Visible-light-induced degradation of rhodamine B by nanosized Ag2S–ZnS loaded on cellulose†
Received
22nd July 2018
, Accepted 5th October 2018
First published on 8th October 2018
Abstract
In the present work, new visible-light-active nanosized Ag2S–ZnS loaded on cellulose (AZCE) was synthesized by a precipitation method. The AZCE composite was systematically characterized using powder X-ray diffraction (XRD), scanning electron microscopy (SEM), transmission electron microscopy (TEM), Brunauer–Emmett–Teller (BET) surface area, and UV-visible diffuse reflectance spectroscopy (UV-DRS). The activities of the photocatalysts were evaluated for rhodamine B dye (RhB) degradation under simulated sunlight and the amounts of the dye samples were analysed using a UV-vis spectrophotometer at λmax 554 nm. The effects of the reaction conditions such as pH, catalyst, hydrogen peroxide and dye concentration on the photodegradation rate have been investigated. The degradation profile reveals that 30 ppm of the dye could be effectively oxidized using 30 mg of the AZCE dose in the pH range 4–12 within 90 min. The oxidation of the RhB dye follows first-order kinetics and the rate constant was calculated to be 6.4 × 10−3 min−1. Various organic intermediates were identified during degradation using high performance liquid chromatography (HPLC), total organic content (TOC) and electron-spray ionization-mass spectrometry (ESI-MS). In order to determine the effectiveness of AZCE photocatalytic activity, other catalysts such as Ag2S loaded on cellulose (AZE) and ZnS loaded on cellulose (ZCE) were used as photocatalysts. The results show that photocatalytic activity follows the order AZCE > ACE > ZCE and this is due to the fact that a cellulose network is used as a catalyst carrier. The alkali pre-treated cellulose provides an activated surface hydroxyl groups to enhance the deposition efficiencies of Ag2S and ZnS and thereby a large amount of visible light can be absorbed and the photocatalytic activity is increased.
Introduction
Photocatalysis has been used for various environmental processes such as water purification, air purification and disinfection.1–4 Many engineers and scientists have put their efforts into studying the degradation and mineralization of a variety of toxic substances by photocatalytic oxidation. The majority of organic wastes comprise dyes and used in textile, leather, plastic, and cosmetic industries to impart colour to a wide range of products. According to WHO, every year more than 700
000 tonnes of synthetic dyes are manufactured across the world and the discarding of dyes is mostly through industrial effluents.5 In particular, RhB is extensively used as a colorant in paper, printing, textiles, and food products.6 Due to its widespread usages, RhB may be released to the environment. The toxicity profile in animal studies shows that it causes carcinogenicity and neurotoxicity.7,8 Moreover, the natural degradation of this type of compound is very difficult and may take a long time. Hence, various conventional treatment methods such as adsorption, biological oxidation and coagulation are used to treat the dye-polluted water.9 However, most of these techniques are time consuming and require the use of expensive chemicals.
Taking advantage of the high efficiency, simplicity, low costs, and use of solar light as a source of radiation, heterogeneous photocatalysis is receiving greater attention for water purification.10 In order to increase the photooxidation process, a sufficient number of photons interacted with the photocatalytic materials to carry out the redox reaction of the toxic compounds and determine the reusability of the catalyst.11–13 This can be achieved by providing a suitable supporting bio-polymeric network material for photocatalysis to degrade the toxic compound and also to avoid leaching of the photocatalytic material. Among all natural polymers, cellulose and its derivatives are considered significant for catalyst carriers. Further, cellulose is the most abundant natural polymer and has been used for a wide range of applications, such as filtration, food, medicine and healthcare due to its low-toxicity, hydrophilicity, biocompatibility and flexibility. Besides, cellulose has a high density of hydroxyl groups that will make it less prone to organic fouling.14–17
Among all the studied semiconductors as photocatalytic materials, metal sulphides have shown as most promising activities for water treatment under visible-light because of their suitable band energies. In particular, ZnS has emerged as one of the best photocatalysts, due to the high negative reduction potentials of the excited electrons and rapid generation of electron–hole pairs by photoexcitation, as well as due to its lack of toxicity, eco-friendliness, high stability, and low cost. However, some drawbacks of ZnS are the poor detachment efficiency and low migration ability of the photoexcited charge carriers. Besides, the main disadvantage of ZnS is its limited photocatalytic activity under visible light because of its wide band gap. To increase the photocatalytic activity of ZnS nanoparticles, it is advantageous to unite narrow bandgap (Eg) materials such as either metals or semiconducting materials.18–20 Hence, Ag2S has been used and this material has attracted great attention due to its potential in many applications such as photoconductors, solar cells, and near infrared photodetectors and due to less toxicity.21–24 Hence, the newly designed visible light photocatalytic material Ag2S–ZnS loaded on cellulose was synthesized by the precipitation method used for RhB dye degradation.
