Ozonolysis of quinoline and quinoline derivatives in a Corning low flow reactor†
Received
12th June 2017
, Accepted 31st July 2017
First published on 31st July 2017
Abstract
Efficient ozonolysis of quinoline, electron deficient 8-nitroquinoline, and electron rich 6-methoxyquinoline is conducted in a Corning low flow reactor (Corning LFR) with recycling. The conversions of quinoline and 8-nitroquinoline from single-pass experiments were 75.6 and 52.4%, respectively. Upon successive oxidative work-up in a batch reactor, pyridine-2,3-dicarboxylic acid was obtained in 72.7 and 24.7% yields from the ozonolysis products of quinoline and 8-nitroquinoline, respectively. The recycling increased the overall conversions to 95.2 and 76.9%, respectively. For 6-methoxyquinoline, the conversion from the single-pass experiment, 45.2%, was increased to 73.5% with recycling under a higher liquid flow rate and substrate concentration for ozonolysis. Experimental results, conversions, residence time distribution (RTD), and the overall mass transfer coefficient are included in reactor models to determine the rate constants for ozonolysis. Predictions with the rate constants for quinoline, 8-nitroquinoline, and 6-methoxyquinoline show good agreement with the experimental results for different recycle ratios and concentrations of ozone and substrates.
Introduction
Pyridine-2,3-dicarboxylic acid has been extensively studied for its importance in metabolism and use in the diagnosis of diseases like Huntington's, Alzheimer's, and HIV diseases.1–5 A common way to produce pyridine-2,3-dicarboxylic acid is by oxidation of quinoline. For example, electrolytic oxidation of quinoline in H2SO4 produced pyridine-2,3-dicarboxylic acid with a yield of 44% using a PbO2 electrode.6,7 Wet oxidation of quinoline by oxygen resulted in pyridine-2,3-dicarboxylic acid as an intermediate product at high pressures (58–76 bar) and high temperatures (220–280 °C).8 However, considering the ease of preparation and control, ozonolysis has been extensively studied as an efficient way to oxidize quinoline since ozone is a strong oxidant as well as a “green” alternative to other oxidants. Ozone is generally produced through electrical discharge from oxygen and nitrogen, and the only by-product is oxygen molecules. Work-up after ozonolysis converts the ozonide into alcohol, aldehyde, ketone, or carboxylic acid depending on the conditions.9 For example, various olefins including styrene, naphthalene, and 4-vinylpyridine were converted to their corresponding aldehydes with dimethyl sulfide under mild conditions with yields of 62–97%.10 Ozonolysis of methyl podocarpate produced its acid-lactone in 90% yield after oxidative work-up with hydrogen peroxide while reductive work-up with sodium borohydride formed the hydroxyl-lactone in yields of 10–30%.11 Also, pyridine-2,3-dicarboxylic acid was synthesized up to 78% yield from ozonolysis of quinoline in the presence of mineral acid followed by oxidative work-up with hydrogen peroxide in a batch reactor after 20–22 h of reaction.12,13
Although ozonolysis is considered to be an effective oxidation method, a major concern lies in safety issues that the intermediate cyclic ozonide or peroxides may cause explosion.14 In particular, the accumulation of ozonide in a batch reactor can significantly increase the possibility of explosion triggered by the reaction with the solvent. Over the past decade, flow reactors have been developed and employed for reactions requiring careful control of operation conditions and that could be dangerous when carried out in conventional batch reactors.15–18 In a flow system, the liquid phase including the substrate is continuously flowing, inhibiting the accumulation of explosive intermediates inside the reactor. Moreover, a relatively small amount of reactants required to perform experiments further mitigates such safety hazards. In addition to the safety aspect, the residence time can be precisely controlled and scale-up is often easier. Consequently, several studies have considered the advantages of performing ozonolysis in flow. For example, Wada et al. fabricated a multichannel microreactor to demonstrate the safe performance of highly reactive processes in the microreactor. They carried out ozonolysis of 1-decene, triethyl phosphite, and octylamine achieving high conversions and yields of up to 100% even at short gas–liquid contact times less than 1 s.19 O'Brien et al. demonstrated a continuous tube-in-tube reactor using a semipermeable Teflon® AF-2400 that allowed ozone to permeate into liquid phase from the gas phase, and conducted ozonolysis of alkenes with isolated yields of 57–95%.20 In addition to ozonolysis, Irfan et al. successfully performed work-up and quenching in the same flow reaction unit, which prevented the accumulation of dangerous intermediates during work-up and showed isolated yields of 72–91%.21
