DOI:
10.1039/D0RA06409B
(Paper)
RSC Adv., 2020,
10, 33747-33752
A strategy towards the synthesis of superhydrophobic/superoleophilic non-fluorinated polypyrrole nanotubes for oil–water separation†
Received
23rd July 2020
, Accepted 29th August 2020
First published on 11th September 2020
Abstract
Superhydrophobic/superoleophilic materials have shown great potential for applications in oil/water separation. However, practical applications of these materials are restricted due to their toxicity and complicated, expensive, and non-eco-friendly fabrication procedures. Here, we have successfully developed an easy, simple, cost-effective, and environmentally friendly strategy towards the synthesis of superhydrophobic and superoleophilic porous polypyrrole nanotubes. Such wettability has been introduced into polypyrrole by co-doping with sodium dodecylbenzenesulfonate, a surfactant for lowering surface energy and controlling the morphology of the nanotubes. These non toxic and environment friendly polymer nanotubes exhibit oil absorption capability from oil/water mixtures with a reasonable efficiency with good reusability.
Introduction
Accidental oil spillages constitute a significant source to pollute and imbalance the marine ecosystem.1,2 Oil spill or leakage frequently occurs during exploration in the sea, transportation through pipelines or tankers by the sea, storage of oil, and from industrial waste-oil discharge.3 The gravity of oil spills to marine water could be understood from the 1989 Exxon Valdez oil spill (EVOS) which had disastrous consequences.4 Therefore, effective and efficient oil remediation is needed to save marine ecology.5–10
Many conventional techniques are used for oil/water separation, including booms, skimming, oil burning etc.5,6,12 These energy intensive and time-consuming techniques have issues of inefficient separation and secondary pollutants. For example, use of oil booms requires a water velocity of less than 1 knot.1,6,9,12 Similarly, the skimming of oil from water requires vacuum pumps, relatively calm water, and chemical surfactants that are harmful to the marine ecosystem.6,9,12 Therefore, to overcome these shortcomings, many new materials or techniques have been explored.
Recently, bioinspired superhydrophobic/superoleophilic (SHSO) materials have attracted significant interest in oil/water separation owing to their unique surface wettability properties of having an extremely high water contact angle (CA) > 150°, and very low oil CA < 10°.5,6,12 When SHSO materials are dipped in an oil–water mixture, oil permeates easily through these but water is rejected at the surface. In addition, these materials also have advantages of self-cleaning, corrosion resistance, anti-fouling, anti-bacterial, and UV resistance etc.5–16
These special materials are synthesized by making hierarchal micro or nano structures such as nanotubes/nanofibers. The air could get trapped in such structures, which contributes to increasing water contact angle or hydrophobicity.17,18 The contact angle can further be increased by coating with low surface energy materials.17 Based on these properties, filters or oil absorbers have been developed using various porous materials, which include membranes, polymer fibers, metal mess cloths, cotton hydrogels/aerogels, and sponges, etc.5,6,12,13,19,20 The membranes are used to separate oil from oil/water mixture by filtration, making the process efficient, simple, and cost-effective.5,12 On the other hand, polymer nanofibers are used as sorbents which separate water by selectively absorbing/adsorbing oil from the oil/water mixture. These sorption characteristics of polymer nanofibers arise from: (a) superoleophilic and superhydrophobic properties of the fibers, (b) the porosity of the fibers (for retaining oil), and (c) capillary effect/adsorption by the fibers (for oil absorption).13 The absorbed oil can be collected by squeezing, solvent extraction, or centrifugation. For oil spillage in open water systems where collection of contaminated water is difficult, such oil sorbents are applied by hand on the polluted water.7,12,13,20
The fabrication processes of these superhydrophobic materials are complex, time-consuming, and require sophisticated instruments.13,16,20 Therefore, quest for a cheaper, efficient, reusable, and environment friendly oil–water separator is a need of the time, and new strategies need to be devised for fabrication of SHSO materials.7,16
Synthesis of nano/microtubes or fibers of conjugated polymer materials could be a prospective option. These nanofibers can be cost-effectively synthesized by chemical methods using predesigned templates (porous alumina) or soft template method, where self-assembled nanostructures of organic molecules, surfactants, and dyes act as templates.21–23 The specialty of this class of polymers is that the positive charges are delocalized in the conjugated system counterbalanced by anions called dopants. The wettability properties of such polymers can be tuned by dopants, for illustration, perfluorinated doped polypyrrole (PPy) is hydrophobic whereas ClO4− doped PPy is hydrophilic.24 Since these polymers are conducting polymers, studies of their hydrophobic properties were mainly focused for electrical, opto-electrical, and sensors applications.24–27 However, conjugated polymers such as polyaniline, polythiophene, and polypyrrole are hardly explored exclusively for oil–water separation despite their potential for the same.
