DOI:
10.1039/C8RA09615E
(Paper)
RSC Adv., 2019,
9, 4583-4590
Simultaneous immobilization of NH4+ and Mn2+ from electrolytic manganese residue using phosphate and magnesium sources
Received
22nd November 2018
, Accepted 16th January 2019
First published on 6th February 2019
1. Introduction
Electrolytic manganese residue (EMR) is an industrial waste product from electrolytic metal manganese (EMM) plants which is discharged from the process of sulfuric acid leaching of manganese carbonate, neutralization of ammonia and the pressure filtration treatment of mineral pulp. Currently, about 10–12 metric tons of EMR are derived from each EMM plant for every metric ton of EMM produced.1 In China, these EMM plants discharge up to 10 million tons of EMR into the environment each year and the accumulated amount is over 60 million tons during the past few years.1,2 As the grade of manganese carbonate ore falls, the amount of EMR discharged increases further for the production of every metric ton of EMM, which causes further environmental and human health problems. At present, owing to the shortage of reutilization techniques for EMR, it is primarily transported to the stockyard for stacking without undergoing any preprocessing.3,4 There is a great quantity of heavy metal ions from the raw ore and NH4+ from the neutralization process of EMM in EMR products. In addition, EMR possesses the following characteristics, fineness, high humidity, viscosity and toxicity.5 These characteristics cause serious threat to the surrounding environment and the surface and ground water. It is crucial to exploit reusability technology and find harmless disposal methods for EMR.
Some research has been previously conducted on the reuse of EMR, including preparation of adsorbents,6,7 photocatalytic materials8 and soil fertilizers,9 production of fillers for sulfur cement concrete,2 granulated blast furnace slag cement,10 steam-autoclaved bricks,11,12 road beds13 and quasi-sulphoaluminate cementitious materials,14 the recovery of valuable metals1 and so on. Owing to the reduced amount of EMR added, and the process instability and high cost, few studies have reported the industrial utilization of EMR. To date, the harmless disposal of EMR has remained the main focus, before the stacking and reuse of EMR. Some compounds, such as quicklime, carbonates, phosphates, caustic magnesia,15 sodium hydroxide,16 carbon dioxide3 and so forth, were used to immobilize the heavy metal ions in EMR, although with less consideration of the NH4+ in EMR.
Owing to operational simplicity, low cost, the availability in large amounts and the ability to treat pollutants in a large scale operation, stabilization/solidification technology has been extensively applied to the harmless disposal of various pollutants.17 Solidification or immobilization prompts a reduction in the potential hazards from the waste by converting the contaminants into their least soluble, mobile or toxic form and also imparts some strength to the waste, which is favorable for their utilization or stacking. Ammonium from the leachate is removed by forming a struvite precipitation with phosphate and magnesium sources of magnesite,18 MgO19 and MgCl2·6H2O,20 and heavy metal ions from soil21 and waste ash22 are immobilized by the phosphate. The objective of this study was to propose a novel and low cost method for the immobilization of NH4+ and heavy metal ions from EMR. The optimum reaction conditions, characteristics of immobilization, mechanism and the economy of alternative chemicals are discussed and determined. The results of this study results are conducive to harmless disposal, prior to the stacking and reuse of EMR.
2. Materials and methods
2.1 Materials
EMR was collected from a residue storage facility at an EMM plant in Chongqing, China. Before immobilization, the residue sample was dried to a constant weight at 80 °C. The dried residue sample was ground using a ball mill and sieved using a screen with a 180 μm bore diameter for all experiments. The chemicals used were of analytical grade, CaO, MgSO4·7H2O, MgO,Na3PO4·12H2O and so forth, and deionized water was used in the process of contaminant immobilization.
