DOI:
10.1039/C9RA00217K
(Paper)
RSC Adv., 2019,
9, 9828-9837
Facile synthesis of ordered mesoporous zinc alumina catalysts and their dehydrogenation behavior†
Received
10th January 2019
, Accepted 23rd March 2019
First published on 28th March 2019
Abstract
Ordered mesoporous Zn/Al2O3 materials with varying Zn content were simply prepared via an evaporation-induced self-assembly (EISA) method. Dehydrogenation of isobutane to isobutene was carried out on these materials; an isobutane conversion of 45.0% and isobutene yield of 39.0% were obtained over the 10%Zn/Al2O3 catalyst at 580 °C with 300 h−1 GHSV. The obtained materials with Zn content up to 10% possess large specific surface area and big pore volume and zinc species can be highly dispersed on the surface or incorporated into the framework. The acidity of these catalysts was changed by the introduction of Zn, the decrease of strong acid sites is conducive to the promotion of isobutene selectivity and the weak and medium acidic sites played an important role in isobutane conversion. In addition, these catalysts exhibited good catalytic stability, due to the effective inhibition of coke formation by the ordered mesoporous structure.
1. Introduction
Isobutene is one of the most important raw materials and intermediates to produce butyl rubber, ETBE (ethyl tert-butyl ether), polyisobutene and other chemicals.1,2 To better fulfill the ever-increasing market demand, a small portion of its production is by isobutane dehydrogenation.3 Currently, Cr2O3/Al2O3 and Pt/Al2O3 are the two most common and employable catalysts in industrial production.4,5 However, some unavoidable drawbacks limit their further application, because Pt is expensive and has poor availability, while Cr is not environmentally-friendly due to its toxicity. Therefore, the exploitation of novel catalysts with superior catalytic properties, low cost and non-pollution for isobutane dehydrogenation is highly recommendable.6–8
At present, all kinds of metal catalysts, such as vanadium-based, iron-based, molybdenum-based catalysts, have been widely investigated in this dehydrogenation reaction.9–12 In particular, owing to the excellent catalytic performance, Zn based catalysts have been interested and gazed considerably in the direct dehydrogenation of isobutane. For example, Zn modified HZSM-5 materials were found effective for activation of isobutane and high conversion obtained.13,14 Unfortunately, the poor selectivity with respect to the formation of many undesired dry gas (CH4 and C2H6) impeded its more broad applications, which probably derived from redundant strong acidic sites of HZSM-5 zeolite. Liu et al. reported that 27.5% isobutane conversion and 83.8% isobutene selectivity obtained in isobutane dehydrogenation over Zn/S-1 catalyst, because strong acid sites were absent.15 Moreover, Zn/Ti thin film and Zn/Ga oxide catalyst has also been referred in isobutane dehydrogenation.16,17
Recently, ordered and adjustable mesoporous alumina materials have drawn research much attention. Coupled with their moderate surface acidity and good thermostability, ordered mesoporous alumina as heterogeneous catalyst support has a wonderful applying prospect.18 Morris et al. successfully synthesized NiO–Al2O3 composites with ordered mesoporous structure and the metal oxide well dispersed on the alumina support.19 Yuan et al. reported a simple route to synthesize γ-Al2O3 using P123 template agent, which have high quality mesoporous structure.20 Schweitzer et al. put forward the computed minority catalytic pathway consists of undesired C–C bond cleavage at Zn(II) site had a significantly higher activation energy barrier and the high olefin selectivity observed for single-site Zn(II) on SiO2.21 In our previous work, well-ordered mesoporous Cr2O3/Al2O3 catalysts were synthesized and showed an advantage in catalytic stability.22 So far, almost no research was reported on ordered mesoporous zinc alumina composites for alkane dehydrogenation.
This study firstly prepared ordered mesoporous xZn/Al2O3 catalysts with different Zn content via evaporation-induced self-assembly (EISA) method and evaluated the catalytic performances in isobutane dehydrogenation. The textural properties of obtained materials were characterized by XRD analysis, N2 adsorption–desorption and TEM. And we also discussed the form of Zn species, metal-support interaction and surface acidity by XPS, H2-TPR and NH3-TPD. Besides, all the characterizations were associated with catalytic reactions.
2. Experimental
2.1. Catalyst preparation
Ordered mesoporous Zn/Al2O3 materials were prepared via EISA method according to the previous literatures.20,23,24 In a typical procedure, 1.0 g P123 as surfactant was added to 20 ml ethanol and the solution was stirred for 40 min, followed by the addition of a mmol aluminum isopropoxide, b mmol Zn(NO3)2·6H2O (a + b = 10 mmol) and 1.6 ml nitric acid. After 6 h of stirring, the mixed solution was transferred to a culture dish and kept in drying oven at 60 °C for two days. The obtained xerogel was calcined at 600 °C for 5 h. The catalysts were denoted as xZn/Al2O3, where the nominal molar ratio x = (b/(a + b) × 100%).
2.2. Catalytic dehydrogenation
The direct dehydrogenation of isobutane was studied in fixed-bed quartz reactor. Typically, 900 mg of catalyst was sieved at 60–80 mesh. The reaction temperature was set at 560–620 °C. The reactant gas was fed by gas hourly space velocity (GHSV) of 300 h−1. The composition of the gaseous products was analyzed on-line using gas chromatography fitted with flame ionization detector (FID) and thermal conductivity detector (TCD).
