DOI:
10.1039/D0GC02913K
(Critical Review)
Green Chem., 2021,
23, 51-76
Interfacial catalysts for sustainable chemistry: advances on atom and energy efficient glycerol conversion to acrylic acid
Received
26th August 2020
, Accepted 23rd November 2020
First published on 26th November 2020
Abstract
Conversion of glycerol to acrylic acid represents an emerging application in transforming waste biomass to valuable products in chemical industry. However, achieving almost perfect atomic efficiency and intrinsic zero-waste generation still remain a grand challenge to meet stricter regulations on energy consumption. Interfacial catalysis plays a central role in bridging nanostructured catalysts with green chemistry. Despite a few preliminary attempts in academia and industry, the application of interfacial catalysts remains limitedly successful. In this review, we first describe morphological & electronic uniqueness of three important interfacial catalysts, (I) bimetallic nanoclusters, (II) metal–acid composites and (III) Brønsted/Lewis acid hybrids. The resulting catalytic properties for C–H and C–O bond cleavage during oxidation and dehydration of glycerol to acrylic acid will then be critically discussed, to reveal the key advances and challenges in this area. As oxidation and dehydration represent two important reactions in industry, the outcome of this work is to provide insightful information developing cost-effective catalytic materials for various other sustainable chemical applications.
1. Acrylic acid: a key essential for sustainable chemical industry
1.1 Background
Acrylic acid (AA), a C3 carboxylic acid, is an important commodity intermediate in modern chemical industry. AA is also known as 2-peropenoic acid as there is a C
C bond existing in the molecular structure. It has a density of 1.062 g cm−3 at 20 °C and is miscible with water in all ratios. As a key building block, AA can be transformed into a variety of downstream products (Fig. 1).1,2 More importantly, AA is used as a performance enhancer in superabsorbents, BPA-free plastics (BPA: bisphenol a), and synthetic rubbers as well as coatings, textiles and detergents.
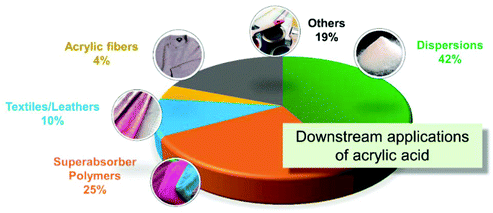 |
| Fig. 1 Acrylic acid as building blocks for various applications. | |
The market share for various consumers’ product is also presented in Fig. 1. Superabsorbers and detergents are the most popular applications, which were projected to a global consumption of more than 1 million tons in 2020, with 15–20% annual growth. Other applications include phosphate-free washing agents, coatings for printed circuit boards.2–4
AA can be manufactured from fossil- and bio-based feedstocks (Fig. 2).5,6 AA is conventionally produced by catalytic oxidation of propylene in a two-step conversion route, involving production of acrolein or a modified Reppe process from acetylene (Scheme 1).6–9 AA can also be produced from hydrolysis of acrylonitrile. For propylene-based route, in the first step, propylene can be partially oxidized into acrolein over Mo-based catalyst materials at temperatures in the range of 310–400 °C with 0.1–0.3 MPa of steam vapor and air, the product of which is then fed to a second reactor to produce AA at 260–300 °C. The overall conversion of propylene is 95% with yield to AA of 80–90%. Catalysts used include Bi, Co, Fe, Mo based heterogenoues materials for the first stage, while second-stage catalysts are mixed metal oxides containing Mo and V.
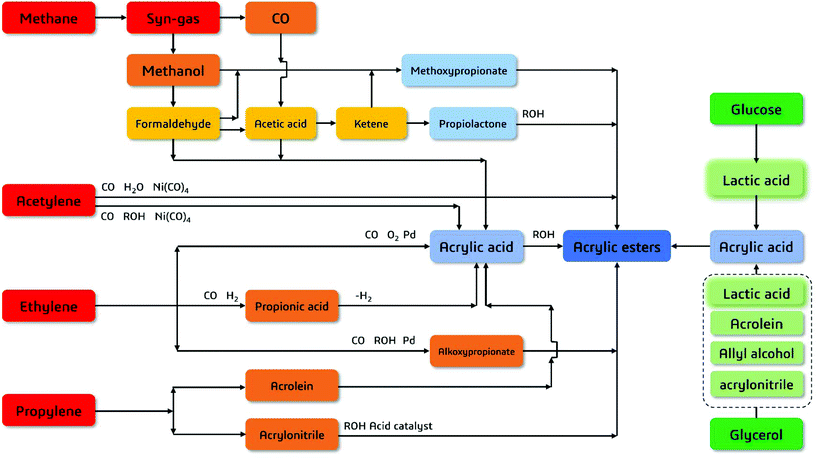 |
| Fig. 2 Manufacture of acrylic acid and esters from fossil-based (red) and bio-derived (green) feedstocks. | |
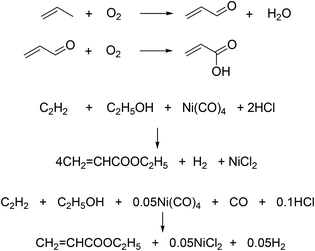 |
| Scheme 1 Propylene-based and acetylene-based routes. | |
Walter Reppe, the founder of modern acetylene chemistry, discovered the reaction involving Ni carbonyl promoted acetylene and water/alcohols reaction to give AA and derivatives.10 Acrylonitrile route is often considered as modified propylene oxidation route. The yield of acrylonitrile is lower than that of AA from propylene oxidation.
AA has been produced in large quantities, for example in European Union (EU) and North America.10 The market for downstream products is very dynamic, as production worldwide for AA has reached 6.5 million tons in 2019 with a strong growth rate of 5% per annum. Actually, market reports on global consumption have suggested that the demand for AA and its derivatives has already exceeded 8.0 million tons in 2019. From the perspective of life cycle analysis, propylene-, acetylene- and acrylonitrile-based routes all demand significant energy input for cracking, partial oxidation and ammoxidation reactions. Although currently dominant, the strong interests worldwide seeking for more “greener” feedstocks and processes motivated researchers to explore more opportunities.6,11
1.2 Bio-derived acrylic acid: scope of the review
Replacing propylene and acetylene with bio-oxygenates has been emerging as a promising route to manufacture AA from renewable resources.6,11 Although extensive attention being paid for bio-AA synthesis, up to date, there are only two review articles discussing the progress on manufacture of AA from biomass as the starting material. Ueda and colleagues summarized the key challenges in converting glycerol to acrylic acids via multiple routes, including (i) glycerol–acrolein (red route in Fig. 3), (ii) glycerol–allyl alcohol (purple route in Fig. 3) and (iii) glycerol–lactic acid routes (green route in Fig. 3).12 The most recent review from Zhou's group critically revised the highlights in catalyst perfomances for (i) glycerol–acrolein route.5
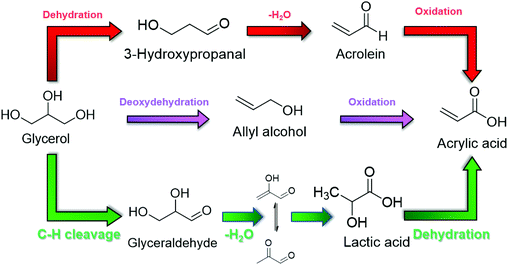 |
| Fig. 3 Conversion of glycerol to AA via multiple transformation routes. | |
1.2.1 Atom and energy economics for route (iii).
As all three routes start with glycerol and end with AA as the final product, one would expect similar atom efficiency and energy input for all three routes. However, detailed inspection of the three routes reveals that, route (iii) shows several possible atomic and energetic advantages over the other two.3,13,14 Conversion of glycerol to lactic acid generally needs much lower temperature (90–200 °C) compared with the first step involved in (i) and (ii).15–18 More importantly, removal of H species from glycerol molecules obviously undergoes varied reaction pathways for the three conversion routes.19–22 While (i) and (ii) often involves hydration as the first step to lose H species in the form of water molecules,4,7,9,12,23,24 (iii) oxidation of glycerol can occur in the absence of O2, thus producing valuable H2 as an important co-product.7,8,25,26 Obviously, oxidative reaction of glycerol in the presence of O2 still occur under much milder condition (<130 °C) compared with other two routes (>260 °C). This is the main advantage for synthesis of AA from glycerol via lactic acid as key intermediate.27–30 Dehydration of lactic acid to AA requires inexpensive heterogeneous catalysts, rather than homogeneous or noble metal species.8,25
With global efforts in developing poly-lactic acid for bio-degradable polymers, bans on single-use fossil-derived plastics have become stricter in the past few years. Thus one can predict the strong growth in the market of lactic acid as a cost-effective intermediate for sustainable production of AA in the coming future.2,6,8,23,29,31 Therefore, this review article will be particularly focused on selective synthesis of AA from glycerol via lactic acid as the key intermediate, with focused discussion on catalyst design and molecular catalysis involved in oxidation of glycerol to lactic acid, and dehydration of lactic acid to AA as final product.
2. Fundamentals on interfacial catalysis
2.1 Interfacial catalysis: morphological & electronic uniqueness
According to the brief summary on catalyst design, hybridized materials have been studied for glycerol conversion to lactic acid and subsequent dehydration of lactic acid to AA. Specifically, supported metallic catalysts, mixed metal oxides and metal–acid composites, with 2D or 3D morphology (Fig. 4) are commonly used for conversion of glycerol to lactic acid.27,28,32 For dehydration of lactic acid, mostly widely studied candidates are modified zeolites, phosphate and sulfates (Fig. 5).33–35 This is because each of the reactions actually involves multiple elementary steps. Among those above-mentioned hybridized materials, three key interfacial structures are crucial for tunable activity, selectivity and durability of solid catalysts (see Fig. 6 for conceptual description).
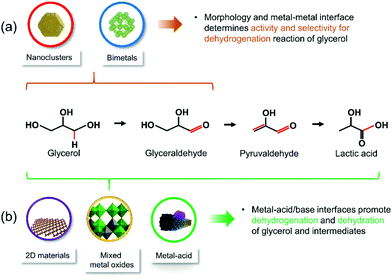 |
| Fig. 4 Hybridized catalysts for glycerol conversion to lactic acid, (a) dehydrogenation step, (b) dehydrogenation–dehydration step. | |
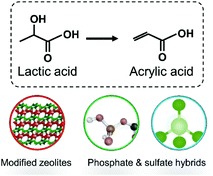 |
| Fig. 5 Dehydration of lactic acid to acrylic acid over hybridized catalysts. | |
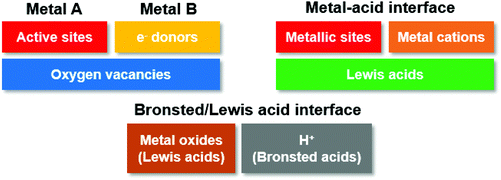 |
| Fig. 6 Conceptual description for three types of interfacial catalysis. | |
2.1.1 Metal–metal interface.
Morphological and electronic coupling at metal–metal interfaces contributes to tunable activity for C–H bond cleavage. The hybridization of d orbitals could alter surface electronic density and number of valence electrons for active sites. Furthermore, non-noble Cu, Co and Ni have been often selected as the second metal/promoters, which show strong electronic donor properties.36–38 For metal–metal interfaces, as the number of metal neighbors or the coordination number of the surface metal changes, the bandwidth of the d-DOS (density of states) also changes.39–46 The general rule is that, higher coordination number contributes to broader band (Fig. 7(a)). Broader band may partially lower the overall energy level of unoccupied orbitals below Fermi level. The lowered electron orbitals will not easily be accessible to reactants. Thus, formation of metal–H and metal–O bond can be affected during activation of glycerol molecule. In particular, the consequence of a nearly constant d-band filling is an upshift in the d-band center, leading to a more catalytically reactive surface, as more unoccupied orbitals interact with substrate molecules for selective activation of chemical bonds. Therefore, upshift of d-band center could result in improved activity for metal catalysts when activating oxygenated molecules.42,43,45
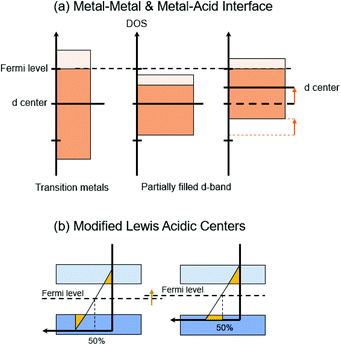 |
| Fig. 7 Electronic reconfiguration for three interfacial catalysts: (a) Metal–Metal & Metal–Acid Interface (b) Modified Lewis Acidic Centers. | |
This is the reason that bimetallic catalysts often display relatively better activity compared with monometallic candidates. The morphological effect is also important for redox reactions. But it seems that very few studies were focused on this aspect. At present, application of bimetallic catalysts is only primarily on oxidation of glycerol to glyceraldehyde, after which acidic or basic promoters are needed to facilitate dehydration reactions.
2.1.2 Metal–acid interface.
Metal–acid interface is one of the most commonly studied subjects in the past few decades, particularly in the areas of petroleum and coal refining. Different from the case with metal–metal interface, Lewis acid often show strong electronic withdrawing capability from metals, altering the d-band center of metallic sites.39 Strong metal–acid interaction actually induces the formation of additional interfaces. This is because as metallic sites display more cationic nature, the coordination number of metal centers is actually enhanced, leading to broader d-bandwidth.46 For biomass conversion, the electronic interaction at metal–Lewis acid interfaces alters the intrinsic activity of metal sites for C–H bond cleavage reaction of glycerol. Different from the case with metal–metal interfaces, the presence of Lewis acidic centers induces the formation of metallic cations (Fig. 7(a)) with strong electronic withdrawing capabilities against oxygenates. Therefore, the additional interfaces are often found to promote tandem catalysis for C–H and C–O bond cleavage during glycerol conversion. Interestingly such combination is often useful for enhanced oxidation reactions, therefore there should exist alternative mechanism for metal–Lewis acid catalyzed C–H cleavage.
Nevertheless, the presence of Lewis acidic sites also contributes to dehydration and structural rearrangement reactions. This is the main advantage for metal–acid systems over bimetallic catalysts. However, to our best knowledge, such hybridized materials have not been utilized in dehydration of lactic acid or one-pot oxidation–dehydration of glycerol to AA. Existing studies are still focused on electronic coupling enhancement for C–H cleavage reaction.
2.1.3 Brønsted/Lewis acid interface.
Growing trends to substitute metallic catalysts with nonmetallic catalysts have motivated researchers to explore Brønsted acids as effective alternatives. As a matter of fact, synthesis of predominant Brønsted acidic sites is difficult as most acidic materials have both Brønsted and Lewis acidic sites.47–49 Interestingly, such formation is beneficial for tandem C–H cleavage and dehydration reactions during glycerol conversion to lactic acid.
Brønsted/Lewis acid interface is crucial for dehydration of lactic acid to AA, which will be heavily discussed in later sections. Brønsted acids can exchange metallic cations during activation of lactate molecules, generating stabilized intermediate species, while Lewis acid can promote formation of C
C bond under elevated temperatures.50–58
We should not neglect the band gap shift induced by the presence of heteroatoms, such as non-metallic P, B, S as well as metal cations in modified Lewis acid catalysts.59 The presence of impurities in metal oxides (often characterized as Lewis acids) upshifts Fermi levels (Fig. 7(b)), and generates more reactive surface due to enhanced electronic conductivity of semiconductor materials.
