Pirri, Flexible Tactile Sensing Based on Piezoresistive Composites: A Review, Sensors, 2014, 14, 5296–5332 CrossRef CAS PubMed.
- C. Gau, H. Ko and H. Chen, Piezoresistive Characteristics of MWNT Nanocomposites and Fabrication as a Polymer Pressure Sensor, Nanotechnology, 2009, 20, 185503–185514 CrossRef CAS PubMed.
- Y. R. Wang, J. M. Zheng, G. Y. Ren, P. H. Zhang and C. Xu, A Flexible Piezoelectric Force Sensor Based on PVDF Fabrics, Smart Mater. Struct., 2011, 20, 045009–045016 CrossRef.
- K. J. Kim, Y. M. Chang, S. Yoon and H. J. Kim, A Novel Piezoelectric PVDF Film-Based Physiological Sensing Belt for a Complementary Respiration and Heartbeat Monitoring System, Integr. Ferroelectr., 2009, 107, 53–68 CrossRef CAS.
- C. Dagdeviren, Y. Su, P. Joe, R. Yona, Y. Liu, Y.-S. Kim, Y. Huang, A. R. Damadoran, J. Xia and L. W. Martin, Conformable Amplified Lead Zirconate Titanate Sensors with Enhanced Piezoelectric Response for Cutaneous Pressure Monitoring, Nat. Commun., 2014, 5, 1–10 Search PubMed.
- M. Rothmaier, M. P. Luong and F. Clemens, Textile Pressure Sensor Made of Flexible Plastic Optical Fibers, Sensors, 2008, 8, 4318–4329 CrossRef CAS PubMed.
- S. Tjin, R. Suresh and N. Ngo, Fiber Bragg Grating Based Shear-Force Sensor: Modeling and Testing, J. Lightwave Technol., 2004, 22, 1728–1733 CrossRef.
- F. Ceyssens, M. Driesen, K. Wouters and R. Puers, A Low-Cost and Highly Integrated Fiber Optical Pressure Sensor System, Sens. Actuators, A, 2008, 145, 81–86 CrossRef.
- J. Park, Y. Lee, J. Hong, M. Ha, Y.-D. Jung, H. Lim, S. Y. Kim and H. Ko, Giant Tunneling Piezoresistance of Composite Elastomers with Interlocked Microdome Arrays for Ultrasensitive and Multimodal Electronic Skins, ACS Nano, 2014, 8, 4689–4697 CrossRef CAS PubMed.
- S. Stassi and G. Canavese, Spiky Nanostructured Metal Particles as Filler of Polymeric Composites Showing Tunable Electrical Conductivity, J. Polym. Sci., Part B: Polym. Phys., 2012, 50, 984–992 CrossRef CAS.
- M.-J. Jiang, Z.-M. Dang, H.-P. Xu, S.-H. Yao and J. Bai, Effect of Aspect Ratio of Multiwall Carbon Nanotubes on Resistance-Pressure Sensitivity of Rubber Nanocomposites, Appl. Phys. Lett., 2007, 91, 0729071–0729073 Search PubMed.
- B. Han, Y. Wang, S. Sun, X. Yu and J. Ou, Nanotip-Induced Ultrahigh Pressure-Sensitive Composites: Principles, Properties and Applications, Composites, Part A, 2014, 59, 105–114 CrossRef CAS.
- N. Hu, Y. Karube, C. Yan, Z. Masuda and H. Fukunaga, Tunneling Effect in a Polymer/Carbon Nanotube Nanocomposite Strain Sensor, Acta Mater., 2008, 56, 2929–2936 CrossRef CAS.
- A. Celzard, E. McRae, J.-F. Marêché, G. Furdin and B. Sundqvist, Conduction Mechanisms in Some Graphite–Polymer Composites: Effects of Temperature and Hydrostatic Pressure, J. Appl. Phys., 1998, 83, 1410–1419 CrossRef.
- S. Stassi, G. Canavese, F. Cosiansi, R. Gazia, C. Fallauto, S. Corbellini, M. Pirola and M. Cocuzza, Smart Piezoresistive Tunnelling Composite for Flexible Robotic Sensing Skin, Smart Mater. Struct., 2013, 22, 125039–125047 CrossRef.
- D. D. Liana, B. Raguse, J. J. Gooding and E. Chow, An Integrated Paper-Based Readout System and Piezoresistive Pressure Sensor for Measuring Bandage Compression, Adv. Mater. Technol., 2016 DOI:10.1002/admt.201600143.
- H. Águas, T. Mateus, A. Vicente, D. Gaspar, M. J. Mendes, W. A. Schmidt, L. Pereira, E. Fortunato and R. Martins, Thin Film Silicon Photovoltaic Cells on Paper for Flexible Indoor Applications, Adv. Funct. Mater., 2015, 25, 3592–3598 CrossRef.
- A. C. Siegel, S. T. Phillips, M. D. Dickey, N. Lu, Z. Suo and G. M. Whitesides, Foldable Printed Circuit Boards on Paper Substrates, Adv. Funct. Mater., 2010, 20, 28–35 CrossRef CAS.
- A. C. Siegel, S. T. Phillips, B. J. Wiley and G. M. Whitesides, Thin, Lightweight, Foldable Thermochromic Displays on Paper, Lab Chip, 2009, 9, 2775–2781 RSC.
