DOI:
10.1039/C7RA00508C
(Paper)
RSC Adv., 2017,
7, 19257-19261
Novel terpolymers as viscosity reducing agent for Tahe super heavy oil
Received
12th January 2017
, Accepted 26th February 2017
First published on 31st March 2017
Abstract
The four components of extra-heavy oil (saturates, aromatic, resins, asphaltene) were analyzed by chemical separation. The terpolymers with different contents of styrene (S), alkyl chain (MM/DM), and vinyl acetate (V) were designed, synthesized and employed as the viscosity reducers for super heavy oil. Thus, structure and average molecular weight of the oil-soluble terpolymers were measured by Fourier-transform infrared (FTIR) and gel permeation chromatography (GPC), respectively. Comparing with the apparent viscosity of heavy oil in a wide range of shear rates (0.1–200 s−1) and temperatures (25–75 °C), it can be seen that optimal efficiency could be achieved to reduce viscosity when the terpolymer has a high percentage of long-chain alkyl. Furthermore, the molar ratio between long-chain alkyl groups and aromatic ring as well as molecular weight of terpolymers play a fundamental role in viscosity reduction of super heavy oil.
1 Introduction
Advances in exploration and development technologies in the petroleum industry make the production of new energy resources possible. Currently, heavy and extra-heavy oil resources maintain a good and upward momentum in global energy markets because of the decreasing production of light crude oil. Extra-heavy oil resources in China are abundant and mainly distributed in oil fields, such as Xinjiang and Northeast China. The process of exploitation and transportation faces enormous challenges in flow assurance, where the principal objective is viscosity reduction.
The high viscosity of heavy oils has been attributed to condensed polyaromatic compounds such as resins and asphaltene and content of heavy metals such as nickel and vanadium. The resin and asphaltene molecules contain hydroxyl, amino, carboxyl, carbonyl and other functional groups which can form hydrogen bonds. Therefore, there are strong hydrogen bonds between the resin and asphaltene molecules. The overlap of aromatic ring planes in resin and asphaltene is fixed by hydrogen bond, and associated super molecular structure.1–3 When the relative displacement of the crude oil molecules can generate a great internal friction, there is heavy viscosity of crude oil.
High viscosity can lead to a series of problems in exploitation, transportation, and refining of crude oil.4–6 Currently, the most common and successful method is thermal technologies in the world, which include steam flooding, high temperature oxidation, steam assisted gravity drainage, etc.7–9 However, reservoirs in Northwest China are deeply buried and geological environment is complex. Deep wells will cause energy loss and low productivity. In addition, horizontal well production practice is not suitable for heterogeneous reservoirs. Other common-used approach in China that has been used to reduce viscosity in heavy crude oils will employ blending light oil.10 However, such dilution and blending method usually requires a lot of light oil, which must have a convenient source.11,12
Another method of reducing the viscosity of heavy oil is to use viscosity reducer chemicals. All chemical additives have a strong selectivity for crude oil.13,14 Many chemical polymers have been developed as flow improvers for heavy crude oils, but these compounds of polymers are designed for paraffin, to reduce the pour point, and have moderate to little effect in asphaltenic oils.15 The researchers all pay attention to the structure characterization of resin and asphaltene in crude oils. Moreover, the reactivity ratios of the monomers employed in the polymerization are different, and the research show that homogeneous terpolymerizations are obtained under monomer-starved conditions in semi-continuous processes independent of reactivity values.2 In recent years, molecular simulation method was introduced to analyses the interactions among resin, asphaltene and synthesized polymer. Therefore, it is highly desirable for the development of the polymer molecules, which are capable of dispersing or breaking aggregates of resins and asphaltene.
2 Materials and methods
A. Materials
Maleic anhydride, stearyl alcohol, styrene (S), vinyl acetate (V), azobisisobutyronitrile (AIBN), benzoylperoxide (BPO), p-toluenesulfonic acid, toluene, heptane, methanol and 1-dodecanethiol were purchased and used without further purification. Distilled water was used during the experiments. Heavy crude oil was obtained from the Tahe Oilfield (in China's Xinjiang), the properties of which are shown in Table 1.
