DOI:
10.1039/C6PY01849A
(Review Article)
Polym. Chem., 2017,
8, 177-219
RAFT polymerization to form stimuli-responsive polymers†
Received
21st October 2016
, Accepted 21st November 2016
First published on 22nd November 2016
Abstract
Stimuli-responsive polymers adapt to their surrounding environment. These polymers are capable of responding to a variety of external stimuli, which include optical, electrical, thermal, mechanical, redox, pH, chemical, environmental and biological signals. They are encountered in many environments. They can have a variety of architectures (e.g., copolymers, blocks, stars). They may be present as isolated macromolecules in a medium, as supramolecular assemblies, as smart coatings, as networks or some combination of these possibilities. This paper is concerned with the process of forming such polymers by radical polymerization with reversible addition fragmentation chain transfer (RAFT). RAFT polymerization has an advantage over most processes for reversible deactivation radical polymerization (RDRP) in its tolerance of a wide range of unprotected functionalities. Three basic strategies for forming stimuli-responsive polymers are considered: RAFT polymerization of functional monomers (a “grafting through” approach), the post-polymerization modification of RAFT-synthesized polymers (some combination of “grafting through”, “from” and “to”), and the use of functional RAFT agents and RAFT end-group transformation (often “grafting from”). Other syntheses involve combinations of these processes and of RAFT polymerization with other processes. We also consider the responsiveness of the thiocarbonylthio-functionality of macroRAFT agents in terms of their ability to directly initiate and control RAFT polymerization and to regulate the properties of RAFT-synthesized polymers.
Introduction
Stimuli-responsive polymers are capable of adapting to their environment. They respond to a variety of external stimuli that include optical, electrical, thermal, mechanical, redox, pH, chemical, environmental and biological signals.1 This paper will not discuss the details of the many-fold applications and properties of stimuli-responsive materials, rather it is concerned at a more fundamental level with the processes of forming such functional polymers by RAFT (Reversible Addition Fragmentation chain Transfer) polymerization. We also largely exclude explicit coverage of biopolymer conjugates from this review. While these materials represent an extremely important class of stimuli-responsive polymers, their properties are adequately covered in other documents.2,3 Moreover, in this review emphasis is placed on polymers which respond reversibly to a stimulus rather than polymers that undergo an irreversible change.
Stimuli-responsive elements of RAFT-synthesized polymers may originate from functionality present in the RAFT agent or macroRAFT agent, the monomers polymerized, or might be incorporated post-polymerization by transformation of the RAFT-synthesized polymer. Each of these possibilities will be considered. With the above constraints in mind, we commence with a brief overview of RAFT polymerization.
RAFT polymerization
RAFT polymerization4 is a reversible deactivation radical polymerization (RDRP);5 a process that, with appropriate attention to reagents and reaction conditions, can possess most of the attributes normally associated with living polymerization.6,7 These attributes include, low molar mass dispersity, high end group fidelity, capacity for continued chain growth and access to complex architectures. RDRP are often called living or controlled radical polymerizations. However, the use of these terms in this context is now discouraged by IUPAC.5
The attributes of low molar mass dispersity, uniform chemical composition and high end group fidelity offered by RAFT polymerization are crucial to many applications in ensuring a reproducible, reliable and uniform response.
In the context of synthesis of stimuli-responsive polymers, RAFT polymerization has an advantage over other RDRP processes,5 which include nitroxide mediated polymerization (NMP),8,9 and atom transfer radical polymerization (ATRP) or transition metal-mediated RDRP,10–15 in its tolerance of a wide range of functionalities in monomer, RAFT agent and the polymerization medium.
RAFT provides reversible deactivation by a degenerate chain transfer mechanism (Scheme 1). The chain transfer steps that comprise the main equilibria are termed degenerate because they involve only an exchange of functionality between propagating radicals and dormant polymer chains (called macroRAFT agents). The only distinction between the species on the two sides of the equilibria is their degree of polymerization (n and m). Moreover, in an effective RAFT process, where the rate of chain equilibration is rapid with respect to propagation, there should be less than one monomer unit added per activation cycle, so these also will be similar.
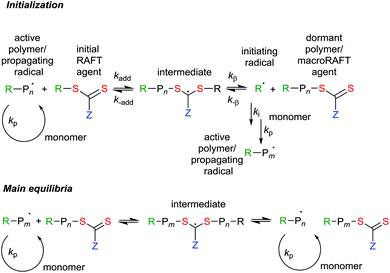 |
| Scheme 1 Mechanism for reversible addition-fragmentation chain transfer. Initiation requires a source of radicals (initiation and termination reactions are not shown). | |
The overall RAFT process (Scheme 2) then comprises the sequential insertion of monomer units into an initial RAFT agent. The R and ZCS2 groups are retained in the macro RAFT agent. The species labelled ‘intermediate’ in Scheme 1 should ideally be transient species and play no direct role in the process.
 |
| Scheme 2 Two representations of the overall RAFT Process. | |
In that the steps comprise chain transfer reactions, there should be no net formation or loss of radicals as a consequence of the RAFT process. Initiating radicals must be formed in a separate step from an added initiator, from monomer, or from the RAFT agent. However, all radical species (initiating radicals, propagating radicals, even the intermediates) can, in principle, be involved in termination by radical–radical reaction. It is important to choose reaction conditions such that termination events are minimized. This generally means that targeted molecular weights should be substantially smaller than those that would be formed in a similar radical polymerization without the RAFT agent.
Monomers in RAFT polymerization
While the reactivity of monomers in radical polymerization forms a continuum, it is useful to consider them as belonging to one of two broad classes.16,17 The ‘less activated’ monomers or LAMs (see Fig. 1) are those where the double bond is adjacent to one or more oxygen, nitrogen, halogen or sulfur lone pairs [e.g., vinyl acetate (VAc), N-vinylpyrrolidone (NVP), N-vinylcaprolactam (VCL), 5,6-benzo-2-methylene-1,3-dioxepane (BMDO), vinyl chloride (VC), vinylidene fluoride (VF2), (4-bromophenyl)(vinyl)sulfane (BPVS)] or saturated carbon (e.g., diallyldimethylammonium chloride (DADMAC), BOC-protected allylamine (ABOC)).
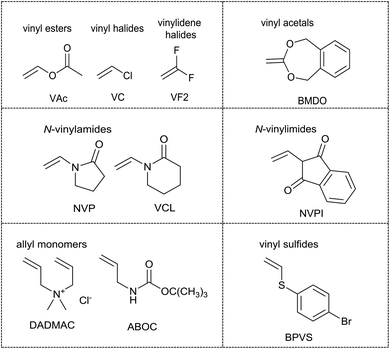 |
| Fig. 1 Abbreviations for and examples of some less-activated monomers (LAMs). Polymer abbreviations are formed by including the monomer abbreviation in parentheses and suffixing with “P”, e.g., P(VAc) is poly(vinyl acetate). | |
The ‘more-activated’ monomers (MAMs, see Fig. 2) are those where the double bond is conjugated to an aromatic ring [e.g., the styrenes and vinyl aromatics: styrene (St) and substituted styrenes, 4-vinylpyridine (4VP), acenaphthalene (AcN)], a double bond [e.g., the dienes: butadiene (Bd), isoprene (Ip), chloroprene (Cp)], a carbonyl group [e.g., methacrylic acid (MAA), methyl methacrylate (MMA), acrylic acid (AA), methyl acrylate (MA), acrylamide (Am)] or a nitrile [e.g., acrylonitrile (AN)]. Maleic anhydride (MAH) and maleimides [e.g., N-phenylmaleimide (NPMI)] also belong to this class.
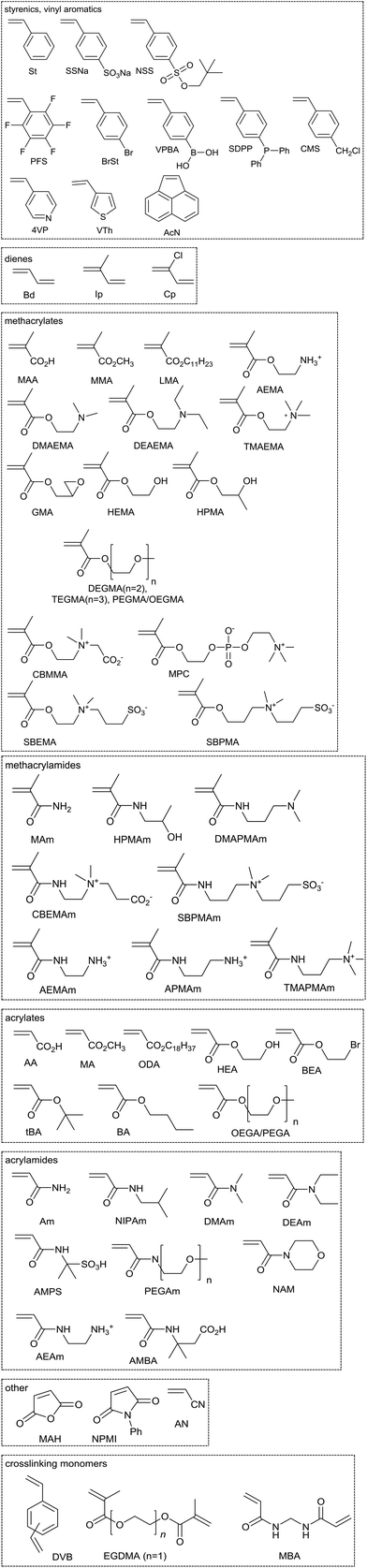 |
| Fig. 2 Examples of some more-activated monomers (MAMs). Polymer abbreviations are formed by including the monomer abbreviation in parentheses and suffixing with “P”, e.g., P(St) is polystyrene. | |
As with any continuum some monomers fall at the boundary of the extremes. Thus, N-vinylcarbazole (NVC), and most likely other N-vinyl aromatics, are intermediate stabilized monomers (IAMs).18
To date, most syntheses of stimuli-responsive polymers have involved the polymerization of MAMs. The reason for this is partly historical, reflecting the fact that most RDRP processes (e.g., ATRP and NMP) are not generally applicable to LAMs (or IAMs).
With appropriate selection of the RAFT agent, RAFT polymerization is compatible with all monomer classes. Indeed, the polymerization of most monomers amenable to radical polymerization can be mediated by RAFT. The exceptions are those that contain functionality that may react with the thiocarbonylthio group of the RAFT agent. Of specific concern are monomers which contain nucleophilic substituents such as primary or secondary amino-, or thiol-substituents. For example, RAFT polymerization of AEMA as the free amine is not well-controlled. However, low dispersity P(AEMA) can be successfully prepared when the monomer is maintained in fully protonated form. RAFT polymerization can be performed for monomers containing primary aromatic amines (e.g., 53,19 see section Nitric oxide responsive polymers).
Monomers that are not readily polymerized by conventional radical polymerization, e.g., those that contain functionality that is reactive toward the propagating radicals (such as nitro-groups20), are also likely to be problematical in RAFT polymerization (or other RDRP). Nonetheless, RAFT does offer, some benefits in this context. For example, it is possible to achieve higher monomer conversions without gelation (significant crosslinking) in RAFT (co)polymerization of the conjugated diene monomers, butadiene (Bd), isoprene (Ip) and chloroprene (Cp), than in conventional radical polymerization.21 This result can be attributed to the lower dispersity of the RAFT-synthesized (co)polymers and, in particular, to the elimination of the high molecular weight tail of the molecular weight distribution.
Factors limiting the control exerted in RDRP of LAMs are the relatively high incidence of propagation involving head addition to monomer and of irreversible chain transfer. This has been studied for RAFT polymerization of VAc22,23 and VF224 and may be significant for other LAMs which show some proclivity for head addition during radical polymerization.25 Interestingly, RAFT polymerization of VC26 and of certain vinyl ethers27 has been found less problematical than would have been expected on the basis of studies of the conventional process.
Theoretical arguments suggest that side reactions that involve rearrangement of transient intermediates (propagating species) should be less prevalent in RDRP, which impacts, in particular, on RDRP of acrylates, VAc and VC.28
RAFT agents
RAFT agents, their design, selection and synthesis, are well-described in recent reviews.16,17,29–32 The choice of the initial RAFT agents (ZC(
S)SR) for a set of monomer(s) and reaction conditions is crucial to achieving good control over dispersity and end-group fidelity. The effectiveness of RAFT agents is determined by the substituents Z (the activating group) and R (the homolytic leaving group). General guidelines for their selection are summarized in Fig. 3 and 4, respectively.16,32
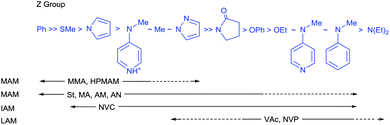 |
| Fig. 3 Guidelines for selection of the ‘Z’ group of RAFT agents (Z–C( S)S–R) for various polymerizations. RAFT agent addition rates and transfer constants decrease and fragmentation rates increase from left to right. For ‘R’, fragmentation rates decrease from left to right. A dashed line indicates limited control (e.g., retardation and/or high dispersity likely under some conditions). Figure updated from the similar guidelines that appeared in earlier reviews.32,47 For monomer abbreviations see Fig. 1 and 2. | |
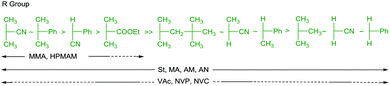 |
| Fig. 4 Guidelines for selection of the ‘R’ group of RAFT agents (Z–C( S)S–R) for various polymerizations. Fragmentation rates decrease from left to right. A dashed line indicates limited control (e.g., retardation and/or high dispersity likely under some conditions). Figure updated from the similar guidelines that appeared in earlier reviews.32,47 For monomer abbreviations see Fig. 1 and 2. | |
RAFT agents referred to in the text are shown in Table 1 (aromatic dithioesters), Table 2 (trithiocarbonates), Table 3 (dithiocarbonates or xanthates) and Table 4 (dithiocarbamates).
Table 1 Aromatic dithioester RAFT agents
Table 2 Trithiocarbonate RAFT agents
Table 3 Xanthate or dithiocarbonate RAFT agents
Table 4 Dithiocarbamate RAFT agents
Z group selection.
It was pointed out some time ago32 that, with access to just two types of RAFT agent differing in the Z group, it is possible to control the polymerization of most monomers so as to provide low dispersities, high end group fidelity and minimal retardation.32 One RAFT agent would be suited to MAMs (e.g., a trithiocarbonate) and the other to LAMs (e.g., a xanthate or dithiocarbamate).
Aromatic dithioesters such as the dithiobenzoates are amongst the most active RAFT agents (Fig. 3) and are arguably the reagents of choice for methacrylates and methacrylamides.33 They are, however, also more prone to side reactions, which include hydrolysis. Polymerizations of monosubstituted MAMs may be retarded by dithiobenzoates and those of LAMs and IAM are often inhibited. This is attributed to the “intermediate” species (Scheme 1) having a sufficient lifetime that some are consumed in side reactions. The polymerizations may also show greater oxygen sensitivity.
Trithiocarbonates, while not as active as the dithiobenzoates, provide a better balance between activity and incidence of side reactions. They are currently the most popular RAFT agents for controlling polymerization of MAMs.34,35
The dithiocarbonate (or xanthate)36 and dithiocarbamate37–40 RAFT agents towards the centre of Fig. 3 provide a measure of control over the polymerization of both MAMs and LAMs. Recent examples of such RAFT agents are the 3,5-dimethyl-1H-pyrazole-1-carbodithioates.41 These dithiocarbamates have wide-spread applicability. The cyanomethyl-derivative 44 offers very low dispersities (Đ < 1.1) for MAM-derived polymers P(MA), P(DMAm) and P(St) and Đ < 1.3 for the LAM, P(VAc).41 The 4-chloro-3,5-dimethyl-1H-pyrazole-1-carbodithioate 46 provides reasonable control (Đ ∼ 1.3) in MMA polymerization.42
Switchable RAFT agents (e.g., 43/43-H+), so-called because they can be reversibly switched by an external stimulus to give very good control over polymerization of either MAMs or LAMs, have been also described43,44 Protonation provides a pH switch in most current examples. As indicated in Fig. 3, the unswitched 43 is similar to 45 in activity and provides good control over LAMs (e.g., VAc), while the switched 43-H+ has similar activity to 42 and is effective with MAMs (e.g., St). These RAFT agents are further discussed below (see Switchable (pH responsive) RAFT agents).
In the context of stimuli-responsive polymer synthesis, requirements for specific end-group-functionality, architecture and/or solubility characteristics will also play a role in dictating the selection of the type of RAFT agent.45,46
R group selection.
The R group of the initial RAFT agent (ZC(
S)SR) must be selected to equal or better the homolytic leaving group ability of the propagating radical(s) formed in polymerization and also be a good initiating radical for the monomer(s) being polymerized. The rate constant for reaction of the radical R˙ with monomer (ki) should be greater than or equal to that for propagation (kp).
When ki is substantially lower than kp, polymerizations may be subject to an inhibition period until the initial RAFT agent is converted to a macroRAFT agent. This situation pertains in the case of more highly stabilized or sterically hindered radicals that are good homolytic leaving groups but add to monomer only slowly, e.g., when the RAFT agent R group is benzyl or substituted benzyl and the monomer is a LAM or IAM. This behaviour accounts for some of the dashed lines in Fig. 4. It does not mean that low dispersity polymers cannot be formed at higher monomer conversions. However, the behaviour can result in an inhibition period and places a constraint on the end-group fidelity.
RAFT agents for stimuli-responsive polymers.
RAFT agents that have found use in the context of synthesis of stimuli-responsive polymers are shown in Tables 1–4. In selecting RAFT agents for use in polymerization there are many factors to consider other that the reactivity or the RAFT agent.
For homogeneous RAFT polymerization, the solubility of the RAFT agent in the polymerization medium, can be a key concern. Aqueous soluble RAFT agents are of particular interest for many bio-applications and also for the synthesis of thermoresponsive polymers.48–50 RAFT agents which show a degree of water solubility include 6, 8, 12, 15, 21, 22, 28, 39 and 43/43H+.51 Note that some require at least partial ionization for solubility.
For heterogeneous polymerization, the solubility of the RAFT agent determines whether the RAFT agent or macroRAFT is localized in the desired phase and the transport/partitioning of the RAFT agent between phases.52,53 The selection of RAFT agents for emulsion and other forms of heterogeneous polymerization is complex and space limitations prevent a detailed discussion.
The selection of RAFT agent must also take into account the functionality required for the end-use application and whether thiocarbonylthio group removal/transformation is required. It is important to note that the Z group and its functionality will typically be lost if the RAFT end group is cleaved (see RAFT end-group transformation chemistry).
Initiators in RAFT polymerization
The RAFT mechanism (Scheme 1) requires an external source of radicals for polymerization to proceed. The initiators used in RAFT polymerization are most commonly a thermal source of radicals such as 2,2′-azobis(2-methylpropanenitrile), AIBN.54 However, other initiators, including various peroxides, can also be used. Even though the peroxide-derived radicals may react irreversibly with RAFT agents, the kinetic parameters55 generally ensure that oxygen-centred peroxide-derived radicals react preferentially with monomer under most polymerization conditions.
The initiating radicals may also be formed from directly from the monomer (e.g., in thermal St polymerization56), or from the RAFT agent by direct photolysis,57–62 or by redox (e.g., by atom transfer radical addition)63,64 or photo-redox chemistry.65–70 The redox- and photo-responsiveness of the RAFT agent thiocarbonylthio-functionality, and photo electron/energy transfer-RAFT (PET-RAFT), are considered further later in this review.
In RAFT polymerization, the rate of initiation should be as low as possible commensurate with achieving an acceptable rate of polymerization. When conventional initiators are used the usual guideline is that the amount of initiator (or more correctly, the amount of initiator-derived radicals formed) should be less than 10 mole% of the amount of RAFT agent. This should ensure an end-group fidelity of greater than 90%.
The fraction of living chains (L) in RDRP is defined as the number of active chain ends plus the number of dormant chain ends. In a RAFT polymerization, this equates to the fraction of chains with RAFT agent functionality and can be estimated from the relationship (eqn (1)):32
| 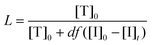 | (1) |
where [T]
0 is the RAFT agent concentration,
d is the number of chains produced from radical–radical termination (1.0 for termination by combination, 2.0 for termination by disproportionation),
f is the initiator efficiency and [I]
0 − [I]
t is the initiator consumed. The expression applies to initiators which decompose to form two similar radicals, such as AIBN. If the initiator decomposition rate constant (
kd) is known,
54 the initiator consumption at time
t can be estimated using
eqn (2):
| [I]0 − [I]t = [I]0 (1 − e−kdt) | (2) |
In cases where polymerization is slow, rather than boost the rate of initiation, a better strategy when possible is to choose conditions that facilitate propagation (e.g., by increasing the temperature and/or the monomer concentration).
In order to maximize RAFT end-group fidelity and/or block purity, it is important to stop the polymerization once the desired conversion is achieved. Continued production of radicals beyond this point will lead to further loss of living ends.
One criticism of RAFT, in comparison to RDRP such as NMP or ATRP, is that because an exogenous initiator is used in RAFT there must be (a greater number of) dead chains. However it should also be noted that both the rate of polymerization and the rate of termination are determined by the radical concentration. It follows that all RDRP that proceed at a similar rate will experience a similar amount of termination.
Gradient copolymer synthesis
In a random copolymer, the polymer composition and sequence distribution are determined only by the concentrations of monomers in the feed. In a statistical copolymer, the polymer composition and sequence distribution is additionally determined by the monomer reactivity ratios. Random copolymers, alternating copolymers and gradient copolymers are each a subset of statistical copolymers that may be formed depending on the polymerization method and the monomer reactivity ratios.71
Most copolymers formed by RAFT copolymerization of two or more monomers will, by default, be gradient copolymers. Any compositional drift that arises from disparities in the reactivity ratios will be captured within each individual polymer chain. The more reactive monomer will appear closer to the “R” end. The less reactive monomer(s) will be concentrated at the “ZCS2” end (Scheme 3). In RAFT copolymerization, chains will not be identical but all will possess the same gradient composition with the monomer sequence distribution being determined by the monomer reactivity ratios.
 |
| Scheme 3 RAFT gradient copolymer synthesis making use of two monomers with disparate reactivity ratios. | |
Forced gradient copolymers are made by purposefully skewing the monomer feed.72,73 Any changes in monomer composition will be immediately reflected in the composition of each polymer chain at the “ZCS2” end. Feed addition protocols can be designed to form random copolymers when reactivity ratios would dictate that a gradient would be formed for a batch polymerization. In batch heterogeneous polymerization, gradient compositions may also reflect the differential solubility of the monomers.74
In the context of forming stimuli-responsive copolymers, an important benefit of RAFT polymerization and gradient copolymer formation, is that all chains formed have essentially the same composition. In these circumstances, conventional radical copolymerization of monomers with disparate reactivity ratios would yield a polymer blend (Scheme 4). In the conventional (non-RDRP) process, polymer chains formed at low monomer conversion will differ in composition and molar mass from those formed at high conversion. This behaviour provides one explanation for RAFT-synthesized copolymers showing properties that are substantially different to those of conventionally prepared copolymers in various applications. Examples of stimuli-responsive polymers which take advantage of such spontaneous gradient formation include RAFT copolymerization of St with AA.75 Particularly disparate reactivity ratios enables the RAFT-synthesis of “blocky” copolymers in a batch process (e.g., in copolymerizations of St with MAH76,77 or in the copolymerization of ODA with NVP78,79) and allows the concept of “writing to polymer chains” by shot addition of small amounts of monomer during polymerization.80,81
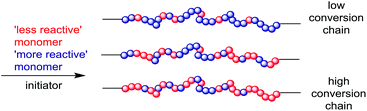 |
| Scheme 4 Conventional copolymer synthesis making use of two monomers with disparate reactivity ratios will form a blend. Chains formed at low conversion will comprise mainly the more reactive monomer. | |
A recent example of gradient polymer synthesis in the context of stimuli-responsive polymers is the synthesis of gradient polymer electrolytes for application in lithium batteries.82
Good control in RAFT MAM/LAM copolymerization is possible in circumstances where a given RAFT agent may be specific for MAMs or LAMs. Thus, trithiocarbonates provide good control in copolymerizations of tBA and VAc even though the same RAFT agent inhibits VAc homopolymerization. Xanthates and dithiocarbamates also provide good control in such copolymerizations (e.g., 40 in MA/VAc copolymerization83 or 20 in DMAm/VAc copolymerization41).
Non-gradient (random) copolymer synthesis
In forming stimuli-responsive polymers it is sometimes desirable to have monomer functionalities randomly distributed within copolymer chains. As stated above, the default product in RAFT copolymerization (and other RDRP) will be a gradient copolymer. Random copolymers will only be formed when the monomer reactivity ratios are unity (e.g., copolymerization of two similar methacrylates approach this ideal), when a constant ratio of monomers in the feed can be maintained by judicious additions of monomer(s), and when copolymerizations are performed at an azeotropic monomer composition.
For binary copolymerizations of two monomers A and B that can be represented by the terminal model,84 and where the monomer reactivity ratios are both greater than or less than unity, there will be exactly one azeotropic composition for the monomer feed when the fraction of monomer A in the feed (fA) is (1 − rA)/(1 − rB).84 In RAFT copolymerization this value may be perturbed for short chain lengths by specificity shown by the RAFT agent-derived radical. Conditions for azeotropic compositions for binary copolymerization when a penultimate model applies85 and for ternary and quaternary copolymerizations86 have also been defined.
In the context of RAFT copolymerization, polymerization under azeotropic conditions has been made use of in forming, e.g., St/MMA87 St/Bd88 and St/AN copolymers.4 Moraes et al. have explored the strategy for the case of HPMA copolymers.89
Sequence defined polymers by RAFT
There is much interest been in the preparation of sequence defined polymers by RAFT and other RDRP wherein the sequence of monomers in a polymer chain is decided by the synthetic chemist rather than statistical factors. The goal is to attain the precision demonstrated by nature in molecules such as proteins or nucleic acids. The development of a practical strategy should immediately lead to a major advance in stimuli-responsive polymers.
Multi-block polymer synthesis.
Many have decided that that sequence control and the monomer level is impractical and have turned their attention to the production of multi-block copolymers in which the sequence of blocks is controlled. This approach is described in the section Block copolymer synthesis below.
RAFT single unit monomer insertion.
RAFT single unit monomer insertion (SUMI) was demonstrated by Zard and coworkers90 as a useful technique in organic synthesis, a decade before the invention of the RAFT as a method for RDRP. Much recent interest placed in performing sequential SUMI to form copolymers with sequence distribution that is precisely defined at the monomer level. Using conventionally initiated RAFT with appropriate selection of RAFT agent and monomer, high yield (>95%) SUMI has been demonstrated for monosubstituted MAMs (e.g., St,91,92 2-vinylthiophene,93 DMA,92 NIPAM91). Successful SUMI requires a RAFT agent with Ctr such that, on average, there is <1 monomer inserted per activation cycle (i.e., kp[M] ≪ ktr[RAFT agent]) and is facilitated by ki ≫ kp, by kβ ≫ k−add (refer Scheme 1), by low relative monomer concentrations (stoichiometric with RAFT agent) and an initiator-derived radical that is identical to the RAFT agent ‘R’ group.91,92 SUMI is an important technique for converting macromonomers to macroRAFT agents.93
In cases where high yield SUMI is not possible, the application of separation techniques, such as preparative recycling size exclusion chromatography,94–96 can enable separation of discrete oligomers from the reaction-derived oligomer mixtures. However, yields are then lowered.
