DOI:
10.1039/C7NH00185A
(Review Article)
Nanoscale Horiz., 2018,
3, 235-260
Rational design of materials interface at nanoscale towards intelligent oil–water separation
Received
12th November 2017
, Accepted 4th January 2018
First published on 4th January 2018
Abstract
Oil–water separation is critical for the water treatment of oily wastewater or oil-spill accidents. The oil contamination in water not only induces severe water pollution but also threatens human beings’ health and all living species in the ecological system. To address this challenge, different nanoscale fabrication methods have been applied for endowing biomimetic porous materials, which provide a promising solution for oily-water remediation. In this review, we present the state-of-the-art developments in the rational design of materials interface with special wettability for the intelligent separation of immiscible/emulsified oil–water mixtures. A mechanistic understanding of oil–water separation is firstly described, followed by a summary of separation solutions for traditional oil–water mixtures and special oil–water emulsions enabled by self-amplified wettability due to nanostructures. Guided by the basic theory, the rational design of interfaces of various porous materials at nanoscale with special wettability towards superhydrophobicity–superoleophilicity, superhydrophilicity–superoleophobicity, and superhydrophilicity–underwater superoleophobicity is discussed in detail. Although the above nanoscale fabrication strategies are able to address most of the current challenges, intelligent superwetting materials developed to meet special oil–water separation demands and to further promote the separation efficiency are also reviewed for various special application demands. Finally, challenges and future perspectives in the development of more efficient oil–water separation materials and devices by nanoscale control are provided. It is expected that the biomimetic porous materials with nanoscale interface engineering will overcome the current challenges of oil–water emulsion separation, realizing their practical applications in the near future with continuous efforts in this field.
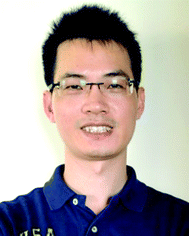
Yuxin Tang
| Yuxin Tang obtained his BS in applied chemistry and MS degree in materials science from Nanjing University of Aeronautics and Astronautics in 2006 and 2009 respectively, and completed his PhD in materials science in 2013 from Nanyang Technological University, Singapore. Currently, he is a research fellow at the same university. His research interest is rational design of advanced functional materials for energy conversion and storage, flexible electronics, and environmental remediation. |

Zhong Chen
| Zhong Chen obtained his PhD in 1997 from the University of Reading, U.K. After completing the study, he joined the newly established Institute of Materials Research and Engineering, a national research institute funded by Singapore government. In March 2000, he moved to Nanyang Technological University as an Assistant Professor, and was subsequently promoted to Associate Professor and Professor in the School of Materials Science and Engineering. Prof. Chen's research interests include Surface Engineering, Thin Films and Nanostructured Materials, and Mechanical Behaviour of Materials. He is the author of over 200 SCI journal papers, 5 book chapters and 5 granted patents. |
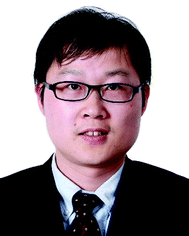
Yuekun Lai
| Yuekun Lai received his PhD degree from the Department of Chemistry, Xiamen University. During 2009–2011, he worked as a research fellow at the School of Materials Science and Engineering, Nanyang Technological University, Singapore. After that, he moved to Muenster University with Prof. Harald Fuchs and Prof. Lifeng Chi under the support of the Humboldt Foundation Scholarship of Germany. He has been a professor at National Engineering Laboratory for Modern Silk, and School of Textile and Clothing Engineering in Soochow University since 2013. His research interests focus on the bio-inspired intelligent surfaces with special wettability, and energy and environmental materials. |
1. Introduction
Oil leakage and oil spill accidents happening during oil exploitation and transportation1–5 have led to severe water and soil contamination, which threatens the health of human beings and other living species.6–8 In this regard, oil–water separation is urgently desirable to solve the above problems.9–11 Although the conventional oil contamination treatment techniques, such as in situ burning, centrifugation separation, filtration, neutralization, etc., are effective to solve the pollution issues, they normally face the drawbacks of low separation efficiency, time consumption, high cost or even inducing secondary pollution. More seriously, the incomplete separation often leads to oil remaining in water or water remaining in oil, which is still a potential risk for living species.12–16 Therefore, it is highly desirable to develop reliable technologies based on rational materials design for highly efficient oil–water separation.
The unique superhydrophobic self-cleaning property of lotus leaves is attributed to micro/nanoscale hierarchical architectures and the waxy nanocrystals on top of the papillae. Inspired by this, the nanoscale-implicated wettability concept has been widely used to fabricate superwetting surfaces for oily water remediation.17–22 The nanofabrication process can normally be divided into two steps: firstly, some particles or polymers are used to create micro/nano architectures on a surface. Secondly, functional F-containing atoms/molecules or CH3-containing groups are self-assembled and grafted onto the rough surface to achieve low surface energy. Compared to the traditional separation techniques, the as-prepared bio-inspired materials by nanotechnologies with special wettability exhibit unique advantages in terms of both separation rate and efficiency. Due to the opposite affinities towards oil and water, both superhydrophobic–superoleophilic and superhydrophilic–superoleophobic materials are suitable for oil–water separation.23–29 Generally speaking, it is simple to fabricate superhydrophobic–superoleophilic materials for oil–water separation by allowing oil to permeate the as-prepared materials and blocking water outside simultaneously.30 However, it is a challenge to construct superhydrophilic–superoleophobic materials for oil–water separation because an oleophobic surface inherently exhibits hydrophobicity.31 To overcome this challenge, scientists have ingeniously developed superhydrophilic–underwater superoleophobic materials to realize oil–water separation.32–35 Due to the underwater superoleophobicity, the membranes can overcome the drawbacks of being easily fouled or even blocked by oil. Therefore, the separation efficiency is improved greatly. From a material perspective, porous materials with special wettability are ideal candidates for oil–water separation due to the unique interconnected structures with micro/nano-sized pores, which can significantly accelerate the separation efficiency and rate.36–41 Oil–water separation can be realized based on filtration or absorption. For instance, two-dimensional (2D) membrane-like materials such as polymeric membranes, fabrics, and meshes are usually based on filtration, while three-dimensional (3D) porous materials such as foams, sponges and carbon-derived aerogels are normally based on absorption.
To further promote the oil–water separation efficiency and to meet special oil–water separation demands, intelligent superwetting materials with stimuli-responsive wettability, magnetism-assisted wettability and Janus-featured wettability have been developed for the efficient separation of sundry oil–water-mixtures, such as simple oil–water-mixtures, ternary phases of oil–water–oil-mixtures and even oil–water emulsion.42,43 To be specific, biomimetic porous materials with some polymers or functional inorganic nanoparticles can switch between super-wetting and super-anti-wetting by applying an external stimulus such as pH, light illumination, temperature, voltage, etc. This offers a significant advantage for oil–water mixture and emulsion separation by selectively allowing only water or oil to pass through.44–46 Besides, when endowing special wettable materials with magnetic nanoparticles, they can be remotely controlled by a magnet during the oil-absorption process, saving a large amount of human labour and time.47–49 Furthermore, Janus wettable surfaces, such as asymmetric and patterned membranes, exhibit unique unidirectional and non-uniform properties for oil–water separation and oil/water collection.50–54 Therefore, endowing these special wettable materials with intelligent functions is promising for efficient oil–water separation.55–59
In this review, we summarize the latest development of materials interface engineering techniques at micro/nanoscale for oil–water separation (Fig. 1). Firstly, a comprehensive understanding of the mechanism of oil–water mixture and emulsion separation is introduced. Secondly, nanoscale fabrication considerations of various porous materials with special wettability towards superhydrophobicity–superoleophilicity, superhydrophilicity–superoleophobicity, and superhydrophilicity–underwater superoleophobicity are described in detail. Thirdly, intelligent superwetting materials are also reviewed, which are developed to further promote the separation efficiency and to meet special oil–water separation demands such as oil–water emulsion remediation, switchable oil–water separation, remote controllable oil-absorption, oil/water collection, etc. Lastly, the challenges and an outlook of this field are briefly discussed.
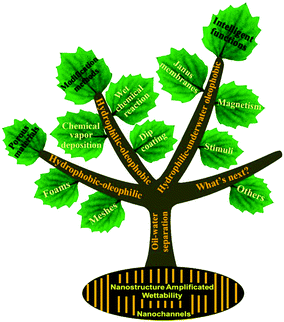 |
| Fig. 1 Recent developments in the rational design of interface structures of different porous materials with special wettability including superhydrophobicity–superoleophilicity (hydrophobicity–oleophilicity), superhydrophilicity–superoleophobicity (hydrophilicity–oleophobicity) and superhydrophilicity–underwater superoleophobicity (hydrophilicity–underwater oleophobicity) and emerging intelligent functions for special oil–water separation. | |
2. Basic considerations for oil–water separation
Surface wettability is one of the most important parameters when applying oil–water separation, water collection, liquid manipulation, etc. In the past few decades, extensive studies on the surfaces of biomaterials have promoted a comprehensive understanding of the mechanism behind superwetting surfaces.60–62 Inspired by these discoveries, four types of wetting behaviors, including Young's mode,63,64 Wenzel's mode,65,66 Cassie's mode,67,68 and the intermediate state between the Wenzel and the Cassie modes,69,70 have emerged to describe the relationship between surface roughness and surface wettability, which has been reviewed in recent review papers71–73 and will not be discussed in detail here. Based on Young's model, an ideally flat surface has limited hydrophobicity as the low-surface-energy alone will not be able to achieve superhydrophobicity in any known solids without micro/nano hierarchical structures. By creating a rough surface with architectures at the micro/nanoscle, the Wenzel and Cassie models that predict the superhydrophobic contact angle can be easily realized. Among the two, the Wenzel state is a wet-contact mode and displays high contact hysteresis, while the Cassie state exhibits a high contact angle and low contact hysteresis. And the Lotus effect is considered as the special case of the superhydrophobic Cassie state. Additionally, in practical situations, there often exists a transitional state between Wenzel's and Cassie's states, wherein surface water droplets can slide when the surface is tilted at a certain angle. Therefore, various biomimetic surfaces with special wettability could be achieved by adjusting surface architectures at micro/nano scales and the chemical composition.
Special wettable materials with superhydrophobic–superoleophilic, superhydrophilic–superoleophobic or superhydrophilic–underwater superoleophobic properties are suitable for oil–water separation.74–77 Generally, oil–water-mixture or oil–water-emulsion separation mainly depends on the selective rejection of oil or water.78–81 Taking the superhydrophobic–superoleophilic membranes as an example, with a suitable pore size larger than several tens of micrometers, oil droplets quickly penetrate through the big pores of the membranes, while water droplets are rejected by the superhydrophobic surface and still remain above the surface, resulting in separation of the layered oil–water-mixture (Fig. 2a, above). On the other hand, by adjusting the pore size to be smaller than or comparable to the diameter of emulsified droplets (usually smaller than 20 μm), oil–water emulsion (oil-in-water emulsion or water-in-oil emulsion) can also be separated by allowing oil to pass through the membrane and repelling water droplets (Fig. 2b, above).82,83 Under this condition, polymer membranes with smaller pores have been successfully synthesized and widely used for this task. While for metal meshes and fabrics, their pore size should be less than tens of micrometers, which can be achieved by depositing a surface-active polymer or by growing inorganic nanoparticles on the surface. However, the separation efficiency of a membrane is largely decreased on reducing the pore size and it is a time-consuming process. In addition, when using polymer membranes for oil–water emulsion separation, they can be easily fouled and the pores will be blocked by oil, leading to a quick decline of permeation.84,85 Therefore, membranes with too small pores are ineffective and they are undesirable for practical oil–water separation.
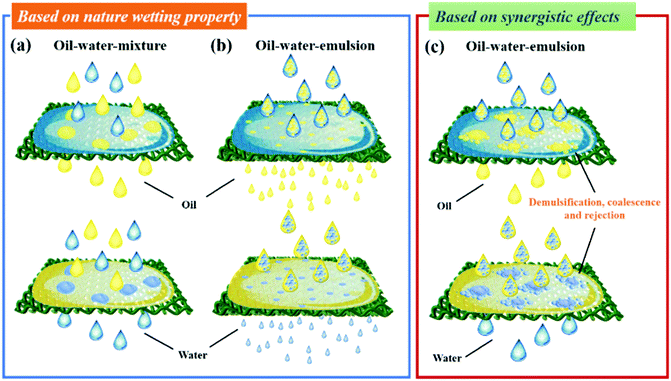 |
| Fig. 2 Design strategies for oil–water-mixture and oil–water emulsion separation. Membranes with large pore size for oil–water-mixture separation based on the rejection of oil/water (a). Membranes with small pore size for oil–water-emulsion separation based on the rejection of oil/water (b). Membranes with large pore size for oil–water-emulsion separation based on the synergistic effects of demulsification, coalescence and rejection of oil/water (c). | |
Commercial porous materials such as fabrics and metal meshes usually possess large pore size larger than several tens of micrometers, which seems not to be applicable for oil–water-emulsion separation.
In order to overcome this limitation, a promising separation strategy based on the synergistic effect of demulsification, coalescence and rejection has emerged. Based on this novel strategy, emulsified oil–water droplets were firstly demulsified upon contacting the membrane surface, and then coalesced to form a normal oil–water-mixture. Following the rejection of water, oil–water emulsions are finally separated (Fig. 2c, above). Likewise, in the superhydrophilic–superoleophobic or superhydrophilic–under water superoleophobic condition, the mechanism of oil–water separation is similar to the superhydrophobic–superoleophilic situation, where water will pass through the membrane and oil droplets will remain above the surface by the rejection of oil, which exhibits an opposite phenomenon (Fig. 2a–c, below).
Until now, great progress has been made in superwetting porous materials with small or large pore size for simple oil–water-mixture separation. However, the field of stabilized oil–water emulsion separation is far from mature and has seen much less progress when compared to traditional oil–water-mixture separation. Most special wettability stimulated membranes with small pore size and compact structure have been successfully applied in emulsified oil–water-mixture separation, but the separation efficiency is relatively low. Besides, though intelligent superwetting materials with large pore size exhibit superior efficiency in emulsion separation, the separation conditions are hard to be controlled. Therefore, realizing emulsion separation in a more efficient and effective way is still a big challenge. The recent progress in superwetting porous materials with various special wettabilities or intelligent functions for oil–water emulsion separation has been summarized in Table 1, and some typical works will be discussed in the following sections.
Table 1 Recent progress in supperwetting porous materials for oil–water-emulsion separation
Substrate |
Modification materials |
Modification method |
Special wettability |
Intelligent functions |
Emulsion type |
Permeation flux (L m−2 h−1) |
Separation efficiency (%) |
Ref. |
Notes: Poly(stearyl methacrylate). Polydopamine. Poly(3-(N-2-methacryloxyethyl-N,N-dimethyl)) ammonatopropanesultone. Atom transfer radical polymerization. Poly(N-isopropylacrylamide). Polyacrylonitrile. Polyethylene-co-polyvinyl alcohol. Poly(N-isopropylacrylamide-co-acrylamide). Polystyrene. Poly(N,N-dimethylaminoethyl methacrylate). Polyacrylamide. Polydivinylbenzene. Polyethylenimine. Poly(dodeyl methacrylate). Poly((trimethoxysilyl)propyl methacrylate). Polypyrrole. 1H,1H,2H,2H-Heptadecafluorodecyl polyhedral oligomeric silsequioxane. Polyethylenepolyamine. |
PVDF membranes |
Poly(acrylic acid) |
Phase separation |
Superhydrophilicity–underwater superoleophobicity |
— |
Oil-in-water |
570 |
— |
86
|
Ammonia |
Phase separation |
Superhydrophobicity–superoleophilicity |
— |
Water-in-oil |
3415 ± 150 |
>99.95 |
87
|
PVDF |
Phase separation |
Superamphiphobic/underwater superoleophobicity–underoil superhydrophobicity |
Switchable wettability |
Oil-in-water/water-in-oil |
9380 ± 874/8180 ± 755 |
>99.96 |
88
|
Polyamide 6 |
Electrospinning |
Hydrophilicity–underwater oleophobicity |
— |
Oil-in-water |
890 |
>99 |
89
|
PSMAa |
Phase separation |
Hydrophobicity–oleophilicity |
Thermal-response |
Water-in-oil |
— |
>99.9 |
90
|
PDA,b SiO2 |
Wet chemical reaction |
Superhydrophilicity–underwater superoleophobicity |
— |
Oil-in-water |
140 |
— |
91
|
Dopamine |
Self-polymerization |
Superhydrophilicity–underwater superoleophobicity |
— |
Oil-in-water |
6605 |
— |
92
|
PMAPSc |
ATRPd |
Superhydrophilic–underwater superoleophobicity |
— |
Oil-in-water |
16 084 |
>99.999 |
93
|
Polyurethane membrane |
PNIPAMe |
Polymerization |
Switchable superhydrophilicity/superoleophobicity |
Thermal-response |
Oil–water-emulsion |
— |
>99.2 |
94
|
PANf membrane |
PAN, SiO2 |
Electrospinning, electrospraying |
Superhydrophilicity–underwater superoleophobicity |
— |
Oil-in-water |
6290 |
>99.9 |
95
|
EVOHg membrane |
Nanocellulose crystal |
Coating, deposition |
Hydrophilicity–underwater oleophobicity |
— |
Oil–water-emulsion |
378 |
99.6 |
96
|
CNT membrane |
Poly(sulfone) |
Solution casting |
Superhydrophobicity/superoleophilicity |
— |
Oil-in-water |
230 |
98.63 |
97
|
SWCNT |
Vacuum-filtering |
Hydrophobic–superoleophilicity |
— |
Oil-in-water |
100 000 |
>99.95 |
98
|
PDA, Au, pNIPAm-co-AAmh |
Wet chemical reaction |
Superhydrophobic–superoleophilicity |
Photothermal-response |
Oil-in-water |
35 890 |
>99.99 |
99
|
PS,i PDMAEMAj |
Photografting, photopolymerization |
Hydrophobic/oleophilic (one side) |
Janus wettability |
Oil-in-water/water-in-oil |
6780/8550 |
>99.98 |
100
|
Hydrophilic/oleophilic (the other side) |
Nylon membrane |
PAM,k PDVBl |
Hydrothermal method |
Superhydrophilic–underwater superoleophobicity |
— |
Oil-in-water |
<12 |
>99 |
101
|
Ceramic membrane |
CNT |
Chemical vapor deposition |
Superhydrophilic–underwater superoleophobicity |
— |
Oil-in-water |
36 |
100 |
102
|
Polypropylene membranes |
PDA, PEI,m SiO2 |
Dip-coating |
Superhydrophilic–underwater superoleophobicity |
— |
Oil-in-water |
>1200 |
>99 |
103
|
Aerogel membranes |
Agarose, chitosan |
Crosslinking-drying |
Hydrophilicity–underwater superoleophobicity |
— |
Oil-in-water |
>600 |
>99 |
104
|
Polypropylene membrane |
PAA, CaCO3 |
Grafting, dip-coating |
Superhydrophilicity–underwater superoleophobicity |
— |
Oil-in-water |
>2000 |
>99 |
105
|
Filter paper |
PDMA,n PTMSPMA,o PDMAEMA |
Polymerization |
Superhydrophilic/superhydrophobicity |
pH-Response |
Oil-in-water/water-in-oil |
— |
>98 |
106
|
Polyvinyl alcohol |
Crosslinking |
Superhydrophilicity–underwater superoleophobicity |
— |
Oil-in-water |
63 |
>99 |
107
|
Fabric |
PDMS, PDMAEMA |
Grafting |
Superhydrophobicity/superoleophilicity |
Janus wettability |
Oil-in-water |
1500 |
99.7 |
108
|
PDMS, PDMAEMA |
Grafting |
Superhydrophobicity/superoleophilicity |
Janus wettability |
Oil-in-water |
6700 |
99.97 |
109
|
Stainless steel mesh |
Ppyp |
Electrochemical, polymerization |
Underwater superoleophobicity–underoil superhydrophobicity |
— |
Oil-in-water/water-in-oil |
300–500/720 |
99.9 |
110
|
Polyvinyl butyral |
Electrospinning |
Hydrophobicity–superoleophilicity |
— |
Water-in-oil |
6110 |
99.5 |
111
|
Fluorodecyl POSS,q PDMS |
Dip-coating |
Superhydrophilicity–superoleophobicity |
Voltage-response |
Oil-in-water/water-in-oil |
200 |
≥99.9 |
112
|
PDVB |
Solvothermal method |
Superhydrophobicity/superoleophilicity |
— |
Water-in-oil |
— |
>99.99 |
11
|
SiO2, fluoropolymer |
Dip-coating |
Superhydrophobic/superoleophilic |
Patterned wettability |
Water-in-oil |
— |
99.95 |
113
|
PDA, PEPAr |
Dip-coating |
Superhydrophilic–underwater superoleophobicity |
— |
Oil-in-water |
34 096 |
>99.6 |
114
|
Copper mesh |
Cu(OH)2 |
Surface oxidation |
Superhydrophilic–underwater superoleophobicity |
— |
Oil-in-water |
— |
— |
115
|
Cu(OH)2, HS(CH2)10COOH, HS(CH2)9CH3 |
Grafting |
Superhydrophobic/superhydrophilicity–underwater superoleophobicity |
pH-Response |
Oil-in-water |
— |
— |
116
|
HS(CH2)9CH3 HS(CH2)10COOH |
In situ growth |
Superhydrophobic–superoleophilic/superhydrophilicity–underwater superoleophobicity |
pH-Response |
Oil-in-water/water-in-oil |
3000–12 000 |
>99.9 |
117
|
RGO sponge |
GO |
Freeze-drying |
Hydrophobic/oleophilic (one side) |
Janus wettability |
Oil-in-water/water-in-oil |
— |
≥99.2 |
118
|
Hydrophilic/oleophilic (the other side) |
Melamine sponge |
Hydrophobic polymer solution |
Solvent-immersing |
Superhydrophobic–superoleophilicity |
— |
Water-in-oil |
156 700 |
>99.98 |
119
|
Cellular aerogels |
PAN, SiO2 |
Electrospinning, freeze-drying |
Superhydrophobic–superoleophilicity |
— |
Water-in-oil |
1590 |
>99.995 |
120
|
Cu foam |
Cu nanoparticles, N-dodecyl mercaptan |
Electrodeposition, liquid phase reaction |
Superhydrophobic–oleophilic |
— |
Water-in-oil |
6560 |
>99.89 |
121
|
Ti foam |
Fluorine-containing electrolyte |
Anodization |
Superhydrophobic–superoleophilicity |
— |
Oil-in-water |
— |
>99 |
122
|
3. Special wettability stimulated porous materials for oil–water separation
Endowing different porous materials with special wettability, including superhydrophobicity–superoleophilicity, superhydrophilicity–superoleophobicity and superhydrophilicity–underwater superoleophobicity, is desirable for oil–water separation. Therefore, different types of porous materials and the nanofabrication strategies for constructing special wettability will be introduced in this section (Fig. 3).
