DOI:
10.1039/D0RA02979C
(Review Article)
RSC Adv., 2020,
10, 20231-20244
Application progress of enhanced coagulation in water treatment
Received
2nd April 2020
, Accepted 19th May 2020
First published on 27th May 2020
Abstract
Water industries worldwide consider coagulation/flocculation to be one of the major treatment methods for improving the overall efficiency and cost effectiveness of water and wastewater treatment. Enhancing the coagulation process is currently a popular research topic. In this review article, the latest developments in enhanced coagulation are summarized. In addition, the mechanisms of enhanced coagulation and the effect of process parameters on processing efficiency are discussed from the perspective of ballast-enhanced coagulation, preoxidation, ultrasound, and composite coagulants. Finally, improvements and new directions for enhanced coagulation are proposed.
1. Introduction
Coagulation is one of the most common phenomena in nature and artificially enhanced water treatment systems. Coagulation is a process in which small particles are combined into larger aggregates (flocs) and dissolved organic matter is adsorbed onto particulate aggregates so that these impurities can be removed in the subsequent solid/liquid separation processes.1 The mechanism for the removal of organics via coagulation has three main aspects:2 (1) positively charged metal ions and negatively charged organic colloids are electrically neutralized, destabilized and aggregated; (2) metal ions and soluble organic matter molecules form insoluble complexes and precipitates; and (3) physical and chemical adsorption of organics occurs on the surface of alum. As environmental pollution problems become more serious and water quality standards become more stringent, conventional coagulation technology has clearly failed to meet people's requirements for water quality safety. Enhanced coagulation and optimized coagulation are improved based on existing water treatment process facilities and by considering the operating conditions of previous and subsequent process flows to achieve the effect of advanced water and wastewater treatment.
The concept of enhanced coagulation has a long history and was discussed in a paper in the American AWWA Journal in 1965. The enhanced coagulation proposed by the American Hydraulic Association in the 1990s refers to the improvement of organic matter removal rates by increasing the amount of coagulant in the conventional coagulation treatment process of water while ensuring the turbidity removal effect process.3 This concept of enhanced coagulation is based on an increase in the amount of coagulant added or the coagulation process controlled by the reaction pH conditions. Optimized coagulation is proposed based on enhanced coagulation, which is a coagulation process with multiple goals: maximizing particulate matter and turbidity removal, maximizing TOC and DBP precursor removal, reducing residual coagulant content, reducing sludge production, and minimizing production costs.4,5
In recent years, the intensity of research on enhanced coagulation has been unprecedentedly increased, with many scholars conducting more in-depth research on enhanced coagulation. For example, studies have attempted to gain an in-depth understanding of the characteristics of organic matter in water bodies, identify organic matter removal rules to establish an organic matter removal mode, and summarize the mechanisms of enhanced coagulation removal of organic matter. Previous studies found that increases in efficiency are affected not only by the dose and pH of the coagulant but also by the nature and distribution of the organic matter and particulate matter in the water, including the temperature, hydraulic condition, and coagulant morphology.6–8 With the continuous expansion of modern coagulation treatment processes, the concept of pollutants in water bodies has become increasingly extensive, the treatment difficulty has become increasingly difficult, and ways to strengthen coagulation have become more diverse. For example, permanganate oxidation-assisted coagulation has been widely used to improve turbidity and natural organic matter (NOM) and algae removal in the coagulation–filtration process.9,10 Ballast microsand and magnetic powder are very mature technologies,11,12 including “Actiflo” technology and “CoMag” technology. Researchers have further enhanced the application of ballast technology in wastewater treatment by modifying or changing the dosing materials based on this principle. Jessica13 studied the potential impact of adding powdered activated carbon or organoclay (OC) adsorbent and ferric chloride (FeCl3) coagulant together on the coagulation, and the results showed that the turbidity of the clarified water sample was lower when OC was added during the coagulation process and powdered activated carbon removed more than half or almost all of the dissolved aromatic compounds. Kadouche14 used synthetic hydroxyapatite in combination with chitosan and showed that it can effectively remove 88–95% of copper and zinc ions. Chitosan significantly improves the speed of coagulation and precipitation. Another popular topic of research is the development and utilization of new coagulants, such as inorganic polymer flocculants, biopolymer flocculants and natural coagulants.15 Many problems occur under enhanced coagulation. For example, preoxidation may damage the cell membrane, resulting in toxin release and increased taste and odor,16 and the addition of microsand will adversely affect the maintenance of the pump. Therefore, it is not only necessary but also meaningful to study the working mechanism, challenges and new discoveries associated with strengthening the coagulation process to minimize its disadvantages. This article summarizes the application of enhanced coagulation in water treatment, including the current advantages and disadvantages, and discusses the challenges associated with the development of enhanced coagulation technology in the future.
2. Ballasted reaction nuclei enhance coagulation
The process of ballasted reaction nuclei-enhanced coagulation mainly refers to improving the flocculation stage to strengthen its sedimentation characteristics and optimize the flocculation agent and hydraulic conditions in the flocculation stage to form flocs with good sedimentation performance.17–19
2.1 Technical principle
Floc characteristics are important parameters for controlling the flocculation process and have a significant impact on subsequent sedimentation units and effluent water quality. Related research results showed20 that flocs with large particle sizes and high densities have higher sedimentation speeds and better solid–liquid separation effects than those with small particle sizes and low densities and the turbidity of water after they sunk was correspondingly lower. Therefore, the formation of flocs with good sedimentation performance is an important way to improve the water quality of submerged water.12,21 Miyahara22 confirmed the higher fractal dimension and higher density of flocs with larger particle diameters using the Stokes formula. Many researchers17,18,23,24 believe that denser flocs have higher strength than less dense flocs, are not easily broken and are better for achieving solid–liquid separation. Ballasted nuclei-enhanced coagulation technology aims to increase the speed of floc formation and the density of flocs through ballasted nuclei, such as silica sand, magnetite sand, anthracite, recycled glass, etc., so that the flocs can settle quickly.21,25 The ballast nuclei strengthening flocculation process keeps the core medium in suspension by mixing, and the mixing strength is controlled by the specific gravity and size of the nuclei medium. Ballast nuclei with different specific gravities have the advantages of increasing the sedimentation speed of the shallow layer or increasing the particle removal rate because the specific gravity of the flocs is determined by the specific gravity of the nuclei.17 Different ballast nuclei have different characteristics. For example, the total suspended solid load of magnetite sand is twice that of silica sand, although the residual turbidity after sedimentation increases.25
2.2 Microsand
The ballasted sand flocculation (BSF) technique is based on coagulation and flocculation with the injection of microsand by increasing the sedimentation rate26 and overflow rate of the microsand to enhance coagulation. Depending on the type of wastewater, the amount of microsand added, and the amount of flocculant, there are significant differences in treatment effects. The ballasted sand flocculation technique has appeared to be an efficient method for the treatment of water and wastewater. The BSF trade named “Actiflo” was introduced in 1990.17 The BSF unit is shown in Fig. 1.27 Before the first stage, the water is typically screened through a settling tank to remove large particulates. Then, the coagulant, microsand and polymer are injected and then mixed and stirred at a high rpm to fully coagulate. In the second stage, the maturation process, gentle mixing is performed at a low rpm to enhance the coagulation process. The third stage is clarification, wherein the mixed flocs and influent move downward in the unit. The clarified effluent is then either discharged into natural water bodies or directed to the next treatment process.
