DOI:
10.1039/C8RA07144F
(Paper)
RSC Adv., 2018,
8, 33972-33979
Magnetic core–shell-structured Fe3O4@CeO2 as an efficient catalyst for catalytic wet peroxide oxidation of benzoic acid†
Received
27th August 2018
, Accepted 18th September 2018
First published on 3rd October 2018
Abstract
A magnetic core–shell-structured Fe3O4@CeO2 catalyst was prepared by a simple solvothermal method and applied in the solid state for catalytic wet peroxide oxidation (CWPO) of benzoic acid. The obtained catalyst was characterized by N2 adsorption–desorption, X-ray diffraction (XRD), magnetic measurements, transmission electron microscopy (TEM) and X-ray photoelectron spectroscopy (XPS). The experimental results showed that Fe3O4@CeO2 possessed superior catalytic efficiency for CWPO of benzoic acid than that of Fe3O4. The high catalytic activity was caused by a synergistic effect between Fe3O4 and CeO2, which assisted the decomposition of H2O2 into hydroxyl radicals (·OH). Fe3O4@CeO2 exhibited low Fe leaching of 4.2 mg L−1, which approximately accounted for barely 0.76% of the total Fe amount in the catalyst. The effects of radical scavengers indicated that benzoic acid was degraded mainly by ·OH attack, which occurred both in the bulk solution and on the Fe3O4@CeO2 surface. In the stability tests, there was loss of merely 4% in the benzoic acid removal rate after six cycles of reaction, and the saturation magnetization of Fe3O4@CeO2 hardly changed, which suggested that the Fe3O4@CeO2 catalyst was fairly effective in reutilization and stability.
1. Introduction
Benzoic acid is well-known for its wide range of applications in food preservatives and reaction intermediates,1 but wastewater containing benzoic acid in manufacturing industries can be highly toxic and harmful. Traditional processes such as biological treatments have negligible effect on benzoic acid due to its low biodegradability. Other approaches including adsorption,2,3 photocatalytic degradation4,5 and chemical oxidation6 have also been extensively investigated to remove benzoic acid from aqueous solutions. Among the advanced oxidation processes, catalytic wet peroxide oxidation (CWPO) has attracted increasing attention due to its low cost, ambient reaction conditions, and nontoxic products from H2O2 decomposition.7,8
As favorable catalysts for CWPO, iron-based materials can initiate a modified Fenton process over solid surfaces by heterogeneously catalyzing the degradation of organics.9–13 During this process, H2O2 is decomposed effectively into ·OH, and the radicals then react rapidly with organics along with their intermediates. Some metals with multiple redox states other than Fe-containing catalysts, such as Mn, Cu, and Ce, can also function as Fenton-like catalysts with similar catalytic mechanisms to that of the iron-based ones.14–16
An important but inexpensive rare earth oxide, cerium oxide, demonstrates broad applications in developed oxidation processes either as a catalyst or as a non-inert support for catalysts.17–20 Both the presence of oxygen vacancies on the oxide surface and the availability of surface Ce3+ at such defect sites can contribute to excellent catalytic activity. Fe3O4/CeO2 composite particles were prepared via an impregnation method and applied as Fenton-like catalysts for 4-chlorophenol degradation.21 Compared with isolated Fe3O4 or CeO2, the obtained composites exhibited higher catalytic activity, suggesting the existence of a certain synergistic effect between these two metal oxides. The thermodynamically favored electron transfer from Fe2+ to Ce4+ resulted in increasing Ce3+ ions during the CWPO reaction process, whereas serious iron leaching up to 11.8 mg L−1 occurred in the meantime.
Magnetic catalysts with a core–shell structure have received increasing attention these days as they can prevent undesired aggregation and metal leaching while maintaining the necessary stability and reusability.22–24 Moreover, the magnetic property of Fe3O4 is conducive to recover the catalyst from solution, which plays an important role in practical applications. On this basis, further investigation was carried out for the usage of magnetic core–shell-structured cerium oxide for CWPO reactions. Here, magnetic core–shell-structured Fe3O4@CeO2 nanoparticles were successfully prepared and subsequently characterized using N2 adsorption–desorption, X-ray diffraction (XRD), magnetic measurements, transmission electron microscopy (TEM), and X-ray photoelectron spectroscopy (XPS). Their performance with respect to adsorption and CWPO of benzoic acid was evaluated by examining the benzoic acid and TOC removal. The influences of initial solution pH and radical scavengers on the degradation rate of benzoic acid during the CWPO process were systematically studied, whereas leaching of iron and cerium from the catalyst into aqueous solution was measured as well. The possible catalysis mechanism of Fe3O4@CeO2 in the CWPO process was thus proposed according to the results of above-mentioned analyses. Finally, the stability of the Fe3O4@CeO2 catalyst was tested with six successive runs.
