DOI:
10.1039/D0RA05699E
(Paper)
RSC Adv., 2020,
10, 38515-38523
Investigation of the emission control of sulfur trioxide aerosols based on heterogeneous condensation and the deflectors tray of the desulfurization tower
Received
30th June 2020
, Accepted 1st October 2020
First published on 20th October 2020
Abstract
In this paper, control over the emission of sulfur trioxide aerosols was investigated based on heterogeneous condensation in the wet flue gas desulfurization process. The influence of the deflectors tray of the desulfurization tower on the removal performance of the sulfur trioxide aerosols was also studied. The results show that the critical supersaturation degree of sulfur trioxide aerosols is in inverse proportion to the sizes. Heterogeneous condensation has a significant effect on the reduction of sulfur trioxide aerosols. The number concentration of the sulfur trioxide aerosols with sizes <0.1 μm decreases, while the number concentration of sizes >0.1 μm increases at the outlet with this method. The relative humidity of the flue gas is likely to be the most influential in the formation of a supersaturated environment and the removal of sulfur trioxide aerosols. Addition of the tray in the desulfurization tower also increases the reduction of sulfur trioxide aerosols. Heterogeneous condensation can improve the removal efficiency of sulfur trioxide aerosols by 14.3% as well as the installation of a tray by 21.4%.
1. Introduction
Recently, environmental pollution has been a growing area of interest, especially the air pollution. Sulfur trioxide aerosols and fine particle aerosols, mainly produced in power plants, are having a significantly serious impact on the environment and human health.1,2 Actually, the amount of sulfur trioxide aerosols of original flue gas generated from boilers is low, approximately 0.5–1.5%.3,4 However, a selective catalytic reduction (SCR) denitration system is widely used, promoting the oxidation of sulfur dioxide to sulfur trioxide. Therefore, the sulfur trioxide content of flue gas increases. Generally, the oxidation rate of sulfur dioxide is about 0.5–2.0%,5 and the oxidation rate of sulfur dioxide increases with the increasing temperature. Due to the moisture-absorbing characteristics of sulfur trioxide, 99% sulfur trioxide transforms into sulfuric acid vapor as the temperature exceeds 200 °C and the moisture content in the flue gas is about 8%.6–8 Subsequently, the sulfuric acid vapor easily forms sulfur trioxide aerosols in the process of desulfurization. The toxicity of SO3 is about ten times greater than that of SO2, which is also the main cause of blue smoke and yellow smoke in power plants.9 SO3 can form sub-micron sulfuric acid mist after being discharged into the atmosphere, which is one of the main causes of acid rain formation. Sulfuric acid mist reacts with particulate matter forming sulfate, which is one of the important sources of PM2.5 in the atmosphere.10–13 In addition, SO3 may cause equipment corrosion, such as desulfurization absorption tower, flue, and chimney. However, there is no effective method to control the emission of sulfur trioxide aerosols.14
The wet flue gas desulfurization (WFGD) system has been widely applied to control the emission of SO2.15–18 Although wet desulfurization has a significant effect on the removal of sulfur dioxide, the removal effect on the sulfur trioxide aerosols is not ideal.
According to previous reports,19,20 some strategies have been used to control the emission of sulfur trioxide aerosols, such as reducing the formation of gaseous sulfur trioxide during combustion in the boiler, optimization of the denitration catalyst, spraying alkaline absorbent in the flue after the boiler or removing sulfur trioxide with equipment. The initial SO2 concentration, O2 concentration and the temperature have an influence on the concentration of SO3 during combustion in the boiler.21 When the temperature reaches 1200 °C, the equilibrium generation rate decreases to 2.2%. During the SCR process, approximately 1–2% SO2 would be oxidized to SO3. High H2O and high CO2 concentrations result in the decrease of SO3 generation.22 Spraying alkaline absorbent in the flue after the boiler could decrease the mass concentration of SO3 by 49%. Some power plants adopt a double-desulfurization tower instead of single-desulfurization tower to improve the removal efficiency of dust.23 A low–low temperature electrostatic precipitator and wet electrostatic precipitator have also been applied to achieve ultra-low emissions.24 These methods have a significant effect on the removal of the particles while the effect on the removal of the sulfur trioxide aerosols is still unsatisfactory. In the double-desulfurization tower process, the removal efficiency of SO3 is about 60%.25 The removal efficiency of SO3 is about 50% with the low–low temperature electrostatic precipitator.26 In addition, the installation of a wet electrostatic precipitator has an effect on the removal of SO3, and the removal efficiency is about 30–60%.27 These methods have an influence on the removal of SO3, but the investment and operating cost are high.
Recently, a method controlling the emission of sulfur trioxide aerosols by combining heterogeneous condensation with traditional pollution control equipment was proposed.28 Heterogeneous condensation would enlarge the size of the particles by establishing a supersaturated environment, and then the particles could be removed by the traditional pollution control equipment.
