DOI:
10.1039/D0MA00629G
(Paper)
Mater. Adv., 2020,
1, 2831-2839
Development of an ultra-sensitive para-nitrophenol sensor using tri-metallic oxide MoO2·Fe3O4·CuO nanocomposites†
Received
21st August 2020
, Accepted 21st September 2020
First published on 22nd September 2020
Abstract
A tri-metal oxide, MoO2·Fe3O4·CuO (TMO), was synthesized by the co-precipitation method and characterized by XRD, SEM-EDS, and FTIR. The average particle size of the nanocomposite was found to be 34.85 nm. The zeta potential and hydrodynamic size of the MoO2·Fe3O4·CuO nanocomposite were studied in acidic and basic pH respectively. A glassy carbon electrode (GCE) was modified by MoO2·Fe3O4·CuO to develop a chemical sensor for para-nitrophenol (p-NP). A simple I–V method was employed for this study. Excellent sensitivity, an ultra-low detection limit, long-term stability, and reproducibility of the MoO2·Fe3O4·CuO/Nafion/GCE sensor were observed towards p-NP. A linear calibration plot (r2: 0.9995) was obtained for 1.0 pM to 0.01 mM aqueous p-NP solution, with a sensitivity value of 5.2430 μA μM−1 cm−2 and remarkably low detection limit (LOD) of 0.2 pM.
Introduction
There have been a number of studies on advances of mixed metal oxide catalysts.1–3 The electronic and molecular structures of metal oxides have attracted special attention because of the presence of multiple oxidation states and variable nonconventional local coordination. They have simultaneous bulk and surface phases as well as different surface functionalities. Mixed metal oxides comprise the largest family of heterogeneous catalysts for numerous applications. Composite oxides are better in terms of their catalytic activity than constituent oxides. It is due to the increasing active acidic or basic sites as well as the increasing surface area on mixed metal oxides.4
Many industrially important processes have been explored with mixed metal oxide nanocomposites.5–7 Significant progress for technological development might be achieved by the use of those nano mixed metal oxides. MoO2 is a larger band-gap semiconductor (3.85 eV) than MoO3 (2.90 eV). When crystallized, MoO2 showed spherical morphology whereas MoO3 forms hexagonal or rectangular plates, based on the synthesis conditions.8,9 MoO2 has excellent applications in field emission devices, promising anode materials, and optical materials.9 Thermodynamically, the stability of the amorphous phases is lower than that of orthorhombic MoO3.10 This oxide is normally found in the orthorhombic phase, which has many applications. This phase can be described as a layered structure formed by covalent double layers of MoO6 octahedra. There have been studies on the antimicrobial, antioxidant, and cytotoxic effects of molybdenum oxide nanoparticles.11
In nature, iron(III) oxide is found in the form of rust. Generally, iron oxides are widespread, widely used as they are inexpensive, and play an important role in many biological as well as geological processes. They are also extensively used by humans including iron ores in thermite, catalysts, durable pigments (coatings, paints, and colored concrete), and hemoglobin. The three most common forms of iron oxides in nature are magnetite (Fe3O4), maghemite (γ-Fe2O3), and hematite (α-Fe2O3). NPs composed of ferromagnetic materials and with size <10–20 nm exhibit a unique form of magnetism, i.e., super para-magnetism.
Oxide-based nanomaterials such as CuO have been gaining interest in nanomaterials research. Semiconducting oxides such as CuO and Cu2O have distinguishing properties and are now widely used as transparent semiconducting oxide materials and chemical and biological sensors. This study was conducted to synthesize and characterize a tri-metal oxide from single metal oxides of interest, for exploring electrochemical sensor applications, because trimetallic oxide nanocomposites are promising systems for toxin sensors, photocatalytic applications and environmental safety, an efficient anti-bacterial agent against MDR bacteria, and industrial sterilization mediators.12–16
Phenolic compounds and their derivatives are extensively used in the production of pharmaceuticals, dyes, pesticides, etc., and are known as severe environmental toxins.17,18 They cause severe damage to organisms and plants.19para-Nitrophenol (p-NP) is an ingredient of the parathion-insecticide, which is a reason for anxiety because of its severe effects. p-NP is considered as one of the major toxic pollutants by the US Environmental Protection Agency (EPA).20,21 As a result, for ecological security and food safety, there is an urgent need to produce an effective method for the detection and quantification of p-NP. Some traditional analytical methods have been reported for the detection of p-NP.22–25 The electrochemical method offers various potential advantages such as a fast response, cost-effectiveness, and simple operation steps with good sensitivity and selectivity for the detection of p-NP. Electrodes including gold and glassy carbon electrodes in the electrochemical analysis are known to show good performance. However, still there is a need for ultrasensitive detection for a very low concentration of p-NP in pM in water. Modification of electrodes with various nanostructured materials may offer such opportunities.26,27 Carbon-based nanomaterial containing electrodes such as carbon paste, carbon nanotube, and graphene electrodes are used extensively in the electrochemical determination of p-NP.28,29 Nanographene is an excellent electrode material for p-NP determination because of its excellent charge transport properties, large surface to volume ratio, high electrocatalytic activity, and thermal conductivity.30,31 There have been studies on the detection of p-NP using graphene/graphene oxide modified electrodes within the range of a few hundred nanomolar.32
In the present study, we prepared a MoO2·Fe3O4·CuO nanocomposite by the co-precipitation method for the electrochemical detection of p-NP at ambient conditions. The structural and morphological properties of MoO2·Fe3O4·CuO were studied by various techniques. After synthesis of MoO2·Fe3O4·CuO, we coated the nanocomposite onto a GCE for the evaluation of the electrochemical performance for the detection of p-NP.33,34 Besides, we also compared the electrochemical response of the MoO2·Fe3O4·CuO nanocomposite with a bare GCE and MoO2·Fe3O4·CuO/GCE for the detection of p-NP, which indicates that the MoO2·Fe3O4·CuO nanocomposite shows better performance.