2.2 Interfacial catalysts for glycerol conversion to lactic acid
Synthesis of lactic acid from glycerol involves catalytic C–H bond cleavage as key reaction step (see Fig. 4(a)),27,28,32 which has been recognized extensively. There exist some controversies over the role of alkaline promoters during C–H bond cleavage reactions.31,60–65 To our best knowledge on experimental and computational studies, alkaline species act as catalysts for C–H cleavage, under hydrothermal conditions. However, when reaction temperature is lower than 250 °C, alkaline promoters have often been to be effective in facilitating metal-catalyzed C–H cleavage reactions.66
2.2.1 Bimetallic catalysts.
It is not surprising to find in literature that, Pt and Au are most commonly used materials for dehydrogenation of glycerol to glyceraldehyde.23 In general, many bimetallic catalysts show enhanced activity for C–H bond cleavage of glycerol to glyceraldehyde. Examples include supported PtAu, PtCo and PtSn catalysts.66
2.2.2 Metal–acid composites.
For non-noble metal catalysts, Cu-based materials seem to outplay other candidates, mainly in terms of selectivity. According to literature survey, immobilization of Cu species on metal oxides (metal–acid interface) and low dimensional supports, and morphological manipulation are widely reported in existing literature. Examples include two-dimensional CuNi on layered double hydroxides (LDH), Cu/LDHs, Cu/CoO and Cu/graphene oxide.67 Overall high lactic acid selectivity of 90+% can be achieved over Cu catalysts under inert conditions.
2.2.3 Brønsted/Lewis acid composites.
Lewis acid promoters have also been found to be effective for facilitating tandem C–H cleavage and Cannizzaro rearrangement reactions (Fig. 4(b)).13,23 Mixed metal oxide with dual-acid interfacial catalysis play key roles in tandem conversion of glycerol to lactic acid. The most promising example presented in literature is heteropoly acid.68 However, it is necessary to point out that, limited attention has been paid to base-free synthesis.69 As Lewis acids and relevant hybridized materials can effectively facilitate tandem oxidation, dehydration and Cannizzaro rearrangement reactions, increasing research efforts should be dedicated to this area to obtain environmental ways of producing lactic acid.70
2.3 Interfacial catalysts for dehydration of lactic acid to acrylic acid
The first case on dehydration of lactic acid to AA was dated back to 1960s using metal phosphates and sulfates as catalysts.2,33 Even till today, extensive efforts have been put on developing more efficient phosphate and sulfate-based materials for enhanced performances on dehydration of lactic acid.50–58 But good selectivity toward dehydration against coking is still difficult to achieve to satisfy the need of commercial implementation.
2.3.1 Cation mediated acidic catalysts.
Up to today, main research focus has been primarily focused on modified zeolite and hybridized phosphate materials with remarkable performances (Fig. 5), examples of which include Co/Cu/Fe modified beta zeolites,15 alkali/alkaline earth modified beta zeolite,22,71,72 LiNO3 modified ZSM-5,73 Na2HPO4 and rare earth metal cation modified NaY,47–49 phosphate and sulfate modified MCM-41,74 NaNO3 modified SBA-15,75etc.33–35 Ionic liquids have also been studied for this reaction.76–78 Clearly, modification of interfacial electronic coupling effect, between cation–silica, cation–cation and cation–phosphate/sulfate is important to enhance chemoselectivity for dehydration reactions over other side reactions.
The general strategy for synthesizing effective dehydration catalysts involves modification of surface Brønsted and Lewis acidity/basicity. Because, according to mechanistic study, strong acidic sites often induce decarbonylation and coke formation above 370 °C, leading to irreversible deactivation of catalysts and poor product yield. Modified phosphates and sulfates are also among most popular candidates, as altering the stoichiometry of the crystal often leads to the formation of vacant O or cationic sites.
3. Synthesis of lactic acid from glycerol: chemistry & catalysis
Catalytic conversion of glycerol to lactic acid is achieved through oxidation in the presence of O2, or non-oxidative dehydrogenation in aqueous medium.79–83 This area has been extensively reviewed in the past decade, as it provides an important alternate to replace glucose-based biological conversion route (Fig. 2 and 8).7,23,29–31,66,84 As already mentioned, catalytic dehydrogenation (C–H bond cleavage) of glycerol to lactic acid generates H2 as a valuable co-product. Current efforts are clearly classified into two categories, (a) continuing development of active and durable noble and non-noble catalysts for dehydrogenation reactions in alkaline medium, (b) catalyst and solvent engineering in exploring more effective C–H cleavage and subsequent structural rearrangement in base-free medium.32,85–88
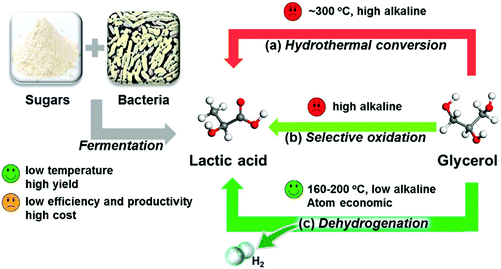 |
| Fig. 8 Oxidation of glycerol via hydrothermal, oxidation and non-oxidative dehydrogenation routes (permission obtained from ref. 60). | |
3.1 Noble metal catalysts
Rational control of desorption step of glyceraldehyde is key for tunable selectivity for lactic acid against glyceric acid (a deep oxidation product).89–91 Experimental work has indicated that, formation of glyceric acid from glyceraldehyde is a competitive reaction with isomerization of glyceraldehyde to dihydroxyacetone, which is the precursor for lactic acid. Current efforts have been focused on the influence of metal composition on tunable C–H cleavage selectivity. Therefore, the fundamentals on tuning adsorption strength of glyceraldehyde on metallic sites, and isomerization rate over acidic sites are crucial for enhanced selectivity towards lactic acid.36–38 Unfortunately in most cases, base promoters are still needed for enhancing isomerization pathway.92–94 Lewis acids, such as oxidized carbon, carbon nitride, TiO2, can also play an important role, because the electronic withdrawing capabilities of those support could alter electronic density over Pt and Au sites, thus shifting reaction pathways to lactic acid.94–96
3.1.1 Metal–acid composites.
Metal–support (Lewis acid) interaction is key to enhance C–H cleavage of glycerol. Representative examples for Pt and Au catalysts are presented in Table 1. The electronic interaction between Pt and supports was also investigated by Yang and Jin recently (Fig. 9(a–h)).60 They found that the electronic coupling effect between PtCo clusters and CeO2 support contributes to red shift of binding energy for Pt species, with two-fold enhancement in activity for dehydrogenation of glycerol. Co and CeO2 both play as electronic mediators for Pt sites. As a result, electronic density at Pt sites was enhanced in the presence of Co2+ and Ce3+. The selectivity for lactic acid is about 80% with 1,2-propanediol (1,2-PDO) and ethylene glycol (EG) as main co-products at 90+% conversion level of glycerol. In another study, Pescarmona and colleagues prepared near atomically dispersed Pt0/Pt4+/Pt2+ catalysts on ZrO2 supports (Fig. 9(l)). Such material displays remarkable conversion (96%) and lactic acid yield (95%) at 160 °C and 2.0 MPa N2.97 Clearly, the Lewis acidic properties of ZrO2 support promote dispersion of Pt elements with electronic deficient active centers. They optimized valence states of Pt nanoparticles, and found that more Pt0 over Pt4+/Pt2+ components favor activity enhancement with almost unchanged selectivity towards lactic acid. The remarkable selectivity of lactic acid is possibly due to the addition of H2 scavenger (cyclohexene). Because H2 formed in situ might also facilitate transfer hydrogenolysis thus formation of lactic acid could be restrained. The presence of cyclohexene consumes H2 generated from C–H cleavage of glycerol, to enhance selectivity towards lactic acid. Catalyst stability still needs to be improved in this area.
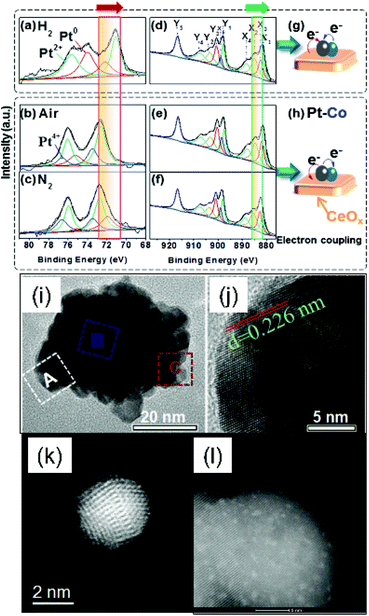 |
| Fig. 9 Catalyst structures for conversion of glycerol to lactic acid, (a–h) electronic coupling in Pt–Co/CeO2 hybrids,60 (i and j) PtAu@Ag nanoparticles,98 (k) AuPt//H-beta zeolite,99 (l) Pt/ZrO2 catalyst.100 | |
Table 1 Performances of noble metal nanocatalysts for glycerol conversion to lactic acid
# |
Catalyst |
Reaction condition |
TOF (h−1) |
X (%) |
S (%) |
Feature |
Ref. |
1 |
AuPt/USY |
160 °C |
— |
80 |
60 |
Twinned particles |
ref. 99 |
0.3 MPa O2 (RT) |
2–4 nm |
Base free |
2 |
PtCo/CeO2 |
200 °C |
1534 |
82 |
80 |
Electronic coupling in Pt–Co |
ref. 60 |
1.0 MPa N2 (RT) |
NaOH |
3 |
Pt/ZrO2 |
160 °C |
995 |
96 |
95 |
Pt0/Pt4+/Pt2+ formation due to electronic withdrawing of ZrO2 |
ref. 97 |
2.0 MPa N2 |
NaOH |
4 |
PtAu@Ag |
0.5 M KOH, N2 |
— |
100 |
18 |
Displacement of Ag with Au and Pt creates more surface defects |
ref. 98 |
5 |
AuCu/CeO2 |
250 °C |
|
87.2 |
76.5 |
AuCu nanorod |
ref. 91 |
H2 |
NaOH |
3.1.2 Bimetallic catalysts.
For compositional and morphological control, Heeres and colleagues reported AuPt/USY catalysts for direct glycerol oxidation to lactic acid in base-free medium.99 They found that the formation of bimetallic AuPt nanoparticles actually induces twinned boundaries, which could be active sites for oxidation reactions. The influence of surface acidity on the synergistic performances needs further attention in this field.
3.2 Non-noble metal-based catalysts
Inexpensive materials include heteropoly acids,101 ZrO2,102 ZnO,103 Cu-based metal oxides104–106 and bimetallic nanoparticles,107–110 Co-based catalysts,111,112 Ni-based catalysts,113–115 alkaline metal oxides.116 The main strategy for designing non-noble catalysts includes manipulation of structural morphology and incorporation of metal with Lewis/Brønsted acidic/basic sites.
3.2.1 Bimetallic catalysts.
Recently, Ni and Cu based metal catalysts are among most popular candidates in literature (Table 2). While Cu materials display high chemoselectivity for C–H bond cleavage, the choice of selecting Ni-based catalysts was inspired by their dual functionalities for both dehydrogenation combined with remarkable activity in catalyzing hydrogenation reactions as significantly cheaper alternatives to noble metals.115 Pescarmona and colleagues found that ceria support tends to atomically disperse bimetallic NiCo species thus catalytic performances can be enhanced. The remarkable selectivity towards lactic acid over NiCo catalysts is partially due to the presence of H scavengers in the system.115 Unfortunately, most current studies have not paid sufficient attention to the electronic coupling behaviors for non-noble metal catalysts.
Table 2 Performances of Ni and Cu catalysts for synthesis of sodium lactate
# |
Catalyst |
Reaction condition |
TOF (h−1) |
X (%) |
S (%) |
Feature |
Ref. |
1 |
NiCo/CeO2 |
160 °C |
13.3 |
91 |
85 |
Atomically dispersed NiCo |
ref. 115 |
2.0 MPa N2 |
NaOH |
2 |
CuBr2 |
155 °C |
— |
72 |
90 |
Nanobranch CuBr2 |
ref. 109 |
NaOH |
3 |
Cu |
230 °C |
— |
71 |
69 |
Cu nanoparticles |
ref. 117 |
NaOH |
4 |
CuO/ZrO2 |
180 °C |
— |
67 |
85 |
Weak Cu2+ and ZrO2 interaction |
ref. 118 |
NaOH |
CuO particles enters the pores of ZrO2 support |
3.2.2 Metal–acid composites.
Cu-Based materials are regarded as one of the most promising inexpensive candidates, because of the poor activity for C–O cleavage but high chemoselectivity for C–H bond rupture. It seems that current interests on developing Cu catalysts, are focused on tuning Cu-promoter/support interaction. For example, Li and colleagues reported branched CuBr2 catalysts with about 90% selectivity towards lactic acid during glycerol conversion.109 The morphology is key for tunable Cu–Br interaction. Zavrazhnov and colleagues conducted vigorous kinetic modeling on Cu catalyzed glycerol dehydrogenation in base medium.117 They found that glycerol molecule and NaOH tend to be activated in different mechanism, thus a combined Power law, Eley–Rideal and Langmuir–Hinshelwood model best represent the trend in experimental studies. In another study, Yin and colleagues investigated the kinetics of Cu catalyzed glycerol hydrogenation to lactic acid in base medium.119 They found that the electronic transfer between Cu and ZrO2 support is critical for tunable reaction rates. Liu and Dong also observed similar electronic transfer effect for CuO/ZrO2 catalysts.118 Manfro and colleagues studied Cu–MgO interaction and confirmed that electronic donating properties of MgO stabilize CuO particles.120 Although Cu dispersion is as low as <10%, the strong electrostatic force enable excellent performances in continuous production of lactic acid (selectivity: 85% at 180 °C).
3.3 Synthesis of lactic acid in base-free medium
Currently, fermentative production of lactic acid has the advantage of very high enantiomeric purity of the product. But the need for disposing calcium sulfate co-produced in equal amounts with lactic acid, has posed a major drawback of existing biotechnological processes. Therefore, chemical synthesis of lactic acid in base-free medium show both technological and economic advantages over the biological route. Two main classes of hybridized catalyst materials, including heteropoly acids and metal–acid hybrid materials, will be critically discussed in this part.
3.3.2 Metal–acid composites.
Huang and Wang correlated Brønsted and Lewis acidity of Ag modified H3PMo12O40 catalysts for glycerol oxidation. It was found that Brønsted acid facilitate oxidation of glycerol to dihydroxyacetones and pyruvaldehyde, while balanced Brønsted and Lewis acidity contributes to the formation of lactic acid.122 The concept of metal–Lewis acid pair catalysts was also studied by Shishido and colleagues for Pt/Nb2O5 catalysts (Fig. 12(a)).123 The acidic sites were measured by layer structured Nb2O5 materials. They found that layered Nb2O5 has larger amounts of Lewis and Brønsted acid sites per weight than conventional Nb2O5 and Nb(OH)5. The strong dual-acid materials promote dehydration and rearrangement reactions during glycerol conversion. The experimental results at different temperature further confirm that, rearrangement of pyruvaldehyde in neutral condition needs to overcome much higher activation barriers, because conversion of dihydroxyacetone at 90 °C does not give lactic acid as the main product. But glycerol conversion at 150 °C show 80% selectivity toward lactic acid in one pot. Although detailed information on metal–acid interaction is still not clear, the tandem catalysis at metal and acid interface is key for improved yield of lactic acid in alkali-free medium.
 |
| Fig. 12 TEM images of solid catalysts for tandem glycerol conversion to lactic acid. (a) Layered Nb2O5 catalyst (permission obtained from ref. 123), (b) nanobranched CuBr2 catalysts (permission obtained from ref. 109), (c) AuPd/CNT catalyst (permission obtained from ref. 124), (d) Au–Sn-USY catalysts (permission obtained from ref. 69), (e) Sn-MCM-41 (permission obtained from ref. 70), (f) Au/CuO catalyst (permission obtained from ref. 125), (g) Ag/Al2O3 catalyst (permission obtained from ref. 126). | |
3.4 Oxidation of glycerol to alkyl lactate
Crude glycerol is produced with approximately 30–60% water. Most attention is being paid to conduct oxidation in aqueous medium. Conversion of glycerol in neutral condition requires sophisticated design of metal–acid pair catalysts, however, often leading to poor chemoselectivity towards lactic acid. One pot conversion of glycerol to lactate esters has attracted increasing attention recently, as production of methyl and ethyl lactate from glycerol actually need formation of lactic acid followed by esterification processes.