Fletcher29 proposed that the heterogeneous condensation starts from the embryo droplets formed on the surface of fine particles. Rich et al.30 carried out an experimental study on the enhancement of metal oxide powder removal by heterogeneous condensation and revealed that the mass concentration removal efficiency of fine particles is 99.4% with heterogeneous condensation. Yan et al.31 carried out the experiment to promote the removal of fine particles with the heterogeneous condensation. The results showed that when water vapor was added, the removal efficiency of fine particles could be greatly improved and the number concentration removal efficiency could be increased to about 80%. Bao et al.32 added steam to the flue gas in the desulfurization tower to establish a supersaturated environment. They reported that heterogeneous condensation can significantly improve the removal efficiency of fine particles. This method has been applied to remove fine particles in coal-fired power plants and the effect is significant. However, removing sulfur trioxide aerosols with this method is insufficient.
In this work, the removal of the sulfur trioxide aerosols based on heterogeneous condensation was investigated. The influence of the deflectors tray of the desulfurization tower on the removal efficiency of the sulfur trioxide aerosols was also studied. Moreover, the supersaturation degree distribution along the desulfurization tower height was calculated. Simultaneously, the effect of the temperature of the flue gas, the temperature of the desulfurization slurry, the ratio of the liquid to gas (L/G) and the relative humidity of the flue gas on the removal performance were also investigated. In addition, the influence of the desulfurization tower on the reduction of sulfur trioxide aerosols with and without trays was also discussed in detail.
2. Experimental section
2.1 Experimental system
The outline of the experimental system is shown in Fig. 1. This system mainly consists of a flue gas generator system, a desulfurization system, a slurry circulation system and an analytical test system.
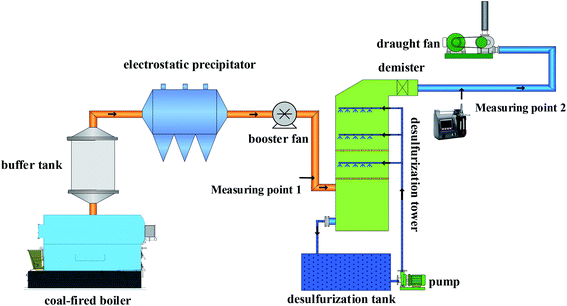 |
| Fig. 1 Schematic diagram of the experimental system. | |
The flue gas was provided by an automatic coal-fired boiler. The flue gas volume of the system was 350 ± 5 Nm−3 h−1 and the flue gas velocity was 3.5 m s−1. The flue gas and SO3 were mixed uniformly in the buffer vessel and SO3 was provided by the SO3 generator. Then, the mixed flue gas would go through the ESP, desulfurization tower, wet electrostatic precipitator, and, finally, discharge into the atmosphere. The coarse particles were removed in the ESP. Subsequently, the flue gas entered the desulfurization tower, and countercurrent contacted the desulfurization slurry. The desulfurization tower type was a spray tower with three spray layers and a baffle defogger was installed above the spray layer. The sprayed desulfurization slurry flowed into the desulfurization slurry tank for circulation. In the desulfurization tower, trays were installed to promote the contact between the flue gas and desulfurization slurry, improving the removal efficiency of the sulfur trioxide aerosols. The hole porosity of the tray is 39% and the thickness of the tray is 5 mm. The diameter of the hole is 10 mm, the center distance of the hole is 14.2 mm and the degrees staggered is 60 between holes. The tray was installed below the spray layer or above the first-level spray. It is possible to avoid scaling and clogging of the tray when the tray was installed above the first-level spray. A steam generator was used to add the steam into flue gas to simulate the high humidity environment.
The SO3 generator is shown in Fig. 2, where SO3 was produced by means of oxidation of SO2 by O3. The O3 and SO2 were provided by the O3 generator and SO2 cylinder gas. The amount of SO2 and O3 were accurately controlled through the mass flow meter.