Consecutive high yield SUMI has been demonstrated for St-MAH92 and St-NPMI co-dimer97 with 2. Success in these cases can be attributed to MAH and NPMI being inert to the initiator-derived radical from AIBN. Zard and co-workers98 reported consecutive SUMI of NVPI followed by an allyl monomer into a xanthate. A key factor contributing to success in these examples is the use of a non-homopolymerizable monomer99 (kp ∼ 0) in the second SUMI step. However, in general, yields in conventionally initiated consecutive SUMI experiments are substantially lowered by the concurrent formation of products from initiator-derived chains.91,92 SUMI of non-homopolymerizable monomers also provides a method of chain-end functionalization for RAFT synthesized polymers. MAH,100–103 maleimides,104,105 β-pinene,105 and ABOC (for a primary amino end-group)106 have been used in this context.
A recent development is PET-RAFT-SUMI wherein radicals are generated directly by photo-activation of the RAFT agent (see section on Light-responsive RAFT agents below). It has been possible to form discrete, e.g., St-NPMI-VAc co-trimers in near quantitative yield.107 The full scope of this process is currently being explored.
Template polymerization.
The use of templates, many biologically derived or at least biologically inspired, has been studied.108 One approach makes use of polymers comprising nucleobase pendants with the aim of preparing precisely defined daughter polymers of the complementary nucleobase.109–111
Block copolymer synthesis
Di-, tri- and higher order block copolymers or multi-blocks can be simply made by sequential addition of monomers (Scheme 5).112 Details are provided in many reviews.17,32,113 However, it is worthwhile stressing some of the critical factors for achieving high quality blocks.
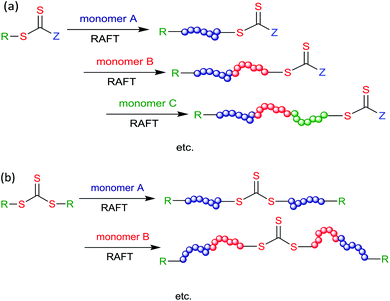 |
| Scheme 5 Representations of RAFT multi-block copolymer synthesis by sequential monomer addition using (a) a mono-RAFT agent or (b) a symmetrical trithiocarbonate. | |
The factors mentioned above under Initiators in RAFT polymerization with respect to maintaining end-group fidelity are also extremely important to attaining block purity in block copolymer synthesis.112 For each chain initiated, between one and two chains will terminate depending on the termination mechanism. Thus, in making an AB diblock, there will be an amount of homopolymer A contaminant corresponding to the number of initiator-derived chains generated during the synthesis of the A block. Any Initiator-derived chains formed during formation of the B block will comprise a homopolymer B impurity. Moreover, if termination occurs by combination, some ABA triblock will also be formed during this step. The situation become progressively more complex for multi-block copolymers, as the number of generations increases.
For high kp monomers such as acrylates and acrylamides, it is possible to achieve high polymerization rates with very low amounts of initiator. It is, therefore, also possible to achieve high (e.g., >99%) monomer conversions whilst maintaining the integrity of the RAFT end groups. For example, this strategy was to advantage used in making amphiphilic copolymers comprising a P(ODA) block,79 where any residual ODA is difficult to remove. It was also applied in the Perrier approach114–117 to multi-block copolymer synthesis.
Nonetheless, in order to maximize end-group fidelity, it is desirable to limit monomer conversion to e.g., <90%, particularly in the case of low kp monomers such as styrenes and methacrylates. As monomer conversion increases, termination becomes progressively more important. In these cases, it may be expedient to prepare what have been called quasi-block copolymers.118,119 These arise when block copolymers are formed by sequential addition of monomers where there is incomplete monomer conversion and no purification is performed to remove the residual monomer. For the case of sequential addition of two monomers A and B, the product “quasi-block” will be a gradient copolymer, P(A)-b-P(A-grad-B), due to the incorporation of the residual first block monomer into the second block. The detailed structure of the “quasi-block” will depend on the monomer reactivity ratios. Where reactivity ratios are similar (e.g., for copolymerization of several methacrylates120) the copolymer structure may approximated as P(A)-block-P(A-ran-B). Where the monomer reactivity ratios are such that there is a strong tendency for alternation (e.g., St/MAH), the copolymer structure will be P(A)-b-P(A-grad-B)-b-P(B). The quasi-block protocol is particularly attractive when using high-throughput methods.119–121 However, the impact on polymer properties always needs to be considered. For many applications, purity is of paramount importance.
The factors that were mentioned as important for R group selection above also determine the order in which blocks should be constructed in block copolymer syntheses based sequential monomer addition. The propagating radical derived from the first-made block must be a good homolytic leaving group (i.e., equal or better) with respect to that to be produced from the monomers of the next-made block. The propagating radical derived from the first-made block must add efficiently to at least one of the monomer(s) that will comprise the second block.
For example, in attempted synthesis of P(St-b-VAc) the P(St) propagating species adds VAc only slowly.43 As a consequence, the P(St) macroRAFT agent is only slowly consumed, there is significant retardation particularly in the presence of any residual St monomer, and, even though a low dispersity diblock is possible, complete conversion to a diblock is only achieved for high monomer conversions. This situation can be remedied by installing a short block of a more suitable monomer (MA) between the P(St) and P(VAc) blocks to form P(St)-b-P(MA)-b-P(VAc).43,122 The P(MA) block length should be sufficient to ensure at least one unit of MA at the end of every chain. A second remedy is to add a small amount of MA as a comonomer in forming the VAc block [to form P(St)-b-(P(MA)-grad-P(VAc))-b-P(VAc)]. The St/MA and MA/VAc reactivity ratios are such as to ensure the desired structure.43,122
Another method of achieving improved block integrity when constructing “wrong-way” blocks, or when using low transfer constant macroRAFT agents, involves use of starved-feed addition protocol.123,124 The rate of consumption of an initial RAFT or macroRAFT agent can be approximated by the expression (eqn (3))
|  | (3) |
where
Ctr (= [
kadd/(
k−add +
kβ)]/
kp) and
C−tr (= [
k−β/(
k−add +
kβ)]/
ki) are the forward and reverse transfer constants associated with the initialization process (refer
Scheme 1). This indicates that the relative rate of consumption of the initial RAFT agent can be enhanced by reducing the monomer concentration. In early work, this strategy was employed in preparing low dispersity block copolymers from so-called macromonomer RAFT agents.
125,126 Very recently, this strategy has been applied in the synthesis of multi-block copolymers.
127
Star polymer synthesis
Star structures and the general approaches to star polymer synthesis are described in detail in a recent review.128 There are two main routes to star polymers by RDRP. These are (a) the core-first methods, in which chains are grown from a core containing multiple RAFT agent functionalities (a “grafting from” approach) and (b) the arm-first methods, in which arms are prepared first and linked to provide a star structure (may be “grafting to” or “grafting through”).
Particularly For the case of core-first methods that involve RAFT polymerization, we should additionally consider processes based on Z-connected or R-connected RAFT agents (Scheme 6). These are sometimes known as the convergent- and divergent-growth approaches, respectively. For the process based on Z-connected RAFT agent propagating radicals are always detached from the core. Dormant chains are attached to the core by a cleavable thiocarbonylthio linkage. No star–star coupling is likely. For the process based on R-connected RAFT agents most propagating radicals remain attached to the core (initiator-derived chains whether active or dormant remain detached from the core). The polymer is directly attached to the core and the thiocarbonylthio group is an end group. Star–star coupling is frequently observed.
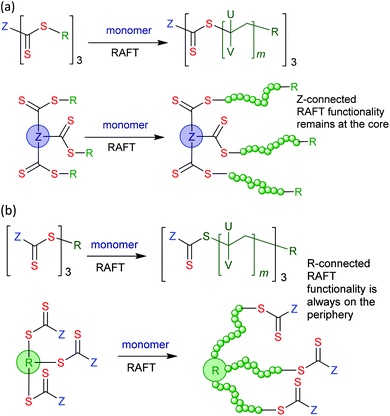 |
| Scheme 6 Representation of core-first processes for 3-arm star synthesis by RAFT polymerization with (a) Z-connected and (b) R-connected RAFT agents. | |
The core in core-first star synthesis can be a well-defined low molecular weight compound.123,129 However, a wide range of multifunctional substrates can be converted to multi-RAFT agents using well-established chemistry.130 These substrates may take the form of:
• a dendrimer, a hyperbranched oligomer/polymer, or a nano- or microgel.
• a particle or nanoparticle.131,132 See Surface-initiated RAFT polymerization (SI-RAFT) below.
• a metal complex133–140 There are now many examples of using metal complexes directly as the core of star polymers. The metal complex must be compatible with the redox properties of RAFT agent.
The early CSIRO work129 showed that low dispersity stars could be synthesized making use of both Z-connected and R-connected multi-RAFT agent cores. Later work established mechanisms for accelerated termination in polymerizations with Z-connected RAFT agents.141 This has served to emphasize the importance of RAFT agent design and the choice of polymerization conditions.142
Two convenient processes for forming nanogel cores by RAFT polymerization are RAFT-mediated crosslinking copolymerization143,144 and RAFT self-condensing vinyl polymerization.145–149 The crosslinking copolymerization approach involves RAFT mediated copolymerization of a multi-olefinic crosslinking monomer e.g., DVB, EGDMA or MBA. The self-condensing vinyl polymerization route involves RAFT (co)polymerization mediated by a RAFT agent containing monomer functionality (sometimes these are referred to as RAFT inimers). Recently, we compared these two approaches in preparing star architectures for antigen delivery.150
The arm-first route often involves a crosslinking copolymerization mediated by a macroRAFT agent.151,152 The method involving RAFT polymerization was first described in patent applications that appeared during 1999–2000 by Solomon et al.153 and Berge et al.154 A variant on the approach makes use of a macromonomer, a crosslinking agent and a low molecular weight RAFT agent.155 Examples of arm-first star synthesis making use of redox sensitive crosslinkers comprising a disulphide linkage can be found in Table 7.
The optimal conditions for achieving low dispersities when preparing RAFT-synthesized stars by the arm-first process are not fully understood. Some early studies found that the use of RAFT polymerization in the arm-first method provided polymers with a relatively broad molar mass distribution.156 The use of heterogeneous (emulsion) polymerization has been advocated to resolve this issue.157,158 For homogeneous polymerization, the dispersities of star polymers appear strongly solvent dependent. It was suggested that one requirement for attaining low dispersities that polymerization medium is a poor solvent for the crosslinker.159,160 Low dispersity stars (POEGA, PtBA or PNIPAm arms) were obtained with use of the crosslinker N,N′-bis(acryloyl)cystamine in toluene as solvent.159 However, this appears to be neither a necessary nor a sufficient condition for forming low dispersity stars and further study is needed.161
In the arm-first process the RAFT functionality is retained in the core. Thus arm-first stars can be used subsequently as macroRAFT agents in the so called “in–out” process for mikto-arm star synthesis.162 Mikto-arm stars comprise arms of two or more different compositions attached to a central core163,164 and various approaches using RAFT polymerization have been applied in their synthesis.100,152,165–172
Cylindrical polymer brushes
In this section, we consider so-called bottle brush polymers or cylindrical polymer brushes. Brushes formed on surfaces or particles are discussed below under SI-RAFT.173
Strategies for bottle brush polymers and cylindrical polymer brush synthesis by RAFT polymerization generally parallel those already described for star polymer synthesis. Thus, core-first approaches have been described that commence with synthesis of polymers with pendant RAFT agent functionality.174–176 In the case of low kp monomers (e.g., St, MMA) use of a “sacrificial” RAFT agent has been shown to facilitate synthesis R-connected polymer brushes.177
Arm-first approaches usually involve polymerization of macromonomers; a “grafting through” strategy. Examples are generally limited to those monomers that are sterically less demanding such as, PEGA,178 PODA,79,179,180 and the corresponding methacrylates.
Other methods involve formation of a functional polymer backbone and brush formation by some combination of RAFT polymerization, “click” chemistry, and sometimes another RDRP method, most commonly ATRP. Examples include:
• the syntheses of alkyne-end-functional arms by RAFT polymerization, which are then “clicked” to an azide functional backbone.181,182
• the preparation of a backbone with pendant protected primary amine functionality by RAFT polymerization, which is then deprotected and “armed” by active ester chemistry.183
Surface-initiated RAFT polymerization (SI-RAFT)
A variety of processes for surface-initiated RAFT polymerization (SI-RAFT) have been described.184–186 Often a preliminary step in SI-RAFT involves some chemical transformation to attach RAFT agent functionality to the surface. Another method involves forming radicals on the surface, e.g., by irradiation or through attached initiator functionality, and initiating RAFT polymerization in the presence of a ‘free’ RAFT agent that becomes surface-bound as a consequence of RAFT polymerization.
Some examples of forming polymer bushes on two-dimensional surfaces by surface-initiated RAFT polymerization include the following.
• Z-connected RAFT agent: BA from silicon wafer.132 4VP from ZnO nanoparticles.187
• R-connected RAFT agent: MMA from stainless steel.188 HEMA,189 CMS,190 or DMAPMAm191 from silicon wafer. NIPAm from glass.192,193 POSS-MA/DMAEMA from poly(dimethylsiloxane).194 SBEMA from cellulose.195 VPBA196 or SDPP197 from a P(St-co-DVB) monolith. MAA from polypropylene.198 HPMAm from carbon nanotubes.199 St from clay nanoparticles.200 Am201 or St202 from iron oxide nanoparticles. HEMA from silica nanoparticles.203
R-connected strategies are the most popular and are more suited for applications that require permanent surface modification. The Z-connected approach affords a coating that is readily cleaved from the surface using “end-group” transformation/removal techniques.
Strategies for attaching the RAFT agent to the surface vary. Sacrificial RAFT agents are often used and generally necessary to provide good control over graft length and dispersity. In SI-RAFT, the RAFT process can become diffusion controlled. This problem can be alleviated by the presence of low molar mass RAFT agent in the polymerization medium. The approach making use of sacrificial RAFT agents will necessarily produce a linear polymer derived from the sacrificial RAFT agent as a by-product. This, being of low molar mass, is usually readily separated. The sacrificial RAFT agent strategy is useful when grafts of a defined length are required and essential when these are of low molar mass. The graft-length obtained in such experiments is defined largely by the concentration of the sacrificial RAFT agent. For example, in grafting VPBA196 or SDPP197 from a P(St-co-DVB) porous monolith, it was necessary to form very short graft (5–10 units) to avoid clogging the pores.
Various groups have modelled surface-initiated RAFT polymerization for both Z-connected204 and R-connected RAFT agents205 with a view to better defining termination processes and their influence on the efficiency of the process. Zhou et al.206 have recently reviewed processes for surface-initiated RDRP with a focus on biomaterials.
Network polymer synthesis
There has been a recent increase in publications on polymer networks formed by RAFT polymerization in line with the growth in applications of stimuli-responsive systems such as dynamic covalent polymers (see Self-healing polymers), porous polymer monoliths or gels (used as chromatographic media,207–210 flow reactors,196,197,211 controlled release media,212 drug delivery vehicles and molecular imprinting207,208,213,214) and coatings.215 RAFT crosslinking polymerization to form network polymers has recently been reviewed.216
It might be naively anticipated, that in applying RAFT to network synthesis, that just as RAFT provides control over molecular weight and molecular weight distribution for linear polymers, it would allow control over the distance between crosslinks and thence of pore size in RAFT-synthesized polymer networks. However, controlling the distance between crosslinks in crosslinking (co)polymerization is more akin to controlling monomer sequence distribution during linear polymer formation; a target that remains elusive in the field RAFT91,92 and RDRP generally.217
The development of network structure for two forms of RAFT agent: (a) mono-RAFT agents, R–SC(
S)Z, and (b) symmetrical trithiocarbonates (these are ‘Z’-connected bis-RAFT agents, R–SC(
S)[Z′C(
S)]n–S–R with n = 0) are shown in Fig. 5.216 The first provides a network with pendant RAFT functionality, the second a network with internal trithiocarbonate linkages.
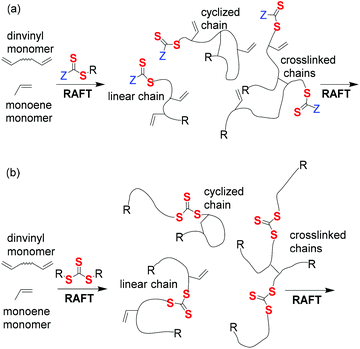 |
| Fig. 5 Structure of “sol” formed with two types of RAFT agent: (a) monofunctional, R–SC( S)Z (b) difunctional, R–SC( S)–S–R. | |
Covalently crosslinked networks are an important class of stimuli-responsive materials. Often these take the form of swollen gels, commonly hydrogels, which respond to stimuli such as a change in pH, temperature or ionic strength to trigger a change in equilibrium degree of swelling. Polymer networks also find a role in molecular imprinting, monoliths for chromatography or flow chemistry196,197 and in self-healing polymers or covalent adaptable networks (CAN) based on reversible crosslinks.218–222
RAFT polymerization induced self-assembly
Self-assembly of polymers has traditionally involved two steps: (i) dissolution and (ii) microphase separation. The latter step is driven by some change in solvent properties, e.g., by adding a non-solvent, evaporating some solvent or changing the temperature.
A now common approach to forming nano-objects, by block copolymer self-assembly based on RAFT or other RDRP, involves chain-extending a polymer with a second monomer in a solvent chosen such that it is a good solvent for the monomer but a poor solvent for the growing second block, which gradually becomes insoluble. There are, however, many cases where some form of supramolecular order develops as a consequence of polymerization that may also be considered RAFT polymerization-induced self-assembly (PISA), and which are relevant in the context of preparing stimuli-responsive materials.223
For example:224
• the initialization step in ab initio emulsion and some other forms of heterogeneous polymerization.
• the formation of micelles and other structures when forming amphiphilic copolymers by homogeneous RAFT polymerization.
• the formation of micro- or nanogels by RAFT crosslinking polymerization (e.g., core synthesis for core-first stars).225
• the formation of stars and other structures by crosslinking polymerization mediated by a macroRAFT agent (e.g., arm-first star synthesis).
RAFT (co)polymerization of functional monomers and the “grafting through” approach to stimuli-responsive polymers
In the design and synthesis of stimuli-responsive polymers the major role of RAFT polymerization is simply as a tool for the construction of well-defined low dispersity polymers from monomers or macromonomers containing appropriate functionality. These processes can be considered examples of the “grafting through” approach of introducing functionality.
As discussed above, most monomers are compatible with RAFT polymerization in unprotected form. However, selection of polymerization conditions to provide appropriate solubility/compatibility for all of the RAFT agent, the monomer(s) and their polymer(s), particularly in the case of amphiphilic copolymers, is often a challenge and can by itself dictate a need for protection strategies.
In the following sections we will briefly consider thermo-, pH-, redox- and light- and chemical-responsive polymers which are prepared by (co)polymerization of monomers already mentioned in Monomers in RAFT polymerization. We will then discuss RAFT polymerization of several monomers classes that have assumed a special role in the synthesis of stimuli-responsive polymers, in particular, betaine (or zwitterionic) monomers, ionic liquid monomers and metallo- (or metal chelating) monomers. Finally we will consider the synthesis of polymers based on monomers designed for post-polymerization modification. A big advantage of the post-polymerization modification processes is that they enable libraries of polymers to be prepared from a common precursor.
Thermo-responsive polymers
In the present context, the term “thermoresponsive” generally relates to the solution properties of polymers that display either a lower critical solution temperature (LCST) such that they phase separate from aqueous solution upon heating, or to polymers with an upper critical solution temperature (UCST), which phase separate from solution upon cooling. Most reviews on the subject have a strong focus on materials displaying LCST behaviour.226,227 A relative few detail UCST behaviour.228 Aqueous LCST or UCST values must normally be within the temperature range 10–100 °C to attract interest.
The best known examples of RAFT-synthesized polymers showing LCST behaviour are P(NIPAm) and P(OEGMA).226,229 LCST behaviour is also displayed by many other acrylamide and methacrylamide homo- and copolymers.226 The respective monomers present no difficulty in RAFT polymerization. Other polymers to show LCST behaviour include poly(vinyl alcohol) copolymers [formed from P(VAc)],230 P(VCL),231 P(DAEMA)232 and some polymer ionic liquids (see below).233,234 RAFT-synthesized polymers showing UCST behaviour include some based on zwitterionic betaine monomers (see below). LCST values can be tuned with the synthesis of copolymers (block, gradient), by controlling the polymer architecture (stars), even by changing the end groups.235
Much interest lies in materials (blocks, biopolymer conjugates, particles, surfaces) that contain segments showing thermoresponsive behaviour where such behaviour may provide a trigger for therapeutic release.
pH-Responsive polymers
Polymers that are pH-responsive display a change in solubility or conformational properties as a function of the acidity of the medium.236–238 These polymers commonly possess ionizable groups that are pendant to the backbone, e.g., tertiary amino in P(DMAEMA) or pyridyl in P(4VP), which are cationic at lower pH, or carboxy in P(AA), which is anionic at higher pH. Other ionisable pH-responsive polymers are based on amino acid-derived acrylamides239,240 and methacryloyl sulphonamides (47) (Table 5).241
Table 5 Examples of RAFT-synthesized pH responsive polymers
Monomers |
RAFT agent |
Comment |
Ref. |
2-(Diisopropylamino)ethyl methacrylate, 2-(piperidin-1-yl)ethyl methacrylate, 2-(dibutylamino)ethyl methacrylate.
|
Tertiary amino methacrylatea |
6
|
PEG block copolymers |
243
|
DMAEMA/MMA |
2
|
Compared with DMAEA/MA |
244
|
DMAEA/MA |
29
|
Compared with DMAMEA/MMA |
244
|
|
6
|
Polymer pKa ∼4.5–7.5 dependent on R. Water soluble in ionized form |
241
|
15
|
Incorporation of acidic or basic comonomers into polymers which show LCST behaviour paves the way for using a pH change to shift the LCST.242
Another class of pH-responsive polymers, not considered here, are those that undergo an irreversible pH-induced chemical transformation.236
Redox-responsive polymers
Redox responsive polymers for biomedical applications have been reviewed.245 An important class of redox-responsive comprises the metallopolymers, which are described separately below.
A second major class of RAFT-synthesized redox-responsive polymers are those that contain disulfide linkages149,246–249 that can be reversibly cleaved by reduction. This includes microgel, hyperbranched or star polymer formed by self-condensing vinyl polymerization (Table 6) or RAFT crosslinking polymerization (Table 7).
Table 6 RAFT disulphide monomers used in-synthesis of redox-responsive polymers
RAFT disulfide monomer |
Comment |
Ref. |
|
R = CH3 |
250
|
R = H |
251–253
|
|
|
246
|
Table 7 Crosslinking monomers containing disulphide linkages used in-RAFT-synthesis of redox-responsive polymers
Photo- or light-responsive polymers
There are a wide variety of materials that can be considered within the category of light or photo-responsive polymers. The light responsive functionality can be introduced into the RAFT-synthesized polymer through functionality the monomer (Table 8),277 the RAFT agent (Table 9)278 or by post-polymerization functionalization.279 These polymers fall into a number of, not mutually exclusive, classes, which include photochromic polymers, certain electroactive polymers and light-harvesting polymers.
Table 8 Monomers for synthesis of light-responsive polymers
Photochromic monomer |
Polymerizationa/comment |
Polymerizations shown as: monomer(s) (RAFT agent)ref.
Other naphthopyran monomers also described.285
|
|
48 (2)277 |
Light induced self-assembly, gold nanoparticles |
|
SI-RAFT287 |
Photochromic particles |
|
50-co-MMA (2)285 |
50-co-MA (2)285 |
MMA-b-50-co-MA (2)285 |
MMA-b-50-co-MA (2)286 |
Photochromic statistical and block copolymers |
|
51-co-4VP (6)301 |
Photochromic nanowires prepared by electrospinning |
|
NAM-b-(52-co-NIPAm) (35)302 |
Table 9 RAFT agents for synthesis of light-responsive polymers
Photochromic RAFT agent |
Polymer/comment |
|
P(NIPAm)303 |
Thermo-responsive gold nanoparticles |
|
P(St)-b-P(BA)284 |
P(BA)-b-P(St)284 |
P(NIPAm)-b-P(NAM)302 |
Control of photochromic switching speed |
Other light-responsive polymers that are not considered within the scope this review, since the changes induced are most often irreversible, include photo-scissionable polymers, which undergo main-chain280 or side chain photocleavage,20 photo-crosslinkable polymers, which contain various photo-initiator functionality to achieve photo-crosslinking,281 and polymers for photo-lithography, which are typically pH sensitive polymers containing a photo-acid generator.282
In forming light responsive polymers it is important to consider the properties of the thiocarbonylthio group which is itself photoactive and can, e.g., quench florescence or photo-dissociate, necessitating end group removal.283
Photochromic polymers.
Photochromic polymers contain functionality that can undergo some form of, preferably reversible, light-induced isomerization to change colour or light absorption characteristics.284–289
Often there is an associated change in the hydrophilic–hydrophobic balance or more generally the solvophilic-solvophobic balance for the material so as to change solubility. This can be used cause light-induced self-assembly/disassembly, or otherwise modify polymer properties.290 This response can also be used a trigger mechanism for the delivery of therapeutics.
RAFT-synthesized tails on matrix encapsulated photochromic dyes provide a method of tuning the dye switching speed.284
Light harvesting polymers.
There are now many examples of RAFT-synthesis of light harvesting polymers.133–136,291–300 For example, Chen et al. prepared polymers comprising a RAFT-synthesized P(CMS) backbone (prepared with 5), which was then functionalized by Huisgen cycloaddition to have pendant oligomeric π-conjugated chromophores.299
Chemical-responsive polymers
In the present context chemical-responsive polymers show a reversible change in the presence of reagents, which can be introduced to or removed from the system. These reagents include gases such as O2,304 CO2 and NO.
Carbon dioxide-responsive polymers.
CO2 responsive polymers can also be considered a sub-class of pH responsive polymers. They find application in various fields,305–307 which include CO2-capture and storage, in CO2 switchable surfactants and in polymersomes with CO2 triggered release.
The most common CO2 responsive monomers are those possessing basic amine, amidine or guanidine functionality.306 These groups react with the carbonic acid formed when CO2 dissolves in water to form the respective ammonium, amidinium or guanidinium bicarbonate salts.
