DOI:
10.1039/C7RA03118A
(Paper)
RSC Adv., 2017,
7, 24418-24424
Facile and controllable synthesis of solid Co3V2O8 micro-pencils as a highly efficient anode for Li-ion batteries†
Received
16th March 2017
, Accepted 26th April 2017
First published on 4th May 2017
Abstract
Mixed metal vanadate oxides are promising superior anode materials for lithium ion batteries due to their high specific capacities, improved cycling performance and excellent rate properties. In this work, we demonstrate a facile and controllable synthesis of solid Co3V2O8 micro-particles with different morphologies through a hydrothermal method. By controlling the reaction time, either Co3V2O8 micro-plates or micro-pencils could be fabricated. Characterization via X-ray diffraction (XRD) and transmission electron microscopy (TEM) demonstrated the pure phase and solid morphology of the Co3V2O8 micro-pencils. Scanning electron microscopy (SEM) images of the products obtained at different stages clearly revealed the formation process of the Co3V2O8 micro-pencils. Electrochemical measurements of the Co3V2O8 micro-pencils showed an excellent lithium storage capacity (1137 mA h g−1 at 200 mA g−1), good cycling retention (∼670 mA h g−1 after 330 cycles), desirable coulombic efficiency (∼100% for 350 cycles) and notable rate capability (300 mA h g−1 at 2000 mA g−1). The improved electrochemical performances of the solid Co3V2O8 micro-pencils indicate their great potential as high-performance anode materials for lithium ion batteries.
Introduction
Transition metal oxides for anode materials of lithium-ion batteries (LIBs) have attracted much attention owing to their high capacities, eminent initial coulombic efficiencies, and enhanced cycling performance.1–4 However, they may undergo various problems such as volume expansion and capacity fading5,6 which limit their practical application. Therefore, the morphology and particle size of the transition metal oxides need to be carefully designed and modulated7–11 to solve the above issues. Recently, researchers have reported that mixed metal oxides might have better electrochemical performance than single-phase metal oxides, with features such as higher ionic and electrical conductivity, enhanced reversible capacity and improved mechanical stability,12–15 which could be attributed to the interfacial effects and the synergistic effects of mixed cation species in the mixed metal oxides.16
Among various diverse mixed metal oxides, metal vanadates have attracted a lot of interest for their unique morphology and prominent electrochemical properties.17–24 For instance, through a simple solvothermal method, Yin et al. successfully synthesized MoV2O8 nanorods,18 which exhibited excellent specific capacity (over 1325 mA h g−1 after 50 cycles at 0.2 A g−1), high rate performance (a high specific capacity of 570 mA h g−1 at a current density of 10.0 A g−1), and good cycling stability, when employed as anode materials for LIB. Wu et al. recently obtained Co2V2O7 hexagonal microplates via a hydrothermal synthesis method, and the materials showed a high reversible capacity of 866 mA h g−1 with a nearly 100% capacity retention after 150 cycles.25 Similarly, Luo et al. prepared Co2V2O7 nanosheets on graphene oxide templates, which also displayed a high reversible capacity of 962 mA h g−1 at 0.5 A g−1, and an excellent rate capacity (441 mA h g−1 after 900 cycles at 5.0 A g−1).20 Besides Co2V2O7, other cobalt vanadium oxides (CVO), such as CoV2O6 and Co3V2O8, also exhibited good electrochemical performance when applied in both LIB anode materials and supercapacitors electrodes.26–31 In particular, Co3V2O8 with various morphologies (e.g., macroporous nanosheets,17 multilayered nanosheets,26 hollow hexagons,28 hollow microspheres,32,33 sponge networks,34 and nanowires35,36) have captivated loads of researchers because of their outstanding lithium storage properties. Although a few studies have manifested the promising electrochemical properties of Co3V2O8, there are still many interesting areas unexplored, e.g., the phase selection and electrochemical behavior of Co3V2O8. Wu and co-works have successfully procured the samples of Co3V2O8 micro-pencils for the first time,37 and revealed the transformation from solid to hollow structures. However, the solid Co3V2O8 micro-pencils as high performance anodes have not been exploited and the formation process of the Co3V2O8 micro-pencils have not been reported. On the other hand, the reported Co3V2O8 generally have porous or hollow structures, which may limit the electrochemical behavior in several aspects when utilized as LIB anodes.