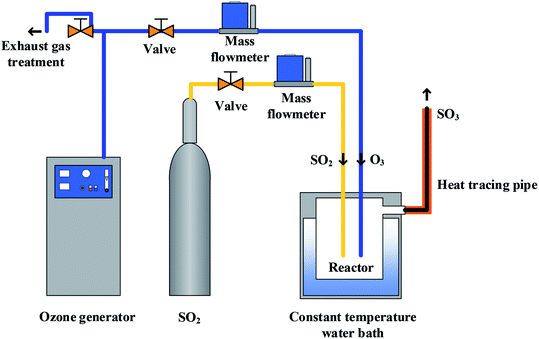 |
| Fig. 2 Sulfur trioxide aerosols generating device. | |
2.2 Testing and analytic methods
The experiment was based on the lime-gypsum method. The composition of the original slurry feed was limestone and the mass concentration was about 15%. The main composition of the slurry was limestone and gypsum with the circulation of desulphurization slurry. The pH of desulfurization slurry was 5.5, and the ORP was 178 mV. The mass concentration and number concentration of sulfur trioxide aerosols were measured by different ways. The controlled condensation method was adopted to measure the SO3 mass concentration according to the national standard.33,34 The sampling system contained a sampling probe, a filter cartridge, a sampling gun, a serpentine glass collection tube, a thermostatic water bath, and a dust sampler, as shown in Fig. 3. The flue gas first went into the sampling probe constant velocity, and then through the filter cartridge, in which particles in the flue gas could be separated. Subsequently, the filtered flue gas went into the sampling gun. The flue gas in the sampling gun was heated to 180 °C to prevent the condensation of sulfur trioxide aerosols since the typical sulfuric acid dew point is between 95 °C and 160 °C.35 The flue gas was cooled in the serpentine glass collection tube through a cooling water bath. The temperature of cooling water was set at about 60 °C. Hence, the sulfur trioxide in the flue gas would condense on the wall of the serpentine condenser. Then, the serpentine glass collection tube was rinsed with deionized water to collect SO4.2 Finally, an ion chromatographic analyzer was used to measure the mass concentration of the SO4.2 Then, the mass concentration of the sulfur trioxide aerosols was obtained.
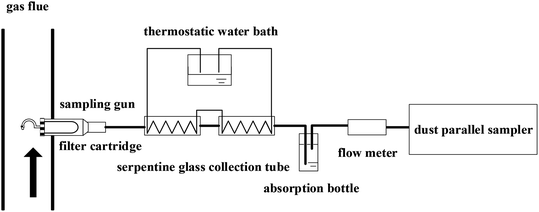 |
| Fig. 3 The sampling system of sulfur trioxide aerosols. | |
The number concentration of the sulfur trioxide aerosols was measured in real-time by high-temperature ELPI (electric low-pressure impactor, Finland Dekati), as shown in Fig. 4. Dekati RTHTU (Dekati real-time high-temperature unit) and ELPI+ combine to complete the real-time high-temperature aerosols measurement. The temperature of the flue gas was heated by HT-ELPI+ to 120 °C above the dew point of the water and below the acid dew point. Simultaneously, the impact plate was heated and insulated. This could avoid the condensation of water vapor of flue gas, resulting in the higher accuracy of the test. In the experiment, the temperature and the humidity of flue gas were obtained by a humidity transmitter. The flue gas was sampled at the inlet and outlet of the desulfurization tower, respectively.
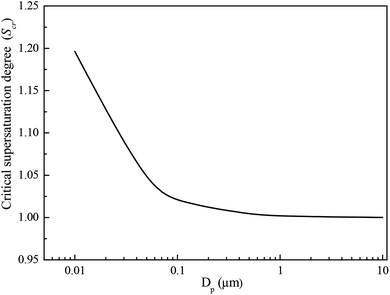 |
| Fig. 4 The critical supersaturation degree of sulfur trioxide aerosols with different sizes. | |
The removal efficiency based on the mass or number concentration of sulfur trioxide aerosols was determined by
|
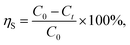 | (1) |
where
ηS is the removal efficiency of the emitted sulfur trioxide aerosols, and
C0 and
Ct are the mass or number concentration of sulfur trioxide aerosols of the desulfurization tower inlet and outlet, respectively. In this paper, the removal efficiency was characterized based on mass concentration.
2.3 Critical supersaturation of the sulfur trioxide aerosols
When the supersaturation degree of the environment is higher than the critical supersaturation degree of the sulfur trioxide aerosols, heterogeneous condensation will occur. Subsequently, the sulfur trioxide aerosols will nucleate and enlarge. The supersaturation degree of environment is given by |
 | (2) |
where S is the supersaturation degree, P(T) is the actual vapor partial pressure and PS(T) is the saturated vapor partial pressure. The critical supersaturation degree of the sulfur trioxide aerosols is obtained as36 |
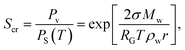 | (3) |
where Scr is the critical supersaturation degree of the sulfur trioxide aerosols, Pv is the surface vapor pressure of the sulfur trioxide aerosols, PS(T) is the saturation vapor at temperature T, σ is the surface tension, Mw is the molar mass, RG is the gas constant, ρw is the density of the liquid, and r is the radius.
