DOI:
10.1039/C9RA09505E
(Paper)
RSC Adv., 2020,
10, 3040-3047
Comparison of two different nickel oxide films for electrochemical reduction of imidacloprid†
Received
14th November 2019
, Accepted 5th January 2020
First published on 16th January 2020
Abstract
A nickel oxide (NiO) thin film was successfully prepared on Ni foil via a sol–gel method and a reduced state nickel oxide (r-NiO) thin film was obtained by etching NiO with hydrazine hydrate solution. Structure characterization through X-ray diffraction and scanning electron microscopy revealed the growth of nanostructure films on the surface of nickel foil. Cyclic voltammetry, linear sweep voltammetry and electrochemical impedance spectroscopy were used to assess the performance of the two films. Electroreduction of alkaline imidacloprid solution under potentiostatic conditions was carried out in a three-electrode system. The removal efficiencies of 80.2% (r-NiO) and 66.3% (NiO), and the current efficiencies of 67.3% (r-NiO) and 58.9% (NiO) were much higher than 41.7% (removal efficiency) and 0.003% (current efficiency) on the bare Ni electrode. This study prepared two novel thin films with composites of NiO or r-NiO, and thus provided feasible and efficient electrochemical degradation of imidacloprid. The degradation products were characterized and the possible degradation pathways were proposed.
1. Introduction
Imidacloprid (IMD), a systemic chloronicotinyl insecticide with remarkable water solubility, high toxicity, and good stability in water, is mainly applied to agriculture for controlling sucking insects in crops such as aphids, white flies and termites, and can cause IMD pollution in water sources and soil.1,2
To solve the pollution problem, various treatment processes have been studied. While diverse microorganisms may potentially degrade insecticides, IMD is none biodegradable due to its high toxicity.3,4 A lot of work has focussed on exploring effective methods for IMD treatment. Ultraviolet (UV) photolysis with photocatalysis and photo-Fenton's reagent are the most intensively applied technologies. However, photolysis is usually not a competitive option due to the low quantum efficiency as most pesticide compounds are only partially degraded.5,6 Alternative to advanced oxidation processes with production of hydroxyl radicals (·OH) through hydroxyl radical attack,7–9 direct or indirect electrochemical generation of ·OH in electrochemical advanced oxidation processes (EAOPs) was proposed as a potential option to remove pesticides from contaminated waste water.10–12 This electrochemical process based on redox reactions overcomes the drawbacks of consuming extra chemical reagents or producing secondary pollution in conventional chemical or physical treatments.13 However, the need for expensive electrodes and thus the relatively large capital investment limits their practical application.14 Much effort is still needed to employ highly efficient and cost effective electrodes in order to broaden the applicable field of electrochemical degradation for IMD and other pesticide contaminated wastewater.
While electrochemical oxidation is effective for the degradation of IMD, anodes with expensive materials including TiO2/Ti,15,16 Ti/RuO2–TiO2, Ti/RuO2–IrO2–TiO2,17 Ti/SnO2–Sb2O3,18 or Pt and boron-doped diamond (BDD)19 were purposely used.
In these reports, electrochemical oxidation was carried out using expensive anode to resist the strong oxidative effect of hydroxyl radical. In parallel to the electrochemical oxidation, electrochemical reduction on the low-cost cathode has been scarcely reported for IMD degradation. The reasons of choosing electrochemical reduction instead of oxidation for IMD removal lies in: (i) inexpensive materials can be used as cathode electrodes due to their much less destruction by cathodic processes; (ii) cathodic reduction reactions feasibly occur with lower overvoltage, compared to anodic oxidation with higher overvoltages for ·OH generation; and (iii) species of IMD, difficultly degraded by electrochemical advanced oxidation might be feasibly removed through electrochemical reduction.
In this study, two novel materials of NiO based on Ni foils via a sol–gel method and r-NiO by etching NiO with hydrazine hydrate solution were prepared as cathodes and assessed for efficient IMD degradation in alkaline aqueous solution. NiO has been regarded as a promising electrode candidate due to its cost effectiveness, superior chemical and electrical stability, and transparently p-type semi-conductivity based high efficiency.20,21 The characterization of the oxides is investigated by X-ray diffraction (XRD), scanning electron microcopy equipped with energy dispersive spectrometer (SEM-EDS) and electrochemical tests. IMD degradation products were characterized by high performance liquid chromatograph-mass spectrometer (HPLC-MS) and the possible degradation pathways were proposed.
2. Experiment
2.1 Chemical reagents
All organic reagents were commercial products of the highest purity available (>98%). Sulfuric acid, citric acid, acetone, ethanol, n-butyl alcohol, sodium borohydride (NaBH4) and nickel dichloride hexahydrate (NiCl2·6H2O) were analytical grade. Imidacloprid (98.6%) was obtained from Agricultural Research Institute of Shanghai.
