DOI:
10.1039/D0RA02229B
(Paper)
RSC Adv., 2020,
10, 19736-19746
Environmentally friendly approach to recover vanadium and tungsten from spent SCR catalyst leach liquors using Aliquat 336
Received
10th March 2020
, Accepted 13th May 2020
First published on 26th May 2020
Abstract
This research paper deals with an environmentally friendly approach for the treatment of spent selective catalytic reduction (SCR) catalyst. To recover vanadium (V) and tungsten (W) from spent SCR catalyst, leach liquors from hydrometallurgical processing were utilized to develop a proper methodology for extraction and possible separation of vanadium and tungsten from each other. This study investigated the solvent extraction (also called liquid–liquid extraction) of vanadium and tungsten utilizing the alkaline roasted leached solution containing approximately ∼7 g L−1 of tungsten and ∼0.7 g L−1 of vanadium. The commercial extractant, N-methyl-N,N,N-tri-octyl-ammonium chloride [R3NCH3]+Cl− (commercial name Aliquat 336), was dissolved in Exxsol™ D80 (diluent) system and adopted in this research. Solvent extraction studies were performed to determine the following experimental parameters: equilibrium pH, extractant concentration, diluent influence, chloride ion concentration, temperature, and stripping reagent concentration, which were systematically scanned to ascertain the optimum conditions for quantitative extraction of both title metals. An anion exchange mechanism was proposed using the quaternary ammonium chloride solvent reagent after slope analysis. Excess supplement of chloride proved to have adverse effects, further supporting the extraction mechanism. Thermodynamics results show positive values for enthalpy (ΔH) for vanadium and tungsten, favoring the endothermic nature of the extraction reaction towards the uptake of either metal. McCabe–Thiele plots for extraction were constructed, suggesting 2 and 3 stages for vanadium and tungsten extraction, respectively, at the aqueous (A) to organic (O) phase ratio of 7
:
1, ensuring more than 99.9% and 7-fold enrichment of both title metals. The stripping trend follows the order: (NaOH + NaCl) > (NaOH + NaNO3) > NaOH > NaNO3 > NaCl. Stripping isotherm followed by stripping counter-current (CCS) study was carried out for quantitative stripping of the metals.
1. Introduction
In the past two decades, various secondary wastes, such as sludge, scrap, spent catalyst, e-waste, and battery waste, have been extensively exploited for the recovery of valuable metals, raising concerns over environmental issues vis-a-vis the rapid depletion of primary grade ore(s). From these wastes containing spent catalysts accomplishing desulphurization and ozonization, the spent selective catalytic reduction (SCR) catalysts are being generated to a greater extent from the respective industrial sectors and are gaining more attention, owing to containing a very high concentration of the strategic as well as base metals like vanadium, tungsten, molybdenum, and other metals.1 These waste catalysts are usually subjected to recycling through an integrated hydrometallurgical route to recover the valuable metal and at the same time address the global environmental issues encountered therein. One such SCR catalyst, V2O5–WO3/TiO2, contains a considerable amount of valuable metals (7–10% of W, 0.5–1.5% V and 70–80% Ti). However, the presence of a combination of both title metals, such as tungsten and vanadium, in the catalyst phase leads to the issue of attaining selective separation of either metal (W/V) during subsequent solvent extraction methods downstream, after leaching. This is due to the similar speciation behavior of both vanadium and tungsten in aqueous media. To date, considerable works have been devoted by researchers to processing these types of catalysts.1–6 The investigations carried out by our research group5–8 include the selective extraction of titanium followed by quantitative leaching of tungsten and vanadium carried out through soda roasting, followed by alkali dissolution, generating a leach solution with about ∼7000 mg L−1 tungsten and ∼700 mg L−1 vanadium.5–8 Hence, the real issue for this leach solution is to extract and separate out the enriched content of either of these metals from the above leached solution.
To extract vanadium and tungsten from the alkali/acid media in leach solution(s), the liquid–liquid extraction,9–15 supported liquid membrane (SLM),16–19 ion exchange (IX),3,20–23 and adsorption24–27 methods are often adopted. Amongst these, solvent extraction (liquid–liquid extraction) appears to be a highly promising approach for wider adoption in downstream separation processess.14,15,28 Nevertheless, the usage of numerous commercial extractants, including di-(2-ethylhexyl) phosphoric acid (D2EHPA),29–34 2-ethyl hexyl phosphonic acid mono-2-ethyl hexyl ester (PC 88A),33 bis (2,4,4-trimethylpentyl) phosphinic acid (Cyanex 272), LIX (oximes) series reagents,31,35 tri-butyl-phosphate (TBP),29,30,34 and amines (Alamine 336, Alamine 308),6,36,37 has shown excellent extraction behavior in solvent extraction processes towards the uptake of tungsten/vanadium from the corresponding aqueous phase(s), depending on the speciation of either metal ion in the aqueous media. Both tungsten and vanadium are commonly termed as strategic elements in the periodic table, as they exhibit variable oxidation states. In particular, while varying the aqueous condition (acidic to alkaline), either of these metals are found to exist as cation and/or anion moieties. In alkaline media, vanadium is mostly present as anionic species such as HVO42−, V4O124−, H2VO4−, V3O93−, V2O74−and VO43−, while in slightly acidic media (pH > 4), V4O92− and HV10O285− are found as the predominant species. In the case of tungsten, the aqueous chemistry tends to be more complicated due to the slow reactions, and para-tungstates31 are the predominant species at solution pH between 5 to 9. At pH < 6, several oxo-anionic species are formed,9,31 such as HWO4−, H3W6O213−, HW6O215−, H2WO4 and W6O216−. Thus, it becomes a critical aspect to consider a suitable solvent reagent for quantitative as well selective extraction of either of the metals when both metals are found in one phase, along with other metal ion impurities.
