High-performance rechargeable zinc-based dual-ion batteries†
Received
3rd September 2019
, Accepted 6th October 2019
First published on 15th October 2019
Abstract
Zinc-ion batteries (ZIBs) are promising candidates for large-scale energy storage applications due to the large abundance, low toxicity, and low cost of zinc. In this work, we configured a zinc-based nonaqueous dual-ion battery (ZDIB) for the first time by using an expanded graphite cathode, a zinc foil anode, and an ionic liquid (IL) electrolyte. The adoption of the IL suppressed the dendritic growth of zinc and avoided hydrogen evolution, resulting in satisfactory safety of the battery. Notably, the prepared ZDIB delivered a reversible discharge capacity of 57 mA h g−1 and a capacity retention of ∼86% after 500 cycles. In addition, we developed a nonaqueous battery with a dual-carbon configuration (ZDCB), exhibiting a reversible discharge capacity of 58 mA h g−1 and a capacity retention of ∼88% after 500 cycles. These two kinds of nonaqueous zinc-based battery systems show potential applications for large-scale energy storage with good safety and environmental friendliness.
Introduction
With the continuous development of renewable energy, such as solar, tide, and wind energy, the exploration of grid-scale energy storage technologies is very important for storing the electricity generated from such intermittent energy sources.1–4 Over the last decade, lithium-ion batteries (LIBs) have been gradually becoming one of the most promising technologies dominating the markets of portable electronic devices and electric vehicles (EVs) owing to their merits such as long lifetime, high energy density, and no memory effect.5–9 However, the limited resource of Li in the earth has hindered further applications of LIBs in large-scale energy storage systems (ESSs).5,6 Multivalent cations such as Ca2+, Mg2+, Zn2+, and Al3+ are attractive options due to the potentially high energy density that originates from multiple electron transfers.10–23 Among them, Zn-ion based devices have exhibited distinctive features since Zn has been demonstrated as a feasible anode material with high capacity, high electrical conductivity, nontoxicity, and low cost.24–28 In recent years, tremendous progress has been made in zinc ion batteries (ZIBs). For instance, Na2V6O16·1.63H2O nanowires were used as the cathode for aqueous ZIBs, which delivered a stable discharge capacity of 352 mA h g−1 and a high capacity retention of 90% after 6000 cycles.24 Recently, a V2O5 porous microsphere cathode demonstrated a discharge capacity of 401 mA h g−1 and a lifespan of 1000 cycles in ZIBs.25 Until now, most of the reported zinc-ion batteries (ZIBs) have operated in aqueous electrolytes, where several issues have been detected, such as shape change and hydrogen evolution.17–19,24–31 However, the studies of ZIBs based on non-aqueous IL electrolytes are rarely reported.
Recently, dual-ion batteries (DIBs) have been developed as a novel rechargeable energy storage system.20,22,32–40 The mainstream functional materials in DIBs include carbon-based electrodes for cation/anion intercalation/deintercalation, metal-based electrodes for alloying/dealloying reactions, and non-aqueous electrolytes with movable cations and anions. This has endowed DIBs with the advantages of low cost, good safety, and environmental friendliness.41,42 In addition, the high anion intercalation potential at the cathode side has led to the high working voltage of the DIBs and therefore high energy density.
For instance, an aluminium–graphite dual-ion battery delivered a stable discharge capacity of 104 mA h g−1 and a high capacity retention of 88% after 200 cycles.32 More recently, all-carbon electrode DIBs showed a discharge capacity of ∼140 mA h g−1 and a lifespan of 1000 cycles.33 After intensive studies, the concept of DIBs has been successfully realized in non-Li based systems with excellent electrochemical performance.20,22,32–40
Herein, we report a Zn-ion DIB (ZDIB) based ionic liquid (IL) electrolyte, which avoids hydrogen evolution that occurs in aqueous systems and restrains the growth of zinc dendrites on the electrode.43 The configuration of expanded graphite (EG) as the cathode with a Zn counter electrode delivered a reversible discharge capacity of 57 mA h g−1, and displayed a high capacity retention of ∼86% after 500 cycles. In addition, we further constructed a dual-carbon configuration battery (ZDCB) based on the nonaqueous electrolyte, which exhibited comparable performance to that of the ZDIB, indicating potential for large-scale energy storage.
Experimental
Materials
Zinc foil (thickness of 100 μm, 99.9%) was provided by Sinopharm Chemical Reagent Co Ltd. Expanded graphite (EG), acetylene black, polyvinylidene fluoride (PVDF), and N-methyl-2 pyrrolidone (NMP) were purchased from Shenzhen Kejingstar Technology Ltd. Commercial carbon molecular sieves (CMS, 1.5GN-H) were purchased from Kuraray Chemical (Japan). Raw CMS was ball milled for 15 minutes using a high-energy planetary ball mill. Glass fiber sheets (Whatman, 47 mm) as the battery separator were purchased from Shanghai Huanao Technology Ltd. Zinc bis(trifluoromethanesulfonyl)imide (Zn(TFSI)2) and ethylene sulfite (ES) were obtained from Dodochem. The IL N-butyl-N-methylpyrrolidinium bis(trifluoromethanesulfonyl)imide (Pyr14TFSI) was purchased from Lanzhou Institute of Chemical Physics. All the chemicals were used directly without further purification.