2.2 Preparation of NiO and r-NiO films
Specimens with dimensions of 70 × 10 × 0.1 mm cut from Ni plates were utilized as substrates. The Ni plates were sequentially and ultrasonically pretreated with acetone, hydrochloric acid (1.0 mol L−1 HCl), and deionized water.
The Ni plates were put at the bottom of a beaker. Then, 3.5 g of NiCl2·6H2O was dissolved in an n-butyl alcohol–ethanol (100 mL
:
50 mL) solvent and 18.9 g of citric acid solution was added with magnetic stirring for 30 min. Afterwards, deionized water was added drop by drop. Light green sol–gel was then formed and coated on Ni plate under 90 °C heating reflux. After 60 min, the Ni plate coated sol–gel was taken out from the beaker and calcined at 300 °C for 20 min for preparation of NiO. Repeat the coating steps several times until NiO film on the surface of Ni plates were uniform. Finally, the NiO film coated on Ni plate was sequentially and ultrasonically washed with acetone and deionized water.
The as-prepared NiO film coated Ni plate was put in 10% NaBH4 solution for 240 min at room temperature. The r-NiO film was then obtained, and sequentially and ultrasonically washed with acetone and deionized water.
2.3 Electroreduction of imidacloprid
Stock solution of IMD (40 mg L−1) in alkaline (0.1 mol L−1 NaOH) was prepared with deionized water.
Electroreduction of IMD under potentiostatic condition was carried out at a series of potential (−1.0 V, −1.1 V, 1.2 V, −1.3 V and −1.4 V) in 50 mL basic solution containing 100 mg L−1 IMD and 0.1 mol L−1 NaOH for 1000 s at room temperature. The removal efficiency of imidacloprid was calculated based on eqn (1):
|
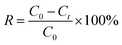 | (1) |
where
C0 is the initial concentration of imidacloprid,
Ct is the concentration after a certain time of electroreduction using NiO, r-NiO or Ni electrodes.
Current efficiency was calculated as eqn (2)
|
 | (2) |
where, 96
![[thin space (1/6-em)]](https://www.rsc.org/images/entities/char_2009.gif)
500 is Faraday constant (C mol
−1);
η is the current efficiency (%);
R is removal efficiency calculated according to
eqn (1) (%);
Qt is the theoretical charge needed to reduce IMD (C);
Qp is the practically consumed charge for IMD reduction (C);
c is the molar bulk concentration of imidacloprid, here is 0.000156 mol L
−1 (100 mg L
−1);
V is the electrolyte volume, here is 0.05 L (50 mL);
n is the number of electrons, here is 1.
2.4 Liquid chromatography analysis
The concentration of imidacloprid and its transformation products were monitored by liquid chromatography (Agilent HP 1200, Agilent Technologies, Inc., USA), equipped with an Agilent model pump, autosampler, column compartment, and an ultraviolet detector with a C-18 column with the dimensions 4.6 × 150 nm. The mobile phase used a mixture of acetonitrile and water (40
:
60) at a flow rate of 0.5 mL L−1. The injection volume of the sample was 5 μL, and the ultraviolet detection was λ = 270 nm. The samples were filtered through 0.45 μm filter paper before injection.
An HPLC-MS (Agilent 1100-6224) system was used to analyze the transformation products obtained in imidacloprid degradation, with an LC column Luna 5C18100A. The samples were filtered through 0.45 μm filter paper before injection. In this case, the isocratic eluent was 98% (1 nmol L−1 aqueous sodium formate and 0.1% formic acid) and 2% acetonitrile (0.1% of formic acid), which was pumped at a rate of 0.4 mL min−1 for 80 min. Detection was carried out with the diode array detector set at 270 nm and the column temperature maintained at 35 °C.
2.5 Structure characterization and electrochemical tests
The as-prepared NiO and r-NiO were characterized through XRD performed on a Panalytical Empyrean diffractometer with Cu Kα radiation. The morphology and the elements of the surface of NiO and r-NiO were analyzed by SEM-EDS (JSM-6360LV).
For electrochemical tests, a three-electrode system was employed. NiO, r-NiO film coated Ni plates or the bare Ni plate were used as working electrodes, whereas a platinum plate and a saturated calomel electrode (SCE) were used as counter and reference electrodes, respectively in electrolyte of NaOH aqueous solution (0.1 mol L−1). Cyclic voltammetry (CV) was performed at a scan rate of 50 mV s−1 between −0.4 V and 0.3 V. Linear sweep voltammetry (LSV) was performed at −1.4 V to 0 V at a scan rate of 5 mV s−1. The electrochemical impedance spectroscopy (EIS) test was carried out in a frequency range of 0.01 Hz to 100 kHz. All the electrochemical measurements were performed on an electrochemical work station (PARSTAT2273, Princeton Applied Research, USA) at 20 °C.