Here, we are reporting the strategy for the synthesis of superhydrophobic/superoleophilic polypyrrole (PPy) nanotubes network for separating oil from water and the collection of the separated oil efficiently. The objectives of present work are: (1) to develop a cost-effective environmentally friendly method for synthesizing conjugated polymer nanotube networks similar to polymer nanofibers, (2) synthesized polymer should be self-standing, which could be spread in the open area and collected easily, and (3) the polymer should be environment friendly. For this purpose, polypyrrole is a suitable candidate as it is biocompatible and can be easily synthesized from monomers with varying morphologies by chemical oxidation.22,23,28–32 We followed the ferric chloride-methyl orange soft template method for synthesizing polypyrrole (PPy) nanotubes.22 The PPy was co-doped with a surfactant, sodium dodecylbenzenesulfonate (SDBS) to enhance hydrophobicity and control its morphology. The surface wettability properties of these PPy–SDBS co-doped nanotubes networks were studied. These nanotubes were utilized for oil/water separation and exhibited a robust absorption capacity, reusability, and retrievability of absorbate.
Experimental
Materials
Pyrrole (Sigma-Aldrich, reagent-grade 98%) was vacuum distilled and stored at 4 °C. Sodium dodecylbenzenesulfonate (SDBS) (Sigma-Aldrich, technical-grade), ferric chloride (FeCl3) (Thomas Baker, Anhydrous, AR grade), methyl orange (Sigma-Aldrich, ACS reagent, dye content, 85%) were used as purchased.
Method
Polypyrrole (PPy) nanotubes were synthesized using ferric chloride–methyl orange template method with SDBS as a co-dopant at room temperature. For this, 5 mM of methyl orange aqueous (50 ml) solution was prepared in a beaker. To this, ferric chloride (0.406 g) was added under constant stirring. After 10 minutes, 17.4 mg of SDBS was added under continuous stirring followed by drop wise addition of 170 μl of pyrrole. After 2 hours, the reaction was stopped, and PPy powder was obtained by filtration. The PPy powder was washed with deionized water and ethanol. After drying at 50–55 °C for 30 minutes and PPy flakes were obtained by peeling off from the filter paper. Fig. 1 shows the schematic of the experimental procedure for synthesizing PPy nanotubes.
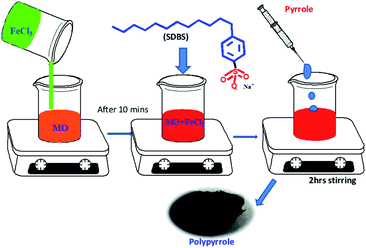 |
| Fig. 1 The schematic of the experimental steps involved and the photograph of the synthesized polypyrrole. | |
Characterization
Fourier transform infrared (FTIR) spectra of the PPy were recorded in reflection mode using 80 V Bruker FTIR Spectrophotometer. The surface wettability properties of the polymer were investigated by measuring the water contact angle (WCA) using OCA 200 of Data Physics. The surface morphology of synthesized PPy was studied by field emission scanning electron micrographs (Zeiss make).
Oil–water separation
For oil–water separation studies, the flakes were crushed to powder and spread on the hexane/water mixture. To make two layers distinctly visible BODIPY dye was added to the hexane layer for coloration. For studying the retrievability, hexane-absorbed polymer was heated in a sealed bottle, which contained an empty tube for collecting the evaporated hexane. The oil absorption capacity was evaluated by saturating the known amount of polymer with hexane.