Thus, RAFT-synthesized P(DMAEMA)-block-P(DMA) copolymers have been developed as the basis for CO2-breathing vesicles.308 Dual CO2–O2 responsive P(DEAEMA/PFS) microgels with have been prepared by RAFT crosslinking-copolymerization.309
Other polymers shown to be both CO2- and pH-responsive include the methacryloyl sulphonamides.241 These polymers are notable for having pKas in a biologically relevant range (pH = 4.5–7.4).
In that nucleophilic groups may react with the thiocarbonylthio RAFT agent functionality, polymers are often formed by post-polymerization modification, e.g., using active ester chemistry.310
Nitric oxide responsive polymers.
The monomer 53 (Table 10), and derived polymers, react with NO in aqueous solution in the presence of O2 to generate light-sensitive phenyldiazonium groups.19
Table 10 RAFT-synthesis of NO-responsive polymers
NO-responsive monomer |
Polymerizationa |
Polymerization shown as: monomer(s) (RAFT agent)ref.
|
|
PEG-b-(NIPAm-co-53) (8)19 |
The dithiobenzoate RAFT end of the low dispersity PEG-b-P(NIPAm-co-53) was apparently stable in the presence of the primary aromatic amine.19
Other chemical-responsive polymers.
A wide range of polymers have been prepared with functionalities designed to invoke a specific response. These include polymers containing monomer units with, e.g., boronic acid (Table 11, see also Brooks et al.311) or phosphine functionality (e.g., DPPS, Table 12) and glycopolymers (Table 13). Other materials that might be considered here are (typically crosslinked) polymers prepared with molecular imprinting.210 Applications include fluorescent or colorimetric sensors312 and stationary phases for chromatography.
Table 11 Boronic acid monomers
monomer |
RAFT agent |
Comment |
Ref. |
Surface-bound RAFT agent based on the RAFT agent indicated.
|
|
24
|
Fluoride ion responsive polymers |
316
|
|
(20)a |
Monomer used in SI-RAFT monolith functionalization. Monolith for catalyst in flow chemistry |
196
|
|
25
|
Sugar responsive polymers |
317 and 318
|
|
(24)a |
Sugar responsive polymers |
319 and 320
|
Monomer used in SI-RAFT to form affinity column |
321
|
Table 12 Phosphine monomers
Monomer |
RAFT agent |
Comment |
Ref. |
Surface-bound RAFT agent based on the RAFT agent 20.
PEGMA-co-MAA macro RAFT agent formed with 6.
|
|
(20)a |
Monomer used in SI-RAFT monolith functionalization. Monolith for catalyst in flow chemistry |
196
|
30
|
DPPS-co-St potential use in forming catalysts |
322
|
6
|
DPPS-co-(alkylstyrene) potential use in forming catalysts |
323
|
(6)b |
DPPS-co-St block used as arm macro RAFT agent in forming nanoreactor by crosslinking polymerization |
324
|
Table 13 Glycomonomers
Glycomonomer |
Polymerizationa |
Polymerizations shown as: monomer(s) (RAFT agent)ref.
FMA – fluorescein O-methacrylate.
Poly(ethylene-alt-propylene) macroRAFT agent derived from 24.
See Table 34 for structure.
|
|
91-co-54 (24)325 |
54-b-HEMA-b-NIPAM (6)326 |
|
DEGMA-b-55 (43/43H+)327 |
55-co-NIPAM-b-NIPAM (24)328 |
|
56-co-AEMA-co-HEAm (6)329 |
|
57-co-AEMA-co-HEAm (6)329 |
|
58 (26)259 |
58-co-FMAb (5)330 |
58 (6)331 |
|
59-
b-AEMA (16)332 |
PEP-b-(59-grad-DMA)c 333 |
|
60 (150d)334 |
Glycopolymers possess an all carbon backbone and have pendant oligosaccharide groups. They are usually derived by polymerization of acrylic, styrenic or vinyl glycomonomers. The polymers have attracted widespread attention for various biological and biomedical uses with expectation that the polymers might mimic analogous polysaccharides in terms of engendering a bioresponse.313
In that it can carried out in homogeneous aqueous media, at moderate to ambient temperature, with monomers carrying complex functional groups, RAFT polymerization is particularly well-adapted to the synthesis of glycopolymers. Ghadban and Albertin313 have comprehensively reviewed the synthesis of glycopolymers by various RDRP, including RAFT polymerization (see also ref. 314). RAFT and ATRP are clearly the dominant processes for forming such polymers.313,314 The immobilization of glycopolymers on surfaces by various processes, including SI-RAFT, has also been recently reviewed.315
Polymers based on betaine or zwitterionic monomers
Polymers based on carboxybetaine (e.g., CBMMA,240,335,336 CBEMAm337), sulfobetaine (e.g., SBPMAm338–340 SBPMA341–343), and phosphobetaine monomers (e.g., MPC344–347) monomers (for additional examples see ref. 339 and 348) often display UCSTs and can show salt ionic strength-responsive behaviour. These polymers are also used in biosensors for their ultra-low fouling characteristics. The betaine monomers can be polymerized directly by RAFT polymerization (Table 14).349 However, these polymers have also been made by post-polymerization modification of RAFT-synthesized polymers.
Table 14 RAFT-synthesis of polymers based on betaine monomers
Betaine monomera |
Polymerizationb |
Monomer abbreviation are provided in Fig. 2.
Polymerizations shown as: monomer(s) (RAFT agent)ref.
Hyperbranched polymer.
|
CBMMA |
CBMMA-b-BMA (6)335 |
CBMMA-b-HPMA (19)240 |
CBMMA-b-EHMA (6)336 |
CBMMA-co-HEMA-co-MBA (28)c 350 |
CBMMA-co-DMAEMA (24)256 |
CBEMAm |
HPMAm (6)337 |
HPMAm-b-CBEMAm (6)337 |
SBPMAm |
NIPAm-b-SBPMAm-b-AMBA (22)340 |
SBPMAm (6)339 |
SBPMAm-b-DMAm (6)339 |
DMAm-b-SBPMAm (12)339 |
NIPAm-b-SBPMAm (13)338 |
|
61 X = CH3, Y = O, n = 2, m = 3, 4 (2)343 |
61 X = H, Y = O, n = 2, m = 4 (34)343 |
MPC |
BA-b-MPC (33)344 |
MPC-b-DEAM (6)346 |
MPC-b-SBEMA (6)346 |
MPC-b-TMAPMAm (6)347 |
MPC-b-AMPS (6)347 |
A library of sulfobetaine polymers with general structure 61 X = H, CH3, Y = O, NH, n = 2, m = 3, 4 was prepared using three different synthetic strategies.343 The (meth)acryates (Y = O) were prepared by direct RAFT polymerization of the sulfobetaine monomers or by modification of P(DMAEMA) with the appropriate sulfone (Scheme 7).
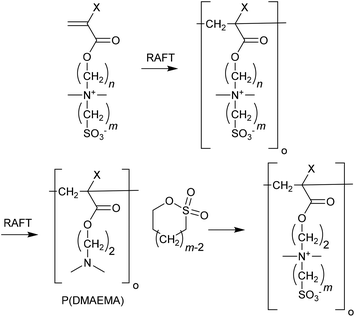 |
| Scheme 7 Synthetic routes to sulfobetaine (meth)acrylates. | |
The (meth)acrylamides were prepared by active ester chemistry (Scheme 8). UCST behaviour was found to depend strongly on structure.343
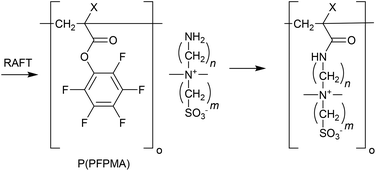 |
| Scheme 8 Synthesis of sulfobetaine methacrylamides by active ester chemistry from P(PFPMA). | |
Polymer ionic liquids
The term ionic liquid monomer is often used to embrace monomers comprising permanent ionic functionality whether or not they meet the more generally accepted definition that they exist as a liquid at some temperature below 100 °C. The term polymer ionic liquid is used to refer to polymers that comprise units of an ionic liquid monomer.351,352 The polymers themselves may not be ionic liquids.
Polymer ionic liquids can be prepared directly by RAFT polymerization of “so-called” ionic liquid monomers (62–65, Table 15). Polymer ionic liquids have also been prepared by introduction of the liquid crystal functionality post-polymerization by quaternization of a halo-functional polymer (e.g., P(CMS)353,354) or by thiol-ene chemistry.355
Table 15 RAFT-synthesis of polymer ionic liquids
Ionic liquid monomer |
RAFT agent |
Comment |
Ref. |
MacroRAFT agent derived from 37.
|
|
24
|
X− = BF4− |
233
|
|
Polymer shows UCST behaviour in methanol/water |
|
21
|
X− = Cl− |
357
|
|
Nanogels formed by crosslinking polymerization |
|
|
(37)a |
X− = BF4−, R = C2H5 |
358
|
|
Double hydrophilic block from PNIPAm or PDMAm macroRAFT agents |
|
38
|
X− = Br−, NTf2−, R = C2H5 |
359
|
|
Polymer is catalyst for Diels-Alder reaction |
|
38
|
X− = Br−, R = C4H9 |
360
|
|
NIPAM copolymer shows UCST in CH3CN |
|
37, 38 |
X− = Br−, R = alkyl |
356
|
|
6
|
R = CH3, C2H5 Polymer is salt responsive |
361
|
22
|
R = CH3, CH2Ph Polymerization induced self-assembly in forming block copolymer |
362
|
1
|
R = C4H9 |
363
|
|
Block copolymer with N-(thiazol-2-yl)methacrylamide. Magnetic properties of derived metal complexes |
|
|
21
|
R = Ph, C4H9 |
357
|
|
Nanogels formed by crosslinking polymerization |
|
Most ionic liquid monomers are (meth)acrylate- or styrene-based and dithiobenzoates or trithiocarbonates used to mediate their RAFT polymerization (Table 15). Xanthate RAFT agents (63) were used to control polymerization N-vinyl imidazolium salts, which are presumed to be LAMs (or IAM).356
The polymer ionic liquids display a range of stimuli-responsive behaviours dependant on the particular structures and conditions (e.g., Table 15).
Self-healing polymers
Various groups have described self-healing polymers or stress relieving polymers. These polymers are networks that comprise a fraction of dynamic bonds, which may take the form of non-covalent supramolecular interactions or dynamic covalent bonds. These bonds allow the polymers able adapt their structures in response to external stimuli which may take the form of heat, UV irradiation or mechanical stress.
In some case the dynamic bonds involve a trithiocarbonate group and the dynamic process is UV or thermally stimulated RAFT.221,222,364–367 In other cases RAFT is simply a tool to construct functional copolymers and the dynamic process is acylhydrazone formation,368–370 imine formation,371–373 Diels Alder reaction,374 boronic acid ester formation,375,376 metal complex formation377 or (multiple) hydrogen bond formation.378
Metallopolymers
Many have studied the incorporation of metal complexes into polymers to provide materials that combine the catalytic, magnetic, and/or electronic properties of metal complexes with the desirable mechanical and processing properties of the host polymers.379–381 This section relates to RAFT polymerization of monomers that incorporate a metal complex (Table 16) or possess metal chelating group (Table 17) as pendant functionality. The section is, in part, an update to that embraced in the review of optoelectronic polymers published in 2011.283 Metallopolymers formed by RDRP methods, including RAFT, and other forms of living or controlled polymerization have also been reviewed by Whittell et al. in 2011379 and by Hardy et al. in 2014.380
Table 16 Metallopolymers
Metallomonomer |
RAFT agent/comment |
Ref. |
|
24, 32 |
383–385
|
Loss of control for homopolymer, low dispersity for copolymer with MA and copolymer blocks |
|
|
1
|
386, 387
|
Low dispersity homopolymer, block copolymers |
|
|
1
|
386, 387
|
Low dispersity homopolymer, block copolymers |
|
|
1
|
386–388
|
Low dispersity homopolymer, block copolymers |
|
|
9
|
387
|
Block copolymer with macroRAFT formed from cobaltocenium monomer (67) |
|
|
1
|
389
|
Low dispersity homopolymer for conversion <50% |
|
|
2, 25 |
390, 391
|
MacroRAFT used in block synthesis |
|
Self-assembly of PEO block |
|
|
17
|
392
|
Triblock copolymer prepared to make responsive vesicles |
|
|
2
|
298
|
Light harvesting copolymer |
|
Table 17 Metal chelating polymers
Metal chelating monomer |
Polymerizationa/comment |
Polymerizations shown as: monomer(s) (RAFT agent)ref.
|
|
68-co-BMA (2)393 |
68-co-LMA (2)393 |
Self-healing network formed by cross-linking copolymer with Zn2+ |
|
69-co-MMA (2)377 |
69-co-BMA (2)377 |
69-co-LMA (2)377 |
Self-healing network formed by cross-linking copolymer with Cd2+ |
|
(66-co-MMA)-b-70(32)385 |
Precursor to gold-containing block copolymer |
|
71-co-HPMAm (149)394 |
Used in forming platinum drug |
RAFT polymerization making use of metal containing RAFT agents139 or metallopolymer macroRAFT agents382 have also been described (Table 18, for additional examples see previous review283).
Table 18 Metallo-RAFT agents
RAFT agent |
Monomera/ref. |
Monomer polymerized.
|
|
OEGMA395 |
|
DEAm382 |
Electroactive polymers
Organic semiconductors.
The synthesis of polymers with an organic semiconductor moiety either as a block or as pendant group to the backbone. We also consider polymers with attached dyes for use in light-harvesting, photochromic and some imaging applications under Light responsive polymers above.
Polymers containing thiophene and other conjugated rings such as part of the backbone are not directly available by radical polymerization except in special circumstances. For example, RAFT Ring-opening polymerization provides a route to a rod-polymer with in-chain acene (anthracene) functionality (Scheme 9).396 It is, however, possible to efficiently convert preformed conjugated polymers to macroRAFT agents.
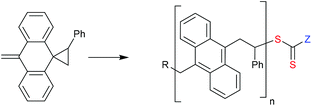 |
| Scheme 9 Example of RAFT ring-opening polymerization (R = PhCH2, Z = Ph or N-pyrrole). | |
Poly(3-hexylthiophene) (P3HT) macroRAFT agents are summarized in Table 19. MacroRAFT agents 72–74 possess a P3HT moiety as the Z group. A potential disadvantage is that the P3HT can be readily cleaved from the RAFT-synthesized polymer. On the other hand, macroRAFT agents 75–80 possess P3HT as the R group and thus possess a relatively stable block linkage allowing the RAFT ZCS2 to be removed or transformed keeping the block structure intact. P3HT may also be introduced post-RAFT polymerization as a block397 or a pendant functionality.398
Table 19 Poly(3-hexylthiophene) (P3HT) macroRAFT agents
P3HT macroRAFT agent |
Monomera/ref. |
Monomer polymerized.
Use of macroRAFT agent in RAFT polymerization not reported.
|
|
St407,408 |
4VP409 |
|
Copolymer410 |
|
MMA411 |
|
St412 |
|
St413 |
|
414 |
|
St413 |
|
415 |
|
2VP416 |
Earlier, pre-2011, studies on grafting from/to electroactive graphitic nanoparticles (graphene, carbon nanotubes) and fullerene are documented in our review.283 There are also more recent reviews that embrace this topic.399 Fullerene containing polymers have been prepared by RAFT polymerization and various strategies have been used in incorporate the fullerene functionality. Most recent studies involve polymer modification post-RAFT polymerization to introduce the fullerene moiety as a pendant group,400–404 as an end group405 or as some form of supramolecular assembly (Table 20).406
Table 20 Monomers for organic semiconductors
Monomer |
Polymerizationa/comment |
Polymerizations shown as: monomer(s) (RAFT agent)ref.
|
|
81 (5)417,418 |
Precursor to phthalocyanine dye |
|
82 (1)419 |
Precursor to transparent conducting polymer |
|
83-co-St (36)402 |
Precursor to fullerene functional polymer |
Modification of RAFT-synthesized polymers
The installation of functionality into appropriately reactive, RAFT-synthesized precursor polymers provides a versatile method for forming stimuli-responsive polymers. The procedure then requires the preparation of a polymer containing monomer units suitable for efficient modification, to introduce the groups of interest. An advantage of this methodology is that libraries of polymers are then available that differ only in the type of introduced functionality; all have the same backbone structure. The application of this strategy in the context of thermoresponsive polymers has been reviewed by Roth.420 A second advantage is the provision of polymers with functionality that might interfere with radical polymerization or with the RAFT process if a more direct grafting through route was employed. One of the more important applications of this technology is in the synthesis of polymer-drug conjugates. However, there are many other applications.
It is possible to use conventional chemistry for polymer modification either to directly introduce a desired functionalities. For example,
• esterification of polymers with hydroxyl functionality, e.g., P(VA) and VA copolymers (P(VA) from RAFT-synthesized P(VAc))230 or HEMA copolymers,421 making use of N,N-dicyclohexyl carbodiimide (DCC) coupling.
• halogen substitution. There are many examples of modification of RAFT-synthesized halogen-functional polymers, e.g., of P(CMS) and post-functionalisation by quaternization with a tertiary amine422 or a phosphine,79,423 by reaction with a phosphonate,424 potassium phthalimide,401 use in a Williamson ether synthesis,323 or conversion to an azide (Scheme 10);297 of poly[(4-bromophenyl)(vinyl)sulphane] [P(BPVS)] by Buchwald–Hartwig amination425,426 or Suzuki coupling;425,426 of poly(bromoethyl acrylate) – a variety of processes have been described by Barlow et al.427
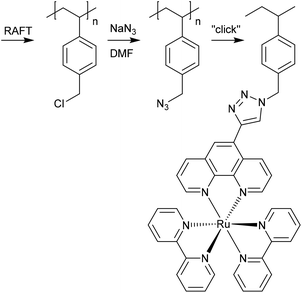 |
| Scheme 10 Synthesis of metallopolymer from RAFT-synthesized P(CMS) by click chemistry. | |
However, a common approach is to introduce appropriate groups for subsequent transformation by what are often called “click” processes, though the quality of the “click” reactions is in some cases questionable.428 In this context, we consider the RAFT polymerization of monomers for azide–alkyne 1,3-dipolar (Huisgen) cycloaddition, monomers containing active ester groups, monomers with latent amino- or thiol-functionality, and monomers with isocyanate or isothiocyanate groups.
Monomers for azide–alkyne dipolar cycloaddition.
Many papers have been published concerning the combination of RAFT and azide–alkyne 1,3-dipolar cycloaddition.
Some alkyne-functional monomers and the polymers formed with them by RAFT polymerization are listed in Table 21. In most cases monomers with protected alkyne functionality have been used since the alkyne group is susceptible to reaction with radicals. It was observed that homopolymerization of 85 gave an insoluble (crosslinked) product.429 However, no issues were reported in the case of the copolymerizations reported in Table 21.
Table 21 Alkyne-functional monomers used in RAFT (co)polymerization
Monomer |
Polymerizationa |
For the case of block copolymer the monomers are listed in the sequence they were used. Polymerizations shown as: monomer(s) (RAFT agent)ref.
Side-reactions were observed.
|
|
84-b-PEGMA (1)435 |
84-co-MMA-b-St (2)436 |
84 (2)429 |
84-co-MMA (4)437 |
84-co-MMA (6)438 |
84-co-PEGMA (2)439 |
84-b-PEGMA (2)439 |
84-b-PEGMA (6)440 |
Methacrylate multi-block (8)441 |
Methacrylate multi-block (6)442 |
|
PEGMA-b-85 (6)443 |
[85 (2)429]b |
|
86-co-EGDMA (27)444 |
Acrylate multi-block (33)445 |
Acrylate multi-block (24)446 |
|
87-co-PEGA (24)447 |
87-co-AA (31)448–450 |
87-co-NAS-co-NIPAM (31)451 |
|
88-b-St (30)452,453 |
PTHPA-b-88-co-St (9)454 |
|
89-co-4VP-b-St (24)436 |
St-b-89455 |
89 (30)456 |
Azides also may undergo side reactions under polymerization conditions. In particular, azides are known to undergo 1,3-dipolar cycloaddition with electron deficient monomers, such as methacrylates.430 However, these issues and appear to be largely mitigated by conducting polymerization at near ambient temperature or below.431,432 Azide functional monomers that have been exploited in RAFT polymerization are listed in Table 22. Azide functionality is often incorporated post-RAFT polymerization,297,433,434e.g., poly(4-vinylbenzyl azide) was prepared by reaction of P(CMS) with sodium azide in DMF in high yield (Scheme 10).297
Table 22 Azide functional monomers used in RAFT (co)polymerization
Monomer |
Polymerizationa,b |
Polymerizations shown as: monomer(s) (RAFT agent)ref.
The suffix S before the RAFT agent indicates a surface initiated RAFT polymerization.
|
|
90 (S28)457,458 |
90 (S6)459,460 |
90-co-MMA (6)404 |
|
91 (17)461 |
91-co-St (24)325 |
91-co-54 (24)325 |
|
92-b-MMA (10)431 |
|
93-co-MA (25)462 |
93-co-MMA (2)432 |
93-co-MA (41)432,462 |
93-co-St (41)432 |
|
DMA-b-(94-co-NIPAm)(6)463 |
Monomers with “ene” or diene functionality.
The Diels–Alder or hetero-Diels Alder reaction can be an efficient process for polymer modification or assembly. Ene-functionality is also used as a thiol-reactive functionality.
Even though it seems possible to introduce certain diene functionality (Table 23) by direct RAFT polymerization of the appropriate monomers, the same diene groups can also be produced by post-polymerization modification (e.g., 2,4-pentadieneyl,464 furfuryl465).
Table 23 Monomers with diene functionality used in RAFT (co)polymerization
Monomer |
Polymerizationa |
Polymerizations shown as: monomer(s) (RAFT agent)ref.
|
|
95 (17)468 |
95-b-PEGMA (17)469 |
95-b-BMA (17)374 |
OEGMA-b-95 (18)470 |
|
95-co-St (21)471 |
Allyl functionality reacts only very slowly under conditions required to polymerize methacrylates or styrenes and can be incorporated directly by copolymerization of the appropriate monomers (e.g., AMA) to give a low dispersity polymer (Table 24). With more reactive propagating species, e.g., in AN/AMA copolymerization, it is clear that the allyl functionality is not unreactive such that hyperbranched polymers are formed even a modest monomer conversions.466
Table 24 Monomers with ene or protected ene functionality used in RAFT (co)polymerization
Monomer |
Polymerizationa |
Polymerizations shown as: monomer(s) (RAFT agent)ref.
Dopamine-Functional RAFT agent derived from 23.476
Bis-RAFT agent derived from bis(hydroxyethyloxypropyl)polydimethylsiloxane and 24.474
|
|
97-co-PEGA (23b)472 |
|
98-co-St (24)473 |
98-co-107 (24)473 |
|
DMAm-b-AMA (24c)474 |
AMA SIP with xanthate475 |
Maleimide “ene”-functionality always needs protection during RAFT polymerization, which can be achieved by forming a Diels–Alder adduct, (Table 24). The maleimide functionality is regenerated by heating the product at >110 °C. However, in unpublished work, we have found that the rate of retro Diels–Alder reaction for furan-maleimide adducts may also be significant at commonly used polymerization temperatures (e.g., 60 °C) and is of particular concern when longer polymerization times are used (e.g., 24 h).467
Monomers with latent amino- or thiol-functionality.
Monomers containing primary or secondary amino or thiol-groups are not easily amenable to RAFT polymerization. However, this functionality can be present in protected form, e.g., the pyridyldisulfide in 110–112 and the thioacetyl group of 113 are protected thiol-groups, and the tBOC-group in monomers 114–117 and the phthalimido group of 118 are protected primary amine-groups (Table 26).
Table 26 Monomers with protected thiol, hydrazide or amino functionality used in RAFT (co)polymerization
Simple protonation has been shown to provide protection for primary amino-functional monomers. Thus (co)polymerizations of AEMA,502–507 AEAm,508 AEMAm509 and APMAm510–513 have been successfully performed to provide low dispersity polymers with retention of the RAFT end groups. Acetate buffer pH 5 appears to be a suitable polymerization medium.506,513
Protonation (with glacial acetic acid solvent) also allows polymerization of other difficult monomers (e.g., 4-vinylimidazole).514
The RAFT-synthesis of end-functional polymers and the responsiveness of RAFT-functionality to external stimuli
One of the important features of RAFT polymerization is that the end-groups (R and ZCS2) of the initial RAFT agent are retained in the product macroRAFT agent. The overall process simply inserts a polymer chain (Pn) between the R and Z–C(
S)S groups of the initial RAFT agent (Schemes 1 and 2). In a well-designed reaction the fraction of chains formed by initiation and termination should be negligibly small. The end group fidelity, which equates to the fraction of living chains (L) can be estimated using the relationships given in the section Initiators in RAFT polymerization above. Thus RAFT polymerization is a way of preparing end-functional polymers. The functionality can be present in the R and ZCS2 or can be formed by transformation of these groups post-RAFT polymerization. In this context we discuss processes for transforming the RAFT end group and the synthesis of polymers with functional RAFT agents. Many of examples relate to the “grafting to” approach for synthesizing functional polymers where a RAFT-synthesized functional polymer is covalently attached to a substrate.
In this section we also consider the chemistry of the thiocarbonylthio RAFT agent functionality, not simply as a RAFT agent, but rather in terms of its responsiveness to pH, light and other stimuli.
RAFT end-group transformation chemistry
A discussion of RAFT end-group transformation chemistry is of major importance to any consideration of the RAFT-synthesis of stimuli-responsive polymers. End group transformation provides can provide a method of tuning the properties of stimuli-responsive polymers. In other cases, the RAFT end group will need to be removed from the polymers to preclude interference with a desired response. For example, it is known the self-assembly behaviour of hydrophilic or amphiphilic polymers can be influenced by the presence of hydrophobic RAFT agent-derived end-groups,180,532,533 dithiobenzoate groups quench fluorescence and should be removed to avoid interference with optoelectronic properties.
There are a number of reviews that relate directly to RAFT end group transformation.534–539 A summary of the procedures available based on our 2011 review536 is provided in Fig. 6.
