DOI:
10.1039/C8RA06847J
(Paper)
RSC Adv., 2018,
8, 39074-39082
Thermally-healable network solids of sulfur-crosslinked poly(4-allyloxystyrene)†
Received
16th August 2018
, Accepted 12th November 2018
First published on 20th November 2018
Abstract
Network polymers of sulfur and poly(4-allyloxystyrene), PAOSx (x = percent by mass sulfur, where x is varied from 10–99), were prepared by reaction between poly(4-allyloxystyrene) with thermal homolytic ring-opened S8 in a thiol-ene-type reaction. The extent to which sulfur content and crosslinking influence thermal/mechanical properties was assessed. Network materials having sulfur content below 50% were found to be thermosets, whereas those having >90% sulfur content are thermally healable and remeltable. DSC analysis revealed that low sulfur-content materials exhibited neither a Tg nor a Tm from −50 to 140 °C, whereas higher sulfur content materials featured Tg or Tm values that scale with the amount of sulfur. DSC data also revealed that sulfur-rich domains of PAOS90 are comprised of sulfur-crosslinked organic polymers and amorphous sulfur, whereas, sulfur-rich domains in PAOS99 are comprised largely of α-sulfur (orthorhombic sulfur). These conclusions are further corroborated by CS2-extraction and analysis of extractable/non-extractable fractions. Calculations based on TGA, FT-IR, H2S trapping experiments, CS2-extractable mass, and elemental combustion microanalysis data were used to assess the relative percentages of free and crosslinked sulfur and average number of S atoms per crosslink. Dynamic mechanical analyses indicate high storage moduli for PAOS90 and PAOS99 (on the order of 3 and 6 GPa at −37 °C, respectively), with a mechanical Tg between −17 °C and 5 °C. A PAOS99 sample retains its full initial mechanical strength after at least 12 pulverization-thermal healing cycles, making it a candidate for facile repair and recyclability.
Introduction
Vulcanization is a process developed by Charles Goodyear1 in which the mechanical properties of natural rubber (polyisoprene) are dramatically enhanced by heating it in the presence of up to 5 wt% elemental sulfur (as S8 at STP). The increase in material strength of a rubber following vulcanization results from covalent crosslinking between polymer chains.2 Such crosslinking is derived from homolytic thermal ring opening of S8 to afford sulfur-centered radicals3 that subsequently add to C
C bonds, leading to polysulfide crosslinks between polymer chains (Scheme 1a). Without the dramatic increase in mechanical strength endowed upon rubber products by polysulfide crosslinks formed during vulcanization, the modern automobile tire would not be accessible, and early automobiles would have been severely limited in the types and duration of tasks they could perform.
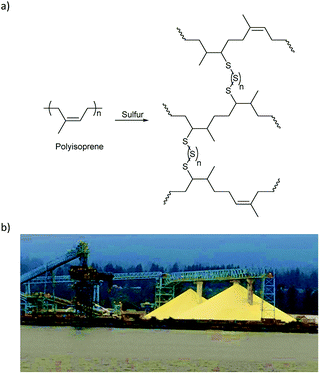 |
| Scheme 1 (a) Sulfur vulcanization of polyisoprene. (b) By-product sulfur at North Vancouver Sulphur Works, originating from tar sand-processing facilities in Alberta, Canada. | |
Despite the dramatic structural improvement mediated by sulfur as a minor component by mass of vulcanized rubber, elemental sulfur is currently underutilized as a bulk component of materials. The underutilization of sulfur is especially surprising considering the titanic quantities of S8 (Scheme 1b) that are produced by petrochemical industries. Petrochemical by-product sulfur is produced by the Claus process,4,5 wherein H2S is oxidized to S8. Sulfur removal from fuels is necessary to prevent catalyst poisoning in subsequent steps of the petroleum-refining process and to attenuate the environmental impact of acid rain that results from combustion of sulfur-rich fossil fuels.6 Currently, the primary use of the S8 generated from fossil fuels is in the production of sulfuric acid, with lesser quantities being used in fertilizers/pesticides, vulcanization of rubber, and as an additive to asphalt.7–9 Even after consumption of S8 by these processes, however, 7 million tons of S8 accumulate each year as unused waste.10 Vast quantities of S8 have been stockpiled at industrial centers and storage sites, so S8 is an inexpensive, abundant, and readily accessible feedstock for valorization.6,11–13 Furthermore, the formation of S–S bonds is thermally reversible, a property that could be exploited to generate recyclable thermoplastics and thermally self-healing materials.14
Although elemental sulfur itself has very poor mechanical properties, significant advances have been achieved with the advent of inverse vulcanization.15 Inverse vulcanization is a term coined by Pyun for a process in which S8 is the bulk material and organic small molecules form the covalent crosslinks between polysulfide chains.6,15–27 Pyun's breakthrough studies on such high sulfur-content materials have inspired a flurry of related studies to better employ byproduct sulfur.12 Materials prepared by inverse vulcanization can retain some of the advantageous properties of S8. For example, S8 exhibits high electrical resistivity (2 × 1023 μΩ cm) and low thermal conductivity (0.205 W m−1 K−1). In addition, S8 actively resists several material degradation pathways, as it is resistant to corrosion by strong acids. It also repels insects and rodents,28 as well as having antibacterial and anti-microbial properties,29–34 and has long been used as a treatment for timbers to prevent decay.35,36 Moreover, if an organic small molecule used in inverse vulcanization has more than one C
C bond, then that molecule can crosslink multiple polysulfide chains to afford a networked covalent composite (NCC) or polymer material.
Many of the inverse vulcanized materials prepared by Pyun exhibit significantly greater durability compared to sulfur itself, even for materials containing >90% sulfur by weight. Because even small amounts of an alkene-functionalized organic small molecule can afford materials with dramatically enhanced mechanical properties relative to pure S8, we envisioned that using an alkene-functionalized organic polymer would afford an NCC with enhanced networking. We hypothesized that using this strategy to increase networking in NCCs would increase the mechanical strength of the NCCs. Herein we report the synthesis of allyloxy-functionalized polystyrene, its crosslinking with S8 via inverse vulcanization, and the thermomechanical properties of the resulting NCCs, PAOSx (x = percent by mass sulfur in the material), wherein x is varied from 10 to 99.