Using eqn (3), the critical supersaturation degree as a function of the sizes of the sulfur trioxide aerosols is obtained. With respect to the numerical calculation, the temperature of the flue gas was set at 55 °C. As shown in Fig. 4, the critical supersaturation degree of the sulfur trioxide aerosols is in inverse proportion to the sizes. With larger sulfur trioxide aerosol sizes, the sulfur trioxide aerosols critical supersaturation degree is lower. Therefore, larger sizes of sulfur trioxide aerosols (more than 0.1 μm) are more easily nucleated and enlarged, while the sulfur trioxide aerosols between 0.01–0.1 μm require higher vapor supersaturation for the heterogeneous condensation. It has been reported that the size of sulfur trioxide aerosols in desulfurized flue gas is mainly concentrated in the range of 0.01–0.1 μm.18
3. Result and discussion
3.1 Effect of heterogeneous condensation to the removal of sulfur trioxide aerosols
Fig. 5 describes the distribution of the supersaturation degree along the desulfurization tower calculated under typical conditions. The temperature of the desulfurization tower inlet was set as 80 °C, the L/G was 15, the temperature of the desulfurization slurry was 40 °C and the flue gas velocity of the desulfurization tower inlet was 3.5 m s−1. It can be seen that the supersaturation degree increases as the desulfurization tower height increases. As the relative humidity shifts from 16% to 32%, the maximum supersaturation degree formed in the desulfurization tower increases from 0.82 to 1.28. When the relative humidity is 22%, the position beginning to form a supersaturated environment is 0.45 m, and this position shifts lower with increasing relative humidity. Therefore, a higher relative humidity is beneficial to the formation of the supersaturated environment. As the relative humidity reaches 22%, the supersaturated environment is formed, and the heterogeneous condensation of sulfur trioxide aerosols occurs. Thus, the relative humidity of the flue gas was set as 22% in the experiment.
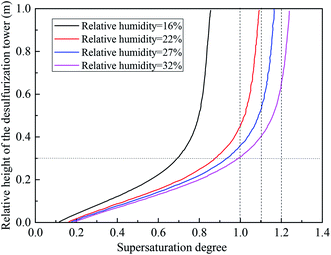 |
| Fig. 5 The supersaturation degree distribution in the desulfurization tower. | |
3.2 Removal performance of the sulfur trioxide aerosols under typical conditions
Fig. 6 describes the number concentration of the sulfur trioxide aerosols at the inlet and outlet of the desulfurization tower under different typical conditions. In the experiment, the flue gas temperature of the desulfurization tower inlet was set as 80 °C, the temperature of the slurry was 40 °C, the relative humidity was 16% for condition (a) and 22% for conditions (b)–(d), and the L/G was 15. Condition (a) was without heterogeneous condensation or a tray, condition (b) was with heterogeneous condensation, condition (c) was with heterogeneous condensation and a single tray, and condition (d) was with heterogeneous condensation and a double tray. The number concentration of sulfur trioxide aerosols in the inlet of the desulfurization tower was about 1.88 × 107 cm−3, and the number concentration of the sulfur trioxide aerosols at the outlet were 1.0 × 107 cm−3, 8.1 × 106 cm−3, 7.2 × 106 cm−3 and 5.9 × 106 cm−3 for conditions (a)–(d), respectively. It can be seen that the number concentration of the sulfur trioxide aerosols decreases with the conditions shifting from (a) to (d). It can be seen from Fig. 6 that the removal of sulfur trioxide aerosols with condition (b) is better than condition (a). Thus, heterogeneous condensation can effectively improve the removal of sulfur trioxide aerosols. Compared with conditions (b) and (c), the tray has a function to promote the removal of sulfur trioxide aerosols. Simultaneously, the effect of the double tray on the reduction of sulfur trioxide aerosols is better than the single tray.
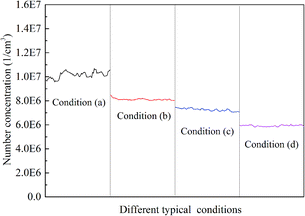 |
| Fig. 6 The number concentration of sulfur trioxide aerosols under different typical conditions. | |
Fig. 7 describes the size distribution of the sulfur trioxide aerosols under conditions (a)–(d). The size distribution of the sulfur trioxide aerosols at the inlet presents a single peak distribution. Additionally, the sulfur trioxide aerosols are mainly sub-micron, and mainly distributed below 0.1 μm. The number of sulfur trioxide aerosols with a particle size greater than 1 μm is almost 0. The number concentration of sulfur trioxide aerosols shows a decreasing tendency under different conditions. As seen in Fig. 8, the number concentration of sulfur trioxide aerosols under conditions (b)–(d) with diameter >0.1 μm increases but almost remains unchanged with condition (a). This could be attributed to the effect of the heterogeneous condensation on the growth of the sulfur trioxide aerosols. The supersaturation vapor environment is established in the desulfurization tower under conditions (b)–(d). Then, the heterogeneous condensation occurs, and thus, the vapor condenses with sulfur trioxide aerosols as condensed nodules. Finally, this results in sulfur trioxide aerosols with larger sizes.