Experimental section
Materials and methods
MoCl2 (Sigma Aldrich, Germany), Fe(NO3)3·9H2O (MERCK, India), CuCl2·3H2O (AR, BDH), Na2CO3 (AR, BDH), NaOH (AR, BDH), and HCl (AR, BDH) (GPR, BDH) were purchased and used without further purification. Disodium phosphate, monosodium phosphate, 2-aminophenol, 4-methoxyphenol, p-NP, 3-chlorophenol, 2,4-dinitrophenol, bisphenol A, hydrazine, paracetamol, 4-nitrophenyl hydrazine, and 5% ethanolic Nafion solution were also purchased from Sigma-Aldrich. All chemicals were of analytical grade and used without further purification. The identification of the crystal phase and evaluation of other structural information of the nanomaterials studied in this work was performed by X-ray diffraction (XRD, Bruker D8 Advance diffractometer, equipped with a graphite monochromator). The diffraction patterns were recorded within the 2θ angle range from 10° to 80° in the step scan mode at 0.05 steps and at a rate of 10 s per step.34 The surface morphology was studied using a Scanning Electron Microscope (SEM) with an Energy-Dispersive X-ray Spectrometer (EDS) (JSM-7100F) linked with an EDS mapping appliance. FTIR analysis of the samples was carried out using an FTIR spectrometer (Shimadzu, FTIR-8400S). The hydrodynamic size and zeta potential were measured using a Zetasizer Nanoseries (Nano-ZS90). I–V measurements of the fabricated MoO2·Fe3O4·CuO/Nafion/GCE composites were conducted to detect p-nitrophenol using a Keithley electrometer (6517A, USA) at ambient conditions as reported recently.34
Preparation of the TMO MoO2·Fe3O4·CuO nanocomposite
The MoO2·Fe3O4·CuO nanocomposite was synthesized by a reliable and low-cost co-precipitation method. This synthetic process was started by preparing 0.25 M solutions of MoCl2, Fe(NO3)3·9H2O, and CuCl2·3H2O, which act as sources of molybdenum, iron, and copper, respectively. All of them were mixed in a beaker in the same volume ratio (50 mL) with constant stirring for 15 minutes. To the above mixture 0.5 M Na2CO3 was added dropwise until completion of the reaction at 45 °C. The resultant mixture was stirred constantly for another 1 hour at 45 °C. When the reaction was completed, the white precipitate was separated from the solution by centrifugation, then washed several times with deionized water and finally dried at 120 °C in an oven for 2 hours. The white sample was calcined in an electric muffle furnace (Gallenkamp, Korea) at 600 °C.35 The calcination transformed the metal carbonates into metal oxides.36 The reactions can be summarized as below:
(Mo2+ + Cl−) + (Na+ + CO32−) + HOH → MoCO3·(OH)2 + CO2 + (Na+ + Cl−) |
2Fe(NO3)3·9H2O + 3(Na+ + CO32−) + HOH → Fe2(CO3)2·(OH)2+ (Na+ + NO3−) |
(Cu2+ + Cl−) + (Na+ + CO32−) + HOH → CuCO3·(OH)2 + (Na+ + Cl−) |
3MoCO3·(OH)2 → 3MoO2 + 3CO2 |
3Fe2(CO3)2·(OH)2 → 2Fe3O4 + 6CO2 |
MoO2 + Fe3O4 + CuO → MoO2·Fe3O4·CuO |
Modification of a GCE with the TMO nanocomposite
The synthesized MoO2·Fe3O4·CuO was used to fabricate a GCE by using a 5% ethanolic solution of Nafion to get an approximately 0.4 mm thick film. It was then heated in an oven at 45.0 °C for 2 hours to get the dry film on the GC electrode. In an electro-chemical cell, the MoO2·Fe3O4·CuO nanocomposite fabricated GCE was used as a working electrode (WE), a platinum wire was the counter electrode (CE), and aqueous p-NP in 0.1 M phosphate buffer solution (PBS; pH 7.0) was used as the supporting electrolyte. To utilize the target chemical, aqueous p-NP (1.0 mM) was systematically diluted to various concentrations (1.0 mM to 1.0 pM) using deionized water. All the I–V measurements were performed in 5.0 mL of PBS (pH = 7.0). From the slope of the calibration plot, the sensitivity of the proposed p-NP sensor was calculated by considering the active surface area of the GCE. By using an electrometer (Keithley, 6517A electrometer, USA) the I–V method was applied to aqueous p-NP taking MoO2·Fe3O4·CuO/GCE as a working electrode.
Results and discussion
Structural characterization of the MoO2·Fe3O4·CuO nanocomposite
The XRD pattern of MoO2·Fe3O4·CuO is as depicted in Fig. 1. There are three oxides MoO2, Fe3O4 and CuO in the synthesized nanocomposite. One of them is monoclinic, C2/c(15), tenorite (CuO), which shows peaks at 2θ = 32.505°, 35.498°, 38.698°, 46.153°, 48.702°, 51.346°, 58.144°, 61.548°, 65.659°, 66.152°, 67.954°, and 72.208° (JCPDS#72-0629) with lattice constants a, b, c and (αβγ) of 4.6837, 3.4226, 5.1288 and (90.0 × 99.54 × 90.0), density (ρ) = 6.515 and volume = 81.1. Another one is magnetite (Fe3O4) (cubic, Fd
m(227)) having 2θ = 18.326°, 35.498°, 37.139°, 43.01°, 57.044°, 66.152°, 71.101°, 74.243°, and 79.086° (JCPDS#88-0315). Its lattice constants a, b, c and (αβγ) are 8.375, 8.375, 8.375 and (90.0 × 90.0 × 90.0) with density (ρ) = 5.235, and volume 587.4. The third one is also monoclinic, P21/c(14), MoO2, with 2θ peaks at 18.326°, 37.139°, 41.303°, 41.913°, 49.467°, 59.834°, 63.999°, 66.152°, 70.306°, 72.208°, and 79.086° (JCPDS#86-0135). Its lattice constants a, b, c and (αβγ) are 5.609, 4.86, 5.628 and (90.0 × 120.94 × 90.0) respectively. The particle size of the nanocomposite was estimated from XRD data using Scherrer's formula τ = Kλ/(β
cos
θ). Here τ is the mean size, K is a dimensionless shape factor with a value 0.94, λ is the X-ray wavelength (0.1506 nm), β is the line broadening at half the maximum intensity (FWHM) and θ is the Bragg angle. The average particle size of the MoO2·Fe3O4·CuO nanocomposite was found to be 34.85 nm.
