DOI:
10.1039/C6RA26643F
(Paper)
RSC Adv., 2017,
7, 17085-17094
The effect of micelles with random pH-sensitive/hydrophobic structure on the workability, hydration process and microstructure of cement paste
Received
11th November 2016
, Accepted 13th March 2017
First published on 17th March 2017
Abstract
In this study, the workability, hydration rate and microstructure of cement paste in the presence of the micelles prepared by two different diblock copolymers with random pH sensitive/hydrophobic structure (poly(polylactide methacrylate-co-tert-butyl methacrylate)-b-poly(poly(ethylene glycol) methyl ether methacrylate) (P(PLAMA-co-tBMA)-b-PPEGMA) and poly(ethylene glycol) methyl ether-b-(poly-lactic acid-co-poly(β-amino esters)) (MPEG-b-(PLA-co-PAE)) copolymers, respectively) were investigated. In fresh cement paste, the micelles were efficiently adsorbed on cement particles; although the average zeta potential of cement particles was not significantly changed in the presence of the micelles due to their low concentrations, with a high water to cement ratio, the adsorbed micelles altered the zeta potential of partial cement particles, leading to a better workability of cement paste. In hardened cement paste, the micelles retarded the hydration rate of C3S at very early hydration age, but accelerated the hydration rate of cement paste at later stages, resulting in a denser cement matrix and increased mechanical property. The most plausible mechanisms are related to the nucleation effect, molecular structure and adsorption performance of the polymeric micelles.
1. Introduction
Polymers are widely used as important additives to improve material properties of cement-based materials (as typical inorganic materials), i.e. the workability of cement-based materials can be significantly improved by polymer-based superplasticizers.1–3 However, the application of polymeric micelles (with core–shell structures) in cement-based materials is very limited.
Micelles are based on amphiphilic copolymers normally presenting core–shell molecular structures, with a hydrophobic core and hydrophilic shell. If certain chemical substances are successfully encapsulated, micelles can act as drug vehicles.4,5 Chemical substances are reserved in the core, and the shell avoids the aggregation of the micelles and maintains the stability of the reserved chemical substances under a certain environment.6–8 When the environment changes (e.g. ion concentrations, temperature, pH value etc.), the reserved chemical substances can be efficiently released.6,8 In reinforced concrete, after corrosion of the steel reinforcement is initiated, the pH value of the pore solution can drop from 12.6–13.5 to 8–9 (for carbonation) or even below 6 (for chloride induced corrosion).9,10 Therefore, based on the special controlled release property (sensitive to environmental alterations), micelles can be potentially used as self-healing agents in reinforced concrete for the corrosion control.
In our previous studies, the micelles prepared by polyethylene oxide-b-polystyrene (PEO-b-PS) diblock copolymers were admixed in cement-based materials and investigated for the corrosion control of reinforced concrete.11,12 The experiment results indicate that with a very low concentration (0.025 wt% per dry cement weight), the admixed PEO-b-PS micelles altered both the material properties of hardened cement-based materials and corrosion performance of the reinforcing steel: on one hand, the micelles reduced the total porosity and permeability (3 orders of magnitude lower) of cement matrix (however, the influence of the micelles on the workability of fresh cement-based materials was not clarified in the previous study); on the other hand, the micelles led to a more protective product layer on steel surface and increased chloride-binding capacity of cement matrix, thus halting the corrosion propagation of the reinforcement.
When used as self-healing materials for corrosion control of reinforced concrete, the high loading content of healing agents under high alkaline environment and their efficient release are very important challenges for the micelles preparation. One important method to improve the above mentioned properties is to introduce pH sensitive functional group into copolymers to generate pH-sensitive/hydrophobic structure.13–15 In this way, on one hand, the stability of micelles and encapsulated amount of healing agents can be increased due to the increased length of the hydrophobic block;16 on the other hand, the release rate of healing agents can be optimized by the introduced pH-sensitive functional group.16,17 Therefore, compared to regular diblock copolymer micelles, micelles prepared by diblock copolymers with pH-sensitive/hydrophobic structure may be more suitable to prepare the self-healing materials for the corrosion control of reinforced concrete, due to the increased loading capacity and controlled release of the healing agents.
Due to the more complex molecular structures and properties of diblock micelles with pH-sensitive/hydrophobic structure, their influence on the material properties of cement-based materials is very important and should be clarified first. To this end, the motivation of this present study is to investigate the influence of the micelles prepared by two different diblock copolymers with random pH-sensitive/hydrophobic structure (poly(polylactide methacrylate-co-tert-butyl methacrylate)-b-poly(poly(ethylene glycol) methyl ether methacrylate) (P(PLAMA-co-tBMA)-b-PPEGMA) and poly(ethylene glycol) methyl ether-b-(poly-lactic acid-co-poly(β-amino esters)) (MPEG-b-(PLA-co-PAE)) copolymers respectively) on the micro/macro properties of both fresh and hardened cement paste. In fresh cement paste, the total organic carbon (TOC) content was used to evaluate the adsorption behavior of the micelles on cement particles, and the workability of cement paste in the presence of the micelles was characterized by zeta potential and mini slump measurements. In hardened cement paste, isothermal calorimetry tests were applied to determine the hydration process of cement paste; the microstructural alterations of cement matrix in the presence of the micelles were checked by mercury intrusion porosimetry (MIP). The influence of the admixed micelles on the compressive strength of cement paste was also investigated.