Results and discussion
Synthesis and characterization of the polypyrrole nanotubes
Our strategy is inspired by superhydrophobic properties shown by polymer nanofibers or carbon nanotubes functionalized with low surface energy materials such as fluorinated silane, PTFE.17,20 Thus, in present work, we replicated this carbon nanotube/nanofiber design by choosing polypyrrole nanotubes doped with SDBS. The choice of SDBS, a non-fluoro compound with a long hydrophobic alkyl chain, was made to use it as a low surface energy material to increase the hydrophobicity of PPy.33 Moreover, SDBS is one of the important surfactants used in oil/water separation.34 For synthesizing polypyrrole nanotubes, we adopted a soft template method in which ferric chloride–methyl orange (FeCl3–MO) template was used. The formation of PPy nanotubes using this soft template is well reported.22,31,32 Our group also reported the synthesis of polypyrrole acicular nanorods using ferric chloride–methyl orange template.30 Thus, the mechanism of the formation of nanotubes is briefly described in two steps. Under first step, FeCl3–MO nanorods are prepared for templates, and in second step, pyrrole gets polymerized by ferric chloride present in the template during which ferric ions convert to ferrous ions resulting in the decomposition of the template. Therefore, the polymerized pyrrole replicates the template structure resulting in polypyrrole nanotubes, which is obtained after washing the decomposed templates. The absence of the template in PPy is confirmed from the missing –N
N– stretching vibration at 1608 cm−1 in the FTIR spectra of PPy, as shown in Fig. 2.35 The formation of PPy is confirmed from its characteristics vibrations such as the anti-symmetric and symmetric pyrrole ring C
C stretching vibrations at 1581 cm−1 and 1482 cm−1, C–N stretching vibration at 1448 cm−1, C–H deformation vibrations at 1240 cm−1 and 1059 cm−1, and ring bending vibrations at 948cm−1and 979 cm−1.36–38 The band from 1300 cm−1 to 1440 cm−1 is assigned to C–N and C–H in-plane deformation vibration modes.39 The band at 1604 cm−1 and 1490 cm−1 are attributed to aryl C
C anti-symmetric and symmetric stretching and 693 cm−1 to –SO3− bending vibration modes of dodecylbenzenesulfonate and corresponded to doping state of PPy.36,37,40
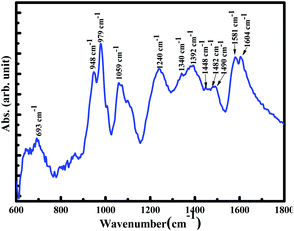 |
| Fig. 2 FTIR spectra of polypyrrole showing the characteristics vibration bands in the spectra. | |
Surface morphology
The surface morphologies of PPy doped with SDBS were studied by field emission scanning electron microscope (FESEM). Fig. 3(a) shows nanotube-like structures that are uniformly distributed and are interconnected to make porous structures. These tubes have an average length of 4.5 ± 0.2 μm and diameters of 200 ± 50 nm. The high-magnified SEM images show small branches or initiation of branching as dots that increase the roughness of the tubes (inset of Fig. 3(a)). Such 3D nanoporous structures are reported for polymer nanofibers synthesized by electrospinning technique, which we could get using a simple soft template method.13,20 We also studied the effect of concentration of SDBS on the morphology of the PPy. Broadly, the morphology has tubular-structure for PPy with or without SDBS as expected due to the template effect (Fig. 3(a)–(c)). Besides, the variation of the concentration of SDBS from 1 mM to 5 mM does not affect the morphology significantly, as shown in Fig. 3(a) and (b), respectively. However, the variation in morphology is observed for PPy without SDBS, where the length of nanotubes (10 ± 0.1 μm) and their diameters (500 ± 50 nm) get doubled as compared to SDBS doped PPy (Fig. 3(c)).Consequently, its morphology appears more compact and less porous than that for the SDBS doped PPy.