2.3. Characterization
N2 adsorption–desorption isotherms were measured by Autosorb-iQ analyzer. The specific surface area was calculated by Brunauer–Emmett–Teller (BET) equation and pore size distribution was calculated by Barret–Joyner–Halenda (BJH) equation from the N2 sorption isotherm.
X-ray diffraction (XRD) were collected on X'Pert Pro diffraction instrument using Cu Kα radiation over the range 0.6° < 2θ < 5° and 5° < 2θ < 80°.
Transmission electron microscopy (TEM) images were conducted at TECNAIG2 F20 instrument.
X-ray photoelectron spectroscopy (XPS) were recorded on Thermon ESCALAB 250xi spectrometer. The binding energies were calibrated against at 284.8 eV of C1s.
H2 temperature-programmed reduction (H2-TPR) was performed on ChemBET Pulsar Analyzer. Prior to the tests, sample was pretreated at 300 °C in He flow for 30 min. After cooling to ambient temperature, then raised temperature to 650 °C in 10% H2–Ar mixed flow.
NH3 temperature-programmed desorption (NH3-TPD) was recorded on ChemBET Pulsar analyzer combining with mass spectroscopy. After being pretreated at 300 °C in He flow, the sample adsorbed NH3 to saturation at 120 °C. The profile was detected from 50 °C to 600 °C.
Thermogravimetric-differential scanning calorimetry (TG-DSC) was based on a NETZSCH STA 449F3 analyzer under air within 20–800 °C at 10 °C min−1.
The Zn content in a series of xZn/Al2O3 catalysts were measured by inductively coupled plasma optical emission spectrometer (ICP-OES, 725-ES, Agilent).
3. Results and discussion
3.1. XRD analysis
The XRD patterns of all the as-synthesized xZn/Al2O3 materials are presented in Fig. 1. As displayed from Fig. 1A inside, a distinct reflection peak was observed in 3–10%Zn/Al2O3 samples at the characteristic reflection (100) of p6mm space group, which confirming that these materials were composed of a well ordered mesoporous structure.25 With further increasing Zn content to 15%, the diffraction peak at 0.8° became almost disappeared, indicating the significant effect of zinc content in building the ordered mesoporous structure. Part B of Fig. 1 presents the wide-angle XRD patterns of all the materials, which revealed the existence of amorphous Al2O3. Only the 15%Zn/Al2O3 sample exhibited sharp diffraction peaks associated with hexagonal crystalline ZnO (no. 89-1397 from the ICDD). The average size of these ZnO particles is 23.8 nm. On the contrary, no diffraction peaks for Zn species came into sight in 3–10%Zn/Al2O3 materials with ordered mesopore, implying Zn species highly dispersed on support surface or incorporated into amorphous alumina framework.26 In conclusion, the presence of ordered mesoporous structure played an important role in promoting the dispersion of Zn species on the catalyst support.
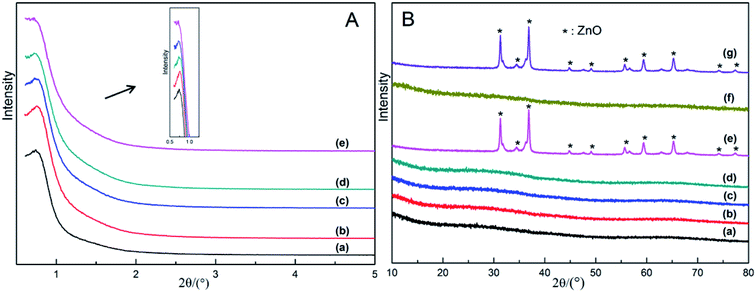 |
| Fig. 1 The XRD patterns of the as-synthesized and spent xZn/Al2O3 catalysts: (a) 3%Zn/Al2O3; (b) 5%Zn/Al2O3; (c) 7%Zn/Al2O3; (d) 10%Zn/Al2O3; (e) 15%Zn/Al2O3; (f) the spent 10%Zn/Al2O3; (g) the spent 15%Zn/Al2O3. | |
3.2. Nitrogen adsorption–desorption analysis
The nitrogen adsorption–desorption analysis of all the as-synthesized xZn/Al2O3 materials is displayed in Fig. 2. Each sample but 15%Zn/Al2O3 exhibited typical IV type isotherm as well as H1 shaped hysteresis loop, implying the presence of uniform cylindrical mesoporous channel in these catalysts.27 Furthermore, the 3–10%Zn/Al2O3 samples possessed quite narrow pore size distribution around 9.5 nm, while that of 15%Zn/Al2O3 sample was bigger (around 12.4 nm). It suggested that the larger pores could be accumulated by ZnO particles. Table 1 listed the detailed data regarding to the textural properties of above samples. It has been observed that the specific surface area of as-synthesized 3–10%Zn/Al2O3 materials was similar (around 163 m2 g−1), which because Zn species highly dispersed on support surface or incorporated into alumina framework wouldn't lead to pore plugging. At a Zn content of 15%, the specific surface area was only 31 m2 g−1 owing to the mesoporous structure collapsed. It has been known that a larger surface area conduced to the better dispersion of active species, thereby can provide more “accessible” active centers for the reactant gas.28 Therefore, these as-synthesized 3–10%Zn/Al2O3 catalysts may own preferable catalytic performance.