2. Experimental
2.1. Catalyst preparation
Fe3O4 and CeO2 nanoparticles were obtained from Sigma-Aldrich. The commercially obtained Fe3O4 and CeO2 particles were uniform with a diameter of around 100 nm. Core–shell-structured Fe3O4@CeO2 nanoparticles were synthesized referring to the following description.25 First, a ceria precursor solution was prepared by the solvothermal method; 1 g Ce(NO3)3·6H2O and 1 g NaOH were separately dissolved in 20 mL of ethanol, and the mixture was stirred vigorously at a constant temperature of 50 °C for 24 h. Then, 0.05 mL of 30% H2O2 was added to the mixture solution under continuous stirring for 2 h. The precipitate was collected by centrifugation and washed before drying at 60 °C for 4 h. Under continuous stirring, 1 g of precipitate was then dispersed in 20 mL distilled water. The pH of the solution was adjusted to 0.1 using concentrated nitric acid. After stirring for 2 h, the ceria precursor solution was obtained when the solution was cooled to room temperature naturally. Afterwards, 0.1 g of Fe3O4 nanoparticles was dispersed in a mixture containing 30 mL distilled water and 3 mL of ceria precursor solution through an ultrasonic treatment process for 15 min. Also, 0.5 mol L−1 ammonium hydroxide solution was added to adjust the pH to 6.8. The final mixed solution was agitated vigorously by stirring for 4 h at 60 °C. After the reaction was completed, the particles were collected using an external magnet, washed thoroughly with ethanol, and dried in a vacuum oven at 60 °C overnight. The final products were obtained by heat treatment of the particles in a tube furnace under N2 flow, which lasted for 3 h at 300 °C with a heating rate of 3 °C min−1.
X-ray powder diffraction (XRD) was conducted on a Philips X'Pert MPD diffractometer using Cu Kα radiation. The specific surface area and pore volume of catalysts were calculated from N2 adsorption and desorption isotherms at −196 °C, which were acquired using a Builder SSA-420 instrument. Samples should be in vacuo outgassed at 300 °C overnight prior to the measurements. Magnetic testing was carried out on the VSM Digital Measurement System JDM-13 by applying a vibrating sample magnetometer. The morphology and structure of the prepared catalysts were observed and characterized by transition electron microscopy (TEM, JEOL model JEM-2010, acceleration voltage 200 kV) with samples suspended in ethanol and dropped on copper grids with a holey-carbon film support. X-ray photoelectron spectroscopy (XPS) was performed on a Kratos XSAM800 spectrometer with monochromatic Al Kα as the radiation source, and all binding energies were calibrated by the C 1s peak at 284.6 eV. XPS data of Ce 3d and Fe 2p spectra were fitted using the software CasaXPS.
2.2. Oxidation experiments
Oxidation was conducted in a 250 mL jacketed glass reactor equipped with a magnetic stirrer. In each operation, the reactor was first filled with benzoic acid solution (100 mL, initial concentration 50 mg L−1), followed by adjusting the initial pH to set values with 0.1 mol L−1 HCl or 0.1 mol L−1 NaOH solution. The reaction temperature was set as 30 °C, which was maintained constant with water circulation in the thermostatic bath provided by the jacket. Then, a certain volume of 30% H2O2 (the theoretically stoichiometric amount required for complete mineralization of benzoic acid) and 100 mg of catalyst were added simultaneously to initiate the reaction. For adsorption experiments, the H2O2 solution was replaced by deionized water of identical volume. Samples were periodically extracted and immediately filtered with a 0.45 μm membrane for further analyses, whereas the residual H2O2 was consumed by adding sodium hydrogen sulfite. Each experiment was run three times, and the average value was reported.
2.3. Analytical techniques
The concentration of benzoic acid was evaluated by a high performance liquid chromatograph (HPLC, Shimadzu Prominence LC-20A) equipped with a UV detector and a C18 reverse phase column (4.6 × 250 mm, 5 μm). The mobile phase was methanol/ammonium acetate (5/95), flow rate was 1.0 mL min−1, injection volume was 10 μL, and detection wavelength was 230 nm. The solution pH was monitored by a PHC-3C pH meter. The leaching amount of Fe and Ce from Fe3O4@CeO2 catalyst to the solution during oxidation was determined by inductively coupled plasma atomic emission spectrometry (ICP-AES, ICPE-9000, Thermo Electron Corporation, USA). The total organic carbon (TOC) was measured using a Shimadzu TOC-5000A analyzer.