As of now, a number of studies have been devoted by researchers to the solvent extraction of vanadium and tungsten from various aqueous media. Talla et al.38 proposed Cyanex 923 as an extractant to separate tungsten from molybdenum from a liquor containing 5 mg L−1 of tungsten using selective stripping with NaOH. Though they successfully separated the metals, the low concentration of tungsten in the liquor shows a disadvantage for the industrial application of this extractant for high-concentration leach liquor.38 Ning et al.37 have proposed the use of N1923 (primary amine) for tungsten extraction at ∼1 g L−1 concentration level and solution pH of 7.07. The separation factor for tungsten over molybdenum was reported to be 329, which showed great potential for separation behavior; however, similar to the previously proposed reagent, it cannot be applied to highly concentrated leach liquor, and the extraction has to be done at 15.5 °C, posing a further difficulty for the process. Nguyen and Lee proposed31,39 LIX 63 to separate vanadium from tungsten at pH 8 due to its ability to extract metals in their hydroxide form; at that pH, vanadium only is found as a hydroxide, while tungsten is found in the anionic form WO42−. In their study, the initial concentration of vanadium and tungsten were 0.1 g L−1 and 1 g L−1, respectively, which does not offer an industrial application of the process for spent SCR catalyst liquor, which is composed of 0.7 g L−1 and 7 g L−1 of vanadium and tungsten, respectively. To date, the reported studies reveal the successful adoption of organophosphorus, oxidic, ammine and LIX reagents for the removal of both metals from a liquor bearing a very low content of either metal. The use of Aliquat 336 for the exclusive extraction of tungsten is scant, though limited use for the extraction of vanadium has been reported.39,40 The main shortcoming of this approach is the not significantly high extraction properties of the reagents and the fact that the studied pH ranges have been deliberately maintained as strongly acidic (as they follow the cation exchange mechanism) and, in consequence, use a high amount of caustics. Nevertheless, the reported works that accomplish the quantitative and effective separation of vanadium and tungsten from alkaline leach liquor are limited, and therefore, more investigations in this domain are necessary. In addition, unlike other commercial reagents, Aliquat 336 (used in the present investigation) has also been considered as a suitable green ionic liquid (IL) and41–44 is poised to be a potential reagent for application in the extraction of various base and strategic metal(s) (Mo, Co, Ni) from spent catalyst leach solutions, due to its high loading ability, quick extraction, and the unique complexation mechanism (anion exchange mechanism) of ILs.41–46
Therefore, this work aims to develop a promising liquid–liquid extraction technology using Aliquat 336 for the effective and enriched extraction of both tungsten and vanadium from industrially processed leach liquor obtained from the recycling of spent SCR catalyst. In this investigation, the solvent extraction mechanism, kinetics, thermodynamics, process optimization and extraction, and stripping isotherm were extensively examined.
2. Experimental
2.1. Reagents and materials
The extractant commonly known as Aliquat 336 (N-methyl-N,N,N-tri-octyl-ammonium chloride), acquired from Sigma-Aldrich, was used as is. For most experiments, the industrial “de-aromatized” aliphatic hydrocarbon solvent Exxsol™ D80 purchased from ExxonMobil Chemical was used in addition to other diluents, such as xylene, toluene, n-heptane and benzene. These diluents are used as is without further purification. All the chemicals (Merck) and reagents (Junsei Chemical Co Ltd., Japan) used in experimental studies are of analytical grade (AR). The leach liquor used for this study was based on the previous works of our research group.7 The deactivated catalyst used for leaching was obtained from the Samcheonpo Thermoelectric plant of Korea and contains 7.11% and 0.98% WO3 and V2O5, respectively. Soda roasting at a temperature of 1173 K for 2 h was performed, followed by water leaching at 80 °C to obtain a leach liquor bearing approximately 0.7 g L−1 of V and 7 g L−1 of W at a pH 9.19. The provided leach liquor was used without further treatment for this solvent extraction investigation. For the stripping studies, NaOH from Samchun Pure Chemical Co. Ltd., South Korea (purity above 98.0%) and NaCl from Tedia Company Inc., USA (purity above 99.0%) were used as is without further treatment or purification.
2.2. Apparatus and analysis
The metal ion analysis of each of the resulting samples after the extraction/stripping study was performed by ICP-OES (Thermo Scientific, USA, iCAP6000 series). A pH meter (Thermo Scientific Orion Star A215) was used to control the pH of the aqueous phase. The extraction and stripping experiments were conducted with a SI-300/300R/600/600R incubated shaker, and all experiments were performed at the shaking speed of 250 rpm. All the studies were carried out using separation funnels for the solvent extraction processes. Overall, analytical and experimental errors were observed to be within ±3%.
2.3. Method
The desired organic and aqueous phases (each phase 20 mL, except phase ratio experiments) were contacted in separation funnels (125 mL capacity) for each experiment for the time limit of 30 minutes (mostly, besides the case of contact time effect) at ambient temperature (in most of the study, except the extraction/stripping temperature variation effect) and equilibrated under incubated shaker at a speed of 250 rpm. After equilibration and phase disengagement, either of the samples was collected. The resulting raffinate samples were subjected to pH measurement (equilibrium pH). The aqueous samples were read with ICP-OES to analyze the metal ion contents after making appropriate dilutions with distilled water. To ensure the mass balance (extraction/stripping), the amount of tungsten and vanadium in the organic phase was also determined. The loaded organic (LO) samples were stripped with NaOH + NaCl, followed by subsequent dilution for metal ion analysis. The metal distribution coefficient (D) was determined as per eqn (1). Based on the values of D, the percentage of metal extraction was evaluated as stated in eqn (2). |
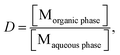 | (1) |
where M represents vanadium or tungsten. |
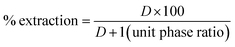 | (2) |
3. Results and discussion
3.1. Time effect
The liquid–liquid extraction kinetics were investigated to minimize the overall energy consumption as well as to maintain a minimum contact time for solvent extraction of vanadium and tungsten from the leached solution. For this research, contact time was modified from 1 min to 120 min, while other experimental conditions were: 0.5 mol L−1 Aliquat 336, pH 7.0 (equilibrium pH 7.95), phase ratio O
:
A = 1 and temperature 25 °C. As shown in Fig. 1, the metal extraction equilibrium was achieved just after 30 minutes of shaking time, and thereafter, the metal extraction efficiency did not improve significantly. As can be seen from the results, extraction kinetics for both metals was faster with Aliquat 336, and within 1 min of contact time, ∼44% of tungsten and 65% of vanadium are extracted. The attainment of quick extraction of both tungsten and vanadium with Aliquat 336 is consistent and in good agreement with the extraction behavior of Aliquat 336 with the heavy as well as rare metals.45–47 Thus, 30 minutes of contact time was kept constant for further experimental investigations.
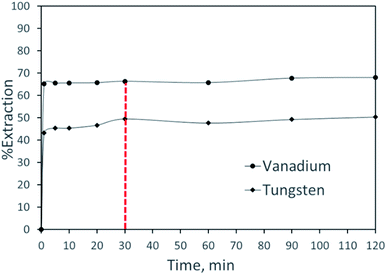 |
| Fig. 1 Effect of time on extraction of vanadium and tungsten from spent SCR catalyst leach liquor. | |
3.2. Effect of extractant concentration
Aliquat 336 concentration was varied from 0.01 mol L−1 to 1 mol L−1, and it showed strong influence in the extraction of metals from a chloride-mediated leach solution, which was studied at the phase ratio O
:
A = 1 and pH 7.0. The extraction efficiency for both tungsten and vanadium at different Aliquat 336 concentrations was plotted as presented in Fig. 2. From the results, the extraction of vanadium increased from 29.1% to 68.0%, while tungsten extraction improved from 27.9% to 60% when Aliquat 336 was varied from 0.01 to 0.5 mol L−1. Beyond 0.5 mol L−1 Aliquat 336, the extraction trend almost reached a plateau for both metals. Thus, 0.5 mol L−1 extractant was considered a suitable condition for the effective extraction of tungsten and vanadium.