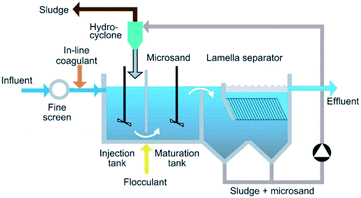 |
| Fig. 1 Schematic of a ballasted sand flocculation process.20 | |
The BSF process improves the sedimentation speed and overflow rate, reduces the footprint of the system, and greatly reduces the cost of coagulation treatment. Many researchers have conducted in-depth research. For example, Desjardins17 conducted comparative experiments in three different water treatment plants, and the results showed that the amount of coagulant was the key parameter that controlled the response parameters. Plant no. 1 confirmed that the amount of coagulant was the key to clarification. The raw water of plant no. 2 was different, and the effect of coagulant dose on clarification was small. The results were consistent with the research by Edzwald.28 Experiments were conducted at plant no. 3 in winter, and the quality of the raw water was very similar to that of the water in plant no. 1. Considering the cold water conditions, the hydraulic load rate was increased by 10 m h−1 compared to that of plant no. 1. The effects of coagulation time and precipitation time were investigated, and the results showed that as the reaction kinetics decreased with decreasing temperature, a longer contact time favored floc growth in cold water, excessive microsand (7 mg L−1) caused erosion of the flocs, and a low microsand dose (1 mg L−1) caused poor flocculation. James29 found that the sedimentation velocity of discrete microsand particles and discrete ballast flocs fit the traditional sedimentation theory with reasonable accuracy. The key to increasing the sedimentation rate is to increase the size and roundness of the floc30 and reduce its shape factor. The most important factors contributing to the high settling velocities of ballasted flocs seem to be the increased floc density. Zhu31 used alum and anionic polymers as the main coagulants and used silica sand as a carrier. The settleability of the silica sand was improved approximately five times, and the removal efficiency of suspended solids and BOD was 98% and 60%, respectively. Sumant Kumar20 summarized the combined sewer overflow (CSO) treatment method. Depending on the type and characteristics of the water/wastewater, the amount of flocculant (cation/anionic polymer) ranged from 0.3 to 1 mg L−1. The size was 40–150 μm, and the dose was 2–12 g L−1. In most cases, the turbidity, total suspended solids (TSS) and TP removal rates were reported to be over 90%, while the BOD was over 60%. On this basis, researchers have conducted further research. Sieliechi23 proved that the root cause of the improved flocculation of sedimentation in ballast aggregates is related not only to the increase in the specific gravity of flocs but also to the increase in the specific gravity of the ballast. The sediment volume is relatively small in the CSO treatment, which proves the reorganization of flocs. Alan26 proposed a new method to predict the settling conditions encountered by concentrated suspensions containing sand and mud floc mixtures. The results showed that by considering the total reflux effect of the two fractions, the best results can be provided. A frame model was used to predict hindered settlement conditions in various sand and mud mixtures. In addition, there are many literature data showing the improvement of the overall coagulation efficiency of microsand-enhanced flocculation.21,31,32
The BSF process has been widely used in many countries, and the advantages of the BSF process are as follows:20 (1) the floor area is reduced by 5–20 times, which reduces the cost of equipment installation and operation; (2) its adaptability is very high, the treatment effect does not change with the change in raw water conditions, and it can be applied to surface water, wastewater and industrial sewage; and (3) it only takes 20–30 min for the system to reach stable operations. The limitations of the system are as follows: (1) the chemical reagent dose is increased; (2) the microsand will adversely affect the operation and maintenance of the pump; and (3) there is a low removal rate during startup. The BSF process has proven to be a promising technology that can be used to clarify drinking water and reduce pollution loads before wastewater and COS treatment systems enter biological processes or natural water systems, and it has a small footprint and low cost. However, in some applications, it may be better to replace microsand with a different core medium: (1) nuclei media with a higher density than that of microsand can increase the specific gravity and sedimentation speed of flocs and achieve a high rate clarification; (2) nuclei media with adsorption–desorption capabilities can simultaneously achieve a high rate of clarification and adsorption of pollutants;33 (3) dolomite as a nuclei medium can increase the alkalinity of water while increasing the sedimentation speed;34 and (4) low-density nuclei media can reduce the mixing strength, thereby limiting the shear force of sensitive flocs. Lapointe25 evaluated the effects of 5 nuclei media (anthracite, recycled broken glass, conventional silica sand, garnet sand, and magnetite sand) on ballast flocculation. The results show that the choice of core media is determined by the sedimentation water quality and the highest applicable flow rate. The highest applicable flow rate can directly affect operating costs.
2.3 Magnetic technology
To achieve separation, magnetic separation technology affects the aggregation of particles through various external forces, such as magnetic gravity, van der Waals forces, an electric double layer, gravity, Brownian motion and fluid motion. Ferromagnetic materials have been widely used in magnetic separation processes35–37 and successfully applied in the separation and recovery of solid waste, nanotechnology, ultra-purification and biotechnology.38–41 CoMag technology is a new water treatment technology combining conventional coagulation and magnetic separation. On the basis of conventional coagulation, magnetic seeds are used as flocculated nodules and they work to combine flocs to form composite flocs. Under the action of an external magnetic field, precipitation is accelerated to improve the treatment efficiency.42 Magnetic separation is the core part of CoMag technology. The first patent for magnetic separation was proposed by William Fullarton in 1792 and applied to the beneficiation industry.43 In the late 1960s, the Massachusetts Institute of Technology developed the first set of magnetic separation equipment and proposed an iron-free, high-gradient magnetic separation patent. In the late 1980s, Sweden began to apply magnetic disk separation to steel wastewater treatment, thus marking the beginning of magnetic technology in the field of water treatment.
In recent years, the CoMag process has been widely used in water treatment due to its advantages, such as a short solid–liquid separation time and good running effect. Li38 used magnetite (Fe3O4) for magnetic seed flocculation combined with high-gradient superconducting magnetic separation (HGMS) to remove arsenic. Under the conditions of a polymeric ferric sulfate (PFS) dose as a flocculant of 108.75 mg L−1 and a seeding time of 15 min, the efficiency of removing arsenic reached 94.5%. Studies have shown that ultrafine magnetic particles have low separation efficiency and recovery due to low magnetic and collision efficiency issues. Many techniques induce ultrafine particles to form aggregates by increasing the effective particle size and mass.41,44,45 Mandel46 used magnetic nanocomposite particles as the flocculation core of iron hydroxide and protected its surface with silicon dioxide to avoid its dissolution, which is conducive to recycling. Under the action of external magnetic fields, flocs adsorb and trap heavy metal ions. Shuang47 prepared a new quaternized magnetic resin, NDMP, to study its adsorption behavior in dye wastewater. The results showed that NDMP has good adsorption, regeneration and separation and is an efficient adsorbent. Many researchers have also synthesized various types of magnetic particles for removing algae from lakes.48–50 The interaction of forces in the flocculation process is one of the important factors controlling the flocculation effect. Under the action of an external magnetic field, when a single particle approaches another particle, the external force on the particle changes (such as with gravity, van der Waals forces, magnetic attraction, etc.). The size of the external force depends on various parameters, such as the particle size, particle density, magnetic susceptibility and magnetic field. Therefore, a single study of the effects of individual forces is needed. Luo51 summarized the effects of various forces in magnetic flocculation and conducted in-depth discussions on the factors of magnetic flocculation stability, such as collision efficiency, flocculation frequency, flocculation potential energy, and flocculation kinetics.
Magnetic flocculation can be used for separation and has applications in improving the solid coagulation rate, producing clean water, increasing the amount of filtration and reducing the amount of flocculant added. Magnetic flocculation has many advantages, such as no chemical use, fast separation, low operating costs, relatively few ecological problems, space savings, etc.52,53 The applications of ballast flocculation are summarized in Table 1.
Table 1 Application of ballast flocculation
Raw water |
Ballast agent |
Coagulation |
Polymer |
Ballast agent dose (g L−1) |
Particle size |
Coagulation dose (mg L−1) |
pH |
Stirring intensity (rpm) |
Observation |
Reference |
Surface water |
Microsand |
Al2(SO4)3 |
PASS-100 |
5 |
<160 mm |
6.1–9.3 |
6 |
|
Filterability is more sensitive to coagulant and microsand dosage |
17 |
Combined sewer overflow |
Silica sand |
Alum |
A-3330 |
3 |
74–250 μm |
9.7–17.8 |
|
|
Suspended solids and BOD removal efficiencies of >98% and >60% |
31 |
Microalgae |
Flocculated biomass |
FeCl3 |
PAA |
|
|
50 |
|
200 |
Flocculation efficiency achieved approximately 90% |
32 |
Synthetic water |
Pozzolana particles |
FeCl3 |
|
0.5 |
|
|
6 |
250 |
Describes the turbulent viscous effect of floc compaction |
23 |
Distillery wastewater |
Activated carbon |
FeCl3 |
|
1.4 |
|
840 |
7 |
3–250 |
Precipitation rate increased by 8 times |
18 |
Synthetic water As(V) |
Magnetite |
PFS |
CPA |
0.3 |
|
108.75 |
|
200 |
The removal efficiency of arsenic was more than 90.9% |
38 |
Backside grinding wastewater |
FeO·Fe2O3 |
PAC |
|
1.24 |
310–450 nm |
10 |
5 |
30–100 |
PAC use was reduced sixfold |
19 |
Synthetic water |
MNPs |
Al2(SO4)3 |
|
0.1–5 |
|
|
7 |
20–100 |
Significant removal of dissolved organic matter (98.7%) |
35 |
3. Chemical oxidation-enhanced coagulation
The study of chemical oxidization-enhanced coagulation is one of the hotspots in coagulation treatment research. The main goals of scholars are to reduce the toxicity of traditional oxidation and improve the efficiency of coagulation removal. Potassium permanganate preoxidation as a simple enhanced coagulation method that has been successfully applied in countries around the world.54–56 There are an increasing number of preoxidant coagulation agents, such as ferrate, ozone, permanganate complex agents, persulfate, Fenton reagent and sodium hypochlorite.57–60
3.1 Technical principle
Although the mechanism of preoxidation for improving coagulation is different for different oxidants, the progress of preoxidation is usually aimed at changing the zeta potential by destroying the organic coating on the surface of the particles, which results in colloids and suspended particle aggregates, as shown in Fig. 2.61 For highly toxic and difficult-to-degrade wastewater, the combination of one or more oxidation methods is also an approach,62–64 and this is described in detail below.