This topic is still new in this area. At present, the main strategy for one pot glycerol conversion to alkyl lactate is hybridization of metallic nanoparticles with Lewis acid in methanol or ethanol solvent (Table 3).127,128 Lewis acidity is necessary to transform pyruvaldehyde into lactic acid. In this context, modified zeolite catalysts are extensively investigated in this area. USY and Beta are most popular candidates for supports as tunable Lewis acidity can be easily achieved by doping Sn and other hetero atoms.125,129,130 According to the characterization results, the Lewis acidity caused by the presence of Sn and other heteroatoms leads to coordinated intermediate complexes, which would promote isomerization reactions. This is the key that, weak Lewis acidic centers are favorable for the formation of dehydrated species, which are the precursors for lactate in neutral medium. The formation of such coordinated species is critical for improved selectivity for lactate. Noble metals such as Au and Pd are commonly used to provide metallic centers for oxidation step (glycerol to glyceraldehyde), while dehydration of glyceraldehyde and condensation between lactic acid and alcohols occur in the presence of acidic sites.131–133
Table 3 Oxidation of glycerol to alkyl lactate
# |
Catalyst |
Reaction condition |
TOF (h−1) |
X (%) |
S (%) |
Feature |
Ref. |
1 |
Au/Sn-USY |
Methanol |
94.6 |
88 |
89 |
Electron sufficient SnOx depress Au nanoparticles |
ref. 69 |
0.5 MPa O2 |
160 °C |
2 |
AuPd/CNT |
Methanol |
— |
55 |
75 |
Synergy between AuPd and acidic sites |
ref. 124 |
Sn-MCM-41 |
0.6 MPa O2 |
140 °C |
3 |
Au/CuO |
Methanol |
208 |
74 |
62 |
Au and CuO interaction contributes to α-bond activation of O–H group |
ref. 70 |
Sn-MCM-41 |
3.0 MPa O2 |
140 °C |
4 |
Au/TiO2 |
Methanol |
|
55 |
62 |
— |
ref. 70 |
Sn-MCM-41 |
3.0 MPa O2 |
140 °C |
5 |
Au/CuO |
Methanol |
— |
86 |
60 |
Au–CuO interaction leads to lower Cu2+ reduction temperature |
ref. 125 |
Sn-Beta |
1.5 MPa O2 |
90 °C |
3.4.1 Metal–acid composites.
Lu and colleagues studied Au/CuO catalysts with Sn-Beta catalysts for effective oxidation of glycerol.125 They used copper acetate as precursor to prepare thin CuO layers. H2-TPR characterization suggested that Au–Cu2+ strong interaction leads to unusual electronic transfer from Au to Cu2+. Such interaction weakens Cu–O bond strength, thus reduction temperature of CuO decreases from 330 °C to 279 °C. TEM images further confirmed that such strong electrostatic interaction contributes to finely dispersed Au particles of approximately 3–4 nm. Catalytic conversion of glycerol at 90 °C and 1.5 MPa shows that the synergistic performances induced by Au–Cu2+ strong interaction results in a four-fold enhancement of oxidation activity. The synergy between Au and Sn-Beta zeolite is also important, as dihydroxyacetone is the major by-product during oxidation, indicating that isomerization to form pyruvaldehyde is slow in this system (glycerol conversion: 86%, selectivity of lactic acid: 60% at 90 °C).
Based on the above-mentioned experimental results, it is clear that conversion of glycerol to lactate in alcoholic medium also undergoes three steps, dehydrogenation of glycerol, dehydration and structural rearrangement. While the first reaction is conducted over metallic catalysts, the latter two need acidic catalytic materials. Pérez-Ramírez and colleagues investigated the possibility of glycerol oxidation to lactate over one catalyst.126 Interestingly, oxidation of glycerol to pyruvaldehyde seems to be independent on Lewis acidity of alumina support. It is the Ag–Al2O3 interaction that induces the formation of active Brønsted and Lewis acidic sites for tandem conversion of glycerol. Poor selectivity of lactate is achieved due to low density of Lewis acidic sites on Al2O3 surface.
3.4.2 Bimetallic and metal–acid composites.
Combining the advantages of bimetallic catalysts with metal–acid pairs could synergistically promote oxidation and dehydration step during glycerol conversion. Pescarmona and colleagues reported AuPd/CNT + Sn-MCM-41 catalyst admixtures for one pot glycerol conversion to methyl lactate (Fig. 12(c)).124 They found that well-dispersed bimetallic AuPd catalysts with small particle size facilitate primary oxidation, while surface Brønsted acid group promote dehydration of glyceraldehyde to pyruvaldehyde. Lewis acidic Sn-MCM-41 accelerates rearrangement of pyruvaldehyde with methanol to methyl lactate (glycerol conversion: 88%, selectivity of lactic acid: 89% at 160 °C). Yang and colleagues designed Sn-USY supported Au catalysts. They found that framework Sn leads to formation of Lewis acidic sites in USY structure. Acidity measurement suggested that Au nanoparticles tend to locate at extra-framework of Sn sites, which receive electrons USY. The electron sufficient environment depresses aggregation of Au nanoparticles. The role Sn in the framework of was also studied in details by Huang and colleagues.134 They investigated the role of Brønsted and Lewis acidity induced by incorporation of Sn on dehydration of dihydroxyacetone to pyruvaldehyde. It is shown that structural Sn species enhances the amounts of Brønsted acidity, which is beneficial for dehydration of dihydroxyacetone. But Lewis acidic sites are critical for rearrangement of pyruvaldehyde to lactate. NMR analysis demonstrates that extra-framework Sn species contribute to the formation of Lewis acidic sites. Therefore, effective dehydration and rearrangement of dihydroxyacetone can be achieved at 65 °C with 90% selectivity to ethyl lactate in ethanol medium.
3.5 Summary and outlook
Nanostructured and metal–acid hybrid catalysts are among most popular candidates for catalytic synthesis of lactic acid from glycerol. It is important to mention that, global incentive for sustainable conversion technologies for biomass to renewable chemicals has driven the research efforts from synthesis of lactate salts in base medium, towards base-free oxidation of glycerol in either aqueous or alcoholic medium. Undoubtedly, existing efforts for improving production rates of lactate salts in base medium are clearly shifting towards non-noble metal catalysts such as Ni and Cu. However, the durability of these inexpensive materials is not yet to be fully investigated in literature. Based on experimental studies, it indicates that electronic coupling effect between metal and promoters rather than size of metal particles, is key to contributing enhanced performances for C–H bond cleavage.
(i) Base-free synthesis of lactic acid in aqueous medium suggests that heteropoly acids and metal–acid hybrid catalysts show promising performances. Fundamental understanding on the nature of Brønsted and Lewis acidic sites is crucial for successful implementation of this technology in industry. At present, experimental studies on catalyst design are primarily focused on morphological features of metallic sites, with limited attention paid to metal–acid interaction in hybridized materials. Clearly, more research efforts need to be paid on this topic in future studies.
(ii) Another unaddressed issue which has bottlenecked this area for decade, is how to achieve asymmetrical synthesis of L-lactic acid over D-lactic acid, as the former has wider applications in polymer industry. As for chemical synthesis of lactic acid, this issue seems to be difficult to be addressed using conventional solid catalysts. Alternative strategies such as immobilization of bio-active or organometallic species and formation of unique active sites should be considered in this field for future studies.
4. Dehydration of lactic acid to acrylic acid: chemistry & catalysis
4.1 Design strategy for dehydration catalysts
Different from the reaction involving dehydrogenation of glycerol, conversion of lactic acid to AA does not need a metal catalyst to facilitate the formation of C
C bond. The main reactions for conversion of lactic acid include dehydration, decarbonylation and decarboxylation. Decarboxylation of lactic acid to acetaldehyde and CO2 is the main side reaction. Since the first study in 1958 by Holmen and colleagues, various sulfate, phosphate and modified zeolite based catalysts have been proposed and studied in details.135–138 Acidic sites are necessary for dehydration reactions, strong acidic sites, however often leads to C–C cleavage side reactions. Therefore, the main focus on the rational design of catalysts is to achieve medium or weak acidity of solid catalysts, in order to get good selectivity towards dehydration rather than decarboxylation products.
Tunable acidity is also crucial for improving catalyst stability. This is because decarboxylation induced C–C cleavage produces coke precursors such as acetaldehyde, which might undergo condensation reactions and eventually form aromatics on acidic sites, completely inhibiting dehydration reactions.139–141 Therefore, weakly acidic sites seems to be beneficial to minimize the competing reactions that destroy carboxylic group in lactic acid and maintain long-term stability under elevated reaction temperature (e.g., >350 °C). Furthermore, it is important to emphasize that, basic sites are also needed for selective dehydration reaction. Basic sites could potentially protect the carboxylic group, while the acidic sites activate the α-hydroxyl for the dehydration reaction.19,142–144 This is the underlying reason that, phosphate anions, alkaline, alkaline-earth metal cations are often incorporated into the framework of acidic catalysts.
Therefore, in this section, we will discuss the rational design of dehydration catalysts from the perspective of the nanostructure for acidic/basic sites and molecular catalysis involving C–H and O–H bond activation during dehydration processes.
4.2 Dehydration of alkyl lactate
As already mentioned in the previous sections, oxidation of glycerol in aqueous medium leads to the formation of lactic acid or lactate salts, while lactate esters can be formed in alcoholic medium.145–149 Direct dehydration of lactate esters represents an atomic economical way to produce acrylic esters. Alkali–metal-exchanged zeolite materials, such as NaY is among the most extensively investigated materials for dehydration of methyl lactate to methyl acrylate.136,150,151 Modified NaY materials show improved performances, as metallic cations often alter acidic centers thus reaction pathways for decarbonylation and coking can be restrained.152 Notably, the use of lactate esters as substrates also avoid the unwanted self-oligomerization by induced by lactic acid.153 Mechanistic studies demonstrated that the presence of metallic cations can generate Brønsted acidity in situ, facilitating dissociative adsorption of lactate and generating surface methoxy groups.153,154 Besides Y zeolites, phosphate salts are often hybridized with metal oxide to enhance the dispersion of dehydration sites (see Table 4 for summary of catalyst performances).155,156
Table 4 Oxidation of glycerol to alkyl lactate
# |
Catalyst |
Reaction condition |
TOF (h−1) |
X (%) |
S (%) |
Feature |
Ref. |
1 |
Poisoned NaY |
330 °C |
— |
38 |
95 |
Poisoned Brønsted acidic sites by pyridine |
ref. 153 |
30 wt% aqueous ML |
2 |
NaY |
330 °C |
80 |
∼13 |
50 |
Significant decarbonylation on NaY |
ref. 157 |
30 wt% aqueous ML |
3 |
NaH2PO4/SiO2 |
340 °C |
— |
80 |
29 |
Chain of polyphosphate key for selectivity |
ref. 156 |
Pure ML |
4 |
K2HPO4-Al2(SO4)3/MCM-41 |
410 °C |
— |
98 |
68 |
Formation of K2SO4 and AlPO4 phase on MCM-41 |
ref. 74 |
60 wt% aqueous ML |
5 |
CaPOH |
380 °C |
— |
100 |
35 |
–OH in polyphosphates as active sites |
ref. 159 |
30 wt% aqueous ML |
4.2.1 Modified zeolites (medium/weak acid composites).
Early studies on dehydration of lactate were focused on tunable surface Brønsted and Lewis acidity by introducing various sodium and potassium salts into the framework of zeolites. Huang and colleagues studied the influence of various KX (X: Cl, Br, I) on surface acidity and basicity.151 They found that KI/NaY materials display the strongest basicity among other samples, because loss of I− species during calcination promotes the formation of basic K2O species. Such active sites interact strongly with O species and form a cyclic transition state with lactate molecule.151 As an alternative reaction mechanism, in situ FTIR studies in literature also revealed that the presence of cations such as K+ and Na+ mediated the Brønsted acidity and inhibited decarbonylation pathways by forming relevant lactate salts on catalyst surface.150,151,157
The strong hydrophilicity of parent and modified NaY materials may have detrimental influence on chemoselectivity and catalyst stability. The formation of H2O during dehydration may block the weak Lewis acidic sites thus inhibiting further turnovers, in particular with the fact that lactate esters are much more hydrophobic in comparison with sodium lactate (Fig. 13(a)).154 Based on the experimental studies, it is possible that, weak Lewis acidic sites may selectively promote dehydration reactions, while strong Lewis and Brønsted acidity could accelerate decarbonylation, proton transfer and coke formation due to strong hydrophilicity nature. The presence of Na+ and K+ is important to prevent the reaction pathways for the formation of hydrophobic site due to strong adsorption of ester species.
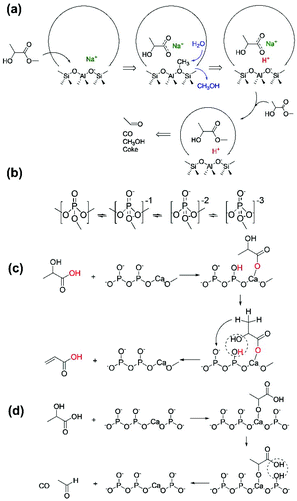 |
| Fig. 13 (a) Proposed mechanisms for dehydration and decarbonylation of methyl lactate (redrawn from ref. 153 and 154), (b) formation of PO4 species (redrawn from ref. 156), (c and d) structure of CaP hydroxyapatite catalysts for dehydration and decarbonylation reactions (redrawn from ref. 138). | |
4.2.2 Phosphates (cation-acid composites).
Clearly, traditional approaches using NH3 and CO2 desorption measurement attempting to finely tune surface properties, cannot reveal the nature of reaction on the level of molecular catalysis.158 To overcome the intrinsic issues caused by the blockage of water molecules, Loridant and colleagues prepared alkaline earth phosphates as inexpensive catalytic materials for conversion ethyl lactate.159 Surface characterization show that orthophosphates and pyrophosphates leads to weakened PO–H bond. Experimental studies confirm that alkaline earth mono and dihydrogenophosphates or polyphosphates are active sites for dehydration reactions. Such unique structural properties tend to enhance hydrolysis of ethyl acrylate into AA and ethanol, over in situ formed Brønsted acidic sites, preventing polymerization (coke formation) and C–C cleavage side reactions. With regard to the possible rate limiting step for conversion of alkyl lactate, the formation of sodium lactate in situ is not believed to be the rate limiting step. Acid catalyzed dehydration or desorption of acrylate are highly possible to be the slowest step, although the dynamic equilibrium between sodium and alkyl lactates determines the chemoselectivity toward AA or ester.154
The nature of Na+ and phosphate anions for activation of C–OH groups was studied by Wang and colleagues.160 Proton transfer involved between the reaction molecules and the active sites is supposed to be confined to the terminal P–OH and P
O groups of the terminal (HO-PO2Na) units. It is strongly believed that the terminal and internal P–OH groups could be two key sites for H transfer reactions. The “methoxyl” further donates one proton to the P
O group and dissociates from the catalyst surface, which regenerates the active site and leads to the formation of acrylate. Wang and colleagues also found that the loading of NaH2PO4 influence the surface acidity on SiO2, because the extent of condensation of phosphate determine the surface ratio of silica surfaces, which could catalyze lactate into decarboxylation products (Fig. 13(b)).156 This is because strong acidity of phosphate promotes C–C cleavage rather than dehydration reactions. This is the main reason that excess Brønsted and Lewis acidity is not favorable for dehydration reactions. Excess coverage of phosphate species however could lead to poor surface area and pore volume.