3. Results and discussion
3.1. Characterization of catalysts
The crystal structures of nanoparticles were examined by XRD, and the XRD pattern of Fe3O4@CeO2 nanoparticles is shown in Fig. 1a. The diffraction peaks for Fe3O4@CeO2 can be clearly discerned at 30.2°, 35.5°, 36.8°, 43.2°, 53.5°, 57.2°, and 62.7°, which correspond to the lattice planes of (220), (311), (222), (400), (422), (511), and (440).26 Diffraction peaks assigned to CeO2 with a cubic fluorite structure appear at 28.6°, 33.1°, 47.6° and 56.5°, which correspond to the lattice planes of (111), (200), (220) and (311).17
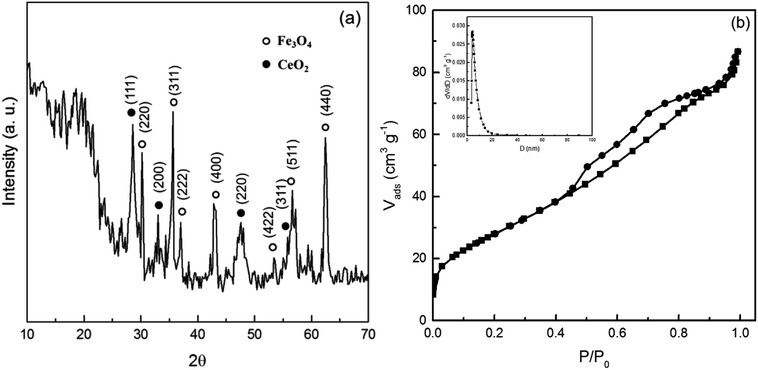 |
| Fig. 1 (a) X-ray pattern of Fe3O4@CeO2 nanoparticles; (b) N2 adsorption–desorption isotherms and pore size distribution (inset) of Fe3O4@CeO2 nanoparticles. | |
The physical and chemical properties of Fe3O4, CeO2 and Fe3O4@CeO2 nanoparticles are summarized in Table 1. The Brunauer–Emmett–Teller surface area (SBET), pore size, and pore volume of Fe3O4 were 65.6 m2 g−1, 0.026 cm3 g−1, and 5.19 nm, respectively. CeO2 covering the Fe3O4 surface enhanced both the surface area and pore volume, which was due to the existence of large channels resulting from CeO2 deposition in the coating layer. Besides, as presented in Fig. 1b, the N2 adsorption–desorption isotherm of Fe3O4@CeO2 was type IV accompanied with an apparent type H3 hysteresis loop, indicating a mesoporous structure.27 The corresponding pore size distribution (inset of Fig. 1b) further confirmed such a structure.
Table 1 Physical and chemical properties of Fe3O4 and Fe3O4@CeO2 nanoparticles
Sample |
SBET (m2 g−1) |
Pore volume (cm3 g−1) |
Average pore size (nm) |
Ms (emu g−1) |
Particle size (nm) |
Fe3O4 |
65.6 |
0.026 |
5.19 |
69.1 |
100 |
CeO2 |
85.6 |
0.041 |
5.12 |
— |
100 |
Fe3O4@CeO2 |
104.9 |
0.15 |
4.49 |
22.9 |
100–150 |
The room temperature magnetization curves of Fe3O4 and Fe3O4@CeO2 nanoparticles are presented in Fig. S1 of the ESI.† Superparamagnetic properties were observed for both types of nanoparticles with nearly zero coercivity and remanence. The saturation magnetization (Ms) values were 69.1 and 22.9 emu g−1 for Fe3O4 and Fe3O4@CeO2 nanoparticles, respectively. The lower Ms value for Fe3O4@CeO2 was mainly ascribed to the existence of CeO2.25 As shown in the inset of Fig. S1,† the core–shell-structured Fe3O4@CeO2 nanoparticles were proven to be a promising candidate for the removal of organic contaminants as suggested by the easy separation from reaction solution under an external magnetic field due to the magnetic nature.
Fig. 2 presents the morphology of Fe3O4@CeO2 nanoparticles with particle sizes listed in Table 1. Fig. 2a demonstrates the regularity and uniformity of the obtained Fe3O4@CeO2 nanoparticles with diameters ranging from 100 nm to 150 nm; CeO2 nanoparticles were well dispersed on the surface of Fe3O4 nanocrystals with negligible aggregation. The lattice fringe spacing of the nanoparticles (Fig. 2b) was about 0.25 nm, corresponding to the (311) reflection plane with a diffraction peak at 35.5°. The lattice fringe spacing of Fe3O4@CeO2 was about 0.32 nm, which could be assigned to the (111) reflection plane of CeO2 with the diffraction peak at 28.6° (Fig. 1a).
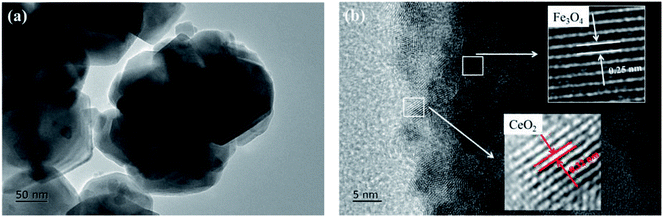 |
| Fig. 2 TEM and HR-TEM images of Fe3O4@CeO2. | |
Ce 3d and Fe 2p peaks were analyzed in detail by XPS for better understanding of the chemical states of Ce and Fe in Fe3O4@CeO2. XPS spectra for Fe3O4@CeO2 before and after reaction are given in Fig. 3. The Ce 3d region could be resolved into eight peaks; peaks v1 and u1 were ascribed to Ce3+, whereas other peaks were assigned to Ce4+.17,21,25 The reaction with H2O2 led to larger v1 and u1 peaks (Fig. 3b), which indicated the increasing amount of Ce3+ on the Fe3O4@CeO2 surface.
