DOI:
10.1039/C7NR07349F
(Paper)
Nanoscale, 2018,
10, 231-238
Controllable manipulation of bubbles in water by using underwater superaerophobic graphene-oxide/gold-nanoparticle composite surfaces†
Received
2nd October 2017
, Accepted 21st November 2017
First published on 21st November 2017
Abstract
Manipulation of bubbles in water is of great importance in the mineral industry, oil production and separation, wastewater treatments, boiling processes, biological cell incubations, microfluidics and miniature reactor technologies. Generally, bubbles in an aqueous environment are inclined to stick to the channel walls, resulting in blockage and energy-consuming treatments. Herein, we report the fabrication of low-adhesion graphene-oxide (GO)/gold-nanoparticle (GNP) hybrid films with a good underwater superaerophobicity, which have the ability to arbitrarily manipulate bubbles in water. Owing to the hydrophilic nature of GO nanosheets and hierarchical structures of aggregated GNPs, the GO/GNP hybrid films showed low adhesion towards bubbles in water. Thus, bubbles could be freely manipulated using home-made tools coated with these low-adhesion, underwater superaerophobic GO/GNP hybrid films. The controlled 1D and 2D movements of one bubble and merging/reaction of two bubbles can be achieved. This study provides a new avenue to design new strategies for bubble manipulations, and further extends the application of superwettable 2D materials in interface fields involving gas phases.
Introduction
The study of bubbles is one of the important topics in physics, chemistry, engineering or medicine and other fields.1,2 Controlling the bubble performances is of great importance in the mineral industry,3 oil production and separation,4 wastewater treatments,5 boiling processes,6 biological cell incubations,7 and so on. In particular, in the past few decades since the beginning of microfluidics and miniature reactor technologies,8,9 manipulating bubbles has attracted tremendous attention due to its both scientific and industrial potential. Generally, bubbles in water media are inclined to stick to the channel walls,10 resulting in blockage and energy-consuming treatments. Another issue of bubbles is their buoyancy resulting in upward floating, rather than controllable movements towards horizontal directions. Therefore, a variety of methods11–22 have been explored to manipulate the bubbles, which can be divided into two categories: indirect and direct strategies.
Indirect strategies, including thermal,11,12 optical,13,14 electrical15–17 or acoustic18,19 methods, commonly generate an asymmetrical pressure difference among the bubbles, allowing for directional bubble movements. Angelsky's group14 demonstrated the photo-thermal generation and manipulation of bubbles by focusing a near-infrared laser beam in the water suspension. Jackel's group15 exhibited the first electrochemical method to control the bubbles through bistable optical switching. Cho's group16 reported controllable bubble motions by an electrowetting on dielectric (EWOD) method. Marmottant and Hilgenfeldt18 showed tunable bubble manipulation by acoustic streaming. In addition to external indirect manipulations, very recently, direct contact strategies by using superwettable interface materials to control water/oil droplets have been proposed by our group.20,21 Extreme wettabilities of interface materials can minimize adhesion among solid/liquid/gas interfaces, allowing for the potential to control bubbles in water media.22
Two directional (2D) nanomaterials, with few-atomic-layer thickness, are current “superstar” materials due to their unique physical and chemical properties.23,24 Besides their excellent applications in electronics,25 optics,26,27 valleytronics,28 catalysis and biosensing,29 2D nanomaterials exhibit considerable potential in forming superwettable surfaces. The porosity of stacked graphene oxide (GO) nanosheets can cause nano-capillaries, allowing water transport 1010 times faster than helium.30 Therefore, highly hydrophilic GO stacking layers assisted by nanowires31 or nanoparticles32 have been reported. Although 2D nanomaterials have been successfully exploited in the preparation of superwetting materials, efforts to build underwater superaerophobic surfaces (the contact angle of bubbles >150°), as well as the controllable manipulation of bubbles, have not yet been realized.
Herein, we have fabricated low-adhesion GO/gold-nanoparticle (GNP) hybrid films with a good underwater superaerophobicity, which have the ability to arbitrarily manipulate bubbles in water. The superwettability of GO/GNP hybrid films strongly depends on the number of assembly layers. Due to the hydrophilic nature of GO nanosheets and hierarchical structures of aggregated GNPs, water could be trapped in the interstices of GO/GNP hybrid films, resulting in the low adhesion of films towards bubbles in water. Thus, bubbles could be freely manipulated using home-made tools coated with these low-adhesion, underwater superaerophobic GO/GNP hybrid films. The controlled 1D and 2D movements of one bubble and merging/reaction of two bubbles can be achieved. This study will inspire researchers to design new strategies for bubble manipulations, and further extend the application of GO nanosheets or GNPs in catalysis,33,34 hydrogen production,35 and other fields involving gas phases.