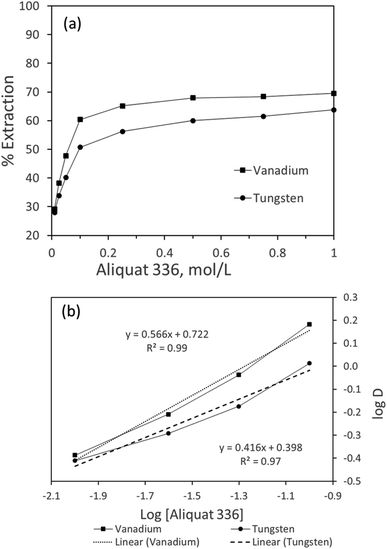 |
| Fig. 2 Plot of (a) [Aliquat 336] vs. the extraction of vanadium and tungsten, (b) log D vs. log[Aliquat 336]. | |
To determine the number of moles of Aliquat 336 participating for the loading of either metal (tungsten/vanadium), the log
D was plotted against the log[Aliquat 336]. As shown in Fig. 2, the linearized plot resulted in the slope of 0.566 and 0.416 (close to unity) for vanadium and tungsten, respectively, ascertained on the association of one mole of Aliquat 336 during extraction. Unlike other metal extraction processes, both tungsten and vanadium exhibit variable anionic species (H2VO4− and H2WO4) at the studied pH of the solution (pH 7.0), favoring an anion exchange phenomenon with Aliquat 336.40 The detailed association mechanism of Aliquat 336 with either of the metals is described in Section 3.5.
3.3. pH effect
To investigate the equilibrium pH (eq. pH) effect on the extraction of vanadium and tungsten from deactivated SCR catalyst leaching solution, the pH was modified from 5.0 to 7.35 while keeping Aliquat 336 concentration at 0.5 mol L−1, phase ratio O
:
A = 1, and time of 30 min constant. It was observed that the respective equilibrium pH of the solution increased from 5.87 to 7.98 with the corresponding change in initial pH from 5.01 to 7.35. However, the extraction followed an adverse trend, 99.79% to 50.24% and 95.9% to 39.93% for vanadium and tungsten, respectively, when equilibrium pH increased (Fig. 3). The observation on the increase in the corresponding equilibrium pH can be explained based upon the association/co-extraction of protons (H+) in the organic phases during the complexation of either of the metals (tungsten/vanadium), leading to decreased solution acidity and thus the enhancement of the equilibrium pH.9,31 This was attributed to the speciation of vanadium as well as tungsten at the wide range of pH in aqueous phase.9,31 The association of one proton in the organic phase is well evident from the log
D vs. eq. pH plot, which resulted in the slope of 1.11 for log
D vs. eq. pH, which is close to unity (1). Furthermore, it is well known from the literature31 that both tungsten and vanadium usually do exist in H2VO4−2 and H2WO4 form in the alkalinity range of solution (pH > 6.0), but while progressing towards mild acidity (pH < 6.0), the major probability of existence of tungsten and vanadium is as the oxo-ionic species, such as HV2O5− and HWO4−. Consequently, the extraction of tungsten and vanadium is noticeably observed as HV2O5− and HWO4− at the solution pH of 5.0 with Aliquat 336, leading to efficient extraction of both metals at this condition. Overall, the slope analysis study for both metals shows that one mole of H+ becomes a complex with the extractant, which indicates an anionic exchange mechanism (Fig. 3). The detailed mechanism due to the speciation of metal and association of pH and Aliquat 336 is explained later in Section 3.5. On the other hand, the decreasing trend of extraction of either of the metals with the increase in equilibrium pH of the solution (alkalinity range) may be due to the significant change in speciation of vanadium (polymeric form: VO43−, HVO42−, V2O74− H2VO4−, V3O93− and V4O124−) and complex aqueous chemistry of tungsten, since it follows slow reactions and the predominant existence of para-tungstates at the pH range of 5.0 to 9.0.31 The limit of not reducing the solution pH < 5.0 may be explained based upon two reasons: (i) the possibility of tungsten precipitation as WO3 and vanadium as V2O5 at high acidic range in the solution, and (ii) formation of cationic species VO2+ at that range.31
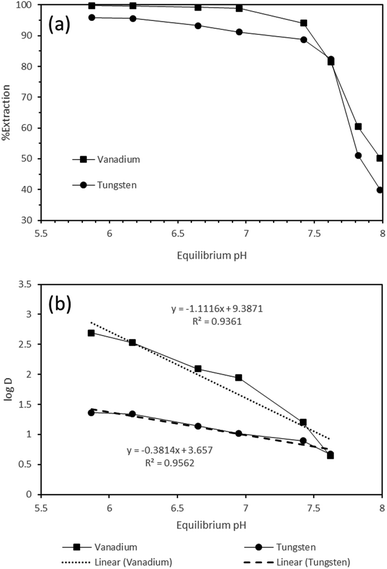 |
| Fig. 3 (a) Extraction of metals with equilibrium pH, (b) plot of log D vs. equilibrium pH. | |
3.4. Effect of chloride and its role in extraction
To understand the role of chloride ions during complexion of vanadium and tungsten with the extractant, the desired dose of NaCl, varying from 0.025 mol L−1 to 1 mol L−1, was added to the aqueous phase. For this experiment, the conditions were kept at the solution equilibrium pH of 7.98, phase ratio O
:
A = 1, phase contact during of 30 minutes and 0.5 mol L−1 of Aliquat 336. While increasing chloride ion concentration from 0.025 mol L−1 to 1.0 mol L−1, the efficacy in the extraction of vanadium showed a decreasing trend, i.e., from 65.37% to 57.24%, whereas tungsten extraction decreased from 57.63% to 46.66%. To further ensure the behavior of chloride on the extraction of metals, the relation of the distribution ratio (D) and [Cl−] was established and interpreted based upon the log
D vs. log[Cl−] plot (Fig. 4), which reveals a negative slope. This further indicated the negative effect on the metal extraction trend with the addition of chloride ions, though this effect was restricted to 10%. The adverse effect in extraction efficiency for both metals was attributed to the shift in extraction equilibrium on the excess supplement of the chloride ions in the aqueous solution. During extraction, as expected, there is the possibility of release of one mole of chloride into the aqueous phase while both metals become complexed with Aliquat 336 (anion exchange mechanism), and as a result, the equilibrium is shifted on further addition of chloride ion. The result obtained is in agreement with the previously reported works by various other authors while extracting metals from the mild acidic media of aqueous solution with Aliquat 336.31,35,40
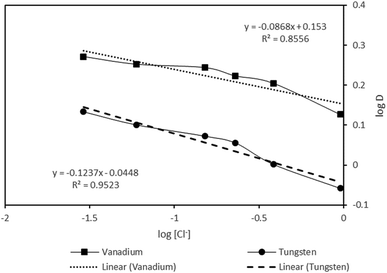 |
| Fig. 4 Plot of log D vs. log[Cl−]. | |
As explained in the above section, there is the possibility of releasing Cl− into the raffinate phase after extraction of both metals (tungsten/vanadium) with Aliquat 336. To establish the presence of Cl− after extraction, the raffinate obtained after equilibrating the leached solution with 0.5 mol L−1 of Aliquat 336 at a pH = 5.01 was subjected to testing against AgNO3 solution. Precipitation resulted due to AgCl formation (as per eqn (3)), which further confirmed the presence of Cl−.
