DOI:
10.1039/C8QM00201K
(Research Article)
Mater. Chem. Front., 2018,
2, 1467-1474
A novel post-polymerizable polynorbornene prepared via ROMP: easy synthesis and conversion into a free-standing film with high Tg and low dielectric constant
Received
3rd May 2018
, Accepted 27th May 2018
First published on 28th May 2018
Abstract
A novel linear silicon-containing polynorbornene (BCB-PNB, Mn = 93
000 g mol−1) with thermo-crosslinkable benzocyclobutene side chains was synthesized through ring-opening metathesis polymerization (ROMP). This polymer displayed good solubility and film-forming ability. After post-polymerization at high temperature, a free-standing film based on BCB-PNB was easily converted to a crosslinked network, which exhibited a dielectric constant of 2.60 for frequencies ranging from 40 Hz to 30 MHz. In particular, this crosslinked film exhibited a high Tg of up to 400 °C, which was much higher than that of the previously reported polynorbornenes prepared by ROMP. This is the first example of a polynorbornene prepared by ROMP with such a high Tg and good processability. Besides, the crosslinked film also displayed high hydrophobicity. These results indicate that the introduction of thermo-crosslinkable benzocyclobutene groups into polynorbornene side chains can greatly enhance the properties of the polymers. This work also develops a facile method for the preparation of a new free-standing post-polymerizable polynorbornene film.
Introduction
Polynorbornenes (PNBs) have drawn considerable interest due to their various applications in the fields of optics, electronics, gas separation, and theranostics.1–10 Different types of PNBs can be synthesized from norbornene (NB) monomers by three routes via vinyl addition polymerization, ring-opening metathesis polymerization (ROMP) or cationic (or radical) polymerization.11–16 Among them, PNBs prepared by vinyl addition polymerization exhibit high thermal stability and high glass transition temperature (Tg) due to the saturated bicyclic structures in their backbones.17,18 However, their poor solubility in organic solvents and high Tg preclude solution- or melt-processing, which limits their potential applications. Therefore, developing PNBs with high thermal stability and good processability is of particular importance. Although many studies have been carried out such as introducing pendant groups into the polycyclic backbones19 and copolymerizing norbornene monomers with olefins,20,21 effective and facile methods to synthesize soluble PNBs with high Tg are still lacking, especially for a large scale preparation.
In comparison with vinyl addition polymerization, ROMPs of NB monomers have been widely used to prepare functional PNBs due to their high reaction efficiency, mild polymerization conditions, and short reaction time.22–26 Because of the high tolerance to functional groups, NB monomers with various substituents can be converted to many functionalized PNBs via ROMP. However, ROMP-type PNBs usually exhibit a Tg of less than 200 °C because of the excess unsaturated bonds and relatively flexible chains.27–31
On the basis of the salient features of ROMP, PNBs with good processability and high thermostability prepared via a post-polymerization process would be highly desirable for academia and industry. It is noted that introducing crosslinkable groups into the main chain or side chains of polymers can increase the thermostability of the polymers. Among various crosslinkable groups, benzocyclobutene (BCB) units have been paid much attention because they can form crosslinked networks with high thermostability and good dielectric properties via ring-opening reaction.32–35 A typical example is CYCLOTENE, a crosslinked polymer prepared from a BCB-functionalized siloxane and commercialized by DOW Chemical Company. It shows a dielectric constant (Dk) of 2.65 and a Tg of above 350 °C.36,37 Thus, in order to obtain ROMP-type PNBs with good thermostability and good dielectric properties, we designed and synthesized a NB monomer with a BCB unit. Based on this NB monomer, a linear PNB with high molecular weight was prepared via the ROMP procedure under mild conditions. This linear PNB displayed good solubility and excellent film-forming ability. A highly transparent PNB film was easily prepared by casting. After post-polymerization at high temperature, the film was converted to a crosslinked network which was still flexible. As it was expected, the crosslinked PNB exhibited a Tg of higher than 400 °C and a Dk of about 2.6. To the best of our knowledge, this is the first example of a PNB prepared by ROMP with such a high Tg and a low Dk as well. Here, we report the details.
