DOI:
10.1039/C8RA02699H
(Paper)
RSC Adv., 2018,
8, 24464-24469
Graphene/cardanol modified phenolic resin for the development of carbon fiber paper-based composites
Received
28th March 2018
, Accepted 21st June 2018
First published on 6th July 2018
Abstract
Carbon fiber paper-based composites (GCPC) were prepared by impregnating carbon fiber papers in a solution of graphene and cardanol modified phenolic resin (GCP). GCP was characterized by thermal gravimetric analysis (TGA), and the electrical conductivity, mechanical properties, pore distribution, and porosity of GCPC were investigated by a four-probe tester, universal testing machine, microtopography, and porous material analyzer, respectively. The results show that the electrical properties and mechanical strength of GCPC were improved with the increase of graphene and cardanol content. The porosity decreased and the proportion of small holes increased with the increase of graphene, while the porosity increased and the proportion of small holes decreased with the increase of cardanol. When the content of cardanol was 20% (mass fraction), the tensile strength of the composite reached 38.17 MPa, the resistivity reached 18.46 mΩ cm, and the porosity reached 67.46%.
1 Introduction
The proton exchange membrane fuel cell (PEMFC) has attracted extensive interests for its efficient, convenient, low-cost, stable, and environment-friendly conversion of chemical energy into electric energy.1,2 The gas diffusion layer (GDL) is a key part in the PEMFC. Currently, the GDL is mainly composed of carbon fiber papers or carbon fiber clothes. Carbon fiber is a kind of super-fiber material, with carbon forming more than 90% of its chemical composition. Carbon fiber possesses excellent conductivity, high strength, high modulus, low-temperature resistance, high-temperature resistance, good thermal conductivity, a small thermal expansion coefficient, corrosion resistance, etc.3,4 Carbon fiber paper is an important raw material for fabricating the GDL in fuel cells, and its structure and properties have an extremely important influence on the performance of PEMFCs.
Because the surface of carbon fiber is very smooth, unlike plant fiber, the laboratorial beating cannot induce fibrillation of carbon fibers. Also, unlike the formation of hydrogen bonds in plant fibers for paper production, carbon fibers cannot form hydrogen bonds. To obtain carbon fiber papers with a certain degree of strength, adhesive agents are needed.
Currently, phenolic resin is often used as a binder for producing carbon fiber papers. However, the pure phenolic resin has brittleness, poor toughness, high hardness, low heat resistance, and low strength, which greatly affect the physical properties of the material. Therefore, phenolic resin needs to be modified.
In the preparation of carbon fiber paper, the process of impregnating carbon fiber raw paper in resin, and resin curing will have a crucial impact on the performance of carbon fiber papers. In the process of resin molding, the curing temperature and molding pressure will affect the thickness and density of carbon fiber papers. Before the carbonization, if the curing of phenolic resin is complete, the carbon fiber paper will less likely to have pores and cracks. The resin in carbon fiber papers can thus give full play to the bonding effect, thereby enhancing the processing performance of carbon fiber papers. In the process of carbon fiber paper curing, in case the curing temperature is too low, curing time is too long, or curing is incomplete, will lead to the reduced rate of phenolic resin residue carbon. When curing temperature is too high, the resin will be too fluid, which leads to the resin content being uncontrollable.
Previous studies have proven that adding graphene into phenolic resin will promote material's conductivity, while keeping its role of reinforcement.5,6 Modifying phenolic resin with cardanol can significantly improve the toughness and heat resistance of materials.7 However, there are no previous reports on the modification of phenolic resins with both graphene and cardanol.
In this study, graphene/cardanol modified phenolic resin (GCP) was prepared by synergistic modification of phenolic resin with cardanol and graphene. Carbon fiber paper raw papers were prepared by a wet papermaking technology and further impregnated in GCP. After hot pressing and carbonization, a carbon fiber paper-based composite material (GCPC) was obtained. The structure, mechanical properties, electrical properties, and pore distribution of GCPCs were characterized by a variety of modern testing techniques. It was expected to obtain carbon fiber paper-based composites with high mechanical and electrical properties, along with uniform pore size and pore distribution. Also, it was expected to provide the theoretical basis for the development of efficient carbon fiber composite materials in the future.