|
AgNO3(aq) + Cl(aq)− → AgCl(s) + NO3(aq)−
| (3) |
3.5. Extraction mechanism
It is well known that both vanadium and tungsten metals are extracted in anionic form at slightly acidic solution medium, and they usually exist predominantly as oxo-anionic species with different degrees of condensation, ranging from 2 to 10 (poly-anionic species).48 Thus, based upon the slope analysis method of this investigation, the existence of vanadium as HV2O5− and tungsten as HWO4− was presumed at the mildly acidic pH range of the solution (pH < 6.0), which is strongly supported by the reported literature9,31 describing the speciation of V/W at varying solution pH ranges. In consequence of which, the above anionic form of either metal is readily exchanged with the chloride ion of Aliquat 336 during complex formation, with Aliquat 336 leading to the liberation of one mole of Cl− into the raffinate phase, and the mechanism can be expressed based on eqn (4) and (8). |
HV2O5[aq]− + CH3R3N+Cl−[org] ↔ CH3R3N × HV2O5[org] + Cl[aq]−
| (4) |
The equilibrium constant is represented as:
|
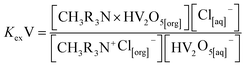 | (5) |
|
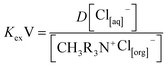 | (6) |
Taking the logarithm on both sides of the equation:
|
log D = log KexV + log[CH3R3N+Cl[org]−] − log[Cl[aq]−]
| (7) |
|
HWO4[aq]− + CH3R3N+Cl[org]− ↔ CH3R3N × HWO4[org] + Cl[aq]−
| (8) |
where the extraction equilibrium constant is:
|
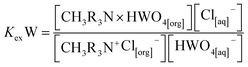 | (9) |
|
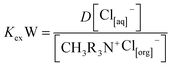 | (10) |
Taking the logarithm on both sides, we obtain:
|
log D = log KexW + log[CH3R3N+Cl[org]−] − log[Cl[aq]−]
| (11) |
The above proposed mechanism was described based upon the resulting slope of 0.44 and 0.46 (close to unity), as revealed from the log
D vs. log[Aliquat 336] plot, for tungsten and vanadium, respectively. The liberation of a mole of Cl− during complexation of either of the metals with Aliquat 336 was supported by the response in the test carried out for raffinate solution (described in Sec. 3.4) and the negative effect observed on the metal extraction trend upon supplement of excess chloride into the aqueous medium. The association of one H+ ion was also well evident from the resulting slope values, i.e., 1.11 and 0.38 for tungsten and vanadium, respectively. Moreover, the tendency of the complexation of HV2O5− and HWO4− in the organic phase was further supported by increasing solution equilibrium pH values to the respective studied pH of solution. The observations are in good agreement with the extraction behavior of Aliquat 336 in the reported studies.31,35,40,49
3.6. Diluent effect
Diluents used in solvent extraction greatly influence the extraction behavior of the organic extractant through the solvation interaction mechanism between the diluents and the extractant. The main role of diluents is to dissolve the extractant to modify the concentration of extractant in the organic phase and to reduce its viscosity.50 For the case of Aliquat 336, a highly viscous extractant, different diluents were compared in order to understand the role they possess in the extraction, based on previous literature indicating that diluents with a low dielectric constant favor higher extractant solvation,51,52 improving the extraction of the desired metal.53 As per theory, the solubility of the extractant is greatly influenced by the polar nature of the diluents used. Therefore, the selection of diluents is based on the solvents having low dielectric constant values. As the diluents should have no reactive affinity towards the extractant, when the dielectric constant of a solvent is low, then the tendency of the association with either extractant or metal is inhibited. In that way, extractants such as Aliquat 336 become readily solubilized in the diluent phase without losing their extracting capacity.53 In addition, as the diluents affect solvation of the extractant, they may lead to improved phase dispersion as well as coalescence properties of the extractant to a significant extent.51
The dielectric constant (DC) values of common diluents in the solvent extraction process are mostly in the range of 1.0 to 3.0.54 Therefore, benzene, cyclohexane, n-heptane, toluene, xylene and Exxsol™ D80 (dielectric constants shown in Table 1) were tested for the vanadium and tungsten extraction study, and results were examined. In this research, the diluents were examined at 0.01 mol L−1 and 0.05 mol L−1 of Aliquat 336 at the equilibrium pH of 5.87 and ambient temperature condition. As shown in Fig. 5, it was determined that greater extraction of both metals could be achieved while using n-heptane as the diluent, followed by cyclohexane and Exxsol™ D80. At 0.05 mol L−1 m−1, Aliquat 336 dissolved in either of the diluents; the extraction efficiency for vanadium varied from 89.9% to 97.1%, and in the case of tungsten, the extraction efficiency was within 84.9% to 92.0%.
Table 1 Dielectric constants of the various diluents54
Diluent |
Dielectric constant |
Kerosene |
2.0 |
Exxsol™ D80 |
1.98 |
Cyclohexane |
2.02 |
n-Hexane |
2.06 |
Benzene |
2.27 |
Toluene |
2.38 |
O-Xylene |
2.57 |
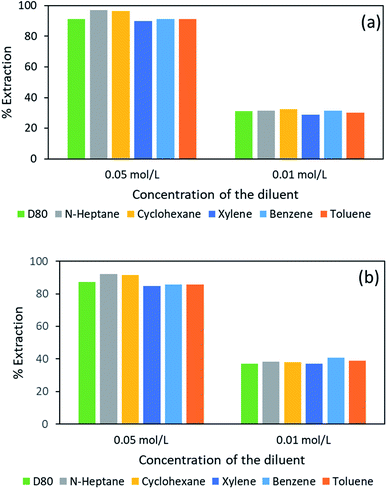 |
| Fig. 5 Effect of diluent on extraction of (a) vanadium and (b) tungsten. | |
The overall efficiency of tungsten and vanadium extraction varied within 5 to 6% with both studied Aliquat 336 concentration ranges, though they follow the order: n-heptane > cyclohexane > Exxsol™ D80 > benzene > toluene > xylene. The above observation can be explained based on the dielectric constant of the diluents; as the dielectric constant was low (1.9) for aliphatic diluents like n-heptane, the metal(s) extraction was maximized over other diluents. Besides the diluent cyclohexane (dielectric constant of 2.0), whose extraction efficiency followed that of n-heptane, the other three diluents (benzene, toluene, xylene) showed merely equal extraction behavior for both metals. The commercial non-aromatic diluent Exxsol™ D80 also showed better extraction tendency (though marginally lower than n-heptane and cyclohexane). It was evident that the diluents with low dielectric constants do favor higher solvation and thus metal extraction efficiency.53 Due to the extraction behavior and the economical aspect, the diluent Exxsol™ D80 was chosen as suitable for this study.