Table 1 Physical characterization of crude oil
Parameter |
Unit |
Value |
Density |
g cm−3, 25 °C |
0.966 |
API gravity |
60/60 °F |
14.9 |
Wax content |
wt% |
1.8 |
Pour point |
°C |
42 |
Viscosity |
mm2 s−1, 50 °C |
3665 |
Sediment |
wt% |
7.05 |
Saturates |
wt% |
20.29 |
Aromatic |
wt% |
26.12 |
Resin |
wt% |
19.03 |
Asphaltene |
wt% |
27.51 |
B. Synthesis and evaluation
The dioctadecyl maleate (DM) was prepared using maleic anhydride and stearyl alcohol as raw materials in the presence of p-toluenesulfonic acid as catalyst, and the reaction was carried out for 3.5 h at 95 °C. Monostearyl maleate (MM) was also synthesized from maleic anhydride and stearyl alcohol for 5 h at 140 °C. The mole ratios of DM and MM were 2.1
:
1 and 1.2
:
1. Random terpolymers with various molar ratios of polymer monomers (DM or MM), S and VA were synthesized via free-radical polymerization in toluene solution under an argon atmosphere, using azobisisobutyronitrile as the initiator (0.8 wt%) and 1-dodecanethiol as the chain transfer agent at 75 °C. About 4 h later, the reaction mixture was cooled to room temperature and poured dropwise in cooled methanol with continuous stirring. The precipitate was collected by filtration and dried at 65 °C for 24 h, appearing as either white viscous liquid or white powder. The structure of the polymer monomers (DM, MM) and copolymer were confirmed by Fourier-transform infrared (FTIR) spectroscopy (BRUKER). The molecular weights of synthesized copolymers (DM–S–V, MM–S–V) were determined by using gel permeation chromatography (GPC; Perkin Elmer Corporation).
C. Sample preparation
Heavy crude oil is a black solid at room temperature and the apparent viscosity could not be measured. Firstly, heavy oil was heated in an oven for 2 h and then blended and stirred with light oil (kerosene, diesel oil) to form a stable homogeneous mixture. To obtain results consistent with accurate rheological properties, the memory of the evaluated untreated crude oil sample and all crude oil used as an additive with viscosity reducer, have to be removed by heating at 50 °C while stirring. Finally, all samples in the container were maintained at the temperature required for the reaction for a few minutes.
D. Rheological behavior of crude oil
Samples of 20 g of heavy crude oils were dosed with 0.2 g of a solution of terpolymers. The rheological investigation was carried out using the MCR-302 rheometer (Anton-Paar Physica, made in Austria), equipped with a variety of concentric cylinders. The crude oil was examined under a shear rate range of 1.0–200.0 s−1 at 50 °C. For comparative purposes, untreated crude oil was measured to be used as reference samples.
3 Results and discussion
A. Characterizations of viscosity reducer chemicals
The compositions of the synthesized monomers were characterized by the IR spectrometry. The spectrum of MM is clearly shown in Fig. 1, and an absorption band corresponding to the OH stretch of the carboxyl group is present at 3522.50 cm−1. The ester group bands resulting from the C
O and C–O–C stretching were found at 1728.56 cm−1 and 1222.51 cm−1, respectively, and an absorption band corresponding to the carboxyl group is present at 1706.79 cm−1. The characteristic C
C stretching peak appears near 1636.86 cm−1. The spectrum of DM, which contains two long-chain alkanes, is shown in Fig. 2, displaying absorption bands near 2916.60 and 2850.19 cm−1 for methyl and methylene groups, respectively, as well as stretches at 1729.08 and 1222.92 cm−1 for the ester group (C
O and C–O–C). A characteristic C
C stretching band appears near 1637.40 cm−1. The antisymmetric and symmetric peaks of C
O in maleic anhydride do not appear near 1850 and 1780 cm−1, and thus the product is proved to be DM.
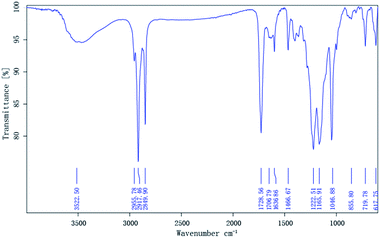 |
| Fig. 1 IR spectrum of MM. | |
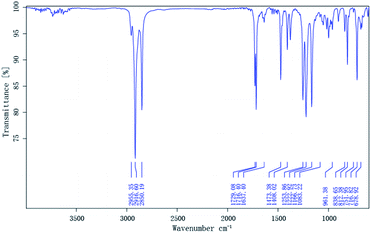 |
| Fig. 2 IR spectrum of DM. | |
The free-radical polymerization, widely employed in many modern industrial processes, consists of three stages: initiation, propagation, and termination. The amount of chain-transfer agent (CTA), monomer molar ratio, reaction time can affect the performance of the polymer. The chemical structure of the synthesized compounds is shown in Fig. 3. It is important to mention that the conversion rate of the polymerization reaction is above 80% and therefore, the monomer mixtures were added in one.8
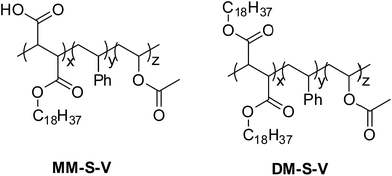 |
| Fig. 3 Structural representation of terpolymers (MM–S–V and DM–S–V). | |
Terpolymers composition were determined by GPC. Table 2 shows the polymer composition (PC), average molecular weights (Mw and Mn), polydispersity (PD), and degree of polymerization of the terpolymers. The IR spectra of the prepared terpolymers of MM–S–V and DM–S–V are shown in Fig. 4 and 5, respectively. For example, the methyl and methylene absorption bands (2916.84 and 2849.91 cm−1), as well as stretches at 1729.51 and 1223.66 cm−1 for the ester group (C
O and C–O–C), and the strong absorption peak of the benzene ring (1473.33 cm−1) appear in Fig. 5, and DM was confirmed.