2 Materials and methods
2.1 Materials
Phenol (99.0%), NaOH, HNO3, H2SO4, ethanol (95%), and ammonia (analytical grade) were purchased from Sinopharm Chemical Reagent Co., Ltd. Anionic polyacrylamide was obtained from French SNF Company. Short cut polyacrylonitrile carbon fiber (CF, length 5 mm) and graphene were purchased from a company in Jiangsu, China. Cardanol (50–55%), formaldehyde (37–40%), and phenolic resin were purchased from Shandong Chemical Co., Ltd. (Shandong, China).
2.2 Methods
2.2.1 Preparation of graphene/cardanol modified phenolic resin (GCP). A certain amount of phenol (60 g), formaldehyde (62 g), and ammonia (3.2 g) were added in a three-necked flask, which was placed inside a water bath with constant stirring. When the temperature reached at 70 °C, the solution was incubated for 3 h, and then a certain amount of cardanol was slowly added to the reaction system. The temperature was further raised to 103 °C and the reaction was kept for another 2.5 hours, before pouring the products out at hot conditions. Cardanol modified phenolic resin was obtained when the product was cooled down.8A certain amount of graphene was placed in a beaker, in which concentrated sulfuric acid and concentrated nitric acid were added and mixed at a volume ratio of 3
:
1. The solution was treated with ultrasonication at 40 °C for 2–3 hours before vacuum filtration. Graphene after acid treatment was washed to neutral and then vacuum dried at 100 °C. The surface of acidified graphene was grafted with hydroxyl and carboxyl groups, which increased the negative charge of graphene and enhanced the electrostatic repulsion between graphene, thus improving the dispersion of graphene in the resin.
The modified graphene was added to the above cardanol phenolic resin solution, which was ultrasonicated at 70 °C for 4 h to generate a graphene modified cardanol phenolic resin solution. The solution was stored as impregnating solution.
2.2.2 Preparation of graphene/cardanol-modified phenolic resin-based carbon fiber paper-based composite (GCPC). The wet papermaking technology was used to prepare carbon fiber raw papers, which were subsequently immersed in the above-mentioned impregnating solution. GCPC was obtained after drying, hot-pressing, and heat-treatment at 1800 °C.9
2.3 Materials characterization and testing
The samples were analyzed by the SDT Q600 thermogravimetric analyzer manufactured by American TA Company at a heating rate of 10 °C min−1. The tensile mechanical properties of the composites were tested by using the 3385H electronic universal material testing machine manufactured by INSTRON, USA at a scanning rate of 2 mm min−1. The electrical properties of the composites were tested using the SZT-2A four-probe tester (FPT) manufactured by Suzhou Tongchuang Electronics Co., Ltd. The pore diameter of the composite material was tested and analyzed by using the CFP-1100A porous material analyzer produced by PMI Company of United States.
2.3.1 Porosity test of carbon fiber paper-based composites. The dry–wet method was used to determine the porosity of GCPC material. After drying at 60 °C for 24 hours, the mass of the GCPC material was recorded as W1. Then, the material was soaked in absolute ethanol for 12 h, and the mass was weighed as W2.The porosity of GCPC can be calculated by:
|
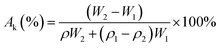 | (1) |
while
Ak is the porosity of GCPC,
W2 is the weight of wet GCPC,
W1 is the weight of dry GCPC,
ρ2 is the density of absolute ethanol, and
ρ1 is the average density of GCPC.
3 Results and discussions
3.1 Effect of phenolic resin modification on carbon residue rate
The pyrolysis behavior of resin during curing was analyzed with the thermogravimetric analysis. In Fig. 1, curves P and GCP stand for the weight loss of phenolic resin before and after modification, respectively. Based on Fig. 1, we can see that phenolic resin without modification shows a rapid weight loss starting at 25 °C and a slight decrease in the rate of weight loss starting at 180 °C, with a carbon residue of 40.1% at 800 °C. GCP (with 5% of graphene and 20% of cardanol) thermal degradation can be roughly divided into three stages. The first stage is in a temperature range of 30–400 °C, during which mainly occurs the release of water and other free small molecules. The second stage is the temperature range between 400–600 °C, in which the resin decomposes to produce H2O, CH4, CO, CO2, benzene, phenol, alkyl phenol, and other substances. The second stage is the main stage of weight loss. The third stage is between 600–800 °C, in which the resin is carbonized, mainly releasing H2, and the rate of weight loss increases slightly, but the rate of change is small. When the temperature is about 800 °C, the TG curve becomes flat, indicating the rate of weight loss is close to zero and the phenolic resin is fully decomposed to form a carbonized structure. During this process, the benzene rings gradually move closer with each other to form a multi-benzene fused ring structure, and carbon residues form a condensed ring. Finally, a deoxygenated carbonaceous turbulent structure is formed. The residual carbon not only helps increasing the conductivity of carbon fiber papers, but also increases the strength of carbon fiber papers.10–13 At 800 °C, the residual carbon of P is 40.1% and the residual carbon of GCP is 50.9%. Compared with P, GCP has higher decomposition temperature and higher char yield, which is beneficial to the enhanced conductivity, uniform gas release, mitigated cracking, and reduced delamination.