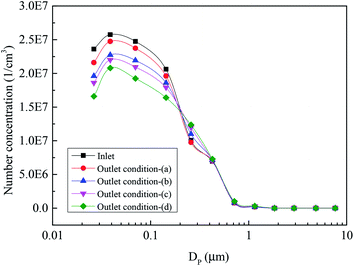 |
| Fig. 7 The size distribution of sulfur trioxide aerosols under different typical conditions. | |
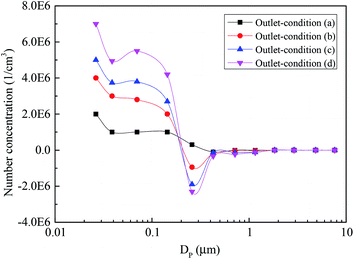 |
| Fig. 8 The size captured by desulfurization tower under different typical conditions. | |
Fig. 8 presents the size distribution of sulfur trioxide aerosols captured in the desulfurization process under different typical conditions. It can be interestingly observed from Fig. 8 that the number concentration of the sulfur trioxide aerosols with sizes <0.1 μm decreases, while the number concentration of sizes >0.1 μm increases. The reason for this phenomenon is that the sulfur trioxide aerosols condense and grow under heterogeneous condensation. Fig. 9 describes the cumulative number distribution of sulfur trioxide aerosols under different typical conditions. It can be obtained that the proportion of sulfur trioxide aerosols in large sizes becomes higher. This is mainly attributed to heterogeneous condensation because the sulfur trioxide aerosols are activated and grow during heterogeneous condensation. Comparing the result of condition (b) and conditions (c) and (d) (see in Fig. 6–9), the tray has a promoting effect on the removal of sulfur trioxide aerosols. This is because the tray can make the distribution of flue gas more uniform, and the supersaturation degree distribution is also more uniform. Simultaneously, the desulfurization slurry can stay on the tray for a period of time, increasing the contact time between flue gas and desulfurization slurry. Therefore, flue gas and desulfurization slurry can completely react, enhancing the heat and mass transfer during the desulfurization process, and then the flue gas becomes supersaturated and homogeneous nucleation occurs subsequently.
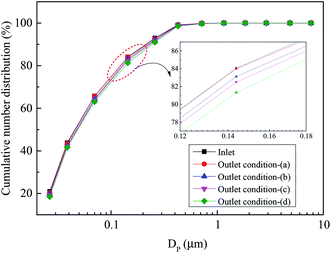 |
| Fig. 9 The cumulative number distribution of sulfur trioxide aerosols under different typical conditions. | |
Fig. 10 shows the removal efficiency of the sulfur trioxide aerosols under the different conditions. The removal efficiency for condition (a) is 41.3% and condition (b) is 55.6%. This is because the vapor heterogeneous condensation improves the removal of the sulfur trioxide aerosols. The removal efficiency for conditions (c) and (d) are 60.4% and 65.9%, respectively. This shows that the installation of the tray promotes the removal of sulfur trioxide aerosols. Moreover, the double tray is better for the capture of sulfur trioxide aerosols. This is because the tray makes the distribution of flue gas uniform, and then the flue gas and the desulfurization slurry can contact each other and react more completely. Therefore, more sulfur trioxide aerosols can be enlarged and removed due to the effect of gravity and desulfurization slurry washing.
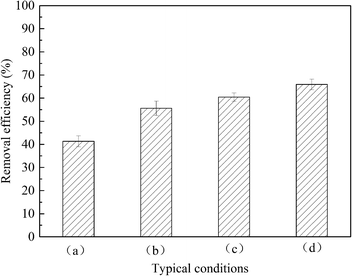 |
| Fig. 10 The removal efficiency of sulfur trioxide aerosols under different typical conditions. | |
3.3 Removal efficiency of the sulfur trioxide aerosols under typical conditions
3.3.1 Influence of the flue gas humidity. The effects of the single tray and double tray on the removal of sulfur trioxide aerosols were investigated separately. Fig. 11 presents the influence of the flue gas relative humidity on the removal efficiency of the sulfur trioxide aerosols. The temperature of the flue gas was set as 80 °C, the temperature of the slurry was 40 °C and the L/G was 15. As the relative humidity shifts from 16% to 32%, the removal efficiency increases from 47.3% to 67.6% with the single tray and 49.6% to 71.4% with the double tray. Previous reports37 have revealed the appropriate supersaturated degree range is from 1.15 to 1.20 for active fine particulate matter and sulfur trioxide aerosols in coal-fired flue gas. When the relative humidity is 16%, the supersaturated environment cannot be established in the desulfurization tower. Thus, as the relative humidity is 16%, the removal efficiency of the sulfur trioxide aerosols is low. As the relative humidity shifts from 16% to 22%, the removal efficiency increases significantly. This is due to the establishment of the supersaturated vapor environment, and thus, sulfur trioxide aerosols are activated and enlarged. When the relative humidity increases, the actual vapor partial pressure increases while the saturated vapor partial pressure is a constant. According to eqn (2), the supersaturation degree increases. Therefore, more small size sulfur trioxide aerosols are nucleated and enlarged, resulting in a higher removal efficiency of the sulfur trioxide aerosols.