2.2 Immobilization process for contaminants
A series of experiments were conducted at room temperature using a convoluted shaking table. Each trial was run in triplicate for statistical accuracy, and the trial data were averaged for reporting. The treated sample was poured from the reactor at a specified time and air pump filtration was used to collect the leach liquor for further analyses. Contaminants of EMR were immobilized using Na3PO4·12H2O and MgSO4·7H2O (or PS, for short) agents, as well as Na3PO4·12H2O and MgO (or PO, for short) agents. CaO was used to increase the alkalinity of the EMR slurry. A 10 g residue sample was used and the water
:
EMR mass ratio was 4
:
1 in each trial. The effect of different Mg
:
NH4+ (1
:
1–4
:
1) and P
:
NH4+ (0.5
:
1–2
:
1) molar ratios, the dose of added CaO (0–1 g) and the reaction time (0.5–4 h) were evaluated. The P concentration and the pH of the treated EMR slurry were examined. In addition, the immobilization efficiencies of NH4+ and Mn2+ at specified times, the concentrations of contaminants and the economic analysis under the optimum conditions were measured. The immobilization efficiencies of NH4+ (η) and Mn2+ (ζ) were defined respectively using eqn (1) and (2). |
η = (m − mt)/m × 100%
| (1) |
|
ζ = (n − nt)/n × 100%
| (2) |
In which m and mt are the NH4+ mass (mg) in the raw EMR and the leach liquor of the treated EMR at the specified time, respectively. Both n and nt are the Mn2+ mass (mg) in the raw EMR and the leach liquor of the treated EMR at the specified time, respectively.
2.3 Characterization
The pH of the EMR slurry was measured using a pH meter (pHS-25, INESA, China). The chemical compositions of the raw EMR samples were determined using an X-ray fluorescence (XRF) spectrometer (XRF-1800, Shimazu, Japan). The phase compositions and the morphology characteristics of the raw EMR and the treated EMR were analyzed using an X-ray diffractometer (XRD) technique (X'Pert PRO, Panalytical, Holland), a scanning electron microscopy (SEM) and an energy dispersive X-ray spectroscopy system (EDS) (∑IGMA+X-Max20, Zeiss, Germany). The concentration of Mn2+ and other metal ions in the leach liquor were measured using a flame atomic absorption spectrophotometer (180-80, Hitachi, Japan). The concentrations of NH4+ and P were measured by a UV-vis spectrometer (UV-8000S, Shanghai Metash, China) at wavelengths of 420 nm and 700 nm, respectively.
3. Results and discussion
3.1 Characterization of raw EMR
The major chemical compositions of the raw EMR determined using X-ray fluorescence analysis are shown in Table 1, amounting to 98.2% of the total amount of the sample. Fig. 1 shows that the crystalline phases of the raw EMR mainly included MnSO4·H2O, (NH4)2SO4, (NH4)2Mn(SO4)2·6H2O, (NH4)2Mg(SO4)2·6H2O, CaSO4·2H2O, SiO2 and so forth. The compounds of NH4+ and Mn2+ were easily dissolved in water. In Fig. 2, the SEM image indicates that the regular cylindrical particles and the irregular shaped particles are overlapped randomly and loosely. A leaching experiment of the raw EMR was conducted with a water
:
EMR mass ratio of 4
:
1 and an 8 h mixing time. The results (shown in Table 2) stated that the concentrations of NH4+ and Mn2+ were 1264 mg L−1 and 3518 mg L−1 respectively and that trace amounts of the heavy metal ions were detected, of which the concentrations were at low levels. Thus, the main contaminants of the EMR sample were NH4+ and Mn2+.15
Table 1 Chemical compositions of raw EMR
Element |