A systematic study of mass transfer coefficients for an ozone/ethyl acetate–alkene system was conducted in multichannel microreactors, a Corning low flow reactor (LFR) and a Corning advanced flow reactor (AFR) by Nieves-Remacha et al., where the overall mass transfer coefficients for the LFR and AFR were of the same order of magnitude as those of the microreactors and at least one order of magnitude larger than those of conventional contactors.22 While various cyclic and aliphatic olefins have been successfully oxidized in flow reactors, ozonolysis of quinoline or quinoline derivatives has not shown high yields in flow. For example, Roydhouse et al. showed that ozonolysis of 8-hydroxyquinoline followed by oxidative work-up in a flow reactor produced pyridine-2,3-dicarboxylic acid with a low yield of 21% despite significant changes in temperature, solvent, and the amount of ozone molecules.23
In this contribution, we use a Corning low flow reactor (LFR) to achieve high conversion for ozonolysis of quinolines. The LFR is composed of heart-shaped structures to split and recombine flows for efficient mixing between phases.22,24 With the successive oxidative work-up carried out in a batch reactor, pyridine-2,3-dicarboxylic acid is synthesized from the ozonolysis product of quinoline and 8-nitroquinoline as shown in Scheme 1. Recycling of the liquid stream enhances the overall conversion by increasing the residence time under high ozone concentration. Kinetic analysis determines the rate constants for ozonolysis of three substrates, quinoline, 8-nitroquinoline, and 6-methoxyquinoline. Experimental conversions show good agreement (within one standard deviation) with conversions predicted by physical model simulations for varying concentrations of the substrates and ozone. To our knowledge, this contribution represents the first combined experimental and modelling study of the ozonolysis of quinolines in a recycle flow system.
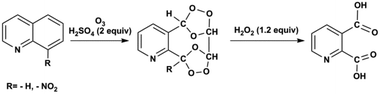 |
| Scheme 1 Ozonolysis and oxidative work-up of quinoline and 8-nitroquinoline. | |
Experimental section
Materials
Quinoline (98%), 8-nitroquinoline (98%), pyridine-2,3-dicarboxylic acid (98%), sulfuric acid (99.999%), aqueous hydrogen peroxide (30 wt%), sodium sulfite (≥98%), deionized (DI) water, acetonitrile (HPLC Plus, ≥99.9%), water (HPLC grade), phosphoric acid (85 wt% in water), and 1,1′-biphenyl (≥99.9%) were purchased from Sigma Aldrich. Acetic acid (glacial, 99+%), 6-methoxyquinoline (98%), and methanol (HPLC grade) were purchased from Alfa Aesar. All materials were used as received without further purification.
Reactor
A Corning low flow reactor (Corning LFR) was used for the reaction experiments (Fig. 1a). The volume of each plate was 0.45 ml. When connected in series, eight plates gave a total reactor volume of 4.6 ml including the connection. The liquid phase was flowed into the reactor using a Harvard PHD Ultra Infuse/Withdraw pump with an 8 ml Harvard stainless steel syringe. A mass flow controller (Aalborg Instruments) measured the flow rate of gas. A backpressure regulator (Equilibar) connected in parallel to the reactor controlled the system pressure between 20–25 psig, which was the working pressure for the ozone generator. After passing through the ozone generator, the gas stream split into two portions with one portion flowing into the reactor in the desired flow rate. The other portion exited the system through the back-pressure regulator. A process thermostat (Lauda Integral XT 150) regulated the temperature of the reactor. The liquid product was separated from the gas phase by gravity. Two ozone destruction units (Ozone Solutions Inc., ODS-3) destroyed any unreacted ozone.
