DOI:
10.1039/D0RA04888G
(Paper)
RSC Adv., 2020,
10, 26052-26058
Thermal oxidation curing polycarbosilane fibers by alternating air and vacuum process
Received
3rd June 2020
, Accepted 30th June 2020
First published on 10th July 2020
Abstract
Polycarbosilane (PCS) fibers were cured by a process of alternating air and vacuum atmosphere periodically at thermal oxidation temperature. It was found that the oxygen diffusion in the micron PCS fibers could be observed and controlled by this novel curing process. The out surface layer of the cured fibers was rich in oxygen while the inner core had a lower status. Chemical structure analysis indicated that the groups of Si–H, Si–CH2–Si, and Si–CH3 in the out surface layer were oxidized into oxygen containing structures such as Si–OH, Si–O–Si and C
O. Ascribe to the controlled oxygen diffusion, the oxidation degree of the inner core was much lower than the surface layer. The oxygen containing structures, Si–H bond reaction degree, molecular weight and ceramic yield of the cured PCS fibers increased with thermal oxidation temperature and alternating cycles. Theoretical calculation results demonstrated that the Si–H bonds reacted with oxygen was the main reason which made the PCS fiber increase weight. This modified process was a high effective surface layer oxidation curing method. Moreover, silicon carbide (SiC) or silicon nitride (Si3N4) ceramic fibers with skin-core or hollow structure also could be prepared from the surface cured PCS fibers with proper following process.
1. Introduction
Silicon carbide (SiC) ceramic fibers have been widely applied to reinforcement components in metals and ceramics, due to their excellent properties such as high strength, high module, low expansion coefficient, oxidation resistance as well as chemical stability in extreme environments.1–5 In 1975, Yajima and his co-workers reported a pioneering work for preparing fine diameter SiC fibers from polycarbosilane (PCS) precursor.6 It mainly included four steps: synthesis of PCS precursor, melt-spinning, thermal oxidation curing and pyrolysis conversion to ceramic fibers.7,8 The thermal oxidation curing step was necessary to render the melted spinning PCS fibers infusible and remain fibrous shape during pyrolysis. However, this curing process introduced much oxygen in the final SiC fibers and resulted in unsatisfactory high temperature properties.9 To degrade oxygen concentration, other curing processes such as irradiation in oxygen free atmosphere and chemical vapor curing with active gas had been developed.
Recently, SiC ceramic fibers derived from PCS with hollow structure and element distribution gradient on radial direction have attracted more attention. Electron beam irradiation in air, partial curing with ozone and chemical vapor curing with active gas can prepare SiC ceramic fibers with such structures.10–12 The essence of these processes was cross-linking the out surface layer of the PCS fibers. However, these existing methods which mentioned above were technique complex, low efficiency, environment harmful and costly. At present, it's urgent to seek for new process to overcome the disadvantages which mentioned above. Thermal oxidation was a traditional curing process, and didn't acquire any progresses and novel applications since 1970s. It had many advantages such as low cost, easy operation, simple device and environment friendly. The traditional thermal oxidation curing process only can cure the whole cross section of the PCS fibers and obtain dense SiC ceramic fibers. To cross-link the out surface layer of the PCS fibers and obtain hollow structure SiC ceramic fibers, a modified thermal oxidation approach with processes of alternating air and vacuum periodically was used to cure the PCS fibers at thermal oxidation temperature. The SiC ceramic fibers with skin-core or hollow structures could be obtained from the surface layer cured PCS fibers with proper following process. It's a new progress and application based on traditional thermal oxidation curing process. This modified process had promise in the fields of polymer derived inorganic fibers like polyacrylonitrile-based carbon fibers and organosilicon polymer conversion ceramic fibers such as SiBCN(O), SiCN, SiC(Al) and SiC fibers. However, there is no information about the thermal oxidation curing characteristics of the PCS fibers under alternating air and vacuum condition. The object of this work is to report the thermal oxidation characteristics of the PCS fibers under altering atmosphere condition. The weight gain, chemical structure, molecular weight, element distribution, theoretical calculation and ceramic yield were systemically investigated. The oxygen diffusion behavior and surface layer curing mechanism were also discussed.