Experimental
Materials
4-Bromobenzocyclobutene was purchased from Chemtarget Technologies Co., China. n-Butyllithium (2.5 M in hexane) was purchased from J&K Chemical Ltd and used without further purification. Grubbs’ second generation catalyst (Grubbs II) was obtained from Adamas Reagent Co. Ltd and used as received. Tetrahydrofuran (THF) was dehydrated and distilled under an inert atmosphere before use. 5-Ethoxydimethylsilyl-2-norbornene was synthesized from the Diels–Alder reaction between dicyclopentadiene and ethoxydimethylvinylsilane according to the previous literature.3
Characterization
1H NMR and 13C NMR spectra were recorded on JEOL 400YH and Bruker DPX 400 instruments at room temperature. Elemental analysis (EA) was carried out on an Elementar vario EL III. Molecular weight was determined by gel permeation chromatography (GPC) using a Waters Breeze2a 200 GPC system equipped with a 2414 refractive index (RI) detector using polystyrene as the standard and tetrahydrofuran (THF) as the eluent at a flow rate of 1.0 mL min−1. Fourier transform infrared (FT-IR) spectra were recorded on a Nicolet spectrometer with KBr pellets. Differential scanning calorimetry (DSC) analysis was performed using a TA Instrument DSC Q200 at a heating rate of 10 °C min−1 in a nitrogen atmosphere with a flow rate of 50 mL min−1. Thermogravimetric analysis (TGA) was carried out on a TG 209F1 apparatus at a heating rate of 10 °C min−1 in a nitrogen atmosphere with a protective flow rate of 10 mL min−1 and a purge flow rate of 50 mL min−1. Dielectric properties were investigated using a 4294A precision impedance analyzer (Agilent) via the noncontact method in a range of frequencies from 40 Hz to 30 MHz at room temperature. Ultraviolet-visible-near-infrared (UV-vis-NIR) spectra were recorded on a Varian CARY 5000 spectrometer at room temperature with a scan rate of 600 nm min−1. Static contact angles were obtained using a JC2000C contact angle meter of Shanghai Zhongchen Equipment Ltd, China, at room temperature and ambient humidity. Surface roughness of the polymer films was measured by atomic force microscopy (AFM) using an environment control scanning probe microscope (Nanonavi Esweep) at room temperature in AC (tapping) mode in a 10 μm × 10 μm area. Dynamic mechanical analysis (DMA) was performed at a heating rate of 5 °C min−1 in air using a Mettler Toledo DMA/SDTA861e instrument.
Synthesis of monomer BCB-NB
n-Butyllithium (45 mL, 2.5 M in hexane) was added dropwise into a solution of 4-bromobenzocyclobutene (20.15 g, 0.11 mol) in THF (200 mL) at −78 °C. After addition, the mixture was stirred at this temperature for 3 h, and a solution of 5-ethoxydimethylsilyl-2-norbornene (21.6 g, 0.11 mol) in THF (20 mL) was added. The mixture was naturally warmed to room temperature (about 22 °C), stirred at this temperature for an additional 12 h, and quenched by adding deionized water (200 mL). The resulting mixture was extracted with n-hexane. After removing the solvent under reduced pressure, the residue was purified by column chromatography on silica gel using n-hexane as the eluent. Pure BCB-NB was obtained as a colorless liquid with a yield of 78%. 1H NMR (CDCl3, 400 MHz), δ (ppm) 7.34–7.38 (t, 1H), 7.20–7.22 (d, 1H), 7.04–7.06 (d, 1H), 5.90–6.15 (m, 2H), 3.19 (s, 4H), 2.78–2.94 (m, 2H), 0.58–1.94 (m, 5H), 0.12–0.29 (m, 6H). 13C NMR (CDCl3, 100 MHz), δ (ppm) 146.90, 146.72, 145.54, 145.47, 138.58, 138.27, 137.36, 135.66, 134.18, 133.50, 132.27, 132.06, 127.71, 127.52, 121.96, 121.91, 51.65, 46.95, 45.13, 43.19, 42.72, 42.62, 30.04, 29.87, 27.59, 27.55, 25.01, 24.86, −2.31, −2.68, −2.95, −3.09. HRMS-EI (m/z): calcd, 254.1491, found, 254.1497.
