DOI:
10.1039/C9RA02456E
(Paper)
RSC Adv., 2019,
9, 15791-15797
N-doped graphene/CoFe2O4 catalysts for the selective catalytic reduction of NOx by NH3
Received
1st April 2019
, Accepted 14th May 2019
First published on 21st May 2019
Abstract
In this paper, CoFe2O4/graphene catalysts and N-doped graphene/CoFe2O4 (CoFe2O4/graphene-N) catalysts were prepared using the hydrothermal crystallization method for the selective catalytic reduction of NOx by NH3. The results of the test showed that CoFe2O4/graphene catalysts exhibited the best denitrification activity when the loading was at 4% and the conversion rate of NOx reached 99% at 250–300 °C. CoFe2O4/graphene-N catalysts presented a better denitrification activity at low temperature than CoFe2O4/graphene catalysts, and the conversion rate of NOx reached more than 95% at 200–300 °C. The intrinsic mechanism of CoFe2O4/graphene-N catalysts in promoting SCR activity was preliminarily explored. The physicochemical properties of the samples were characterized using XRD, TEM, N2 adsorption, XPS, NH3-TPD, and H2-TPR. The results indicated that nitrogen doping can improve the dispersion of CoFe2O4, and it also increased the acidic sites and the redox performance conducive to improving the denitrification activity of the catalysts. In addition, CoFe2O4/graphene-N catalysts demonstrated a better resistance to water and sulfur than CoFe2O4/graphene catalysts.
1. Introduction
Nitrogen oxide (NOx) is one of the typical atmospheric pollutants.1 Selective catalytic reduction (SCR) is an effective method to control the emission of nitrogen oxides from coal-fired power plants.2 At present, V2O5–WO3/TiO2 catalysts are still widely used in the denitrification process of coal-fired boilers and power plants. However, there are many disadvantages in practical applications, such as high running temperature, poor sulfur and water resistance, and short service life.3 Therefore, the development of high activity denitrification catalysts at a low temperature is of great significance for environmental protection.
In recent years, iron-based catalysts have been widely used in SCR because of their fine catalytic performance, such as Fe/ZSM-5,4 Fe/MCM-56,5 Co–Fe,6 Fe–Mn,7 and Co3O4–CoFe2O4@SiO2@Au.8 Among them, Spinel ferrite AFe2O4 (A = Zn, Ni, Co, Mn) has the advantages of good chemical stability, high mechanical strength and excellent electromagnetic properties.9–11 Kennedy et al. found that the photocatalytic degradation rate of Rhodamine B by Co0.6Mg0.4Fe2O4 reached 99.5%.12 Wang et al. found that the photochemical degradation ability of CoFe2O4/MoS2 nanocomposites prepared for organic dyes reached 94.9%.13 The Co1−xZnxFe2O4 nanocomposite studied by Das and co-workers exhibits good photocatalytic properties.14 Graphene (GE) has been widely used as a carrier to improve the performance of catalysts due to its large specific surface area, high electron mobility and stable chemical properties.15,16 Yao et al. found that CoFe2O4/graphene has better catalytic activity than CoFe2O4 in phenol degradation.17 Bian et al. found that CoFe2O4/graphene nanocomposites exhibit excellent catalytic activity in redox reactions.18
N-doped mesoporous carbon materials have been widely used in catalytic reactions. The modification of mesoporous carbon by incorporating nitrogen leads to the better particle dispersity, but also probably disturbs the electronic structure of carbon solids owing to the formation of a semiconductor-like energy gap.19 To the best of our knowledge, the research of N-doped graphene/CoFe2O4 (CoFe2O4/graphene-N) for NH3-SCR has been rarely reported. In this paper, graphene as catalysts carrier was used to prepare CoFe2O4/graphene catalysts for NH3-SCR reaction. The proper proportion of CoFe2O4/graphene catalysts was determined, and the effect of nitrogen doped on the denitrification performance of CoFe2O4/graphene catalyst was also investigated. The mechanism of CoFe2O4/graphene-N catalyst in promoting SCR activity was preliminarily explored, which provided a theoretical basis for the practical application of AFe2O4 catalysts in NH3-SCR reaction.