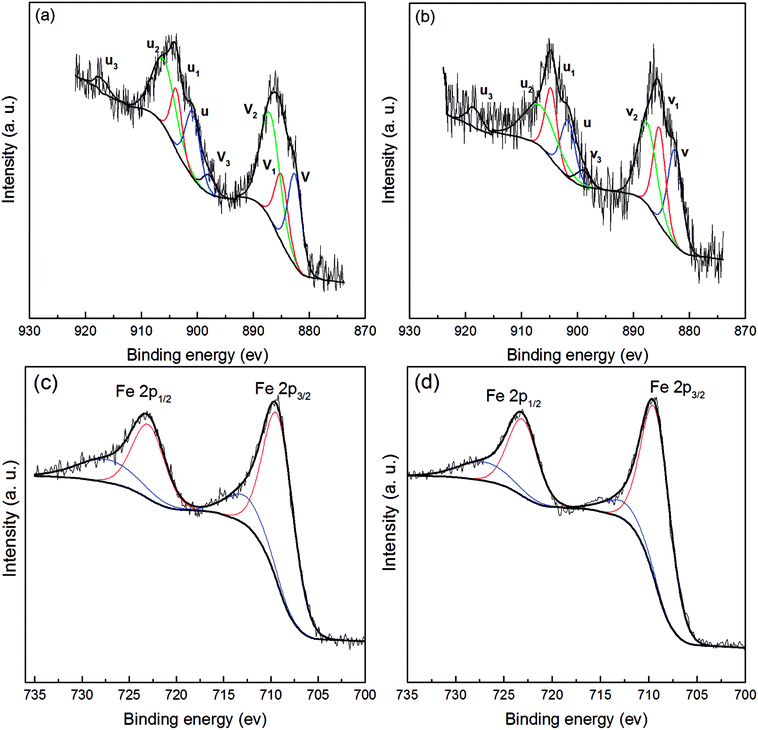 |
| Fig. 3 (a) Ce 3d and (c) Fe 2d XPS spectra of Fe3O4@CeO2 before reaction; (b) Ce 3d and (d) Fe 2d XPS spectra of Fe3O4@CeO2 after reaction. | |
Fe 2p spectra in both Fig. 3c and d display a spin–orbit doublet with binding energies of 723.6 eV for Fe 2p1/2 and 709.8 eV for Fe 2p3/2. The Fe 2p3/2 peak was deconvoluted into two parts in terms of an Fe2+ peak at 709.0 eV and Fe3+ peak at 711.0 eV.21,28 After reacting for 120 min, a decreased peak area for Fe2+ was observed, implying the oxidation of Fe2+ to Fe3+ by H2O2 on the surface of Fe3O4@CeO2.
3.2. Catalytic activity of catalysts
The removal efficiencies of benzoic acid among varied processes were compared (initial benzoic acid concentration of 50 mg L−1) to investigate the catalytic activity of Fe3O4@CeO2 in benzoic acid CWPO. As shown in Fig. 4a, the removal efficiency was approximately 10% after 120 min of reaction without catalyst; in other words, it was difficult to degrade benzoic acid by H2O2 alone. On the other hand, about 4%, 3%, and 6% removal was observed for Fe3O4, CeO2, and Fe3O4@CeO2 alone primarily due to surface adsorption, which was almost negligible compared to the fast removal in the CWPO reaction. In the CWPO process, a small amount of benzoic acid degraded in the presence of pure CeO2. The removal efficiency with Fe3O4@CeO2 as the catalyst became notably higher than that for pure Fe3O4, indicating that the catalytic activity was enhanced by CeO2 coating. Moreover, the degradation of benzoic acid by a physical mixture of Fe3O4 and CeO2 materials (concentration of 1 g L−1 and mass ratio of 1
:
1) was also examined. The catalytic performance of Fe3O4@CeO2 was higher that of the physical mixture of Fe3O4 and CeO2 materials, which suggested that a synergistic effect might exist between Fe3O4 and CeO2 in Fe3O4@CeO2 nanoparticles.29
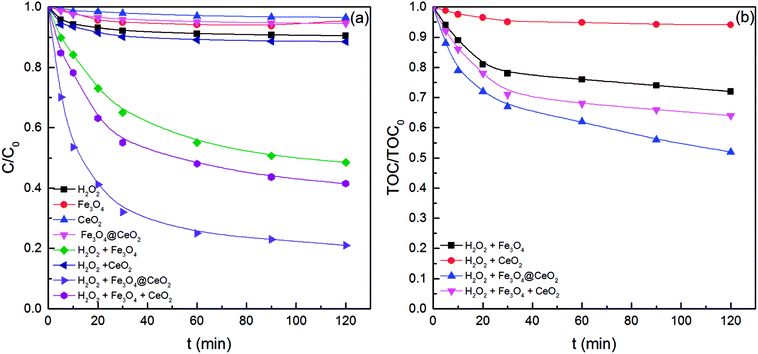 |
| Fig. 4 Removal efficiency of (a) benzoic acid and (b) TOC in different processes. Experimental conditions: 50 mg L−1 of benzoic acid, 1 g L−1 of catalyst, 250 mg L−1 of H2O2, T = 30 °C, pH = 3.2. | |
Fig. 4b depicts the TOC removal trend during benzoic acid degradation by CWPO. As can be seen, the mineralization degree was 48% after 120 min of reaction in the presence of Fe3O4@CeO2, whereas the removal rate of benzoic acid reached 80% under the same conditions. Such phenomena suggested the remainder of several intermediates that formed during oxidation in the solution such as small chain carboxylic acids. Besides, the best TOC removal performance exhibited by Fe3O4@CeO2 could be explained by the synergetic effect of Fe3O4 and CeO2 that accelerated ·OH generation and induced deeper oxidation of intermediates.29
3.3. Effect of initial pH
Since CWPO is a strongly pH-dependent process, we further studied how the initial solution pH can influence benzoic acid degradation with Fe3O4@CeO2 as a catalyst. Fe3O4@CeO2 could function over a wide pH range, as suggested by the degradation efficiency of benzoic acid up to 80% at both acidic and neutral pH (Fig. 5). Nevertheless, further increase in solution pH reduced the removal rate of benzoic acid as the rapid decomposition of H2O2 in alkaline solution (pH 8.5 and 10.3 in this case) could generate molecular oxygen rather than ·OH; molecular oxygen is incapable of efficiently oxidizing organics under mild conditions.21,29 As a result, the lowest removal rate of benzoic acid was shown at pH 10.3.