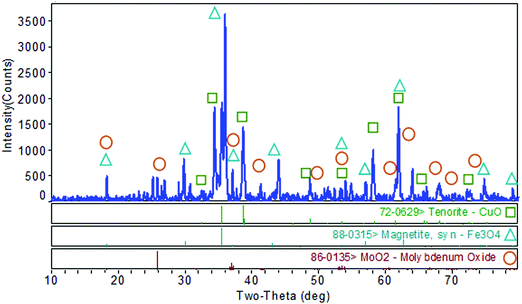 |
| Fig. 1 XRD pattern of the MoO2·Fe3O4·CuO nanocomposite. | |
Morphological and elemental analysis of the MoO2·Fe3O4·CuO nanocomposite
An SEM study (as in Fig. 2a and b) was performed to reveal a clear image of the surface morphology and particles of synthesized nanocomposite MoO2·Fe3O4·CuO. Fig. 2(a) shows that the nanocomposite formed in mixed cubic, rectangular and spherical morphologies. EDS mapping was carried out to map the elemental compositions of the nanocomposite. As is seen from the EDS data (Fig. S1 and Table S1, ESI†) the nanocomposites consist of Mo, Fe, Cu, and O with an atomic percentage of 2.5%, 30.85%, 14.8%, and 51.85% respectively. The EDS mapping also indicated that the elements were distributed throughout the matrix (Fig. S2, ESI†).
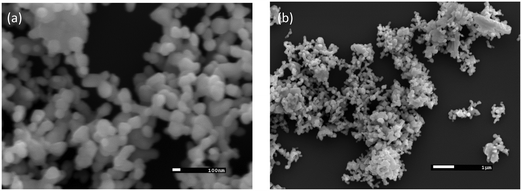 |
| Fig. 2 SEM image of ternary MoO2·Fe3O4·CuO nanocomposites at different magnification (a and b). | |
FTIR study of the MoO2·Fe3O4·CuO nanocomposite
Fig. S3 (ESI†) shows the FTIR spectrum of the MoO2·Fe3O4·CuO nanocomposite in 400–4000 cm−1. The band centred at 3433 cm−1 is assigned to the stretching mode of atmospheric H2O.37 The FTIR spectrum of the sample calcined at 600 °C showed the stretching mode of Mo
O at 966 cm−1 and Mo–O at 823 cm−1, and 775 cm−1. The IR peak at 717 cm−1 is attributed to the Mo–O–Mo stretching vibrations.38 The sample exhibited an intense peak at 599 cm−1 due to the stretching vibration mode associated with the iron–oxygen band (Fe–O bonds in the crystalline lattice of Fe3O4).39 The peak at 433 cm−1 is attributed to the Cu–O bond frequency. No peak at 873 cm−1 was found, which may indicate that there is no CO32− left in MoO2·Fe3O4·CuO. Thus, the nanocomposite contains only oxides with little or no unknown compounds.
Zeta potential and hydrodynamic size of the MoO2·Fe3O4·CuO nanocomposite
The zeta potential and hydrodynamic size of the MoO2·Fe3O4·CuO nanocomposite were studied in acidic and basic pH to know the size and charge in dispersed media. The hydrodynamic size, zeta potential, and polydispersity index (PDI) are listed in Table 1. The hydrodynamic size of MoO2·Fe3O4·CuO in acidic pH and basic pH was found to be 1284 and 850.7 nm. The zeta potential in acidic and basic pH has been observed to be −24.7 and −24.55 meV respectively. The results indicated that negatively charged MoO2·Fe3O4·CuO particles may adsorb organic compounds, dyes, and organic chemical toxins on the particle surface and perform catalytic functions.
Table 1 Hydrodynamic size and zeta potential of the MoO2·Fe3O4·CuO nanocomposite
Compound |
Na-citrate buffer (pH 4.95) |
PBS buffer (pH 7.4) |
Size (nm) |
Zeta potential |
PDI |
Size (nm) |
Zeta potential |
PDI |
MoO2·Fe3O4·CuO |
1234 |
−24.55 |
0.66 |
850.7 |
−24.7 |
0.33 |
Applications: chemical sensor study of the MoO2·Fe3O4·CuO/Nafion/GCE assembly.