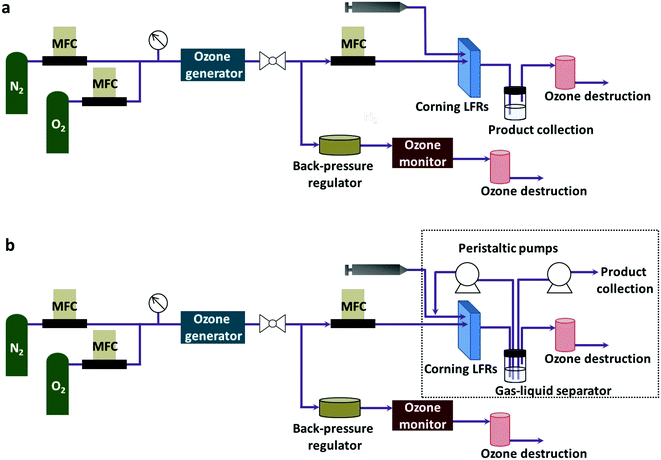 |
| Fig. 1 System configuration (a) for through flow ozonolysis and (b) for ozonolysis with recycling of the liquid reaction stream. | |
Ozonolysis
An electric discharge based ozone generator (Absolute Ozone, Atlas 30) generated ozone from oxygen (Airgas, UHP grade) and nitrogen gas (Airgas, UHP grade) in a 40
:
1 molar ratio. Unit mass flow controllers (UFC series) measured the flow rates of oxygen and nitrogen. An ozone monitor (Teledyne Instruments Inc., Model 454) determined the concentration of ozone in wt%. The maximum concentration was 15–15.5 wt% under these conditions. Two ozone destruction units connected to the reactor and to the ozone monitor removed any unreacted ozone. The solution was prepared to a concentration of 0.075 M (quinoline and 8-nitroquinoline) or 0.225 M (6-methoxyquinoline) in acetic acid and DI water with a volumetric ratio of 86
:
14. Two equiv. of sulfuric acid were mixed with the substrates to reduce the electron density in the pyridine ring.25 The liquid flow rates were 0.05 ml min−1 for quinoline and 8-nitroquinoline and 0.1 ml min−1 for 6-methoxyquinoline. The gas flow rates were 4 ml min−1 for all substrates.
Recycle reactor
Connecting two peristaltic pumps (Masterflex L/S, Cole-Palmer) to the reactor set-up created the recycle reactor (Fig. 1b). As indicated in the dotted box, one pump redirected the liquid product to the inlet of the reactor where a fresh liquid feed was mixed with the recycle stream while another pump kept removing the residual liquid product at a fixed flow rate. For recycling, a recycle loop was initially filled with the liquid product with the same flow rate as the liquid feed rate (0.05 ml min−1 for quinoline and 8-nitroquinoline or 0.1 ml min−1 for 6-methoxyquinoline) under identical conditions for a single-pass experiment. Then, the flow rate was decreased to the desired flow rate right after the recycle stream reached the mixing point with a fresh feed. At the same time, the fresh feed rate was also decreased accordingly to give the same total flow rate as the single-pass experiment in the reactor. This change in the flow rates maintained the constant total flow rate in the reactor for all recycle experiments, resulting in the same residence time of the reactor.
Oxidative work-up
Oxidative work-up with hydrogen peroxide was performed in a glass vial. Before adding hydrogen peroxide, a gentle nitrogen stream was flowed through the post ozonolysis mixture for 5–10 min to remove the remaining ozone. Aqueous hydrogen peroxide (1.2 equiv.) was then added, and the glass vial was placed in an oil bath at constant temperature with stirring. After work-up, the unreacted hydrogen peroxide was quenched with aqueous sodium sulfite solution (1.2 equiv.).
Residence time distribution
The residence time distribution (RTD) was measured for two liquid flow rates of 0.05 ml min−1 and 0.1 ml min−1 by connecting an automated Rheodyne six-way valve containing a 20 μl sample loop between the stainless steel syringe and the reactor. The solvent mixture (acetic acid
:
DI water = 86
:
14 vol%) with an internal standard (0.1 M 1,1′-biphenyl in methanol) flowed with a rate of 0.05 ml min−1 or 0.1 ml min−1 while nitrogen was flowing at 4 ml min−1. The sample loop was filled with tracer solution, 0.075 M quinoline in the solvent mixture (acetic acid
:
DI water = 86
:
14 vol%), and injected into the reactor 1 h after the start of the solvent flow. Then, samples were collected every 1 min and analyzed by HPLC to obtain the ratio of the peak area of quinoline to 1,1′-biphenyl. To exclude any effect not from the reactor, a bypass experiment was performed by directly connecting the six-way valve with the tube connected to the outlet of the reactor. The RTDs from the whole system and bypass experiments were deconvoluted via the fast Fourier transform (FFT) and inverse fast Fourier transform (iFFT) functions of MATLAB.26 From there, the mean residence time of the liquid (τL), Péclet number (Pe), and liquid hold-up (ϕ) were calculated as shown in Table S1 (see the ESI†).