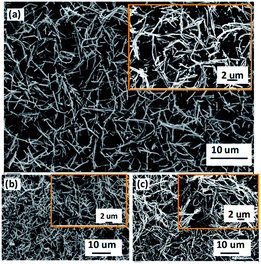 |
| Fig. 3 SEM images of the PPy flakes with different doping concentration (a) 1 mM, (b) 5 mm of SDBS, and (c) without SDBS. The insets show the magnified images. | |
These morphological studies suggest that the presence of SDBS affects the extent of polymerization and agglomeration of PPy nanotubes. Thus, the SDBS acts as a stabilizer for the PPy nanotubes, which could be explained as follows. During doping of SDBS, its anionic part (sulphonate group) along with Cl− generated during the reduction of FeCl3 act as counter ions for polarons present in the oxidized PPy, and the tail part (alkyl chain) lies away from the polymer chain as schematically shown in Fig. 4(a). After a certain doping concentration of SDBS, the presence of the long alkyl chains (C12) around PPy becomes prominent. Then these SDBS chains prevent the monomer from approaching the polymerization sites. Thus, this causes the termination of chain propagation, which leads to small polymer tubes (Fig. 4(a)). Similarly, the presence of long alkyl chain prevents nanotubes from getting agglomerated (Fig. 4(b)). Such steric effects are not present in the PPy without SDBS causing chain propagation and agglomeration, as shown schematically in Fig. 4(c). In this case, only Cl− acts as the counter ion for polaron present in the PPy. Moreover, the reduced diameter for PPy polymerized tubes in the presence of SDBS may be attributed to partial dissolution of FeCl3–MO nanorod template on the addition of SDBS.41
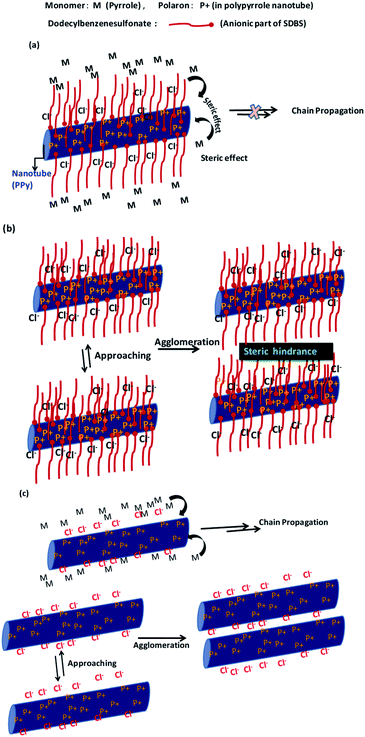 |
| Fig. 4 Schematic representation of the effect of concentration of SDBS on morphology of PPy with SDBS causes (a) termination of chain propagation and (b) agglomeration. (c) Without SDBS causing chain propagation and agglomeration. In situ chloride (Cl−) doping arises from the reduction ferric chloride to ferrous chloride during oxidation of pyrrole. | |
Contact angle measurement
The surface wettability of synthesized PPy film was evaluated by the water contact angle (WCA) and oil contact angle (OCA). As shown in Fig. 5, the water drops on PPy are perfectly spherical with water contact angle (WCA) 157° ± 5°confirming its superhydrophobic nature. When a drop of hexane was placed on PPy, the organic drop was immediately absorbed, exhibiting excellent superoleophilicity. We also carried out a control experiment in which PPy was synthesized without SDBS as dopants. Such polymer was found to be hydrophilic possessing low WCA, although they have nanotube structure. The effect of concentration of SDBS (1 mM and 5 mM) was also studied on the wettability of PPy, and found to be superhydrophobic. These results suggest that the presence of SDBS alters the morphology of PPy as discussed above and also lowers the surface energy of the PPy. Since these qualities of the PPy nanotube doped SDBS match with superhydrophobic oil/water separators, this polymer should be useful for oil recovery.
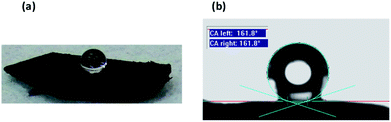 |
| Fig. 5 Optical images of (a) water droplet on PPy flakes doped with SDBS and (b) water contact angles (161.8°) measurement. | |
Oil/water separation and absorption
For exploring its actual potential in oil/water separation, a model system of hexane/water mixture was chosen. Owing to lower density, the hexane layer floats over the water layer. The hexane was also dyed with BODIPY so that two distinct layers of water and oil are visible (Fig. 6(a)). When the powder of SDBS co-doped PPy was added in the liquid mixture, the colored layer was absorbed by PPy powder within a few seconds, as seen in Fig. 6(b) and (c). The mixture was then filtered, and the filtrate did not show any coloration, confirming the total separation of hexane (Fig. 6(d)). Since surfactants are generally used to remove slick oil from the water, we explored further the possibility to remove the thin oil layer from water using PPy nanotubes. For this, in a similar fashion a few drops of hexane were spread on the surface of the water, and then the nanotubes were added (Fig. 7(a)–(c)). Within a few seconds, this polymer absorbed the colored layer (hexane) leaving behind the colorless water, as shown in the photographs (Fig. 7). No polymer powder was observed in the water layer, owing to its superphydrophobic nature. These results confirm the good oil absorption and separation properties of SDBS co-doped PPy.