2. Experimental
2.1 Catalysts preparation
2.1.1 Preparation of GO. Graphene oxide was prepared using the Hummers' method.20 The preparation process was as follows: 5 g of graphite powder, 2.5 g of sodium nitrate and 115 ml of concentrated sulfuric acid were firstly added to a three-necked flask placed in an ice water bath for stirring, and after being uniformly mixed, 15 g of potassium permanganate was added. The mixture was kept in the ice-water bath for 2 hours, and then transferred from the flask into the thermostat water bath again, and stirred for 30 min at 35 °C. Transfer the mixture in the three-necked flask into an ice water bath and then add 230 ml of deionized water. Finally, react at a constant temperature of 98 °C for 20 min. The reaction mixture was then cooled down naturally to room temperature. Subsequently, the hydrogen peroxide (50 ml) was added and stirred for 10 min. Wash and dry with HCl and deionized water, respectively.
2.1.2 Preparation of CoFe2O4/graphene and CoFe2O4/graphene-N catalysts. The CoFe2O4/graphene catalysts was prepared by the hydrothermal method.21 0.12 g GO was added to 60 ml anhydrous alcohol under ultrasonic for 30 min, as solution A. Another solution was to add a certain amount of cobalt nitrate and ferric nitrate to 20 ml absolute alcohol, namely solution B. Solution B was then added to solution A, and stirred for 30 minutes; after that, 2.16 g sodium acetate was added to continue stirring for 30 minutes, by then crystallized at 200 °C for 12 hours. In the meantime, the loads of 1CoFe2O4/graphene, 4CoFe2O4/graphene, 7CoFe2O4/graphene and 11CoFe2O4/graphene were prepared by changing the amount of cobalt nitrate and ferric nitrate added respectively. Adding solution B into A and adding 1 ml ammonia to prepare CoFe2O4/graphene-N, the preparation process is the same as above.
2.2 Evaluation of denitrification activity of the catalysts
The denitrification activity of the catalysts was tested with Shanghai Jiangke QJK45 denitrification experimental facility with 0.3 g catalysts. N2 was used as balanced gas; NH3 500 ppm; NO 500 ppm; SO2 100 ppm; O2 5%; H2O 3%; the total gas flow was 100 ml min−1; the reaction temperature was 150–400 °C. The conversion rate of NOx was calculated according to the content of NOx at the inlet and outlet at 150, 200, 250, 300, 350 and 400 °C respectively. The NOx content of the inlet gas was marked as [CNOx]in, and the NOx content of the outlet gas was marked as [CNOx]out. NOx conversion rate is calculate as: |
 | (1) |
2.3 Catalysts characterization
The crystal structure of the catalysts was characterized by Smart lab X-ray diffraction (XRD) of Nippon Science Corporation, with a scanning range of 5–80 degree, an operating current of 200 mA and an operating voltage of 45 kV. Hitachi H-7650 transmission electron microscopy (TEM) was used to characterize the microstructures of the samples (resolution 0.2 nm, acceleration voltage 40–120 kV, magnification 60
000×). The specific surface area, pore size distribution and pore volume of the catalysts was characterized by Autosorb IQ of Conta Instruments Company, USA. Thermo Fisher's ESCALAB250XI X-ray photoelectron spectroscopy (XPS) was used to characterize the surface chemical composition and the chemical state of each element. The surface acidity of the catalysts was characterized by temperature programmed desorption (NH3-TPD) of AutoChem 2920 NH3, an American company. AutoChem 2920 H2 temperature programmed reduction (H2-TPR) was used to characterize and analyze the redox performance of the catalysts.