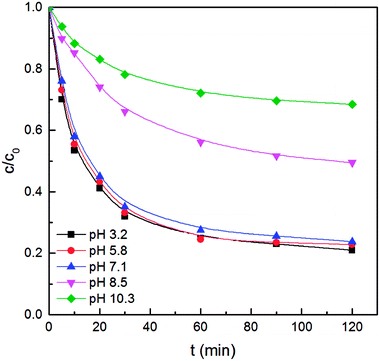 |
| Fig. 5 Effect of solution pH on the degradation of benzoic acid in CWPO with Fe3O4@CeO2 catalyst. Experimental conditions: 50 mg L−1 of benzoic acid, 1 g L−1 of catalyst, 250 mg L−1 of H2O2, T = 30 °C. | |
3.4. Metal leaching
The concentrations of leached Fe and Ce in solution during CWPO of benzoic acid were monitored at an initial pH of 3.2, and dissolved Ce was hardly detected due to cerium oxide's insolubility in water.30,31 As shown in Fig. 6, the total concentration of Fe leaching was 4.2 mg L−1, which barely accounted for 0.76% of Fe content in the original Fe3O4@CeO2 catalyst. The leaching level of Fe in this study was much lower than the reported value for Fe3O4/CeO2 composites prepared by the impregnation method.21
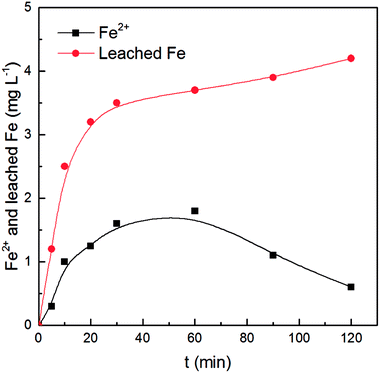 |
| Fig. 6 Variation of the concentration of Fe2+ and leached Fe in the solution during CWPO of benzoic acid. Experimental conditions: 50 mg L−1 of benzoic acid, 1 g L−1 of catalyst, 250 mg L−1 of H2O2, T = 30 °C, pH = 3.2. | |
The variation of Fe2+ concentration is given in Fig. 6, where a tendency to increase first and then decrease was observed. The concentration of Fe2+ increased and then reached a peak value of about 1.8 mg L−1 at 60 min when the degradation rate of benzoic acid no longer sharply increased. As the oxidation reaction progressed, the concentration of Fe2+ decreased to about 0.6 mg L−1 after 120 min of the reaction. Similar results were reported in previous studies.32,33 In the ascending stage, the oxidation of the Fe3O4@CeO2 catalyst by H2O2 could release Fe2+ into solution.16,21 Fe2+ in the aqueous solution played an important role in the decomposition of H2O2 and the generation of ·OH. In the descending stage, dissolved Fe2+ was oxidized to Fe3+ by the remaining H2O2. Accordingly, the total leached Fe increased the entire time, which could be ascribed to the leaching of Fe2+ and Fe3+ from the Fe3O4@CeO2 catalyst as well as the oxidation of Fe2+ in solution.