Experimental section
General considerations
All NMR spectra were recorded on a Bruker Avance spectrometer operating at 300 MHz for protons. Thermogravimetric analysis (TGA) was recorded on a TA SDT Q600 instrument over the range 20 to 800 °C, with a heating rate of 5 °C min−1 under a flow of N2 (100 mL min−1). Differential Scanning Calorimetry (DSC) was acquired using a Mettler Toledo DSC 3 STARe System over the range of −50 to 140 °C, with a heating rate of 10 °C min−1 under a flow of N2 (200 mL min−1). Each DSC measurement was carried out over five heat-cool cycles to confirm consistent results following the first heat-cool cycle. The data reported were taken from the second cycle of the experiment. Dynamic Mechanical Analysis (DMA) was performed using a Mettler Toledo DMA 1 STARe System in dual cantilever mode. DMA samples were cast from silicone resin molds (Smooth-On Oomoo® 30 tin-cure). The sample dimensions were 1.5 × 8 × 50 mm. Clamping force was 1 cN m and the temperature was varied from −60 to 88 °C with a heating rate of 2 °C min−1. The measurement mode was set to displacement control with a displacement amplitude of 5 μm and a frequency of 1 Hz. Fourier transform infrared spectra were obtained using a Shimadzu IRAffinity-1S instrument operating over the range of 400–4000 cm−1 at ambient temperature using an ATR attachment. Poly(4-vinylphenol) (Mw = 11
000 g mol−1, Sigma Aldrich), allyl bromide (Oakwood Chemical), elemental sulfur (99.5+%, Duda Energy, LLC) were used without further purification.
Preparation of poly(4-allyloxystyrene) (PAO)
The procedure that follows is based on a reported method.37 To a 500 mL round bottom flask equipped with a Teflon-coated magnetic stir bar was added 22.489 g (185.87 mmol) of allyl bromide, 20.000 g (166.44 mmol) of poly(4-vinylphenol) (PVP) and 200 mL of acetonitrile. The contents of the flask were stirred for 5 min to facilitate complete dissolution of PVP. The flask was then equipped with a water-cooled reflux condenser and placed under an atmosphere of N2. The flask was heated in an oil bath at 80 °C while stirring. While the heated reaction mixture was stirring, 49.999 g (361.77 mmol) of K2CO3 was added portionwise to the reaction mixture. The reaction was then refluxed with stirring for 72 h, after which time the mixture was allowed to cool to room temperature. The flask was opened to the air and deionized water (250 mL) was added to the reaction flask to dissolve the remaining K2CO3.
The reaction mixture was then extracted with dichloromethane (450 mL). The organic layer was collected and washed with 1 M HCl(aq.) (1 × 250 mL), and then with deionized water (1 × 250 mL). The organic layer was collected, and the solvent was evaporated under reduced pressure. The product was collected as a beige solid. 1H NMR (300 MHz, DMSO-d6, δ: 1.41 (br, 2H), 1.72 (br, 1H), 4.45 (br, 2H), 5.21 (br, 1H), 5.35 (br, 1H), 5.99 (br, 1H), 6.48–6.69 (br, 4H). Elemental analysis calculated for C11H12O: C, 82.45; H, 7.56%. Found C, 81.88; H, 7.77%. These data are consistent with those previously reported.37 DSC data for this compound are provided in the ESI.†
General synthesis of PAOSx
Elemental sulfur was weighed directly into an aluminum reaction vessel. The vessel was heated to 180 °C, over which time the sulfur melted. Once the sulfur turned a viscous dark red-orange color (indicative of thermal ring-opening), the appropriate amount of PAO was slowly added to the molten sulfur. The reaction media was manually stirred with a spatula for 60 min. After 60 min the reaction was stopped, the mixture was allowed to cool, and the solid was removed from the reaction vessel. Reagent masses and results of elemental combustion microanalysis are provided below.
Synthesis of PAOS99
CAUTION: Heating elemental sulfur with organics can result in the formation of H2S gas. H2S is toxic, foul-smelling, and corrosive. The general synthesis above was used to synthesize PAOS99 (99 wt% sulfur) where 9.90 g of elemental sulfur and 0.0994 g of PAO were used in the reaction. Elemental analysis calculated: C, 0.82; S, 99.00; H, 0.07%. Found: C, 1.02; S, 98.21; H, 0.0%.
Synthesis of PAOS90
The general synthesis above was used to synthesize PAOS90 (90 wt% sulfur) where 9.00 g of elemental sulfur and 0.998 g of PAO were used in the reaction. Elemental analysis calculated: C, 8.29; S, 90.00; H, 0.69%. Found: C, 8.07; S, 89.37; H, 0.64%.
Synthesis of PAOS80
The general synthesis above was used to synthesize PAOS80 (80 wt% sulfur) where 2.40 g of elemental sulfur and 0.600 g of PAO were used in the reaction. Elemental analysis calculated: C, 16.59; S, 80.00; H, 1.40%. Found: C, 16.32; S, 79.70; H, 1.48%.
Synthesis of PAOS70
The general synthesis above was used to synthesize PAOS70 (70 wt% sulfur) where 2.10 g of elemental sulfur and 0.900 g of PAO were used in the reaction. Elemental analysis calculated: C, 24.89; S, 70.00; H, 2.08%. Found: C, 25.75; S, 63.18; H, 2.24%.
Synthesis of PAOS60
The general synthesis above was used to synthesize PAOS60 (60 wt% sulfur) where 1.80 g of elemental sulfur and 1.20 g of PAO were used in the reaction. Elemental analysis calculated: C, 33.19; S, 60.00; H, 2.79%. Found: C, 34.54; S, 61.91; H, 3.08%.