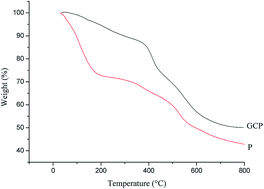 |
| Fig. 1 TG curves of phenolic resin before and after modification. | |
3.2 Effects of GCP with different graphene and cardanol contents on GCPC pore size
Effects of phenolic resin with different graphene contents on the pore size of carbon fiber paper-based composites (cardanol content is 0) are shown in Fig. 2 and 3. With the increase of graphene content, the pore size of carbon fiber paper-based composites decreases, and porosity shows a downward trend. The addition of graphene increases the tightness of the carbon fiber paper and reduces the porosity of the material. Furthermore, graphene not only fills the pores in the matrix left by the graphitization process, but also fills the gaps between the matrix and fibers, as well as gaps between fibers and fibers, so that the porosity of the carbon fiber paper-based composite material decreases, and the ratio of small holes increases.14 The gas diffusion layer should have an appropriate porosity and pore distribution to benefit the transport of gas and liquid. When the graphene content is 5% as shown in Fig. 2 and 3, porosity changes significantly, which is not beneficial to the transport of gas and liquid. The graphene content of 5% is used as a comparison.
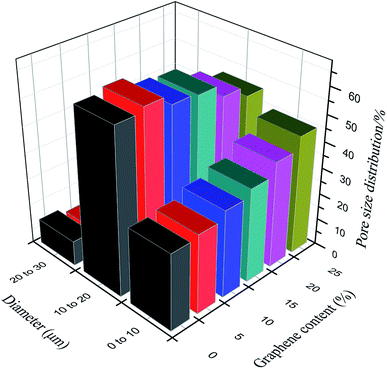 |
| Fig. 2 Effects of phenolic resin with different graphene contents on the pore size of carbon fiber paper-based composites (cardanol content is 0). | |
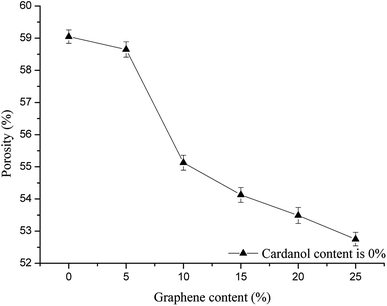 |
| Fig. 3 Effects of phenolic resin with different graphene contents on the porosity of carbon fiber paper-based composites (cardanol content is 0). | |
Effects of GCP with different cardanol contents on GCPC pore size (graphene content was fixed at 5%) are shown in Fig. 4 and 5. From the overall pore size distribution, as the cardanol content increases, the proportion of small pores decreases, while the proportion of large pores increases, along with the narrowing of pore size distribution and increasing of porosity. When cardanol is used to modify phenolic resin, these two chemicals can undergo a variety of reactions which generate strong chemical bonds and result in a cross-linked network. After pyrolytic graphitization of cardanol modified phenolic resin at high temperature, most of the decomposition products would escape in the form of gas, leaving holes in the matrix.