Analysis
The product was analyzed with an HPLC (Agilent 1200 series) equipped with a Zorbax SB-Aq column (Agilent Technologies). The calibration curves were obtained using 1,1′-biphenyl (0.1 M in methanol) as an internal standard. Two mobile phases, methanol/acetonitrile (1
:
1 volume ratio) and water with 0.2 vol% of phosphoric acid (85 wt% in water) were used. The calibration curves were obtained from HPLC peak areas at a wavelength of 230 nm for quinoline and 6-methoxyquinoline. Wavelengths of 255 nm and 275 nm were used for 8-nitroquinoline and pyridine-2,3-dicarboxylic acid, respectively. All ozonolysis products were collected after running the reaction for 1 h assuming a steady state, and then analyzed by HPLC to obtain the conversion of quinolines. The yield was calculated from the concentration of pyridine-2,3-dicarboxylic acid measured after oxidative work-up (see S2†).
Results and discussion
The effect of the temperature on ozonolysis was explored at 10, 20, and 40 °C. Table 1 shows the temperature dependence of conversion and yield. The conversion increased from 10 °C to 20 °C, and there was no significant further increase at 40 °C. Therefore, the remaining ozonolysis experiments were performed at 20 °C. The oxidative work-up to pyridine-2,3-dicarboxylic acid was carried out at two temperatures, 45 and 70 °C, for 1 h. The higher temperature, 70 °C, produced a yield of 72.7 ± 2.8% as shown in entries 3 and 4 in Table 1.
Table 1 Effect of temperature on the conversion of quinoline and yield of pyridine-2,3-dicarboxylic acid
Entry |
Temperature (°C) |
Conversion (%) |
Yield (%) |
Ozonolysis |
Work-up |
1 |
10 |
NA |
68.2 |
NA |
2 |
40 |
NA |
74.1 |
NA |
3 |
20 |
45 |
75.6 ± 1.6 |
49.6 ± 3.0 |
4 |
70 |
72.7 ± 2.8 |
The variation of the work-up yield with reaction time was investigated for 5 to 60 min (see the ESI†). After ozonolysis at 20 °C, aqueous hydrogen peroxide was added to the ozonolysis product mixture at a constant temperature of 70 °C and the reaction time was varied. Work-up for more than 10 min produced pyridine-2,3-dicarboxylic acid in a similar range of 72–73%, but the yield significantly decreased to 53.7 ± 4.2% with a reaction time of 5 min. Therefore, the oxidative work-up was completed in 10 min to give a yield of 72–73% and this time was used in further work-up.
The single-pass experiment from eight Corning LFRs converted 75.6 ± 1.6% of quinoline through ozonolysis. To overcome the limited reactor volume and increase the reaction time, we implemented a recycle system (Fig. 1b) in which the ozonolysis product mixture was separated by gravity from the gas and a portion of it was recycled back to the reactor inlet.27–29 In general, the recycle reactor performance depends on the recycle ratio (R), which is defined as the ratio of the recycle flow rate to the fresh feed flow rate. For example, after filling the recycle loop at a flow rate of 0.05 ml min−1, the recycle flow rate was decreased to 0.04 ml min−1 while the fresh feed rate decreased to 0.01 ml min−1, resulting in a recycle ratio of R = 4. Four recycle ratios were examined for the ozonolysis of quinoline by varying the recycle flow rate as 0.04, 0.03, 0.02, and 0.01 ml min−1 and the fresh feed flow rate as 0.01, 0.02, 0.03, and 0.04 ml min−1 (Table 2). When the recycle ratio increased from 0.25 to 4, the conversion went up to 95.2%.