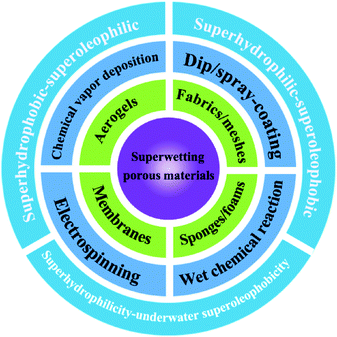 |
| Fig. 3 The latest efforts in the nanofabrication strategies of traditional porous materials such as 2D-membranes, textiles, meshes and 3D-sponges, foams, and carbon-derived aerogels with special wettability from superhydrophobicity–superoleophilicity and superhydrophilicity–superoleophobicity to superhydrophilicity–underwater superoleophobicity. | |
3.1 Superhydrophobic–superoleophilic materials
Superhydrophobic–superoleophilic materials are the most typical oil removing materials for oil–water separation through either oil filtration (2D-membranes, textiles, and metal meshes) or oil absorption (3D-sponges, foams, carbon and carbon-derived materials).123,124 Since surface roughness and surface chemical composition are the two key factors to construct special wettability, superhydrophobic–superoleophilic materials can be fabricated by two methods: (1) enhancing surface roughness by creating micro/nano architectures on the substrate; (2) modifying hydrophobic rough surfaces with low-surface-energy F-containing atoms/molecules or CH3-containing groups.125,126 Accordingly, different types of superhydrophobic–superoleophilic materials and their corresponding fabrication methods will be introduced below.
3.1.1 Construction of 2D-membranes, metal meshes, and fabrics with special wettability.
As mentioned before, 2D metal meshes, fabrics and membranes can be applied to oil–water separation based on filtration. These superhydrophobic–superoleophilic porous materials have been successfully synthesized by modification via the electrospinning technique, the dip/spray-coating method, wet chemical reaction, chemical vapor deposition, phase separation, gas phase coating strategies, etc.
(1) Electrospinning method.
Electrospinning is a versatile technique to create polymer-based membranes, which spontaneously exhibit high specific surface areas and 3D interconnected architectures with micro/nanopores. Electrospun membranes exhibit promising potential in oil–water separation when endowed with special wettability, and they can be fabricated by direct electrospinning or surface modification.127–129 In the first step, hydrophobic polymeric materials such as polystyrene (PS), poly(vinylidene fluoride) (PVDF), polydimethylsiloxane (PDMS) and fluorinated silane functionalized polymers have been widely used for direct electrospinning of hydrophobic membranes.130,131 Jiang et al. fabricated hydrophobic films by electrospinning of polystyrene/dimethylformamide (PS/DMF) solutions.132 By controlling PS concentration, surface micro/nano architectures were significantly enhanced (Fig. 4a and b) and subsequently super water-repellency was realized. Cao et al. developed an intrinsic superhydrophobic–superoleophilic microfibrous membrane with microporosity by electrospinning nanotechnology.133 Due to its high contrast wettability towards oil and water, both immiscible oil–water mixtures and water-in-oil emulsions can be separated with high efficiency. In addition, an environment-friendly polymer, polyvinyl butyral, has been chosen to fabricate superhydrophobic–superoleophilic nanofibrous membranes by electrospinning because of its stability and hydrophobicity, and stainless steel wire meshes with different mesh numbers (12#, 20#, 30#, 40#) were used as collectors.111 The pore size of the nanofibrous membranes could be finely controlled by using different mesh numbers and all of the nanofibrous membranes showed highly hydrophobic and superoleophilic properties (Fig. 4c). It was demonstrated that the nanofibrous membranes could selectively and rapidly separate oil from both a layered oil–water-mixture and water-in-oil emulsion, and the enlarged pore size could greatly improve the oil flux without obvious influence on the separation efficiency (Fig. 4d–f and Table 1). The designed nanofibrous membranes with controllable pore sizes showed large oil flux, high separation efficiency, excellent durability, and recyclability for oil–water separation, which have made them great candidates in the management of oily water. Apart from solvent and polymer concentration, external additives such as micro/nano particles (ZnO, SiO2, TiO2, Fe3O4, etc.), nanotubes and ionic liquids also have a significant impact on surface wettability.134–137 Moreover, electrospinning followed by nano modification is more effective for fabricating superhydrophobic membranes with suitable surface wettability and durable mechanical/chemical durability. In this way, superhydrophobicity can be obtained by combining electrospinning with some other modification techniques such as phase separation, wet chemical reaction, chemical vapor deposition, etc.138,139 Rutledge et al. constructed a superhydrophobic membrane by electrospinning and then coated it with a thin layer of a hydrophobic polymer by chemical vapor deposition.140 Though electrospun membranes have been used for oil–water separation, they suffer from low penetration speed, and inadequate mechanical strength and integrity, which greatly limit their practical applications.
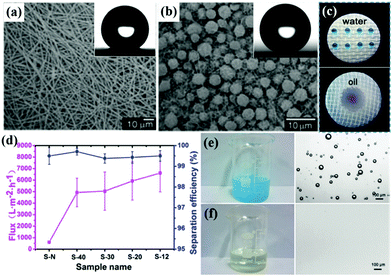 |
| Fig. 4 SEM images of a film prepared from 25% (a) and 7% PS/DMF solution (b), respectively. The insets are the corresponding water droplets on the film. Digital images of water droplets stained with methylene blue and liquid paraffin droplets stained with oil red on the surface of nanofibrous membranes (c). Oil flux and separation efficiency of five kinds of nanofibrous membranes for separation of a water-in-oil emulsion (d). Digital images of water-in-oil emulsion before (e) and after separation (f), and the corresponding optical images of water-in-oil emulsion before and after separation. (a and b) Reproduced with permission.132 Copyright 2004, Wiley-VCH. (c–f) Reproduced with permission.111 Copyright 2016, American Chemical Society. | |
(2) Dip/spray-coating method.
Dip-coating is one of the simplest approaches to decorate different substrates with either micro/nano-architectures or low-surface-energy components. Thus, dip-coating is suitable for one-step modification to achieve superhydrophobicity without further treatment.141,142 For example, Zhou et al. used a nanocomposite, which contained PDMS, fluorinated alkyl silane functionalized silica nanoparticles and fluoroalkylsilane, as a nanocoating material to endow fabrics with superhydrophobicity.143 When compared to the unmodified fabric (Fig. 5a), the silica nanoparticles were uniformly dispersed on the fiber surface after dip-coating, which created architectures at the nanoscale and made fabric highly water-repellent (Fig. 5b). Besides, Deng et al. successfully fabricated a superhydrophobic fabric by immersing it in TiO2–SiO2@PDMS hybrid solution.144 The prepared superhydrophobic fabric exhibited excellent resistance to strong acid attack (Fig. 5c), and can be applied to a filter cloth for oil–water separation. Though nanoparticles can be easily dispersed in the polymer solution and directly coated on various substrates by the one-step dip-coating method, the dispersed particles are unstable and tend to aggregate in a short time, limiting the large-scale production.
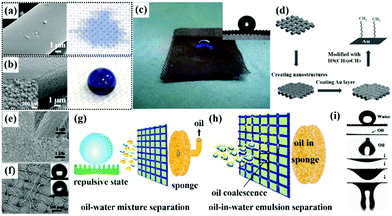 |
| Fig. 5 SEM images of the unmodified (a) and modified (b) polyester fabrics and the right pictures are the corresponding optical images of water drops on the polyester fabrics, respectively. The optical image of an acid water droplet dyed with methyl blue on a superhydrophobic–superoleophilic steel mesh (c). Schematic diagram of the fabrication process for the superhydrophobic–superoleophilic film (d). SEM images of PDMS-ormosil@fabric (e and f), the inset of (e) is its corresponding low-magnification image and the insets of (f) represent the static and dynamic behavior of the droplet on PDMS-ormosil@fabric. Schematic illustration of the continuous separation mechanism of the oil–water-mixture (g) and the surfactant-free oil-in-water emulsion (h). (i) Optical picture of a water droplet on the coated mesh film with a high contact angle (top image), and the process of oil spreading and permeating the coated mesh film (bottom image). (a and b) Reproduced with permission.143 Copyright 2012, Wiley-VCH. (c) Reproduced with permission.144 Copyright 2012, Royal Society of Chemistry. (d) Reproduced with permission.154 Copyright 2016, Wiley-VCH. (e–h) Reproduced with permission.155 Copyright 2016, Royal Society of Chemistry. (i) Reproduced with permission.158 Copyright 2015, Royal Society of Chemistry. | |
Considering that there are no distinct micro/nano architectures on most pristine substrates, the dip-coating process combined with pre-treatment to roughen smooth surfaces is more appealing to construct superhydrophobic interfaces.145,146 Among various pre-treatment approaches, chemical etching,147,148in situ growth,149,150 and particle-coating151,152 are the most widely used techniques to endow surfaces with micro/nano architectures for suitable roughness. Lu et al. created a superhydrophobic–superoleophilic steel surface by first immersing it in a salt solution to etch micro/nano-sized structures on its surface, and then modifying it using a low-surface-energy material by dip-coating.153 Besides, Cheng et al. synthesized a superhydrophobic–superoleophilic copper mesh by creating micro/nano architectures on its surface and then modifying it with the hydrophobic/oleophilic components (Fig. 5d).154 In addition, our group developed a superhydrophobic fabric by a simple and fast dip-coating of an organically modified silica aerogel (ormosil) thin film onto the fabric first, followed by PDMS top-coating. The process endowed the fabric with a rough surface and low surface energy at the same time (Fig. 5e and f).155 By varying the grafted PDMS concentration, the surface exhibited repulsive and adhesive states, which are applicable for both oil–water-mixture separation and oil-in-water emulsion separation, respectively (Fig. 5g and h).
Beyond the dip-coating method, spray-coating is another effective and low-cost technique for making desirable substrates superhydrophobic.156,157 For example, Feng et al. sprayed a polytetra-fluoroethylene coating on a stainless steel mesh, and the polytetra-fluoroethylene coated mesh exhibited superhydrophobicity–superoleophilicity due to the superhydrophobicity of the polytetra-fluoroethylene coating for water rejection.158 As shown in Fig. 6i, water droplets maintained the original morphology above the surface, while oil droplets spread and permeated the mesh quickly. Though dip-coating and spray-coating are very efficient and cost-effective, adhesion between decorative micro/nano coatings and various substrates is generally low and it is easy to destroy by either chemical etching or mechanical actions.159–161 To enhance the durability, a robust coating can be realized by other more promising techniques, such as wet chemical reaction, chemical vapor deposition and so on.
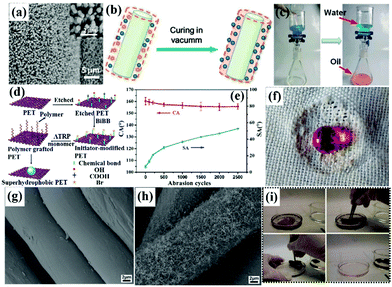 |
| Fig. 6 SEM images of the as-prepared micro-structured ZnO nanorods on the stainless-steel mesh films (a) and the inset is the corresponding magnified image. Schematic diagram of in situ polymerization of a fluorinated polybenzoxazine functional layer on the membrane surface (b). The process of oil–water separation using the as-prepared membranes (c). Schematic illustration of the fabrication of superhydrophobic fabrics by the ATRP technique (d). Changes of contact angle and sliding angle with repeated abrasion cycles (e). Photograph of a water droplet on the superhydrophobic fabrics after 2500 cycles (f). SEM images of uncoated (g) and coated (h) polyester textiles. The process of oil removal from an oil–water-mixture (i). (a) Reproduced with permission.172 Copyright 2012, American Chemical Society. (b and c) Reproduced with permission.174 Copyright 2013, Royal Society of Chemistry. (d–f) Reproduced with permission.178 Copyright 2015, American Chemical Society. (g and h) Reproduced with permission.184 (i) Reproduced with permission.189 Copyright 2014, Royal Society of Chemistry. | |
(3) Wet chemical reaction method.
Wet chemical reaction includes various processes, such as in situ growth of both metal oxides and metallic nanomaterials, in situ polymerization, electrochemical deposition and atom transfer radical polymerization (ATRP).162–165 Both surface chemical composition and rough surface micro/nano architectures can be controlled by gradually growing or grafting reaction materials. The binding force between created micro/nano-coatings and substrates is largely enhanced due to the strong chemical bonding energy between each them, which is more favorable for practical application.166,167 For example, Wang et al. constructed a rough structure on fabrics and sponges via in situ growth of metal oxide/metallic nanocrystals followed by a coating of thiols.168 These as-prepared superhydrophobic–superoleophilic fabrics and sponges were successfully used for oil–water separation. Besides, hierarchically structured fabric surfaces can also be achieved by in situ growth of some other metal oxide particles, such as TiO2 and ZnO, via one-pot hydrothermal technology. And surfaces with remarkable superhydrophobicity could be constructed by subsequent chemical modification of low-surface-energy components.169–171 Chang et al. grew micro/nano-structured ZnO nanorods on a stainless-steel mesh film via a simple hydrothermal method.172 After the hydrothermal treatment, aligned ZnO nanorod arrays were formed radially and uniformly along every wire (Fig. 6a). After post-modification with stearic acid, superhydrophobicity–superoleophilicity was achieved. When an oil droplet (toluene, gasoline and diesel oil) was placed on the mesh surface, it spread and penetrated quickly, with the oil eventually dripping down, while water would stay on the mesh surface. Furthermore, we successfully fabricated TiO2@fabric composites by a one-pot hydrothermal reaction and fluoroalkylsilane modification.173 After the treatment, micro-marigold flower-like hierarchical TiO2 particles were uniformly coated on the fiber surface and the superhydrophobic TiO2@fabric demonstrated highly efficient oil–water separation due to its extreme wettability contrast (superhydrophobicity/superoleophilicity).
The surface micro/nano structure will be unstable if the polymers are simply dissolved in a solution and then coated on the substrate surface without chemical actions. However, if the polymer chains are cross-linked, the coating will be resistant to damage by either chemical or mechanical attack. In situ crosslinking has been proven to be an effective technique to enhance coating stability. In addition to copolymers, monomers can self-polymerize and form micro/nano particles in the presence of a catalyst on the surface of substrates. For example, Tang et al. fabricated a superhydrophobic–superoleophilic membrane by in situ polymerization of a fluorinated polybenzoxazine functional layer on the membrane surface (Fig. 6b).174 With the incorporation of SiO2 nanoparticles on the surface, water-repellency was largely enhanced and the water contact angle could reach 161°. Thus, layered oil–water-mixtures can be separated efficiently (Fig. 6c).
