DOI:
10.1039/C8RA06506C
(Paper)
RSC Adv., 2018,
8, 30180-30185
DABCO-catalyzed Knoevenagel condensation of aldehydes with ethyl cyanoacetate using hydroxy ionic liquid as a promoter†
Received
2nd August 2018
, Accepted 14th August 2018
First published on 28th August 2018
Abstract
N-(2-Hydroxy-ethyl)-pyridinium chloride ([HyEtPy]Cl) was synthesized and explored as a novel promoter for 1,4-diazabicyclo [2.2.2] octane (DABCO)-catalyzed Knoevenagel condensation reactions, which showed better catalytic activity compared to other ionic liquid (IL) that had no hydroxyl group attached to the IL scaffold. The effect of hydrogen bond formation between the hydroxyl group of [HyEtPy]Cl and the carbonyl group of aldehyde played an important role in the Knoevenagel condensation reaction. In the [HyEtPy]Cl–H2O–DABCO composite system, Knoevenagel condensation reactions proceeded smoothly and cleanly, and the corresponding Knoevenagel condensation products were obtained in good to excellent yields in all cases examined. This protocol provides a versatile solvent–catalyst system, which has notable advantages such as being eco-friendly, ease of work-up and convenient reuse of the ionic liquid.
Introduction
The Knoevenagel reaction, which was discovered by Knoevenagel in 1896, is a condensation reaction between activated methylene and carbonyl compounds.1 Owing to the fact that the α,β-unsaturated carbonyl compounds produced by Knoevenagel reaction can further be used in the synthesis of fine chemicals,2 therapeutic drugs,3 natural products4 and functional polymers,5 research on this reaction has been a hot topic in organic synthesis. In recent years, a large number of catalytic systems were developed for this reaction and various new catalysts such as functionalized MOFs,6 functionalized fibers,7 simple molecular complexes,8 C3N4,9 cage,10 copper powder,11 zeolites,12 enzymes,13 polymers,14 bovine serum albumin,15 magnetic nanoparticles,16 graphene oxide17 and ammonium salts18 have been employed to catalyze this reaction, each affording variable yields of Knoevenagel condensation compounds. However, even for the most favorable systems, this reaction often suffers from expensive catalysts, laborious work-up procedures, long reaction times and use of organic solvents or toxic metals. Hence, there is an existing need for developing efficient and new methods based on green chemistry to improve the Knoevenagel condensation reaction.
Currently, ionic liquids (ILs) are receiving great attention for their application as innovative solvents or additives in a variety of organic reactions.19 In comparison to the common molecular solvents, the main characteristic of ILs is that they are completely composed of ions, which makes them ideal candidates to stabilize the intermediate of the addition reaction.20 For the Knoevenagel reaction, the base-catalyzed addition to a carbonyl group results from the nucleophilic attack of a strong nucleophile followed by protonation. Acid-catalyzed addition begins with protonation, followed by the attack of a weaker nucleophile. Protonation of the carbonyl oxygen atom plays an important role in the Knoevenagel reaction and hydrogen bond formation between the carbonyl group and the solvent or catalyst can accelerate this reaction. Based on the catalytic effect of hydrogen bond formation on the reaction and the stabilizing effect of ionic liquid on the reaction intermediate, we speculate that the use of an ionic liquid containing a hydroxyl group may exert an excellent accelerating effect. This deduction was considered to be reasonable because it was observed previously that hydroxyl groups or active hydrogens in an amine type catalyst did exert accelerating effects on some coupling reactions.21
To meet our research interests, the ionic salt containing hydroxyl group was synthesized and applied in the DABCO-catalyzed Knoevenagel reaction (Scheme 1). To our delight, a significant beneficial effect of the ionic salt ([HyEtPy]Cl) over its non-hydroxyl counterpart was observed, and short reaction time and good to excellent yields of products were achieved. Herein, we would like to present the catalytic application of the hydroxyl pyridinium ionic liquid ([HyEtPy]Cl) in the Knoevenagel reaction.