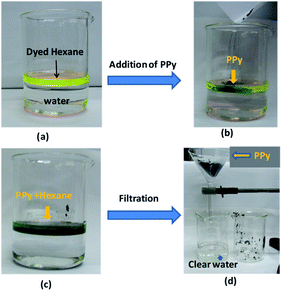 |
| Fig. 6 Photographs of (a) water hexane mixture, (b) and (c) the addition PPy nanotubes and PPy nanotubes + hexane layer, and (d) filtration. The BODIPY dye was added for coloration of hexane layer. | |
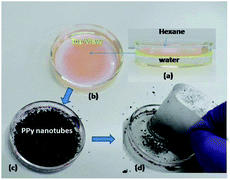 |
| Fig. 7 Photographic images of thin layer of hexane (dyed with BODIPY) on water (a) side view and (b) top view; (c) PPy naotubes on the hexane layer, and (d) after absorption hexane layer (disappearance of color) by PPy. | |
The absorption capacity of PPy was calculated using eqn (1),
| 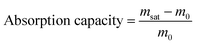 | (1) |
where,
m0 and
msat represent the polymer before and after saturation by oil.
The absorption capacity was found to be 8 g g−1. The measured absorption capacity of PPy is comparable to other reported absorbents for hexane viz. polypropylene sponges (∼8g g−1),42 polypropylene aerogel material (3–5 g g−1).28
Further, absorbate retrievability and recyclability were also studied as these are important attributes for an ideal absorber.7,12,15Fig. 8 shows the retrieved hexane in a tube, obtained from hexane absorbed PPy nanotubes powder after heating at 70 °C. This low retrieval temperature indicates very weak interactions between hexane and PPy network, making it a low energy process. The powder was reused to absorb hexane for 10 cycles and exhibited consistent repeatability. As far as hexane retrievability is concerned, very little difference (<0.5%) was observed between 1st and 10th cycle. These results clearly demonstrate that the hexane was stored in voids and nanotubes. The morphology of PPy after retrieving the hexane was also investigated. However, surface morphographs of the used PPy were found the same as before the oil/water separation (Fig. S1†). This study confirmed robust reversibility in absorption/retrieval and, therefore a good reusability of PPy for oil/water separation applications.
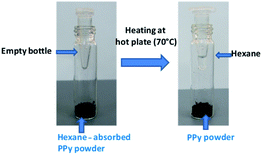 |
| Fig. 8 The photographs showing the collection of hexane by heating the absorbed PPy powder. The empty tube was perforated to collect the condensed hexane. | |
Although the absorption capacity of PPy is less than the commonly used oil absorbers like sponges, hydrogel aerogel, polypropylene/PVC nanofibers, these absorbers require complex, expensive fabrication process and also these are not environmentally friendly.7,10 In contrast, PPy is freestanding and does not require any additional support material. The preparation method discussed in this paper is simple and easy, and the raw as well as product materials, are environmentally friendly and cheaper, making the process cost-effective. Therefore, these many advantages of PPy compensate for its limitation in the present absorption capacity and place it in the league of many options available for cleaning oil spills.
Conclusions
In conclusion, we have successfully demonstrated a strategy for synthesizing superhydrophobic and superoleophilic conjugated polymers by tuning the dopants for oil–water separation and absorption. For this purpose, we have synthesized superhydrophobic polypyrrole nanotubes co-doped with SDBS, a surfactant using an easy and cost-effective soft template method. It is proposed that the wettability properties of the polypyrrole arise due to SDBS, which acts as a stabilizer for nanotubes and lowers their surface energy. This environment-friendly and non-toxic polymer was tested for the oil/water separation and showed a reasonable efficiency with good reusability.
Thus, in this paper, the potential of PPy nanotube doped with surfactants is demonstrated as a probable contender for the application in oil/water separation. These results will also inspire synthesis of conjugated polymer nanofibers doped with different surfactants using soft template methods for oil/water separation.
Conflicts of interest
There are no conflicts to declare.