In this work, we successfully synthesized solid Co3V2O8 particles via a facile and controllable hydrothermal method. The solid Co3V2O8 particles could form either micro-plate or micro-pencil structures depending on the controlled reaction time. The energy dispersive X-ray spectroscopy (EDS) and XRD results demonstrated the formation and phase selection of Co3V2O8. The SEM images of Co3V2O8 materials obtained at different reaction time remarkably unveiled the evolution process of Co3V2O8 micro-plates and micro-pencils. Through TEM and scanning TEM (STEM), the solid and hexagonal morphology were successfully observed. Simultaneously, the electrochemical performances of the Co3V2O8 solid micro-pencils as the anode materials for LIB were further characterized. The corresponding results demonstrated that the Co3V2O8 solid micro-pencils have a high specific capacity (initial discharge capacity of 1137 mA h g−1), long life span (capacity of ∼670 mA h g−1 after 330 cycles at 200 mA g−1), and notable rate performance (capacity of 300 mA h g−1 at 2000 mA g−1), which has great potential to be used as superior anode materials for lithium ion battery.
Experimental section
Sample preparation
Hydrothermal reactions were employed to synthesize Co3V2O8 materials. For Co3V2O8 micro-plates, 0.374 g of ammonium metavanadate was dissolved into 64 ml of deionized water at 80 °C. The solution was kept stirring until its color changed from pale yellow to green. Later, 0.08 g of LiOH H2O was dissolved into the above solution, which changed to be transparent and colorless after several minutes. Subsequently, 0.14 g of CoCl2·6H2O was added into the mixed solution. After stirring for 10 min, the reddish brown transparent solution was transferred into a 100 ml Teflon-lined autoclave, tightly sealed, put into an oven and heated at 200 °C for 2 h. After cooling to room temperature in air, the final products were washed several times by deionized water and absolute ethanol, and dried at 80 °C for 6 h, followed by annealing in air atmosphere at 300 °C for 4 h. For Co3V2O8 micro-pencils, all the conditions were kept same as used for Co3V2O8 micro-plates synthesis, except the hydrothermal reaction time was changed to 8 h.
Materials characterization
XRD analysis of the prepared samples were performed on a Bruker-D8 Advanced X-ray Diffractometer (Cu Kα radiation: λ = 1.5406 Å) with a scanning speed of 2 deg min−1. The morphologies of the prepared samples were observed by field-emission scanning microscope (FE-SEM, JSM-5900LV, JEOL). TEM, high resolution TEM (HRTEM) and scanning TEM (STEM) images were taken on a JEOL JEM-2100F microscope.
Electrochemical measurement
The electrochemical characterization was performed using 2032-type coin cells with two electrodes, assembled in an Ar-filled dry glove box with both the moisture and the oxygen content below 1 ppm. Co3V2O8 and Li metal were employed as the working and counter electrodes, respectively. The working electrode was prepared with 80 wt% active materials (Co3V2O8), 10 wt% conducting acetylene black, and 10 wt% PVDF. The slurry was pasted on a clean copper foil with a thickness of 0.2 mm. The loading density of the active material was about 1–2 mg cm−2. 1 M LiPF6 in ethyl carbonate (EC)–dimethyl carbonate (DMC) (1
:
1 by volume) was used as the electrolyte and a Celgard 2400 microporous membrane as the separator. Coin-type half-cells were tested at a voltage range of 0.01–3.0 V (vs. Li+/Li) at room temperature, using a CT2001A LAND Cell test system. Cyclic voltammetry (CV) testing was carried out between 0.01 and 3 V (vs. Li/Li+) at a scan rate of 0.5 mV s−1.
