DOI:
10.1039/C9RA10183G
(Paper)
RSC Adv., 2019,
9, 42430-42437
Cs4PbBr6/CsPbBr3 perovskite composites for WLEDs: pure white, high luminous efficiency and tunable color temperature
Received
5th December 2019
, Accepted 15th December 2019
First published on 20th December 2019
Abstract
Cs4PbBr6/CsPbBr3 perovskite composites are fabricated by room-temperature one-pot mixing synthesis, which is short in time, free from inert gases and delivers a high product yield. Temperature-dependent photoluminescence shows that a larger exciton binding energy of 291.1 meV exhibits better thermal stability compared with that of pure Cs4PbBr6 and CsPbBr3 materials. The CIE chromaticity coordinates (0.1380, 0.7236) of green LEDs designed with Cs4PbBr6/CsPbBr3 perovskite composites show almost no variation under driving current changing from 5 to 30 mA. Furthermore, the ground Cs4PbBr6/CsPbBr3 perovskite composites mixed with red emitting K2SiF6:Mn4+ phosphor are dropped and casted on a blue-emitting InGaN chip. The white light emitting diodes (WLEDs) are presented, which have good luminous efficiency of 65.33 lm W−1 at 20 mA, a correlated color temperature of 5190 K, and the white gamut with chromaticity coordinate of (0.3392, 0.3336). According to the state of art, these excellent characteristics observed are much superior to the reported results of conventional perovskite-based WLEDs, which demonstrate the immense potential and great prospect of Cs4PbBr6/CsPbBr3 perovskite composites to replace conventional phosphors in lighting devices.
1 Introduction
An increasing awareness of the necessity for energy conservation has directed scientific research to develop various energy-saving materials and techniques for use in displays and lighting applications.1 In this context, white light emitting diodes (WLEDs) promise great potential to replace traditional incandescent white light sources because of their significantly economic and technological advantages in energy conservation. On all counts, commercial WLEDs have been adopted as a combination of an InGaN blue chip with a YAG: Ce3+ yellow phosphor.2 The red and green phosphors are used to realize a high color rendering index and color tuning with adding red and green phosphors for trichromatic LEDs.3 Traditional phosphors, delivering up to 150–230 lm W−1 of luminous efficiency LEDs,4 rely solely on using combinations of rare-earth ions.5,6 The use of these rare-earth based phosphors is restricted by some intrinsic optical defects, limited and hard preparation conditions, high cost, toxicity and pollution in mining and refining, as well as the requirement of limited resource.7,8 Accordingly, an immense and challenging assignment concernful to modern solid-state lighting is the discovery of highly efficient phosphors free of rare-earth elements.9
Recently, luminescent metal-halide perovskite semiconductors have attracted enormous attention owing to their excellent optoelectronic properties such as high quantum yield,10,11 chromatogram purity,12 wide wavelength (400–800 nm) tunability and narrow emission linewidth,13,14 which enable them to achieve promising applications in phosphor-converted LEDs,15,16 solar cells17,18 and photodetectors.19,20 Among them, cesium lead bromine has emerged as a promising optoelectronic material and attracted an enormous amount of interests. It is a medium-bandgap semiconductor which can be synthesized cost-effectively on large scales through simple solution-based processes.21,22 In particular, the rapid advances in perovskite materials are drawn significant attention to nanocrystals (NCs) based on the perovskite for use in WLEDs. For example, both CsPbBr3 NCs23 and Cs4PbBr6/CsPbBr3 nanocomposites24 as the visible color emitting materials are combined with a blue LED chip and conventional phosphors such as CaAlSiN3:Eu2+. Unfortunately, colloidal CsPbBr3 NCs are found to show relatively poor thermal stability because of the damage of ligands and the ensuing particle aggregation or fusion at elevated temperature, reflected by the rapid PL quenching and ripening of the NCs.25 CsPbBr3 NCs imbedded in a Cs4PbBr6 host matrix achieve photoluminescence quantum yield (PLQY) up to 90% (ref. 26) in contrast to very low light yield from bulk single crystal or polycrystalline CsPbBr3.27 The thermal stability of PL for CsPbBr3 NCs is enhanced due to the passivation of Cs4PbBr6 host matrix.24,28 In these senses, Cs4PbBr6/CsPbBr3 perovskite composites are promising candidates to replace ordinary phosphors for future solid-state lighting technology. The optical performance of these perovskites is impressive, several challenging issues, such as the ability to perform large-scale synthesis as well as the product yield, remain inevitable obstructions for practical applications in optoelectronic devices. Furthermore, in the WLEDs working process, the influence of operating time and driving current is obvious. Although the luminous efficiency and CIE coordinates of perovskite-based WLEDs are reported, to the best of our knowledge, there are no comprehensive reported on parameters in these regards.
In this work, we use a facile and rapid approach for the synthesis of high-yield Cs4PbBr6/CsPbBr3 perovskite composites at room temperature. The strong green PL from Cs4PbBr6/CsPbBr3 composites is observed, and the characterization and temperature-dependent PL of them are investigated. Here, pure and stable WLED devices are fabricated by combining the highly luminescent Cs4PbBr6/CsPbBr3 composites as green emitters and commercial K2SiF6:Mn4+ phosphors as red emitters with blue-emitting InGaN chips. Moreover, the optoelectronic characteristics of the WLEDs under different driving current and treating time are investigated in detail.
