DOI:
10.1039/C6QM00317F
(Research Article)
Mater. Chem. Front., 2017,
1, 1073-1078
Cross-linked perforated honeycomb membranes with improved mechanical and chemical properties†
Received
16th November 2016
, Accepted 7th December 2016
First published on 7th December 2016
Abstract
Ultrathin perforated honeycomb-patterned membranes show promise for high-resolution separation, in which the mechanical strength and chemical stability of membranes are very important. Here we report facile and versatile modification methods for preparing cross-linked honeycomb membranes with tunable mechanical and chemical properties. Commercially available polystyrene-b-polyisoprene-b-polystyrene (SIS), which contains double bonds for post modification, together with an amphiphilic block copolymer was utilized as the membrane-forming material. Robust and self-standing honeycomb membranes were obtained by the rapid vapor diffusion cross-linking of S2Cl2 in 5 min. X-ray photoelectron spectroscopy (XPS) and energy dispersive X-ray spectroscopy (EDX) results demonstrate effective cross-linking. The cross-linked membranes show excellent resistance to organic solvents and other harsh environments. Water flux measurements indicate that the cross-linked membranes can endure trans-membrane pressure as high as 0.12 MPa. The cross-linked membranes are stable in a wide temperature range. Another cross-linking method based on thiol–ene click chemistry is also proved to be able to form robust membranes with both improved stabilities and controllable surface properties. Moreover, the cross-linked perforated honeycomb membranes can be used for separation under higher operation pressure.
Introduction
Ordered porous films prepared using the breath figure method have been proved to be promising in a variety of applications in the fields of micro-patterned templates, superhydrophobic surfaces, sensors, catalysis, high-resolution separation, and responsive surfaces.1–14 Polystyrene (PS) is the most used matrix for breath figure films, featuring a glass transition temperature (Tg) of about 100 °C. The films tend to undergo softening and deformation processes at high temperature. Moreover, PS films suffer from unsatisfactory brittleness and sensitivity to a wide range of organic solvents. In our previous work, we reported that the addition of an elastomer polystyrene-b-polyisoprene-b-polystyrene (SIS) to the film-forming material can improve the flexibility of honeycomb films.15 The double bonds in SIS will also provide abundant reactive sites, and therefore will provide diversity and flexibility for postmodification.
Inspired by the cross-linking process of rubber, vulcanization can be applied to polymer films to increase the stability of porous structures. It has been reported that ultraviolet cross-linking greatly improved the thermal stability and solvent resistance of porous films.16 Cross-linked films remain rather stable without deformation and collapse at 250 °C.17 It was also proposed by Malkoch et al. that the honeycomb films showed an endurance temperature of up to 400 °C and an exhilarating stability in various pH environments from 1 to 14.18 However, the UV cross-linking process may lead to the acceleration of unexpected structure ageing and damage. To overcome the above disadvantages, Li et al. developed a simple and promising cross-linking process by S2Cl2 and accomplished room-temperature cross-linking for polymers with double bonds.19–21 On the other hand, click chemistry provides another route to the double-bond based modification and multifunction of porous films in a convenient and efficient way. For example, it was reported that slippery liquid-infused surfaces can be prepared based on the thiol–ene reaction.22
Herein, we prepared honeycomb-patterned porous membranes with the blends of amphiphilic block copolymer PS-b-PDMAEMA and commercially available SIS via the breath figure method. The membranes have through-pore or dead-end pore structures, depending on the substrates for membrane formation.12 Using S2Cl2 as a cross-linking agent, we obtained self-supporting perforated membranes with excellent thermal stability and solvent resistance. Compared with the reported method, our low-pressure cross-linking strategy greatly decreased the reaction time from over 1 hour to 5 min, providing a fast and effective cross-linking method. On the other hand, the thiol–ene reaction was also introduced to prepare cross-linked honeycomb membranes. The facile strategies we proposed here for cross-linking and functionalization are versatile for various functional cross-linkers and may endow the membranes with designed bulk and surface properties.
