DOI:
10.1039/C8RA04426K
(Paper)
RSC Adv., 2018,
8, 26469-26475
One-pot synthesis of highly active Ni/Fe nano-bimetal by simultaneous ball milling and in situ chemical deposition†
Received
24th May 2018
, Accepted 17th July 2018
First published on 25th July 2018
Abstract
In this study, nanoscale bimetallic particles (Ni/Fe) were prepared by a simultaneous ball milling and in situ chemical deposition process (B&C) with high dechlorination activity for 4-chlorophenol (4-CP). The results suggest that the introduction of Ni significantly improved the dechlorination of 4-CP. The dechlorination activity of Ni/Fe-B&C (kobs = 0.168 min−1) was increased significantly with a lengthening of the milling time and showed maximum activity at the milling time of 4 h. Bimetals prepared with the incorporation of Ni into Fe can quickly and completely dechlorinate 4-CP within 90 min reaction time. The dechlorination activity was mainly attributed to the synergistic effects of Ni and Fe. The dechlorination rate was increased with increasing Ni–Fe dosage but decreased with increasing solution pH and 4-CP concentration. Ni/Fe-B&C catalyst could be reused 10 times at pH below 5.0. This approach could offer great opportunities for both research and industrial applications to eliminate chlorinated organic pollutants.
1. Introduction
Chlorinated organic compounds (COC) are widely used as raw materials, intermediates or solvents in the chemical and pharmaceutical industries for various applications.1–5 Most of them are toxic or carcinogenic and have been linked to developmental toxicity problems, and liver, lung and nervous system damage.6–9 In recent years, nano-sized zero valent iron (nZVI) has been widely applied to treat a wide range of contaminants due to nZVI being cheap, abundant and non-toxic and possessing excellent chemical, surface and adsorptive properties.10–15 However, using nZVI for remediation of contaminated wastewater is limited due to its lack of stability, easy aggregation and easy passivation and the poor retrievability of nZVI from the treated solution.16–20 Various nZVI based bimetallic catalysts were developed to study the reductive dechlorination of COC contaminants. Compared with iron alone, bimetallic systems such as Ni/Fe, Pd/Fe, Cu/Ni, and Pd/Sn have shown higher efficiencies for the dechlorination of many chlorinated compounds. In a bimetallic system, primary metal (Fe, Zn, Sn, Mg or Al) serves as an electron donor to detoxify the contaminants, whereas the secondary metal (Cu, Ni, Pd, Pt or Ag) accelerates the dechlorination rate and prevents the deposition of by-products on the surface.21–23 Although, Pd, Pt, and Ag showed an excellent enhancement towards the dechlorination activity of COCs, but its high cost limits its wide application. Recently, nickel ions incorporated on ZVI exhibited a higher efficiency compared with iron alone in the detoxification of chlorinated aromatic compounds.24,25 Besides, owing to its better hydrogenation ability and low cost, selection of Ni is good choice to prepare cost-effective bimetallic catalysts for the reductive dechlorination of organic compounds.
In general, bimetallic particles preparation process involved the deposition of secondary metal on the primary metal through reduction or substitution reactions by chemical solution deposition (CSD).26–28 The presence of excessive amount of secondary metal on a bimetallic system may completely cover the primary metal surface leading to low dechlorination efficiency. Moreover, the secondary metal which covered the primary metal will be released into the water during the erosion and dissolution of the primary metal resulting in a significant reduction in the dechlorination activity.29
Recent studies suggested that Ni–Fe bimetals showed superior degradation activity prepared by ball milling (BM).21,29–32 Whereas, in BM process Ni can be homogeneously distributed over the Fe surface instead of the surface coverage of metals occurred in the CSD process.33 But bimetals prepared by BM usually have larger grain size and low compactness of two metals, which is unfavorable for dechlorination reaction. Thus, it is highly desirable to design more economic catalysts with high dechlorination activity. In this study, we used simultaneous ball milling and in situ chemical deposition process (B&C) to prepare the nano-Ni/Fe bimetallic can effectively resolve the problems mentioned above.