Wang and Tan studied K2HPO4 and Al2(SO4)3 modified MCM-41 materials. The two precursors react with each other and form AlPO4 and K2SO4 phases on the surface of support.74,161 They found that the acid/base density is strongly dependent with K2HPO4/Al2(SO4)3 ratio. Reaction between the two precursors generates H+ as strong Brønsted acidic species, and formation of K4P2O7 through condensation as medium basic sites. The presence of AlPO4 and K2SO4 phases alleviate the total acidity and basicity. The optimal ratio for acid/base sites is 1.9, which are different from other reports, indicating dehydration of methyl lactate involves cation induced formation of methyl group and lattice oxygen facilitated H transfer reactions. Therefore, the activation energy might be reduced on the surface of bifunctional materials. Chang, Halligudi and Han reported Ca3(PO4)2–Ca2(P2O7) nanocomposites for dehydration of methyl lactate (Fig. 14(b)).56 Different from zeolite or silica supported phosphates, Ca3(PO4)2–Ca2(P2O7) show both acidity and basicity. This could mediate some of the side reactions due to the uncontrollable formation of acidity sites on catalyst surface. They found that ratio of Ca3(PO4)2/Ca2(P2O7) affects the acidity–basicity, which is key for enhanced properties of dehydration reactions.
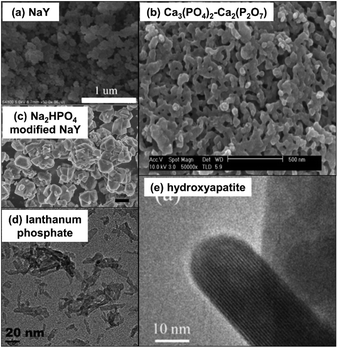 |
| Fig. 14 (a) NaY catalyst (permission from ref. 47), (b) Ca3(PO4)2–Ca2(P2O7) nanocomposites (permission from ref. 56), (c) Na2HPO4 modified NaY catalyst (permission from ref. 21), (d) lanthanum phosphate nano-rods (permission from ref. 50), (e) hydroxyapatite catalyst (permission from ref. 139). | |
4.3 Dehydration of lactic acid
4.3.1 Modified zeolites (weak acid/base pairs).
Direct dehydration of lactic acid or sodium lactate have also been widely studied over modified acidic catalysts. The most general strategy for improving chemoselectivity toward dehydration rather than decarbonylation and decarboxylation is doping foreign ions to modify the nature of acidic sites in zeolites.48,49,52,73,162,163 Performances of various solid catalysts for dehydration of lactic acid are presented in Table 5. For example, Zhang and co-workers studied phosphate doped ZSM-5 zeolite for 97% conversion of lactic acid to 78% selectivity of AA at 350 °C.135 It is interesting to find that, while NaOH treated ZSM-5 materials show poor surface area due to pore blockage. But subsequent impregnation of Na2HPO4 hardly causes substantial damage to the structure of ZSM-5. Structural analysis showed that surface acidity has been mediated owing to the presence of Na2HPO4 species. However, experimental results showed that selectivity of AA is not dependent with the modified ratio of medium/weak sites. New mesopores were also created by NaOH treatment, which may favor the incorporation of Na2HPO4 into the inner wall. Therefore, the chemoselectivity has been shift from more decarbonylation products to AA (dehydration). But the underlying reason still need further experimental investigations. The role of Na2HPO4 species on modifying surface acidity and basicity has also been investigated in details by Ji and Au.21,47 The presence of Na2HPO4 species on NaY surface almost completely remove acidity sites. In addition, the presence of Na+ on the surface facilitate the in situ generation of sodium lactate during dehydration step, thus internal –OH and terminal C–H group can be activated on relatively basic sites. As a result, selectivity for acetic aldehyde is minimized from 22% to <5%, with increased AA formation from 35.5% to 71% at 340 °C.
Table 5 Dehydration of lactic acid to AA
# |
Catalyst |
Reaction condition |
X (%) |
S (%) |
Feature |
Ref. |
1 |
Phosphate doped ZSM-5 |
350 °C |
97 |
78 |
Phosphate immobilized within mesopores |
ref. 135 |
30 wt% aqueous LA |
2 |
Ba/NaY |
370 °C |
100 |
45 |
Medium basicity key for high selectivity |
ref. 142 |
38 wt% aqueous LA |
LHSV: 3 h−1 |
3 |
KCaNa/NaY |
350 °C |
100 |
83 |
Ion exchange of Ca2+ with proton leads to formation of CaCO3 during catalyst regeneration |
ref. 19 |
20 wt% aqueous LA |
LHSV: 3 h−1 |
4 |
K/NaY |
320 °C |
99 |
50 |
K+ as electronic modulator |
ref. 22 |
29 wt% aqueous LA |
LHSV: 3 h−1 |
5 |
Na2HPO4/NaY |
340 °C |
93 |
77 |
Na2HPO4 effectively remove acidity sites |
ref. 47 |
34 wt% aqueous LA |
6 |
Na2HPO4/NaY |
340 °C |
78 |
72 |
HPO42− adjacent to Na+ interact with OH entities |
ref. 21 |
34 wt% aqueous LA |
LHSV: 2.27 h−1 |
7 |
KNa/ZSM |
360 °C |
96 |
80 |
Charge compensation of K+ in AlO4 anions modify surface basicity |
ref. 20 |
36 wt% aqueous LA |
WHSV: 2.1 h−1 |
8 |
K/ZSM-5 |
365 °C |
95 |
76.5 |
Balanced Lewis acidity/basicity |
ref. 72 |
40 wt% aqueous LA |
WHSV: 2.1 h−1 |
9 |
CsNa/Beta-Y |
360 °C |
97 |
70 |
Reduction of acidity by Cs+ and Na+ |
ref. 71 |
35.7 wt% aqueous LA |
WHSV: 2.1 h−1 |
10 |
NaNO3-SBA-15 |
370 °C |
91 |
41 |
NaNO3 (104) and (113) facets |
ref. 75 |
34 wt% aqueous LA |
11 |
Hydroxyapatite |
350 °C |
∼90 |
65–73 |
Aliphatic and aromatic growth of coke on catalyst surface |
ref. 139 |
40 wt% aqueous LA |
12 |
Hydroxyapatite |
375 °C |
100 |
60 |
Ca/P ratio determines morphology and selectivity |
ref. 138 |
50 wt% aqueous LA |
WHSV: 3 h−1 |
13 |
Hydroxyapatite |
375 °C |
100 |
74 |
Both Na+ content and Ca/P ratio determine morphology and selectivity |
ref. 55 |
50 wt% aqueous LA |
WHSV: 3 h−1 |
14 |
Hydroxyapatite |
360 °C |
74 |
62 |
Ca/P ratio determines the ratio of acidity/basicity and selectivity |
ref. 33 |
(Ca(NO3)2–(NH4)2HPO4 |
35.7 wt% aqueous LA |
WHSV: 2.1 h−1 |
15 |
Hydroxyapatite doping Na+ |
350 °C |
90 |
78 |
Na+ and Ca2+ as charge compensating pairs for H+ |
ref. 35 |
38 wt% aqueous LA |
16 |
Hydroxyapatite |
380 °C |
76 |
45 |
— |
ref. 143 |
Ca10(PO4)6(OH)2Sr10(PO4)6(OH)2 |
38 wt% aqueous LA |
17 |
Hydroxyapatite |
400 °C |
99.7 |
76 |
— |
ref. 51 |
Ba2P2O7 |
38 wt% aqueous LA |
18 |
Sr3(PO4)2 + H3PO4 |
400 °C |
90 |
72 |
Sr3(PO4)2 + H3PO4 show acid–base pair features |
ref. 144 |
20 wt% aqueous LA |
19 |
BaSO4 |
400 °C |
100 |
82 |
Acidity/basicity ratio: 5/7 show optimal performance |
ref. 165 |
20 wt% aqueous LA |
It is generally accepted that phosphate anions can act both Lewis acidic and basic sites for liberating water molecules during dehydration reactions. But alkali- and alkaline earth-metal cations modified zeolite catalysts often exhibit different kinetic behaviors for activation of lactic acid. This is because that cations tend to coordinately modify the preexisting Brønsted acidic sites by altering polarity of adjacent Al3+ in framework. The relatively large cation replaces H+ and Na+ in the framework is enthalpy favorable. But such modification unavoidably changes the surface electronic density at lattice O. Therefore, Huang and colleagues also demonstrated that the nature of cation species is also critical for improving chemoselectivity for dehydration reactions. They modified NaY with various alkaline earth metal ions including Mg2+, Ca2+, Sr2+ and Ba2+.142 They have ascribed the varied performances for dehydration of lactic acid to surface basicity after incorporating those cations. The amphoteric properties of lattice oxygen determines the nucleophilic nature of catalysts. CO2 desorption profiles indicated that medium basicity sites (240–320 °C) should be the main active sites for the formation of AA. Since oxygen sites provide main basicity, it is found that cation-oxygen distance increases with cation radius: Mg2+ < Ca2+ < Sr2+ < Ba2+. In addition, the presence of cations with much larger radius than H+, could modify the electronic density of framework O close to the extra-framework cations, inducing weakened bonding between lactic acid and acidic sites.19 Therefore, the modified chemisorption properties of zeolite catalysts show preferably good selectivity for dehydration reactions rather than decarbonylation reactions catalyzed by strong acids.
Xu's group studied the influence of alkaline cations on surface basicity of ZSM-5 and beta zeolites (Fig. 15(a)).20,71 They also confirmed that the presence of relatively larger cations such as K+ improves both conversion and selectivity for AA. The presence of K+ could interact with surface silanol group and adsorbed water, leading to displacement of protons with K+, contributing to much higher basicity compared with original silanol sites. This is the main difference between silica supported weak Lewis acidic catalysts and phosphate materials. However, one might ignore the fact that the type of cages in aluminsilicates also affects the charge compensation when alkaline cations are presents in the framework.20 Therefore, a balance should be achieved for weakly basic sites and sufficient charge compensation in AlO4− anions to maintain good selectivity toward dehydration rather than C–C cleavage. They also studied the influence of electrostatic potential of Cs+ and Na+ modified beta zeolite on acidity/basicity and chemoselectivity of AA. Overall medium and weak acidic and basic sites are beneficial for selective formation of AA.
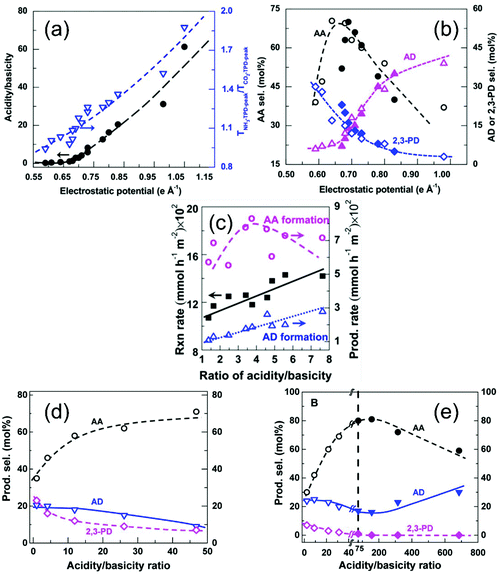 |
| Fig. 15 Influence of surface properties on catalytic performances for dehydration of lactic acid. (a) Influence of electrostatic potential on acidity/basicity and selectivity of AA (permission obtained from ref. 71), (b and c) surface ratio of acidity/basicity for hydroxyapatite on activity and product selectivity (permission obtained from ref. 33). (d and e) Acidity/basicity ratio on product selectivity KNa-Beta and KNa-ZSM-5 zeolites. | |
Similar observation was also achieved by Chen and colleagues.72 In their work, ZSM-5 zeolites were modified with alkali metal cations (Li+, Na+, K+, Rb+, and Cs+). As radius of cations increases, acidity of ZSM-5 decreases significantly. Among all modified ZSM-5 samples, the surface basicity only increases slightly when doping alkali metal cations. KZSM-5 catalyst displays 91% conversion of lactic acid at 350 °C with 70.3% AA selectivity. Compared the acidity and basicity before and after ion exchange with alkali metal cations, it is found that Brønsted acidic sites almost completely disappear, while Lewis acidity and basicity are enhanced slightly. Based on the above mentioned studies, it is clear that the strong adsorption of lactate species could potentially shift the dynamic equilibrium towards kinetically unfavorable state,141 when electronic reconfiguration of lactic acid molecule inhibit decarbonylation due to weakened acidic sites.
Most experimental studies have been focused on dehydration of commercial lactic acid rather than crude lactic acid. Jaimes and colleagues investigated the performances of several modified NaY catalysts for conversion of lactic acid derived from sugarcane molasses.164 Lactic acid with 152 g L−1 concentration was derived for dehydration reactions. KBr/NaY, KI/NaY and Ca3(PO4)2/NaY display different performances, where KI/NaY and Ca3(PO4)2/NaY both show good tolerance to impurities in crude lactic acid. KI/NaY catalyst show a 90% conversion of lactic acid and 15% selectivity for AA.
4.3.2 Modified mesoporous catalysts (Brønsted/Lewis acids/bases).
For neutral silica materials, doping alkali cations has also been widely accepted for an effective strategy. This is because post-treatment of impregnated alkali-doped silica enable generation of strong basic oxide species such as Na2O and K2O for dehydration reactions.75 Previous results have already confirmed that sodium ion in catalyst structure can be transferred to lactate intermediates to facilitate dehydration reactions.
4.3.3 Modified hydroxyapatite catalysts (Lewis acids).
Similar to Ca3(PO4)2–Ca2(P2O7) materials, where both acidity and basicity coexist, calcium hydroxyapatite materials often contain both weak acidic and medium basic sites in crystal phases, therefore regarded as promising candidates for dehydration reactions. Because weak acidity and medium basicity could coordinately accelerate dehydration reactions. In a typical stoichiometric hydroxyapatite structure, O2− atoms in –OH groups often interact strongly with Ca2+ cations to form a triangle structure. However, excess or substoichiometric doping of cations create defected sites to maintain overall charge balance in the distorted framework. Missing cations often lead to oxygen defects in such triangle structure, which display a Lewis acid-type properties. In general, calcium modified hydroxyapatite materials display a Ca/P atomic ratio of 1.67 as single crystal. Therefore, two strategies have often been applied, one involving structural defects with non-stoichiometric cation content, while the other focused altered acid/base ratio due to doping of foreign cations with larger radius.
Alkaline-earth phosphate catalysts materials were studied for dehydration of lactic acid by Loridant and colleagues.137 They compared the performances of CaHPO4 and SrHPO4 at 170–380 °C. While dilactide is the main product in the absence of solid catalysts, AA, acetaldehyde and CO are main products over the phosphate materials. Similar to the case of alkaline metal cation modified catalysts, IR spectra of used catalysts suggested that there also exists a cation transfer from surface of catalysts to lactate molecule, promoting dehydration reactions. But how to control the purity of phosphate species still remains a grand challenge. In another study, Dongare and Umbarkar showed that the content of Na+ and ratio of Ca/P significantly affect the selectivity for dehydration reaction.55,138 With Ca/P ratio decreasing from 1.9 to 1.3, hydroxyapatite rod morphologies become more favorable. Their studies employed FTIR spectra to probe the surface active sites for C–OH bond activation. Typically, the detection of P–O stretching for PO43− species and –OH groups confirm the existence of hydroxyapatite species.138 Conversion of lactic acid reached 100% at 375 °C with 60% selectivity for AA. Again, carbonyl stretching peaks for calcium lactate was observed in IR spectra, suggesting that Ca2+ interact with lactic acid and form seven member ring to activate internal –OH group in the molecule of lactic acid. Mechanistic studies further show that phosphate groups tend to activate internal –OH while Ca2+ active carboxylic group. Therefore, optimal ratio of Ca/P is important.