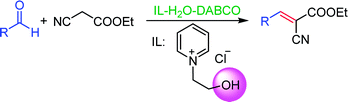 |
| Scheme 1 Knoevenagel condensation reaction. | |
More recently, amine-functionalized ionic liquids,22 protic ionic liquid23 and DABCO24 or pyrrolidinium25 based ionic liquids were employed in the Knoevenagel reaction. The use of these ionic liquids effectively facilitated the Knoevenagel reaction. Some even achieved excellent results. However, the preparation of these ionic liquids often involved a consecutive quaternization–metathetic procedure, which made them expensive and their large scale industrial application difficult.26 Therefore, exploration of low cost, simple synthesis of ionic liquids and their use in organic synthesis will be of significance. At present, halogenated ionic salts can be easily prepared with high yields in large scale by one-step reaction of tertiary amines, tertiary phosphines or heterocyclic compounds containing nitrogen with halogenated hydrocarbons, but these ionic salts are mostly solid at room temperature, which hampers their direct use as solvents in organic reactions.27
Recently, as an environment friendly solvent, water has been used to promote organic reaction.28 To the best of our knowledge, it is generally easy to dissolve halogenated ionic salts in water to form homogeneous systems. Compared to pure ionic salts or water, the homogeneous system made up of water and ionic salts may have more excellent properties, which helps in the application of solid state halogenated ionic salts in organic reactions. Based on this point, the ionic salt containing hydroxyl group, 1-(2-hydroxy-ethyl)-pyridinium chloride ([HyEtPy]Cl), was conveniently synthesized by a one-step reaction according to literature procedures.29 Then, it was mixed with water, and the water–ionic liquid composite system formed was used in the Knoevenagel reaction of 4-chlorobenzaldehyde with ethyl cyanoacetate. Experimental results are summarized in Table 1.
Table 1 Effects of the [HyEtPy]Cl–H2O–DABCO composite system on Knoevenagel condensationa

|
Entry |
Solvent–catalyst system |
Temperature |
Time (min) |
Yieldb (%) |
General reaction conditions: IL ([HyEtPy]Cl, 3 g), H2O (3 mL), DABCO (10 mmol), 4-chlorobenzaldehyde (10 mmol), ethyl cyanoacetate (12 mmol). Refers to work-up yield. Almost no product was detected. H2O (6 mL). H2O(1.5 mL). DABCO (20 mmol). DABCO (30 mmol). IL is [PrPy]Cl (3 g). IL is [BuPy]Cl (3 g). |
1 |
IL–H2O–HMTA |
30 °C |
40 |
61 |
2 |
IL–H2O–K2CO3 |
30 °C |
40 |
NDc |
3 |
IL–H2O–NaOH |
30 °C |
40 |
36 |
4 |
IL–H2O–DABCO |
30 °C |
40 |
72 |
5 |
IL–H2O–DABCO |
40 °C |
20 |
86 |
6 |
IL–H2O–DABCO |
50 °C |
10 |
92 |
7 |
IL–H2O–DABCO |
60 °C |
10 |
88 |
8d |
IL–H2O–DABCO |
50 °C |
20 |
85 |
9e |
IL–H2O–DABCO |
50 °C |
30 |
82 |
10f |
IL–H2O–DABCO |
50 °C |
10 |
98 |
11g |
IL–H2O–DABCO |
50 °C |
10 |
98 |
12 |
IL–H2O |
50 °C |
30 |
ND |
13 |
H2O–DABCO |
50 °C |
30 |
46 |
14h |
IL–H2O–DABCO |
50 °C |
20 |
82 |
15i |
IL–H2O–DABCO |
50 °C |
20 |
84 |
As seen in Table 1, in the presence of water–ionic liquid composite system, moderate yield of 61% and good yield of 72% were obtained when the organic base hexamethylenetetramine (HMTA) or DABCO was used (Table 1, entries 1 and 4), and for the inorganic weak base K2CO3, almost no product was detected (Table 1, entry 2). Unfortunately, when the inorganic base NaOH was used, only 36% yield was obtained (Table 1, entry 3); it may be caused by Cannizzaro reaction of the aldehyde and hydrolysis of ethyl cyanoacetate in the presence of NaOH. When the reaction temperature was changed (Table 1, entries 4–7), the yield too changed, and the best yield of 92% was obtained at 50 °C (Table 1, entry 6). The reasons for this might be attributed to two factors: (i) high temperature enhanced the molecular reaction; and (ii) high temperature improved the solubility of the raw material and product and effectively avoided the inclusion of raw material with the product. However, when the temperature was higher than 50 °C, the reaction color became darker and the yield decreased, which may be caused by enhanced side reaction. Further optimization of reaction conditions revealed that the amount of H2O also affected the reaction. When the amount of water was 50% (Table 1, entry 6), excellent yield of 92% was obtained after 10 min. When the amount of H2O