Materials and methods
Materials
All chemicals used in this study such as rhodamine B dye, zinc acetate, silver nitrate, and ammonia were of AR grade and purchased from Hi Media, Mumbai, India.
Extraction of cellulose from coconut spathe
As-received coconut spathe (CS) biomass was dried and crushed to an average particle size of 0.4 mm using a miller. The material was subject to dewaxing by refluxing with toluene–ethanol (1
:
1, v/v) for 2 h in a Soxhlet apparatus. After the extraction, the biomass was washed with ethanol and dried in an oven at 45 °C for 24 h. The extractive and lignin-free biomass was used to extract cellulose using the following procedure. 2 g of dried extractive biomass was taken in a dried 250 mL flask, and to this was added 10 mL of 17.5% NaOH solution. The flask was covered with a lid, kept in a water bath at 20 °C and the contents were stirred occasionally. Further, to this solution mixture, 5 mL of 17.5% NaOH solution was added after a gap of 5 min in three steps and the contents of the flask were left for 30 min after adding 33 mL of water to attain the required temperature. The solution mixture was filtered through a fritted glass filter and washed with 100 mL of 8.3% NaOH solution to get cellulose (CE). Further, it was treated with 15 mL of 10% acetic acid to remove trace amounts of NaOH. The final material was washed with distilled water, and the material was dried at 60 °C for about 10 h and stored in an air-tight container for further use.25
Preparation of the AZCE photocatalytic material
To prepare AZCE, 50 mL of zinc acetate dihydrate (0.1 M) and silver nitrate (0.1 M) were added to a 40 mL solution containing extracted CE (1.5 g), urea (4 g), thiourea (3.25 g), and sodium hydroxide (4 g). The suspension was stirred for 10 h for completion of the reaction. The obtained product (AZCE) was washed several times with deionized water to remove the impurities and the product was dried in a hot air oven at 100 °C for 6 h. For comparison purposes, ACE and ZCE composites were prepared using a similar method as mentioned above.26
Characterization
The crystalline structures of the prepared materials were examined using PXRD with Cu Kα radiation (λ = 1.5406 Å). The morphology of the samples was characterized using a FEI XL30 FESEM and a high-resolution transmission electron microscope (HRTEM) (JEOL JEM 2100). The specific surface area of the sample was determined using a Quantachrome instrument. Fourier transform infrared spectroscopy (FTIR) spectra were recorded in the range of 4000–400 cm−1 using a Nicolet 380 FT-IR spectrometer. The optical properties of the prepared samples were analysed using a JASCO-630 diffuse reflectance spectrophotometer. Photocatalytic dye degradation under UV was done using a Heber 500 W tungsten halogen lamp. The dye degradation progress was carried out using a JASCO-730 UV-vis spectrophotometer. Shimadzu HPLC was equipped with a UV-vis diode array detector using a C18 column (4.6 mm × 250 mm) in the reverse phase mode. HPLC separation was carried out using a mixed eluent (CH3CN
:
H2O = 1
:
1 v/v, H3PO4 = 50 mM, pH = 3.5, λ = 554 nm) at a flow rate of 1 mL min−1. The degraded end products of RhB identified using HPLC and TOC contents were measured using a total organic carbon analyzer (Liquid TOC, Elementar, Germany), respectively. Finally, the degradation pathway of RhB dye mass spectral fragmentation was studied using time of flight (TOF) performed on a Water Q-TOF micro Y A-260 (Micromass).