The objective of the present study was to evaluate the performance of nano-Ni/Fe bimetallic material prepared by simultaneous ball milling and in situ chemical deposition process (B&C), a novel method for dechlorination of 4-CP in wastewater. In addition, other factors contributing to the dechlorination of bimetallic systems such as preparation methods, Ni loading, milling time, solution pH, Ni/Fe dosage, and the initial 4-CP concentration were also investigated. The mechanism of catalytic reaction for the removal of 4-CP by Ni/Fe material was also discussed.
2. Experimental
2.1 Materials
The materials used in this paper were described in the Text S1 of the ESI.†
2.2 Preparation and characterization of Ni/Fe bimetal
Iron sponge, Ni/Fe bimetal prepared by chemical solution deposition (CSD) and ball milling (BM) are described in ESI Text S2.† Ni/Fe bimetal prepared by B&C briefly described as: 3 g iron sponge powder and 90 g steel balls were put into a grinding jar, then 40 mL Ni2+ dissolved in ethanol at different concentrations (the weight ratios of Ni to Fe was 1
:
19, 1
:
9, 3
:
17, 1
:
4.) was added. By a planetary ball mill, this mixture with different Ni2+ concentrations was milled for different times at a rotation speed of 270 rpm without inert gas protection. After milling, the mud of Ni/Fe was separated carefully and washed five times with absolute ethyl alcohol before freeze-drying. Characterization of the prepared catalysts was described in ESI Text S3.†
2.3 Degradation experiments
Firstly, the prepared materials were treated with H2SO4 solution (10 mL per 1 g particles) at pH 1.0 for 15 min and then washed with DI water (aerated by N2 for 15 min) three times, in order to remove the possible oxidation film before to conduct the dechlorination reaction. All the experiments were carried out in a serum vial with 20 mL of 20 mg L−1 4-CP solution and required amount of prepared materials. Serum vials were shaken constantly in a shaker at 220 rpm (25 °C) and samples were taken at different intervals by an injector with a 0.45 μm nylon membrane. To optimize Ni/Fe bimetal, 2 g particles prepared in different Ni wt% and different milling times were added in 4-CP solution at pH 2.0. To contrast the dechlorination ability of particles prepared by different methods, 2 g particles were added in 4-CP solution at pH 2.0. In order to study the initial pH effect, 2 g bimetal particles were added in 4-CP solution at different initial pH (from 2.0 to 8.0). Further, the effect of the initial concentration of 4-CP and dosage of Ni/Fe particles was also investigated. Reuse experiments were also carried out at different pH (from 2.0 to 8.0). The efficiency of dechlorination was measured after 60 min in the successive ten cycles. Each dechlorination experiment was conducted in triplicate and protected by N2 gas. Samples collected after the dechlorination experiments were filtered by a 0.45 μm nylon membrane.
2.4 Sample analysis
The concentration of 4-CP was determined with a high performance liquid chromatograph (HPLC; ELITE P1201) equipped with a C18 reversed-phase column (4.6 mm × 250 mm) and a UV detector at wavelength of 254 nm. The mobile phase used for BPA was a mixture of methanol and water (70
:
30, v/v) at a constant flow rate of 1.0 mL min−1 with a constant column temperature of 40 °C.