Results and discussion
Fabrication of GO/GNP hybrid films
We prepared underwater superaerophobic GO/GNP hybrid films by a typical layer-by-layer (LbL) assembly process and post-heating treatment (Fig. 1). The LbL assembly process is regarded as a simple, versatile, and low-cost approach that can combine diverse functions into a single surface by tuning the film compositions.36 In our experimental design, glass substrates were primarily coated with one bilayer of positively charged poly(diallyldimethylammonium chloride) (PDDA) and negatively charged GNPs. Then, another bilayer of PDDA and negatively charged GO nanosheets were deposited on the PDDA/GNP film. This LbL cycle can be repeated up to five times to generate rough surface structures. Finally, a post heating treatment was performed to remove the organic component from these (PDDA/GNP/PDDA/GO)n composites, yielding (GNP/GO)n hybrid films. The removal of organic parts was confirmed by FT-IR results, shown in ESI Fig. S1.†
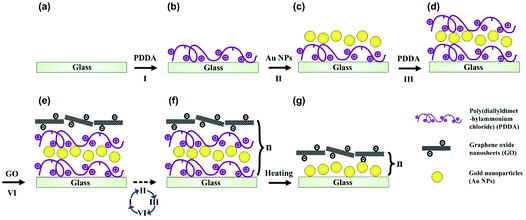 |
| Fig. 1 Layer-by-layer schematic process of fabricating a (GNP/GO)n hybrid film. (a–e) Steps I and III represent the adsorption of positively charged poly(diallyldimethylammonium chloride) (PDDA). Steps II and IV show the adsorption of negatively charged gold nanoparticles (GNPs) and graphene oxide (GO) nanosheets, respectively. (f) By repeating the cycles from I to IV, a multi-layered LbL assembly can be formed upon the desired substrate. (g) Inorganic (GNP/GO)n hybrid films can be prepared by removing the organic component from the (PDDA/GNP/PDDA/GO)n composite through a post-heating treatment. | |
The surface microstructures and the wettabilities of as-prepared (GNP/GO)n hybrid films have been carefully studied. Fig. 2a and b show the transmission electron microscope (TEM) images of GO nanosheets and GNPs; both are the building blocks to construct the hybrid films. The GO nanosheets are within few-atomic-layer thickness, while the GNPs have a narrow particle distribution with the average diameter of 42 nm. When these two components were assembled through the LbL process, their surface structures were investigated by using a scanning electron microscope (SEM). Fig. 2c shows a top-view SEM observation of a (GNP/GO)5 hybrid film. The stacking of GO nanosheets provided a continuous surface, allowing their hydrophilic chemical groups to be exposed to air. Owing to the aggregation of GNPs in the LbL process, hierarchical roughness can be observed, which was further proved by atomic force microscope (AFM) imaging. Fig. 2d exhibits the surface morphology of the (GNP/GO)5 hybrid film, showing the RMS roughness of the film to be ∼137 nm. As can be found from cross-sectional analysis, the maximum height fluctuation of the film is more than 210 nm. It should be pointed out that the heating treatment facilitated the construction of considerable surface roughness. The temperature change caused partial aggregation/merging of GNPs, which was investigated using AFM results, as shown in ESI Fig. S2.† In the control experiment, the bare glass substrate was found to have a RMS roughness of only ∼28 nm (see ESI Fig. S3a–c†).
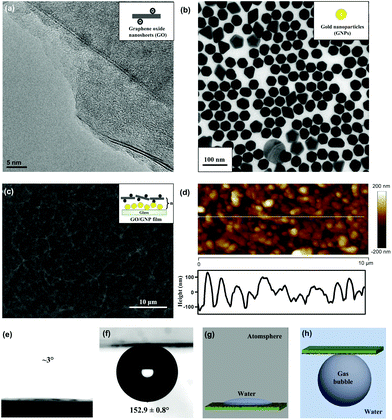 |
| Fig. 2 Surface morphology and wettabilities of (GNP/GO)5 hybrid films. Transmission electron microscope (TEM) images of dispersive (a) GO nanosheets with few-atomic-layer thickness and (b) GNPs prepared through a wet chemical method. (c) The top-view scanning electron microscope (SEM) image of a (GNP/GO)5 hybrid film. Inset images in (a–c) are schematic illustrations. (d) The atomic force microscope (AFM) investigation of the (GNP/GO)5 hybrid film. The bottom part is the cross-sectional profile of the rough surface. (e) A water drop placed on the (GNP/GO)5 hybrid film under atmosphere. (f) A bubble placed below the downward (GNP/GO)5 hybrid film under the water surface. (g, h) are schematic illustrations of (e, f), respectively. | |
Superaerophobic, low-adhesion GO/GNP hybrid films and their tunable wettability
The rough structures of the (GNP/GO)5 hybrid film, as well as the hydrophilic nature of GO nanosheets, played a crucial role in their underwater superaerophobic property. Under atmosphere, the water droplet could dramatically spread out upon the (GNP/GO)5 hybrid film within 1 second (Fig. 2e). When being immersed in water, the (GNP/GO)5 hybrid film showed superaerophobicity, with an air contact angle (CA) of 152.9 ± 0.8°. In contrast, the bare glass substrate was just aerophobic, with an air CA of 137.7 ± 8.1° (see ESI Fig. S3d†). According to the modified Cassie model37 in a water/gas/solid system,
cos θ′ = f·cos θ + f − 1 |
where f is the area fraction of the solid, θ is the CA of a bubble on a flat solid surface in water, and θ′ is the CA of a bubble on a rough solid surface in water. θ is recorded to be ∼91° when the bubble was in contact with a GO bulk material in water.38 In this study, θ′ was measured to be 152.9°, indicating that more than 88% contact area was water/air instead of GO/air when the bubble made contact with the (GNP/GO)5 hybrid film. In contrast, the air CA of (PDDA/GO)5 films was around 117.9 ± 1.3° (ESI Fig. S4†), indicating the importance of GNPs in constructing surface roughness.