3.7. Temperature effect
To ascertain the thermodynamic behavior of Aliquat 336 for solvent extraction of tungsten and vanadium, the effect of temperature was investigated. As per the woks reported,2,4,8 in most of the liquid–liquid extraction systems, the thermodynamics results help predict the complexation behavior of the metal with extractants while separating it from the abundant waste liquors. Moreover, the distribution coefficient is strongly associated with the operating temperature of the extraction process. In addition, the issues of the highly viscous nature of the extractant (e.g. Aliquat 336, which hinders the overall metal loading) could be prevented by maintaining a slightly elevated temperature. To investigate such for this study, the temperature of either of the solution(s) was changed between 298 K to 323 K at the following conditions: 0.025 mol L−1 Aliquat 336 in Exxsol™ D80 at initial pH 5 (equilibrium pH 5.2) and A
:
O = 1. It is evident from the results in Fig. 6 that increasing the temperature of either of the phases has a significant effect by increasing extraction efficacy of vanadium from 65.47% to 71.20%, as well as tungsten from 61.93% to 75.52%. The enhancement of the extraction of both metals indicated the endothermic nature of the reaction. The different thermodynamic parameters, including enthalpy, entropy and free energy were evaluated based upon the thermodynamics eqn (12)–(14).
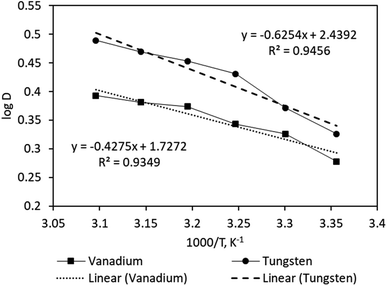 |
| Fig. 6 Plot of log D vs. 1000/T. | |
The log
D vs. 1000/T plot (shown in Fig. 6) based on the Van't Hoff relation (given in eqn (12)) could yield the slope and intercept corresponding to the enthalpy and entropy, respectively. The positive values of the resulting standard enthalpy of 8.19 kJ mol−1 and 11.97 kJ mol−1 for tungsten and vanadium, respectively, strongly favor endothermic behavior. The other thermodynamics parameters, including ΔG and ΔS, were evaluated based upon eqn (12) and (13) is displayed in Table 2.
|
ΔG = −RT ln Kex
| (12) |
Table 2 Thermodynamic results for extraction of tungsten and vanadium
Thermodynamic parameter |
Vanadium |
Tungsten |
ΔH, kJ mol−1 |
8.19 |
11.97 |
ΔS, J K−1 mol−1 |
33.07 |
46.70 |
ΔG, kJ mol−1 at 298 K |
−1.66 |
−1.95 |
By combining eqn (12) and (13) with eqn (4) and (8):
|
 | (14) |
where
R = 8.314 J mol
−1 K
−1.
Table 2 shows positive values of ΔSo for vanadium and tungsten extraction by Aliquat 336, which indicates the spontaneous nature of the process; having obtained a negative change in the free Gibbs energy ensures the viability of the extraction. The nitrogen atom of Aliquat 336 is assumed to be characterized by a positive enthalpy change,55 and also, because of the decrease in hydration of either of the metal ions (tungsten and vanadium), the randomness of the extraction process is well improved.
3.8. Extraction isotherm (McCabe–Thiele plot) and counter-current simulation (CCS)
To construct the McCabe–Thiele diagram, the leach liquor containing 666.5 mg L−1 of vanadium and 7237 mg L−1 of tungsten was contacted to 0.5 mol L−1 of Aliquat 336 at the changed phase ratio A
:
O from 1
:
1 to 10
:
1, while the total volume solution was kept constant. The experiment was performed at solution pH of 5.01 and phase contact time of 30 minutes. The McCabe–Thiele plots for the extraction of tungsten and vanadium are shown in Fig. 7. The plots predict that at A
:
O = 7
:
1, a quantitative extraction of tungsten and vanadium could be achieved at 3 stages and 2 stages, respectively. Moreover, almost 7-fold enrichment of either of these metals can be achieved at the above predicted condition.
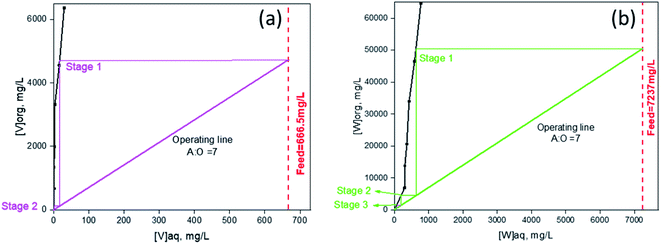 |
| Fig. 7 McCabe–Thiele plot for (a) vanadium and (b) tungsten extraction (*aq = aqueous, org = organic). | |
To validate the above predicted extraction isotherm, a three-stage as well as two-stage counter-current study for tungsten and vanadium were performed. The counter-current simulation (CCS) study was done for several cycles. To ensure consistency and performance, the typical raffinate samples obtained from the CCS study were read to analyze the substantial metal content retained in either of the phases. The raffinates after extraction of sample 1, 2 and 3 contain ≤1.6 mg L−1 of W and ≤1.0 mg L−1 of V, confirming greater than 99% of extraction of either of the metals at the simulation condition. In this connection, the simulation results are summarized and presented in Table 3.
Table 3 Counter-current simulation results for extraction of vanadium and tungstena
Sample |
Metal ion concentration at feed aqueous phase, mg L−1 |
Metal ion concentration at raffinate (aq), mg L−1 |
Metal ion concentration at organic phase, mg L−1 |
Metal ion concentration at LO, mg L−1 |
% extraction |
aq = aqueous phase, LO = loaded organic phase. |
For vanadium |
1 |
666.50 |
0.50 |
666.00 |
4662.00 |
99.92 |
2 |
666.50 |
1.07 |
665.43 |
4658.00 |
99.84 |
3 |
666.50 |
0.79 |
665.71 |
4660.00 |
99.88 |
![[thin space (1/6-em)]](https://www.rsc.org/images/entities/char_2009.gif) |
For tungsten |
1 |
7237.00 |
1.29 |
7235.71 |
50 650.00 |
99.98 |
2 |
7237.00 |
1.00 |
7236.00 |
50 652.00 |
99.99 |
3 |
7237.00 |
1.57 |
7235.43 |
50 648.00 |
99.98 |
To strip the enriched content of metal loaded-Aliquat 336 phase, adequate amount of loaded organic (LO) was generated at the above simulation condition. The loaded organic generated at the optimum condition is calculated to contain 4.66 g L−1 of vanadium and 50.65 g L−1 of tungsten, ascertaining ∼7 times enrichment with >99.9% extraction of either of the metals (vanadium and tungsten).