Experimental
Materials
A block copolymer, polystyrene-b-polydimethylaminoethyl methacrylate PS-b-PDMAEMA (Mw = 27
900 g mol−1, PDI = 1.24), was synthesized in laboratory.23 Triblock copolymer polystyrene-b-polyisoprene-b-polystyrene (SIS, 14 wt% PS block, Mw = 182
600 g mol−1, PDI = 1.12) was purchased from Sigma-Aldrich and used as received. S2Cl2 (98%) was obtained from Macklin. Diphenyl(2,4,6-trimethylbenzoyl)phosphine oxide (TPO, 98%) and trimethylolpropane tris(3-mercaptopropionate) (TRIM) (85%) were supplied by Energy Chemical Company. 1H,1H,2H,2H-Perfluorodecanethiol (PFDT, 97%) was provided by Aladdin. The poly(ethylene terephthalate) (PET) substrate with a thickness of 50 μm was kindly provided by Hangzhou Tape Company. The thickness of glass substrates (Navigare) was 1.0 mm to 1.2 mm. Ultrapure water was obtained from ELGA LabWater. All the other reagents from Sinopharm Chemical Reagent Company were used without further purification and pretreatment. All substrates, including transmission electron microscope (TEM) copper mesh, PET film, and glass substrates were first soaked in acetone with 5 minutes ultrasonic treatment three times and then blow-dried by nitrogen.
Fabrication of honeycomb-patterned porous membranes
Polymer solutions with a series of concentrations were prepared by dissolving PS-b-PDMAEMA and SIS in carbon disulfide (CS2). A humid nitrogen flow was obtained by bubbling through a flowmeter and a glass vessel filled with ultrapure water. A piece of cleaned PET or a glass substrate was placed on a plastic stand, 1 cm lower than the outlet of nitrogen. The honeycomb membrane was prepared by casting ∼30 μL of polymer solution onto the substrate using a microsyringe. Owing to solvent volatilization, the water vapor condensed, and the solution surface became turbid rapidly. The membrane solidified in about 2 min after the solvent and water evaporated completely.
To obtain a through-pore honeycomb membrane, TEM copper mesh substrates with ice on them were used. The thickness of the ice was approximately 1 mm. Upon solvent volatilization, the polymer solution became a turbid membrane on the surface of the ice.24,25 After several seconds, the ice melted gradually and infiltrated through the pores of the copper mesh. The honeycomb membrane was then adhered on top of the TEM copper mesh in a few minutes, resulting in a composite membrane. The as-prepared membrane was immersed in ethanol for 10 s to substitute the water in it, preventing membrane breakage induced by capillary force. All steps were carried out at room temperature.
Cross-linking by S2Cl2
TEM copper mesh substrates composited with honeycomb membranes were adhered to the bottom of a rubber plug with double-sided tape. 3 mL of S2Cl2 were added into a suction flask with the rubber plug. Then the pressure was decreased down to 10 kPa in 1 min in the flask to accelerate volatilization of S2Cl2. The vulcanizing agent volatilized and was absorbed into the honeycomb membranes slowly by vapor phase transfer, reacting with residual double bonds of SIS in the membranes. After 5 min, the samples were taken out and put into a vacuum desiccator for over 1 h to remove unreacted S2Cl2 and other by-products for further observation.
To obtain a self-supporting through-pore honeycomb membrane, several more steps were taken. Cross-linked honeycomb membranes were immersed in sodium hydroxide solution (0.01 M) for 2 h. The marginal part of the membrane was lift up carefully using tweezers, separated from the substrate gradually, and then the membrane floated on the solution. A ring made of iron wire with a size slightly smaller than the membrane was placed just below the through-pore honeycomb membrane. Then the liquid level was lowered, and the membrane was adhered to the iron ring automatically. A self-supporting through-pore honeycomb membrane can be obtained by carefully removing the iron ring and washing the surface of the membrane by ultrapure water to get rid of excess NaOH. The membrane can be operated directly after immersion in ethanol followed by air drying at room temperature.