Polymerization of BCB-NB
The Grubbs II catalyst (0.14 g, 0.17 mmol) was added to a solution of BCB-NB (4.25 g, 16.7 mmol) in THF (80 mL), and the obtained mixture was stirred at room temperature for 4 h. After being poured into methanol (800 mL), the precipitate was filtered and dried under vacuum. BCB-PNB was thus prepared as a white fiber-like solid (4.22 g). 1H NMR (CDCl3, 400 MHz), δ (ppm) 7.35 (1H), 7.20 (1H), 7.04 (1H), 5.13–5.27 (2H), 3.18 (4H), 1.07–2.63 (7H), 0.25 (6H). 13C NMR (CDCl3, 100 MHz), δ (ppm) 146.27, 144.82, 137.61, 136.47, 133.34, 131.72, 127.19, 121.22, 31.70–44.58, 29.28, −2.84, −4.76. Anal. calcd: C, 80.25; H, 8.72. Found: C, 80.11; H, 8.61.
Preparation of a free-standing polymer film
A solution of linear BCB-PNB in 1,1,2,2-tetrachloroethane (50 mg mL−1) was dropped onto the surface of a glass sheet, followed by removal of the solvent at 130 °C on a hot plate. A free-standing BCB-PNB film was thus obtained after being peeled off from the glass surface.
A crosslinked BCB-PNB film was prepared according to the following procedure. A BCB-PNB film on a glass sheet was allowed to be heated at 250 °C for 3 h in argon. After being cooled to room temperature, a crosslinked free-standing BCB-PNB film was obtained when the glass sheet was removed.
Preparation of BCB-PNB and cross-linked films on silicon wafers
A solution of linear BCB-PNB in mesitylene (50 mg mL−1) was spin-coated onto silicon wafers to prepare BCB-PNB films. After treatment at 250 °C for 3 h, the cross-linked BCB-PNB films were obtained, which were then used for the measurement of the surface morphology and static water contact angle.
Results and discussion
As shown in Scheme 1, monomer BCB-NB is easily prepared in the presence of n-BuLi. Polymerization of BCB-NB is carried out using the Grubbs II catalyst in THF at room temperature.26,38,39 After being precipitated in methanol, polymer BCB-PNB is obtained in a quantitative yield. The GPC result (Fig. 1) indicates that BCB-PNB has a number average molecular weight (Mn) of 93
000 g mol−1 with a PDI of 1.65. The chemical structure of BCB-PNB was characterized using NMR (Fig. 2 and 3) and elemental analysis. As can be seen from Fig. 3, the signals of the cyclic alkene at 138.58, 135.66, 134.18 and 133.50 ppm (both endo and exo structure) disappear and a new wide peak (133.44–133.96 ppm) appears, which is attributed to the internal alkene groups in the main chain of BCB-PNB after ROMP. Besides, the elemental analysis also gave a positive result. All data are consistent with the proposed structure of BCB-PNB.
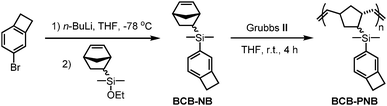 |
| Scheme 1 Synthesis of benzocyclobutene-functionalized norbornene (BCB-NB) and polynorbornene (BCB-PNB). | |
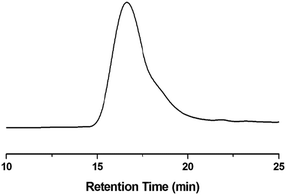 |
| Fig. 1 GPC trace of BCB-PNB using THF as the eluent. | |
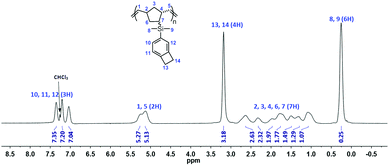 |
| Fig. 2
1H NMR spectrum of BCB-PNB (400 MHz, CDCl3). | |
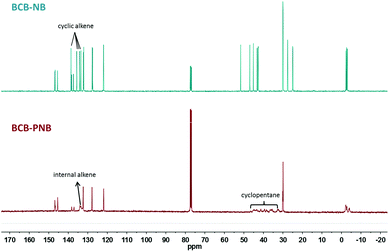 |
| Fig. 3
13C NMR spectra of BCB-NB (endo and exo) and BCB-PNB (100 MHz, CDCl3). | |
Because of the high flexibility of both the PNB main chain and the side chains with BCB units, BCB-PNB is easily soluble in common organic solvents, and the details are listed in Table 1. Good solubility in common organic solvents endows the linear BCB-PNB with good processability, which is very important for the following post-polymerization step.