Results and discussion
Structure and morphology
The EDS results and the XRD pattern of the obtained Co3V2O8 micro-pencils are presented in Fig. 1, which demonstrate the composition and the successful phase selection of Co3V2O8 micro-pencils. As shown in Fig. 1(a) and S1,† the EDS results indicate the Co3V2O8 micro-pencils are composed of elements O, Co, and V. The detailed atomic ratio of Co/V is presented in Table S1† and reveals that the atomic ratio of Co/V is ∼1.67, indicating the formation of Co3V2O8. The XRD pattern in Fig. 1(b) shows that all the diffraction planes of the obtained Co3V2O8 micro-pencils can be perfectly indexed to the cubic crystal structure of Co3V2O8 (JCPDS no. 16-0675), which is consistent with other reported results.19,26 Fig. S2† displays the XRD pattern of the Co3V2O8 micro-pencils before annealing, which is notably compatible with the previous report of Co3V2O8·H2O.37
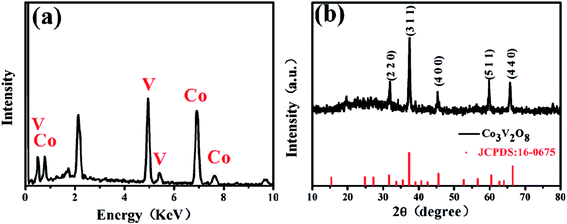 |
| Fig. 1 EDS spectrum (a) and XRD pattern (b) of the obtained Co3V2O8 micro-pencils. EDS spectrum indicates the obtained materials are composed of elements Co, V and O, while the XRD pattern demonstrates the obtained Co3V2O8 micro-pencils have cubic crystal structures (JCPDS no. 16-0675). | |
The SEM image in Fig. 2(a) clearly shows the morphology of the materials manufactured through the hydrothermal reaction for 6 h. A short pencil-like structure with a hexagonal cross section can be observed in the SEM image. The pencil-like Co3V2O8 particles have a uniform micro-scale size distribution (i.e., ∼3 μm in the hexagonal side length and ∼5 μm in the length). The Co3V2O8 micro-pencils exhibited a solid morphology, different from the commonly reported hollow structure28,38 is favorable for a high tap density and an enhanced volumetric lithium storage capacity when employed as LIB electrodes.30,39 Both the TEM image with low magnification in Fig. 2(b) and the scanning TEM (STEM) image in Fig. 2(c) can also demonstrated the solid morphology and the hexagonal cross section of the obtained Co3V2O8 micro-pencils. The high-resolution TEM image in Fig. 2(d) displays the measured inter-plane distance. The two inter-plane distance values, 0.252 nm and 0.209 nm, are in good agreement with the (311) (0.251 nm) and (400) (0.207 nm) lattice fringes of the cubic crystalline Co3V2O8. These two planes also correspond to the main peaks in the XRD results of the cubic crystalline Co3V2O8, as illustrated in Fig. 1(b).
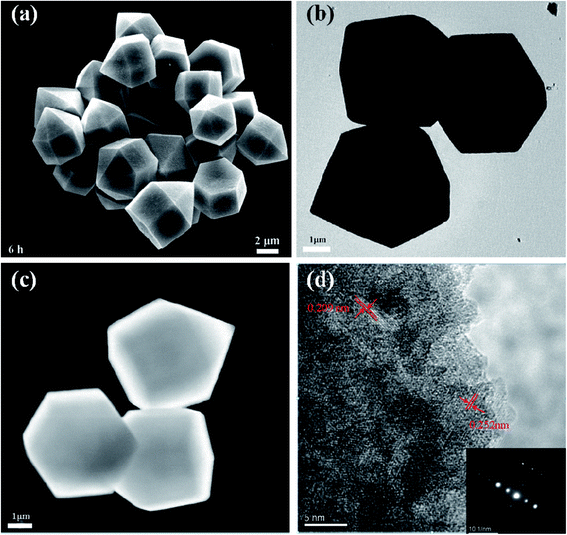 |
| Fig. 2 (a) SEM image of Co3V2O8 obtained for 6 h of hydrothermal reaction. The pencil-like structure with hexagonal cross section can be clearly observed. The Co3V2O8 micro-pencils have uniform size distribution. (b) TEM image with low magnification of Co3V2O8 micro-pencils. (c) STEM image of Co3V2O8 micro-pencils. The TEM and STEM images indicate the solid feature of Co3V2O8 micro-pencils. (d) High-resolution TEM image of Co3V2O8 micro-pencils. The two measured inter-plane distances agree well with the (311) and (400) lattice fringes of the cubic crystalline Co3V2O8, as shown in Fig. 1(b). The inset image in (d) is the corresponding SAED pattern. | |