Besides, atom transfer radical polymerization is a controlled radical polymerization technology that has been proven to be a useful tool for the synthesis of functional macromolecules with controllable architectures on various substances.175,176 Generally, the hydroxyl group is often used to produce active sites for reacting with an initiator. Thus, cellulose fabric containing abundant hydroxyl groups is readily used to graft functional monomers. For example, Li et al. developed a highly hydrophobic silk by grafting acrylate fluoride monomers via the ATRP route.177 For other substrates without abundant hydroxyl groups, they can be pre-treated easily by O2 plasma sputtering or chemical modification to generate large quantities of hydroxyl groups. Xue et al. prepared a superhydrophobic–superoleophilic poly(ethylene terephthalate) fabric surface by surface initiated atom transfer radical polymerization of fluorinated methacrylates on sodium hydroxide solution etched poly(ethylene terephthalate) fabrics (Fig. 6d).178 The obtained superhydrophobic fabric showed excellent chemical robustness and mechanical durability. Even after 2500 abrasion cycles, it still maintained high superhydrophobicity and water droplets could stand spherically on the fabric surface (Fig. 6e and f). In addition to hydroxyl groups, an amino-containing dye intermediate (2-chloro-4,6-diamino-1,3,5-triazine) was also used to make more active sites for in situ polymerization.179 Besides the in situ growth, in situ polymerization and ATRP methods, cathodic electrodeposition is another common wet chemical reaction technique to achieve superhydrophobicity–superoleophilicity. Wang et al. constructed a micro/nano-structured copper mesh by an electrodeposition method in an aqueous solution containing copper sulfate and sulfuric acid.180 After the long-chain fatty acid monolayer polymerized on the as-prepared surface-roughed copper mesh, a superhydrophobic copper mesh was obtained.
(4) Chemical vapor deposition method.
Chemical vapor deposition (CVD) has been demonstrated to be another facile technique to gradually construct hierarchical structures on substrates.181–183 Compared to the simple dip/spray-coating method and the wet chemical reaction technique, chemical vapor deposition is controllable and tends to form a more uniform coating with high density on the substrates. For example, Zhang's group developed a one-step technique to construct a superhydrophobic–superoleophilic polyester textile via chemical vapor deposition of trichloromethylsilane for applications in oil–water separation and selective oil absorption.184 The uncoated polyester textile composed of microfibers with a diameter from 15 to 20 μm exhibited a smooth surface (Fig. 6g). After CVD, the textile displayed a rough surface with a dense layer of randomly grown silicone nanofilaments (Fig. 6h), which resulted in super water-repellency. Besides, Crick et al. used an aerosol assisted CVD technique to coat copper meshes with a hydrophobic silicone elastomer.185 When compared to the pristine copper meshes, the modified surfaces were made up of agglomerations of micro/nano polymer microparticles and exhibited superhydrophobicity–superoleophilicity. Likely, Zhou et al. also produced a superhydrophobic–superoleophilic fabric via a vapor phase deposition technique.186 Compared to pristine cotton, the modified fabric had outstanding superhydrophobic properties for oil–water separation. As CVD has limited effects on surface roughness, pre-treatment via chemical etching or nanoparticle decoration is essential to enhance micro/nano architectures.187,188 From this view, Cortese et al. used O2 plasma pre-treatment to introduce a dual-scale nanostructure on the textile surface, followed by diamond-like carbon coating on the cotton fabric via the CVD technique to achieve low surface energy and a rough surface simultaneously.189 With the special superhydrophobicity–superoleophilicity property, the fabric could absorb oil from the oil–water-mixture (Fig. 6i). Although the CVD method was usually conducted under high temperature and vacuum conditions, this facile method may destroy the textile texture and accelerate the aging process.
(5) Other methods.
Beyond the modification methods mentioned above, other methods such as layer by layer assembling, candle-soot coating, incorporation, phase separation and gas phase coating strategies have also been developed to achieve special wettability.190–194
The layer-by-layer assembling approach, usually with electrostatic interactions between each layer, can provide the flexibility to improve adhesion to the substrate and create a low surface tension coating at the air interface.195 For example, Lin et al. created a superhydrophobic surface firstly via a versatile electrostatic layer by the layer self-assembly technique for constructing micro/nano surface structures, followed by a post-fluorination modification.196 Compared to the pristine cotton, modified cotton fabrics grafted with a number of silica-nanoparticle multilayers showed largely enhanced surface roughness. Besides, candle-soot as a low-surface-energy material exhibits excellent durability towards chemical attack and in harsh environments, and thus it has been utilized for constructing superhydrophobic surfaces. Li et al. used an overlapping deposition of candle-soot on the metal mesh to obtain a hydrophobic surface. Subsequently, superhydrophobic surfaces were successfully achieved with post-modification of hydrophobic silica nanoparticles.197 The obtained superhydrophobic candle-soot and silica coated meshes could maintain high separation efficiency above 98.5% for many types of organic oils and exhibited stable recyclability after ten cycles of separation. Recently, a facile and inexpensive one-step sonochemistry irradiation method appeared for the fabrication of SiO2 nanoparticles functionalized with octadecyltrimethoxysilane and in situ incorporation onto cotton fabrics.198 The double sides of as-prepared fabrics showed both superhydrophobic and superoleophilic properties simultaneously with a high water contact angle of 159° and an oil contact angle of 0°, and were successfully used to separate oil–water-mixtures. What's more, phase separation is also effective for enhancing micro/nano architectures. Xue et al. constructed a rough PDMS coating on the fabric surface via a phase-separation method.199 The phase-separated polydimethylsiloxane/polyvinyl chloride composite coating was rougher than the original polydimethylsiloxane/polyvinyl chloride coating. In addition, Zimmermann et al. developed superhydrophobic textile fibers through a similar gas phase coating technique.200 Compared to traditional techniques, all the newly emerged methods make superwetting porous materials much easier to be obtained.
3.1.2 Construction of 3D-sponges, foams and aerogels with special wettability.
Both sponges and foams are cheap and commercial porous materials with a high absorption capacity for various liquids. When endowing them with superhydrophobicity–superoleophilicity, sponges and foams can be applied in oil–water separation based on selective oil absorption, which can also be fabricated by the nanoscale fabrication strategies mentioned above such as dip-coating, wet chemical reaction, chemical vapor deposition, etc. Zhu et al. developed a robust superhydrophobic polyurethane (PU) sponge by the immersion method, accompanied with the hydrolysis of methyltrichlorosilane on the surface (Fig. 7a).201 After the treatment, a hierarchically porous coating covered the interconnected skeleton of the as-prepared sponge, which is responsible for robust superhydrophobicity (Fig. 7b and c). Moreover, it can be used to absorb oil at the water surface, and oil can also be collected through a simple mechanical squeezing process (Fig. 7d). Likely, Zhu et al. also fabricated a superhydrophobic PU sponge by a simple dip-coating method.202 The soft and elastic sponges could be deformed readily by an external force, e.g. mechanical squeezing, which is useful for oil absorption and collection (Fig. 7e). In general, octadecylamine, PDMS and other low-surface-energy polymers and monomers have been coated on the surface of sponges to improve their water-repellency (Fig. 7f).203,204 In addition to these polymers, hydrophobic carbon nanomaterials such as carbon nanotubes (CNTs) and graphene have also been applied as coating materials for fabricating superhydrophobic sponges and foams. For example, Zhou et al. developed a graphene coated PU sponge via the one-pot solvothermal technique.205 Because the functionalized PU sponge retained the original structural integrity with high porosity, it was chemically robust and capable of separating oil up to 53
000 times its own weight with a high oil–water separation efficiency over 99.5% (Fig. 7g). Besides, Chen et al. prepared an elastic carbon foam by carbonization of a polymer foam, as shown in Fig. 7h.206 The as-prepared carbon foam exhibited a number of excellent characteristics including good elasticity and extremely high porosity for efficient oil-absorption (Fig. 7i and j). Furthermore, Wu et al. developed polymer-based graphene foams by self-assembly of graphene sheets on a 3D polymer skeleton.207 The obtained polymer-based graphene foams exhibited hydrophobicity, outstanding mechanical properties and excellent cycling performances, making them ideal oil–water separators. In addition, Ding et al. created 3D hierarchical cellular aerogel sponges by combining the electrospinning method and the freeze-shaping technique.120 Significantly, all the cellular aerogel sponges exhibited prominent superoleophilicity with an extremely low oil contact angle approaching zero because of the oleophilicity of polybenzoxazine, which contained numerous benzene groups (Fig. 7k). Besides, the cellular aerogel sponges with 0.5 wt% SiO2 nanoparticles could effectively separate water-in-oil emulsions with a high flux of 1590 L m−2 h−1 and stable recyclability (Fig. 7l, m and Table 1). Unlike fabrics and meshes, superhydrophobic–superoleophilic sponges and foams displayed a 3D interconnected framework with huge space for oil absorption and storage, which is more favourable for oil–water separation.
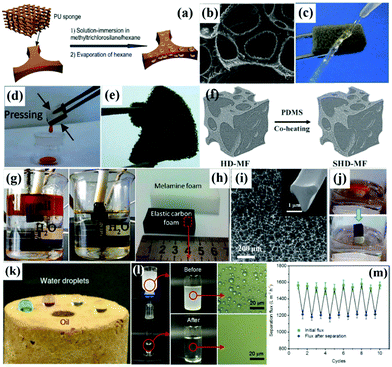 |
| Fig. 7 Schematic illustration process of the fabrication of robust superhydrophobic PU sponges (a). SEM image of the sponges treated with methyltrichlorosilane (b). Optical image of a water column squirted on the superhydrophobic sponge (c). Photograph of collection of lubricating oil from the superhydrophobic sponge (d) and a piece of sponge deformed by tweezers (e). Schematic illustration of the fabrication process of the superhydrophobic melamine foam (SHD-MF) with hierarchical-dimension microstructures (f). Images of the oil–water-mixture before and after absorption (g). Photos of a piece of MF and the derived carbon foam (h). SEM image of the carbon foam (i) and the inset is the cross-sectional image of the one network fiber in the carbon foam. Removal process of benzene from the water surface using the carbon foam (j). Optical images of droplets of dyed water and oil on 3D hierarchical cellular aerogel sponges (k). Process of water-in-oil emulsion separation using the aerogels and the microscopic images of emulsions before and after separation (l). Changes in the separation flux and flux recovery after separation within 10 cycles (m). (a–d) Reproduced with permission.201 Copyright 2013, Royal Society of Chemistry. (e) Reproduced with permission.202 Copyright 2011, American Chemical Society. (f) Reproduced with permission.204 Copyright 2015, Royal Society of Chemistry. (g) Reproduced with permission.205 Copyright 2016, Elsevier. (h–j) Reproduced with permission.206 Copyright 2013, Royal Society of Chemistry. (k–m) Reproduced with permission.120 Copyright 2015, American Chemical Society. | |
Compared to the metal (Cu, Ni, Ti, etc.) foams and polymer-derived foams/sponges, carbon-derived aerogels are another type of ideal candidates for oil-absorption owing to low-cost and their outstanding properties such as low density, high porosity, large surface area, good stability, excellent flexibility, etc.208,209 To date, the template method, pyrolysis and freeze-drying techniques have been utilized to achieve carbon-derived aerogels.
(1) Template method.
Using the template technique to fabricate carbon-derived aerogels usually can be realized first by modification of the self-supported porous template with carbon nanomaterials and then by removing the template.210,211 In the first step, CVD is the most frequently combined modification method to deposit carbon materials such as graphene, CNTs, etc. onto the porous template. For example, Dong et al. developed a superhydrophobic–superoleophilic monolithic 3D hybrid via rational coating of graphene and carbon nanotubes onto the nickel foam, followed by removal of the template by acid etching.212 Thus, a dense forest of CNTs uniformly wrapped around the 3D graphene scaffold. Besides, Yu et al. fabricated a uniform carbonaceous nanofiber aerogel by using ultrathin Te nanowires as template.213 The prepared carbonaceous nanofiber aerogels exhibited extremely low density and high flexibility and they could sustain a large compression strain and almost recovered their original volume after releasing the compression. The carbonaceous nanofiber aerogels also exhibited a high adsorption rate and good cyclability for toxic metal ions and organic dyes (Fig. 8a). Owing to the synergistic effects of flexibility and excellent adsorption performance, carbonaceous nanofiber aerogels could be used directly as compressible adsorbents for simple removal of dye pollutants and recovered by burning (Fig. 8b).
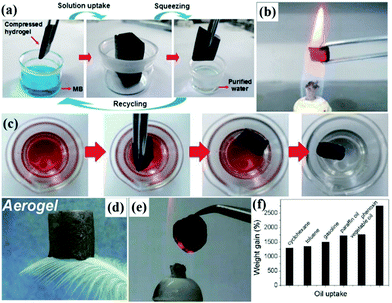 |
| Fig. 8 Process of dye pollutant removal and squeezing for reuse (a). Photograph of carbonaceous nanofiber aerogels in a hot flame for distilling the absorbed oil (b). Process of uptake of organic liquids by the carbonaceous nanofiber aerogels (c). Photograph of an ultra-light aerogel sitting on a green bristle grass (d). Image of an aerogel glowing on a flame with fire-resistance (e). Adsorption capacities of the aerogels for a range of organic solvents and oils in terms of their weight gain (f). (a and b) Reproduced with permission.213 Copyright 2012, Wiley-VCH. (c) Reproduced with permission.217 Copyright 2013, Wiley-VCH. (d and e) Reproduced with permission.225 Copyright 2013, Royal Society of Chemistry. (f) Reproduced with permission.228 Copyright 2012, American Chemical Society. | |
(2) Pyrolysis strategy.
Since the template method often encounters many difficulties in prefabrication and removal of the previous templates and usually results in impurities, the pyrolysis strategy is another widely used technique to form carbon-based aerogels.214,215 Sun et al. fabricated twisted carbon fiber aerogels by carbonization of economic raw cotton.216 The twisted carbon fiber aerogels could absorb a wide range of oils and exhibited excellent recyclability. Similarly, Yu et al. also fabricated ultralight, flexible and fire-resistant carbon nanofiber aerogels via a facile pyrolysis technique.217 The as-prepared carbon nanofiber aerogels showed excellent recyclability and selectivity for different types of organic solvents and oils due to hydrophobicity, high porosity and mechanical stability (Fig. 8c). Besides, they also reported PDMS-coated carbonaceous nanofiber hydrogels and aerogels as oil removing materials by combining the hydrothermal method and the carbonization strategy.218 Moreover, the pyrolysis-induced carbon-derived aerogels can be divided into flexible and inflexible materials based on their elastic property. It should be noted that the flexible carbon-derived aerogel sponges can be reused by the direct squeezing method, combustion method or distillation method.
(3) Freeze-drying technique.
Besides the template and pyrolysis methods, freeze-drying is also frequently used to achieve carbon-derived aerogels.219,220 Generally, precursor solutions used for freeze-drying to form aerogels are prepared by dispersing graphene oxide (GO) or CNTs in a suitable solvent. Then, to reduce the density and enhance absorption property, chemical reductants such as dopamine, metal nanoparticles, ethylenediamine and hydrazine are often employed to transform GO into graphene after freeze-drying.221,222 Gao et al. developed an all carbon ultra-light aerogel by freeze-drying a mixed solution of CNTs and giant graphene oxide sheets, followed by chemical reduction with hydrazine vapor.223 Due to the synergistic effect of hierarchical nanostructures and superhydrophobic properties, all carbon aerogels exhibited integrated properties of ultra-low density, super recyclable compressibility, and excellent conductivity. In addition to chemical reductants, the thermal reduction strategy is also employed to transform GO to graphene. For example, He et al. developed three kinds of GO foams by using different freezing methods and then the corresponding RGO foams were prepared by thermal reduction.224
On the other hand, reduction-assembly before freeze-drying is another popular method to construct carbon-derived sponges for oil–water separation. Li et al. developed compressive graphene aerogels through one-step reduction followed by freeze-drying.225 The aerogels displayed extremely low density, good compressibility and fire-resistance (Fig. 8d and e). The aerogels were able to absorb different organic liquids due to their inherent high porosity with a hydrophobic nature. Besides, oil collection can be realized by the absorption-squeezing process. Furthermore, macroscopic graphene monoliths can be easily achieved by incorporating functional nanomaterials such as α-FeOOH nanorods and magnetic Fe3O4 nanoparticles into graphene sheets during the freeze-drying process.226,227 Such functional graphene-based aerogels exhibited excellent capability for removal of pollutants, and thus could be used as promising adsorbents for wastewater treatment. Cong et al. developed a macroscopic graphene/iron oxide aerogel by using metal-oxide nanoparticles as reductants, followed by freeze-drying.228 The aerogel exhibited high adsorption capacity towards different organic solvents and oils (Fig. 8f). In addition, Bi et al. developed a superhydrophobic graphene sponge via hydrothermal treatment of GO suspension followed by freeze-drying.229 The spongy graphene showed highly efficient absorption towards toxic solvents with higher efficiency than conventional absorbers. And it can be reused by heat treatment. Since doping graphene with substituent heteroatoms could effectively improve its electrical properties and physical and chemical features, Zhao et al. developed a versatile ultralight 3D N-doped graphene framework with fire-resistant properties, exhibiting a very high capacity for the reversible absorption of oils and organic solvents.230 Therefore, freeze-drying is one of the most promising techniques to produce porous carbon-based aerogels with low density, high porosity and large surface area for oil-absorption because of low-cost, less time, facile manipulation and large-scale production.
3.2 Superhydrophilic–superoleophobic and superhydrophilic–underwater superoleophobic materials
Theoretically, superhydrophilic–superoleophobic porous materials are also applicable for oil–water separation based on water filtration or absorption. However, according to the basic wetting theory, a superoleophobic surface generally exhibits superhydrophobicity because oils commonly exhibit lower surface free energy. Therefore, it is a challenge to achieve a surface with superhydrophilicity–superoleophobicity in a normal environment.231,232 Researchers have found that some stimuli-responsive materials can simultaneously show hydrophilic and oleophobic properties based on opposite adhesion properties toward polar liquids (e.g., water) and non-polar liquids (e.g., hexadecane). Based on this mechanism, Zhang et al. fabricated a smart superhydrophilic–superoleophobic surface using poly(diallyldimethylammoniumchloride)–perfluorooctanoate/SiO2 as functional coatings.31 The combination of fluorinated groups together with carboxyl and quaternary ammonium groups resulted in a superhydrophilic–superoleophobic property. Moreover, micro/nano surface roughness was largely realized by the incorporation of SiO2 nanoparticles, which led to enhanced wettability and anti-wettability. The poly(diallyldimethylammoniumchloride)–perfluorooctanoate/SiO2 coated mesh showed water permeation and excellent oil repellent behaviors, indicating that the modified mesh could be applied in oil–water separation. It is interesting that the meshes could be cleaned with water and dried to bring them back to their original state. Besides, Kota et al. successfully fabricated intelligent membranes with both superhydrophilicity and superoleophobicity in air and underwater (Fig. 9a and b).233 The prepared membranes can separate large quantities of different oil–water-mixtures with over 99.9% separation efficiency by the different capillary forces on the two phases. Likewise, the superhydrophilic–superoleophobic fabrics displayed a similar performance toward oil–water emulsion. When an emulsion is placed on the intelligent membranes, and water in the emulsion is in contact with the membrane, the surface starts to reconfigure. Within several minutes, the water passed through the membrane while the hexadecane-rich counterpart was retained above the membrane surface. These superhydrophilic–superoleophobic porous materials are the ideal tools for the clean-up of oil spills, wastewater treatment and the separation of oil–water emulsions. Though this novel strategy is desirable for constructing superhydrophilic–superoleophobic surfaces, the achievements are still limited in practical applications.