3. Results and discussion
3.1 Structure and microstructure analysis of catalysts
Fig. 1 shows the XRD patterns of the graphene oxide (GO), CoFe2O4, CoFe2O4/graphene, and CoFe2O4/graphene-N. The XRD diagram of GO in Fig. 1(a) finds the strong diffraction peak of GO appears at 12 degrees, which indicates that the oxide of graphite has been successfully synthesized.22 It can be seen from Fig. 1(a) that the obvious diffraction peaks are observed at 30.0, 35.4, 43.4, 57.1 and 62.7 degrees respectively. According to the PDF card, namely PDF#03-0864, CoFe2O4 has been successfully synthesized. Fig. 1(b) XRD patterns of CoFe2O4/graphene catalysts with different CoFe2O4 loadings show that there are obvious characteristic peaks of graphene at 25.2 degrees,23 proving that graphene oxide has been successfully reduced during the preparation of the catalysts. At the same time, the diffraction peaks of CoFe2O4 can be observed, indicating that CoFe2O4/graphene catalysts has been successfully synthesized.
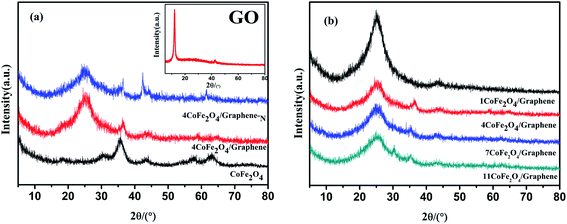 |
| Fig. 1 XRD patterns of (a) GO, CoFe2O4, CoFe2O4/graphene, CoFe2O4/graphene-N, (b) CoFe2O4/graphene catalysts with different loadings. | |
Fig. 2 reveals CoFe2O4 nanoparticles distribute on the surface of graphene. From the TEM diagram of CoFe2O4/graphene, it can be found that the active components are aggregated, and the distribution of CoFe2O4 in CoFe2O4/graphene-N catalysts is more uniform. The results show that nitrogen doped was beneficial to the uniform distribution of the active components and to make a good contact with the reactants in NH3-SCR test, thereby enhancing the reactivity of the catalysts.
 |
| Fig. 2 TEM patterns of CoFe2O4/graphene (a) and CoFe2O4/graphene-N (b). | |
Fig. 3 shows nitrogen adsorption–desorption isotherms of CoFe2O4/graphene and CoFe2O4/graphene-N. It can be seen from the diagram that all types of catalytic isotherms are IV type and the lagging ring type is H1 type. The results show that the catalysts of CoFe2O4/graphene and CoFe2O4/graphene-N contain typical mesoporous structures, and the isotherm hysteresis is related to the existence of voids.
 |
| Fig. 3 Nitrogen adsorption–desorption isotherms of CoFe2O4/graphene and CoFe2O4/graphene-N. | |
Table 1 is the specific surface area, pore volume and pore size parameters of GO, CoFe2O4/graphene and CoFe2O4/graphene-N catalysts. It was found that the specific surface area of CoFe2O4/graphene-N catalysts was reduced, but its denitrification activity was higher than that of CoFe2O4/graphene catalysts. This indicated that the denitrification activity of the catalysts was not only related to the specific surface area but also to the acidic site and redox performance of the catalysts.
Table 1 The specific surface area, pore volume and average pore size of GO, CoFe2O4/graphene and CoFe2O4/graphene-N
Sample |
SBET (m2 g−1) |
VTotal (cm3 g−1) |
Average pore size (nm) |
GO24 |
337 |
1.290 |
3.820 |
CoFe2O4/graphene |
58 |
0.268 |
3.828 |
CoFe2O4/graphene-N |
40 |
0.158 |
3.825 |
3.2 Nitrogen-doped enhances the denitrification activity of CoFe2O4/graphene-N catalysts
Fig. 4 shows the CoFe2O4/graphene catalysts of different loadings and the denitrification activity of CoFe2O4/graphene-N. It can be seen from the graph that the denitrification activity of CoFe2O4/graphene catalysts with different loading amount increases with the increase of the reaction temperature when it is less than 250 °C. When the reaction temperature is at 250 °C, the conversion of NOx of all catalysts is above 95%, which indicates that the catalysts have good denitrification activity at low temperature. The SCR catalytic activity of CoFe2O4/graphene catalyst increases and then decreases with the increasing of the loadings. Compared with CoFe2O4/graphene catalysts of 1%, 7% and 11% loading respectively, CoFe2O4/graphene catalysts with 4% loading have the highest denitrification conversion in the range of 200–400 °C, indicating that the optimum loading of the prepared CoFe2O4/graphene catalysts was 4%. Compared