In addition to static bubble-repellent ability in water, the hierarchically rough structures of (GNP/GO)5 hybrid films showed significantly lower adhesion than the bare glass counterpart. A high-sensitivity micromechanical balance system was used to record the adhesion forces between the bubble and the solid substrates (Fig. 3a). The advancing distance of the samples and the volume of bubbles were fixed to be 3.0 mm and 5 μL, respectively. Besides the recording of adhesion forces, the whole contacting processes were observed using an optical microscope lens and a charge-coupled device (CCD) camera system. For the (GNP/GO)5 hybrid film, the shape of the bubble was spherical during the whole measurement (Fig. 3c). The adhesion force was just 18 ± 2 μN (Fig. 3b), and the bubble could leave without any loss. However, for the bare glass counterpart, the shape of the bubble obviously deformed (Fig. 3d), indicating considerable adhesion between its surface and the bare glass plate. It should be noted that the force curve was unable to return to zero after a cycle (Fig. 3a), indicating the weight loss of the bubble onto the glass plate. The corresponding adhesion force was measured to be as high as 163 ± 12 μN. These results show that the rough surfaces of the (GNP/GO)5 hybrid film can prevent the penetration of the bubbles, leading to low-adhesion, underwater superaerophobic surfaces in water.
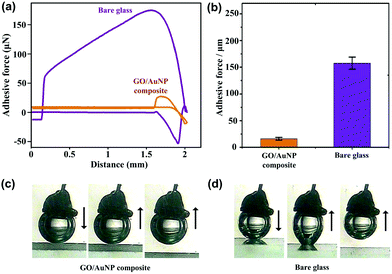 |
| Fig. 3 Lower bubble adhesion of (GNP/GO)5 hybrid films in water. (a) Typical force–distance curves for a bare glass plate (purple line) and an underwater superaerophobic (GNP/GO)5 hybrid film (orange line). (b) The adhesive force values of the (GNP/GO)5 hybrid film (orange) and a bare glass plate (purple). The inset images on the top of columns are the shapes of bubbles, taken at different stages during the adhesive-force measurement process. The (GNP/GO)5 hybrid film showed ultra-low adhesive properties while the bare glass plate exhibited high adhesive behavior in water. Photographic images of a bubble coming into contact with (c) a (GNP/GO)5 hybrid film and (d) a bare glass substrate. Images on the left were taken before the bubble came into contact with the surface; images in the middle were obtained as the bubble was leaving the surface; and images on the right were taken after the bubble left the surface. | |
The roughness of (GNP/GO)n hybrid films was enhanced following the increase in the number of assembly layers (see AFM results in ESI Fig. S5†). Accordingly, the wettability of (GNP/GO)n hybrid films was improved. Fig. 4a shows the real-time water CA depending on the number of assembly layers. When only one layer of the GNP/GO composite was deposited on the glass substrate, the water CA gradually reduced and remained at around 12°. In contrast, the water CA rapidly dropped to less than 5° when coming in contact with the (GNP/GO)5 hybrid film. Reduced water CAs under atmosphere indicate increased bubble CAs under the water surface. Fig. 4b exhibits the dependence of adhesion forces and bubble CAs on the number of assembly layers. The increased number of assembly layers contributed to enhanced surface roughness, allowing for more water to be trapped inside the interstices of the GO/GNP hybrid film. Thus, the adhesion forces were dramatically reduced. Meanwhile, the bubble CA increased. A further increase in the number of assembly layers showed negligible contributions to their wettabilities. Thus, (GNP/GO)5 hybrid films were used in the following procedures unless otherwise specified.