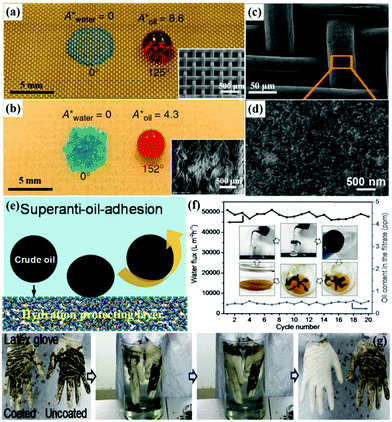 |
| Fig. 9 Images of droplets of water (dyed blue) and rapeseed oil (dyed red) on a superhydrophilic–superoleophobic stainless steel mesh (a) and a polyester fabric (b), respectively. Insets of (a and b) are the corresponding SEM images. SEM images of a poly(acrylic acid)-grafted poly(vinylidenefluoride)-coated copper mesh (c and d). The mechanism of the poly(acrylic acid)-grafted poly(vinylidenefluoride) coated membrane for underwater superanti-oil-adhesion (e). Separation flux and oil content in the filtrate within 20 cycles for the crude oil–water-mixture separation (f). Self-cleaning processes of latex glove with and without PAAS-g-PVDF coating (g). (a and b) Reproduced with permission.233 Copyright 2012, Nature Publishing Group. (c–g) Reproduced with permission.239 Copyright 2016, Wiley-VCH. | |
Inspired by fish, which are known to be well protected from oil contamination underwater, porous materials with superhydrophilicity–underwater superoleophobicity are of great interest and seem to be more desirable for oil–water separation.86 Generally, rough fish scales are covered by a layer of mucus mainly consisting of a hydrophilic hydrogel. Due to this hydrophilic chemical composition on the surfaces and hierarchical micro/nanoscale structures, the fish skin exhibits superhydrophilicity in air and superoleophobicity underwater with an oil contact angle of 156.4 ± 3.0°. Another type of underwater superoleophobic organism, clams, can remain clean on the outside and internal surfaces of their shells, especially in the pallium-covered region. The inorganic CaCO3 composition of their shells and their surface hierarchical structures are two key factors in determining their excellent underwater oil repellency.234 By the simulation of natural architectures at nanoscale and low-surface-energy compositions, researchers have developed numerous artificial superhydrophilic–underwater superoleophobic porous materials for both oil–water-mixture and oil–water emulsion separation.235
Considering GO with a characteristic layered nanostructure, it is expected to be an ideal building block for the construction of underwater superoleophobic films.236,237 For example, Dong et al. coated hydrophilic GO onto stainless steel meshes by immersing the meshes in GO aqueous solution.238 After repeating this process several times, GO layers formed uniform nanostructures on the steel mesh and it showed excellent superhydrophilicity–underwater superoleophobicity. By taking advantage of this underwater opposite wettability, a series of oil–water-mixtures were successfully separated. Besides, the hydrogel is another typical hydrophilic composition for designing superhydrophilic–underwater superoleophobic surfaces, due to its excellent water-absorbing and water-retaining capacities. Jin et al. developed a robust poly(acrylic acid)-grafted poly(vinylidenefluoride) hydrogel-coated copper mesh (Fig. 9c and d) with unprecedented underwater anti-adhesion and self-cleaning properties toward crude oils under an aqueous environment, which could effectively separate a crude oil–water-mixture with an extremely high flux of about 50
000 L m−2 h−1 and a high separation efficiency of 97.1% (Fig. 9e–g).239 It also displayed superior performance for oil–water emulsion separation due to ultralow oil-adhesion and oil-blocking properties. Furthermore, Jiang et al. constructed a hydrogel-coated filter paper, which exhibited superior separation performance for both oil–water-mixtures and oil-in-water emulsion with high separation efficiency (>99%) in a complex environment (Table 1).107 Beyond GO and hydrogels, some hydrophilic nanomaterials such as palygorskite, TiO2, and Cu(OH)2 have also been used for constructing superhydrophilic–underwater superoleophobic materials with micro/nano architectures.240–243 Yu et al. also reported an outstanding superhydrophilic–underwater superoleophobic mesh for oil–water separation by growing pure silica zeolite crystals on the film.244 What's more, Zhang et al. used a one-step chemical oxidation of a smooth copper mesh to obtain a superhydrophilic–underwater superoleophobic Cu(OH)2-covered mesh.115 They all exhibited stable recyclability and high efficiencies for oil–water emulsion separation. Compared to conventional superhydrophilic–superoleophobic materials, superhydrophilic–underwater superoleophobic materials exhibit more promising potential in oil–water separation.
4. Intelligent functions for on-demand oil–water separation
Compared to traditional materials with special wettability, on-demand intelligent superwetting materials have become more appealing for improving separation efficiency and meeting special oil–water separation demands such as oil–water-emulsion remediation, switchable oil–water separation, remote controllable oil absorption and oil/water collection.
4.1 Stimuli-responsive wettability
Porous materials with stimuli-responsive wettability can switch between super-wetting and super-anti-wetting by applying an external stimulus (e.g., pH, light illumination, temperature, voltage, etc.), which can be constructed by grafting some stimuli-responsive polymers or functional inorganic micro/nano particles, offering a significant advantage for selectively allowing oil or water alone to pass through.215,245–249 Therefore, porous materials with extreme wettability transition have been successfully developed for controllable oil–water separation in various situations, such as simple oil–water-mixture separation, continuous oil-in-water and water-in-oil emulsion separation, etc.
4.1.1 pH-Responsive wettability.
Among various external stimuli, pH-induced reversible special wettability is attractive because of its easy operation, rapid response and no need for special facilities. Most pH-responsive components have ionizable groups, such as sulfonates, carboxylic acids, pyridines, amines, etc., which are very sensitive to pH changes and can dramatically change their conformation quickly in response to minor changes of pH, leading to switchable affinity between oil/water and the substrate interface.250,251 Weak polybases and weak polyacids are the most commonly used pH-responsive polymers for achieving switchable wetting properties. Weak polybases transform into polyelectrolytes at low pH with electrostatic repulsion forces between the molecular chains, while they transform into neutral polymers at high pH. A momentum along with the hydrophobic interaction is suggested to govern the hydrophobic/hydrophilic characteristics of surfaces. At the same time, weak polyacids have a pH-responsive carboxyl group, consisting of a carbonyl and a hydroxyl group. The carboxyl groups can be protonated, and the surface exhibits hydrophobicity at low pH, while the carboxyl groups dissociate into carboxylate anions with hydrophilicity at high pH.252 Therefore, by combining the pH-responsive polymers with rough surface structures, various smart pH-responsive surfaces with controllable wettability have been fabricated. For example, Zhang et al. constructed an intelligent surface by grafting a block copolymer made up of blocks of pH-responsive poly(2-vinylpyridine) and oleophilic/hydrophobic polydimethylsiloxane (P2VP-b-PDMS).253 On the one hand, the P2VP block could change its wettability and conformation via protonation and deprotonation upon pH changes, which provided switchable access of oil by the block, resulting in the switchable oil wettability in an aqueous environment (Fig. 10a). On the other hand, the PDMS block also had switching reversibility towards surface oil wettability. Moreover, a smart fiber membrane was achieved by depositing pH-responsive copolymer poly(methyl methacrylate)-block-poly(4-vinylpyridine) on a stainless steel mesh via electrospinning (Fig. 10b).254 The obtained mesh exhibited two switchable wettability states (superhydrophobicity–superoleophilicity/superhydrophilicity–underwater superoleophobicity) and it also could be used in separating water–oil or water–organic solvent mixtures (Fig. 10c and d). Furthermore, Dang et al. fabricated smart 2D membranes (cotton fabric and filter paper) and a 3D foam (PU foam) by a simple dip-coating of a non-fluorinated random copolymer, poly(dodeyl methacrylate-co-3-trimethoxysilylpropyl methacrylate-co-2-dimethylaminoethyl methacrylate) (PDMA-co-PTMSPMA-co-PDMAEMA).106 The coated membranes and foams exhibited switchable superhydrophilicity/superhydrophobicity with different pH values (Fig. 10e) and can be applied in different types of continuous oil–water emulsion separation with high separation efficiency (Table 1). At neutral and high pH values, PDMAEMA chains were not protonated and maintained their collapsed conformations. The dominantly exposed PDMA chains prohibited the coating from being wetted by water and kept their high affinity to oil, leading to superoleophilicity. Upon contacting oil, the PDMA chains preferentially stretched out into the oil because of their oleophilic nature (Fig. 10f, left). When the pH decreased to 2.0, the nanocoatings became hydrophilic and were wetted by the acidic water because of the protonated PDMAEMA chains, which exhibited an extended conformation due to the electrostatic repulsion of the protonated tertiary amine group and were dominantly exposed. The dominantly exposed PDMAEMA chains were hydrophilic and could trap water, and thus, an oil–water–solid composite interface could be formed (Fig. 10f, right). In addition to block copolymers, monomers can also be utilized to fabricate pH-responsive surfaces with wettability. For example, Cheng et al. developed a smart copper mesh with pH-responsive wettability by the grafting of HS(CH2)9CH3 and HS (CH2)10COOH molecules.255 The smart wetting responsive ability was attributed to the synergistic effect of the surface chemistry variation and rough structures. The surface showed superoleophilicity in acidic water while it showed superoleophobicity in basic water, which can be realized by changing the pH of the solution. The smart surface exhibited underwater superoleophilicity due to its high affinity to oil under non-basic water (Fig. 10g). When the pH increased to basic values, surface carboxylic acid groups were deprotonated, resulting in a strong hydrogen bonding between water and the deprotonated carboxylic acid (Fig. 10h). Due to the reversible wettability, oil–water-mixtures can be separated in a more controllable way. This strategy opens a new perspective in controlling the surface oil wettability and can be applied to other relevant applications such as antifouling, antipollution, microfluidic devices, etc.
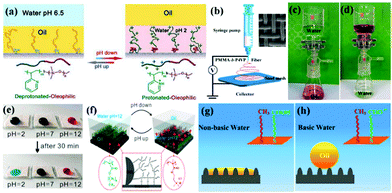 |
| Fig. 10 Schematic diagrams of the switchable oil wettability of the P2VPb-PDMS-grafted textile at different pH (a). Schematic diagram of the electrospun pH-responsive membrane fabrication process (b). Oil/water separation process: oil passed through the membrane, whereas water remained in the upper glass apparatus (c); water passed through the membrane, while oil remained in the upper glass apparatus (d). Photographs of the acidic, neutral, and basic droplet on the coated fabric before and after 30 minutes (e). Mechanism of pH responsive coatings at different pH (f). Schematic illustration of the responsive oil wettability on the rough surface in non-basic water (g) and basic water (h). (a) Reproduced with permission.253 Copyright 2012, Nature Publishing Group. (b–d) Reproduced with permission.254 Copyright 2015, American Chemical Society. (e and f) Reproduced with permission.106 Copyright 2016, American Chemical Society. (g and h) Reproduced with permission.255 Copyright 2014, American Chemical Society. | |
4.1.2 Photo-responsive wettability.
Photo-responsive wettability switching between superhydrophobicity and superhydrophilicity in materials decorated by UV-sensitized semiconductors (ZnO, TiO2, etc.) for effective controllable oil–water separation has also been widely studied.256–261 When the decorative ZnO or TiO2 particles are exposed to UV illumination, electron–hole pairs are produced on the surface, forming high-surface-energy hydroxyl radicals. Thus, the wetting state can change from hydrophobicity to hydrophilicity due to the existence of hydrophilic hydroxyl groups. While storing in the dark for a period of time, the hydroxyl groups are removed easily by oxygen in the environment. As a result, the surfaces recover their original hydrophobic wettability. For example, Jiang et al. fabricated a ZnO nanorod array-coated stainless steel mesh with switchable superhydrophobicity–superhydrophilicity and underwater superoleophobicity for photo-induced oil–water separation.262 Herein, due to the excellent UV-sensitive property of ZnO, extreme wettability transition can be realized by UV irradiation and storage in the dark place (Fig. 11a). Namely, after UV illumination, the superhydrophobic surface changed into superhydrophilic owing to the lower intrusion pressure, while superoleophilicity displayed extreme underwater superoleophobicity with an oil contact angle higher than 150°. By combining UV-induced superhydrophilicity and underwater superoleophobicity, they showed excellent controllability and high separation efficiency of different types of oil–water-mixtures. Especially, the underwater superoleophobicity of the ZnO-coated stainless steel mesh film can effectively prevent the mesh film from being polluted by oils, exhibiting good self-cleaning performance. Besides, photo-induced wettability changes enable external manipulation of liquid droplet motion and further could facilitate demulsification. Kwon et al. demonstrated that the wettability state of a dye-sensitized TiO2 surface could be changed upon visible light illumination.263 By utilizing this photo-induced changeable surface wetting, liquid droplet motion on the surface can be manipulated (Fig. 11b). After irradiation, surfactant-stabilized brine-in-oil emulsion gradually demulsified via interfacial coalescence of brine droplets under visible light illumination (Fig. 11c). This novel strategy serves as an interesting example towards sunlight-driven oil–water separation technologies in the future.
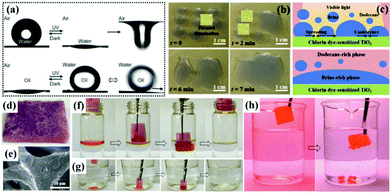 |
| Fig. 11 Photo-induced surface wettability of the aligned ZnO nanorod array-coated mesh films (a). Process of manipulating droplet motion on a dye-sensitized TiO2 surface under light irradiation (b). Schematic illustration of demulsification of brine-oil emulsion via interfacial coalescence of brine droplets on a dye-sensitized TiO2 surface upon visible light illumination (c). Optical image (d) and SEM image (e) of a light-responsive superhydrophobic melamine-formaldehyde sponge. Removal process of toluene floating on water (f) and chloroform sinking at the bottom (g). Process of oil desorption under UV irradiation (h). (a) Reproduced with permission.262 Copyright 2012, Royal Society of Chemistry. (b and c) Reproduced with permission.263 Copyright 2017, Nature Publishing Group. (d–h) Reproduced with permission.265 Copyright 2016, Wiley-VCH. | |
However, most smart membranes with large pore size at the micrometer scale are not applicable for the separation of emulsified oil–water-mixtures. Taking advantages of single-walled carbon nanotube (SWCNT) ultrathin network films with a unique micro/nano structure in thickness and pore size, smart membranes with photo-responsive wettability for oil–water emulsion separation have been widely investigated.98 Jiang et al. reported a facile approach to construct photo-responsive Au nanorod decorated ultrathin SWCNT network membranes with light-modulated pore sizes for switchable ultrafast separation of oil–water nano-emulsions (35
890 L m−2 h−1).99 It is remarkable that the permeation flux can be simply adjusted by light illumination density during the separation process (Table 1). Furthermore, Gao et al. developed an ultrathin film made up of an SWCNT network and TiO2 nanocomposites, which possessed photo-induced superhydrophilic and underwater superoleophobic properties. The film can be used in both surfactant-free emulsion separation and surfactant stabilized oil-in-water emulsion separation with a high flux.264 All of the above as-prepared TiO2-containing membranes showed outstanding self-cleaning performance resulting from the excellent photocatalytic property of TiO2, which has practical significance in recyclability and saving solvents. What's more, in addition to photo-responsive filtration for oil–water separation, a novel strategy based on the oil-absorption and oil-desorption process was reported recently. Zhu et al. prepared a robust and superhydrophobic melamine-formaldehyde sponge by modifying with a light-responsive spiropyran methacrylate derivative via radical copolymerization (Fig. 11d and e).265 Interestingly, the superhydrophobic melamine-formaldehyde sponge exhibited excellent absorption capacity for both light oil and heavy oil (Fig. 11f and g). Meanwhile, the absorbed oil can be effectively desorbed under UV light irradiation (Fig. 11h).
4.1.3 Thermal-responsive wettability.
Similar to photo-responsive wettability, thermal-response has also been utilized to control the surface wettability in recent years.266–268 Poly(N-isopropylacrylamide) (PNIPAAm) is an excellent thermal responsive polymer with a relatively low critical solution temperature of about 32–33 °C. Below the low critical solution temperature, the intermolecular H-bonding between the PNIPAAm chains and water molecules is predominant, which results in an extended brush structure displaying hydrophilicity. Above the low critical solution temperature, intermolecular H-bonding in the PNIPAAm chains leads to a compact and collapsed conformation with hydrophobicity (Fig. 12a).269 Therefore, PNIPAAm and PNIPAAm-containing polymers can be grafted or coated on the rough substrates to realize controllable wettability. For example, Zhou et al. modified metal meshes with poly(2,2,3,4,4,4-hexafluorobutyl methacrylate)-block-poly(N-isopropylacrylamide) through a simple dip-coating method.270 After coating, their average diameter increased from 36 μm (Fig. 12b) to about 39 μm (Fig. 12c). Compared to the pristine mesh, the modified one showed controllable wettability under different temperatures, which can be used for switchable oil–water separation (Fig. 12d). Besides, Jiang et al. reported an underwater thermal-responsive surface that can switch between superoleophobicity and superoleophilicity by grafting heptadecafluorodecyltrimethoxysilane and PNIPAAm.271 Heptadecafluorodecyltrimethoxysilane acted as the oleophilic component in an aqueous environment, while PNIPAAm could conceal or expose the oleophilic component by an inherent thermoresponsive conformational change. Therefore, it is a big breakthrough in the fabrication of underwater temperature-responsive surfaces with switchable underwater wettability and exhibits great potential for special oil–water separation. Moreover, copolymers such as (methyl methacrylate)-block-poly(N-isopropyl-acrylamide),272 poly(N-isopropylacrylamide)-block-polystyrene,273 and poly(N-isopropylacrylamide-co-1-adamantan-1-ylmethyl acrylate)274 have also been used for fabricating smart thermal-responsive surfaces.