2. Experimental
2.1 Alternating thermal oxidation curing
PCS (average molecular weight 1300) fibers were provided from National University of Defense Technology (China). Bundles of PCS fibers were put into a vacuum oven (DZF-6050, Changzhou Hengzheng Electronic Instrument Co., Ltd, China) and heated to 175–185 °C under vacuum atmosphere (−0.08 MPa). After holding for 10 minutes in vacuum, the fresh air was flowed into the oven to increase the atmosphere pressure to ordinary. The ordinary pressure air and vacuum atmosphere were alternated after each status holding for 10 minutes. The alternating cycles were from 10 to 50. The thermal oxidation reaction between oxygen and PCS molecular took place in air atmosphere, and stopped in vacuum. Alternating vacuum and air made the thermal oxidation only take place at the out surface layer, while the inner core area didn't oxidize.
2.2 Characterization
The weight gain of the PCS fibers was calculated by the following equation: Weight gain (%) = (W1 − W0)/W0, wherein the W0 and W1 were the weight of the fibers before and after alternating thermal oxidation curing, respectively. Thermal analysis was carried out on a thermal gravimetric analyzer (TGA, NETZSCH SAT 449 F3, Germany) in nitrogen atmosphere from room temperature to 1200 °C with a ramping rate of 10 °C min−1, and the mass residue at 1200 °C was defined as ceramic yield. The chemical structures were analyzed by fourier transform infrared spectrometer (FT-IR, Bruker Tensor 27, Germany) with KBr disks, and the wavenumber was from 4000 to 400 cm−1. The Soxhlet extraction method was used to measure the gel fraction of the fibers after curing. The extraction solvent was tetrahydrofuran (THF), and the extraction times were 15. Scanning electron microscopy (SEM, Hitachi S-4300, Japan) and energy disperse spectroscopy (EDS, Apollo X-SDD, America) were used to measure the cross section morphology and radial direction element distribution. Molecular weight was characterized by gel permeation chromatograph (GPC, Tosoh HLC-8320, Japan) with polystyrene as standard for calibration and tetrahydrofuran (THF) as eluent with 0.6 mL min−1 at 40 °C. 29Si nuclear magnetic resonance (NMR) was detected by cavity solid nuclear magnetic resonance spectrometer (Bruker AVANCE III 400, Switzerland) with chemical shift from −80 to 80 ppm.
3. Results and discussion
3.1 Weight gain
The weight gain can characterize the crosslinking degree between the PCS fibers and oxygen indirectly. The weight gain of the PCS fibers cured by alternating air and vacuum process is shown in Fig. 1. It can be seen that the weight gain obviously increased at temperature range from 170 to 185 °C, and increased with alternating cycles at the same temperature. The higher curing temperature had a higher weight gain. The minimum weight gain was 0.78% at 170 °C with 10 alternating cycles, and the maximum was about 3.99% at 185 °C with 50 cycles. The weight gain increasing indicated that the PCS fibers can be oxidized by using alternating air and vacuum process at thermal oxidation temperature. Compared with the traditional thermal oxidation process, it can be concluded that the alternating atmosphere curing process was also an effective process to oxidize PCS fibers. On the basis of alternating air and vacuum in a periodical way, this process provided feasibility to control the oxygen diffusion and distribution in polymer fibers especially in the fields of oxidation crosslinking polymer. To find out the weight gain mechanism under alternating atmosphere condition, it's necessary to measure the chemical structures and molecular weight.