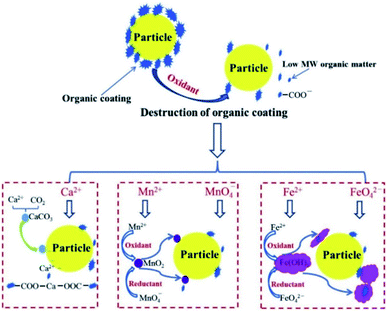 |
| Fig. 2 Mechanisms of peroxidation to enhance coagulation.61 | |
3.2 Chlorine and chlorine dioxide
Chlorine is a disinfectant. Chlorine oxidation of slightly contaminated water can effectively remove the color and taste of water. Chlorination has little use for enhancing coagulation, but chlorine pre-oxidation can effectively enhance coagulation and improve the removal of algae cells.65,66 Chlorine dioxide for potable water application, chlorine dioxide is commonly generated from sodium chlorite reacting with gaseous chlorine, hypochlorous acid, or hydrochloric acid. Chlorine dioxide pretreatment, like chlorine, has a positive effect on algae removal.67 Lin68 found that ClO2 dosing had a strongest ability to lower algae viability and oxidize ionic and complexed soluble Mn. Shi69 found that the optimal dose of 0.5 mg L−1 of Cl2 could prevent the outbreak of Pseudomonas aeruginosa. The pre-oxidation of ClO2 will destroy the cell walls of algae, leading to severe degradation of membrane glycoproteins or certain amino acids;70 the reduction of cell integrity by ClO2 pre-oxidation significantly improves the removal of algae by the coagulation precipitation method. However, the pre-oxidation of chlorine dioxide only has a limited effect when treating surface water that contains little or no algae. Alam71 used 0.6 and 1.0 mg L−1 of chlorine dioxide for pre-oxidation in the drinking water process and found no significant improvement in drinking water quality. In addition, NaOCl possesses the ability to penetrate the cell membrane of Microcystis aeruginosa causing the release of intracellular organic matter (IOM) and potassium ions (K+) from the cells, thereby destroying cell chemosphere and enhancing the removal of the algae by coagulation–sedimentation.65
3.3 Ozone
Ozone is a powerful disinfectant and oxidant, and it has been used in water treatment facilities in Europe since 1906.72 The main uses of ozone are to disinfect, decolorize, inactivate algae and reduce inorganic substances.73 Advantages of ozone in water treatment include the following:74 (a) ozone kills chlorine-resistant viruses and spores; (b) it is scarcely affected by sewage pH and temperature; (c) it removes color, odor, and phenols from sewage, increases the dissolved oxygen content and improves water quality; (d) it can improve the biodegradability of pollutants; and (e) it is difficult to degrade and will not cause secondary pollution due to residues. Therefore, it has been widely studied and applied. Studies have shown that moderate amounts of ozone (low doses) enhance coagulation.75 Several explanations have been proposed:10,76–79 (1) ozone oxidation can increase the concentration of oxygenated functional groups on solid surfaces (such as carboxylic acids), leading to complexation with cations (such as Ca2+, Mg2+, Al3+, etc.) and formation of metal humic acid complex precipitates; (2) ozone can convert high-molecular-weight chemicals into low-molecular-weight chemicals, reducing space and electrostatic repulsion, and ozonation reduces the stabilization of organics that cover the surface of particles, which results in their desorption; (3) ozonation polymerizes metastable organics, which results in particle aggregation through bridging reactions; (4) ozonation changes the surface chemistry of organics and increases coagulation via charge neutralization; and (5) ozone oxidation ruptures organometallic complexes, resulting in the in situ production of coagulants.
Ozone peroxidation has been widely applied to enhance coagulation75 and is often used to treat NOM, algae, heavy metal ions, humus and dye wastewater.77,80,81 NOM is adsorbed on the surface of minerals. Studies have shown that ozone can induce the accumulation of NOM. However, due to the composition of NOM and the complexity of the ozone chemical reaction, it is difficult to develop accurate models. A large number of studies have shown that preozonation has a more significant effect on the coagulation of particles in water of medium hardness than on the coagulation of particles in soft water.77,79 Chandrakanth78 studied the mechanism of ozone removal of NOM, and the results show that ozone can cause particle instability only in the presence of calcium. A theory based on electrostatic (complexation/charge neutralization) and calcium oxalate precipitation was proposed: (a) the components of ozonated NOM can complex with calcium, and (b) the ozonation of NOM increases the number of coordination sites on the surface and the complexation of NOM with calcium is relatively easy. Many studies have shown the biggest influencing factors that affect the efficiency of ozonation coagulation: the characteristics of the raw water (hardness, pH, alkalinity, and type and concentration of NOM), and ozone dose and coagulation conditions (dose and type of coagulant).9,82,83 Francisco's79 research showed that the effect of the efficiency of preozonation-enhanced coagulation seems to vary depending on the characteristics of the raw water, especially the calcium hardness and NOM fractionation. The ozone dose was 0.25–2.5 mg L−1, and the THMFP removal rate was 5–25%. Smith9 developed a study of preozonation-enhanced electroflocculation for the treatment of municipal wastewater. The results showed that the technology could effectively reduce the total phosphorus and TSS from water sources, such as highly toxic textile wastewater and landfill leachate. Preozonation can be used in combination with other oxidation methods (Fenton, permanganate, etc.).64 The application of preozonation to enhance coagulation is very wide. Table 2 describes the application of ozonation in natural water and sewage treatment and the corresponding results.
Table 2 Application of pre-ozone oxidation to treat water
Raw water |
Coagulant |
Dose (mg L−1) |
Observation |
Reference |
Disperse dye-bath |
FeSO4 |
2300 |
Eliminated 95% color and 48% COD |
98 |
Saline landfill leachates |
Fe2(SO4)3 |
49 |
Leachate treatment led to 100% removal of leachate color and 78% removal of COD |
99 |
Textile wastewater |
Al2(SO4)3, FeSO4 |
53.7–82.3 |
Almost complete color absorbance (over 98%) was removed in 20 min ozone contact time |
80 |
Taihu Lake |
Alum |
0.45 |
THMFP removal by approximately 60% |
100 |
Oilfield-produced water |
PAC, PAM |
5 |
PAC and PAM could be saved by approximately 10 mg L−1 and 5 mg L−1 |
101 |
Waterworks |
PAC |
0.5 |
Improve THMFP coagulation removal by 14% |
73 |
Municipal wastewater |
PACl |
0.8 |
DON, DOC, and UV254 removal of 71%, 66%, and 97% |
10 |
Chodatella sp. |
Alum |
0–2.1 |
Increasing algae removal by approximately 50% |
88 |
Oscillatoria agardii |
Al2(SO4)3 |
0–2 |
Increasing algae removal by 8% |
102 |
Green algae mixture |
FeCl3 |
1 |
Increasing algae removal by approximately 20% |
103 |
In most cases, only low amounts of ozone can improve the coagulation effect and high doses of ozone may increase the turbidity of the final water. The optimal dose of ozone is always closely related to the charge density of the humus. The higher the charge density of humus is, the higher the required dose of ozonation.84 Therefore, for some raw water, ozone can always find its optimal dose to enhance coagulation.
3.4 Permanganate
Permanganate shows high reactivity in oxidizing a wide variety of organic substances and inorganic substances. The main uses of permanganate are to control odor and taste, remove iron, manganese, and algae and act as a disinfectant.62,85,86 The principle of permanganate preoxidation to enhance coagulation is as follows. Permanganate is oxidized to produce manganese dioxide. Manganese dioxide is a strong adsorbent. It can increase the flocculation kinetics by increasing the particle concentration. It can also be adsorbed on the surface of other particles to enhance flocculation.87–89 Permanganate preoxidation can effectively remove heavy metals and organics in water.87,90,91
Over the past three decades, permanganate preoxidation-enhanced coagulation has attracted increasing attention, especially in the field of surface water treatment.92–94 Cyanobacteria in surface water treatment can produce metabolites or toxins that are difficult to remove by conventional water treatment processes. Therefore, preoxidation technologies are widely used, such as chlorine, ozone, chlorine dioxide, and permanganate. To control indicators, such as water taste, odor and toxin content,95 and because chlorine gas and chlorine dioxide can produce disinfection byproducts (DBP), permanganate preoxidation technology is widely used. Ma96 reported that permanganate can significantly enhance the coagulation of several surface waters. Studies show that the enhanced coagulation of permanganate is the formation of the strong adsorbent manganese dioxide, which adsorbs onto particle surfaces. Colthurst97 found that manganese dioxide adsorbs humus only when Ca2+ is present, which may be due to the negative charge of both. Chen87 studied the mechanism of permanganate preoxidation to enhance coagulation. With increasing calcium ion concentration, the sedimentation speed was significantly accelerated, and calcium ions promoted permanganate function by electrically neutralizing surface bridging. In addition to permanganate incorporation of algae flocs to increase sedimentation speed, the use of permanganate may also induce algal cells to release organic matter.104 As shown in Fig. 3, SEM observations showed that EOM may enhance the combination of algae flocs and manganese dioxide. Studies have found that the flocculation efficiency of severely damaged algal cells is very low.105 Takaara106 reported that materials with too high of a molecular weight will adhere to the coagulant, causing its failure, which may also reduce the coagulation efficiency. In addition, permanganate is used at a common dose (0–2 mg L−1); thus, there is little or no damage to algae. Wang94 studied the damage of the dose of permanganate to algal cells and observed the cell morphology at different potassium permanganate concentrations using stereoscopic scanning camera technology. The potassium permanganate concentrations were 1 mg L−1, 2 mg L−1 and 6 mg L−1. As shown in Fig. 4, an appropriate concentration of potassium permanganate (for example, 2 mg L−1) promoted EOM secretion by cells. Chen87 showed that EOM may improve the combination of algae flocs and manganese dioxide and achieve the purpose of enhanced coagulation. Many studies have also proven that the commonly used dose of high-acid salt oxidation (0–2 mg L−1) does little or no damage to algae.60,107–109 Excessive manganese will affect the quality of the effluent water. Usually, excess manganese dioxide is removed through a precipitation tank during the water treatment process, although it increases the burden on the filter and shortens the backwash cycle. The characteristics of the raw water need to be studied to ensure the complete conversion of the peracid salt into manganese dioxide. The disadvantages of permanganate preoxidation are overcome to enhance coagulation to the greatest extent.