2 Experimental technique
2.1 Materials and chemicals
Lead bromide (PbBr2, 99%, Macklin), cesium acetate (CsAc, 99%, Aladdin), HBr water solution (48% by weight in H2O, Macklin), Dimethyl sulfoxide (DMSO, 99.8%, Macklin), K2SiF6:Mn4+, silicone gel A and B, and blue LED chip (460 nm, 1 W, looking long). All of these chemicals are used without any further purification.
2.2 Preparation of perovskite composites
Here, the perovskite composites are prepared based on the modified one-pot mixing method through the reaction of CsAc and PbBr2 powder in DMSO with aqueous HBr solution.29 In detail, 0.22 mmol of PbBr2 and 0.88 mmol of CsAc are dissolved in 0.9 mL of DMSO, which are stirred in a closed beaker for 30 minutes at room temperature to form the precursor solution. Then, 0.1 mL of aqueous HBr solution is slowly injected into the precursor solution to induce the reaction via stirring. Limited by the solubility of CsBr in DMSO, in order to obtain a higher concentration of precursor solution, we use CsAc with higher solubility instead of CsBr as the Cs source and PbBr2 as the Pb source. Meanwhile, aqueous HBr solution is used to make up for the deficiency of Br in CsAc. Immediately, yellow-green precipitates can be observed in the mixed solution, which is stirred 6 h at room temperature. The precipitation is separated from the mixed solution by centrifugation at 4000 rpm for 5 minutes and washed once with 0.2 mL DMSO. After this purification process, the powder is collected and dried at 50 °C for 12 h under vacuum. The solvent (DMSO) used in this work is 0.9 mL unless otherwise noted.
2.3 Construction of WLEDs
The perovskite composites are used as phosphors to fabricate WLEDs. A blue LED chip, emitting at 460 nm, is attached on the bottom of the reflector cup by using conductive silver paste. In a typical procedure, 0.05 g perovskite composites with peak wavelength centered at 521 nm are mixed with 0.05 g K2SiF6:Mn4+ phosphors emitting at 630 nm, then mixing them with 1 mL silicone gel A and B (0.2 mL of A, 0.8 mL of B). Afterward, removing the bubbles in the silicone gel in a vacuum chamber and overcoating the mixture on the chip. After that, capping the reflector cup with an optical lens. Finally, the chip is dried at 50 °C for 2 h.
2.4 Characterization
Powder X-ray diffraction (XRD) pattern is recorded with a powder diffractometer (Dmax2500, Rigaku) using Cu Kα radiation (λ = 0.154 nm). Photoluminescence (PL) spectra are recorded on a spectrometer (HR4000CG-UV-NIR, Ocean Optics). The temperature-related PL of Cs4PbBr6/CsPbBr3 composites is evaluated using a vacuum liquid-nitrogen cryostat (Cryo-77, Oriental Koji) and a continuous-wave (CW) laser (UV-FN-405-200 mW, CNI) at 405 nm with the capability to give the temperature variation from 100 to 400 K. The PL dynamics are excited by 200 ps laser pulses at 450 nm and measured by a time-correlated single photon counting (TCSPC) system from Boston Electronics with the time resolution of 200 ps to reveal the process of exciton recombination. Photoelectric parameters including electroluminescence (EL) spectra, luminous efficiency (LE), color rendering index (CRI), correlated color temperature (CCT), and Commission Internationale de L'Eclairage (CIE) chromaticity coordinates are evaluated using the spectrometer connected to an integrating sphere (HP30, Hopoo) with an optical fiber under the different operating current.
3 Results and discussions
3.1 Synthesis and characterization of Cs4PbBr6/CsPbBr3 composites
Herein, we use a one-pot reaction strategy to realize the high yield room temperature synthesis of novel perovskite-related Cs4PbBr6/CsPbBr3 semiconductors. As shown in Fig. 1a, the high product yield of 86.2%, 80.1%, 70.9%, 67.5%, and 59.3% are obtained by adding different amounts (0.6, 0.7, 0.8, 0.9, 1.0 mL, respectively) of DMSO solvent. It's commonly known that DMSO is a good solvent for CsPbBr3 NCs but not for micron-sized Cs4PbBr6, so after washing with DMSO, the precipitation is Cs4PbBr6/CsPbBr3 perovskite composites.30 The possible conversion reactions can be the following: |
PbBr2 + 4CsAc + 4HBr → Cs4PbBr6
| (1) |
|
PbBr2 + CsAc + HBr → CsPbBr3 (rarely, embedded in Cs4PbBr6)
| (2) |
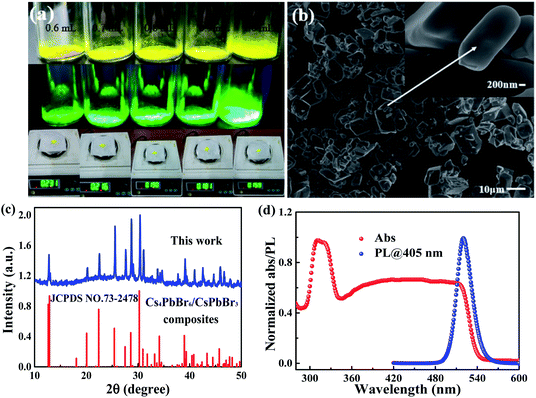 |
| Fig. 1 (a) Images of the Cs4PbBr6/CsPbBr3 perovskite composites under daylight (top) and UV light (365 nm) (middle). The bottom from left to right is the product yield of 86.2%, 80.1%, 70.9%, 67.5%, 59.3%, respectively. (b) SEM image, (c) XRD pattern and (d) absorption, PL spectra of Cs4PbBr6/CsPbBr3 perovskite composites. | |
Only the micron-sized Cs4PbBr6 and the very small amount of nano-sized CsPbBr3 embedded therein exists in the target product, which makes it easy for us to calculate the yield by element conservation of lead and assuming that the obtained product is all Cs4PbBr6. Here, we emphasize again that this approach of synthesizing perovskites has a high yield, which can be calculated using the following equation, certainly indicating its promising applications in the industry field.