with 4CoFe2O4/graphene catalysts, 4CoFe2O4/graphene-N catalyst exhibits higher denitrification activity at low temperature in the range of 150–300 °C. It is due to the more uniform distribution of CoFe2O4 after nitrogen doped. It is also related to the acidic site, redox performance of the catalysts and the synergetic effect between CoFe2O4 and N-doped graphene support. The literature reported the synergetic effect can enhance photocatalytic activity and photostability.25,26 Compared with the reported supported catalysts, CoFe2O4/graphene-N catalysts have better denitrification activity (Table 2).27–29
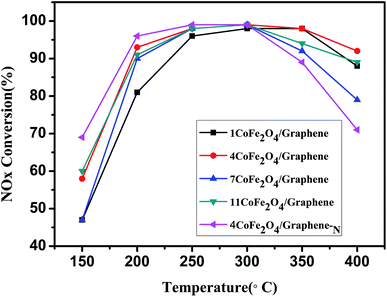 |
| Fig. 4 NH3-SCR activity of CoFe2O4/graphene catalysts with different loadings and CoFe2O4/graphene-N catalysts. Reaction conditions: NH3 (500 ppm), NO (500 ppm), O2 5%, N2 as balanced gas, total gas flow (100 ml min−1). | |
Table 2 The catalytic activities of the reported denitrification catalysts
Catalysts |
NOx conversion (temperature range) |
GHSV |
References |
Cu-ZSM-5 |
≥80% (250–350 °C) |
80 000 h−1 |
27 |
CeO2–ZrO2/TiO2 |
≥80% (250–350 °C) |
71 400 h−1 |
28 |
CeO2/Al2O3 |
≥90% (300–400 °C) |
7200 h−1 |
29 |
3.3 Nitrogen-doped enhances the denitrification mechanism of CoFe2O4/graphene-N catalysts
Fig. 5(a) is a wide scan of XPS spectrum of CoFe2O4/graphene and CoFe2O4/graphene-N. The binding energy at 284.6 eV, 529.8 eV, 711.6 eV and 780.9 eV attributes to C 1s, O 1s, Fe 2p and Co 2p, respectively.30 Fig. 5(b) is a C 1s XPS diagram of CoFe2O4/graphene and CoFe2O4/graphene-N. The peaks at 284.6 eV and 286.5 eV belong to the C
C and C–O functional groups of graphene, respectively.31 The C–N bonds were also detected at 285.6 and 287.1 eV, which is attributed to sp2 and sp3 bonded C–N, respectively.32 Fig. 5(c) is a Fe 2p XPS diagram of CoFe2O4/graphene and CoFe2O4/graphene-N. The Fe 2p spectrum shows two peaks at 711.1 eV and 725.1 eV, which can be assigned to Fe 2p3/2 and Fe 2p1/2, respectively, indicating the presence of Fe3+.33 Fig. 5(d) is a Co 2p XPS diagram of CoFe2O4/graphene and CoFe2O4/graphene-N. The Co 2p spectrum shows two peaks at 781.0 eV and 786.6 eV, which can be attributed to Co 2p3/2 and its satellite peak. Other peaks are observed at 796.6 eV and 802.8 eV corresponding to the Co 2p1/2 and its satellite peak, indicating the presence of Co2+.34 It indicates that CoFe2O4/graphene and CoFe2O4/graphene-N catalysts have been successfully synthesized, which is consistent with the XRD results. Fig. 5(e) is the N 1s XPS diagram of CoFe2O4/graphene-N. The peak at 398.8 eV belongs to pyridinic nitrogen; the peak at 399.8 eV belongs to pyrrolic nitrogen; and the peak at 401.6 eV belongs to graphitic nitrogen.35 Table 3 exhibits the percentage of pyridinic nitrogen, pyrrolic nitrogen, graphitic nitrogen for the CoFe2O4/graphene-N according to the XPS. The percentage of pyridinic nitrogen, pyrrolic nitrogen, graphitic nitrogen for CoFe2O4/graphene-N is 42.42%, 35.89% and 21.69%, respectively. Among the three nitrogen species, pyridinic nitrogen is considered as the main active site for catalyzing oxygen reduction reaction, which can effectively improve the catalytic performance of CoFe2O4/graphene-N.36 Fig. 5(f) is the O 1s XPS diagram of CoFe2O4/graphene and CoFe2O4/g-N. The characteristic peaks of lattice oxygen (Oβ) at 530.4 eV, adsorb oxygen (Oα) at 531.7 eV and surface oxygen (Oγ) at 533.6 eV can be clearly seen from Fig. 5. It can be seen that the adsorbed oxygen (Oα) ratio is calculated by Oα/(Oα + Oβ) for CoFe2O4/graphene and CoFe2O4/graphene-N. The calculated Oα ratio (42.9%) of CoFe2O4/graphene is slightly higher than that (40.3%) of CoFe2O4/graphene-N. Surface adsorbed oxygen (Oα) has higher mobility than lattice oxygen (Oβ) in SCR reaction,37 which is helpful to improve the denitrification activity of catalysts, which is consistent with the test results of denitrification activity of catalysts. It means that the high denitrification activity of the CoFe2O4/graphene-N catalysts is related to other factors.
