DOI:
10.1039/C8RA04600J
(Paper)
RSC Adv., 2018,
8, 25368-25377
Lead (Pb2+) sorptive removal using chitosan-modified biochar: batch and fixed-bed studies†
Received
29th May 2018
, Accepted 6th July 2018
First published on 17th July 2018
Abstract
Chitosan-Modified fast pyrolysis BioChar (CMBC) was used to remove Pb2+ from water. CMBC was made by mixing pine wood biochar with a 2% aqueous acetic acid chitosan (85% deacylated chitin) solution followed by treatment with NaOH. The characterizations of both CMBC and Non-Modified BioChar (NMBC) were done using diffuse reflectance infrared Fourier transform spectroscopy (DRIFTS), scanning electron microscopy (SEM), surface area measurements (SBET), elemental analysis, thermogravimetric analysis (TGA), differential scanning calorimetry (DSC) and ζ-potential measurements. Elemental analysis indicated that chitosan accounts for about 25% weight of the CMBC. The Langmuir maximum adsorption capacity of CMBC at pH 5 was 134 mg g−1 versus 48.2 mg g−1 for NMBC at 318 K. CMBC column adsorption studies resulted in a capacity of 5.8 mg g−1 (Pb2+ conc. 150 mg L−1; pH 5; column dia 1.0 cm; column length 20 cm; bed height 5.0 cm; flow rate 2.5 mL min−1). CMBC removed more Pb2+ than NMBC suggesting that modification with chitosan generates amine groups on the biochar surface which enhance Pb2+ adsorption. The modes of Pb2+ adsorption on CMBC were studied by comparing DRIFTS and X-ray photoelectron spectroscopy spectra before and after Pb2+ adsorption.
1. Introduction
Lead is a primary water pollutant observed in many developing countries.1 It is introduced to the environment in a variety of ways. The combustion of fossil fuels emits lead into the atmosphere and it is deposited back onto land, where it washes into nearby water systems. Acid mine drainage and discharge from industries that produce ceramics, glass, and acid batteries have been known to release lead into lakes and rivers.2,3 Lead can cause neurological, renal, hematological, endocrine, gastrointestinal, and cardiovascular problems in humans, and growth, cell division, water absorption and balance problems in flora and fauna.4 In humans, acute lead poisoning can cause severe kidney,5 brain, and neurological damage,6 while long term exposure can induce sterility and abortion.7 According to the World Health Organization (WHO), lead exposure accounts for approximately 143
000 deaths per year around the world. To reduce such health tragedies, the WHO and the American Water Works Association (AWWA) have determined the lead concentration in drinking water must fall below 10 μg L−1, while the U.S Environmental Protection Agency (EPA) set the maximum concentration in drinking water at 15 μg L−1.2
Many procedures have been developed to purify water contaminated with heavy metals. Aqueous solutions of these heavy metals have been treated by physical, chemical,8 and biochemical9 processes. However, adsorption techniques have become increasingly widely applied.10 Activated carbon, commonly used for adsorption, is expensive and selective for few contaminants.11 Thus, new, low cost adsorbents to remove heavy metals from aqueous solution are desirable.
Many low cost water purification methods have been studied.12 Viable choices include algae, which has a high lead uptake capacity (∼1.67 mmol g−1) and an almost unlimited ocean supply,13,14 red mud (a byproduct from aluminum industries composed mainly of iron oxide),15 and biochar.16–18 Fast biomass pyrolysis produces bio-oil and solid carbonaceous biochar, as a byproduct. Extensive research on biochar has proven its potential as a cheap and effective adsorbent to remove environmental contaminants from water.2,19–23 In an effort to improve biochar's adsorption performance, recent studies have focused on modifying the biochar surface.24–30
Chitosan is a low-cost, biodegradable, and non-toxic material that is created through the hydrolysis of chitin's amide functions to amine groups using alkali sodium hydroxide (Scheme 1).31 Chitin is found in shrimp and other crustacean shells. It is the most abundant renewable and biodegradable natural amino polysaccharide in the world, making chitosan potentially inexpensive. Chitosan is an excellent alternative adsorbent for heavy metal removal from aqueous solutions.32–34 Previously, lead adsorption on chitosan has been studied on chitosan hydrogel, chitosan/PVA hydrogel beads, and chitosan-coated sand.35–37 Therefore, combining chitosan and biochar could produce a novel material with increased lead ion uptake capacity above that of the biochar.38
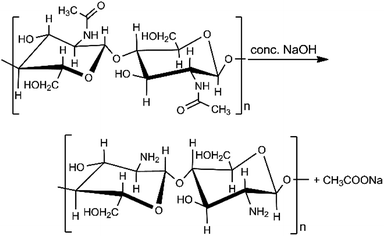 |
| Scheme 1 Chitin base hydrolysis to chitosan. | |
Chitosan-modified bamboo, potato peel, and rice straw biochar have previously been used to study the sorption of Pb2+.34,39,40 However, the feedstock biomass used in these studies are not widely available in large quantities and reported Pb2+ adsorption capacities are relatively low compared to the literature reported values for other Pb2+ adsorbents. Another impediment to commercialization is that most adsorption data is from batch studies while wastewater treatment plants typically use fixed-bed columns for metal adsorption. The required column parameters for scaling up fixed-bed columns can be obtained through column studies. Thus, additional investigations are needed to develop high capacity and cost-effective chitosan-modified biochar adsorbents.
The main objectives of this work were to develop a new chitosan-modified biochar composite from pinewood, evaluate its batch and column sorption capacity, and elucidate sorption mechanisms for Pb2+. Pine wood was used as the feedstock to produce biochar due to its worldwide availability, cost effectiveness (available as a waste product from pulping and bio-oil industry) and high adsorption capacities.41 Chitosan-modified pine wood biochar could lead to low cost adsorbents, because both materials are cheap and widely available.
2. Experimental
2.1. Chemicals and equipment
All chemicals used were either GR or AR grades. They were purchased from Sigma Aldrich (Saint Louis, MO) unless otherwise specified. An aqueous stock solution of 1000 mg L−1 Pb2+ was prepared by dissolving Pb(NO3)2 in deionized (DI) water. Analytical grade chitosan (viscosity of 200–500 cP at 20 °C) 0.5 wt% in 0.5% aqueous acetic acid was acquired from VWR (Radnor, PA). This chitosan was derived from chitin by deacylating 85% of the parent chitin's amide groups. Complete deacylation is not required.