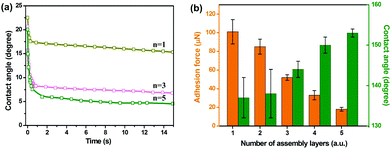 |
| Fig. 4 Tunable underwater aerophobicity and adhesion depending on the number of assembly layers. (a) Water contact angles (CAs)–time characteristics of (GNP/GO)n hybrid films with a diverse number (n) of assembly layers. (b) The dependence of adhesion forces (orange) and bubble CAs (green) on the number of assembly layers. The increased number of assembly layers led to improved underwater aerophobicity. | |
On-demand manipulation of bubbles in water
Owing to their density induced buoyancy, bubbles are inclined to float upwards, rather than move towards the horizontal directions. Therefore, a 5 × 5 cm2 glass plate coated with a low-adhesion, superaerophobic (GNP/GO)5 hybrid film was used to prevent the upward floating of bubbles. Then, a home-made pusher modified by the (GNP/GO)5 hybrid film was used to control the 1D movement of a bubble (Fig. 5a). After being released from the needle of a microinjector, a ∼10 μL bubble remained in a spherical shape in water (Fig. 5c). Owing to superaerophobicity and low adhesion properties of the (GNP/GO)5 hybrid film, the bubble was pushed from the right to the left. Importantly, the bubble could stay at the left point when the pusher was gently withdrawn. In contrast, the bubble movement was different when we replaced the low-adhesion pusher with a high-adhesion bare glass plate (Fig. 5b). The bubble could be pushed towards the left point; however, it returned to its original position following the withdrawal of the pusher (Fig. 5d). This result was attributed to the high adhesion between the bubble and the bare glass plate, showing the crucial role of underwater superaerophobic films in freely manipulating the bubble motion.
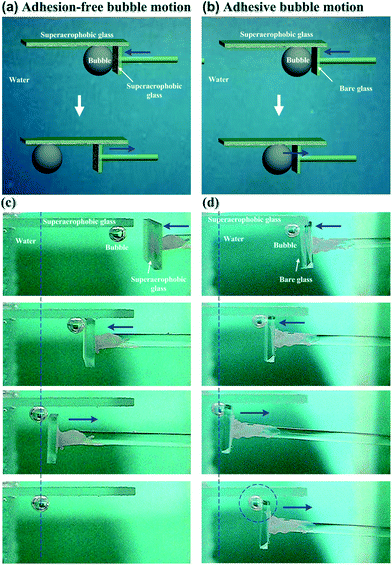 |
| Fig. 5 The process of the controlled 1D movement of a bubble by using home-made tools coated with low-adhesion, superaerophobic (GNP/GO)5 hybrid films. Schematic illustrations of 1D bubble motions by a pusher consisting of (a) a (GNP/GO)5 hybrid film and (b) a bare glass plate. Owing to the presence of low-adhesion, superaerophobic (GNP/GO)5 hybrid films, the bubble can be pushed from the right to the left, and then remained when the pusher was gently withdrawn. In contrast, the bubble could be moved from the right to the left when adhered to the pusher; however it returned to its original position following the withdrawal of the pusher. Photographs of representative stages of the bubble motions by a pusher consisting of (c) a (GNP/GO)5 hybrid film and (d) a bare glass plate. A 5 × 5 cm2 glass plate coated with a (GNP/GO)5 hybrid film was used to prevent the upward floating of bubbles. | |
The on-demand 1D motion of bubbles could be achieved by depositing the (GNP/GO)5 hybrid film onto an etched glass plate (Fig. 6a). A 5 × 5 cm2 glass plate was mechanically etched with an “S” type track with an average depth of 1 mm. Then, this etched glass plate was deposited by the underwater superaerophobic (GNP/GO)5 hybrid film. After being released from the needle of a microinjector, a ∼10 μL bubble remained in a spherical shape at the end of the “S” type track (Fig. 6c). Then, the bubble could move along the track when we gently lifted one side of the glass plate, since the adhesion between the bubble and the (GNP/GO)5 hybrid film was considerably low. The lifting of the glass plate side caused a buoyancy gradient from one end to the other one along the track, driving the bubble to move in the on-demand “S” type track. In contrast, the bubble just stuck to the bare glass plate (Fig. 6b) even when one side of the plate was lifted (Fig. 6d). The adhesion between the bubble and the bare glass plate was large enough to overcome the buoyancy difference, resulting in the sticking of the bubble.