 |
| Fig. 5 (a) XPS spectra of CoFe2O4/graphene and CoFe2O4/graphene-N (b) C 1s XPS spectra of CoFe2O4/graphene and CoFe2O4/graphene-N (c) Fe 2p XPS spectra of CoFe2O4/graphene and CoFe2O4/graphene-N (d) Co 2p XPS spectra of CoFe2O4/graphene and CoFe2O4/graphene-N (e) N 1s XPS spectra of CoFe2O4/graphene-N (f) O 1s XPS spectra of CoFe2O4/graphene and CoFe2O4/graphene-N. | |
Table 3 Percentage of pyridinic nitrogen, pyrrolic nitrogen, graphitic nitrogen of CoFe2O4/graphene-N from the XPS
Catalysts |
Pyridinic nitrogen/% |
Pyrrolic nitrogen/% |
Graphitic nitrogen/% |
CoFe2O4/graphene-N |
42.42% |
35.89% |
21.69% |
Fig. 6 is the NH3-TPD diagram of CoFe2O4/graphene and CoFe2O4/graphene-N. It can be seen that CoFe2O4/graphene and CoFe2O4/graphene-N catalysts have two desorption peaks. Comparing the two curves, CoFe2O4/graphene-N catalysts have higher peak temperature and peak area than CoFe2O4/graphene catalysts. This indicates that the acid strength and quantity of CoFe2O4/graphene-N catalysts are superior to that of CoFe2O4/graphene catalysts, and the increase of acid sites of catalysts promotes the denitrification activity of catalysts.38
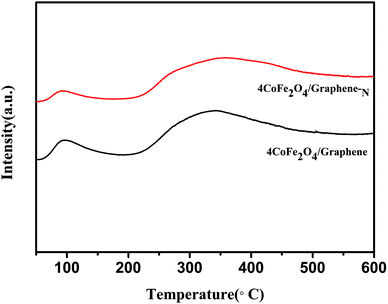 |
| Fig. 6 NH3-TPD diagram of CoFe2O4/graphene and CoFe2O4/graphene-N. | |
Fig. 7 is the H2-TPR diagram of CoFe2O4/graphene and CoFe2O4/graphene-N catalysts. As is shown, the reduction peaks of CoFe2O4/graphene and CoFe2O4/graphene-N catalysts occur at 462 °C and 388 °C respectively. Compared with CoFe2O4/graphene, the peak of CoFe2O4/graphene-N moved to low temperature, indicating that the catalysts have better reduction performance at low temperature. In addition, the reduction peak area of CoFe2O4/graphene-N catalysts increases, indicating that the redox performance of the catalysts increases, thus increasing the denitrification activity of the catalysts.39
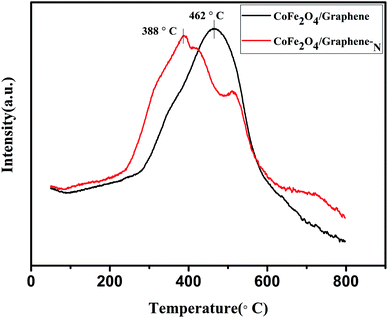 |
| Fig. 7 H2-TPR diagram of CoFe2O4/graphene and CoFe2O4/graphene-N. | |
3.4 Test of water and sulfur resistance of CoFe2O4/graphene and CoFe2O4/graphene-N catalysts
Fig. 8 is a test of water and sulfur resistance of CoFe2O4/graphene and CoFe2O4/graphene-N catalysts. It is obvious that the denitrification activity of CoFe2O4/graphene-N is higher than that of CoFe2O4/graphene, indicating that nitrogen doped is beneficial to improving the water and sulfur resistance of the catalysts. The denitrification activity of CoFe2O4/graphene and CoFe2O4/graphene-N catalysts is tested in the presence of SO2. The denitrification conversion rate of CoFe2O4/graphene-N catalysts is relatively poor when the reaction temperature is below 250 °C. The reason was that SO2 reacts with NH3 to form sulfate that covers the active sites of the catalysts and blocks the channels of the catalysts, which