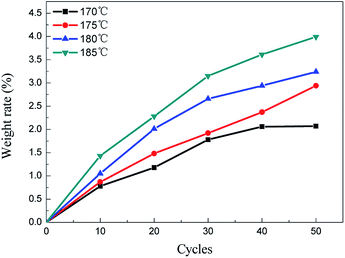 |
| Fig. 1 Weight gain of the PCS fibers. | |
3.2 Chemical structures and molecular weight
Fig. 2 shows the FT-IR spectra of the PCS fibers which cured by alternating air and vacuum process. The typical absorption peaks can be observed at 2961, 2898 (C–H stretching of Si–CH3), 1420 (CH2 deformation of Si–CH3), 1250 (Si–CH3 deformation), 2100 (Si–H stretching) and 1020 cm−1 (Si–CH2–Si).10 Compared with the uncured PCS fibers, the cured PCS fibers appeared two new peaks at 1710 (due to C
O stretching) and 3680 cm−1 (O–H stretching of Si–OH), and the absorption peak at 1020 cm−1 also increased and broadened. Moreover, as can be seen from Fig. 2(b)–(e), the Si–H absorption peaks decreased while the C
O and Si–OH increased with cycles and temperature. According to the literature,11 the Si–H bonds and Si–CH3 groups took place oxidation reaction with oxygen and formed Si–OH and C
O structures. The oxidation reaction resulted in the Si–H absorption peaks decreasing, while the Si–OH and C
O absorption peaks increasing. The absorption peak changes at 1020 cm−1 were ascribed to Si–OH dehydration condensation to form bridge structure of Si–O–Si (1080 cm−1) and overlapped on the peak of Si–CH2–Si (1020 cm−1).12 The overlapped effect made the peak broaden. It's no doubt that the oxygen-containing structures (Si–OH, Si–O–Si and C
O groups) resulted in the PCS fiber increasing weight. Generally, the Si–OH dehydration condensation could result in initiating chain reaction and elongation. The molecular chain variation can be detected by the molecular weight and molecular weight distribution.
 |
| Fig. 2 IR spectra of the PCS fibers. (a) PCS; (b) 170 °C-20 cycles; (c) 170 °C-50 cycles; (d) 175 °C-50 cycles; (e) 185 °C-50 cycles. | |
The gel content of the cured PCS fibers was measured before the GPC testing. Results showed that all of the cured fibers didn't have gel. It's indicated that the cured PCS fibers were ungelatinized and can be used to measure the GPC curves. The molecular weight distribution curves are shown in Fig. 3. As can be seen in Fig. 3, the GPC curve of the received PCS fibers consisted with two peaks, the flow time of the broader peak which ascribed to macromolecular part was 7–10.5 min. After curing at 180 °C with 30 cycles, the flow time of the broader peak widened and was about 6.5–10.5 min. The earlier flow time indicated that the molecular weight of the cured PCS fibers became higher than that of the received. In order to clarify the molecular weight changes in detail, the number-average molecular weight (Mn), weight-average molecular weight (Mw) and polydispersity coefficient (Mw/Mn = PDi) are detected and shown in Table 1. It can be seen that the Mn, Mw and PDi were all increased with alternating cycles and temperature. Based on the FT-IR analysis, the molecular chain elongation and molecular weight increasing can be ascribed to the formation of oxygen containing structures and bridge structures. From the discussed above, it can be concluded that the alternating atmosphere was a novel and effective curing process, and can be used to crosslink the PCS fibers.
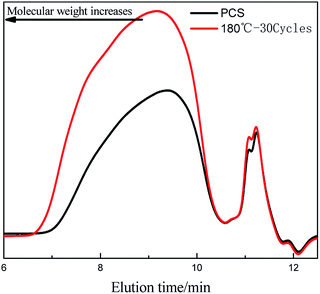 |
| Fig. 3 GPC curves of the PCS fibers before and after alternating atmosphere curing. | |
Table 1 Molecular weight of the PCS fibers
Sample |
Mn (g mol−1) |
Mw (g mol−1) |
PDi |
PCS(original) |
1293 |
3428 |
2.650 |
PCS(175 °C)-30 |
1445 |
4634 |
2.980 |
PCS(185 °C)-30 |
1545 |
5152 |
3.335 |
PCS(180 °C)-10 |
1399 |
4027 |
2.878 |
PCS(180 °C)-50 |
1605 |
5984 |
3.728 |
3.3 Theoretical weight gain
The Si–H bond reaction degree can verify thermal oxidation curing degree intuitively. According to the FT-IR spectra data and literature formulas,13 the calculated results of the Si–H bond reaction degree are shown in Fig. 4. It showed that the reaction degree increased with alternating cycles and temperature, and the effect of temperature was more remarkable than the cycles. The tendency was the same as FT-IR spectra absorption peak at 2100 cm−1. In order to investigate the theoretical weight gain, solid 29Si-NMR spectroscopy was used to measure the molecular structure units of the received PCS fibers. As can be seen in Fig. 5, the PCS mainly included two types of structure. The signal at chemical shift of around −2 ppm was assigned to the resonance of the silicon bonded to four carbons (SiC4). The signal at −20 ppm was assigned to the silicon bonded to one hydrogen atom and three carbons (SiC3H). From the peak area integrals, the ratio of SiC4 to SiC3H was found to be about 3
:
2. It represented that the structure unit number was 3
:
2. According to the GPC data of the received PCS fiber (Mn = 1293), the PCS molecular chain included 8 SiC3H (Mn = 58) and 12 SiC4 (Mn = 72) structure units. It's no doubt that the Si–H bond belonged to SiC3H structure.14,15 Similarly, the Si–H bond reaction corresponded to the SiC3H structure consumption and the formation of Si–OH.