Cross-linking via the thiol–ene reaction of TRIM and PFDT
Solutions with a series of concentrations (10, 20, 40, 60, and 80 mg mL−1) were prepared by dissolving TRIM in ethanol. TPO was added as the photo-initiator with a concentration of 2.5 mg mL−1. Honeycomb membranes on PET substrates were immersed in the solution after a pre-wetting process by ethanol for 2 min. TRIM slowly reacted with double bonds under UV irradiation (500 W, 232–400 nm) in air. All the experiments were conducted at room temperature without extra procedures to get rid of water and air. The surface of the solution became viscous after the reaction. Cross-linked honeycomb membranes were taken out, washed with ethanol, and air dried for further study.
Solutions with different concentrations (10, 20, 40, and 80 mg mL−1) were prepared by dissolving PFDT in ethanol. TPO was added as the photo-initiator with a concentration of 2.5 mg mL−1. The reaction was performed under UV irradiation (500 W, 232–400 nm) for 2.5 h. The surface of the solution became viscous after the reaction. Cross-linked honeycomb membranes were taken out, washed with ethanol, and air dried for further use.
Characterization
Measurement of water flux.
A dead-end filtration process was employed to measure the water flux of the membranes. Membranes with an effective diameter of 8.0 mm were wetted with ethanol before filtration and then washed with ultrapure water three times. Then the membranes were installed into the membrane cell. The operating pressure increased from 0.01 MPa to 0.14 MPa and then decreased to 0.01 MPa. Water flux under different pressures was recorded.
Membrane stability.
In organic solvent treatment, the membranes were immersed in toluene and tetrahydrofuran (THF) for 10 h and then the membranes were air dried at room temperature. In acid and alkali treatments, the membranes were immersed in HAc and NaOH (1 M) solutions for 10 h, washed with ultrapure water 3 times, rinsed with ethanol, and then air dried at room temperature. Thermal treatment was carried out in nitrogen using a tube furnace (SGL-1700). The temperature was increased at a rate of 1 °C min−1 to a certain value and held for 2 h, and then decreased to below 50 °C at a rate of 5 °C min−1. The low-temperature stability was evaluated by immersing the membranes in liquid nitrogen for 2 h.
Measurement of surface and interfacial tension.
Surface tension and interfacial tension were measured on a DropMeter A-200 contact angle meter. Polymer solutions at a total concentration of 20 mg mL−1 were prepared by dissolving PS-b-PDMAEMA and SIS in CS2. The surface/interfacial tension was measured using the pendent drop method.
Measurement of the cloud point.
Non-solvent-induced phase separation of the polymer solutions was studied by analyzing the cloud point. Polymer solutions at a total concentration of 20 mg mL−1 were prepared by dissolving PS-b-PDMAEMA and SIS in toluene. The absorbance of the solution was measured on a UV-2450 spectrophotometer. Droplets of methanol, a non-solvent, were added into the solution slowly. Each time methanol was added, the solution was stirred slightly and placed steadily for 5 min, and then the absorbance was recorded. The cloud point appeared when the absorbance changed significantly, meaning that phase separation occurred. The volume fraction of toluene was measured to analyze the tendency of phase separation.
Analysis of surface morphology and chemistry.
Scanning Electron Microscopy (SEM) images were taken using a Hitachi S-4800 scanning microscope at a working voltage of 3 kV. The samples were coated with platinum using an ion sputtering apparatus. The data of membrane pores and pore spacing were obtained from Image-Pro Plus. Surface elemental composition was analyzed by energy dispersive X-ray spectroscopy (EDX) at a working voltage of 20 kV and ESCAlab 250Xi X-ray photoelectron spectroscopy (XPS). Analysis of the three-dimensional morphology was performed using a Veeco Multimode Atomic Force Microscope (AFM).