3. Results and discussion
3.1 Characterization of Ni/Fe materials
EDS element mappings of Ni/Fe bimetallic particles synthesized by B&C were provided in Fig. 1. The results obviously showed that Ni particles were dispersed homogeneously into Fe phase and blended uniformly after B&C process, leading to effective contact. Reports also mentioned the importance of close contact bimetals for dechlorination.29 The average particle size of Ni/Fe particles was found to be less than 1 μm in Fig. S1,† which helps to achieve more effective contact between the particles compared with those of simple mechanical milling of two metals. To further confirm this result, EDS elemental analysis of the bimetal was performed. Analysis was carried out on the selected points of the bimetal and results suggested the uniform particles were obtained after the B&C process as given in Fig. S2.†
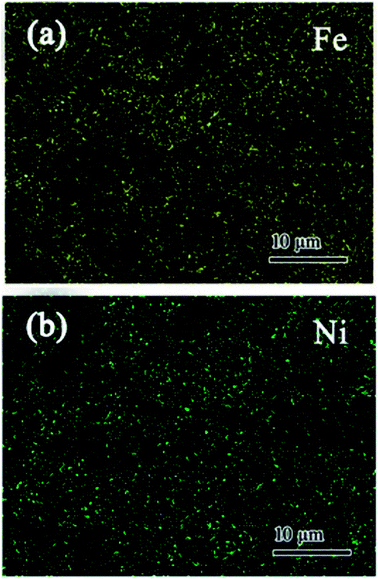 |
| Fig. 1 EDS (a) Fe mapping and (b) Ni mapping of Ni/Fe-B&C bimetal. | |
The presence of internal strain and dislocations in the bimetal can be observed in the XRD patterns given in the Fig. 2a. It can be seen that the mixture of Fe and Ni powders exhibited the major diffraction peaks at 44.77° and 65.17° for Fe, and 44.60°, 51.91° and 76.81° for Ni. But, for the bimetal material prepared by simultaneous B&C process, the diffraction peaks of Ni disappeared and the intensity of Fe diffraction peaks were relatively weak, which may be due to the homogeneous distribution of Ni on Fe surface. Moreover, after B&C process, the diffraction peaks of Fe were slightly shifted to lower angle and broadened, which can be attributed to two factors such as the refinement of grain size and the increase of internal strain. As shown in Fig. S3,† with the increase of milling time, the diffraction peaks were shifted to the low-angle direction and the peak widths tended to get broader due to the formation of grain interface structural defects.31,32 The strains and defects of milled bimetal can also be observed by the change in magnetic properties (Fig. 2b). After B&C process, Ni particles distributed homogeneous in Ni/Fe bimetal, which was favorable for the formation of many galvanic cells. It leads to speeding up the electron transfer of galvanic corrosion. The close and effective contact of two metals in Ni/Fe-B&C decrease the contact resistance and in this way, 4-CP can be reduced directly by galvanic corrosion on the Ni/Fe bimetal, leading to an acceleration of dechlorination.29,34
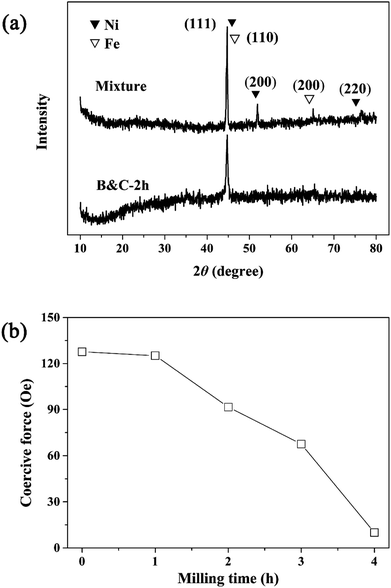 |
| Fig. 2 (a) X-ray diffraction spectra of Ni/Fe materials. (b) Effect of milling time on coercive force of the Ni/Fe-B&C materials. | |
3.2 Optimization of Ni/Fe bimetal materials
Fig. 3a exhibited the influence of milling time on the dechlorination rate of 4-CP. It can be observed that the reaction rate gradually increased when increasing milling time. The dechlorination percent was almost up to 100% in 30 min when the milling time was increased to 4 h. The rate constant of bimetal materials milled after 4 h was 0.168 min−1 in this study. Mass balance showed that the total concentration of 4-CP and phenol in solution was more than 96% of the initial 4-CP concentration. This indicates that 4-CP could be directly reduced to phenol by Ni/Fe bimetallic nanoparticles in this process and their amounts adsorbed on the bimetal were negligible. The reaction was described well by the pseudo-first-order kinetic model in Fig. S4.† Ball milling process helped to achieve more effective contact of Ni and Fe which speeded up the migration rate of electrons. Reports have postulated that the atomic hydrogen adsorbed on the reductant surface (Hads) would be responsible for the bimetallic hydrodechlorination.35,36 Ball-milling led to heavy deformation of the powders, hence the material resulted with a high concentration of strain and defects, which can substantially increase the adsorption of hydrogen.37 The effect of Ni content on 4-CP dechlorination by Ni/Fe bimetallic system was also investigated, as shown in Fig. 3b. The removal and degradation percentages were 37.1% and 42.1% when Ni content was 0 and 35% in 90 min, respectively. These results clearly demonstrated that excessively high or low Ni content will restrain the degradation of 4-CP. Ni serves as role of a catalyst and could be considered as better choice of catalyst to dechlorinate 4-CP.24,38 The degradation percentage increased strongly with the increasing Ni content and it reached ∼100% when Ni content was 20 wt%. The catalytic Ni on the Fe particles surface as the catalytic sites would adsorb hydrogen and transform it to atomic hydrogen more efficiently, thereby facilitated the reaction. It's worth noting that the degradation percentage was decreased when the Ni content above 25 wt%. This may be due to the excessive deposition of nickel metal on the iron metal surface hindering the corrosion of iron and the diffusion of Fe2+ into the solution.