3.9. Screening of reagents for stripping studies
For the stripping studies, the loaded organic layer (LO) obtained from CCS study contained 4.66 g L−1 of vanadium and 50.65 g L−1 of tungsten that were used for the entire stripping study. Various authors have successfully stripped vanadium and tungsten from the ammine-based reagents using sodium hydroxide,40,48,49 sodium carbonate,11,31,39,56,57 sodium bicarbonate,11,31 sodium nitrate and sodium chloride.11,31
Nevertheless, it was also evident that adoption of the above alkaline reagents and/or salts are more effective over other acidic reagents. To investigate the behavior of these reagents for stripping of tungsten/vanadium, an initial screening study was conducted to choose a desirable stripping reagent for efficient back extraction of metals from the LO–Aliquat 336 medium. While keeping the stripping solution concentration for either of the reagents (NaOH, Na2CO3, NaCl and NaNO3) fixed at 2 mol L−1, the stripping study was examined at the phase ratio O
:
A = 1. In this experimental investigation, stripping time of 30 min was kept constant (the time was optimized from preliminary stripping results). Of these reagents, NaOH appears to have high stripping ability over others, and the overall stripping trend follows the order NaOH > NaNO3 > Na2CO3 > NaCl. However, overall stripping efficiency was maximized to 65% vanadium and 23% tungsten, respectively (results are shown in Table 4).
Table 4 Results for stripping of tungsten and vanadium using various stripping reagents
Stripping agent, 2 mol L−1 |
% stripping |
Vanadium |
Tungsten |
NaOH |
64.59 |
23.00 |
Na2CO3 |
35.13 |
24.15 |
NaNO3 |
35.90 |
25.07 |
NaCl |
0.21 |
0.22 |
To enhance stripping efficacy, mixtures of pairs of reagents were tested, and results are reported in Table 5. From results, the combinations of NaOH and NaCl showed better performance (62% for vanadium and 42% for tungsten) over other combinations, though the combination of NaOH and NaNO3 was also somewhat effective. The NaOH + Na2CO3 combination showed a promising extraction exclusively for vanadium, but it was very poor for tungsten stripping. Thus, from this investigation, suitable adoption of NaOH + NaCl mixture was confirmed for stripping of both metals from LO phase. To improve the stripping efficiency, their concentration levels were varied and investigated further.
Table 5 Results for stripping using mixed reagents
Stripping agent |
% stripping |
Vanadium |
Tungsten |
1 mol L−1 of NaOH + 1 mol L−1 of NaCl |
62.39 |
43.89 |
1 mol L−1 of NaOH + 1 mol L−1 of Na2CO3 |
64.18 |
33.31 |
1 mol L−1 of NaOH + 1 mol L−1 of NaNO3 |
62.02 |
42.03 |
3.10. Stripping studies: strip solution concentration variation study
After examining different combinations of stripping reagents, the mixture of NaOH + NaCl was found to be promising compared to the remaining mixtures applied to obtain V/W from LO-Aliquat 336. To obtain a higher stripping ability, either concentration of the reagents, for example NaOH/NaCl, was changed from 0.5 to 2.5 mol L−1, while keeping the total concentration fixed. The best combination was assumed to be the 50% mixture of each, and in particular, 2.5 mol L−1 NaCl + 2.5 mol L−1 NaOH resulted in a maximum of 46.14% tungsten and 61.52% vanadium stripping from LO (Fig. 8). From this study, the stripping of both metals was not quantitative when adopting several combinations of the above reagents, which may be due to the content of the enriched quantity of metal (mainly tungsten) that was not readily extractable with the stripping reagents used in this study. Nevertheless, it was seen from the literature that stripping of numerous metal ions from the Aliquat 336 phase seems appealing when metal content11,31 is of low level at the LO medium, unlike in this case. However, it is essential to regenerate the Aliquat 336 vis-à-vis efficient stripping of tungsten/vanadium from the LO phase, and therefore, to achieve it, a stripping isotherm study was further investigated and reported (described in a later section).
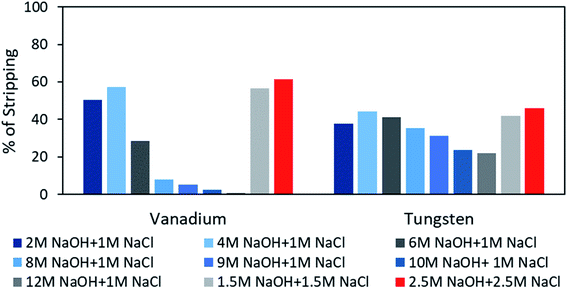 |
| Fig. 8 Effect of mixed reagents at different concentrations on stripping of vanadium and tungsten (M = mol L−1). | |
3.11. Temperature effect on stripping of tungsten and vanadium
The stripping of vanadium and tungsten with 2.5 mol L−1 NaCl + 2.5 mol L−1 NaOH displayed a maximum of 61% and 46% at the ambient temperature condition, and hence, to improve the extraction efficiency for both metals, the effect of temperature (range of 298 K to 328 K) was examined. Table 6 shows that the stripping of vanadium increased from 61.52 to 71.12%, whereas for tungsten it was enhanced from 46.14% to 52.85%, while augmenting the solution temperature from 25 °C to 45 °C, and thereafter, a plateau value was attained. The above observation is in good agreement with earlier studies on stripping metal ions from LO media (mostly for ionic liquid based reagents).57 However, it is essential to regenerate the Aliquat 336 vis-à-vis efficient stripping of tungsten/vanadium from the LO phase, and therefore, to achieve it, the stripping isotherm study was further investigated and is described in the next section.
Table 6 Results for stripping of tungsten and vanadium at different temperatures
Temperature, K |
% stripping |
Vanadium |
Tungsten |
298 |
61.52 |
46.14 |
308 |
63.30 |
46.30 |
318 |
71.12 |
52.85 |
328 |
71.31 |
53.35 |
3.12. Stripping isotherm and counter-current simulation
To confirm the required stages for quantitative removal of tungsten and vanadium from the organic phase, the phase ratio of LO (bearing 4.66 g L−1 of vanadium and 50.65 g L−1 of tungsten) and 2.5 mol L−1 NaCl + 2.5 mol L−1 NaOH (strip liquor) was varied from 1
:
5 to 5
:
1 at the temperature of 45 °C. Based on the results, the stripping McCabe–Thiele diagram was constructed as shown in Fig. 9. The stripping isotherm plot predicted a stripping of more than 98% for W/V at the SO
:
SS (SO – stripped organic, SS – stripping solution) of 2
:
1 in three stages for vanadium and five stages for tungsten. It was noticed that stripping efficiency with unity phase ratio was only considerable for vanadium, where five stages were required for more than 98% stripping. Therefore, the above predicted phase ratio, i.e., SO
:
SS = 2
:
1, was chosen as the ideal for simulation study.