Detection of p-NP using MoO2·Fe3O4·CuO/Nafion/GCE by the I–V method
Toxic p-NP in an aqueous system was determined using the MoO2·Fe3O4·CuO nanocomposite modified GC electrode. When p-NP comes into contact with MoO2·Fe3O4·CuO, it produces a significant response in the I–V technique. The possible use of the p-NP sensor constructed from the MoO2·Fe3O4·CuO/Nafion/GCE assembly was tested to detect and measure the selected toxin in phosphate buffer solution (PBS). The MoO2·Fe3O4·CuO/Nafion/GCE sensor exhibits several advantages such as higher stability in air, improved electro-chemical properties during the determination, versatile operation, and safe electrochemical characteristics.33,34 The probable application of the chemical sensor with MoO2·Fe3O4·CuO/Nafion/GCE was evaluated in detail for the detection of selected compound p-NP in buffer solution and MoO2·Fe3O4·CuO/Nafion/GCE acted as an electron mediator during the sensing process. The MoO2·Fe3O4·CuO/Nafion/GCE assembly was tested as a working electrode for the construction of the proposed sensor for the targeted toxin p-NP. In the sensing procedure of p-NP in PBS solution, the applied current vs. potential (I–V) was examined on a thin film of MoO2·Fe3O4·CuO/Nafion/GCE in the working electrode, which was increased noticeably due to the adsorption of aqueous p-NP on the fabricated working electrode. 1.0 sec was set as the holding period in the electrometer and an improved current vs. potential was detected in the time of p-NP determination by the fabricated chemical sensor.35 A suggested oxidation mechanism of p-NP is demonstrated in Scheme 1. At the time of p-NP oxidation by the constructed working electrode with the MoO2·Fe3O4·CuO/Nafion/GCE assembly, an enrichment of electrons in the buffer solution was detected and it caused an enhancement of the current vs. potential response during the I–V measurement at ambient conditions. According to the proposed p-NP oxidation mechanism, at the beginning, p-NP was converted to 4-hydroxylaminophenol, and, in the second step, 4-hydroxylaminophenol was oxidized to 4-nitrosophenol, followed by a consequent reversible reduction,40 which are presented in eqn (i) and (ii). | HO-Ph-NO2 + 4e− + H+ → HO-Ph-NHOH + H2O | (i) |
| HO-Ph-NHOH ↔ HO-Ph-NO + 2e− + H+ | (ii) |
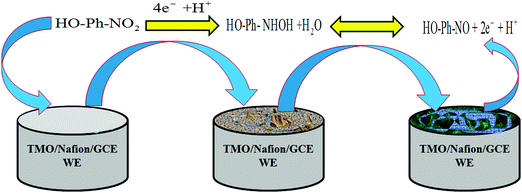 |
| Scheme 1 The proposed mechanism in detection of p-NP by MoO2·Fe3O4·CuO/Nafion/GCE. | |
The pictorial application of the MoO2·Fe3O4·CuO/Nafion/GCE modified electrode as a p-NP chemical sensor is demonstrated in Scheme 1.
A GCE was coated with a slurry of MoO2·Fe3O4·CuO nanomaterials. The constructed working electrode was applied for detection of p-NP compounds due to the oxidation in the buffer system which is proposed and presented above as per chemical reactions eqn (i) and (ii). According to the electrochemical oxidation process of targeted p-NP, several electrons were released to the conduction band, which enhanced the I–V response of the MoO2·Fe3O4·CuO/Nafion/GCE sensors.
Fig. 3(a) shows the current responses for nine toxic chemicals, where (1.0 μM; 25.0 μL) p-NP solution (red line) in PBS (pH = 7.0) produces a distinct peak at +0.3 V with the MoO2·Fe3O4·CuO/Nafion/GCE surface. How the electrochemical property of MoO2·Fe3O4·CuO changes with the pH values was studied in PBS with pH values of 5.7 to 8.0 as in Fig. 3(b). The obtained results showed that MoO2·Fe3O4·CuO exhibits better electro-chemical performance at different pH values. The electrocatalytic property of MoO2·Fe3O4·CuO changes with the pH values, which is revealed by the variation of the current response. In the pH optimization using p-NP (1.0 μM; 25.0 μL) in PBS, pH value 7.0 produces the maximum current response. Hence, pH value 7.0 was used in the rest of the experimental work in this p-NP determination by the MoO2·Fe3O4·CuO/Nafion/GCE assembly. In the absence of target p-NP, the electrochemical signal intensities of the MoO2·Fe3O4·CuO/GCE sensor probe at different pH values are measured and the signal is found to not significantly change in identical conditions (Fig. S4a, ESI†). The signal intensities of the MoO2·Fe3O4·CuO/GCE sensor probe at different times (in the absence of p-NP) are also evaluated in identical conditions (Fig. S4b, ESI†). It is observed that no significant changes are found in the electrochemical response for elongated time in the absence of target analyte p-NP. The current intensities using p-NP (1.0 μM; 25.0 μL) in PBS (5.0 mL, pH = 7.0) for the bare GCE (blue line) and MoO2·Fe3O4·CuO fabricated GCE (red line) are given in Fig. 3(c). MoO2·Fe3O4·CuO/Nafion/GCE produces a much better response than the bare GCE, which demonstrates the excellent electrochemical property of MoO2·Fe3O4·CuO as a selective p-NP sensor. Fig. 3(d) shows the current response of the MoO2·Fe3O4·CuO fabricated GCE in the absence of p-NP (blue line) and the presence of p-NP (red line; 1.0 μM; 25.0 μL) in 5.0 mL of PBS. With p-NP, a remarkable increase of the current response indicates the p-NP sensing capability of the proposed MoO2·Fe3O4·CuO/Nafion/GCE sensor. The I–t response for p-NP (1.0 μM; 25.0 μL) in 5.0 mL of PBS solution using the MoO2·Fe3O4·CuO nanostructure fabricated GCE as a working electrode is shown in Fig. 3(e). With p-NP (1.0 μM; 25.0 μL) in 5.0 mL of PBS, a constant current response was obtained in approximately 10 seconds. The p-NP chemical sensor is also optimized with various single metal oxides (i.e.; CuO, Fe3O4, and MoO2) and compared with the MoO2·Fe3O4·CuO nanostructure in identical conditions (Fig. S4c, ESI†). The highest current is observed with the MoO2·Fe3O4·CuO nanostructure/GCE sensor probe compared to the only CuO, Fe3O4, and MoO2 modified individual material.