Photocatalytic activity
The photocatalytic efficiency of the prepared samples were assessed by the degradation of RhB using a photoreactor instrument as shown in Fig. S1.† It consists of a borosilicate glass immersion vessel containing a 500 W tungsten halogen bulb covered with a water jacket for water circulation to avoid heat generated from the light source. The reaction temperature was maintained throughout the reaction at 27 °C. The light source was kept at the centre, the reaction vessels were placed surrounding the light source and the total setup was covered with a metal outer jacket. In a typical experiment, the synthesized photocatalyst (30 mg) was suspended in a 100 mL capacity glass tube containing 50 mL of RhB solution (10 to100 ppm) and kept in dark for 30 min to confirm good adsorption of the dye on a photocatalytic material prior to the photocatalytic experiment. Air was bubbled into the reactor for maintaining effective mixing of the catalyst and the dye solution. At every 30 min interval, 2 mL of the solution was withdrawn and filtered using a PTFE syringe filter (0.45 μm) to eliminate the impurities. The adsorption–desorption experiment of the prepared nanocomposites were also carried out without light irradiation by the same method as stated above. The concentrations of the dye samples were analysed using a UV-vis spectrophotometer (JASCO 730) at λmax 554 nm. Prior to analysis, a calibration curve was obtained and it was reproducible over the concentration range used in this work. The characteristic absorption peak of RhB at 554 nm was used to evaluate the level of degradation and the degradation efficiency of the photocatalyst was calculated using eqn (1)27,28 as follows: |  | (1) |
where C0 and Ct are the initial dye concentration and the concentration at time t, respectively.
Identification of intermediates
The pathway of degradation and the intermediates formed during the degradation process were analyzed using electrospray ionization mass spectra (ESI-MS) experiments performed on a Water Q-TOF micro Y A-260 (Micromass) tandem quadruple orthogonal TOF instrument, fitted with a lock spray source. During the degradation process, the reaction samples were collected at regular intervals and filtered using a PTFE syringe filter. The obtained solutions were extracted with dichloromethane (DCM). The extracted solution was vacuum dried using a rotary evaporator. The obtained dried samples were dispersed in GC grade methanol and were used for further analysis.
Results and discussion
Powdered XRD analysis
The structure and crystallinity of cellulose and the prepared nanocomposites were confirmed using an XRD pattern. As seen in Fig. 1, the diffraction peaks of all the prepared samples are broader in nature. It shows that the particle size is in the nanoscale range. The XRD pattern of cellulose clearly exhibits typical diffraction peaks at (2θ) 17° and 22° that belong to the crystalline structure of cellulose. The diffractive peaks marked with black stars indicate the formation of Ag2S (JCPDS Card No. 14-0072), and those marked with red diamond-shaped symbols were assigned to the cubic phase of ZnS (JCPDS No. 79-0043). The particle size is estimated by considering the full width half-maximum (FWHM) of the XRD peaks using the Debye–Scherrer formula.29–31 The measured particle sizes are 10 nm (Ag2S), 8 nm (ZnS) and 15–20 nm (cellulose), respectively. Since the cellulose particle size is greater than that of the Ag2S/ZnS particle size, it is expected that these particles are present on the cellulose surface and this confirms the formation of the nanocomposite.
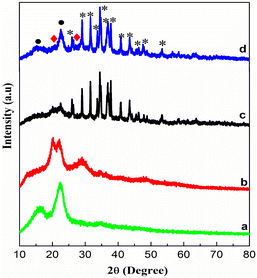 |
| Fig. 1 XRD patterns of (a) CE, (b) ZCE, (c) ACE and (d) AZCE. | |
FTIR analysis
FTIR spectra of cellulose and nanocomposites of sulphides of silver and zinc were analysed in the wavelength range of 4000–400 cm−1 as shown in Fig. S2.† The strong and broad absorption peaks located at 3307 cm−1 and 1163 cm−1 in the spectrum of CE and its composites were attributed to the O–H and C–O–C stretching vibrations. The spectral bands appeared at 2891 cm−1 for C–H symmetrical stretching, and the bands at 1642 cm−1 and 1439 cm−1 were assigned to the characteristic stretching vibration of >C
O, H–O–C, and H–O–H bending of absorbed water and H–C–H and O–H bending vibration, respectively. The bands at 1311 cm−1 and 1360 cm−1 were assigned to the C–C, C–O and –CH, –COO vibrations, and the peak at 662 cm−1 was assigned to the C–OH vibration. However, compared with CE, the intensities of several peaks corresponding to oxygen-containing functional groups are decreased in the composite material due to the strong electrostatic linkage of Ag2S and ZnS nanomaterials with the functional groups of CE.
UV-DRS analysis
The optical properties of ACE, ZCE and AZCE nanocomposites were investigated using UV-DRS as shown in Fig. 2. The bandgaps of the prepared samples were assessed using the Kubelka–Munk equation by plotting the graph of (αhυ)2vs. hυ, where α is the absorption coefficient and hυ is the photon energy (eV) as shown in Fig. 2. This shows that ZCE exhibits an absorption peak in the UV region while ACE exhibits a broader peak in the visible region. However, AZCE shows an absorption peak in the visible region similar to ACE. The intercept of the tangent to the X-axis will provide the band gap energies of the ACE, ZCE and AZCE materials, which are measured to be 1.15 eV, 3.46 eV and 1.3 eV, respectively. It shows that the AZCE sample absorbs a large amount of light in the visible region due to reduction in the band gap of ZnS.