Table 1 Solubility of BCB-PNB before and after thermo-crosslinking
|
Solvents |
CHCl3 |
Toluene |
THF |
Mesitylene |
CHCl2CHCl2 |
(−) insoluble at heating; (+) soluble at heating; (++) soluble at room temperature. |
Before |
++ |
+ |
++ |
++ |
++ |
After |
− |
− |
− |
− |
− |
BCB has been widely used as a crosslinkable group to prepare thermosetting polymers via catalyst-free thermo-polymerizations. When vinyl groups are present, the vinyl groups may react with the o-quinodimethane intermediate produced from a thermo-induced ring-opening reaction of BCB.37 As a result, crosslinked networks with a six-membered ring structure are formed.37,40,41 In our case, DSC traces and FT-IR spectroscopy were used to monitor the crosslinking reaction of BCB-PNB. Two crosslinking steps can be obviously observed at the first scan of DSC (Fig. 4). The first step is attributed to a [4+2] reaction between the internal alkene and the thermo-induced BCB four-membered ring-opening intermediate (o-quinodimethane).42 With this cycloaddition occurring, the polymer chains become so rigid that the o-quinodimethane intermediates are unable to reach the vinyl groups in the main chain any more. Thus, the second step of the crosslinking procedure is mainly the dimerization or polymerization between the o-quinodimethane intermediates. At the second scan, no obvious exothermic peak is observed, illustrating the complete transformation of BCB groups.42,43
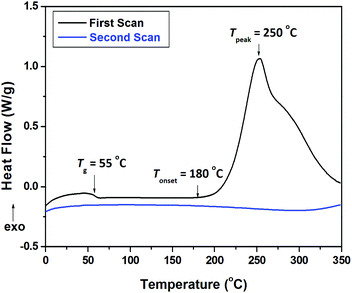 |
| Fig. 4 DSC traces of BCB-PNB at a heating rate of 10 °C min−1 in N2. | |
The crosslinking procedure is also investigated using FT-IR spectroscopy (Fig. 5). It is seen that the characteristic peak of a BCB group at 1460 cm−1 disappears completely undergoing a post-polymerization. The peak of the vinyl groups at 970 cm−1 decreases dramatically but it does not disappear completely. These results illustrate the two-step post-polymerization procedure of BCB-PNB. In order to well understand the post-polymerization process of BCB-PNB, a schematic procedure is given, as described in Scheme 2.
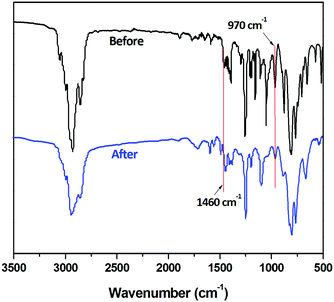 |
| Fig. 5 FT-IR spectra of BCB-PNB before (black line) and after (blue line) thermo-crosslinking. | |
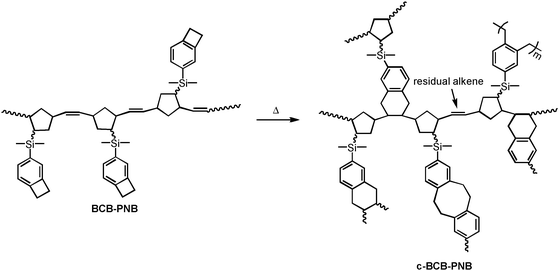 |
| Scheme 2 Schematic conversion process of BCB-PNB. | |
The high molecular weight and good solubility endows BCB-PNB with excellent film-forming ability. A casting method was used for the preparation of a free-standing BCB-PNB film, as described in the Experimental section. As can be seen from Fig. 6b, the free-standing BCB-PNB film is highly transparent with a smooth surface. After being crosslinked at high temperature, this film becomes yellow, whereas it is still highly transparent and uniform (Fig. 6c).
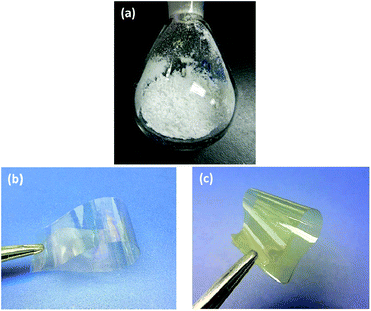 |
| Fig. 6 Images of (a) the BCB-PNB polymer powder, (b) the free-standing BCB-PNB film, and (c) the crosslinked BCB-PNB film. | |
UV-vis-NIR spectra were used to measure the transparency of the free-standing films before and after thermo-crosslinking in a range of wavelengths from 1600 to 200 nm. As can be seen from Fig. 7, a BCB-PNB film exhibits excellent transparency with a transmittance of 90% in the visible and NIR region. The transmittance is sharply decreased to near 0% from 400 nm to 300 nm, which is mainly resulting from the total absorption of the aromatic ring in the side chains. After post-polymerization, the crosslinked BCB-PNB film also exhibits a high transmittance of 90% at a wavenumber higher than 600 nm.