Results and discussion
Preparation of PS-b-PDMAEMA/SIS honeycomb membranes
The breath figure method was used to prepare honeycomb-patterned porous membranes. A similar procedure has been reported in our previous work.26 Here we first investigated the influence of SIS on the surface morphologies of membranes. The blends do not show obvious macrophase separation because the molecular weight of PS-b-PDMAEMA is sufficiently low compared with that of SIS. SEM images in Fig. 1 show the top and bottom surface morphology of the membranes. The concentration of PS-b-PDMAEMA was fixed at 1 mg mL−1. When the content of SIS is lower than 75%, the membrane pores are quite regular, arranged as a hexagonal structure on both surfaces. The SEM images and the statistical analysis (Table S1 in the ESI†) also reveal that the average diameter of pores reduces from about 5.3 μm to 3.3 μm with the increase of SIS. The membrane turns out to be irregular obviously as the proportion of SIS increases to 80%. Both top and bottom views of the membranes demonstrate an increase of pore size and pore spacing (Fig. 1d and h).
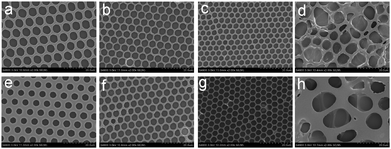 |
| Fig. 1 SEM images of the top (a–d) and bottom (e–h) sides of perforated honeycomb membranes prepared from PS-b-PDMAEMA/SIS blends with different ratios of (a and e) 1 : 1, (b and f) 1 : 2, (c and g) 1 : 3, and (d and h) 1 : 4. The concentration of PS-b-PDMAEMA was fixed at 1 mg mL−1. | |
The surface tension of the polymer solutions and the interfacial tension with water play a crucial role in the membrane morphology and pore size. An increase in the weight fraction of block copolymer PS-b-PDMAEMA results in the decrease of interfacial tension between water and the polymer solution although the surface tension is almost constant (Fig. 2a). This result demonstrates that the amphiphilic PS-b-PDMAEMA can aggregate at the interface of water and polymer solution to decrease the interfacial tension, which also contributes to the spread of polymer solution on the surface of water. In addition, phase separation induced by non-solvent water tends to be facilitated by the addition of SIS (Fig. 2b), and the spread of polymer solution on substrates is also hindered (Fig. S1, ESI†). As a result, polymer blends with a lower content of PS-b-PDMAEMA are more promising for the preparation of thick membranes with smaller pores. On the other hand, higher content of SIS will provide enough double bonds for further modification. Therefore, PS-b-PDMAEMA and SIS with a ratio of 1
:
3 are used for membrane preparation.
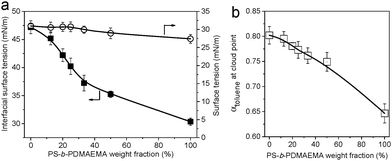 |
| Fig. 2 (a) Effects of the PS-b-PDMAEMA weight fraction in PS-b-PDMAEMA/SIS blends on the surface tension and the interfacial surface tension between water and the polymer solutions. (b) Phase separation tendency of the polymer solutions. | |
Cross-linking by S2Cl2
Vulcanization is an effective method to improve the stability of polymer materials. Cold vulcanization applied with S2Cl2 can be simply and conveniently completed at room temperature (Fig. S2, ESI†). Since S2Cl2 is a good solvent for both components of the block copolymer, the membranes were exposed to S2Cl2 by vapor phase transfer, avoiding the direct contact with a large amount of liquid S2Cl2. Moreover, diffusion was performed at reduced pressure so that we decreased the reaction time to 5 min using a relatively mild process; while it takes hours under atmospheric conditions. In fact, we found that the membranes deform gradually with reaction time (Fig. S3, ESI†). Fig. 3 shows the morphology of perforated honeycomb membranes cross-linked with S2Cl2. Iridescent colors under sunlight can be observed by the naked eye as shown in the inset in Fig. 3a, proving the large-area ordered structure. The cross-section shown in Fig. 3c indicates that the thickness of the obtained membrane is about 2.9 μm. This method provides a fast and cost-effective way to acquire a free-standing perforated honeycomb membrane (Fig. 3f).