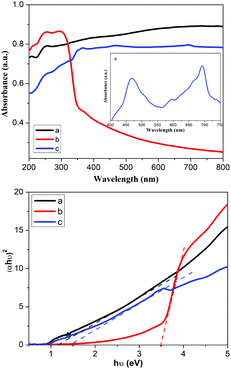 |
| Fig. 2 UV-DRS spectra and the Kubelka–Munk plots of (a) ACE, (b) ZCE, and (c) AZCE. | |
N2 adsorption–desorption study
The N2 adsorption–desorption isotherm of AZCE is type IV according to the IUPAC classification as shown in Fig. S3.† The BET surface area of the AZCE composite was calculated to be 11.62 m2 g−1. The pore volume calculated using the BJH method was found to be 0.00117 cm3 g−1, and the pore size distribution was calculated using DFT and it was found to be 1.5–40 nm. BET data reveal that AZCE having a sufficient surface area and a bigger pore volume are beneficial for the enhancement of photocatalytic performance.
SEM and TEM analysis
As seen in Fig. 3, the FE-SEM image of CE shows that it has a long fibre and a rough surface, which are sufficient to hold photocatalytic materials. The data of electron diffraction studies (EDS) show that it contains only carbon and oxygen and there are no other elements. Further, the FE-SEM image of AZCE composites clearly shows the Ag2S–ZnS distributed on the surface of the CE fibre and EDS shows the presence of C, O, S, Ag and Zn elements and that there are no other elements present. The weight ratio of Ag2S and ZnS in AZCE was found to be 18% and 8%, respectively, and the remaining weight is contributed from the cellulose constituents. The microstructure of the AZCE was further characterized by TEM as shown in Fig. 4. It shows that Ag2S–ZnS nanoparticles are distributed uniformly and also embedded on the surface of CE fibre. The average diameter of the metal sulphide nanoparticle is in the range of 6–10 nm, while the width of cellulose is 15 nm. Further, the SAED shows clear and organized circular spots that exhibit the highly crystalline nature of metal sulphide on CE.32
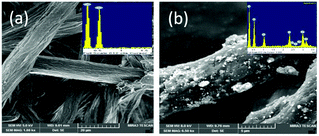 |
| Fig. 3 SEM images and EDS spectra of (a) CE and (b) AZCE. | |
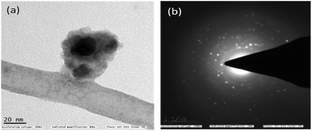 |
| Fig. 4 TEM images of (a) AZCE and (b) SAED image of AZCE. | |
Photocatalytic performance
The activities of the photocatalysts were evaluated for the degradation of RhB dye in the presence and absence of the simulated visible light. As seen in Fig. 5b, in the absence of AZCE, no degradation was observed even after equilibrating for about 150 min; in contrast, in the presence of the AZCE, nearly 98% dye abatement was achieved after exposure to 150 min. But in the absence of visible light, AZCE did not cause any degradation of the dye. The above observation shows that both the visible light source and AZCE are desirable for effective degradation of RhB dye. In order to know the dye degradation effects of ACE and ZCE, similar experiments were carried out and the results reveal that ACE degraded RhB dye to an extent of 28%, while ZCE degraded to only 15%. This is due to the lower amount of visible light absorbed by the photocatalyst. The absorption spectra of the RhB dye solution exposed to visible light for different time periods in the presence of the photocatalyst are recorded as shown in Fig. 5a. The absorption peak at 554 nm decreases rapidly with the visible light exposure time and almost disappears after 150 min. Several new absorption bands appear in the near UV region with a low absorption coefficient due to the formation of the low molecular weight organic intermediates.