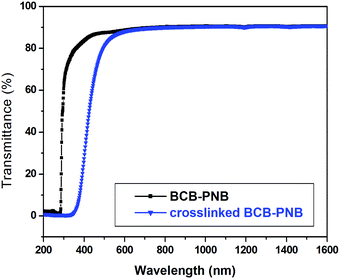 |
| Fig. 7 UV-vis-NIR spectra of a free-standing BCB-PNB film before and after thermo-crosslinking. | |
In order to assess the uniformity of the polymer films before and after crosslinking, the films of BCB-PNB on silicon wafers were prepared by a spin-coating route, as described in the Experimental section. Fig. 8 presents the atomic force microscope (AFM) results of a BCB-PNB film on a silicon wafer before and after post-polymerization. Both BCB-PNB and the crosslinked films are highly uniform with an area of 2 μm × 2 μm. Good film-forming ability is beneficial for application in the manufacture of large-area devices.
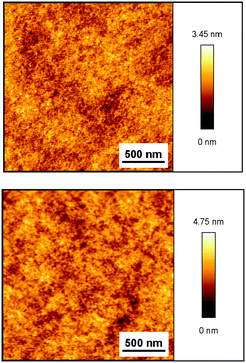 |
| Fig. 8 AFM images of BCB-PNB (top) and crosslinked BCB-PNB (down). | |
The heat-resistance of BCB-PNB and crosslinked BCB-PNB was investigated by dynamic thermomechanical analysis (DMA) and thermomechanical analysis (TMA). Fig. 9 depicts the measurement results, and the detailed data are listed in Table 2. As shown in Fig. 9a, BCB-PNB exhibits a Tg of lower than 60 °C due to the high flexibility of the polymer main chain. Such a low Tg is consistent with those of conventional ROMP-type PNBs.27,44–46 Interestingly, crosslinked BCB-PNB exhibits a Tg of up to 400 °C (Fig. 9b). Such a Tg is much higher than those of the previously reported PNBs prepared via ROMP. This is attributed to the high crosslinking density between the polymer chains when BCB-PNB is post-polymerized. In particular, the crosslinked structure also endows the polymer with low thermal expansion coefficient (CTE). As depicted in Fig. 9d, crosslinked BCB-PNB exhibits a CTE of about 63.6 ppm °C−1, implying its good dimensional stability. Both the high Tg and low CTE demonstrate that crosslinked BCB-PNB can be used at high temperature.
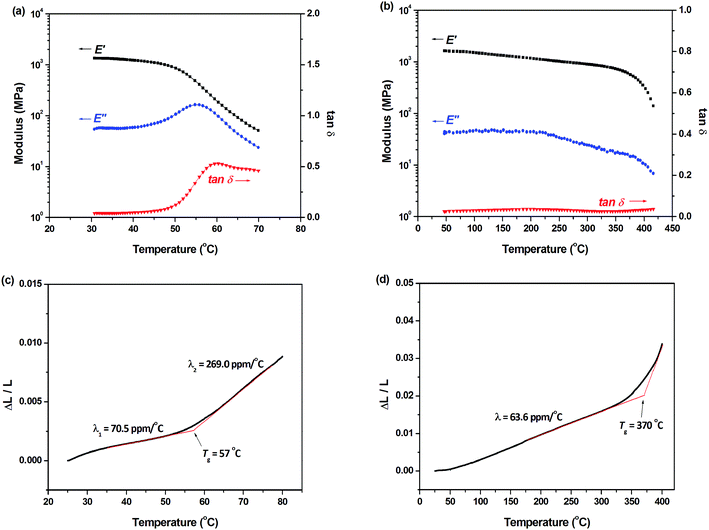 |
| Fig. 9 DMA curves of BCB-PNB before (a) and after (b) post-polymerization (E′ and E′′ represent the storage modulus and loss modulus, respectively), TMA curves of BCB-PNB before (c) and after (d) post-polymerization. | |
Table 2 Thermal properties of BCB-PNB and crosslinked BCB-PNB
Polymer |
T
g
(°C) |
CTEb (ppm °C−1) |
T
5d
(°C) |
DSC |
DMA |
TMA |
Glass transition temperature measured by DSC, DMA, and TMA, respectively.