Content (%) |
Element |
Content (%) |
O |
47.39 |
Mn |
2.35 |
Si |
15.32 |
Mg |
1.83 |
S |
13.05 |
Na |
0.61 |
Ca |
9.26 |
Ti |
0.34 |
Al |
4.14 |
Sr |
0.04 |
Fe |
3.89 |
Zn |
0.01 |
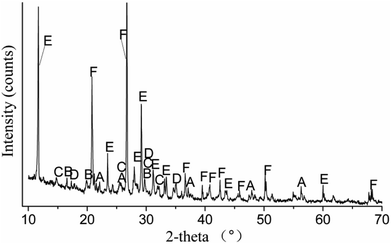 |
| Fig. 1 X-ray diffraction patterns for raw EMR (A – MnSO4·H2O, B – (NH4)2SO4, C – (NH4)2Mn(SO4)2·6H2O, D – (NH4)2Mg(SO4)2·6H2O, E – CaSO4·2H2O, F – SiO2). | |
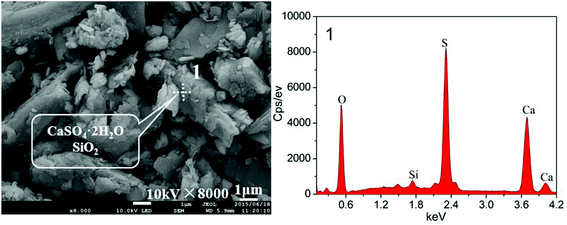 |
| Fig. 2 An SEM micrograph of the raw EMR. | |
Table 2 Leaching compositions of EMR
Parameter |
Concentration (mg L−1) |
Parameter |
Concentration (mg L−1) |
Raw EMR |
PS agents |
PO agents |
Raw EMR |
PS agents |
PO agents |
NH4+ |
1264 |
98 |
207 |
Zn2+ |
2.2 |
0.21 |
0.36 |
Mn2+ |
3518 |
1.3 |
0.7 |
Cu2+ |
0.6 |
0.16 |
0.08 |
Ca2+ |
966 |
1977 |
1286 |
Co2+ |
0.3 |
0.11 |
0.10 |
Mg2+ |
263 |
517 |
181 |
Pb2+ |
0.13 |
0.05 |
0.07 |
K+ |
132 |
213 |
174 |
Cd2+ |
0.06 |
0.03 |
— |
3.2 Effect of the different molar ratios of the immobilizing agents
Immobilization of NH4+ and Mn2+ from EMR was carried out using PS agents and PO agents respectively, under the conditions of a 10 g residue sample, 0.3 g mass of CaO, and a 1 h reaction time. Fig. 3a shows that the efficiency of NH4+ immobilization increased from 46.9% to 93.5% and that the efficiency of Mn2+ immobilization increased from 98.3% to 99.9% as the molar ratio of Mg
:
NH4+ increased from 1
:
1 to 3
:
1 and the P
:
NH4+ molar ratio increased from 0.5
:
1 to 2
:
1 using PS agents. The efficiency of NH4+ and Mn2+ immobilization increased slightly when the molar ratio of Mg
:
NH4+ was greater than 1.5
:
1 and the molar ratio of P
:
NH4+ was over 1.5
:
1. In addition, as shown in Fig. 3b, the concentration of P from the leach liquor increased in proportion to the P
:
NH4+ molar ratio and was inversely proportional to the Mg
:
NH4+ molar ratio. The concentration of P was over 3.3 mg L−1 with a P
:
NH4+ molar ratio of 2
:
1, which implied that excess PO4− was insignificant to the immobilization of contaminants in EMR. To avoid secondary pollution, the molar ratio of P
:
NH4+ was kept lower than 2
:
1. By contrast, the optimum molar ratio of Mg
:
P
:
NH4+ should be 1.5
:
1.5
:
1 (i.e., MgSO4·7H2O
:
Na3PO4·12H2O
:
EMR mass ratio of 0.113
:
0.175
:
1) to allow immobilization efficiencies of 92.4% NH4+ and 99.9% Mn2+.
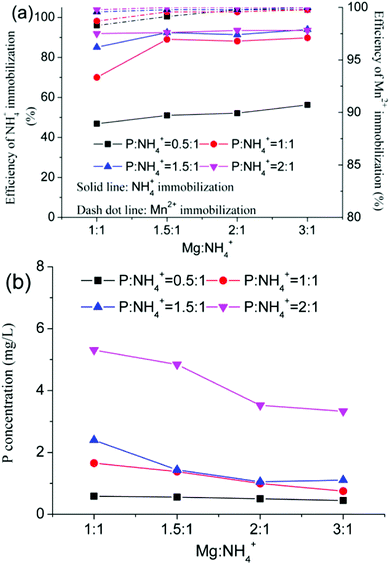 |
| Fig. 3 Immobilization of contaminants (a), and the change in the P concentration (b) using PS agents. | |
Fig. 4a shows the results of the immobilization of NH4+ and Mn2+ from EMR using PO agents under the following conditions: 10 g residue sample, 0.1 g CaO mass, and a 2 h reaction time. The efficiency of NH4+ immobilization increased from 79.4% to 86.7% with an increase of the Mg
:
NH4+ and P
:
NH4+ molar ratios. The immobilization efficiency of NH4+ with a P
:
NH4+ molar ratio of 2
:
1 increased slightly compared to that of a P
:
NH4+ molar ratio of 1.5
:
1 at the same Mg
:
NH4+ ratio. At Mg
:
NH4+ molar ratios of greater than 3
:
1, the efficiency of NH4+ immobilization was almost constant at an invariable P
:
NH4+ molar ratio. Additionally, Mn2+ was immobilized almost completely with a 1
:
1 P
:
NH4+ molar ratio. Thus, the optimum molar ratio of Mg
:
P
:
NH4+ was 3
:
1.5
:
1 (i.e., MgO
:
Na3PO4·12H2O
:
EMR mass ratio of 0.037
:
0.175
:
1), in which the immobilization efficiencies of NH4+ and Mn2+ were 83.5% and 99.9% respectively, with a P concentration of the leach liquor of under 0.5 mg L−1 (as shown in Fig. 4b).