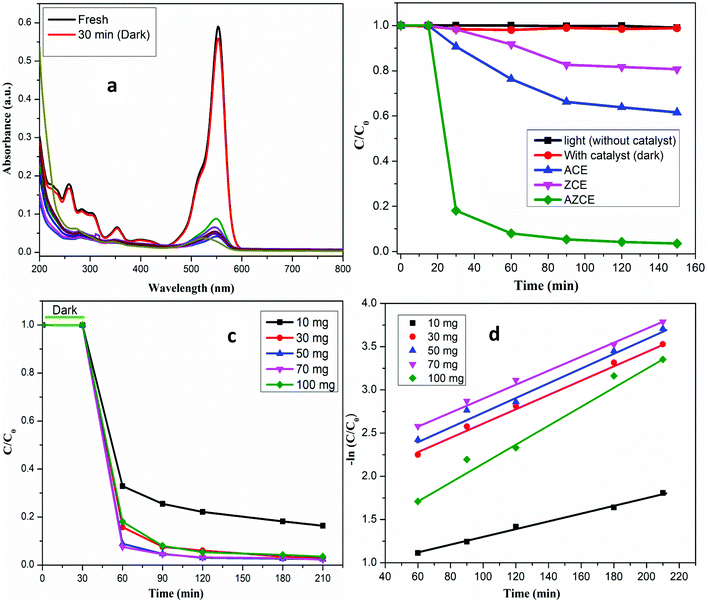 |
| Fig. 5 (a) UV-Vis spectra of RhB dye degradation using AZCE. (b) Photocatalytic catalyst performance regarding RhB dye degradation using ACE, ZCE and AZCE. (c) Photocatalyst performance at different doses of AZCE regarding RhB dye degradation. (d) A first-order kinetics of AZCE. | |
Effect of catalyst dose
To find out an optimum dose of the catalyst for maximum photocatalytic degradation, the catalyst amount was varied from 10 to 100 mg L−1 and the concentration of RhB (30 ppm) was kept constant as shown in Fig. 5c. The results show that the degradation of RhB dye increases by increasing the amount of catalyst from 10 to 50 mg and above 70 mg catalyst dose, the degradation performance remains the same and at 100 mg catalytic dose, the degradation rate shows a decreasing trend. This may be due to the increase in the scattering of light and screening effect, resulting in the decrease in the catalytic performance.33,34 The obtained results suggested that the minimal amount of the catalyst (30 mg) is enough for a maximum degradation rate and reducing the contaminant.
Effect of pH
It is important to perform the degradation of dyes at different pH values because the effluents of various industries have different pH values.35 The pH of the dye solution was varied from 2 to 12 by fixing the RhB dye concentration (30 ppm) and catalyst amount (30 mg) as shown in Fig. S4.† The pH was adjusted by the addition of 0.1 N HCl or NaOH. At pH 2, the photodegradation of the dye was retarded by the high concentration of protons, resulting in the decrease in the degradation, while the degradation efficiency was increased in the pH range 4–12. However, the maximum degradation occurred at pH 6.
Effect of H2O2
To enhance the photocatalytic degradation of the dye, the reactions were carried out in the presence of hydrogen peroxide (H2O2) to enhance the hydroxyl radical species and thereby the photocatalytic reaction can be accelerated.36 Hence, to study the effect of H2O2 on the degradation of RhB dye, H2O2 was added in the range of 1–5 mM by maintaining the RhB dye concentration (30 ppm) and catalyst amount (30 mg) during the experiment. As seen in Fig. S5,† the percentage degradation of RhB dye without the addition of H2O2 was 92% and after the addition of 1, 2, 3, 4 and 5 mM of H2O2, the degradation was found to be 72, 95, 95, 98 and 95% respectively. After adding 1 mM of H2O2, the degradation was reduced to 71%, and this may be due to the oxidation of H2O2 by ˙OH radicals and thereby a sufficient number of ˙OH radicals are not available for dye degradation. At a higher concentration of H2O2 (2–5 mM), a sufficient number of ˙OH radicals are produced, leading to the maximum degradation of the dye. Hence, 4 mM of H2O2 is required for the maximum degradation of the dye.
Kinetics
The photocatalytic degradation of the dye has been verified using first-order kinetics37 and the rate of the reaction was estimated using eqn (2). | ln C/C0 = kt | (2) |
where k is the first-order rate constant (min−1), t is the irradiation time (min), and C0 and C are the initial concentration and the concentration of the dye at regular time (t) intervals, respectively. The plot of ln(C/C0) against the irradiation time (t) is shown in Fig. 5d and the obtained data show that first-order kinetics was confirmed from the linearity of ln
C/C0vs. time. The rate constant was calculated from the intercept of the straight line and it was found to be 6.4 × 10−3 min for a 30 mg catalyst dose and dye concentration of 30 ppm.