Linear thermal expansion coefficient (λ) before the glass transition temperature.
5 wt% loss temperature under a nitrogen atmosphere measured by TGA.
|
BCB-PNB
|
55 |
59 |
57 |
70.5 |
— |
Crosslinked BCB-PNB |
— |
>400 |
370 |
63.6 |
430 |
The thermostability of crosslinked BCB-PNB was studied using thermogravimetric analysis (TGA), and the results are presented in Fig. 10. It is seen that crosslinked BCB-PNB displays a 5% weight loss up to 430 °C, which is also much higher than those of many previously reported ROMP-type PNBs.29,47
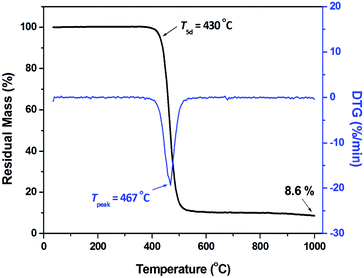 |
| Fig. 10 TGA traces of crosslinked BCB-PNB at a heating rate of 10 °C min−1 in N2. | |
The above-mentioned results clearly indicate that the heat-resistance and thermostability of ROMP-type PNB can be effectively improved by introducing thermo-crosslinkable BCB groups to the polymer side chains after a thermo-induced post-polymerization route.
It is noted that BCB-containing polymers and oligomers usually show low dielectric constants (Dk). For the investigation of the dielectric behaviors of crosslinked BCB-PNB, the Dk and dissipation factor (Df) in frequencies ranging from 40 Hz to 30 MHz were detected. As can be seen from Fig. 11, crosslinked BCB-PNB exhibits a Dk of about 2.60 with low Df, which is comparable to that of commercial CYCLOTENE. On the basis of the excellent film-forming ability of BCB-PNB, this new polymer has an attractive prospect as a dielectric material for microelectronic components or thin-layer packaging.
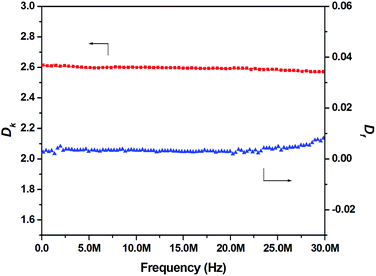 |
| Fig. 11 Dielectric properties of crosslinked BCB-PNB at room temperature. | |
The hydrophobicities of the BCB-PNB and crosslinked BCB-PNB films were characterized using the static water contact angle (WCA) depicted in Fig. 12. As shown in Fig. 12, both the linear BCB-PNB and the crosslinked BCB-PNB films show high WCA values, suggesting their good hydrophobicity. This behavior is beneficial for maintaining good dielectric properties of the polymers under wet conditions.
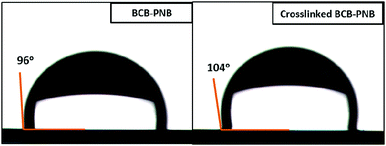 |
| Fig. 12 Static water contact angle of water on the surface of the BCB-PNB and crosslinked BCB-PNB films on silicon wafers. | |
Conclusions
In summary, a BCB-functionalized PNB (BCB-PNB) was successfully prepared via a standard ROMP procedure. This polymer showed good solubility and film-forming ability. After a post-polymerization process at high temperature, BCB-PNB was converted to a crosslinked network, which exhibited good heat-resistance and high thermostability, as well as low dielectric constant. This work provides a facile and effective route for the preparation of high-performance ROMP-type PNBs used in the microelectronics industry.
Conflicts of interest
There are no conflicts to declare.
Acknowledgements
Financial support from the Ministry of Science and Technology of China (2015CB931900), the Natural Science Foundation of China (NSFC, No. 21574146, 21504103 and 21774140), the Science and Technology Commission of Shanghai Municipality (16JC1403800), and the Strategic Priority Research Program of the Chinese Academy of Sciences (Grant No. XDB 20020000) is gratefully acknowledged.
References
- D. T. Welna, D. A. Stone and H. R. Allcock, Chem. Mater., 2006, 18, 4486–4492 CrossRef.
