DOI:
10.1039/C6QM00277C
(Research Article)
Mater. Chem. Front., 2017,
1, 1217-1222
Composition-controllable synthesis of defect-rich PtPdCu nanoalloys with hollow cavities as superior electrocatalysts for alcohol oxidation†
Received
25th October 2016
, Accepted 30th December 2016
First published on 30th January 2017
Abstract
Preparing defect-rich Pt-based nanocatalysts for alcohol fuel cell applications remains a huge challenge. Here, we introduce a facile, environmentally friendly, one-pot approach to synthesize trimetallic PtPdCu nanoalloys with hollow cavities and numerous defects, such as lower coordination atoms, corners, interior boundaries, lattice disorders and dislocations and twin boundaries. The as-synthesized Pt34Pd33Cu33 nanoalloys exhibit excellent electrocatalytic properties for alcohol oxidation in acidic medium. The peak current density of the Pt34Pd33Cu33 nanoalloys is, respectively, 2.2 times (for methanol), 1.2 times (for ethanol) and 2.1 times (for glycol) that on commercial Pt black. Furthermore, after 1000 cycles, the current density of the Pt34Pd33Cu33 nanoalloys is 2.4 times (for methanol), 1.8 times (for ethanol) and 3.0 times (for glycol) that on commercial Pt black.
1. Introduction
Today, Pt-based nanoalloys are being paid increasing attention because of their enhanced catalytic activity and durability compared with pure Pt nanocrystals for fuel cell applications.1–5 It is well known that the catalytic properties of Pt-based nanoalloys are strongly dependent not only on their size and shape, but also on their composition and structure (hollow or solid).6–10 Moreover, alloying Pt with a cheaper metal can not only lower the cost of the catalyst, but also improve the catalytic performance owing to synergistic effects and electronic effects.11–15 The pioneer research shows that each transition metal (e.g., Pd, Cu and Ni) can tailor the electrocatalytic behavior when alloyed with Pt and improve the electrocatalytic performance of Pt-based nanoalloys.16–22 For this reason, it would be worth investigating the engineering of more complex alloy compositions, such as from bimetallic nanoalloys to trimetallic nanoalloys.
Besides the composition, the electrocatalytic reaction is also very sensitive to the structure (e.g., hollow or solid) of metal nanoalloys.23–27 Among the Pt-based nanoalloys, hollow structures have many merits, such as saving material, lowering the cost of the catalyst and low density, and have attracted a lot of attention because of their distinctly different properties compared to their solid counterparts. To this end, building an effective synthetic strategy for engineering trimetallic nanoalloys with a hollow structure is of great significance. Furthermore, controlling the composition of trimetallic hollow nanoalloys would provide a platform to investigate the relationship between composition and electrocatalytic properties.
Currently, the template-assisted method is the most commonly used to acquire hollow metal structures.28–32 To the best of our knowledge, to date no synthesis methods have been reported for trimetallic hollow PtPdCu nanoalloys without prefabricated templates. Herein, for the first time, we report the synthesis of composition-controllable trimetallic PtPdCu nanoalloys with hollow cavities and numerous defects through an environmentally friendly aqueous-phase process using cetyltrimethylammonium chloride (CTAC), citric acid and ascorbic acid (AA) as a surfactant and reductant, respectively (see the ESI† for details). The as-synthesized PtPdCu nanoalloys displayed composition-dependent properties toward methanol, ethanol and glycol electrooxidation in acidic medium. Among them, Pt34Pd33Cu33 exhibited enhanced specific activity and durability compared with commercial Pt black.