Table 2 Conversions of quinoline with various recycle ratios
Entry |
Fresh feed rate (ml min−1) |
Recycle flow rate (ml min−1) |
Recycle ratio (R) |
Conversion (%) |
1 |
0.01 |
0.04 |
4 |
95.2 |
2 |
0.02 |
0.03 |
1.5 |
90.1 |
3 |
0.03 |
0.02 |
0.67 |
82.9 |
4 |
0.04 |
0.01 |
0.25 |
77.0 |
As a quinoline derivative, the ozonolysis of 8-nitroquinoline was carried out for single-pass and recycle experiments. With an electron-withdrawing nitro group, 8-nitroquinoline was expected to show lower conversion and yield than quinoline.30 Under identical experimental conditions for the gas and liquid flow rates (Ql = 0.05 ml min−1 and Qg = 4 ml min−1) and initial concentration of 0.075 M, the conversion of 8-nitroquinoline was 52.4 ± 2.3% from the single-pass experiment. The ozonolysis and oxidative work-up of 8-nitroquinonline also lead to the formation of pyridine-2,3-dicarboxylic acid because the nitro group is unstable and easily replaced with the hydroxyl group in acid in the presence of water.31 After ozonolysis, oxidative work-up at 70 °C for 10 min with 1.2 equivalents of H2O2 yielded 24.7% of pyridine-2,3-dicarboxylic acid. Similar to quinoline, the overall conversion was increased to 76.9% with a recycle ratio of 4 in the recycle reactor (Table 3).
Table 3 Conversions of 8-nitroquinoline with various recycle ratios
Entry |
Fresh feed rate (ml min−1) |
Recycle flow rate (ml min−1) |
Recycle ratio (R) |
Conversion (%) |
1 |
0.01 |
0.04 |
4 |
76.9 |
2 |
0.02 |
0.03 |
1.5 |
70.5 |
3 |
0.03 |
0.02 |
0.67 |
65.6 |
4 |
0.04 |
0.01 |
0.25 |
58.6 |
Assuming that ozonolysis reaction was first order with respect to ozone and quinoline, the rate constant was determined by means of least squares fitting with mass balance equations. The reaction order was assumed to be first order for each reactant, since the addition of one equivalent of ozone to quinoline proceeds very quickly while the second addition to form diozonide is considerably slow as studied by Lindenstruth et al.30 Only reactions in the liquid phase were considered because of the low vapor pressure of quinoline under experimental conditions. Dissolved ozone was replenished from the gas phase as the reaction proceeded throughout the reactor, and there were no changes in liquid hold-up, density, and linear velocity of each phase. Based on these assumptions, the mass balance equations were developed for each phase similar to an earlier study of a multi-phase system with a volatile tracer.32,33
Liquid phase:
|  | (1a) |
| 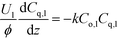 | (1b) |
Vapor phase:
|  | (2) |
Here, k, U, C, ϕ, (ka)gl, and He represent the rate constant, linear velocity, concentration, liquid hold-up, overall mass transfer coefficient at the interface of liquid and gas, and dimensionless Henry's constant, respectively. For each term, subscripts l or g means liquid or gas phase, and o or q represents ozone or quinoline. The dimensionless Henry's constant for ozone,
, is fixed at 0.55 assuming that there is no effect of water on the constant in acetic acid as a solvent.34 The overall mass transfer coefficient, (ka)gl, was determined experimentally to be 0.02 s−1 by detecting the concentration of bicarbonate ions from the absorption of carbon dioxide in aqueous N-methyldiethanolamine (see the ESI†).35,36 This low mass transfer coefficient compared to the values determined earlier for the LFR by Nieves-Remacha et al.22 resulted from using low flow rates. Nevertheless, the Péclet numbers were sufficient to assume plug flow in the above model (see the ESI†).
Employing the physical parameters and experimental results including the residence time distribution and conversions in the mass balance equations, the rate constant was determined by minimizing the sum of squares difference between predicted conversions and observed conversions for the flow through experiments. Calculations were performed with the fmincon nonlinear optimization routine of MATLAB. Using the determined rate constant for quinoline, k = 0.150 ± 0.013 M−1 s−1 (one standard deviation), the conversions depending on the recycle ratio (R) were predicted for the recycle reactor and compared to the experimental data (Fig. 2a). The experimental data falls within one standard deviation of the predicted performance. The kinetic analysis of 8-nitroquinoline was performed under identical assumptions and physical parameters, and produced a rate constant of 0.068 ± 0.006 M−1 s−1. Again, the model predicts the observed performance of the recycle system within one standard deviation (Fig. 2b).