|
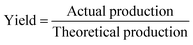 | (3) |
The perovskite composites are characterized using the scanning electron microscope (SEM), which shows irregular morphology and size of Cs4PbBr6/CsPbBr3 perovskite composites on the micrometer scale as shown in Fig. 1b. The inset is observed on 200 nm scale to study more detailed structures. Fig. 1c shows the X-ray diffraction (XRD) pattern of the resulting composites powder. The XRD pattern of the sample matches well with that of rhombohedral Cs4PbBr6 crystals with no obvious difference observed. It should be noted that the unavoidable coexistence of CsPbBr3 NCs with Cs4PbBr6 crystals and the detection limit of XRD measurements is about 5 wt%, the content of CsPbBr3 NCs in Cs4PbBr6/CsPbBr3 composites can't be accurately measured. Consequently, further discussion is much needed to clarify the origin of highly green emission in zero-dimensional Cs4PbBr6 crystals. To our knowledge, no explanation is given for the absorption in the green region for supposedly pure Cs4PbBr6.31 The extreme similarity of wide bandgap Cs4PbBr6 green emission with that of CsPbBr3 NCs, and the green PL in Cs4PbBr6 is often reported to have a very narrow FWHM, this narrow PL matches that of CsPbBr3 NCs. It is believed that the embedded CsPbBr3 NCs are responsible for the highly efficient PL. This viewpoint is further strengthened by direct imaging of CsPbBr3 NCs in Cs4PbBr6.32 In the PL spectrum of the Cs4PbBr6/CsPbBr3 composites, a narrow emission band centered at 521 nm (2.38 eV) with the full width at half maximum (FWHM) of 25 nm (116 meV) are observed at 290 K as seen in Fig. 1d. The result obtained for PL spectrum is similar to CsPbBr3 NCs.33 UV-vis absorption spectrum of the composites shows that absorption onset at 550 nm and a strong absorption peak at 310 nm. Moreover, the PLQY of Cs4PbBr6/CsPbBr3 perovskite composites is determined using a spectrofluorometer equipped with an integrating sphere under the excitation of 365 nm illumination. The result of 32% is obtained for the product when the volume of the solvent (DMSO) is 0.9 mL.
3.2 Photophysical properties of Cs4PbBr6/CsPbBr3 composites
To explore the PL mechanism of Cs4PbBr6/CsPbBr3 perovskite composites, temperature-dependent PL spectra are recorded at the temperature ranging from 100 to 400 K as seen in Fig. 2a. The PL peak at 100 K is as narrow as 13.5 nm and exhibits a temperature-sensitive evolution, i.e., monotonously decreases as the temperature is elevated. The important physical parameter of exciton binding energy, which is vital for excitation and recombination processes of semiconductors, can be estimated according to temperature-dependent PL behavior using Arrhenius equation:34 |
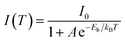 | (4) |
where I(T) and I0 are the integrated PL intensities at temperature T and 0 K, respectively, Eb is the exciton binding energy, and kB is the Boltzmann constant. The corresponding exciton binding energy of Cs4PbBr6/CsPbBr3 perovskite composites is experimentally obtained as 291.1 meV in Fig. 2b, which is higher than pure CsPbBr3 and Cs4PbBr6 crystal,35 and close to that of similar Cs4PbBr6/CsPbBr3 composites,36 Such a large exciton binding energy confirms that PL of Cs4PbBr6/CsPbBr3 perovskite composites mainly occurs through exciton recombination rather than free carrier recombination.37 Interestingly, a significant broadening of the FWHM is observed with an increase of temperature as shown in Fig. 2b, which can be fitted as:28 |
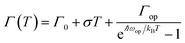 | (5) |