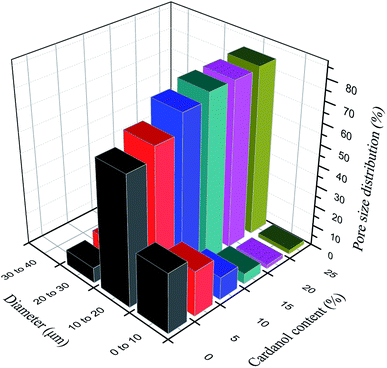 |
| Fig. 4 Effects of GCP with different cardanol contents on GCPC pore size (graphene content is fixed at 5%). | |
 |
| Fig. 5 Effects of GCP with different cardanol contents on GCPC porosity (graphene content is fixed at 5%). | |
With the increase of cardanol contents, more cardanol is decomposed into gas by the graphitization at high temperature to form pores in the matrix. The formation of large holes is due to an increase in small pores leading to a decrease in the spacing of pores. Compared with pure carbon fiber materials, GCPC has better pore structure, reduced pore size, and more uniform pore distribution. The reduction of material porosity and pore size can significantly improve the filtration efficiency.
3.3 Effects of GCP with different graphene and cardanol contents on tensile strength of GCPC
Fig. 6 shows the effects of different graphene contents and different cardanol contents in phenolic resin on the tensile strength of carbon fiber paper-based composites. It can be seen from the figure that as the graphene content increases, the tensile strength of carbon fiber paper increases. The added graphene acts as a repairer, filling the gaps between fibers and matrix. It can be seen that cardanol and graphene co-modified carbon fiber composites possess superior tensile strength compared with that of carbon fiber composites modified with a single component. The tensile strength of GCPC increases with the increase of cardanol content. GCPC reaches the best tensile strength of 38.13 MPa when the content of cardanol is 20%, which is significantly higher than that of GCPC (31.47 MPa) with single addition of graphene, or with single addition of cardanol (32.18 MPa), or pure carbon fiber paper-based composite materials (30.13 MPa). Compared to tensile strength of GCPC modified with only graphene, only cardanol, and pure carbon fiber paper materials, the tensile strength of GCPC modified with both graphene and cardanol increases 21.2%, 18.5%, and 26.6%, respectively.
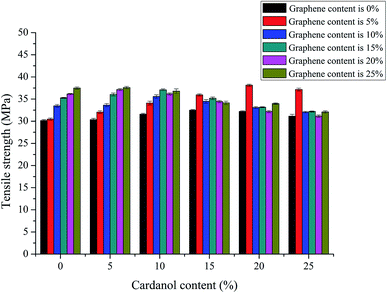 |
| Fig. 6 Effects of different graphene contents (graphene content is 0%, 5%, 10%, 15%, 20%, 25%) and different cardanol contents (cardanol content is 0%, 5%, 10%, 15%, 20%, 25%) in phenolic resin on the tensile strength of carbon fiber paper-based composites. | |
Cardanol modified phenolic resins usually show toughness compared to common phenolic resin, due to the long aliphatic chain of cardanol decreasing the cross-linkage density after the modified resin curing. With the increase of cardanol content, the number of functional groups involved in the reaction increases, promotes the uniform distribution of pores and facilitates the molding process.15–17 Furthermore, it prevents the particles from agglomerating, effectively relieves the stress, and blocks the crack propagation, thus increasing the tensile strength of the material. However, although cardanol with flexible long chains can improve the toughness of the material, too much cardanol content will result in steric hindrance and poor dispersion, which lead to the crack growth and expansion inside composite materials, generating a rapid growth of stress and fracture of fibers, resulting in decreased strength.
3.4 Effect of GCP with different graphene and cardanol contents on microtopography of GCPC
It can be seen from the SEM of the fracture of the carbon fiber paper in Fig. 7 that the cardanol content has a significant effect on the interface bonding between the carbon fiber paper and the resin. Fig. 7(a), it can be observed that carbon fiber and resin are poorly bonded and the interfacial bonding force is weak. As can be seen from Fig. 7(b–f), with the content of cardanol increasing from 0% to 25%, the adhesion between the fiber and the resin becomes increasingly tight and the interfacial bonding gradually becomes stronger. Due to the increase of the content of cardanol, the chemical bonding between the carbon fiber and the phenolic resin is facilitated, the carbon fiber and the phenolic resin play a connecting role, also the binding between the carbon fiber and the resin becomes increasingly tight, that is, the interface bonding pyramidally good. However, if the interface strength between the carbon fiber and the resin is too large. When the external force occurs, the internal stress of the carbon fiber paper is concentrated, and the internal matrix generates fatigue cracks. The deformation does not transfer at the interface and the strength of the carbon fiber paper is decreased. This is consistent with the effects of GCP with different cardanol contents on tensile strength of GCPC.