Synthesis of PAOS50
The general synthesis above was used to synthesize PAOS50 (50 wt% sulfur) where 1.50 g of elemental sulfur and 1.50 g of PAO were used in the reaction. Elemental analysis calculated: C, 41.49; S, 50.00; H, 3.49%. Found: C, 41.50; S, 49.90; H, 3.75%.
Synthesis of PAOS40
The general synthesis above was used to synthesize PAOS40 (40 wt% sulfur) where 1.20 g of elemental sulfur and 1.80 g of PAO were used in the reaction. Elemental analysis calculated: C, 49.78; S, 40.00; H, 4.18%. Found: C, 51.42; S, 37.65; H, 4.81%.
Synthesis of PAOS30
The general synthesis above was used to synthesize PAOS30 (30 wt% sulfur) where 0.900 g of elemental sulfur and 2.10 g of PAO were used in the reaction. Elemental analysis calculated: C, 58.08; S, 30.00; H, 4.89%. Found: C, 60.25; S, 27.08; H, 5.70%.
Synthesis of PAOS20
The general synthesis above was used to synthesize PAOS20 (20 wt% sulfur) where 0.600 g of elemental sulfur and 2.40 g of PAO were used in the reaction. Elemental analysis calculated: C, 66.38; S, 20.00; H, 5.58%. Found: C, 66.55; S, 18.22; H, 6.11%.
Synthesis of PAOS10
The general synthesis above was used to synthesize PAOS10 (10 wt% sulfur) where 0.300 g of elemental sulfur and 2.70 g of PAO were used in the reaction. Elemental analysis calculated: C, 74.67; S, 10.00; H, 6.28%. Found: C, 73.62; S, 9.40; H, 7.10%.
Results and discussion
Synthesis
Polystyrene (PS) was selected as the scaffold for the alkene-bearing polymer substrate to access NCCs because a wide variety of functionalized PS derivatives are commercially available with relatively high molecular weights and well-defined polydispersities. The cross-linking mechanism in inverse vulcanization is analogous to the well-known thiol–ene click reaction (Scheme 2a).38 Whereas the thiol–ene reaction requires a thiol group and an organic radical initiator to generate a sulfur-centered radical, in inverse vulcanization elemental sulfur (S8) undergoes thermal homolytic ring-opening above 159 °C to generate a S-centered radical that can react with an olefin (Scheme 2b).
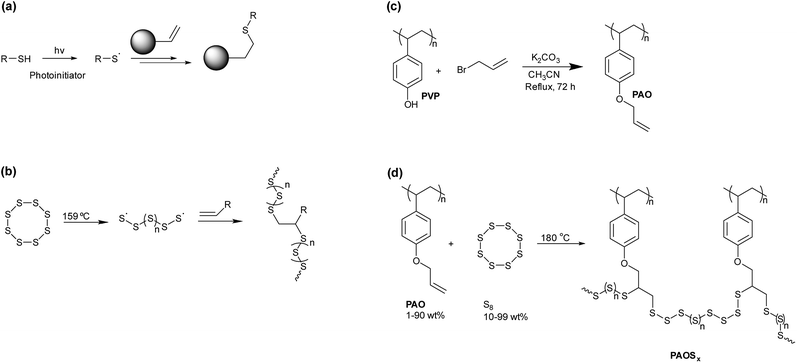 |
| Scheme 2 (a) The general synthetic scheme of a thiol–ene reaction. (b) The homolytic ring-opening of S8 to form a sulfur-centered radical, which then can react with olefins. (c) Synthetic route to prepare PAO. (d) Synthetic route to PAOSx, where x represents the wt% of S8. | |
We reasoned that a PS derivative functionalized with hydroxyl groups could be readily modified with allyl bromide, thus poly(4-vinylphenol) (PVP) was employed as the initial starting material. Exhaustive alkylation was achieved upon reaction of PVP with allyl bromide in the presence of K2CO3, affording the desired PS derivative with alkene side chains, poly(4-allyloxystyrene) (PAO), in quantitative yield (Scheme 2c).37
Analysis of PAO by 1H NMR and FT-IR spectroscopy (Fig. 1a) revealed that the signals for the OH proton and the O–H stretching vibration (3300 cm−1) had disappeared. Two new peaks appeared in the FT-IR spectrum at 922 and 995 cm−1 that were consistent with monosubstituted alkene (i.e., R–CH
CH2) C–H bending modes (Fig. 1b). The ratio of integrals for the allyloxy proton signals to the integral of all PS-backbone proton signals revealed that allylation of hydroxyl groups in PVP was quantitative.39,40
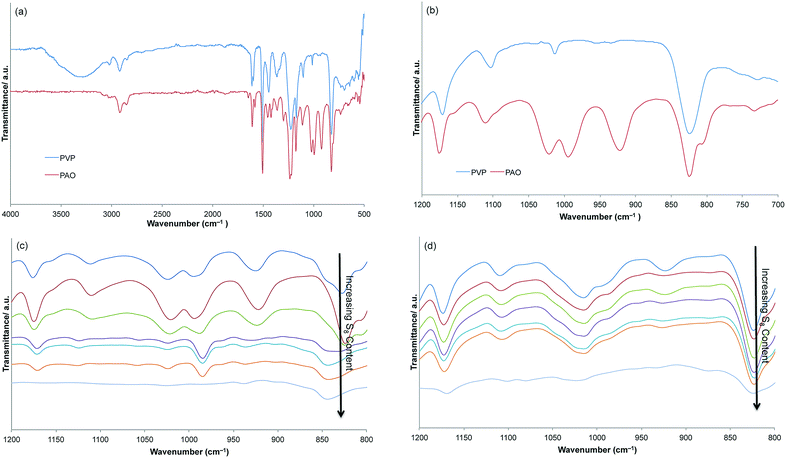 |
| Fig. 1 FT-IR spectra for poly(4-vinylphenol) and PAO over the full scan range (a), poly(4-vinylphenol) and PAO highlighting the range for the monosubstituted alkene C–H bending mode (b), CS2-soluble fractions from PAOSx (x = 40–99, (c)), and CS2-insoluble fractions from PAOSx (x = 40–99, (d)). | |
Thermal reaction of PAO with sulfur (Scheme 2d) was achieved by heating the polymer to 180 °C in the presence of varying amounts of sulfur to afford the desired NCCs comprising PAO crosslinked with varying relative wt% of sulfur (PAOSx; x = 10, 20, 30, 40, 50, 60, 70, 80, 90, and 99 wt% S). Each PAOSx was a brown-red solid with a glass-like appearance. The general physical appearance was consistent across the series, but the materials became more brittle with decreasing wt% sulfur. Mass losses in the range of 2–7% were observed during the reactions of PAO with S8 (Table 1), which were attributed to the release of H2S gas, as confirmed by elemental microanalysis. CAUTION: H2S gas is foul-smelling, toxic, and corrosive and should be trapped as it is produced. Literature examples of H2S-trapping strategies include zinc oxide-titanium dioxide sorbents,41 zinc oxide nanoparticles,42 reaction with Ag+ salts for precipitation as Ag2S,43 and other systems.44 Analysis of PAOSx by FT-IR spectroscopy revealed that not all C
C bonds in PAO had reacted with S8, as peaks were still observed at 922 and 995 cm−1 in all samples (spectra are provided in the ESI†). Unfortunately, 1H NMR spectrometric analysis could not be performed due to the poor solubility of PAOSx in all solvents examined. Combustion analysis was performed for the elements C, H, N, and S for all PAOSx, which demonstrated that S was efficiently incorporated into PAOSx.