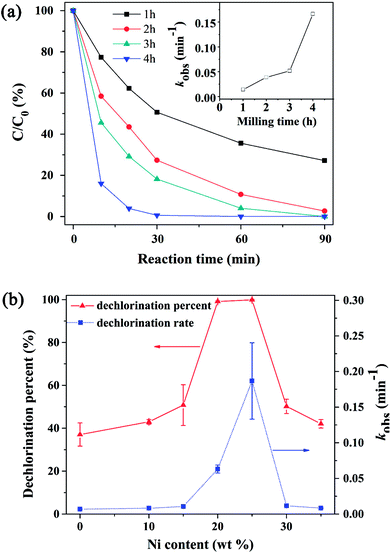 |
| Fig. 3 Effect of (a) milling time (Ni content = 25 wt%) and (b) Ni content (milling time = 2 h) on the dechlorination of 4-CP. | |
3.3 Effects of synthetic method, pH, Ni/Fe load and 4-CP concentration on dechlorination
Batch experiments were conducted to compare the removal efficiencies of 4-CP using Ni/Fe bimetals prepared by different methods. As can be observed from Fig. 4, 4-CP degradation percentage using Ni/Fe bimetal prepared by B&C method reached almost 100% in 60 min while Ni/Fe bimetals prepared by BM and CSD were 81.2% (Ni/Fe-BM) and 60.9% (Ni/Fe-CSD) in 90 min, respectively. Besides, much lower degradation percentage about 42.3% was observed for iron sponge particles. Evidently, the homogeneous Ni/Fe bimetal prepared by B&C possessed higher dechlorination activity for 4-CP than Ni/Fe-BM and Ni/Fe-CSD particles. The superior degradation activity of Ni/Fe-B&C composite could be ascribed to smaller Ni crystal particles homogeneously deposited on Fe surface via B&C process and the formation of crystal defects.
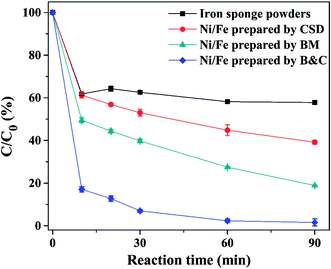 |
| Fig. 4 Effect of synthesis method on the dechlorination of 4-CP (reaction conditions: 4-CP concentration = 20 mg L−1, Ni/Fe dose = 1 g/10 mL, Ni content = 20 wt%, initial pH 2.0). | |
Solution pH not only affects the dechlorination of 4-CP and the dissolution of Fe and Ni but also influences the formation of iron hydroxide precipitate and the passivation.33 Therefore, the removal of 4-CP was studied at different solution pH. As observed in Fig. 5a, the degradation percentage decreased from 100% to 89.97% as pH increased from 2.0 to 8.0, which demonstrated acidic condition favored the degradation of 4-CP. Low pH can accelerate the corrosion of Fe and produces enough electrons to generate atomic hydrogen (eqn (1)–(4)) and thereby further facilitate the reaction. Conversely, at high pH solution, Fe2+ can easily transform into iron hydroxide precipitate (eqn (5)) and form passivating films on the surface of bimetal, inhibiting the contact of target compounds with the reactive sites and blocking the electron transfer.39,40 To further investigate the pH effect on the dechlorination, the pH change profile at different initial pH (Fig. 5b) was studied. When initial pH is below 5, solution pH values were increased during the initial period of 10 min, then the pH values of the solutions gradually reached the highest pH. The reason is the consumption of H+ and generation of OH−.34,36 In contrast, when initial pH was above 7, solution pH decreased rapidly during the initial period of 10 min. All pH values tended to be stable after 90 min and were stabilized in a similar range (pH = 6.5 to 7.0).