- E. Elacqua, D. S. Lye and M. Weck, Acc. Chem. Res., 2014, 47, 2405–2416 CrossRef PubMed.
- K. R. Gmernicki, E. Hong, C. R. Maroon, S. M. Mahurin, A. P. Sokolov, T. Saito and B. K. Long, ACS Macro Lett., 2016, 5, 879–883 CrossRef.
- S. Mukherjee, J. Das Sarma and R. Shunmugam, ACS Omega, 2016, 1, 755–764 CrossRef.
- S. Mukherjee, H. Dinda, I. Chakraborty, R. Bhattacharyya, J. Das Sarma and R. Shunmugam, ACS Omega, 2017, 2, 2848–2857 CrossRef.
- V. Rao N, M. N. Ganivada, S. Sarkar, H. Dinda, K. Chatterjee, T. Dalui, J. Das Sarma and R. Shunmugam, Bioconjugate Chem., 2014, 25, 276–285 CrossRef PubMed.
- V. Rao N, H. Dinda, M. N. Ganivada, J. Das Sarma and R. Shunmugam, Chem. Commun., 2014, 50, 13540–13543 RSC.
- Y. Gao, Y. Zhao, Y. C. Li, Q. Huang, T. E. Mallouk and D. Wang, J. Am. Chem. Soc., 2017, 139, 15288–15291 CrossRef PubMed.
- K. Feng, C. Zuniga, Y.-D. Zhang, D. Kim, S. Barlow, S. R. Marder, J. L. Brédas and M. Weck, Macromolecules, 2009, 42, 6855–6864 CrossRef.
- S. Mukherjee, D. Patra, H. Dinda, I. Chakraborty, L. Shashank, R. Bhattacharyya, J. Das Sarma and R. Shunmugam, Macromolecules, 2016, 49, 2411–2418 CrossRef.
- Y. Yoshida, J. Mohri, S. Ishii, M. Mitani, J. Saito, S. Matsui, H. Makio, T. Nakano, H. Tanaka, M. Onda, Y. Yamamoto, A. Mizuno and T. Fujita, J. Am. Chem. Soc., 2004, 126, 12023–12032 CrossRef PubMed.
- S. Sutthasupa, M. Shiotsuki, T. Masuda and F. Sanda, J. Am. Chem. Soc., 2009, 131, 10546–10551 CrossRef PubMed.
- C. W. Bielawski, D. Benitez, T. Morita and R. H. Grubbs, Macromolecules, 2001, 34, 8610–8618 CrossRef.
- E. S. Finkelshtein, K. L. Makovetskii, M. L. Gringolts, Y. V. Rogan, T. G. Golenko, L. E. Starannikova, Y. P. Yampolskii, V. P. Shantarovich and T. Suzuki, Macromolecules, 2006, 39, 7022–7029 CrossRef.
- C. Janiak and P. G. Lassahn, J. Mol. Catal. A: Chem., 2001, 166, 193–209 CrossRef.
- K. Vijayakrishna and G. Sundararajan, Polymer, 2006, 47, 8289–8296 CrossRef.
- N. R. Grove, P. A. Kohl, S. A. B. Allen, S. Jayaraman and R. Shick, J. Polym. Sci., Part B: Polym. Phys., 1999, 37, 3003–3010 CrossRef.
- B. Liu, Y. Li, A. S. Mathews, Y. Wang, W. Yan, S. Abraham, C.-S. Ha, D.-W. Park and I. Kim, React. Funct. Polym., 2008, 68, 1619–1624 CrossRef.
- D.-G. Kim, A. Bell and R. A. Register, ACS Macro Lett., 2015, 4, 327–330 CrossRef.
- A. Ravasio, L. Boggioni and I. Tritto, Macromolecules, 2011, 44, 4180–4186 CrossRef.
- S. J. Diamanti, P. Ghosh, F. Shimizu and G. C. Bazan, Macromolecules, 2003, 36, 9731–9735 CrossRef.
- G. M. Miyake, R. A. Weitekamp, V. A. Piunova and R. H. Grubbs, J. Am. Chem. Soc., 2012, 134, 14249–14254 CrossRef PubMed.
- T. P. Lin, A. B. Chang, H. Y. Chen, A. L. Liberman-Martin, C. M. Bates, M. J. Voegtle, C. A. Bauer and R. H. Grubbs, J. Am. Chem. Soc., 2017, 139, 3896–3903 CrossRef PubMed.