2.2. Preparation of pine wood biochar
The biochar used for this study was obtained as a byproduct of fast pyrolysis bio-oil production.42 The pine wood chips were pyrolyzed in a continuous auger-fed reactor where, after preheating, it was passed through the pyrolysis zone at 425 °C for 20–30 s. The heating protocol was previously described.43 The biochar was collected and washed with DI water several times to remove salt impurities and ash. Biochar was then ground, sieved to a uniform particle size distribution between 0.1 to 0.6 mm, oven dried at 110 °C for 12 h to remove moisture, and stored in a closed container for further use. Resulting non-modified pine wood biochar is hereafter referred as NMBC.
2.3. Preparation of chitosan-modified biochar
Chitosan-modified biochar was prepared as described by Y. Zhou et al.34 Briefly, 3 g of chitosan was dissolved in 180 mL of aqueous acetic acid (2%) followed by the addition of 3 g of biochar. The mixture was stirred for 30 min at ambient temperature. The biochar–chitosan suspension in aqueous acetic acid was then added dropwise to a 900 mL NaOH (1.2%) solution over approximately 2 h, and the resulting suspension was held for an additional 12 h. The solid was filtered through Whatman no. 1 filter paper. The chitosan-modified biochar was then washed with DI water to remove excess NaOH and oven dried for 24 h at 70 °C. The final weight of the dried sample was 4 g indicating the biochar had complexed 1 g of chitosan, giving a ∼25% w/w ratio of chitosan to the biochar in the chitosan-modified biochar. The resulting chitosan-modified biochar samples are hereafter referred as CMBC.
2.4. Biochar characterization
Diffuse reflectance infrared Fourier transform spectroscopy (DRIFTS) analysis (Thermo Nicolet 6700 FT-IR spectrometer) of the samples were obtained after grinding and pressing into a 5% by weight adsorbent KBr pellet. A total of 64 scans were taken from 4000 cm1 to 600 cm−1 with a resolution of 4 cm−1. Scanning electron microscopy (SEM) analysis was performed using a JEOL JSM-6500F FE-SEM operated at 5 kV. The biochar was applied to a carbon stub attached to carbon tape and then sputtered-coated under argon with a 5 nm layer of platinum. The biochar samples were then attached to a sample holder for SEM analysis. Transmission electron microscopy (TEM) analysis was carried out using a JEOL model 2100 TEM operated at 80 kV. About 10 mg of the samples were mixed with ∼0.5 mL of 100% ethanol, sonicated for about 4 min, deposited on carbon film on a 300 mesh copper grid, followed by a 24 h drying. Surface areas and pore size distributions were determined using nitrogen physisorption (BET) at 77 K with a NOVA 2200e surface area and pore analyzer purchased from Quantachrome Instruments. Isotherms were analyzed with Quantachrome's NovaWin software version 10.01. Thermogravimetric analysis (TGA) analysis was performed under air at a heating rate of 10 °C min−1 from 25 to 1000 °C for both NMBC and CMBC using a TA Instrument's Q50 thermogravimetric analyzer. Differential scanning calorimetry (DSC) analysis was performed under air at a heating rate of 10 °C min−1 from 25 to 550 °C for Chitosan, NMBC, and CMBC using a TA Instrument's Q20 differential scanning calorimeter. ζ-Potential measurements were conducted using a ZetaPALS instrument (Brookhaven Instruments Corporation (BIC), Holtsville, NY). The elemental C and N composition of both NMBC and CMBC determined by dry combustion using an ECS 4010 elemental combustion system CHNS–O (ECS 4010, Costect Analytical Technologies Inc.). X-ray photoelectron spectroscopy (XPS) analysis was performed using a Thermo Scientific K-Alpha XPS system equipped with a monochromatic X-ray source at 1486.6 eV corresponding to the Al Kα line.
2.5. Batch sorption studies
The effects of pH, contact time, and Pb2+ concentration on uptake were carried out using the batch adsorption method.44 Both kinetic and adsorption isotherm studies for Pb2+ were carried out at pH 5 and temperatures at 298, 308, and 318 K. A known amount of CMBC was added to 25 mL solutions of adsorbate containing 150 to 230 mg L−1 of Pb2+ from the 1000 mg L−1 Pb2+ stock solution prepared by dissolving Pb(NO3)2 into DI water. This range was selected based on the natural levels of lead in soil (range between 50 and 400 mg L−1). Samples were then shaken using a mechanical shaker at 200 rpm for 24 h (3 replicates were done for each test). Supernatants were then filtered through Whatman no. 1 filter paper. (As a test to determine if Pb2+ was adsorbed or retained on the filter paper, an aqueous Pb(NO3)2 solution (150 mg L−1) was filtered through the filter paper and the Pb2+ concentration in the filtrate was measured. It was found that the Whatman no. 1 filter paper can hold about 3.3% total wt of Pb2+ in solution. This was easily washed out from the filter paper with additional DI water). The Pb2+ concentration remaining in the filtrate was measured with Atomic Absorption Spectrometry (AAS) and the amount of Pb2+ removed by adsorption was calculated by:
here Qe is the amount of Pb2+ (mg) removed per gram of CMBC, Co and Ce are the initial and equilibrium Pb2+ concentrations (mg L−1) in solution, V is the solution volume (L), and M is the CMBC weight (g).
2.6. Column sorption studies
The CMBC (1 g) was mixed with hot water producing a slurry that was packed into a glass column (20.0 × 1.0 cm) avoiding air entrapment. A small quartz wool plug was used to prevent any escape of CMBC. The bed height was 5.0 cm. The column was loaded with Pb2+ solution (150 mg L−1 and pH = 5.0) infiltrated downward through the column under gravity with a flow rate of 2.5 mL min−1. Effluents were collected and analyzed until Pb2+ concentration became close to the 150 mg L−1.