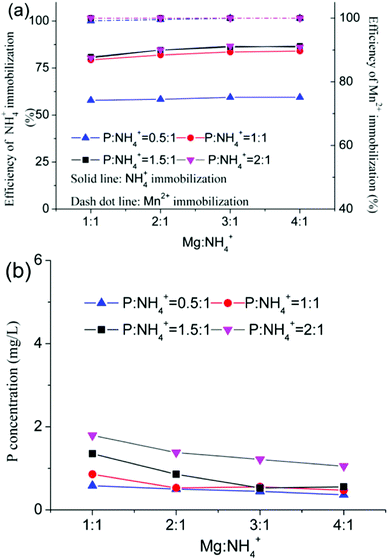 |
| Fig. 4 Immobilization of contaminants (a), and the change in the P concentration (b) using PO agents. | |
3.3 Effect of the dose of CaO and the reaction time
The immobilization of NH4+ and Mn2+ from EMR are influenced by the pH.15,23 To adjust the pH of the EMR slurry, different doses of CaO with PS agents or PO agents were added to the EMR samples.
Fig. 5a shows that the immobilization of NH4+ and Mn2+ were influenced by adding CaO using PS agents under the following conditions: 10 g residue sample, a water
:
EMR mass ratio of 4
:
1, and a Mg
:
P
:
NH4+ molar ratio of 1.5
:
1.5
:
1. The efficiency of the NH4+ immobilization firstly increased and decreased later with an increase in the dose of CaO within the same reaction time, the maximum value obtained was 92.4% over a 1 h reaction time. This was attributed to using the appropriate pH. As shown in Fig. 5b, the pH of the EMR slurry after completion of the reaction was raised as the dosage of the added CaO increased at the specified time. When the dose of added CaO was 0.3 g, the pH of the EMR slurry ranged from 9.66 to 9.13 with a reaction time from 0.5 to 4 h, which allowed the NH4+ to form deposits and to be immobilized. A higher pH resulted in the conversion of NH4+ into NH3 and allowed it to escape from the EMR, which could cause secondary pollution. Ahmet Gunay reported that the minimum solubility of struvite in a reaction product was observed in the range of pH 8.8–9.4.18 The efficiency of Mn2+ immobilization remained constant in general when the dose of added CaO was greater than 0.3 g and the reaction time was over 1 h. To summarize, the optimum conditions were 0.3 g of added CaO (i.e., CaO
:
EMR mass ratio of 0.03
:
1) and a 1 h reaction time using PS agents.
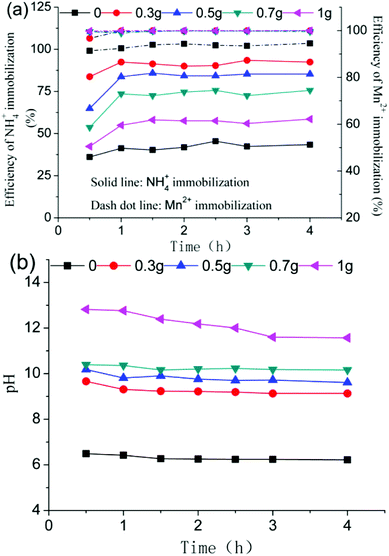 |
| Fig. 5 Immobilization of contaminants (a), and the pH change (b) at different doses of CaO using PS agents. | |
Fig. 6a shows that the immobilization of NH4+ and Mn2+ were influenced by the added CaO using PO agents at a Mg
:
P
:
NH4+ molar ratio of 3
:
1.5
:
1. The efficiency of the NH4+ immobilization first increased and then decreased as the dose of added CaO was increased at the same reaction time. The maximum efficiency was 83.5% when the amount of added CaO was 0.1 g and the reaction time was 2 h. Adding further CaO (>0.3 g) gave rise to a higher pH (as shown in Fig. 5b) and a lower efficiency of the immobilization of NH4+, which was due to higher pH of the slurry of EMR which was unfavorably to forming NH4+ deposits.24 As shown in Fig. 5a, the immobilization of Mn2+ was weakly influenced by the amount of added CaO. When the reaction time was greater than 1 h, the efficiency of the Mn2+ immobilization was 99.9%. Thus, the optimum conditions for the immobilization of NH4+ and Mn2+ using PO agents were less than 0.1 g of added CaO (i.e., an CaO
:
EMR mass ratio of 0.01
:
1), a 2 h reaction time, and a MgO
:
Na3PO4·12H2O
:
EMR mass ratio of 0.037
:
0.175
:
1. The Mg
:
NH4+ molar ratio when using PO agents was greater than those used for the PS agents to give the optimum conditions for the immobilization of the contaminants. This was due to the slow release of Mg2+ from MgO. The hydrolysis reaction of MgO released OH− and resulted in a reduced amount of CaO being added during the immobilization process when using PO agents compared with PS agents.