3. Results and discussion
3.1 Structural characterization of NiO and r-NiO films
The structure characterizations of the NiO and r-NiO films were analyzed by XRD (Fig. 1). The peaks at 2θ angle values of 37.2°, 43.2°, 62.8°, 75.4° and 79.3° corresponded to characteristics of nickel oxide, which could be assigned to (101), (012), (110), (113) and (202) reflection of NiO (JCPDS 44-1159), respectively. The peaks of Ni foils were not observed in the diffraction pattern of NiO. For the diffraction pattern of r-NiO, however, the peaks at 2θ angle values in the same positions of NiO were decreased slightly. Meanwhile, three remarkable peaks at 44.5°, 51.8° and 76.3° corresponded to characteristics of nickel, which could be assigned to (111), (200) and (220) reflection of Ni (JCPDS 4-850) respectively. These results collectively demonstrated the difference of r-NiO and NiO films each other.
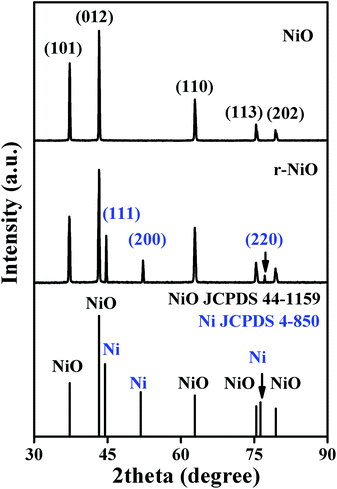 |
| Fig. 1 XRD patterns of NiO and r-NiO films coated on Ni plate. | |
The grain sizes of NiO and r-NiO were calculated using Scherrer equation:
|
 | (3) |
where
D is crystallite size,
λ is the wavelength of X-ray radiation,
β is the full width at half height of symmetrical shape of the diffraction peak and
θ is the Bragg angle. The average grain size of NiO film was about 50 nm, while r-NiO film was about 30 nm, suggesting r-NiO finer nanocrystalline film than NiO by reduction of NaBH
4 solution.
Fig. 2 showed the SEM images of the surface views and the corresponding tilted views of Ni substrate, and NiO and r-NiO films. Both NiO and r-NiO films were composed of granular particles with the size of about 0.2–2 μm. However, r-NiO film exhibited thinner thickness and smaller particles than NiO film, meaning better conductivity for the former.22 The morphology of even r-NiO thin films demonstrated that the etching by NaBH4 played an important role in the formation of r-NiO nanocrystals.
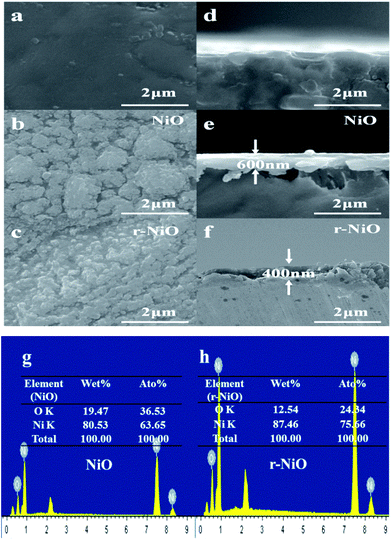 |
| Fig. 2 SEM images of surface view (a–c) and tilted view (d–f) of Ni, NiO and r-NiO, EDS spectra of NiO (g) and r-NiO (h). | |
EDS analysis showed that the NiO thin films consisted of 80.5% (w) of Ni element and 19.5% (w) of O element. However, r-NiO film consisted of higher Ni elements of 87.5% (w) and lower O element of 12.5% (w) due to the reduction effect of NaBH4. This result was well consistent with the result in the XRD patterns (Fig. 1), indicating that r-NiO can effectively improve the structure characteristics and thus the enhanced the electrochemical performance demonstrated hereinafter.
3.2 Electrochemical performance of NiO and r-NiO electrodes
The electrochemical tests of CV, LSV and EIS were carried out to investigate the characteristics of NiO and r-NiO films. Fig. 3 presented the CV curves of different electrodes in the range of −0.4 V to 0.3 V. Both the r-NiO and the NiO films showed much larger and more symmetric current response than the Ni electrode, suggesting the faster electron-transfer kinetics and the better electrochemical catalytic activity than the bare electrode by the formation of the crystallization films. In addition, the r-NiO film displayed much larger current values than the NiO film, mainly ascribed to the former thinner film and favorable morphology (Fig. 1 and 2).