2. Materials and methods
2.1 Materials
2.1.1 Micelles. In this study, the diblock copolymers used for preparing the micelles with pH-sensitive/hydrophobic structure were poly(polylactide methacrylate-co-tert-butyl methacrylate)-b-poly(poly(ethylene glycol) methyl ether methacrylate) (P(PLAMA-co-tBMA)-b-PPEGMA, m1) and poly(ethylene glycol) methyl ether-b-(poly-lactic acid-co-poly(β-amino esters)) (MPEG-b-(PLA-co-PAE), m2) copolymers respectively. The synthesis process and detail information of the copolymers were reported in.15,18 The micelles were prepared through dialysis method described as follows:For P(PLAMA-co-PtBMA)-b-PPEGMA micelles (m1),17 40 mg copolymers were dissolved in 80 mL N,N-dimethylformamide (DMF, analytical reagent (AR) and used as received) and vigorous stirred for 4 h. The polymer solution was then dialyzed against deionized water for 24 h at room temperature by using a cellulose membrane bag (MWCO 11300, Aldrich). Deionized water was replaced every 2 h for the first 12 h and then every 6 h. After dialysis, the core–shell micelles with a hydrophobic P(PLAMA-co-tBMA) core and hydrophilic PEGMA corona was obtained.
For MPEG-b-(PLA-co-PAE) micelles (m2),18 40 mg copolymers were dissolved in 80 mL DMF, and 4 mL deionized water was added drop-wise. The polymer solution was then dialyzed against deionized water for 24 h (the dialysis procedure was similar to the preparation of micelles m1). MPEG-b-(PLA-co-PAE) micelles presented a hydrophobic PLA-co-PAE core and hydrophilic MPEG corona.
After dialysis, the concentrations of both micelles solutions were adjusted to 0.25 g l−1 by deionized water. The hydrodynamic radius characterized by DLS measurement (as shown in Fig. 1) was about 180 nm for micelles m1 and 400 nm for micelles m2, respectively. The zeta potential (determined by Malven Zetasizer Nano ZS90, U.K., and there were three replicates for each type of micelles) was about −53.8 mV for micelles m1 and −36.7 mV for micelles m2, respectively.
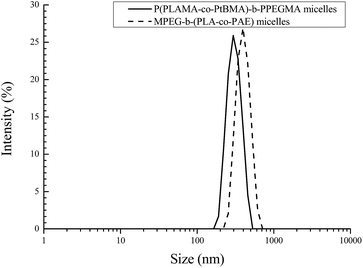 |
| Fig. 1 Hydrodynamic radius of the micelles derived by DLS measurement. | |
2.1.2 Cement paste specimens. The cement paste in this study was prepared by ordinary Portland Cement OPC CEM I 42.5 R with the chemical composition listed in Table 1. Three water to cement (w/c) ratios (0.3, 0.4 and 0.5) were used to cast cement paste specimens. For the micelles-containing specimens, the above prepared micelles solution was used as the mixing water instead of tap water (for the micelles-free specimen). Finally, the micelles concentration was 7.50 × 10−3 wt%, 1.00 × 10−2 wt% and 1.25 × 10−2 wt% by dry cement weight in cement paste with a w/c ratio of 0.3, 0.4 and 0.5, respectively.
Table 1 Chemical composition of OPC CEM I 42.5 R used in this study
Chemical composition of OPC CEM I 42.5 R |
LOI is the loss on ignition. |
Oxide |
CaO |
SiO2 |
Al2O3 |
SO3 |
Fe2O3 |
MgO |
Na2O |
K2O |
LOIa |
Rest |
Weight (%) |
63.28 |
20.07 |
4.98 |
2.75 |
3.65 |
1.10 |
— |
0.44 |
0.35 |
2.89 |
For hardened cement paste, samples were tightly sealed after casting and cured in a standard curing box (20 °C, 98% relative humility). At the curing ages of 3 days and 7 days, the specimen was immersed in liquid nitrogen to stop hydration and then placed in a freeze-dryer at −28 °C. Additionally, the sample preparation for isothermal calorimetry tests is described in detail in Section 2.2.4, and the details about the sample preparation for fresh cement paste are described in Section 2.2.
The sample designations in this study are as follows: specimen “OPC” is the control specimen cast with tap water; specimen “OPCm1” is the specimen cast with P(PLAMA-co-PtBMA)-b-PPEGMA micelles solution; specimen “OPCm2” is the specimen cast with MPEG-b-(PLA-co-PAE) micelles solution.
2.2. Methods
2.2.1 Adsorption amount. The total organic carbon analyzer (Liqui TOC) was used to evaluate the adsorption behavior of the micelles on cement particles in this study. Before the tests, all cement pastes were mixed for 2 min and diluted for 20 times with deionized water. The samples were centrifuged at 4200 rpm for 10 min to separate the liquid, and the collected solution was then filtered by a 0.8 μm filter. The concentration of the micelles remained in solution was measured and the amount of the micelles adsorbed on cement particles was calculated based on the difference between the amount of micelles in solution before and after mixing. There were at least 3 replicates for each specimen.