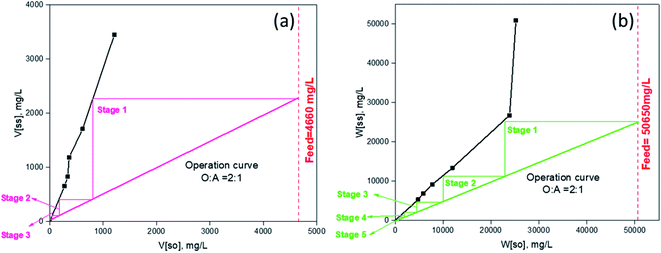 |
| Fig. 9 McCabe–Thiele plot for stripping of (a) vanadium and (b) tungsten (*SO = stripped organic, SS = stripping solution). | |
To validate the results predicted by the stripping isotherm, a 6-stage counter-current study was performed for several cycles. The stripping solution samples were analysed to determine the total metal stripped from LO phase. The stripped organic phase after 6 stages was calculated to contain <93.48 mg per L V and <800 mg per L W, which confirms >98% stripping of both metals at the simulation condition. In order to separate vanadium and tungsten, selective precipitation can be obtained by controlling the stripping solution pH. As illustrated in the investigation by Choi et al. (2018), the crystalline form of CaWO4 can be selectively precipitated in solution pH values between 7–11 from the solution bearing vanadium and tungsten.1 Later, the vanadium content can be selectively precipitated at pH ∼ 9.0 as NH4VO3.58
4. Conclusion
The comprehensive liquid–liquid extraction of tungsten and vanadium by Aliquat 336 in Exxsol™ D80 from the spent SCR catalyst leach liquor containing approximately 7000 mg L−1 of tungsten and 700 mg L−1 of vanadium was investigated. Due to the unique speciation and extraction behaviour of both tungsten and vanadium with Aliquat 336 at the solution pH of 5.0, more than 99% extraction for both metals was confirmed. The presence of the anionic forms of tungsten and vanadium as HV2O5− and HWO4−, respectively, at the mild acidic solution pH (equilibrium pH 5.56) favours an anion exchange mechanism while complexing with Aliquat 336. The association of one mole each of Aliquat 336 and H+ ions at the extracted complexed species has been revealed from the slope analysis results. The addition of chloride ion shows a negative effect due to the shifting of extraction equilibrium, which further strongly supports the proposed extraction mechanism. The diluent effect was examined, and Exxsol™ D80 was determined to be a suitable diluent for the process. The quantitative extraction of either of the metals (tungsten/vanadium) can be achieved at the predicted extraction isotherm condition of leach liquor at equilibrium pH 5.56, with 2 stages for vanadium and 3 stages for tungsten, respectively, at phase ratio O
:
A = 1
:
7 by 0.5 mol L−1 Aliquat 336, which was validated from the 6-cycle counter-current simulation study. The subsequent raffinate and loaded organic resulting after CCS study was read to contain <1 mg L−1 of either of the metals and 4.66 g L−1 of vanadium and 50.65 g L−1 of tungsten, ensuring a 7-fold enrichment of both metals while extracting from the original leached liquor phase. Stripping screening effects proved that the adoption of a mixture, i.e., NaOH + NaCl, over the sole stripping agents led to a higher stripping efficiency in this study. The significant enhancement of stripping efficiency of metals (tungsten/vanadium) took place with increasing stripping temperature up to 45 °C. The stripping isotherm confirms a complete stripping at SO
:
SS = 2
:
1 in three stages for vanadium and five stages for tungsten, which was later confirmed from the CCS study. The proposed process is promising exclusively on the suitable adoption of Aliquat 336 as a green ionic liquid (IL) for effective extraction of both vanadium and tungsten from alkaline leached media.
Conflicts of interest
There are no conflicts to declare.
Acknowledgements
This study was supported by the R&D Center for Valuable Recycling (Global-Top R&D Program) of the Ministry of Environment (Project Number: 2019002230001), Korea.
References
- I. H. Choi, Study on the recovery of vanadium and tungsten from spent V2O5-WO3/TiO2 Catalyst, PhD dissertation thesis, Department of Resources Recycling, University of Science and Technology (UST), Daejeon, Korea, 2018.
- W. Wu, C. Wang, W. Bao and H. Li, Hydrometallurgy, 2018, 179, 52–59 CrossRef CAS.
- W. C. Wu, T. Y. Tsai and Y. H. Shen, Minerals, 2016, 6(4), 107 CrossRef.
- Y. Huo, Z. Chang, W. Li, S. Liu and B. Dong, Waste Biomass Valorization, 2015, 6, 159–165 CrossRef CAS.
- I. H. Choi, G. Moon, J. Y. Lee and R. K. Jyothi, J. Cleaner Prod., 2018, 197, 163–169 CrossRef CAS.
- H. I. Kim, G. Moon, I. H. Choi, J. Y. Lee and R. K. Jyothi, J. Cleaner Prod., 2018, 187, 449–458 CrossRef CAS.
- R. K. Jyothi, G. Moon, H.-R. Kim, J.-Y. Lee and I. H. Choi, Hydrometallurgy, 2017, 175, 292–299 Search PubMed.
- I. H. Choi, G. Moon, J. Y. Lee and R. K. Jyothi, Hydrometallurgy, 2018, 178, 137–145 CrossRef CAS.
- T. Nakamura, S. Nishihama and K. Yoshizuka, Solvent Extr. Res. Dev., 2009, 16, 47–56 CAS.
- J. Coca, F. V. Díez and M. A. Morís, Hydrometallurgy, 1990, 25, 125–135 CrossRef CAS.
- M. A. Olazabal, M. M. Orive, L. A. Fernandez and J. M. Madariaga, Solvent Extr. Ion Exch., 1992, 10, 623–635 CrossRef CAS.
- B. D. Pandey, V. Kumar, D. Bagchi, R. K. Jana and Premchand, Miner. Process. Extr. Metall. Rev., 2001, 22, 101–120 CrossRef CAS.
- L. Zeng and C. Y. Cheng, Hydrometallurgy, 2010, 101, 141–147 CrossRef CAS.
- M. Atanassova and V. Kurteva, RSC Adv., 2016, 6, 11303–11324 RSC.
- M. Atanassova, V. Kurteva and I. Dukov, RSC Adv., 2016, 6, 81250–81265 RSC.
- A. B. Lende and P. S. Kulkarni, J. Water Process Eng., 2015, 8, 75–81 CrossRef.