Characterization
Ex situ X-ray diffraction (XRD) of the electrodes and materials was conducted on a Rigaku MiniFlex 600 X-ray diffractometer (Japan) using Cu Kα radiation (20 kV, λ = 0.154056 nm) operated at 40 kV and 15 mA with a scan rate of 4° min−1. Ex situ Raman spectroscopy of the EG cathode at different charging/discharging states and the Raman spectroscopy of CMS were carried out using a LabRAM HR Raman spectrometer (532 nm) in the frequency range from 1500 to 1700 cm−1 and from 1000 to 3250 cm−1, respectively. Field-emission scanning electron microscopy (FE-SEM) and energy dispersion X-ray spectrum (EDX) measurements of materials and electrodes were conducted on a ZEISS SUPRA®55 equipped with an energy dispersive X-ray detector. All the electrodes for XRD, Raman, and SEM test were washed with the IL and sealed in an Ar-filled glove box for preventing oxidation.
Electrochemical characterization
The electrochemical performance of the ZDIB and ZDCB were investigated using CR2032 coin-type cells. The EG cathode was prepared by mixing 80 wt% EG, 10 wt% acetylene black, and 10 wt% PVDF, followed by the addition of several drops of NMP solvent to form a homogeneous slurry. The slurry was homogeneously coated onto Al foil and dried at 80 °C overnight in a vacuum oven. The cathode sheet was then pressed and punched into circular sheets with 1.0 cm in diameter and a mass loading of ∼1.0 mg cm−2. The Zn foil was punched into circular sheets with 1.2 cm in diameter and directly employed as the anode material. The preparation of the CMS anode is similar to that of the EG cathode, except that the slurry was coated on Cu foil. Punched circular sheets of glass fiber with 1.6 cm in diameter were directly used as the separator. The homemade electrolyte 1 M Zn(TFSI)2 in Pyr14TFSI and 2 wt% ES as the additive were used. All operations were carried out in a glove box (MIKROUNA, Universal 12440-750) filled with argon. Galvanostatic charge–discharge (GCD) measurements were carried out on a battery test system (NEWARE CT-4008). Cyclic voltammetry (CV), electrochemical impedance spectroscopy (EIS), and linear sweep voltammetry (LSV) measurements were performed on an Autolab (PGSTAT302N, Switzerland) electrochemical workstation.
Results and discussion
Characterization of the working mechanism in the ZDIB
A schematic illustration of the charge–discharge processes of the ZDIB configuration is shown in Fig. 1a. During the charging process, Zn ions in the electrolyte migrate to the Zn anode and plate on the Zn foil, while the anions in the electrolyte, TFSI−, simultaneously migrate to the cathode material and intercalate between the graphite layers of EG to form the intercalated Cx(TFSI) compound. In the meantime, the solid electrolyte interface (SEI) film is generated on the surface of the electrodes. Conversely, upon discharging, metal zinc strips from the Zn foil anode to the electrolyte, while TFSI− de-intercalates from the graphite layers of the EG cathode.