where Γ(T) is the FWHM at temperature T, and Γ0 is the inhomogeneous broadening contribution, which is ascribed to the scattering of excitons by defects or doped carriers and is temperature-independent. σ and Γop are the coupling coefficients of exciton-acoustic phonon and exciton-optical phonon, respectively. The fitting result is shown in Fig. 2b, which indicates that the optical phonon is dominant for the exciton–phonon interactions in the present Cs4PbBr6/CsPbBr3 perovskite composites. Accordingly, the optical phonon energy (ℏωop) involved in the exciton recombination is determined to be 138.9 meV, confirming strong exciton–phonon interactions and weak nonradiative transition for exciton recombination. Finally, an obvious blue-shift of the emission peak position is observed during the temperature increasing from 100 to 220 K as shown in Fig. 2c. It is well known that the excitons will occupy a lower discrete energy state below the conduction band at low temperature. As the temperature is elevated, electrons may migrate from lower energy states to higher ones with the assistance of phonons, resulting in a blue shift in the emission band.38 The related process is shown in the inset of Fig. 2c. But when the temperature gradually from 220 rises to 400 K, the emission band of Cs4PbBr6/CsPbBr3 perovskite composites remains steady. This reveals that composites are less sensitive to relatively high temperature. To further unravel the excitonic recombination mechanism, wavelength-dependent time-resolved PL of Cs4PbBr6/CsPbBr3 perovskite composites are performed. Based on nonlinear least squares fitting, the measured PL decays are fitted and calculated. It can be seen from Fig. 2d that the exciton PL decays are single-exponential, indicating the existence of one emission centers in Cs4PbBr6/CsPbBr3 perovskite composites. As is commonly known, the morphology and the size of crystals influence their optical properties.39 The lifetime decay component becomes longer from 4.2 to 6.4 ns with the change of detection wavelength from 500 to 540 nm, which exhibits the PL lifetime increases steadily with increasing NCs size embedded in Cs4PbBr6 microcrystals consistent with the reported CsPbBr3 NCs.40
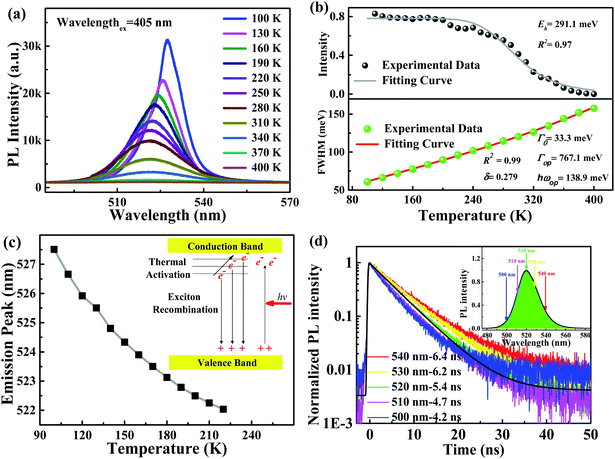 |
| Fig. 2 (a) Temperature-dependent PL spectra of Cs4PbBr6/CsPbBr3 perovskite composites. (b) Integrated PL emission intensity (top), FWHM (bottom). (c) Emission peak as a function of temperature, the inset shows the related process of a thermally-induced exciton emission blue-shift. (d) Wavelength-dependent time-resolved PL. | |
3.3 Applications of Cs4PbBr6/CsPbBr3 composites on WLEDs
In order to study the color stability of perovskite materials, the ultraviolet LEDs with the peak emission at 360 nm and Cs4PbBr6/CsPbBr3 perovskite composites are used to fabricate green perovskite LEDs (green pero-LEDs). The CIE chromaticity coordinates of the green pero-LEDs (0.1380 ± 0.0035, 0.7236 ± 0.0026) are overlapped as displayed in Fig. 3a, and no obvious change with the increasing driving current (5–30 mA), indicating greater color stability of output light.
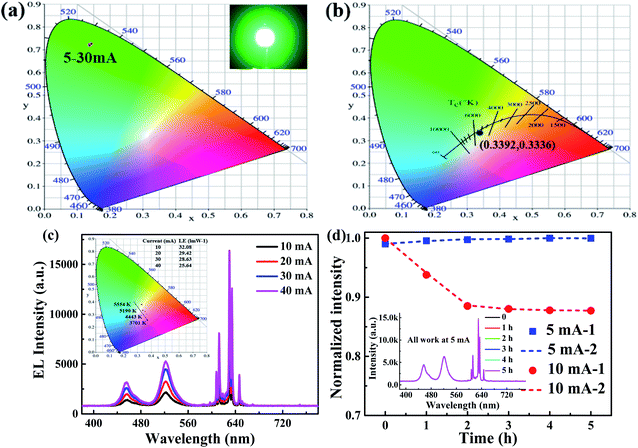 |
| Fig. 3 (a) CIE coordinates of the green pero-LEDs, the inset shows the related photograph of the working LED. (b) Optimized CIE chromaticity coordinates of pero-WLEDs. (c) EL spectra of the constructed pero-WLEDs operated under different driving current, the inset shows overall luminous characteristics at 20 mA. (d) The changes of EL integrated intensity of green band in pero-WLEDs at 5 and 10 mA, respectively. The short dash and square symbols represent our repetitive experiments to increase reliability. The inset shows the EL spectra of the constructed pero-WLEDs operated under 5 mA, which has barely changed within five hours. | |
From the viewpoint of application exploration, the strong PL emission and color stability from Cs4PbBr6/CsPbBr3 perovskite composites are inspired their use in light-emitting applications. EL spectra of perovskite WLEDs (pero-WLEDs) under various driving current are indicated in Fig. 3c, showing three peaks centered at 460, 521 and 630 nm, corresponding to the emission of blue LED chip, Cs4PbBr6/CsPbBr3 perovskite composites and K2SiF6:Mn4+ phosphors, respectively. Blue and green-red emission intensities steadily raise with increased current, revealing that LEDs had stable light-conversion and color quality. The optical parameters of pero-WLEDs at different driving current are shown in the inset of Fig. 3c. With increase in driving current, the CCT of pero-WLEDs is changed from 5554 to 3701 K. Although a slight decrease in luminous efficiency from 32.08 to 25.64 lm W−1 is observed when driving current increases from 10 to 40 mA. After optimization, the maximum luminous efficiency of 65.33 lm W−1 at 20 mA can be obtained by changing the mass ratio of perovskites and K2SiF6:Mn4+ on 1