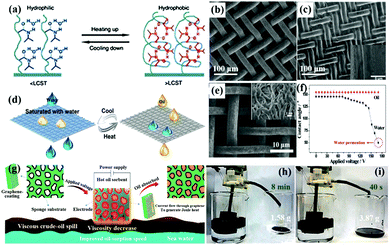 |
| Fig. 12 The effect of temperature on the changes in hydrogen bonding and corresponding conformation of PNIPAAm for surface wettability (a). SEM of an uncoated stainless steel mesh (b) and a coated mesh (c), the inset of (c) is its corresponding magnified image. Schematic illustration of the switchable oil–water separation at different temperatures (d). SEM image of the hierarchical-structured polyaniline mesh (e). The contact angle of water and oil changes by different applied voltages on the mesh (f). Schematic illustration of the Joule-heated graphene modified sponge used to clean up a viscous crude-oil spill (g). Continuous collection of the viscous crude oil from the surface of seawater by in situ pumping through the graphene modified sponge under applied voltages of 0 (h) and 17 V (i), respectively. (a) Reproduced with permission.269 Copyright 2010, Royal Society of Chemistry. (b–d) Reproduced with permission.270 Copyright 2015, American Chemical Society. (e and f) Reproduced with permission.277 Copyright 2016, Wiley-VCH. (g–i) Reproduced with permission.279 Copyright 2017, Nature Publishing Group. | |
4.1.4 Voltage-responsive wettability.
Applying voltage is an electrowetting stimulus to control the surface chemistry, which is the re-arrangement of charges and dipoles between a liquid and a solid, resulting in a reduction in the interfacial energy and an increase in surface wettability. This approach has been successfully applied in surface wettability control without changes in the surface composition and structure.112,252,275,276 In order to achieve the selective permeation of oil or water, the hydrostatic pressure can be overcome by applying an electric field. The conducting materials such as polyaniline, polypyrrole, etc. are widely used to decorate porous materials with potential-induced switchable wettability. For example, Zhang et al. coated a potential-responsive polyaniline coating on a stainless steel mesh through emulsion polymerization (Fig. 12e).277 After modification, different surface wettability to water appeared by changing the applied voltage (Fig. 12f), which could be used for controllable oil–water separation. Besides, Lin et al. modified a 3D copper foam with a voltage-sensitive N-dodecyltrimethoxysilane polymer to realize the reversible wettability between superhydrophobicity and superhydrophilicity.278 Such electricity-induced switchable wettability showed rapid responses and wide-ranging variations, which was considered to be more applicable in controllable water permeation and oil–water emulsion separation. Considering that electricity can generate heat, Yu et al. pioneered a strategy for the clean-up of the viscous crude-oil spill by applying a voltage to the superhydrophobic graphene modified sponge (Fig. 12g, left).279 When the graphene modified sponge contacted the viscous crude oil on a water surface, the oil was absorbed selectively into the pores at a low oil-sorption speed because of the hydrophobic property of graphene. After applying a voltage to the graphene modified sponge, the current flew through the graphene coating and Joule heat was generated, quickly heating up the superhydrophobic graphene modified sponge (Fig. 12g, middle). Then the hot graphene modified sponge can heat up the surrounding crude oil and thus the oil viscosity decreases, which then increased the diffusion of the crude oil into the graphene modified sponge (Fig. 12g, right). After cutting off the applied voltage, the absorbed oil localized in the pores of the graphene modified sponge was still hot and of low viscosity, which also facilitated the subsequent oil-recovery and transportation processes. Compared to the non-heated graphene modified sponge (Fig. 12h), the oil sorption time was reduced by 94.6% and also the oil-recovery speed was increased to a certain extent (Fig. 12i). This novel strategy offers an alternative way for viscous oil remediation, which has contributed to the fabrication technologies of advanced absorbers to deal with the oil spills and oil accidents.
4.1.5 Magnetism-responsive wettability.
Endowing sponges, foams and other 3D self-supporting porous superhydrophobic materials with magnetic properties can greatly facilitate and control the water-remediation process.280–282 In particular, 3D porous superhydrophobic materials with magnetic properties can be remotely driven by a magnet during the adsorption process. In this way, the 3D superhydrophobic materials could be easily guided to absorb oil spills. For example, Calcagnile et al. coated polyurethane foams with superparamagnetic iron oxide nanoparticles and sub-micrometer polytetrafluoroethylene particles.283 The functionalized foams exhibited both excellent water repellency and magnetic responsivity and they could float freely on water due to their ultra-light weight (Fig. 13a and b). Hence, they can absorb the floating oil from the polluted regions by simply moving them around the oil-polluted region using a magnet control. The materials exhibited much high oil adsorption capability, up to hundreds or thousands times their own weight (Fig. 13c). Besides, Du et al. devised 3D magnetic melamine foams with a well-defined rough surface morphology (Fig. 13d and e) that are remotely controllable by magnetism. The materials displayed substantially enhanced oil/water selectivity (Fig. 13f and g).284 Likewise, various 3D porous superhydrophobic materials with magnetism such as CNT sponges, MWCNT/PDMS nanocomposites, and polyurethane/iron oxide foams have also been demonstrated to be effective for controllable water-remediation.285,286 More importantly, 3D porous superhydrophobic materials with magnetism can be simply collected by a magnet after using, avoiding secondary pollution.287–290 For example, Gui et al. successfully synthesized a magnetic carbon nanotube sponge with porous structures consisting of interconnected CNTs with rich Fe encapsulation.291 The magnetic carbon nanotube sponge exhibited high mass adsorption capacity for diesel oil. In addition, they can be guided by magnetic force for water reclamation and desorption by simple heat treatment (Fig. 13h). Though magnetic materials exhibit desirable properties for controllable oil adsorption, the 3D self-supporting porous superhydrophobic materials would undergo several tens or even several hundred times weight gain when a large quantity of oil was adsorbed. This will cause a potential problem in the collection of the used adsorbent by magnetism.
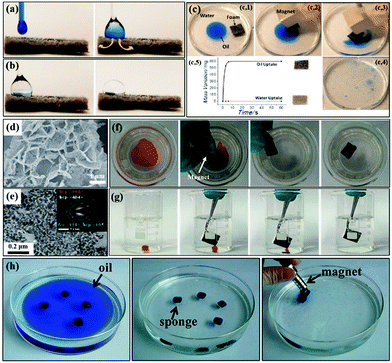 |
| Fig. 13 Mixed oil (a) and water drop (b) are phase separated, and the oil is immediately absorbed while water remains on the superhydrophobic foam surface. Subsequent removal of the oil by the magnetically driven superhydrophobic foam (c1–c4) and photograph showing the variation of the weight of the foam with time (c5). SEM (d) and TEM (e) images of the superhydrophobic magnetic melamine foam. The inset of (d) is the corresponding SAED patterns. On-water (f) and underwater adsorption (g) of organic solvents by the superhydrophobic magnetic melamine foam, respectively. Clean-up process of oil (dyed blue) by the magnetic carbon nanotube sponge using a magnet (h). (a and c) Reproduced with permission.283 Copyright 2012, American Chemical Society. (d–g) Reproduced with permission.284 Copyright 2016, Royal Society of Chemistry. (h) Reproduced with permission.291 Copyright 2013, American Chemical Society. | |
Besides modifying porous materials with a single intelligent function, a combination of binary or ternary intelligent functions has also emerged for oil–water-mixture and emulsion separation with customized configuration. Though some achievements have been made in external stimuli-induced switchable surface wettability such as by pH, light, heat, voltage, etc., they may cause damage to the inherent structures of the substrate and shorten their life-time. What's more, gas, salts, stress, etc. have been used as external stimuli to control surface wettability, but they are rarely reported for oil–water-separation.290–294 Therefore, more attention should be paid to these more environmental-friendly, less-toxic and cost-effective external-responsive technologies for on-demand oil–water separation.
4.2 Janus-featured wettability
In addition to stimuli-responsive wettability, Janus-featured wettability is also widely investigated for both oil–water-mixture and oil–water emulsion separation with high efficiencies.
4.2.1 Asymmetric membranes with heterogeneous wettability.
Asymmetric membranes with opposing wettability (superhydrophobic/superhydrophilic or superoleophilic/superoleophobic) on each side exhibit directional transport behaviors for oil and water. On the one hand, asymmetric membranes with oleophobic/oleophilic wettability on each side have been used to selectively filter oil from oil–water-mixtures due to their combined effect of directional oil transport and prevention of water penetration. In detail, when an oil–water-mixture contacts the oleophobic side, oil will be gradually pulled through to the oleophilic side, while water will be repelled above the surface.110,295 For example, Wang et al. fabricated a superamphiphobic/oleophilic fibrous membrane via a layered electrospinning technique.296 By taking advantage of the combined effect of highly water-repellent and directional oil-transport ability, oil–water-mixtures could be effectively separated. Besides, since the superoleophobic surface is also superhydrophobic, undesirable adhesion and blocking by water is avoided. Thus, asymmetric membranes with oleophobicity/oleophilicity are more efficient and cost-effective in oil–water separation when compared to the ones with homogeneous wettability.
On the other hand, asymmetric membranes with hydrophobicity/hydrophilicity on each side can also be used for oil–water separation. When the oil–water-mixture contacts the hydrophilic side, water will spread on the hydrophilic side but cannot penetrate through the whole membrane, while oil can easily pass through the membrane. Thus, oil–water-mixture separation is realized.297,298 Moreover, inspired by their special property of repelling water by the hydrophobic side, oil–water-emulsion can be separated under the synergistic effects of demulsification, coalescence and rejection of water. Taking oil-in-water emulsion as an example, when the emulsion contacts the hydrophilic side, water will spread on the hydrophilic surface but will be repelled by the superhydrophobic side, while oil droplets will gradually coalesce and penetrate through the membranes. In this regard, Wang et al. reported a novel Janus fabric for separating emulsified oil, which was composed of hydrophilic (PDMAEMA) and superhydrophobic (PDMS) surfaces.108 Though the fabric has large filter pore size, it seems not to be suitable for oil–water emulsion separation. However, the emulsion oil droplets will be demulsified upon contacting the hydrophilic side and then the coalesced oil droplets would penetrate through the fabric, while water could wet the hydrophilic side but is prevented from penetrating through the fabric by the hydrophobic PDMS layer (Fig. 14a and b). The prepared asymmetric membranes exhibited high separation efficiency towards both oil–water-mixture and oil–water-emulsion (Table 1). Besides, by combining membranes with small pore size and asymmetric wettability, both oil-in-water emulsion and water-in-oil emulsion can be separated with ultra-high permeation flux and separation efficiency when compared to the ones with a single function. Hu et al. developed bilayer membranes by depositing a thin layer of polydopamine-coated SWCNTs on their surface.299 By modulating the applied pressure across the membrane, surfactant-stabilized water-in-oil and oil-in-water emulsions can be easily separated. Furthermore, Gu et al. constructed asymmetric hydrophobic/hydrophilic polymer/CNT membranes, by respectively grafting a hydrophobic polymer (PS) and a hydrophilic polymer (PDMAEMA) on different sides of CNT membranes.100 When the superhydrophobic PS side contacted the feed emulsions, only continuous oil could pass through the membrane (Fig. 14c, left). When the hydrophilic (PDMAEMA) side was in contact with the feed emulsions, the membrane only allowed the continuous water phase to pass through (Fig. 14c, right). Therefore, the obtained asymmetric polymer/CNT membrane has been applied in oil–water emulsion separation with good recyclability (Table 1).
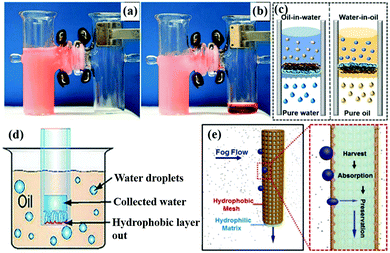 |
| Fig. 14 The emulsified oil–water-mixture before (a) and after separation (b). Schematic illustration of the hydrophobic/hydrophilic membrane for separating oil-in-water emulsions with the PDMAEMA side toward the feed emulsions (c, left) and with the polystyrene side toward the feed emulsions (c, right) for separating water-in-oil emulsions. Schematic illustration of the construction of “Janus trapper” for water droplet collection from oil (d). The schematic diagram (e, left) and the cross-section diagram (e, right) of the continuous fog harvesting process. (a and b) Reproduced with permission.108 Copyright 2016, Wiley-VCH. (c) Reproduced with permission.100 Copyright 2014, American Chemical Society. (d) Reproduced with permission.302 Copyright 2014, Wiley-VCH. (e) Reproduced with permission.303 Copyright 2015, Wiley-VCH. | |
Moreover, asymmetric membranes can be applied in oil/water collection from oil–water-mixtures due to their directional liquid transport property.300,301 For example, Tian et al. developed a Janus membrane by depositing a thin hydrophobic layer on a hydrophilic cotton membrane, and then exposed the hydrophobic side to the dispersed water drops in the oil (Fig. 14d).302 The water droplets permeated the membrane but the oil could not. Similarly, oil droplets could be collected by exposing the hydrophilic side to the dispersed oil droplets. Besides, Cao et al. fabricated a hydrophobic/hydrophilic integrated system by combining a hydrophobic dodecanethiol modified copper mesh and a hydrophilic commercial cotton absorbent.303 When fog contacted the hydrophobic side, it condensed, and then it was absorbed by the hydrophilic side. Besides, the hydrophobic mesh could prevent the surface from being wetted by water, which is undesirable due to water evaporation (Fig. 14e). Thus, it was more efficient and effective to collect water from the atmosphere. This asymmetric system offers an ideal design of smart interfaces for oil–water emulsion separation and oil/water collection.
4.2.2 Patterned surfaces with heterogeneous wettability.
Inspired by certain beetle species in the Namib Desert, which collect water from fog on their backs by way of wettability micro/nano patterns (i.e., hydrophilic wax-free bumps surrounded by a hydrophobic waxy background), a large number of patterned porous materials with hydrophobic–hydrophilic contrast emerged to realize water collection.304–306 For example, Bai et al. successfully fabricated a surface with star-shaped wettability patterns for fog collection.307 On the surfaces with star-shaped wettability patterns, fog droplets can be directionally collected toward more wettable regions. When a water droplet grew to a critical size, it would roll off the surface (Fig. 15a). Besides, Zeng et al. prepared a hydrophilic bumps-superhydrophobic/superoleophilic stainless steel mesh by firstly assembling hydrophilic silica micro particles on the as-cleaned stainless steel mesh surface, followed by further modification with a fluoropolymer/SiO2 nanoparticle solution (Fig. 15b).113 Attributed to the steep surface energy gradient, the superhydrophilic bumps, made up of hydrophilic silica micro particles, were able to capture emulsified water droplets and collect water from the emulsion, while the oil portion permeated the mesh freely. The hydrophilic bumps-superhydrophobic/superoleophilic stainless steel mesh exhibited a high efficiency for water-in-oil emulsion separation of over 99.95% (Table 1), showing great application potential for oil–water emulsion separation and oil purification.
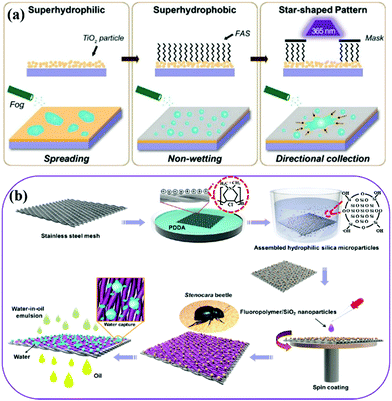 |
| Fig. 15 Schematic illustration of the fabrication process of bioinspired surfaces with star-shaped wettability patterns (a) and preparation of a superhydrophilic bumps-superhydrophobic/superoleophilic stainless steel mesh (b). (a) Reproduced with permission.307 Copyright 2014, Wiley-VCH. (b) Reproduced with permission.113 Copyright 2017, American Chemical Society. | |
5. Conclusions and outlook
In this review, we provide a comprehensive review of the state-of-the-art developments of oil–water separation based on the rational control of materials interface wettability, covering from traditional superhydrophobic–superoleophilic materials, superoleophobic–superhydrophilic materials to superhydrophilic–underwater superoleophobic materials. Among the reported nanofabrication routes, electrospinning, dip/spray-coating, wet chemical reaction and chemical vapor deposition are the main strategies used to construct superwetting materials due to the ease of the process and rational surface control of the nanostructures. The incorporation of certain nano features on the surface, including particles, nanofibers, and nanopores, has clearly improved the surface properties and thus the separation performance. Besides, special wettable porous materials with intelligent functions, such as stimuli-responsive wettability, Janus-featured wettability, etc., have been demonstrated to meet the on-demand oil–water separation and further improve the separation efficiency. All these biomimetic materials with an intelligent interface have exhibited superior advantages for oil–water separation, especially for the more stubborn oil–water-emulsion separation, when compared to traditional oil–water separation materials.
Although great progress has been made in the special wettable materials for oil–water separation, there still exist some crucial issues and challenges. Firstly, in the past few decades, porous materials with special wettability have been demonstrated with high performance in low viscosity solvent or oil uptake. However, crude oil spills always have a high-viscosity and penetrate the membrane with low speed. Therefore, fabrication of advanced functional devices/materials for the rapid and efficient separation of high-viscous oil–water mixtures should be taken into consideration. Secondly, commonly superhydrophobic or superoleophobic fabrics often contain expensive and toxic fluorine-containing groups, which are harmful to human beings and the environment after disposal. Consequently, novel nanofabrication technologies for new materials creation are highly desirable for construction of fluorine-free and environmentally friendly superhydrophobic or superoleophobic fabrics. Thirdly, the materials science and surface chemistry are the two key factors to construct superwetting surfaces for oil/water separation. However, most surface coatings can be easily damaged by external influences such as mechanical force (abrasion, washing) and chemical contamination (strong acid/alkaline etching, harsh weathering), which limits their wide practical applications. Thus, nanoscale fabrications have the advantages of synthesis of robust and durable rough micro/nano architectures with self-healing ability by atom/molecule manipulation. Last but not the least, most of the traditional fabrication strategies for special wettable materials are not suitable for large-scale production, which is undesirable to meet industrial demands. The novel nanofabrication techniques such as direct inkjet printing or 3D printing display promising prospects for mass production to cope with the oil spill accidents and oily wastewater from industries. In summary, compared to the conventional fabrication methods, the nanoscale fabrication strategies exhibit much higher efficiency for oil–water separation and pioneer the future-direction of technologies.
In light of the fruitful progress in this field, we believe that the rational design of artificial superwetting materials at nanoscale will provide us unprecedented chances to overcome the current challenges for oil–water separation. Besides, by continuous efforts put on the fundamental research, large-scale production and industrialization of the special wettable materials will be realized for water-remediation in the near future. In addition, by taking full advantage of intelligent functions, the smart interfacial materials will exhibit higher efficiencies for on-demand oil–water separation and facilitate oil/water collection processes. Furthermore, beyond the application in oily-water remediation, these special wettable materials are also of great interest in other research fields, such as energy storage and conversion, liquid transportation and delivery, bio-engineering, and so on. Overall, a continuous research effort is highly demanded to address the globally serious water pollution arising from oil spills and organic pollutants, and the design of intelligent materials interface proves particularly useful for oil–water separation with significant environmental implications.
Conflicts of interest
There are no conflicts to declare.
Acknowledgements
M. Z. Ge, C. Y. Cao and J. Y. Huang contributed equally to this work. The authors thank the National Natural Science Foundation of China (21501127 and 51502185), Nantong Science and Technology Project (GY12016030), and Jiangsu Advanced Textile Engineering Center Project (Project No. SPPGO[2014]22). We also acknowledge the funds from the Priority Academic Program Development of Jiangsu Higher Education Institutions (PAPD), and Project for Jiangsu Scientific and Technological Innovation Team (2013). M. Z. Ge acknowledges the financial support from the China Scholarship Council (201606920059).
Notes and references
- A. Jernelov, Nature, 2010, 466, 182–183 CrossRef PubMed.
- G. Hayase, K. Kanamori, M. Fukuchi, H. Kaji and K. Nakanishi, Angew. Chem., Int. Ed., 2013, 52, 1986–1989 CrossRef CAS PubMed.
- J. Ge, H. Y. Zhao, H. W. Zhu, J. Huang, L. A. Shi and S. H. Yu, Adv. Mater., 2016, 28, 10459–10490 CrossRef CAS PubMed.
- J. Lahann, Nat. Nanotechnol., 2008, 3, 320–321 CrossRef CAS PubMed.