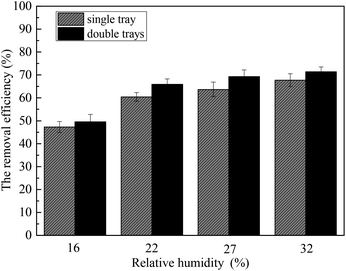 |
| Fig. 11 The influence of the relative humidity to the removal performance of the sulfur trioxide aerosols. | |
3.3.2 Influence of the temperature of flue gas. Fig. 12 shows the influence of the flue gas temperature on the removal efficiency of sulfur trioxide aerosols. In this work, the temperature of the slurry was set as 40 °C, the relative humidity was 22%, and the L/G was 15. It can be seen that the temperature drop of inlet flue gas has a positive influence on the removal efficiency of the sulfur trioxide aerosols. As the temperature shifts from 100 °C to 60 °C, the removal efficiency of the sulfur trioxide aerosols increases from 49.7% to 68.9% with the single tray and increases from 50.6% to 69.4% with the double tray. When the temperature decreases to 80 °C, the removal efficiency significantly increases. In this process, the actual vapor partial pressure increases while the saturated vapor partial pressure remains unchanged, leading to a high supersaturation degree, according to eqn (2). Then, the sulfur trioxide aerosols get activated and grow into lager droplets. Subsequently, the enlarged sulfur trioxide aerosols could be removed more easily using gravity, scrubbing of the desulfurization slurry and defogger. Obviously, the effect of the double tray is better than the single tray. This is because the double tray results in an evenly distributed flue gas. Furthermore, the time of tray holding slurry and the residence time of the flue gas increases, causing sufficient contact and reaction of flue gas with the desulfurization slurry. Additionally, the flue gas bubbling through the desulfurization slurry layer on the tray increases the mass transfer area. Its effect is equivalent to a spray layer. Since the height occupied by a tray in the tower is less than the height occupied by a spray layer, the same desulfurization efficiency can be maintained by adding a layer of porous tray to replace a spray layer. This also can reduce the high of the desulfurization tower and the spray volume of the desulfurization slurry.38 In addition, it can also reduce investment costs.
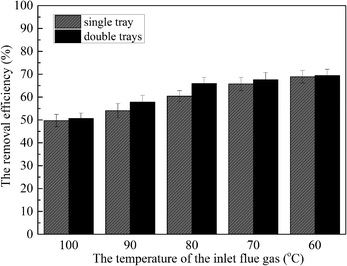 |
| Fig. 12 The influence of the flue gas temperature to the removal efficiency. | |
3.3.3 Influence of the temperature of desulfurization slurry. Fig. 13 presents the influence of the slurry temperature on the removal efficiency of the sulfur trioxide aerosols. In this condition, the temperature of flue gas was set as 80 °C, the relative humidity was 22%, and the L/G was 15. When the temperature of desulfurization slurry shifts from 60 °C to 20 °C, the removal efficiency of sulfur trioxide aerosols increases from 50.1% to 67.6% with a single tray, and from 52.4% to 69.9% with a double tray. In addition, the removal efficiency of the sulfur trioxide aerosols increases as the temperature of the desulfurization slurry reduces. When the temperature of desulfurization slurry decreases, the temperature difference between the desulfurization slurry and flue gas temperature increases, leading to increasing mass transfer and heat transfer between the flue gas and desulfurization slurry. Thus, the water content of the flue gas increases. Simultaneously, the supersaturation degree increases because the actual vapor partial pressure increases, and thus, the saturated vapor partial pressure decreases according to eqn (2). Therefore, the nucleation number of the sulfur trioxide aerosols increases (see in Fig. 3), and the condensation rate increases,39 resulting in the increasing of the removal efficiency. In addition, the removal efficiency of the sulfur trioxide aerosols is higher with the double tray than that with the single tray. This is because the flue gas retention time and the holding desulfurization slurry time of the tray increase, promoting the contact and reaction of flue gas and desulfurization slurry to completion.
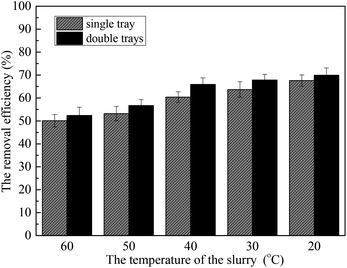 |
| Fig. 13 The influence of the slurry temperature to the removal efficiency. | |
3.3.4 Influence of the L/G. Fig. 14 presents the influence of the ratio of the liquid to gas (L/G) on the removal efficiency of the sulfur trioxide aerosols. The temperature of flue gas temperature was set as 80 °C, the temperature of the slurry was 40 °C, and the relative humidity was 22%. As seen in Fig. 14, the removal efficiency of the sulfur trioxide aerosols increases from 49.3% to 65.7% with the single tray and increases from 51.2% to 69.4% with the double tray when the ratio of the liquid to gas (L/G) increases from 5 to 20. The increase of the L/G means there is more desulfurization slurry with the flue gas flow rate constant, and thus the temperature drop increases. In this process, the mass and heat transfer between flue gas and desulfurization slurry is enhanced. For constant actual water pressure, the saturated water pressure decreases, causing a higher supersaturation degree in the desulfurization tower. Then, more sulfur trioxide aerosols are activated, and the condensation rate is increased. Thus, the sulfur trioxide aerosols that condensed into large particle sizes are more easily removed. Generally, the spray density near the tower wall is low, and thus, the desulfurization slurry has a poor washing effect on the flue gas. The tray can improve the uniform distribution of flue gas in the tower. Therefore, it can be concluded that the optimum values of the L/G, relative humidity and slurry temperature are 20, 32%, and 20 °C, respectively.