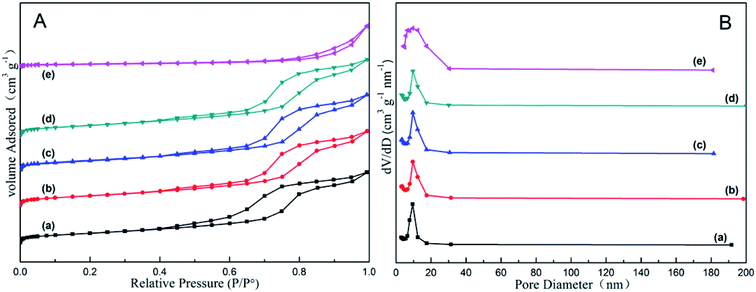 |
| Fig. 2 The nitrogen adsorption–desorption analysis of the as-synthesized xZn/Al2O3 catalysts: (a) 3%Zn/Al2O3; (b) 5%Zn/Al2O3; (c) 7%Zn/Al2O3; (d) 10%Zn/Al2O3; (e) 15%Zn/Al2O3. | |
Table 1 The textural data of the as-synthesized xZn/Al2O3 catalystsa
Samples |
SBET (m2 g−1) |
VP (cm3 g−1) |
dP (nm) |
Isotherm type |
Zn content (%) |
XPS |
ICP-OES |
a,bStand for the corresponding spent and fifth regenerated catalyst, respectively. |
3%Zn/Al2O3 |
163.3 |
0.41 |
9.5 |
IV |
1.6 |
2.5 |
5%Zn/Al2O3 |
162.6 |
0.43 |
9.6 |
IV |
2.3 |
4.3 |
7%Zn/Al2O3 |
163.4 |
0.44 |
9.6 |
IV |
3.0 |
6.4 |
10%Zn/Al2O3 |
163.3 |
0.43 |
9.6 |
IV |
3.8 |
9.7 |
15%Zn/Al2O3 |
31.3 |
0.23 |
12.4 |
III |
14.6 |
12.8 |
10%Zn/Al2O3a |
149.7 |
0.40 |
9.3 |
IV |
— |
— |
10%Zn/Al2O3b |
158.6 |
0.42 |
9.5 |
IV |
— |
— |
15%Zn/Al2O3a |
25.2 |
0.16 |
11.8 |
III |
— |
— |
3.3. TEM analysis
The morphology and structure of all the as-synthesized xZn/Al2O3 materials were performed by TEM (Fig. 3). From the images, all the sample except 15%Zn/Al2O3 presented one dimensional parallel channel along [1 1 0], which intuitively confirmed the presence of well-ordered mesoporous structure in the 3–10%Zn/Al2O3 catalysts. Notably, no distinct ZnO clusters were invisible in the images, illustrating the high dispersion of Zn species on the ordered mesoporous channel. This result conformed to the low-angle XRD analysis. Only a fraction of ordered mesopore was formed for 15%Zn/Al2O3 sample. In the EDX profile of 10%Zn/Al2O3 sample (Fig. 3f), the characteristic peaks of Al, Zn, O element can be observed clearly, which verified that Zn species had been successfully loaded. Besides, elemental mapping has further confirmed the ordered mesoporous structure and shown Zn species on the surface to be highly dispersed and distributed homogeneously over the 10%Zn/Al2O3 catalyst. However, an obvious aggregation of ZnO particles was visible on the surface of 15%Zn/Al2O3 catalyst, which conformed the result of wide-angle XRD analysis (Fig. 4).
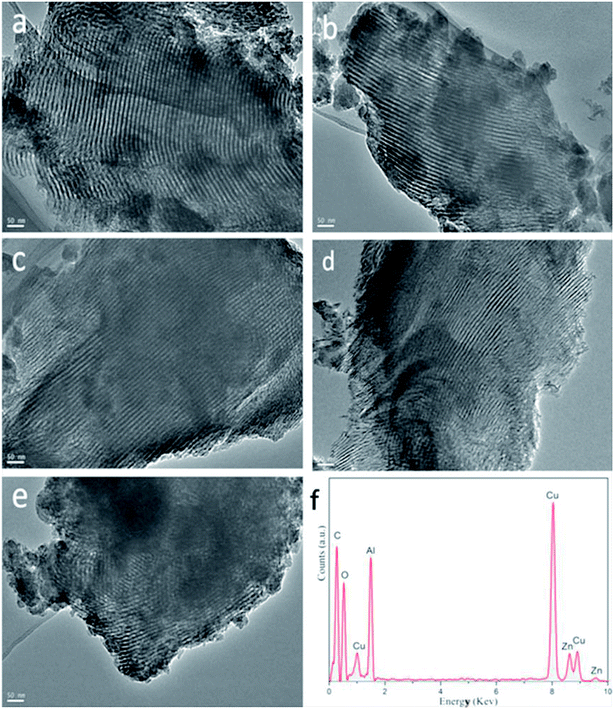 |
| Fig. 3 The TEM images of the as-synthesized xZn/Al2O3 catalysts: (a) 3%Zn/Al2O3; (b) 5%Zn/Al2O3; (c) 7%Zn/Al2O3; (d) 10%Zn/Al2O3; (e) 15%Zn/Al2O3. (f) EDX characterization for 10%Zn/Al2O3. | |
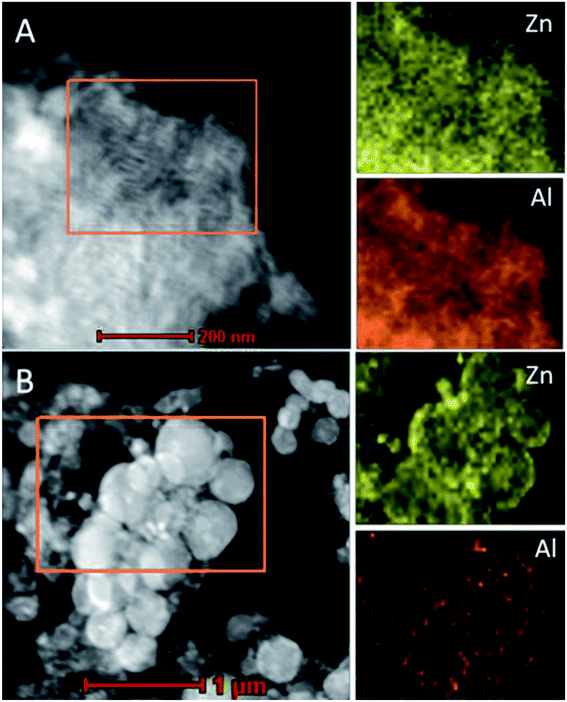 |
| Fig. 4 TEM image and Zn, Al elemental mappings of the fresh samples: (A) 10%Zn/Al2O3; (B) 15%Zn/Al2O3. | |
3.4. XPS analysis
The XPS spectra of Zn 2p orbital for all the as-synthesized xZn/Al2O3 materials are depicted in Fig. 5. As displayed, the binding energy located at 1021.2–1201.6 eV and 1044.3–1044.7 eV was assigned to Zn2+, as proved by spin–orbital splitting of 23.1 eV between Zn 2p3/2 and Zn 2p1/2.29,30 Noteworthy, the binding energy of Zn 2p in the sample 15%Zn/Al2O3 was lower than that of 10%Zn/Al2O3, which may be derived from the difference of Zn species in these catalysts. By deconvolution, the peak of 15%Zn/Al2O3 was divided into two peaks, the big one may be assigned to bulk ZnO particle on the surface, another small one may belonged to Zn species incorporated into alumina framework. The Zn content calculated by XPS and ICP-OES was used to affirmed and the corresponding data listed in Table 1. We can see that the bulk Zn contents were closely to the calculated data, only 15%Zn/Al2O3 had a larger deviation. Moreover, the surface Zn content (14.6%) of this sample from XPS was higher than the actual Zn content (12.8%), suggesting aggregation of ZnO particles on the surface. In contrast, the surface Zn was less than the bulk for 3–10%Zn/Al2O3 samples, which was due to most of Zn species incorporated into alumina framework. These results were accorded with wide-angle XRD analysis and confirmed the change of Zn species when increased Zn content from 10% to 15%. Besides, the higher binding energy meaning a stronger interaction between Zn species and support in 3–10%Zn/Al2O3 catalysts. This result will be further confirmed by following H2-TPR characterization.