- K. Li, J. Ju, Z. X. Xue, J. Ma, L. Feng, S. Gao and L. Jiang, Nat. Commun., 2013, 4, 2276 Search PubMed.
- Q. L. Ma, H. F. Cheng, Y. F. Yu, Y. Huang, Q. P. Lu, S. K. Han, J. Z. Chen, R. Wang, A. G. Fane and H. Zhang, Small, 2017, 13, 1700391 CrossRef PubMed.
- Q. L. Ma, Y. F. Yu, M. Sindoro, A. G. Fane, R. Wang and H. Zhang, Adv. Mater., 2017, 29, 1605361 CrossRef PubMed.
- T. Close, G. Tulsyan, C. A. Diaz, S. J. Weinstein and C. Richter, Nat. Nanotechnol., 2015, 10, 418–422 CrossRef CAS PubMed.
- C. P. D. Brussaard, L. Peperzak, S. Beggah, L. Y. Wick, B. Wuerz, J. Weber, J. S. Arey, B. van der Burg, A. Jonas, J. Huisman and J. R. van der Meer, Nat. Commun., 2016, 7, 11206 CrossRef CAS PubMed.
- X. F. Gao, L. P. Xu, Z. X. Xue, L. Feng, J. T. Peng, Y. Q. Wen, S. T. Wang and X. J. Zhang, Adv. Mater., 2014, 26, 1771–1775 CrossRef CAS PubMed.
- W. F. Zhang, N. Liu, Y. Z. Cao, Y. N. Chen, L. X. Xu, X. Lin and L. Feng, Adv. Mater., 2015, 27, 7349–7355 CrossRef CAS PubMed.
- J. Aurell and B. K. Gullett, Environ. Sci. Technol., 2010, 44, 9431–9437 CrossRef CAS PubMed.
- S. W. Gao, X. L. Dong, J. Y. Huang, S. H. Li, Y. W. Li, Z. Chen and Y. K. Lai, Chem. Eng. J., 2018, 333, 621–629 CrossRef CAS.
- H. Liu, J. Huang, Z. Chen, G. Chen, K. Zhang, S. S. Al-Deyab and Y. Lai, Chem. Eng. J., 2017, 330, 26–35 CrossRef CAS.
- K. Huang, G. P. Liu, Y. Y. Lou, Z. Y. Dong, J. Shen and W. Q. Jin, Angew. Chem., Int. Ed., 2014, 53, 6929–6932 CrossRef CAS PubMed.
- J. Li, L. Yan, X. H. Tang, H. Feng, D. C. Hu and F. Zha, Adv. Mater. Interfaces, 2016, 3, 1500770 CrossRef.
- M. Aono and K. Ariga, Adv. Mater., 2016, 28, 989–992 CrossRef CAS PubMed.
- J. K. Yuan, X. G. Liu, O. Akbulut, J. Q. Hu, S. L. Suib, J. Kong and F. Stellacci, Nat. Nanotechnol., 2008, 3, 332–336 CrossRef CAS PubMed.
- C. L. Hao, J. Li, Y. Liu, X. F. Zhou, Y. H. Liu, R. Liu, L. F. Che, W. Z. Zhou, D. Sun, L. Li, L. Xu and Z. K. Wang, Nat. Commun., 2015, 6, 7986 CrossRef CAS PubMed.
- J. V. I. Timonen, M. Latikka, O. Ikkala and R. H. A. Ras, Nat. Commun., 2013, 4, 2398 Search PubMed.
- K. Ariga, Q. M. Ji, W. Nakanishi, J. P. Hill and M. Aono, Mater. Horiz., 2015, 2, 406–413 RSC.
- A. H. Khan, S. Ghosh, B. Pradhan, A. Dalui, L. K. Shrestha, S. Acharya and K. Ariga, Bull. Chem. Soc. Jpn., 2017, 90, 627–648 CrossRef.
- C. F. Wang and S. J. Lin, ACS Appl. Mater. Interfaces, 2013, 5, 8861–8864 CAS.
- K. Jayaramulu, F. Geyer, M. Petr, R. Zboril, D. Vollmer and R. A. Fischer, Adv. Mater., 2017, 29, 1605307 CrossRef PubMed.
- Z. H. Sun, L. F. Wang, P. P. Liu, S. C. Wang, B. Sun, D. Z. Jiang and F. S. Xiao, Adv. Mater., 2006, 18, 1968–1971 CrossRef CAS.
- T. Verho, C. Bower, P. Andrew, S. Franssila, O. Ikkala and R. H. A. Ras, Adv. Mater., 2011, 23, 673–678 CrossRef CAS PubMed.
- G. Godeau, S. Amigoni, T. Darmanin and F. Guittard, Appl. Surf. Sci., 2016, 387, 28–35 CrossRef CAS.
- Y. J. Wang, M. Dugan, B. Urbaniak and L. Li, Langmuir, 2016, 32, 6723–6729 CrossRef PubMed.
- Y. J. Wang and X. Gong, J. Mater. Chem. A, 2017, 5, 3759–3773 CAS.
- Z. X. Xue, S. T. Wang, L. Lin, L. Chen, M. J. Liu, L. Feng and L. Jiang, Adv. Mater., 2011, 23, 4270–4273 CrossRef CAS PubMed.
- J. Yang, Z. Z. Zhang, X. H. Xu, X. T. Zhu, X. H. Men and X. Y. Zhou, J. Mater. Chem., 2012, 22, 2834–2837 RSC.
- T. Chen, M. Duan and S. W. Fang, Ceram. Int., 2016, 42, 8604–8612 CrossRef CAS.
- P. H. Pi, K. Hou, C. L. Zhou, X. F. Wen, S. P. Xu, J. Cheng and S. F. Wang, Mater. Lett., 2016, 182, 68–71 CrossRef CAS.
- F. Zhang, S. J. Gao, Y. Z. Zhu and J. Jin, J. Membr. Sci., 2016, 513, 67–73 CrossRef CAS.
- U. B. Gunatilake and J. Bandara, Chemosphere, 2017, 171, 134–141 CrossRef CAS PubMed.
- Y. Y. Zhang, Z. L. Jiang, J. Y. Huang, L. Y. Lim, W. L. Li, J. Y. Deng, D. G. Gong, Y. X. Tang, Y. K. Lai and Z. Chen, RSC Adv., 2015, 5, 79479–79510 RSC.
- L. R. Shi, K. Chen, R. Du, A. Bachmatiuk, M. H. Rummeli, K. W. Xie, Y. Y. Huang, Y. F. Zhang and Z. F. Liu, J. Am. Chem. Soc., 2016, 138, 6360–6363 CrossRef CAS PubMed.
- Y. K. Takahara, S. Ikeda, S. Ishino, K. Tachi, K. Ikeue, T. Sakata, T. Hasegawa, H. Mori, M. Matsumura and B. Ohtani, J. Am. Chem. Soc., 2005, 127, 6271–6275 CrossRef CAS PubMed.
- B. Su, Y. Tian and L. Jiang, J. Am. Chem. Soc., 2016, 138, 1727–1748 CrossRef CAS PubMed.
- W. D. Liu, X. Y. Liu, S. Y. Xiang, Y. X. Chen, L. P. Fang and B. Yang, Nano Res., 2016, 9, 3141–3151 CrossRef CAS.
- J. L. Song, L. Huang, Y. Lu, X. Liu, X. Deng, X. L. Yang, S. Huang, J. Sun, Z. J. Jin and I. P. Parkin, Sci. Rep., 2016, 6, 31818 CrossRef CAS PubMed.
- A. Airoudj, F. Bally-Le Gall and V. Roucoules, J. Phys. Chem. C, 2016, 120, 29162–29172 CAS.
- R. Elashnikov, P. Slepicka, S. Rimpelova, P. Ulbrich, V. Svorcik and O. Lyutakov, Mater. Sci. Eng., C, 2017, 72, 293–300 CrossRef CAS PubMed.
- K. C. Park, P. Kim, A. Grinthal, N. He, D. Fox, J. C. Weaver and J. Aizenberg, Nature, 2016, 531, 78–82 CrossRef CAS PubMed.
- X. H. Tan, Y. Y. Zhu, T. L. Shi, Z. R. Tang and G. L. Liao, J. Micromech. Microeng., 2016, 26, 115009 CrossRef.
- Y. C. Wang, L. B. Zhang, J. B. Wu, M. N. Hedhili and P. Wang, J. Mater. Chem. A, 2015, 3, 18963–18969 CAS.
- A. Turco, C. Malitesta, G. Barillaro, A. Greco, A. Maffezzoli and E. Mazzotta, J. Mater. Chem. A, 2015, 3, 17685–17696 CAS.
- L. Wu, L. X. Li, B. C. Li, J. P. Zhang and A. Q. Wang, ACS Appl. Mater. Interfaces, 2015, 7, 4936–4946 CAS.
- J. Zhang, M. D. Baro, E. Pellicer and J. Sort, Nanoscale, 2014, 6, 12490–12499 RSC.
- D. A. Christian, A. W. Tian, W. G. Ellenbroek, I. Levental, K. Rajagopal, P. A. Janmey, A. J. Liu, T. Baumgart and D. E. Discher, Nat. Mater., 2009, 8, 843–849 CrossRef CAS PubMed.
- B. D. B. Tiu, S. B. Tiu, A. M. Wen, P. Lam, N. F. Steinmetz and R. C. Advincula, Langmuir, 2016, 32, 6185–6193 CrossRef CAS PubMed.
- P. Xiao, J. C. Gu, J. He, S. Wang, J. W. Zhang, Y. J. Huang, S. W. Kuo and T. Chen, J. Mater. Chem. C, 2016, 4, 9750–9755 RSC.
- I. Kim, D. C. Choi, J. Lee, H. R. Chae, J. H. Jang, C. H. Lee, P. K. Park and Y. J. Won, J. Membr. Sci., 2015, 490, 190–196 CrossRef CAS.
- Y. J. Won, J. Lee, D. C. Choi, H. R. Chae, I. Kim, C. H. Lee and I. C. Kim, Environ. Sci. Technol., 2012, 46, 11021–11027 CrossRef CAS PubMed.
- X. J. Feng and L. Jiang, Adv. Mater., 2006, 18, 3063–3078 CrossRef CAS.
- B. Bhushan and Y. C. Jung, Prog. Mater. Sci., 2011, 56, 1–108 CrossRef CAS.
- A. Lafuma and D. Quere, Nat. Mater., 2003, 2, 457–460 CrossRef CAS PubMed.
- X. M. Li, D. Reinhoudt and M. Crego-Calama, Chem. Soc. Rev., 2007, 36, 1350–1368 RSC.
- T. L. Sun, L. Feng, X. F. Gao and L. Jiang, Acc. Chem. Res., 2005, 38, 644–652 CrossRef CAS PubMed.
- K. S. Liu, X. Yao and L. Jiang, Chem. Soc. Rev., 2010, 39, 3240–3255 RSC.
- K. S. Liu, M. Y. Cao, A. Fujishima and L. Jiang, Chem. Rev., 2014, 114, 10044–10094 CrossRef CAS PubMed.
- S. N. Zhang, J. Y. Huang, Z. Chen and Y. K. Lai, Small, 2017, 13, 1602992 CrossRef PubMed.
- S. Jung, M. K. Tiwari, N. V. Doan and D. Poulikakos, Nat. Commun., 2012, 3, 615 CrossRef PubMed.
- J. Y. Huang, Y. K. Lai, F. Pan, L. Yang, H. Wang, K. Q. Zhang, H. Fuchs and L. F. Chi, Small, 2014, 10, 4865–4873 CrossRef CAS PubMed.
- H. Bai, J. Ju, Y. M. Zheng and L. Jiang, Adv. Mater., 2012, 24, 2786–2791 CrossRef CAS PubMed.
- G. D. Bixler and B. Bhushan, Nanoscale, 2014, 6, 76–96 RSC.
- L. Feng, Y. L. Song, J. Zhai, B. Q. Liu, J. Xu, L. Jiang and D. B. Zhu, Angew. Chem., Int. Ed., 2003, 42, 800–802 CrossRef CAS PubMed.
- X. F. Gao, X. Yan, X. Yao, L. Xu, K. Zhang, J. H. Zhang, B. Yang and L. Jiang, Adv. Mater., 2007, 19, 2213–2217 CrossRef CAS.
- S. Wang and L. Jiang, Adv. Mater., 2007, 19, 3423–3424 CrossRef CAS.
- Q. D. Xie, J. Xu, L. Feng, L. Jiang, W. H. Tang, X. D. Luo and C. C. Han, Adv. Mater., 2004, 16, 302–305 CrossRef CAS.
- E. L. Papadopoulou, M. Barberoglou, V. Zorba, A. Manousaki, A. Pagkozidis, E. Stratakis and C. Fotakis, J. Phys. Chem. C, 2009, 113, 2891–2895 CAS.
- T. L. Sun, G. Y. Qing, B. L. Su and L. Jiang, Chem. Soc. Rev., 2011, 40, 2909–2921 RSC.
- B. Wang, W. X. Liang, Z. G. Guo and W. M. Liu, Chem. Soc. Rev., 2015, 44, 336–361 RSC.
- R. Du, Q. C. Zhao, Z. Zheng, W. P. Hu and J. Zhang, Adv. Energy Mater., 2016, 6, 1600473 CrossRef.
- S. H. Li, J. Y. Huang, Z. Chen, G. Q. Chen and Y. K. Lai, J. Mater. Chem. A, 2017, 5, 31–55 CAS.
- Y. Liu, X. L. Li, J. F. Jin, J. A. Liu, Y. Y. Yan, Z. W. Han and L. Q. Ren, Appl. Surf. Sci., 2017, 400, 498–505 CrossRef CAS.
- U. Zulfiqar, M. Awais, S. Z. Hussain, I. Hussain, S. W. Husain and T. Subhani, Mater. Lett., 2017, 192, 56–59 CrossRef CAS.
- Y. K. Lai, X. F. Gao, H. F. Zhuang, J. Y. Huang, C. J. Lin and L. Jiang, Adv. Mater., 2009, 21, 3799–3803 CrossRef CAS.
- W. F. Zhang, N. Liu, Y. Z. Cao, X. Lin, Y. N. Liu and L. Feng, Adv. Mater. Interfaces, 2017, 4, 1700029 Search PubMed.
- L. P. Wen, Y. Tian and L. Jiang, Angew. Chem., Int. Ed., 2015, 54, 3387–3399 CrossRef CAS PubMed.
- Y. Z. Zhu, W. Xie, F. Zhang, T. L. Xing and J. Jin, ACS Appl. Mater. Interfaces, 2017, 9, 9603–9613 CAS.
- Q. D. Zhang, Y. Z. Cao, N. Liu, W. F. Zhang, Y. N. Chen, X. Lin, L. Tao, Y. Wei and L. Feng, Adv. Mater. Interfaces, 2016, 3, 1600291 CrossRef.
- W. Zhang, N. Liu, Y. Cao, X. Lin, Y. Liu and L. Feng, Adv. Mater. Interfaces, 2017, 4, 1600029 CrossRef.
- Y. B. Peng and Z. G. Guo, J. Mater. Chem. A, 2016, 4, 15749–15770 CAS.
- R. Zolfaghari, A. Fakhru'l-Razi, L. C. Abdullah, S. Elnashaie and A. Pendashteh, Sep. Purif. Technol., 2016, 170, 377–407 CrossRef CAS.
- W. B. Zhang, Y. Z. Zhu, X. Liu, D. Wang, J. Y. Li, L. Jiang and J. Jin, Angew. Chem., Int. Ed., 2014, 53, 856–860 CrossRef CAS PubMed.
- W. B. Zhang, Z. Shi, F. Zhang, X. Liu, J. Jin and L. Jiang, Adv. Mater., 2013, 25, 2071–2076 CrossRef CAS PubMed.
- M. M. Tao, L. X. Xue, F. Liu and L. Jiang, Adv. Mater., 2014, 26, 2943–2948 CrossRef CAS PubMed.
- R. H. Lv, M. Yin, W. Z. Zheng, B. Na, B. Wang and H. S. Liu, J. Appl. Polym. Sci., 2017, 134, 44980 Search PubMed.
- X. Y. Yuan, W. Li, Z. G. Zhu, N. Han and X. X. Zhang, Colloids Surf., A, 2017, 516, 305–316 CrossRef CAS.
- Z. X. Wang, X. Jiang, X. Q. Cheng, C. H. Lau and L. Shao, ACS Appl. Mater. Interfaces, 2015, 7, 9534–9545 CAS.
- Z. X. Wang, C. H. Lau, N. Q. Zhang, Y. P. Bai and L. Shao, J. Mater. Chem. A, 2015, 3, 2650–2657 CAS.
- Y. Z. Zhu, F. Zhang, D. Wang, X. F. Pei, W. B. Zhang and J. Jin, J. Mater. Chem. A, 2013, 1, 5758–5765 CAS.
- R. Ou, J. Wei, L. Jiang, G. P. Simon and H. Wang, Environ. Sci. Technol., 2016, 50, 906–914 CrossRef CAS PubMed.
- J. L. Ge, J. C. Zhang, F. Wang, Z. L. Li, J. Y. Yu and B. Ding, J. Mater. Chem. A, 2017, 5, 497–502 CAS.
- D. D. Xu, X. T. Zheng and R. Xiao, RSC Adv., 2017, 7, 7108–7115 RSC.
- J. Saadati and M. Pakizeh, J. Taiwan Inst. Chem. Eng., 2017, 71, 265–276 CrossRef CAS.
- Z. Shi, W. B. Zhang, F. Zhang, X. Liu, D. Wang, J. Jin and L. Jiang, Adv. Mater., 2013, 25, 2422–2427 CrossRef CAS PubMed.
- L. Hu, S. J. Gao, X. G. Ding, D. Wang, J. Jiang, J. Jin and L. Jiang, ACS Nano, 2015, 9, 4835–4842 CrossRef CAS PubMed.
- J. C. Gu, P. Xiao, J. Chen, J. W. Zhang, Y. J. Huang and T. Chen, ACS Appl. Mater. Interfaces, 2014, 6, 16204–16209 CAS.
- W. F. Zhang, N. Liu, Y. Z. Cao, Y. N. Chen, Q. D. Zhang, X. Lin, R. X. Qu, H. F. Li and L. Feng, ACS Appl. Mater. Interfaces, 2016, 8, 21816–21823 CAS.
- X. W. Chen, L. Hong, Y. F. Xu and Z. W. Ong, ACS Appl. Mater. Interfaces, 2012, 4, 1909–1918 CAS.
- H. C. Yang, J. K. Pi, K. J. Liao, H. Huang, Q. Y. Wu, X. J. Huang and Z. K. Xu, ACS Appl. Mater. Interfaces, 2014, 6, 12566–12572 CAS.
- J. P. Chaudhary, N. Vadodariya, S. K. Nataraj and R. Meena, ACS Appl. Mater. Interfaces, 2015, 7, 24957–24962 CAS.
- P. C. Chen and Z. K. Xu, Sci. Rep., 2013, 3, 2776 CrossRef PubMed.
- Z. Dang, L. Liu, Y. Li, Y. Xiang and G. Guo, ACS Appl. Mater. Interfaces, 2016, 8, 31281 CAS.