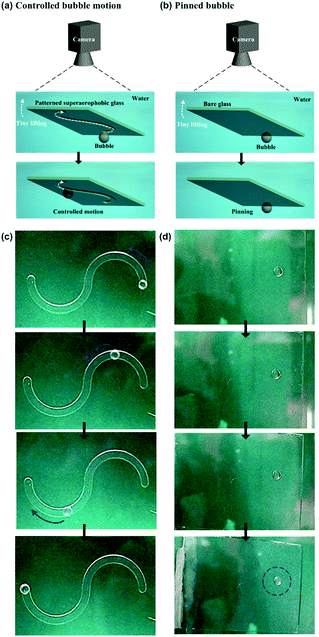 |
| Fig. 6 The process of the on-demand 1D movement of a bubble through the guidance of an etched “S” type track of (GNP/GO)5 coated substrates. Schematic illustrations of (a) on-demand bubble motions upon an etched glass substrate coated with a (GNP/GO)5 hybrid film and (b) a pinned bubble on a bare glass plate. When the etched plate was gently lifted on one side, the bubble could move along the track due to the buoyancy gradient from one end to the other one along the track. In contrast, the bubble just stuck to the bare glass plate even when the side of the plate was lifted. Photographs of representative stages of the bubble motions upon (c) an etched substrate modified by a (GNP/GO)5 hybrid film and (d) a bare glass counterpart. | |
Besides the 1D motion, the 2D motion of bubbles could be achieved due to these low-adhesion hybrid films (Fig. 7a). The bubble was firstly positioned at the top right hand corner of a underwater superaerophobic plate (Fig. 7b). A home-made pusher could force it to horizontally move from the right to the left. Owing to the low-adhesion between the bubble and the pusher, the bubble could stay when the pusher was withdrawn. Then, the pusher turned to 90° to move the bubble from the top to the bottom, resulting in the controllable 2D motion of bubbles based on the superaerophobic (GNP/GO)5 hybrid films.
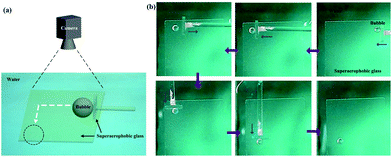 |
| Fig. 7 The process of the controlled 2D movement of a bubble by using home-made tools coated with (GNP/GO)5 hybrid films. (a) Schematic illustrations of 2D bubble motions by a pusher coated with a (GNP/GO)5 hybrid film. Owing to the low-adhesion between the bubble and the pusher, the bubble could be moved from the top right hand corner to the bottom left hand corner. (b) Photographs of representative stages of 2D bubble motions. A 5 × 5 cm2 glass plate coated with a (GNP/GO)5 hybrid film was used to prevent the upward floating of bubbles. | |
This underwater superaerophobic material based manipulation of bubbles is different from existing external field (thermal, optical, electrical or acoustic) strategies.11–19 Owing to less than 12% soild/air contact area, this facile strategy can provide a non-contaminative strategy for controllable bubble coalescence and reactions.
Controlled merging/reaction of two bubbles
We performed a proof-of-principle demonstration of bubble merging/reaction based on the controllable movement of bubbles by using underwater superaerophobic (GNP/GO)5 hybrid films (Fig. 8a). A 5 × 5 cm2 modified plate was used to prevent the upward floating of bubbles. Then, a carbon monoxide (CO) bubble and an oxygen (O2) bubble in the same volume were carefully placed below the opposite ends of the plate (Fig. 8b). The O2 bubble was forced to move towards the CO bubble by using a superaerophobic pusher. When these two bubbles made contact with each other closely, they coalesced into a larger CO2 bubble due to the rapid oxidation reaction of CO. The reacted CO2 bubble could exist because we decreased the pH value of the surrounding aqueous environment by adding hydrochloric acid. The increase of H+ amount could suppress the dissolution of CO2 into water.
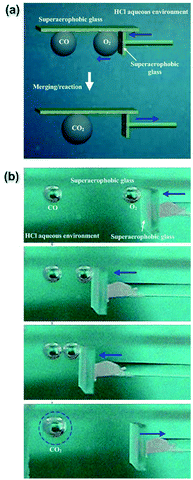 |
| Fig. 8 The controlled merging/reaction of two bubbles by using home-made tools coated with (GNP/GO)5 hybrid films. (a) Schematic illustrations of the bubble merging/reaction. A 5 × 5 cm2 glass plate coated with a (GNP/GO)5 hybrid film was used to prevent the upward floating of bubbles. A carbon monoxide (CO) bubble and an oxygen (O2) bubble in the same volume were carefully placed below the opposite ends of the plate. The O2 bubble was forced to move towards the CO bubble by using a superaerophobic pusher, and coalesced into a larger CO2 bubble. The reacted CO2 bubble could exist because we decreased the pH value of the surrounding aqueous environment to suppress the dissolution of CO2 into water. (b) Photographs of representative stages of the controlled merging/reaction of two bubbles. | |
Durability is a key parameter to judge the application potential of these low-adhesion, superaerophobic films. The working life of (GNP/GO)5 hybrid films was tested by numerous cycles of “contacting then releasing” a bubble. Even after 1000 cycles, the (GNP/GO)5 hybrid films showed a good underwater superaerophobicity and low adhesion. The volume of bubbles has been investigated. Bubbles ranging from 3 μL to 300 μL could all be manipulated by these home-made superaerophobic tools, and their reaction products were easy to collect.