Table 1 Summary of mass loss in synthesis, TGA, and DSC data
Material |
Tda (°C) |
Tg (°C) |
Tm (°C) |
Tα–β (°C) |
% Mass lossb(±2%) |
Td was determined by calculating the temperature at which 5% mass was lost. Mass loss was determined by weighing the mass of the product after the reaction. No visible transition in the range studied. Was not recorded. |
PVP |
310 |
—c |
—c |
—c |
NA |
PAO |
395 |
43.3 |
—c |
—c |
NA |
S8 |
210 |
—c |
118.7 |
—c |
NA |
PAOS99 |
203 |
—c |
117.0 |
—c |
—d |
PAOS90 |
191 |
−37.0 |
115.8 |
—c |
3 |
PAOS80 |
199 |
—c |
116.5 |
105.3 |
4 |
PAOS70 |
192 |
—c |
114.3 |
—c |
4 |
PAOS60 |
195 |
—c |
114.6 |
—c |
3 |
PAOS50 |
238 |
—c |
115.2 |
103.4 |
2 |
PAOS40 |
241 |
—c |
116.6 |
105.8 |
2 |
PAOS30 |
244 |
—c |
—c |
—c |
2 |
PAOS20 |
263 |
—c |
—c |
—c |
2 |
PAOS10 |
290 |
—c |
—c |
—c |
7 |
Given that unreacted C
C linkages remained in each PAOSx NCC, we hypothesized that there might also be uncrosslinked S8. Each NCC was therefore stirred with an excess of carbon disulfide (CS2) to extract and enable quantification of free (non-cross-linked) sulfur. As anticipated, NCCs with higher sulfur contents (x > 50 wt%) comprised substantial amounts of CS2-extractable mass. In contrast, PAOSx materials containing less than 50 wt% sulfur afforded little to no CS2-extractable mass, indicating that essentially all the sulfur is covalently incorporated in these cases. The CS2-soluble and insoluble fractions resulting from extraction of PAOSx, (x = 99, 90, 80, 70, 60, 50, and 40) were isolated and then analyzed by FT-IR spectroscopy (Fig. 1d). FT-IR analysis suggested that nearly no organics are present in CS2-soluble fractions for PAOSx (x > 50). Elemental analysis on the CS2-extractable fraction of PAOS90 confirmed their identity as being >99% by mass sulfur. The CS2-insoluble fraction from PAOS90 contained 47% by mass of non-extractable sulfur and the FT-IR spectrum confirms nearly complete consumption of the alkene moiety in the polymer backbone. On the basis of the extent of alkene consumption and the amount of non-extractable (crosslinked) sulfur present, the average crosslink is comprised of five sulfur atoms.
Thermal stability
Thermogravimetric analysis (TGA) of PAOSx revealed decomposition temperatures (Td, here defined as the temperature at which 5% mass loss was observed upon heating under an atmosphere of N2) ranging from 191–290 °C (Fig. 2a). For comparison, the Td values for S8 and PAO are 210 and 395 °C, respectively. For lower sulfur content PAOSx (x = 10–50%), Td values generally decreased as the wt% of S8 increased. However, samples with x > 50% exhibited Td values lower than that of S8 and did not appear to vary significantly in response to changes in S8 content. This depression of Td is attributable to decomposition of an amount of non-crosslinked sulfur corresponding to the amount of CS2-extractable sulfur (vide supra). Higher sulfur content PAOSx (x > 70) exhibit very low char yields due to the clean decomposition of sulfur-rich domains, whereas materials containing <70 wt% sulfur – and comprised by correspondingly little non-cross-linked sulfur – have char yields ranging from 20–28% (Fig. 2a).