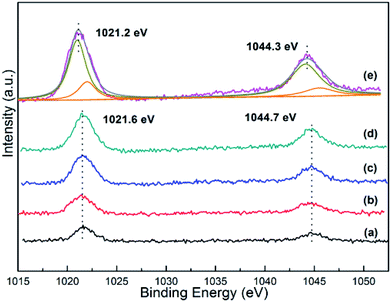 |
| Fig. 5 The Zn 2p XPS spectra of the as-synthesized xZn/Al2O3 catalysts: (a) 3%Zn/Al2O3; (b) 5%Zn/Al2O3; (c) 7%Zn/Al2O3; (d) 10%Zn/Al2O3; (e) 15%Zn/Al2O3. | |
3.5. H2-TPR profiles
H2-TPR characterization is a very useful instrument to investigate the interaction between Zn species and catalyst support. The results for the as-synthesized xZn/Al2O3 materials and pure ZnO are shown in Fig. 6. All profiles of xZn/Al2O3 showed a broad reduction peak around 490 °C, which could be assigned to the reduction of highly dispersed zinc species on support surface and Zn species incorporated into alumina framework. However, 15%Zn/Al2O3 catalyst presented a unique reduction peak at 416 °C, which was similar with the reduction peak of pure bulk ZnO. More specifically, this peak belonged to the reduction of binuclear (Zn–O–Zn)2+ clusters.31 It has been known that the higher reduction temperature, the stronger interaction between metal and support. Therefore, the Zn species with the reduction peak around 490 °C have stronger interaction with support.32 The characterization of H2-TPR was coincided with the above XRD and XPS analysis.
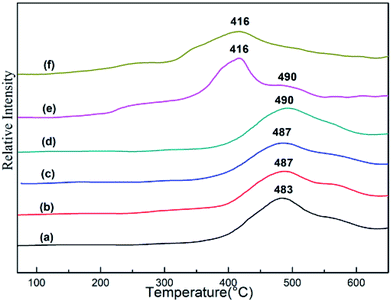 |
| Fig. 6 The H2-TPR profiles of the as-synthesized xZn/Al2O3 catalysts: (a) 3%Zn/Al2O3; (b) 5%Zn/Al2O3; (c) 7%Zn/Al2O3; (d) 10%Zn/Al2O3; (e) 15%Zn/Al2O3; (f) ZnO. | |
3.6. NH3-TPD analysis
The acidic property of all the as-synthesized xZn/Al2O3 materials was determined by NH3-TPD and the corresponding results are displayed in Fig. S1.† All the samples exhibited a broad peak at 50–600 °C, indicating abundant different intensities of acidic sites in xZn/Al2O3 catalysts. By deconvolution, the broad peak was divided into four peaks accredited to physically adsorbed NH3, weak, medium and strong acidic sites respectively.33,34 The detailed calculation result was in Table 2. As displayed, all the samples except for 15%Zn/Al2O3 exhibited similar amount of physically adsorbed NH3, which due to their comparable pore property. However, the specific surface area and pore volume of 15%Zn/Al2O3 was much smaller, then physically adsorbed NH3 also less than other samples. Besides, we can see that there are three different acidic sites on pure ordered mesoporous Al2O3. With the introduction of 3%Zn, the amount of three acidic sites significantly enhanced. It indicated that a part of three types acid sites originated from surface hydroxyl group and coordinative unsaturated Al sites on Al2O3 support, and other derived from Zn species.15,35 Note that the total and weak acidic sites gradually increased, while the strong acidic sites decreased slowly with the increase of Zn content until 10%. When the Zn content reached 15%, the total acidic strength of this catalyst declined sharply, which may due to bulk ZnO has rarely acidic sites (Fig. S2†). It was well established that weak and medium acid sites played a key role to isobutane conversion in dehydrogenation reaction.15 However, side reactions (polymerization, isomerization and cracking) are mainly catalyzed by strong acid sites.36 As a conclusion, the various xZn/Al2O3 catalysts with the different number of acidic sites may present distinct catalytic performance.