References
-
M. Fingas, The Basics of Oil Spill Cleanup, Lewis Publishers, 2012 Search PubMed.
-
M. Fingas, Handbook of Oil Spill Science and Technology, 2015 Search PubMed.
- H. Wang, E. Wang, Z. Liu, D. Gao, R. Yuan, L. Sun and Y. Zhu, J. Mater. Chem. A, 2015, 3, 266–273 RSC.
-
Facts on File, Environmental disasters: The Exxon Valdez Oil Spill, 2005 Search PubMed.
-
(a) T. A. Saleh, N. Baig, F. I. Alghunaimi and N. W. Aljuryyed, RSC Adv., 2020, 10, 5088–5097 RSC;
(b) W. Ma, Y. Li, M. Zhang, S. Gao, J. Cui, C. Huang and G. Fu, ACS Appl. Mater. Interfaces, 2020, 12, 34999 CrossRef CAS PubMed;
(c) H. Zhang, Y. Shen, M. Li, G. Zhu, H. Feng and J. Li, ACS Sustain. Chem. Eng., 2019, 7, 10880 CrossRef CAS;
(d) W. Ma, Y. Ding, M. Zhang, S. Gao, Y. Li, C. Huang and G. Fu, J. Hazard. Mater., 2020, 384, 121476 CrossRef CAS.
-
(a) W. Barthlott, M. Moosmann, I. Noll, M. Akdere, J. Wagner, N. Roling, L. Koepchen-Thomä, M. A. K. Azad, K. Klopp, T. Gries and M. Mail, Philos. Trans. R. Soc., A, 2020, 378, 201904 CrossRef;
(b) M. Zhang, W. Ma, J. Cui, S. Wu, J. Han, Y. Zou and C. Huang, J. Hazard. Mater., 2020, 383, 121152 CrossRef CAS;
(c) X. Bai, Y. Shen, H. Tian, Y. Yang, H. Feng and J. Li, Sep. Purif. Technol., 2019, 210, 402 CrossRef CAS.
- A. T. Abdulhussein, G. K. Kannarpady and A. S. Biris, npj Clean Water, 2019, 2, 10 CrossRef CAS.
- X. Cui, H. Shao, Y. Song, S. Yang, F. Wang and H. Liu, RSC Adv., 2019, 9, 25730 RSC.
- B. Bhushan, Philos. Trans. R. Soc., A, 2019, 377, 201901 Search PubMed.
- Y. Guan, F. Cheng and Z. Pan, Polymers, 2019, 11, 806 CrossRef CAS.
- S. Yu and Z. Guo, RSC Adv., 2015, 5, 107880 RSC.
-
(a) R. K. Gupta, G. J. Dunderdale, M. W. England and A. Hozumi, J. Mater. Chem. A, 2017, 5, 16025 RSC;
(b) M. Zhang, W. Ma, S. Wu, G. Tang, J. Cui, Q. Zhang, F. Chen, R. Xiong and C. Huang, J. Colloid Interface Sci., 2019, 547, 136 CrossRef CAS PubMed.
-
(a) R. Sarbatly, D. Krishnaiah and Z. Kamin, Mar. Pollut. Bull., 2016, 106, 8 CrossRef CAS;
(b) H. Zhu, S. Qiu, W. Jiang, D. Wu and C. Zhang, Environ. Sci. Technol., 2011, 45, 4527 CrossRef CAS PubMed.
- M. Qu, L. Ma, Y. Zhou, Y. Zhao, J. Wang, Y. Zhang, X. Zhu, X. Liu and J. He, ACS Appl. Nano Mater., 2018, 1, 5197 CrossRef CAS.
- J. Yong, F. Chen, J. Huo, Y. Fang, Q. Yang, H. Bian, W. Li, Y. Wei, Y. Dai and X. Hou, ACS Omega, 2018, 3, 1395 CrossRef CAS.
-
(a) Z. H. Zhang, H. J. Wang, Y. H. Liang, X. J. Li, L. Q. Ren, Z. Q. Cui and C. Luo, Sci. Rep., 2018, 8, 1 Search PubMed;
(b) W. Ma, M. Zhang, Y. Li, M. Kang, C. Huang and G. Fu, Environ. Sci. Nano, 2019, 6, 3699 RSC.
- K. K. S. Lau, J. Bico, K. B. K. Teo, M. Chhowalla, G. A. J. Amaratunga, W. I. Milne, G. H. McKinley and K. K. Gleason, Nano Lett., 2003, 3, 1701 CrossRef CAS.