Table 2 Composition and molecular-weight characterization of terpolymers
Polymer code |
MM (mol%) |
DM (mol%) |
S (mol%) |
VA (mol%) |
Mw |
Mn |
S1 |
5.0 |
— |
71.5 |
23.5 |
3172 |
2420 |
S2 |
20.0 |
— |
60.0 |
20.0 |
4315 |
3171 |
S3 |
20.0 |
— |
60.0 |
20.0 |
42 660 |
19 852 |
S4 |
— |
33.5 |
16.5 |
50.0 |
4561 |
3014 |
S5 |
— |
50.0 |
12.5 |
37.5 |
3752 |
3146 |
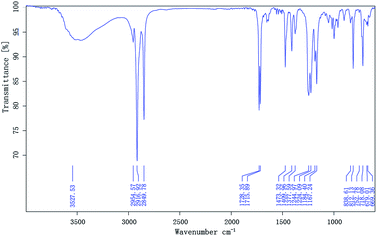 |
| Fig. 4 IR spectrum of MM–S–V. | |
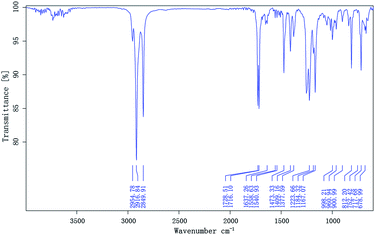 |
| Fig. 5 IR spectrum of DM–S–V. | |
B. Rheological studies
The apparent viscosity of the crude oil sample was determined at different shear rates and temperatures, using a Physica MCR302 rheometer. The original rheological properties of Tahe crude oil is shown in Fig. 6. It is clearly seen that at 50 °C, the apparent viscosity is not constant at different shear rates (shear curve). The changes of viscosities curve at shear rates between 0.1 and 143 s−1 are very small (e.g., from 2.78 Pa s at 0.1 s−1 to 2.12 Pa s at 143 s−1). By increasing the shear rate, the apparent viscosity decreases dramatically. This rheological behavior of the crude oil is “non-Newtonian” fluid (similar to Bingham plastic fluid).16,17 It is also obvious that heavy oil is very sensitive to temperature. When the temperature rises by 10 degrees, the viscosity almost became the half (temperature curve in Fig. 9), which is due to the reason that the thermal recovery method is so common in the petroleum sector.