Table 2 The acidic properties of the as-synthesized Al2O3 and xZn/Al2O3 catalysts
Samples |
Physically adsorbed NH3 (mmol g−1) |
The amount of acidic sites (mmol g−1) |
Weak |
Medium |
Strong |
Total |
Al2O3 |
0.007 |
0.037 |
0.021 |
0.009 |
0.067 |
3%Zn/Al2O3 |
0.008 |
0.048 |
0.051 |
0.026 |
0.125 |
5%Zn/Al2O3 |
0.009 |
0.061 |
0.043 |
0.024 |
0.128 |
7%Zn/Al2O3 |
0.010 |
0.066 |
0.041 |
0.023 |
0.130 |
10%Zn/Al2O3 |
0.009 |
0.069 |
0.048 |
0.016 |
0.133 |
15%Zn/Al2O3 |
0.004 |
0.036 |
0.033 |
— |
0.069 |
3.7. Catalytic performance in the isobutane dehydrogenation
The reactivity of isobutane dehydrogenation over a series of xZn/Al2O3 catalysts is displayed in Fig. 7. As we can notice that the catalytic activity of xZn/Al2O3 catalysts gradually increased until 10% Zn content. The 10%Zn/Al2O3 catalyst exhibited a notably higher initial isobutane conversion (46.6%) and initial isobutene selectivity (81.8%) by contrast with the 3%Zn/Al2O3 (29.4% conversion and 69.4% selectivity), indicating that Zn content was a very significant factor in isobutane dehydrogenation reaction. In addition to this, with increasing reaction time, the reactivity over the 3–10%Zn/Al2O3 catalysts can basically hold steady, while the 15%Zn/Al2O3 catalyst presented poor catalytic stability.
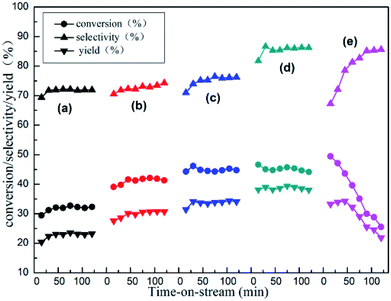 |
| Fig. 7 The reactivity of isobutane dehydrogenation over the as-synthesized xZn/Al2O3 catalysts: (a) 3%Zn/Al2O3; (b) 5%Zn/Al2O3; (c) 7%Zn/Al2O3; (d) 10%Zn/Al2O3; (e) 15%Zn/Al2O3. Reaction condition: T = 580 °C, GHSV = 300 h−1. | |
Isobutane dehydrogenation is an endothermic reaction in thermodynamics, which need relatively high temperature to obtain excellent isobutene yield. The effect of reaction temperature on catalytic activity of 10%Zn/Al2O3 catalyst was investigated in Fig. 8. The conversion of isobutane was 45.0% and the selectivity of isobutene was 86.7% at 580 °C after 30 min. With the increase of the reaction temperature, the conversion of isobutane obviously increased and selectivity of isobutene significantly decreased, which was quite conformed to the characteristic of alkane dehydrogenation reaction. However, the isobutane conversion dropped drastically, isobutene selectivity just increased slightly with the reaction temperature decreased to 560 °C. In view of catalytic stability, 580 °C was deemed as the optimal reaction temperature.
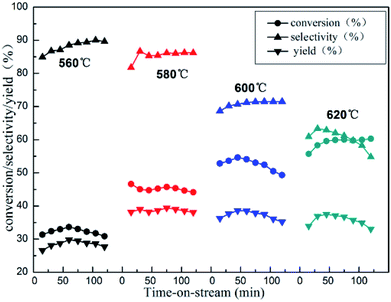 |
| Fig. 8 The reactivity of isobutane dehydrogenation over the 10%Zn/Al2O3 catalyst. Reaction condition: GHSV = 300 h−1. | |
The impact of the GHSV on catalytic activity was also carefully studied over 10%Zn/Al2O3 catalyst (Fig. 9). As we can see, with GHSV increasing from 300 to 600 h−1, the initial isobutane conversion decreased obviously (from 46.6% to 30.6%), while initial isobutene selectivity increased (from 81.8% to 91.1%). As the GHSV continues to rise, it became slope that isobutane conversion decreased with time on stream.