2. Results and discussion
Fig. 1a–c show the representative transmission electron microscopic (TEM) images of the as-synthesized trimetallic Pt34Pd33Cu33 (the composition was determined by ICP-OES) nanocrystals with a feeding molar ratio of H2PtCl6
:
K2PdCl4
:
CuCl2 of 1
:
1
:
1. The composition of the as-synthesized trimetallic Pt34Pd33Cu33 nanocrystals is in accordance with the feed ratio of metal precursors (Table S1, ESI†), which implies that the metal precursors are almost quantitatively converted. The size of the trimetallic Pt34Pd33Cu33 nanocrystals has a narrow distribution, from 35 to 52 nm. On the other hand, there are many hollow cavities dispersed in the nanocrystals, which is also confirmed by the high-angle annular dark-field scanning transmission electron microscopic (HAADF-STEM) image (Fig. 1b, inset). Upon careful observation of Fig. 1c, we can notice that the trimetallic Pt34Pd33Cu33 nanocrystals consist of many small grains, and the size of most of the small grains is below 5.0 nm. On the other hand, the small grains are interconnected, thus leading to formation of hollow cavities. Furthermore, the energy-dispersive X-ray (EDX) spectra also confirm that the as-synthesized nanoparticles are made of Pt, Pd and Cu (Fig. 1d). From Fig. 1e and Fig. S1, ESI,† well-resolved lattice fringes are clearly observed in the nanoparticles. The distance between the lattice fringes was measured to be 0.22 nm, which matches well with the (111) lattice spacing of face-centered cubic (fcc) Pt (0.227 nm; JCPDS-65-2868)/Pd (0.225 nm; JCPDS-65-2867)/Cu (0.209 nm; JCPDS-04-0836). Moreover, the surface of the PtPdCu nanocrystals is very rough and has many defects such as lower coordination atoms, corners and interior boundaries. These defects can act as highly active catalytic sites in catalytic reactions.33–38
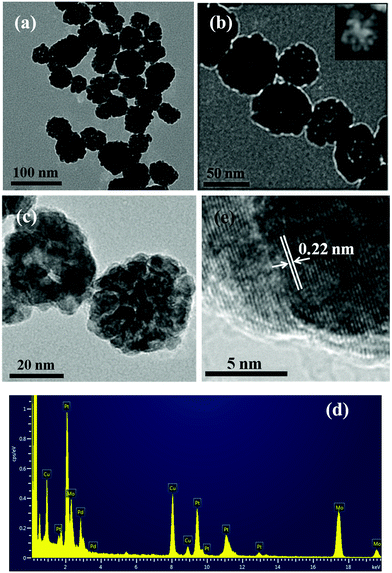 |
| Fig. 1 TEM (a–c) and HRTEM (e) images, and EDX spectra (d) of the as-synthesized Pt34Pd33Cu33 nanoalloys. (The inset in Fig. 1b is the HAADF-STEM image. The signals of Mo come from the Mo grid.) | |
The structure and element distribution of the as-synthesized trimetallic Pt34Pd33Cu33 nanocrystals were characterized by X-ray diffraction (XRD), EDX line scanning and EDX element mapping. The XRD spectra (Fig. 2a) of the as-synthesized product showed four peaks corresponding to the (111), (200), (220) and (311) planes of fcc Pt/Pd/Cu (Pt: JCPDS-65-2868; Pd: JCPDS-65-2867; Cu: JCPDS-04-0836). The XRD peaks shifted to a higher angle because of the incorporation of Cu atoms into the Pt/Pd fcc lattice, and the peaks between the Pt standard value, Pd standard value and the Cu standard value showed no single Pt, Pd and Cu peak, which indicated that the as-synthesized trimetallic PtPdCu nanoparticles are alloy structures. The results of EDX line-scan analysis (Fig. 2b) show that the compositional line profiles of Pt, Pd and Cu on the Pt34Pd33Cu33 nanocrystals consecutively vary without any segregation of each component, which implies that the nanocrystal is indeed a PtPdCu alloy. Besides, the signals of Pt, Pd and Cu fluctuate along the scanning direction, which indicates that the Pt, Pd and Cu atoms are randomly distributed in the trimetallic alloys. On the other hand, HAADF-STEM–EDX elemental mapping of Pt, Pd and Cu was used to reveal the distribution of Pt, Pd and Cu in the as-synthesized PtPdCu nanocrystals. The full coverage of Pt, Pd and Cu (Fig. 2c) in the whole particle also shows the alloy structure of the as-synthesized PtPdCu nanocrystals. Furthermore, the composition of the trimetallic PtPdCu alloys can be tuned by changing the ratio of metal precursors while maintaining the hollow cavity shape (Fig. S2, ESI†).