- H. Liu, Y. Min Zhang, J. Huang, T. Liu, N. Nan Xue and Q. Hua Shi, Chem. Eng. Res. Des., 2017, 123, 111–119 CrossRef CAS.
- H. Liu, Y. Min Zhang, J. Huang, T. Liu, N. Nan Xue and D. Shuang Luo, Chem. Eng. Res. Des., 2018, 136, 262–270 CrossRef CAS.
- M. R. Yaftian, M. I. G. S. Almeida, R. W. Cattrall and S. D. Kolev, J. Membr. Sci., 2018, 545, 57–65 CrossRef CAS.
- H. I. Gomes, A. Jones, M. Rogerson, I. T. Burke and W. M. Mayes, Environ. Sci. Pollut. Res., 2016, 23, 23034–23042 CrossRef CAS PubMed.
- W.-J. Guo and Y.-H. Shen, Environ. Prog. Sustainable Energy, 2016, 35, 156–160 CrossRef CAS.
- T. H. Nguyen and M. S. Lee, Sep. Sci. Technol., 2015, 50, 2060–2065 CAS.
- X. Zhu, W. Li, Q. Zhang, C. Zhang and L. Chen, Hydrometallurgy, 2018, 176, 42–48 CrossRef CAS.
- M. K. Dinker, N. V. Patil and P. S. Kulkarni, Polym. Int., 2016, 65, 1387–1394 CrossRef CAS.
- T. Ogi, T. Makino, F. Iskandar, E. Tanabe and K. Okuyama, Bioresour. Technol., 2016, 218, 140–145 CrossRef CAS PubMed.
- T. Ogi, T. Makino, K. Okuyama, W. J. Stark and F. Iskandar, Ind. Eng. Chem. Res., 2016, 55, 2903–2910 CrossRef CAS.
- H. Peng, Z. Liu and C. Tao, Water, Air, Soil Pollut., 2017, 228, 272 CrossRef.
- M. Regadío, T. Vander Hoogerstraete, D. Banerjee and K. Binnemans, RSC Adv., 2018, 8, 34754–34763 RSC.
- A. Cheraghi, M. S. Ardakani, E. Keshavarz Alamdari, D. Haghshenas Fatmesari, D. Darvishi and S. K. Sadrnezhaad, Int. J. Miner. Process., 2015, 138, 49–54 CrossRef CAS.
- X. Li, Z. Deng, C. Wei, C. Li, M. Li, G. Fan and H. Huang, Hydrometallurgy, 2015, 154, 40–46 CrossRef CAS.
- T. H. Nguyen and M. S. Lee, Geosyst. Eng., 2016, 19, 247–259 CrossRef CAS.
- B. Shakib, M. Torab-Mostaedi, M. Outokesh and M. Asadollahzadeh, Sep. Sci. Technol., 2019, 1–11 CrossRef.
- Q. Shi, Y. Zhang, J. Huang, T. Liu, H. Liu and L. Wang, Sep. Purif. Technol., 2017, 181, 1–7 CrossRef CAS.
- R. Zheng, S. Bao, Y. Zhang and B. Chen, Minerals, 2018, 8, 1–12 Search PubMed.
- L. Zeng and C. Yong Cheng, Hydrometallurgy, 2009, 98, 10–20 CrossRef CAS.
- K. K. Sahu, A. Agrawal and D. Mishra, J. Environ. Manage., 2013, 125, 68–73 CrossRef CAS.
- P. Ning, H. Cao and Y. Zhang, Sep. Purif. Technol., 2009, 70, 27–33 CrossRef CAS.
- R. G. Talla, S. U. Gaikwad and S. D. Pawar, Indian J. Chem. Technol., 2010, 17, 436–440 CAS.
- Y. Bal, K. E. Bal and G. Cote, Miner. Eng., 2002, 15, 377–379 CrossRef CAS.
- Y. A. El-Nadi, N. S. Awwad and A. A. Nayl, Int. J. Miner. Process., 2009, 92, 115–120 CrossRef CAS.
- A. Rout, S. Wellens and K. Binnemans, RSC Adv., 2014, 4, 5753–5758 RSC.
- A. Rout, E. R. Souza and K. Binnemans, RSC Adv., 2014, 4, 11899–11906 RSC.
- S. Riaño, M. Petranikova, B. Onghena, T. Vander Hoogerstraete, D. Banerjee, M. R. S. Foreman, C. Ekberg and K. Binnemans, RSC Adv., 2017, 7, 32100–32113 RSC.
- M. Atanassova, V. Kurteva, L. Lubenov and I. Billard, RSC Adv., 2014, 4, 38820–38829 RSC.
- W. Wei, C. W. Cho, S. Kim, M. H. Song, J. K. Bediako and Y. S. Yun, J. Mol. Liq., 2016, 216, 18–24 CrossRef CAS.
- W. Wei, D. H. K. Reddy, J. K. Bediako and Y. S. Yun, Chem. Eng. J., 2016, 289, 413–422 CrossRef CAS.
- E. Padhan and K. Sarangi, Hydrometallurgy, 2017, 167, 134–140 CrossRef CAS.
- Y. Bal, K. E. Bal, G. Cote and A. Lallam, Hydrometallurgy, 2004, 75, 123–134 CrossRef CAS.
- R. K. Mishra, P. C. Rout, K. Sarangi and K. C. Nathsarma, Hydrometallurgy, 2011, 108, 93–99 CrossRef CAS.
- N. K. Batchu and K. Binnemans, Hydrometallurgy, 2018, 177, 146–151 CrossRef CAS.
- G. M. Ritcey and A. W. Ashbrook, Solvent Extraction. Principles and Applications to Process Metallurgy. Part I, 1984 Search PubMed.
- K. Rezaei and H. Nedjate, Hydrometallurgy, 2003, 68, 11–21 CrossRef CAS.
- V. S. Smidt, Amine extraction, Israel Program of Scientific Translations, 1971 Search PubMed.
- P. K. Kuipa and M. A. Hughes, Sep. Sci. Technol., 2002, 37, 1135–1152 CrossRef CAS.
- N. Swain, S. Pradhan and S. Mishra, Miner. Eng., 2019, 139, 105872 CrossRef.
- J. F. Paulino, J. C. Afonso, J. L. Mantovano, C. A. Vianna and J. W. Silva Dias Da Cunha, Hydrometallurgy, 2012, 127–128, 121–124 CrossRef CAS.
- Y. Yang, B. Xie, R. Wang, S. Xu, J. Wang and Z. Xu, Hydrometallurgy, 2016, 164, 97–102 CrossRef CAS.
- L. Luo, T. Miyazaki, A. Shibayama, W. Yen and T. Fujita, Miner. Eng., 2003, 16, 665–670 CrossRef CAS.
|
This journal is © The Royal Society of Chemistry 2020 |
Click here to see how this site uses Cookies. View our privacy policy here.