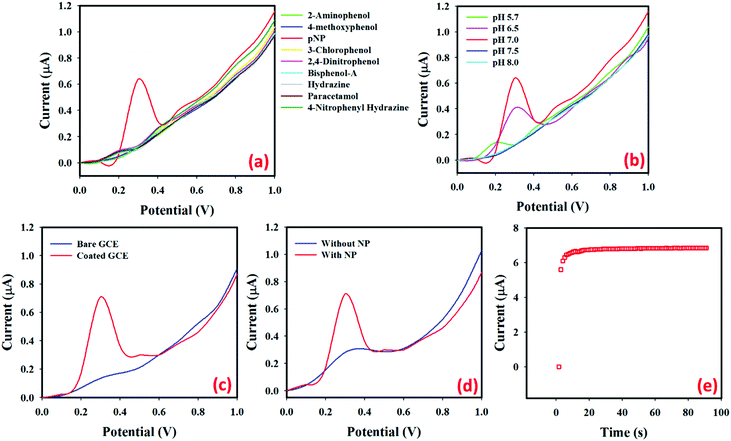 |
| Fig. 3
I–V responses: (a) selectivity study using nine interferents, (b) pH variation; (c) bare GCE and MoO2·Fe3O4·CuO/GCE, and (d) without and with the presence of p-NP (1.0 μM; 25.0 μL), and (e) current variation with time for MoO2·Fe3O4·CuO/Nafion/GCE in 1.0 μM; 25.0 μL p-NP. | |
In 5.0 mL PBS, low (1.0 pM) to high (1.0 mM) concentration p-NP solutions (25.0 μL) were injected sequentially and the surface current response variations were studied after every injection. The I–V responses from the MoO2·Fe3O4·CuO fabricated GCE surface were estimated using an aqueous p-NP solution of different concentrations (1.0 pM to 1.0 mM), given in Fig. 4(a) (the inset shows the magnification peak current at 0.3 V). It showed that when the potential increases, the I–V responses are also increased for the MoO2·Fe3O4·CuO fabricated GCE sensor. It was also observed that, from dilute (1.0 pM) to concentrated (1.0 mM) p-NP solution, the I–V responses also increased regularly. Aqueous p-NP (1.0 pM to 1.0 mM) was taken to select the limit of detection (LOD) of the developed sensor. The calibration plot (at +0.3 V) for the full concentration range is given in Fig. 4(b). A higher sensitivity value of 5.2430 μA μM−1 cm−2 was estimated from the calibration plot. From the calibration plot, the linear dynamic range of the developed MoO2·Fe3O4·CuO/GCE sensor was attained as 1.0 pM to 0.01 mM (r2 = 0.9995), and the LOD was estimated as 0.2 pM [3 × noise (N)/slope (S)]. Fig. 4(c) shows the reproducibility of the current response with the MoO2·Fe3O4·CuO fabricated GCE with 25.0 μL of 0.1 μM p-NP using seven distinct working electrodes in run R1 to R7 under the same experimental conditions. The almost similar current responses in all seven experiments confirm the outstanding reproducibility of the sensor (RSD = 4.17%, n = 7). Fig. 4(d) presents the repeatability where the same working electrode was used in run R1–R7. The almost similar I–V responses in the seven repeated experiments demonstrate the outstanding repeatability of the sensor (RSD = 3.85%, n = 7). With the same working electrode in different solutions with the same conditions, the I–V response decreases slightly. This may be because of the fall of the number of active sites in MoO2·Fe3O4·CuO after each run.
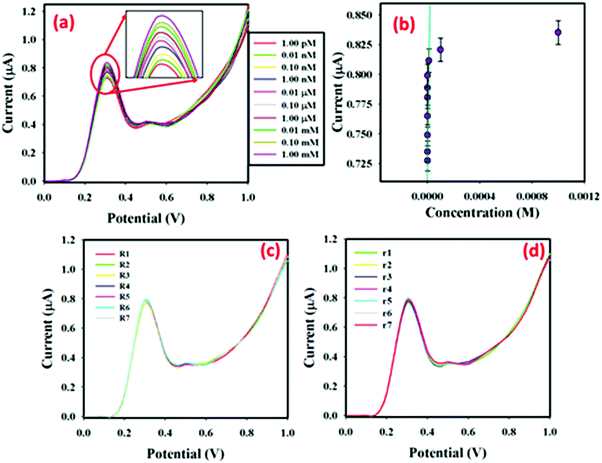 |
| Fig. 4 (a) Current variations for different concentrations (1.0 pM to 1.0 mM) of aqueous p-NP in 0.0 to +1.0 V, (b) calibration plot of the MoO2·Fe3O4·CuO fabricated GCE at +0.3 V, (c) repeatability using different WEs (0.1 μM, 25.0 μL p-NP; 5.0 mL, 0.1 M PBS at pH 7.0), and (d) reproducibility using the same WE (0.1 μM, 25.0 μL p-NP; 5.0 mL, 0.1 M PBS at pH 7.0). | |
Real sample analysis by the MoO2·Fe3O4·CuO/Nafion/GCE sensor
To confirm the functionality of the proposed sensor material MoO2·Fe3O4·CuO, MoO2·Fe3O4·CuO/Nafion/GCE had been employed to determine p-NP in industrial effluent water and drinking water from a plastic bottle after 7 days of sunlight irradiation kept inside a car (S2). For this, we use the standard addition method to verify the accuracy of the aqueous p-NP determination. 25.0 μL of aqueous p-NP of different concentrations and equal amounts of real samples were mixed and analyzed in PBS (5.0 mL, pH 7.0) with MoO2·Fe3O4·CuO/GCE as a WE. Table 2 presents the obtained outcomes, which demonstrated that the MoO2·Fe3O4·CuO/GCE modified sensor exhibited a quantitative (∼100%) recovery of p-NP. So, we can conclude that the I–V method can be an appropriate and reliable technique in analyzing real samples using the MoO2·Fe3O4·CuO/Nafion/GCE assembly.