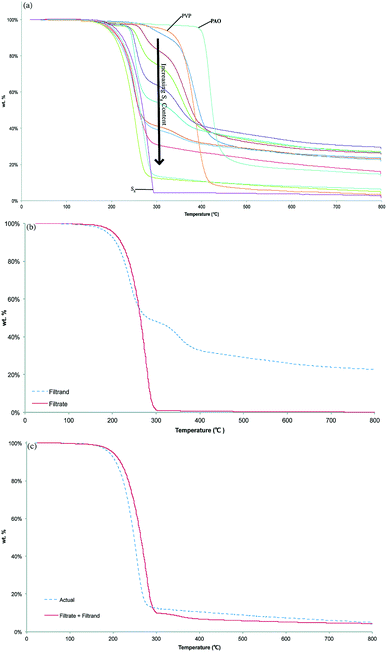 |
| Fig. 2 (a) TGA curves of PVP, PAO, elemental sulfur, and PAOSx. (b) The TGA curves for the CS2-extractable (solid line) and CS2-insoluble fraction (dashed line) of PAOS90. (c) The calculated (solid line) TGA curve for independent thermal decomposition of the two fractions overlaid with the experimentally observed TGA curve (dashed line) from the PAOS90 bulk material. | |
The first degradation step observed for all PAOSx materials was attributed to the loss of the extractable sulfur portion as H2S gas, which can form via hydrodesulfurization reaction between S and the organic components. To confirm this hypothesis, a bulk sample of PAOS50 was subjected to heating at 250 °C, just above the observed Td for this material. The vessel was equipped with a bubbler containing 1 M AgNO3(aq.) to trap evolved H2S gas via reaction with AgNO3 to form insoluble Ag2S. The mass of Ag2S isolated from this experiment accounts for >83% of the mass loss observed in the TGA trace for PAOS50. The shortfall of isolated Ag2S is likely a result of gas escape prior to reaction or incomplete collection of the finely-dispersed solid. PAOSx samples with x < 70 exhibit a second degradation step at roughly 290 °C attributable to degradation of the organic polymer backbone. The assertion that the covalently-linked and extractable sulfur domains undergo thermal decomposition independently even when commingled in PAOS90 is further supported by the observation that the curve resulting from summing mass-normalized TGA traces of CS2-soluble and -insoluble fractions is nearly coincident with that of the TGA trace of the original sample of PAOS90 (Fig. 2C).
Morphology
Differential scanning calorimetry (DSC) data for fully cured samples of PAOSx are summarized in Table 1. PAO is shown to have a Tg at 43.3 °C, while pure orthorhombic α-sulfur does not exhibit a glass transition in the range studied. Additionally, sulfur has a melt peak at 118.7 °C. The higher sulfur content PAOSx (x = 60–99) exhibit endothermic features at ∼106 °C. The feature at ∼106 °C in DSC analysis is attributable to an orthorhombic to monoclinic phase change (Tα–β, for the α-S(s) → β-S(s) process).45–47 Older literature has variably attributed this transition to occurring at 95 °C,48–51 possibly confused by the significant variability in properties of sulfur based on its thermal history and complex phase behavior36,49,52–55 The peak at ∼115 °C is attributed to the melt peak of sulfur-rich domains in the materials. The normalized integral of the sulfur melt peak decreases predictably as the wt% of sulfur is decreased (Fig. S13–S24 in the ESI†), consistent with progressively lower amounts of non-cross-linked S in these materials. More interestingly, there is no apparent Tg in the measured temperature range for any of the PAOSx materials except for PAOS90. PAOS90 exhibits a weakly-observable Tg at −37.0 °C, a transition which has been suggested in amorphous sulfur as well.56–58 The lack of a comparable Tg in even more sulfur-rich PAOS99 suggests that a lower ratio of cross-linking of PAO may facilitate continuity of a more purely orthorhombic sulfur state. An alternate explanation is that PAO may act as a plasticizer for amorphous sulfur and stabilize the polymeric and orthorhombic domains in the NCC, consistent with the observed decrease in Tg for PAOS90 relative to amorphous sulfur (−30 °C). DSC data show that the lower wt% sulfur materials (PAOS10–30) have neither a Tg nor a Tm in the temperature range studied. The predominating absence of these thermal transitions or those attributable to either orthorhombic sulfur or polymeric sulfur further supports the formulation of PAOSx as extensively cross-linked materials with oligosulfide chains separating organic polymer chains.
Mechanical properties
One of the primary objectives of the current study was to investigate the extent to which low loading of polymers can endow bulk sulfur with enhanced mechanical strength. On this basis, PAOS90 and PAOS99 were selected for study by dynamic mechanical analysis (DMA).
The responses of PAOS90 and PAOS99 to flexural stress were studied by DMA in dual cantilever mode with a 1 Hz frequency of oscillation from −60 to 88 °C. The thermal history of sulfur has a dramatic impact on its subsequent thermomechanical properties. To assess whether this would hold true of high sulfur-content NCCs, DMA was undertaken 1.5 h (Fig. 3a–c) and 96 h (Fig. 3d–f) of curing at room temperature after initial melt-casting of samples. The TGA and DSC data discussed in the previous sections is for samples that were cured for at least 96 h. One telling metric in assessing the curing process is the Tg. The Tg can be elucidated in many different ways from DMA data.59 In the present case, the Tg was determined from the onset of storage modulus (Tg,SM) or as a local maximum in either loss modulus (Tg,LM) or tan
δ curves (Tg,tan). For samples analysed 1.5 h after preparation, the onset of storage moduli (Fig. 3a) for PAOS90 and PAOS99 occur at the same temperature (−17 °C), however the magnitude of the storage modulus for PAOS90 is only 50% that of PAOS99. The Tg calculated from loss moduli are −4.7 and −6.3 °C for PAOS90 and PAOS99, respectively. The calculated Tg from the tan
δ peaks are 2.3 °C for PAOS90 and 5.0 °C for PAOS99 (Fig. 3c). The magnitude of the tan
δ peak provides evidence for effective damping by the material. The damping factor indicates how well a material can dissipate energy through segmental motions or relaxations. Fig. 3c shows that over the entire temperature range studied, PAOS99 has a higher tan
δ value than PAOS90. This suggests that PAOS99 exhibits far more viscous than elastic properties relative to PAOS90. PAOS99 is thus able to dissipate energy more efficiently than its PAOS90 counterpart. Notably, the tan
δ curve for PAOS99 increases from 60 to 88 °C, a result of the large amounts of free sulfur in the material. These insights further support the inference from DSC data that there is a greater predominance of orthorhombic sulfur in PAOS99 than in PAOS90.