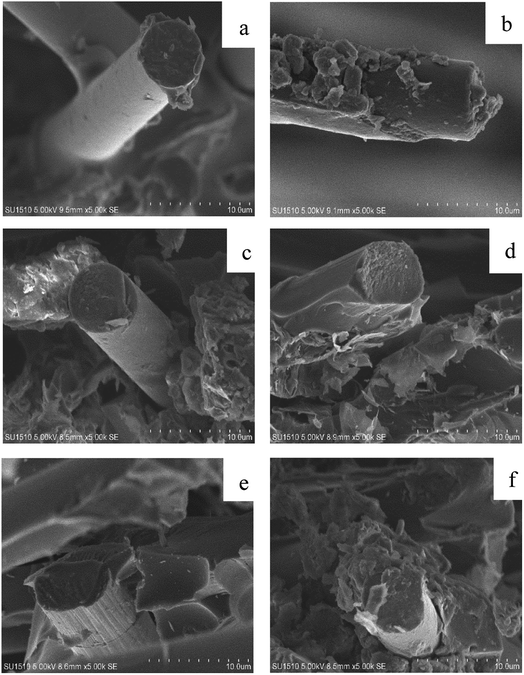 |
| Fig. 7 Fracture morphology of carbon fiber paper with different cardanol content. (a) Cardanol content is 0, (b) cardanol content is 5%, (c) cardanol content is 10%, (d) cardanol content is 15%, (e) cardanol content is 20%, (f) cardanol content is 25%. | |
3.5 Effects of GCP with different graphene and cardanol contents on electrical conductivity of GCPC
Fig. 8 shows the effects of different graphene contents in phenolic resin on the electrical conductivity of GCPC (cardanol content was 0). Fig. 9 shows the effects of GCP with different cardanol contents on the electrical conductivity of GCPC (graphene content was fixed at 5%). It can be seen from the figures that the conductivity of the composite materials increases with the increase of graphene and cardanol contents. When the content of cardanol exceeds 20%, however, the conductivity only increases slightly. This result suggests the saturation of conductivity of GCPC at high content of cardanol. The contact of conductive particles generates a chain-like conductive network. When the conductive network is close to completion, the increase of conductivity is slow.
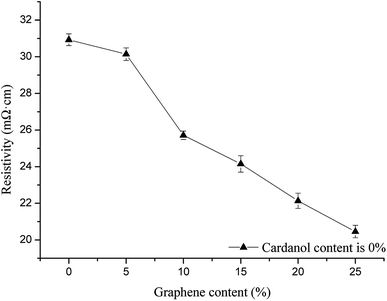 |
| Fig. 8 Effects of different graphene content in phenolic resin on electrical conductivity of carbon fiber paper-based composites (cardanol content is 0). | |
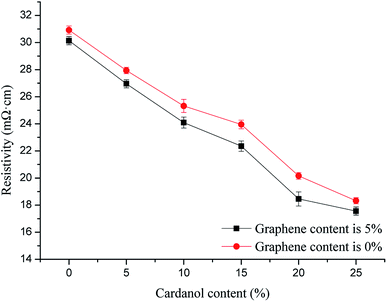 |
| Fig. 9 Effects of GCP with different cardanol contents on electrical conductivity of GCPC (graphene content is fixed at 5%). | |
With the increase of cardanol contents, the number of functional groups from cardanol that can react with phenolic resin's reactive groups also increases, so the interfacial binding between fiber and matrix becomes stronger, favoring the contact of conductive particles with each other to form a tunneling current with decreased resistivity and improved conductivity. Furthermore, graphene has excellent conductivity and is able to generate tunneling current with free moving electrons, providing a continuous conductive path in the material.
4 Conclusions
Mechanical tests, electrical tests and pore tests show that the tensile strength and electrical properties of carbon fiber paper-based composites impregnated with graphene and cardanol-modified phenolic resin have been significantly improved, with more uniformly distributed pores, decreased proportion of small pores, and increased porosity. The tensile strength of carbon fiber paper-based composites increases first and then decreases with the increase of graphene and cardanol, the resistivity decreases with the increase of the content of graphene and cardanol, and the porosity increases with the content of graphene and cardanol in composites. When the cardanol content is 20%, the carbon fiber composites show the best tensile strength of 38.17 MPa, which is 26.68% higher than that of pure carbon fiber composites (30.13 MPa). The composites also show a resistivity of 18.46 mΩ cm and a porosity of 67.46%.