2.2.2 Zeta potential. Samples for zeta potential measurements were prepared by the similar procedure as the adsorption tests. After mixing, the samples were diluted for 50 times with deionized water and dispersed for 30 s by an ultrasonic bath. The solution from the topside was then taken for the measurements. The zeta potential of cement particles was measured within 3 min after mixing by Zeta potential analyzer (Nano ZS90). There were at least 3 replicates for each specimen.
2.2.3 Mini slump tests. The influence of the micelles on the fluidity of fresh cement paste was evaluated by mini-slump tests. The sample preparation and measurement were conducted according to Chinese Standard GB/T 8077-2000. The flow value was measured by using a mini-slump cone with a height of 60 mm, top diameter of 30 mm and bottom diameter of 60 mm. There were at least 3 replicates for each specimen.
2.2.4 Hydration process of cement paste. Isothermal calorimetry tests were conducted by using an eight-channel micro-calorimeter (TEM Air 314) to determine the hydration process of cement paste. Before the isothermal calorimetry tests, the materials (cement, tap water and micelles solutions) and mixing tools were kept at 20 °C for 24 h to avoid the influence of environment temperature. Cement was mixed with the mixing water (tap water or micelles solutions) for 1 min and about 10 g cement paste was added into glass ampoules. The released heat of cement paste was monitored up to 7 days and normalized per gram of cement weight.
2.2.5 Mercury intrusion porosimetry (MIP). In this study, the microstructural alterations of cement paste caused by the admixed micelles were characterized by mercury porosimeter (Quantachrome Pore master GT33). Washburn equation19 (eqn (1)) was used to calculate the diameter of pores intruded at each pressure step: |
D = −4γ cos θ/P
| (1) |
where D is the pore diameter (μm), γ is the surface tension of mercury (485 × 10−3 N m−1 in this study), θ is the contact angle between mercury and the pore wall (140° in this study) and P is the applied pressure (MPa). The applied pressure range for MIP measurements in this study was from 0.0036 MPa to 207 MPa, corresponding to a determined pore size ranging from 350 μm to 0.006 μm.
2.2.6 Standard compressive strength. At the curing ages of 3 days and 7 days, the compressive strength was measured on cement paste cubes with dimensions of 20 × 20 × 20 mm. There were at least 3 replicates for each specimen.
3. Experimental results
3.1 Workability of fresh cement paste in the presence of the micelles
3.1.1 Adsorption amount of the micelles on cement particles. The adsorption amounts of micelles on the surface of cement particles are presented in Fig. 2. In cement paste with different w/c ratios, two polymeric micelles were both effectively adsorbed on the surface of cement particles. For example, in fresh cement paste with a w/c ratio of 0.5, the adsorption amount was about 0.11 mg g−1 for micelles m1 and 0.05 mg g−1 for micelles m2, respectively. The difference in the adsorption amount of two micelles may be related to the following reasons: first, as mentioned in Section 2.1.1, the zeta potential of micelles m1 (−53.8 mV) was more negative, compared to micelles m2 (−36.7 mV), leading to a larger electrostatic adsorption force between the positively charged cement particles (the measured zeta potential of cement particles was about 5 mV in this study as shown in Table 2, and similar positive zeta potential values were also reported in ref. 2 and 20) and negatively charged micelles; second, the particle size of micelles m1 (180 nm) was smaller than micelles m2 (400 nm), thus the larger specific surface and surface energy of micelles m1 made them easier to adsorb on the surface of cement particles. Additionally, the molecular weight of micelles m1 was also larger than micelles m2 (20
390 for micelles m1 and 10
852 for micelles m2 (ref. 15 and 18)), meaning that if same quantity of micelles was adsorbed on cement particles, the adsorbed weight of micelles m1 was larger, compared to micelles m2. Therefore, the combination of the above effects resulted in a larger adsorption amount of micelles m1 on the surface of cement particles.
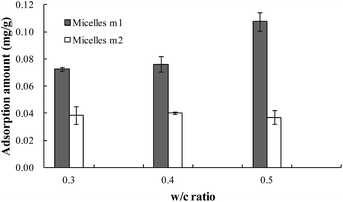 |
| Fig. 2 Adsorption amount of the micelles on cement particles. | |
Table 2 Average zeta potential of cement particles for different specimens
w/c |
Zeta potential (mV) |
OPC |
OPCm1 |
OPCm2 |
0.3 |
6.02 |
4.00 |
5.95 |
0.4 |
5.51 |
5.35 |
6.35 |
0.5 |
3.42 |
5.33 |
5.53 |
3.1.2 Zeta potential of cement particles in the presence of the micelles. Table 2 presents the average zeta potential values of cement particles for different specimens. During the early hydration period, due to the dissolution of Ca2+ and OH− ions, Ca/Si ratio in cement pore solution is much higher than 3, leading to a Si-rich layer formed on the surface of tri-calcium silicate (C3S); Ca2+ ions then adsorb on the surface of Si-rich layer to form an electric double layer, making it positively charged.21 After the micelles were admixed into cement paste, due to the low concentration (the concentration of the admixed micelles was 7.50 × 10−3 wt%, 1.00 × 10−2 wt%, and 1.25 × 10−2 wt% by dry cement weight in cement paste with w/c ratios of 0.3, 0.4 and 0.5 respectively), the average zeta potential value of cement particles was not significantly changed, as shown in Table 2. However, the admixed micelles altered the zeta potential distribution of cement particles, as shown in Fig. 3. It is observed from Fig. 3(a) that for the micelles-free specimen OPC, cement particles presented a monomodal zeta potential distribution (with a peak at about 5 mV) in cement paste with different w/c ratios. For the micelles-containing specimens OPCm1 and OPCm2 (as shown in Fig. 3(b) and (c) respectively), when w/c ratio was 0.3, there was also only one main peak on the zeta potential distribution curves; however, when w/c ratio increased (w/c = 0.4, 0.5), except the main peak at about 5 mV, a new small peak at about −12 mV appeared and this peak was more obvious with a higher w/c ratio. It indicates that with the increase of w/c ratio, the micelles concentration in cement paste gradually increases; they can absorb on cement particles and make partial cement particles negatively charged.