was increased or decreased, the reaction time got significantly longer (Table 1, entries 8 and 9). After careful observation of the reaction, we noticed that the reaction system had insoluble raw material when the amount of water was increased to over 50% or decreased to less than 50%. This suggested that the amount of water, more than or less than 50%, can reduce the dissolution of raw material, which may affect the product yield. Further, increase in the amount of DABCO resulted in increase in the yield, and the highest reaction yield of 98% was obtained when 20 mmol DABCO was added (Table 1, entry 10). However, the reaction time and yield remained same when the amount of catalyst was changed to 30 mmol (Table 1, entry 11). To further confirm that the enhancement was from the [HyEtPy]Cl–H2O–DABCO composite system, the [HyEtPy]Cl–H2O and H2O–DABCO composite system were used to test this reaction (Table 1, entries 12 and 13). In the [HyEtPy]Cl–H2O composite system, the product was not detected after 30 min, and in the H2O–DABCO composite system, only 46% yield was obtained after 30 min. Indeed, the ionic salt [HyEtPy]Cl played an important role in the solvent–catalyst system. Comparing the ionic salt [HyEtPy]Cl with N-propylpyridinium chloride ([PrPy]Cl) (Table 1, entry 14) and N-butylpyridinium chloride ([BuPy]Cl) (Table 1, entry 15), the hydroxyl ionic salt [HyEtPy]Cl provided slightly better results in terms of reaction yield and reaction time. Considering the similarity in the structures of the three pyridinium ionic salts, it was envisioned that the hydroxyl group in the ionic liquid [HyEtPy]Cl was responsible for its higher activity, and [HyEtPy]Cl itself served as a protic additive to promote the Knoevenagel reaction in a manner similar to protic additives in conventional cases. Analysis of the results of Table 1 showed that the [HyEtPy]Cl–H2O–DABCO composite system was most suitable for the Knoevenagel reaction, and the best yield of 98% and the shortest reaction time of 10 min were obtained (Table 1, entry 10).
To further explore the catalytic efficacy of the [HyEtPy]Cl–H2O–DABCO composite system in Knoevenagel condensation, a number of aromatic aldehydes were chosen to condense with general active ethyl 2-cyanoacetate; the results are summarized in Table 2. The reaction was found to be applicable to aromatic aldehydes bearing various substituent groups such as nitro, chloro, cyano, methoxyl, hydroxyl, etc., and good to excellent yields (83–99%) were obtained in short reaction times (5–40 min). Electron-rich salicylic aldehyde, which is usually an inert substrate, could provide a fairly good yield (86%, entry 11) under the present conditions. The reactions of ethyl 2-cyanoacetate with electron-deficient 4-nitrobenzaldehyde, 4-fluorobenzaldehyde and 4-cyanobenzaldehyde provided excellent yields of 99% (entry 9), 97% (entry 5) and 98% (entry 8), respectively. Interestingly, when terephthalaldehyde was used as substrate, two aldehyde groups reacted with ethyl 2-cyanoacetate, and excellent yield of 91% of dual Knoevenagel adduct was obtained (entry 12). Generally, aromatic aldehydes bearing electron-withdrawing groups reacted more easily than those containing electron-donating groups.
Table 2 Knoevenagel condensation of aldehydes with ethyl cyanoacetatea
To evaluate the possibility of recycling the composite system ([HyEtPy]Cl–H2O) used for the Knoevenagel reaction, ethyl cyanoacetate (12 mmol) and DABCO (20 mmol) were added to a solution of 4–chlorobenzaldehyde (10 mmol) in the composite system [HyEtPy]Cl–H2O (3 mL H2O and 3 g [HyEtPy]Cl). The reaction mixture was stirred at 50 °C. The reaction progress was monitored by thin layer chromatography (TLC) until the aldehyde was consumed. The reaction mixture was extracted with diethyl ether (2 × 20 mL). The combined diethyl ether mixture was washed with saturated brine (2 × 20 mL) and dried over anhydrous Na2SO4, and then the solvent was removed on a rotary vacuum evaporator and almost pure product was obtained. Then, 4-chlorobenzaldehyde, ethyl cyanoacetate and DABCO were added to the recycled composite system [HyEtPy]Cl–H2O to repeat the reaction. The recovered composite system was used at least six times without notable reduction in the reaction yields (Table 3, entries 1–6).