- S. C. Radzinski, J. C. Foster, R. C. Chapleski, Jr., D. Troya and J. B. Matson, J. Am. Chem. Soc., 2016, 138, 6998–7004 CrossRef PubMed.
- A. M. Anderson-Wile, G. W. Coates, F. Auriemma, C. De Rosa and A. Silvestre, Macromolecules, 2012, 45, 7863–7877 CrossRef.
- Y. Xia, J. A. Kornfield and R. H. Grubbs, Macromolecules, 2009, 42, 3761–3766 CrossRef.
- M. S. Ganewatta, W. Ding, M. A. Rahman, L. Yuan, Z. Wang, N. Hamidi, M. L. Robertson and C. Tang, Macromolecules, 2016, 49, 7155–7164 CrossRef.
- B. Pulamagatta, S. Pankaj, M. Beiner and W. H. Binder, Macromolecules, 2011, 44, 958–965 CrossRef.
- M. A. Rahman, H. N. Lokupitiya, M. S. Ganewatta, L. Yuan, M. Stefik and C. Tang, Macromolecules, 2017, 50, 2069–2077 CrossRef.
- Y. Shao, C. Lavigueur and X. X. Zhu, Macromolecules, 2012, 45, 1924–1930 CrossRef.
- Z.-L. Li, F.-R. Zeng, H.-C. Li, W.-L. Zeng, H.-C. Cai and H. Jiang, Polymer, 2017, 121, 155–164 CrossRef.
- R. A. Kirchhoff and K. J. Bruza, Prog. Polym. Sci., 1993, 18, 85–185 CrossRef.
- J. Yang, S. Liu, F. Zhu, Y. Huang, B. Li and L. Zhang, J. Polym. Sci., Part A: Polym. Chem., 2011, 49, 381–391 CrossRef.
- S. Tian, J. Sun, K. Jin, J. Wang, F. He, S. Zheng and Q. Fang, ACS Appl. Mater. Interfaces, 2014, 6, 20437–20443 Search PubMed.
- Y. Cheng, J. Yang, Y. Jin, D. Deng and F. Xiao, Macromolecules, 2012, 45, 4085–4091 CrossRef.
- M. E. Mills, P. Townsend, D. Castillo, S. Martin and A. Achen, Microelectron. Eng., 1997, 33, 327–334 CrossRef.
- S. F. Hahn, S. J. Martin, M. L. McKelvy and D. W. Patrick, Macromolecules, 1993, 26, 3870–3877 CrossRef.
- S. Sutthasupa, F. Sanda and T. Masuda, Macromolecules, 2009, 42, 1519–1525 CrossRef.
- N. Leventis, C. Sotiriou-Leventis, D. P. Mohite, Z. J. Larimore, J. T. Mang, G. Churu and H. Lu, Chem. Mater., 2011, 23, 2250–2261 CrossRef.
- T. Endo, T. Koizumi, T. Takata and K. Chino, J. Polym. Sci., Part A: Polym. Chem., 1995, 33, 707–715 CrossRef.
- Y. Cheng, S. Tian, Y. Shi, W. Chen, Z. Li, T. Zhu and Z. Zhang, Eur. Polym. J., 2017, 95, 440–447 CrossRef.
- H. Hu, L. Liu, Z. Li, C. Zhao, Y. Huang, G. Chang and J. Yang, Polymer, 2015, 66, 58–66 CrossRef.
- K. Cao, L. Yang, Y. Huang, G. Chang and J. Yang, Polymer, 2014, 55, 5680–5688 CrossRef.
- K. Stubenrauch, M. Sandholzer, F. Niedermair, K. Waich, T. Mayr, I. Klimant, G. Trimmel and C. Slugovc, Eur. Polym. J., 2008, 44, 2558–2566 CrossRef.
- X. Yin, Y. Qiao, M. R. Gadinski, Q. Wang and C. Tang, Polym. Chem., 2016, 7, 2929–2933 RSC.
- M. A. Amendt, L. M. Pitet, S. Moench and M. A. Hillmyer, Polym. Chem., 2012, 3, 1827–1837 RSC.
- J. Wang, X. He, H. Zhu and D. Chen, RSC Adv., 2015, 5, 43581–43588 RSC.
Footnote |
† Jiajia Wang and Junfeng Zhou contributed equally to this work. |
|
This journal is © the Partner Organisations 2018 |
Click here to see how this site uses Cookies. View our privacy policy here.