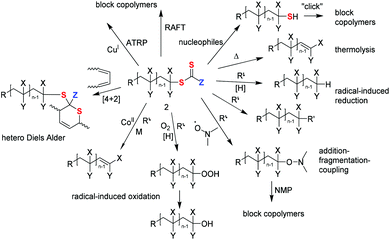 |
| Fig. 6 Processes for RAFT end-group transformation (scheme reproduced with minor changes from ref. 536 © 2011 Society of Chemical Industry). R′˙ = radical, [H] = hydrogen atom donor, M = monomer. | |
The RAFT thiocarbonylthio group can be considered as a protected thiol group. Many of the methods for RAFT end-group transformation involve elaboration of a thiol that can be formed from the thiocarbonylthio group by reduction or through reaction with nucleophiles (Fig. 7).536,540
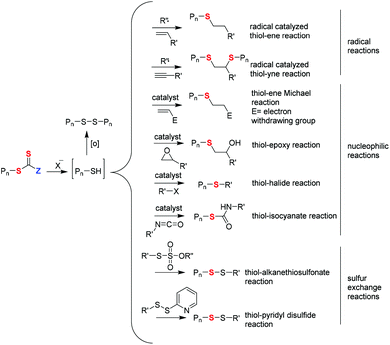 |
| Fig. 7 Reactions of RAFT end-group with nucleophiles with trapping of the thiol end-group formed (scheme reproduced with minor changes from ref. 536 © 2011 Society of Chemical Industry). | |
There are now many examples of forming thiol end groups from RAFT end groups and forming functionality by radical-induced thiol–ene, thiol–yne or thio–Michael reaction either as a separate reaction step or in a one-pot process.541–549 Other efficient thiol transformation processes include the thiol–epoxy reaction,550 thiol–halide reaction,551 thiol–isocyanate reaction,552 thiol–alkanethiosulfonate reaction553 and thiol–disufide reaction.554
Often processes that provide for complete desulfurization of the polymer are preferred. These include thermolysis,555–558 radical addition–fragmentation coupling558,559 and radical addition fragmentation reduction.180
A particular challenge, which is of some relevance in the context of this review, is in situ end-group removal from polymers in dispersed media. End group oxidation by ozonolysis has been put forward as a possible solution.560
Switchable (pH responsive) RAFT agents
As mentioned above, with appropriate selection of ‘R’, there are RAFT agents that provide control over polymerization of both LAMs and MAMs. However, the level control is less than that required to give very low dispersities and facile polymerization with the full range of monomers.
Switchable N-methyl-N-(4-pyridinyl)dithiocarbamate RAFT agents were introduced mainly to provide a viable synthesis of low dispersity polyMAM-block-polyLAM.43,44,122 These RAFT agents can be switched by use of an external stimulus to give very good control over polymerization of both MAMs and LAMs.44,122 Although a variety of switches may be envisioned most current examples use a pH switch. The RAFT agents are compatible with aqueous media.51 Developments in this area have now been reviewed.561 Examples of their application are as follows.
MAMs: St,43,44,122 MMA,44,122 MA,562 BA,44,122 DMA51
LAMs: VAc,43,44,122,562 NVP44,122,563
IAM: NVC18,44,122,562
It should be noted that macroRAFT agents formed with LAMs and IAM are extremely acid sensitive and it is important to ensure no acid remains when switching to polymerizae a LAM or IAM.
Initial studies focused on the N-methyl-N-(4-pyridinyl) dithiocarbamates.44,122 The N-aryl-N-(4-pyridinyl) dithiocarbamates are more active with more activated monomers (MAMs) in protonated (switched) form and more active with less activated monomers (LAMS) in non-protonated (unswitched) form.561,562 Their activity can be tuned through choice of the aryl substituent.562
Redox-responsive RAFT agents
Thiocarbonylthio-compounds have found use as initiators in atom transfer radical polymerization (ATRP). The first reports involved the use of N,N-dialkyl dithiocarbamate derivatives as ATRP initiators.564–567 As mentioned above, these reagents do not provide effective RAFT control over the polymerization of more activated monomers (MAMs) so the control mechanism is most likely through an ATRP mechanism with the thiocarbonylthio-compound behaving as a pseudo-halide initiator.
More recently, RAFT agents such as N,N-diaryldithiocarbamates,568,569 1-pyrrolecarbodithioates570 and dithioesters (1-dithionaphthalates571,572 and dithiobenzoates573,574) have been used in combination with ATRP activators. Under the conditions reported, in that compounds are very effective RAFT agents, the processes should be considered as RAFT polymerizations with ATRA initiation (Scheme 11). Both ISET and OSET mechanisms have been proposed for the ATRA process involving thiocarbonylthio-compounds and Cu(0). It is most likley that all copper mediated ATRA involve a SARA-ATRP (ISET) mechanism.
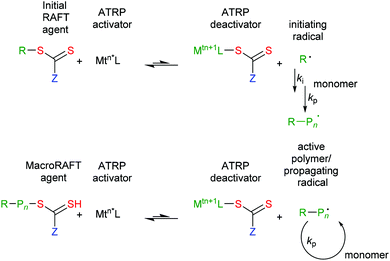 |
| Scheme 11 Possible ATRA initiation mechanism for RAFT polymerization. | |
Light-responsive RAFT agents
There has been recent marked interest in photo-controlled RDRP and, in particular, in polymerizations that can be induced with visible light. Such polymerizations allow for both spatial and temporal control of polymer synthesis.575,576
Photo-RAFT may involve may involve RAFT polymerization with a photoinitiator or photo-redox initiator with generation of radicals only from the added initiator.577 It may involve direct photodissociation of a RAFT agent (without and added photoinitiator or sensitizer). This form of RAFT polymerization should be compared the so-called iniferter method for RDRP described by Otsu and coworkers. As originally described, the process involved polymerization initiated by reversible photo-dissociation of what we now know to be a poor RAFT agent, usually an N,N-dialkyldithiocarbamate.578–580 The method has been reviewed by Otsu and Matsumoto,581 with respect to the literature through 2000, and more recently by Atilla Tasdelen and Yagci.582 When instead performed with a good RAFT agent (e.g., a dithiobenzoate or trithiocarbonate)57,583,584 the dominant mechanism for conveying living characteristics (moleculer weight control) has been shown to be RAFT.57 Recently, Qiao and coworkers60,61,585 have shown that very good control in acrylate polymerization can be achieved with visible (blue light) light irradiation. Xu et al.586 (batch) and Gardiner et al.587 (flow) have investigated photo-initiated RAFT of a wider range of monomers under visible light irradiation. Poly et al. have exploited xanthate as macroRAFT agents and macro-initiators.588 Irradiation with lower wavelength light provides for faster polymerization but also more by-products. Irrespective of irradiation wavelength, there is need to pay attention to the rate of radical generation to avoid high radical concentrations and excessive termination.
Another important method for photo-RAFT polymerization is PET-RAFT. This may involve (a) photosensitised reversible dissociation of the RAFT agent or (b), a photo-electron transfer process with the RAFT agent or photo-ATRP-like initiation. In all cases, when a good RAFT agent is used, polymerization is most likely controlled by RAFT equilibria. Some monomers/catalysts/RAFT agents for which good control was reported include (see Fig. 2 and Table 25 for monomer abbreviations):
Organometallics
(MMA, HPMAm)/fac-[Ir(ppy)3]/6,65
MA/fac-[Ir(ppy)3]/(27 or 33)65
(OEGA, DMAm, NIPAm, St, Ip)/fac-[Ir(ppy)3]/2765
MMA/Ru(bpy)3Cl2/6589
(MA, St, DMAm)/Ru(bpy)3Cl2/27589
(MMA, HPMAm)/ZnTPP/667
(MA, OEGA, DMAEA, DMAm, NIPAm, St)/ZnTPP/2767
(MMA, DMAEMA, GMA, HPMAm)/chlorophyll/6590
(MA, PFPA, NIPAm)/chlorophyll/27590
Organic dyes
MMA/(Fluorescein, Eosin Y or Rhodamine 6G)/666
(HEMA, DMAEMA, MAA, GMA, HPMAm)/(Eosin Y)/666
MMA/pheophorbide/669
NIPAm/curcumin/33.591
Blocks, multi-blocks, stars and grafts have also been reported.65,66,69,589 The catalyst choice influences the irradiation wavelength and what RAFT agent or macroRAFT agents can be activated.
Electrocyclic reactions of thiocarbonylthio compounds
Certain RAFT agents undergo reversible electrocyclic reactions with dienes (hetero-Diels Alder reaction) or diazo compounds (1,3-dipolar cycloaddition).
Hetero-Diels Alder reaction of thiocarbonylthio compounds.
RAFT agents and macroRAFT agents with electron withdrawing ‘Z’ groups have been shown to undergo a hetero-Diels Alder reactions with suitable dienes (Scheme 12).592–596 The process has been developed as a route to block copolymers,595,597–601 graft, star and network polymers594,602,603 and modified surfaces.592,604,605 The method has precedent in synthetic organic chemistry.606 Suitable electron-withdrawing ‘Z’ groups include 2-pyridyl, phosphonate or phenylsulfonyl groups. The reaction may be catalyzed by a Bronsted or Lewis acid, e.g., trifluoroacetic acid or zinc chloride, respectively. However, for reaction in aqueous solution no catalyst is necessary.598 The reaction is thermally reversible600–602,607 prompting a proposal that it might be used to provide a thermally stimulated colour switch600,607 or be applied in reversible block copolymer608 or network formation.602
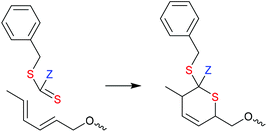 |
| Scheme 12 The thiocarbonyl hetero-Diels Alder process. | |
1,3-Dipolar cycloaddition of thiocarbonylthio compounds.
Diazomethane undergoes a facile 1,3-dipolar cycloaddition with dithiobenzoate RAFT agents and with dithiobenzoate end-groups of polymers formed by RAFT polymerization.609 The process does not require a catalyst. For example, 2-cyanoprop-2-yl dithiobenzoate (2), on treatment with diazomethane at ambient temperature (22 °C), provided stereoisomeric 1,3-dithiolanes in near quantitative (>95%) yield.
The process was discovered when attempting to methylate RAFT-synthesized P(MAA) with diazomethane to facilitate characterization.609 A low molar mass RAFT-synthesized P(MMA) with dithiobenzoate end-groups underwent similar reaction as indicated by immediate decolorization and a quantitative doubling of molar mass. Higher molar mass P(MMA) were also rapidly decolorized by diazomethane and provided a product with a bimodal molar mass distribution.
The process is only seen with more active RAFT agents. The trithiocarbonate group does not react with diazomethane under similar conditions. The proposed mechanism is shown in Scheme 13.
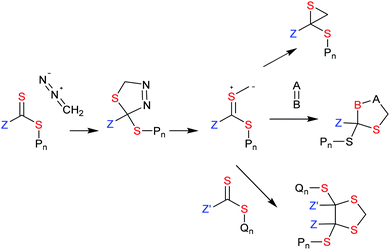 |
| Scheme 13 Thiocarbonyl 1,3-dipolar cycloaddition reaction. A = B is an unsaturated compound.609 | |
RAFT agents with reactive functionality
RAFT agents containing a variety of reactive functionalities have been designed to enable efficient polymer modification post- or sometimes during RAFT polymerization. These include RAFT agents with active ester functionality (to allow efficient reaction with primary amino groups), with alkyne or azide functionality (to enable modification by Huisgen cycloaddition), with latent amino or thiol functionality or with ene-functionality (usually for use in thiol–ene or ring opening methathesis chemistry). Ideally these functionalities should be inert to the conditions of RAFT polymerization, to reaction with radicals that are likely to be generated and to direct reaction with monomers or with the RAFT thiocarbonylthio group. However this is not always the case for all of the functionalities mentioned.
RAFT agents with active ester functionality.
The major use of RAFT agents containing active ester functionality is in the preparation of other functional RAFT agents rather than mediating RAFT polymerization directly. Nonetheless these RAFT agents can and have been used. Care must be taken in exclude reactive nucleophiles in the polymerization medium. Only examples of dithiobenzoate RAFT agents containing active ester functionality are shown in Table 29. Additional examples are provided in Table S1 (ESI†). The active ester functionalities for the examples shown in Table 29 are substantially more reactive that the thiocarbonylthio functionality towards, in particular, primary amines. Thus functionalization, conjugation and surface modification pre- or post-RAFT polymerization can be carried out without loss of the RAFT functionality.
Table 29 RAFT agents for active ester chemistry
RAFT agents with isocyanate or masked isocyanate functionality.
The carbonyl azide functionality of 144 and 145 undergoes a Curtius rearrangement to form isocyanate functionality during RAFT polymerization at 60 °C (Table 32). The process has been used to form polymers with isocyanate ends and for RAFT polymerization with concurrent isocyanate formation and reaction.654,655 A low molecular weight amine (benzylamine) or an alcohol (propargyl alcohol) were used as reaction partners for the isocyanate ends. Remarkably, no aminolysis of the RAFT thiocarbonylthio group was observed with benzylamine for the polymerization conditions used.
Table 32 RAFT agents with masked isocyanate functionality
RAFT agent |
Monomer(s) |
|
Methacrylates: MMA654 |
Acrylates: MA654 |
Acrylamides: NIPAm654 |
Styrenes: St654,656,657 |
|
Methacrylates: MMA655 |
Acrylates: BA655 PEGA655 |
Acrylamides: NAM655 |
Styrenes: PFS658 |
RAFT agents with ene or diene functionality.
RAFT agents with norbornene functionality have been prepared and successfully used in RAFT polymerization of methacrylates (MMA) and styrene to form low dispersity polymers (Table 33). Broader dispersities for longer reaction times were seen with MA which was attributed to reactivity of the norbornene in copolymerization. The norbornene functionality can be subsequently used in thiol–ene or ring-opening metathesis processes.
Table 33 RAFT agents with ene functionality
Ene-functionality that is reactive in radical polymerization must be protected. For example maleimide functionality is usually used in the form of a Diels–Alder adduct. When again deprotected, maleimide end-functional polymers are used in forming conjugates by thio–Michael reaction,659–661 or Diels Alder or other electrocyclic reaction.662,663 Maleimide-based structures have a long-established history in bioconjugate chemistry.664 The protected maleimide chain-end is an ene-functional polymer in its own right and a potential macromonomer in ring-opening metathesis polymerization.665
RAFT agents with latent primary amino or thiol-functionality.
While it possible to carry out reaction between substrates containing RAFT agent functionality (e.g., those also comprising active esters) and primary amines, in general, the thiocarbonylthio group and the primary amine are incompatible, and the primary amine functionality must generally be protected in some way. Common forms of protected amines are the phthalimido-group and the tBOC-group both of which have been used in RAFT agents (Table 34).
Table 34 RAFT agents with latent primary amino-functionality
Similar considerations apply in the case of other nucleophilic groups. Free thiol functionality also needs to be protected.
Conclusions
RAFT is an extremely versatile process for forming stimuli-responsive polymers. The stimuli-responsive elements of RAFT-synthesized polymers may originate from functionality present in the RAFT agent or macroRAFT agent, the monomers polymerized, or might be incorporated post-polymerization by transformation of a RAFT-synthesized polymer. Many functionalities can be introduced directly with the use of appropriately designed monomers or RAFT agents. In the rare case where this is not possible, there exist many possibilities for modification of RAFT-synthesized polymers post-polymerization.
The aim of this paper has been to illustrate how RAFT process can be applied in this context, by pointing out the features necessary to achieve the desired level of control and providing key references to the now vast literature on this application.
Acknowledgements
The author would like to thank Andrew Lowe and Peter Roth for encouraging him to persist in producing this survey.
Notes and references
- M. A. C. Stuart, W. T. S. Huck, J. Genzer, M. Muller, C. Ober, M. Stamm, G. B. Sukhorukov, I. Szleifer, V. V. Tsukruk, M. Urban, F. Winnik, S. Zauscher, I. Luzinov and S. Minko, Nat. Mater., 2010, 9, 101–113 CrossRef PubMed.
- I. Cobo, M. Li, B. S. Sumerlin and S. Perrier, Nat. Mater., 2015, 14, 143–159 CrossRef CAS PubMed.
- C. Boyer, V. Bulmus, T. P. Davis, V. Ladmiral, J. Liu and S. Perrier, Chem. Rev., 2009, 109, 5402–5436 CrossRef CAS PubMed.
- J. Chiefari, Y. K. Chong, F. Ercole, J. Krstina, J. Jeffery, T. P. T. Le, R. T. A. Mayadunne, G. F. Meijs, C. L. Moad, G. Moad, E. Rizzardo and S. H. Thang, Macromolecules, 1998, 31, 5559–5562 CrossRef CAS.
- A. D. Jenkins, R. I. Jones and G. Moad, Pure Appl. Chem., 2010, 82, 483–491 CAS.
- M. Szwarc, Nature, 1956, 178, 1168–1169 CrossRef CAS.
- M. Szwarc, J. Polym. Sci., Part A: Polym. Chem., 1998, 36, IX–XV CrossRef CAS.
-
Nitroxide Mediated Polymerization: From Fundamentals to Applications in Materials Science, ed. D. Gigmes, The Royal Society of Chemistry, Cambridge, UK, 2016 Search PubMed.
-
G. Moad and E. Rizzardo, in Nitroxide Mediated Polymerization: From Fundamentals to Applications in Materials, ed. D. Gigmes, The Royal Society of Chemistry, Cambridge, UK, 2016, pp. 1–44 Search PubMed.
-
N. V. Tsarevsky and K. Matyjaszewski, in Fundamentals of Controlled/Living Radical Polymerization, ed. N. V. Tsarevsky and B. S. Sumerlin, Royal Society of Chemistry, Cambridge, 2013, pp. 287–357 Search PubMed.
- K. Matyjaszewski, Macromolecules, 2012, 45, 4015–4039 CrossRef CAS.
- K. Matyjaszewski and N. V. Tsarevsky, J. Am. Chem. Soc., 2014, 136, 6513–6533 CrossRef CAS PubMed.
- M. Ouchi, T. Terashima and M. Sawamoto, Chem. Rev., 2009, 109, 4963–5050 CrossRef CAS PubMed.
- C. Boyer, N. A. Corrigan, K. Jung, D. Nguyen, T.-K. Nguyen, N. N. M. Adnan, S. Oliver, S. Shanmugam and J. Yeow, Chem. Rev., 2016, 116, 1803–1949 CrossRef CAS PubMed.
- A. Anastasaki, V. Nikolaou, G. Nurumbetov, P. Wilson, K. Kempe, J. F. Quinn, T. P. Davis, M. R. Whittaker and D. M. Haddleton, Chem. Rev., 2016, 116, 835–877 CrossRef CAS PubMed.
- D. J. Keddie, G. Moad, E. Rizzardo and S. H. Thang, Macromolecules, 2012, 45, 5321–5342 CrossRef CAS.
-
G. Moad, E. Rizzardo and H. Thang San, in Fundamentals of Controlled/Living Radical Polymerization, ed. N. V. Tsarevsky and B. S. Sumerlin, Royal Society of Chemistry, Cambridge, UK, 2013, pp. 205–249 Search PubMed.
- D. J. Keddie, C. Guerrero-Sanchez and G. Moad, Polym. Chem., 2013, 4, 3591–3601 RSC.
- J. Hu, M. R. Whittaker, J. F. Quinn and T. P. Davis, Macromolecules, 2016, 49, 2741–2749 CrossRef CAS.
- J.-M. Schumers, C.-A. Fustin, A. Can, R. Hoogenboom, U. S. Schubert and J.-F. Gohy, J. Polym. Sci., Part A: Polym. Chem., 2009, 47, 6504–6513 CrossRef CAS.
- G. Moad, Polym. Int., 2016 DOI:10.1002/pi.5173 , ahead of print.
- S. Harrisson, X. Liu, J.-N. Ollagnier, O. Coutelier, J.-D. Marty and M. Destarac, Polymer, 2014, 6, 1437–1488 CAS.
- A. N. Morin, C. Detrembleur, C. Jérôme, P. De Tullio, R. Poli and A. Debuigne, Macromolecules, 2013, 46, 4303–4312 CrossRef CAS.
- M. Guerre, S. M. W. Rahaman, B. Améduri, R. Poli and V. Ladmiral, Macromolecules, 2016, 49, 5386–5396 CrossRef CAS.
- K. Van Cauter, V. Van Speybroeck and M. Waroquier, ChemPhysChem, 2007, 8, 541–552 CrossRef CAS PubMed.
- C. M. R. Abreu, P. V. Mendonça, A. C. Serra, J. F. J. Coelho, A. V. Popov, G. Gryn'ova, M. L. Coote and T. Guliashvili, Macromolecules, 2012, 45, 2200–2208 CrossRef CAS.
- S. Sugihara, Y. Kawamoto and Y. Maeda, Macromolecules, 2016, 49, 1563–1574 CrossRef CAS.
- N. Ballard, S. Rusconi, E. Akhmatskaya, D. Sokolovski, J. C. de la Cal and J. M. Asua, Macromolecules, 2014, 47, 6580–6590 CrossRef CAS.
- G. Moad, E. Rizzardo and S. H. Thang, Aust. J. Chem., 2012, 65, 985–1076 CrossRef CAS.
- G. Moad, E. Rizzardo and S. H. Thang, Aust. J. Chem., 2009, 62, 1402–1472 CrossRef CAS.
- G. Moad, E. Rizzardo and S. H. Thang, Aust. J. Chem., 2006, 59, 669–692 CrossRef CAS.
- G. Moad, E. Rizzardo and S. H. Thang, Aust. J. Chem., 2005, 58, 379–410 CrossRef CAS.
- G. Moad, Macromol. Chem. Phys., 2014, 215, 9–26 CrossRef CAS.
- R. T. A. Mayadunne, E. Rizzardo, J. Chiefari, J. Krstina, G. Moad, A. Postma and S. H. Thang, Macromolecules, 2000, 33, 243–245 CrossRef CAS.
- E. Rizzardo, M. Chen, B. Chong, G. Moad, M. Skidmore and S. H. Thang, Macromol. Symp., 2007, 248, 104–116 CrossRef CAS.
- M. Destarac, W. Bzducha, D. Taton, I. Gauthier-Gillaizeau and S. Z. Zard, Macromol. Rapid Commun., 2002, 23, 1049–1054 CrossRef CAS.
- R. T. A. Mayadunne, E. Rizzardo, J. Chiefari, Y. K. Chong, G. Moad and S. H. Thang, Macromolecules, 1999, 32, 6977–6980 CrossRef CAS.
- M. Destarac, D. Charmot, X. Franck and S. Z. Zard, Macromol. Rapid Commun., 2000, 21, 1035–1039 CrossRef CAS.
- V. Malepu, C. D. Petruczok, T. Tran, T. Zhang, M. Thopasridharan and D. A. Shipp, ACS Symp. Ser., 2009, 1024, 37–47 CrossRef CAS.
- L. A. Dayter, K. A. Murphy and D. A. Shipp, Aust. J. Chem., 2013, 66, 1564–1569 CrossRef CAS.
- J. Gardiner, I. Martinez-Botella, J. Tsanaktsidis and G. Moad, Polym. Chem., 2016, 7, 481–492 RSC.
-
J. Gardiner and J. Tsanaktsidis, 2017, to be submitted.
- M. Benaglia, M. Chen, Y. K. Chong, G. Moad, E. Rizzardo and S. H. Thang, Macromolecules, 2009, 42, 9384–9386 CrossRef CAS.
- M. Benaglia, J. Chiefari, Y. K. Chong, G. Moad, E. Rizzardo and S. H. Thang, J. Am. Chem. Soc., 2009, 131, 6914–6915 CrossRef CAS PubMed.
- G. Moad, Y. K. Chong, E. Rizzardo, A. Postma and S. H. Thang, Polymer, 2005, 46, 8458–8468 CrossRef CAS.
- G. Moad, R. T. A. Mayadunne, E. Rizzardo, M. Skidmore and S. Thang, Macromol. Symp., 2003, 192, 1–12 CrossRef CAS.
-
G. Moad, in Controlled Radical Polymerization: Mechanisms, ed. K. Matyjaszewski, B. S. Sumerlin, N. V. Tsarevsky and J. Chiefari, American Chemical Society, Washington, DC, 2015, pp. 211–246 Search PubMed.
- C. L. McCormick and A. B. Lowe, Acc. Chem. Res., 2004, 37, 312–325 CrossRef CAS PubMed.
- A. B. Lowe and C. L. McCormick, Prog. Polym. Sci., 2007, 32, 283–351 CrossRef CAS.
- A. E. Smith, X. Xu and C. L. McCormick, Prog. Polym. Sci., 2010, 35, 45–93 CrossRef CAS.
- D. J. Keddie, C. Guerrero-Sanchez, G. Moad, E. Rizzardo and S. H. Thang, Macromolecules, 2011, 44, 6738–6745 CrossRef CAS.
- P. B. Zetterlund, Y. Kagawa and M. Okubo, Chem. Rev., 2008, 108, 3747–3794 CrossRef CAS PubMed.
- P. B. Zetterlund, S. C. Thickett, S. Perrier, E. Bourgeat-Lami and M. Lansalot, Chem. Rev., 2015, 115, 9745–9800 CrossRef CAS PubMed.
- G. Moad, Prog. Polym. Sci., 2016 Search PubMed , accepted.
-
G. Moad and D. H. Solomon, in The Chemistry of Radical Polymerization, Elsevier, Oxford, 2006, pp. 49–166 Search PubMed.
- J. Chiefari, R. T. A. Mayadunne, C. L. Moad, G. Moad, E. Rizzardo, A. Postma, M. A. Skidmore and S. H. Thang, Macromolecules, 2003, 36, 2273–2283 CrossRef CAS.
- J. F. Quinn, L. Barner, C. Barner-Kowollik, E. Rizzardo and T. P. Davis, Macromolecules, 2002, 35, 7620–7627 CrossRef CAS.
- M. Chen, M. Zhong and J. A. Johnson, Chem. Rev., 2016, 116, 10167–10211 CrossRef CAS PubMed.
- S. Dadashi-Silab, S. Doran and Y. Yagci, Chem. Rev., 2016, 116, 10212–10275 CrossRef CAS PubMed.
- T. G. McKenzie, Q. Fu, E. H. H. Wong, D. E. Dunstan and G. G. Qiao, Macromolecules, 2015, 48, 3864–3872 CrossRef CAS.
- T. G. McKenzie, L. P. d. M. Costa, Q. Fu, D. E. Dunstan and G. G. Qiao, Polym. Chem., 2016, 7, 4246–4253 RSC.
- J. Yeow, O. R. Sugita and C. Boyer, ACS Macro Lett., 2016, 5, 558–564 CrossRef CAS.
- Q. Zhang, Z. Zhang, W. Wang, J. Zhu, Z. Cheng, N. Zhou, W. Zhang and X. Zhu, J. Polym. Sci., Part A: Polym. Chem., 2012, 50, 1424–1433 CrossRef CAS.
- A. M. Elsen, R. Nicolaÿ and K. Matyjaszewski, Macromolecules, 2011, 44, 1752–1754 CrossRef CAS.
- J. Xu, K. Jung, A. Atme, S. Shanmugam and C. Boyer, J. Am. Chem. Soc., 2014, 136, 5508–5519 CrossRef CAS PubMed.
- J. Xu, S. Shanmugam, H. T. Duong and C. Boyer, Polym. Chem., 2015, 6, 5615–5624 RSC.
- S. Shanmugam, J. Xu and C. Boyer, J. Am. Chem. Soc., 2015, 137, 9174–9185 CrossRef CAS PubMed.
- S. Shanmugam and C. Boyer, J. Am. Chem. Soc., 2015, 137, 9988–9999 CrossRef CAS PubMed.
- J. Xu, S. Shanmugam, C. Fu, K.-F. Aguey-Zinsou and C. Boyer, J. Am. Chem. Soc., 2016, 138, 3094–3106 CrossRef CAS PubMed.