Table 3 Reuse of the solvent system [HyEtPy]Cl–H2Oa

|
Cycle |
Time (min) |
Yield (%) |
General reaction conditions: [HyEtPy]Cl (3 g), H2O (3 mL), DABCO (20 mmol), 4-chlorobenzaldehyde (10 mmol) and ethyl cyanoacetate (12 mmol). |
1 |
10 |
98 |
2 |
10 |
97 |
3 |
10 |
99 |
4 |
10 |
98 |
5 |
10 |
97 |
6 |
10 |
97 |
A plausible mechanism for the formation of Knoevenagel adduct in the presence of [HyEtPy]Cl–H2O–DABCO composite system is depicted in Scheme 2. First, the carbonyl group of the aldehyde was protonated by O–H of [HyEtPy]Cl (IL-OH), and the hydrogen atom of the active methylene interacted with the lone pair of electrons on the basic N centre (DABCO). The basic N abstracted a hydrogen from the active methylene and formed a carbanion, which attacked the carbonyl carbon and formed intermediate I. Then, the hydrogen atom of the active methylene interacted with the basic O centre in the IL-OH through a six-member ring (intermediate II), and intermediate III was formed. In intermediate III, the acidic N–H of the quaternary ammonium interacted with the lone pair electrons on the oxygen atom of the hydroxyl group, and subsequent elimination of water resulted in the formation of the olefin. In this process, [HyEtPy]Cl (IL-OH) not only activated the carbonyl group of aldehyde and stabilized the reaction intermediates, but also accelerated the Knoevenagel reaction by allowing proton-transfer to occur via a six-member ring in which IL-OH acted as a shuttle to transfer the proton from the C-position to the alkoxide of intermediate II.
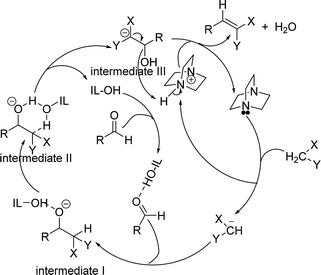 |
| Scheme 2 Possible mechanism of Knoevenagel condensation in the [HyEtPy]Cl–H2O–DABCO composite system. | |
Conclusions
A recyclable protic-ionic-liquid solvent–catalyst system, [HyEtPy]Cl–H2O–DABCO, was developed and used in the Knoevenagel condensation reaction of aromatic aldehydes with ethyl 2-cyanoacetate. The composite system ([HyEtPy]Cl–H2O–DABCO) was readily prepared by simply mixing solid [HyEtPy]Cl with water and DABCO at a given ratio. At 50 °C, the Knoevenagel condensation promoted by the composite system proceeded well, and the solvent–catalyst system [HyEtPy]Cl–H2O was recycled at least 6 times, showing no significant loss of activity. This protocol has notable advantages such as being eco-friendly, having low disposal costs, ease of work-up and convenient reuse of ionic liquid, which makes the present protocol practical for preparing multifunctional Knoevenagel condensation products.
Experimental section
1H-NMR (600, 500 or 400 MHz) and 13C-NMR (151, 126 or 101 MHz) spectra were recorded at ambient temperatures using DMSO-d6 or CDCl3 as solvent. 1H- and 13C-NMR chemical shifts were reported in ppm relative to internal Me4Si. IR spectra were determined on an FTIR-8400 infrared spectrometer by dispersing samples in KBr disks. Melting points were measured on a WRS-1B digital melting point meter and are uncorrected. All chemical reagents were obtained from commercial suppliers and used without further purification.
Preparation and characterization of the ionic salts
1-(2-Hydroxy-ethyl)-pyridinium chloride([HyEtPy]Cl). The ionic salt [HyEtPy]Cl was prepared according to a literature procedure38 with the following modifications: excess 2-chloroethanol (51 mL, 0.76 mol) and pyridine (53 mL, 0.63 mol) were transferred to a 250 mL round bottom flask, which was fitted with reflux condenser and nitrogen protecting facilities, and the reaction mixture was gently stirred at 70 °C for 24 h in the dark; the crude product [HyEtPy]Cl was formed. Then, the crude product was purified by recrystallization with 5 mL acetonitrile and 25 mL ethyl acetate solvent, and the residual solvent was removed in vacuum to give the product [HyEtPy]Cl (95 g, 94%) as white crystals. Mp 124 °C; 1H-NMR (600 MHz, DMSO-d6) δ 9.12 (d, J = 5.3 Hz, 2H, CH
N+), 8.63 (t, J = 7.8 Hz, 1H, CH
), 8.26–8.10 (m, 2H, CH
), 5.61 (d, J = 4.9 Hz, 1H, OH), 4.79–4.62 (m, 2H, N–CH2), 3.85 (dd, J = 10.1, 5.2 Hz, 2H, CH2O); 13C-NMR (151 MHz, DMSO-d6) δ 148.86, 148.61, 131.01, 66.28, 63.28.