:
2 (in detail, 0.05 g of Cs4PbBr6/CsPbBr3 perovskite composites, 0.10 g of K2SiF6:Mn4+, both are uniformly mixed in 1 mL of silicone gel A and B (0.2 mL of A, 0.8 mL of B)). These results show that the white light generated from the pero-WLEDs has high color chromatics stability against the increase of driving current, which is consistent with the high photostability of our perovskite materials. We do know that the device performance is comparable to some states of the art WLEDs based on conventional perovskite MCs or NCs, which are summarized and compared with other research groups as shown in Table 1. First, such high luminous efficiency is inseparable from the high PLQY of the product, work has reported that the latter can be further improved by optimizing perovskites structure such as doping of lanthanide ions41 or forming a quasi core/shell structure.42 Second, the PL line-widths of our product are obviously narrower, which is significant for wide color-gamut display. Third, as we known that the CIE coordinates accurately represent the color of the light source, when mass ratio of Cs4PbBr6/CsPbBr3 perovskite composites and K2SiF6:Mn4+ is between 1
:
2 and 1
:
3, optimized color coordinates is generated and reached (0.3392, 0.3336) at 20 mA as shown in Fig. 3b, this value of CIE is almost equal to the standard white light (0.33, 0.33). Last but not the least, high-quality Cs4PbBr6/CsPbBr3 perovskite composites can be formed at room temperature even relatively low temperature, within short time, free from inert gas and injection operation.
Table 1 Parameter comparisons of WLEDs based on Cs4PbBr6/CsPbBr3 perovskite composites and conventional perovskite MCs/NCs-based LEDs
Emitting materials |
LE (lm W−1) |
CIE coordinate |
References |
Mn-doped CsPbBr0.5I2.5 NCs |
29.7 |
(0.3327, 0.3688) |
43 |
Cs4PbBr6 MCs |
9.79 |
(0.3623, 0.3765) |
12 |
Cs4PbBr6 MCs |
13.91 |
(0.2879, 0.2434) |
44 |
CsPbBr3 NCs |
— |
(0.33, 0.30) |
23 |
CH3NH3PbBr3/NaNO3 |
22.39 |
(0.28, 0.32) |
45 |
CH3NH3PbBr3@POSS |
38 |
(0.30, 0.33) |
46 |
CsPbBr3@NH4Br |
— |
(0.36, 0.35) |
47 |
CsPbBr3 NCs |
— |
(0.33, 0.36) |
48 |
CsPb (Br/I)3/POSS |
14.1 |
(0.35, 0.38) |
49 |
CH3NH3PbBr3/SiO2 |
60.5 |
(0.26, 0.25) |
50 |
CH3NH3PbX3 NCs/SiO2 |
61.2 |
(0.33, 0.33) |
51 |
Cs4PbBr6/CsPbBr3 |
65.33 |
(0.3392, 0.3336) |
This work |
Optical stability under operation time is one of the key factors to evaluate the performance of a light emitting device. From Fig. 3d, the EL intensity of the pero-WLEDs still maintains stability of the initial value after 5 h of continuous operation at 5 mA. When the driving current reaches 10 mA, its relative emission intensity declines slowly to 88% after 2 h and then tends to remain constant. In order to further explore the optical performance of pero-WLEDs after working for a period of time. The result in Table 2 illustrates the luminous efficiency dropped by only ∼7% after 4 h of operation at 20 mA, the CIE color coordinate and CCT show the changes from (0.3379, 0.3369) to (0.3461, 0.2632) and 5256 to 4253 K, respectively. Because more current addition will cause mixture stronger emitting of the red versus blue color, and relatively weaker green color in WLEDs due to loss green light. These results demonstrate the highly optical stability of the pero-WLEDs at low current. Additionally, the CRI is measured for this WLEDs with warm perception. It is approximately 60 dues to the deficiency in yellow wave band, and we believe it can be improved further after optimization over the concentrations of phosphors or used the phosphor with a wider band52 in the WLEDs.