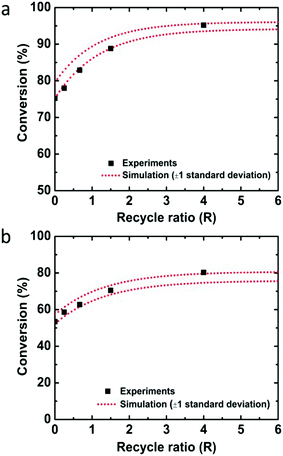 |
| Fig. 2 Conversions of (a) quinoline and (b) 8-nitroquinoline depending on the recycle ratio (R) from experiments (black squares) and simulation with one standard deviation (red dotted lines). | |
In order to verify the determined rate constants, the concentrations of ozone and quinoline or 8-nitroquinoline were varied for single-pass experiments, and the experimental results were compared with the simulation results (Fig. 3). Compared with the conversions obtained from simulations, the experimental results fall well within one standard deviation of the predicted performance results for quinoline (Fig. 3a and b) and 8-nitroquinoline (Fig. 3c and d).
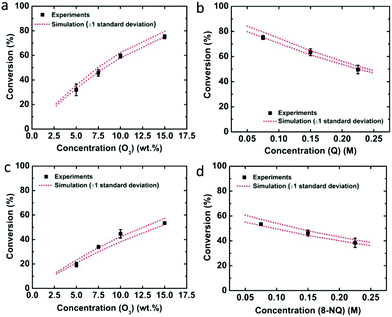 |
| Fig. 3 Conversions of substrates under (a) various ozone concentrations with 0.075 M quinoline, (b) various quinoline concentrations with 15 wt% of ozone, (c) various ozone concentrations with 0.075 M 8-nitroquinoline, and (d) various 8-nitroquinoline concentrations with 15 wt% of ozone. Black squares represent the experimental results and red dotted lines represent the simulation results with one standard deviation from the mean. | |
Ozonolysis of 6-methoxyquinoline was also investigated as an example of a quinoline with an electron donating group. Since the reaction rate was expected to increase relative to quinoline, different experimental conditions were considered. The concentration of 6-methoxyquinoline was 0.225 M and the liquid flow rate was increased to 0.1 ml min−1 in one Corning LFR plate. Under these conditions, the conversion from single-pass experiments was 45.2%, and increased to 73.5% with a recycle ratio of 4 (Table 4).
Table 4 Conversions of 6-methoxyquinoline with various recycle ratios
Entry |
Fresh feed rate (ml min−1) |
Recycle flow rate (ml min−1) |
Recycle ratio (R) |
Conversion (%) |
1 |
0.01 |
0.04 |
4 |
73.5 |
2 |
0.02 |
0.03 |
1.5 |
62.6 |
3 |
0.03 |
0.02 |
0.67 |
54.8 |
4 |
0.04 |
0.01 |
0.25 |
47.5 |
Since the flow rate and reactor volume were changed, the RTD was measured again in one Corning LFR plate and the mean residence time was calculated from the deconvolution between the total reactor and the bypass experiments (see Fig. S1†). Also, the overall mass transfer coefficient for the flowrates of Ql = 0.1 ml min−1 and Qg = 4 ml min−1 was determined experimentally to be 0.074 s−1 because of the increased liquid flow rate. The determined rate constant from the kinetic analysis for 6-methoxyquinoline was k = 8.84 × 104 M−1 s−1. This value is several orders of magnitude larger than that for quinoline or 8-nitroquinoline, presumably because the electron donating methoxy group increases the electron density in the electron deficient quinoline ring promoting electrophilic addition of ozone.37 Similarly, anisole has a much higher rate constant (290 ± 50 M−1 s−1) than benzene (2 ± 0.4 M−1 s−1) or nitrobenzene (0.09 ± 0.02 M−1 s−1).38 The predicted performance of the recycle system again compares well with experimental data for varying recycle ratios as well as ozone and 6-methoxyquinoline concentrations (Fig. 4).