Identification of intermediates generated during photocatalytic process using HPLC, TOC and mass analysis
To confirm the degradation of RhB dye, the photocatalytic degradation experiment was conducted by taking the RhB concentration of 30 ppm and AZCE dosage of 30 ppm irradiated and irradiating with visible light for a time period of 0–150 min. The irradiated samples were analysed by HPLC, TOC and mass analysis. As seen in Fig. 6, it clearly confirms that the HPLC chromatogram consists of six peaks with different retention times. Peak 1 indicates the presence of RhB at a retention time of 7.35 min without irradiation of light. After irradiation by a light source (30–150 min), peaks 2 to 6 are shifted towards lower retention times of 7, 6.8, 6.6, 6.2 and 5.6 min and these results show that there is a cleavage of RhB dye and there is formation of low molecular organic intermediates.
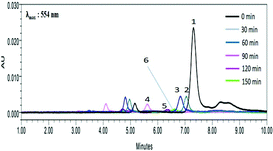 |
| Fig. 6 HPLC chromatogram for RhB dye degradation. | |
The TOC results show that there is 95% reduction of dye concentration after irradiation under visible light for 150 min. The residual 5% of TOC values could be within the permissible limit of the TOC level approved by WHO. In order to identify the intermediate products of RhB, GC-TOF-ESI/MS was used. The total ion chromatogram of the degradation products of RhB is shown in Fig. S6.† Fig. S7a† shows the degradation pattern of RhB at 0 min and exhibits a molecular ion peak at 443 assigned to RhB and no other peaks were observed; this shows that there is no degradation of dye during this period. The second spectrum shown in Fig. S7b† was recorded after an irradiation time of 60 min; the degradation pattern shows that the peaks appeared at 388, 359, 331, 301, 290, 282, 218, 109 and 101, which indicates that the dye molecule has undergone an N-deethylated cleavage leading to these many intermediate products. In Fig. S7c,† mass spectra were recorded after exposure to 120 min irradiation. After N-deethylation, RhB was degraded into several intermediates with cleavage of the C
N, which is responsible for the formation of several aromatic intermediates shows molecular ion peak at 101, 127, 129, and 145. Hence, according to UV-visible spectral analysis, HPLC, TOC and mass spectral analyses show that the RhB dye has undergone degradation into several low molecular weight organic intermediate products as shown in Fig. S6.†
Photocatalytic mechanism
The photocatalytic performance of AZCE was attributed to the superior separation efficiency of the generated electrons and holes through electronic interactions between Ag2S and ZnS.38 In particular, for AZCE, the conduction band of Ag2S was less negative than that of ZnS. Hence, under visible light irradiation, electrons are easily transferred to Ag2S from the conduction band of ZnS, where the generated holes gather in the valence band of ZnS as shown in Fig. 7. The simultaneous movement of electrons and holes in AZCE increases the yield and lifetime of the photogenerated carriers, such as hydroxyl radicals (˙OH) and superoxide radical anions (O2−), by separating the electron–hole pairs.39 These generated reactive oxygen species react with the adsorbed RhB dye molecules and oxidise into small molecules, which enhances the photodegradation performance. It is confirmed by analysis through UV-Vis spectra that the absorption peak intensity at 554 nm decreased suddenly after 30 min of visible light irradiation as shown in Fig. 5a. The absorbance peak decreased to the maximum extent when AZCE was used, and the colour of the solution transformed from dark pink to almost colourless. The enhanced photodegradation performance of AZCE was mainly due to the band conjunctions of Ag2S and ZnS contributing to charge separation and transport; and the recombination of the photogenerated electron–hole pairs decreases due to the synergic effects of Ag2S and ZnS.40,41 Besides, the alkali pre-treated cellulose provides activated surface hydroxyl groups to enhance the deposition efficiency of Ag2S due to which a large amount of visible light can be absorbed and the photocatalytic activity is increased.
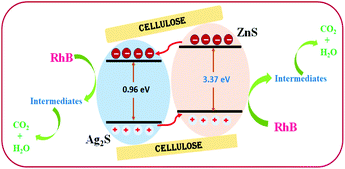 |
| Fig. 7 Schematic representation of a AZCE photocatalyst material in RhB dye degradation. | |
The assessment of AZCE compared with previously reported photocatalysis is shown in Table 1. It shows that AZCE has been found to be a potent material for the degradation of RhB in a short period of time. In photocatalytic degradation processes, recycling or reuse of catalysts is one of the important criteria. In our study, AZCE is repeatedly used four times, and it shows good efficiency for the degradation of RhB dye up to 98%; in the fifth cycle, the degradation efficiency was reduced to 94%. This shows that AZCE can be repeatedly used for the degradation process and it maintains the stability of the composite.