1-Butylpyridinium chloride ([BuPy]Cl). The same procedure as that described above for [HyEtPy]Cl was followed except for the use of 1-chlorobutane (99 mL, 0.95 mol) instead of 2-chloroethanol. The product [BuPy]Cl (99 g, 92%) was obtained as white crystalline solid. Mp 87 °C (lit.,38 86 °C); 1H-NMR (500 MHz, DMSO-d6) δ 0.89 (s, 3H, CH3), 1.28 (s, 2H, CH2), 1.89 (s, 2H, CH2), 4.72 (t, J = 10.0 Hz, 2H, N–CH2), 8.20 (s, 2H, CH
), 8.66 (s, 1H, CH
), 9.35 (s, 2H, CH
N+); 13C-NMR (125 MHz, DMSO-d6) δ 145.66, 144.77, 128.04, 60.19, 32.60, 18.95, 13.45.
General procedure for Knoevenagel condensation reaction
20 mmol DABCO was added to a stirred mixture of 10 mmol aldehyde and 12 mmol ethyl cyanoacetate in 6.0 g [HyEtPy]Cl–H2O (3 mL H2O and 3 g [HyEtPy]Cl) at room temperature. The reaction progress was monitored by thin layer chromatography (TLC) until the aldehyde was consumed. Then, the reaction mixture was diluted with water (30 mL) and extracted with Et2O (2 × 20 mL); the organic phase was washed with brine (2 × 20 mL), dried over anhydrous Na2SO4, and the solvent removed on a rotary vacuum evaporator to yield the almost pure product. Further purification could be achieved by recrystallization from ethanol. The products were characterized by melting point determination, IR and NMR spectroscopy; the spectral data of all products (Table 2) are listed as follows.
Ethyl-2-cyano-3-phenylacrylate (entry 1). White crystalline solid; 1H-NMR (400 MHz, CDCl3) δ 8.25 (s, 1H, CH
), 7.99 (d, J = 7.2 Hz, 2H, ArH), 7.60–7.39 (m, 3H, ArH), 4.39 (q, J = 7.1 Hz, 2H, CH2), 1.40 (t, J = 7.1 Hz, 3H, CH3). FT-IR (KBr, cm−1): 3035 (C
CH), 2980 (–CH2CH3), 2223 (–CN), 1729 (C
O), 1608 (C
C), 1263 (C–O), 768 (ArH), 680 (ArH).
Ethyl-2-cyano-3-(4-methoxy-phenyl)acrylate (entry 2). Pale yellow crystalline solid; 1H-NMR (400 MHz, CDCl3) δ 8.17 (s, 1H, CH
), 8.01 (d, J = 8.8 Hz, 2H, ArH), 7.00 (d, J = 8.9 Hz, 2H, ArH), 4.37 (q, J = 7.1 Hz, 2H, CH2), 3.9 (s, 3H, OCH3), 1.40 (t, J = 7.1 Hz, 3H, CH3). FT-IR (KBr, cm−1): 3024 (C
CH), 2992 (–CH2CH3), 2216 (–CN), 1717 (C
O), 1585 (C
C), 1262 (C–O), 838 (ArH).
Ethyl-2-cyano-3-(4-hydroxy-3-methoxyphenyl)acrylate (entry3). Pale yellow crystalline solid; 1H-NMR (400 MHz, CDCl3) δ 8.14 (s, 1H, CH
), 7.85 (s, 1H, ArH), 7.40 (d, J = 6.3 Hz, 1H, ArH), 7.00 (d, J = 6.3 Hz, 1H, ArH), 4.38 (q, J = 7.2 Hz, 2H, CH2), 3.98 (s, 3H, OCH3), 1.34 (t, J = 7.2 Hz, 3H, CH3). FT-IR (KBr, cm−1): 3024 (C
CH), 2992 (–CH2CH3), 2216 (–CN), 1717 (C
O), 1585 (C
C), 1262 (C–O), 835 (ArH).
Ethyl-2-cyano-3-(2,4-dimethoxyphenyl)acrylate (entry 4). Yellow crystalline solid; 1H-NMR (400 MHz, CDCl3) δ 8.67 (s, 1H, CH
), 8.38 (d, J = 8.9 Hz, 1H, ArH), 6.58 (d, J = 11.2 Hz, 1H, ArH), 6.58 (d, J = 11.2 Hz, 1H, ArH), 4.35 (q, J = 7.1 Hz, 2H, CH2), 3.89 (s, 6H, OCH3), 1.38 (t, J = 7.1 Hz, 3H, CH3). FT-IR (KBr, cm−1): 3024 (ArH), 2983 (–CH2CH3), 2215 (–CN), 1713 (C
O), 1610 (C
C), 1249 (C–O), 836 (ArH).