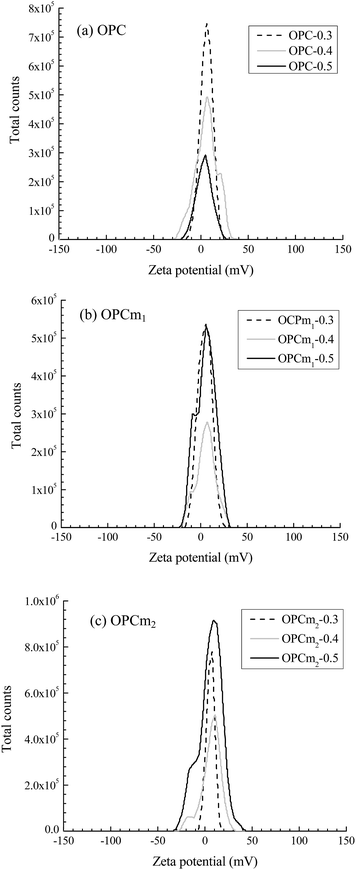 |
| Fig. 3 Influence of the admixed micelles on the zeta potential distribution of cement particles. | |
3.1.3 Mini slump flow of cement paste in the presence of the micelles. The mini slump flow values of cement paste for specimens OPC, OPCm1 and OPCm2 are presented in Fig. 4. Two micelles both slightly increased the fluidity of fresh cement paste: when w/c ratio was low (w/c = 0.3), the mini slump flow was increased by 5 mm; when w/c ratio increased (w/c = 0.4, 0.5), the mini slump flow was increased by more than 10 mm. Further, because the adsorption amount of micelles m1 was larger on the surface of cement particles (Fig. 2), the effect of micelles m1 on the mini slump flow of cement paste was more pronounced, compared to micelles m2.
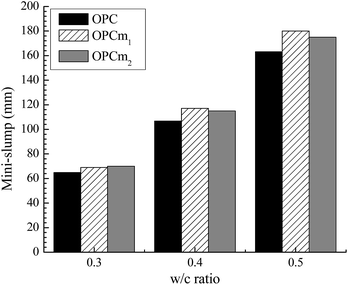 |
| Fig. 4 Influence of the admixed micelles on the mini-slump flow of cement paste. | |
3.2 Hydration rate and microstructural alterations of cement paste in the presence of the micelles
3.2.1 Hydration process of cement paste in the presence of the micelles. The heat release rate and cumulative heat release amount of different specimens are presented in Fig. 5. The influence of the admixed micelles on the hydration process of cement paste was different during the first 15 h and later hydration ages (up to 7 days), respectively. During the very early hydration age (first 15 h), the admixed micelles slightly retarded the hydration rate of C3S (corresponding to the main peak in Fig. 5(a), (c) and (e)). For example, with a w/c ratio of 0.3, the hydration of C3S was retarded by about 30 min and 46 min in the presence of micelles m1 and micelles m2 respectively. However, it is observed from the cumulative heat release amount curves (Fig. 5(b), (d) and (f)) that the total heat release amount (up to 7 days) was increased by the admixed micelles. For example, with a w/c ratio of 0.3, the cumulative heat release amount (up to 7 days) was increased by 12.55 W g−1 and 12.98 W g−1 in the presence of micelles m1 and micelles m2 respectively. The heat release results indicate that in the presence of the admixed micelles, although the hydration rate of C3S is retarded during the first 15 h, the hydration degree of cement paste is increased at the hydration age of 7 days.