Table 1 Assessment of the present work compared with the previously reported work
Photocatalyst |
Dose (mg L−1) |
Dye used |
Dye conc. (mg L−1) |
Time taken (min) |
Efficiency (%) |
RGO-ZnS21 |
500 |
DB53 |
40 |
90 |
97.1 |
ZnO-Ag2S23 |
250 |
MB |
10 |
60 |
90.5 |
Gr/ZnS-Ag2S34 |
1000 |
RhB |
10 |
120 |
98.0 |
CNT/Ag2S-TiO2 41 |
300 |
RhB |
30 |
150 |
84.0 |
AZCE
|
300 |
RhB |
60 |
90 |
98.0 |
Conclusion
In the present work, visible-light-active nanosized AZCE was synthesized by the precipitation method. The oxidation data indicate that the dye can be most effectively oxidized at a pH of greater than 4, at a dye concentration of 30 mg L−1 and a catalyst concentration of 30 mg. The AZCE catalysed oxidation of the RhB dye follows first-order kinetics and a rate constant value of 6.4 × 10−3 min−1. Various organic intermediates were identified by high performance liquid chromatography (HPLC), total organic content (TOC) and electron-spray ionization-mass spectrometric (ESI-MS) studies during the photodegradation process of the RhB dye. The catalyst can be reused four times without any divergence in the degradation process.
Conflicts of interest
There are no conflicts to declare.
Acknowledgements
The authors would like to thank the Chancellor, VIT Vellore, India for providing research facilities. The authors are thankful to Water Initiative Technology, Department of Science and Technology (Government of India) for supporting financial support vide project number No. DST/TM/WTI/2K12/61(G).
References
- Y. Zhang, C. Liu, G. Zhu, X. Huang, W. Liu and W. Hu, RSC Adv., 2017, 7, 48176–48183 RSC.
- M. Pang, J. Hu and H. C. Zeng, J. Am. Chem. Soc., 2010, 132, 10771–10785 CrossRef CAS PubMed.
- X. Ma, Y. Zhao, X. Jiang, W. Liu, S. Liu and Z. Tang, ChemPhysChem, 2012, 13, 2531–2535 CrossRef CAS PubMed.
- R. Zamiri, H. A. Ahangar, D. M. Tobaldi, A. Rebelo, M. P. Seabra, M. Shabani and J. M. F. Ferreira, Phys. Chem. Chem. Phys., 2014, 16, 22418–22425 RSC.
- D. Bhatia, N. R. Sharma, J. Singh and R. S. Kanwar, Crit. Rev. Environ. Sci. Technol., 2017, 47(19), 1836–1876 CrossRef CAS.
- P. V. Nidheesh and R. Rajan, RSC Adv., 2016, 6, 5330–5340 RSC.
- M. A. Brown and S. C. De Vito, Crit. Rev. Environ. Sci. Technol., 2009, 249–324 Search PubMed.
- N. Puvaneswari, J. Muthukrishnan and P. Gunasekaran, Indian J. Exp. Biol., 2006, 44, 618–626 CAS.
- W. Deng, H. Zhao, F. Pan, X. Feng, B. Jung, A. Abdel-wahab, B. Batchelor and Y. Li, Environ. Sci. Technol., 2017, 51, 13372–13379 CrossRef CAS PubMed.
- W. Y. Teoh, J. A. Scott and R. Amal, J. Phys. Chem. Lett., 2012, 3, 629–639 CrossRef CAS PubMed.
- M. R. Hoffmann, S. T. Martin, W. Choi and D. W. Bahnemannt, Chem. Rev., 1995, 95, 69–96 CrossRef CAS.
- M. A. Fox and M. T. Dulay, Chem. Rev., 1995, 93, 341–357 CrossRef.
- A. Fujishima and K. Honda, Nature, 1972, 238, 37–38 CrossRef CAS PubMed.
- C. Lin, M. Zhu, T. Zhang, Y. Liu, Y. Lv, X. Li and M. Liu, RSC Adv., 2017, 7, 12255–12264 RSC.
- S. Wang, Q. Ma, H. Liu, K. Wang and L. Ling, RSC Adv., 2015, 5, 40521–40530 RSC.
- N. E. Kochkina, A. V. Agafonov, A. V. Vinogradov, N. S. Karasev, N. L. Ovchinnikov and M. F. Butman, ACS Sustainable Chem. Eng., 2017, 5, 5148–5155 CrossRef CAS.