3. Results and discussion
3.1. Chitosan-modified biochar characterization
The FTIR spectra for chitosan, NMBC, and CMBC are shown in Fig. S1 (ESI†). The IR bands from 3300 to 3500 cm−1 are characteristic of N–H and O–H stretching vibrations. Chitosan (Fig. S1(a)†) shows the typical FTIR spectrum of chitosan with N–H and O–H vibrations centered in the 3300 to 3500 cm−1 regions and sp3-hybridized C–H stretching at 2871 cm−1. The bands at 1653 cm1 and 894 cm−1 are due to the N–H bending and N–H wagging respectively. The NMBC surface has a large number of alcohols and ethers (sp3-C–O and sp2-C–O stretching 1124–1205 cm−1), phenolic O–H (3200–3550 cm−1), and cyclic alkene (1566–1650 cm−1) which can be seen in the Fig. S1(b).† The CMBC surface contains amine and amide functional groups from chitosan and a few functional groups from the biochar including phenolic OH and carbonyls (Fig. S1(c)†).
Thermogravimetric analysis (TGA) of chitosan, NMBC, and CMBC are shown in Fig. 1(a). All of these materials exhibit initial weight losses of 4–10% from 50–100 °C due to the loss of moisture. The NMBC starts to decompose just above 300 °C and loose about 90% of its mass by the time it reaches 480 °C 18 min later. CMBC exhibits two major weight drops. The first in the range of 220–290 °C due to chitosan decomposition. The second weight drop occurs from 300 to 530 °C and can be attributed to both biochar decomposition and the thermal reactions between the decomposing biochar and chitosan residues. The first weight drop accounts for about 20% of the weight of the sample, thus the CMBC TGA curve suggests that about 5% wt becomes chitosan residues reacted onto the decomposing char out of the initial chitosan ∼25% mass percentage present from the original synthesis of CMBC. Fig. 1(b) shows the DSC curves for the Chitosan and CMBC. The negative values of heat evolution observed beginning at 130 °C and continuing through 170 °C correspond to an endothermic phenomenon which could be due to the dehydration, nonbound water loss, and loss of low molecular weight organic compounds.45,46 Chitosan and CMBC show exothermic peaks around 300 °C which may relate to the decomposition of amine groups.47 A small endotherm for NMBC exists at ∼170 °C.
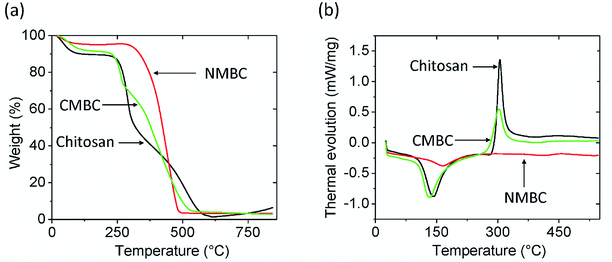 |
| Fig. 1 (a) Thermogravimetric analysis and (b) differential scanning calorimetry analysis for chitosan, CMBC, and NMBC at a heating rate of 10 °C min under air. | |
The elemental composition of biochar depends on a variety of factors such as feedstock type, pyrolysis residence time, temperature, and heating rate. The C and N composition of both NMBC and CMBC from combustion analysis are given in the Fig. S2.† The instrument response for N in CMBC indicates the presence of chitosan. No N was detected in the NMBC sample (Table S1†). The N in the CMBC accounts for about 4.6% of the weight of the CMBC indicating 25/75 chitosan/biochar wt/wt mixture. This compares well to the 25% chitosan composition derived from the weight gain obtained from the synthesis of CMBC. The ∼20% mass loss in the 220–290 °C portion of the TGA shows that about one fifth of the chitosan adsorbed still remained on the biochar at temperatures above 290 °C.
The N2 BET adsorption isotherm (Fig. S3†) and pore size distributions (Fig. S4†) of CMBC and NMBC demonstrate that more N2 is adsorbed by CMBC than by NMBC except in the low-pressure region. The single point surface area of CMBC (7.13 m2 g−1) is smaller than that of NMBC (10.5 m2 g−1), while the total average pore volume of CMBC (0.160 cm3 g−1) is higher than that of the NMBC (0.091 cm3 g−1). This is likely due to blockage of some small biochar pores by chitosan on CMBC, which leads to the high average total pore volume (Table S1†). Both biochars have a large amount of well distributed mesopores with different sizes (Fig. S4†) and negligible micropores (Table S1†).
The ζ-Potential of CMBC under different solution pH values is shown in Fig. S5.† ζ-Potential measures the surface charge present at different solution pH values. CMBC has point of zero ζ-Potential at pH 9.5. Below this pH, the CMBC surface charge is positive, while above pH 9.5 the surface is negative. At pH 7–12, Pb(OH)+ and Pb(OH)2 are the major lead(II) species present in solution and both species will precipitate in this pH range.
The morphological structures of CMBC and NMBC were investigated before lead adsorption using SEM and TEM. SEM images (Fig. S6(a and b)†) of NMBC illustrate that the original mesoporous cell structure morphology of the pine wood largely remains after fast pyrolysis for 20 to 30 s at 425 °C. Areas of the surface pore structure appear to be blocked or partially obscured by deposited chitosan in the CMBC (Fig. S6(c and d)†).
TEM/EDX analysis reveals no nitrogen on NMBC (Fig. S7(a)†) versus substantial surface region nitrogen (5.4 wt%) on CMBC (Fig. S7(b)†) for the selected sample area, confirming chitosan modification in this surface region. Element mapping of N clearly shows that the N is uniformly and densely distributed over the region mapped on the CMBC surface.
3.2. Batch sorption studies
3.2.1. Effect of pH on adsorption. The Pb2+ adsorption of CMBC and NMBC at different initial pH values is shown in Fig. 2. The maximum pH studied was 5 to avoid Pb2+ precipitation (another remediation technique).48 Pb2+ removal by CMBC at equilibrium is more than two times higher than that of NMBC at every solution pH's except at pH 2. Lead removal by both CMBC and NMBC increases with increased pH, as expected from the ζ-potential data, which shows decreasing positive surface charge with increased pH. However, the maximum removal of Pb2+ is at pH 5, where the net surface charge is positive and lead ion repulsion still exists. Therefore, the mechanism of Pb2+ adsorption on CMBC must include specific non-electrostatic interactions to achieve this removal. Possible mechanisms include specific sorption by amine group coordination of Pb2+, physical attraction, precipitation, and reduction.