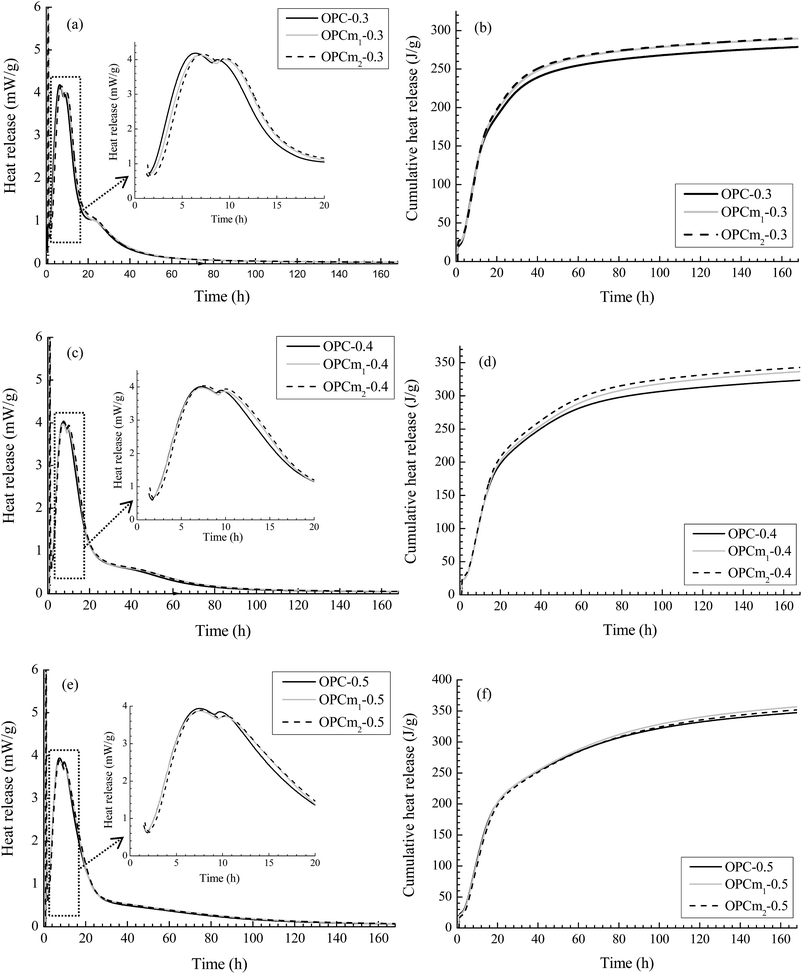 |
| Fig. 5 (a), (c) and (e) Hydration rate and (b), (d) and (f) cumulative heat evolution of cement pastes with a w/c ratio of 0.3, 0.4 and 0.5 respectively. | |
3.2.2 Microstructure of cement paste in the presence of the micelles. Fig. 6 shows the cumulative intruded volume curves and differential distribution curves for both the micelles-free and micelles-containing specimens (with different w/c ratios) derived from MIP tests at the hydration age of 7 days. The differential distribution curves (Fig. 6(b), (d) and (f)) show that at the hydration age of 7 days, the critical pore size of both gel pores and capillary pores (defined as the peaks in the differential distribution curves, giving the rate of mercury intrusion per change in pressure22,23) was similar both for the micelles-free and micelles-containing specimens. However, the total porosity of cement paste was reduced by the admixed micelles as shown in the cumulative intruded volume curves (Fig. 6(a), (c) and (e)). For example, with a w/c ratio of 0.4, the total porosity was 0.107 mL g−1 for specimen OPC, 0.093 mL g−1 for specimen OPCm1 and 0.100 mL g−1 for specimen OPCm2 respectively. The results indicate that due to the accelerated hydration rate, in the presence of the admixed micelles, cement paste presents a denser microstructure.
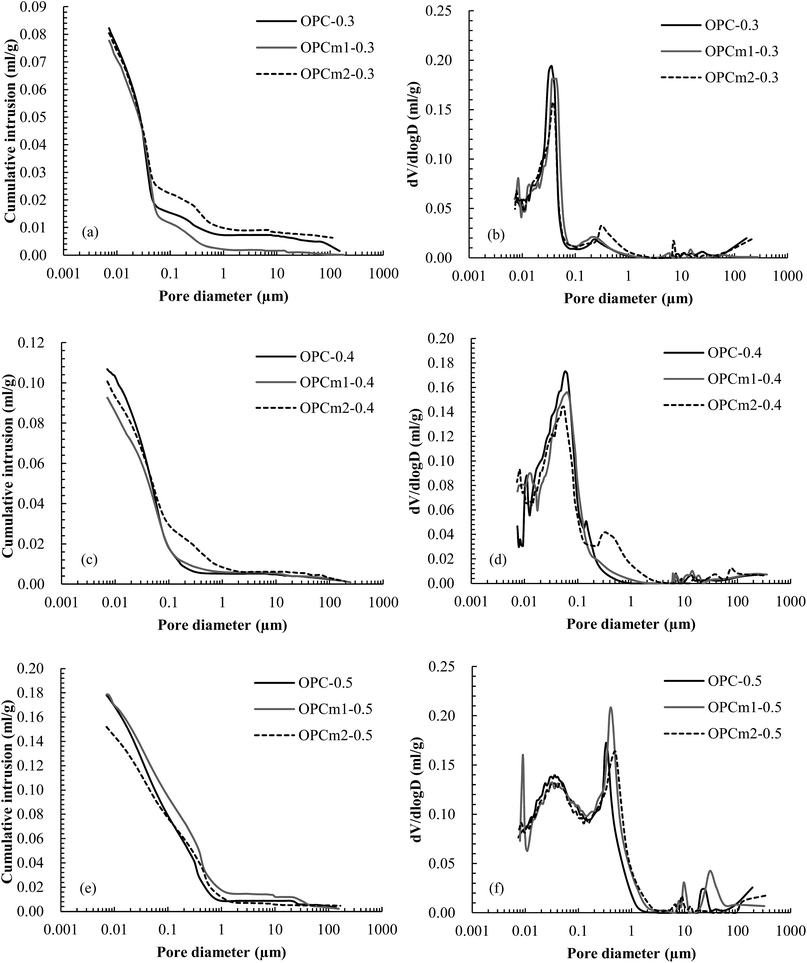 |
| Fig. 6 (a), (c) and (e) Cumulative intruded volume curves and (b), (d) and (f) differential distribution curves of cement pastes with a w/c ratio of 0.3, 0.4 and 0.5 at 7 days hydration age respectively. | |
3.2.3 Compressive strength of cement paste in the presence of the micelles. Fig. 7 shows the influence of the admixed micelles on the compressive strength of cement paste at the hydration ages of 3 days and 7 days, respectively. The compressive strength results were consistent with the hydration process determined by isothermal calorimetry tests. At each hydration age (3 d and 7 d respectively), the admixed micelles slightly increased the compressive strength of cement paste. For example, at the hydration age of 7 days, with a w/c ratio of 0.4, the compressive strength was 40.66 MPa for specimen OPC, 44.23 MPa for specimen OPCm1 and 42.24 MPa for specimen OPCm2 respectively. The increased compressive strength is related the accelerated hydration rate and denser microstructure of cement paste in the presence of the admixed micelles.