Table 2 Overall luminous characteristics with different treating time at 20 mA
Time (h) |
LE (lm W−1) |
CRI |
CCT (K) |
CIE coordinate |
0 |
30.40 |
63.1 |
5256 |
(0.3379, 0.3369) |
1 |
30.29 |
63.8 |
5014 |
(0.3392, 0.2876) |
2 |
29.41 |
62.1 |
4555 |
(0.3442, 0.2742) |
3 |
28.42 |
60.3 |
4375 |
(0.3454, 0.2671) |
4 |
28.27 |
54.3 |
4253 |
(0.3461, 0.2632) |
Obviously, the color temperature of these WLEDs can be tuned through controlling the composites ratio of green and red components. To confirm the change of white target, the Cs4PbBr6/CsPbBr3 phosphor is composited with K2SiF6:Mn4+ phosphor with the mass ratio of 1
:
x (1
:
0, 1
:
0.5, 1
:
1, 1
:
2, 1
:
3 and 1
:
4) as shown in Fig. 4a. With an increasing composite ratio, generated warm-white light due to the addition of the red component, this perfect combination of green and red components is suitable for lighting technology. These results indicate that the relatively low intensity of green color compared to that of red color is suitable for a warm color. And the intensity of green should be stronger to achieve a cool color.
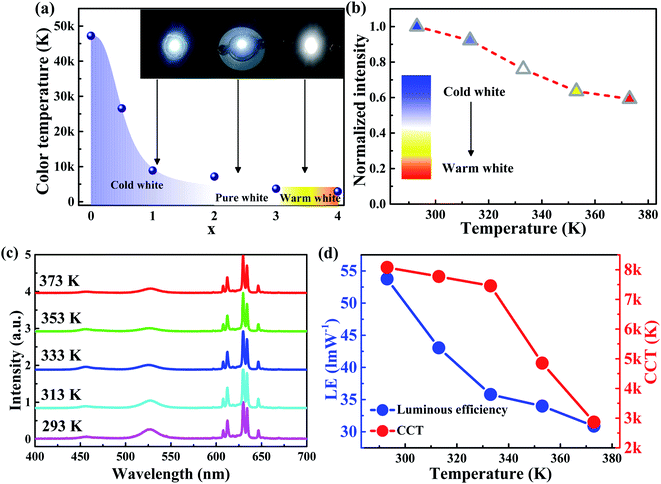 |
| Fig. 4 (a) Color temperatures of pero-WLEDs as a function of mass ratio of green-to-red materials, where x comes from 1 : x. The insets show the related photograph of the working WLEDs. (b) Normalized intensity of green emission peak of the constructed pero-WLEDs operated under different drying temperature of silicone gel and phosphors. (c) EL spectra operating at different temperatures. (d) The changes of LE and CCT with drying temperature. | |
Considering the sensitivity of the perovskite materials to heat, degrees raise in temperature would be remarkably influenced for the stability of the perovskites. As we change the drying temperature of silicone gel and phosphors from 293 to 373 K and keeping the drying time for 2 h, the integrated intensity of the green emission peak of pero-WLEDs decreases as shown in Fig. 4b. Fig. 4c is the EL spectra operating at temperatures 293, 313, 333, 353, 373 K, respectively. We know that perovskite materials are generally unstable at high temperatures, with increasing temperature, the thermal distribution will become worse as more non-emissive NCs generation around could hinder the thermal re-emission. From Fig. 4d, the luminous efficiency of pero-WLEDs decreases from 53.76 to 30.88 lm W−1 and CCT from 8077 to 2866 K at 20 mA on account of the unstable characteristics of the Cs4PbBr6/CsPbBr3 perovskite composites at high temperature.
4 Conclusion
In summary, the Cs4PbBr6/CsPbBr3 perovskite composites are synthesized using a one-pot mixing method, and boast large-scale production possibility. The prepared perovskites show the behavior of excellent luminous properties (PLQY = 32%) with narrow FWHM (25 nm) and large binding energy of 291.1 meV. The optimal device for WLEDs shows favorable white light characteristics with the CIE coordinates, CCT and LE of (0.3392, 0.3336), 5190 K and 65.33 lm W−1, respectively. What is more, excellent optical stability is demonstrated with increasing driving current from 10 to 40 mA. And high device stability is also proved after working 5 h. More importantly, this is a comprehensive report for perovskite-based WLEDs and would provide a new pathway toward low cost, high product yield, and highly efficient perovskites applicable for high-performance WLEDs. We anticipate that further improving the stability of perovskite at high temperature, which will make more leaps and bounds in perovskite phosphors-based WLEDs.
Conflicts of interest
There are no conflicts to declare.
Acknowledgements
The authors are grateful for the financial support from the Project of Scientific Foundation of Returned Overseas Scholars by Heilongjiang Province (LC2017030) and Key Project of Scientific Foundation by Heilongjiang Province (JJ2018ZZ0010).
References
- W. Zhang, G. E. Eperon and H. J. Snaith, Nat. Energy, 2016, 1, 16048–16055 CrossRef CAS.
- P. Li, L. Tan, L. Wang, J. Zheng, M. Peng, Y. Wang and H. Guo, J. Am. Ceram. Soc., 2016, 99, 2029–2034 CrossRef CAS.
- Y. Wang, K. Wang, Z. Han, Z. Yin, C. Zhou, F. Du, S. Zhou, P. Chen and Z. Xie, J. Mater. Chem. C, 2017, 5, 9629–9637 RSC.
- P. Von Dollen, S. Pimputkar and J. S. Speck, Angew. Chem., Int. Ed., 2014, 53, 13978–13980 CrossRef CAS PubMed.