3.5. Possible catalysis mechanism of Fe3O4@CeO2
To verify the actual reactive species mediated in the CWPO process, the effect of tert-butanol and KI as radical scavengers on the degradation of benzoic acid was investigated. tert-Butanol has a fast reaction rate with ·OH and can terminate radical chain reactions; iodide ions can eliminate surface-bound ·OH (·OHs) produced at the surface of the Fe3O4@CeO2 catalyst.21,26
It can be seen from Fig. 7 that the degradation rate decreased by about 61.5% in the presence of 300 mmol L−1 tert-butanol, which implied significant influence of ·OH reaction on benzoic acid decomposition. Compared to the result for single H2O2 oxidation, the removal efficiency obtained in the presence of tert-butanol increased by about 6%, which could be due to the adsorption of Fe3O4@CeO2 (Fig. 4a). Moreover, with the addition of 10 mmol L−1 KI, the benzoic acid degradation rate decreased from 80% (in the absence of KI) to 62% after 120 min of the reaction, suggesting that surface reactions involving ·OHs play a considerable role in benzoic acid degradation.16,21
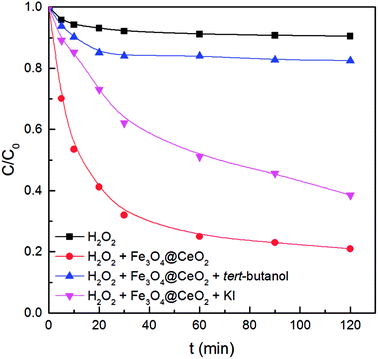 |
| Fig. 7 Effect of radical scavengers on CWPO of benzoic acid. Experimental conditions: 50 mg L−1 of benzoic acid, 1 g L−1 of catalyst, 250 mg L−1 of H2O2, T = 30 °C, pH = 3.2. | |
On the basis of the results obtained above, it could be concluded that benzoic acid degradation occurred both in the bulk solution and on the catalyst surface. A possible catalysis mechanism of core–shell-structured Fe3O4@CeO2 in CWPO was proposed. As proposed by other researchers,34 the existing Ce3+ on the surface of the CeO2 shell could react with H2O2 to produce surface-bound ·OHs, and Ce3+ was simultaneously oxidized to Ce4+. When H2O2 diffused from the bulk solution to the surface of the Fe3O4 core through the channels of CeO2, the existing Fe2+ reacted with H2O2 to generate ·OHs,35–37 which could explain why the amount of Fe2+ on the Fe3O4@CeO2 surface determined by XPS decreased after the CWPO reaction (Fig. 3). Some produced ·OHs species reacted with benzoic acid on the catalyst surface, and the rest diffused from the catalyst surface into the bulk solution. Furthermore, the transfer of electrons from Fe2+ to Ce4+ occurred, and the amount of Ce3+ on the catalyst surface increased after the CWPO reaction, which was confirmed by the results of XPS (Fig. 3). Similar to Fe2+ on the catalyst surface, the leached Fe2+ in bulk solution initiated the decomposition of H2O2 to produce ·OH for the oxidation of benzoic acid and other intermediates.
3.6. Stability tests
The stability of the Fe3O4@CeO2 catalyst is an important factor for potential industrial applications. To evaluate recyclability, the Fe3O4@CeO2 catalyst was subjected to successive degradation of benzoic acid six times. The used catalyst after each run was filtered out, washed with deionized water, and then dried at 110 °C for 24 h. As shown in Fig. 8, the removal rate of benzoic acid was reduced by merely 4% after six cycles of reaction. A slight loss of the used catalyst was inevitable during the recovery process. However, residual organic compounds adsorbed onto the catalyst might function negatively against its reusability.28 Moreover, the saturation magnetization (Ms) of the catalyst before the reaction was 22.9 emu g−1, and it remained almost unchanged after successive reactions. Overall, Fe3O4@CeO2 was regarded as an excellent catalyst in terms of reutilization and stability.
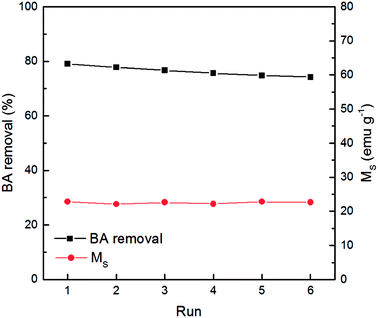 |
| Fig. 8 Benzoic acid removal and the saturation magnetization of Fe3O4@CeO2 catalyst in the stability tests. Experimental conditions: 50 mg L−1 of benzoic acid, 1 g L−1 of catalyst, 250 mg L−1 of H2O2, T = 30 °C, pH = 3.2. | |
4. Conclusions
Magnetic core–shell-structured Fe3O4@CeO2 nanoparticles were successfully prepared, characterized, and systematically evaluated as a solid catalyst for CWPO of benzoic acid. Fe3O4@CeO2 exhibited excellent catalytic performance for the degradation of benzoic acid. The excellent catalytic efficiency could be due to the synergistic effect between Fe3O4 and CeO2, which enhanced the H2O2 decomposition into ·OH. In addition, it was found that Fe3O4@CeO2 was highly effective for CWPO of benzoic acid in aqueous solutions at acidic and neutral pH. Compared to other previously reported results, the level of leaching Fe for Fe3O4@CeO2 catalyst was very low. Based on the results of catalyst characterization and the effects of radical scavengers, a probable degradation pathway of benzoic acid by the attack of ·OH produced both in bulk solution and on the Fe3O4@CeO2 surface was proposed. Fe3O4@CeO2 was demonstrated to be an effective and stable catalyst in CWPO of benzoic acid in stability tests. In conclusion, Fe3O4@CeO2 shows great potential in the treatment of benzoic acid-containing wastewater due to its catalytic and magnetic properties.
Conflicts of interest
There are no conflicts to declare.
Acknowledgements
The authors would like to convey their gratitude for the financial support from Provincial Key Disciplines of Chemical Engineering and Technology in Guizhou Province (No. ZDXK [2017] 8), Fund of Guizhou Department of Science and Technology (No. KY [2017] 1190 and KY [2017] 1187), United Fund of Guizhou Department of Science and Technology (No. LH [2017] 7317 and LH [2016] 7296), Fund of Tongren Department of Science and Technology (No. KY [2017] 36) and the Guizhou Provincial Department of Education Foundation (No. QJHKYZ2016-107).
References
- X. D. Xin, W. Si, Z. X. Yao, R. Feng, B. Du, L. G. Yan and Q. Wei, Adsorption of benzoic acid from aqueous solution by three kinds of modified bentonites, J. Colloid Interface Sci., 2011, 359(2), 499–504 CrossRef CAS PubMed.