Ethyl-2-cyano-3-(4-fluorophenyl)acrylate (entry 5). White solid; 1H-NMR (400 MHz, CDCl3) δ 8.22 (s, 1H, CH
), 8.04 (d, J = 8.6 Hz, 2H, ArH), 7.20 (t, J = 8.6 Hz, 2H, ArH), 4.39 (q, J = 7.1 Hz, 2H, CH2), 1.41 (t, J = 7.1 Hz, 3H, CH3). FT-IR (KBr, cm−1): 3025 (C
CH), 2990 (–CH2CH3), 2219 (–CN), 1717 (C
O), 1585 (C
C), 1270 (C–O), 896 (ArH).
Ethyl-3-(4-chlorophenyl)-2-cyanoacrylate (entry 6). White crystalline solid; 1H-NMR (400 MHz, CDCl3) δ 8.18 (s, 1H, CH
), 7.92 (d, J = 8.4 Hz, 2H, ArH), 7.46 (d, J = 8.4 Hz, 2H, ArH), 4.38 (q, J = 7.1 Hz, 2H, CH2), 1.39 (t, J = 7.1 Hz, 3H, CH3). 13C-NMR (101 MHz, CDCl3) δ 162.0, 153.3, 139.5, 132.2, 129.9, 129.6, 115.2, 103.5, 62.8, 14.1. FT-IR (KBr, cm−1): 3035 (ArH), 2989 (–CH2CH3), 2954 (–CH2CH3), 2223 (–CN), 1724 (C
O), 1652 (C
C), 1612 (C
C), 1200 (C–O), 831 (ArH).
Ethyl-3-(2,4-dichlorophenyl)-2-cyanoacrylate (entry 7). White solid; 1H-NMR (400 MHz, CDCl3) δ 8.63 (s, 1H, CH
), 8.22 (d, J = 8.6 Hz, 1H, ArH), 7.55 (s, 1H, ArH), 7.42 (d, J = 10.3 Hz, 1H, ArH), 4.43 (q, J = 7.1 Hz, 2H, CH2), 1.43 (t, J = 7.1 Hz, 3H, CH3). FT-IR (KBr, cm−1): 3038 (ArH), 2990 (–CH2CH3), 2223 (–CN), 1725 (C
O), 1652 (C
C), 1580 (C
C), 1257 (C–O), 865 (ArH).
Ethyl-2-cyano-3-(4-cyanophenyl)acrylate (entry 8). White crystalline solid; 1H-NMR (500 MHz, CDCl3) δ 8.25 (s, 1H, CH
), 8.07 (d, J = 8.4 Hz, 2H, ArH), 7.80 (d, J = 8.3 Hz, 2H, ArH), 4.42 (q, J = 6.8 Hz, 2H, CH2), 1.42 (t, J = 7.5 Hz, 3H, CH3). FT-IR (KBr, cm−1): 3032 (ArH), 2994 (–CH2CH3), 2943 (–CH2CH3), 2226 (–CN), 1714 (C
O), 1620 (C
C), 1260 (C–O), 840 (ArH).
Ethyl-3-(4-nitrophenyl)-2-cyanoacrylate (entry 9). Yellow crystalline solid; 1H-NMR (400 MHz, CDCl3) δ 8.37 (d, J = 8.8 Hz, 2H, ArH), 8.33 (s, 1H, CH
), 8.16 (d, J = 8.8 Hz, 2H, ArH), 4.45 (q, J = 7.1 Hz, 2H, CH2), 1.44 (t, J = 7.1 Hz, 3H, CH3). FT-IR (KBr, cm−1): 3040 (ArH), 2990 (–CH2CH3), 2240 (–CN), 1721 (C
O), 1617 (C
C), 1202 (C–O), 861 (ArH).
Ethyl-3-(3-nitrophenyl)-2-cyanoacrylate (entry 10). Pale yellow solid; 1H-NMR (400 MHz, CDCl3) δ 8.72 (s, 1H, ArH), 8.42 (d, J = 6.6 Hz, 2H, ArH), 8.33 (s, 1H, C
CH), 7.76 (d, J = 8.1 Hz, 1H, ArH), 4.43 (q, J = 7.1 Hz, 2H, CH2), 1.42 (t, J = 7.1 Hz, 3H, CH3). FT-IR (KBr, cm−1): 3035 (ArH), 2998 (–CH2CH3), 2226 (–CN), 1727 (C
O), 1627 (C
C), 1272 (C–O), 764 (ArH).
Ethyl-2-cyano-3-(4-hydroxyphenyl)acrylate (entry 11). Yellow solid; 1H-NMR (500 MHz, CDCl3) δ 8.22 (s, 1H, CH
), 7.98 (d, J = 8.2 Hz, 2H, ArH), 7.01 (d, J = 8.2 Hz, 2H, ArH), 4.41 (q, J = 6.8 Hz, 2H, CH2), 3.52 (s, 1H, OH), 1.43 (t, J = 6.8 Hz, 3H, CH3). FT-IR (KBr, cm−1): 3410 (–OH), 3032 (ArH), 2994 (–CH2CH3), 2226 (–CN), 1712 (C
O), 1618 (C
C), 1258 (C–O), 835 (ArH).