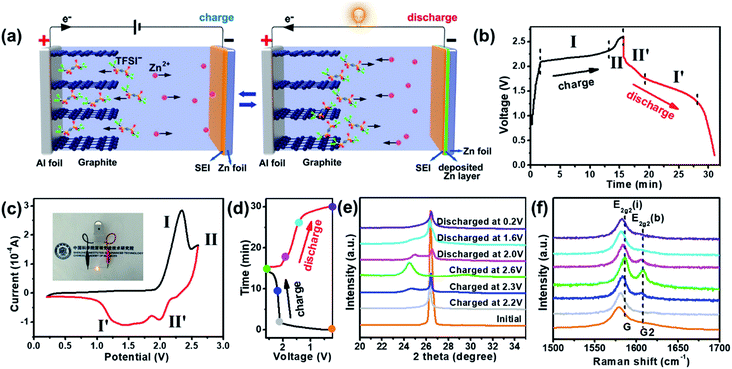 |
| Fig. 1 (a) Schematic diagram showing the configuration and mechanism of the designed ZDIB battery by using EG as the cathode and Zn foil as the anode. (b) Typical galvanostatic charging–discharging curves of the ZDIB. (c) CV curves of the ZDIB at a scan rate of 1 mV s−1. Inset is a ZDIB coin cell which can light up one yellow LED. (d) Corresponding ex situ characterization charging–discharging profiles at 2C. (e) Ex situ XRD and (f) ex situ Raman patterns of the EG cathode in various charging and discharging states. | |
Fig. 1b presents the typical GCD curves of the ZDIB based on the IL at a current density of 2C (1C corresponding to 100 mA g−1), with a working voltage window of 0.2–2.6 V. 2.6 V was chosen as the cutoff voltage (vs. Zn2+/Zn) depending on the electrochemical window of the IL electrolyte, obtained from the linear sweep voltammetry test (Fig. S1†). During the charging process, two regions, in the range of 2.0–2.3 V (stage I) and 2.3–2.6 V (stage II), respectively, can be identified from the charging curve, which correspond to different processes of the TFSI− intercalation into graphitic layers, similar to other DIB systems.32–38 Similarly, during the discharging process, two potential regions can be recognized in the voltage range of 2.2–1.75 V (stage II′) and 1.75–1.3 V (stage I′), respectively, corresponding to different processes of the TFSI− deintercalation from graphitic layers. The corresponding CV curves are presented in Fig. 1c, in which the peaks are in accordance with the intercalation/deintercalation stages in the GCD curves shown in Fig. 1b. It is worth noting that the medium discharge voltage (Vm) of the ZDIB reached approximately 1.6 V, which is higher than those of most so-far reported conventional aqueous ZIBs. Accordingly, one prepared ZDIB can light up one light-emitting diode (LED) with a yellow color (around 2.0–2.2 V) (inset of Fig. 1c). Besides, the high working voltage of the ZDIB is beneficial for improving the energy density.
To better understand the working mechanism of the ZDIB, we characterized the intercalation/de-intercalation into/from the graphitic layers of TFSI− during the charging–discharging processes by ex situ XRD and ex situ Raman spectroscopy. We selected seven states indicated by the colored circles in Fig. 1d and the corresponding XRD and Raman patterns are shown in Fig. 1e and f. As shown in Fig. 1e, the (002) diffraction peak at 26.5° of pristine EG is quite sharp, indicating the high crystallinity degree of EG. When the charging process started, the (002) diffraction peak of the EG cathode gradually split into two weak peaks, and the intensity of the new peak gradually increased, accompanied by a shift to the lower angle. It indicated that the TFSI− anions gradually intercalated into the graphitic layers of the EG cathode. Upon full charging, the (002) peak completely deflects at 24.5°, indicating the complete anion intercalation process. Conversely, during the discharge process, the deflected peak at 24.5° gradually moved back to a higher degree and also split into two peaks, corresponding to the process of TFSI− de-intercalation from the graphitic layers. Finally, the split peaks merged into one peak and returned to the initial angle upon full discharging (0.2 V), indicating the end of the de-intercalation process. It is worth noting that the (002) diffraction peak of EG after one intercalation/de-intercalation process is wider and the intensity is lower than in pristine EG, which suggests the existence of certain irreversible reaction in the initial cycle. This phenomenon is similar to other reported DIBs.32,37
Fig. 1f shows the ex situ Raman spectra of the EG cathode at different charging–discharging stages in the first cycle, corresponding to the intercalation/de-intercalation processes of the TFSI− anions. Only one wide peak at 1580 cm−1 is clearly observed in the Raman spectrum of pristine EG, which is known as the G band of the graphite. This peak is attributed to the E2g vibrational mode, which is caused by the bond stretching of sp2 carbon. During the charging process (from 0.2 to 2.6 V), this peak was blue-shifted and is denoted as the E2g2(i) mode. In addition, a new peak emerged in the spectra at 1608 cm−1 and is recognized as the E2g2(b) mode, which is attributed to a stage-II like structure. With the gradual intercalation of TFSI− anions into the layers of the graphite, the intensity of the E2g2(b) peak gradually increased. Conversely, during the discharging process, the E2g2(b) peak gradually disappeared, and E2g2(i) was red-shifted, illustrating the de-intercalation process of the TFSI− anions. All the Raman spectra results are in accordance with the XRD results.