- J. Bico, C. Marzolin and D. Quéré, Europhys. Lett., 1999, 47, 220 CrossRef CAS.
- P. Yi, H. Hu, W. Sui, H. Zhang, Y. Lin and G. Li, ACS Appl. Polym. Mater., 2020, 2, 1764 CrossRef CAS.
- W. Ma, Q. Zhang, D. Hua, R. Xiong, J. Zhao, W. Rao, S. Huang, X. Zhan, F. Chen and C. Huang, RSC Adv., 2016, 6, 12868 RSC.
- J. Liu, T. Yang, D. W. Wang, G. Q. Lu, D. Zhao and S. Z. Qiao, Nat. Commun., 2013, 4, 1 Search PubMed.
- X. Yang, Z. Zhu, T. Dai and Y. Lu, Macromol. Rapid Commun., 2005, 26, 1736 CrossRef CAS.
- L. Pan, H. Qiu, C. Dou, Y. Li, L. Pu, J. Xu and Y. Shi, Int. J. Mol. Sci., 2010, 11, 2636 CrossRef CAS PubMed.
- L. Xu, W. Chen, A. Mulchandani and Y. Yan, Angew. Chem. Int. Ed., 2005, 44, 6009 CrossRef CAS PubMed.
- Y. Zhu, L. Feng, F. Xia, J. Zhai, M. Wan and L. Jiang, Macromol. Rapid Commun., 2007, 28, 1135 CrossRef CAS.
- Y. Zhu, J. Zhang, Y. Zheng, Z. Huang, L. Feng and L. Jiang, Adv. Funct. Mater., 2006, 16, 568 CrossRef CAS.
- X. Wang, B. Ding, J. Yu and M. Wang, Nano Today, 2011, 6, 510 CrossRef CAS.
- X. H. Lang, T. Y. Zhu, L. Zou, K. Prakashan and Z. X. Zhang, Prog. Org. Coating, 2019, 137, 105370 CrossRef CAS.
- Z. B. Huang, G. F. Yin, X. M. Liao and J. W. Gu, Front. Mater. Sci., 2014, 8, 39 CrossRef.
- P. Jha, P. Veerender, S. P. Koiry, C. Sridevi, A. K. Chauhan, K. P. Muthe and S. C. Gadkari, Polym. Adv. Technol., 2018, 29, 401 CrossRef CAS.
- J. Kopecká, D. Kopecký, M. Vrňata, P. Fitl, J. Stejskal, M. Trchová, P. Bober, Z. Morávková, J. Prokeš and I. Sapurina, RSC Adv., 2014, 4, 1551 RSC.
- Ishpal and A. Kaur, J. Appl. Phys., 2013, 113, 094504 CrossRef.
- A. J. Queimada, I. M. Marrucho and J. A. P. Coutinho, Fluid Phase Equilib., 2001, 183–184, 229 CrossRef CAS.
- C. Negin, S. Ali and Q. Xie, Petroleum, 2017, 3, 197 CrossRef.
- D. C. Kalyani, A. A. Telke, S. P. Govindwar and J. P. Jadhav, Water Environ. Res., 2009, 81, 298 CrossRef CAS.
- L. C. Scienza and G. E. Thompson, Polímeros, 2001, 11, 142 CrossRef CAS.
- R. G. Davidson and T. G. Turner, Synth. Met., 1995, 72, 121 CrossRef CAS.
- B. Tian and G. Zerbi, J. Chem. Phys., 1990, 92, 3886 CrossRef CAS.
- J. John, P. Saheeda, K. Sabeera and S. Jayalekshmi, Mater. Today: Proc., 2018, 5, 21140 CAS.
- Z. P. Xu and P. S. Braterman, J. Mater. Chem., 2003, 13, 268 RSC.
- T. Dai, X. Yang and Y. Lu, Nanotechnology, 2006, 17, 3028 CrossRef CAS.
- G. Wang and H. Uyama, Sci. Rep., 2016, 6, 1 CrossRef.
Footnote |
† Electronic supplementary information (ESI) available. See DOI: 10.1039/d0ra06409b |
|
This journal is © The Royal Society of Chemistry 2020 |
Click here to see how this site uses Cookies. View our privacy policy here.