- D. M. Yang, Z. Q. Song and X. R. Qian, Adsorption of benzoic acid by hydrotalcites and their calcined products, Environ. Eng. Sci., 2010, 27(10), 853–860 CrossRef CAS.
- M. Koh and T. Nakajima, Adsorption of aromatic compounds on CxN-coated activated carbon, Carbon, 2000, 38(14), 1947–1954 CrossRef CAS.
- T. Velegraki and D. Mantzavinos, Conversion of benzoic acid during TiO2-mediated photocatalytic degradation in water, Chem. Eng. J., 2008, 140(1), 15–21 CrossRef CAS.
- K. Mehrotra, G. S. Yablonsky and A. K. Ray, Macro kinetic studies for photocatalytic degradation of benzoic acid in immobilized systems, Chemosphere, 2005, 60(10), 1427–1436 CrossRef CAS PubMed.
- M. I. Pariente, F. Martinez, J. A. Melero, J. A. Botas, T. Velegraki, N. P. Xekoukoulotakis and D. Mantzavinos, Heterogeneous photo-Fenton oxidation of benzoic acid in water: effect of operating conditions, reaction by-products and coupling with biological treatment, Appl. Catal., B, 2008, 85(1), 24–32 CrossRef CAS.
- S. Esplugas, J. Gimenez, S. Contreras, E. Pascual and M. Rodríguez, Comparison of different advanced oxidation processes for phenol degradation, Water Res., 2002, 36(4), 1034–1042 CrossRef CAS PubMed.
- N. Azbar, T. Yonar and K. Kestioglu, Comparison of various advanced oxidation processes and chemical treatment methods for COD and color removal from a polyester and acetate fiber dyeing effluent, Chemosphere, 2004, 55(1), 35–43 CrossRef CAS PubMed.
- C. Catrinescu, C. Teodosiu, M. Macoveanu, J. Miehe-Brendle and R. Le Dred, Catalytic wet peroxide oxidation of phenol over Fe-exchanged pillared beidellite, Water Res., 2003, 37(5), 1154–1160 CrossRef CAS PubMed.
- J. A. Melero, F. Martínez, J. A. Botas, R. Molina and M. I. Pariente, Heterogeneous catalytic wet peroxide oxidation systems for the treatment of an industrial pharmaceutical wastewater, Water Res., 2009, 43(16), 4010–4018 CrossRef CAS PubMed.
- A. Rey, M. Faraldos, J. A. Casas, J. A. Zazo, A. Bahamonde and J. J. Rodríguez, Catalytic wet peroxide oxidation of phenol over Fe/AC catalysts: influence of iron precursor and activated carbon surface, Appl. Catal., B, 2009, 86(1), 69–77 CrossRef CAS.
- A. Rey, A. Bahamonde, J. A. Casas and J. J. Rodríguez, Selectivity of hydrogen peroxide decomposition towards hydroxyl radicals in catalytic wet peroxide oxidation (CWPO) over Fe/AC catalysts, Water Sci. Technol., 2010, 61(11), 2769–2778 CrossRef CAS PubMed.
- G. Q. Gan, J. Liu, Z. X. Zhu, Z. Yang, C. L. Zhang and X. H. Hou, A novel magnetic nanoscaled Fe3O4/CeO2 composite prepared by oxidation-precipitation process and its application for degradation of orange G in aqueous solution as Fenton-like heterogeneous catalyst, Chemosphere, 2017, 168, 254–263 CrossRef CAS PubMed.
- H. Zhao, H. J. Cui and M. L. Fu, Synthesis of core-shell structured Fe3O4@α-MnO2 microspheres for efficient catalytic degradation of ciprofloxacin, RSC Adv., 2014, 74(7), 39472–39475 RSC.
- F. J. Cui, J. W. Shi, B. Yuan and M. L. Fu, Synthesis of porous magnetic ferrite nanowires containing Mn and their application in water treatment, J. Mater. Chem. A, 2013, 19(1), 5902–5907 RSC.
- L. Xu and J. Wang, Degradation of 2,4,6-trichlorophenol using magnetic nanoscaled Fe3O4/CeO2 composite as a heterogeneous Fenton-like catalyst, Sep. Purif. Technol., 2015, 149, 255–264 CrossRef CAS.
- H. D. Qin, H. L. Chen, G. Yang, X. M. Zhang and Y. J. Feng, Efficient degradation of fulvic acids in water by catalytic ozonation with CeO2/AC, J. Chem. Technol. Biotechnol., 2014, 89(9), 1402–1409 CrossRef CAS.
- H. D. Qin, Q. Z. Dong, H. L. Chen, G. Yang and X. M. Zhang, Kinetics and mechanism of humic acids degradation by ozone in the presence of CeO2/AC, Ozone: Sci. Eng., 2015, 37(4), 1–8 CrossRef.
- H. D. Qin and H. L. Chen, Pretreatment of concentrated leachate by the combination of coagulation and catalytic ozonation with Ce/AC catalyst, Water Sci. Technol., 2016, 73(3), 511–519 CrossRef CAS PubMed.
- T. Montini, M. Melchionna, M. Monai and P. Fornasiero, Fundamentals and applications of CeO2-based materials, Chem. Rev., 2016, 116(10), 5987–6041 CrossRef CAS PubMed.