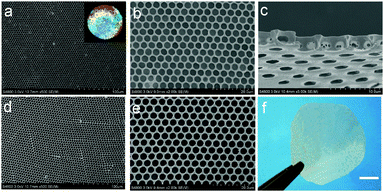 |
| Fig. 3 (a–e) SEM images of perforated honeycomb membranes after vulcanization. (a and b) top, (c) cross-sectional, and (d and e) bottom view. The inset in (a) shows the optical image of the membrane viewed under sunlight. (f) A digital photograph of a freestanding membrane peeled off from the glass slide. Scale bar in (f): 5 mm. | |
To further evaluate the effects of cross-linking by S2Cl2, we characterized the surface chemical composition of cross-linked membranes by both XPS and EDX. XPS results are shown in Fig. 4a. The spectrum of the nascent membrane shows obvious C1s and O1s peaks; the cross-linked membrane shows an additional S2s peak at 228.6 eV, an S2p peak at 163.8 eV, and a Cl2p peak at 200.8 eV, suggesting successful modification with S2Cl2. The distribution of the S element was plotted in Fig. 4b. The pattern of S element distribution is consistent with the honeycomb porous structures.
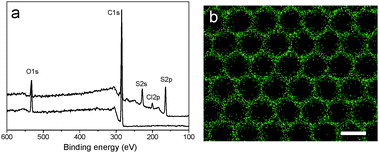 |
| Fig. 4 (a) XPS spectra of perforated honeycomb membranes before (down) and after (top) vulcanization. (b) Distribution of the S element on the vulcanized honeycomb membrane surface measured by EDX mapping. Scale bar: 5 μm. | |
It is crucial to ensure the stability of the cross-linked honeycomb membranes in harsh environments such as extreme temperatures and organic solvents. The nascent membrane can be completely dissolved by many kinds of organic solvents. Cross-linked membranes immersed in toluene and THF for up to 10 h still have intact honeycomb arrays as shown in Fig. 5(a–d), it is worth noting that there are some small holes with a diameter of dozens of nanometers on the membrane surface. It is due to the dissolution of a small amount of non-cross-linked polymer. The cross-linked membranes are robust enough to endure such small holes in the matrix. Similar to the resistance to organic solvents, the membranes are strong enough to resist the treatment with NaOH aqueous solution (1 M) and glacial acetic acid (Fig. 5e–h).
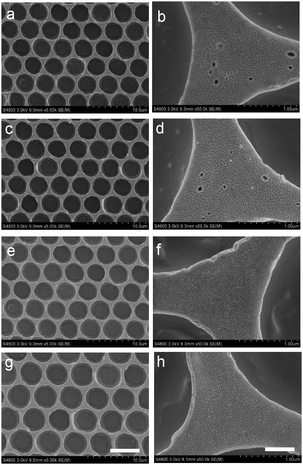 |
| Fig. 5 SEM images of cross-linked perforated honeycomb membranes after immersion in (a and b) toluene, (c and d) THF, (e and f) NaOH aqueous solution (1 M), and (g and h) glacial acetic acid for 10 h. Scale bars: 5 μm (left column) and 500 nm (right column). | |
Cross-linking not only enhances the stability of the membranes in organic solvents, but also increases tolerance to extreme temperature. Tg of PS-b-PDMAEMA is around 100 °C. However, the cross-linked membranes retain a uniform porous structure after 2 hours thermal treatment at 200 °C (Fig. 6a). When the temperature was further increased to 400 °C, collapse and deformation of the porous structure occur; but the honeycomb-patterned porous structure remains clear (Fig. 6b and c). Some polymer particles can be found at the center of membrane pores. These disc-in-pore structures appear because of the melting and moving of the unreacted polymer.27 Although the morphology of the membrane changes at 400 °C, the remaining framework indicates that the cross-linking occurred inside the membrane instead of only at the surface. Apparently, the membrane still exhibits nacre color because of sunlight diffraction and interference. In contrast, the non-cross-linked membrane does not exhibit nacre color after thermal treatment at as low as 100 °C (Fig. 6d), indicating the disappearance of the patterned structure. It should be mentioned that the highly ordered structures are deformed entirely when the treatment temperature is over 450 °C. In addition, the honeycomb-patterned membranes after vulcanization can stand the test at low temperature; the membranes are not damaged in liquid nitrogen for 2 h (Fig. S4, ESI†). In such a case, the nascent non-cross-linked membranes crack even for 2 min.