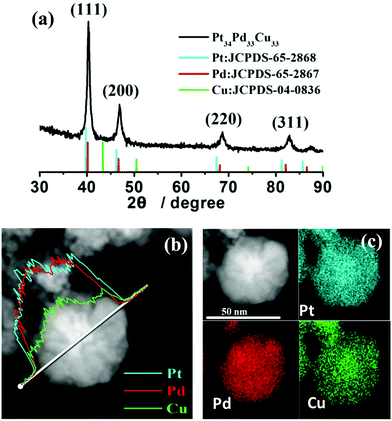 |
| Fig. 2 XRD pattern (a), HADDF-STEM images and corresponding EDX line scanning profiles (b) and EDX elemental mapping (c) of the as-synthesized Pt34Pd33Cu33 nanoalloys. | |
The role of the metal precursors and surfactants was investigated in the synthesis of the trimetallic PtPdCu alloys with hollow cavities. In the current synthetic approach, for pure Pt (Fig. S3a, ESI†) or Pd (Fig. S3b, ESI†), the product consisted of irregular polyhedral nanocrystals and no hollow cavity structure, and the size of these polyhedral nanocrystals is not uniform. In the presence of Pd and Cu precursors, the product also consisted of irregular, non-uniform polyhedral nanocrystals without hollow cavities (Fig. S3c, ESI†). In the presence of Pt and Pd precursors or Pt and Cu precursors, the product consisted of porous nanocrystals (Fig. S3d and e, ESI†). In the absence of CTAC, the product was made up of spherical nanoparticles without hollow cavities (Fig. S3f, ESI†), which implied that CTAC was a key factor to obtain trimetallic PtPdCu nanoalloys with hollow cavities. In the absence of citric acid, the product was made up of irregular particles (Fig. S3g, ESI†). In the absence of ascorbic acid, the product was made up of aggregates of small grains (Fig. S3h, ESI†). Without citric acid and ascorbic acid, no product can be acquired, which means that citric acid and ascorbic acid act as reducing agents in the current system.
The electrocatalytic properties of the as-synthesized trimetallic PtPdCu nanoalloys toward alcohol (methanol and ethanol, glycol) oxidation have been investigated in acidic media. For comparison, the electrocatalytic properties of commercial Pt black were also tested. The specific current was normalized by the electrochemical surface area (ECSA) calculated by measuring the charge collected in the hydrogen adsorption–desorption region and assuming a value of 210 μC cm−2, which corresponds to the intrinsic catalytic activity of the catalyst. From Fig. S4, ESI,† we can see that the as-synthesized PtPdCu trimetallic nanoalloys displayed a composition-dependent property toward methanol, ethanol and glycol oxidation. Among them, Pt34Pd33Cu33 exhibited the best activity. It is well known that the alcohol oxidation reaction is a structure-sensitive reaction.39–42 Thus, the composition change of the trimetallic PtPdCu nanoalloys easily leads to activity variation, although they have similar morphology. The peak current densities of the Pt34Pd33Cu33 nanoalloys were, respectively, 4.18 mA cm−2 (for methanol, peaked at 0.6 V; Fig. 3a), 1.13 mA cm−2 (for ethanol, peaked at 0.70 V; Fig. 3c) and 1.09 mA cm−2 (for glycol, peaked at 0.63 V; Fig. 3e) and the peak current densities of commercial Pt black were 2.03 mA cm−2 (for methanol, peaked at 0.73 V), 0.93 mA cm−2 (for ethanol, peaked at 0.70 V) and 0.51 mA cm−2 (for glycol, peaked at 0.63 V), which showed that the catalytic activity of the as-synthesized Pt34Pd33Cu33 nanoalloys was obviously superior to that of commercial Pt black. And the onset potential (Fig. S5, ESI†) for methanol, ethanol and glycol oxidation on the Pt34Pd33Cu33 nanoalloys was lower that on commercial Pt black, which implies faster reaction kinetics toward methanol, ethanol and glycol oxidation. Moreover, at 0.5 V, the specific activity of the Pt34Pd33Cu33 nanoalloys/commercial Pt black toward methanol, ethanol and glycol oxidation is 3.29/0.69 mA cm−2, 0.31/0.25 mA cm−2 and 0.50/0.30 mA cm−2, respectively. The enhancement in activity for the Pt34Pd33Cu33 nanoalloys may be ascribed to the unique structure assembled by sub-5.0 nm particles that have many low coordination atoms, corners, and interconnected interfaces originating from the interconnection between the sub-5.0 nm particles (Fig. 1c). Besides, there are many other defects on the surface of the as-synthesized Pt34Pd33Cu33 nanoalloys. Lattice disorders and dislocations and twin boundaries have been locally observed in Fig. 5a and b respectively, highlighting the existence of abundant defects on the crystal surface, which can act as the catalytic active sites in catalytic reactions.43,44 On the other hand, for Pt-based nanoalloys, the possible synergistic effect between Pt and the exotic metal atoms was also another important factor for improving the catalytic activity.45,46Fig. 6 shows the XPS spectra of Pt 4f, Pd 3d and Cu 2p for the as-synthesized Pt34Pd33Cu33 nanoalloys, which show that metallic Pt, Pd and Cu atoms coexist on the surface of the Pt34Pd33Cu33 nanoalloys. On the other hand, as shown in Fig. S6, ESI,† the specific activity of the Pt34Pd33Cu33 nanoalloys is superior to that of the as-synthesized Pt, PtPd and PtCu samples and the specific activities of PtPd and PtCu are superior to that of pure Pt, which also indicates the synergistic effect between Pt and Pd and Cu. Furthermore, the hollow cavities (Fig. 1a–c) of the Pt34Pd33Cu33 nanoalloys can act as “nano reaction pools” for all the fuel molecules entering in a nano range, which helps in increasing the catalytic activity of the catalyst.47,48 Furthermore, we also compare the mass activity of Pt34Pd33Cu33 nanoalloys and commercial Pt black. The mass activity of the Pt34Pd33Cu33 nanoalloys/commercial Pt black toward methanol, ethanol and glycol oxidation is 0.66/0.47 A mg−1 Pt (Fig. 4a), 0.18/0.19 A mg−1 Pt (Fig. 4b) and 0.17/0.11 A mg−1 Pt (Fig. 4c), respectively. The mass activity of the Pt34Pd33Cu33 nanoalloys is obviously higher than that of commercial Pt black toward methanol and glycol oxidation and is almost the same as commercial Pt black toward ethanol oxidation. Moreover, we deduce that the mass activity could be increased if the size of the trimetallic PtPdCu catalyst particles could be reduced in some way.