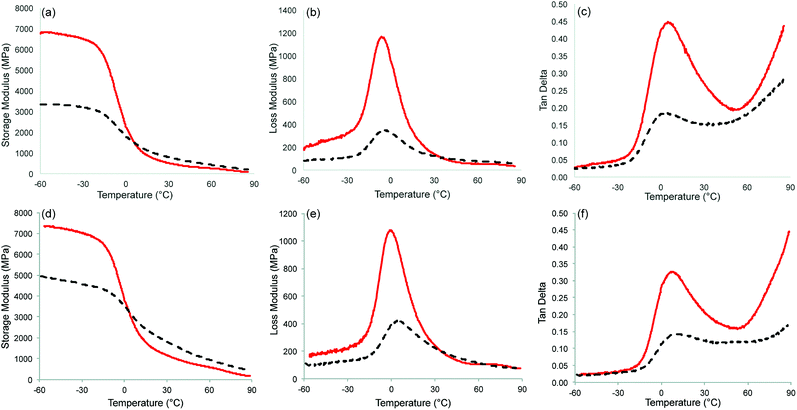 |
| Fig. 3 Temperature dependence of storage and loss modulus and tan δ of PAOS90 (dashed line) and PAOS99 (solid line) in dual cantilever mode after 1.5 h of cooling (graphs a–c) and 96 h of cooling (graphs d–f). | |
The 96 h-cured samples of PAOS90 and PAOS99 were subjected to testing by DMA under identical experimental conditions as were the 1.5 h-cured samples. For comparison, a 96 h-cured sample of pure sulfur is too brittle to be clamped in the DMA instrument even at minimum clamping force. The storage and loss moduli and tan
δ curves are shown in Fig. 3d–f. All parameters exhibit modest shifts between 1.5 h and 96 h post-casting. In every case the calculated Tg increased over the 96 h time period. Table 2 summarizes the calculated Tg values for PAOS90 and PAOS99 after 1.5 and 96 h post-casting. In both PAOSx materials, the storage modulus is seen to increase over the 96 h period, whereas, the tan
δ values for both PAOSx materials are shown to decrease over the entire temperature range. The increase in storage modulus is attributed to the slow reversion of free polymeric sulfur back to the thermodynamically-favored, more crystalline orthorhombic S8.60 Moreover, the decrease in magnitude of tan
δ is an indication that the materials' elastic behaviour concomitantly increases.
Table 2 Tg values for PAOS90 and PAOS99 determined from DMA data
Material |
Tg,SM (°C) |
Tg,LM (°C) |
Tg,tan (°C) |
1.5 h |
96 h |
1.5 h |
96 h |
1.5 h |
96 h |
PAOS90 |
−17 |
−10 |
−4.7 |
5.7 |
2.3 |
9.7 |
PAOS99 |
−17 |
−13 |
−6.3 |
−0.5 |
5.0 |
7.3 |
Thermal healing and materials comparison
One driving force for the current work was that the thermal reversibility of S–S bond formation offers intriguing possibilities for thermal healing and recycling of high sulfur-content materials. To test the thermal healing/recyclability of PAOS99, a sample of the material was subject to DMA analysis and then pulverized into small pieces prior to reannealing to heal the material, and finally allowing the sample to cool to room temperature over 15 min. After repeating this pulverization-thermal healing process ten times, the mechanical properties of the twelve-times-healed sample were identical to that of the first sample within error of the measurement (Fig. 4).
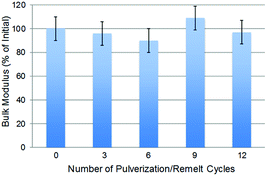 |
| Fig. 4 The bulk modulus (measured at −45 °C) for PAOS99 after pulverization/remelting cycles remains consistent within error for at least twelve cycles. | |
Another driving force behind this study was to determine whether crosslinking by small amounts of organic material could improve the mechanical integrity of bulk sulfur to levels that make it viable for practical applications: without additives to stabilize it, polymeric sulfur is unstable, reverting to the S8 form at STP. Comparison of the mechanical features of polymer-cross-linked high-sulfur content PAOS90–99 to other small molecule-cross-linked, high-sulfur content materials is also of interest. Pyun's group has prepared 1,3,5-triisopropenylbenzene/sulfur crosslinked materials.61 The storage modulus of this small molecularly-cross-linked material comprising 30 wt% 1,3,5-triisopropenylbenzene and 70 wt% sulfur was 1 GPa at 30 °C under a shear stress. Polymer-cross-linked PAOS90 and PAOS99 exhibit a notably higher storage modulus of approximately 2.6 GPa at 30 °C under a flexural stress despite the significantly higher sulfur content in these NCCs.
Compared to other reversibly-crosslinked/thermally healable polymers, PAOS99 has a higher flexural storage modulus than for epoxy shape-memory polymers62 and comparable to that of crosslinked and thermally healable (via Diels–Alder reaction) poly(dicyclopentadiene)s.63 The improved mechanical strength of polymer-crosslinked PAOSx over other sulfur-rich materials and the similarity in room-temperature storage modulus to polystyrene (1.8 GPa at 30 °C)64 provide sound proof-of-principle to justify further efforts to prepare value-added materials from affordable/plentiful by-product sulfur by the strategy employed in this study.
Conclusions
A commercially-available polystyrene derivative was modified to facilitate cross-linking with elemental sulfur. The crosslinked materials, PAOSx were prepared with sulfur content of 10–99% by mass. The thermal and mechanical properties of PAOSx were elucidated. Target high sulfur-content PAOS99 and PAOS90 were comprised of a mixture of sulfur trapped in the amorphous state and short-chain sulfur crosslinks between organic polymer chains. The storage moduli of both PAOS90 and PAOS99 increased over a 96 h setting time as free polymeric sulfur slowly relaxed to the orthorhombic state. The fully-set mechanical strength of even PAOS99, which is 99% by mass sulfur, increased significantly when compared to a pure sulfur sample prepared under the same conditions. PAOS99 maintains its mechanical integrity after physical breakdown and thermally recasting for at least a dozen cycles, demonstrating the facile recyclability of these materials. PAOS90 and PAOS99 materials thus show promise for valorizing elemental sulfur as a component of durable, recyclable material applications for which petrochemicals are currently used. Follow-up studies on improving the mechanical properties of high sulfur-content network solids are currently underway.