|
2H+ + 2e− → H2 (in acidic solution)
| (2) |
|
 | (3) |
|
 | (4) |
|
Fe2+ + 2OH− → Fe(OH)2↓
| (5) |
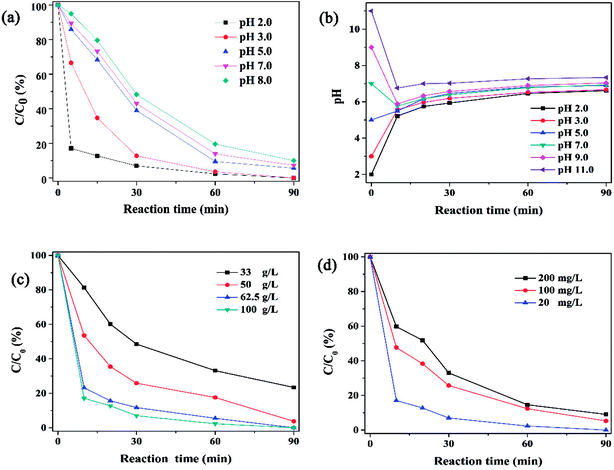 |
| Fig. 5 (a) Effect of initial pH on 4-CP dechlorination. (b) The pH change profile in the reaction process at different initial pH. Effect of (c) Ni/Fe dosage and (d) initial 4-CP concentration on 4-CP dechlorination (reaction condition: 4-CP concentration = 20 mg L−1, Ni/Fe dose = 1 g/10 mL, pH = 2, Ni content = 20 wt%). | |
Effect of initial bimetal dosage on the dechlorination of 4-CP was observed in Fig. 5c and S5.† The results indicated that the degradation rate of 4-CP increased with the increasing of bimetal dosage and the mass-normalized rate constants (km) was given in Fig. S5,† where km is the specific value of kobs and CNi/Fe (g L−1).32 With the Ni–Fe bimetal dosage increasing, the pseudo-first-order rate constant kobs increased, while km decreased. It indicates that the rate of dechlorination activity actually decreased per unit of Ni–Fe dosage. The similar results were also reported by Zhu et al.21 for degradation of 4-CP on Ni/Fe bimetal prepared by BM. The influence of the initial concentration of 4-CP on dechlorination activity was shown in Fig. 5c and S6.† The concentration-normalized rate constants (kc) was calculated, where kc is the specific value of kobs and the initial C4-CP (mg L−1).32 The results showed kobs decreased as the initial 4-CP concentration increased from 20 mg L−1 to 200 mg L−1. At the same time, the value of kc in this study showed the same trend which indicated that the dechlorination activity was inhibited by the high concentration of target contaminants. The surface reaction in dechlorination process may account for the decrease of kobs and kc due to the increase of initial 4-CP concentration.32 When the concentration of 4-CP was a constant, the utilization efficiency of active sites was higher at lower catalyst dosage. When the dosage of catalyst, illustrating the number of active sites was a constant, the higher concentration of target contaminants would lead to the severe competition, which may result in low degradation rate.
3.4 Reusability and stability of Ni/Fe-B&C
Ten runs experiments were performed using the Ni/Fe-B&C materials to evaluate its stability and recyclability at different initial pH solutions. As can be seen in Fig. 6, the dechlorination rate was high and kept relatively stable when it was reused for 10 times at the acidic condition, but decreased tremendously after 3 run at the initial pH of 7.0 and 8.0. In acidic solution, passivating film was difficult to form and accumulate. So the material can maintain high catalytic reactivity in acidic conditions. In contrast, passivating film formed on the surface of Fe would cover active sites so that significantly decreased the dechlorination efficiency and even stopped the dechlorination reaction completely in neutral or alkaline solution.26,41
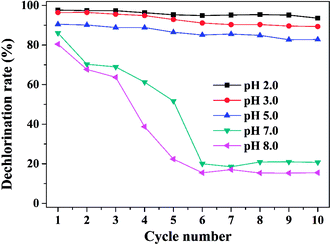 |
| Fig. 6 The dechlorination activity of the Ni/Fe-B&C at different initial pH in the ten-cycle dechlorination reaction (reaction condition: Ni/Fe dose = 1 g/10 mL, 4-CP concentration = 20 mg L−1, Ni content = 20 wt%, reaction time = 30 min). | |
The dissolved Fe and Ni concentration and respective loss rate after 10-cycles at different initial pH were shown in Fig. S7.† The Fe ion and Ni ion contents in solution decreased from 41.89 mg L−1 to 1.86 mg L−1 and 2.55 mg L−1 to 0.31 mg L−1 with the initial pH increased from 2.0 to 8.0. Overall iron and nickel in solution after ten-cycles was determined to be 0.523% and 0.128% at pH 2.0, 0.023% and 0.015% at pH 8.0. The loss of metallic iron and nickel at initial pH below 3.0 was much higher than these at the pH above 7.0. The dechlorination of 4-CP was accompanied by dissolution and precipitation.33 The dissolution was faster than the precipitation at initial pH below 3.0, resulting in the stable dechlorination activity in the successive use. The dissolution became slow with the increase of initial pH, leading to the