To demonstrate the controllable manipulation of bubbles at the microscale, superaerophobic microfluidic circuits have been built (Fig. 9). Microchannels with a width of ∼4.8 μm were fabricated using soft-lithography techniques, and then modified by superaerophobic, low-adhesion (GNP/GO)5 hybrid films. The on-demand 1D motion of bubbles at the microscale has been achieved (Fig. 9a and b). A bubble with a diameter of ∼3.7 μm stayed and remained in a spherical shape when the microfluidic circuit was placed horizontally. Then, the bubble could move along the channel when we gently lifted one side of the microfluidic circuit. Owing to low adhesion between the bubble and the (GNP/GO)5 hybrid film, lifting one side of the microfluidic circuit caused a buoyancy gradient along the channel, driving the bubble to move spontaneously. In contrast, the bubble just stuck to the bare PDMS channel (the underwater air CA of PDMS was around 92.8 ± 1.3°) even when one side of the plate was lifted (Fig. 9c and d), indicating the importance of superaerophobicity for bubble motions at the microscale. Furthermore, multi-bubble motions were manipulated by generating multi-channel superaerophobic microfluidic circuits (Fig. 9e and f). Similar to the individual bubble (Fig. 9b), the bubble in each channel firstly stayed and then spontaneously moved when one side of the microfluidic circuit was lifted, showing the ability of superaerophobic, low-adhesion (GNP/GO)5 hybrid films to spontaneously control a large amount of bubbles.
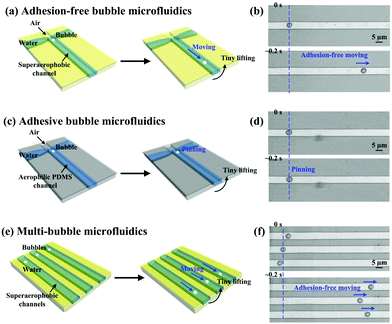 |
| Fig. 9 The process of the on-demand 1D movement of bubbles in superaerophobic microfluidic circuits. Schematic illustrations of (a) on-demand bubble motions in a (GNP/GO)5 hybrid film modified microfluidic circuit, and (c) a pinned bubble in a bare PDMS microfluidic circuit and (e) multi-bubble on-demand motions in (GNP/GO)5 hybrid film modified multi-channel microfluidic circuits. Photographs of representative stages of the bubble motions upon (b) (GNP/GO)5 hybrid film modified, superaerophobic and (d) bare PDMS microfluidic circuits. (f) Photographs of representative stages of multi-bubble on-demand motions. | |
Conclusions
A facile method using underwater superaerophobic materials to manipulate bubbles in water has been proposed in this study. The combination of the hydrophilic nature of GO nanosheets and hierarchical structures of aggregated GNPs allowed the trapping of water inside the rough surfaces, leading to superaerophobic and low adhesion surfaces in water. As a result, on-demand 1D and 2D movements of bubbles with ultra-low friction drags could be performed by using home-made underwater superaerophobic tools. The controlled coalescence of bubbles containing different reagents was achieved, indicating a miniature gas reaction occurring inside a bubble based reactor. These results proposed a facile, equipment-free and low-cost strategy for the on-demand manipulation of bubbles. Owing to the chemical activities of GNPs/GO-nanosheets, these underwater superaerophobic surfaces might find promising applications in miniature-reactors, collectors, sensors, catalysis,33,34 hydrogen production,35 and other fields involving gas phases.
Experimental
Materials
GO nanosheets were prepared from natural graphite by using a modified Hummers method.39 A representative procedure for preparing 45 nm GNPs is as follows: 2.352 mL HAuCl4 solution (25 mM) was diluted with 200 mL Milli-Q water and heated to 100 °C until boiling. Sodium citrate solution (34 mM) was added into the above auric solution. After heating for 3 min, the clear solution changed to a violet color, yielding the formation of GNPs. After further boiling for 10 min, the heating source was removed and the dispersion was cooled to room temperature.