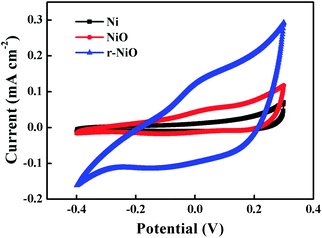 |
| Fig. 3 CV curves obtained on NiO, r- NiO and Ni electrodes from −0.4 to 0.3 V at a scan rate of 50 mV s−1 in 0.1 mol L−1 NaOH solution. | |
LSV curves demonstrated that Ni electrode showed a larger current sharp than NiO or r-NiO at potentials more negative than −1.15 V (Fig. 4), mainly attributed to strong hydrogen evolution in this region. These results precisely demonstrated that hydrogen evolution was greatly reduced by the NiO or r-NiO films, compared to the bare Ni. This merit of the NiO or r-NiO films favored for the electroreduction of imidacloprid and improved the current efficiency because of the alleviation of the side reaction of hydrogen evolution at the negative potentials.23 Moreover, the crystallization of the NiO and r-NiO films exhibited much better electrochemical catalytic activity for imidacloprid reduction than the bare Ni demonstrated hereinafter. The r-NiO film exhibited a larger current response than NiO film, presumably due to its thinner thickness, higher conductivity and better electrochemical activity than the former.
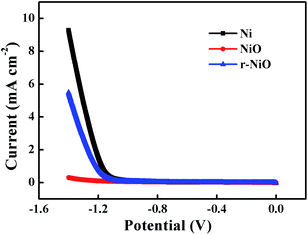 |
| Fig. 4 LSV curves obtained on Ni, NiO and r-NiO electrodes from −1.4 to 0 V at a scan rate of 5 mV s−1 in 0.1 mol L−1 NaOH solution. | |
The Nyquist plots of EIS spectra for NiO and r-NiO films (Fig. 5) were characteristic of semicircle, which was significantly different from the bare Ni, suggesting the growth of nanostructure films on the surface of nickel foil. An intercept at high frequency region with real axis of Z′ is inner resistance (Rs) and distorted semicircle is charge-transfer resistance (Rct) across the electrode–electrolyte interface.24,25 From the fitting equivalent circuit (inset of Fig. 5), it can be concluded that the Rs of NiO thin film electrode is about 0.89 Ω, while the Rs of r-NiO is about 0.85 Ω. The span of the semicircle along the x-axis from high to low frequency represented the Rct. The smaller the diameter of the semicircle, the better the electrochemical activity. The r-NiO shows much smaller Rct of 220 Ω cm2 than 465 Ω cm2 for NiO. The better conductivity and less Rct of the r-NiO film can be ascribed to its thinner thickness and smaller particles. As a consequence, the r-NiO thin film exhibited better electrochemical activity and higher electrochemical reduction ability than the NiO film, as subsequently demonstrated.
 |
| Fig. 5 Nyquist plots of Ni, NiO, r-NiO electrodes in 0.1 mol L−1 NaOH solution (inset: fitting equivalent circuit). | |
3.3 Electroreduction of imidacloprid
For all electrodes of Ni, NiO and r-NiO, degradation efficiency of IMD increased with the more negative potential (Fig. 6d), due to the abundant electrons supply at more negative potentials. At the highly negative potentials, hydrogen was observed to evolve drastically on the bare Ni electrode (Fig. 6a), consistent with the much larger current response obtained on Ni electrode (Fig. 6b and c), while hydrogen evolution were slightly generated on NiO and r-NiO electrodes. This result implied the undesired side reaction of hydrogen evolution has been greatly reduced on the NiO or r-NiO films.26 In addition, better electrochemical catalytic activity could be achieved by the formation of crystallization films of NiO or r-NiO. As a result, the removal efficiencies of 80.2% (r-NiO) and 66.3% (NiO), and the current efficiencies of 67.2% (r-NiO) and 58.9% (NiO) were much higher than 41.7% and 0.003% on the bare Ni electrode at −1.3 V (Fig. 6d and Table 1). The values obtained on r-NiO were higher than on NiO, explaining the better electrochemical catalytic activity and the lower charge transfer resistance in the former.