Table 2 Analysis of some environmental samples with MoO2·Fe3O4·CuO/Nafion/GCE by the electrochemical process
Real sample |
p-NP concentrationa added |
p-NP concentrationa determinedb by MoO2·Fe3O4·CuO/Nafion/GCE |
Recoveryb (%) |
RSDc (%) (n = 3) |
S1 and S2: real water samples collected from an industrial effluent treatment plant and Safa drinking water bottle respectively, Jeddah, Saudi Arabia. Mean of three repeated determinations (S/N = 3) with MoO2·Fe3O4·CuO/Nafion/GCE. Concentration of p-NP determined/concentration of p-NP taken. The relative standard deviation value indicates the precision among three repeated determinations. |
S1 |
2.000 nM |
2.102 nM |
105.1 |
3.1 |
S1 |
2.000 μM |
2.056 μM |
102.8 |
2.9 |
S2 |
2.000 nM |
2.036 nM |
101.8 |
2.8 |
S2 |
2.000 μM |
2.006 μM |
100.3 |
3.4 |
The I–V responses in the p-NP measurements mostly depend on the size, porosity, and morphology of the nanomaterials. When the MoO2·Fe3O4·CuO surface comes into contact with the reducing p-NP, a surface-mediated oxidation reaction takes place. Oxidation of p-NP provides electrons to the MoO2·Fe3O4·CuO nanocomposite surface, which ultimately enhances the conductance of the MoO2·Fe3O4·CuO/Nafion/GCE assembly. Consequently, when the potential increases, the I–V response also increases. The MoO2·Fe3O4·CuO/Nafion/GCE sensor has also displayed consistency and stability. Overall, the proposed MoO2·Fe3O4·CuO/Nafion/GCE sensor for p-NP detection showed better performance than others as shown in Table 3.41–45
Table 3 Comparison of sensor analytical parameters of other nanostructure materials with the MoO2·Fe3O4·CuO/Nafion/GCE sensor probe using the electrochemical method for the detection of p-NP
Sensor material |
Method |
LDR |
LOD |
Sensitivity |
Ref. |
TLISS = tremella-like indium silver sulfide modified GCE, ABPGH = acetylene blackpaste and graphene hybrid, BDAC = biomass derived activated carbons. |
ABPGH |
LSV |
20 nM to 8.0 μM and 8.0 μM to 0.1 mM |
8.0 nM |
2.717, 1.8117 μA μM−1 |
41
|
BDAC |
LSV |
Up to 500 μM |
0.16 μM |
5.810 μA μM−1 cm−2 |
42
|
Fe3O4/graphene |
DPV |
0.01 to 0.10 mM |
0.004 mM |
8.067 × 10−5 μA mM−1 |
43
|
TLISS |
DPV |
1.43–55.93 and 55.93–553.7 μM |
1.09 μM |
— |
44
|
NiO–CeO2 |
CV |
1 to 20 μM |
2.48 μM |
3.68 A μM−1 cm−2 |
45
|
MoO
2
·Fe
3
O
4
·CuO
|
I–V
|
1.0 pM to 0.01 mM
|
0.2 pM
|
5.2430 μA μM
−1
cm
−2
|
This work
|
Conclusions
MoO2·Fe3O4·CuO was synthesized by the coprecipitation method. MoO2·Fe3O4·CuO was characterized by several techniques including XRD, SEM-EDS, hydrodynamic size and zeta-potential analysis, and FTIR. The average particle size of the nanocomposite was determined to be 34.85 nm. The surface morphology of the composite was observed in the SEM study. The zeta potential of MoO2·Fe3O4·CuO in acidic and basic pH has been observed to be −24.7 and −24.55 meV respectively. A MoO2·Fe3O4·CuO/Nafion/GCE electrode was successfully employed as a chemical sensor for the determination of aqueous para-nitrophenol. The fabricated p-NP chemical sensor based on MoO2·Fe3O4·CuO coated on a GCE showed a very efficient electron mediator property in the oxidation of p-NP in the PBS system. The proposed MoO2·Fe3O4·CuO/Nafion/GCE sensor for p-NP exhibits a high sensitivity (5.2430 μA nM−1 cm−2) and ultra-low LOD = 0.2 pM with an excellent linear response (r2: 0.9995) for a wide range of concentrations in a short response time. It initiated a new route in developing an effective chemical sensor using nanostructured nanomaterials for a sustainable and safe environment.
Conflicts of interest
We declare that there is no conflict of interest.
Acknowledgements
Md Abdus Subhan acknowledges Fulbright USA for offering a Fulbright Visiting Scholar Award 2018–2019 for 9 months. MOE (Ministry of Education), Bangladesh, Grant (PS 14290) is gratefully acknowledged for support. Center of Excellence for Advanced Materials Research (CEAMR), King Abdulaziz University, Jeddah, Saudi Arabia, is highly acknowledged for the lab facilities and instrumental support.
References
-
J. F. Brazdil, Bulk metal oxides, in Characterization of Catalytic Materials, ed. I. E. Wachs, Butterworth-Heinemann, Boston, Massachusetts, 1992, pp. 47–68 Search PubMed.
-
I. E. Wachs and K. Segawa, Supported metal oxides, in Characterization of Catalytic Materials, ed. I. E. Wachs, Butterworth-Heinemann, Boston, Massachusetts, 1992, pp. 69–88 Search PubMed.
-
C. L. Thomas, Catalytic Processes and Proven Catalysts, Academic Press, New York, 1970 Search PubMed.
- S. J. Singh and R. V. Jayaram, Tetrahedron Lett., 2008, 49, 4249 CrossRef CAS.