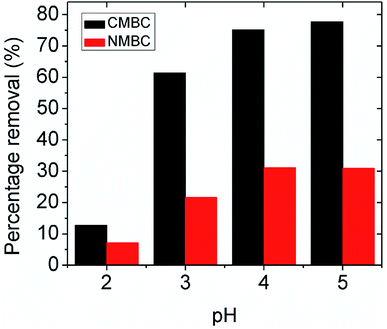 |
| Fig. 2 Percentage removal of lead at equilibrium by NMBC and CMBC at different pH values by 0.05 g adsorbent in 25 mL of aqueous Pb(NO3)2, concentration = 150 mg L−1 at 25 °C. | |
3.2.2. Adsorption mechanisms.
3.2.2.1 pH dependent mechanism. The possible Pb2+ ion adsorption sites on CMBC include the chitosan amino groups, biochar carboxylic acid groups and the aliphatic hydroxyl groups on chitosan and phenolic biochar hydroxyls. Many studies have explored the effect on the chitosan amine group in metal chelation and reported that the C, O, and H atoms are not involved in the lead adsorption.34,35 In this study, the maximum percentage removal was observed at pH 5 (see Fig. 2), where the surface charge is positive (below the point of zero ζ-potential). The surface coating of chitosan on the CMBC surface in water undergoes a pH dependent protonation equilibrium at its primary amine functions.49 Since the chitosan used had 85% of its –NHCOCH3 functions hydrolyzed to amine groups, 85% of its monosaccharide rings contain primary amine functions.Depending on the solution pH, chitosan's basic –NH2 groups will undergo protonation to –NH3+. As the pH rises, the fraction of amine sites that is protonated drops, as illustrated in Table S2.†50 Chitosan adsorbs Pb2+ ions by amino group coordination to Pb2+ ions. This is shown in Scheme 2. As the pH drops (more acidic), less Pb2+ is adsorbed. Strong acids should increasingly remove Pb2+ from the adsorbent.
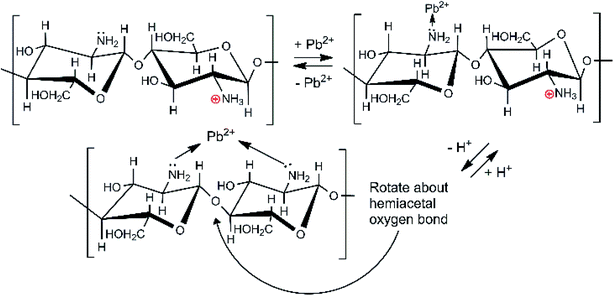 |
| Scheme 2 Chitosan's amino group coordination with Pb2+ ions. | |
As noted in Table S2,† at pH 5 only about 5–6% of the chitosan amine groups are not protonated. Nevertheless, every monomer ring has an –NH2 or –NH2+ function. Thus, even at pH 3, the chitosan can adsorb a substantial amount of Pb2+ by amine coordination.
Surface carboxylic acid sites on the biochar can also complex Pb2+ as they do with Ca2+ and Mg2+ ions via chelation, 2RCOO− + Pb2+ → [(RCOO−)2Pb2+].24 These are acidic sites (pKa ∼4.20–4.75) because their carboxylate conjugate bases are stable and complex metal cations like Pb2+.
3.2.2.2 Mechanistic studies by FTIR and XPS. Comparing the FTIR spectra before and after Pb2+ adsorption suggests the nature of Pb2+ adsorption occurring on the CMBC surface (Fig. 3). A small N–H vibration band shift from 3282 to 3290 cm−1 is observed after Pb2+ adsorption. This indicates the attachment of Pb2+ to the N group affecting the N–H vibration. This observation is in parallel to a previous study where binding of iron ions to NH2 group of chitosan shifted the N–H bending vibration from 1638 to 1681 cm−1.51 Moreover, the subtracted spectrum (Fig. 4) clearly indicates the transmittance drops in the 3534, 1612, 1396 and 1045 cm−1 regions, which are related to the N–H stretching, bending, scissoring and wagging, and C–N stretching bands respectively. All of these changes could be attributed to Pb2+ ions binding onto the amino groups. These results are in accord with those already reported for the Pb2+ adsorption on chitosan/PVA hydrogels.35
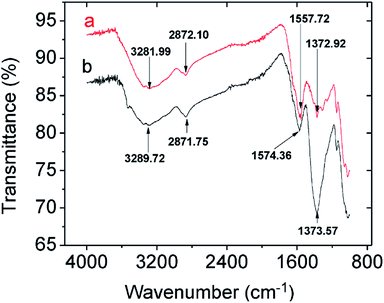 |
| Fig. 3 FTIR spectra of CMBC (a) before lead adsorption (b) after lead adsorption. | |
 |
| Fig. 4 The subtracted FTIR spectrum from spectra obtained before and after lead adsorption onto CMBC. | |
XPS is a powerful tool for studying the surface/near surface (∼100 Å) chemistry of a material. Fig. S8(a)† shows the chitosan XPS spectrum and Figs. S8(b) and (c)† show the XPS spectra for CMBC before and after the lead adsorption. Nearly identical peak positions with different intensities were observed with chitosan and CMBC illustrating the successful coating of chitosan on the biochar surface. Following adsorption, the 4f peak for lead appears in Fig. S8(c)† indicating the adsorption of lead on the surface of CMBC.
High resolution XPS spectra of chitosan and CMBC before and after lead adsorption (Fig. 5) revealed the presence of two N 1s peaks upon deconvolution. Both amide nitrogen at 400.43 eV and amine nitrogen at 399.26 eV are present for this ∼85% deacylated chitin. The peak at binding energy 400.43 eV is attributed to the N atom in the R–NHCOCH3 (amide) group, and the peak at binding energy 399.26 eV is attributed to the N atom in the R–NH2 group (chitosan).52 Each peak's relative intensity is proportional to the percentage of each component in that material (Fig. 5(a)).