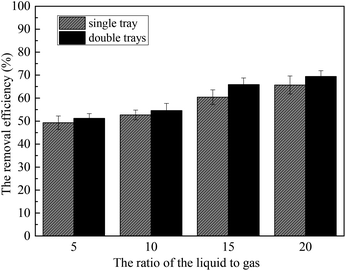 |
| Fig. 14 The influence of L/G to the reduction efficiency. | |
4. Conclusions
This paper mainly studied the removal performance of sulfur trioxide aerosols based on heterogeneous condensation in the wet flue gas desulfurization process, and the promoting effect of the deflectors tray on the reduction of sulfur trioxide aerosols. The results show that when sulfur trioxide aerosol sizes are larger, the sulfur trioxide aerosols critical supersaturation degree is lower. Further, heterogeneous condensation can effectively promote the removal of sulfur trioxide aerosols. The size of the sulfur trioxide aerosols increases to higher values under heterogeneous condensation. Simultaneously, the number concentration of the sulfur trioxide aerosols with sizes <0.1 μm decreases, while the number concentration of sizes >0.1 μm increases. Moreover, lower temperature, lower desulfurization slurry and higher L/G are beneficial to the removal of sulfur trioxide aerosols. The relative humidity of the flue gas is likely to be the most influential in the formation of a supersaturated environment and the removal of the sulfur trioxide aerosols. Additionally, the tray results in an evenly distributed flue gas that increases the residence time of the flue gas in the desulfurization tower and the holding time of the desulfurization slurry, and promotes sufficient contact and reaction between the flue gas and the desulfurization slurry. Heterogeneous condensation could improve the removal efficiency of sulfur trioxide aerosols by 14.3%, and the installation of a tray can efficiency improve the removal of sulfur trioxide aerosols by 21.4%.
Conflicts of interest
There are no conflicts to declare.
Acknowledgements
This work was supported by the National Key R&D Plan (2016YFB0600602) and the Postgraduate Research & Practice Innovation Program of Jiangsu Province (KYCX18_0090).
References
- Z. Yang, P. Ji, Q. Li, Y. Jiang, C. Zheng, Y. Wang, X. Gao and R. Lin, J. Cleaner Prod., 2019, 239, 118096 CrossRef CAS.
- D. Pan, C. Gu, D. Zhang and F. Zeng, Energy Fuels, 2019, 33, 7813–7818 CrossRef CAS.
- C. Zheng, Y. Wang, Y. Liu, Z. Yang, R. Qu, D. Ye, C. Liang, S. Liu and X. Gao, Fuel, 2019, 241, 327–346 CrossRef CAS.
- Y. Cao, H. Zhou, W. Jiang, C. Chen and W. Pan, Environ. Sci. Technol., 2010, 44, 3429–3434 CrossRef CAS.
- P. Paasonen, T. Nieminen, E. Asmi, H. E. Manninen, T. Petäjä, C. Plass-Dülmer, H. Flentje, W. Birmili, A. Wiedensohler, U. Hõrrak, A. Metzger, A. Hamed, A. Laaksonen, M. C. Facchini, V.-M. Kerminen and M. Kulmala, Atmos. Chem. Phys., 2012, 10, 11223–11242 CrossRef.
- Y. Sarbassov, L. Duan, V. Manovic and E. J. Anthony, Greenhouse Gases: Sci. Technol., 2018, 8, 402–428 CrossRef CAS.
- L. Brachert, T. Kochenburger and K. Schaber, Aerosol Sci. Technol., 2013, 47, 1083–1091 CrossRef CAS.
- C. A. Brown and P. A. Hohne, Environ. Prog., 2001, 20, 182–186 CrossRef CAS.
- A. Wix, L. Brachert, S. Sinanis and K. Schaber, J. Aerosol Sci., 2010, 41, 1066–1079 CrossRef CAS.
- J. Yang, L. Li, S. Wang, H. Li, J. S. Francisco, X. C. Zeng and Y. Gao, J. Am. Chem. Soc., 2019, 141, 19312–19320 CrossRef CAS.