- D. J. Wang, L. Xu, T. C. Gu, L. Ma and H. M. Zhang, Rare Met. Mater. Eng., 2008, 37, 1656–1659 CAS.
- H. Y. Fu, X. S. Qiao, S. Cui, Q. Luo, J. Y. Qian, X. P. Fan and X. H. Zhang, Mater. Lett., 2012, 71, 15–17 CrossRef CAS.
- S.-Y. Kwak, S. Yang, N. R. Kim, J. H. Kim and B.-S. Bae, Adv. Mater., 2011, 23, 5767–5772 CrossRef CAS PubMed.
- I. O. Huyal, U. Koldemir, T. Ozel, H. V. Demir and D. Tuncel, J. Mater. Chem., 2008, 18, 3568–3574 RSC.
- Q. Gong, Z. Hu, B. J. Deibert, T. J. Emge, S. J. Teat, D. Banerjee, B. Mussman, N. D. Rudd and J. Li, J. Am. Chem. Soc., 2014, 136, 16724–16727 CrossRef CAS.
- X. Chen, F. Zhang, Y. Ge, L. Shi, S. Huang, J. Tang, Z. Lv, L. Zhang, B. Zou and H. Zhong, Adv. Funct. Mater., 2018, 28, 1706567–1706573 CrossRef.
- Q. Shan, J. Song, Y. Zou, J. Li, L. Xu, J. Xue, Y. Dong, B. Han, J. Chen and H. Zeng, Small, 2017, 13, 1701770–1701794 CrossRef PubMed.
- Y. H. Song, S. H. Choi, W. K. Park, J. S. Yoo, S. B. Kwon, B. K. Kang, S. R. Park, Y. S. Seo, W. S. Yang and D. H. Yoon, Sci. Rep., 2018, 8, 2009–2014 CrossRef PubMed.
- X. Chen, D. Chen, J. Li, G. Fang, H. Sheng and J. Zhong, Dalton Trans., 2018, 47, 5670–5678 RSC.
- J. C. Yu, J. H. Park, S. Y. Lee and M. H. Song, Nanoscale, 2019, 11, 1505–1514 RSC.
- S. Yang, W. Niu, A.-L. Wang, Z. Fan, B. Chen, C. Tan, Q. Lu and H. Zhang, Angew. Chem., Int. Ed., 2017, 56, 4252–4255 CrossRef CAS PubMed.
- D. H. Park, J. S. Han, W. Kim and H. S. Jang, Dyes Pigm., 2018, 149, 246–252 CrossRef CAS.
- L. Zhou, K. Yu, F. Yang, J. Zheng, Y. Zuo, C. Li, B. Cheng and Q. Wang, Dalton Trans., 2017, 46, 1766–1769 RSC.
- J. P. Park, T. K. Lee, S. K. Kwak and S. W. Kim, Dyes Pigm., 2017, 144, 151–157 CrossRef CAS.
- B. Saparov and D. B. Mitzi, Chem. Rev., 2016, 116, 4558–4596 CrossRef CAS PubMed.
- G. Chen, W. Lin, H. Chen and T. Guo, Mater. Des., 2019, 181, 108100–108106 CrossRef CAS.
- A. Pan, B. He, X. Fan, Z. Liu, J. J. Urban, A. P. Alivisatos, L. He and Y. Liu, ACS Nano, 2016, 10, 7943–7954 CrossRef CAS PubMed.
- S. Sun, D. Yuan, Y. Xu, A. Wang and Z. Deng, ACS Nano, 2016, 10, 3648–3657 CrossRef CAS PubMed.
- X. Li, Y. Wu, S. Zhang, B. Cai, Y. Gu, J. Song and H. Zeng, Adv. Funct. Mater., 2016, 26, 2435–2445 CrossRef CAS.
- Y. Wang, D. Yu, Z. Wang, X. Li, X. Chen, V. Nalla, H. Zeng and H. Sun, Small, 2017, 13, 1701587–1701594 CrossRef PubMed.
- A. Swarnkar, R. Chulliyil, V. K. Ravi, M. Irfanullah, A. Chowdhury and A. Nag, Angew. Chem., Int. Ed., 2015, 54, 15424–15428 CrossRef CAS PubMed.
- L. N. Quan, R. Quintero-Bermudez, O. Voznyy, G. Walters, A. Jain, J. Z. Fan, X. Zheng, Z. Yang and E. H. Sargent, Adv. Mater., 2017, 29, 1605945–1605950 CrossRef PubMed.
- J.-H. Cha, J. H. Han, W. Yin, C. Park, Y. Park, T. K. Ahn, J. H. Cho and D.-Y. Jung, J. Phys. Chem. Lett., 2017, 8, 565–570 CrossRef CAS PubMed.
- Q. Wang, W. Wu, R. Wu, S. Yang, Y. Wang, J. Wang, Z. Chai and Q. Han, J. Colloid Interface Sci., 2019, 554, 133–141 CrossRef CAS.
- Y. M. Chen, Y. Zhou, Q. Zhao, J. Y. Zhang, J. P. Ma, T. T. Xuan, S. Q. Guo, Z. J. Yong, J. Wang, Y. Kuroiwa, C. Moriyoshi and H. T. Sun, ACS Appl. Mater. Interfaces, 2018, 10, 15905–15912 CrossRef CAS.