Layer-by-layer assembly
The glass plates were cleaned by immersion in a “piranha” solution (3
:
1 H2SO4/H2O2, dangerous if coming into contact with organics) followed by thorough rinsing with distilled water. The preparation of the LBL films consists of the following steps. The glass substrates were coated with one bilayer of positively charged poly(diallyldimethylammonium chloride) (PDDA, 1 mg mL−1) and negatively charged GNPs (0.2 mg mL−1). Then, another bilayer of PDDA (1 mg mL−1) and negatively charged GO (1 mg mL−1) nanosheets were deposited on the PDDA/GNP film. This process was repeated several times to produce a film of desired thickness. Each deposition was accompanied by rinsing with distilled water for 5 min and drying under a stream of N2 for 1 min. Finally, the as-prepared (PDDA/GNP/PDDA/GO)n composite was heated at 350 °C for 2 hours to remove the organic component, yielding (GNP/GO)n hybrid films.
Superaerophobic microfluidic circuits
Superaerophobic microfluidic circuits were built using soft-lithography techniques. The circuit consists of two layers. The first layer includes the channels and liquid plus bubble inlets which were molded in polydimethylsiloxane (PDMS) (Sylgard 184, Dow Corning) to generate flow geometry. The second layer was a thin 100 μm film of PDMS. These two layers underwent the LbL assembly process, and were covered by superaerophobic, low adhesion (GNP/GO)5 hybrid films. Then, these two layers were finally bonded by air plasma exposure (Harrick Plasma), yielding superaerophobic microfluidic circuits.
Instruments and characterization
The surface structures of (GNP/GO)n hybrid films were studied by scanning electron microscopy (SEM, JEOL, JSM-6700F, Japan) at an accelerating voltage of 3.0 kV. Static contact angles were measured using a Dataphysics OCA20 contact-angle system at ambient temperature. The average CA was obtained by measuring more than five different positions of the same sample. The adhesive force for taking a 5 μL bubble away from the coated layer was measured using a high-sensitivity microelectromechanical balance system with a resolution of 10 mg (Data-Physics DCAT 11, Germany) and a charge-coupled device (CCD) camera system at ambient temperature. The videos or photographs were obtained by using a commercial digital camera with 7.2 megapixels (Sony, DSC-W120, Japan). The optical micrographs of the microfluidic circuits were obtained using an optical microscope (Vision Engineering Co., UK) that was coupled to a CCD camera and connected to a desktop computer.
Conflicts of interest
There are no conflicts to declare.
Acknowledgements
This research was financially supported by the National Natural Science Foundation of China (21404042), the Natural Science Foundation of Guangdong Province (2014A030310166), and Australian Research Council's Discovery Early Career Researcher Award (DECRA) funding scheme (DE140100541). This work was in part performed at the Melbourne Centre for Nanofabrication (MCN) in the Victorian Node of the Australian National Fabrication Facility (ANFF).
References
- T. P. Witelski, Nat. Phys., 2009, 5, 315–316 CrossRef CAS.
- R. Manica, E. Klaseboer and D. Y. C. Chan, Adv. Colloid Interface Sci., 2016, 235, 214–232 CrossRef CAS PubMed.
- D. Tao, Sep. Sci. Technol., 2004, 39, 741–760 CrossRef CAS.
- P. Bandyopadhyay and A. Sharma, J. Pet. Sci. Eng., 2011, 78, 719–731 CrossRef CAS.
- T. V. Le, T. Imai, T. Higuchi, K. Yamamoto, M. Sekine, R. Doi, H. T. Vo and J. Wei, Chem. Eng. Sci., 2013, 94, 1–6 CrossRef CAS.
- I. U. Vakarelski, N. A. Patankar, J. O. Marston, D. Y. C. Chan and S. T. Thoroddsen, Nature, 2012, 489, 274–277 CrossRef CAS PubMed.
- Y. L. Xie and C. L. Zhao, Nanoscale, 2017, 9, 6622–6631 RSC.
- P. Domachuk, K. Tsioris, F. G. Omenetto and D. L. Kaplan, Adv. Mater., 2010, 22, 249–260 CrossRef CAS PubMed.
- D. G. Rackus, M. H. Shamsi and A. R. Wheeler, Chem. Soc. Rev., 2015, 44, 5320–5340 RSC.
- M. Mohammadi and K. V. Sharp, J. Fluids Eng., 2015, 137, 312081–312087 Search PubMed.
- R. B. Maxwell, A. L. Gerhardt, M. Toner, M. L. Gray and M. A. Schmidt, J. Microelectromech. Syst., 2003, 12, 630–640 CrossRef.
- R. S. Taylor and C. Hnatovsky, Opt. Express, 2004, 12, 916–928 Search PubMed.
- H. Takeuchi, M. Motosuke and S. Honami, Heat Transfer Eng., 2012, 33, 234–244 CrossRef CAS.