Formation process of Co3V2O8 micro-pencils
To understand the growth mechanism of the unique Co3V2O8 micro-pencils, sample materials were collected at different reaction time during the hydrothermal process and their morphologies were characterized by SEM. As shown in Fig. 3, the morphologies of samples garnered at six stages during the hydrothermal reaction lucidly uncovered the formation process of the Co3V2O8 micro-pencils. Meanwhile, a proposed formation process of the Co3V2O8 micro-pencils and the corresponding schematic plot is presented in Fig. 4. At the initial stage, nanoscale spherical particles were formed (Fig. 3(a) and 4(a)) and gradually grow in both longitudinal and transverse directions to form microscale large clusters (Fig. 3(b) and 4(b)). As the reaction continues, hexagonal micro-plates are first observed, which are probably evolve from the nanoparticle clusters (Fig. 3(b)). When the reaction continues to 1 h, the hexagonal micro-plates probably undergo a crystallization process because of their more regular shape and smoother surface, as indicated by Fig. 3(c) and 4(c). The hexagonal micro-plates continue to grow both radially and longitudinally and larger diameter and thickness are obtained, which can be derived from Fig. 3(d). The hexagonal micro-plates start to peel off and the thinner sheets are observed when the reaction time is increased to 4 hours. More interestingly, micro-pencils begin to appear at this stage, as shown in Fig. 4(e) where both the micro-plates and micro-pencils can be clearly detected. After reaction for 5 h, the density of Co3V2O8 micro-plates is remarkably decreased, while the Co3V2O8 micro-pencils grow rapidly and attain the ultimate pencil-like morphology. When the reaction time is increased to 6 hours, the Co3V2O8 micro-plates completely disappear, and only the Co3V2O8 micro-pencils exist in the final products, as shown in Fig. 2(a). Based on the SEM images in Fig. 3, it can be concluded that the morphology and size of the products are entirely controlled by the hydrothermal reaction time. Therefore, Co3V2O8 with either micro-plate or micro-pencil structures can be successfully fabricated by easily controlling the reaction time. Moreover, we provided the XRD patterns of the samples collected at the six stages during the hydrothermal reaction in Fig. S3.†
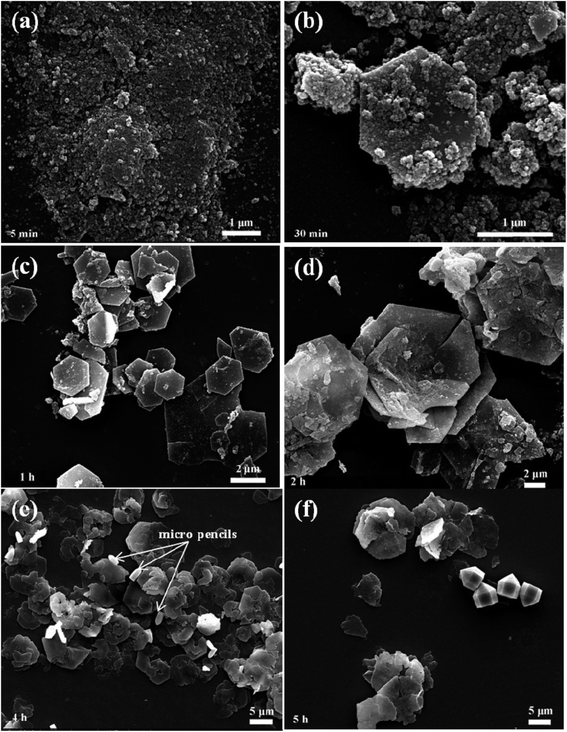 |
| Fig. 3 Typical SEM images of the products obtained during the hydrothermal reaction at different stages: (a) 5 min, (b) 30 min, (c) 1 h, (d) 2 h, (e) 4 h, and (f) 5 h. | |
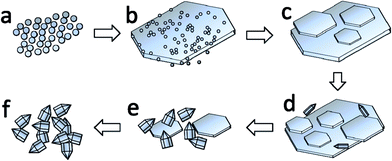 |
| Fig. 4 Schematic plot of the potential evolution process of the Co3V2O8 micro-pencils. | |
Electrochemical properties