Conflicts of interest
There are no conflicts to declare.
References
- F. Jaouen, E. Proietti and M. Lefevre, et al., Recent advances in non-precious metal catalysis for oxygen-reduction reaction in polymer electrolyte fuel cells, Energy Environ. Sci., 2011, 4, 114–130 RSC.
- J. Pan, M. Li and S. K. Wang, et al., Hybrid effect of carbon nanotube film and ultrathin carbon fiber prepreg composites, J. Reinf. Plast. Compos., 2017, 36, 452–463 CrossRef.
- B. Y. Kaplan, L. I. Şanlı and S. A. Gürsel, Flexible carbon-cellulose fiber-based composite gas diffusion layer for polymer electrolyte membrane fuel cells, J. Mater. Sci., 2017, 52, 4968–4976 CrossRef.
- J. Bai, P. F. Qi and X. T. Ding, et al., Graphene composite coated carbon fiber: electrochemical synthesis and application in electrochemical sensing, RSC Adv., 2016, 6, 11250–11255 RSC.
- A. P. Luz, C. G. Renda and A. A. Lucas, et al., Graphitization of phenolic resins for carbon-based refractories, Ceram. Int., 2017, 43, 8171–8182 CrossRef.
- Z. C. Zhang, M. M. Song and J. X. Hao, et al., Visible light laser-induced graphene from phenolic resin: a new approach for directly writing graphene-based electrochemical devices on various substrates, Carbon, 2018, 127, 287–296 CrossRef.
- C. Francisco, L. K. T. Alan and F. Jessica, Novel phenolic resins with improved mechanical and toughness properties, J. Appl. Polym. Sci., 2012, 123, 2131–2139 CrossRef.
- B. C. Liang, X. Y. Li and L. H. Hu, et al., Foaming resol resin modified with polyhydroxylated cardanol and its application to phenolic foams, Ind. Crops Prod., 2016, 80, 194–196 CrossRef.
- X. Zhang and Z. Shen, Carbon fiber paper for fuel cell electrode, Fuel, 2002, 81(17), 2199–2201 CrossRef.
- E. Papadopoulou and K. Chrissafis, Thermal study of phenol-formaldehyde resin modified with cashew nut shell liquid, Thermochim. Acta, 2011, 512, 105–109 CrossRef.
- L. Pilato, Phenolic resins: 100 years and still going strong, React. Funct. Polym., 2013, 73, 270–277 CrossRef.
- W. Zhang, Y. F. Ma and Y. Z. Xu, et al., Lignocellulosic ethanol residue-based lignin–phenol–formaldehyde resin adhesive, Int. J. Adhes. Adhes., 2013, 40, 11–18 CrossRef.
- S. Spina, X. Zhou and C. Segovia, et al., Phenolic resin adhesives based on chestnut (castanea sativa) hydrolysable tannins, J. Adhes. Sci. Technol., 2013, 27, 2103–2111 CrossRef.
- S. Sabagh, A. A. Azar and A. R. Bahramian, High temperature ablation and thermo-physical properties improvement of carbon fiber reinforced composite using graphene oxide nanopowder, Composites, Part A, 2017, 101, 326–333 CrossRef.
- Z. Z. Fu, B. T. Suo and R. P. Yun, et al., Development of eco-friendly brake friction composites containing flax fibers, J. Reinf. Plast. Compos., 2012, 31, 681–689 CrossRef.
- F. Y. Wang, Z. X. Huang and Y. Liu, et al., Novel cardanol-containing boron-modified phenolic resin composites: non-isothermal curing kinetics, thermal properties, and ablation mechanism, High Perform. Polym., 2017, 29, 279–288 CrossRef.
- X. L. Yi, A. Feng and W. Y. Shao, et al., Synthesis and properties of graphene oxide–boron-modified phenolic resin composites, High Perform. Polym., 2016, 28, 505–517 CrossRef.
|
This journal is © The Royal Society of Chemistry 2018 |
Click here to see how this site uses Cookies. View our privacy policy here.