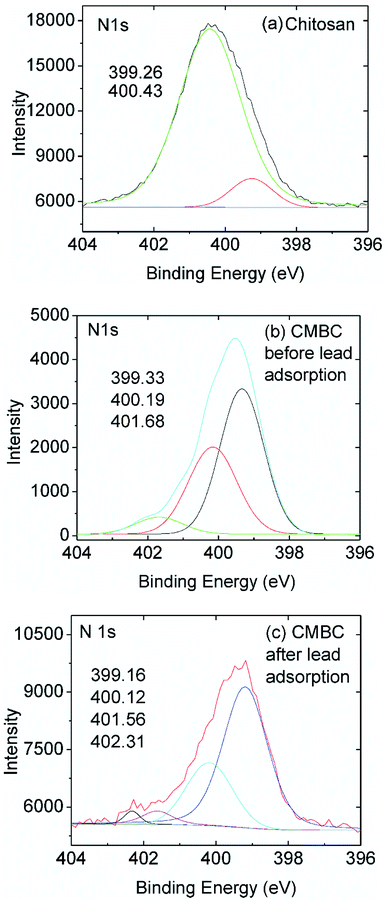 |
| Fig. 5 High resolution N 1s XPS spectra of (a) chitosan and (b) CMBC before and (c) CMBC after lead adsorption. | |
The XPS N 1s spectrum of CMBC has three resolved peaks with binding energies of 399.33, 400.19, and 401.68 eV (Fig. 5(b)). The binding energy of the first two match the XPS spectrum of chitosan. This indicates that the functional groups of chitosan remained on the biochar surface even after the chitosan coating modification of the biochar. The additional peak at a binding energy of 401.68 is attributed to the N atom in the protonated R–NH2 group confirming that a positive charge is present on the biochar surface as shown from the ζ-potential. After lead adsorption, CMBC exhibits four N 1s peaks at binding energies of 399.16, 400.12, 401.56 and 402.31 eV (Fig. 5(C)). The first three peaks belong to amine, amide, and protonated amine N atoms, similar to the previous XPS spectrum of CMBC before lead adsorption. The fourth N peak at 402.31 eV is attributed to amine functions coordinated to Pb2+ sites [ R–NH2 → Pb2+ and/or (R–NH2)2Pb2+ chelated sites].
3.2.3. Sorption dynamics. The effect of temperature on lead adsorption was studied using 2 g L−1 of CMBC, 150 mg L−1 Pb2+, shaking for 24 h, pH of 5 at 298, 308, and 318 K. Significant lead adsorption was observed within 1 h and equilibrium was reached after approximately 6 h (Fig. S9†). The amount of lead adsorption at 298 and 308 K were similar, while greater adsorption occurred at 318 K, suggesting endothermic behavior. All kinetic studies were carried out over 6 h to ensure that equilibrium was achieved.The effect of Pb2+ concentrations on adsorption was studied using 25 mL of 150, 175, and 230 mg L−1 lead solutions, 2 g L−1 of CMBC, and 6 h shaking at pH 5. Adsorption capacity increased with increasing initial lead concentration, and a significant adsorption capacity increment was observed upon increased Pb2+ from 175 mg L−1 to 230 mg L−1 (Fig. S10†).
3.2.4. Adsorption kinetics. The pseudo first order linear kinetics model53 was fit to
where, qt is the amount of lead adsorbed at time “t”, qe is the amount adsorbed at equilibrium, and k1 (h−1) is the first order adsorption rate constant. Plots of log(qe − qt) versus t can be found in Fig. S11† for lead solutions of 150, 175, and 230 mg L−1 at 298, 308, and 318 K. The parameters, correlation coefficients (0.915–0.970) for the first order kinetics model and the calculated versus observed qe values (Table S3†) were not satisfactory. Thus, pseudo second order fittings were conducted.The linear version of the pseudo second order kinetics model54 is given by,
where,
qt is the amount of lead adsorbed at time “
t”,
qe is the amount adsorbed at equilibrium, and
k2 (h
−1) is the second order adsorption rate constant. Linear plots of
t/
qt vs. t (slope of 1/
qe) are shown in Fig. S12.
† The second order kinetic model parameters for the lead solutions of 150, 175, and 230 mg L
−1 at 298, 308, and 318 K are provided in
Table 1. The correlation coefficients for the second order kinetics model are all larger than 0.991, and the calculated
qe values and the experimental
qe values matched well. We conclude lead adsorption on CMBC is second order.
Table 1 Pseudo-second order parameters for lead adsorption (pH = 5) at (a) 298 K, (b) 308 K, and (c) 318 K for Pb2+ concentrations of 150, 175, and 230 mg L−1, using 2 g CMBC/L
Pseudo-second order parameters on CMBC |
Temp. (K) |
Initial conc. (mg L−1) |
qe exp. (mg g−1) |
qe calc. (mg g−1) |
k2 (g m g−1 h) |
R2 |
298 |
150 |
63.8 |
62.5 |
0.085 |
0.999 |
175 |
79.6 |
71.4 |
0.049 |
0.991 |
230 |
88.3 |
83.3 |
0.072 |
0.996 |
308 |
150 |
63.6 |
66.7 |
0.056 |
0.998 |
175 |
76.1 |
83.3 |
0.048 |
0.999 |
230 |
91.3 |
90.9 |
0.061 |
0.996 |
318 |
150 |
73.4 |
76.9 |
0.084 |
0.999 |
175 |
79.5 |
83.3 |
0.072 |
0.998 |
230 |
96.1 |
100 |
0.100 |
0.999 |
3.2.5. Adsorption isotherm models. The lead adsorption on CMBC was studied using different adsorption isotherm models. Adsorption isotherm data were collected at 298, 308, and 318 K, Pb2+ concentrations from 3–350 mg L−1, using a 12 h shaking period. The data was evaluated using the two parameter Langmuir55 and Freundlich,56 models applying a nonlinear regression calculated employing OriginPro 2016 software (Fig. S13†).The endothermic behavior of lead adsorption on CMBC is further indicated by the adsorption isotherm studies, which show greater amounts of adsorption at higher temperatures. The isotherm parameters are shown in Table 2. Pb2+ uptake is endothermic for oak wood and oak bark biochar,2 as well as pine wood and rice husk biochar.57 Higher temperatures also favored significant increases of Cu(II) and Zn(II) adsorption onto corn straw and hardwood biochars.58 The chitosan coating renders CMBC surfaces amine-group rich, hence chemically different than biochar surfaces.