The electrochemical properties of the obtained Co3V2O8 micro-pencils were characterized using 2032-type coin cells. The cyclic voltammograms (CVs) of the Co3V2O8 micro-pencils are presented in Fig. 5(a), which was obtained at a scan rate of 0.5 mV s−1 and in the potential window of 3 V to 0.01 V. In the first cathodic sweep, three reduction peaks were found at 1.59 V, 0.49 V, and 0.02 V, respectively, which could be assigned to the reduction of Co3V2O8 to CoO (Co3V2O8 → 3CoO + V2O5), the further reduction of CoO to metallic Co (CoO + 2Li+ + 2e− → Co + Li2O), and the formation of Li–Co alloys,40 respectively. Meanwhile, the reductions were accompanied with the lithiation of V2O5 (V2O5 + xLi+ + xe− → LixV2O5), and the further insertion of Li ions into LixV2O5 (LixV2O5 + yLi+ + ye− → Lix+yV2O5). During the reverse scan, two oxidation peaks were conspicuously observed at 1.65 V and 2.35 V. The lower oxidation peak at 1.65 V was owing to the de-alloying of Li–Co, Li+ extraction from Lix+yV2O5, and the oxidation of Co to CoO. The higher peak at 2.35 V was ascribed to the further extraction of Li ions from LixV2O5, and the oxidation of CoO to Co3V2O8.
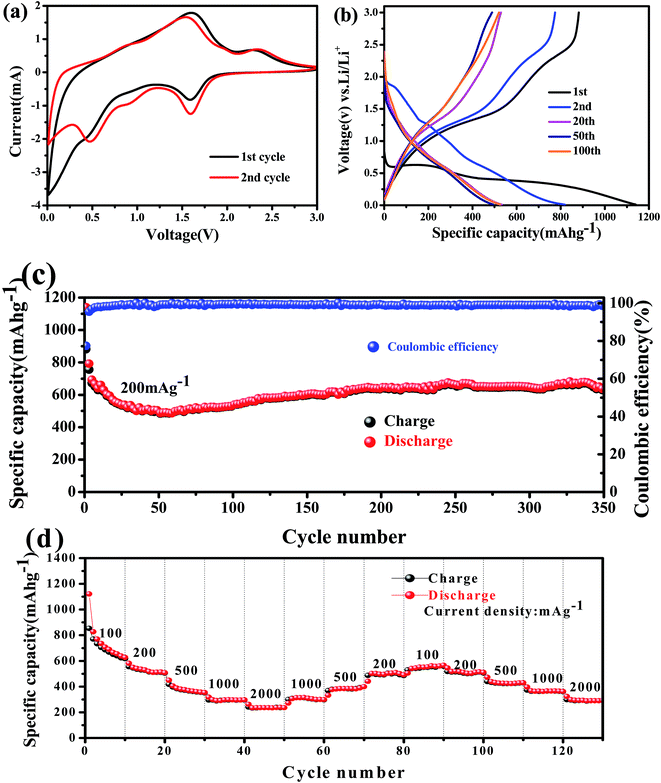 |
| Fig. 5 Electrochemical properties of Co3V2O8 micro-pencils: (a) cyclic voltammogram profiles of the Co3V2O8 micro-pencils; (b) discharge and charge curves at the current density of 200 mA g−1; (c) cycling property at the current density of 200 mA g−1, and (d) rate performance at different current densities. | |
Fig. 5(b) displays the galvanostatic discharge and charge results at the 1st, 2nd, 20th, 50th, and 100th cycle of the Co3V2O8 micro-pencil anode at a current density of 200 mA g−1 and a voltage range of 0.01 V to 3 V (vs. Li+/Li). In the first discharge curve, the potential sharply drops to 0.55 V, then reaches a plateau, and dwindle till reaching a specific capacity of 1137 mA h g−1. The first charge capacity of 882 mA h g−1 is obtained, therefore, the coulombic efficiency of 77% is calculated. The higher initial discharge capacity is caused by the interfacial lithium storage, in which the electrolyte decomposes to form a solid electrolyte interphase (SEI) layer.41 The Faraday's law of electrolysis can be used to estimate the amount of Li atoms per formula unit in lithiation and delithiation processes, which is expressed as below:42
|
 | (1) |
where
m is the mass of the active materials in electrode in grams (
i.e. Co
3V
2O
8 in this work),
Q is the total electric charge passed through the electrode in coulombs,
M is the molar mass of the active materials in grams per mole,
n is the number of intercalated/deintercalated Li atoms in the electrodes, and
F is the Faraday constant, which is 96
![[thin space (1/6-em)]](https://www.rsc.org/images/entities/char_2009.gif)
485 C mol
−1. Thus, the theoretical capacity of an active material can be derived from
eqn (1) and described as:
|
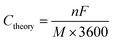 | (2) |
where
Ctheory is the theoretical specific capacity of the active material in the unit of mA h g
−1. As we measured the specific capacity of the Co
3V
2O
8 micro-pencils, the number of Li atoms per formula unit in lithiation and delithiation can be calculated as 16.1 and 11.2 according to
eqn (2), which is close but slightly lower than that of the previous study.