Conflicts of interest
There are no conflicts to declare.
Acknowledgements
This work was supported by the National Science Foundation (CHE-1708844). Gratitude is kindly extended for assistance from Tucker McFarlane of Stephen F. Foulger's Group (Clemson University, TGA and DSC). We thank Catherine A. Conrad for help with early work to begin this project.
Notes and references
- G. Charles, US Pat. 3633A, 1844.
- E. H. Farmer and F. W. Shipley, J. Chem. Soc., 1947, 1519–1532, 10.1039/jr9470001519.
- R. S. Glass, Top. Curr. Chem., 2018, 376, 1–42 CrossRef CAS PubMed.
- X. Zhang, Y. Tang, S. Qu, J. Da and Z. Hao, ACS Catal., 2015, 5, 1053–1067 CrossRef CAS.
- A. Demirbas, H. Alidrisi and M. A. Balubaid, Pet. Sci. Technol., 2015, 33, 93–101 CrossRef CAS.
- J. Lim, J. Pyun and K. Char, Angew. Chem., Int. Ed., 2015, 54, 3249–3258 CrossRef CAS PubMed.
- D.-y. Lee, Ind. Eng. Chem. Prod. Res. Dev., 1975, 14, 171–177 CrossRef CAS.
- Elemental Sulfur and Sulfur-Rich Compounds I, in Top. Curr. Chem., ed. R. Steudel, 2003, 230, p. 2003 Search PubMed.
- Elemental Sulfur and Sulfur-Rich Compounds II, in Top. Curr. Chem., ed. R. Steudel, 2003, 231, p. 2003 Search PubMed.
- G. Kutney, Sulfur. History, Technology, Applications & Industry, ChemTec, Toronto, 2007 Search PubMed.
- U. S. G. Survey, Mineral Commodity Summaries, 2017, p. 202, DOI:10.3133/70180197.
- M. J. H. Worthington, R. L. Kucera and J. M. Chalker, Green Chem., 2017, 19, 2748–2761 RSC.
- M. P. Crockett, A. M. Evans, M. J. H. Worthington, I. S. Albuquerque, A. D. Slattery, C. T. Gibson, J. A. Campbell, D. A. Lewis, G. J. L. Bernardes and J. M. Chalker, Angew. Chem., Int. Ed., 2016, 55, 1714–1718 CrossRef CAS PubMed.
- F. Garcia and M. M. J. Smulders, J. Polym. Sci., Part A: Polym. Chem., 2016, 54, 3551–3577 CrossRef CAS PubMed.
- W. J. Chung, J. J. Griebel, E. T. Kim, H. Yoon, A. G. Simmonds, H. J. Ji, P. T. Dirlam, R. S. Glass, J. J. Wie, N. A. Nguyen, B. W. Guralnick, J. Park, A. Somogyi, P. Theato, M. E. Mackay, Y.-E. Sung, K. Char and J. Pyun, Nat. Chem., 2013, 5, 518–524 CrossRef CAS PubMed.
- Y. Zhang, K. M. Konopka, R. S. Glass, K. Char and J. Pyun, Polym. Chem., 2017, 8, 5167–5173 RSC.
- Y. Zhang, J. J. Griebel, P. T. Dirlam, N. A. Nguyen, R. S. Glass, M. E. MacKay, K. Char and J. Pyun, J. Polym. Sci., Part A: Polym. Chem., 2017, 55, 107–116 CrossRef CAS.
- J. Park, E. T. Kim, C. Kim, J. Pyun, H.-S. Jang, J. Shin, J. W. Choi, K. Char and Y.-E. Sung, Adv. Energy Mater., 2017, 7, 1700074 CrossRef.
- V. P. Oleshko, A. A. Herzing, C. L. Soles, J. J. Griebel, W. J. Chung, A. G. Simmonds and J. Pyun, Microsc. Microanal., 2016, 22, 1198–1221 CrossRef CAS PubMed.
- V. P. Oleshko, A. A. Herzing, K. A. Twedt, J. J. Griebel, J. J. McClelland, J. Pyun and C. L. Soles, Langmuir, 2017, 33, 9361–9377 CrossRef CAS PubMed.
- J. Lim, U. Jung, W. T. Joe, E. T. Kim, J. Pyun and K. Char, Macromol. Rapid Commun., 2015, 36, 1103–1107 CrossRef CAS PubMed.
- E. T. Kim, W. J. Chung, J. Lim, P. Johe, R. S. Glass, J. Pyun and K. Char, Polym. Chem., 2014, 5, 3617–3623 RSC.
- E. T. Kim, J. Park, C. Kim, A. G. Simmonds, Y.-E. Sung, J. Pyun and K. Char, ACS Macro Lett., 2016, 5, 471–475 CrossRef CAS.
- J. J. Griebel, N. A. Nguyen, A. V. Astashkin, R. S. Glass, M. E. MacKay, K. Char and J. Pyun, ACS Macro Lett., 2014, 3, 1258–1261 CrossRef CAS.
- J. J. Griebel, N. A. Nguyen, S. Namnabat, L. E. Anderson, R. S. Glass, R. A. Norwood, M. E. MacKay, K. Char and J. Pyun, ACS Macro Lett., 2015, 4, 862–866 CrossRef CAS.
- J. J. Griebel, G. Li, R. S. Glass, K. Char and J. Pyun, J. Polym. Sci., Part A: Polym. Chem., 2015, 53, 173–177 CrossRef CAS.
- P. T. Dirlam, A. G. Simmonds, T. S. Kleine, N. A. Nguyen, L. E. Anderson, A. O. Klever, A. Florian, P. J. Costanzo, P. Theato, M. E. Mackay, R. S. Glass, K. Char and J. Pyun, RSC Adv., 2015, 5, 24718–24722 RSC.
- K. J. Rao and S. Paria, RSC Adv., 2013, 3, 10471–10478 RSC.
- U. S. E.P.A., R.E.D. Sulfur Facts, U.S. Environmental Protection Agency, Pesticides and Toxic Substances Branch, Washington, D.C., 1991 Search PubMed.