- R. Li, M. He, T. Li and L. Zhang, Carbohydr. Polym., 2015, 115, 269–275 CrossRef CAS PubMed.
- Y. Zhang, N. Zhang, Z. Tang and Y. Xu, ACS Nano, 2012, 6, 9777–9789 CrossRef CAS PubMed.
- T. Kato, Y. Hakari, S. Ikeda, Q. Jia, A. Iwase and A. Kudo, J. Phys. Chem. Lett., 2015, 6, 1042–1047 CrossRef CAS PubMed.
- S. Dutta, S. Chatterjee, I. Mukherjee, R. Saha and B. P. Singh, Ind. Eng. Chem. Res., 2017, 56, 4768–4778 CrossRef CAS.
- P. Wu, J. Yu, H. Chao and J. Chang, Chem. Mater., 2014, 26, 3485–3494 CrossRef CAS.
- S. Khanchandani, P. K. Srivastava, S. Kumar, S. Ghosh and A. K. Ganguli, Inorg. Chem., 2014, 53, 8912–8902 CrossRef PubMed.
- W. Jiang, Z. Wu, X. Yue, S. Yuan, H. Lu and B. Liang, RSC Adv., 2015, 5, 24064–24071 RSC.
- B. Subash, B. Krishnakumar, M. Swaminathan and M. Shanthi, Powder Technol., 2013, 241, 49–59 CrossRef CAS.
-
R. M. Rowell, Chemical modification of wood, in Handbook of wood chemistry & wood composite, ed. R. M. Rowell, Taylor & Francis, CRC Press, 2005, pp. 381–420 Search PubMed.
- H. Jin, C. Zha and L. Gu, Carbohydr. Res., 2007, 342, 851–858 CrossRef CAS PubMed.
- L. Yang, X. Guan, G. Wang, X. Guan and B. Jia, New J. Chem., 2017, 41, 5732–5744 RSC.
- S. C. Yan, Z. S. Li and Z. G. Zou, Langmuir, 2010, 26, 3894–3901 CrossRef CAS PubMed.
- C. Zhang, R. Z. Zhang, Y. Q. Ma, W. B. Guan, X. L. Wu, X. Liu, H. Li, Y. L. Du and C. P. Pan, ACS Sustainable Chem. Eng., 2015, 3, 396–405 CrossRef CAS.
- S. Bai, X. Shen, G. Zhu and H. Zhou, Eur. J. Inorg. Chem., 2013, 256–262 CrossRef CAS.
- D. A. Reddy, R. Ma, M. Yong and T. Kyu, Appl. Surf. Sci., 2015, 324, 725–735 CrossRef.
- X. Yang, H. Xue, J. Xu, X. Huang, J. Zhang, Y. Tang, T. Ng, H. Kwong, X. Meng and C. Lee, ACS Appl. Mater. Interfaces, 2014, 6, 9078–9084 CrossRef CAS PubMed.
- J. Herrmann, Catal. Today, 1999, 53, 115–129 CrossRef CAS.
- A. Akyol, H. C. Yatmaz and M. Bayramoglu, Appl. Catal., B, 2004, 54, 19–24 CrossRef CAS.
- Y. Wang, Water. Res., 2000, 34, 990–994 CrossRef CAS.
- D. Tseng, L. Juang and H. Huang, Int. J. Photoenergy, 2012, 2012, 1–9 Search PubMed.
- M. Lan, G. Fan, L. Yang and F. Li, Ind. Eng. Chem. Res., 2014, 53, 12943–12952 CrossRef CAS.
- H. Zhang, B. Wei, L. Zhu, J. Yu, W. Sun and L. Xu, Appl. Surf. Sci., 2013, 270, 133–138 CrossRef CAS.
- W. He, H. Jia, D. Yang, P. Xiao, X. Fan, Z. Zheng and H. Kim, ACS Appl. Mater. Interfaces, 2015, 7, 16440–16449 CrossRef CAS PubMed.
- S. Shen and Q. Wang, Chem. Mater., 2013, 25, 1166–1178 CrossRef CAS.
- T. R. Mandlimath, A. Moliya and K. I. Sathiyanarayanan, Appl. Catal., A, 2016, 519, 34–47 CrossRef CAS.
Footnote |
† Electronic supplementary information (ESI) available. See DOI: 10.1039/c8pp00330k |
|
This journal is © The Royal Society of Chemistry and Owner Societies 2019 |
Click here to see how this site uses Cookies. View our privacy policy here.