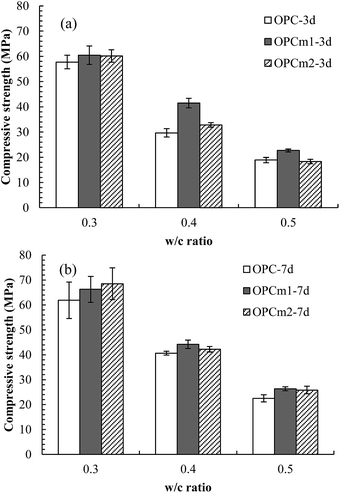 |
| Fig. 7 Compressive strength of cement pastes with different w/c ratios: (a) 3 days and (b) 7 days. | |
4. Discussions
4.1 The influence of the admixed micelles on the workability of cement paste
It is well known that the fluidity of fresh cement paste is closely related to the dispersion of cement particles, which is mainly determined by the electrostatic repulsive force and van der Waals force among particles.24,25 Polymers (normally used as superplasticizers) were widely reported to improve the workability of cement-based materials by increasing the electrostatic repulsive force and steric hindrance between cement particles.26,27 In the present study, the admixed micelles also improved the workability of cement paste, and the mechanisms may be related to the molecular structure and adsorption performance of the micelles as shown in Fig. 8. In this study, the TOC results indicate that because of the large negative zeta potential and high specific surface area, two micelles were both effectively adsorbed on the surface of positively charged cement particles (Fig. 2). Although the adsorbed micelles didn't significantly alter the average zeta potential value of cement particles (Table 2), with a higher w/c ratio, partial cement particles presented larger negative zeta potential values in the presence of the admixed micelles (Fig. 3); thus the electrostatic repulsive force among cement particles was increased. Further, the micelles are amphiphilic formations, presenting a hydrophobic core and hydrophilic corona;15,18 the adsorption of the spherical micelles also provides steric hindrance effect to improve the distribution of cement particles. Therefore, in the presence of the micelles, the combination of the above effects leads to a better dispersion of cement particles and increased fluidity of fresh cement paste (Fig. 4).
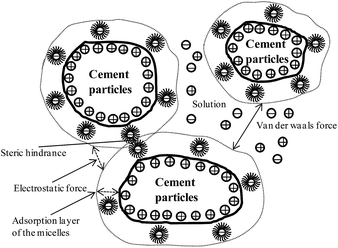 |
| Fig. 8 Effect of the admixed micelles on the dispersion properties of cement particles. | |
4.2 The influence of the admixed micelles on the hydration process and microstructure of cement paste
As mentioned in Section 3.1.1, the influence of the admixed micelles on the hydration process of cement paste was different during the first 15 h and later hydration ages (up to 7 days) respectively. The most plausible reasons are described as follows: during the first 15 h, because the micelles effectively adsorb on the surface of cement particles, the exchange of Ca2+ ions at cement particle/solution interface is hindered. The early hydration rate of cement is significantly influenced by the dissolution of Ca2+ and OH+ ions,28 thus this hindrance effect delays the hydration of C3S and impedes the formation of hydration products during the first 15 h (Fig. 5(a), (c) and (e)). This is also consistent with the experiment results about the influence of polymer-based superplasticizers on the hydration of cement-based materials reported elsewhere24,26 and our previous investigations on the early hydration process of cement paste in the presence of PEO-b-PS dibolck copolymer micelles.11 At later hydration ages (up to 7 days), as mentioned in Section 4.1, the adsorbed micelles alter the surface properties of cement particles, improving their dispersion and initial particle packing density. It was also reported that if the solid surface (cement particles or micelles in this case) matched well with the formed solid (hydration products in this case), the interfacial energy between the two solids was smaller than that between the formed solid and solution; thus nucleation might take place at a lower saturation ratio on solid surface than in solution.29 Therefore, when a small amount of micelles is uniformly dispersed in cement paste, hydration products can easily grow around the micelles due to their great surface energy and form conglomeration containing the micelles as nucleus.30,31 The micelles acting as nucleus can further accelerate cement hydration by reducing the energy barrier. Further, another hypothesis explaining the promoted hydration rate of cement paste is related to the more uniform distribution of hydration products in the presence of the admixed micelles, as shown in Fig. 9. In cement paste without the micelles (Fig. 9(a)), hydration products mainly form around cement grains, leading to a thick hydration product layer which retards the diffusion of Ca2+ and OH+ ions. In cement paste with the micelles (Fig. 9(b)), hydration products can also form on the admixed micelles both adsorbed on the surface of cement particles and in pore solution, leading to an reduced thickness of hydration product layer and more homogeneous cement matrix, which is beneficial for further cement hydration. The above experiment results and discussions are well in line with nano indentation results of cement paste in the presence of PEO-b-PS micelles in our previously reported study.11 Therefore, at later hydration age, the nucleation effect, together with the better dispersion of cement particles, improved particle packing density and uniform distribution of hydration products promote the hydration rate of cement paste (Fig. 5(b), (d) and (f)), which is beneficial for the formation of a denser and more homogeneous matrix (Fig. 6) and strength development (Fig. 7).