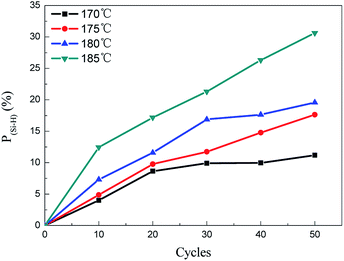 |
| Fig. 4 Si–H bond reaction degree of the PCS fiber. | |
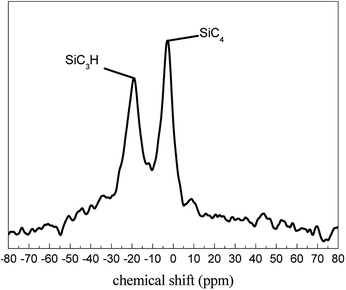 |
| Fig. 5 29Si-NMR spectrum of the received PCS fibers. | |
To demonstrate the effect of Si–OH formation on weight gain, the theoretical weight gain of the PCS fibers were calculated by SiC3H structure consumption with the formula of
, wherein the Twt, W0, PSi–H, Ow, Mn PCS and NSiC3H were the theoretical weight gain of the PCS fibers, mass of the received PCS fibers, Si–H reaction degree, relative atomic mass of the oxygen, number-average molecular weight of the received PCS fibers and the number of SiC3H structure in a PCS molecule, respectively. The theoretical weight gain is shown in Fig. 6. As can be seen in Fig. 6 and 4, the theoretical weight gain of the cured PCS fibers was proportional with Si–H bond reaction degree at the temperature range from 170 to 185 °C, and the variation tendency was consistent with each other. The maximum theoretical weight gain was about 3.03% at 185 °C with 50 alternating cycles. However, based on Fig. 1 analysis, the actual weight gain was higher than that of the theoretical. This indicated that the actual weight gain was consisted with other oxidation weight gain approach. According to the FT-IR analysis, the formation of C
O also contributed to the oxidation weight gain.