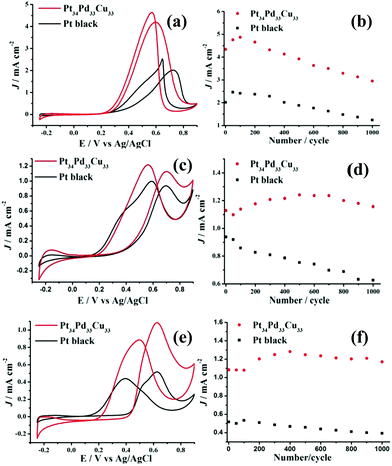 |
| Fig. 3 The cyclic voltammetric curves (CVs) of the as-synthesized Pt34Pd33Cu33 nanoalloys and the commercial Pt black for glycol oxidation with a scan rate of 50 mV s−1 at room temperature (a) in 0.1 M HClO4 + 0.5 M methanol solution, (c) in 0.1 M HClO4 + 0.5 M ethanol solution and (e) in 0.1 M HClO4 + 0.5 M glycol solution. The durability performance of the Pt34Pd33Cu33 nanoalloys and commercial Pt black (b) in 0.1 M HClO4 + 0.5 M methanol solution, (d) in 0.1 M HClO4 + 0.5 M ethanol solution and (f) in 0.1 M HClO4 + 0.5 M glycol solution. | |
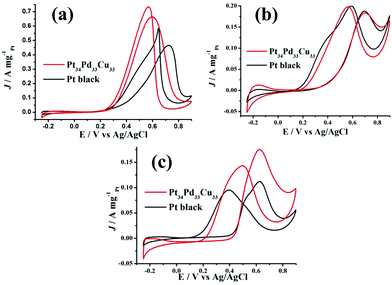 |
| Fig. 4 Mass activity of the Pt34Pd33Cu33 nanoalloys and commercial Pt black (a) in 0.1 M HClO4 + 0.5 M methanol solution, (b) in 0.1 M HClO4 + 0.5 M ethanol solution and (c) in 0.1 M HClO4 + 0.5 M glycol solution. | |
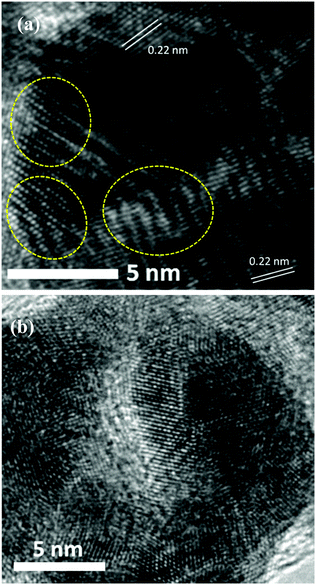 |
| Fig. 5 HRTEM images (a and b) of the as-synthesized Pt34Pd33Cu33 nanoalloys. The lattice disorders induced by defects are marked by yellow cycles. | |
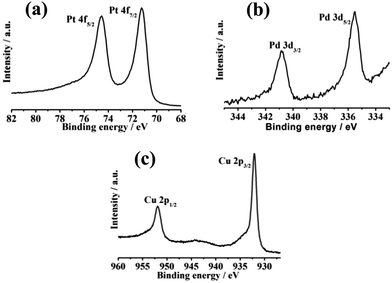 |
| Fig. 6 XPS of the as-synthesized Pt34Pd33Cu33 nanoalloys. (a) Pt 4f region, (b) Pd 3d region and (c) Cu 2p region. | |
The stability of the as-synthesized Pt34Pd33Cu33 nanoalloys has been investigated compared with that of commercial Pt black. As can be seen in Fig. S7, ESI,† after 1200 s, the remaining current density value of the Pt34Pd33Cu33 nanoalloys is higher than that of commercial Pt black for methanol and glycol oxidation. While for ethanol oxidation, the remaining current density value of the Pt34Pd33Cu33 nanoalloys is lower than that of commercial Pt black. These results show that the tolerance to poisoning of the Pt34Pd33Cu33 nanoalloys is better for methanol and glycol oxidation and worse for ethanol oxidation than commercial Pt black. The results maybe explained using the ratio of forward and backward current densities (If/Ib) of the Pt34Pd33Cu33 nanoalloys because the value of If/Ib is often used to evaluate the anti-poisoning ability for alcohol oxidation.45,49 The value of If/Ib of the Pt34Pd33Cu33 nanoalloys is 0.90 (for methanol), 0.92 (for ethanol) and 1.24 (for glycol) and that of commercial Pt black is 0.80 (for methanol), 0.94 (for ethanol) and 1.18 (for glycol), respectively. The durability of the as-synthesized Pt34Pd33Cu33 nanoalloys was much better than commercial Pt black. After 1000 cycles, the current density value of the Pt34Pd33Cu33 nanoalloys was 2.4 times (for methanol, Fig. 3b), 1.8 times (for ethanol, Fig. 3d) and 3.0 times (for glycol, Fig. 3f) that on commercial Pt black (Fig. S8, ESI†). On the other hand, after 1000 