- O. V. Angelsky, A. Y. Bekshaev, P. P. Maksimyak, A. P. Maksimyak, S. G. Hanson and S. M. Kontush, Opt. Express, 2017, 25, 5232–5243 CAS.
- J. L. Jackel, J. J. Johnson and W. J. Tomlinson, Opt. Lett., 1990, 15, 1470–1472 CrossRef CAS PubMed.
- Y. J. Zhao and S. K. Cho, Lab Chip, 2007, 7, 273–280 RSC.
- J. Li, Y. X. Wang, H. S. Chen and J. D. Wan, Lab Chip, 2014, 14, 4334–4337 RSC.
- P. Marmottant and S. Hilgenfeldt, Nature, 2003, 423, 153–156 CrossRef CAS PubMed.
- D. Rabaud, P. Thibault, J. P. Raven, O. Hugon, E. Lacot and P. Marmottant, Phys. Fluids, 2011, 23, 042003 CrossRef.
- B. Su, S. T. Wang, Y. L. Song and L. Jiang, Nano Res., 2011, 4, 266–273 CrossRef.
- B. Su, S. T. Wang, Y. L. Song and L. Jiang, Soft Matter, 2011, 7, 5144–5149 RSC.
- C. M. Yu, M. Y. Cao, Z. C. Dong, J. M. Wang, K. Li and L. Jiang, Adv. Funct. Mater., 2016, 26, 3236–3243 CrossRef CAS.
- R. Mas-Balleste, C. Gomez-Navarro, J. Gomez-Herrero and F. Zamora, Nanoscale, 2011, 3, 20–30 RSC.
- S. Ornes, Proc. Natl. Acad. Sci. U. S. A., 2015, 112, 13128–13130 CrossRef CAS PubMed.
- K. Xu, L. Yin, Y. Huang, T. A. Shifa, J. W. Chu, F. Wang, R. Q. Cheng, Z. X. Wang and J. He, Nanoscale, 2016, 8, 16802–16818 RSC.
- S. L. Yu, X. Q. Wu, Y. P. Wang, X. Guo and L. M. Tong, Adv. Mater., 2017, 29, 1606128 CrossRef PubMed.
- Z. P. Sun, A. Martinez and F. Wang, Nat. Photonics, 2016, 10, 227–238 CrossRef CAS.
- J. R. Schaibley, H. Y. Yu, G. Clark, P. Rivera, J. S. Ross, K. L. Seyler, W. Yao and X. D. Xu, Nat. Rev. Mater., 2016, 1, 16055 CrossRef CAS.
- R. Kurapati, K. Kostarelos, M. Prato and A. Bianco, Adv. Mater., 2016, 28, 6052–6074 CrossRef CAS PubMed.
- R. R. Nair, H. A. Wu, P. N. Jayaram, I. V. Grigorieva and A. K. Geim, Science, 2012, 335, 442–444 CrossRef CAS PubMed.
- H. B. Huang, Z. G. Song, N. Wei, L. Shi, Y. Y. Mao, Y. L. Ying, L. W. Sun, Z. P. Xu and X. S. Peng, Nat. Commun., 2013, 4, 2979 Search PubMed.
- J. Y. Zhu, L. G. Xu and J. H. He, Chem. – Eur. J., 2012, 18, 163 CrossRef PubMed.
- W. W. He, Y. T. Zhou, W. G. Warner, X. N. Hu, X. C. Wu, Z. Zheng, M. D. Boudreau and J. J. Yin, Biomaterials, 2013, 34, 765–773 CrossRef CAS PubMed.
- C. M. Yu, M. Y. Cao, Z. C. Dong, K. Li, C. L. Yu, J. M. Wang and L. Jiang, Adv. Funct. Mater., 2016, 26, 6830–6835 CrossRef CAS.
- W. Zhang, S. L. Hu, J. J. Yin, W. W. He, W. Lu, M. Ma, N. Gu and Y. Zhang, J. Am. Chem. Soc., 2016, 138, 5860–5865 CrossRef CAS PubMed.
- C. Y. Jiang and V. V. Tsukruk, Adv. Mater., 2006, 18, 829–840 CrossRef CAS.
- A. B. D. Cassie and S. Baxter, Trans. Faraday Soc., 1944, 40, 0546–0550 RSC.
- S. Thampi, A. M. Nandkumar, V. Muthuvijayan and R. Parameswaran, ACS Appl. Mater. Interfaces, 2017, 9, 4498–4508 CAS.
- W. S. Hummers and R. E. Offeman, J. Am. Chem. Soc., 1958, 80, 1339–1339 CrossRef CAS.
Footnote |
† Electronic supplementary information (ESI) available. See DOI: 10.1039/c7nr07349f |
|
This journal is © The Royal Society of Chemistry 2018 |
Click here to see how this site uses Cookies. View our privacy policy here.