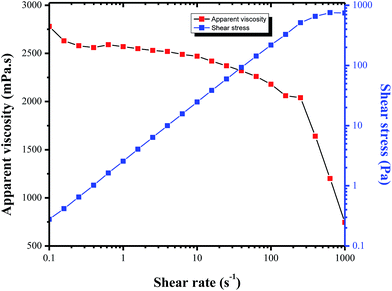 |
| Fig. 6 Rheogram of the heavy oil sample at 50 °C. | |
C. Effect of the molecular weight and molecular composition on viscosity-reducing property
Fig. 7 shows representative plots of shear rate (γ) versus apparent viscosity (η) of heavy crude oil containing 1 wt% of terpolymers at 50 °C. Untreated crude oil and that containing terpolymers showed non-Newtonian fluid properties, and thus using simple Newtonian behavior to explain flow properties is inaccurate. At a shear rate lower than 2.5 s−1, the apparent viscosity fluctuation is more evident. Shear continued to increase, showing a slow decline trend, as mentioned in the literature.2
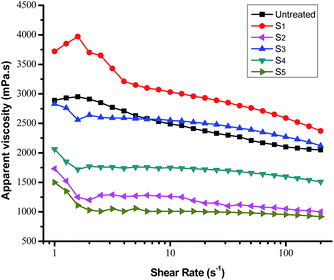 |
| Fig. 7 Apparent viscosity of heavy crude oil containing 1 wt% of terpolymer solution as a function of the shear rate at 50 °C. | |
It can be seen that terpolymers S2, S4 and S5 diminish the crude oil apparent viscosity obviously. The efficiency of viscosity reducing chemicals depends upon the average molecular weight, alkane chain length, solubility and intermolecular interactions between polymer and crude oil. The performance of terpolymer, with an adequate molecular weight, mainly depends upon its composition and monomer ratio. For example, the terpolymer S2, with an adequate molecular weight, was a better flow improver than S3 in almost similar composition conditions. Similarly, the terpolymer S3 and S2, with very different molecular weights and similar composition, show completely different flow behavior. In contrast, S4 and S5, with a rich alkane chain composition, both show the apparent viscosity reduction. The viscosity curve confirms that terpolymer S5 exhibited the most considerable reduction of apparent viscosity. An analysis of rheological behavior of a series of terpolymers used as viscosity reducers reveals that, the higher content of DM, the greater the viscosity reduction. Furthermore, suitable long-chain alkanes (MM, DM) can improve the performance of terpolymer, when the content of styrene is higher. The performance of a terpolymer as a flow improver can be explained: (1) long-chain alkyl of terpolymer stretch in the periphery of the new structure, with a large degree of spatial extension, preventing further agglomeration of resin and asphaltene molecules and improve mobility of crude oil; (2) aromatic compounds with a certain rigidity in the terpolymer head capable of interacting with asphaltene aggregates by π–π stacking and hydrogen-bond formation. Also, the sheet structure of aromatic rings has dispersion and dissolution functions; (3) vinyl acetate is widely used in pour point depressants in the oil industry. Smaller molecules have more penetrating character, to fit into the crude chemical structure, and they also have a certain effect on viscosity reduction. Terpolymers added to the crude oil disperses in asphaltenes and resins, overcoming hydrogen bonds, creating new spaces, and thus reducing the apparent viscosity of heavy crude oil.
D. Effect of the concentration of terpolymers on apparent viscosity
Viscosity reducing chemicals' (VRC) efficiencies as a function of terpolymers concentration are shown in Fig. 8. It can be seen that efficiencies grow rapidly for terpolymers S2 and S5, but it is lower for terpolymer S4 than for terpolymers S2 and S5, which have efficiencies above 30% at 1 wt%. The efficiency of the terpolymer is higher in the optimal concentration. When it exceeds the optimum additive concentration, the effect of viscosity reduction will be worse. The main reason for the increase in viscosity could be that the higher molecular weight polymer is adsorbed on the resin and asphaltene molecules,10 and, a large number of experiments have confirmed this phenomenon. Therefore, optimal concentration of terpolymers should also be concerned in the laboratory experiment.
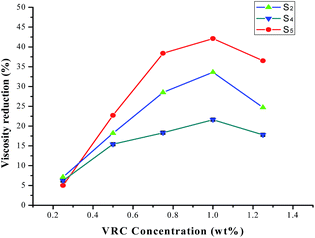 |
| Fig. 8 Viscosity reduction of heavy oil with different VRC concentration at 50 °C. | |
E. Effect of formation temperature on apparent viscosity
Fig. 9 shows the results of both untreated and treated heavy oil viscosity versus temperature (in 25–75 °C), in which all samples were examined at a shear rate (γ) of 50 s−1. Also, it clearly shows that the addition of the viscosity reducer causes viscosity reduction, being more evident between 30–50 °C. The terpolymer S5 is the best additive for reducing viscosity, sensibly improving the flow. Indeed, crude oil with the S5 agent presents 40.5% of viscosity reduction at 50 °C. It is possible to compare viscosity variation of the three best terpolymers.
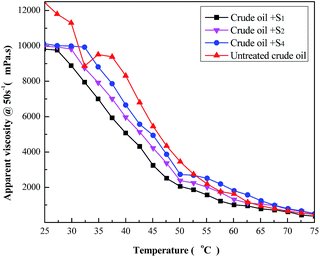 |
| Fig. 9 Temperature effect on the apparent viscosity of the heavy crude oil containing 1 wt% of terpolymer solution. | |
4 Conclusions
In this study, SARA analysis shows that the content of asphaltene and resins in the crude oil was up to 27.51 wt% and 19.03 wt%. These two parts of non-hydrocarbon component are the main aims in the process of reducing the viscosity of heavy oil. The following conclusions can be drawn from this research work:
(1) A series of terpolymers additives (DM–S–VA, MM–S–VA) were successfully designed, synthesized, and evaluated as viscosity reducing chemicals for heavy crude oil from Tahe Oilfield. Terpolymers S2, and S5 show good efficiency as viscosity reducing chemicals and satisfy the requirements of flow improvers. The molecular weight of terpolymers is a problem worthy of attention when comparing the S2 and S3, which is closely related to the solubility in the heavy crude oil.