Diethyl-3,3′-(1,4-phenylene)bis(2-cyanoacrylate) (entry 12). White crystalline solid; 1H-NMR (400 MHz, CDCl3) δ 8.27 (s, 2H, CH
), 8.11 (s, 4H, ArH), 4.42 (q, J = 7.1 Hz, 4H, CH2), 1.42 (t, J = 7.1 Hz, 6H, CH3). FT-IR (KBr, cm−1): 3010 (ArH), 2995 (–CH2CH3), 2223 (–CN), 1714 (C
O), 1602 (C
C), 1270 (C–O), 844 (ArH).
Conflicts of interest
There are no conflicts to declare.
Acknowledgements
We are grateful for the financial support for this work from Natural Science Foundation of Shanxi Province (No. 201601D102015), the Higher School Science & Technology Development Project of Shanxi Province Education Department (No. [2017]171), the Key Research and Development Project of Xinzhou City ([2017]0302) and the College Students Innovation Project of Xinzhou Teachers University ([2016]32).
Notes and references
- L. F. Tietze, Chem. Rev., 1996, 96, 115 CrossRef PubMed.
- F. Freeman, Chem. Rev., 1980, 80, 329 CrossRef.
- G. A. Kraus and M. E. Krolski, J. Org. Chem., 1986, 51, 3347 CrossRef.
- L. F. Tietze and N. Rackelmann, Pure Appl. Chem., 2004, 76, 1967 Search PubMed.
- F. Liang, Y.-J. Pu, T. Kurata, J. Kido and H. Nishide, Polymer, 2005, 46, 3767 CrossRef.
-
(a) F.-G. Xi, H. Liu, N.-N. Yang and E.-Q. Gao, Inorg. Chem., 2016, 55, 4701 CrossRef PubMed;
(b) P. V. Dau and S. M. Cohen, Inorg. Chem., 2015, 54, 3134 CrossRef PubMed;
(c) M. Zhao, K. Deng, L. He, Y. Liu, G. Li, H. Zhao and Z. Tang, J. Am. Chem. Soc., 2014, 136, 1738 CrossRef PubMed.
- G. Li, J. Xiao and W. Zhang, Green Chem., 2012, 14, 2234 RSC.
- S. K. Panja, N. Dwivedi and S. Saha, RSC Adv., 2015, 5, 65526 RSC.
- H. Wang, C. Wang, Y. Yang, M. Zhao and Y. Wang, Catal. Sci. Technol., 2017, 7, 405 RSC.
- T. Murase, Y. Nishijima and M. Fujita, J. Am. Chem. Soc., 2012, 134, 162 CrossRef PubMed.
- E. M. Schneider, M. Zeltner, N. Kränzlin, R. N. Grass and W. J. Stark, Chem. Commun., 2015, 51, 10695 RSC.
- T. C. Keller, S. Isabettini, D. Verboekend, E. G. Rodrigues and J. Pérez-Ramírez, Chem. Sci., 2014, 5, 677 RSC.
- X. Garrabou, B. I. M. Wicky and D. Hilvert, J. Am. Chem. Soc., 2016, 138, 6972 CrossRef PubMed.
-
(a) S. Kumar Dey, N. de Sousa Amadeu and C. Janiak, Chem. Commun., 2016, 52, 7834 RSC;
(b) A. Karmakar, A. Paul, K. T. Mahmudov, M. F. C. G. da Silva and A. J. L. Pombeiro, New J. Chem., 2016, 40, 1535 RSC.
- P. Ramesh, B. Shalini and N. W. Fadnavis, RSC Adv., 2014, 4, 7368 RSC.
- A. Ying, F. Qiu, C. Wu, H. Hu and J. Yang, RSC Adv., 2014, 4, 33175 RSC.
- F. Zhang, H. Jiang, X. Li, X. Wu and H. Li, ACS Catal., 2014, 4, 394 CrossRef.
-
(a) N. Mase and T. Horibe, Org. Lett., 2013, 15(8), 1854 CrossRef PubMed;
(b) W. Li, S. N. Fedosov, T. Tan, X. Xu and Z. Guo, ACS Catal., 2014, 4, 3294 CrossRef.