Table 2 Langmuir and Freundlich model parameters for Pb2+ adsorption on CMBC
Isotherm parameters |
298 K |
308 K |
318 K |
Langmuir |
Q0 (mg g−1) |
50.5 |
103 |
134 |
b |
0.0791 |
0.0149 |
0.0113 |
R2 |
0.996 |
0.994 |
0.988 |
Freundlich |
Kf (mg g−1) |
13.5 |
6.58 |
6.33 |
n |
3.82 |
2.09 |
1.93 |
R2 |
0.999 |
0.996 |
0.994 |
The Langmuir model provided a better fit than the Freundlich model with R2 values all greater than 0.988. This favors a proposed monolayer lead adsorption mechanism (an assumption in the Langmuir model) for Pb2+ ion binding. This observation is consistent with previous studies of heavy metal ion adsorption onto amine-functionalized materials.59 In a previous study of Pb2+ adsorption on magnetic (containing Fe3O4) char, diffusion controlled adsorption was suggested at low Pb2+ concentrations and monomolecular adsorption at high Pb2+ concentrations.60
Lead adsorption on CMBC is mainly due to the chitosan amine functions coordinating to Pb2+ with additional adsorption by the biochar. The CMBC Langmuir adsorption capacity is 134 mg g−1 at 318 K compared to a value of 48.2 mg g−1 for the NMBC, despite the fact that CMBC has only 68% of NMBC's surface area. This value is also much higher than previously reported biochar capacities for the lead adsorption (Table 3).
Table 3 Comparison of CMBCs' Pb2+ adsorption capacity with those of pine wood, bamboo, potato peel biochar, chitosan, and activated carbon (carbon F-400)
Adsorbent |
pH |
Temp. (K) |
Conc. range (mg L−1) |
Surface area (m2 g−1) |
Pb2+ adsorption capacity (mg g−1) |
Pb2+ adsorption capacity (mg m−2) |
Ref. |
Chitosan-modified pine wood biochar (CMBC) |
5.0 |
298 |
50–350 |
7.13 |
50.5 |
7.08 |
This study |
308 |
103 |
14.4 |
318 |
134 |
18.8 |
Non-modified pine wood biochar (NMBC) |
5.0 |
318 |
10–350 |
10.5 |
48.2 |
4.59 |
This study |
Chitosan-modified bamboo biochar (BB-C) |
5.5 |
298 |
2–100 |
166.9 |
14.3 |
0.085 |
34 |
Chitosan-modified potato peel biochar |
Not available |
Not available |
Not available |
Not available |
0.147 |
— |
40 |
Chitosan and pyromellitic- modified rice straw biochar (CPMB) |
5 |
298 |
5–500 |
62.6 |
9.24 |
0.15 |
39 |
303 |
11.91 |
0.19 |
308 |
13.93 |
0.22 |
Chitosan |
4.5 |
293 |
10–1000 |
Not available |
0.558 (mmol g−1) |
— |
61 |
Carbon F-400 |
5.0 |
278 |
0.125–100 |
984 |
44.3 |
0.0450 |
2 |
298 |
30.1 |
0.0306 |
323 |
25.2 |
0.0256 |
3.3. Fixed-bed studies
A column (length = 20 cm; diameter = 1 cm) packed with 1 g of CMBC was used to study Pb2+ sorption. A gravity propelled Pb2+ solution (150 mg L−1, pH = 5) ran through the column at flow rate of 2.5 mL min−1 until column saturation was reached. A breakthrough curve using the normalized concentration (Ce/Co) versus time is shown in Fig. 6.
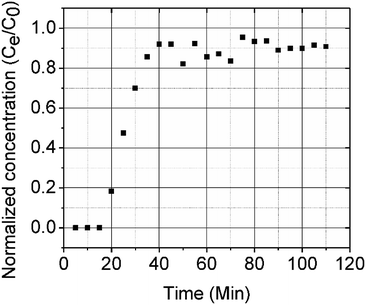 |
| Fig. 6 CMBC breakthrough curve (Pb2+ concentration = 150 mg L−1, pH = 5). | |
The column parameters were obtained by analyzing the column experimental data. Following mathematical expressions were used.62
|
 | (1) |
|
 | (2) |
|
 | (3) |
|
 | (4) |
|
 | (5) |
|
 | (6) |
|
 | (7) |
|
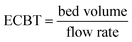 | (8) |
where
tx is the total time involved for primary adsorption zone establishment,
tδ is the time for the primary adsorption zone (PAZ) to move down to its length,
δ is the length of the primary adsorption zone,
f is the fractional capacity,
D is the bed depth,
tb is the time required for initial PAZ formation,
Fm is the mass rate of flow to the adsorber,
Vb and
Vx are the total effluent mass quantity per unit adsorbent area at the breakpoint, and the total effluent mass quantity per unit adsorbent area when adsorbent is approaching saturation, respectively.
Cx is the effluent concentrations at
Vx. The percent saturation of column at breakthrough, bed volume, and the empty-bed-contact-time (EBCT) were also calculated.
Table 4 summarizes the values of all the column parameters. The obtained column capacity (5.8 mg g
−1) is significantly lower than batch adsorption capacity (134 mg g
−1). This observation is similar to those reported for Pb
2+ adsorption by tea waste and modified activated carbon.
7,63
Table 4 Fixed bed parameters for Pb2+ adsorption by CMBC
Parameters |
Values |
Column diameter (cm) |
1.0 |
Column radius (cm) |
0.5 |
Bed volume (cm3) |
3.9 |
Column capacity (mg g−1) |
5.8 |
Breakpoint capacity (mg g−1) |
0.16 |
Co (mg mL−1) |
0.15 |
Cx (mg mL−1) |
0.13 |
Vb (mg cm−2) |
6.5 |
Vx (mg cm−2) |
12.1 |
tx (min) |
110 |
Fm (mg cm−2 min) |
0.11 |
D (cm) |
5.0 |
tb (min) |
55 |
tδ (min) |
50.5 |
F |
−0.09 |
δ (cm) |
2.5 |
EBCT (min) |
1.6 |
Saturation (%) |
45.50 |
4. Conclusions
Pine wood biochar was modified through a surface deposition of chitosan which greatly increased the Pb2+ adsorption capacity. Chitosan deposition allowed rapid flow through columns or beds due to the biochar particle sizes. Maximum lead removal occurred at pH 5 and 318 K displaying the pH dependent and endothermic behavior for lead adsorption. Pseudo-second order kinetics provided the best fit with regression coefficients of 0.991 or greater. Sorption was evaluated from 298 to 318 K using the Freundlich and Langmuir isotherm models and best fit observed with the Langmuir model. A fixed-bed column study for Pb2+ showed a column capacity of 5.8 mg g−1. The Pb2+ adsorption mechanism on CMBC biochar was mainly controlled by the coordination between the chitosan amine groups and Pb2+ ions based on FTIR and XPS evidence. CMBC has great potential for heavy metal contaminant removal from aqueous solution.