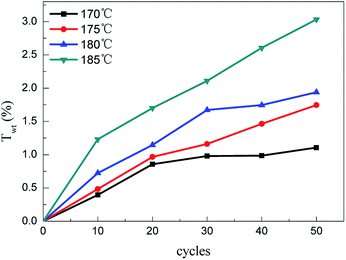 |
| Fig. 6 Theoretical weight gain caused by Si–H bond consumption. | |
In order to investigate the effect of Si–H bond reaction which corresponded to the formation of Si–OH on weight gain contribution rate, the ratio of theoretical weight gain to actual weight gain was defined as contribution rate. The contribution rate is shown in Table 2. It can be seen that the Si–H reaction consumption was the main factor for increasing weight. The minimum contribution rate was above 47.86% at 170 °C with 40 cycles, and the maximum was 86.06% at 185 °C with 10 cycles. In addition, it also can be seen that the contribution rate increased with temperature under the same alternating cycle condition. The higher temperature had a higher contribution rate. It's proved that the Si–H bonds in the PCS molecular were very active and quite sensitive to temperature, and easy to react with oxygen in air atmoshpere. This phenomena was also consistent with the literature described.16
Table 2 Weight gain contribution rate led by Si–H bond consumption
Cycles |
Temperature (°C) |
170 |
175 |
180 |
185 |
10 |
50.86% |
55.54% |
68.88% |
86.06% |
20 |
72.54% |
65.28% |
57.00% |
74.57% |
30 |
55.10% |
60.48% |
62.84% |
66.96% |
40 |
47.86% |
61.72% |
59.34% |
72.15% |
50 |
53.48% |
59.37% |
59.82% |
75.98% |
3.4 Ceramic yield
Fig. 7 shows the TG curves of the PCS fiber before and after alternating atmosphere thermal oxidation curing. It showed that the weight loss of the received PCS fibers was the largest, and the ceramic yield was about 65% at 1200 °C. After curing by alternating process, the ceramic yield enhanced dramatically and increased with temperature and alternating cycles. The ceramic yield reached the maximum 86.7% under the condition of 185 °C with 50 cycles. Based on the chemical structure and weight gain analysis, the improved ceramic yield was ascribed to increase the crosslinking degree of the PCS fibers. Moreover, Fig. 7(c) and (f) showed that the ceramic yield increased with alternating cycles at same temperature. Nevertheless, the effect of temperature on ceramic yield was more obvious than the alternating cycle. This phenomenon was also associated with the theoretical and actual weight gain. Combined with the weight gain, chemical structures and molecular weight analysis, it can be concluded that the alternating process was a novel and effective process to cure PCS fibers, and can increase the ceramic yield greatly with several alternating cycles at any thermal oxidation temperature.
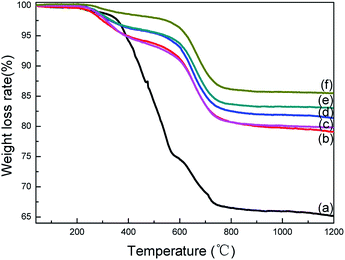 |
| Fig. 7 TG curves of the PCS fibers. (a) PCS; (b) 170 °C-50 cycles; (c) 185 °C-20 cycles; (d) 175 °C-50 cycles; (e) 180 °C-50 cycles; (f) 185 °C-50 cycles. | |
3.5 Oxygen distribution and diffusion mechanism
The above analysis showed that a large amount of oxygen was introduced into the PCS molecular and formed a lot of oxygen-containing functional groups by this modified process. According to the oxygen diffusion principle in polymer, it's quite necessary to identify the oxygen distribution status and diffusion mechanism in the PCS fibers. The oxygen distribution in out surface layer and inner core area is shown in Fig. 8 and Table 3. As shown in Fig. 8(a), the cross section of the direct oxidation (traditional way) fiber was dense and smooth, and the diameter was about 14 μm. The EDS analysis showed that the composition was Si, C and O, and the oxygen amount in out surface and inner core area was almost the same in proportion. The oxygen content in out and inner area was 12.33% and 11.48% respectively. After 50 circles curing at 180 °C, the micro structure and EDS peaks of the cured fibers are shown in Fig. 8(b). It can be seen that the composition of the cured fiber was still Si, C and O, but the oxygen was rich in surface layer (13.81%) and lower in inner core area (6.08%). This proved that the cured PCS fibers had an oxygen gradient distribution status, and the out surface was rich in oxygen while the inner core with a lower status. It's a typical oxygen distribution skin-core structure. The oxygen distribution indicated that oxygen diffused into PCS fiber and fixed on molecular chain by oxidation reaction under this modified process, and the diffusion was limited in a finite distance by vacuum. Based on the polymer fiber molding theory, the PCS molecular chains were accumulated together to form micron PCS fiber during melting spinning. The PCS chains in the out surface layer area were firstly oxidized when exposed to air atmosphere at thermal oxidation temperature. Subsequently, the oxygen diffused from the out layer into the inner core in a limited distance, and took place inner oxidation. The inner oxidation would stop because of lack oxygen by vacuum process. In this cycle cuing way, the oxygen distribution in the cross section of the PCS fibers presented a gradient. However, the direct oxidation process (Yajima approach) would oxidize the whole fiber, and the oxygen diffused from the out surface into the inner core continuously, and resulted in the inner core had the same oxygen concentration as the surface. Based on the FT-IR and SEM-EDS analysis, the diagram of diffusion and thermal oxidation mechanism by altering atmospheres is shown in Fig. 9. The surface layer of the PCS fiber had higher oxidation reaction degree due to much oxygen acted on the surface layer repeatedly, while the inner core had a lower oxidation status because of lacking oxygen with vacuum blocking oxygen diffusion. The PCS fibers with oxygen gradient distribution skin-core structure could be obtained through this novel process. The surface layer cured PCS fibers provided the feasibility for preparation of skin-core and hollow structure SiC or Si3N4 ceramic fibers as illustrated in literature.17,18 In addition, this process also had potential applications in the fields of organic polymer or organosilicon polymer conversion inorganic fibers with special structures and element gradient distribution.