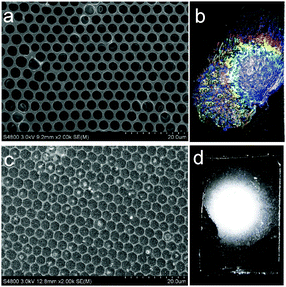 |
| Fig. 6 (a and c) SEM images of cross-linked perforated honeycomb membranes after thermal treatment at different temperatures for 2 h, (a) 200 °C, (c) 400 °C. (b and d) Digital photographs of cross-linked perforated honeycomb membranes after thermal treatment at 400 °C (b) and nascent membranes heated at 100 °C (d) for 10 min. | |
Cross-linking by thiol–ene click chemistry
As mentioned above, cross-linking with S2Cl2 is very fast and can be finished in 5 minutes. Considering the large number of double bonds in SIS, the thiol–ene click reaction also provides a route to prepare cross-linked membranes with surface functionalities (Fig. 7). Moreover, the thiol–ene click reaction using TRIM can be easily controlled, and the cross-linking degree varies with the concentration of the click reagent. The concentration of TRIM is very important. The surface morphology of cross-linked membranes with three different concentrations of TRIM was observed (Fig. 8 and Fig. S5, ESI†). The results indicate that the increase of concentration leads to an increase of cross-linking density. The pores and surface roughness of the membranes remain when the concentration of TRIM is relatively low (20 and 30 mg mL−1). However, the honeycomb-patterned porous structure disappears when the concentration of TRIM reaches 40 mg mL−1 (Fig. S5, ESI†). At different cross-linker concentrations, the membrane possesses different resistances to organic solvents. For example, after being immersed in toluene for 180 min, the membranes cross-linked with 20 mg mL−1 TRIM retain the porous structure (Fig. 8c and e); however, the pores deform and the depth decreases to less than 100 nm. Membranes cross-linked with 30 mg mL−1 TRIM show excellent resistances to toluene (Fig. 8d and f). In addition, the results of water contact angle and XPS also demonstrate resistance to toluene (Fig. S6 and S7, ESI†).
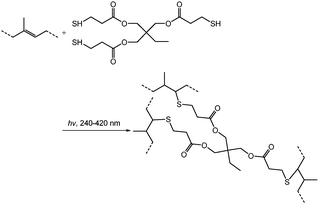 |
| Fig. 7 Thiol–ene cross-linking reaction between SIS and TRIM. | |
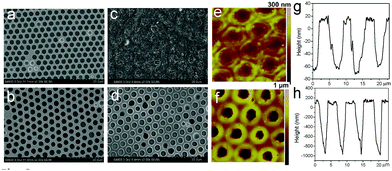 |
| Fig. 8 SEM images of perforated honeycomb films cross-linked with the thiol–ene reaction (a and b) and those immersed in toluene for 180 min (c and d). (e–h) AFM height images and the corresponding depth profiles along the lines. The concentration of cross-linker TRIM is 20 mg mL−1 (a, c, e and g) and 30 mg mL−1 (b, d, f and h). | |
The thiol–ene click chemistry endows honeycomb-patterned membranes with not only bulk cross-linking but also surface properties such as superhydrophobicity. By introducing PFDT, a thiol with a fluorinated chain, the membrane retains the honeycomb structure (Fig. S8, ESI†) and shows superhydrophobicity with a water contact angle higher than 150° (Fig. S9, ESI†). Interestingly, the superhydrophobic honeycomb-patterned membranes show high adhesion to water because of the negative pressure principle,11 which makes the modified membranes useful in fields such as no-loss transportation of water droplets.28,29
Properties of cross-linked perforated membranes at different pressures
The vulcanization process also endows honeycomb membranes with remarkable tolerance to pressure. The tolerance to pressure was evaluated during water flux measurement. With the increase of trans-membrane pressure, water fluxes of cross-linked membranes show a linear growth, and the actual numerical value is close to the theoretical value calculated from the Hagen–Poiseuille equation (Fig. 9).30 However, the water flux of the nascent membrane is higher than the theoretical value when the pressure is up to 0.07 MPa and the deviation becomes larger gradually, demonstrating that the membrane is broken at such high pressure. For cross-linked membranes, the extreme pressure obviously increases to about 0.12 MPa.