- M. M. Rahman, A. Umar and K. Sawada, Development of amperometric glucose biosensor based on glucose oxidase co-immobilized with multi-walled carbon nanotubes at low potential, Sens. Actuators, B, 2009, 137, 327 CrossRef.
- D. I. Enache, J. K. Edwards, P. Landon, B. Solsona-Espriu, A. F. Carley, A. A. Herzing, M. Watanabe, C. J. Kiely, D. W. Knight and G. J. Hutchings, Science, 2006, 311, 362 CrossRef CAS.
- X. Guo, H. Zhou, T. Fan and D. Zhang, Electrochemical detection of p-nitrophenol on surface imprinted gold with lamellar-ridge architecture, Sens. Actuators, B, 2015, 220, 33–39 CrossRef CAS.
- Z. C. Xiang, Q. Zhang, Z. Zhang, X. J. Xu and Q. B. Wang, Preparation and photoelectric properties of semiconductor MoO2 micro/nanospheres with wide bandgap, Ceram. Int., 2015, 41, 977–981 CrossRef CAS.
- R. J. Elliot, Phys. Rev., 1957, 108, 1384 CrossRef.
- C. Julien, A. Khelfa, O. M. Hussain and J. A. Nazri, J. Cryst. Growth, 1995, 156, 235 CrossRef CAS.
- A. Fakhri and P. Afshar Nejad, J. Photochem. Photobiol., B, 2016, 159, 211 CrossRef CAS.
- M. A. Subhan, T. P. Rifat, P. C. Saha, M. M. Alam, A. M. Asiri, M. M. Rahman and J. Uddin, Enhanced visible light-mediated photocatalysis, antibacterial functions and fabrication of a 3-chlorophenol sensor based on ternary Ag2O·SrO·CaO, RSC Adv., 2020, 10(19), 11274–11291 RSC.
- M. A. Subhan, P. C. Saha, S. A. Sumon, J. Ahmed, A. M. Asiri, M. M. Rahman and Al-M Mamun, Enhanced photocatalytic activity and ultrasensitive benzaldehyde sensing performance of a SnO2·ZnO·TiO2 nanomaterial, RSC Adv., 2018, 8, 33048–33058 RSC.
- M. A. Subhan, S. S. Jhuma, P. C. Saha, M. M. Alam, A. M. Asiri, M. Al- Mamun, S. A. Attia, T. H. Emon, A. K. Azad and M. M. Rahman, Efficient selective 4-aminophenol sensing and antibacterial activity of ternary Ag2O3·SnO2·Cr2O3 nanoparticles, New J. Chem., 2019, 43, 10352 RSC.
- M. A. Subhan, S. S. Jhuma, P. C. Saha, J. Ahmed, A. M. Asiri, T. P. Rifat, T. Raihan, A. K. Azad and M. M. Rahman, Photocatalysis, enhanced anti-bacterial performance and discerning thiourea sensing of Ag2O·SnO2·TiO2 hetero-structure, J. Environ. Chem. Eng., 2020, 8, 104051 CrossRef CAS.
- M. A. Subhan, P. C. Saha, M. M. Rahman, J. Ahmed, A. M. Asiri and M. A. Mamun, Fabrication of a 2,4-dinitrophenol sensor based on Fe3O4@Ag@Ni nanomaterials and studies on their antibacterial properties, New J. Chem., 2018, 42, 872 RSC.
- X.-Q. Qiao, Z.-W. Zhang, F.-Y. Tian, D.-F. Hou, Z.-F. Tian, D. Li and Q. Zhang, Enhanced catalytic reduction of p-nitrophenol on ultrathin MoS2 nanosheets decorated noble-metal nanoparticles, Cryst. Growth Des., 2017, 17(6), 3538–3547 CrossRef CAS.
- X.-Q. Qiao, Z.-W. Zhang, D.-F. Hou, D.-S. Li, Y. Liu, Y.-Q. Lan, J. Zhang, P. Feng and X. Bu, Tunable MoS2/SnO2 P–N Heterojunctions for an Efficient Trimethylamine Gas Sensor and 4-Nitrophenol Reduction Catalyst, ACS Sustainable Chem. Eng., 2018, 6, 12375–12384 CrossRef CAS.
- Z. Liu, J. Du, C. Qiu, L. Huang, H. Ma, D. Shen and Y. Ding, Electrochemical sensor for detection of p-nitrophenol based on nanoporous gold, Electrochem. Commun., 2009, 11, 1365–1368 CrossRef CAS.
- H. Yin, Y. Zhou, S. Ai, L. Cui and L. Zhu, Electrochemical determination of 2-nitrophenol in water samples using Mg–Al–SDS hydrotalcite-like clay modified glassy carbon electrode, Electroanalysis, 2010, 22(10), 1136–1142 CrossRef CAS.
- X. Huang, N. Qiu and D. Yuan, Direct enrichment of phenols in lake and sea water by stir bar sorption extraction based on poly (vinylpyridine-ethylene dimethacrylate) monolithic material and liquid chromatographic analysis, J. Chromatogr., 2008, A1194, 134–138 CrossRef.
- X. Guo, Z. Wang and S. Zhou, The separation and determination of nitrophenol isomers by high-performance capillary zone electrophoresis, Talanta, 2004, 64, 135–139 CrossRef CAS.
- A. Niazi and A. Yazdanipour, Spectrophotometric simultaneous determination of nitrophenol isomers by orthogonal signal correction and partial least squares, J. Hazard. Mater., 2007, 146, 421–427 CrossRef CAS.
- H. Yin, Y. Zhou, S. Ai, X. Liu, L. Zhu and L. Lu, Electrochemical oxidative determination of 4-nitrophenol based on a glassy carbon electrode modified with a hydroxyapatite nano powder, Microchim. Acta, 2010, 169, 87–92 CrossRef CAS.