weakens the catalytic activity. At the high temperature, SO2 on the surface of the catalysts is converted to SO42−, resulting in the increase of surface acidity of the catalysts and the enhancement of the denitrification activity of the catalysts.40 The poor water resistance of CoFe2O4/graphene and CoFe2O4/graphene-N catalysts is attributed to the competitive adsorption of H2O and reactive gases (NH3, O2, NO) on the surface of the catalysts, and the hydroxyl groups generated by the adsorbed water on the surface of the catalysts neutralize the acidic sites on the surface of the catalysts, resulting in the deterioration of the denitrification activity of the catalysts.41
 |
| Fig. 8 The effect of SO2 and H2O on NOx conversion over CoFe2O4/graphene and CoFe2O4/graphene-N. Reaction conditions: NH3 (500 ppm), NO (500 ppm), O2 5%, SO2 (100 ppm), H2O 3%, N2 as balanced gas, total gas flow (100 ml min−1). | |
3.5 Repeatability test of CoFe2O4/graphene-N catalyst
Fig. 9 shows the repeatability of CoFe2O4/graphene-N catalyst for four times. It can be seen from the Fig. 9 that the denitrification activity of the reused CoFe2O4/graphene-N (four times) significantly decreased under 250 °C compared with the fresh catalyst. However, it is interesting that the activity of the reused catalyst can basically maintain invariable in the temperature of 250–300 °C. In addition, the reused CoFe2O4/graphene-N do not significantly decrease the conversion of NOx in the range of temperature from 300 °C to 400 °C.
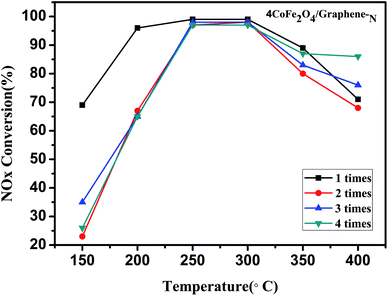 |
| Fig. 9 Repeatability of CoFe2O4/graphene-N catalyst. | |
4. Conclusions
CoFe2O4/graphene catalysts and CoFe2O4/graphene-N catalysts were prepared. When the loading amount is 4%, the denitration activity of the catalysts is the best, and the conversion rate of NOx reaches 99% at 250–300 °C. TEM showed that nitrogen doped made the distribution of the active components more uniform on the carrier. NH3-TPD and H2-TPR showed that nitrogen doped resulted in more acidic sites on the surface of the catalysts and improved the redox performance of the catalysts. CoFe2O4/graphene-N has better denitrification activity at low temperature than CoFe2O4/graphene, and the conversion rate of NOx reaches more than 95% at 200–300 °C.
Conflicts of interest
There are no conflicts to declare.
Acknowledgements
This article was supported by National Natural Science Foundation of China (51708309), Heilongjiang Provincial Natural Science Foundation (QC2017065), The Fundamental Research Funds in Heilongjiang Provincial Universities (No. 135109103), Specialized Subject of Plant Food Processing Technology of Heilongjiang Education Department (YSTSXK201872), Qiqihar University Graduate Student Innovative Research Projects (YJSCX2018-032X).