Conflicts of interest
There are no conflicts to declare.
Acknowledgements
The authors would like to acknowledge support from the University Grants Commission for the Joint Research Program entitled “Indo-US initiatives on Cleaner Energy and Water 17 Research” between Jawaharlal Nehru University and Mississippi State University Chemistry Department for support of this project. The authors are also thankful to Griffin Burk and Guangchao Liang, Mississippi State University Chemistry Department, for fitting data with OriginPro software and for drawing chemical structures for us.
References
- P. Gottesfeld and A. K. Pokhrel, J. Occup. Environ. Hyg., 2011, 8, 520–532 CrossRef PubMed.
- D. Mohan, C. U. Pittman Jr., M. Bricka, F. Smith, B. Yancey, J. Mohammad, P. H. Steele, M. F. Alexandre-Franco, V. Gómez-Serrano and H. Gong, J. Colloid Interface Sci., 2007, 310, 57–73 CrossRef PubMed.
- M. Momčilović, M. Purenović, A. Bojić, A. Zarubica and M. Ranđelović, Desalination, 2011, 276, 53–59 CrossRef.
- A. Demayo, M. C. Taylor, K. W. Taylor, P. V. Hodson and P. B. Hammond, Crit. Rev. Environ. Control, 1982, 12, 257–305 CrossRef.
- A. C. D. Santos, S. Colacciopo, C. M. R. D. Bó and N. A. G. D. Santos, Am. J. Ind. Med., 1994, 26, 635–643 CrossRef PubMed.
- K. M. Cecil, C. J. Brubaker, C. M. Adler, K. N. Dietrich, M. Altaye, J. C. Egelhoff, S. Wessel, I. Elangovan, R. Hornung, K. Jarvis and B. P. Lanphear, PLoS Med., 2008, 5, e112 CrossRef PubMed.
- J. Goel, K. Kadirvelu, C. Rajagopal and V. Kumar Garg, J. Hazard. Mater., 2005, 125, 211–220 CrossRef PubMed.
- G. Dermont, M. Bergeron, G. Mercier and M. Richer-Laflèche, J. Hazard. Mater., 2008, 152, 1–31 CrossRef PubMed.
- G. Wu, H. Kang, X. Zhang, H. Shao, L. Chu and C. Ruan, J. Hazard. Mater., 2010, 174, 1–8 CrossRef PubMed.
- I. Ali and V. K. Gupta, Nat. Protoc., 2007, 1, 2661–2667 CrossRef PubMed.
- R. Li, J. J. Wang, L. A. Gaston, B. Zhou, M. Li, R. Xiao, Q. Wang, Z. Zhang, H. Huang, W. Liang, H. Huang and X. Zhang, Carbon, 2018, 129, 674–687 CrossRef.
- M. Minamisawa, H. Minamisawa, S. Yoshida and N. Takai, J. Agric. Food Chem., 2004, 52, 5606–5611 CrossRef PubMed.
- F. Luo, Y. Liu, X. Li, Z. Xuan and J. Ma, Chemosphere, 2006, 64, 1122–1127 CrossRef PubMed.
- S. Klimmek, H. J. Stan, A. Wilke, G. Bunke and R. Buchholz, Environ. Sci. Technol., 2001, 35, 4283–4288 CrossRef PubMed.
- V. K. Gupta and S. Sharma, Environ. Sci. Technol., 2002, 36, 3612–3617 CrossRef PubMed.
- A. G. Karunanayake, O. A. Todd, M. L. Crowley, L. B. Ricchetti, C. U. Pittman Jr., R. Anderson and T. E. Mlsna, Chem. Eng. J., 2017, 319, 75–88 CrossRef.
- M. Essandoh, B. Kunwar, C. U. Pittman Jr., D. Mohan and T. Mlsna, Chem. Eng. J., 2015, 265, 219–227 CrossRef.
- A. R. Betts, N. Chen, J. G. Hamilton and D. Peak, Environ. Sci. Technol., 2013, 47, 14350–14357 CrossRef PubMed.
- V. K. Gupta, I. Ali, Suhas and D. Mohan, J. Colloid Interface Sci., 2003, 265, 257–264 CrossRef PubMed.
- D. Mohan, C. U. Pittman Jr. and P. H. Steele, J. Colloid Interface Sci., 2006, 297, 489–504 CrossRef PubMed.
- D. Mohan and C. U. Pittman Jr., J. Hazard. Mater., 2006, 137, 762–811 CrossRef PubMed.
- A. G. Karunanayake, N. Bombuwala Dewage, O. A. Todd, M. Essandoh, R. Anderson, T. Mlsna and D. Mlsna, J. Chem. Educ., 2016, 93, 1935–1938 CrossRef.
- X. Cao, L. Ma, B. Gao and W. Harris, Environ. Sci. Technol., 2009, 43, 3285–3291 CrossRef PubMed.
- R. Li, W. Liang, J. J. Wang, L. A. Gaston, D. Huang, H. Huang, S. Lei, M. K. Awasthi, B. Zhou, R. Xiao and Z. Zhang, J. Environ. Manage., 2018, 212, 77–87 CrossRef PubMed.
- D. H. K. Reddy and S. M. Lee, Colloids Surf., A, 2014, 454, 96–103 CrossRef.
- S. Wang, B. Gao, Y. Li, A. Mosa, A. R. Zimmerman, L. Q. Ma, W. G. Harris and K. W. Migliaccio, Bioresour. Technol., 2015, 181, 13–17 CrossRef PubMed.
- C. Gan, Y. Liu, X. Tan, S. Wang, G. Zeng, B. Zheng, T. Li, Z. Jiang and W. Liu, RSC Adv., 2015, 5, 35107–35115 RSC.