Electrochemical performance of the ZDIB
The electrochemical performance of the ZDIB based on the IL electrolyte was investigated, and the results are shown in Fig. 2. The typical CV curves in the first three cycles scanned between 0.2 and 2.6 V at a scan rate of 1 mV s−1 are shown in Fig. 2a. It is seen that the curves are similar to those in Fig. 1c and nearly overlap with each other, indicating the good reversibility and cycling stability of the EG cathode. Fig. 2b and c illustrate the rate performance of the ZDIB after electrochemical activation at 2C for several cycles. The typical GCD curves under various current rates from 2C to 5C within the voltage window of 0.2–2.6 V are shown in Fig. 2b. Obviously, the GCD curves show similar profiles, and the voltage plateau moderately altered with the change of the current density during the charging–discharging processes, illustrating relatively small electrochemical polarization. Furthermore, the charging–discharging capacities and the corresponding coulombic efficiencies (CEs) of the ZDIB at various current rates are shown in Fig. 2c. At the current rates of 2C, 3C, 4C, and 5C, the corresponding discharge capacities are 56, 47, 45, and 42 mA h g−1, respectively. The discharge capacity resumed to 56 mA h g−1 when the current rate returned to 2C, which demonstrates the excellent rate performance and good reversibility of the ZDIB. The relatively low CE at 2C could be ascribed to the formation of SEI layers on both electrodes at low current density.37,38Fig. 2d illustrates the long-term cycling stability of the ZDIB at 2C for 500 cycles. Notably, this battery delivered a reversible discharge capacity of 57 mA h g−1 after electrochemical activation and exhibited a high capacity retention of ∼86% after 500 cycles. It is noted that the capacity of the battery decreases rapidly in the first several cycles. This phenomenon is probably due to the electrochemical activation and the formation of SEI film, which has also been observed in other reported batteries.44–46Fig. 2e shows the typical GCD curves of different cycles (50th, 100th, 200th, 300th, 400th and 500th), which coincide with each other, indicating the good cycling stability and good capacity reversibility of the ZDIB. The Vm of the cell is maintained at around 1.6 V for 500 cycles (Fig. 2f), and the charging–discharging profiles for the last 30 cycles are exemplified in the inset of Fig. 2f. These results display the excellent cycling stability of the cell during the testing process (∼280 h). Long-term cycling performances of ZDIBs in different voltage windows are also presented in Fig. S2.† The ZDIB over the voltage window of 0.2–2.6 V presents the best long-term cycling performance, which is in accordance with previous LSV results.
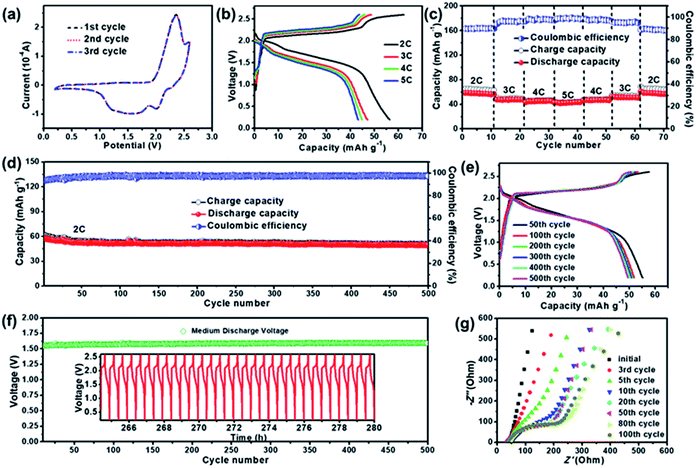 |
| Fig. 2 Electrochemical measurements of ZDIB based on the electrolyte 1 M Zn(TFSI)2 in Pyr14TFSI + 2 wt% ES. (a) CV curves in the first three cycles after stabilizing for several cycles at a scan rate of 1 mV s−1. (b) Galvanostatic charge–discharge curves at different current densities from 2C to 5C. (c) Charge–discharge capacities and corresponding coulombic efficiency at different current densities. (d) Long cycling performance at 2C for 500 cycles in the voltage window of 0.2–2.6 V. (e) Corresponding charge–discharge curves of different cycles. (f) Medium discharge voltage for 500 cycles (inset: charge–discharge profiles for the final 30 cycles.). (g) Nyquist plots at different cycles. | |
Electrochemical impedance spectroscopy (EIS) tests were performed to further characterize the long-term reaction kinetics of the EG cathode. The Nyquist plots of the ZDIB in different cycles (initial, 3rd, 5th, 10th, 20th, 50th, 80th, 100th) are shown in Fig. 2g. The plots after the first five cycles consist of a sloping line at the low-frequency region and a depressed semicircle at the high-and-middle frequency region, corresponding to Warburg impedance and charge transfer resistance (Rct), respectively. It is clearly observed that the diameter of the semicircle gradually becomes larger with the increase of the cycle number, revealing the increase of the Rct value, suggesting the formation of SEI layers attributed to the decomposition of the electrolyte on the electrodes. The Rct value is almost constant after the 80th cycle, which indicates that the SEI film was completely formed, and the cell remained stable in the following cycles, which coincides with the long-term cycling results.