References
- K. W. Zha, S. X. Cai, H. Hu, H. R. Li, T. T. Yan, L. Y. Shi and D. S. Zhang, J. Phys. Chem. C, 2017, 121, 25243–25254 CrossRef CAS.
- X. L. Li and Y. H. Li, React. Kinet., Mech. Catal., 2014, 112, 27–36 CrossRef CAS.
- H. Q. Wang, X. B. Chen, S. Gao, Z. B. Wu, Y. Liu and X. L. Weng, Catal. Sci. Technol., 2013, 3, 715–722 RSC.
- X. Y. Shi, F. D. Liu, L. J. Xie, W. P. Shan and H. He, Environ. Sci. Technol., 2013, 47, 3293–3298 CrossRef CAS PubMed.
- J. Grzybek, B. Gil, W. J. Roth, M. Skoczek, A. Kowalczyk and L. Chmielarz, Spectrochim. Acta, Part A, 2018, 196, 281–288 CrossRef CAS PubMed.
- C. Z. Shao, X. F. Liu, D. M. Meng, Q. Xu, Y. L. Guo, Y. Guo, W. C. Zhan, L. Wang and G. Z. Lu, RSC Adv., 2016, 6, 66169–66179 RSC.
- C. A. Zhang, T. H. Chen, H. B. Liu, D. Chen, B. Xu and C. S. Qing, Appl. Surf. Sci., 2018, 457, 1116–1125 CrossRef CAS.
- W. L. Ma, H. Li, Q. Xu, Y. Zhang, W. Wang and J. D. Wang, New J. Chem., 2018, 42, 14757–14765 RSC.
- J. M. Feng, X. H. Zhong, G. Z. Wang, L. Dong, X. F. Li and D. J. Li, J. Mater. Sci., 2016, 52, 3124–3132 CrossRef.
- X. Y. Liu, Q. Li, J. N. Shu and H. Cui, J. Mater. Chem. C, 2017, 5, 7612–7620 RSC.
- N. Dong, F. Z. He, J. L. Xin, Q. Z. Wang, Z. Q. Lei and B. T. Su, Mater. Res. Bull., 2016, 80, 186–190 CrossRef CAS.
- M. Sundararajan, L. John Kennedy, P. Nithya and J. Judith Vijaya, J. Phys. Chem. Solids, 2017, 108, 61–75 CrossRef CAS.
- B. Y. Ren, W. Shen, L. Li, S. Z. Wu and W. Wang, Appl. Surf. Sci., 2018, 447, 711–723 CrossRef CAS.
- P. A. Vinosha, B. Xavier, S. Krishnan and S. J. Das, J. Nanosci. Nanotechnol., 2018, 18, 5354–5366 CrossRef CAS PubMed.
- Q. A. Zhao, H. B. Zhao, L. Yan, M. X. Bi, Y. W. Li, Y. Q. Zhou, Z. J. Song and T. S. Jiang, J. Nanosci. Nanotechnol., 2017, 17, 3951–3958 CrossRef CAS.
- S. H. Wu, H. J. He, X. Li, C. P. Yang, G. M. Zeng, B. Wu, S. Y. He and L. Lu, et al., Chem. Eng. J., 2018, 341, 126–136 CrossRef CAS.
- Y. J. Yao, Z. H. Yang, D. W. Zhang, W. C. Peng, H. Q. Sun and S. B. Wang, Ind. Eng. Chem. Res., 2012, 51, 6044–6051 CrossRef CAS.
- W. Y. Bian, Z. R. Yang, P. Strasser and R. Z. Yang, J. Power Sources, 2014, 250, 196–203 CrossRef CAS.
- F. Yang, L. T. Jia, B. Hou, D. B. Li, J. G. Wang and Y. H. Sun, J. Phys. Chem. C, 2014, 118, 268–277 CrossRef.
- Y. B. Shao, T. Jing, J. Z. Tian and Y. J. Zheng, RSC Adv., 2015, 5, 103943–103955 RSC.