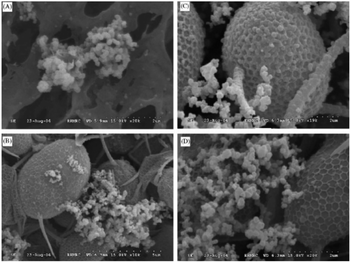 |
| Fig. 3 SEM micrographs of algal cell surface morphology with and without preoxidation. (A) Preformed MnO2, (B) preformed MnO2 adsorbed onto algal cell surface, (C) KMnO4 preoxidized algae cell, and (D) EOM elimination due to trypsin dosing after KMnO4 preoxidation.87 | |
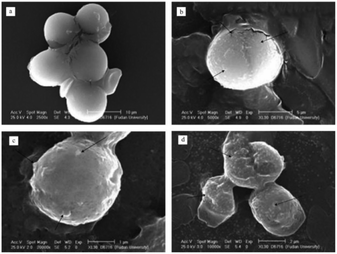 |
| Fig. 4 Stereoscan photograph of algal cell influenced by different concentrations of KMnO4. (a) Protococcus; (b) KMnO4 1 mg L−1; (c) KMnO4 2 mg L−1; and (d) KMnO4 6 mg L−1.94 | |
3.5 Ferrate
Ferrate is a chemical reagent (coagulant and oxidant) with dual functions in drinking water treatment and has great potential in the treatment of water and wastewater.110 It has a strong redox potential across the entire pH range, from 2.2 V in acidic conditions to 0.7 V in alkaline conditions.110,111 During the reduction of ferrate, with the precipitation of ferric hydroxide, hydrolyzed substances with a high positive charge may be produced. These hydrolysates will lead to colloids, cause the particles to be electrically neutralized, and adsorb water molecules and fine particles, thus increasing the sedimentation speed of the coagulation.110,112,113 Ferrate can destabilize colloidal particles in one minute, while ferrous and iron salts need 30 min to achieve stable results.110 Ferrate is an emerging multifunctional oxidant, disinfectant and coagulant. Ferrate does not produce any mutagenic byproducts in water treatment. It is an ideal water and wastewater treatment material in the 21st century.111,114–116
Research has shown that ferrate can effectively remove many organic and inorganic pollutants, such as nitrogenous organics, drugs, antibiotics, hydrogen sulfide, algae, persistent organics, etc.112,113,117–123 Ferrate can also remove various metals, such as Fe2+, Fe3+, Mn2+, Cu2+, Pb2+, Cd2+, Cr3+, Hg2+, etc.117,124 Jiang evaluated the application and preparation of ferrate, and the results showed that ferrate was superior to iron sulfate under low-dose conditions when treating colored water. Ferrate can effectively reduce the UV250 and turbidity of water. Dissolved organic carbon can also reduce the formation of trihalomethane (THMFP).119,125,126 In terms of wastewater treatment,120 compared with the same doses of AS and FS, potassium ferrate showed a 50% increase in color removal rate and a 30% increase in COD, resulting in less sludge. Ma112,113 used ferrate preoxidation to improve coagulation and treat algae-containing water and surface water. Studies have found that ferrate preoxidation can enhance the removal and turbidity of algal cells at various oxidant doses. In terms of synthetic preparation, Stanford and Jiang127 electrochemically synthesized potassium ferrate and showed that 1 mg L−1 potassium ferrate and 10 mg L−1 iron salt had the same treatment effect. Alsheyab and Jiang designed an electrochemical method for a Chinese factory. The reactor proved the operation concept and online application of the electrochemical generation of potassium ferrate, which is a step forward for the comprehensive application of potassium ferrate in water and wastewater. The decomposition rate of ferrate depends on the pH value, solution temperature, initial potassium ferrate concentration and coexisting ions. Before using ferrate, the characteristics and quality of raw water need to be analyzed.110,128
4. Other enhanced coagulation methods
4.1 Ultrasound-enhanced coagulation
In recent years, ultrasound has proven to be an effective water treatment technology.129,130 Ultrasound irradiation produces cavitation, thereby causing reactive free radicals and shock waves.131,132 Studies have shown that ultrasound combined with other technologies has better results than ultrasound alone.133–135 Ultrasound-enhanced coagulation is one of the current research hotspots, and the working principle is as follows:136 (1) low-frequency (20–150 kHz) ultrasonic irradiation will increase molecular vibrations, improve the ion collision efficiency and make the flocs more compact and easy to precipitate; and (2) ultrasound irradiation can change the morphology and surface characteristics of ions, cause particle surface damage, significantly increase specific surface area, and increase particle aggregation. A large number of studies have shown that ultrasonic treatment can significantly increase the flocculating capacity of algae in the treatment of algae-containing water, reduce the amount of coagulant added, and reduce costs.137
In algae-containing water, it is difficult to remove algal cells due to their special characteristics (negative surface potential), and algae metabolites tend to adsorb to colloidal particles. Zhang133 reported the removal of algal cells from the water source in a water treatment plant by ultrasound-enhanced coagulation. Studies have shown that ultrasound irradiation applied for 5 seconds can increase the desiccation efficiency by 20%. Zhang134 reported that the main theory involved the destruction during ultrasonic irradiation of gas vacuoles inside algal cells that acted as “nuclei” for acoustic cavitation and collapsed during the “bubble crushing” period, causing the settlement of cyanobacteria, whereas the ultrasound frequency had little impact on the removal effect. However, studies have shown that increasing ultrasound duration and power can negatively affect coagulation,138 such as by causing microcystin release.137 Therefore, the parameters of ultrasound-enhanced coagulation are very important, as shown in Table 3. Li139 reported the effects of ultrasonic power, action time, coagulant dose and pH value on the removal of organic matter in low-temperature and low-turbidity water. The results showed that the optimal ultrasound power was 25 W, the optimal ultrasound treatment time was 9 min, the optimal PFS dose was 12 mg L−1, the optimal pH was 7, and the COD removal rate was 87.2%. Fast140 reported the effects of several different process parameters, such as chemical dose, ultrasonic time, pH value, concentration factor, and flocculation time, on algae removal. A comparison between ultrasound-alum and ultrasound-chitosan flocculation of turbid algal waters as well as a comparison with conventional rapid mix and direct flocculation were conducted. Three processes were designed on the basis of single-factor experiments. The results showed that the removal rate of the ultrasonic-chitosan-enhanced coagulation process could reach more than 98%.
Table 3 Application of ultrasound-enhanced coagulation
Raw water |
Coagulant |
Ultrasonic irradiation |
Ultrasonic power |
Observation |
Reference |
Algae-containing water |
Chitosan |
<60 s |
100 W |
Higher removal efficiencies (>97%) |
140 |
Luan River |
FeCl3 |
15 s |
60 W |
Improve algae coagulation removal by 12.4% |
137 |
Low-temperature and low-turbidity water |
PFS |
9 min |
25 W |
COD removal rate will reach 87.2% |
139 |
Algae-containing water |
PAC |
5 min |
0.02 W mL−1 |
Turbidity removal rate of approximately 80% to 90% |
141 |
Algae-containing water |
PACl |
30 s |
<100 W |
Dosage of PACl was reduced, and the sedimentation rate of flocs was increased |
136 |
Algae-containing water |
PAC |
1–5 s |
48 W |
Pre-sonication reduced the coagulant dose by two-thirds |
133 |
Algae-containing water |
PAC |
5 s |
47.2 W cm−2 |
Increased algae removal efficiency from 35% to 67% |
134 |
The ultrasonic enhanced coagulation process has attracted much attention in the treatment of algae-containing water, although the current research is still very unsystematic, and it is often limited to static ultrasonic experiments at a single frequency. It lacks multi-frequency, multi-intensity and multi-time comparisons. The actual application is still far away. In the future, it is necessary to further strengthen the research on the influence of the interaction of various parameters, clarify the mechanism of ultrasound enhancement, and lay the foundation for future applications.
4.2 Composite coagulants
4.2.1 Inorganic polymer flocculants. Aluminum salts and iron salts have been widely used as inorganic flocculants in water and wastewater treatment. The main products are aluminum sulfate, ferrous sulfate, iron sulfate, polyaluminum chloride (PAC) and PFS. The hydrolyzed polymerization products of these products have a positive charge, and through the adsorption and neutralization sweeping effect, they condense with the negatively charged colloidal pollutants in the water, although their ability to adsorb and bridge the colloidal pollutants in the water is weak. A higher dose is required to achieve a good flocculation effect.2,142 To further improve the flocculation effect of inorganic flocculants and reduce the amount of products, a large amount of research and application practice found that iron salt and aluminum salt are copolymerized under certain conditions or an inorganic component with flocculation or coagulation aid is added to the iron salt, aluminum salt or iron salt/aluminum salt solution and reacted. Through synergistic effects, inorganic–inorganic composite flocculant products produce better flocculation effects.143–145 Because the composite flocculant can overcome many of the shortcomings of using a single flocculant, it can improve the flocculation performance while reducing the cost of water treatment. Therefore, the development and application of composite flocculants has become one of the issues of interest in the current water and wastewater treatment field, and it is also the main development direction of new, efficient and economical flocculants. An early composite flocculant was polyaluminum plus polyacrylamide146 and then polyaluminum plus activated silicic acid was used147,148 in an attempt to combine an original coagulant and a new coagulant into one dose. With a more in-depth understanding of the principle of flocculants, it was gradually realized that the combination of flocculants is based on the principle of strengthening complementarity, combining flocculants with different flocculating properties, and improving the performance of a single coagulant. At present, there are two main types of composite coagulants: inorganic composite types and inorganic–organic composite types. For example, in polyaluminum chloride composite flocculants,145 the active component is still aluminum hydrolysis and polymerization to form high-valent hydroxyl polymer ions. By adding an organic flocculant, the inorganic flocculant enhances its ability to adsorb to particles and bridge and neutralize electrical charges, thereby improving its coagulation ability. Inorganic polymer composite flocculants are mainly prepared by adding inorganic salt compounds,143,145 such as Al3+, Fe3+, Ca2+, SO42−, Cl−, etc. According to the type of metal ions that the composite flocculant is associated with in flocculation, the inorganic polymer composite flocculant can be divided into the polyaluminum salt type, polyiron salt type and polyaluminum iron salt type.144,149–151 One or several kinds of them are added to form inorganic composite polymer flocculants, fully optimizing their respective advantages and achieving the purpose of efficient purification treatment. At present, a variety of inorganic–inorganic and inorganic–organic composite flocculant products have been developed, mainly including polyaluminum chloride sulfate (PACS), polyaluminum ferric chloride (PAFC), polyaluminum silicate sulfate (PASiS), polyaluminum silicate chloride (PASiC), polyferric silicate sulfate (PFSiS), polyaluminum ferric silicate chloride (PAFSiC), PAC/PDM composite coagulants and PAC/PDMDAAC composite coagulants.143,144,149,152–155 In recent years, many researchers156–158 have also enhanced coagulation by improving the performance of coagulant aids. Table 4 summarizes the application of composite flocculants in water treatment.