-
(a) L. Bai, J.-X. Wang and Y. Zhang, Green Chem., 2003, 5, 615 RSC;
(b) S.-H. Zhao, Q.-J. Zhang, X.-E. Duan and L. H. Feng, Synth. Commun., 2011, 41, 3289 CrossRef;
(c) S. Zhao, X. Wang and L. Zhang, RSC Adv., 2013, 3, 11691 RSC;
(d) G. Chatel and D. R. MacFarlane, Chem. Soc. Rev., 2014, 43, 8132 RSC.
-
(a) S.-H. Zhao, H.-R. Zhang, L.-H. Feng and Z.-B. Chen, J. Mol. Catal. A: Chem., 2006, 258, 251 CrossRef;
(b) M. G. Freire, A. F. M. Cláudio, J. M. M. Araújo, J. A. P. Coutinho, I. M. Marrucho, J. N. C. Lopesac and L. P. N. Rebelo, Chem. Soc. Rev., 2012, 41, 4966 RSC.
-
(a) Y. Zhu, L. Zhang and S. Luo, J. Am. Chem. Soc., 2014, 136, 14642 CrossRef PubMed;
(b) N. Fu, L. Zhang and S. Luo, Org. Lett., 2015, 17(2), 382 CrossRef PubMed.
- D. Elhamifar, S. Kazempoor and B. Karim, Catal. Sci. Technol., 2016, 6, 4318 RSC.
-
(a) Z. N. Siddiqui and K. Khan, ACS Sustainable Chem. Eng., 2014, 2, 1187 CrossRef;
(b) S. Zhao, X. Wang and L. Zhang, RSC Adv., 2013, 3, 11691 RSC.
-
(a) D.-Z. Xu, Y. Liu, S. Shi and Y. Wang, Green Chem., 2010, 12, 514 RSC;
(b) C. Yang, W.-Q. Su and D.-Z. Xu, RSC Adv., 2016, 6, 99656 RSC.
- R. C. M. A. Sobrinho, P. M. de Oliveira, C. R. M. D'Oca, D. Russowsky and M. G. M. D'Oca, RSC Adv., 2017, 7, 3214 RSC.
-
(a) J. S. Wilkes and M. J. Zaworotko, Chem. Commun., 1992, 965 RSC;
(b) J. D. Holbrey, M. B. Turner, W. M. Reichert and R. D. Rogers, Green Chem., 2003, 5, 731 RSC.
-
(a) F. Bellina, A. Bertoli, B. Melai, F. Scalesse, F. Signoric and C. Chiappe, Green Chem., 2009, 11, 622 RSC;
(b) M. Deetlefs and K. R. Seddon, Green Chem., 2003, 5, 181 RSC.
-
(a) J. Li, X. Wang and Y. Zhang, Tetrahedron Lett., 2005, 46, 5233 CrossRef;
(b) J. S. Yadav, B. V. S. Reddy and G. Baishya, J. Org. Chem., 2003, 68, 7098 CrossRef PubMed;
(c) C.-J. Li and L. Chen, Chem. Soc. Rev., 2006, 35, 68 RSC.
-
(a) G. S. Owens and M. M. Abu-Omar, J. Mol. Catal. A: Chem., 2002, 187, 215 CrossRef;
(b) F. Bellina, C. Chiappe and M. Lessl, Green Chem., 2012, 14, 148 RSC.
- A. Song, X. Wang and K. S. Lam, Tetrahedron Lett., 2003, 44, 1755 CrossRef.
- G. Li, J. Xiao and W. Zhang, Green Chem., 2011, 13, 1828 RSC.
- F. D. Popp, J. Org. Chem., 1960, 25, 646 CrossRef.
- H. Yasuda and H. Midorikawa, Bull. Chem. Soc. Jpn., 1966, 39, 1754 CrossRef.
- C. Yue, A. Mao, Y. Wei and M. Lue, Catal. Commun., 2008, 9, 1571 CrossRef.
- A. Ying, L. Wang, L. Wang, X. Chen and W. Ye, J. Chem. Res., 2010, 34, 30 CrossRef.
- D. T. Mowry, J. Am. Chem. Soc., 1943, 65, 992 CrossRef.
- J. Zhang, T. Jiang, B. Han, A. Zhu and X. Ma, Synth. Commun., 2006, 36, 3305 CrossRef.
- S. Zhao, M. He, Z. Guo, N. Zhou and L. Zhang, RSC Adv., 2015, 5, 32839 RSC.
Footnote |
† Electronic supplementary information (ESI) available: NMR spectra of ionic salts and Knoevenagel products. See DOI: 10.1039/c8ra06506c |
|
This journal is © The Royal Society of Chemistry 2018 |
Click here to see how this site uses Cookies. View our privacy policy here.