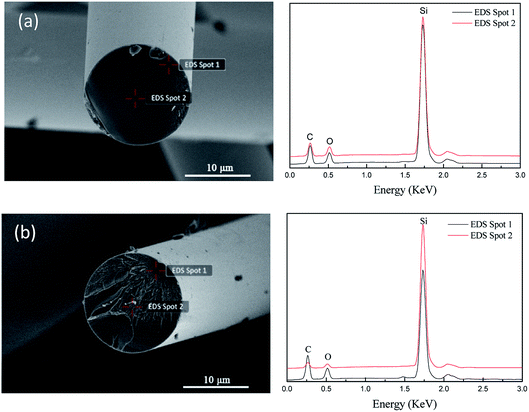 |
| Fig. 8 SEM-EDS photograph of the PCS fibers. (a) 180 °C-6.67 h; (b) 180 °C-50 cycles. | |
Table 3 EDS results of the cured PCS fibers by traditional and modified thermal oxidation
Element |
180 °C-6.67 h |
180 °C-50 cycles |
Spot 1 wt% |
Spot 2 wt% |
Spot 1 wt% |
Spot 2 wt% |
C K |
44.12 |
39.67 |
51.07 |
29.96 |
O K |
12.33 |
11.48 |
13.81 |
6.08 |
Si K |
43.55 |
48.85 |
35.12 |
63.96 |
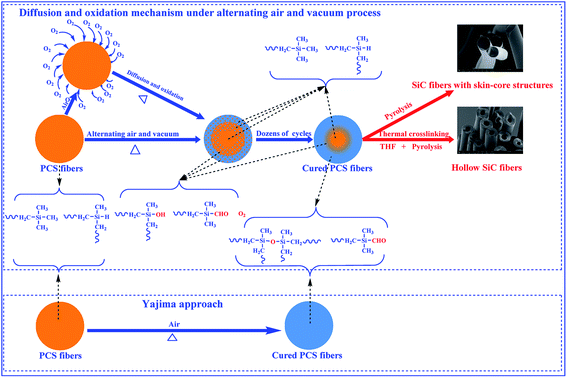 |
| Fig. 9 Diagram of diffusion and alternating thermal oxidation curing mechanism. | |
4. Conclusions
Altering air and vacuum periodically was a novel and effective process to cure the PCS fibers. The PCS fibers exposed in air and vacuum atmosphere periodically made the surface layer take place thermal oxidation reaction, and formed oxygen gradient distribution structure. The surface layer was rich in oxygen in forms of Si–OH, Si–O–Si and C
O structures, while the inner core had a much lower oxygen content. The weight gain, oxygen containing structures, Si–H bond reaction degree, molecular weight and ceramic yield of the PCS fibers were all increased with thermal oxidation temperature and alternating cycles. The Si–H bond reacted with oxygen was the main reason which made the PCS fiber increase weight. The minimum weight gain contribution rate from Si–H bonds reaction was 47.86% at 170 °C with 40 cycles, and the maximum contribution rate was 86.06% at 185 °C with 10 cycles. The ceramic yield of the cured PCS fibers increased greatly under several alternating cycles. This process provided feasibility to control the oxygen diffusion and distribution in polymer fibers especially in the field of gas–solid reaction crosslinking polymer. The cured PCS fibers could be used to prepare fine diameter SiC ceramic fibers with skin-core or hollow structures. It's a new breakthrough and novel application mode which modified from traditional curing process.