- N. Corrigan, J. Xu and C. Boyer, Macromolecules, 2016, 49, 3274–3285 CrossRef CAS.
-
A. D. Jenkins, P. Kratochvíl, R. F. T. Stepto and U. W. Suter, in Compendium of Polymer Terminology and Nomenclature (The Purple Book), ed. R. G. Jones, J. Kahovec, R. Stepto, E. S. Wilks, M. Hess, T. Kitayama and W. V. Metanomski, RSC Publishing, Cambridge, UK, 2009, pp. 3–21 Search PubMed.
- P. Escalé, S. R. S. Ting, A. Khoukh, L. Rubatat, M. Save, M. H. Stenzel and L. Billon, Macromolecules, 2011, 44, 5911–5919 CrossRef.
- Y. Guo, J. Zhang, P. Xie, X. Gao and Y. Luo, Polym. Chem., 2014, 5, 3363–3371 RSC.
- X. Zhang, F. Boisson, O. Colombani, C. Chassenieux and B. Charleux, Macromolecules, 2014, 47, 51–60 CrossRef CAS.
- S. Harrisson, F. Ercole and B. W. Muir, Polym. Chem., 2010, 1, 326–332 RSC.
- H. de Brouwer, M. A. J. Schellekens, B. Klumperman, M. J. Monteiro and A. L. German, J. Polym. Sci., Part A: Polym. Chem., 2000, 38, 3596–3603 CrossRef CAS.
- F. S. Du, M. Q. Zhu, H. Q. Guo, Z. C. Li, F. M. Li, M. Kamachi and A. Kajiwara, Macromolecules, 2002, 35, 6739–6741 CrossRef CAS.
- G. Moad, K. Dean, L. Edmond, N. Kukaleva, G. Li, R. T. A. Mayadunne, R. Pfaendner, A. Schneider, G. Simon and H. Wermter, Macromol. Symp., 2006, 233, 170–179 CrossRef CAS.
-
G. Moad, G. Li, R. Pfaendner, A. Postma, E. Rizzardo, S. Thang and H. Wermter, in Controlled/Living Radical Polymerization. From Synthesis to Materials, ed. K. Matyjaszewski, American Chemical Society, Washington, DC, 2006, pp. 514–532 Search PubMed.
- J.-F. Lutz, Acc. Chem. Res., 2013, 46, 2696–2705 CrossRef CAS PubMed.
-
B. Klumperman, in Sequence-Controlled Polymers: Synthesis, Self-Assembly, and Properties, ed. J.-F. Lutz, M. Ouchi, M. Sawamoto and T. Meyer, American Chemical Society, Washington DC, 2014, pp. 213–221 Search PubMed.
- Z. Zheng, X. Gao, Y. Luo and S. Zhu, Macromolecules, 2016, 49, 2179–2188 CrossRef CAS.
- C. Guerrero-Sanchez, S. Harrisson and D. J. Keddie, Macromol. Symp., 2013, 325–326, 38–46 CrossRef CAS.
-
G. Moad and D. H. Solomon, in The Chemistry of Radical Polymerization, Elsevier Science Ltd, Amsterdam, 2nd edn, 2006, pp. 333–412 Search PubMed.
- G. Moad, D. H. Solomon, T. H. Spurling and D. J. Vearing, Aust. J. Chem., 1985, 38, 1287–1292 CrossRef CAS.
- G. Moad, D. H. Solomon, T. H. Spurling and D. J. Vearing, Aust. J. Chem., 1986, 39, 1877–1881 CrossRef CAS.
- K. Kubo, A. Goto, K. Sato, Y. Kwak and T. Fukuda, Polymer, 2005, 46, 9762–9768 CrossRef CAS.
- C. J. Dürr, S. G. J. Emmerling, A. Kaiser, S. Brandau, A. K. T. Habicht, M. Klimpel and C. Barner-Kowollik, J. Polym. Sci., Part A: Polym. Chem., 2012, 50, 174–180 CrossRef.
- J. Moraes, I.-M. Simionca, H. Ketari and H.-A. Klok, Polym. Chem., 2015, 6, 3245–3251 RSC.
- P. Delduc, C. Tailhan and S. Z. Zard, J. Chem. Soc., Chem. Commun., 1988, 308–310 RSC.
- S. Houshyar, D. Keddie, G. Moad, R. Mulder, S. Saubern and J. Tsanaktsidis, Polym. Chem., 2012, 3, 1879–1889 RSC.
-
G. Moad, C. Guerrero-Sanchez, J. J. Haven, D. J. Keddie, A. Postma, E. Rizzardo and S. H. Thang, in Sequence-Controlled Polymers: Synthesis, Self-assembly and Properties, ed. J.-F. Lutz, M. Ouchi, M. Sawamoto and T. Meyer, American Chemical Society, Washington DC, 2014, pp. 133–147 Search PubMed.
- M. Chen, M. Haeussler, G. Moad and E. Rizzardo, Org. Biomol. Chem., 2011, 9, 6111–6119 Search PubMed.
- J. Vandenbergh, G. Reekmans, P. Adriaensens and T. Junkers, Chem. Sci., 2015, 6, 5753–5761 RSC.
- J. J. Haven, J. Vandenbergh, R. Kurita, J. Gruber and T. Junkers, Polym. Chem., 2015, 6, 5752–5765 RSC.
- J. Vandenbergh, G. Reekmans, P. Adriaensens and T. Junkers, Chem. Commun., 2013, 49, 10358–10360 RSC.
-
J. J. Haven, P. Leenaers and G. Moad, 2017, to be submitted.
- B. Quiclet-Sire, G. Revol and S. Z. Zard, Tetrahedron, 2010, 66, 6656–6666 CrossRef CAS.
- D. Braun and F. Hu, Prog. Polym. Sci., 2006, 31, 239–276 CrossRef CAS.
- X. S. Feng and C. Y. Pan, Macromolecules, 2002, 35, 4888–4893 CrossRef CAS.
- G. Y. Shi, X. Z. Tang and C. Y. Pan, J. Polym. Sci., Part A: Polym. Chem., 2008, 46, 2390–2401 CrossRef CAS.
- B. Sasso, M. Dobinson, P. Hodge and T. Wear, Macromolecules, 2010, 43, 7453–7464 CrossRef CAS.
- E. T. A. van den Dungen, J. Rinquest, N. O. Pretorius, J. M. McKenzie, J. B. McLeary, R. D. Sanderson and B. Klumperman, Aust. J. Chem., 2006, 59, 742–748 CrossRef CAS.
- S. M. Henry, A. J. Convertine, D. S. W. Benoit, A. S. Hoffman and P. S. Stayton, Bioconjugate Chem., 2009, 20, 1122–1128 CrossRef CAS PubMed.
- C. Zhou, S. Qian, A. Zhang, L. Xu, J. Zhu, Z. Cheng, E.-T. Kang, F. Yao and G. D. Fu, RSC Adv., 2014, 4, 8144–8156 RSC.
- N. Isahak, G. Gody, L. R. Malins, N. J. Mitchell, R. J. Payne and S. Perrier, Chem. Commun., 2016, 52, 12952–12955 RSC.
- J. Xu, C. Fu, S. Shanmugam, C. J. Hawker, G. Moad and C. Boyer, Angew. Chem., Int. Ed., 2017 DOI:10.1002/anie.201610223R201610221.
- N. ten Brummelhuis, Polym. Chem., 2015, 6, 654–667 RSC.
- Y. Kang, A. Lu, A. Ellington, M. C. Jewett and R. K. O'Reilly, ACS Macro Lett., 2013, 581–586 CrossRef CAS.
- E. G. L. Williams, S. Thang, R. J. Mulder, G. Moad, B. D. Fairbanks and E. Rizzardo, Polym. Chem., 2015, 6, 228–232 RSC.
- Y. Kang, A. Pitto-Barry, H. Willcock, W.-D. Quan, N. Kirby, A. M. Sanchez and R. K. O'Reilly, Polym. Chem., 2015, 6, 106–117 RSC.
- Y. K. Chong, T. P. T. Le, G. Moad, E. Rizzardo and S. H. Thang, Macromolecules, 1999, 32, 2071–2074 CrossRef CAS.
- D. J. Keddie, Chem. Soc. Rev., 2013, 2014, 496–505 Search PubMed.
- G. Gody, R. Barbey, M. Danial and S. Perrier, Polym. Chem., 2015, 6, 1502–1511 RSC.
- G. Gody, T. Maschmeyer, P. B. Zetterlund and S. Perrier, Nat. Commun., 2013, 4, 2505 Search PubMed.
- G. Gody, T. Maschmeyer, P. B. Zetterlund and S. Perrier, Macromolecules, 2014, 47, 3451–3460 CrossRef CAS.
- G. Gody, P. B. Zetterlund, S. Perrier and S. Harrisson, Nat. Commun., 2016, 7 CAS.
- I. Chaduc, W. Zhang, J. Rieger, M. Lansalot, F. D'Agosto and B. Charleux, Macromol. Rapid Commun., 2011, 32, 1270–1276 CrossRef CAS PubMed.
- C. Guerrero-Sanchez, L. O'Brien, C. Brackley, D. J. Keddie, S. Saubern and J. Chiefari, Polym. Chem., 2013, 4, 1857–1862 RSC.
- J. J. Haven, C. Guerrero-Sanchez, D. J. Keddie, G. Moad, S. H. Thang and U. S. Schubert, Polym. Chem., 2014, 5, 5236–5246 RSC.
- J. J. Haven, C. Guerrero-Sanchez, D. J. Keddie and G. Moad, Macromol. Rapid Commun., 2014, 35, 492–497 CrossRef CAS PubMed.
-
G. Moad, M. Benaglia, M. Chen, J. Chiefari, Y. Chong, K. D. Keddie, J. E. Rizzardo and S. H. Thang, in Non-Conventional Functional Block Copolymers, ed. P. Theato, A. F. M. Kilbinger and E. B. Coughlin, American Chemical Society, Columbus, Ohio, 2011, pp. 81–102 Search PubMed.
- G. Moad, J. Chiefari, J. Krstina, A. Postma, R. T. A. Mayadunne, E. Rizzardo and S. H. Thang, Polym. Int., 2000, 49, 993–1001 CrossRef CAS.
- A. Ilchev, R. Pfukwa, L. Hlalele, M. Smit and B. Klumperman, Polym. Chem., 2015, 6, 7945–7948 RSC.
- J. Krstina, C. L. Moad, G. Moad, E. Rizzardo, C. T. Berge and M. Fryd, Macromol. Symp., 1996, 111, 13–23 CrossRef CAS.
- J. Krstina, G. Moad, E. Rizzardo, C. L. Winzor, C. T. Berge and M. Fryd, Macromolecules, 1995, 28, 5381–5385 CrossRef CAS.
- N. G. Engelis, A. Anastasaki, G. Nurumbetov, N. P. Truong, V. Nikolaou, A. Shegiwal, M. R. Whittaker, T. P. Davis and D. M. Haddleton, Nat. Chem., 2016 DOI:10.1038/nchem.2634.
- J. M. Ren, T. G. McKenzie, Q. Fu, E. H. H. Wong, J. Xu, Z. An, S. Shanmugam, T. P. Davis, C. Boyer and G. G. Qiao, Chem. Rev., 2016, 116, 6743–6836 CrossRef CAS PubMed.
- R. T. A. Mayadunne, J. Jeffery, G. Moad and E. Rizzardo, Macromolecules, 2003, 36, 1505–1513 CrossRef CAS.
- R. T. A. Mayadunne, G. Moad and E. Rizzardo, Tetrahedron Lett., 2002, 43, 6811–6814 CrossRef CAS.
- R. Barbey, L. Lavanant, D. Paripovic, N. Schüwer, C. Sugnaux, S. Tugulu and H.-A. Klok, Chem. Rev., 2009, 109, 5437–5527 CrossRef CAS PubMed.
- D. Huebner, V. Koch, B. Ebeling, J. Mechau, J. E. Steinhoff and P. Vana, J. Polym. Sci., Part A: Polym. Chem., 2015, 53, 103–113 CrossRef CAS.
- M. Chen, K. P. Ghiggino, A. Launikonis, A. W. H. Mau, E. Rizzardo, W. H. F. Sasse, S. H. Thang and G. J. Wilson, J. Mater. Chem., 2003, 13, 2696–2700 RSC.
- M. Chen, K. R. Ghiggino, S. H. Thang and G. J. Wilson, Angew. Chem., Int. Ed., 2005, 44, 4368–4372 CrossRef CAS PubMed.
- M. Chen, K. P. Ghiggino, S. H. Thang and G. J. Wilson, Polym. Int., 2006, 55, 757–763 CrossRef CAS.
- M. Chen, K. P. Ghiggino, S. H. Thang and G. J. Wilson, J. Chin. Chem. Soc., 2006, 53, 79–83 CrossRef CAS.
- G. E. Southard, K. A. Van Houten, E. W. Ott Jr. and G. M. Murray, Anal. Chim. Acta, 2007, 581, 202–207 CrossRef CAS PubMed.
- G. E. Southard, K. A. Van Houten and G. M. Murray, Macromolecules, 2007, 40, 1395–1400 CrossRef CAS.
- W. Zheng, L.-J. Chen, G. Yang, B. Sun, X. Wang, B. Jiang, G.-Q. Yin, L. Zhang, X. Li, M. Liu, G. Chen and H.-B. Yang, J. Am. Chem. Soc., 2016, 138, 4927–4937 CrossRef CAS PubMed.
- L. Munuera and R. K. O'Reilly, Dalton Trans., 2010, 39, 388–391 RSC.
- Y. Tsujii, M. Ejaz, K. Sato, A. Goto and T. Fukuda, Macromolecules, 2001, 34, 8872–8878 CrossRef CAS.
- L. Barner, T. P. Davis, M. H. Stenzel and C. Barner-Kowollik, Macromol. Rapid Commun., 2007, 28, 539–559 CrossRef CAS.
- J. Poly, D. J. Wilson, M. Destarac and D. Taton, Macromol. Rapid Commun., 2008, 29, 1965–1972 CrossRef CAS.
- X. Li, M. Chen, B. Yang, S. Zhang, X. Jia and Z. Hu, RSC Adv., 2014, 4, 43278–43285 RSC.
- C. Zhang, Y. Zhou, Q. Liu, S. Li, S. B. Perrier and Y. Zhao, Macromolecules, 2011, 44, 2034–2049 CrossRef CAS.
- J. A. Alfurhood, P. R. Bachler and B. S. Sumerlin, Polym. Chem., 2016, 7, 3361–3369 RSC.
- S. Ghosh Roy and P. De, Polym. Chem., 2014, 5, 6365–6378 RSC.
- J. Schmitt, N. Blanchard and J. Poly, Polym. Chem., 2011, 2, 2231–2238 RSC.
- S. Pal, M. R. Hill and B. S. Sumerlin, Polym. Chem., 2015, 6, 7871–7880 RSC.
- J. T. Wilson, A. Postma, S. Keller, A. J. Convertine, G. Moad, E. Rizzardo, L. Meagher, J. Chiefari and P. S. Stayton, AAPS J., 2015, 17, 358–369 CrossRef CAS PubMed.
- N. Y. Ahn and M. Seo, RSC Adv., 2016, 6, 47715–47722 RSC.
- Z.-M. Wu, H. Liang, J. Lu and W.-L. Deng, J. Polym. Sci., Part A: Polym. Chem., 2010, 48, 3323–3330 CrossRef CAS.
-
D. H. Solomon, G. G. Qiao and S. Abrol, Process for microgel preparation, The University of Melbourne, WO9958588A1, 1999 Search PubMed.
-
C. T. Berge, M. Fryd, J. W. Johnson, G. Moad, E. Rizzardo, C. Scopazzi and S. H. Thang, Microgels and process for their preparation, Du Pont, CSIRO, WO2000002939A1, 2000 Search PubMed.
- X. Cao, C. Zhang, S. Wu and Z. An, Polym. Chem., 2014, 5, 4277–4284 RSC.
- H. T. Lord, J. F. Quinn, S. D. Angus, M. R. Whittaker, M. H. Stenzel and T. P. Davis, J. Mater. Chem., 2003, 13, 2819–2824 RSC.
- Q. Chen, X. Cao, Y. Xu and Z. An, Macromol. Rapid Commun., 2013, 34, 1507–1517 CrossRef CAS PubMed.
- Q. Chen, Y. Xu, X. Cao, L. Qin and Z. An, Polym. Chem., 2014, 5, 175–185 RSC.
- J. Ferreira, J. Syrett, M. Whittaker, D. Haddleton, T. P. Davis and C. Boyer, Polym. Chem., 2011, 2, 1671–1677 RSC.
- X. Shi, W. Zhou, Q. Qiu and Z. An, Chem. Commun., 2012, 48, 7389–7391 RSC.
- X. Wei, G. Moad, B. W. Muir, E. Rizzardo, J. Rosselgong, W. Yang and S. H. Thang, Macromol. Rapid Commun., 2014, 35, 840–845 CrossRef CAS PubMed.
- T. G. McKenzie, E. H. H. Wong, Q. Fu, A. Sulistio, D. E. Dunstan and G. G. Qiao, ACS Macro Lett., 2015, 4, 1012–1016 CrossRef CAS.
- N. Hadjichristidis, M. Pitsikalis, S. Pispas and H. Iatrou, Chem. Rev., 2001, 101, 3747–3792 CrossRef CAS PubMed.
- K. Khanna, S. Varshney and A. Kakkar, Polym. Chem., 2010, 1, 1171–1185 RSC.
- A. P. Bapat, J. G. Ray, D. A. Savin and B. S. Sumerlin, Macromolecules, 2013, 46, 2188–2198 CrossRef CAS.
- C. J. Dürr, L. Hlalele, A. Kaiser, S. Brandau and C. Barner-Kowollik, Macromolecules, 2012, 46, 49–62 CrossRef.
- C. Ye, G. Zhao, M. Zhang, J. Du and Y. Zhao, Macromolecules, 2012, 45, 7429–7439 CrossRef CAS.
- Z. Wu, H. Liang and J. Lu, Macromolecules, 2010, 43, 5699–5705 CrossRef CAS.
- A. Vora, K. Singh and D. C. Webster, Polymer, 2009, 50, 2768–2774 CrossRef CAS.
- C. Liu, M. A. Hillmyer and T. P. Lodge, Langmuir, 2009, 25, 13718–13725 CrossRef CAS PubMed.
- C. Liu, Y. Zhang and J. Huang, Macromolecules, 2007, 41, 325–331 CrossRef.
- J. Zhu, X. Zhu, E. T. Kang and K. G. Neoh, Polymer, 2007, 48, 6992–6999 CrossRef CAS.
-
P.-F. Cao, E. Foster, A. de Leon and R. Advincula, in Controlled Radical Polymerization: Materials, ed. K. Matyjaszewski, B. S. Sumerlin, N. V. Tsarevsky and J. Chiefari, American Chemical Society, Washington DC, 2015, pp. 169–185 Search PubMed.
- T. Krivorotova, J. Jonikaite-Svegzdiene, P. Radzevicius and R. Makuska, React. Funct. Polym., 2014, 76, 32–40 CrossRef CAS.
- J. Bolton and J. Rzayev, ACS Macro Lett., 2012, 1, 15–18 CrossRef CAS.
- D. Tang, X. Jiang, H. Liu, C. Li and Y. Zhao, Polym. Chem., 2014, 5, 4679–4692 RSC.
- Z. Zheng, J. Ling and A. H. E. Müller, Macromol. Rapid Commun., 2014, 35, 234–241 CrossRef CAS PubMed.
- N. Li, W. Liu, L. Xu, J. Xu and J. Du, Macromol. Chem. Phys., 2015, 216, 172–181 CrossRef CAS.
- J. Zhu, X. Zhu, Z. Cheng, J. Lu and F. Liu, J. Macromol. Sci., Part A: Pure Appl. Chem., 2003, 40, 963–975 CrossRef.
- J. Y. T. Chong, D. J. Keddie, A. Postma, X. Mulet, B. J. Boyd and C. J. Drummond, Colloids Surf., A, 2015, 470, 60–69 CrossRef CAS.
- D. Wu, X. Song, T. Tang and H. Zhao, J. Polym. Sci., Part A: Polym. Chem., 2010, 48, 443–453 CrossRef CAS.
- Y. Yan, Y. Shi, W. Zhu and Y. Chen, Polymer, 2013, 54, 5634–5642 CrossRef CAS.
- M. Sahl, S. Muth, R. Branscheid, K. Fischer and M. Schmidt, Macromolecules, 2012, 45, 5167–5175 CrossRef CAS.
- M. Beija, J.-D. Marty and M. Destarac, Prog. Polym. Sci., 2011, 36, 845–886 CrossRef CAS.
-
Y. Li, L. S. Schadler and B. C. Benicewicz, in Handbook of RAFT Polymerization, ed. C. Barner-Kowollik, Wiley-VCH, Weinheim, Germany, 2008, pp. 423–453 Search PubMed.
- S. K. Kumar, N. Jouault, B. Benicewicz and T. Neely, Macromolecules, 2013, 46, 3199–3214 CrossRef CAS.
- X. T. Cao, A. M. Showkat, L. G. Bach, W.-K. Lee and K. T. Lim, Mol. Cryst. Liq. Cryst., 2014, 599, 55–62 CrossRef CAS.
- N. Zammarelli, M. Luksin, H. Raschke, R. Hergenröder and R. Weberskirch, Langmuir, 2013, 29, 12834–12843 CrossRef CAS PubMed.
- M. Zamfir, C. Rodriguez-Emmenegger, S. Bauer, L. Barner, A. Rosenhahn and C. Barner-Kowollik, J. Mater. Chem. B, 2013, 1, 6027–6034 RSC.
- W. H. Yu, E. T. Kang and K. G. Neoh, Ind. Eng. Chem. Res., 2004, 43, 5194–5202 CrossRef CAS.
- N. Gurbuz, S. Demirci, S. Yavuz and T. Caykara, J. Polym. Sci., Part A: Polym. Chem., 2011, 49, 423–431 CrossRef CAS.
- H. Takahashi, N. Matsuzaka, M. Nakayama, A. Kikuchi, M. Yamato and T. Okano, Biomacromolecules, 2012, 13, 253–260 CrossRef CAS PubMed.
- H. Takahashi, M. Nakayama, M. Yamato and T. Okano, Biomacromolecules, 2010, 11, 1991–1999 CrossRef CAS PubMed.
- B. Wang, T. Jin, Y. Han, C. Shen, Q. Li, J. Tang, H. Chen and Q. Lin, Int. J. Polym. Mater. Polym. Biomater., 2016, 65, 55–64 CrossRef CAS.
- J. Yuan, X. Huang, P. Li, L. Li and J. Shen, Polym. Chem., 2013, 4, 5074–5085 RSC.
- K. J. Barlow, X. Hao, T. C. Hughes, O. E. Hutt, A. Polyzos, K. A. Turner and G. Moad, Polym. Chem., 2014, 5, 722–732 RSC.
- K. J. Barlow, V. Bernabeu, X. Hao, T. C. Hughes, O. E. Hutt, A. Polyzos, K. A. Turner and G. Moad, React. Funct. Polym., 2015, 96, 89–96 CrossRef CAS.
- B. Couturaud, A. Mas and J. J. Robin, Eur. Polym. J., 2015, 70, 276–285 CrossRef CAS.
- C. Y. Hong, Y. Z. You and C. Y. Pan, J. Polym. Sci., Part A: Polym. Chem., 2006, 44, 2419–2427 CrossRef CAS.
- H. Chirowodza, P. C. Hartmann and H. Pasch, Macromol. Chem. Phys., 2014, 215, 791–801 CrossRef CAS.
- Y. Liu, J. Qiu, Y. Jiang, Z. Liu, M. Meng, L. Ni, C. Qin and J. Peng, Microporous Mesoporous Mater., 2016, 234, 176–185 CrossRef CAS.
- Y. Jiao and P. Akcora, J. Polym. Sci., Part A: Polym. Chem., 2014, 52, 1700–1705 CrossRef CAS.
- L. G. Bach, Q. T. P. Bui, X. T. Cao, V. T. T. Ho and K. T. Lim, Polym. Bull., 2016, 73, 2627–2638 CrossRef CAS.
- S. Eisenhaber and G. Zifferer, Macromol. Theory Simul., 2014, 23, 198–206 CrossRef CAS.
- D. Zhou, E. Mastan and S. Zhu, Macromol. Theory Simul., 2012, 21, 602–614 CrossRef CAS.
- T. Zhou, Y. Zhu, X. Li, X. Liu, K. W. K. Yeung, S. Wu, X. Wang, Z. Cui, X. Yang and P. K. Chu, Prog. Mater. Sci., 2016, 83, 191–235 CrossRef CAS.
- H. N. Liu, X. L. Zhuang, M. Turson, M. Zhang and X. C. Dong, J. Sep. Sci., 2008, 31, 1694–1701 CrossRef CAS PubMed.
- M. Turson, X. L. Zhuang, H. N. Liu, P. Jiang and X. C. Dong, Chin. Chem. Lett., 2009, 20, 1136–1140 CrossRef CAS.
- M. Turson, M. Zhou, P. Jiang and X. Dong, J. Sep. Sci., 2011, 34, 127–134 CrossRef CAS PubMed.
- H.-S. Wang, M. Song and T.-J. Hang, ACS Appl. Mater. Interfaces, 2016, 8, 2881–2898 Search PubMed.
- P. López-Domínguez, J. C. Hernández-Ortiz, K. J. Barlow, E. Vivaldo-Lima and G. Moad, Macromol. React. Eng., 2014, 8, 706–722 CrossRef.
- J. Huang, W.-J. Wang, B.-G. Li and S. Zhu, Macromol. Mater. Eng., 2013, 298, 391–399 CrossRef CAS.
- V. D. Salian and M. E. Byrne, Macromol. Mater. Eng., 2013, 298, 379–390 CrossRef CAS.
- C. Gonzato, P. Pasetto, F. Bedoui, P.-E. Mazeran and K. Haupt, Polym. Chem., 2014, 5, 1313–1322 RSC.
- R. Henkel and P. Vana, Macromol. Chem. Phys., 2014, 215, 182–189 CrossRef CAS.
- G. Moad, Polym. Int., 2015, 64, 15–24 CrossRef CAS.
- J.-F. Lutz, Polym. Chem., 2010, 1, 55–62 RSC.
- C. J. Kloxin and C. N. Bowman, Chem. Soc. Rev., 2013, 42, 7161–7173 RSC.
- G. L. Fiore, S. J. Rowan and C. Weder, Chem. Soc. Rev., 2013, 42, 7278–7288 RSC.
- K. Yamamoto and A. Takasu, Macromolecules, 2010, 43, 8519–8523 CrossRef CAS.
- Y. Amamoto, J. Kamada, H. Otsuka, A. Takahara and K. Matyjaszewski, Angew. Chem., Int. Ed., 2011, 50, 1660–1663 CrossRef CAS PubMed.