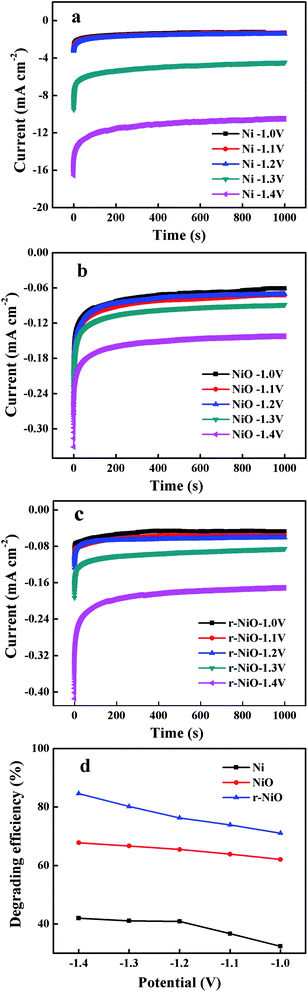 |
| Fig. 6 Current vs. time curves obtained on electrodes of (a) Ni, (b) NiO, (c) r-NiO and (d) degradation efficiency of imidacloprid of the three electrodes at different potentials in 0.1 mol L−1 NaOH solution. | |
Table 1 Comparison of degradation efficiency and current efficiency by potentiostatic reduction at −1.3 V on different electrodes
Electrode |
Removal efficiency/% |
Current efficiency/% |
Ni |
41.7 |
0.003 |
NiO |
66.3 |
58.9 |
r-NiO |
80.2 |
67.2 |
Comparing these results with literature, the removal rate of IMD (equivalent to 4.81 mg L−1 min−1) observed in this study at an initial IMD of 100 mg L−1 and much lower current density of 0.10 mA cm−2, was much higher than the rate achieved on a boron-doped diamond anode at a much higher current density by EAOPs.27–29 In addition, ·OH generation on anodic oxidation during EAOPs processes at high-voltage anodes means high electric price or low current efficiency compared to the results of this study with fairly high current efficiency.
The main possible reactions involved in the electrochemical reduction processes were as follows:30
|
2H2O + 2e → H2↑ + OH−
| (4) |
|
Imidacloprid + e → reduction products
| (5) |
|
Imidacloprid + [H] → reduction products
| (6) |
In alkaline solution, the IMD was reduced by direct reduction with accepting electrons (eqn (5)) or by indirect reduction by reaction with the freshly generated atom hydrogen ([H]) (eqn (6)) generated on the surface of the electrode, and then turned into transitional products and finally terminal products.
In alkaline solution, the IMD was reduced by direct reduction with accepting electrons (eqn (5)) or by indirect reduction by reaction with the freshly generated atom hydrogen ([H]) (eqn (6)) generated on the surface of the electrode, and then turned into transitional products and finally terminal products. The occurrence of the side reaction of more hydrogen evolution through water hydrolysis (eqn (4)) on the surface of the Ni electrode than that on the NiO or r-NiO films, explained the higher current efficiencies in the latter (Table 1).
Fig. 7 showed the intermediates identified by HPLC-MS after electroreduction of IMD with r-NiO electrode. Apparent decrease in peak height of IMD along with the appearance of some new peaks was observed, demonstrating the decrease of IMD and the appearance of new intermediates by electrochemical degradation.
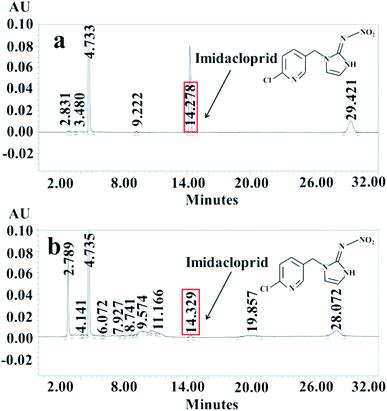 |
| Fig. 7 Analysis results of HLLC-MS before (a) and after (b) electroreduction of imidacloprid at −1.3 V in 0.1 mol L−1 NaOH for 1000 s. | |
The intermediates identified by mass spectra (MS) indicated IMD was degraded to alkene IMD (m/z = 266.1), imidacloprid guanidine (m/z = 211), IMD urea (m/z = 212) and 6-chloronicotinic acid (m/z = 141) (Fig. 8).
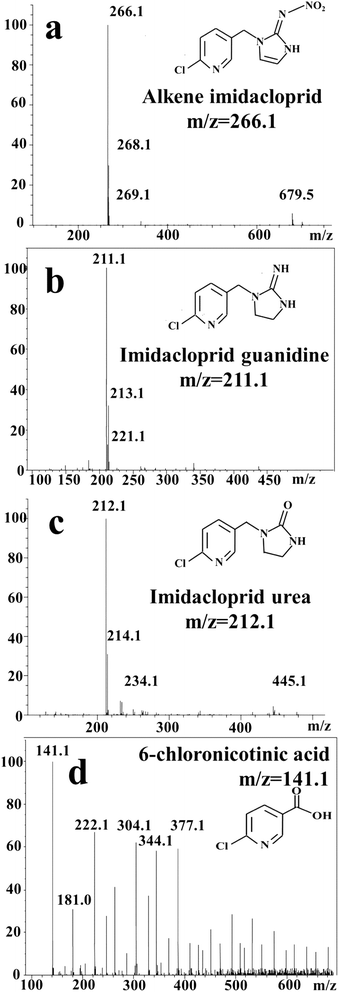 |
| Fig. 8 MS of intermediates after electroreduction of imidacloprid by r-NiO electrode. | |
Based on the detected intermediates, a pathway for electrochemical degradation of IMD with r-NiO electrode was proposed (Fig. 9). The charge transfer led to the formation of alkene IMD upon elimination of H atoms.31 The alkenes were further degraded to yield the 6-chloronicotinic acid, which exhibited a higher insecticidal activity than IMD. However, this 6-chloronicotinic acid displayed a large degree of mineralization and lost its acute toxicity with extended time.32 IMD urea was the principal degradation product by hydrolysis and in weak alkaline media, which has been proven to have lower toxicity than the parent compound and can be easily mineralized.33,34 IMD guanidine was formed by the loss of the –NO2 group after H+ attacking the moiety of N–NO2 of IMD,35 which showed higher mammalian toxicity than the parent compound. However, this intermediate could eventually be converted into nontoxic molecular fragments in the natural environment. The 6-chloronicotinic acid was the major degradation product of IMD with simple chemical structure, and had less ecotoxicity than the IMD.36 More importantly, this compound can be easily mineralized into CO2 and H2O under acid conditions.