- L. Brachert, T. Kochenburger and K. Schaber, Aerosol Sci. Technol., 2013, 47, 1083–1091 CrossRef CAS.
- F. Sheng, L. Jingjing, C. Yu, T. Fu-Ming, D. Xuemei and L. Jing-yao, RSC Adv., 2018, 8, 7988–7996 RSC.
- W. Chen, H. Hu, Q. Cai and S. Zhang, Energy Fuels, 2020, 34, 2238–2245 CrossRef CAS.
- K. D. Good and J. M. VanBriesen, Environ. Sci. Technol., 2019, 53, 213–223 CrossRef CAS.
- S. Yao, S. Cheng, J. Li, H. Zhang, J. Jia and X. Sun, J. Environ. Sci., 2019, 77, 32–42 CrossRef.
- J. Y. Huang, F. Zhang, Y. J. Shi, X. Q. Dang, H. Zhang, Y. Shu, S. Deng and Y. Liu, J. Aerosol Sci., 2016, 100, 38–52 CrossRef CAS.
- Q. Wu, M. Gu, Y. Du and H. Zeng, R. Soc. Open Sci., 2019, 6, 144–151 Search PubMed.
- L. Brachert, J. Mertens, P. Khakharia and K. Schaber, J. Aerosol Sci., 2014, 67, 21–27 CrossRef CAS.
- M. Ostrycharczyk, K. Krochmalny, M. Czerep, H. Pawlak-Kruczek, J. Zgóra and M. Baranowski, Fuel, 2019, 241, 579–584 CrossRef CAS.
- S. Sarkar, B. K. Oram and B. Bandyopadhyay, J. Phys. Chem. A, 2019, 123, 3131–3141 CrossRef CAS.
- X. Wang, X. Liu, D. Li, Y. Zhang and M. Xu, Int. J. Greenhouse Gas Control, 2015, 43, 1–9 CrossRef.
- M. Qing, S. Su, L. Wang, L. Liu, Z. Sun, M. E. Mostafa, K. Xu, S. Hu, Y. Wang and J. Xiang, Fuel, 2019, 237, 545–554 CrossRef CAS.
- W. Buckley and B. Altshuler, Power Eng., 2002, 11, 132–136 Search PubMed.
- Z. Qi, J. Li, D. Wu, W. Xie, X. Li and C. Liu, Energy Fuels, 2017, 31, 1741–1746 CrossRef CAS.
- C. A. Brown and P. A. Hohne, Environ. Prog., 2001, 20, 182–186 CrossRef CAS.
- B. Hu, Y. Liu, F. Ren, D. Pan, Z. Yuan and L. Yang, Proceedings of the CSEE, 2016 Search PubMed.
- Z. Yang, C. Zheng, X. Zhang, H. Zhou, A. A. Silva, C. T. Liu, B. Snyder, Y. Wang and X. Gao, Fuel, 2018, 217, 597–604 CrossRef CAS.
- H. Wu, D. Pan, G. Hong, Y. Jiang, L. Yang, B. Yang and Z. Peng, J. Chem. Technol. Biotechnol., 2016, 92, 1026–1034 CrossRef.
- N. H. Fletcher, The Physics of Rainclouds, Cambridge University Press, Cambridge, 1966; J. Chem. Phys., 1958, 29, 572–576 Search PubMed.
- S. R. Rich and T. G. Pantazelos, J. Air Pollut. Control Assoc., 1974, 24, 952–954 CrossRef.
- J. Yan, J. Bao, L. Yang, F. Fan and X. Shen, J. Aerosol Sci., 2011, 42, 604–614 CrossRef CAS.
- J. Bao, L. Yang and J. Yan, Chin. J. Chem., 2010, 27, 2242–2248 CrossRef.
- D. Pan, L. Yang, H. Wu and R. Huang, J. Air Waste Manage. Assoc., 2017, 67, 352–357 CrossRef CAS.
- J. Cheney and J. Homolya, Characterization of combustion source sulfate emissions with a selective condensation sampling system, Environmental Protection Agency Industrial Environmental Research Laboratory, Washington, 1978 Search PubMed.
- A. G. Okkes, Hydrocarbon Process., 1987, 66, 53–55 CAS.
- S. Heidenreich, U. Vogt, H. Büttner and F. Ebert, Chem. Eng. Sci., 2000, 55, 2895–2905 CrossRef CAS.
- L. Yang, J. Bao, J. Yan, J. Liu, S. Song and F. Fan, Chem. Eng. J., 2010, 156, 25–32 CrossRef CAS.
- G. Li, S. Li, Q. Huang and Q. Yao, Fuel, 2015, 143, 430–437 CrossRef CAS.
- G. Dreyfuss, M. S. Swanson and S. Pinol-Roma, Trends Biochem. Sci., 1988, 13, 86–91 CrossRef CAS.
|
This journal is © The Royal Society of Chemistry 2020 |
Click here to see how this site uses Cookies. View our privacy policy here.