- Y. Amamoto, H. Otsuka, A. Takahara and K. Matyjaszewski, ACS Macro Lett., 2012, 1, 478–481 CrossRef CAS.
- C. Barner-Kowollik, A. S. Goldmann and F. H. Schacher, Macromolecules, 2016, 49, 5001–5016 CrossRef CAS.
- S. L. Canning, G. N. Smith and S. P. Armes, Macromolecules, 2016, 49, 1985–2001 CrossRef CAS PubMed.
- B. Liu, A. Kazlauciunas, J. T. Guthrie and S. Perrier, Polymer, 2005, 46, 6293–6299 CrossRef CAS.
-
V. Aseyev, H. Tenhu and F. M. Winnik, in Self Organized Nanostructures of Amphiphilic Block Copolymers II, ed. A. H. E. Müller and O. Borisov, Springer Berlin Heidelberg, Berlin, Heidelberg, 2011, pp. 29–89 Search PubMed.
- D. Roy, W. L. A. Brooks and B. S. Sumerlin, Chem. Soc. Rev., 2013, 42, 7214–7243 RSC.
- J. Seuring and S. Agarwal, Macromol. Rapid Commun., 2012, 33, 1898–1920 CrossRef CAS PubMed.
- J.-F. Lutz, Adv. Mater., 2011, 23, 2237–2243 CrossRef CAS.
- T. Congdon, P. Shaw and M. I. Gibson, Polym. Chem., 2015, 6, 4749–4757 RSC.
- N. A. Cortez-Lemus and A. Licea-Claverie, Prog. Polym. Sci., 2016, 53, 1–51 CrossRef CAS.
- C. Pietsch, U. Mansfeld, C. Guerrero-Sanchez, S. Hoeppener, A. Vollrath, M. Wagner, R. Hoogenboom, S. Saubern, S. H. Thang, C. R. Becer, J. Chiefari and U. S. Schubert, Macromolecules, 2012, 45, 9292–9302 CrossRef CAS.
- C. Liu, S. Wang, H. Zhou, C. Gao and W. Zhang, J. Polym. Sci., Part A: Polym. Chem., 2016, 54, 945–954 CrossRef CAS.
- Y. Kohno, S. Saita, Y. Men, J. Yuan and H. Ohno, Polym. Chem., 2015, 6, 2163–2178 RSC.
- C. Herfurth, A. Laschewsky, L. Noirez, B. von Lospichl and M. Gradzielski, Polymer, 2016 DOI:10.1016/j.polymer.2016.09.089.
- H. Frisch and P. Besenius, Macromol. Rapid Commun., 2015, 36, 346–363 CrossRef CAS PubMed.
- S. Dai, P. Ravi and K. C. Tam, Soft Matter, 2008, 4, 435–449 RSC.
- J. Hu, G. Zhang, Z. Ge and S. Liu, Prog. Polym. Sci., 2014, 39, 1096–1143 CrossRef CAS.
- S. G. Roy and P. De, J. Appl. Polym. Sci., 2014, 131 CAS.
- Y. Ning, L. A. Fielding, K. E. B. Doncom, N. J. W. Penfold, A. N. Kulak, H. Matsuoka and S. P. Armes, ACS Macro Lett., 2016, 5, 311–315 CrossRef CAS PubMed.
- B. A. Abel, M. B. Sims and C. L. McCormick, Macromolecules, 2015, 48, 5487–5495 CrossRef CAS.
- H. Zhang, T. Marmin, E. Cuierrier, A. Soldera, Y. Dory and Y. Zhao, Polym. Chem., 2015, 6, 6644–6650 RSC.
- L. Zhu, S. Powell and S. G. Boyes, J. Polym. Sci., Part A: Polym. Chem., 2015, 53, 1010–1022 CrossRef CAS.
- P. Cotanda, D. B. Wright, M. Tyler and R. K. O'Reilly, J. Polym. Sci., Part A: Polym. Chem., 2013, 51, 3333–3338 CrossRef CAS.
- E. Lallana and N. Tirelli, Macromol. Chem. Phys., 2013, 214, 143–158 CrossRef CAS.
- Y. Zhuang, H. Deng, Y. Su, L. He, R. Wang, G. Tong, D. He and X. Zhu, Biomacromolecules, 2016, 17, 2050–2062 CrossRef CAS PubMed.
- K. Tappertzhofen, S. Beck, E. Montermann, D. Huesmann, M. Barz, K. Koynov, M. Bros and R. Zentel, Macromol. Biosci., 2016, 16, 106–120 CrossRef CAS PubMed.
- Y. Zhuang, Y. Su, Y. Peng, D. Wang, H. Deng, X. Xi, X. Zhu and Y. Lu, Biomacromolecules, 2014, 15, 1408–1418 CrossRef CAS PubMed.
- Y. Wang, C.-Y. Hong and C.-Y. Pan, Biomacromolecules, 2013, 14, 1444–1451 CrossRef CAS PubMed.
- L. Tao, J. Liu, B. H. Tan and T. P. Davis, Macromolecules, 2009, 42, 4960–4962 CrossRef CAS.
- M. Zhang, H. Liu, W. Shao, K. Miao and Y. Zhao, Macromolecules, 2013, 46, 1325–1336 CrossRef CAS.
- X. Hu, G. Liu, Y. Li, X. Wang and S. Liu, J. Am. Chem. Soc., 2015, 137, 362–368 CrossRef CAS PubMed.
- C. Li, H. Liu, D. Tang and Y. Zhao, Polym. Chem., 2015, 6, 1474–1486 RSC.
- M. Beija, Y. Li, A. B. Lowe, T. P. Davis and C. Boyer, Eur. Polym. J., 2013, 49, 3060–3071 CrossRef CAS.
- C.-D. Vo, J. Rosselgong, S. P. Armes and N. C. Billingham, Macromolecules, 2007, 40, 7119–7125 CrossRef CAS.
- X. Wang, G. Jiang, Y. Wang, R. Wang, X. Sun, R. Hu, X. Xi, Y. Zhou, S. Wang and T. Wang, J. Macromol. Sci., Part A: Pure Appl. Chem., 2013, 50, 644–652 CrossRef CAS.
- J. An, X. Dai, Y. Zhao, Q. Guo, Z. Wu, X. Zhang and C. Li, Polym. Chem., 2015, 6, 6529–6542 RSC.
- Y. Wang, G. Jiang, X. Sun, M. Ding, H. Hu and W. Chen, Polym. Chem., 2010, 1, 1638–1643 RSC.
- S. R. S. Ting, E. H. Min, P. B. Zetterlund and M. H. Stenzel, Macromolecules, 2010, 43, 5211–5221 CrossRef CAS.
- S. Liang, X. Li, W.-J. Wang, B.-G. Li and S. Zhu, Macromolecules, 2016, 49, 752–759 CrossRef CAS.
- J. Rosselgong and S. P. Armes, Polym. Chem., 2015, 6, 1143–1149 RSC.
- J. Rosselgong, S. P. Armes, W. Barton and D. Price, Macromolecules, 2009, 42, 5919–5924 CrossRef CAS.
- Y. T. Li and S. P. Armes, Macromolecules, 2009, 42, 939–945 CrossRef CAS.
- X. Wei, P. A. Gunatillake, G. Moad, E. Rizzardo, J. Rosselgong, W. Yang and S. H. Thang, Sci. China: Chem., 2014, 57, 995–1001 CrossRef CAS.
- E. Themistou, G. Battaglia and S. P. Armes, Polym. Chem., 2014, 5, 1405–1417 RSC.
- W.-J. Zhang, C.-Y. Hong and C.-Y. Pan, Biomacromolecules, 2016, 17, 2992–2999 CrossRef CAS PubMed.
- J. Teo, J. A. McCarroll, C. Boyer, J. Youkhana, S. M. Sagnella, H. T. T. Duong, J. Liu, G. Sharbeen, D. Goldstein, T. P. Davis, M. Kavallaris and P. A. Phillips, Biomacromolecules, 2016, 17, 2337–2351 CrossRef CAS PubMed.
- S. J. Kim, D. M. Ramsey, C. Boyer, T. P. Davis and S. R. McAlpine, ACS Med. Chem. Lett., 2013, 4, 915–920 CrossRef CAS PubMed.
- C. Boyer, J. Teo, P. Phillips, R. B. Erlich, S. Sagnella, G. Sharbeen, T. Dwarte, H. T. T. Duong, D. Goldstein, T. P. Davis, M. Kavallaris and J. McCarroll, Mol. Pharm., 2013, 10, 2435–2444 CrossRef CAS PubMed.
- J. Liu, H. Duong, M. R. Whittaker, T. P. Davis and C. Boyer, Macromol. Rapid Commun., 2012, 33, 760–766 CrossRef CAS PubMed.
- C. Boyer, M. Whittaker and T. P. Davis, J. Polym. Sci., Part A: Polym. Chem., 2011, 49, 5245–5256 CrossRef CAS.
- H. Yang, Q. Wang, W. Chen, Y. Zhao, T. Yong, L. Gan, H. Xu and X. Yang, Mol. Pharm., 2015, 12, 1636–1647 CrossRef CAS PubMed.
- H. Wutzel, F. H. Richter, Y. Li, S. S. Sheiko and H.-A. Klok, Polym. Chem., 2014, 5, 1711–1719 RSC.
- L.-H. Wang, S.-G. Ding, J.-J. Yan and Y.-Z. You, Macromol. Rapid Commun., 2014, 35, 298–302 CrossRef CAS PubMed.
- Z.-K. Wang, L.-H. Wang, J.-T. Sun, L.-F. Han and C.-Y. Hong, Polym. Chem., 2013, 4, 1694–1699 RSC.
- X.-L. Sun, W.-D. He, J. Li, L.-Y. Li, B.-Y. Zhang and T.-T. Pan, J. Polym. Sci., Part A: Polym. Chem., 2009, 47, 6863–6872 CrossRef CAS.
- D. Huebner, C. Rossner and P. Vana, Polymer, 2016 DOI:10.1016/j.polymer.2016.05.073.
- Q. Yan, Y. Xin, R. Zhou, Y. Yin and J. Yuan, Chem. Commun., 2011, 47, 9594–9596 RSC.
- F. D. Jochum, L. zur Borg, P. J. Roth and P. Theato, Macromolecules, 2009, 42, 7854–7862 CrossRef CAS.
- Q. Yan, D. Han and Y. Zhao, Polym. Chem., 2013, 4, 5026–5037 RSC.
- Y. Kitayama, K. Yoshikawa and T. Takeuchi, Langmuir, 2016, 32, 9245–9253 CrossRef CAS PubMed.
- T.-Y. Lee, Y.-J. Lin, C.-Y. Yu and J.-F. Chang, J. Appl. Polym. Sci., 2010, 118, 3245–3254 CrossRef CAS.
- G. Moad, M. Chen, M. Häussler, A. Postma, E. Rizzardo and S. H. Thang, Polym. Chem., 2011, 2, 492–519 RSC.
- G. K. Such, R. A. Evans and T. P. Davis, Macromolecules, 2006, 39, 9562–9570 CrossRef CAS.
- W. Sriprom, M. Neel, C. D. Gabbutt, B. M. Heron and S. Perrier, J. Mater. Chem., 2007, 17, 1885–1893 RSC.
- W. Sriprom, C. Neto and S. Perrier, Soft Matter, 2010, 6, 909–914 RSC.
- R. Seno and S. Kobatake, Dyes Pigm., 2015, 114, 166–174 CrossRef CAS.
- F. Ercole, T. P. Davis and R. A. Evans, Polym. Chem., 2010, 1, 37–54 RSC.
- M. Beija, M.-T. Charreyre and J. M. G. Martinho, Prog. Polym. Sci., 2011, 36, 568–602 CrossRef CAS.
- Y. Zhao, Macromolecules, 2012, 45, 3647–3657 CrossRef CAS.
- M. Chen, K. P. Ghiggino, A. W. H. Mau, E. Rizzardo, W. H. F. Sasse, S. H. Thang and G. J. Wilson, Macromolecules, 2004, 37, 5479–5481 CrossRef CAS.
- M. Chen, K. P. Ghiggino, A. W. H. Mau, E. Rizzardo, S. H. Thang and G. J. Wilson, Chem. Commun., 2002, 2276–2277 RSC.
- M. Chen, K. P. Ghiggino, A. W. H. Mau, W. H. F. Sasse, S. H. Thang and G. J. Wilson, Macromolecules, 2005, 38, 3475–3481 CrossRef CAS.
- A. D. Kitchin, S. Velate, M. Chen, K. P. Ghiggino, T. A. Smith and R. P. Steer, Photochem. Photobiol. Sci., 2007, 6, 853–856 Search PubMed.
- P. J. Roth, M. Haase, T. Basché, P. Theato and R. Zentel, Macromolecules, 2010, 43, 895–902 CrossRef CAS.
- C. Pietsch, J. Schäfer, R. Menzel, R. Beckert, J. Popp, B. Dietzek and U. S. Schubert, J. Polym. Sci., Part A: Polym. Chem., 2013, 51, 4765–4773 CrossRef CAS.
- Y. Sun, Z. Chen, E. Puodziukynaite, D. M. Jenkins, J. R. Reynolds and K. S. Schanze, Macromolecules, 2012, 45, 2632–2642 CrossRef CAS.
- A. M. Breul, I. Rabelo de Moraes, R. Menzel, M. Pfeffer, A. Winter, M. D. Hager, S. Rau, B. Dietzek, R. Beckert and U. S. Schubert, Polym. Chem., 2014, 5, 2715–2724 RSC.
- Z. Chen, E. M. Grumstrup, A. T. Gilligan, J. M. Papanikolas and K. S. Schanze, J. Phys. Chem. B, 2014, 118, 372–378 CrossRef CAS PubMed.
- B. Happ, J. Schäfer, R. Menzel, M. D. Hager, A. Winter, J. Popp, R. Beckert, B. Dietzek and U. S. Schubert, Macromolecules, 2011, 44, 6277–6287 CrossRef CAS.
- W.-J. Zhang, C.-Y. Hong and C.-Y. Pan, Macromol. Chem. Phys., 2013, 214, 2445–2453 CrossRef CAS.
- F. Ercole, S. Harrisson, T. P. Davis and R. A. Evans, Soft Matter, 2011, 7, 2687–2696 RSC.
- S. Imao, H. Nishi and S. Kobatake, J. Photochem. Photobiol., A, 2013, 252, 37–45 CrossRef CAS.
- K. Bauri, A. Pan, U. Haldar, A. Narayanan and P. De, J. Polym. Sci., Part A: Polym. Chem., 2016, 54, 2794–2803 CrossRef CAS.
- A. Darabi, P. G. Jessop and M. F. Cunningham, Chem. Soc. Rev., 2016, 45, 4391–4436 RSC.
- H. Liu, S. Lin, Y. Feng and P. Theato, Polym. Chem., 2016 10.1039/C6PY01101B.
- S. Lin and P. Theato, Macromol. Rapid Commun., 2013, 34, 1118–1133 CrossRef CAS PubMed.
- B. Yan, D. Han, O. Boissiere, P. Ayotte and Y. Zhao, Soft Matter, 2013, 9, 2011–2016 RSC.
- L. Lei, Q. Zhang, S. Shi and S. Zhu, Polym. Chem., 2016, 7, 5456–5462 RSC.
- P. Schattling, I. Pollmann and P. Theato, React. Funct. Polym., 2014, 75, 16–21 CrossRef CAS.
- W. L. A. Brooks and B. S. Sumerlin, Chem. Rev., 2016, 116, 1375–1397 CrossRef CAS PubMed.
-
G. E. Southard, K. A. Van Houten, E. W. Ott and G. M. Murray, in Antiterrorism and Homeland Defense, American Chemical Society, 2007, pp. 19–37 Search PubMed.
- A. Ghadban and L. Albertin, Polymers, 2013, 5, 431–526 CrossRef.
-
Q. Zhang and D. M. Haddleton, in Hierarchical Macromolecular Structures: 60 Years after the Staudinger Nobel Prize II, ed. V. Percec, Springer International Publishing, Cham, 2013, pp. 39–59 Search PubMed.
- C. von der Ehe, C. Weber, M. Gottschaldt and U. S. Schubert, Prog. Polym. Sci., 2016, 57, 64–102 CrossRef CAS.
- W.-M. Wan, F. Cheng and F. Jäkle, Angew. Chem., Int. Ed., 2014, 53, 8934–8938 CrossRef CAS PubMed.
- H. Kim, Y. J. Kang, E. S. Jeong, S. Kang and K. T. Kim, ACS Macro Lett., 2012, 1, 1194–1198 CrossRef CAS.
- H. Kim, Y. J. Kang, S. Kang and K. T. Kim, J. Am. Chem. Soc., 2012, 134, 4030–4033 CrossRef CAS PubMed.
- D. Roy, J. N. Cambre and B. S. Sumerlin, Chem. Commun., 2008, 2477–2479 RSC.
- D. Roy, J. N. Cambre and B. S. Sumerlin, Chem. Commun., 2009, 2106–2108 RSC.
- C. Wang, H. Xu and Y. Wei, Anal. Chim. Acta, 2016, 902, 115–122 CrossRef CAS PubMed.
- K. J. Sykes, S. Harrisson and D. J. Keddie, Macromol. Chem. Phys., 2016, 217, 2310–2320 CrossRef CAS.
- T. V. Khamatnurova, D. Zhang, J. Suriboot, H. S. Bazzi and D. E. Bergbreiter, Catal. Sci. Technol., 2015, 5, 2378–2383 Search PubMed.
- X. Zhang, A. F. Cardozo, S. Chen, W. Zhang, C. Julcour, M. Lansalot, J.-F. Blanco, F. Gayet, H. Delmas, B. Charleux, E. Manoury, F. D'Agosto and R. Poli, Chem. – Eur. J., 2014, 20, 15505–15517 CrossRef CAS PubMed.
- X. Chen and N. Ayres, Macromolecules, 2010, 43, 1341–1348 CrossRef CAS.
- Y. Luo, L. Liu, X. Wang, H. Shi, W. Lv and J. Li, Soft Matter, 2012, 8, 1634–1642 RSC.
- K. Sun, M. Xu, K. Zhou, H. Nie, J. Quan and L. Zhu, Mater. Sci. Eng., C, 2016, 68, 172–176 CrossRef CAS PubMed.
- K. Sun, S. W. A. Bligh, H.-L. Nie, J. Quan and L.-M. Zhu, RSC Adv., 2014, 4, 34912–34921 RSC.
- W. Wang, D. L. Chance, V. V. Mossine and T. P. Mawhinney, Glycoconjugate J., 2014, 31, 133–143 CrossRef CAS PubMed.
- Z. Li, P. Zhang, W. Lu, L. Peng, Y. Zhao and G. Chen, Macromol. Rapid Commun., 2016, 37, 1513–1519 CrossRef CAS PubMed.
- Y. Cui, Z. Li, L. Wang, F. Liu, Y. Yuan, H. Wang, L. Xue, J. Pan, G. Chen, H. Chen and L. Yuan, J. Mater. Chem. B, 2016, 4, 5437–5445 RSC.
- Z. P. Tolstyka, H. Phillips, M. Cortez, Y. Wu, N. Ingle, J. B. Bell, P. B. Hackett and T. M. Reineke, ACS Biomater. Sci. Eng., 2016, 2, 43–55 CrossRef CAS PubMed.
- S. R. Tale, L. Yin and T. M. Reineke, Polym. Chem., 2014, 5, 5160–5167 RSC.
- R. J. Mancini, J. Lee and H. D. Maynard, J. Am. Chem. Soc., 2012, 134, 8474–8479 CrossRef CAS PubMed.
- S. Murugaboopathy and H. Matsuoka, Colloid Polym. Sci., 2015, 293, 1317–1328 Search PubMed.
- H. Matsuoka, Y. Yamakawa, A. Ghosh and Y. Saruwatari, Langmuir, 2015, 31, 4827–4836 CrossRef CAS PubMed.
- C. Rodriguez-Emmenegger, B. V. K. J. Schmidt, Z. Sedlakova, V. Šubr, A. B. Alles, E. Brynda and C. Barner-Kowollik, Macromol. Rapid Commun., 2011, 32, 958–965 CrossRef CAS PubMed.
- M. Arotçaréna, B. Heise, S. Ishaya and A. Laschewsky, J. Am. Chem. Soc., 2002, 124, 3787–3793 CrossRef.
- M. S. Donovan, A. B. Lowe, T. A. Sanford and C. L. McCormick, J. Polym. Sci., Part A: Polym. Chem., 2003, 41, 1262–1281 CrossRef CAS.
- J. D. Flores, X. Xu, N. J. Treat and C. L. McCormick, Macromolecules, 2009, 42, 4941–4945 CrossRef CAS.
- H. Willcock, A. Lu, C. F. Hansell, E. Chapman, I. R. Collins and R. K. O'Reilly, Polym. Chem., 2014, 5, 1023–1030 RSC.
- C.-C. Chang, R. Letteri, R. C. Hayward and T. Emrick, Macromolecules, 2015, 48, 7843–7850 CrossRef CAS.
- Y. Zhu, J.-M. Noy, A. B. Lowe and P. J. Roth, Polym. Chem., 2015, 6, 5705–5718 RSC.
- M. H. Stenzel, C. Barner-Kowollik, T. P. Davis and H. M. Dalton, Macromol. Biosci., 2004, 4, 445–453 CrossRef CAS PubMed.
- S.-I. Yusa, K. Fukuda, T. Yamamoto, K. Ishihara and Y. Morishima, Biomacromolecules, 2005, 6, 663–670 CrossRef CAS PubMed.
- B. Yu, A. B. Lowe and K. Ishihara, Biomacromolecules, 2009, 10, 950–958 CrossRef CAS PubMed.
- S. Sakamoto, Y. Sanada, M. Sakashita, K. Nishina, K. Nakai, S.-I. Yusa and K. Sakurai, Polym. J., 2014, 46, 617–622 CrossRef CAS.
- M. S. Donovan, B. S. Sumerlin, A. B. Lowe and C. L. McCormick, Macromolecules, 2002, 35, 8663–8666 CrossRef CAS.
- A. B. Lowe and C. L. McCormick, Chem. Rev., 2002, 102, 4177–4190 CrossRef CAS PubMed.
- Q. Liu, X. Wen, S. Xu, P. Pi, J. Cheng and R. Zeng, Colloid Polym. Sci., 2015, 293, 1705–1712 Search PubMed.
- J. Yuan and M. Antonietti, Polymer, 2011, 52, 1469–1482 CrossRef CAS.
- J. Yuan, D. Mecerreyes and M. Antonietti, Prog. Polym. Sci., 2013, 38, 1009–1036 CrossRef CAS.
- S. Montolio, L. Gonzaez, B. Altava, H. Tenhu, M. I. Burguete, E. Garcia-Verdugo and S. V. Luis, Chem. Commun., 2014, 50, 10683–10686 RSC.
- J. Guo, Y. Zhou, L. Qiu, C. Yuan and F. Yan, Polym. Chem., 2013, 4, 4004–4009 RSC.
- B. J. Adzima, S. R. Venna, S. S. Klara, H. He, M. Zhong, D. R. Luebke, M. S. Mauter, K. Matyjaszewski and H. B. Nulwala, J. Mater. Chem. A, 2014, 2, 7967–7972 RSC.
- H. Mori, M. Yahagi and T. Endo, Macromolecules, 2009, 42, 8082–8092 CrossRef CAS.
- Y. Zuo, N. Guo, Z. Jiao, P. Song, X. Liu, R. Wang and Y. Xiong, J. Polym. Sci., Part A: Polym. Chem., 2016, 54, 169–178 CrossRef CAS.
- J. Yuan, H. Schlaad, C. Giordano and M. Antonietti, Eur. Polym. J., 2011, 47, 772–781 CrossRef CAS.
- N. Pothanagandhi, A. Sivaramakrishna and K. Vijayakrishna, React. Funct. Polym., 2016, 106, 132–136 CrossRef CAS.
- Y. Lu, G. Yu, W.-J. Wang, Q. Ren, B.-G. Li and S. Zhu, Macromolecules, 2015, 48, 915–924 CrossRef CAS.
- K. Vijayakrishna, S. K. Jewrajka, A. Ruiz, R. Marcilla, J. A. Pomposo, D. Mecerreyes, D. Taton and Y. Gnanou, Macromolecules, 2008, 41, 6299–6308 CrossRef CAS.
- B. Zhang, X. Yan, P. Alcouffe, A. Charlot, E. Fleury and J. Bernard, ACS Macro Lett., 2015, 4, 1008–1011 CrossRef CAS.
- J. Yang, W. Sun, W. Lin and Z. Shen, J. Polym. Sci., Part A: Polym. Chem., 2008, 46, 5123–5132 CrossRef CAS.
- R. Nicolaÿ, J. Kamada, A. Van Wassen and K. Matyjaszewski, Macromolecules, 2010, 43, 4355–4361 CrossRef.
- L.-X. Yu, D. Zhuo and R. Ran, Int. J. Polym. Mater. Polym. Biomater., 2013, 62, 749–754 CrossRef CAS.
- C. Cheng, X. Bai, X. Zhang, H. Li, Q. Huang and Y. Tu, J. Polym. Res., 2015, 22, 46 CrossRef.
- D. Yoshimura, S. Yamada and A. Takasu, Polym. Chem., 2014, 5, 3689–3696 RSC.
- R. Chang, X. Wang, X. Li, H. An and J. Qin, ACS Appl. Mater. Interfaces, 2016, 8, 25544–25551 Search PubMed.
- D. E. Whitaker, C. S. Mahon and D. A. Fulton, Angew. Chem., Int. Ed., 2013, 52, 956–959 CrossRef CAS PubMed.
- X. Wang, L. Wang, S. Yang, H. Zhao and L. Liu, Polym. Chem., 2014, 5, 4797–4804 RSC.
- A. W. Jackson and D. A. Fulton, Chem. Commun., 2010, 46, 6051–6053 RSC.
- A. W. Jackson, C. Stakes and D. A. Fulton, Polym. Chem., 2011, 2, 2500–2511 RSC.
- S. G. Roy, K. Bauri, S. Pal and P. De, Polym. Chem., 2014, 5, 3624–3633 RSC.
- N. B. Pramanik, G. B. Nando and N. K. Singha, Polymer, 2015, 69, 349–356 CrossRef CAS.
- P. De, S. R. Gondi, D. Roy and B. S. Sumerlin, Macromolecules, 2009, 42, 5614–5621 CrossRef CAS.
- A. P. Bapat, D. Roy, J. G. Ray, D. A. Savin and B. S. Sumerlin, J. Am. Chem. Soc., 2011, 133, 19832–19838 CrossRef CAS PubMed.
- S. Bode, R. K. Bose, S. Matthes, M. Ehrhardt, A. Seifert, F. H. Schacher, R. M. Paulus, S. Stumpf, B. Sandmann, J. Vitz, A. Winter, S. Hoeppener, S. J. Garcia, S. Spange, S. van der Zwaag, M. D. Hager and U. S. Schubert, Polym. Chem., 2013, 4, 4966–4973 RSC.