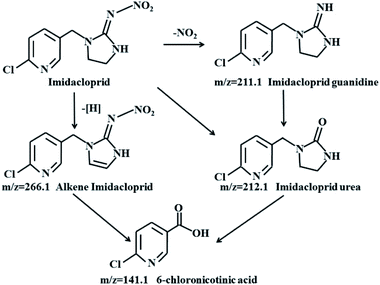 |
| Fig. 9 The proposed pathway for electroreduction of imidacloprid by r-NiO electrode. | |
4. Conclusions
The novel films of NiO prepared by sol–gel method and the r-NiO by reduction of NiO film were successfully explored for electrochemical reduction of IMD. While NiO and r-NiO crystallization films were composed of granular particles, the r-NiO film exhibited thinner thickness, smaller particles and better conductivity than the NiO film. The NiO and r-NiO films also displayed the merit of the alleviation of the side reaction of hydrogen evolution at the negative potentials. Electroreduction of alkaline IMD solution under potentiostatic conditions was successfully carried out in a three-electrode system, achieving removal efficiencies of 80.2% (r-NiO) and 66.3% (NiO), current efficiencies of 67.3% (r-NiO) and 58.9% (NiO), much higher than 41.7% (removal efficiency) and 0.003% (current efficiency) on the bare Ni electrode. The higher removal efficiencies were mainly ascribed to the better electrochemical catalytic activity and the lower charge transfer resistance of the r-NiO and the NiO films, whereas the higher current efficiencies were due to the alleviation of the side reactions of hydrogen evolution during the IMD removal process. Four degradation intermediates were detected and the possible pathway for electrochemical degradation of IMD was proposed. The novel nickel oxide prepared on Ni foil was proved to be feasible and cost effective for efficient electrochemical degradation of IMD.
Conflicts of interest
There are no conflicts to declare.
Acknowledgements
The authors gratefully acknowledge financial support from the Natural Science Foundation of China (No. 21273025, 21377019 and 21777017).
References
- N. Simondelso, V. Amaralrogers, L. P. Belzunces, J. M. Bonmatin, M. Chagnon, C. A. Downs, L. Furlan, D. W. Gibbons, C. Giorio, V. Girolami, D. Goulson, P. David, C. Krupke, M. Liess, E. Long, M. Mcfield, P. Mineau, A. D. Mitchell, C. Morrissey, A. Noome, L. Pisa, J. Settele, J. D. Stark, A. Tapparo, H. Vandyck, J. Vanpraagh, P. R. Whitehom and M. Wiemers, Systemic insecticides (neonicotinoids and fipronil): trends, uses, mode of action and metabolites, Environ. Sci. Pollut. Res., 2015, 22, 5–34 CrossRef CAS.
- Q. Zhou, Y. Ding and J. Xiao, Chemistry, sensitive determination of thiamethoxam, imidacloprid and acetamiprid in environmental water samples with solid-phase extraction packed with multiwalled carbon nanotubes prior to high-performance liquid chromatography, Anal. Bioanal. Chem., 2006, 385, 1520–1525 CrossRef CAS PubMed.
- X. H. Zhou, Y. Tian, X. Liu, L. P. Huang and Y. Wen, Reduction of Imidacloprid by Sponge Iron and Identification of its Degradation Products, Water Environ. Res., 2018, 90, 2049–2055 CrossRef CAS PubMed.
- S. Gligorovski, R. Strekowski, S. Barbati and D. Vione, Environmental Implications of Hydroxyl Radicals, Chem. Rev., 2015, 115, 13051–13092 CrossRef CAS PubMed.