- J. B. Fan, Y. Y. Song, S. T. Wang, J. X. Meng, G. Yang, X. L. Guo, L. Feng and L. Jiang, Adv. Funct. Mater., 2015, 25, 5368–5375 CrossRef CAS.
- Z. J. Wang, Y. Wang and G. J. Liu, Angew. Chem., Int. Ed., 2016, 55, 1291–1294 CrossRef CAS PubMed.
- Z. J. Wang, G. J. Liu and S. S. Huang, Angew. Chem., Int. Ed., 2016, 55, 14610–14613 CrossRef CAS PubMed.
- M. Liu, Y. Hou, J. Li and Z. Guo, Langmuir, 2017, 33, 3702–3710 CrossRef CAS PubMed.
- B. Song and Q. Xu, Langmuir, 2016, 32, 9960–9966 CrossRef CAS PubMed.
- G. Kwon, A. K. Kota, Y. X. Li, A. Sohani, J. M. Mabry and A. Tuteja, Adv. Mater., 2012, 24, 3666–3671 CrossRef CAS PubMed.
- X. Zeng, L. Qian, X. Yuan, C. Zhou, Z. Li, J. Cheng, S. Xu, S. Wang, P. Pi and X. Wen, ACS Nano, 2017, 11, 760–769 CrossRef CAS PubMed.
- Y. Cao, N. Liu, W. Zhang, L. Feng and Y. Wei, ACS Appl. Mater. Interfaces, 2016, 8, 3333–3339 CAS.
- F. Zhang, W. B. Zhang, Z. Shi, D. Wang, J. Jin and L. Jiang, Adv. Mater., 2013, 25, 4192–4198 CrossRef CAS PubMed.
- Z. J. Cheng, J. W. Wang, H. Lai, Y. Du, R. Hou, C. Li, N. Q. Zhang and K. N. Sun, Langmuir, 2015, 31, 1393–1399 CrossRef CAS PubMed.
- Z. Cheng, C. Li, H. Lai, Y. Du, H. Liu, M. Liu, L. Jin, C. Zhang, N. Zhang and K. Sun, RSC Adv., 2016, 6, 72317–72325 RSC.
- J. Yun, F. A. Khan and S. Baik, ACS Appl. Mater. Interfaces, 2017, 9, 16694–16703 CAS.
- C. F. Wang and L. T. Chen, Langmuir, 2017, 33, 1969–1973 CrossRef CAS PubMed.
- Y. Si, Q. X. Fu, X. Q. Wang, J. Zhu, J. Y. Yu, G. Sun and B. Ding, ACS Nano, 2015, 9, 3791–3799 CrossRef CAS PubMed.
- Z. D. Wang, C. M. Xiao, Z. J. Wu, Y. T. Wang, X. Du, W. Kong, D. H. Pan, G. Q. Guan and X. G. Hao, J. Mater. Chem. A, 2017, 5, 5895–5904 CAS.
- Z. Y. Luo, S. S. Lyu, Y. Q. Wang and D. C. Mo, Ind. Eng. Chem. Res., 2017, 56, 699–707 CrossRef CAS.
- J. C. Gu, P. Xiao, P. Chen, L. Zhang, H. L. Wang, L. W. Dai, L. P. Song, Y. J. Huang, J. W. Zhang and T. Chen, ACS Appl. Mater. Interfaces, 2017, 9, 5968–5973 CAS.
- G. Q. Li, H. Fan, F. F. Ren, C. Zhou, Z. Zhang, B. Xu, S. Z. Wu, Y. L. Hu, W. L. Zhu, J. W. Li, Y. S. Zeng, X. H. Li, J. R. Chua and D. Wu, J. Mater. Chem. A, 2016, 4, 18832–18840 CAS.
- S. Gao, J. Huang, S. Li, H. Liu, F. Li, Y. Chen, G. Chen and Y. Lai, Mater. Des., 2017, 128, 1–8 CrossRef CAS.
- S. N. Zhang, J. Y. Huang, Y. Cheng, H. Yang, Z. Chen and Y. K. Lai, Small, 2017, 13, 1701867 CrossRef PubMed.
- W. J. Ma, Q. L. Zhang, D. W. Hua, R. H. Xiong, J. T. Zhao, W. D. Rao, S. L. Huang, X. X. Zhan, F. Chen and C. B. Huang, RSC Adv., 2016, 6, 12868–12884 RSC.
- H. T. Zhu, S. S. Qiu, W. Jiang, D. X. Wu and C. Y. Zhang, Environ. Sci. Technol., 2011, 45, 4527–4531 CrossRef CAS PubMed.
- J. Y. Lin, B. Ding, J. M. Yang, J. Y. Yu and G. Sun, Nanoscale, 2012, 4, 176–182 RSC.
- Z. P. Zhou and X. F. Wu, Mater. Lett., 2015, 160, 423–427 CrossRef CAS.
- V. A. Ganesh, A. S. Nair, H. K. Raut, T. T. Y. Tan, C. B. He, S. Ramakrishna and J. W. Xu, J. Mater. Chem., 2012, 22, 18479–18485 RSC.
- L. Jiang, Y. Zhao and J. Zhai, Angew. Chem., Int. Ed., 2004, 43, 4338–4341 CrossRef CAS PubMed.
- C. L. Zhang, P. Li and B. Cao, Ind. Eng. Chem. Res., 2015, 54, 8772–8781 CrossRef CAS.
- M. H. Tai, P. Gao, B. Y. L. Tan, D. D. Sun and J. O. Leckie, ACS Appl. Mater. Interfaces, 2014, 6, 9393–9401 CAS.
- S. Jiang, L. P. Lv, K. Landfester and D. Crespy, Acc. Chem. Res., 2016, 49, 816–823 CrossRef CAS PubMed.
- Z. J. Liu, H. Y. Wang, E. Q. Wang, X. G. Zhang, R. X. Yuan and Y. J. Zhu, Polymer, 2016, 82, 105–113 CrossRef CAS.
- R. Menini and M. Farzaneh, Polym. Int., 2008, 57, 77–84 CrossRef CAS.
- M. L. Ma, M. Gupta, Z. Li, L. Zhai, K. K. Gleason, R. E. Cohen, M. F. Rubner and G. C. Rutledge, Adv. Mater., 2007, 19, 255–259 CrossRef CAS.
- X. Li, M. Wang, C. Wang, C. Cheng and X. F. Wang, ACS Appl. Mater. Interfaces, 2014, 6, 15272–15282 CAS.
- M. L. Ma, Y. Mao, M. Gupta, K. K. Gleason and G. C. Rutledge, Macromolecules, 2005, 38, 9742–9748 CrossRef CAS.
- L. Wu, J. P. Zhang, B. C. Li and A. Q. Wang, J. Colloid Interface Sci., 2014, 413, 112–117 CrossRef CAS PubMed.
- Q. Wang, M. G. Yu, G. X. Chen, Q. F. Chen and J. F. Tian, J. Mater. Sci., 2017, 52, 2549–2559 CrossRef CAS.
- H. Zhou, H. X. Wang, H. T. Niu, A. Gestos, X. G. Wang and T. Lin, Adv. Mater., 2012, 24, 2409–2412 CrossRef CAS PubMed.
- Z. Y. Deng, W. Wang, L. H. Mao, C. F. Wang and S. Chen, J. Mater. Chem. A, 2014, 2, 4178–4184 CAS.
- X. Chen, L. L. Zhang, H. Li, J. H. Sun, H. Y. Cai and D. F. Cui, Sens. Actuators, A, 2013, 193, 54–58 CrossRef CAS.
- S. Sokolov, E. Ortel, J. Radnik and R. Kraehnert, Thin Solid Films, 2009, 518, 27–35 CrossRef CAS.
- J. Song, S. Huang, Y. Lu, X. Bu, J. E. Mates, A. Ghosh, R. Ganguly, C. J. Carmalt, I. P. Parkin, W. Xu and C. M. Megaridis, ACS Appl. Mater. Interfaces, 2014, 6, 19858–19865 CAS.
- X. J. Su, H. Q. Li, X. J. Lai, L. Zhang, T. Liang, Y. C. Feng and X. R. Zeng, ACS Appl. Mater. Interfaces, 2017, 9, 3131–3141 CAS.
- X. J. Liu, L. Ge, W. Li, X. Z. Wang and F. Li, ACS Appl. Mater. Interfaces, 2015, 7, 791–800 CAS.
- Z. H. Wen, Q. Wang, Q. Zhang and J. H. Li, Adv. Funct. Mater., 2007, 17, 2772–2778 CrossRef CAS.
- C. H. Xue, P. T. Ji, P. Zhang, Y. R. Li and S. T. Jia, Appl. Surf. Sci., 2013, 284, 464–471 CrossRef CAS.
- Q. Zhu and Q. M. Pan, ACS Nano, 2014, 8, 1402–1409 CrossRef CAS PubMed.
- Y. Lu, S. Sathasivam, J. Song, F. Chen, W. Xu, C. J. Carmalt and I. P. Parkin, J. Mater. Chem. A, 2014, 2, 11628–11634 CAS.
- Z. J. Cheng, C. Li, H. Lai, Y. Du, H. W. Liu, M. Liu, K. N. Sun, L. G. Jin, N. Q. Zhang and L. Jiang, Adv. Mater. Interfaces, 2016, 3, 1600370 CrossRef.
- C. Y. Cao, M. Z. Ge, J. Y. Huang, S. H. Li, S. Deng, S. N. Zhang, Z. Chen, K. Q. Zhang, S. S. Al-Deyab and Y. K. Lai, J. Mater. Chem. A, 2016, 4, 12179–12187 CAS.
- J. Li, L. Yan, H. Li, J. Li, F. Zha and Z. Lei, RSC Adv., 2015, 5, 53802–53808 RSC.
- Y. Lu, S. Sathasivam, J. L. Song, C. R. Crick, C. J. Carmalt and I. P. Parkin, Science, 2015, 347, 1132–1135 CrossRef CAS PubMed.
- L. Feng, Z. Y. Zhang, Z. H. Mai, Y. M. Ma, B. Q. Liu, L. Jiang and D. B. Zhu, Angew. Chem., Int. Ed., 2004, 43, 2012–2014 CrossRef CAS PubMed.
- J. P. Zhang, B. C. Li, L. Wu and A. Q. Wang, Chem. Commun., 2013, 49, 11509–11511 RSC.
- J. W. Krumpfer and T. J. McCarthy, J. Am. Chem. Soc., 2011, 133, 5764–5766 CrossRef CAS PubMed.
- D. T. Ge, L. L. Yang, G. X. Wu and S. Yang, Chem. Commun., 2014, 50, 2469–2472 RSC.
- F. Shi, X. X. Chen, L. Y. Wang, J. Niu, J. H. Yu, Z. Q. Wang and X. Zhang, Chem. Mater., 2005, 17, 6177–6180 CrossRef CAS.
- L. P. Yang, A. Raza, Y. Si, X. Mao, Y. W. Shang, B. Ding, J. Y. Yu and S. S. Al-Deyab, Nanoscale, 2012, 4, 6581–6587 RSC.
- S. H. Li, J. Y. Huang, M. Z. Ge, S. W. Li, T. L. Xing, G. Q. Chen, Y. Q. Liu, K. Q. Zhang, S. S. Al-Deyab and Y. K. Lai, Mater. Des., 2015, 85, 815–822 CrossRef CAS.
- N. Zhao, F. Shi, Z. Q. Wang and X. Zhang, Langmuir, 2005, 21, 4713–4716 CrossRef CAS PubMed.
- X. Q. Chen, Y. Y. Liu, H. F. Lu, H. R. Yang, X. A. Zhou and J. H. Xin, Cellulose, 2010, 17, 1103–1113 CrossRef CAS.
- Z. G. Guo, F. B. Han, L. B. Wang and W. M. Liu, Thin Solid Films, 2007, 515, 7190–7194 CrossRef CAS.
- B. Wang, J. Li, G. Wang, W. Liang, Y. Zhang, L. Shi, Z. Guo and W. Liu, ACS Appl. Mater. Interfaces, 2013, 5, 1827–1839 CAS.
- M. Z. Ge, C. Y. Cao, J. Y. Huang, S. H. Li, Z. Chen, K. Q. Zhang, S. S. Al-Deyab and Y. K. Lai, J. Mater. Chem. A, 2016, 4, 6772–6801 CAS.
- S. H. Li, J. Y. Huang, M. Z. Ge, C. Y. Cao, S. Deng, S. N. Zhang, G. Q. Chen, K. Q. Zhang, S. S. Al-Deyab and Y. K. Lai, Adv. Mater. Interfaces, 2015, 2, 1500220 CrossRef.
- S. N. Zhang, J. Y. Huang, Y. X. Tang, S. H. Li, M. Z. Ge, Z. Chen, K. Q. Zhang and Y. K. Lai, Small, 2017, 13, 1600687 CrossRef PubMed.
- C. F. Wang, F. S. Tzeng, H. G. Chen and C. J. Chang, Langmuir, 2012, 28, 10015–10019 CrossRef CAS PubMed.
- J. Y. Huang, S. H. Li, M. Z. Ge, L. N. Wang, T. L. Xing, G. Q. Chen, X. F. Liu, S. S. Al-Deyab, K. Q. Zhang, T. Chen and Y. K. Lai, J. Mater. Chem. A, 2015, 3, 2825–2832 CAS.
- X. M. Tang, Y. Si, J. L. Ge, B. Ding, L. F. Liu, G. Zheng, W. J. Luo and J. Y. Yu, Nanoscale, 2013, 5, 11657–11664 RSC.
- D. Nystrom, J. Lindqvist, E. Ostmark, P. Antoni, A. Carlmark, A. Hult and E. Malmstrom, ACS Appl. Mater. Interfaces, 2009, 1, 816–823 Search PubMed.
- X. L. Zhan, Y. D. Yan, Q. H. Zhang and F. Q. Chen, J. Mater. Chem. A, 2014, 2, 9390–9399 CAS.
- S. W. Li, T. L. Xing, Z. X. Li and G. Q. Chen, Appl. Surf. Sci., 2013, 268, 92–97 CrossRef CAS.
- C. H. Xue, X. J. Guo, J. Z. Ma and S. T. Jia, ACS Appl. Mater. Interfaces, 2015, 7, 8251–8259 CAS.
- J. D. Wu, Y. L. Jiang, D. J. Jiang, J. He, G. Q. Cai and J. P. Wang, Mater. Lett., 2015, 160, 384–387 CrossRef CAS.
- S. T. Wang, Y. L. Song and L. Jiang, Nanotechnology, 2007, 18, 015103 CrossRef.
- C. R. Crick and I. P. Parkin, J. Mater. Chem., 2011, 21, 14712–14716 RSC.
- X. J. Liu, Y. Xu, Z. Chen, K. Y. Ben and Z. S. Guan, RSC Adv., 2015, 5, 1315–1318 RSC.
- M. Thieme, F. Streller, F. Simon, R. Frenzel and A. J. White, Appl. Surf. Sci., 2013, 283, 1041–1050 CrossRef CAS.
- J. P. Zhang and S. Seeger, Adv. Funct. Mater., 2011, 21, 4699–4704 CrossRef CAS.
- C. R. Crick, J. A. Gibbins and I. P. Parkin, J. Mater. Chem. A, 2013, 1, 5943–5948 CAS.
- X. Zhou, Z. Zhang, X. Xu, F. Guo, X. Zhu, X. Men and B. Ge, ACS Appl. Mater. Interfaces, 2013, 5, 7208–7214 CAS.
- A. Hozumi and O. Takai, Thin Solid Films, 1997, 303, 222–225 CrossRef CAS.
- T. Ishizaki, J. Hieda, N. Saito, N. Saito and O. Takai, Electrochim. Acta, 2010, 55, 7094–7101 CrossRef CAS.
- B. Cortese, D. Caschera, F. Federici, G. M. Ingo and G. Gigli, J. Mater. Chem. A, 2014, 2, 6781–6789 CAS.
- M. C. Wu, N. An, Y. Li and J. Q. Sun, Langmuir, 2016, 32, 12361–12369 CrossRef CAS PubMed.
- X. Y. Li, D. Hu, L. X. Cao and C. F. Yang, RSC Adv., 2015, 5, 71345–71354 RSC.
- P. Li, H. Li, J. Yang and Y. H. Meng, BioResources, 2016, 11, 6552–6565 CAS.
- S. Piltan, J. Seyfi, I. Hejazi, S. M. Davachi and H. A. Khonakdar, Cellulose, 2016, 23, 3913–3924 CrossRef CAS.
- N. Karthik and M. G. Sethuraman, New J. Chem., 2015, 39, 3337–3340 RSC.
- L. B. Zhang, H. Chen, J. Q. Sun and J. C. Shen, Chem. Mater., 2007, 19, 948–953 CrossRef CAS.
- Y. Zhao, Z. G. Xu, X. G. Wang and T. Lin, Langmuir, 2012, 28, 6328–6335 CrossRef CAS PubMed.
- J. Li, R. M. Kang, X. H. Tang, H. D. She, Y. X. Yang and F. Zha, Nanoscale, 2016, 8, 7638–7645 RSC.
- J. Li, L. Yan, Y. Zhao, F. Zha, Q. Wang and Z. Lei, Phys. Chem. Chem. Phys., 2015, 17, 6451–6457 RSC.
- Y. Hou, Z. Wang, J. Guo, H. Shen, H. Zhang, N. Zhao, Y. P. Zhao, L. Chen, S. M. Liang, Y. Jin and J. Xu, J. Mater. Chem. A, 2015, 3, 23252–23260 CAS.
- J. Zimmermann, F. A. Reifler, G. Fortunato, L. C. Gerhardt and S. Seeger, Adv. Funct. Mater., 2008, 18, 3662–3669 CrossRef CAS.
- Q. Zhu, Y. Chu, Z. K. Wang, N. Chen, L. Lin, F. T. Liu and Q. M. Pan, J. Mater. Chem. A, 2013, 1, 5386–5393 CAS.
- Q. Zhu, Q. M. Pan and F. T. Liu, J. Phys. Chem. C, 2011, 115, 17464–17470 CAS.
- Q. L. Ma, H. F. Cheng, A. G. Fane, R. Wang and H. Zhang, Small, 2016, 12, 2186–2202 CrossRef CAS PubMed.
- X. M. Chen, J. A. Weibel and S. V. Garimella, Ind. Eng. Chem. Res., 2016, 55, 3596–3602 CrossRef CAS.
- S. Zhou, G. Hao, X. Zhou, W. Jiang, T. Wang, N. Zhang and L. Yu, Chem. Eng. J., 2016, 302, 155–162 CrossRef CAS.
- S. L. Chen, G. H. He, H. Hu, S. Q. Jin, Y. Zhou, Y. Y. He, S. J. He, F. Zhao and H. Q. Hou, Energy Environ. Sci., 2013, 6, 2435–2439 CAS.
- C. Wu, X. Huang, X. Wu, R. Qian and P. Jiang, Adv. Mater., 2013, 25, 5658–5662 CrossRef CAS PubMed.
- S. Wan, H. C. Bi and L. T. Sun, Nanotechnol. Rev., 2016, 5, 3–22 CAS.