cycles, the peak potential of the Pt34Pd33Cu33 nanoalloys/commercial Pt black toward methanol, ethanol and glycol oxidation is, respectively, 0.63/0.72 V, 0.72/0.71 V and 0.63/0.63 V (Fig. S9, ESI†). Moreover, most of the Pt34Pd33Cu33 nanoalloys can maintain their hollow cavity structure after the 1000 cycle test (Fig. S10, ESI†). The difference in the catalytic properties of the Pt34Pd33Cu33 nanoalloys toward methanol, ethanol and glycol oxidation maybe ascribed to the different structure of methanol, ethanol and glycol molecules and different oxidation mechanisms.50–52 For example, methanol, ethanol and glycol oxidation, respectively, involve 6 electrons, 12 electrons and 10 electrons for complete oxidation to CO2. Also, for ethanol and glycol oxidation, the C–C bond needs to be broken.
3. Conclusion
In conclusion, composition-controllable trimetallic PtPdCu nanoalloys with hollow cavities have been synthesised by a facile aqueous solution approach. These PtPdCu nanoalloys demonstrated composition-dependent catalytic properties toward alcohol (methanol, ethanol and glycol) oxidation in acidic medium. Among them, the Pt34Pd33Cu33 nanoalloys displayed the best catalytic performance because of their numerous defects existing on the surface of the nanoalloys, hollow cavities and possible synergistic effects between Pt, Pd and Cu. In comparison with commercial Pt black, the peak current density of the as-synthesized Pt34Pd33Cu33 nanoalloys is 2.2 times (for methanol), 1.2 times (for ethanol) and 2.1 times (for glycol) that on commercial Pt black. The stability of the as-synthesized Pt34Pd33Cu33 nanoalloys is superior to commercial Pt black for methanol and glycol oxidation. Besides, the durability of the as-synthesized Pt34Pd33Cu33 nanoalloys was much better than that of commercial Pt black. This work thus provides an example to prepare trimetallic PtPdCu nanoalloys with numerous defects and hollow cavities for alcohol fuel cell applications.
4. Experimental
4.1 Chemicals
Chloroplatinic acid hydrate (99.9%), palladium chloride (99.9%), cupric chloride (99.99%), potassium chloride (99%), cetyltrimethylammonium chloride (97%) and citric acid monohydrate (99%) were purchased from Sigma-Aldrich. L-Ascorbic acid (99.7%) was purchased from Kermel. Pt black was purchased from Johnson Matthey. Chemicals were used as received without further purification. Super pure water (18 MΩ cm) was used as a solvent. 0.1 M of K2PdCl4 aqueous solution was prepared by adding 0.313 g (4.0 mmol) of KCl and 0.354 g (2.0 mmol) of PdCl2 into 20 mL of water and stirring for 40 minutes. Then this solution was left without stirring for a whole day before it was used.