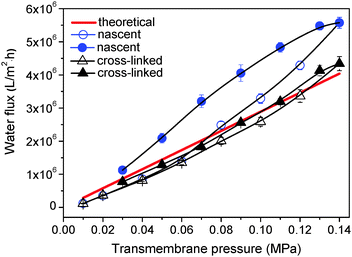 |
| Fig. 9 Relationship between pure water flux and operation pressure for perforated honeycomb membranes before and after vulcanization. The fluxes were measured by increasing the operation pressure (open dots) and subsequently by decreasing the pressure (filled dots) to verify membrane integrity and performance. | |
Conclusions
In summary, we prepared cross-linked honeycomb membranes using two methods, i.e., vulcanization with S2Cl2 and the thiol–ene click chemistry. Using S2Cl2 as the vulcanizer can conveniently form a porous structure with enhanced resistance to harsh environments including extreme temperatures, organic solvents, and alkaline or acidic agents. The cross-linking method based on thiol–ene click chemistry is able to form robust membranes with controllable surface properties. Moreover, it has been demonstrated that the cross-linked perforated honeycomb membranes can be used for separation under higher operation pressure.
Acknowledgements
Financial support from Zhejiang Provincial Sci & Tech Plan (2015C31028), the National Natural Science Foundation of China (51522305, 21374100) and the Fundamental Research Funds for the Central Universities (2015XZZX004-26) is gratefully acknowledged.
Notes and references
- G. Widawski, M. Rawiso and B. François, Nature, 1994, 369, 387–389 CrossRef CAS.
- L. Xue, J. Zhang and Y. Han, Prog. Polym. Sci., 2012, 37, 564–594 CrossRef CAS.
- A. Zhang, H. Bai and L. Li, Chem. Rev., 2015, 115, 9801–9869 CrossRef CAS PubMed.
- T. Nishikawa, R. Ookura, J. Nishida, K. Arai, J. Hayashi, N. Kurono, T. Sawadaishi, M. Hara and M. Shimomura, Langmuir, 2002, 18, 5734–5740 CrossRef CAS.
- T. Guo, M. Li, L. Heng and L. Jiang, Phys. Chem. Chem. Phys., 2015, 17, 6242–6247 RSC.
- A. Bolognesi, C. Mercogliano, S. Yunus, M. Civardi, D. Comoretto and A. Turturro, Langmuir, 2005, 21, 3480–3485 CrossRef CAS PubMed.
- H. Yabu, M. Takebayashi, M. Tanaka and M. Shimomura, Langmuir, 2005, 21, 3235–3237 CrossRef CAS PubMed.
- L. Heng, J. Li, M. Li, D. Tian, L.-Z. Fan, L. Jiang and B. Z. Tang, Adv. Funct. Mater., 2014, 24, 7241–7248 CrossRef CAS.
- J. Li, Y. Li, C. Y. K. Chan, R. T. K. Kwok, H. Li, P. Zrazhevskiy, X. Gao, J. Z. Sun, A. Qin and B. Z. Tang, Angew. Chem., Int. Ed., 2014, 53, 13518–13522 CrossRef CAS PubMed.