19
Fig. 5(c) presents the cycling performance of the Co3V2O8 micro-pencils at the current density of 200 mA g−1. The specific capacity decreases progressively from the initial capacity of 1137 mA h g−1 with the increase of cycles, followed by a slow rise of the specific capacity after the 50th cycle and reached 670 mA h g−1 at 330th. Even after 350 cycles, the capacity still maintained a plateau at ∼620 mA h g−1. This similar interesting change behavior of the capacity has also been shown in some other studies.26,28 However, the mechanism is not clear and therefore further studies are still required. As shown in Fig. 5(c), after the initial discharge/charge, the discharge and charge capacities overlap well with each other, indicating an superb capacity reversibility. The capacity retention is further demonstrated by the calculated coulombic efficiency, which maintain at almost 100% after the first cycle. The discharge capacity was measured at different current densities from 100 to 2000 mA g−1, as presented in Fig. 5(d). The average discharge capacities of at the current density of 100, 200, 500, 1000 and 2000 mA g−1 are stabilized at 700, 550, 420, 350, and 300 mA h g−1, respectively, regardless of change direction of the current density, thus revealing the stability of the Co3V2O8 micro-pencils in the rate performance. The overlaps between the discharge and charge capacities indicate the high capacity retention (∼100%) during the rate performance.
Conclusions
In summary, we have demonstrated a facile hydrothermal approach to synthesize Co3V2O8 solid micro-particles with controllable morphology. Through the XRD, SEM, TEM and STEM, pure phase Co3V2O8 solid micro-plates and micro-pencils are thoroughly scrutinized. When evaluated as anode materials for lithium ion battery, the Co3V2O8 solid micro-pencils exhibit satisfactory electrochemical performance: high Li storage capacity (initial discharge capacity of 1137 mA h g−1 at 200 mA g−1), superior cycling performances (capacity of ∼620 mA h g−1 after 350 cycles at 200 mA h−1), and notable rate capability (capacity of 300 mA h g−1 at 2000 mA g−1). The present study demonstrates the potential of Co3V2O8 solid micro-pencils as the promising anode materials for LIB. Hydrothermal approach can also be employed for synthesizing other mixed transition metal oxides for diverse energy storage applications. Nevertheless, further studies should be conducted to shed light on the formation of the Co3V2O8 with different morphology, and to ameliorate the electrochemical performances of Co3V2O8 related materials.
Acknowledgements
The authors would like to appreciate the financial support from National Natural Science Foundation of China (201503036, 51602038), Sichuan Science and Technology Support Program (2015GZ0130, 2016000156, 2015GZ0132, 2016JY0183) and the Fundamental Research Funds for the Central Universities (ZYGX2015KYQD030).
References
- W. W. Lee and J.-M. Lee, J. Mater. Chem. A, 2014, 2(6), 1589–1626 CAS.
- Y. S. Wu, L. Zhan, K. T. Huang, H. J. Wang, H. Yu, S. Q. Wang, F. Peng and C. Y. Lai, J. Alloys Compd., 2016, 684, 47–54 CrossRef CAS.