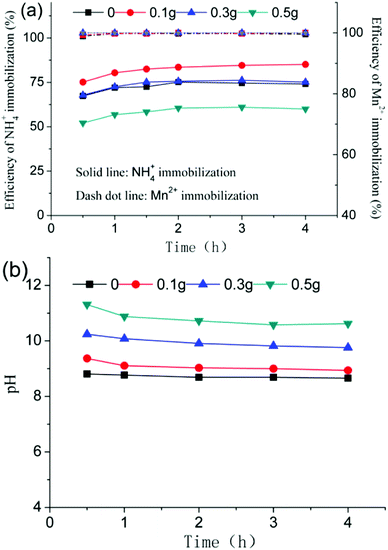 |
| Fig. 6 Immobilization of contaminants (a), and the pH change (b) at different doses of CaO using PO agents. | |
3.4 Analysis of the mechanism
The crystalline phases of the treated EMR samples using PS agents and PO agents were analyzed using XRD technology. As shown in Fig. 7a and b, the loss of the X-ray diffraction peaks for MnSO4·H2O, (NH4)2SO4, (NH4)2Mn(SO4)2·6H2O and (NH4)2Mg(SO4)2·6H2O was observed in the treated samples. The diffraction peaks for NH4MgPO4·6H2O, Mn5(PO4)2(OH)4, Mn(OH)2, Mn3(PO4)2·3H2O, Mg2(PO4)(OH), Mg(OH)2 and Ca3(PO4)2 were discovered in the treated samples. The peaks of SiO2 were detected both in the raw EMR (Fig. 1) and the treated samples, indicating that the compound could not be changed using immobilizing agents.
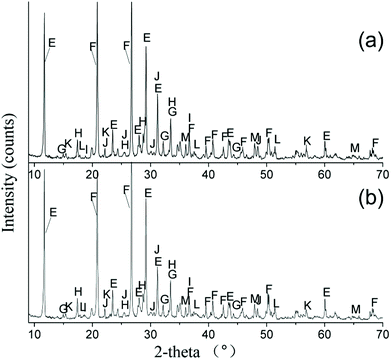 |
| Fig. 7 X-ray diffraction patterns of the treated EMR (E – CaSO4·2H2O, F – SiO2, G – NH4MgPO4·6H2O, H – Mn5(PO4)2(OH)4, I – Mn(OH)2, J – Mn3(PO4)2·3H2O, K – Mg2(PO4)(OH), L – Mg(OH)2, M – Ca3(PO4)2) using PS agents (a) and PO agents (b). | |
The SEM micrographs and EDS data for the point analysis of the treated EMR samples using PS and PO agents respectively are displayed in Fig. 8. The results demonstrated that the crystalline and amorphous phases overlapped and were linked to each other. The number of regular cylindrical particles from the treated EMR using PS and PO agents respectively declined obviously, compared to the raw EMR data shown in Fig. 2. This meant that the micro-morphology of CaSO4·2H2O could be changed by the immobilization reaction.25 EDS analysis determined that the formed phase of NH4MgPO4·6H2O was linked to NH4+ immobilization and the formed phase of Mn5(PO4)2(OH)4, Mn3(PO4)2·3H2O and Mn(OH)2 were linked to Mn2+ immobilization. The main equations for the reaction that used PO agents (eqn (3)–(10)) and those using PS agents (eqn (4)–(10)) are given below. Schematic illustrations of the proposed mechanisms of the PS and PO agents are shown in Fig. 9 and are based on the reaction equations.