- L. S. Wan, Q. L. Li, P. C. Chen and Z. K. Xu, Chem. Commun., 2012, 48, 4417–4419 RSC.
- L. Heng, X. Meng, B. Wang and L. Jiang, Langmuir, 2013, 29, 9491–9498 CrossRef CAS PubMed.
- L. S. Wan, J. W. Li, B. B. Ke and Z. K. Xu, J. Am. Chem. Soc., 2012, 134, 95–98 CrossRef CAS PubMed.
- L. S. Wan, L. W. Zhu, Y. Ou and Z. K. Xu, Chem. Commun., 2014, 50, 4024–4039 RSC.
- L. Heng, R. Hu, S. Chen, M. Li, L. Jiang and B. Z. Tang, Langmuir, 2013, 29, 14947–14953 CrossRef CAS PubMed.
- L. W. Wu, L. S. Wan, Y. Ou, L. W. Zhu and Z. K. Xu, Adv. Mater. Interfaces, 2015, 2, 1500285 CrossRef.
- L. Li, Y. Zhong, J. Li, C. Chen, A. Zhang, J. Xu and Z. Ma, J. Mater. Chem., 2009, 19, 7222–7227 RSC.
- L. Li, C. Chen, A. Zhang, X. Liu, K. Cui, J. Huang, Z. Ma and Z. Han, J. Colloid Interface Sci., 2009, 331, 446–452 CrossRef CAS PubMed.
- S. Mongkhontreerat, M. V. Walter, O. C. J. Andrén, Y. Cai and M. Malkoch, Adv. Funct. Mater., 2015, 25, 4837–4843 CrossRef CAS.
- L. Li, Y. Zhong, J. Gong, J. Li, J. Huang and Z. Ma, J. Colloid Interface Sci., 2011, 354, 758–764 CrossRef CAS PubMed.
- L. Li, Y. Zhong, J. Gong, J. Li, C. Chen, B. Zeng and Z. Ma, Soft Matter, 2011, 7, 546–552 RSC.
- C. Du, A. Zhang, H. Bai and L. Li, ACS Macro Lett., 2013, 2, 27–30 CrossRef CAS.
- J. Kamei and H. Yabu, Adv. Funct. Mater., 2015, 25, 4195–4201 CrossRef CAS.
- B. B. Ke, L. S. Wan, P. C. Chen, L. Y. Zhang and Z. K. Xu, Langmuir, 2010, 26, 15982–15988 CrossRef CAS PubMed.
- J. S. Phipps, R. M. Richardson, T. Cosgrove and A. Eagleshamt, Langmuir, 1993, 9, 3530–3537 CrossRef CAS.
- G. R. Guillen, Y. Pan, M. Li and E. M. V. Hoek, Ind. Eng. Chem. Res., 2011, 50, 3798–3817 CrossRef CAS.
- B. H. Wu, L. W. Zhu, Y. Ou, W. Tang, L. S. Wan and Z. K. Xu, J. Phys. Chem. C, 2015, 119, 1971–1979 CAS.
- V. T. Bui, H. S. Lee, J. H. Choi and H. S. Choi, Polymer, 2015, 74, 46–53 CrossRef CAS.
- H. Yabu, T. Nakanishi, Y. Hirai and M. Shimomura, J. Mater. Chem., 2011, 21, 15154–15156 RSC.
- D. Ishii, H. Yabu and M. Shimomura, Chem. Mater., 2009, 21, 1799–1801 CrossRef CAS.
- H. Cong, J. Wang, B. Yu and J. Tang, Soft Matter, 2012, 8, 8835–8839 RSC.
Footnotes |
† Electronic supplementary information (ESI) available. See DOI: 10.1039/c6qm00317f |
‡ Both authors contributed equally to the present work. |
|
This journal is © the Partner Organisations 2017 |
Click here to see how this site uses Cookies. View our privacy policy here.