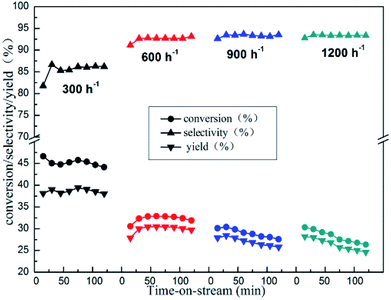 |
| Fig. 9 The reactivity of isobutane dehydrogenation over the 10%Zn/Al2O3 catalyst. Reaction condition: T = 580 °C. | |
In order to further investigate what were active sites for isobutane dehydrogenation, we tested this reaction at 580 °C over ordered mesoporous Al2O3 and commercial ZnO as a contrast (Fig. S3†). It can be seen that initial isobutane conversion and initial isobutene yield over Al2O3 were only 3.1% and 2.1%, which illustrated that ordered mesoporous Al2O3 was inactive to the reaction. ZnO exhibited slightly higher initial dehydrogenation activity (9.2% isobutane conversion and 5.5% isobutene yield). It seemed that bulk ZnO particle had some catalytic ability. Surprisingly, with the introduction of Zn, the xZn/Al2O3 catalysts exhibited very excellent initial catalytic activity, even then the ordered mesopore collapsed and Zn species was not highly dispersed over 15%Zn/Al2O3 catalyst. Considering the possibility of zinc incorporated into Al2O3 framework over 15%Zn/Al2O3 catalyst, we deduced that the existence of framework zinc may play a crucial role. However, there is no direct evidence for this. The essential role of Zn species of xZn/Al2O3 in isobutane dehydrogenation still need to be identified, which is the focus of the following work in our laboratory. In addition, it is well-known that the amount of different acidic sites of catalyst are the key to affect catalytic activity in alkane dehydrogenation reaction.37 The isobutane conversion rate vs. the number of different acidic sites on the basis of Table 2 were plotted (Fig. 10). The isobutane conversion rate versus the amount of strong acidic sites showed the worst linear correlation (R2 = 0.19), nevertheless, versus the amount of weak and medium acidic sites presented the best linear correlation (R2 = 0.96), indicating that strong acidic sites were not the decisive factor for isobutane conversion, while both the weak and medium acidic sites took the important part in isobutane conversion. Besides, the isobutane selectivity was obviously increased with the decrease of the amount of strong acidic sites over 3–10%Zn/Al2O3 catalysts, indicated strong acid sites mainly catalyzed side reactions.
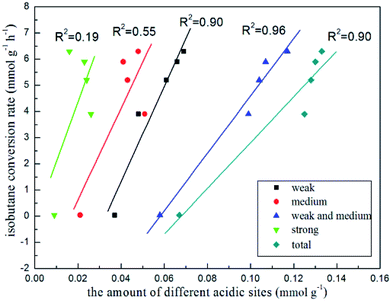 |
| Fig. 10 The trend of isobutane conversion rate with the amount of different kinds of the acidic sites. | |
3.8. The stability of ordered mesoporous Zn/Al2O3 catalyst
3.8.1. XRD analysis. The wide-angle XRD patterns of the spent catalysts are shown in Fig. 1. It was observed that there is no difference between fresh and spent catalysts. The crystalline ZnO phase was also visible over spent 15%Zn/Al2O3 catalyst, and no Zn species over the spent 10%Zn/Al2O3 catalyst as well, indicating that Zn species were stable without phase transformation during this dehydrogenation reaction.
3.8.2. Nitrogen adsorption–desorption analysis. The nitrogen adsorption–desorption analysis of the spent and regenerated catalysts are in Fig. S4.† Compared with the corresponding fresh catalysts, the isotherms of spent catalysts had no obvious changed and still presented uniform pore size. The textural properties are presented in Table 1. It was clearly seen that the BET specific surface areas of the spent 10%Zn/Al2O3 and 15%Zn/Al2O3 catalysts were greatly reduced to 149.7 m2 g−1 and 25.2 m2 g−1, respectively. It was probably due to that coke deposition on the spent catalyst blocked a portion of the pore, thus leading to the decrease of textural performance. After five dehydrogenation–regeneration cycles, the slightly diminished specific surface area (163.3 → 158.6 m2 g−1) and pore volume (0.43 → 0.42 cm3 g−1) of the regenerated 10%Zn/Al2O3 demonstrated the formed coke can be eliminated by regeneration process.
3.8.3. TG-DSC analysis. As we all know, coking is usually the main reason for catalyst deactivation in alkane dehydrogenation reaction. TG-DSC is a very efficient technique to analyze the coke amount and the characterization results are shown in Fig. 11. The TG curves presented downtrend with the increase of temperature, which could be divided into two stages. In the first stage, the weight losses in TG curves up to 300 °C, ascribed to the loss of physically adsorbed water and impurities. The second stage, located in the 350–600 °C, the losses was assigned to the removal of coke. The coke amount in the spent 3%Zn/Al2O3, 5%Zn/Al2O3, 7%Zn/Al2O3 and 10%Zn/Al2O3 were 2.97%, 3.22%, 3.29% and 3.45%, respectively. Which similar coke amount was consistent with the same good stability of these ordered mesoporous catalysts. However, with increasing Zn content to 15%, coke amount was markedly increased (5.19%). Combined with the poor stability of 15%Zn/Al2O3 catalyst, the reason of serious deactivation may caused by more coke, which also indicated ordered meso-structure could effectively inhibited the formation of coke.38 Moreover, during 620 °C reaction temperature, the coke amount in the spent 10%Zn/Al2O3 catalyst increased to 3.79%. It explained the stability decreased with the increase of reaction temperature.