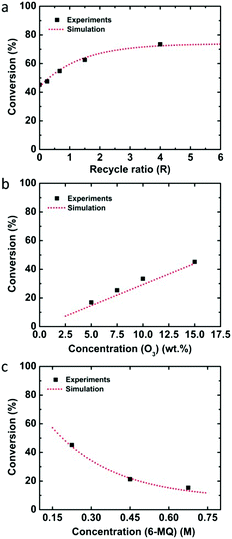 |
| Fig. 4 Conversions of 6-methoxyquinoline (a) depending on the recycle ratio (R), (b) under various ozone concentrations with 0.225 M 6-methoxyquinoline, and (c) under various 6-methoxyquinoline concentrations with 15 wt% of ozone from experiments (black dots) and the simulation results (red dotted lines). | |
Conclusions
Ozonolysis of quinoline and 8-nitroquinoline was successfully carried out in eight Corning LFR plates, the conversion of quinoline was 75.6 ± 1.6% in single-pass experiments at 20 °C, and the yield of pyridine-2,3-dicarboxylic acid after oxidative work-up with hydrogen peroxide in a batch reactor was 72.7 ± 2.8%. 8-Nitroquinoline with an electron-withdrawing group showed a lower conversion of 52.4 ± 2.3% and a yield of 24.7% of pyridine-2,3-dicarboxylic acid under identical conditions, as expected. When the ozonolysis was performed in the recycle system where a portion of the liquid phase is recycled to the inlet of the reactor, the conversion increased to 95.2% for quinoline and 76.9% for 8-nitroquinoline with a recycle ratio of 4. The ozonolysis of 6-methoxyquinoline was investigated at an increased liquid flow rate and concentration in one Corning LFR plate resulting in 45.2% conversion in single-pass and 73.5% conversion in the recycle system when the recycle ratio was 4. A multiphase reactor model combined with measurements of mass transfer coefficients and residence time distributions enables the determination of the rate constants for the ozonolysis of quinoline, 8-nitroquinoline, and 6-methoxyquinoline. Moreover, model simulations with those rate constants correctly predicted additional experimental results for varying recycle ratios, as well as ozone and substrate concentrations.
Acknowledgements
The authors thank Novartis for financial support and Corning, Inc. for use of the LFR.
References
- M. P. Heyes, K. Saito, J. S. Crowley, L. E. Davis, M. A. Demitrack, M. Der, L. A. Dilling, J. Elia, M. J. P. Kruesi, A. Lackner, S. A. Larsen, K. Lee, H. L. Leonard, S. P. Markey, A. Martin, S. Milstein, M. M. Mouradian, M. R. Pranzatelli, B. J. Quearry, A. Salazar, M. Smith, S. E. Strauss, T. Sunderland, S. W. Swedo and W. W. Tourtellotte, Brain, 1992, 115, 1249–1273 CrossRef PubMed.
- G. J. Guillemin, S. J. Kerr and B. J. Brew, Neurotoxic. Res., 2005, 7, 103–123 CrossRef CAS.
- P. R. Sanberg, S. F. Calderon, M. Giordano, J. M. Tew and A. B. Norman, Exp. Neurol., 1989, 105, 45–53 CrossRef CAS PubMed.
- M. P. Heyes, B. J. Brew, A. Martin, R. W. Price, A. M. Salazar, J. J. Sidtis, J. A. Yergey, M. M. Mouradian, A. E. Sadler, J. Keilp, D. Rubinow and S. P. Markey, Ann. Neurol., 1991, 29, 202–209 CrossRef CAS PubMed.
- M. F. Beal, N. W. Kowall, D. W. Ellison, M. F. Mazurek, K. J. Swartz and J. B. Martin, Nature, 1986, 321, 168–171 CrossRef CAS PubMed.
- J. C. Cochran and W. F. Little, J. Org. Chem., 1961, 26, 808–811 CrossRef CAS.
- M. Kulka, J. Am. Chem. Soc., 1946, 68, 2472–2473 CrossRef CAS PubMed.
- A. B. Thomsen, Water Res., 1998, 32, 136–146 CrossRef CAS.
- S. G. Van Ornum, R. M. Champeau and R. Pariza, Chem. Rev., 2006, 106, 2990–3001 CrossRef CAS PubMed.
- J. J. Pappas, W. P. Keaveney, E. Gancher and M. Berger, Tetrahedron Lett., 1966, 7, 4273–4278 CrossRef.
- R. A. Bell and M. B. Gravestock, Can. J. Chem., 1970, 48, 1105–1113 CrossRef CAS.
- C. O'murchu, Synthesis, 1989, 880–882 CrossRef.
- B. T. Kalakutskii, M. A. Kosareva, N. D. Rusyanova and N. V. Malysheva, J. Appl. Chem. USSR, 1977, 50, 2024–2025 Search PubMed.
- J. Kula, Chem. Health Saf., 1999, 6, 21–22 CrossRef CAS.