|
MgO + H2O → Mg(OH)2 → Mg(OH)+ + OH− → Mg2+ + 2OH−
| (3) |
|
2Mg2+ + PO3−4 + OH− → Mg2PO4(OH)
| (4) |
|
CaO + H2O → Ca(OH)2 → Ca(OH)+ + OH− → Ca2+ + 2OH−
| (5) |
|
3Ca2+ + 2PO3−4 → Ca3(PO4)2
| (6) |
|
3Mn2+ + 2PO3−4 + 3H2O → Mn3(PO4)2·3H2O
| (7) |
|
5Mn2+ + 2PO3−4 + 4OH− → Mn5(PO4)2(OH)4
| (8) |
|
Mn2+ + 2OH− → Mn(OH)2
| (9) |
|
NH+4 + Mg2+ + PO3−4 + 6H2O → NH4MgPO4·6H2O
| (10) |
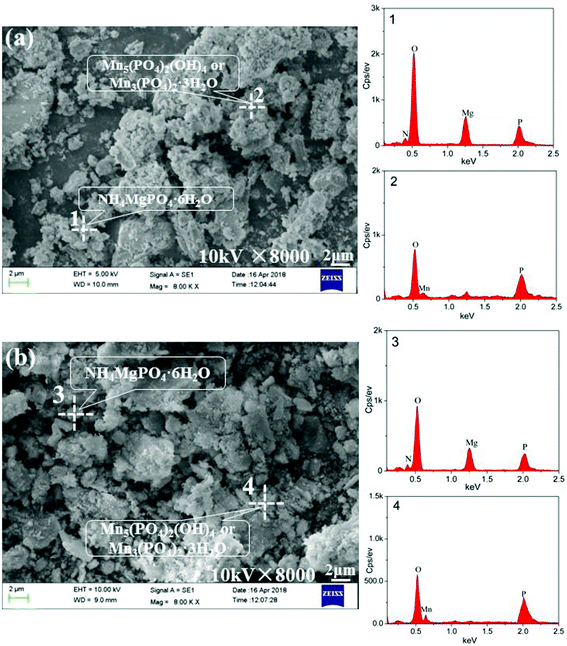 |
| Fig. 8 SEM micrographs of the treated EMR samples using PS agents (a) and PO agents (b). | |
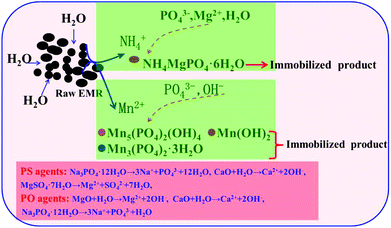 |
| Fig. 9 Schematic illustrations of the immobilization of contaminants. | |
By contrast, the PS agents demonstrated a faster release of Mg2+ from MgSO4·7H2O compared to the PO agents. This is the reason why the 1 h reaction time gave the maximum efficiency of immobilization using PS agents. The Mg2+ from the PO agents came from a slow hydrolysis reaction of MgO, which resulted in the requirement for more MgO.
3.5 Leaching test and economic analysis
After the immobilization of NH4+ and Mn2+ under the optimum conditions, the concentrations of NH4+ and Mn2+ in the leach liquor decreased respectively from 1264 to 98 mg L−1 and from 3518 to 1.3 mg L−1 using the PS agents. The concentration of NH4+ and Mn2+ in the leach liquor was reduced to 207 and 0.7 mg L−1 respectively using PO agents. The concentration of other heavy metal ions in the leach liquor were relatively small and were harmless to the environment. The concentration of heavy metal ions met the Integrated Wastewater Discharge Standard of China (GB8978-1996). This method can be used to immobilize NH4+ and Mn2+ simultaneously in the EMR slurry, in comparison with other EMR studies (shown in Table 4).