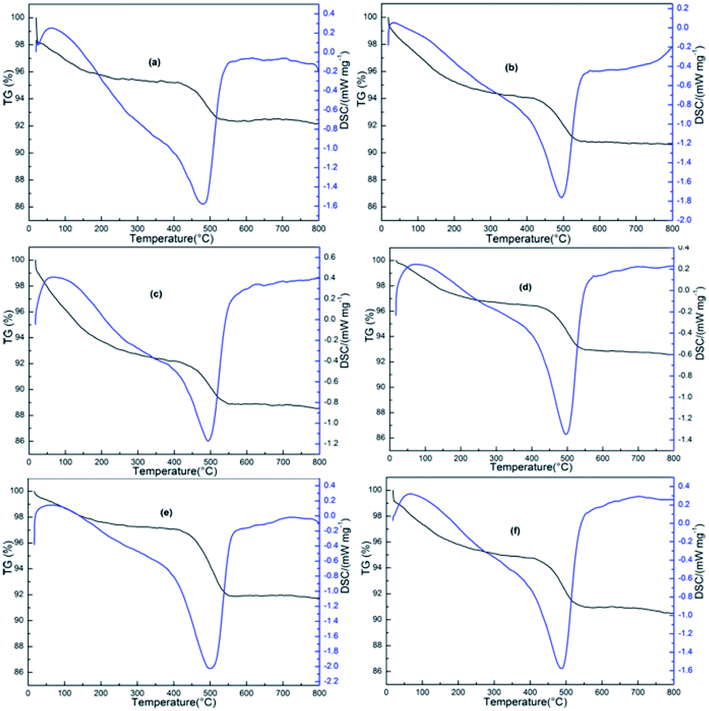 |
| Fig. 11 TG-DSC curves of the spent catalysts at 580 °C reaction: (a) 3%Zn/Al2O3; (b) 5%Zn/Al2O3; (c) 7%Zn/Al2O3, (d) 10%Zn/Al2O3; (e) 15%Zn/Al2O3 and the spent catalyst at 620 °C reaction: (f) 10%Zn/Al2O3. | |
3.8.4. The dehydrogenation–regeneration cycles. In order to examine the regenerative ability of the 10%Zn/Al2O3 catalyst, the five dehydrogenation–regeneration cycles were investigated (Fig. 12). By calculation, the initial isobutane conversion, isobutene selectivity and yield were 45.1%, 83.6% and 37.7% in the first cycle, respectively. With increasing reaction time, the catalytic activity decreased gradually. Following by 2 h regeneration of catalyst at 600 °C in air, the activity of catalyst was obviously restored, which affirmed coke was the main reason of catalyst deactivation. In the five cycle, the initial isobutane conversion, isobutene selectivity and yield were decrease slightly, indicated the high regenerative ability of the catalyst.
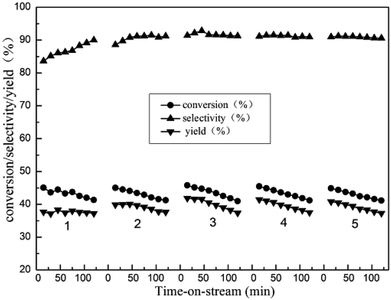 |
| Fig. 12 The five dehydrogenation–regeneration cycles of isobutane dehydrogenation over 10%Zn/Al2O3 catalyst. Reaction condition: T = 580 °C, GHSV = 300 h−1. | |
4. Conclusions
A series of xZn/Al2O3 materials with various Zn content were simply prepared via one pot EISA strategy and tested in isobutane dehydrogenation reaction. The obtained materials with Zn content up to 10% possessed well-ordered mesopore with large specific surface areas, big pore volumes and uniform pore size. Zinc species in these catalysts was highly dispersed on support surface or incorporated into framework, while ZnO crystal particles were observed with 23.8 nm size in the case of 15%Zn. It was found that these materials presented excellent catalytic activity. Note that the total acidic sites gradually increased, while the strong acidic sites decreased slowly with the increase of Zn content until 10%. The decrease of strong acid sites is conducive to the promotion of isobutene selectivity and the weak and medium acidic sites played a role in isobutane conversion. In addition, the catalyst exhibited excellent stability and high regenerative ability, which demonstrated potential for commercial applications.
Conflicts of interest
There are no conflicts to declare.
Acknowledgements
The authors sincerely acknowledge the financial support from the National Natural Science Foundation of China (no. 21573260 and No. 21403255), Youth Innovation Promotion Association CAS (no. 2017460) and Jiangsu Science and Technology Program (no. BY2016048-01).
References
- I. Gniot, P. Kirszensztejn and M. Kozłowski, Appl. Catal., A, 2009, 362, 67–74 CrossRef CAS.
- A. Feller, I. Zuazo, A. Guzman, J. O. Barth and J. A. Lercher, J. Catal., 2003, 216, 313–323 CrossRef CAS.
- Y. Tian, X. Liu, M. Rood and Z. Yan, Appl. Catal., A, 2017, 41, 1–9 CrossRef.
- S. Al-Zahran, N. Elbashir, A. Abasaeed and M. Abdulwahed, Ind. Eng. Chem. Res., 2001, 40, 781–784 CrossRef.
- L. Wan, Y. Zhou, Y. Zhang, Y. Duan, X. Liu and M. Xue, Ind. Eng. Chem. Res., 2011, 58, 4280–4285 CrossRef.
- J. Zhang, D. Su, A. Zhang, D. Wang, R. Schlögl and C. Hebert, Angew. Chem., Int. Ed., 2007, 46, 7319–7323 CrossRef CAS PubMed.
- J. Grant, C. Carrero, F. Goeltl, J. Venegas, P. Mueller, S. Burt, S. Specht, W. McDermott, A. Chieregato and I. Hermans, Science, 2016, 354, 1570–1573 CrossRef CAS PubMed.