- L. Xu and J. Wang, Magnetic nanoscaled Fe3O4/CeO2 composite as an efficient Fenton-like heterogeneous catalyst for degradation of 4-chlorophenol, Environ. Sci. Technol., 2012, 46(18), 10145–10153 CrossRef CAS PubMed.
- W. K. Chang, K. R. Koteswara and H. K. Cing, A novel core-shell like composite In2O3@CaIn2O4 for efficient degradation of methylene blue by visible light, Appl. Catal., A, 2007, 321(1), 1–6 CrossRef CAS.
- K. Maeda, N. Sakamoto, T. Ikeda, H. Ohtsuka, A. Xiong, D. Lu, M. Kanehara, T. Teranishi and K. Domen, Preparation of core-shell-structured nanoparticles (with a noble-metal or metal oxide core and a chromia shell) and their application in water splitting by means of visible light, Chemistry, 2010, 16(26), 7750–7759 CrossRef CAS PubMed.
- S. Li, Y. H. Lin, B. P. Zhang, J. F. Li and C. W. Nan, BiFeO3/TiO2 core-shell structured nanocomposites as visible-active photocatalysts and their optical response mechanism, J. Appl. Phys., 2009, 105(5), 238–244 Search PubMed.
- Q. Wang, Y. Li, B. Liu, Q. Dong, G. Xu, L. Zhang and J. Zhang, Novel recyclable dual-heterostructured Fe3O4@CeO2/M (M = Pt, Pd and Pt-Pd) catalysts: synergetic and redox effects for superior catalytic performance, J. Mater. Chem. A, 2014, 3(1), 139–147 RSC.
- S. T. Xing, Z. C. Zhou, Z. C. Ma and Y. S. Wu, Characterization and reactivity of Fe3O4/FeMnOx core/shell nanoparticles for methylene blue discoloration with H2O2, Appl. Catal., B, 2011, 107(3), 386–392 CrossRef CAS.
- M. Kruk and M. Jaroniec, Gas adsorption characterization of ordered organic-inorganic nanocomposite materials, Chem. Mater., 2001, 13(10), 3169–3183 CrossRef CAS.
- H. D. Qin, R. Xiao and J. Chen, Catalytic wet peroxide oxidation of benzoic acid over Fe/AC catalysts: effect of nitrogen and sulfur co-doped activated carbon, Sci. Total Environ., 2018, 626, 1414–1420 CrossRef CAS PubMed.
- K. Y. Li, Y. Q. Zhao, C. S. Song and X. W. Guo, Magnetic ordered mesoporous Fe3O4/CeO2 composites with synergy of adsorption and Fenton catalysis, Appl. Surf. Sci., 2017, 425, 526–534 CrossRef CAS.
- P. C. C. Faria, D. C. M. Monteiro, J. J. M. Orfao and M. F. R. Pereira, Cerium, manganese and cobalt oxides as catalysts for the ozonation of selected organic compounds, Chemosphere, 2009, 74(6), 818–824 CrossRef CAS PubMed.
- P. C. C. Faria, J. J. M. Orfao and M. F. R. Pereira, Activated carbon and ceria catalysts applied to the catalytic ozonation of dyes and textile effluents, Appl. Catal., B, 2009, 88(3), 341–350 CrossRef CAS.
- M. L. Luo, D. Bowden and P. Brimblecombe, Catalytic property of Fe-Al pillared clay for Fenton oxidation of phenol by H2O2, Appl. Catal., B, 2009, 85(3), 201–206 CrossRef CAS.
- J. Y. Feng, X. J. Hu and P. L. Yue, Discoloration and mineralization of orange II using different heterogeneous catalysts containing Fe: a comparative study, Environ. Sci. Technol., 2004, 38(21), 5773–5778 CrossRef CAS PubMed.
- E. G. Heckert, S. Seal and W. T. Self, Fenton-like reaction catalyzed by the rare earth inner transition metal cerium, Environ. Sci. Technol., 2008, 42(13), 5014–5019 CrossRef CAS PubMed.
- R. C. C. Costa, F. C. C. Moura, J. D. Ardisson, J. D. Fabris and R. M. Lago, Highly active heterogeneous Fenton-like systems based on Fe0/Fe3O4 composites prepared by controlled reduction of ironoxides, Appl. Catal., B, 2008, 83(1), 131–139 CrossRef CAS.
- X. B. Hu, B. Z. Liu, Y. H. Deng, H. Z. Chen, S. Luo, C. Sun, P. Yang and S. G. Yang, Adsorption and heterogeneous Fenton degradation of 17α-methyltestosterone on nano Fe3O4/MWCNTs in aqueous solution, Appl. Catal., B, 2011, 107(3), 274–283 CrossRef CAS.
- W. Luo, L. H. Zhu, N. Wang, H. Q. Tang, M. J. Cao and Y. B. She, Efficient removal of organic pollutants with magnetic nanoscaled BiFeO3 as a reusable heterogeneous Fenton-like catalyst, Environ. Sci. Technol., 2010, 44(5), 1786–1791 CrossRef CAS PubMed.
Footnote |
† Electronic supplementary information (ESI) available. See DOI: 10.1039/c8ra07144f |
|
This journal is © The Royal Society of Chemistry 2018 |
Click here to see how this site uses Cookies. View our privacy policy here.