An economic evaluation of the immobilization of contaminants from EMR was performed. In the evaluation, the market prices of the used chemicals were obtained from the trading platform of Alibaba and the results are shown in Table 3. The cost of the chemicals used for NH4+ and Mn2+ immobilization using PS agents and PO agents were calculated as being $81.9 per t and $87.5 per t, respectively. Obviously, the use of PS agents has a lower associated cost. In addition, the optimal reaction time for using PS agents is 1 h, which was less than that required when using PO agents (shown in Fig. 5a and 6a). By comparison, the optimal method for NH4+ and Mn2+ immobilization from EMR was using PS agents and the optimum mass ratio of MgSO4·7H2O
:
Na3PO4·12H2O
:
EMR was 0.113
:
0.175
:
1.
Table 3 Market prices of the chemicals used
Chemical |
Market price ($ per kg) |
PS agents |
PS agents |
kg t−1 EMR |
$ per t EMR |
kg t−1 EMR |
$ per t EMR |
CaO |
0.06 |
30 |
1.8 |
10 |
0.6 |
MgSO4·7H2O |
0.12 |
113 |
13.6 |
— |
— |
MgO |
0.55 |
— |
— |
37 |
20.4 |
Na3PO4·12H2O |
0.38 |
175 |
66.5 |
175 |
66.5 |
Total |
— |
— |
81.9 |
— |
87.5 |
Table 4 Comparison of the relevant studies on the treatment of EMR to form a harmless product
Reagent |
Experiment objective |
Leached toxic substance concentrations of the treated EMR |
Note |
Ref. |
MgSO4·7H2O, Na3PO4·12H2O and CaO |
Immobilization of NH4+ and Mn2+ |
98 mg L−1 NH4+, 1.3 mg L−1 Mn2+ |
NH4+ and Mn2+ were immobilized simultaneously and a modest pH was obtained in the EMR |
This paper |
Inorganic chemicals |
Immobilization of heavy metal ions |
The leached amount of Mn2+ was reduced to 100 mg per kilogram of EMR |
NH4+–N was not studied |
15 |
CaO |
Stabilization of Mn2+ and removal of NH4+ |
0.5 mg L−1 Mn2+ |
NH4+ was transformed into NH3 and released into the air |
16 |
Calcium sulfide |
Immobilization of Mn2+ |
0.05 mg L−1 Mn2+ |
NH4+ was not studied |
26 |
Modified sulfur and sand |
EMR used as filler in sulfur concrete |
0.05 mg L−1 Mn2+ |
NH4+–N was not studied |
2 |
4. Conclusions
It was found that NH4+ and Mn2+ were the main contaminants from EMR by performing a leaching experiment. Simultaneous immobilization of NH4+ and Mn2+ was conducted using the chemicals; CaO, MgSO4·7H2O, MgO and Na3PO4·12H2O. Higher immobilization efficiencies of contaminants were found when using PS agents compared to using PO agents. The optimum conditions for immobilizing NH4+ and Mn2+ using PS agents were determined to be as follows: a MgSO4·7H2O
:
Na3PO4·12H2O
:
EMR mass ratio of 0.113
:
0.175
:
1, a CaO
:
EMR mass ratio of 0.03
:
1, and a 1 h reaction time. Under these conditions, the immobilization efficiencies of NH4+ and Mn2+ were 92.4% and 99.9%, respectively. The concentration of heavy metal ions decreased sharply in the leach liquor after immobilization and met the Integrated Wastewater Discharge Standard of China (GB8978-1996). The economic evaluation showed that using PS agents had lower associated costs compared to using PO agents.
In the process of contaminant immobilization, NH4+ was immobilized to form NH4MgPO4·6H2O (struvite). Mn2+ was immobilized to form Mn5(PO4)2(OH)4, Mn3(PO4)2·3H2O and Mn(OH)2. These newly formed phases were stable and insoluble, which was conducive to the stacking and reuse of EMR.
Conflicts of interest
The authors declare no conflicts of interest.
Acknowledgements
This work was financially supported by the Top-notch Talent Project of Science and Technology of the Education Department of Guizhou Province (No. Qianjiaohe KY[2016]094), the National Natural Science Foundation of China (No. 21868001) and the Doctoral Scientific Fund Project of Anshun University (asubsjj201604).
Notes and references
- N. Wang, Z. Fang, S. Peng, D. Cheng, B. Du and C. Zhou, Hydrometallurgy, 2016, 164, 288–294 CrossRef CAS.