- J. H. B. Sattler, J. Ruiz-Martinez, E. Santillan-Jimenez and B. M. Weckhuysen, Chem. Rev., 2014, 114, 10613–10653 CrossRef CAS PubMed.
- J. Mu, J. Shi, L. France, Y. Wu, Q. Zeng, B. Liu, Li. Jiang, J. Long and X. Li, ACS Appl. Mater. Interfaces, 2018, 10, 23112–23121 CrossRef CAS PubMed.
- H. Zhao, H. Song, J. Yang, J. Zhao, L. Yan and L. Chou, Catal. Sci. Technol., 2017, 15, 3256–3267 Search PubMed.
- S. Wang, K. Wang and X. Wang, Appl. Surf. Sci., 2016, 386, 442–450 CrossRef CAS.
- M. Cheng, H. Zhao, J. Yang, J. Zhao, L. Yan, H. Song and L. Chou, Microporous Mesoporous Mater., 2018, 266, 117–125 CrossRef CAS.
- J. Liu, A. Hong, N. He, G. Liu, C. Liang, X. Zhang and H. Guo, Chem. Eng. J., 2013, 218, 1–8 CrossRef CAS.
- Y. Sun and T. Brown, Int. J. Chem. Kinet., 2002, 34, 467–480 CrossRef CAS.
- G. Liu, J. Liu, N. He, C. Miao, J. Wang, Q. Xin and H. Guo, RSC Adv., 2018, 8, 18663–18671 RSC.
- Z. Chen, A. Derking, W. Koot and M. van Dijk, J. Catal., 1996, 161, 730–741 CrossRef CAS.
- G. Wang, C. Li and H. Shan, Catal. Sci. Technol., 2016, 6, 3128–3136 RSC.
- W. Wang, K. Zhang, Y. Yang, H. Liu, Z. Qiao and H. Luo, Microporous Mesoporous Mater., 2014, 193, 47–53 CrossRef CAS.
- S. M. Morris, P. F. Fulvio and M. Jaroniec, J. Am. Chem. Soc., 2008, 130, 15210–15216 CrossRef CAS PubMed.
- Q. Yuan, A. Yin, C. Luo, L. Sun, Y. Zhang, W. Duan, H. Liu and C. Yan, J. Am. Chem. Soc., 2008, 130, 3465–3472 CrossRef CAS PubMed.
- N. M. Schweitzer, B. Hu, U. Das, H. Kim and A. S. Hock, ACS Catal., 2014, 4, 1091–1098 CrossRef CAS.
- L. Xu, Z. Wang, H. Song and L. Chou, Catal. Commun., 2013, 35, 76–81 CrossRef CAS.
- M. Morris, P. Fulvio and M. Jaroniec, J. Am. Chem. Soc., 2008, 130, 15210–15216 CrossRef PubMed.
- L. Xu, H. Song and L. Chou, Int. J. Hydrogen Energy, 2013, 38, 7307–7325 CrossRef CAS.
- D. Pan, W. Chen, F. Yu, S. Chen, X. Yan, X. Shi, B. Fan and R. Li, Mater. Lett., 2018, 224, 33–36 CrossRef CAS.
- X. Xiang, H. Zhao, J. Yang, J. Zhao, L. Yan, H. Song and L. Chou, Appl. Catal., A, 2016, 520, 140–150 CrossRef CAS.
- M. Kruk and M. Jaroniec, Chem. Mater., 2001, 13, 3169–3183 CrossRef CAS.
- Z. He, Y. Jiao, J. Wang and Y. Chen, Fuel, 2018, 212, 193–201 CrossRef CAS.
- A. Choi, J. Park, Y. Kang, S. Lee and Y. Kang, Phys. B, 2018, 537, 251–257 CrossRef CAS.
- W. Gu, X. Wu and J. Zhang, Mater. Sci. Semicond. Process., 2018, 81, 89–93 CrossRef CAS.
- S. Tamiyakul, W. Ubolcharoen, D. N. Tungasmita and S. Jongpatiwut, Catal. Today, 2015, 256, 325–335 CrossRef CAS.
- C. Yu, H. Xu, Q. Ge and W. Li, J. Mol. Catal. A: Chem., 2007, 266, 80–87 CrossRef CAS.
- H. Ham, M. H. Jeong, H. M. Koo, C. H. Chung and J. W. Bae, React. Kinet., Mech. Catal., 2015, 116, 173–189 CrossRef CAS.
- U. Rodemerck, E. V. Kondratenko, T. Otroshchenko and D. Linke, Chem. Commun., 2016, 52, 12222–12225 RSC.
- S. Zhang, Y. Zhou, Y. Zhang and L. Huang, Catal. Lett., 2010, 135, 76–82 CrossRef CAS.
- Y. Ren, F. Zhang, W. Hua, Y. Yue and Z. Gao, Catal. Today, 2009, 148, 316–322 CrossRef CAS.
- M. Dixit, P. Kostetskyy and G. Mpourmpakis, ACS Catal., 2018, 8, 11570–11578 CrossRef CAS.
- L. Xu, Z. Miao, H. Song, W. Chen and L. Chou, Catal. Sci. Technol., 2014, 4, 1759–1770 RSC.
Footnote |
† Electronic supplementary information (ESI) available. See DOI: 10.1039/c9ra00217k |
|
This journal is © The Royal Society of Chemistry 2019 |
Click here to see how this site uses Cookies. View our privacy policy here.