- R. Musah, S. Kim and R. Kubec, Phosphorus, Sulfur Silicon Relat. Elem., 2005, 180, 1455–1456 CrossRef CAS.
- S. Kim, R. Kubec and R. A. Musah, J. Ethnopharmacol., 2006, 104, 188–192 CrossRef CAS PubMed.
- J. T. Weld and A. Gunther, J. Exp. Med., 1947, 85, 531–542 CrossRef CAS PubMed.
- G. B. Lawson, Am. Rev. Tuberc., 1934, 29, 650–651 CAS.
- L. Libenson, F. P. Hadley, A. P. McIlroy, V. M. Wetzel and R. R. Mellon, J. Infect. Dis., 1953, 93, 28–35 CrossRef CAS PubMed.
- G. Robert and S. W. John Jr, Application, WO Pat., 1997-US19812 9818872, 1998.
- M. Takeji, Application, US Pat., 1976-754266 4127686, 1978.
- C. Wang, W.-Y. Lee, R. Nakajima, J. Mei, D. H. Kim and Z. Bao, Chem. Mater., 2013, 25, 4806–4812 CrossRef CAS.
- A. B. Lowe, Polym. Chem., 2014, 5, 4820–4870 RSC.
- A. V. Raghu, G. S. Gadaginamath, N. Mathew, S. B. Halligudi and T. M. Aminabhavi, J. Appl. Polym. Sci., 2007, 106, 299–308 CrossRef CAS.
- D. S. Donawade, A. V. Raghu, U. M. Muddapur and G. S. Gadaginamath, Indian J. Chem., Sect. B: Org. Chem. Incl. Med. Chem., 2005, 44B, 1470–1475 CAS.
- S. Lew, K. Jothimurugesan and M. Flytzani-Stephanopoulos, Ind. Eng. Chem. Res., 1989, 28, 535–541 CrossRef CAS.
- M. A. Sayyadnejad, H. R. Ghaffarian and M. Saeidi, Int. J. Environ. Sci. Technol., 2008, 5, 565–569 CrossRef CAS.
- M. Arslan, B. Kiskan and Y. Yagci, Macromolecules, 2016, 49, 767–773 CrossRef CAS.
- S. Potivichayanon, P. Pokethitiyook and M. Kruatrachue, Process Biochem., 2006, 41, 708–715 CrossRef CAS.
- Q. Lian, Y. Li, K. Li, J. Cheng and J. Zhang, Macromolecules, 2017, 50, 803–810 CrossRef CAS.
- S. Z. Khawaja, S. Vijay Kumar, K. K. Jena and S. M. Alhassan, Mater. Lett., 2017, 203, 58–61 CrossRef CAS.
- V. K. Shankarayya Wadi, K. K. Jena, S. Z. Khawaja, K. Yannakopoulou, M. Fardis, G. Mitrikas, M. Karagianni, G. Papavassiliou and S. M. Alhassan, ACS Omega, 2018, 3, 3330–3339 CrossRef CAS.
- B. Meyer, Chem. Rev., 1964, 64, 429–451 CrossRef CAS.
- B. Meyer, Inorg. Sulphur Chem., 1968, 241–258 CAS.
- B. Meyer, Adv. Inorg. Chem. Radiochem., 1976, 18, 287–317 CrossRef CAS.
- B. Meyer, Chem. Rev., 1976, 76, 367–388 CrossRef CAS.
- R. F. Bacon and R. Fanelli, J. Am. Chem. Soc., 1943, 65, 639–648 CrossRef CAS.
- R. H. Arntson, F. W. Dickson and G. Tunell, Science, 1958, 128, 716–718 CrossRef CAS PubMed.
- Y. Akahama, M. Kobayashi and H. Kawamura, Phys. Rev. B: Condens. Matter Mater. Phys., 1993, 48, 6862–6864 CrossRef CAS.
- A. G. M. Ferreira and L. Q. Lobo, J. Chem. Thermodyn., 2010, 43, 95–104 CrossRef.
- A. V. Tobolsky, J. Polym. Sci., Part C: Polym. Symp., 1966, 12, 71–78 CrossRef.
- A. V. Tobolsky, J. Polym. Sci., Part C: Polym. Symp., 1966, 12, 71–78 CrossRef.
- A. V. Tobolsky, W. MacKnight, R. B. Beevers and V. D. Gupta, Polymer, 1963, 4, 423–427 CrossRef CAS.
- K. Menard, Dynamic Mechanical Analysis: A Practical Introduction to Techniques and Applications, CRC, 1999 Search PubMed.
- N. L. Batista, P. Olivier, G. Bernhart, M. C. Rezende and E. C. Botelho, Mater. Res., 2016, 19, 195–201 CrossRef CAS.
- T. S. Kleine, N. A. Nguyen, L. E. Anderson, S. Namnabat, E. A. LaVilla, S. A. Showghi, P. T. Dirlam, C. B. Arrington, M. S. Manchester, J. Schwiegerling, R. S. Glass, K. Char, R. A. Norwood, M. E. Mackay and J. Pyun, ACS Macro Lett., 2016, 5, 1152–1156 CrossRef CAS.
- J. Hu, W. Chen, P. Fan, J. Gao, G. Fang, Z. Cao and F. Peng, Polym. Test., 2017, 62, 335–341 CrossRef CAS.
- E. B. Murphy, E. Bolanos, C. Schaffner-Hamann, F. Wudl, S. R. Nutt and M. L. Auad, Macromolecules, 2008, 41, 5203–5209 CrossRef CAS.
- M. Worzakowska, J. Therm. Anal. Calorim., 2015, 121, 235–243 CrossRef CAS.
Footnote |
† Electronic supplementary information (ESI) available: Proton NMR of PVP and PAO; IR spectra of PAOS10–99; DSC curves of PVP, S8, PAO, and PAOS10–99. See DOI: 10.1039/c8ra06847j |
|
This journal is © The Royal Society of Chemistry 2018 |
Click here to see how this site uses Cookies. View our privacy policy here.