- K. Giribabu, R. Suresh, R. Manigandan, S. Munusamy, S. P. Kumar, S. Muthamizh and V. Narayanan, Nanomolar determination of 4-nitrophenol based on a poly(methylene blue)-modified glassy carbon electrode, Analyst, 2013, 138, 5811–5818 RSC.
- M. K. Alam, M. M. Rahman, M. Abbas, S. R. Torati, A. M. Asiri, D. Kim and C. G. Kim, Ultra-sensitive 2-nitrophenol detection based on reduced graphene oxide/ZnO nanocomposites, J. Electroanal. Chem., 2017, 788, 66–73 CrossRef CAS.
- H. Yin, Y. Zhou, S. Ai, Q. Ma, L. Zhu and L. Lu, Electrochemical oxidation determination and voltammetric behaviour of 4-nitrophenol based on Cu2O nanoparticles modified glassy carbon electrode, Int. J. Environ. Anal. Chem., 2012, 92(6), 742–754 CrossRef CAS.
- Y. Tang, R. Huang, C. Liu, S. Yang, Z. Lu and S. Luo, Electrochemical detection of 4-nitrophenol based on a glassy carbon electrode modified with a reduced graphene oxide/Au nanoparticle composite, Anal. Methods, 2013, 5, 5508–5514 RSC.
- J. Li, D. Kuang, Y. Feng, F. Zhang, Z. Xu and M. Liu, A graphene oxide-based electrochemical sensor for sensitive determination of 4-nitrophenol, J. Hazard. Mater., 2012, 201–202, 250–259 CrossRef CAS.
- K. Chen, Z.-L. Zhang, Y.-M. Liang, W. Liu and A. Graphene-Based, Electrochemical Sensor for Rapid Determination of Phenols in Water, Sensors, 2013, 13, 6204–6216 CrossRef CAS.
- A. Arvinte, M. Mahosenaho, M. Pinteala, A.-M. Sesay and V. Virtanen, Electrochemical oxidation of p-nitrophenol using graphene-modified electrodes, and a comparison to the performance of MWNT-based electrodes, Microchim. Acta, 2011, 174, 337–343 CrossRef CAS.
- M. M. Rahman, M. M. Alam, A. M. Asiri and M. A. Islam, Fabrication of selective chemical sensor with ternary ZnO/SnO2/Yb2O3 nanoparticles, Talanta, 2017, 170, 215–223 CrossRef CAS.
- M. A. Subhan, P. C. Saha, M. M. Rahman, M. A. R. Akand, A. M. Asiri and M. Al-Mamun, Enhanced photocatalytic activity and chemical sensor development based on ternary B2O3·Zn6Al2O9·ZnO nanomaterials for environmental safety, New J. Chem., 2017, 41(15), 7220–7231 RSC.
- M. A. Subhan, T. Ahmed, P. Sarker, T. T. Pakkanen, M. Suvantoc, M. Horimoto and H. Nakata, J. Lumin., 2014, 148, 98 CrossRef CAS.
- Md A. Subhan, M. R. Awal, T. Ahmed and M. Younus, Acta Metall. Sin., 2014, 27(2), 223–232 CrossRef CAS.
- H. H. Kung, Stud. Surf. Sci. Catal., 1989, 45, 1 CrossRef.
- N. Dukstiene, D. Sinkeviciute and A. Guobiene, Cent. Eur. J. Chem., 2012, 10(4), 1106–1118 CAS.
- G. Gundiah and C. N. R. Rao, Solid State Sci., 2000, 2, 877 CrossRef CAS.
- Y. Haldorai, K. Giribabu, S. K. Hwang, C. H. Kwak, Y. S. Huh and Y. K. Han, Facile synthesis of a-MnO2nanorod/graphene nanocomposite paper electrodes using a 3D precursor for supercapacitors and sensing platform to detect 4-nitrophenol, Electrochem. Acta., 2016, 222, 717–727 CrossRef CAS.
- M. M. Rahman, S. B. Khan, A. M. Asiri and A. G. Al-Sehemi, Chemical sensor development based on polycrystalline gold electrode embedded low-dimensional Ag2O nanoparticles, Electrochem. Acta., 2013, 112, 422–430 CrossRef CAS.
- Q. He, Y. Tian, Y. Wu, J. Liu, G. Li, P. Deng and D. Chen, Facile and Ultrasensitive Determination of 4-Nitrophenol Based on Acetylene Black Paste and Graphene Hybrid Electrode, Nanomaterials, 2019, 9, 429 CrossRef CAS.
- R. Madhu, C. Karuppiah, S.-M. Chen, P. Veerakumar and S.-B. Liu, Electrochemical detection of 4-nitrophenol based on biomass derived activated carbons, Anal. Methods, 2014, 6, 5274–5280 RSC.
- M. Sarno and E. Ponticorvo, Fe3O4/Graphene Electrode for the Electrochemical Detection of 4-Nitrophenol, Chem. Eng. Trans., 2020, 79, 427 Search PubMed.
- P. Chen, Y. Shi, X. Li, T. Wang, M. Zhou, E. Tian, W. Wang, H. Jiang and H. Shu, Highly Effective Detection of 4-Nitrophenol by Tremella-like Indium Silver Sulfide Modified GCE, Int. J. Electrochem. Sci., 2018, 13, 6158–6168 CrossRef CAS.
- N. Ahmad, M. Alam and R. Wahab, Synthesis of NiO–CeO2 nanocomposite for electrochemical sensing of perilous 4-nitrophenol, J. Mater. Sci.: Mater. Electron., 2019, 30, 17643–17653 CrossRef CAS.
Footnote |
† Electronic supplementary information (ESI) available. See DOI: 10.1039/d0ma00629g |
|
This journal is © The Royal Society of Chemistry 2020 |
Click here to see how this site uses Cookies. View our privacy policy here.