To further characterize the intercalation/deintercalation process of TFSI− in EG layers, CV curves with various sweep rates have been obtained, and a diagram of log(i) versus log(v) is depicted for the oxidation/reduction peaks in the ZDIB. In general, the relationship between peak currents (i) and sweep rates (v) could be expressed using the equation i = avb, where a and b are constants. A b value of 0.5 means the redox reaction is a semi-infinite diffusion process, that is, the reaction appears to be a diffusion-controlled process. Meanwhile, a b value of 1.0 shows that the redox reaction is a surface-limited process, i.e., the reaction displays a capacitive behavior. Based on CV measurements at scan rates ranging from 0.1 to 0.6 mV s−1 (Fig. 3a), b values were calculated to be ∼0.58 and 0.56 for cathodic peaks, and ∼0.54 and 0.58 for anodic peaks, corresponding to stage I and II, and stage II′ and I′ during the cycling processes, respectively (Fig. 3b). All the b values are close to 0.5, which indicates that the kinetics between EG and TFSI− can be mainly attributed to the diffusion-controlled process, i.e., the electrochemical processes in EG are ascribed to the intercalation/deintercalation of the TFSI− in EG layers.
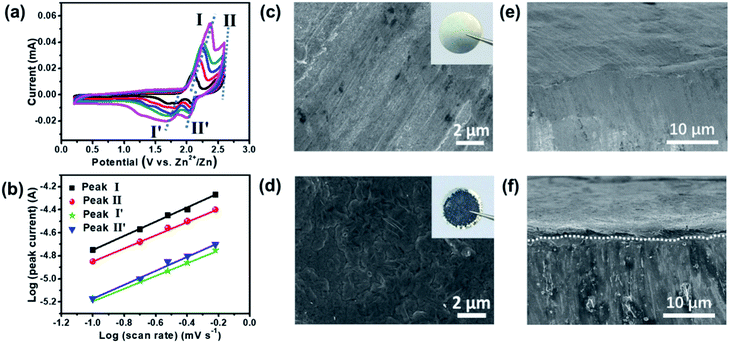 |
| Fig. 3 (a) CV curves at various scan rates from 0.1 to 0.6 mV s−1. (b) Calculation of b-values from the relationship between the scan rate and peak current. (c) SEM image of the fresh Zn foil anode before cycling. Inset is the corresponding optical photograph. (d) SEM image of the Zn foil anode in the ZDIB after 500 cycles. Inset is the corresponding optical photograph. Cross-sectional SEM images of (e) the fresh Zn foil anode and (f) the Zn foil anode in the ZDIB after 500 cycles at 2C. | |
Fig. 3c and d present the SEM images of the Zn foil before and after 500 cycles, with the inset showing their corresponding optical photographs. The optical photograph after long-term cycling clearly shows that a grey layer is formed in the Zn anode, and the SEM images verified the existence of the smooth layer. It is noticeable that no dendrites were detected on the surface of Zn after long-term cycling, revealing satisfactory safety of the ZDIB. The cross-sectional SEM images of the fresh Zn foil and those after 500 cycles at 2C are shown in Fig. 3e and f, which indicate the formation of a dense plating Zn layer on the Zn anode. The EDX profile and the elemental composition (Fig. S3†) illustrate that C, S, F, and O are the basic component elements of the protective SEI layer. In addition, neither the Zn anode (Fig. S4†) nor the EG cathode (Fig. S5†) shows noticeable morphological changes after 500 cycles, implying the excellent structural stability of the electrode materials. It should be noted that the (002) peak in the XRD profile (Fig. S6†) of the EG cathode became broader and left-shifted, indicating a partial microstructural change of the EG cathode after long-term cycling.
Demonstration of the Zn-ion based dual-carbon battery (ZDCB)
In addition, a Zn-ion based dual-carbon battery (ZDCB) was also demonstrated by replacing the Zn anode in the previous ZDIB with commercial carbon molecular sieves (CMS), which have sufficient and ultra-small pores.47 The SEM image of ball-milled CMS and the photograph of bulk CMS are shown in Fig. S7.† The result indicates that bulk CMS is a black, cylindrical solid with the size of 0.5–2.0 μm after ball-milling. The XRD pattern (Fig. S8†) of CMS exhibits a sharp diffraction peak at 2θ = 26.7° attributed to the graphitic-like domain, and another broad peak at 2θ = 22.7° which originates from the long-range disordered graphitic-like domain. In the Raman spectra (Fig. S9†), the ID/IG value of CMS is estimated to be ∼1.22, indicating the existence of a disordered structure and well-exposed edges.