- C. Yang, X. Lv, X. Tian, Y. Wang and S. Komarneni, Constr. Build. Mater., 2014, 73, 305–310 CrossRef.
- H. Chen, R. Liu, Z. Liu, J. Shu and C. Tao, Environ. Sci. Pollut. Res., 2016, 23, 12352–12361 CrossRef CAS PubMed.
- N. Duan, Z. Dan, F. Wang, C. Pan, C. Zhou and L. Jiang, J. Cleaner Prod., 2011, 19, 2082–2087 CrossRef.
- N. Duan, W. Fan, Z. Changbo, Z. Chunlei and Y. Hongbing, Resour., Conserv. Recycl., 2010, 54, 506–511 CrossRef.
- J. Shu, R. Liu, H. Wu, Z. Liu, X. Sun and C. Tao, J. Taiwan Inst. Chem. Eng., 2018, 82, 351–359 CrossRef CAS.
- C. Li, H. Zhong, S. Wang, J. Xue and Z. Zhang, Colloids Surf., A, 2015, 470, 258–267 CrossRef CAS.
- Q. Li, Q. Liu, B. Peng, L. Chai and H. Liu, Constr. Build. Mater., 2016, 106, 236–242 CrossRef CAS.
- J. Lan, China's Manganese Industry, 2005, 4, 27–30 Search PubMed.
- J. Wang, B. Peng, L. Chai, Q. Zhang and Q. Liu, Powder Technol., 2013, 241, 12–18 CrossRef CAS.
- B. Du, C. Zhou, Z. Dan, Z. Luan and N. Duan, Constr. Build. Mater., 2014, 50, 291–299 CrossRef.
- C. Zhou, B. Du, N. Wang and Z. Chen, J. Cleaner Prod., 2014, 84, 707–714 CrossRef CAS.
- D. Qiao, J. Qian, Q. Wang, Y. Dang, H. Zhang and D. Zeng, Resour., Conserv. Recycl., 2010, 54, 1368–1376 CrossRef.
- P. Hou, J. Qian, Z. Wang and C. Deng, Cem. Concr. Compos., 2012, 34, 248–254 CrossRef CAS.
- B. Du, D. Hou, N. Duan, C. Zhou, J. Wang and Z. Dan, Environ. Sci. Pollut. Res., 2015, 22, 7782–7793 CrossRef CAS PubMed.
- C. Zhou, J. Wang and N. Wang, Korean J. Chem. Eng., 2013, 30, 2037–2042 CrossRef CAS.
- K. Anastasiadou, K. Christopoulos, E. Mousios and E. Gidarakos, J. Hazard. Mater., 2012, 207, 165–170 CrossRef PubMed.
- A. Gunay, D. Karadag, I. Tosun and M. Ozturk, J. Hazard. Mater., 2008, 156, 619–623 CrossRef CAS PubMed.
- H. Huang, D. Xiao, Q. Zhang and L. Ding, J. Environ. Manage., 2014, 145, 191–198 CrossRef CAS PubMed.
- G. Jia, H. Zhang, J. Krampe, T. Muster, B. Gao, N. Zhu and B. Jin, J. Cleaner Prod., 2017, 147, 297–305 CrossRef CAS.
- B. Seshadri, N. Bolan, G. Choppala, A. Kunhikrishnan, P. Sanderson, H. Wang, L. Currie, D. C. Tsang, Y. Ok and G. Kim, Chemosphere, 2017, 184, 197–206 CrossRef CAS PubMed.
- J. H. Cho, Y. Eom and T. G. Lee, J. Hazard. Mater., 2014, 278, 474–482 CrossRef CAS PubMed.
- A. Escudero, F. Blanco, A. Lacalle and M. Pinto, J. Environ. Chem. Eng., 2015, 3, 413–419 CrossRef CAS.
- P. Xia, X. Wang, X. Wang, J. Song, H. Wang, J. Zhang and J. Zhao, Colloids Surf., A, 2016, 506, 220–227 CrossRef CAS.
- M. Inoue and I. Hirasawa, J. Cryst. Growth, 2013, 380, 169–175 CrossRef CAS.
- C. Li, H. Zhong, S. Wang, J. Xue and Z. Zhang, China's Manganese Industry, 2014, 4, 23–26 CrossRef.
|
This journal is © The Royal Society of Chemistry 2019 |
Click here to see how this site uses Cookies. View our privacy policy here.