- B. Liu, P. F. Yan, W. Xu, J. M. Zheng, Y. He, L. L. Luo, M. E. Bowden, C. M. Wang and J. G. Zhang, Nano Lett., 2016, 16(8), 4932–4939 CrossRef CAS PubMed.
- K. Zhao, M. Wen, Y. Dong, L. Zhang, M. Yan, W. Xu, C. Niu, L. Zhou, Q. Wei, W. Ren, X. Wang and L. Mai, Adv. Energy Mater., 2017, 7(6), 1601582 CrossRef.
- P. Poizot, S. Laruelle, S. Grugeon, L. Dupont and J. M. Tarascon, Nature, 2000, 407(6803), 496–499 CrossRef CAS PubMed.
- Y. Wang and G. Z. Cao, Adv. Mater., 2008, 20(12), 2251–2269 CrossRef CAS.
- H. B. Wu, J. S. Chen, H. H. Hng and X. W. Lou, Nanoscale, 2012, 4(8), 2526–2542 RSC.
- P. Roy and S. K. Srivastava, J. Mater. Chem. A, 2015, 3(6), 2454–2484 CAS.
- A. Manthiram, A. V. Murugan, A. Sarkar and T. Muraliganth, Energy Environ. Sci., 2008, 1(6), 621–638 CAS.
- L. Zhou, H. Xu, H. Zhang, J. Yang, S. B. Hartono, K. Qian, J. Zou and C. Yu, Chem. Commun., 2013, 49(77), 8695–8697 RSC.
- H. Zhang, X. Sun, X. Huang and L. Zhou, Nanoscale, 2015, 7(7), 3270–3275 RSC.
- C. Yuan, H. B. Wu, Y. Xie and X. W. Lou, Angew. Chem., Int. Ed., 2014, 53(6), 1488–1504 CrossRef CAS PubMed.
- C. Z. Yuan, H. B. Wu, Y. Xie and X. W. Lou, Angew. Chem., Int. Ed., 2014, 53(6), 1488–1504 CrossRef CAS PubMed.
- J. X. Zhu, T. Zhu, X. Z. Zhou, Y. Y. Zhang, X. W. Lou, X. D. Chen, H. Zhang, H. H. Hng and Q. Y. Yan, Nanoscale, 2011, 3(3), 1084–1089 RSC.
- L. Zhou, D. Zhao and X. W. Lou, Adv. Mater., 2012, 24(6), 745–748 CrossRef CAS PubMed.
- L. J. Fu, H. Liu, C. Li, Y. P. Wu, E. Rahm, R. Holze and H. Q. Wu, Solid State Sci., 2006, 8(2), 113–128 CrossRef CAS.
- L. Zhang, K. Zhao, Y. Luo, Y. Dong, W. Xu, M. Yan, W. Ren, L. Zhou, L. Qu and L. Mai, ACS Appl. Mater. Interfaces, 2016, 8(11), 7139–7146 CAS.
- Z. Yin, Y. Xiao, X. Wang, W. Wang, D. Zhao and M. Cao, Nanoscale, 2016, 8(1), 508–516 RSC.
- V. Soundharrajan, B. Sambandam, J. Song, S. Kim, J. Jo, S. Kim, S. Lee, V. Mathew and J. Kim, ACS Appl. Mater. Interfaces, 2016, 8(13), 8546–8553 CAS.
- Y. Luo, X. Xu, Y. Zhang, C.-Y. Chen, L. Zhou, M. Yan, Q. Wei, X. Tian and L. Mai, ACS Appl. Mater. Interfaces, 2016, 8(4), 2812–2818 CAS.
- Y. Luo, X. Xu, X. Tian, Q. Wei, M. Yan, K. Zhao, X. Xu and L. Mai, J. Mater. Chem. A, 2016, 4(14), 5075–5080 CAS.
- F. Y. Cheng and J. Chen, J. Mater. Chem., 2011, 21(27), 9841–9848 RSC.
- H. Ben Yahia, M. Shikano and Y. J. Yamaguchi, Power Sources, 2016, 320, 43–48 CrossRef CAS.