Table 4 Application of composite flocculants in water treatment
Raw water |
Coagulation |
Materials |
Dose (mg L−1) |
Observation |
Reference |
Kaolinite suspensions |
P(DADMAC-AM-VTMS) |
DADMAC + AM + VTMS |
0.1 |
<5 NTU (turbidity) |
159 |
Kaolinite suspensions |
PAFC |
Coal gangue + HCl + CaCO3 |
0.05 |
<5 NTU (turbidity) |
149 |
Kaolinite suspensions |
PACS |
Na2CO3 + AlCl3 + Al2(SO4)3 |
2 |
<4 NTU (turbidity) |
143 |
Synthetic suspensions |
PASiC |
SiO2 + AlCl3 + NaOH |
3 |
<1 NTU (turbidity) |
144 |
Oil field wastewater |
PAC–PDMDAAC |
PDMDAAC + PAC |
8 |
<100 (COD) |
155 |
Landfill leachate |
PFSiS |
PFSiSc + Fe2(SO4)3 |
50 |
>90% (turbidity removal) |
150 |
Lake Taihu waters |
PAC–PDM |
PAC + PDM |
8.32 |
0.41 NUT (turbidity) |
153 |
Oily wastewater |
PFASS |
Fly ash |
140 |
>95% (turbidity removal) |
151 |
Kaolinite suspensions |
CMC-g-PAM |
CMC + CAN + PAM |
15 |
>80% (turbidity removal) |
160 |
Synthetic suspensions |
PTSS |
PTS + PSiA |
35 |
70% (UV254 removal) |
161 |
Taihu Lake |
PAC–PDMDAAC |
PAC + PDMDAAC |
10 |
<1.5 NTU (turbidity) |
154 |
Cd(II) solution |
APAM |
PAM |
2.87 |
93.65% (Cd(II) removal) |
146 |
Synthetic textile wastewater |
PAFC-starch-g-p(AM-DMDAAC) |
PAFC + starch + AM + DMDAAC |
0.2 |
>85% (dye removal) |
162 |
The research on composite flocculants has developed rapidly in recent years. Based on the research results of its performance and flocculation mechanism, a series of new and efficient inorganic–inorganic and inorganic–organic composite polymer flocculants have been developed. It is used in water and wastewater treatment and sludge dewatering, although the research, development and application of composite high-resolution flocculants are still in their infancy. At present, the research and development of composite flocculants is mainly focused on the development of new, efficient, nontoxic or low-toxicity composite flocculants. This work should be strengthened in the following ways.
(1) Further strengthen research on compound polymer flocculant ratio screening, preparation process technology, process parameters and supporting equipment to improve the flocculation effect and reduce the cost.
(2) Carry out in-depth and systematic research on the interaction between the components of the composite flocculant and strengthen the synergy between the component, thereby laying a theoretical foundation for the development of new flocculants.
(3) Carry out in-depth and systematic research on the performance of composite flocculants, the dynamic process of flocculation, and the physical characteristics of the formed flocs. The results of the research are helpful for clarifying the flocculation behavior and mechanism of composite polymer flocculants.
(4) Systematic research is performed on the application conditions and influencing factors of composite flocculants to clarify the applicable objects and lay the foundation for the promotion of new products.
4.2.2 Biopolymer flocculants. Natural polysaccharides derived from biomass feedstocks, marine resources, and microorganisms have been attracting considerable attention as benign and environmentally friendly substitutes for synthetic polymeric products. There are many types of biopolymer flocculants, such as lignin, cellulose, chitosan, xanthan gum, pectin, polysaccharides and proteins, etc.163,164 Among them, cellulose and chitosan are currently the most abundant biopolymers on Earth.165 Biopolymer flocculants are derived from oceans, plants, and microorganisms. For example, chitosan mostly comes from seaweeds, crustacean shells and microorganisms, and cellulose, starch, etc. come from agricultural raw materials. Microorganisms, such as bacteria, yeast and algae, are important sources of biopolymer flocculants.166 Biopolymers have many advantages because they are environmentally friendly, highly biochemical, nontoxic, etc. and can be used in agricultural wastewater,167 oily wastewater,168 heavy metal wastewater,169 algal water, etc.170,171 This research field has received extensive attention. Turunen167 used tannin and chitosan to treat agricultural wastewater. The tannin and chitosan coagulant performed best at a dose of 5–10 mL L−1, with a turbidity removal rate of 80–98%. Henry163 studied the removal of orthophosphate by a variable ternary system of alum, biopolymer and biomass. The removal rate of orthophosphate was 98%. Lichtfouse172 studied the modified chitosan treatment of phosphate solution, and the principle is shown in Fig. 5. This treatment could reduce the phosphate content by 97% under all pH values. Biopolymer flocculants usually exhibit low flocculation activity. Many researchers use chemical modification to improve their flocculation activity. There are two main forms:166 (1) physical reactions, such as ionic interaction, polysaccharide–protein interaction, and (2) chemical reactions, such as graft copolymerization, crosslinking with aldehyde, esterification, etherification, amination, carboxyalkylation, hydroxyalkylation and other addition reactions, and condensation. Peng173 studied a series of amphoteric chitosan-based grafting flocculants (CM-chi)-g-PDMDAAC (denoted as CgPD), which were successfully synthesized by grafting diallyl dimethyl ammonium chloride (DMDAAC) onto carboxymethyl chitosan (CM-chi) with different grafting ratios. By carboxymethyl and grafting modification, dramatically increased water solubility of chitosan was obtained. Many biopolymer flocculants have been synthesized through chemical modification, for example, polysaccharide-g-(PDMA-co-AA),174 AP-g-poly(AM-co-AA),175 PHAP.176 The main challenges faced by biopolymer flocculants are the complex synthesis process, monomer health problems, future production scale and consumption. Future research should focus on reducing production costs and developing large-scale production processes.
 |
| Fig. 5 Bioflocculation mechanism: (a) charge neutralization, (b) bridging, (c) electrostatic patching and (d) sweeping. | |
5. Conclusions
Because of their simple operation, high versatility, low energy consumption and high cost performance, coagulation and flocculation are still essential steps in the field of water treatment. This review summarized the application development of the enhanced coagulation process and outlined the effectiveness of the enhanced coagulation process from the perspective of different enhanced coagulation processes. Ballast reaction nuclei-enhanced coagulation has the potential to treat surface water, wastewater and overflow water from sewers. This method can increase the density of flocs, increase the sedimentation speed of flocs, and improve the fractionation of flocs. Preoxidation and ultrasound are widely used in the treatment of algae-containing waters. Preoxidation enhances coagulation by breaking the organic coating and changing the surface potential of particles. However, the mechanism of oxidative coagulation is completely different for different oxidants and colloids. Ultrasound increases the particle collision efficiency by increasing the molecular vibrations so that the flocs are denser and the sedimentation speed is increased. Composite flocculants were developed based on research on the performance and mechanism of different flocculants, and they represent an optimization and complementation of the action of two or more flocculants. The current research indicates that enhanced coagulation is based on the mechanism and dynamics of traditional coagulation. As long as the coagulation effect is substantially improved, it can be considered enhanced coagulation. In future research, a mathematical model and a stability model for enhanced coagulation should be established, flocculants should be developed, appropriate coagulation nodules should be selected, and different water qualities, preoxidation or ultrasonic methods can be considered to improve raw water flocculation characteristics. Enhanced coagulation is greatly affected by the process parameters. A method for evaluating coagulation and a coagulation process control strategy should be proposed and established to resolve issues at the intersection of coagulation and flocculation stages in the coagulation process during water treatment, as well as coagulation process and coagulant issues such as coordination, mixing conditions, and coagulation process control.
Conflicts of interest
Authors declare no competing interest.
Acknowledgements
This study was supported by the Northeast Petroleum University Youth Science Fund Project (2019QNL-30).
References
- J.-Q. Jiang, Curr. Opin. Chem. Eng., 2015, 8, 36–44 CrossRef.
- C. Y. Teh, P. M. Budiman, K. P. Y. Shak and T. Y. Wu, Ind. Eng. Chem. Res., 2016, 55, 4363–4389 CrossRef CAS.
- J. K. Edzwald, Water Sci. Technol., 1999, 9, 63–70 CrossRef.
- S. Xue, Q. Zhao, L. Wei, X. Ma, Y. Wen and Z. Zhang, Environ. Prog. Sustainable Energy, 2015, 34, 751–760 CrossRef CAS.