- R. Zabar, T. Komel, J. Fabjan, M. B. Kralj and P. Trebše, Photocatalytic degradation with immobilised TiO2 of three selected neonicotinoid insecticides: imidacloprid, thiamethoxam and clothianidin, Chemosphere, 2012, 89, 293–301 CrossRef CAS.
- S. Malato and J. Caceres, Degradation of imidacloprid in water by photo-Fenton and TiO2 photocatalysis at a solar pilot plant: a comparative study, Environ. Sci. Technol., 2001, 35, 4359–4366 CrossRef CAS PubMed.
- M. L. DellArciprete, J. M. Sole, L. Santos-Juanes, A. Arques, D. O. Martire, J. P. Furlong and M. C. Gonzalez, Reactivity of neonicotinoid insecticides with carbonate radicals, Water Res., 2012, 46, 3479–3489 CrossRef CAS PubMed.
- M. Naushad, G. Sharma and Z. A. Alothman, Photodegradation of toxic dye using Gum Arabic-crosslinked-poly(acrylamide)/Ni(OH)2/FeOOH nanocomposites hydrogel, J. Clean. Prod., 2019, 241, 118263–118269 CrossRef.
- M. Bourgin, F. Violleau, L. Debrauwer and J. Albet, Ozonation of imidacloprid in aqueous solutions: reaction monitoring and identification of degradation products, J. Hazard. Mater., 2011, 190, 60–68 CrossRef CAS PubMed.
- E. Brillas, I. Sirés and M. A. Oturan, Electro-Fenton process and related electrochemical technologies based on Fenton's reaction chemistry, Chem. Rev., 2009, 109, 6570–6631 CrossRef CAS PubMed.
- P. Nidheesh and R. Gandhimathi, Trends in electro-Fenton process for water and wastewater treatment: an overview, Desalination, 2012, 299, 1–15 CrossRef CAS.
- M. Turabik, N. Oturan, B. Gözmen and M. Oturan, Efficient removal of insecticide “imidacloprid” from water by electrochemical advanced oxidation processes, Environ. Sci. Pollut. Res., 2014, 21, 8387–8397 CrossRef CAS.
- H. Zhao, X. Cui, M. C. Liu, P. Q. Li, Y. G. Zhang, T. C. Cao, H. X. Li, Y. Z. Lei, L. Liu and D. M. Li, Electrochemical degradation of refractory pollutant using a novel microstructured TiO2 nanotubes/Sb-doped SnO2 electrode, Environ. Sci. Technol., 2009, 43, 1480–1486 CrossRef PubMed.
- L. Z. Wang, S. X. Yang, B. Wu, P. Li, Z. N. Li and Y. M. Zhao, The influence of anode materials on the kinetics toward electrochemical oxidation of phenol, Electrochim. Acta, 2016, 206, 270–277 CrossRef CAS.
- A. Chatzitakis, E. Nikolakaki, S. Sotiropoulos and I. Poulios, Hydrogen production using a photoelectrocatalytic-enzymatic hybrid system, Catal. Today, 2013, 209, 60–65 CrossRef CAS.
- N. Philippidis, S. Sotiropoulos, A. Efstathiou and I. Poulios, Photoelectrocatalytic degradation of the insecticide imidacloprid using TiO2/Ti electrodes, J. Photochem. Photobiol. A Chem., 2009, 204, 129–136 CrossRef CAS.
- L. M. Silva, R. P. A. dos Santos, C. C. O. Morais, C. L. Vasconcelos, C. A. Martinez-Huitle and S. S. L. Castro, Anodic oxidation of the insecticide imidacloprid on mixed metal oxide (RuO2-TiO2 and IrO2-RuO2-TiO2) anodes, J. Electrochem. Soc., 2017, 164, 489–495 CrossRef.
- S. A. Abdelgawad, A. M. Baraka, K. A. Omran and M. M. Mokhtar, Removal of some pesticides from the simulated waste water by electrocoagulation method using iron electrodes, Int. J. Electrochem. Sci., 2012, 7, 6654–6665 CAS.
- K. L. Zhou, H. Wang, J. T. Jiu, J. B. Liu, H. Yan and K. Suganuma, Polyaniline films with modified nanostructure for bifunctional flexible multicolor electrochromic and supercapacitor applications, Chem. Eng. J., 2018, 345, 290–299 CrossRef CAS.
- G. S. Gund, C. D. Lokhande and H. S. Park, Controlled synthesis of hierarchical nanoflake structure of NiO thin film for supercapacitor application, J. Alloys Compd., 2018, 741, 549–556 CrossRef CAS.
- S. T. Navale, V. V. Mali, S. A. Pawar, R. S. Mane, M. Naushad, F. J. Stadler and V. B. Patil, Electrochemical supercapacitor development based on electrodeposited nickel oxide film, RSC Adv., 2015, 5, 51961–51965 RSC.