The typical CV curves of the ZDCB in the first three cycles scanned between 0.2 and 2.6 V at a scan rate of 1 mV s−1 are shown in Fig. 4a. It is seen that the curves nearly overlap with each other, indicating the good cycling stability of the cell. In addition, three pairs of peaks at 1.49/1.03 V, 1.95/1.70 V, and 2.35/1.97 V are associated with the electrochemical processes. The rate performance of the ZDCB over the voltage window of 0.2–2.6 V is illustrated in Fig. 4b and c. Similar profiles of GCD curves (Fig. 4b) are observed and the voltage plateau moderately increased/decreased with the increase of the current densities during the charging–discharging processes, illustrating the relatively small electrochemical polarization of the ZDCB. In addition, the discharge capacity of the ZDCB is approximately 52.6, 49.9, 48.6, 47.5, 46.7 and 45.7 mA h g−1 for 2, 3, 4, 5, 8 and 10C, respectively, with the corresponding CE over 96% (Fig. 4c). The discharge capacity returned to 51.6 mA h g−1 when the current density recovered to 2C, demonstrating both good rate capability and capacity reversibility of the ZDCB. Fig. 4d and e show the cycling performance. The GCD curves at the 300th and 500th cycle almost coincide with that of the 50th cycle (Fig. 4d). The cell delivered a stable discharge capacity of ∼58 mA h g−1 at 2C after electrochemical activation and exhibited a capacity retention of ∼88% after 500 cycles (Fig. 4e). The Vm of the cell is maintained at ∼1.25 V for 500 cycles (Fig. 4f), and the GCD profiles of the last 30 cycles are exemplified in the inset of Fig. 4f. These results display the excellent cycling stability of the ZDCB cell during the testing process (∼290 h). The working mechanism of the ZDCB was also studied. We selected seven states indicated by the colored circles in Fig. 4g, and their corresponding ex situ XRD and ex situ Raman patterns are shown in Fig. 4h and i. These patterns exhibited similar trends to those in the ZDIB characterization, revealing the reversible TFSI− intercalation/de-intercalation into/from the graphitic layers during the charging–discharging processes in the ZDCB.
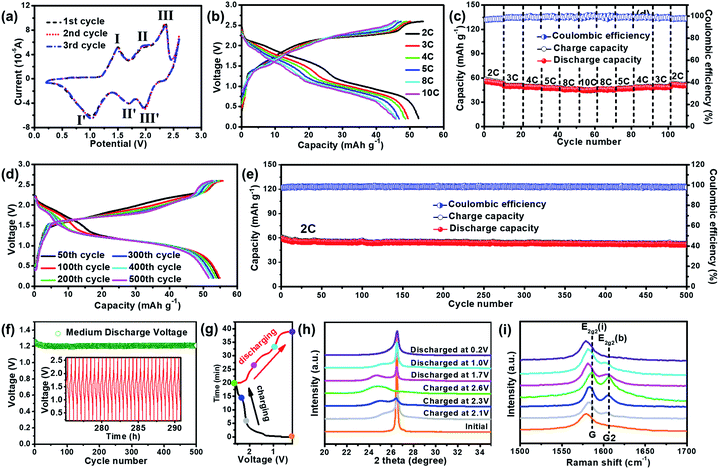 |
| Fig. 4 Electrochemical measurements of the ZDCB based on the electrolyte 1 M Zn(TFSI)2 in Pyr14TFSI + 2 wt% ES. (a) CV curves in the first three cycles after stabilizing for several cycles at a scan rate of 1 mV s−1. (b) Galvanostatic charge–discharge curves at different current densities from 2C to 10C. (c) Charge–discharge capacities and corresponding coulombic efficiency under different current densities. (d) Charge–discharge curves of different cycles. (e) Long cycling performance at 2C for 500 cycles. (f) Medium discharge voltage for 500 cycles (inset: charge–discharge profiles for the final 30 cycles.). (g) Corresponding ex situ characterization charging–discharging profiles at 2C. (h) Ex situ XRD and (i) ex situ Raman patterns of the EG cathode in various charging and discharging states. | |
Conclusions
In summary, we have developed two highly rechargeable nonaqueous zinc-based dual-ion battery systems based on Zn|IL|EG and dual-carbon configurations (CMS|IL|EG). The Zn|IL|EG battery delivered a reversible discharge capacity of ∼57 mA h g−1 and exhibited a high capacity retention of 86% after 500 cycles with a medium discharge voltage of 1.6 V, demonstrating its excellent cycling stability and capacity reversibility. Moreover, the dual-carbon configuration battery (CMS|IL|EG) also showed comparable performance. Notably, adoption of the IL suppressed the dendritic growth of zinc and avoided hydrogen evolution, resulting in satisfactory safety of the battery. In addition, compared to aqueous ZIBs, these two kinds of nonaqueous zinc-based battery systems have higher working voltages. Thus, these two kinds of nonaqueous zinc-based battery systems have potential for large-scale energy storage with good safety and environmental friendliness.
Conflicts of interest
The authors declare no conflicts of interest.
Acknowledgements
This work was supported by the National Natural Science Foundation of China (51822210, 51972329), Shenzhen Science and Technology Planning Project (No. JCYJ20170818153427106, JCYJ20170818153404696, and JCYJ20180507182512042), and Science and Technology Planning Project of Guangdong Province (2018A050506066, 2019B090914003).