- J. Yu, D. Wang, M. Yan, C. Ye, M. Yang and X. Ge, Environ. Monit. Assess., 2007, 131, 377–386 CrossRef CAS PubMed.
- M. Yan, D. Wang, J. Qu, J. Ni and C. W. Chow, Water Res., 2008, 42, 2278–2286 CrossRef CAS PubMed.
- M. Yan, D. Wang, S. You, J. Qu and H. Tang, Water Res., 2006, 40, 3621–3627 CrossRef CAS PubMed.
- S. Ma, C. Liu, K. Yang and D. Lin, Sci. Total Environ., 2012, 439, 123–128 CrossRef CAS PubMed.
- K. Nielson and D. W. Smith, J. Environ. Eng. Sci., 2005, 4, 65–76 CrossRef CAS.
- B. Liu, L. Gu, Q. Li, G. Yu, C. Zhao and H. Zhai, Environ. Technol., 2019, 40, 2684–2694 CrossRef CAS.
- R. D. Ambashta and M. Sillanpaa, J. Hazard. Mater., 2010, 180, 38–49 CrossRef CAS PubMed.
- W. Yu, M. Liu and N. J. D. Graham, ACS Sustainable Chem. Eng., 2019, 7, 18566–18573 CrossRef CAS.
- J. M. Younker and M. E. Walsh, Water Res., 2016, 98, 1–8 CrossRef CAS.
- S. Kadouche, H. Lounici, K. Benaoumeur, N. Drouiche, M. Hadioui and P. Sharrock, J. Polym. Environ., 2012, 20, 848–857 CrossRef CAS.
- S. Boulaadjoul, H. Zemmouri, Z. Bendjama and N. Drouiche, Chemosphere, 2018, 206, 142–149 CrossRef CAS PubMed.
- M. Ma, R. Liu, H. Liu and J. Qu, Water Res., 2012, 46, 73–81 CrossRef CAS PubMed.
- C. Desjardins, B. Koudjonou and R. Desjardins, Water Res., 2002, 30, 744–754 CrossRef.
- M. Zhang, Y. Chen, L. Xie and Q. Zhou, Chemosphere, 2018, 211, 1054–1064 CrossRef CAS PubMed.
- T. J. Wan, S. M. Shen, S. H. Siao, C. F. Huang and C. Y. Cheng, Water Res., 2011, 45, 6301–6307 CrossRef CAS.
- S. Kumar, N. C. Ghosh and A. A. Kazmi, Environ. Technol. Rev., 2016, 5, 57–67 CrossRef CAS.
- M. Lapointe and B. Barbeau, Water Res., 2016, 90, 119–127 CrossRef CAS PubMed.
- K. Miyahara, Y. Adachi, K. Nakaishi and M. Ohtsubo, Colloids Surf., 2002, 196, 87–91 CrossRef CAS.
- J. Sieliechi, B. Lartiges, S. Skali-Lami, J. Kayem and R. Kamga, Water Res., 2016, 105, 361–369 CrossRef CAS PubMed.
- A. J. Manning and D. H. Schoellhamer, Mar. Geol., 2013, 345, 266–280 CrossRef.
- M. Lapointe, C. Brosseau, Y. Comeau and B. Barbeau, J. Environ. Eng., 2017, 143(11), 04017071 CrossRef.
- A. Cuthbertson, P. Dong, S. King and P. Davies, Coastal Engineering, 2008, 55, 1197–1208 CrossRef.
- V. Plum, C. P. Dahl, L. Bentsen, C. R. Petersen, L. Napstjert and N. B. Thomsen, Water Sci. Technol., 1998, 37, 269–275 CrossRef CAS.
- J. E. Van Benschoten and J. K. Edzwald, Water Res., 1990, 24, 1527–1535 CrossRef CAS.
- J. C. Young and F. G. Edwards, Water Environ. Res., 2003, 75, 263–272 CrossRef CAS PubMed.
- W. Yu, J. Gregory, L. C. Campos and N. Graham, Water Res., 2015, 68, 119–126 CrossRef CAS PubMed.
- W. Zhu, R. Seth and J. Lalman, Environ. Technol., 2007, 28, 761–770 CrossRef CAS PubMed.
- K. V. Gorin, Y. E. Sergeeva, V. V. Butylin, A. V. Komova, V. M. Pojidaev, G. U. Badranova, A. A. Shapovalova, I. A. Konova and P. M. Gotovtsev, Bioresour. Technol., 2015, 193, 178–184 CrossRef CAS.
- J. T. Mayo, C. Yavuz, S. Yean, L. Cong, H. Shipley, W. Yu, J. Falkner, A. Kan, M. Tomson and V. L. Colvin, Sci. Technol. Adv. Mater., 2007, 8, 71–75 CrossRef CAS.
- L. Piirtola, B. Hultman, C. Andersson and Y. Lundeberg, Water Res., 1999, 33, 1799–1804 CrossRef CAS.
- M. Kumari and S. K. Gupta, J. Cleaner Prod., 2020, 244, 118899 CrossRef CAS.
- A. D. Ebner, J. A. Ritter, H. J. Ploehn, R. L. Kochen and J. D. Navratil, Sep. Sci. Technol., 1999, 34, 1277–1300 CrossRef CAS.
- J. B. J. Janssen, A. P. Gelder and J. Perenboom, J. Phys. D: Appl. Phys., 1990, 23, 1447 CrossRef CAS.
- Y. Li, J. Wang, Y. Zhao and Z. Luan, Sep. Purif. Technol., 2010, 73, 264–270 CrossRef CAS.
- M. Omran, T. Fabritius, A. M. Elmahdy, N. A. Abdel-Khalek, M. El-Aref and A. E.-H. Elmanawi, Sep. Purif. Technol., 2014, 136, 223–232 CrossRef CAS.
- J. Svoboda and T. Fujita, Miner. Eng., 2003, 16, 785–792 CrossRef CAS.
- Y. Wang, E. Forssberg, R. J. Pugh and S. Åke Elming, J. Dispersion Sci. Technol., 1995, 16, 137–154 CrossRef CAS.
- N. Karapinar, Int. J. Miner. Process., 2003, 71, 45–54 CrossRef CAS.
- C. T. Yavuz, A. Prakash, J. T. Mayo and V. L. Colvin, Chem. Eng. Sci., 2009, 64, 2510–2521 CrossRef CAS.
- T. Miettinen, J. Ralston and D. Fornasiero, Miner. Eng., 2010, 23, 420–437 CrossRef CAS.
- R. Sivamohan, Int. J. Miner. Process., 1990, 28, 247–288 CrossRef CAS.
- K. Mandel, F. Hutter, C. Gellermann and G. Sextl, Sep. Purif. Technol., 2013, 109, 144–147 CrossRef CAS.
- C. Shuang, P. Li, A. Li, Q. Zhou, M. Zhang and Y. Zhou, Water Res., 2012, 46, 4417–4426 CrossRef CAS.
- S.-K. Wang, A. R. Stiles, C. Guo and C.-Z. Liu, Algal Res., 2015, 9, 178–185 CrossRef.
- Y. R. Hu, C. Guo, L. Xu, F. Wang, S. K. Wang, Z. Hu and C. Z. Liu, Bioresour. Technol., 2014, 158, 388–391 CrossRef CAS PubMed.
- P. Y. Toh, B. W. Ng, C. H. Chong, A. L. Ahmad, J.-W. Yang, C. J. Chieh Derek and J. Lim, RSC Adv., 2014, 4, 4114–4121 RSC.
- L. Luo and A. V. Nguyen, Sep. Purif. Technol., 2017, 172, 85–99 CrossRef CAS.
- M. Stolarski, C. Eichholz, B. Fuchs and H. Nirschl, China Particuol., 2007, 5, 145–150 CrossRef CAS.
- E. Carissimi, J. D. Miller and J. Rubio, Int. J. Miner. Process., 2007, 85, 41–49 CrossRef CAS.
- H. T. Kemp, R. G. Fuller and R. S. Davidson, J. AWWA, 1966, 58, 255–263 CrossRef CAS.
- J. C. Zhou, H. C. Zhao, K. H. Pan and Q. P. Xu, J. Zhejiang Univ., Sci., B, 2011, 12, 156–162 CrossRef.
- J. Gasperi, B. Laborie and V. Rocher, Chem. Eng. J., 2012, 211–212, 293–301 CrossRef CAS.
- X.-J. Ma and H.-L. Xia, J. Hazard. Mater., 2009, 162, 386–390 CrossRef CAS PubMed.
- S. Barredo-Damas, M. I. Iborra-Clar, A. Bes-Pia, M. I. Alcaina-Miranda, J. A. Mendoza-Roca and A. Iborra-Clar, Desalination, 2005, 182, 267–274 CrossRef CAS.
- J. Zhou, J. Liu, Z. Zhao, W. Peng, F. Cui and Z. Liang, Chem. Eng. J., 2020, 382, 123012 CrossRef.
- J. Naceradska, M. Pivokonsky, L. Pivokonska, M. Baresova, R. K. Henderson, A. Zamyadi and V. Janda, Water Res., 2017, 114, 42–49 CrossRef CAS.
- P. Xie, Y. Chen, J. Ma, X. Zhang, J. Zou and Z. Wang, Chemosphere, 2016, 155, 550–563 CrossRef CAS.
- H. Liang, J. Y. Tian, W. J. He, H. D. Han, Z. L. Chen and G. B. Li, J. Chem. Technol. Biotechnol., 2009, 84, 1229–1233 CrossRef CAS.