Clearly, the ratio of Ca/P reflects the surface oxygen deficiency in hydroxyapatite catalysts. Xu's work on hydroxyapatite also demonstrated that the ratio of Ca/P is important to influence the ratio of surface acidity/basicity.33 The correlated the catalytic activity and selectivity for AA and acetic aldehyde with acidity and basicity. When Ca/P ratio is 1.62, hydroxyapatite catalyst displays optimal performances with 74% conversion of lactic acid and 71% selectivity for AA. The volcano-type dependence for the production rate of AA and acidity/basicity ratio reveals the nature of cooperative acid–base catalysis for selective dehydration.
Matsuura and Yanagisawa reported a series of selective dehydration hydroxyapatite catalysts containing tunable Ca/P ratios.35 They used NaOH as precipitation agent and modified the ration of Ca/P by different precursor concentrations. However, one might ignore the fact that both Na+ and Ca2+ are present in the structure of hydroxyapatite catalysts. They found that the cooperative catalysis by both of the cations induces the occupation of Na+ at Ca2+ deficient sites. This structural evolution is strongly believed to promote charge compensate interstitial H+, which further favors attachment of the proton to internal –OH to form H2O molecules. Such behaviors are not well reflected in basicity measurement. But acidity profiles agree very well with the ratio of Na+/Ca2+ in catalysts. The catalyst gave 90% conversion of lactic acid and 78% selectivity for AA, which is almost the highest value for hydroxyapatite-type catalysts.
Onda studied different types of hydroxyapatite catalysts with various cations and anions.143 The comparison of Ca10(PO4)6(OH)2, Sr10(PO4)6(OH)2, Pb10(PO4)6(OH)2, Ca10(VO4)6(OH)2 and Sr10(VO4)6(OH)2 catalyst showed that basic catalysts are favorable for conversion of lactic acid. But Ca10(PO4)6(OH)2 and Sr10(PO4)6(OH)2 with balanced acidic and basic sites show much higher yield of AA (conversion: 72–76%, selectivity: 38–45%). The performances of Sr-based phosphate catalysts were studied by Tang and colleagues.144 They showed that Sr3(PO4)2 catalysts immobilized with small amounts of H3PO4 display best performances. It is important to mention that Sr3(PO4)2 materials display weak acidity and poor conversion of lactic acid. But combined Sr3(PO4)2 with H3PO4 show both acidity and basicity exhibit 90% conversion and 70% selectivity for AA.
Other phosphate catalysts, including lanthanum phosphates were also synthesized with controlled morphologies for this reaction. Wang and colleagues prepared lanthanum phosphate nano-rods using butylamine as template agent. They found that the concentration of the template has s strong influence on the agglomeration of lanthanum phosphate nano-rod. It is also proposed that butylamine can react with surface P–OH group on the nano-rod. The electrostatic interaction between butylamine and lanthanum phosphate causes the formation of La2O3 phase. Such surface coordination also induces electronic transfer between O 2p and La 4f orbitals. Such electronic reconfiguration also leads to tunable acidities. For example, as ratio of butylamine/lanthanum phosphate increases, concentration of acidity sites decrease significantly.
The morphological evolution of lanthanum phosphate catalysts also contributes to enhanced surface basicity. IR spectra suggests that –OH species attached on phosphorous atoms show OH− properties in the lattice, which intrinsically enhance surface basicity for dehydration reactions. Based on the experimental studies on hydroxyapatite catalysts, the cations such as Ca2+ and La3+ tend to coordinate with lactate species to avoid unwanted activation of carboxylic group for C–C cleavage, thus adjacent acidic –OH group could selectively promote dehydration reactions.33,138,144
4.3.4 Other novel catalysts.
Other anion species such as sulfates also show good promotional effect for dehydration reactions. Tang and colleagues studied the influence of interplanar spacing of (121) on surface acidity and basicity of BaSO4.165 They prepared the materials using various precipitation agents such as aqueous ammonia, ethylenediamine and butylamine. The sample prepared by aqueous ammonia show acidity/basicity ratio of approximately 5/7, which show 100% conversion of lactic acid with 82% at 400 °C. The authors ascribed such remarkable performance to lattice defects in (121) facet. The escaped cations are electro-positively charged thus often acting as Lewis acid, while electro-negatively charged vacancies can donate electrons and act as basic sites for catalytic reactions. Low acidic/basic site ratio, although contributing to high conversion of lactic acid, also unfavorably promoting decarbonylation reactions (possibly following alternative mechanism from acid-catalyzed decarbonylation).54 Again, this work demonstrated that balanced acidity and basicity is crucial for high yield of AA. The types of precipitation agent, pH values of precipitation and calcination temperature are critical factors altering surface acidity and basicity ratios.
Bouwman and coworkers studied a very interesting system, where catalytic cracking of lactide and poly(lactic acid) is conducted under mild conditions, with 58% yield of AA (Fig. 16).166 Conventional processes for dehydration of lactic acid is carried out at 300–400 °C, which often induces side reactions such as decarbonylation, thus leading to poor selectivity toward AA. Nucleophile agents such as tetrabutylammonium bromide (TBAB) is used as promoter, with sulfonic acid or 3-bromopropionic acid is used as acidic catalyst and create a water-free environment (130–150 °C).
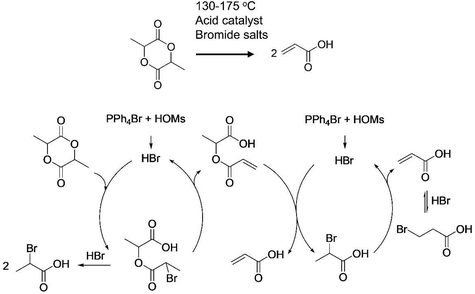 |
| Fig. 16 Plausible mechanism of degradation of lactide to AA.166 | |
4.4 Mechanistic studies
Xu and colleagues conducted kinetic modeling and found that the in situ generation of Brønsted acid sites on NaY leading to acetaldehyde and coke formation, also unfavorably causing suppression of activity of Lewis acidity sites for lactate dehydration.154 The presence of surface H2O is critical for the generation of Brønsted acid. Future improvement of NaY catalysts for dehydration of lactate should be focused on restraining the in situ generation of Brønsted acid using effective inhibition agents.157,158 Control studies on surface poisoning of acidic sites with pyridine species suggest that, inhibition of bulky acid/base complexes on NaY surface prevent coking reactions.153
Traa and colleagues proposed an alternative mechanism to understand the possible cause for side reactions on alkaline cation modified NaY catalysts (Fig. 17(a)).141 They found that high oxygen charge on NaY surface could induce a considerable number of lattice oxygen sites to act as nucleophile agents. Therefore, the Brønsted acidic sites in the zeolite and protons could form a dynamic equilibrium for dehydration and decarbonylation reactions. Relatively less negatively charged oxygen species could contribute to inhibition of decarbonylation reactions. Highly negative charged oxygen sites tend to activation carboxylic group of lactic acid, where medium strong nucleophilic tends to selectively activation -OH and terminal C–H group in the molecule of lactic acid.
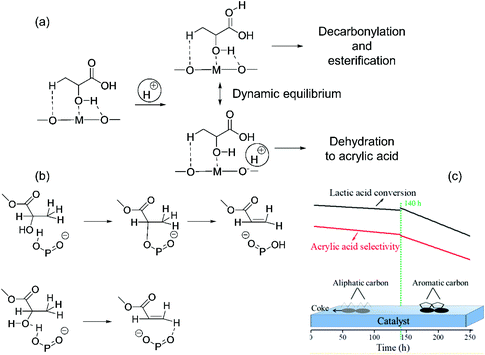 |
| Fig. 17 (a) Dynamic equilibrium of activated lactic acid on acid/base catalysts,141 (b) schematic reaction mechanism for methyl lactate conversion to sodium polyphosphate catalyst,160 (c) proposed deactivation mechanism on hydroxyapatite catalyst.139 | |
Huang and Wang studied the promotional effect of K+ cations on dehydration reactions using in situ characterization techniques.167 IR spectra revealed that C
O stretching mode of lactate salts is the evidence of α-OH activation, agreeing well with DFT results.168 The dried sample of lactic acid in KBr wafer also leads to the formation of potassium lactate, as confirmed in IR spectra. However, there also exist a dynamic equilibrium of lactate salt and lactic acid during direct dehydration of potassium lactate. The rehydration of potassium lactate is key for the formation of lactic acid, which might undergo polymerization and decarbonylation reactions.
Wang and Tan studied the possible deactivation mechanism on hydroxyapatite catalysts (Fig. 17(c)).139 They found the formation of coke undergoes two stages: aliphatic carbon and aromatic carbon growth. Fundamental understanding on the deactivation mechanism on molecular level is very difficult. They employed NMR method to identify carbon species on spent catalysts, in order to probe plausible mechanism for the formation of coke on catalyst surface. The evolution of signal strength for aliphatic and aromatic carbon nuclei suggest that aliphatic species are the precursor for aromatic cokes. However, whether the coke is formed preferably on acidic and basic sites are still not clear. Surface characterization of spent catalyst suggested that the formation of coke does not chemically alter phase purity, but partially blocking both acidic and basic sites. But measurement of acid–base strength indicated that strong acidic and basic sites both contributes to decarbonylation reactions, which provide precursors for coke formation.
Wang and Borgna studied the possible deactivation mechanism of KCa modified NaY zeolites.19 It is found that ion exchange of Ca2+ during activation of lactate molecule leads to phase segregation of Ca2+ from bulk phase, leading to the formation of CaCO3 during catalyst regeneration. Such structural evolution eventually cause performance deterioration. Therefore, finding an effective approach to stabilize the cations in zeolite framework should be the focus of future study.
It is also important to know that the dimer of lactic acid may cause ambiguous detection of AA, resulting in overestimation.169 The degradation of lactide is found to follow this mechanism: (a) activation of lactide involves a carbo-cationic intermediate. An E2 mechanism with bromide ions acting as a weak base is more likely to be plausible, leading to the formation of hypothetical oxiranone intermediate. (b) Once dehydration reaction occurs, transformation of one equivalent of lactide into two AA, in nature, is catalytic cracking by H+ and Br− ions. The key step is involving nucleophile attack of carbon atom in aprotic environments. We need an acidic and strong leaving group, thus Br− ion is more suitable than Cl− ion for this reaction.
4.5 Summary
Numerous literature results have already confirmed the critical role of acid/base pairs in selective dehydration of lactic acid to AA. Experimental studies on the mechanistic aspect of dehydration reactions demonstrated the essence of cations in activating lactate molecules for C–O bond cleavage against C–C bond rupture. With respect to surface characterization, the classic characterization technique such as TPD and IR is still heavily used to estimate the surface acidity and basicity of catalytic materials. Kinetic studies revealed that medium acidity and basicity is optimal for catalytic activity and selectivity toward AA. However, there is lack of fundamental understanding on the nature of acidic and basic sites at lattice level. Surface engineering to precisely control the number of acidic and basic sites still remains a grand challenge. Therefore, continuing efforts should be dedicated to tailored structures for both acidic and basic sites to achieve optimal activity and selectivity.
5. Concluding remarks and outlooks
In the context of searching resource-sufficient technologies for sustainable manufacture of acrylic acid and derivatives, it is strongly believed that glycerol can serve as a promising starting material over crude oil and shale gas feedstocks. Considering the chemistry for aqueous medium oxidation and dehydration reactions over energy intensive gas-phase oxidation and dehydration, glycerol–lactic acid route seems to outstand other conversion routes in terms of atom economics. In this review article, the reaction chemistry involved in glycerol oxidation to lactic acid and further dehydration of lactic acid to acrylic acid, has been critically discussed with various conceptual design of hybridized catalyst materials.
For glycerol conversion to lactic acid, catalytic C–H bond activation of glycerol and structural rearrangement of intermediates to form lactic acid are found to be metal-determined and acid/base promoted reactions, respectively. The morphological and electronic effects in nanoparticle catalysts are key for improving activity and selectivity towards C–H cleavage in alkaline medium. Alternatively, metal–acid/base interaction is crucial for tandem glycerol conversion to lactic acid in base-free medium under mild conditions. This part of study requires extensive efforts for further enhancing the overall activity for both dehydrogenation and structural rearrangement reactions.
Dehydration of lactic acid is not a new topic. But the competing reactions between dehydration and decarboxylation at elevated temperatures demand sophisticated design of acidic and basic sites on the surface of solid catalysts. Experimental investigations have revealed the mechanistic aspects on molecular level. However, engineering the lattice structures of Lewis acid/base sites still remains largely unsolved.
Future work should be particular focused on the follow areas (key points summarized in Fig. 18):
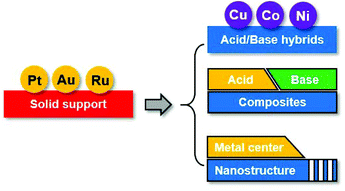 |
| Fig. 18 Development of hybridized materials for effective glycerol conversion to AA. | |
5.1 Replacing noble-based materials with Brønsted acid composites, or metal–acid/base hybridized materials
This is the key to achieve atom economical conversion of glycerol to lactic acid, which is still in the process of commercialization competing with glucose fermentation route. Gaining fundamental understanding on acid-promoted tandem oxidation and dehydration represents the key breakthrough on the development of 2nd generation of glycerol conversion route in base-free medium, more importantly, alleviating the operation and disposal costs due to unfavorable generation of waste salts during acidification of lactates obtained in alkaline medium.
5.2 Lattice engineering for precise control of acidic and basic sites with novel solid acid/base hybridized materials
Despite of decade efforts in synthesizing zeolites, phosphates and sulfates with strong surface acidity, even up to today, rational design of such materials with well-defined Lewis acidity and basicity is still one of the key challenges plaguing catalyst industry. Tailored surface acidity and basicity at lattice level is important to manufacture cost-effective catalysts for dehydration reactions. Computational studies recently revealed that, surface strain is the fundamental driving force to tune the electronic density on acidic or basic sites. Therefore, strain engineering approaches need to be reconsidered for future design of acid/base interfacial catalysts.
5.3 Developing nanostructured solid materials durable in aqueous medium
Long-term stability is still an unsolved issue, as in most experimental studies with continuous reactor, the catalyst life seem to be no less than 50–100 h on stream. Therefore, developing water-tolerant solid materials, via surface modification techniques, could potentially address this issue. In addition, other engineering aspects, such as interfacial mass transfer, surface wetting behaviors and void ratio of catalyst bed also affect the durability of solid catalyst materials.
5.4 Technological and economic consideration
To commercialize the glycerol-to-AA technology, secure and stable supply of crude glycerol and cost-effective power purchase agreement should be considered as priority. As scale of plant plays a key role in determining the economics of glycerol conversion technologies, one should also consider the potential quality of bio-based AA compared with fossil-derived AA. This is because small amounts of unfavorable impurities might be detrimental for current polymer plants.
Author contributions
X. J. drafted the manuscript. K. M. prepared some of the figures. G. Z., M. L. collected literature materials. Y. S., Z. S. and C. Y. provided comments.
Conflicts of interest
The authors declared no competing interests.
Acknowledgements
This work is supported by National Natural Science Foundation of China (22078365, 21706290), Natural Science Foundation of Shandong Province (ZR2017MB004), Innovative Research Funding from Qingdao City, Shandong Province (17-1-1-80-jch), “Fundamental Research Funds for the Central Universities” and “the Development Fund of State Key Laboratory of Heavy Oil Processing” (17CX02017A, 20CX02204A) and New Faculty Start-Up Funding from China University of Petroleum (YJ201601059).
References
- H. T. Truong, S. Rode, D. Roizard, S. Mouzon-Pelletier and S. Tretjak, Dehydration of reactive industrial mixtures by pervaporation: An innovative approach in acrylic esters processes, Sep. Purif. Technol., 2013, 120, 24–34 CrossRef CAS.