- C. Tang, J. Zhu, X. Wei, L. He, K. Zhao, C. Xu, L. Zhou, B. Wang, J. Sheng and L. Mai, Energy Storage Materials, 2017, 7, 152–156 CrossRef.
- F. Wu, C. Yu, W. Liu, T. Wang, J. Feng and S. Xiong, J. Mater. Chem. A, 2015, 3(32), 16728–16736 CAS.
- G. Yang, H. Cui, G. Yang and C. Wang, ACS Nano, 2014, 8(5), 4474–4487 CrossRef CAS PubMed.
- G. Z. Yang, H. Cui, G. W. Yang and C. X. Wang, ACS Nano, 2014, 8(5), 4474–4487 CrossRef CAS PubMed.
- F. Wu, S. Xiong, Y. Qian and S.-H. Yu, Angew. Chem., Int. Ed., 2015, 54(37), 10787–10791 CrossRef CAS PubMed.
- Y. Zhang, Y. Liu, J. Chen, Q. Guo, T. Wang and H. Pang, Sci. Rep., 2014, 4, 5687 CrossRef CAS PubMed.
- S. B. Ni, J. J. Ma, J. C. Zhang, X. L. Yang and L. L. Zhang, J. Power Sources, 2015, 282, 65–69 CrossRef CAS.
- L. Zhang, K. N. Zhao, Y. Z. Luo, Y. F. Dong, W. W. Xu, M. Y. Yan, W. H. Ren, L. Zhou, L. B. Qu and L. Q. Mai, ACS Appl. Mater. Interfaces, 2016, 8(11), 7139–7146 CAS.
- G. X. Gao, S. Y. Lu, B. T. Dong, Y. Xiang, K. Xi and S. J. Ding, J. Mater. Chem. A, 2016, 4(17), 6264–6270 CAS.
- Y. Z. Luo, X. Xu, X. C. Tian, Q. L. Wei, M. Y. Yan, K. N. Zhao, X. M. Xu and L. Q. Mai, J. Mater. Chem. A, 2016, 4(14), 5075–5080 CAS.
- V. Soundharrajan, B. Sambandam, J. Song, S. Kim, J. Jo, S. Kim, S. Lee, V. Mathew and J. Kim, ACS Appl. Mater. Interfaces, 2016, 8(13), 8546–8553 CAS.
- Y. Li, L. Kang, L. B. Kong, M. C. Liu, X. X. Wang and W. B. Zhang, RSC Adv., 2016, 6(43), 36418–36424 RSC.
- M. C. Liu, L. B. Kong, L. Kang, X. H. Li, F. C. Walsh, M. Xing, C. Lu, X. J. Ma and Y. C. Luo, J. Mater. Chem. A, 2014, 2(14), 4919–4926 CAS.
- F. Wu, S. Xiong, Y. Qian and S. H. Yu, Angew. Chem., 2015, 54(37), 10787–10791 CrossRef CAS PubMed.
- Y. Luo, X. Xu, X. Tian, Q. Wei, M. Yan, K. Zhao, X. Xu and L. Mai, J. Mater. Chem. A, 2016, 4(14), 5075–5080 CAS.
- L. Wu, S. N. Shi, X. P. Zhang, J. Q. Liu, D. Chen, H. Ding and S. K. Zhong, Mater. Lett., 2015, 152, 228–231 CrossRef CAS.
- V. Soundharrajan, B. Sambandam, J. Song, S. Kim, J. Jo, S. Kim, S. Lee, V. Mathew and J. Kim, ACS Appl. Mater. Interfaces, 2016, 8(13), 8546–8553 CAS.
- N. Liu, Z. D. Lu, J. Zhao, M. T. McDowell, H. W. Lee, W. T. Zhao and Y. Cui, Nat. Nanotechnol., 2014, 9(3), 187–192 CrossRef CAS PubMed.
- R. G. Ehl and A. J. Ihde, J. Chem. Educ., 1954, 31(5), 226 CrossRef CAS.
Footnotes |
† Electronic supplementary information (ESI) available. See DOI: 10.1039/c7ra03118a |
‡ These two authors contributed equally to this work. |
|
This journal is © The Royal Society of Chemistry 2017 |
Click here to see how this site uses Cookies. View our privacy policy here.