- F. Wu, X. Li, Z. Tan, B. Xue, Y. Wang and X. Yan, Research on cellar rainwater of northwest region villages and small towns enhanced coagulation by potassium permanganate combined with powdered activated carbon, 2012 International Symposium on Geomatics for Integrated Water Resource Management, Lanzhou, 2012, Lanzhou, pp. 1–5 Search PubMed.
- S. Meric, H. Selcuk and V. Belgiorno, Water Res., 2005, 39, 1147–1153 CrossRef CAS PubMed.
- M. Ma, R. Liu, H. Liu, J. Qu and W. Jefferson, Sep. Purif. Technol., 2012, 86, 19–25 CrossRef CAS.
- D. L. Sedlak and U. von Gunten, Science, 2011, 331, 42–43 CrossRef CAS.
- D. Yan, Z. Sun, J. Wang, L. Wang, R. Pan, Q. Wu and X. Liu, Water, 2019, 11, 2302 CrossRef CAS.
- J. L. Lin, L. C. Hua, Y. Wu and C. Huang, Water Res., 2016, 89, 261–269 CrossRef CAS.
- X. Shi, R. Bi, B. Yuan, X. Liao, Z. Zhou, F. Li and W. Sun, Sci. Total Environ., 2019, 656, 1063–1070 CrossRef CAS.
- S. Zhou, Y. Shao, N. Gao, L. Li, J. Deng, M. Zhu and S. Zhu, Sci. Total Environ., 2014, 482–483, 208–213 CrossRef CAS.
- M. Z. B. Alam, R. E. Cantwell, R. Hofmann, R. C. Andrews, J. L. Rand, G. A. Gagnon, M. VanderMarck, E. Moffat and S. A. Andrews, J. Environ. Eng., 2008, 134, 478–485 CrossRef CAS.
- S. D. Chang and P. C. Singer, J. - Am. Water Works Assoc., 1991, 83, 71–79 CrossRef CAS.
- Q. F. Liu, X. T. Zhou, Z. D. Li and Z. G. Zhan, Adv. Mater. Res., 2012, 487, 74–80 CAS.
- M. G. Nagarkatti, J. Environ. Qual., 1991, 20, 881 CrossRef.
- V. Camel and A. Bermond, Water Res., 1998, 32, 3208–3222 CrossRef CAS.
- F. Tumpa, J. Liang, L. Perez Estrada, M. Gamal El-Din and Y. Liu, J. Environ. Manage., 2014, 146, 535–542 CrossRef PubMed.
- M. F. Rahman, S. Y. Jasim, E. K. Yanful, S. Ndiongue and D. Borikar, Ozone: Sci. Eng., 2010, 32, 295–304 CrossRef CAS.
- M. S. Chandrakanth and G. L. Amy, Environ. Sci. Technol., 1996, 30, 431–443 CrossRef CAS.
- F. J. Rodríguez, L. A. Marcos, L. A. Núñez and M. García, Ozone: Sci. Eng., 2012, 34, 342–353 CrossRef.
- H. Selcuk, Dyes Pigm., 2005, 64, 217–222 CrossRef CAS.
- L. Szpyrkowicz, C. Juzzolino and S. N. Kaul, Water Res., 2001, 35, 2129–2136 CrossRef CAS.
- M. Edwards and M. M. Benjamin, J. - Am. Water Works Assoc., 1992, 84, 63–72 CrossRef CAS.
- M. R. Jekel, Ozone: Sci. Eng., 1994, 16, 55–66 CrossRef CAS.
- M. R. Farvardin and A. G. Collins, Water Res., 1989, 23, 307–316 CrossRef CAS.
- M. S. Hobbs, R. S. Grippo, J. L. Farris, B. R. Griffin and L. L. Harding, Environ. Toxicol. Chem., 2006, 25, 3046–3052 CrossRef CAS PubMed.
- K. J. Ficek, Opflow, 1984, 10, 1–7 CrossRef.
- J. J. Chen and H. H. Yeh, Water Res., 2005, 39, 4420–4428 CrossRef CAS PubMed.
- J. J. Chen, H. H. Yeh and I. C. Tseng, Chemosphere, 2009, 74, 840–846 CrossRef CAS PubMed.
- J. Guo, J. Ma and X. Shi, Front. Environ. Sci. Eng. China, 2007, 1, 251–256 CrossRef.
- X. Lu, X. Huangfu, X. Zhang, Y. Wang and J. Ma, Water Res., 2014, 65, 22–31 CrossRef CAS PubMed.
- X. Lu, X. Huangfu and J. Ma, J. Hazard. Mater., 2014, 280, 71–78 CrossRef CAS PubMed.
- Y. L. Song, B. Z. Dong, N. Y. Gao, Y. F. Yang and C. Chang, Appl. Mech. Mater., 2012, 170–173, 2360–2366 CAS.
- J. Ma and G. Li, Water Sci. Technol., 1993, 27, 47–54 CrossRef CAS.
- L. Wang, J. Qiao, Y. Hu, L. Wang, L. Zhang, Q. Zhou and N. Gao, J. Environ. Sci., 2013, 25, 452–459 CrossRef CAS.
- J. L. Lin, L. C. Hua, S. K. Hung and C. Huang, J. Environ. Sci., 2018, 63, 147–155 CrossRef PubMed.
- N. Graham, J. Ma and G. Li, Aqua, 1997, 46, 1–10 Search PubMed.
- J. M. Colthurst and P. C. Singer, J. - Am. Water Works Assoc., 1982, 74, 78–83 CrossRef CAS.
- I. Arslan, J. Hazard. Mater., 2001, B85, 229–241 CrossRef.
- I. Monje-Ramirez and M. T. Orta de Velasquez, Water Res., 2004, 38, 2358–2366 CrossRef CAS PubMed.
- P. C. Chiang, E. E. Chang, P. C. Chang and C. P. Huang, Sci. Total Environ., 2009, 407, 5735–5742 CrossRef CAS.
- L. Cheng, X. Bi and Y. Ni, Presented in part at the 2011 International Conference on Computer Distributed Control and Intelligent, Environmental Monitoring, 2011 Search PubMed.
- J. Ma, J. Y. Fang, L. N. Wang, J. Guo and Z. L. Chen, Water Sci. Technol.: Water Supply, 2006, 6, 145–152 CAS.
- A. Montiel and B. Welte, Water Sci. Technol., 1998, 37, 65–73 CrossRef CAS.
- T. Gayathri, S. Kavitha, S. Adish Kumar, S. Kaliappan, I. T. Yeom and J. Rajesh Banu, Ultrason. Sonochem., 2015, 22, 333–340 CrossRef CAS PubMed.
- M. Drikas, C. W. K. Chow, J. House and M. D. Burch, J. - Am. Water Works Assoc., 2001, 93, 100–111 CrossRef.
- T. Takaara, D. Sano, H. Konno and T. Omura, Water Res., 2007, 41, 1653–1658 CrossRef CAS PubMed.
- F. Qu, X. Du, B. Liu, J. He, N. Ren, G. Li and H. Liang, Chem. Eng. J., 2015, 279, 56–65 CrossRef CAS.
- E. C. Wert, M. M. Dong and F. L. Rosario-Ortiz, Water Res., 2013, 47, 3752–3761 CrossRef CAS PubMed.
- J. Fan, R. Daly, P. Hobson, L. Ho and J. Brookes, Chemosphere, 2013, 92, 529–534 CrossRef CAS.
- J.-Q. Jiang and B. Lloyd, Water Res., 2002, 36, 1397–1408 CrossRef CAS PubMed.
- S. J. DeLuca, A. C. Chao and C. Smallwood, J. Environ. Eng., 1983, 109, 1159–1167 CrossRef CAS.
- W. Liu and J. Ma, Water Res., 2002, 36, 871–878 CrossRef.
- W. Liu and J. Ma, Water Res., 2002, 36, 4959–4962 CrossRef.
- V. K. Sharma, R. Zboril and R. S. Varma, Acc. Chem. Res., 2015, 48, 182–191 CrossRef CAS PubMed.
- V. K. Sharma, Adv. Environ. Res., 2002, 6, 143–156 CrossRef CAS.
- V. K. Sharma, S. K. Mishra and N. Nesnas, Environ. Sci. Technol., 2006, 40, 7222–7227 CrossRef CAS PubMed.
- R. Bartzatt, M. Cano, L. Johnson and D. Nagel, J. Toxicol. Environ. Health, 1992, 35, 205–210 CrossRef CAS.
- V. K. Sharma, J. O. Smith and F. J. Millero, Environ. Sci. Technol., 1997, 31, 2486–2491 CrossRef CAS.
- J.-Q. Jiang and S. Wang, Environ. Eng. Sci., 2004, 20, 627–633 CrossRef.
- J. Q. Jiang, A. Panagoulopoulos, M. Bauer and P. Pearce, J. Environ. Manage., 2006, 79, 215–220 CrossRef CAS PubMed.
- V. K. Sharma, T. M. Triantis, M. G. Antoniou, X. He, M. Pelaez, C. Han, W. Song, K. E. O'Shea, A. A. de la Cruz, T. Kaloudis, A. Hiskia and D. D. Dionysiou, Sep. Purif. Technol., 2012, 91, 3–17 CrossRef CAS.
- K. Manoli, L. M. Morrison, M. W. Sumarah, G. Nakhla, A. K. Ray and V. K. Sharma, Water Res., 2019, 148, 272–280 CrossRef CAS PubMed.