- Y. Li and D. Yu, Progress in acrylic acid production from lactic acid, Chem. Ind. Eng. Prog., 2010, 29, 683–689 CAS.
- C. Gao, C. Ma and P. Xu, Progress in biotransformation of bio-based lactic acid, Chin. J. Biotechnol., 2013, 29, 1411–1420 CAS.
- Q. Meng, J. Yang and F. Wang, Advances in the Research of Biological Production of Acrylic Acid, J. Chin. Biotechnol., 2012, 32, 119–127 CAS.
- S. T. Wu, Q. M. She, R. Tesser, M. D. Serio and C. H. Zhou, Catalytic glycerol dehydration-oxidation to acrylic acid, Catal. Rev., 2020, 1–43 Search PubMed.
- E. V. Makshina, J. Canadell, J. van Krieken, E. Peeters, M. Dusselier and B. F. Sels, Bio-Acrylates Production: Recent Catalytic Advances and Perspectives of the Use of Lactic Acid and Their Derivates, ChemCatChem, 2019, 11, 180–201 CrossRef CAS.
- G. M. Lari, G. Pastore, M. Haus, Y. Ding, S. Papadokonstantakis, C. Mondelli and J. Perez-Ramirez, Environmental and economical perspectives of a glycerol biorefinery, Energy Environ. Sci., 2018, 11, 1012–1029 RSC.
- R. K. Grasselli and F. Trifiro, Acrolein and acrylic acid from biomass, Rend. Lincei Sci. Fis. Nat., 2017, 28, 59–67 CrossRef.
- X. Xu, J. Lin and P. Cen, Advances in the research and development of acrylic acid production from biomass, Chin. J. Chem. Eng., 2006, 14, 419–427 CrossRef CAS.
-
KirkOthmer Encyclopedia of Chemical Technology, ed. H. F. Mark, R. E. Kirk, D. F. Othmer, M. Grayson and D. Eckroth, 2007 Search PubMed.
- B. Yin, X. Jin, G. Zhang, H. Yan, W. Zhang, X. Liu, M. Liu, C. Yang and J. Shen, Catalytic Transfer Hydrogenolysis of Bio-Polyols to Renewable Chemicals over Bimetallic PtPd/C Catalysts: Size-Dependent Activity and Selectivity, ACS Sustainable Chem. Eng., 2020, 8(13), 5305–5316 CrossRef.
- D. Sun, Y. Yamada, S. Sato and W. Ueda, Glycerol as a potential renewable raw material for acrylic acid production, Green Chem., 2017, 19, 3186–3213 RSC.
-
X. P. Ye and S. Ren, Value-Added Chemicals from Glycerol, in Soy-Based Chemicals and Materials, ed. R. P. Brentin, ACS Symposium Series, 2014, vol. 1178, pp. 43–80 Search PubMed.
- Y.-D. Long and Z. Fang, Hydrothermal conversion of glycerol to chemicals and hydrogen: review and perspective, Biofuels, Bioprod. Biorefin., 2012, 6, 686–702 CrossRef CAS.
- N. Sobus, B. Michorczyk, M. Piotrowski, L. Kuterasinski, D. K. Chlebda, J. Lojewska, R. J. Jedrzejczyk, P. Jodlowski, P. Kustrowski and I. Czekaj, Design of Co, Cu and Fe-BEA Zeolite Catalysts for Selective Conversion of Lactic Acid into Acrylic Acid, Catal. Lett., 2019, 149, 3349–3360 CrossRef CAS.
- G. M. Lari, B. Puertolas, M. S. Frei, C. Mondelli and J. Perez-Ramirez, Hierarchical NaY Zeolites for Lactic Acid Dehydration to Acrylic Acid, ChemCatChem, 2016, 8, 1507–1514 CrossRef CAS.
- T. M. Aida, A. Ikarashi, Y. Saito, M. Watanabe, R. L. Smith Jr. and K. Arai, Dehydration of lactic acid to acrylic acid in high temperature water at high pressures, J. Supercrit. Fluids, 2009, 50, 257–264 CrossRef CAS.
- J. Zhang, J. Lin and P. Cen, Catalytic dehydration of lactic acid to acrylic acid over sulfate catalysts, Can. J. Chem. Eng., 2008, 86, 1047–1053 CrossRef CAS.
- L. Zhang, D. S. Theng, Y. Du, S. Xi, L. Huang, F. Gao, C. Wang, L. Chen and A. Borgna, Selective conversion of lactic acid to acrylic acid over alkali and alkaline-earth metal co-modified NaY zeolites, Catal. Sci. Technol., 2017, 7, 6101–6111 RSC.
- B. Yan, L.-Z. Tao, A. Mahmood, Y. Liang and B.-Q. Xu, Potassium-Ion-Exchanged Zeolites for Sustainable Production of Acrylic Acid by Gas-Phase Dehydration of Lactic Acid, ACS Catal., 2017, 7, 538–550 CrossRef CAS.
- J. Zhang, Y. Zhao, M. Pan, X. Feng, W. Ji and C.-T. Au, Efficient Acrylic Acid Production through Bio Lactic Acid Dehydration over NaY Zeolite Modified by Alkali Phosphates, ACS Catal., 2011, 1, 32–41 CrossRef CAS.
- P. Sun, D. Yu, K. Fu, M. Gu, Y. Wang, H. Huang and H. Ying, Potassium modified NaY: A selective and durable catalyst for dehydration of lactic acid to acrylic acid, Catal. Commun., 2009, 10, 1345–1349 CrossRef CAS.
- Y. Wang, Y. Xiao and G. Xiao, Sustainable value-added C-3 chemicals from glycerol transformations: A mini review for heterogeneous catalytic processes, Chin. J. Chem. Eng., 2019, 27, 1536–1542 CrossRef CAS.
- M. E. Davis, Heterogeneous Catalysis for the Conversion of Sugars into Polymers, Top. Catal., 2015, 58, 405–409 CrossRef CAS.
- D. Mack, S. Schaetzle, Y. Traa and E. Klemm, Synthesis of Acrylonitrile from Renewable Lactic Acid, ChemSusChem, 2019, 12, 1653–1663 CrossRef CAS.
- D. Sun, Y. Yamada, S. Sato and W. Ueda, Glycerol hydrogenolysis into useful C3 chemicals, Appl. Catal., B, 2016, 193, 75–92 CrossRef CAS.
- S. A. N. M. Rahim, C. S. Lee, F. Abnisa, M. K. Aroua, W. A. W. Daud, P. Cognet and Y. Peres, A review of recent developments on kinetics parameters for glycerol electrochemical conversion - A by-product of biodiesel, Sci. Total Environ., 2019, 705, 135137–135137 CrossRef.
- A. N. Marchesan, M. P. Oncken, R. Maciel Filho and M. R. Wolf Maciel, A roadmap for renewable C2-C3 glycols production: a process engineering approach, Green Chem., 2019, 21, 5168–5194 RSC.
- N. Razali and A. Z. Abdullah, Production of lactic acid from glycerol via chemical conversion using solid catalyst: A review, Appl. Catal., A, 2017, 543, 234–246 CrossRef CAS.
- H. Lia, R. Kotni, Q. Zhang, S. Shunmugavel and S. Yang, Chemoselective Oxidation of Bio-Glycerol with Nano-Sized Metal Catalysts, Mini-Rev. Org. Chem., 2015, 12, 162–177 CrossRef.
- S. A. Zavrazhnov, A. L. Esipovich, S. M. Danov, S. Y. Zlobin and A. S. Belousov, Catalytic Conversion of Glycerol to Lactic Acid: State of the Art and Prospects, Kinet. Catal., 2018, 59, 459–471 CrossRef CAS.
- R. S. Varma and C. Len, Glycerol valorization under continuous flow conditions-recent advances, Curr. Opin. Green Sustainable Chem., 2019, 15, 83–90 CrossRef.
- B. Yan, L.-Z. Tao, Y. Liang and B.-Q. Xu, Sustainable Production of Acrylic Acid: Catalytic Performance of Hydroxyapatites for Gas-Phase Dehydration of Lactic Acid, ACS Catal., 2014, 4, 1931–1943 CrossRef CAS.
- L. Shen, H. Yin, A. Wang, X. Lu and C. Zhang, Gas phase oxidehydration of glycerol to acrylic acid over Mo/V and W/V Cross Mark oxide catalysts, Chem. Eng. J., 2014, 244, 168–177 CrossRef CAS.
- Y. Matsuura, A. Onda and K. Yanagisawa, Selective conversion of lactic acid into acrylic acid over hydroxyapatite catalysts, Catal. Commun., 2014, 48, 5–10 CrossRef CAS.
- C. Zhang, T. Wang and Y. Ding, Influence of Pt Particle Size on the Activity of Pt/AC Catalyst in Selective Oxidation of Glycerol to Lactic Acid, Catal. Lett., 2017, 147, 1197–1203 CrossRef CAS.
- B. S. Sanchez, M. S. Gross and C. A. Querini, Pt catalysts supported on ion exchange resins for selective glycerol oxidation. Effect of Au incorporation, Catal. Today, 2017, 296, 35–42 CrossRef CAS.
- C. Zhang, T. Wang, X. Liu and Y. Ding, Selective oxidation of glycerol to lactic acid over activated carbon supported Pt catalyst in alkaline solution, Chin. J. Catal., 2016, 37, 502–509 CrossRef CAS.
- C. F. Dickens, J. H. Montoya, A. R. Kulkarni, M. Bajdich and J. K. Norskov, An electronic structure descriptor for oxygen reactivity at metal and metal-oxide surfaces, Surf. Sci., 2019, 681, 122–129 CrossRef CAS.
- Z. W. Ulissi, A. J. Medford, T. Bligaard and J. K. Norskov, To address surface reaction network complexity using scaling relations machine learning and DFT calculations, Nat. Commun., 2017, 8, 1–7 CrossRef.
- L. Li, F. Abild-Pedersen, J. Greeley and J. K. Norskov, Surface Tension Effects on the Reactivity of Metal Nanoparticles, J. Phys. Chem. Lett., 2015, 6, 3797–3801 CrossRef CAS.
- H. Xin, A. Vojvodic, J. Voss, J. K. Norskov and F. Abild-Pedersen, Effects of d-band shape on the surface reactivity of transition-metal alloys, Phys. Rev. B: Condens. Matter Mater. Phys., 2014, 89, 115114 CrossRef.
- C. Tsai, K. Chan, J. K. Norskov and F. Abild-Pedersen, Understanding the Reactivity of Layered Transition-Metal Sulfides: A Single Electronic Descriptor for Structure and Adsorption, J. Phys. Chem. Lett., 2014, 5, 3884–3889 CrossRef CAS.
- J. K. Norskov, T. Bligaard, J. Rossmeisl and C. H. Christensen, Towards the computational design of solid catalysts, Nat. Chem., 2009, 1, 37–46 CrossRef CAS.
- J. R. Kitchin, J. K. Norskov, M. A. Barteau and J. G. Chen, Modification of the surface electronic and chemical properties of Pt(111) by subsurface 3d transition metals, J. Chem. Phys., 2004, 120, 10240–10246 CrossRef CAS.
- J. Greeley, J. K. Norskov and M. Mavrikakis, Electronic structure and catalysis on metal surfaces, Annu. Rev. Phys. Chem., 2002, 53, 319–348 CrossRef CAS.
- J. Zhang, Y. Zhao, X. Feng, M. Pan, J. Zhao, W. Ji and C.-T. Au, Na2HPO4-modified NaY nanocrystallites: efficient catalyst for acrylic acid production through lactic acid dehydration, Catal. Sci. Technol., 2014, 4, 1376–1385 RSC.
- J. Yan, D. Yu, P. Sun and H. Huang, Catalytic Dehydration of Lactic Acid to Acrylic Acid over NaY Zeolites Modified with Metallic Ions, Petrochem. Technol., 2011, 40, 476–481 CAS.
- J. Yan, D. Yu, H. Li, P. Sun and H. Huang, NaY zeolites modified by La3+ and Ba2+: the effect of synthesis details on surface structure and catalytic performance for lactic acid to acrylic acid, J. Rare Earths, 2010, 28, 803–806 CrossRef CAS.
- Z. Guo, D. S. Theng, K. Y. Tang, L. Zhang, L. Huang, A. Borgna and C. Wang, Dehydration of lactic acid to acrylic acid over lanthanum phosphate catalysts: the role of Lewis acid sites, Phys. Chem. Chem. Phys., 2016, 18, 23746–23754 RSC.
- C. Tang, J. Peng, G. Fan, X. Li, X. Pu and W. Bai, Catalytic dehydration of lactic acid to acrylic acid over dibarium pyrophosphate, Catal. Commun., 2014, 43, 231–234 CrossRef CAS.
- Z. Zhi-qiang, Q. U. Yi-xin, W. Ji-dong and W. Shui, The Influence of Sodium Phosphate Catalysts with Different Na/P Ratio on the Conversion of Lactic Acid, J. Mol. Catal., 2009, 23, 318–322 Search PubMed.
- G. Fan, C. Tang and X. Li, Highly efficient pyrophosphate / phosphate catalyst for the dehydration of lactic acid to acrylic acid, J. Mol. Catal., 2012, 26, 506–514 CAS.
- J. Peng, X. Li, C. Tang and W. Bai, Barium sulphate catalyzed dehydration of lactic acid to acrylic
acid, Green Chem., 2014, 16, 108–111 RSC.
- V. C. Ghantani, M. K. Dongare and S. B. Umbarkar, Nonstoichiometric calcium pyrophosphate: a highly efficient and selective catalyst for dehydration of lactic acid to acrylic acid, RSC Adv., 2014, 4, 33319–33326 RSC.
- J. H. Hong, J.-M. Lee, H. Kim, Y. K. Hwang, J.-S. Chang, S. B. Halligudi and Y.-H. Han, Efficient and selective conversion of methyl lactate to acrylic acid using Ca-3(PO4)(2)-Ca-2(P2O7) composite catalysts, Appl. Catal., A, 2011, 396, 194–200 CrossRef CAS.
- S. Lyu and T. Wang, Efficient production of acrylic acid by dehydration of lactic acid over BaSO4 with crystal defects, RSC Adv., 2017, 7, 10278–10286 RSC.
- J. Zhang, J. Lin, X. Xu and P. Cen, Evaluation of catalysts and optimization of reaction conditions for the dehydration of methyl lactate to acrylates, Chin. J. Chem. Eng., 2008, 16, 263–269 CrossRef CAS.
-
R. H. Crabtree, The organometallic chemistry of the transition metals, John Wiley & Sons, 2009 Search PubMed.
- G. Zhang, X. Jin, Y. Guan, B. Yin, X. Chen, Y. Liu, X. Feng, H. Shan and C. Yang, Toward Selective Dehydrogenation of Glycerol to Lactic Acid over Bimetallic Pt-Co/CeOx Catalysts, Ind. Eng. Chem. Res., 2019, 58, 14548–14558 CrossRef CAS.
-
J. Carneiro and E. Nikolla, Electrochemical Conversion of Biomass-Based Oxygenated Compounds, in Annual Review of Chemical and Biomolecular Engineering, Vol 10, ed. J. M. Prausnitz, Annual Review of Chemical and Biomolecular Engineering, 2019, vol. 10, pp. 85–104 Search PubMed.
- C. Len, F. Delbecq, C. Cara Corpas and E. Ruiz Ramos, Continuous Flow Conversion of Glycerol into Chemicals: An Overview, Synthesis, 2018, 50, 723–741 CrossRef CAS.
- M. Dusselier, P. Van Wouwe, A. Dewaele, E. Makshina and B. F. Sels, Lactic acid as a platform chemical in the biobased economy: the role of chemocatalysis, Energy Environ. Sci., 2013, 6, 1415–1442 RSC.