4.2 Synthesis of PtPdCu nanoalloys
In a typical synthesis, a total of 0.9 mL of 0.1 M K2PdCl4, 0.1 M H2PtCl6 and 0.1 M CuCl2 aqueous solution was added with a ratio of Pt, Pd and Cu of 1
:
1
:
1 (marked as Pt34Pd33Cu33), 3
:
2
:
4 (marked as Pt41Pd22Cu37) and 2
:
4
:
3 (marked as Pt30Pd41Cu29) to 9.1 mL of aqueous solution containing 0.256 g of cetyltrimethylammonium chloride (CTAC) and 0.210 g of citric acid (CA), and stirred several minutes. Then 0.03 g of ascorbic acid (AA) was added into the aqueous solution and stirred for 20 minutes. Then the resulting emulsion-like solution was transferred to a 15 mL Teflon-lined stainless-steel autoclave. The sealed vessel was then heated at 190 °C for 4 h before it was cooled to room temperature. The products were separated via centrifugation/washing cycles at 9000 rpm for 10 minutes and treated three times with ethanol. The collected product was redispersed in ethanol.
4.3 Characterization
The TEM images of the samples were acquired with an FEI Tecnai T12 (120 kV). HRTEM, energy-dispersive X-ray spectroscopy (EDX), high-angle annular dark field scanning TEM (HAADF-STEM) and elemental line scanning were performed with an FEI Titan 80 (300 kV). The SEM images of the samples were examined with an FEI Magellan TEGSEM. X-ray diffraction (XRD) patterns of the samples were recorded on a Bruker D8 Advance diffractometer with CuKa radiation (l = 1.5418 Å) with a graphite monochromator (40 kV, 40 mA). X-ray photoelectron spectroscopy (XPS) measurements were performed using a PHI Quantum 2000 Scanning ESCA Microprobe (Physical Electronics, USA), using AlKa X-ray radiation (1486.6 eV) for excitation. The inductively coupled plasma optical emission spectrometry (ICP-OES) analysis of the samples was performed on an IRIS Intrepid II XSP (ThermoFisher).
4.4 Characterization of electrocatalytic activity
Electrochemical experiments were carried out in a standard three-electrode cell at room temperature (25 °C) controlled by a CHI 630E electrochemical analyzer (CHI Instruments, Shanghai, Chenghua Co., Ltd). Ethanol (99.7%) was used as a solvent. The working electrode is a glassy carbon (GC, Φ = 5 mm) electrode embedded into a Teflon holder. Prior to the electrochemical test, the GC electrode was mechanically polished successively using alumina powder of size 1.5, 1, and 0.5 μm. It was then cleaned in an ultrasonic bath. The suspension of the PtPdCu nanoalloys or Pt black was spread on the GC electrode. As soon as the electrode was dried under an infrared lamp, 10 μL Nafion diluents in a 0.5 wt% Nafion® solution were coated onto the electrode surface. An Ag/AgCl electrode and platinum foil were used as the reference and counter electrode, respectively.
Acknowledgements
This work was supported by the National Natural Science Foundation of China (21361005, 21571038, 91127040 and 21221062).
Notes and references
- H. Liu, F. Nosheen and X. Wang, Chem. Soc. Rev., 2015, 44, 3056–3078 RSC.
- X. Sun, D. Li, Y. Ding, W. Zhu, S. Guo, Z. L. Wang and S. Sun, J. Am. Chem. Soc., 2014, 136, 5745–5749 CrossRef CAS PubMed.
- Y. Kuang, Z. Cai, Y. Zhang, D. He, X. Yan, Y. Bi, Y. Li, Z. Li and X. Sun, ACS Appl. Mater. Interfaces, 2014, 6, 17748–17752 CAS.
- A. Chen and P. Holt-Hindle, Chem. Rev., 2010, 110, 3767–3804 CrossRef CAS PubMed.
- L. Zou, J. Fan, Y. Zhou, C. Wang, J. Li, Z. Zou and H. Yang, Nano Res., 2015, 8, 2777–2788 CrossRef CAS.
- J. Ding, L. Bu, S. Guo, Z. Zhao, E. Zhu, Y. Huang and X. Huang, Nano Lett., 2016, 16, 2762–2767 CrossRef CAS PubMed.
- W. Hong, J. Wang and E. Wang, Nano Res., 2015, 8, 2308–2316 CrossRef CAS.
- F. Nosheen, Z. C. Zhang, G. L. Xiang, B. Xu, Y. Yang, X. B. Xu, J. C. Zhang and X. Wang, Nano Res., 2015, 8, 832–838 CrossRef CAS.