- K. S. Novoselov, A. K. Geim, S. V. Morozov, D. Jiang, Y. Zhang, S. V. Dubonos, I. V. Grigorieva and A. A. Firsov, Science, 2004, 306, 666–669 CrossRef CAS PubMed.
- C. L. He, J. Y. Huang, S. H. Li, K. Meng, L. Y. Zhang, Z. Chen and Y. K. Lai, ACS Sustainable Chem. Eng., 2018, 6, 927–936 CrossRef CAS.
- C. L. Long, X. Chen, L. L. Jiang, L. J. Zhi and Z. J. Fan, Nano Energy, 2015, 12, 141–151 CrossRef CAS.
- X. Dong, J. Chen, Y. Ma, J. Wang, M. B. Chan-Park, X. Liu, L. Wang, W. Huang and P. Chen, Chem. Commun., 2012, 48, 10660–10662 RSC.
- H. W. Liang, Q. F. Guan, L. F. Chen, Z. Zhu, W. J. Zhang and S. H. Yu, Angew. Chem.,
Int. Ed., 2012, 51, 5101–5105 CrossRef CAS PubMed.
- W. Luo, B. Wang, C. G. Heron, M. J. Allen, J. Morre, C. S. Maier, W. F. Stickle and X. L. Ji, Nano Lett., 2014, 14, 2225–2229 CrossRef CAS PubMed.
- L. Borchardt, M. Oschatz and S. Kaskel, Mater. Horiz., 2014, 1, 157–168 RSC.
- H. Bi, Z. Yin, X. Cao, X. Xie, C. Tan, X. Huang, B. Chen, F. Chen, Q. Yang, X. Bu, X. Lu, L. Sun and H. Zhang, Adv. Mater., 2013, 25, 5916–5921 CrossRef CAS PubMed.
- Z. Y. Wu, C. Li, H. W. Liang, J. F. Chen and S. H. Yu, Angew. Chem., Int. Ed., 2013, 52, 2925–2929 CrossRef CAS PubMed.
- Z. Y. Wu, C. Li, H. W. Liang, Y. N. Zhang, X. Wang, J. F. Chen and S. H. Yu, Sci. Rep., 2014, 4, 4079 CrossRef PubMed.
- P. Hao, Z. H. Zhao, J. Tian, H. D. Li, Y. H. Sang, G. W. Yu, H. Q. Cai, H. Liu, C. P. Wong and A. Umar, Nanoscale, 2014, 6, 12120–12129 RSC.
- X. L. Wu, T. Wen, H. L. Guo, S. B. Yang, X. K. Wang and A. W. Xu, ACS Nano, 2013, 7, 3589–3597 CrossRef CAS PubMed.
- B. Chen, Q. L. Ma, C. L. Tan, T. T. Lim, L. Huang and H. Zhang, Small, 2015, 11, 3319–3336 CrossRef CAS PubMed.
- Y. R. Lin, G. J. Ehlert, C. Bukowsky and H. A. Sodano, ACS Appl. Mater. Interfaces, 2011, 3, 2200–2203 CAS.
- H. Sun, Z. Xu and C. Gao, Adv. Mater., 2013, 25, 2554–2560 CrossRef CAS PubMed.
- Y. He, Y. Liu, T. Wu, J. Ma, X. Wang, Q. Gong, W. Kong, F. Xing, Y. Liu and J. Gao, J. Hazard. Mater., 2013, 260, 796–805 CrossRef CAS PubMed.
- J. Li, J. Li, H. Meng, S. Xie, B. Zhang, L. Li, H. Ma, J. Zhang and M. Yu, J. Mater. Chem. A, 2014, 2, 2934–2941 CAS.
- T. Wu, M. Chen, L. Zhang, X. Xu, Y. Liu, J. Yan, W. Wang and J. Gao, J. Mater. Chem. A, 2013, 1, 7612–7621 CAS.
- C. Ban, Z. Wu, D. T. Gillaspie, L. Chen, Y. Yan, J. L. Blackburn and A. C. Dillon, Adv. Mater., 2010, 22, E145–E149 CrossRef CAS PubMed.
- H. P. Cong, X. C. Ren, P. Wang and S. H. Yu, ACS Nano, 2012, 6, 2693–2703 CrossRef CAS PubMed.
- H. C. Bi, X. Xie, K. B. Yin, Y. L. Zhou, S. Wan, L. B. He, F. Xu, F. Banhart, L. T. Sun and R. S. Ruoff, Adv. Funct. Mater., 2012, 22, 4421–4425 CrossRef CAS.
- Y. Zhao, C. G. Hu, Y. Hu, H. H. Cheng, G. Q. Shi and L. T. Qu, Angew. Chem., Int. Ed., 2012, 51, 11371–11375 CrossRef CAS PubMed.
- Z. G. Xu, Y. Zhao, H. X. Wang, X. G. Wang and T. Lin, Angew. Chem., Int. Ed., 2015, 54, 4527–4530 CrossRef CAS PubMed.
- J. Yang, H. J. Song, X. H. Yan, H. Tang and C. S. Li, Cellulose, 2014, 21, 1851–1857 CrossRef CAS.
- A. K. Kota, G. Kwon, W. Choi, J. M. Mabry and A. Tuteja, Nat. Commun., 2012, 3, 1025 CrossRef PubMed.
- X. L. Liu, J. Zhou, Z. X. Xue, J. Gao, J. X. Meng, S. T. Wang and L. Jiang, Adv. Mater., 2012, 24, 3401–3405 CrossRef CAS PubMed.
- T. Yuan, J. Q. Meng, T. Y. Hao, Z. H. Wang and Y. F. Zhang, ACS Appl. Mater. Interfaces, 2015, 7, 14896–14904 CAS.
- Y. X. Tang, Y. Y. Zhang, X. H. Rui, D. P. Qi, Y. F. Luo, W. R. Leow, S. Chen, J. Guo, J. Q. Wei, W. L. Li, J. Y. Deng, Y. K. Lai, B. Ma and X. D. Chen, Adv. Mater., 2016, 28, 1567–1576 CrossRef CAS PubMed.
- J. J. Mao, M. Z. Ge, J. Y. Huang, Y. K. Lai, C. J. Lin, K. Q. Zhang, K. Meng and Y. X. Tang, J. Mater. Chem. A, 2017, 5, 11873–11881 CAS.
- Y. Dong, J. Li, L. Shi, X. Wang, Z. Guo and W. Liu, Chem. Commun., 2014, 50, 5586–5589 RSC.
- S. J. Gao, J. C. Sun, P. P. Liu, F. Zhang, W. B. Zhang, S. L. Yuan, J. Y. Li and J. Jin, Adv. Mater., 2016, 28, 5307–5314 CrossRef CAS PubMed.
- C. L. Zhou, J. Cheng, K. Hou, A. Zhao, P. H. Pi, X. F. Wen and S. P. Xu, Chem. Eng. J., 2016, 301, 249–256 CrossRef CAS.
- J. Li, D. M. Li, W. J. Li, H. Y. Li, H. D. She and F. Zha, Sep. Purif. Technol., 2016, 168, 209–214 CrossRef CAS.
- N. Liu, Y. N. Chen, F. Lu, Y. Z. Cao, Z. X. Xue, K. Li, L. Feng and Y. Wei, ChemPhysChem, 2013, 14, 3489–3494 CrossRef CAS PubMed.
- J. Li, L. Yan, H. Li, W. Li, F. Zha and Z. Lei, J. Mater. Chem. A, 2015, 3, 14696–14702 CAS.
- Q. Wen, J. C. Di, L. Jiang, J. H. Yu and R. R. Xua, Chem. Sci., 2013, 4, 591–595 RSC.
- L. B. Zhang, Y. J. Zhong, D. Cha and P. Wang, Sci. Rep., 2013, 3, 2326 CrossRef PubMed.
- X. X. Chen, J. Gao, B. Song, M. Smet and X. Zhang, Langmuir, 2010, 26, 104–108 CrossRef CAS PubMed.
- Q. L. Zhang, F. Xia, T. L. Sun, W. L. Song, T. Y. Zhao, M. C. Liu and L. Jiang, Chem. Commun., 2008, 1199–1201 RSC.
- X. Huang, Y. J. Sun and S. Soh, Adv. Mater., 2015, 27, 4062–4068 CrossRef CAS PubMed.
- S. Taleb, T. Darmanin and F. Guittard, ACS Appl. Mater. Interfaces, 2014, 6, 7953–7960 CAS.
- X. Yu, Z. Q. Wang, Y. G. Jiang, F. Shi and X. Zhang, Adv. Mater., 2005, 17, 1289–1293 CrossRef CAS.
- J. F. Mano, Adv. Eng. Mater., 2008, 10, 515–527 CrossRef CAS.
- F. Guo and Z. G. Guo, RSC Adv., 2016, 6, 36623–36641 RSC.
- L. Zhang, Z. Zhang and P. Wang, NPG Asia Mater., 2012, 4, e8 CrossRef.
- J. J. Li, Y. N. Zhou and Z. H. Luo, ACS Appl. Mater. Interfaces, 2015, 7, 19643–19650 CAS.
- Z. Cheng, H. Lai, Y. Du, K. Fu, R. Hou, C. Li, N. Zhang and K. Sun, ACS Appl. Mater. Interfaces, 2014, 6, 636–641 CAS.
- S. J. Gao, Z. Shi, W. B. Zhang, F. Zhang and J. Lin, ACS Nano, 2014, 8, 6344–6352 CrossRef CAS PubMed.
- Y. K. Lai, F. Pan, C. Xu, H. Fuchs and L. F. Chi, Adv. Mater., 2013, 25, 1682–1686 CrossRef CAS PubMed.
- Y. X. Tang, Y. Y. Zhang, J. Y. Deng, J. Q. Wei, T. L. Hon, B. K. Chandran, Z. L. Dong, Z. Chen and X. D. Chen, Adv. Mater., 2014, 26, 6111–6118 CrossRef CAS PubMed.
- Y. X. Tang, Y. Y. Zhang, W. L. Li, B. Ma and X. D. Chen, Chem. Soc. Rev., 2015, 44, 5926–5940 RSC.
- Y. F. Wang, C. L. Lai, X. W. Wang, Y. Liu, H. W. Hu, Y. J. Guo, K. K. Ma, B. Fei and J. H. Xin, ACS Appl. Mater. Interfaces, 2016, 8, 25612–25620 CAS.
- M. Ge, Q. Li, C. Cao, J. Huang, S. Li, S. Zhang, Z. Chen, K. Zhang, S. S. Al-Deyab and Y. Lai, Adv. Sci., 2017, 4, 1600152 CrossRef PubMed.
- D. L. Tian, X. F. Zhang, Y. Tian, Y. Wu, X. Wang, J. Zhai and L. Jiang, J. Mater. Chem., 2012, 22, 19652–19657 RSC.
- G. Kwon, D. Panchanathan, S. R. Mahmoudi, M. A. Gondal, G. H. McKinley and K. K. Varanasi, Nat. Commun., 2017, 8, 14968 CrossRef PubMed.
- S. J. Gao, Y. Z. Zhu, F. Zhang and J. Jin, J. Mater. Chem. A, 2015, 3, 2895–2902 Search PubMed.
- H. Zhu, S. Yang, D. Chen, N. Li, Q. Xu, H. Li, J. He and J. Lu, Adv. Mater. Interfaces, 2016, 3, 1500683 CrossRef.
- H. Chen, S. J. Pan, Y. Z. Xiong, C. Peng, X. Z. Pang, L. Li, Y. Q. Xiong and W. J. Xu, Appl. Surf. Sci., 2012, 258, 9505–9509 CrossRef CAS.
- L. Chen, M. J. Liu, L. Lin, T. Zhang, J. Ma, Y. L. Song and L. Jiang, Soft Matter, 2010, 6, 2708–2712 RSC.
- S. X. Hu, X. Y. Cao, Y. L. Song, C. Li, P. Xie and L. Jiang, Chem. Commun., 2008, 2025–2027 RSC.
- B. Xin and J. Hao, Chem. Soc. Rev., 2010, 39, 769–782 RSC.
- Y. N. Zhou, J. J. Li and Z.-H. Luo, Ind. Eng. Chem. Res., 2015, 54, 10714–10722 CrossRef CAS.
- H. L. Liu, X. Q. Zhang, S. T. Wang and L. Jiang, Small, 2015, 11, 3338–3342 CrossRef CAS PubMed.
- J. J. Li, Y. N. Zhou and Z. H. Luo, Ind. Eng. Chem. Res., 2014, 53, 18112–18120 CrossRef CAS.
- W. A. Braunecker and K. Matyjaszewski, Prog. Polym. Sci., 2007, 32, 93–146 CrossRef CAS.
- X. J. Shi, G. J. Chen, Y. W. Wang, L. Yuan, Q. Zhang, D. M. Haddleton and H. Chen, Langmuir, 2013, 29, 14188–14195 CrossRef CAS PubMed.
- R. Yerushalmi, A. Scherz, M. E. van der Boom and H. B. Kraatz, J. Mater. Chem., 2005, 15, 4480–4487 RSC.
- S. L. Gras, T. Mahmud, G. Rosengarten, A. Mitchell and K. Kalantar-Zadeh, ChemPhysChem, 2007, 8, 2036–2050 CrossRef CAS PubMed.
- X. Zheng, Z. Guo, D. Tian, X. Zhang and L. Jiang, Adv. Mater. Interfaces, 2016, 3, 1600461 CrossRef.
- X. Lin, F. Lu, Y. Chen, N. Liu, Y. Cao, L. Xu, W. Zhang and L. Feng, Chem. Commun., 2015, 51, 16237–16240 RSC.
- J. Ge, L. A. Shi, Y. C. Wang, H. Y. Zhao, H. B. Yao, Y. B. Zhu, Y. Zhang, H. W. Zhu, H. A. Wu and S. H. Yu, Nat. Nanotechnol., 2017, 12, 434–440 CrossRef CAS PubMed.
- B. Vivek and E. Prasad, ACS Appl. Mater. Interfaces, 2017, 9, 7619–7628 CAS.
- Y. K. Lai, J. Y. Huang, Z. Q. Cui, M. Z. Ge, K. Q. Zhang, Z. Chen and L. F. Chi, Small, 2016, 12, 2203–2224 CrossRef CAS PubMed.
- P. M. Reddy, C. J. Chang, J. K. Chen, M. T. Wu and C. F. Wang, Appl. Surf. Sci., 2016, 368, 27–35 CrossRef.
- P. Calcagnile, D. Fragouli, I. S. Bayer, G. C. Anyfantis, L. Martiradonna, P. D. Cozzoli, R. Cingolani and A. Athanassiou, ACS Nano, 2012, 6, 5413–5419 CrossRef CAS PubMed.
- R. Du, Q. Feng, H. Ren, Q. Zhao, X. Gao and J. Zhang, J. Mater. Chem. A, 2016, 4, 938–943 CAS.
- Y. H. Man, Z. Q. Chen, Y. P. Zhang and P. T. Guo, Mater. Des., 2016, 97, 417–423 CrossRef CAS.
- Z. X. Xue, Y. Z. Cao, N. Liu, L. Feng and L. Jiang, J. Mater. Chem. A, 2014, 2, 2445–2460 CAS.
- R. Du, Q. C. Zhao, P. Li, H. Y. Ren, X. Gao and J. Zhang, ACS Appl. Mater. Interfaces, 2016, 8, 1025–1032 CAS.
- L. Liu, J. L. Lei, L. J. Li, R. Zhang, N. Y. Mi, H. R. Chen, D. Huang and N. B. Li, Mater. Lett., 2017, 195, 66–70 CrossRef CAS.
- S. H. Liu, Q. F. Xu, S. S. Latthe, A. B. Gurav and R. M. Xing, RSC Adv., 2015, 5, 68293–68298 RSC.
- L. H. Yu, G. Z. Hao, S. Zhou and W. Jiang, RSC Adv., 2016, 6, 24773–24779 RSC.
- X. Gui, Z. Zeng, Z. Lin, Q. Gan, R. Xiang, Y. Zhu, A. Cao and Z. Tang, ACS Appl. Mater. Interfaces, 2013, 5, 5845–5850 CAS.
- H. Che, M. Huo, L. Peng, T. Fang, N. Liu, L. Feng, Y. Wei and J. Yuan, Angew. Chem., Int. Ed., 2015, 54, 8934–8938 CrossRef CAS PubMed.
- X. Wang, G. Y. Qing, L. Jiang, H. Fuchs and T. L. Sun, Chem. Commun., 2009, 2658–2660 RSC.
- Y. G. Wang, L. O. Heim, Y. P. Xu, G. Buntkowsky and K. Zhang, Adv. Funct. Mater., 2015, 25, 1434–1441 CrossRef CAS.
- H. Liu, J. Y. Huang, F. Y. Li, Z. Chen, K. Q. Zhang, S. S. Al-Deyab and Y. K. Lai, Cellulose, 2017, 24, 1129–1141 CrossRef CAS.
- H. X. Wang, H. Zhou, H. T. Niu, J. Zhang, Y. Du and T. Lin, Adv. Mater. Interfaces, 2015, 2, 1400506 CrossRef.
- M. Essalhi and M. Khayet, J. Membr. Sci., 2012, 417, 163–173 CrossRef.
- M. Khayet, J. I. Mengual and T. Matsuura, J. Membr. Sci., 2005, 252, 101–113 CrossRef CAS.
- L. Hu, S. J. Gao, Y. Z. Zhu, F. Zhang, L. Jiang and J. Jin, J. Mater. Chem. A, 2015, 3, 23477–23482 CAS.
- H. Zhou, H. X. Wang, H. T. Niu and T. Lin, Sci. Rep., 2013, 3, 2964 CrossRef PubMed.
- Y. Zhao, H. X. Wang, H. Zhou and T. Lin, Small, 2017, 13, 1601070 CrossRef PubMed.
- X. L. Tian, H. Jin, J. Sainio, R. H. A. Ras and O. Ikkala, Adv. Funct. Mater., 2014, 24, 6023–6028 CrossRef CAS.
- M. Cao, J. Xiao, C. Yu, K. Li and L. Jiang, Small, 2015, 11, 4379–4384 CrossRef CAS PubMed.
- R. P. Garrod, L. G. Harris, W. C. E. Schofield, J. McGettrick, L. J. Ward, D. O. H. Teare and J. P. S. Badyal, Langmuir, 2007, 23, 689–693 CrossRef CAS PubMed.
- H. Bai, R. Sun, J. Ju, X. Yao, Y. M. Zheng and L. Jiang, Small, 2011, 7, 3429–3433 CrossRef CAS PubMed.
- Y. Xue, T. Wang, W. W. Shi, L. L. Sun and Y. M. Zheng, RSC Adv., 2014, 4, 40837–40840 RSC.
- H. Bai, L. Wang, J. Ju, R. Z. Sun, Y. M. Zheng and L. Jiang, Adv. Mater., 2014, 26, 5025–5030 CrossRef CAS PubMed.
Footnote |
† These authors contributed equally to this work. |
|
This journal is © The Royal Society of Chemistry 2018 |
Click here to see how this site uses Cookies. View our privacy policy here.