- M. I. Saidaminov, J. Almutlaq, S. Sarmah, I. Dursun, A. A. Zhumekenov, R. Begum, J. Pan, N. Cho, O. F. Mohammed and O. M. Bakr, ACS Energy Lett., 2016, 1, 840–845 CrossRef CAS.
- Q. A. Akkerman, A. L. Abdelhady and L. Manna, J. Phys. Chem. Lett., 2018, 9, 2326–2337 CrossRef CAS PubMed.
- J. Xu, W. Huang, P. Li, D. R. Onken, C. Dun, Y. Guo, K. B. Ucer, C. Lu, H. Wang, S. M. Geyer, R. T. Williams and D. L. Carroll, Adv. Mater., 2017, 29, 1703703–1703712 CrossRef PubMed.
- Q. J. Han, W. Z. Wu, W. L. Liu, Q. X. Yang and Y. Q. Yang, Opt. Mater., 2018, 75, 880–886 CrossRef CAS.
- Q. Wang and W. Wu, Opt. Lett., 2018, 43, 4923–4926 CrossRef CAS PubMed.
- H. Yang, Y. Zhang, J. Pan, J. Yin, O. M. Bakr and O. F. Mohammed, Chem. Mater., 2017, 29, 8978–8982 CrossRef CAS.
- Y. Ling, L. Tan, X. Wang, Y. Zhou, Y. Xin, B. Ma, K. Hanson and H. Gao, J. Phys. Chem. Lett., 2017, 8, 3266–3271 CrossRef CAS PubMed.
- F. Zhang, H. Zhong, C. Chen, X.-g. Wu, X. Hu, H. Huang, J. Han, B. Zou and Y. Dong, ACS Nano, 2015, 9, 4533–4542 CrossRef CAS PubMed.
- V. D. Kulakovskii, G. Bacher, R. Weigand, T. Kümmell, A. Forchel, E. Borovitskaya, K. Leonardi and D. Hommel, Phys. Rev. Lett., 1999, 82, 1780–1783 CrossRef CAS.
- N. Talebian, S. M. Amininezhad and M. Doudi, J. Photochem. Photobiol., B, 2013, 120, 66–73 CrossRef CAS PubMed.
- F. Gabelloni, F. Biccari, G. Andreotti, D. Balestri, S. Checcucci, A. Milanesi, N. Calisi, S. Caporali and A. Vinattieri, Opt. Mater. Express, 2017, 7, 4367–4373 CrossRef CAS.
- D. Zhou, R. Sun, W. Xu, N. Ding, D. Li, X. Chen, G. Pan, X. Bai and H. Song, Nano Lett., 2019, 19, 6904–6913 CrossRef CAS PubMed.
- K. Lin, J. Xing, L. N. Quan, F. P. G. de Arquer, X. Gong, J. Lu, L. Xie, W. Zhao, D. Zhang, C. Yan, W. Li, X. Liu, Y. Lu, J. Kirman, E. H. Sargent, Q. Xiong and Z. Wei, Nature, 2018, 562, 245–248 CrossRef CAS PubMed.
- M. He, S. Liu, L. Ding, Z. Zhang, J. Liu, W. Xiang and X. Liang, J. Am. Ceram. Soc., 2019, 102, 930–935 CAS.
- Z. Bao, H.-C. Wang, Z.-F. Jiang, R.-J. Chung and R.-S. Liu, Inorg. Chem., 2018, 57, 13071–13074 CrossRef CAS.
- G. Yang, Q. Fan, B. Chen, Q. Zhou and H. Zhong, J. Mater. Chem. C, 2016, 4, 11387–11391 RSC.
- H. Huang, Q. Xue, B. Chen, Y. Xiong, J. Schneider, C. Zhi, H. Zhong and A. L. Rogach, Angew. Chem., Int. Ed., 2017, 56, 9571–9576 CrossRef CAS PubMed.
- S. Lou, T. Xuan, C. Yu, M. Cao, C. Xia, J. Wang and H. Li, J. Mater. Chem. C, 2017, 5, 7431–7435 RSC.
- G. Li, H. Wang, T. Zhang, L. Mi, Y. Zhang, Z. Zhang, W. Zhang and Y. Jiang, Adv. Funct. Mater., 2016, 26, 8478–8486 CrossRef CAS.
- H. Huang, B. Chen, Z. Wang, T. F. Hung, A. S. Susha, H. Zhong and A. L. Rogach, Chem. Sci., 2016, 7, 5699–5703 RSC.
- M. Yang, H.-s. Peng, F.-l. Zeng, F. Teng, Z. Qu, D. Yang, Y.-q. Wang, G.-x. Chen and D.-w. Wang, J. Colloid Interface Sci., 2018, 509, 32–38 CrossRef CAS PubMed.
- C. Sun, Y. Zhang, C. Ruan, C. Yin, X. Wang, Y. Wang and W. W. Yu, Adv. Mater., 2016, 28, 10088–10094 CrossRef CAS PubMed.
- Y. Hua, S. K. Hussain and J. S. Yu, Ceram. Int., 2019, 45, 18604–18613 CrossRef CAS.
|
This journal is © The Royal Society of Chemistry 2019 |
Click here to see how this site uses Cookies. View our privacy policy here.