- V. K. Sharma, J. Environ. Sci. Health, Part A: Toxic/Hazard. Subst. Environ. Eng., 2010, 45, 645–667 CrossRef CAS PubMed.
- R. K. R. Robinson, Water Res., 1974, 8, 543–547 CrossRef.
- B. Lloyd, J.-Q. Jiang and L. Grigore, Environ. Eng. Sci., 2004, 18, 323–328 Search PubMed.
- J. Q. Jiang, S. Wang and A. Panagoulopoulos, Chemosphere, 2006, 63, 212–219 CrossRef CAS.
- C. Stanford, J.-Q. Jiang and M. Alsheyab, Water, Air, Soil Pollut., 2009, 209, 483–488 CrossRef.
- M. D. Johnson and K. D. Sharma, Inorg. Chim. Acta, 1999, 293, 229–233 CrossRef CAS.
- D. Chen, Handbook on application of ultrasound: Sonochemistry for sustainability, 2012, p. 373, DOI:10.1201/b11012-16.
- J. H. Gibson, H. Hon, R. Farnood, I. G. Droppo and P. Seto, Water Res., 2009, 43, 2251–2259 CrossRef CAS PubMed.
- M. Furuta, M. Yamaguchi, T. Tsukamoto, B. Yim, C. Stavarache, K. Hasiba and Y. Maeda, Ultrason. Sonochem., 2004, 11, 57–60 CrossRef CAS.
- I. Tsukamoto, E. Constantinoiu, M. Furuta, R. Nishimura and Y. J. Maeda, Ultrason. Sonochem., 2004, 11, 167–172 CrossRef CAS.
- G. Zhang, B. Wang, P. Zhang, L. Wang and H. Wang, J. Environ. Sci. Health, Part A: Toxic/Hazard. Subst. Environ. Eng., 2006, 41, 1379–1390 CrossRef CAS PubMed.
- G. Zhang, P. Zhang and M. Fan, Ultrason. Sonochem., 2009, 16, 334–338 CrossRef CAS.
- R. Lall, R. Mutharasan, Y. T. Shah and P. Dhurjati, Water Environ. Res., 2003, 75, 171–179 CrossRef CAS PubMed.
- H.-X. Shi, J.-H. Qu, H.-J. Liu, Y.-L. Mu, K.-T. Xiao and L. Wang, J. Water Supply: Res. Technol.--AQUA, 2008, 57, 101–108 CrossRef CAS.
- L. Heng, N. Jun, H. Wen-jie and L. Guibai, Desalination, 2009, 239, 191–197 CrossRef CAS.
- P. Rajasekhar, L. H. Fan, T. Nguyen and F. A. Roddick, Water Res., 2012, 46, 1473–1481 CrossRef CAS PubMed.
- J. W. Li, X. Li, X. H. Xu and D. B. Wang, Adv. Mater. Res., 2011, 356–360, 291–297 Search PubMed.
- S. A. Fast, B. Kokabian and V. G. Gude, Chem. Eng. J., 2014, 244, 403–410 CrossRef CAS.
- Y. Li, X. Shi, Z. Zhang and Y. Peng, Ultrason. Sonochem., 2019, 55, 232–242 CrossRef CAS PubMed.
- D. Ghernaout and B. Ghernaout, Desalin. Water Treat., 2012, 44, 15–28 CrossRef CAS.
- B. Y. Gao, Q. Y. Yue and B. J. Wang, J. Environ. Sci. Health, Part A: Toxic/Hazard. Subst. Environ. Eng., 2003, 38, 897–907 CrossRef PubMed.
- B. Y. Gao, Q. Y. Yue, B. J. Wang and Y. B. Chu, Colloids Surf., A, 2003, 229, 121–127 CrossRef CAS.
- B. Y. Gao, G. Abbt-Braun and F. H. Frimmel, Acta Hydrochim. Hydrobiol., 2006, 34, 491–497 CrossRef CAS.
- C. Zhao, S. Shao, Y. Zhou, Y. Yang, Y. Shao, L. Zhang, Y. Zhou, L. Xie and L. Luo, Sci. Total Environ., 2018, 645, 267–276 CrossRef CAS PubMed.
- J. Ma, R. N. Wang, X. Y. Wang, H. Zhang, B. Zhu, L. L. Lian and D. W. Lou, J. Environ. Chem. Eng., 2019, 7, 103049 CrossRef CAS.
- A. Arnold-Smith, R. Christie and C. Jolicoeur, Chemical Water and Wastewater Treatment II, Springer, 1992, pp. 203–219 Search PubMed.
- B. Gao, Q. Yue and J. Miao, Water Sci. Technol., 2003, 47, 127–132 CrossRef CAS.
- P. A. Moussas and A. I. Zouboulis, Sep. Purif. Technol., 2008, 63, 475–483 CrossRef CAS.
- T. Sun, C.-h. Sun, G.-l. Zhu, X.-j. Miao, C.-c. Wu, S.-b. Lv and W.-j. Li, Desalination, 2011, 268, 270–275 CrossRef CAS.
- M. A. Aboulhassan, S. Souabi, A. Yaacoubi and M. Baudu, J. Hazard. Mater., 2006, 138, 40–45 CrossRef CAS PubMed.
- Y. J. Zhang, X. L. Zhao, X. X. Li, C. Liu and L. L. Zhu, Water Sci. Technol., 2010, 62, 330–339 CrossRef CAS.
- X. Li, Y. Zhang, X. Zhao, N. Gao and T. Fu, Sep. Purif. Technol., 2015, 147, 125–131 CrossRef CAS.
- B.-Y. Gao, Y. Wang and Q.-Y. Yue, Acta Hydrochim. Hydrobiol., 2005, 33, 365–371 CrossRef CAS.
- Y. X. Zhao, B. Y. Gao, Y. Wang, H. K. Shon, X. W. Bo and Q. Y. Yue, Chem. Eng. J., 2012, 183, 387–394 CrossRef CAS.
- S. Zhao, B. Gao, Y. Wang and Z. Yang, Colloids Surf., A, 2013, 417, 161–169 CrossRef CAS.
- X. Huang, X. Bo, Y. Zhao, B. Gao, Y. Wang, S. Sun, Q. Yue and Q. Li, Bioresour. Technol., 2014, 165, 116–121 CrossRef CAS PubMed.
- H.-Z. Zhao, Z.-K. Luan, B.-Y. Gao and Q.-Y. Yue, J. Appl. Polym. Sci., 2002, 84, 335–342 CrossRef CAS.
- Z. Yang, B. Yuan, X. Huang, J. Zhou, J. Cai, H. Yang, A. Li and R. Cheng, Water Res., 2012, 46, 107–114 CrossRef CAS PubMed.
- X. Huang, B. Gao, Y. Wang, Q. Yue, Q. Li and Y. Zhang, Chem. Eng. J., 2014, 245, 173–179 CrossRef CAS.
- L. Zhou, H. Zhou and X. Yang, Sep. Purif. Technol., 2019, 210, 93–99 CrossRef CAS.
- H. K. Agbovi, L. D. Wilson and L. G. Tabil, Ind. Eng. Chem. Res., 2017, 56, 37–46 CrossRef CAS.
- S. Bhalkaran and L. D. Wilson, Int. J. Mol. Sci., 2016, 17, 1662 CrossRef PubMed.
- P. Kanmani, J. Aravind, M. Kamaraj, P. Sureshbabu and S. Karthikeyan, Bioresour. Technol., 2017, 242, 295–303 CrossRef CAS PubMed.
- H. Salehizadeh, N. Yan and R. Farnood, Biotechnol. Adv., 2018, 36, 92–119 CrossRef CAS PubMed.
- J. Turunen, A. Karppinen and R. Ihme, SN Appl. Sci., 2019, 1, 210 CrossRef.
- N. Qiao, M. Gao, X. Zhang, Y. Du, X. Fan, L. Wang, N. Liu and D. Yu, Appl. Microbiol. Biotechnol., 2019, 103, 2821–2831 CrossRef CAS PubMed.
- A. S. Ayangbenro, O. O. Babalola and O. S. Aremu, Chemosphere, 2019, 231, 113–120 CrossRef CAS PubMed.
- H. K. Agbovi and L. D. Wilson, Carbohydr. Polym., 2018, 189, 360–370 CrossRef CAS PubMed.
- J. Pérez-Calderón, M. V. Santos and N. Zaritzky, J. Environ. Chem. Eng., 2018, 6, 3808–3818 CrossRef.
- E. Lichtfouse, N. Morin-Crini, M. Fourmentin, H. Zemmouri, I. O. do Carmo Nascimento, L. M. Queiroz, M. Y. M. Tadza, L. A. Picos-Corrales, H. Pei, L. D. Wilson and G. Crini, Environ. Chem. Lett., 2019, 17, 1603–1621 CrossRef CAS.
- B. Peng, Z. Yao, X. Wang, M. Crombeen, D. G. Sweeney and K. C. Tam, Green Energy & Environment, 2020, 5, 37–49 Search PubMed.
- H. Kolya, D. Sasmal and T. Tripathy, J. Polym. Environ., 2017, 25, 408–418 CrossRef CAS.
- D. Sasmal, J. Maity, H. Kolya and T. Tripathy, Int. J. Biol. Macromol., 2017, 97, 585–597 CrossRef CAS PubMed.
- D. Sasmal, H. Kolya and T. Tripathy, Int. J. Biol. Macromol., 2016, 91, 934–945 CrossRef CAS PubMed.
|
This journal is © The Royal Society of Chemistry 2020 |
Click here to see how this site uses Cookies. View our privacy policy here.