References
- F. J. DiSalvo, Science, 1999, 285, 703 CrossRef CAS PubMed.
- F. Yu, Z. Liu, R. Zhou, D. Tan, H. Wang and F. Wang, Mater. Horiz., 2018, 5, 529 RSC.
- Z. Yang, J. Zhang, M. C. Kintner-Meyer, X. Lu, D. Choi, J. P. Lemmon and J. Liu, Chem. Rev., 2011, 111, 3577 CrossRef CAS PubMed.
- L. Liang, X. Sun, J. Zhang, J. Sun, L. Hou, Y. Liu and C. Yuan, Mater. Horiz., 2019, 6, 871 RSC.
- J.-M. Tarascon and M. Armand, Nature, 2001, 414, 359 CrossRef CAS PubMed.
- Z. W. Lebens-Higgins, N. V. Faenza, M. D. Radin, H. Liu, S. Sallis, J. Rana, J. Vinckeviciute, P. J. Reeves, M. J. Zuba, F. Badway, N. Pereira, K. W. Chapman, T.-L. Lee, T. Wu, C. P. Grey, B. C. Melot, A. V. D. Ven, G. G. Amatucci, W. Yang and L. F. J. Piper, Mater. Horiz., 2019 10.1039/c9mh00765b.
- B. Dunn, H. Kamath and J.-M. Tarascon, Science, 2011, 334, 928 CrossRef CAS PubMed.
- Y. Yang, S. Wang, C. Jiang, Q. Lu, Z. Tang and X. Wang, Chem. Mater., 2016, 28, 2417 CrossRef CAS.
- Y. Zhong, M. Yang, X. Zhou and Z. Zhou, Mater. Horiz., 2015, 2, 223 RSC.
- D. Wang, X. Gao, Y. Chen, L. Jin, C. Kuss and P. G. Bruce, Nat. Mater., 2018, 17, 16 CrossRef CAS PubMed.
- R. J. Gummow, G. Vamvounis, M. B. Kannan and Y. He, Adv. Mater., 2018, 30, 1801702 CrossRef PubMed.
- S. Gheytani, Y. Liang, F. Wu, Y. Jing, H. Dong, K. K. Rao, X. Chi, F. Fang and Y. Yao, Adv. Sci., 2017, 4, 1700465 CrossRef PubMed.
- C. Kim, P. J. Phillips, B. Key, T. Yi, D. Nordlund, Y. S. Yu, R. D. Bayliss, S. D. Han, M. He, Z. Zhang, A. K. Burrell, R. F. Klie and J. Cabana, Adv. Mater., 2015, 27, 3377 CrossRef CAS PubMed.
- B. Pan, J. Huang, Z. Feng, L. Zeng, M. He, L. Zhang, J. T. Vaughey, M. J. Bedzyk, P. Fenter, Z. Zhang, A. K. Burrell and C. Liao, Adv. Energy Mater., 2016, 6, 1600140 CrossRef.
- Y. Zhang, H. Geng, W. Wei, J. Ma, L. Chen and C. C. Li, Energy Storage Materials, 2019, 20, 118 CrossRef.
- T. Zhang, Z. Tao and J. Chen, Mater. Horiz., 2014, 1, 196 RSC.
- H. Li, L. McRae, C. J. Firby and A. Y. Elezzabi, Adv. Mater., 2019, 31, 1807065 CrossRef PubMed.
- J. Shin, D. S. Choi, H. J. Lee, Y. Jung and J. W. Choi, Adv. Energy Mater., 2019, 9, 1900083 CrossRef.
- C. Han, W. Li, H.-K. Liu, S. Dou and J. Wang, Mater. Horiz., 2019, 6, 1812 RSC.
- M. C. Lin, M. Gong, B. Lu, Y. Wu, D. Y. Wang, M. Guan, M. Angell, C. Chen, J. Yang, B. J. Hwang and H. Dai, Nature, 2015, 520, 325 CrossRef PubMed.
- D. Y. Wang, C. Y. Wei, M. C. Lin, C. J. Pan, H. L. Chou, H. A. Chen, M. Gong, Y. Wu, C. Yuan, M. Angell, Y. J. Hsieh, Y. H. Chen, C. Y. Wen, C. W. Chen, B. J. Hwang, C. C. Chen and H. Dai, Nat. Commun., 2017, 8, 14283 CrossRef CAS PubMed.
- X. Zhang, S. Jiao, J. Tu, W.-L. Song, X. Xiao, S. Li, M. Wang, H. Lei, D. Tian, H. Chen and D. Fang, Energy Environ. Sci., 2019, 12, 1918 RSC.
- Z. Yu, S. Jiao, S. Li, X. Chen, W.-L. Song, T. Teng, J. Tu, H.-S. Chen, G. Zhang and D.-N. Fang, Adv. Funct. Mater., 2018, 1806799 Search PubMed.