- B. Zhu, N. Jasinski, A. Benitez, M. Noack, D. Park, A. S. Goldmann, C. Barner-Kowollik and A. Walther, Angew. Chem., Int. Ed., 2015, 54, 8653–8657 CrossRef CAS PubMed.
- G. R. Whittell, M. D. Hager, U. S. Schubert and I. Manners, Nat. Mater., 2011, 10, 176–188 CrossRef CAS PubMed.
- C. G. Hardy, J. Zhang, Y. Yan, L. Ren and C. Tang, Prog. Polym. Sci., 2014, 39, 1742–1796 CrossRef CAS.
- K. Y. Zhang, S. Liu, Q. Zhao and W. Huang, Coord. Chem. Rev., 2016, 319, 180–195 CrossRef CAS.
- B. V. K. J. Schmidt, J. Elbert, C. Barner-Kowollik and M. Gallei, Macromol. Rapid Commun., 2014, 35, 708–714 CrossRef CAS PubMed.
- M. Hadadpour, Y. Liu, P. Chadha and P. J. Ragogna, Macromolecules, 2014, 47, 6207–6217 CrossRef CAS.
- M. Hadadpour and P. J. Ragogna, J. Polym. Sci., Part A: Polym. Chem., 2015, 53, 2747–2754 CrossRef CAS.
- M. Hadadpour, J. Gwyther, I. Manners and P. J. Ragogna, Chem. Mater., 2015, 27, 3430–3440 CrossRef CAS.
-
Y. Yan, J. Zhang and C. Tang, in Controlled Radical Polymerization: Materials, ed. K. Matyjaszewski, B. S. Sumerlin, N. V. Tsarevsky and J. Chiefari, American Chemical Society, Washington, DC, 2015, pp. 15–27 Search PubMed.
- J. Zhang, L. Ren, C. G. Hardy and C. Tang, Macromolecules, 2012, 45, 6857–6863 CrossRef CAS.
- Y. Yan, J. Zhang, Y. Qiao and C. Tang, Macromol. Rapid Commun., 2014, 35, 254–259 CrossRef CAS PubMed.
- Y. Yan, T. M. Deaton, J. Zhang, H. He, J. Hayat, P. Pageni, K. Matyjaszewski and C. Tang, Macromolecules, 2015, 48, 1644–1650 CrossRef CAS.
- Z.-P. Xiao, Z.-H. Cai, H. Liang and J. Lu, J. Mater. Chem., 2010, 20, 8375–8381 RSC.
- M. Shi, A.-L. Li, H. Liang and J. Lu, Macromolecules, 2007, 40, 1891–1896 CrossRef CAS.
- P. Shi, Y. Qu, C. Liu, H. Khan, P. Sun and W. Zhang, ACS Macro Lett., 2016, 5, 88–93 CrossRef CAS.
- M. Enke, S. Bode, J. Vitz, F. H. Schacher, M. J. Harrington, M. D. Hager and U. S. Schubert, Polymer, 2015, 69, 274–282 CrossRef CAS.
- A. Dag, Y. Jiang, K. J. A. Karim, G. Hart-Smith, W. Scarano and M. H. Stenzel, Macromol. Rapid Commun., 2015, 36, 890–897 CrossRef CAS PubMed.
- C. Zuo, X. Dai, S. Zhao, X. Liu, S. Ding, L. Ma, M. Liu and H. Wei, ACS Macro Lett., 2016, 5, 873–878 CrossRef CAS.
- H. Mori, S. Masuda and T. Endo, Macromolecules, 2006, 39, 5976–5978 CrossRef CAS.
- H. Erothu, J. Kolomanska, P. Johnston, S. Schumann, D. Deribew, D. T. W. Toolan, A. Gregori, C. Dagron-Lartigau, G. Portale, W. Bras, T. Arnold, A. Distler, R. C. Hiorns, P. Mokarian-Tabari, T. W. Collins, J. R. Howse and P. D. Topham, Macromolecules, 2015, 48, 2107–2117 CrossRef CAS.
- X. Pang, L. Zhao, C. Feng, R. Wu, H. Ma and Z. Lin, Polym. Chem., 2013, 4, 2025–2032 RSC.
- Z. Zhang, P. Zhang, Y. Wang and W. Zhang, Polym. Chem., 2016, 7, 3950–3976 RSC.
- X.-H. Dong, W.-B. Zhang, Y. Li, M. Huang, S. Zhang, R. P. Quirk and S. Z. D. Cheng, Polym. Chem., 2012, 3, 124–134 RSC.
- E. Bicciocchi, M. Chen, E. Rizzardo and K. P. Ghiggino, Polym. Chem., 2013, 4, 53–56 RSC.
- E. Bicciocchi, M. Haeussler, E. Rizzardo, A. D. Scully and K. P. Ghiggino, J. Polym. Sci., Part A: Polym. Chem., 2015, 53, 888–903 CrossRef CAS.
- S. M. Clark, J. A. Campbell and D. A. Lewis, Aust. J. Chem., 2015, 68, 1767–1772 CrossRef CAS.
- J. Li and B. C. Benicewicz, J. Polym. Sci., Part A: Polym. Chem., 2013, 51, 3572–3582 CrossRef CAS.
- S. Aroua, E. G. V. Tiu, M. Ayer, T. Ishikawa and Y. Yamakoshi, Polym. Chem., 2015, 6, 2616–2619 RSC.
- M. H. Nawaz, J. Liu, F. Liu, X. Wang and W. Zhang, Mater. Lett., 2013, 91, 71–74 CrossRef CAS.
- M. C. Iovu, C. R. Craley, M. Jeffries-El, A. B. Krankowski, R. Zhang, T. Kowalewski and R. D. McCullough, Macromolecules, 2007, 40, 4733–4735 CrossRef CAS.
- S. Yao, A. Bethani, N. Ziane, C. Brochon, G. Fleury, G. Hadziioannou, P. Poulin, J.-B. Salmon and E. Cloutet, Macromolecules, 2015, 48, 7473–7480 CrossRef CAS.
- K. Palaniappan, N. Hundt, P. Sista, H. Nguyen, J. Hao, M. P. Bhatt, Y.-Y. Han, E. A. Schmiedel, E. E. Sheina, M. C. Biewer and M. C. Stefan, J. Polym. Sci., Part A: Polym. Chem., 2011, 49, 1802–1808 CrossRef CAS.
- C. Yang, J. K. Lee, A. J. Heeger and F. Wudl, J. Mater. Chem., 2009, 19, 5416–5423 RSC.
- T. Antoun, A. Iraqi, L. Kergoat, L. Miozzo and A. Yassar, Macromol. Chem. Phys., 2011, 212, 1129–1136 CrossRef CAS.
- M. R. Kern and S. G. Boyes, J. Polym. Sci., Part A: Polym. Chem., 2014, 52, 3575–3585 CAS.
-
M. Chen, G. Moad, E. Rizzardo, R. A. Evans and M. Haeussler, Conducting and Semiconducting Organic Materials, CSIRO, WO2009155657A1, 2009 Search PubMed.
- S. Rajaram, P. B. Armstrong, B. J. Kim and J. M. J. Frechet, Chem. Mater., 2009, 1775–1777 CrossRef CAS.
- Y. Lee, J. K. Kim, K. Fukukawa, J. Bang and C. J. Hawker, Polym. Prepr. (Am. Chem. Soc., Div. Polym. Chem.), 2006, 47(2), 679–680 CAS.
- Y.-J. Kim, C.-H. Cho, K. Paek, M. Jo, M.-K. Park, N.-E. Lee, Y.-J. Kim, B. J. Kim and E. Lee, J. Am. Chem. Soc., 2014, 136, 2767–2774 CrossRef CAS PubMed.
- L. Wang, J. Li, W. Zhang, G. Chen, W. Zhang and X. Zhu, Polym. Chem., 2014, 5, 2872–2879 RSC.
- J. Zhang, L. Wang, C. Li, Y. Li, J. Liu, Y. Tu, W. Zhang, N. Zhou and X. Zhu, J. Polym. Sci., Part A: Polym. Chem., 2014, 52, 691–698 CrossRef CAS.
- L. Rostro, A. G. Baradwaj and B. W. Boudouris, ACS Appl. Mater. Interfaces, 2013, 5, 9896–9901 Search PubMed.
- P. J. Roth, Macromol. Chem. Phys., 2014, 215, 825–838 CrossRef CAS.
- R. Adelmann, P. Mela, M. O. Gallyamov, H. Keul and M. Möller, J. Polym. Sci.,
Part A: Polym. Chem., 2009, 47, 1274–1283 CrossRef CAS.
- R. L. Weber, Y. Ye, A. L. Schmitt, S. M. Banik, Y. A. Elabd and M. K. Mahanthappa, Macromolecules, 2011, 44, 5727–5735 CrossRef CAS.
- W. Zhang, Y. Liu, A. C. Jackson, A. M. Savage, S. P. Ertem, T.-H. Tsai, S. Seifert, F. L. Beyer, M. W. Liberatore, A. M. Herring and E. B. Coughlin, Macromolecules, 2016, 49, 4714–4722 CrossRef CAS.
- A. J. Tilley, M. Chen, S. M. Danczak, K. P. Ghiggino and J. M. White, Polym. Chem., 2012, 3, 892–899 RSC.
- K. Nakabayashi, Y. Abiko and H. Mori, Macromolecules, 2013, 46, 5998–6012 CrossRef CAS.
- Y. Abiko, A. Matsumura, K. Nakabayashi and H. Mori, Polymer, 2014, 55, 6025–6035 CrossRef CAS.
- T. R. Barlow, J. C. Brendel and S. Perrier, Macromolecules, 2016, 49, 6203–6212 CrossRef CAS.
- C. Barner-Kowollik, F. E. Du Prez, P. Espeel, C. J. Hawker, T. Junkers, H. Schlaad and W. Van Camp, Angew. Chem., Int. Ed., 2011, 50, 60–62 CrossRef CAS PubMed.
- D. Quemener, M. Le Hellaye, C. Bissett, T. P. Davis, C. Barner-Kowollik and M. H. Stenzel, J. Polym. Sci., Part A: Polym. Chem., 2008, 46, 155–173 CrossRef CAS.
- V. Ladmiral, T. M. Legge, Y. L. Zhao and S. Perrier, Macromolecules, 2008, 41, 6728–6732 CrossRef CAS.
- Y. Li, J. W. Yang and B. C. Benicewicz, J. Polym. Sci., Part A: Polym. Chem., 2007, 45, 4300–4308 CrossRef CAS.
- G. Li, H. Zheng and R. Bai, Macromol. Rapid Commun., 2009, 30, 442–447 CrossRef CAS PubMed.
- W. Yuan, L. Li and H. Zou, RSC Adv., 2015, 5, 80264–80268 RSC.
- W. Yuan, W. Huang and H. Zou, Polym. Bull., 2016, 73, 2199–2210 CrossRef CAS.
- A. B. J. Withey, G. Chen, T. L. U. Nguyen and M. H. Stenzel, Biomacromolecules, 2009, 10, 3215–3226 CrossRef CAS PubMed.
- J. Stadermann, M. Riedel and B. Voit, Macromol. Chem. Phys., 2013, 214, 263–271 CrossRef CAS.
- A. Krieg, C. R. Becer, R. Hoogenboom and U. S. Schubert, Macromol. Symp., 2009, 275–276, 73–81 CrossRef CAS.
- A. Prasher, C. M. Loynd, B. T. Tuten, P. G. Frank, D. Chao and E. B. Berda, J. Polym. Sci., Part A: Polym. Chem., 2016, 54, 209–217 CrossRef CAS.
- K. J. Abd Karim, S. Binauld, W. Scarano and M. H. Stenzel, Polym. Chem., 2013, 4, 5542–5554 RSC.
- M. Callari, D. S. Thomas and M. H. Stenzel, J. Mater. Chem. B, 2016, 4, 2114–2123 RSC.
- O. Altintas, M. Artar, G. ter Huurne, I. K. Voets, A. R. A. Palmans, C. Barner-Kowollik and E. W. Meijer, Macromolecules, 2015, 48, 8921–8932 CrossRef CAS.
- E. Huerta, P. J. M. Stals, E. W. Meijer and A. R. A. Palmans, Angew. Chem., Int. Ed., 2013, 52, 2906–2910 CrossRef CAS PubMed.
- X. Zhang, X. Lian, L. Liu, J. Zhang and H. Zhao, Macromolecules, 2008, 41, 7863–7869 CrossRef CAS.
- M. Semsarilar, V. Ladmiral and S. B. Perrier, Macromolecules, 2010, 43, 1438–1443 CrossRef CAS.
- C. Fu, J. Xu, L. Tao and C. Boyer, ACS Macro Lett., 2014, 3, 633–638 CrossRef CAS.
- C. F. Hansell and R. K. O'Reilly, ACS Macro Lett., 2012, 1, 896–901 CrossRef CAS.
- M. Grogna, R. Cloots, A. Luxen, C. Jerome, C. Passirani, N. Lautram, J.-F. Desreux, M. Collodoro, M.-C. De Pauw-Gillet and C. Detrembleur, Polym. Chem., 2011, 2, 2316–2327 RSC.
- C. R. Kinnane, G. K. Such and F. Caruso, Macromolecules, 2011, 44, 1194–1202 CrossRef CAS.
- G. K. Such, E. Tjipto, A. Postma, A. P. R. Johnston and F. Caruso, Nano Lett., 2007, 7, 1706–1710 CrossRef CAS PubMed.
- G. K. Such, J. F. Quinn, A. Quinn, E. Tjipto and F. Caruso, J. Am. Chem. Soc., 2006, 128, 9318–9319 CrossRef CAS PubMed.
- F. Cavalieri, A. Postma, L. Lee and F. Caruso, ACS Nano, 2009, 3, 234–240 CrossRef CAS PubMed.
- V. D. Goud, R. Dsouza and S. Valiyaveettil, Eur. Polym. J., 2015, 71, 114–125 CrossRef CAS.
- V. D. Goud, R. Dsouza and S. Valiyaveettil, RSC Adv., 2015, 5, 47647–47658 RSC.
- R. K. O'Reilly, M. J. Joralemon, C. J. Hawker and K. L. Wooley, Chem. – Eur. J., 2006, 12, 6776–6786 CrossRef PubMed.
- J. Stadermann, S. Fleischmann, M. Messerschmidt, H. Komber and B. Voit, Macromol. Symp., 2009, 275–276, 35–42 CrossRef CAS.
- J. C. Brendel, F. Liu, A. S. Lang, T. P. Russell and M. Thelakkat, ACS Nano, 2013, 7, 6069–6078 CrossRef CAS PubMed.
- D. Cimen and T. Caykara, Polym. Chem., 2015, 6, 6812–6818 RSC.
- D. Cimen, E. Yildirim and T. Caykara, J. Polym. Sci., Part A: Polym. Chem., 2015, 53, 1696–1706 CrossRef CAS.
-
L. Wang, J. Li, Y. Zheng, Y. Huang, Y. Qiao and B. C. Benicewicz, in Controlled Radical Polymerization: Materials, ed. K. Matyjaszewski, B. S. Sumerlin, N. V. Tsarevsky and J. Chiefari, American Chemical Society, Washington, DC, 2015, pp. 187–201 Search PubMed.
- Y. Li and B. C. Benicewicz, Macromolecules, 2008, 41, 7986–7992 CrossRef CAS.
- E. Crownover, C. L. Duvall, A. Convertine, A. S. Hoffman and P. S. Stayton, J. Controlled Release, 2011, 155, 167–174 CrossRef CAS PubMed.
- G. Li, H. Zheng, Y. Wang, H. Wang, Q. Dong and R. Bai, Polymer, 2010, 51, 1940–1946 CrossRef CAS.
- X. Z. Jiang, J. Y. Zhang, Y. M. Zhou, J. Xu and S. Y. Liu, J. Polym. Sci., Part A: Polym. Chem., 2008, 46, 860–871 CrossRef CAS.
- L. Xiao, Y. Chen and K. Zhang, Macromolecules, 2016, 49, 4452–4461 CrossRef CAS.
- A. P. Bapat, J. G. Ray, D. A. Savin, E. A. Hoff, D. L. Patton and B. S. Sumerlin, Polym. Chem., 2012, 3, 3112–3120 RSC.
- X.-H. Liu, G.-B. Zhang, B.-X. Li and Y.-G. Bai, J. Appl. Polym. Sci., 2009, 114, 663–670 CrossRef CAS.
-
F. Huang, X. Hao, G. Moad, C. Smith, S. H. Thang and E. Rizzardo, unpublished results.
- N. B. Pramanik, D. S. Bag, S. Alam, G. B. Nando and N. K. Singha, J. Polym. Sci., Part A: Polym. Chem., 2013, 51, 3365–3374 CrossRef CAS.
- N. B. Pramanik and N. K. Singha, RSC Adv., 2016, 6, 2455–2463 RSC.
- H. Li, J. Li, W. Ke and Z. Ge, Macromol. Rapid Commun., 2015, 36, 1841–1849 CrossRef CAS PubMed.
- A. Bousquet, C. Barner-Kowollik and M. H. Stenzel, J. Polym. Sci., Part A: Polym. Chem., 2010, 48, 1773–1781 CrossRef CAS.
- M. Arslan, T. N. Gevrek, J. Lyskawa, S. Szunerits, R. Boukherroub, R. Sanyal, P. Woisel and A. Sanyal, Macromolecules, 2014, 47, 5124–5134 CrossRef CAS.
- I. I. Yilmaz, M. Arslan and A. Sanyal, Macromol. Rapid Commun., 2012, 33, 856–862 CrossRef CAS PubMed.
- L. Zhang, C. Zhang, X. Peng and C. He, RSC Adv., 2016, 6, 17228–17238 RSC.
- L. G. Bach, M. Rafiqul Islam, T.-S. Vo, S.-K. Kim and K. T. Lim, J. Colloid Interface Sci., 2013, 394, 132–140 CrossRef CAS PubMed.
- C. Zobrist, J. Sobocinski, J. Lyskawa, D. Fournier, V. Miri, M. Traisnel, M. Jimenez and P. Woisel, Macromolecules, 2011, 44, 5883–5892 CrossRef CAS.
- F. D. Jochum and P. Theato, Macromolecules, 2009, 42, 5941–5945 CrossRef CAS.
- M. Allmeroth, D. Moderegger, B. Biesalski, K. Koynov, F. Rösch, O. Thews and R. Zentel, Biomacromolecules, 2011, 12, 2841–2849 CrossRef CAS PubMed.
- L. Nuhn, M. Hirsch, B. Krieg, K. Koynov, K. Fischer, M. Schmidt, M. Helm and R. Zentel, ACS Nano, 2012, 6, 2198–2214 CrossRef CAS PubMed.
- G. B. H. Chua, P. J. Roth, H. T. T. Duong, T. P. Davis and A. B. Lowe, Macromolecules, 2012, 45, 1362–1374 CrossRef CAS.
- M. I. Gibson, M. Danial and H.-A. Klok, ACS Comb. Sci., 2011, 13, 286–297 CrossRef CAS PubMed.
- V. T. Huynh, S. Binauld, P. L. de Souza and M. H. Stenzel, Chem. Mater., 2012, 24, 3197–3211 CrossRef CAS.
- A. Viswanath, Y. Shen, A. N. Green, R. Tan, A. B. Greytak and B. C. Benicewicz, Macromolecules, 2014, 47, 8137–8144 CrossRef CAS.
- Y. Song, P.-N. Cheng, L. Zhu, E. G. Moore and J. S. Moore, J. Am. Chem. Soc., 2014, 136, 5233–5236 CrossRef CAS PubMed.
- H. Peng, M. Kather, K. Rübsam, F. Jakob, U. Schwaneberg and A. Pich, Macromolecules, 2015, 48, 4256–4268 CrossRef CAS.
- N. Mohri, B. Oschmann, N. Laszczynski, F. Mueller, J. von Zamory, M. N. Tahir, S. Passerini, R. Zentel and W. Tremel, J. Mater. Chem. A, 2016, 4, 612–619 RSC.
- C. M. Evans, C. R. Bridges, G. E. Sanoja, J. Bartels and R. A. Segalman, ACS Macro Lett., 2016, 5, 925–930 CrossRef CAS.
- N. Eschweiler, H. Keul, M. Millaruelo, R. Weberskirch and M. Moeller, Polym. Int., 2014, 63, 114–126 CrossRef CAS.
- M. Messerschmidt, H. Komber, L. Häußler, C. Hanzelmann, M. Stamm, B. Raether, O. da Costa e Silva and P. Uhlmann, Macromolecules, 2013, 46, 2616–2627 CrossRef CAS.
- J. Xu, L. Tao, C. Boyer, A. B. Lowe and T. P. Davis, Macromolecules, 2011, 44, 299–312 CrossRef CAS.
- G. Marcelo, J. M. G. Martinho and J. P. S. Farinha, J. Phys. Chem. B, 2013, 117, 3416–3427 CrossRef CAS PubMed.
- Z. Wei, S. Zhu and H. Zhao, Polym. Chem., 2015, 6, 1316–1324 RSC.
- T. Ueki, S. Sawamura, Y. Nakamura, Y. Kitazawa, H. Kokubo and M. Watanabe, Langmuir, 2013, 29, 13661–13665 CrossRef CAS PubMed.
- P. Relogio, M. Bathfield, Z. Haftek-Terreau, M. Beija, A. Favier, M.-J. Giraud-Panis, F. D'Agosto, B. Mandrand, J. P. S. Farinha, M.-T. Charreyre and J. M. G. Martinho, Polym. Chem., 2013, 4, 2968–2981 RSC.
- S. Adjili, A. Favier, J. Massin, Y. Bretonniere, W. Lacour, Y.-C. Lin, E. Chatre, C. Place, C. Favard, D. Muriaux, C. Andraud and M.-T. Charreyre, RSC Adv., 2014, 4, 15569–15578 RSC.
- Y. Li, H. T. T. Duong, M. W. Jones, J. S. Basuki, J. Hu, C. Boyer and T. P. Davis, ACS Macro Lett., 2013, 2, 912–917 CrossRef CAS.
- R. Kakuchi and P. Theato, Macromolecules, 2012, 45, 1331–1338 CrossRef CAS.
- Y. J. Kim, H. Kang, M. Leolukman, P. F. Nealey and P. Gopalan, Chem. Mater., 2009, 21, 3030–3032 CrossRef CAS.
- K. Nilles and P. Theato, Polym. Chem., 2011, 2, 376–384 RSC.
- K. A. Aamer and G. N. Tew, J. Polym. Sci., Part A: Polym. Chem., 2007, 45, 5618–5625 CrossRef CAS.
- P. Espeel, F. Goethals, M. M. Stamenovic, L. Petton and F. E. Du Prez, Polym. Chem., 2012, 3, 1007–1015 RSC.
- L. He, E. S. Read, S. P. Armes and D. J. Adams, Macromolecules, 2007, 40, 4429–4438 CrossRef CAS.
- Y. Li and S. P. Armes, Macromolecules, 2009, 42, 939–945 CrossRef CAS.
- A. H. Alidedeoglu, A. W. York, D. A. Rosado, C. L. McCormick and S. E. Morgan, J. Polym. Sci., Part A: Polym. Chem., 2010, 48, 3052–3061 CrossRef CAS.
- A. H. Alidedeoglu, A. W. York, C. L. McCormick and S. E. Morgan, J. Polym. Sci., Part A: Polym. Chem., 2009, 47, 5405–5415 CrossRef CAS.
- D. Sprouse and T. M. Reineke, Biomacromolecules, 2014, 15, 2616–2628 CrossRef CAS PubMed.
- M. Williams, N. J. W. Penfold and S. P. Armes, Polym. Chem., 2016, 7, 384–393 RSC.
- Q. Yu, Y. Ding, H. Cao, X. Lu and Y. Cai, ACS Macro Lett., 2015, 4, 1293–1296 CrossRef CAS.
- M. Ahmed and R. Narain, Biomaterials, 2011, 32, 5279–5290 CrossRef CAS PubMed.
- A. W. York, F. Huang and C. L. McCormick, Biomacromolecules, 2010, 11, 505–514 CrossRef CAS PubMed.
- X. Xu, J. D. Flores and C. L. McCormick, Macromolecules, 2011, 44, 1327–1334 CrossRef CAS.
- X. Xu, A. E. Smith and C. L. McCormick, Aust. J. Chem., 2009, 62, 1520–1527 CrossRef CAS.
- S. E. Exley, L. C. Paslay, G. S. Sahukhal, B. A. Abel, T. D. Brown, C. L. McCormick, S. Heinhorst, V. Koul, V. Choudhary, M. O. Elasri and S. E. Morgan, Biomacromolecules, 2015, 16, 3845–3852 CrossRef CAS PubMed.
- M. H. Allen, S. T. Hemp, A. E. Smith and T. E. Long, Macromolecules, 2012, 45, 3669–3676 CrossRef CAS.
- L. Wong, M. Kavallaris and V. Bulmus, Polym. Chem., 2011, 2, 385–393 RSC.
- Z. Jia, J. Liu, C. Boyer, T. P. Davis and V. Bulmus, Biomacromolecules, 2009, 10, 3253–3258 CrossRef CAS PubMed.
- J.-J. Yan, C.-Y. Hong and Y.-Z. You, Macromolecules, 2011, 44, 1247–1251 CrossRef CAS.
- E. F. Crownover, A. J. Convertine and P. S. Stayton, Polym. Chem., 2011, 2, 1499–1504 RSC.
- P. Chytil, T. Etrych, J. Kríz, V. Subr and K. Ulbrich, Eur. J. Pharm. Sci., 2010, 41, 473–482 CrossRef CAS PubMed.
- M. Liang, I. C. Lin, M. R. Whittaker, R. F. Minchin, M. J. Monteiro and I. Toth, ACS Nano, 2009, 4, 403–413 CrossRef PubMed.
- H. T. Ho, S. Pascual, V. Montembault, N. Casse and L. Fontaine, Polym. Chem., 2014, 5, 5542–5545 RSC.
- Y. Maki, H. Mori and T. Endo, Macromol. Chem. Phys., 2007, 208, 2589–2599 CrossRef CAS.
- Y. Maki, H. Mori and T. Endo, Macromol. Chem. Phys., 2010, 211, 1137–1147 CrossRef CAS.
- K. Nakabayashi, D. Noda, Y. Watanabe and H. Mori, Polymer, 2015, 68, 17–24 CrossRef CAS.
- J. D. Flores, J. Shin, C. E. Hoyle and C. L. McCormick, Polym. Chem., 2010, 1, 213–220 RSC.
- J. Moraes, T. Maschmeyer and S. Perrier, J. Polym. Sci., Part A: Polym. Chem., 2011, 49, 2771–2782 CrossRef CAS.
- P. J. Roth and P. Theato, ACS Symp. Ser., 2011, 1066, 23–37 CrossRef CAS.