- A. Rawal, S. D. Joseph, J. M. Hook, C. H. Chia, P. R. Munroe, S. Donne, Y. Lin, D. Phelan, D. R. G. Mitchell, B. Pace, J. Horvat and J. B. W. Webber, Environ. Sci. Technol., 2016, 50, 7706–7714 CrossRef PubMed.
- N. Bombuwala Dewage, A. S. Liyanage, C. U. Pittman Jr., D. Mohan and T. Mlsna, Bioresour. Technol., 2018, 263, 258–265 CrossRef PubMed.
- A. G. Karunanayake, O. A. Todd, M. Crowley, L. Ricchetti, C. U. Pittman Jr., R. Anderson, D. Mohan and T. Mlsna, Chem. Eng. J., 2018, 331, 480–491 CrossRef.
- M. N. V. Ravi Kumar, React. Funct. Polym., 2000, 46, 1–27 CrossRef.
- R. S. Juang and H. J. Shao, Water Res., 2002, 36, 2999–3008 CrossRef PubMed.
- W. S. Wan Ngah, L. C. Teong and M. A. K. M. Hanafiah, Carbohydr. Polym., 2011, 83, 1446–1456 CrossRef.
- Y. Zhou, B. Gao, A. R. Zimmerman, J. Fang, Y. Sun and X. Cao, Chem. Eng. J., 2013, 231, 512–518 CrossRef.
- L. Jin and R. Bai, Langmuir, 2002, 18, 9765–9770 CrossRef.
- W. L. Yan and R. Bai, Water Res., 2005, 39, 688–698 CrossRef PubMed.
- M. W. Wan, C. C. Kan, B. D. Rogel and M. L. P. Dalida, Carbohydr. Polym., 2010, 80, 891–899 CrossRef.
- L. Ronghua, L. Wen, H. Hui, J. Shuncheng, G. Di, L. Manlin, Z. Zengqiang, A. Amajd and J. J. Wang, J. Appl. Polym. Sci., 2018, 135, 46239 CrossRef.
- J. Deng, Y. Liu, S. Liu, G. Zeng, X. Tan, B. Huang, X. Tang, S. Wang, Q. Hua and Z. Yan, J. Colloid Interface Sci., 2017, 506, 355–364 CrossRef PubMed.
- A. Hussain, J. Maitra and K. A. Khan, Appl. Water Sci., 2017, 7, 4525–4537 CrossRef.
- D. Mohan, A. Sarswat, Y. S. Ok and C. U. Pittman Jr., Bioresour. Technol., 2014, 160, 191–202 CrossRef PubMed.
- L. Ingram, D. Mohan, M. Bricka, P. Steele, D. Strobel, D. Crocker, B. Mitchell, J. Mohammad, K. Cantrell and C. U. Pittman Jr., Energy Fuels, 2008, 22, 614–625 CrossRef.
- D. Mohan, C. U. Pittman Jr. and P. H. Steele, Energy Fuels, 2006, 20, 848–889 CrossRef.
- M. Chiban, A. Soudani, F. Sinan and M. Persin, J. Environ. Manage., 2012, 95(suppl.), S61–S65 CrossRef PubMed.
- L. Sun, M. Li, C. Ma and P. Li, Fuel, 2017, 206, 27–33 CrossRef.
- I. Boumanchar, Y. Chhiti, F. E. M'hamdi Alaoui, A. El Ouinani, A. Sahibed-Dine, F. Bentiss, C. Jama and M. Bensitel, Waste management, 2017, 61, 78–86 CrossRef PubMed.
- L. S. Guinesi and É. T. G. Cavalheiro, Thermochim. Acta, 2006, 444, 128–133 CrossRef.
- L. Charerntanyarak, Water Sci. Technol., 1999, 39, 135–138 CrossRef.
- J. J. Park, X. Luo, H. Yi, T. M. Valentine, G. F. Payne, W. E. Bentley, R. Ghodssi and G. W. Rubloff, Lab Chip, 2006, 6, 1315–1321 RSC.
- P. Udaybhaskar, L. Iyengar and A. V. S. P. Rao, J. Appl. Polym. Sci., 1990, 39, 739–747 CrossRef.
- H. V. Tran, L. D. Tran and T. N. Nguyen, Mater. Sci. Eng., C, 2010, 30, 304–310 CrossRef.
- G. Lawrie, I. Keen, B. Drew, A. Chandler-Temple, L. Rintoul, P. Fredericks and L. Grøndahl, Biomacromolecules, 2007, 8, 2533–2541 CrossRef PubMed.
- S. Lagergren, Band, 1898, 24, 1–39 Search PubMed.
- Y. S. Ho, J. C. Y. Ng and G. McKay, Sep. Sci. Technol., 2001, 36, 241–261 CrossRef.
- I. Langmuir, J. Am. Chem. Soc., 1918, 40, 1361–1403 CrossRef.
- H. Freundlich, J. Phys. Chem., 1906, 57, e470 Search PubMed.
- Z. Liu and F. S. Zhang, J. Hazard. Mater., 2009, 167, 933–939 CrossRef PubMed.
- X. Chen, G. Chen, L. Chen, Y. Chen, J. Lehmann, M. B. McBride and A. G. Hay, Bioresour. Technol., 2011, 102, 8877–8884 CrossRef PubMed.
- J. Aguado, J. M. Arsuaga, A. Arencibia, M. Lindo and V. Gascón, J. Hazard. Mater., 2009, 163, 213–221 CrossRef PubMed.
- D. Mohan, H. Kumar, A. Sarswat, M. Alexandre-Franco and C. U. Pittman Jr., Chem. Eng. J., 2014, 236, 513–528 CrossRef.
- J. C. Y. Ng, W. H. Cheung and G. McKay, Chemosphere, 2003, 52, 1021–1030 CrossRef PubMed.
- R. Sharma, A. Sarswat, C. U. Pittman Jr. and D. Mohan, RSC Adv., 2017, 7, 8606–8624 RSC.
- B. M. W. P. K. Amarasinghe and R. A. Williams, Chem. Eng. J., 2007, 132, 299–309 CrossRef.
Footnote |
† Electronic supplementary information (ESI) available. See DOI: 10.1039/c8ra04600j |
|
This journal is © The Royal Society of Chemistry 2018 |
Click here to see how this site uses Cookies. View our privacy policy here.