- S. L. Ma, S. H. Zhan, Y. N. Jia and Q. X. Zhou, ACS Appl. Mater. Interfaces, 2015, 7, 10576–10586 CrossRef CAS PubMed.
- Y. P. Dou, J. J. Peng, W. Li, M. Li, H. H. Liu and H. M. Zhang, J. Nanopart. Res., 2015, 17, 489 CrossRef.
- C. R. Minitha and R. T. Rajendrakumar, Adv. Mater. Res., 2013, 678, 56–60 Search PubMed.
- P. Li, Z. F. Li, C. Geng, Y. Kang, C. Zhang and C. L. Yang, Chin. J. Inorg. Chem., 2018, 34, 2205–2210 Search PubMed.
- Y. Lin, S. H. Wu, X. Li, X. Wu, C. P. Yang, G. M. Zeng, Y. R. Peng, Q. Zhou and L. Lu, Appl. Catal. B Environ., 2018, 227, 557–570 CrossRef CAS.
- Y. Lin, S. H. Wu, C. P. Yang, M. Chen and X. Li, Appl. Catal. B Environ., 2019, 245, 71–86 CrossRef CAS.
- Q. Yuan, Z. Y. Zhang, N. S. Yu and B. Dong, Catal. Commun., 2018, 108, 23–26 CrossRef CAS.
- Q. J. Jin, Y. S. Shen, S. M. Zhu, X. H. Li and M. Hu, Chin. J. Catal., 2016, 37, 1521–1528 CrossRef CAS.
- W. Yan, Y. S. Shen, S. M. Zhu, Q. J. Jin, Y. L. Liu and X. H. Li, Catal. Lett., 2016, 146, 1221–1230 CrossRef CAS.
- S. L. Zhang, Q. Z. Jiao, J. Hu, J. J. Li, Y. Zhao, H. S. Li and Q. Wu, J. Alloys Compd., 2015, 630, 195–201 CrossRef CAS.
- L. X. Zheng, L. T. Guan, G. Yang, S. M. Chen and H. J. Zheng, RSC Adv., 2018, 8, 8607–8614 RSC.
- F. Nie, J. J. Shi, W. C Du, W. S. Ning, Z. Y. Hou and F. S. Xiao, J. Mater. Chem. A, 2013, 1, 9037–9045 RSC.
- H. Xia, D. D. Zhu, Y. S. Fu and X. Wang, Electrochim. Acta, 2012, 83, 166–174 CrossRef CAS.
- M. Zhang, X. Yang, X. F. Kan, X. Wang, L. Ma and M. Q. Jia, Electrochim. Acta, 2013, 112, 727–734 CrossRef CAS.
- S. H. Li, H. Miao, Q. Xu, Y. J. Xue, S. S. Sun, Q. Wang and Z. P. Liu, RSC Adv., 2016, 6, 99179–99183 RSC.
- E. J. Biddinger, D. von Deak and U. S. Ozkan, Top. Catal., 2009, 52, 1566–1574 CrossRef CAS.
- Y. Jiang, Z. M. Xing, X. C. Wang, S. B. Huang, Q. Y. Liu and J. S. Yang, J. Ind. Eng. Chem., 2015, 29, 43–47 CrossRef CAS.
- Z. M. Liu, S. X. Zhang, J. H. Li and L. L. Ma, Appl. Catal. B Environ., 2014, 144, 90–95 CrossRef CAS.
- H. F. Li, G. Z. Lu, Q. G. Dai, Y. Q. Wang, Y. Guo and Y. L. Guo, Appl. Catal. B Environ., 2011, 102, 475–483 CrossRef CAS.
- R. B. Jin, Y. Liu, Z. B. Wu, H. Q. Wang and T. T. Gu, Catal. Today, 2010, 153, 84–89 CrossRef CAS.
- C. C. Xu, W. Sun, L. M. Cao, T. T. Li, X. X. Cai and J. Yang, Chem. Eng. J., 2017, 308, 980–987 CrossRef CAS.
|
This journal is © The Royal Society of Chemistry 2019 |
Click here to see how this site uses Cookies. View our privacy policy here.