formation of hydroxide precipitate and the reduction of dechlorination activity. Low pH can facilitate the dechlorination but increase the loss of Ni and Fe. While at high pH solution, the dissolved nickel and iron can easily hydrolyze to hydroxide precipitation.39 The solution concentration of Ni ion at pH 2.0–5.0 exceeded the highest limitation in sewage (1 mg L−1) which was regulated in China's National Comprehensive Discharge Standard of Sewage (GB8978-1996). Therefore, it is necessary to adopt this method at pH over 5.0, otherwise, appropriate follow-up processing steps are needed in practical application.
3.5 Electrocatalytic characterization of Ni/Fe-B&C
Cyclic voltammetry measurements were carried out to evaluate electrocatalytic hydrodechlorination reactions of prepared catalysts. A solution of 0.1 M Na2SO4 was employed as an electrolyte, which was purged using nitrogen gas before the electrochemical measurement. The scan rate was 100 mV s−1 and the substrate was 4-CP. The cell consisted of a Pt wire as a counter electrode, an Ag/AgCl electrode as a reference, and the Fe catalyst or Ni/Fe catalysts modified carbon paste electrode (the catalysis content was 2 wt%) as a working electrode. All of the potentials in this study were reported with respect to the Ag/AgCl reference electrode. There was an obvious difference between the CV curves of the different catalysts (Fig. 7). An irreversible reduction peak at −0.45 V was detected in the CV curve of different catalysts and this peak corresponds to the reduction of 4-CP to phenol. The CV measurements showed an increase in the reduction peak current of three catalysts (from iron sponge powders to Ni/Fe-B&C), which indicated the increasing reduction ability. The similar results can be seen in the literature.26
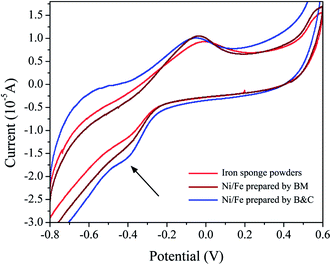 |
| Fig. 7 The electrochemical reactions of iron and iron-based catalysts prepared by different methods. | |
3.6 Mechanistic study
After B&C process, smaller Ni grains homogeneously dispersed into Fe phase and more effective contact of Ni and Fe was achieved, which was favorable for the formation of many galvanic cells and led to speeding up the electron transfer of galvanic corrosion. Moreover, B&C resulted in a high concentration of strain and defects, which can substantially increase the adsorption of hydrogen. Based on the results at literature, a plausible mechanism for the dechlorination of 4-CP by Ni/Fe-B&C bimetal was proposed as illustrated in Scheme 1. Firstly, Fe transferred electrons to H+ and converted it into H2. Then, hydrogen converted to atomic hydrogen under the catalysis of Ni. Finally, the highly reductive atomic hydrogen replace the chlorine of 4-CP (eqn (6)). The total reaction equation was given as eqn (7). |
RCl + 2H* → RH + H+ + Cl−
| (6) |
|
 | (7) |
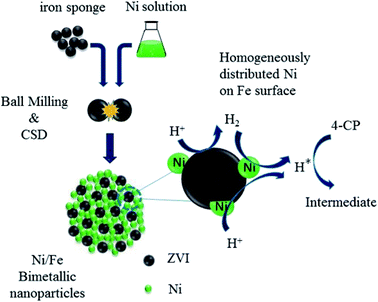 |
| Scheme 1 One-pot synthesis and reaction mechanism of Ni/Fe-B&C. | |
4. Conclusions
The Ni/Fe bimetal nanomaterials prepared by simultaneous ball milling and in situ chemical deposition (B&C) exhibited higher hydrodechlorination activity for 4-CP than Ni/Fe-BC and Ni/Fe-CSD. Bimetals prepared in this way was an efficient route not only to reduce the size of catalysts, but also to attain better control for homogeneous distribution of Ni on the Fe surface. The high dechlorination activity of Ni/Fe-B&C for COC can be attributed to the homogeneous Ni particles in the bimetal and also to lots of internal strains and dislocations formed during the B&C. In addition, this method can be easy scaled-up to industrial applications. The addition of Ni into Fe enhanced the magnetic properties and achieved excellent stability with high dechlorination activity at the acidic conditions. The concentration of Ni2+ after dechlorination at pH 2.0, 3.0 and 5.0 exceed the limitation of Chinese standard (1 mg L−1). Therefore, the emphasis of future research is not only to improve the dechlorination activity of bimetals, but also to control the leaching of nickel ions and prevent secondary pollution.