- D. Tobjörk and R. Österbacka, Paper Electronics, Adv. Mater., 2011, 23, 1935–1961 CrossRef PubMed.
- J. Lessing, A. C. Glavan, S. B. Walker, C. Keplinger, J. A. Lewis and G. M. Whitesides, Inkjet Printing of Conductive Inks with High Lateral Resolution on Omniphobic “RF Paper” for Paper-Based Electronics and MEMS, Adv. Mater., 2014, 26, 4677–4682 CrossRef CAS PubMed.
- A. Russo, B. Y. Ahn, J. J. Adams, E. B. Duoss, J. T. Bernhard and J. A. Lewis, Pen-on-Paper Flexible Electronics, Adv. Mater., 2011, 23, 3426–3430 CrossRef CAS PubMed.
- T. H. Nguyen, A. Fraiwan and S. Choi, Paper-Based Batteries: A Review, Biosens. Bioelectron., 2014, 54, 640–649 CrossRef CAS PubMed.
- Q. Zhong, J. Zhong, B. Hu, Q. Hu, J. Zhou and Z. L. Wang, A Paper-Based Nanogenerator as a Power Source and Active Sensor, Energy Environ. Sci., 2013, 6, 1779–1784 CAS.
- M. M. Hamedi, A. Ainla, F. Güder, D. C. Christodouleas, M. T. Fernández-Abedul and G. M. Whitesides, Integrating Electronics and Microfluidics on Paper, Adv. Mater., 2016, 28, 5054–5063 CrossRef CAS PubMed.
- V. Lakafosis, A. Rida, R. Vyas, L. Yang, S. Nikolaou and M. M. Tentzeris, Progress Towards the First Wireless Sensor Networks Consisting of Inkjet-Printed, Paper-Based RFID-Enabled Sensor Tags, Proc. IEEE, 2010, 98, 1601–1609 CrossRef.
- E. Lemaire, R. Moser, C. Borsa and D. Briand, Green Paper-Based Piezoelectronics for Sensors and Actuators, Sens. Actuators, A, 2016, 244, 285–291 CrossRef CAS.
- H. Liu and R. M. Crooks, Paper-Based Electrochemical Sensing Platform with Integral Battery and Electrochromic Read-Out, Anal. Chem., 2012, 84, 2528–2532 CrossRef CAS PubMed.
- N. Kurra, D. Dutta and G. U. Kulkarni, Field Effect Transistors and RC Filters from Pencil-Trace on Paper, Phys. Chem. Chem. Phys., 2013, 15, 8367–8372 RSC.
- S. K. Mahadeva, K. Walus and B. Stoeber, Paper as a Platform for Sensing Applications and Other Devices: A Review, ACS Appl. Mater. Interfaces, 2015, 7, 8345–8362 CAS.
- D. D. Liana, B. Raguse, J. J. Gooding and E. Chow, Recent Advances in Paper-Based Sensors, Sensors, 2012, 12, 11505–11526 CrossRef CAS PubMed.
- G. Zheng, Y. Cui, E. Karabulut, L. Wågberg, H. Zhu and L. Hu, Nanostructured Paper for Flexible Energy and Electronic Devices, MRS Bull., 2013, 38, 320–325 CrossRef CAS.
- Y. Lin, D. Gritsenko, Q. Liu, X. Lu and J. Xu, Recent Advancements in Functionalized Paper Based Electronics, ACS Appl. Mater. Interfaces, 2016, 8, 20501–20515 CAS.
- D. D. Liana, B. Raguse, J. J. Gooding and E. Chow, Toward Paper-Based Sensors: Turning Electrical Signals into an Optical Readout System, ACS Appl. Mater. Interfaces, 2015, 7, 19201–19209 CAS.
- M. M. Hamedi, V. E. Campbell, O. Rothemund, F. Guder, D. C. Christodouleas, J.-F. Bloch and G. M. Whitesides, Electrically Activated Paper Actuators, Adv. Funct. Mater., 2016, 26, 2446–2453 CrossRef CAS.
- N. Amjadi and M. Sitti, High-Performance Multiresponsive Paper Actuators, ACS Nano, 2016, 10, 10202–10210 CrossRef PubMed.
- M. Brust, M. Walker, D. Bethell, D. J. Schiffrin and R. Whyman, Synthesis of Thiol-Derivatised Gold Nanoparticles in a Two-Phase Liquid–Liquid System, J. Chem. Soc., Chem. Commun., 1994, 7, 801–802 RSC.
- D. I. Gittins and F. Caruso, Spontaneous Phase Transfer of Nanoparticulate Metals from Organic to Aqueous Media, Angew. Chem., Int. Ed., 2001, 40, 3001–3004 CrossRef CAS PubMed.
- F. M. Kelly, L. Meunier, C. Cochrane and V. Koncar, Polyaniline: Application as Solid State Electrochromic in a Flexible Textile Display, Displays, 2013, 34, 1–7 CrossRef CAS.
- D. D. Liana, B. Raguse, L. Wieczorek, G. R. Baxter, K. Chuah, J. J. Gooding and E. Chow, Sintered Gold Nanoparticles as an Electrode Material for Paper-Based Electrochemical Sensors, RSC Adv., 2013, 3, 8683–8691 RSC.
Footnote |
† Electronic supplementary information (ESI) available. See DOI: 10.1039/c6ay02767a |
|
This journal is © The Royal Society of Chemistry 2017 |
Click here to see how this site uses Cookies. View our privacy policy here.