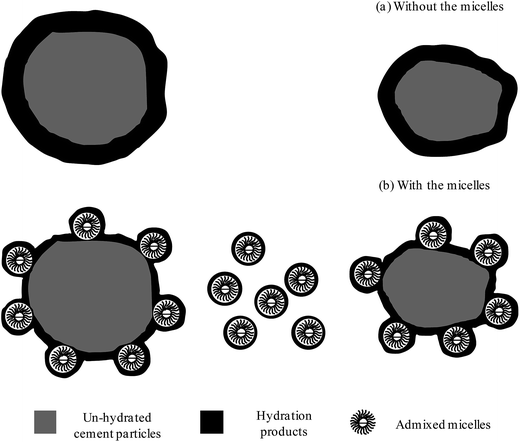 |
| Fig. 9 A hypothesis on the acceleration of cement hydration by the admixed micelles. | |
It needs to be mentioned that the above relevant possible mechanisms related to the influence of admixed micelles on the material properties of both fresh and hardened cement paste are mainly based on the derived experiment results in this study and reported literatures. The exact mechanisms are still to be clarified by further experimental evidences on the physical/chemical reactions between the micelles and cement particles/hydration products, e.g. rheology investigations on the yield stress and plastic viscosity alterations of fresh cement paste in the presence of the micelles, SEM observations on hydrations products formed around the micelles (nucleation effect), digital holographic microscopy observations on the hydration product layer formed around cement particles with/without admixed micelles (reduced hydration product layer). The above investigations will be involved in our future work. However, the influence of the admixed micelles on the workability, hydration process and microstructure development of cement paste is clear and well supported by the experimental results in this paper.
Based on the experiment results, the diblock micelles with pH-sensitive/hydrophobic structure prepared in this study present no harmful influence on the material properties of cement based materials, thus if proper healing agents are efficiently reserved in the micelles, they are promising self-healing materials for the corrosion control of reinforced concrete. However, this is not in the scope of this paper and will be further investigated and reported in the future.
5. Conclusions
In this study, in order to investigate the influence of the incorporated polymeric micelles with pH-sensitive/hydrophobic structure on the workability, hydration process and microstructure of cement paste, two types of micelles (P(PLAMA-co-tBMA)-b-PPEGMA (m1) or MPEG-b-(PLA-co-PAE) micelles (m2)) were admixed in cement paste with different w/c ratios. Based on the experiment results, the main conclusions can be summarized as follows:
(1) In fresh cement paste, the micelles were both efficiently adsorbed on the surface of cement particles: the adsorption amount was in the range of 0.073–0.107 mg g−1 for micelles m1 and 0.037–0.040 mg g−1 for micelles m2 respectively. Because the micelles concentration was quite low, the average zeta potential of cement particles was not significantly altered. However, with a higher w/c ratio (w/c ratio = 0.4 or 0.5), the adsorbed micelles altered the zeta potential distribution of cement particles and made partial cement particles negatively charged, leading to a better dispersion of cement particles and improved workability of fresh cement paste.
(2) In hardened cement paste, the hydration rate of C3S was slightly retarded by the admixed micelles at very early hydration age (first 15 h); however, at later hydration age (up to 7 days), the hydration rate of cement paste was accelerated by the admixed micelles. Further, the cement paste presented a denser and more homogenous microstructure in the presence of the admixed micelles, evidenced by the reduced total porosity derived from MIP tests. The accelerated hydration rate and refined pore structure resulted in increased mechanical properties of cement paste in the presence of the admixed micelles.
(3) The effects of the admixed micelles on the material properties of cement paste are mainly related to: (a) the micelles adsorb on the surface of cement particles and increase the electrostatic repulsive force and steric hindrance effect, improving the dispersion and particle packing density of cement particles; (b) the micelles act as nucleation sites for the formation of hydration products, leading to a more homogeneous matrix and further accelerated hydration rate; (c) the micelles reduce the thickness of the hydration product layer formed around cement grains, which is beneficial for the strength development of cement paste.