- F. Du, H. Wang, X. Jin, W. Deng, C. Li, Z. Ren, H. Yan and B. Yin, Selective Oxidation of 1,2-Propanediol to Lactic Acid Over Synergistic AuCu/TiO2 Catalysts, Catal. Lett., 2019, 149, 1037–1045 CrossRef CAS.
- W. Oberhauser, C. Evangelisti, C. Tiozzo, F. Vizza and R. Psaro, Lactic Acid from Glycerol by Ethylene-Stabilized Platinum-Nanoparticles, ACS Catal., 2016, 6, 1671–1674 CrossRef CAS.
- S. Li, W. Deng, Y. Li, Q. Zhang and Y. Wang, Catalytic conversion of cellulose-based biomass and glycerol to lactic acid, J. Energy Chem., 2019, 32, 138–151 CrossRef.
- G. Dodekatos, S. Schuenemann and H. Tueysuez, Recent Advances in Thermo-, Photo-, and Electrocatalytic Glycerol Oxidation, ACS Catal., 2018, 8, 6301–6333 CrossRef CAS.
- M. Tao, N. Sun, Y. Li, S. Wang and X. Wang, The fabrication of trifunctional polyoxometalate hybrids for the cascade conversion of glycerol to lactic acid, Catal. Sci. Technol., 2020, 10, 207–214 RSC.
- T. Lu, X. Fu, L. Zhou, Y. Su, X. Yang, L. Han, J. Wang and C. Song, Promotion Effect of Sn on Au/Sn-USY Catalysts for One-Pot Conversion of Glycerol to Methyl Lactate, ACS Catal., 2017, 7, 7274–7284 CrossRef CAS.
- Z. Tang, S. L. Fiorilli, H. J. Heeres and P. P. Pescarmona, Multifunctional Heterogeneous Catalysts for the Selective Conversion of Glycerol into Methyl Lactate, ACS Sustainable Chem. Eng., 2018, 6, 10923–10933 CrossRef CAS.
- B. Yan, A. Mahmood, Y. Liang and B.-Q. Xu, Sustainable production of acrylic acid: Rb+- and Cs+-exchanged Beta zeolite catalysts for catalytic gas-phase dehydration of lactic acid, Catal. Today, 2016, 269, 65–73 CrossRef CAS.
- C. Yuan, H. Liu, Z. Zhang, H. Lu, Q. Zhu and Y. Chen, Alkali-metal-modified ZSM-5 zeolites for improvement of catalytic dehydration of lactic acid to acrylic acid, Chin. J. Catal., 2015, 36, 1861–1866 CrossRef CAS.
- G. Zhao, H. Liu, Q. Zhu, Z. Zhang, H. Lu and Y. Chen, Deactivation Behavior of ZSM-5 Zeolites Modified by LiNO_3 in Dehydration of Lactic Acid to Acrylic Acid, J. Mol. Catal., 2017, 31, 152–158 CAS.
- B. Wang, C. Li, Q. Zhu and T. Tan, The effect of K2HPO4 and Al-2(SO4)(3) modified MCM-41 on the dehydration of methyl lactate to acrylic acid, RSC Adv., 2014, 4, 45679–45686 RSC.
- J. Zhang, X. Feng, Y. Zhao, W. Ji and C.-T. Au, Sodium nitrate modified SBA-15 and fumed silica for efficient production of acrylic acid and 2,3-pentanedione from lactic acid, J. Ind. Eng. Chem., 2014, 20, 1353–1358 CrossRef CAS.
- M. Stalpaert, N. Peeters and D. De Vos, Conversion of lactide to acrylic acid by a phosphonium ionic liquid and acid cocatalyst, Catal. Sci. Technol., 2018, 8, 1468–1474 RSC.
-
M. Stalpaert, F. Cirujano and D. De Vos, Tetabutylphosphonium, bromide: A versatile ionic liquid catalyst for the biobased production of butadiene and acrylic acid, Abstr. Pap. Am. Chem. Soc., 2018, 255 Search PubMed.
- J. Nagengast, S. Hahn, N. Taccardi, M. Kehrer, J. Kadar, D. Collias, P. Dziezok, P. Wasserscheid and J. Albert, Highly Selective Synthesis of Acrylic Acid from Lactide in the Liquid Phase, ChemSusChem, 2018, 11, 2936–2943 CrossRef CAS.
- M. R. A. Arcanjo, M. Paniagua, G. Morales, J. Iglesias, J. Melero, I. da Silva Jr., E. Rodriguez-Castellon and R. S. Vieira, Temperature Effect on Pretreatment of the Activated Carbon Support (Pt/AC and Pd/AC) for Glycerin into Lactic Acid, Ind. Eng. Chem. Res., 2020, 59, 14643–14657 CrossRef CAS.
- S. N. M. Saleh and A. Z. Abdullah, Zirconium-Cerium Oxides Supported on SBA-15 as Catalyst for Shape-Selective Synthesis of Lactic Acid from Glycerol, Waste Biomass Valorization, 2020, 7, 1–14 Search PubMed.
- M. Tao, Y. Li, Y. Li, X. Zhang, Y. V. Geletii, X. Wang and C. L. Hill, Heterogenization of polyoxometalates as solid catalysts in aerobic oxidation of glycerol, Catal. Sci. Technol., 2020, 10, 3771–3781 RSC.
- J. Wu, L. Shen, S. Duan, Z.-N. Chen, Q. Zheng, Y. Liu, Z. Sun, J. H. Clark, X. Xu and T. Tu, Selective Catalytic Dehydrogenative Oxidation of Bio-Polyols to Lactic Acid, Angew. Chem., 2020, 59, 13871–13878 CrossRef CAS.
- Z. Xiu, H. Wang, C. Cai, C. Li, L. Yan, C. Wang, W. Li, H. Xin, C. Zhu, Q. Zhang, Q. Liu and L. Ma, Ultrafast Glycerol Conversion to Lactic Acid over Magnetically Recoverable Ni-NiOx@C Catalysts, Ind. Eng. Chem. Res., 2020, 59, 9912–9925 CrossRef CAS.
- R. Abdullah, S. N. M. Saleh, K. Embong and A. Z. Abdullah, Recent developments and potential advancement in the kinetics of catalytic oxidation of glycerol, Chem. Eng. Commun., 2019, 207(9), 1298–1328 Search PubMed.
- L. S. Sharninghausen, J. Campos, M. G. Manas and R. H. Crabtree, Efficient selective and atom economic catalytic conversion of glycerol to lactic acid, Nat. Commun., 2014, 5, 1–9 Search PubMed.
- M. Finn, J. A. Ridenour, J. Heltzel, C. Cahill and A. Voutchkova-Kostal, Next-Generation Water-Soluble Homogeneous Catalysts for Conversion of Glycerol to Lactic Acid, Organometallics, 2018, 37, 1400–1409 CrossRef CAS.
- W. Oberhauser, C. Evangelisti, A. Liscio, A. Kovtun, Y. Cao and F. Vizza, Glycerol to lactic acid conversion by NHC-stabilized iridium nanoparticles, J. Catal., 2018, 368, 298–305 CrossRef CAS.
- A. N. Marchesan, M. P. Oncken, R. Maciel and M. R. W. Maciel, A roadmap for renewable C2-C3 glycols production: a process engineering approach, Green Chem., 2019, 21, 5168–5194 RSC.
- L. Shen, Z. Yu, D. Zhang, H. Yin, C. Wang and A. Wang, Glycerol valorization to lactic acid catalyzed by hydroxyapatite-supported palladium particles, J. Chem. Technol. Biotechnol., 2019, 94, 204–215 CrossRef CAS.
- E. A. Redina, K. V. Vikanova, A. A. Shesterkina and L. M. Kustov, Gold-Doped Fe/TiO2 Catalysts: A Case of Extra-Low Gold Loading in Glycerol Oxidation, Russ. J. Phys. Chem. A, 2018, 92, 2143–2147 CrossRef CAS.
- R. Palacio, D. Lopez and D. Hernandez, Bimetallic AuCu nanoparticles supported on CeO2 as selective catalysts for glycerol conversion to lactic acid in aqueous basic medium, J. Nanopart. Res., 2019, 21, 148 CrossRef.
- A. M. Bruno, C. A. Chagas, M. M. V. M. Souza and R. L. Manfro, Lactic acid production from glycerol in alkaline medium using Pt-based catalysts in continuous flow reaction system, Renewable Energy, 2018, 118, 160–171 CrossRef CAS.
- S. M. A. H. Siddiki, A. S. Touchy, K. Kon, T. Toyao and K.-i. Shimizu, Oxidant-free Dehydrogenation of Glycerol to Lactic Acid by Heterogeneous Platinum Catalysts, ChemCatChem, 2017, 9, 2816–2821 CrossRef CAS.
- H. Tan, O. E. Tall, Z. Liu, N. Wei, T. Yapici, T. Zhan, M. N. Hedhill and Y. Han, Selective Oxidation of Glycerol to Glyceric Acid in Base-Free Aqueous Solution at Room Temperature Catalyzed by Platinum Supported on Carbon Activated with Potassium Hydroxide, ChemCatChem, 2016, 8, 1699–1707 CrossRef CAS.
- F.-F. Wang, S. Shao, C.-L. Liu, C.-L. Xu, R.-Z. Yang and W.-S. Dong, Selective oxidation of glycerol over Pt supported on mesoporous carbon nitride in base-free aqueous solution, Chem. Eng. J., 2015, 264, 336–343 CrossRef CAS.
- Y. Shen, Y. Li and H. Liu, Base-free aerobic oxidation of glycerol on TiO2-supported bimetallic Au-Pt catalysts, J. Energy Chem., 2015, 24, 669–673 CrossRef.
- Z. Tang, P. Liu, H. Cao, S. Bals, H. J. Heeres and P. P. Pescarmona, Pt/ZrO2 Prepared by Atomic Trapping: An Efficient Catalyst for the Conversion of Glycerol to Lactic Acid with Concomitant Transfer Hydrogenation of Cyclohexene, ACS Catal., 2019, 9, 9953–9963 CrossRef CAS.
- Y. Zhou, Y. Shen and J. Xi, Seed-mediated synthesis of PtxAuy@Ag electrocatalysts for the selective oxidation of glycerol, Appl. Catal., B, 2019, 245, 604–612 CrossRef CAS.
- R. K. P. Purushothaman, J. van Haveren, A. Mayoral, I. Melian-Cabrera and H. J. Heeres, Exploratory Catalyst Screening Studies on the Base Free Conversion of Glycerol to Lactic Acid and Glyceric Acid in Water Using Bimetallic Au-Pt Nanoparticles on Acidic Zeolites, Top. Catal., 2014, 57, 1445–1453 CrossRef CAS.
- X. Li, J. Pang, J. Zhang, C. Yin, W. Zou, C. Tang and L. Dong, Vapor-Phase Deoxygenation of Lactic Acid to Biopropionic Acid over Dispersant-Enhanced Molybdenum Oxide Catalyst, Ind. Eng. Chem. Res., 2019, 58, 101–109 CrossRef CAS.
- M. Tao, X. Yi, I. Delidovich, R. Palkovits, J. Shi and X. Wang, Hetropolyacid-Catalyzed Oxidation of Glycerol into Lactic Acid under Mild Base-Free Conditions, ChemSusChem, 2015, 8, 4195–4201 CrossRef CAS.
- E. M. Albuquerque, L. E. P. Borges, M. A. Fraga and C. Sievers, Relationship between Acid-Base Properties and the Activity of ZrO2-Based Catalysts for the Cannizzaro Reaction of Pyruvaldehyde to Lactic Acid, ChemCatChem, 2017, 9, 2675–2683 CrossRef CAS.
- K. M. A. Santos, E. M. Albuquerque, L. E. P. Borges and M. A. Fraga, Discussing Lewis and Bronsted acidity on continuous pyruvaldehyde Cannizzaro reaction to lactic acid over solid catalysts, Mol. Catal., 2018, 458, 198–205 CrossRef CAS.
- T. P. Braga, N. Essayem and A. Valentini, Correlation between the basicity of Cu-MxOy-Al2O3 (M = Ba, Mg, K or La) oxide and the catalytic performance in the glycerol conversion from adsorption microcalorimetry characterization, J. Therm. Anal. Calorim., 2017, 129, 65–74 CrossRef CAS.
- K.-T. Li, J.-Y. Li and H.-H. Li, Conversion of glycerol to lactic acid over Cu-Zn-Al and Cu-Cr catalysts in alkaline solution, J. Taiwan Inst. Chem. Eng., 2017, 79, 74–79 CrossRef CAS.
- R. Palacio, S. Torres, S. Royer, A. Sophie Mamede, D. Lopez and D. Hernandez, CuO/CeO2 catalysts for glycerol selective conversion to lactic acid, Dalton Trans., 2018, 47, 4572–4582 RSC.
- Z. Jiang, Z. Zhang, T. Wu, P. Zhang, J. Song, C. Xie and B. Han, Efficient Generation of Lactic Acid from Glycerol over a Ru-Zn-Cu-I/Hydroxyapatite Catalyst, Chem. – Asian J., 2017, 12, 1598–1604 CrossRef CAS.
- L. Qiu, H. Yin, A. Wang, L. Shen and W. Tao, Oxidation of 1,2-Propanediol to Carboxylic Acid Over Hydroxyapatite Nanorod-Supported Metallic Cu-0 Nanoparticles, J. Nanosci. Nanotechnol., 2020, 20, 1723–1731 CrossRef CAS.
- K.-T. Li and H.-H. Li, Glycerol Conversion to Lactic Acid with Unsupported Copper Salts and Bulk Cupric Oxide in Aqueous Alkali Media, Appl. Biochem. Biotechnol., 2020, 191(4), 1–10 Search PubMed.
- L. Shen, X. Zhou, C. Zhang, H. Yin, A. Wang and C. Wang, Functional characterization of bimetallic CuPdx nanoparticles in hydrothermal conversion of glycerol to lactic acid, J. Food Biochem., 2019, 43, e12931 Search PubMed.
- R. Palacio, S. Torres, D. Lopez and D. Hernandez, Selective glycerol conversion to lactic acid on Co3O4/CeO2 catalysts, Catal. Today, 2018, 302, 196–202 CrossRef CAS.
- A. Lahde, R. J. Chimentao, T. Karhunen, M. G. Alvarez, J. Llorca, F. Medina, J. Jokiniemi and L. B. Modesto-Lopez, Co-Al spinel-based nanoparticles synthesized by flame spray pyrolysis for glycerol conversion, Adv. Powder Technol., 2017, 28, 3296–3306 CrossRef CAS.
- L. Qiu, H. Yin, H. Yin and A. Wang, Catalytic Conversion of Glycerol to Lactic Acid Over Hydroxyapatite-Supported Metallic Ni-0 Nanoparticles, J. Nanosci. Nanotechnol., 2018, 18, 4734–4745 CrossRef CAS.
- H. Yin, H. Yin, A. Wang and L. Shen, Catalytic conversion of glycerol to lactic acid over graphite-supported nickel nanoparticles and reaction kinetics, J. Ind. Eng. Chem., 2018, 57, 226–235 CrossRef CAS.
- Z. Tang, H. Cao, Y. Tao, H. J. Heeres and P. P. Pescarmona, Transfer hydrogenation from glycerol over a Ni-Co/CeO2 catalyst: A highly efficient and sustainable route to produce lactic acid, Appl. Catal., B, 2020, 263, 118273 CrossRef CAS.
-
R. Abdullah and A. Z. Abdullah, Effect of Catalyst to Glycerol Ratio in the Production of Lactic Acid via Hydrothermal Reaction Using Calcium Oxide and Strontium Oxide Catalysts, in Green Design and Manufacture: Advanced and Emerging Applications, ed. M. Abdullah, S. Rahim, M. N. B. Saad, M. F. BinGhazli, R. Ahmad, M. F. B. Tahir and L. B. Jamaludin, AIP Conference Proceedings, 2018, vol. 2030 Search PubMed.