- M. Burriel, J. Santiso, M. D. Rossell, G. V. Tendeloo, A. Figueras and G. Garcia, Enhancing total conductivity of La2NiO4 epitaxial thin films by reducing thickness, J. Phys. Chem. C, 2008, 112, 10982–10987 CrossRef CAS.
- K. Xie, H. P. Wu, Y. N. Meng, K. Lu, Z. X. Wei and Z. Zhang, Poly(3,4-dinitrothiophene)/SWCNT composite as a low overpotential hydrogen evolution metal-free catalyst, J. Mater. Chem. A, 2015, 3, 78–82 RSC.
- M. K. Zate, V. V. Jadhav, S. Gore, J. H. Shendkar, S. U. Ekar, A. Al-Osta, M. Naushad and R. Mane, Structural, morphological and electrochemical supercapacitive properties of sprayed manganese ferrite thin film electrode, J. Anal. Appl. Pyrolysis, 2016, 122, 224–229 CrossRef CAS.
- Y. Tian, R. Xue, X. H. Zhou, Z. Y. Liu and L. P. Huang, Double layer capacitor based on active carbon and its improved capacitive properties using redox additive electrolyte of anthraquinonedisulphonate, Electrochim. Acta, 2015, 152, 135–139 CrossRef CAS.
- Y. Tian, Y. B. Wu, L. P. Huang and F. L. Yang, Comparative investigation on electroreduction of Cu(II) using polypyrrole electrode and stainless steel electrode, J. Appl. Electrochem., 2010, 40, 427–433 CrossRef CAS.
- M. Ben Brahim, H. Belhadj Ammar, R. Abdelhédi and Y. Samet, Electrochemical removal of the insecticide imidacloprid from water on a boron-doped diamond and Ta/PbO2 anodes using anodic oxidation process, Korean J. Chem. Eng., 2016, 33, 2602–2609 CrossRef.
- R. Oriol, M. P. Bernícola, E. Brillas, P. L. Cabot and I. Sir, Paired electro-oxidation of insecticide imidacloprid and electrodenitrification in simulated and real water matrices, Electrochim. Acta, 2019, 317, 753–765 CrossRef CAS.
- M. Sedaghat, B. Vahid, S. Aber, M. H. Rasoulifard, A. Khataee and N. Daneshvar, Electrochemical and photo-assisted electrochemical treatment of the pesticide imidacloprid in aqueous solution by the Fenton process: effect of operational parameters, Res. Chem. Intermed., 2016, 42, 855–868 CrossRef CAS.
- J. Ahmed, T. Ahamad, M. Ubaidullah, A. M. AlEnizi, A. N. Alhabarah, N. Alhokbany and S. M. Alshehri, rGO supported NiWO4 nanocomposites for hydrogen evolution reactions, Mater. Lett., 2019, 240, 51–54 CrossRef CAS.
- M. B. Brahim, H. B. Ammar, R. Abdelhédi and Y. Samet, Electrochemical removal of the insecticide imidacloprid from water on a boron-doped diamond and Ta/PbO2 anodes using anodic oxidation process, Korean J. Chem. Eng., 2016, 33, 2602–2609 CrossRef CAS.
- A. Zapata, I. Oller, E. Bizani, J. A. Sánchez-Pérez, M. I. Maldonado and S. Malato, Evaluation of operational parameters involved in solar photo-Fenton degradation of a commercial pesticide mixture, Catal. Today, 2009, 144, 94–99 CrossRef CAS.
- V. Kitsiou, N. Filippidis, D. Mantzavinos and I. Poulios, Heterogeneous and homogeneous photocatalytic degradation of the insecticide imidacloprid in aqueous solutions, Appl. Catal., B, 2009, 86, 27–35 CrossRef CAS.
- X. H. Zhou, Y. Tian, X. Liu, L. P. Huang and Y. Wen, Reduction of Imidacloprid by Sponge Iron and Identification of its Degradation Products, Water Environ. Res., 2018, 90, 2049–2055 CrossRef CAS PubMed.
- H. N. Guan, D. F. Chi, Y. Jia and X. C. Li, A novel photodegradable insecticide: preparation, characterization and properties evaluation of nano-imidacloprid, Pestic. Biochem. Physiol., 2008, 92, 83–91 CrossRef CAS.
- M. D. García, M. M. Galera, R. S. Valverde, A. Galanti and S. Girotti, Column switching liquid chromatography and post-column photochemically fluorescence detection to determine imidacloprid and 6-chloronicotinic acid in honeybees, J. Chromatogr. A, 2007, 1147, 17–23 CrossRef PubMed.
Footnote |
† Electronic supplementary information (ESI) available. See DOI: 10.1039/c9ra09505e |
|
This journal is © The Royal Society of Chemistry 2020 |
Click here to see how this site uses Cookies. View our privacy policy here.