- Q. Chen, Y. Yang, Z. Cao, Q. Kuang, G. Du, Y. Jiang, Z. Xie and L. Zheng, Angew. Chem., Int. Ed., 2016, 55, 9021–9025 CrossRef CAS PubMed.
- L. S. Mo, Q. Qin, X. Zhao and N. Zheng, Small, 2016, 12, 1572–1577 CrossRef PubMed.
- J. Ryu, J. Choi, D. H. Lim, H. L. Seo, S. Y. Lee, Y. Sohn, J. H. Park, J. H. Jang, H. J. Kim, S. A. Hong, P. Kim and S. J. Yoo, Appl. Catal., B, 2015, 174–175, 526–532 CrossRef CAS.
- C. Zhu, S. Guo and S. Dong, Adv. Mater., 2012, 24, 2326–2331 CrossRef CAS PubMed.
- M. E. Scofield, C. Koenigsmann, L. Wang, H. Liu and S. S. Wong, Energy Environ. Sci., 2015, 8, 350–363 CAS.
- Y. Kuang, Y. Zhang, Z. Cai, G. Feng, Y. Jiang, C. Jin, J. Luo and X. Sun, Chem. Sci., 2015, 6, 7122–7129 RSC.
- M. X. Gong, X. Jiang, T. Y. Xue, T. Y. Shen, L. Xu, D. M. Sun and Y. W. Tang, Catal. Sci. Technol., 2015, 5, 5105–5109 CAS.
- A. X. Yin, X. Q. Min, W. Zhu, W. C. Liu, Y. W. Zhang and C. H. Yan, Chem. – Eur. J., 2012, 18, 777–782 CrossRef CAS PubMed.
- C. Wang, C. Lin, L. Zhang, Z. Quan, K. Sun, B. Zhao, F. Wang, N. Porter, Y. Wang and J. Fang, Chem. – Eur. J., 2014, 20, 1753–1759 CrossRef CAS PubMed.
- P. Zhang, X. Dai, X. Zhang, Z. Chen, Y. Yang, H. Sun, X. Wang, H. Wang, M. Wang, H. Su, D. Li, X. Li and Y. Qin, Chem. Mater., 2015, 27, 6402–6410 CrossRef CAS.
- S. Liu, W. Xiao, J. Wang, J. Zhu, Z. Wu, H. Xin and D. Wang, Nano Energy, 2016, 27, 475–481 CrossRef CAS.
- M. Xiao, L. Feng, J. Zhu, C. Liu and W. Xing, Nanoscale, 2015, 7, 9467–9471 RSC.
- X. X. Wan, D. F. Zhang and L. Guo, CrystEngComm, 2016, 18, 3216–3222 RSC.
- B. Jiang, C. Li, V. Malgrasa and Y. Yamauchi, J. Mater. Chem. A, 2015, 3, 18053–18058 CAS.
- A. Oh, H. Baik, D. S. Choi, J. Y. Cheon, B. Kim, H. Kim, S. J. Kwon, S. H. Joo, Y. Jung and K. Lee, ACS Nano, 2015, 9, 2856–2867 CrossRef CAS PubMed.
- L. Qi, B. Cheng, W. Ho, G. Liu and J. Yu, ChemNanoMat, 2015, 1, 58–67 CrossRef CAS.
- J. W. Hong, S. W. Kang, B. S. Choi, D. Kim, S. B. Lee and S. W. Han, ACS Nano, 2012, 6, 2410–2419 CrossRef CAS PubMed.
- X. Yu, D. Wang, Q. Peng and Y. Li, Chem. Commun., 2011, 47, 8094–8096 RSC.
- S. Huang, N. Yang, S. Wang, Y. Sun and Y. Zhu, Nanoscale, 2016, 8, 14104–14108 RSC.
- L. Zhang, L. T. Roling, X. Wang, M. Vara, M. Chi, J. Liu, S. I. Choi, J. Park, J. A. Herron, Z. Xie, M. Mavrikakis and Y. Xia, Science, 2015, 349, 412–416 CrossRef CAS PubMed.
- L. Wang and Y. Yamauchi, J. Am. Chem. Soc., 2013, 135, 16762–16765 CrossRef CAS PubMed.
- H. Liu and J. Yang, J. Mater. Chem. A, 2014, 2, 7075–7081 CAS.
- W. Zhang, J. Yang and X. Lu, ACS Nano, 2012, 6, 7397–7405 CrossRef CAS PubMed.
- H. You, F. Zhang, Z. Liu and J. Fang, ACS Catal., 2014, 4, 2829–2835 CrossRef CAS.