(2) The introduction of aromatic compounds (styrene) with a certain rigidity, into the terpolymers, make it capable of interacting with asphaltene aggregates by π–π stacking and hydrogen-bond formation. It is important to note that suitable long-chain alkyl groups in terpolymers show better advantage, and this efficiency could directly related to the initial components of crude oil. The role of the aromatic compounds and the long-chain alkyl groups could not be neglected, where terpolymers S2, S4 and S5 have better efficiency than other groups.
(3) The viscosity reducing effect of terpolymers decreased as temperature increased form temperature curve, and temperature is the dominant factor affecting viscosity of crude oil after about 50 °C. However, the higher heat in the pit shaft is helpful in the contact interaction between terpolymers and heavy oil molecules. Therefore, this process can promote the effect of viscosity reduction when the oil is cooled down in lifting and transportation.
(4) The aggregation mechanism of asphaltene and resin is the basis for viscosity reducer, and how the monomers in viscosity reducing chemicals interact with the surfaces to reduce friction and improve flow properties of heavy crude oil in lifting and transportation, are performed in our laboratory.
Acknowledgements
The research is supported by Sichuan Youth Science & Technology Foundation (2017JQ0010), National High Technology Research & Development Program (2016ZX05053), Key Fund Project of Educational Commission of Sichuan Province (16CZ0008), Explorative Project Fund (G201601) of State Key Laboratory of Oil and Gas Reservoir Geology and Exploitation (Southwest Petroleum University), the Major Program of the National Natural Science Foundation of China (51490653) and 973 Program (2013CB228004).
Notes and references
- J. Murillo-Hernández, I. García-Cruz, S. López-Ramírez, C. Durán-Valencia, J. M. Domínguez and J. Aburto, Energy Fuels, 2009, 23, 4584 CrossRef.
- L. V. Castro, E. A. Flores and F. Vázquez, Energy Fuels, 2011, 25, 539 CrossRef CAS.
- T. E. Chávez-Miyauchi, L. S. Zamudio-Rivera and V. Barba-López, Energy Fuels, 2013, 27, 1994 CrossRef.
- B. Wu and J. Gao, Pet. Sci. Technol., 2010, 28, 1919 CrossRef CAS.
- J. J. Ge, A. Z. Feng, G. C. Zhang, P. Jiang, H. H. Pei, R. D. Li and X. Fu, Energy Fuels, 2012, 26, 2875 CrossRef CAS.
- Z. Huang, L. Yang and B. Wang, J. Jilin Inst. Chem. Technol., 2003, 20, 25 Search PubMed.
- H. H. Pei, G. C. Zhang, J. J. Ge, M. G. Tang and Y. F. Zheng, Energy Fuels, 2012, 26, 2911 CrossRef CAS.
- L. V. Castro and F. Vázquez, Energy Fuels, 2008, 22, 4006 CrossRef CAS.
- L. V. Castro and F. Vázquez, Energy Fuels, 2009, 23, 1603 CrossRef CAS.
- M. Cui, C. Li and P. Wen, J. China Univ. Pet., Ed. Nat. Sci., 2013, 37, 161 CAS.
- Y. Peysson, A. Bensakhria, G. Antonini and J. F. Argillier, SPE Prod. Oper., 2007, 22, 135 CrossRef CAS.
- J. Li, Oilfield Chem., 1987, 4, 146 Search PubMed.
- H. Sun and F. S. Zhang, Fine Spec. Chem., 2005, 13, 16 CAS.
- B. F. Wu and J. B. Guo, Oil Gas Storage Transp., 2003, 22, 6 Search PubMed.
- F. S. Zhang and B. Wang, Oilfield Chem., 2003, 12, 117 Search PubMed.
- A. Bensakhria, Y. Peysson and G. Antonini, Oil Gas Sci. Technol., 2004, 59, 523 Search PubMed.
- D. Chanda, A. Sarmah, A. Borthakur, K. V. Rao, B. Subrahmanyam and H. C. Das, Fuel, 1998, 77, 1163 CrossRef CAS.
|
This journal is © The Royal Society of Chemistry 2017 |
Click here to see how this site uses Cookies. View our privacy policy here.