Acknowledgements
The authors would like to express the gratitude to Professor Lijuan Zhang in School of Chemistry and Chemical Engineering, South China University of Technology to provide the copolymers for the micelles preparation in this study. This study was funded by National High Technology Research and Development Program (“863 Program”, No. 2015AA034701), National Natural Science Foundation of China (No. 51572088 and 51402057), Pearl River S&T Nova Program of Guangzhou (No. 201506010004), State Key Laboratory of Silicate Materials for Architectures (Wuhan University of Technology, No. SYSJJ2015-08). Their financial supports are gratefully acknowledged.
References
- Y. Yu, J. Liu, Q. Ran, M. Qiao and N. Gao, Mag. Concr. Res., 2013, 65(3), 202 CrossRef CAS.
- X. Peng, X. Li, D. Chen and D. Ma, Mag. Concr. Res., 2013, 65(7), 422 CrossRef CAS.
- H. Tan, B. Ma, J. Huang and X. Li, Mag. Concr. Res., 2014, 66(23), 1194 CrossRef.
- Y. Luo, R. Huang, F. Xu and Y. Chen, J. Mater. Sci., 2014, 49(22), 7730 CrossRef CAS.
- A. Martin, R. A. Garcia, D. Sen Karaman and J. M. Rosenholm, J. Mater. Sci., 2014, 49(3), 1437 CrossRef CAS.
- R. Savic, L. Luo, A. Eisenberg and D. Maysinger, Science, 2003, 300, 615 CrossRef CAS PubMed.
- J. Fernandez-Carneado, M. J. Kogan, S. Castel and E. Giralt, Angew. Chem., Int. Ed., 2004, 43, 1811 CrossRef CAS PubMed.
- L. Y. Qiu and Y. H. Bae, Biomaterials, 2007, 28, 4132 CrossRef CAS PubMed.
- A. Nasser, A. Clement, S. Laurens and A. Castel, Corros. Sci., 2010, 52(9), 2878 CrossRef CAS.
- M. Mennucci, E. Banczek, P. Rodrigues and I. Costa, Cem. Concr. Compos., 2009, 31(6), 418 CrossRef CAS.
- J. Hu, D. A. Koleva, Y. Ma, E. Schlangen, P. Petrov and K. van Breugel, Cem. Concr. Res., 2012, 42(8), 1122 CrossRef CAS.
- J. Hu, D. A. Koleva and K. van Breugel, J. Mater. Sci., 2012, 47(12), 4981 CrossRef CAS.
- L. Chang, J. Liu, J. Zhang, L. Deng and A. Dong, Polym. Chem., 2013, 4, 1430 RSC.
- C. Y. Zhang, W. S. Wu, N. Yao, B. Zhao and L. J. Zhang, RSC Adv., 2014, 4, 40232 RSC.
- Y. Q. Yang, X. D. Guo, W. J. Lin, L. J. Zhang, C. Y. Zhang and Y. Qian, Soft Matter, 2012, 8(2), 454 RSC.
- R. Lin and H. G. Cui, Curr. Opin. Chem. Eng., 2015, 7, 75 CrossRef.
- M. Licciardi, G. Giammona, J. Z. Du, S. P. Armes, Y. Q. Tang and A. Lewis, Polymer, 2006, 47, 2946 CrossRef CAS.
- C. Y. Zhang, Y. Q. Yang, T. X. Huang, B. Zhao, X. D. Guo, J. F. Wang and L. J. Zhang, Biomaterials, 2012, 33(26), 6273 CrossRef CAS PubMed.
- E. W. Washburn, Phys. Rev., 1921, 17(3), 273 CrossRef.
- Y. Hu, B. Ma and H. Tan, Mag. Concr. Res., 2013, 65(19), 1212 Search PubMed.
- W. McCarter and A. Afshar, J. Mater. Sci., 1988, 23(2), 488 CrossRef CAS.
- X. Jin, Y. Shen and Z. Li, Mag. Concr. Res., 2005, 57(6), 339 CrossRef.
- Y. Ma, J. Hu and G. Ye, J. Mater. Sci., 2012, 47(11), 4568 Search PubMed.
- M. Mollah, W. Adams, R. Schennach and D. Cocke, Adv. Cem. Res., 2000, 12(4), 153 CrossRef CAS.
- Y. W. Li, C. L. Yang, Y. F. Zhang, J. Zheng, H. L. Guo and M. G. Lu, Constr. Build. Mater., 2014, 64, 324 CrossRef.
- D. Jansen, J. Neubauer, F. Goetz-Neunhoeffer, R. Haerzschel and W. D. Hergeth, Cem. Concr. Res., 2012, 42(2), 327 CrossRef CAS.
- H. Uchikawa, S. Hanehara and D. Sawaki, Cem. Concr. Res., 1997, 27(1), 37 CrossRef CAS.
- H. F. W. Taylor. Cement Chemistry, Thomas Telford Publishing, London, 1997 Search PubMed.
- W. Stumm. Chemistry of the Solid-Water Interface, Wiley, New York, 1992 Search PubMed.
- D. A. Silva and P. J. M. Monteiro, Cem. Concr. Res., 2005, 35, 351 CrossRef CAS.
- L. Nicoleau, J. Transp. Res. Board, 2010, 2142, 42–51 CrossRef CAS.
|
This journal is © The Royal Society of Chemistry 2017 |
Click here to see how this site uses Cookies. View our privacy policy here.