Conflicts of interest
There are no conflicts to declare.
Acknowledgements
This work was supported by the National Natural Science Foundation of China (21477063, 21777086), National Basic Research Program of China (2013CB934301), Natural Science Foundation for Distinguished Young Scholars of Shandong Province (JQ201809), Young Scholars Program of Shandong University (2016WLJH16) and Fundamental Research Funds of Shandong University (2016JC031).
References
- P.-T. Huong, B.-K. Lee and J. Kim, Process Saf. Environ. Prot., 2016, 100, 272–280 CrossRef.
- A. Kuleyin, J. Hazard. Mater., 2007, 144, 307–315 CrossRef PubMed.
- X. Liu, J.-H. Fan and L.-M. Ma, Chem. Eng. J., 2014, 236, 274–284 CrossRef.
- Y. Zhou, Y. Kuang, W. Li, Z. Chen, M. Megharaj and R. Naidu, Chem. Eng. J., 2013, 223, 68–75 CrossRef.
- Y. Peng, J. Chen, S. Lu, J. Huang, M. Zhang, A. Buekens, X. Li and J. Yan, Chem. Eng. J., 2016, 292, 398–414 CrossRef.
- L. Chu and J. Wang, Radiat. Phys. Chem., 2016, 119, 194–199 CrossRef.
- G. Pon, M. R. Hyman and L. Semprini, Environ. Sci. Technol., 2003, 37, 3181–3188 CrossRef PubMed.
- N. R. Council, Alternatives for ground water cleanup, National Academies Press, 1994 Search PubMed.
- S. Li, Y.-L. Fang, C. D. Romanczuk, Z. Jin, T. Li and M. S. Wong, Appl. Catal., B, 2012, 125, 95–102 CrossRef.
- A. Kumar, C. Guo, G. Sharma, D. Pathania, M. Naushad, S. Kalia and P. Dhiman, RSC Adv., 2016, 6, 13251–13263 RSC.
- W. Qi, F. Wang, H. Wang, Q. Shi, L. Pang and Z. Bian, J. Environ. Sci., 2015, 36, 2168–2174 Search PubMed.
- Q. Zhang, Y. Guo, M. Huang, H. Li and C. Gu, Chem. Eng. J., 2015, 276, 122–129 CrossRef.
- S.-Q. Ni, Z. Zheng, W. Jiang and J. Zhan, Sci. Adv. Mater., 2013, 5, 1123–1131 CrossRef.
- Z. Wu, C. Sun, Y. Chai and M. Zhang, RSC Adv., 2011, 1, 1179–1182 RSC.
- I. A. Witońska, M. J. Walock, M. Binczarski, M. Lesiak, A. V. Stanishevsky and S. Karski, J. Mol. Catal. A: Chem., 2014, 393, 248–256 CrossRef.
- S. Q. Ni and N. Yang, J. Colloid Interface Sci., 2014, 420, 158–165 CrossRef PubMed.
- F. Fu, D. D. Dionysiou and H. Liu, J. Hazard. Mater., 2014, 267, 194–205 CrossRef PubMed.
- F. He and D. Zhao, Environ. Sci. Technol., 2007, 41, 6216–6221 CrossRef PubMed.