- H. P. L. Gemoets, Y. H. Su, M. J. Shang, V. Hessel, R. Luque and T. Noel, Chem. Soc. Rev., 2016, 45, 83–117 RSC.
- A. Gavriilidis, A. Constantinou, K. Hellgardt, K. K. Hii, G. J. Hutchings, G. L. Brett, S. Kuhn and S. P. Marsden, React. Chem. Eng., 2016, 1, 595–612 CAS.
- B. Gutmann, D. Cantillo and C. O. Kappe, Angew. Chem., Int. Ed., 2015, 54, 6688–6728 CrossRef CAS PubMed.
- C. Wiles and P. Watts, Green Chem., 2012, 14, 38–54 RSC.
- Y. Wada, M. A. Schmidt and K. F. Jensen, Ind. Eng. Chem. Res., 2006, 45, 8036–8042 CrossRef CAS.
- M. O'Brien, I. R. Baxendale and S. V. Ley, Org. Lett., 2010, 12, 1596–1598 CrossRef PubMed.
- M. Irfan, T. N. Glasnov and C. O. Kappe, Org. Lett., 2011, 13, 984–987 CrossRef CAS PubMed.
- M. J. Nieves-Remacha and K. F. Jensen, J. Flow Chem., 2015, 5, 160–165 CrossRef CAS.
- M. D. Roydhouse, W. B. Motherwell, A. Constantinou, A. Gavriilidis, R. Wheeler, K. Down and I. Campbell, RSC Adv., 2013, 3, 5076–5082 RSC.
- A. Woitalka, S. Kuhn and K. F. Jensen, Chem. Eng. Sci., 2014, 116, 1–8 CrossRef CAS.
-
M. G. Sturrock, E. L. Cline, K. R. Robinson and K. A. Zercher, Pyridine carboxylic acid preparation, US Pat., US2964529, 1960 Search PubMed.
- F. Trachsel, A. Gunther, S. Khan and K. F. Jensen, Chem. Eng. Sci., 2005, 60, 5729–5737 CrossRef CAS.
- J. T. Kraemer and D. M. Bagley, Environ. Sci. Technol., 2005, 39, 3819–3825 CrossRef CAS PubMed.
- M. Makri and C. G. Vayenas, Appl. Catal., A, 2003, 244, 301–310 CrossRef CAS.
- C. C. Chen, B. Sen, Y. S. Chuang, C. J. Tsai and C. H. Lay, J. Cleaner Prod., 2012, 32, 236–243 CrossRef CAS.
- A. F. Lindenstruth and C. A. Vanderwerf, J. Am. Chem. Soc., 1949, 71, 3020–3021 CrossRef CAS.
- C. Y. Zhang, Y. J. Shu, Y. G. Huang, X. D. Zhao and H. S. Dong, J. Phys. Chem. B, 2005, 109, 8978–8982 CrossRef CAS PubMed.
- N. Marquez, M. Musterd, P. Castano, R. Berger, J. A. Moulijn, M. Makkee and M. T. Kreutzer, Chem. Eng. Sci., 2010, 65, 3972–3985 CrossRef CAS.
- S. G. Newman, K. Lee, J. H. Cai, L. Yang, W. H. Green and K. F. Jensen, Ind. Eng. Chem. Res., 2015, 54, 4166–4173 CrossRef CAS.
- A. K. Bin, Ozone: Sci. Eng., 2006, 28, 67–75 CrossRef CAS.
- E. B. Rinker, S. S. Ashour and O. C. Sandall, Chem. Eng. Sci., 1995, 50, 755–768 CrossRef CAS.
- A. Naami, M. Edali, T. Sema, R. Idem and P. Tontiwachwuthikul, Ind. Eng. Chem. Res., 2012, 51, 6470–6479 CrossRef CAS.
-
C. VonSonntag and U. VonGunten, Chemistry of Ozone in Water and Wastewater Treatment: From Basic Principles to Applications, 2012, pp. 1–303 Search PubMed.
- J. Hoigne and H. Bader, Water Res., 1983, 17, 173–183 CrossRef CAS.
Footnote |
† Electronic supplementary information (ESI) available. See DOI: 10.1039/c7re00084g |
|
This journal is © The Royal Society of Chemistry 2017 |
Click here to see how this site uses Cookies. View our privacy policy here.