- N. T. Khi, J. Park, H. Baik, H. Lee, J. H. Sohn and K. Lee, Nanoscale, 2015, 7, 3941–3946 RSC.
- C. Chen, Y. Kang, Z. Huo, Z. Zhu, W. Huang, H. L. Xin, J. D. Snyder, D. Li, J. A. Herron, M. Mavrikakis, M. Chi, K. L. More, Y. Li, N. M. Markovic, G. A. Somorjai, P. Yang and V. R. Stamenkovic, Science, 2014, 343, 1339–1343 CrossRef CAS PubMed.
- W. Wang, D. Wang, X. Liu, Q. Peng and Y. Li, Chem. Commun., 2013, 49, 2903–2905 RSC.
- X. Xu, X. Zhang, H. Sun, Y. Yang, X. Dai, J. Gao, X. Li, P. Zhang, H. H. Wang, N. F. Yu and S. G. Sun, Angew. Chem., Int. Ed., 2014, 53, 12522–12527 CAS.
- B. Jeyadevan, J. L. Cuya, Y. Inoue, K. Shinoda, T. Ito, D. Mott, K. Higashimine, S. Maenosono, T. Matsumoto and H. Miyamura, RSC Adv., 2014, 4, 26667–26672 RSC.
- X. Hong, C. Tan, J. Chen, Z. Xu and H. Zhang, Nano Res., 2014, 8, 40–55 CrossRef.
- Y. Kang, J. B. Pyo, X. Ye, T. R. Gordon and C. B. Murray, ACS Nano, 2012, 6, 5642–5647 CrossRef CAS PubMed.
- X. Liu, C. Cui, M. Gong, H. Li, Y. Xue, F. Fan and S. H. Yu, Chem. Commun., 2013, 49, 8704–8706 RSC.
- Y. Qi, T. Bian, S. Choi, Y. Jiang, C. Jin, M. Fu, H. Zhang and D. Yang, Chem. Commun., 2014, 50, 560–562 RSC.
- Q. Yuan, D. B. Huang, H. H. Wang and Z. Y. Zhou, Langmuir, 2014, 30, 5711–5715 CrossRef CAS PubMed.
- N. Zhang, X. Li, H. Ye, S. Chen, H. Ju, D. Liu, Y. Lin, W. Ye, C. Wang, Q. Xu, J. Zhu, L. Song, J. Jiang and Y. Xiong, J. Am. Chem. Soc., 2016, 138, 8928–8935 CrossRef CAS PubMed.
- Y. Liu, X. Hua, C. Xiao, T. Zhou, P. Huang, Z. Guo, B. Pan and Y. Xie, J. Am. Chem. Soc., 2016, 138, 5087–5092 CrossRef CAS PubMed.
- Y. Fan, Y. Zhang, Y. Cui, J. Wang, M. Wei, X. Zhang and W. Li, RSC Adv., 2016, 6, 83373–83379 RSC.
- X. J. Liu, C. H. Cui, H. H. Li, Y. Lei, T. T. Zhuang, M. Sun, M. N. Arshad, H. A. Albar, T. R. Sobahi and S.-H. Yu, Chem. Sci., 2015, 6, 3038–3043 RSC.
- Y. Zhang, M. Janyasup, C. W. Liu, X. Li, J. Xu and C. C. Liu, Adv. Funct. Mater., 2012, 22, 3570–3575 CrossRef CAS.
- D. B. Huang, Q. Yuan, P. L. He, K. Wang and X. Wang, Nanoscale, 2016, 8, 14705–14710 RSC.
- Y. Kang, J. Beom Pyo, X. Ye, T. R. Gordon and C. B. Murray, ACS Nano, 2012, 6, 5642–5647 CrossRef CAS PubMed.
- J. Kang, S. Nam, Y. Oh, H. Choi, S. Wi, B. Lee, T. Hwang, S. Hong and B. Park, J. Phys. Chem. Lett., 2013, 4, 2931–2936 CrossRef CAS.
- I. Kim, O. H. Han, S. A. Chae, Y. Paik, S.-H. Kwon, K.-S. Lee, Y.-E. Sung and H. Kim, Angew. Chem., Int. Ed., 2011, 50, 2270–2274 CrossRef CAS PubMed.
- A. Serov and C. Kwak, Appl. Catal., B, 2010, 97, 1–12 CrossRef CAS.
Footnote |
† Electronic supplementary information (ESI) available: Experimental details, TEM, XRD, CVs, LSV and table. See DOI: 10.1039/c6qm00277c |
|
This journal is © the Partner Organisations 2017 |
Click here to see how this site uses Cookies. View our privacy policy here.