- F. He, D. Zhao and C. Paul, Water Res., 2010, 44, 2360–2370 CrossRef PubMed.
- L. Wang, S.-Q. Ni, C. Guo and Y. Qian, J. Mater. Chem. A, 2013, 1, 6379 RSC.
- L. H. Zhu, Q. W. Huang and H. F. Zhao, Scr. Mater., 2004, 51, 527–531 CrossRef.
- L. Yin, Y. Dai, J. Niu, Y. Bao and Z. Shen, J. Hazard. Mater., 2012, 209–210, 414–420 CrossRef PubMed.
- C. J. Lin, Y. H. Liou and S. L. Lo, Chemosphere, 2009, 74, 314–319 CrossRef PubMed.
- W.-h. Zhang, X. Quan and Z.-y. Zhang, J. Environ. Sci., 2007, 19, 362–366 CrossRef.
- W. Yan, A. A. Herzing, X.-q. Li, C. J. Kiely and W.-x. Zhang, Environ. Sci. Technol., 2010, 44, 4288–4294 CrossRef PubMed.
- Q. Shi, H. Wang, S. Liu, L. Pang and Z. Bian, Electrochim. Acta, 2015, 178, 92–100 CrossRef.
- S. K. Ghosh, M. Mandal, S. Kundu, S. Nath and T. Pal, Appl. Catal., A, 2004, 268, 61–66 CrossRef.
- Y. Lubphoo, J. M. Chyan, N. Grisdanurak and C. H. Liao, J. Taiwan Inst. Chem. Eng., 2016, 59, 285–294 CrossRef.
- T. Li, Y. Chen, P. Wan, M. Fan and X. J. Yang, J. Am. Chem. Soc., 2010, 132, 2500–2501 CrossRef PubMed.
- Y. Liu, J. Zhang, L. Yu, G. Jia, C. Jing and S. Cao, J. Magn. Magn. Mater., 2005, 285, 138–144 CrossRef.
- X. Zhao, Y. Ding, L. Ma, X. Shen and S. Xu, Int. J. Hydrogen Energy, 2008, 33, 6351–6356 CrossRef.
- H. Zhu, F. Xu, J. Zhao, L. Jia and K. Wu, Environ. Sci. Pollut. Res. Int., 2015, 22, 14299–14306 CrossRef PubMed.
- F. Xu, S. Deng, J. Xu, W. Zhang, M. Wu, B. Wang, J. Huang and G. Yu, Environ. Sci. Technol., 2012, 46, 4576–4582 CrossRef PubMed.
- W. Zhang, X. Quan, J. Wang, Z. Zhang and S. Chen, Chemosphere, 2006, 65, 58–64 CrossRef PubMed.
- L. Li, M. Fan, R. C. Brown, J. Van Leeuwen, J. Wang, W. Wang, Y. Song and P. Zhang, Crit. Rev. Environ. Sci. Technol., 2006, 36, 405–431 CrossRef.
- Z. Zhang, N. Cissoko, J. Wo and X. Xu, J. Hazard. Mater., 2009, 165, 78–86 CrossRef PubMed.
- J. Xu, A. Dozier and D. Bhattacharyya, J. Nanopart. Res., 2005, 7, 449–467 CrossRef.
- Y. Liu, F. Yang, P. L. Yue and G. Chen, Water Res., 2001, 35, 1887–1890 CrossRef PubMed.
- B. Yang, J. Zhang, Y. Zhang, S. Deng, G. Yu, J. Wu, H. Zhang and J. Liu, Chem. Eng. J., 2014, 250, 222–229 CrossRef.
- H. Choi, S. R. Al-Abed and S. Agarwal, Environ. Sci. Technol., 2009, 43, 4137–4142 CrossRef PubMed.
- H. Tian, J. Li, Z. Mu, L. Li and Z. Hao, Sep. Purif. Technol., 2009, 66, 84–89 CrossRef.
Footnotes |
† Electronic supplementary information (ESI) available. See DOI: 10.1039/c8ra04426k |
‡ Shuo-Shuo Zhang and Ning Yang contributed equally to this work and share the first authorship. |
|
This journal is © The Royal Society of Chemistry 2018 |
Click here to see how this site uses Cookies. View our privacy policy here.