- P. Hu, T. Zhu, X. Wang, X. Wei, M. Yan, J. Li, W. Luo, W. Yang, W. Zhang, L. Zhou, Z. Zhou and L. Mai, Nano Lett., 2018, 18, 1758 CrossRef CAS PubMed.
- P. Hu, T. Zhu, J. Ma, C. Cai, G. Hu, X. Wang, Z. Liu, L. Zhou and L. Mai, Chem. Commun., 2019, 55, 8486 RSC.
- H. Liang, Z. Cao, F. Ming, W. Zhang, D. H. Anjum, Y. Cui, L. Cavallo and H. N. Alshareef, Nano Lett., 2019, 19, 3199 CrossRef CAS PubMed.
- H. Yang, B. Wang, H. Li, B. Ni, K. Wang, Q. Zhang and X. Wang, Adv. Energy Mater., 2018, 8, 1801839 CrossRef.
- P. Hu, M. Yan, T. Zhu, X. Wang, X. Wei, J. Li, L. Zhou, Z. Li, L. Chen and L. Mai, ACS Appl. Mater. Interfaces, 2017, 9, 42717 CrossRef CAS PubMed.
- Y. Li, Z. Huang, P. K. Kalambate, Y. Zhong, Z. Huang, M. Xie, Y. Shen and Y. Huang, Nano Energy, 2019, 60, 752 CrossRef CAS.
- G. Fang, C. Zhu, M. Chen, J. Zhou, B. Tang, X. Cao, X. Zheng, A. Pan and S. Liang, Adv. Funct. Mater., 2019, 29, 1808375 CrossRef.
- W. Li, K. Wang, S. Cheng and K. Jiang, Energy Storage Materials, 2018, 15, 14 CrossRef.
- X. Zhang, Y. Tang, F. Zhang and C.-S. Lee, Adv. Energy Mater., 2016, 6, 1502588 CrossRef.
- Z. Zhou, N. Li, Y. Yang, H. Chen, S. Jiao, W.-L. Song and D. Fang, Adv. Energy Mater., 2018, 8, 1801439 CrossRef.
- S. Rothermel, P. Meister, G. Schmuelling, O. Fromm, H.-W. Meyer, S. Nowak, M. Winter and T. Placke, Energy Environ. Sci., 2014, 7, 3412 RSC.
- M. Sheng, F. Zhang, B. Ji, X. Tong and Y. Tang, Adv. Energy Mater., 2017, 7, 1601963 CrossRef.
- L. Fan, Q. Liu, S. Chen, Z. Xu and B. Lu, Adv. Energy Mater., 2017, 7, 1602778 CrossRef.
- B. Ji, F. Zhang, X. Song and Y. Tang, Adv. Mater., 2017, 29, 1700519 CrossRef PubMed.
- B. Ji, F. Zhang, N. Wu and Y. Tang, Adv. Energy Mater., 2017, 7, 1700920 CrossRef.
- M. Wang, C. Jiang, S. Zhang, X. Song, Y. Tang and H. M. Cheng, Nat. Chem., 2018, 10, 667 CrossRef CAS PubMed.
- S. Wu, F. Zhang and Y. Tang, Adv. Sci., 2018, 5, 1701082 CrossRef PubMed.
- M. Wang and Y. Tang, Adv. Energy Mater., 2018, 8, 1703320 CrossRef.
- M. Zhang, X. Song, X. Ou and Y. Tang, Energy Storage Materials, 2019, 16, 65 CrossRef.
- Z. Liu, P. Bertram and F. Endres, J. Solid State Electrochem., 2017, 21, 2021 CrossRef CAS.
- S. Wang, S. Jiao, D. Tian, H.-S. Chen, H. Jiao, J. Tu, Y. Liu and D.-N. Fang, Adv. Mater., 2017, 29, 1606349 CrossRef PubMed.
- E. Zhang, W. Cao, B. Wang, X. Yu, L. Wang, Z. Xu and B. Lu, Energy Storage Materials, 2018, 11, 91 CrossRef.
- F. Zhang, B. Ji, X. Tong, M. Sheng, X. Zhang, Y. Tang and C.-S. Lee, Adv. Mater. Interfaces, 2016, 3, 1600605 CrossRef.
- S.-W. Zhang, W. Lv, C. Luo, C.-H. You, J. Zhang, Z.-Z. Pan, F.-Y. Kang and Q.-H. Yang, Energy Storage Materials, 2016, 3, 18 CrossRef.
Footnote |
† Electronic supplementary information (ESI) available: Detailed experimental process and characterizations. See DOI: 10.1039/c9se00744j |
|
This journal is © The Royal Society of Chemistry 2020 |
Click here to see how this site uses Cookies. View our privacy policy here.