- E. A. Hoff, B. A. Abel, C. A. Tretbar, C. L. McCormick and D. L. Patton, Macromolecules, 2016, 49, 554–563 CrossRef CAS.
- H. T. T. Duong, V. T. Huynh, P. de Souza and M. H. Stenzel, Biomacromolecules, 2010, 11, 2290–2299 CrossRef CAS PubMed.
- J. Moraes, T. Maschmeyer and S. Perrier, Aust. J. Chem., 2011, 64, 1047–1053 CrossRef CAS.
- Y. Kim, M. H. Pourgholami, D. L. Morris and M. H. Stenzel, J. Mater. Chem., 2011, 21, 12777–12783 RSC.
- J. Du, H. Willcock, J. P. Patterson, I. Portman and R. K. O'Reilly, Small, 2011, 7, 2070–2080 CrossRef CAS PubMed.
- Y. Zhu, L. Liu and J. Du, Macromolecules, 2013, 46, 194–203 CrossRef CAS.
-
M. Destarac, C. Kalai, A. Wilczewska, L. Petit, E. Van Gramberen and S. Z. Zard, in Controlled/Living Radical Polymerization, American Chemical Society, 2006, pp. 564–577 Search PubMed.
- H. Willcock and R. K. O'Reilly, Polym. Chem., 2010, 1, 149–157 RSC.
- G. Moad, E. Rizzardo and S. H. Thang, Polym. Int., 2011, 60, 9–25 CrossRef CAS.
- M. A. Harvison, P. J. Roth, T. P. Davis and A. B. Lowe, Aust. J. Chem., 2011, 64, 992–1006 CrossRef CAS.
- P. J. Roth, C. Boyer, A. B. Lowe and T. P. Davis, Macromol. Rapid Commun., 2011, 32, 1123–1143 CrossRef CAS PubMed.
-
P. J. Roth and P. Theato, in Thiol-X Chemistries in Polymer and Materials Science, ed. A. Lowe and C. Bowman, The Royal Society of Chemistry, 2013, pp. 76–94 Search PubMed.
-
A. B. Lowe, in Thiol-X Chemistries in Polymer and Materials Science, ed. A. Lowe and C. Bowman, The Royal Society of Chemistry, Cambridge, UK, 2013, pp. 28–58 Search PubMed.
- C. Boyer, A. Granville, T. P. Davis and V. Bulmus, J. Polym. Sci., Part A: Polym. Chem., 2009, 47, 3773–3794 CrossRef CAS.
- G. Delaittre, T. Pauloehrl, M. Bastmeyer and C. Barner-Kowollik, Macromolecules, 2012, 45, 1792–1802 CrossRef CAS.
- A. B. Lowe, Polym. Chem., 2010, 1, 17–36 RSC.
- A. B. Lowe, Polym. Chem., 2014, 5, 4820–4870 RSC.
- S.-S. Zhang, K. Cui, J. Huang, Q.-L. Zhao, S.-K. Cao and Z. Ma, RSC Adv., 2015, 5, 44571–44577 RSC.
- B. A. Abel and C. L. McCormick, Macromolecules, 2016, 49, 6193–6202 CrossRef CAS.
- Q. Zhang, L. Voorhaar, B. G. De Geest and R. Hoogenboom, Macromol. Rapid Commun., 2015, 36, 1177–1183 CrossRef CAS PubMed.
- F. Goethals, D. Frank and F. Du Prez, Prog. Polym. Sci., 2017 DOI:10.1016/j.progpolymsci.2016.09.003 , in press.
- Y. Wang and J. Ling, RSC Adv., 2015, 5, 18546–18553 RSC.
- M. A. Harvison, T. P. Davis and A. B. Lowe, Polym. Chem., 2011, 2, 1347–1354 RSC.
- F. Segui, X.-P. Qiu and Françoise M. Winnik, J. Polym. Sci., Part A: Polym. Chem., 2008, 46, 314–326 CrossRef CAS.
- H. Li, B. Yu, H. Matsushima, C. E. Hoyle and A. B. Lowe, Macromolecules, 2009, 42, 6537–6542 CrossRef CAS.
- P. J. Roth, D. Kessler, R. Zentel and P. Theato, Macromolecules, 2008, 41, 8316–8319 CrossRef CAS.
- A. W. York, C. W. Scales, F. Q. Huang and C. L. McCormick, Biomacromolecules, 2007, 8, 2337–2341 CrossRef CAS PubMed.
- O. Altintas, K. Riazi, R. Lee, C. Y. Lin, M. L. Coote, M. Wilhelm and C. Barner-Kowollik, Macromolecules, 2013, 46, 8079–8091 CrossRef CAS.
- O. Altintas, M. Abbasi, K. Riazi, A. S. Goldmann, N. Dingenouts, M. Wilhelm and C. Barner-Kowollik, Polym. Chem., 2014, 5, 5009–5019 RSC.
- X. Zhang, J. Jiang and Y. Zhang, J. Appl. Polym. Sci., 2016, 133 CAS.
- E. V. Chernikova, A. V. Plutalova, E. S. Garina and D. V. Vishnevetsky, Polym. Chem., 2016, 7, 3622–3632 RSC.
- E. T. Nadres, H. Takahashi and K. Kuroda, J. Polym. Sci., Part A: Polym. Chem., 2016 DOI:10.1002/pola.28384.
- D. Matioszek, P.-E. Dufils, J. Vinas and M. Destarac, Macromol. Rapid Commun., 2015, 36, 1354–1361 CrossRef CAS PubMed.
- G. Moad, D. Keddie, C. Guerrero-Sanchez, E. Rizzardo and S. H. Thang, Macromol. Symp., 2015, 350, 34–42 CrossRef CAS.
- D. J. Keddie, C. Guerrero-Sanchez, G. Moad, R. Mulder, E. Rizzardo and S. H. Thang, Macromolecules, 2012, 45, 4205–4215 CrossRef CAS.
- S. J. Stace, G. Moad, C. M. Fellows and D. J. Keddie, Polym. Chem., 2015, 6, 7119–7126 RSC.
- X. P. Chen, K. Y. Qiu, G. Swift, D. G. Westmoreland and S. Q. Wu, Eur. Polym. J., 2000, 36, 1547–1554 CrossRef CAS.
- P. Li, S. H. Qin, D. Q. Qin and K. Y. Qiu, Polym. Int., 2004, 53, 756–765 CrossRef CAS.
- P. Li and K.-Y. Qiu, Macromol. Rapid Commun., 2002, 23, 1124–1129 CrossRef CAS.
- Y. Kwak and K. Matyjaszewski, Macromolecules, 2008, 41, 6627–6635 CrossRef CAS.
- X. Q. Xue, W. Zhang, Z. P. Cheng, J. Zhu and X. L. Zhu, J. Polym. Sci., Part A: Polym. Chem., 2008, 46, 5626–5637 CrossRef CAS.
- W. Zhang, W. Zhang, Z. Cheng, N. Zhou and X. Zhu, J. Macromol. Sci., Part A: Pure Appl. Chem., 2008, 45, 850–856 CrossRef CAS.
- S. Harihara Subramanian, R. Prakash Babu and R. Dhamodharan, Macromolecules, 2008, 41, 262–265 CrossRef.
- Z. Zhang, W. Wang, H. Xia, J. Zhu, W. Zhang and X. Zhu, Macromolecules, 2009, 42, 7360–7366 CrossRef CAS.
- Z. Zhang, W. Zhang, X. Zhu, Z. Cheng and J. Zhu, J. Polym. Sci., Part A: Polym. Chem., 2007, 45, 5722–5730 CrossRef CAS.
- Y. Kwak, R. Nicolay and K. Matyjaszewski, Macromolecules, 2008, 41, 6602–6604 CrossRef CAS.
- Y. Kwak, R. Nicolay and K. Matyjaszewski, Aust. J. Chem., 2009, 62, 1384–1401 CrossRef CAS.
- A. J. Teator, D. N. Lastovickova and C. W. Bielawski, Chem. Rev., 2016, 116, 1969–1992 CrossRef CAS PubMed.
- X. Pan, M. A. Tasdelen, J. Laun, T. Junkers, Y. Yagci and K. Matyjaszewski, Prog. Polym. Sci., 2016 DOI:10.1016/j.progpolymsci.2016.06.005 , in press.
- K. Koumura, K. Satoh and M. Kamigaito, Polym. J., 2009, 41, 595–603 CrossRef CAS.
- T. Otsu and A. Kuriyama, Polym. J., 1985, 17, 97–104 CrossRef CAS.
- T. Otsu and A. Kuriyama, J. Macromol. Sci., Chem. A, 1984, 21, 961–977 CrossRef.
- T. Otsu, T. Matsunaga, A. Kuriyama and M. Yoshioka, Eur. Polym. J., 1989, 25, 643–650 CrossRef CAS.
- T. Otsu and A. Matsumoto, Adv. Polym. Sci., 1998, 136, 75–137 CrossRef CAS.
-
M. Atilla Tasdelen and Y. Yagci, in Fundamentals of Controlled/Living Radical Polymerization, ed. N. V. Tsarevsky and B. S. Sumerlin, The Royal Society of Chemistry, Cambridge, UK, 2013, pp. 78–111 Search PubMed.
- X. L. Su, Z. G. Zhao, H. Li, X. X. Li, P. P. Wu and Z. W. Han, Eur. Polym. J., 2008, 44, 1849–1856 CrossRef CAS.
- R. Ran, T. Wan, T. Gao, J. Gao and Z. Chen, Polym. Int., 2008, 57, 28–34 CrossRef CAS.
- T. G. McKenzie, Q. Fu, M. Uchiyama, K. Satoh, J. Xu, C. Boyer, M. Kamigaito and G. G. Qiao, Adv. Sci., 2016, 3,
1500394, DOI:10.1002/advs.201500394.
-
J. Xu, S. Shanmugam, N. A. Corrigan and C. Boyer, in Controlled Radical Polymerization: Mechanisms, American Chemical Society, 2015, pp. 247–267 Search PubMed.
- J. Gardiner, C. H. Hornung, J. Tsanaktsidis and D. Guthrie, Eur. Polym. J., 2016, 80, 200–207 CrossRef CAS.
- J. Poly, B. Cabannes-Boue, L. Hebinger, R. Mangin, A. Sauvage, P. Xiao, F. Morlet-Savary and J. Lalevee, Polym. Chem., 2015, 6, 5766–5772 RSC.
- J. Xu, K. Jung and C. Boyer, Macromolecules, 2014, 47, 4217–4229 CrossRef CAS.
- S. Shanmugam, J. T. Xu and C. Boyer, Chem. Sci., 2015, 6, 1341–1349 RSC.
- J. Zhao, J. Lalevee, H. Lu, R. MacQueen, S. H. Kable, T. W. Schmidt, M. H. Stenzel and P. Xiao, Polym. Chem., 2015, 6, 5053–5061 RSC.
- L. Nebhani, P. Gerstel, P. Atanasova, M. Bruns and C. Barner-Kowollik, J. Polym. Sci., Part A: Polym. Chem., 2009, 47, 7090–7095 CrossRef CAS.
- L. Nebhani, S. Sinnwell, C. Y. Lin, M. L. Coote, M. H. Stenzel and C. Barner-Kowollik, J. Polym. Sci., Part A: Polym. Chem., 2009, 47, 6053–6071 CrossRef CAS.
- A. Bousquet, C. Boyer, T. P. Davis and M. H. Stenzel, Polym. Chem., 2010, 1, 1186–1195 RSC.
- A. J. Inglis, M. H. Stenzel and C. Barner-Kowollik, Macromol. Rapid Commun., 2009, 30, 1792–1798 CrossRef CAS PubMed.
- G. Delaittre, N. K. Guimard and C. Barner-Kowollik, Acc. Chem. Res., 2015, 48, 1296–1307 CrossRef CAS PubMed.
- A. J. Inglis, T. Paulöhrl and C. Barner-Kowollik, Macromolecules, 2009, 43, 33–36 CrossRef.
- M. Glassner, G. Delaittre, M. Kaupp, J. P. Blinco and C. Barner-Kowollik, J. Am. Chem. Soc., 2012, 134, 7274–7277 CrossRef CAS PubMed.
- E. Espinosa, M. Glassner, C. Boisson, C. Barner-Kowollik and F. D'Agosto, Macromol. Rapid Commun., 2011, 32, 1447–1453 CrossRef CAS PubMed.
- J. Zhou, N. K. Guimard, A. J. Inglis, M. Namazian, C. Y. Lin, M. L. Coote, E. Spyrou, S. Hilf, F. G. Schmidt and C. Barner-Kowollik, Polym. Chem., 2012, 3, 628–639 RSC.
- M. Langer, J. Brandt, A. Lederer, A. S. Goldmann, F. H. Schacher and C. Barner-Kowollik, Polym. Chem., 2014, 5, 5330–5338 RSC.
- A. J. Inglis, L. Nebhani, O. Altintas, F. G. Schmidt and C. Barner-Kowollik, Macromolecules, 2010, 43, 5515–5520 CrossRef CAS.
- C. J. Dürr, L. Hlalele, A. Kaiser, S. Brandau and C. Barner-Kowollik, Macromolecules, 2013, 46, 49–62 CrossRef.
- L. Nebhani, S. Sinnwell, A. J. Inglis, M. H. Stenzel, C. Barner-Kowollik and L. Barner, Macromol. Rapid Commun., 2008, 29, 1431–1437 CrossRef CAS.
- A. S. Goldmann, T. Tischer, L. Barner, M. Bruns and C. Barner-Kowollik, Biomacromolecules, 2011, 12, 1137–1145 CrossRef CAS PubMed.
- H. Dentel, I. Chataigner, F. Le Cavelier and M. Gulea, Tetrahedron Lett., 2010, 51, 6014–6017 CrossRef CAS.
- T. Paulöhrl, A. J. Inglis and C. Barner-Kowollik, Adv. Mater., 2010, 22, 2788–2791 CrossRef PubMed.
- M. Glassner, J. P. Blinco and C. Barner-Kowollik, Polym. Chem., 2011, 2, 83–87 RSC.
- M. Chen, G. Moad and E. Rizzardo, Aust. J. Chem., 2011, 64, 433–437 CrossRef CAS.
- L. Tao, J. Liu, J. Xu and T. P. Davis, Org. Biomol. Chem., 2009, 7, 3481–3485 Search PubMed.
- C. Li, J. Han, C. Y. Ryu and B. C. Benicewicz, Macromolecules, 2006, 39, 3175–3183 CrossRef CAS.
- J. Liu, W. Yang, H. M. Zareie, J. J. Gooding and T. P. Davis, Macromolecules, 2009, 42, 2931–2939 CrossRef CAS.
- J. Xu, L. Tao, J. Liu, V. Bulmus and T. P. Davis, Macromolecules, 2009, 42, 6893–6901 CrossRef CAS.
- J. Xu, L. Tao, C. Boyer, A. B. Lowe and T. P. Davis, Macromolecules, 2010, 43, 20–24 CrossRef CAS.
- K. T. Wiss and P. Theato, J. Polym. Sci., Part A: Polym. Chem., 2010, 48, 4758–4767 CrossRef CAS.
- P. J. Roth, K. T. Wiss, R. Zentel and P. Theato, Macromolecules, 2008, 41, 8513–8519 CrossRef CAS.
- P. J. Roth, D. Kessler, R. Zentel and P. Theato, J. Polym. Sci., Part A: Polym. Chem., 2009, 47, 3118–3130 CrossRef CAS.
- Q. Zheng and C. Y. Pan, Macromolecules, 2005, 38, 6841–6848 CrossRef CAS.
- Q. Zheng and C. Y. Pan, Eur. Polym. J., 2006, 42, 807–814 CrossRef CAS.
- M. Bathfield, F. D'Agosto, R. Spitz, M. T. Charreyre and T. Delair, J. Am. Chem. Soc., 2006, 128, 2546–2547 CrossRef CAS PubMed.
- A. M. dos Santos, J. Pohn, M. Lansalot and F. D'Agosto, Macromol. Rapid Commun., 2007, 28, 1325–1332 CrossRef CAS.
- K. Yuan, Z. F. Li, L. L. Lu and X. N. Shi, Mater. Lett., 2007, 61, 2033–2036 CrossRef CAS.
- K. Yuan, L.-L. Lu, Z.-F. Li and X.-N. Shi, Chin. J. Chem., 2008, 26, 1929–1934 CrossRef CAS.
- R. Briquel, J. Mazzolini, T. L. Bris, O. Boyron, F. Boisson, F. Delolme, F. D'Agosto, C. Boisson and R. Spitz, Angew. Chem., Int. Ed., 2008, 47, 9311–9313 CrossRef CAS PubMed.
- P. Sun, Y. Zhang, L. Shi and Z. Gan, Macromol. Biosci., 2010, 10, 621–631 CrossRef CAS PubMed.
- X. Jiang, A. Housni, G. Gody, P. Boullanger, M.-T. Charreyre, T. Delair and R. Narain, Bioconjugate Chem., 2010, 21, 521–530 CrossRef CAS PubMed.
- S. Demirci, S. Kinali-Demirci and T. Caykara, J. Polym. Sci., Part A: Polym. Chem., 2013, 51, 1612–1619 CrossRef CAS.
- H. Yang, F. Liang, X. Wang, Y. Chen, C. Zhang, Q. Wang, X. Qu, J. Li, D. Wu and Z. Yang, Macromolecules, 2013, 46, 2754–2759 CrossRef CAS.
- Q. Li, K. Yang, Y. Liang, B. Jiang, J. Liu, L. Zhang, Z. Liang and Y. Zhang, ACS Appl. Mater. Interfaces, 2014, 6, 21954–21960 Search PubMed.
- D. Togashi, I. Otsuka, R. Borsali, K. Takeda, K. Enomoto, S. Kawaguchi and A. Narumi, Biomacromolecules, 2014, 15, 4509–4519 CrossRef CAS PubMed.
- N. J. Warren, O. O. Mykhaylyk, D. Mahmood, A. J. Ryan and S. P. Armes, J. Am. Chem. Soc., 2014, 136, 1023–1033 CrossRef CAS PubMed.
- N. J. Warren, J. Rosselgong, J. Madsen and S. P. Armes, Biomacromolecules, 2015, 16, 2514–2521 CrossRef CAS PubMed.
- T. Koga, E. Aso and N. Higashi, Langmuir, 2016 DOI:10.1021/acs.langmuir.6b01617.
- A. H. Alidedeoglu, C. A. Harris, N. Martinez-Castro, A. W. York, C. L. McCormick and S. E. Morgan, ACS Symp. Ser., 2010, 1053, 113–129 CrossRef CAS.
- P. V. Mendonça, A. C. Serra, A. V. Popov, T. Guliashvili and J. F. J. Coelho, React. Funct. Polym., 2014, 81, 1–7 CrossRef.
- K. Zhang, L. Gao and Y. Chen, Polymer, 2010, 51, 2809–2817 CrossRef CAS.
- M. Müllner, A. Schallon, A. Walther, R. Freitag and A. H. E. Müller, Biomacromolecules, 2010, 11, 390–396 CrossRef PubMed.
- S. R. S. Ting, A. M. Granville, D. Quemener, T. P. Davis, M. H. Stenzel and C. Barner-Kowollik, Aust. J. Chem., 2007, 60, 405–409 CrossRef CAS.
- D. Quemener, T. P. Davis, C. Barner-Kowollik and M. H. Stenzel, Chem. Commun., 2006, 5051–5053 RSC.
- H. Liu, W. Pan, M. Tong and Y. Zhao, Polym. Chem., 2016, 7, 1603–1611 RSC.
- R. K. O'Reilly, M. J. Joralemon, C. J. Hawker and K. L. Wooley, J. Polym. Sci., Part A: Polym. Chem., 2006, 44, 5203–5217 CrossRef.
- R. P. Johnson, S. Uthaman, J. V. John, H. R. Lee, S. J. Lee, H. Park, I.-K. Park, H. Suh and I. Kim, ACS Appl. Mater. Interfaces, 2015, 7, 21770–21779 Search PubMed.
- S. Singh, R. K. Gundampati, K. Mitra, K. Ramesh, M. V. Jagannadham, N. Misra and B. Ray, RSC Adv., 2015, 5, 81994–82004 RSC.
- V. K. Patel, N. K. Vishwakarma, A. K. Mishra, C. S. Biswas, P. Maiti and B. Ray, J. Appl. Polym. Sci., 2013, 127, 4305–4317 CrossRef CAS.
- A. Hanisch, H. Schmalz and A. H. E. Müller, Macromolecules, 2012, 45, 8300–8309 CrossRef CAS.
- Y.-S. Ye, Y.-N. Chen, J.-S. Wang, J. Rick, Y.-J. Huang, F.-C. Chang and B.-J. Hwang, Chem. Mater., 2012, 24, 2987–2997 CrossRef CAS.
- S. R. Gondi, A. P. Vogt and B. S. Sumerlin, Macromolecules, 2007, 40, 474–481 CrossRef CAS.
- A. S. Goldmann, D. Quemener, P. E. Millard, T. P. Davis, M. H. Stenzel, C. Barner-Kowollik and A. H. E. Muller, Polymer, 2008, 49, 2274–2281 CrossRef CAS.
- M. Li, P. De, S. R. Gondi and B. S. Sumerlin, Macromol. Rapid Commun., 2008, 29, 1172–1176 CrossRef CAS.
- P. De, S. R. Gondi and B. S. Sumerlin, Biomacromolecules, 2008, 9, 1064–1070 CrossRef CAS PubMed.
- E. Soto-Cantu, B. S. Lokitz, J. P. Hinestrosa, C. Deodhar, J. M. Messman, J. F. Ankner and S. M. Kilbey Ii, Langmuir, 2011, 27, 5986–5996 CrossRef CAS PubMed.
- V. K. Patel, N. K. Vishwakarma, S. Singh, K. Mitra, K. Ramesh, N. Mishra and B. Ray, Int. J. Polym. Mater. Polym. Biomater., 2016, 65, 269–276 CrossRef CAS.
- K. Ramesh, S. Singh, K. Mitra, D. Chattopadhyay, N. Misra and B. Ray, Colloid Polym. Sci., 2016, 294, 399–407 Search PubMed.
- G. Gody, C. Rossner, J. Moraes, P. Vana, T. Maschmeyer and S. Perrier, J. Am. Chem. Soc., 2012, 134, 12596–12603 CrossRef CAS PubMed.
- J. C. Brendel, G. Gody and S. Perrier, Polym. Chem., 2016, 7, 5536–5543 RSC.
- S. P. Le-Masurier, G. Gody, S. Perrier and A. M. Granville, Polym. Chem., 2014, 5, 2816–2823 RSC.
- Z. Zhang, M.-L. Chen, X.-D. Cheng, Z.-G. Shi, B.-F. Yuan and Y.-Q. Feng, J. Chromatogr., A, 2014, 1351, 96–102 CrossRef CAS PubMed.
- S. P. Le-Masurier, H. T. T. Duong, C. Boyer and A. M. Granville, Polym. Chem., 2015, 6, 2504–2511 RSC.
- J. Zhao, Y. Zhou, Y. Zhou, N. Zhou, X. Pan, Z. Zhang and X. Zhu, Polym. Chem., 2016, 7, 1782–1791 RSC.
- Y. Jiang, H. Lu, F. Chen, M. Callari, M. Pourgholami, D. L. Morris and M. H. Stenzel, Biomacromolecules, 2016, 17, 808–817 CrossRef CAS PubMed.
- D. Chang, C. N. Lam, S. Tang and B. D. Olsen, Polym. Chem., 2014, 5, 4884–4895 RSC.
- K. N. R. Wuest, V. Trouillet, A. S. Goldmann, M. H. Stenzel and C. Barner-Kowollik, Macromolecules, 2016, 49, 1712–1721 CrossRef CAS.
- P. Lederhose, K. N. R. Wust, C. Barner-Kowollik and J. P. Blinco, Chem. Commun., 2016, 52, 5928–5931 RSC.
- J. P. Magnusson, A. O. Saeed, F. Fernandez-Trillo and C. Alexander, Polym. Chem., 2011, 2, 48–59 RSC.
- I. Mitra, X. Li, S. L. Pesek, B. Makarenko, B. S. Lokitz, D. Uhrig, J. F. Ankner, R. Verduzco and G. E. Stein, Macromolecules, 2014, 47, 5269–5276 CrossRef CAS.
- M. M. Stamenović, P. Espeel, W. V. Camp and F. E. Du Prez, Macromolecules, 2011, 44, 5619–5630 CrossRef.
- D. L. Patton and R. C. Advincula, Macromolecules, 2006, 39, 8674–8683 CrossRef CAS.
- A. Postma, T. P. Davis, G. Li, G. Moad and M. O'Shea, Macromolecules, 2006, 39, 5307–5318 CrossRef CAS.
- J. Jacobs, N. Gathergood and A. Heise, Macromol. Rapid Commun., 2013, 34, 1325–1329 CrossRef CAS PubMed.
- A. Postma, T. P. Davis, R. A. Evans, G. Li, G. Moad and M. O'Shea, Macromolecules, 2006, 39, 5293–5306 CrossRef CAS.
- S. Wallyn, Z. Zhang, F. Driessen, J. Pietrasik, B. G. De Geest, R. Hoogenboom and F. E. Du Prez, Macromol. Rapid Commun., 2014, 35, 405–411 CrossRef CAS PubMed.
- J. Rieger, T. Antoun, S.-H. Lee, M. Chenal, G. Pembouong, J. Lesage de la Haye, I. Azcarate, B. Hasenknopf and E. Lacôte, Chem. – Eur. J., 2012, 18, 3355–3361 CrossRef CAS PubMed.
- B. E. B. Jensen, A. A. A. Smith, B. Fejerskov, A. Postma, P. Senn, E. Reimhult, M. Pla-Roca, L. Isa, D. S. Sutherland, B. Städler and A. N. Zelikin, Langmuir, 2011, 27, 10216–10223 CrossRef CAS PubMed.
- A. A. A. Smith, T. Hussmann, J. Elich, A. Postma, M.-H. Alves and A. N. Zelikin, Polym. Chem., 2012, 3, 85–88 RSC.
- A. N. Zelikin, G. K. Such, A. Postma and F. Caruso, Biomacromolecules, 2007, 8, 2950–2953 CrossRef CAS PubMed.
- M. B. L. Kryger, A. A. A. Smith, B. M. Wohl and A. N. Zelikin, Macromol. Biosci., 2014, 14, 173–185 CrossRef CAS PubMed.
- V. Vázquez-Dorbatt, Z. P. Tolstyka and H. D. Maynard, Macromolecules, 2009, 42, 7650–7656 CrossRef PubMed.
- G. N. Grover, J. Lee, N. M. Matsumoto and H. D. Maynard, Macromolecules, 2012, 45, 4958–4965 CrossRef CAS PubMed.
Footnote |
† Electronic supplementary information (ESI) available. See DOI: 10.1039/c6py01849a |
|
This journal is © The Royal Society of Chemistry 2017 |
Click here to see how this site uses Cookies. View our privacy policy here.