Conflicts of interest
There are no conflicts to declare.
Acknowledgements
This study is supported by the National Natural Science Foundation of China (No. 51462004), Foundation of Guizhou Educational Committee of China (No. YJSCXJH[2019]049 and CJYC[2018]01) and the Top Talent Support Program of Guizhou Education Department (No. KY[2015]401 and KY[2016]062).
Notes and references
- Z. He, P. Lian, Y. Song, Z. Liu, J. Song, J. Zhang, X. Ren, J. Feng, X. Yan, Q. Guo and W. Liu, J. Eur. Ceram. Soc., 2018, 38, 453–462 CrossRef CAS.
- Y. Gou, K. Jian, H. Wang and J. Wang, J. Am. Ceram. Soc., 2018, 101, 2050–2059 CrossRef CAS.
- E. Ghasali, M. Alizadeh, A. H. Pakseresht and T. Ebadzadeh, Journal of Asian Ceramic Societies, 2017, 5, 472–478 CrossRef.
- T.-E. Kim, K.-E. Khishigbayar and K. Y. Cho, Journal of Advanced Ceramics, 2017, 6, 59–66 CrossRef CAS.
- Y. W. Kim, K. Y. Lim and W. S. Seo, J. Am. Ceram. Soc., 2014, 97, 923–928 CrossRef CAS.
- S. Yajima, J. Hayashi, M. Omori and K. Okamura, Nature, 1976, 261, 683 CrossRef CAS.
- G. Wang and Y. Song, Ceram. Int., 2018, 44, 6474–6478 CrossRef CAS.
- H. Laadoua, R. Lucas, Y. Champavier, S. Foucaud, R. Zerrouki and F. Brouillette, Mater. Lett., 2017, 191, 46–49 CrossRef CAS.
- B. Yao, B. Lu, Q. Huang, Z.-R. Huang and Q. Yuan, Ceram. Int., 2020, 46, 9894–9900 CrossRef CAS.
- Z. Su, L. Zhang, Y. Li, S. Li, L. Chen and R. Riedel, J. Am. Ceram. Soc., 2015, 98, 2014–2017 CrossRef CAS.
- Y. Shi, F. Luo, D. Ding, F. Wan, W. Zhou and D. Zhu, Int. J. Appl. Ceram. Technol., 2016, 13, 17–22 CrossRef CAS.
- M. Sugimoto, A. Idesaki, S. Tanaka and K. Okamura, Key Eng. Mater., 2003, 247, 133–136 CAS.
- W. Bai, K. Jian and Y. Shi, Adv. Appl. Ceram., 2018, 117, 369–375 CrossRef CAS.
- J. Hong, K.-Y. Cho, D.-G. Shin, S. H. Kim and D.-H. Riu, J. Inorg. Organomet. Polym. Mater., 2018, 28, 2221–2230 CrossRef CAS.
- X. Mao, Y. Song, W. Li and D. Yang, J. Appl. Polym. Sci., 2007, 105, 1651–1657 CrossRef CAS.
- M. Tang, Z. Yu, Y. Yu, L. Zhang and L. Chen, J. Mater. Sci., 2009, 44, 1633–1640 CrossRef CAS.
- Y. Li, Z. Xu, Y. Chen and H. Liao, A method for preparing skin–core structure silicon carbide ceramic fibers, CN Pat. CN108218435A, 2018-06-29.
- Y. Li, X. Li, Z. Xu, W. Liu, K. Ran and L. Chen, A method for preparing micrometer hollow silicon carbide/silicon nitride fibers, CN Pat. CN109750390A, 2019-05-14.
|
This journal is © The Royal Society of Chemistry 2020 |
Click here to see how this site uses Cookies. View our privacy policy here.