- S. A. Zavrazhnov, A. L. Esipovich, S. Y. Zlobin, A. S. Belousov and A. V. Vorotyntsev, Mechanism Analysis and Kinetic Modelling of Cu NPs Catalysed Glycerol Conversion into Lactic Acid, Catalysts, 2019, 9, 231 CrossRef.
- G.-Y. Yang, Y.-H. Ke, H.-F. Ren, C.-L. Liu, R.-Z. Yang and W.-S. Dong, The conversion of glycerol to lactic acid catalyzed by ZrO2-supported CuO catalysts, Chem. Eng. J., 2016, 283, 759–767 CrossRef CAS.
- H. Yin, C. Zhang, H. Yin, D. Gao, L. Shen and A. Wang, Hydrothermal conversion of glycerol to lactic acid catalyzed by Cu/hydroxyapatite, Cu/MgO, and Cu/ZrO2 and reaction kinetics, Chem. Eng. J., 2016, 288, 332–343 CrossRef CAS.
- A. B. F. Moreira, A. M. Bruno, M. M. V. M. Souza and R. L. Manfro, Continuous production of lactic acid from glycerol in alkaline medium using supported copper catalysts, Fuel Process. Technol., 2016, 144, 170–180 CrossRef CAS.
- M. Tao, N. Sun, Y. Li, T. Tong, M. Wielicako, S. Wang and X. Wang, Heteropolyacids embedded in a lipid bilayer covalently bonded to graphene oxide for the facile one-pot conversion of glycerol to lactic acid, J. Mater. Chem. A, 2017, 5, 8325–8333 RSC.
- M. Tao, D. Zhang, H. Guan, G. Huang and X. Wang, Designation of highly efficient catalysts for one pot conversion of glycerol to lactic acid, Sci. Rep., 2016, 6, 1–13 CrossRef.
- S. Feng, K. Takahashi, H. Miura and T. Shishido, One-pot synthesis of lactic acid from glycerol over a Pt/L-Nb2O5 catalyst under base-free conditions, Fuel Process. Technol., 2020, 197, 106202 CrossRef CAS.
- Z. Tang, D. G. Boer, A. Syariati, M. Enache, P. Rudolf, H. J. Heeres and P. P. Pescarmona, Base-free conversion of glycerol to methyl lactate using a multifunctional catalytic system consisting of Au-Pd nanoparticles on carbon nanotubes and Sn-MCM-41-XS, Green Chem., 2019, 21, 4115–4126 RSC.
- L. Zhou, Y. Xu, X. Yang, T. Lu and L. Han, Utilization of biodiesel byproduct glycerol: Production of methyl lactate over Au/CuO and Sn-Beta binary catalyst under mild reaction conditions, Energy Convers. Manage., 2019, 196, 277–285 CrossRef CAS.
- G. M. Lari, R. Garcia-Muelas, C. Mondelli, N. Lopez and J. Pérez-Ramírez, Glycerol oxidehydration to pyruvaldehyde over silver-based catalysts for improved lactic acid production, Green Chem., 2016, 18, 4682–4692 RSC.
- S. Ren and X. P. Ye, Catalytic conversion of glycerol to value-added chemicals in alcohol, Fuel Process. Technol., 2015, 140, 148–155 CrossRef CAS.
- M. Morales, P. Y. Dapsens, I. Giovinazzo, J. Witte, C. Mondelli, S. Papadokonstantakis, K. Hungerbuehler and J. Perez-Ramirez, Environmental and economic assessment of lactic acid production from glycerol using cascade bio- and chemocatalysis, Energy Environ. Sci., 2015, 8, 558–567 RSC.
- W. Dong, C. Wang, M. Gu, L. Yang, Z. Shen and Y. Zhang, Synthesis of Methyl Lactate from Glycerol Using Sn-Beta Zeolite, J. Renewable Mater., 2017, 5, 22–30 CrossRef.
- R. M. West, M. S. Holm, S. Saravanamurugan, J. Xiong, Z. Beversdorf, E. Taarning and C. H. Christensen, Zeolite H-USY for the production of lactic acid and methyl lactate from C-3-sugars, J. Catal., 2010, 269, 122–130 CrossRef CAS.
- J. Li, D. Li, C.-L. Liu, C. Xu and W.-S. Dong, The conversion of glycerol to methyl lactate catalyzed by tin-exchanged montmorillonite-supported gold catalysts, J. Chem. Technol. Biotechnol., 2019, 94, 1958–1967 CrossRef CAS.
- W. Oberhauser, C. Evangelisti, S. Caporali, V. Dal Santo, F. Bossola and F. Vizza, Ethyl lactate from dihydroxyacetone by a montmorillonite-supported Pt(II) diphosphane complex, J. Catal., 2017, 350, 133–140 CrossRef CAS.
- R. K. P. Purushothaman, J. van Haveren, I. Melian-Cabrera, E. R. H. van Eck and H. J. Heeres, Base-Free, One-Pot Chemocatalytic Conversion of Glycerol to Methyl Lactate using Supported Gold Catalysts, ChemSusChem, 2014, 7, 1140–1147 CrossRef.
- K. D. Kim, Z. Wang, Y. Jiang, M. Hunger and J. Huang, The cooperative effect of Lewis and Bronsted acid sites on Sn-MCM-41 catalysts for the conversion of 1,3-dihydroxyacetone to ethyl lactate, Green Chem., 2019, 21, 3383–3393 RSC.
- X. Zhang, L. Lin, T. Zhang, H. Liu and X. Zhang, Catalytic dehydration of lactic acid to acrylic acid over modified ZSM-5 catalysts, Chem. Eng. J., 2016, 284, 934–941 CrossRef CAS.
- H. Wang, D. Yu, P. Sun, J. Yan, Y. Wang and H. Huang, Rare earth metal modified NaY: Structure and catalytic performance for lactic acid dehydration to acrylic acid, Catal. Commun., 2008, 9, 1799–1803 CrossRef CAS.
- E. Blanco, P. Delichere, J. M. M. Millet and S. Loridant, Gas phase dehydration of lactic acid to acrylic acid over alkaline-earth phosphates catalysts, Catal. Today, 2014, 226, 185–191 CrossRef CAS.
- V. C. Ghantani, S. T. Lomate, M. K. Dongare and S. B. Umbarkar, Catalytic dehydration of lactic acid to acrylic acid using calcium hydroxyapatite catalysts, Green Chem., 2013, 15, 1211–1217 RSC.
- C. Li, Q. Zhu, Z. Cui, B. Wang and T. Tan, Insight into Deactivation Behavior and Determination of Generation Time of the Hydroxyapatite Catalyst in the Dehydration of Lactic Acid to Acrylic Acid, Ind. Eng. Chem. Res., 2019, 58, 53–59 CrossRef CAS.
- G. Naefe, Y. Traa, T. Hirth and E. Klemm, True Catalytic Behavior of Lactic Acid Dehydration on Zeolite Na-Y in the Gas Phase Measured by Means of a Novel Apparatus Design, Catal. Lett., 2014, 144, 1144–1150 CrossRef CAS.
- G. Naefe, M. A. Lopez-Martinez, M. Dyballa, M. Hunger, Y. Traa, T. Hirth and E. Klemm, Deactivation behavior of alkali-metal zeolites in the dehydration of lactic acid to acrylic acid, J. Catal., 2015, 329, 413–424 CrossRef CAS.
- J. Yan, D. Yu, P. Sun and H. Huang, Alkaline Earth Metal Modified NaY for Lactic Acid Dehydration to Acrylic Acid: Effect of Basic Sites on the Catalytic Performance, Chin. J. Catal., 2011, 32, 405–411 CrossRef CAS.
- Y. Matsuura, A. Onda, S. Ogo and K. Yanagisawa, Acrylic acid synthesis from lactic acid over hydroxyapatite catalysts with various cations and anions, Catal. Today, 2014, 226, 192–197 CrossRef CAS.
- C. Tang, J. Peng, X. Li, Z. Zhai, N. Jiang, W. Bai, H. Gao and Y. Liao, Strontium pyrophosphate modified by phosphoric acid for the dehydration of lactic acid to acrylic acid, RSC Adv., 2014, 4, 28875–28882 RSC.
- Z.-H. Liu, B. Yan, Y. Liang and B.-Q. Xu, Comparative study of gas-phase “dehydration” of alkyl lactates and lactic acid for acrylic acid production over hydroxyapatite catalysts, Mol. Catal., 2020, 494, 111098 CrossRef CAS.
- D. Song, J.-H. Yang and C.-J. Lee, Conceptual design of water separation process in glycerol-based acrylic acid production, Chem. Eng. Res. Des., 2020, 156, 324–332 CrossRef CAS.
- R. Wojcieszak, T. Bonnotte, S. Paul, B. Katryniok and F. Dumeignil, Lactic Acid Conversion to Acrylic Acid Over Fluoride-Substituted Hydroxyapatites, Front. Chem., 2020, 8, 421 CrossRef CAS.
- B. Yan, Z.-H. Liu, Y. Liang and B.-Q. Xu, Acrylic Acid Production by Gas-Phase Dehydration of Lactic Acid over K+-Exchanged ZSM-5: Reaction Variable Effects, Kinetics, and New Evidence for Cooperative Acid-Base Bifunctional Catalysis, Ind. Eng. Chem. Res., 2020, 59, 17417–17428 CrossRef CAS.
- C. Yin, X. Li, Z. Chen, W. Zou, Y. Peng, S. Wei, C. Tang and L. Dong, Sustainable production of pyruvic acid: oxidative dehydrogenation of lactic acid over the FeMoO/P catalyst, New J. Chem., 2020, 44, 5884–5894 RSC.
- H. F. Shi, Y. C. Hu, Y. Wang and H. Huang, KNaY-zeolite catalyzed dehydration of methyl lactate, Chin. Chem. Lett., 2007, 18, 476–478 CrossRef CAS.
- P. Sun, D. Yu, Z. Tang, H. Li and H. Huang, NaY Zeolites Catalyze Dehydration of Lactic Acid to Acrylic Acid: Studies on the Effects of Anions in Potassium Salts, Ind. Eng. Chem. Res., 2010, 49, 9082–9087 CrossRef CAS.
- A. Takahashi, N. Shibasaki-Kitakawa and T. Fujitani, Conversion of Methyl Lactate to Acrylates over Modified NaY Zeolite Catalysts, Bull. Chem. Soc. Jpn., 2015, 88, 1581–1583 CrossRef CAS.
- B. M. Murphy, M. P. Letterio and B. Xu, Catalyst Deactivation in Pyridine-Assisted Selective Dehydration of Methyl Lactate on NaY, ACS Catal., 2017, 7, 1912–1930 CrossRef CAS.
- B. M. Murphy, T. Mou, B. Wang and B. Xu, The Effect of Cofed Species on the Kinetics of Catalytic Methyl Lactate Dehydration on NaY, ACS Catal., 2018, 8, 9066–9078 CrossRef CAS.
- J.-M. Lee, D.-W. Hwang, Y. K. Hwang, S. B. Halligudi, J.-S. Chang and Y.-H. Han, Efficient dehydration of methyl lactate to acrylic acid using Ca-3(PO4)(2)-SiO2 catalyst, Catal. Commun., 2010, 11, 1176–1180 CrossRef CAS.
- Z. Zhang, Y. Qu, S. Wang and J. Wang, Catalytic Performance and Characterization of Silica Supported Sodium Phosphates for the Dehydration of Methyl Lactate to Methyl Acrylate and Acrylic Acid, Ind. Eng. Chem. Res., 2009, 48, 9083–9089 CrossRef CAS.
- B. M. Murphy, M. P. Letterio and B. Xu, Catalytic dehydration of methyl lactate: Reaction mechanism and selectivity control, J. Catal., 2016, 339, 21–30 CrossRef CAS.
- B. M. Murphy, M. P. Letterio and B. Xu, Selectivity Control in the Catalytic Dehydration of Methyl Lactate: The Effect of Pyridine, ACS Catal., 2016, 6, 5117–5131 CrossRef CAS.
- E. Blanco, C. Lorentz, P. Delichere, L. Burel, M. Vrinat, J. M. M. Millet and S. Loridant, Dehydration of ethyl lactate over alkaline earth phosphates: Performances, effect of water on reaction pathways and active sites, Appl. Catal., B, 2016, 180, 596–606 CrossRef CAS.
- Z. Zhang, Y. Qu, S. Wang and J. Wang, Theoretical study on the mechanisms of the conversion of methyl lactate over sodium polyphosphate catalyst, J. Mol. Catal. A: Chem., 2010, 323, 91–100 CrossRef CAS.
- C. Li, B. Wang, Q. Zhu and T. Tan, Efficient catalytic dehydration of methyl lactate to acrylic acid using sulphate and phosphate modified MCM-41 catalysts, Appl. Catal., A, 2014, 487, 219–225 CrossRef CAS.
- B. Yan, L.-Z. Tao, Y. Liang and B.-Q. Xu, Sustainable Production of Acrylic Acid: Alkali-Ion Exchanged Beta Zeolite for Gas-Phase Dehydration of Lactic Acid, ChemSusChem, 2014, 7, 1568–1578 CrossRef CAS.
- D. Yu, P. Sun, Z. Tang, Z. Li and H. Huang, Modification of NaY by La3+for the Dehydration of Lactic Acid: the Effect of Preparation Protocol on Catalyst Microstructure and Catalytic Performance, Can. J. Chem. Eng., 2011, 89, 484–490 CrossRef CAS.
-
J. H. Bermudez Jaimes, B. T. Da Silva, J. E. Jaimes Figueroa, B. H. Lunelli, R. Maciel Filho, M. R. Wolf Maciel, A. T. Morita and P. L. A. Coutinho, Hybrid Route to Produce Acrylic Acid from Sugarcane Molasses, in Iconbm: International Conference on Biomass, Pts 1 and 2, ed. E. Ranzi and K. KohseHoinghaus, Chemical Engineering Transactions, 2014, vol. 37, pp. 427−+ Search PubMed.
- X. Li, Z. Chen, P. Cao, W. Pu, W. Zou, C. Tang and L. Dong, Ammonia promoted barium sulfate catalyst for dehydration of lactic acid to acrylic acid, RSC Adv., 2017, 7, 54696–54705 RSC.
- F. G. Terrade, J. van Krieken, B. J. V. Verkuijl and E. Bouwman, Catalytic Cracking of Lactide and Poly(Lactic Acid) to Acrylic Acid at Low Temperatures, ChemSusChem, 2017, 10, 1904–1908 CrossRef CAS.
- L. Huang, D. S. Theng, L. Zhang, L. Chen, C. Wang and A. Borgna, In Situ-Generated Supported Potassium Lactate: Stable Catalysis for Vapor-Phase Dehydration of Lactic Acid to Acrylic Acid, ACS Omega, 2019, 4, 8146–8166 CrossRef CAS.
- C. D. Zeinalipour-Yazdi and C. R. A. Catlow, An experimental and computational IR and hybrid DFT-D3 study of the conformations of l-lactic and acrylic acid: new insight into the dehydration mechanism of lactic acid to acrylic acid, Phys. Chem. Chem. Phys., 2019, 21, 22331–22343 RSC.
- Y. Noda, H. Zhang, R. Dasari, R. Singh, C. Ozmeral, Y. Roman-Leshkov and R. M. Rioux, Importance of Dimer Quantification for Accurate Catalytic Evaluation of Lactic Acid Dehydration to Acrylic Acid, Ind. Eng. Chem. Res., 2017, 56, 5843–5851 CrossRef CAS.
|
This journal is © The Royal Society of Chemistry 2021 |
Click here to see how this site uses Cookies. View our privacy policy here.