DOI:
10.1039/D1NA00523E
(Review Article)
Nanoscale Adv., 2021,
3, 5222-5239
High-rate transition metal-based cathode materials for battery-supercapacitor hybrid devices
Received
30th June 2021
, Accepted 30th July 2021
First published on 30th July 2021
Abstract
With the rapid development of portable electronic devices, electric vehicles and large-scale grid energy storage devices, there is a need to enhance the specific energy density and specific power density of related electrochemical devices to meet the fast-growing requirements of energy storage. Battery-supercapacitor hybrid devices (BSHDs), combining the high-energy-density feature of batteries and the high-power-density properties of supercapacitors, have attracted mass attention in terms of energy storage. However, the electrochemical performances of cathode materials for BSHDs are severely limited by poor electrical conductivity and ion transport kinetics. As the rich redox reactions induced by transition metal compounds are able to offer high specific capacity, they are an ideal choice of cathode materials. Therefore, this paper reviews the currently advanced progress of transition metal compound-based cathodes with high-rate performance in BSHDs. We discuss some efficient strategies of enhancing the rate performance of transition metal compounds, including developing intrinsic electrode materials with high conductivity and fast ion transport; modifying materials, such as inserting defects and doping; building composite structures and 3D nano-array structures; interfacial engineering and catalytic effects. Finally, some suggestions are proposed for the potential development of cathodes for BSHDs, which may provide a reference for significant progress in the future.
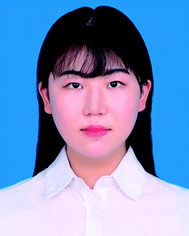 Cong Wang | Cong Wang received her bachelor’s degree from the Faculty of Physics and Mechatronics Engineering, Hubei University of Education, Wuhan, P. R. China. Since 2017, she has been a PhD candidate of the successive postgraduate-doctoral program at the Faculty of Physics and Electronic Science, Hubei University, Wuhan, P. R. China. Her doctoral topic focuses on the synthesis of transition metal selenides and their application in energy storage devices. |
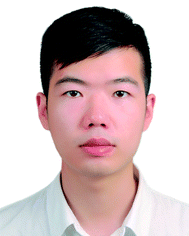 Zehao Song | Zehao Song received his master’s degree from the Faculty of Physics and Electronic Science, Hubei University, Wuhan, P. R. China. Currently, he works as a PhD student at the Institute of Solid State Electronics, Vienna University of Technology, Vienna, Austria. His research interests focus on photodetectors and supercapacitors and their hybrid integrated systems on chips. |
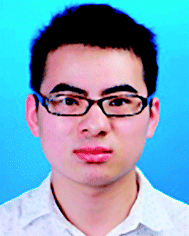 Lin Lv | Lin Lv obtained his PhD in Microelectronics and Solid-State Electronics from the Huazhong University of Science and Technology, Wuhan, P. R. China. He is currently working as an Assistant Professor at the Faculty of Physics and Electronic Science, Hubei University, Wuhan, P. R. China. His research interests include electrocatalysis such as water splitting, oxygen reduction and carbon dioxide electroreduction, and related energy devices such as zinc-air batteries and supercapacitors. |
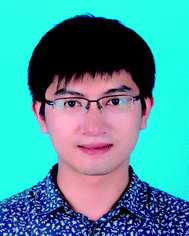 Houzhao Wan | Houzhao Wan is an associate professor at the Faculty of Physics and Electronic Science, Hubei University. He received his PhD degree in Microelectronics and Solid State Electronics at 2015 from the Huazhong University of Science and Technology, Wuhan, P. R. China. His research interests include energy storage materials and devices and their mechanism. |
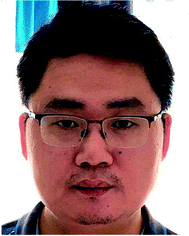 Hanbin Wang | Hanbin Wang obtained his PhD from Hubei University, Wuhan, P. R. China. Currently, he is working as a Professor at the School of Physical and Electronic Science, Hubei University, Wuhan, P. R. China. His research interests include Nano semiconductor materials and devices, and fuel cells. |
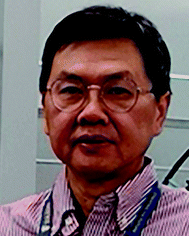 Hao Wang | Hao Wang obtained his PhD from the Huazhong University of Science and Technology, Wuhan, P. R. China. Currently, he is working as Secretary of the Party Committee and Dean of the School of Microelectronics, Hubei University, Wuhan, P. R. China. He did two terms of postdoctoral research on nanomaterials at Peking University and The Chinese University of Hong Kong. His research interests include integrated circuits and new energy materials (advanced memory and brain-like chips, energy storage cells and energy management systems, photodetectors and RF chips, and fuel cell catalysts). |
1. Introduction
The fast-growing economy of modern society has caused transitional consumption of primary energy sources accompanied by alarming environmental pollution, thus making it crucial to create high-performance energy conversion/storage devices.1,2 Energy storage devices should have the ability of supporting the national grid, meeting the expected increment of the global energy demand, and also matching the expanding requirements of the transportation sector in terms of electrification, electric vehicles, etc.3 In the past few decades, lithium-ion batteries have been widely used as a charging power source in portable electronic devices due to their high energy density and high operating voltage. But present lithium-ion batteries are not able to meet some of the new emerging demands, such as fast charging, due to their low power density.4–6 Supercapacitors are an ideal energy storage device because of some favourable features, including higher power density than batteries, and higher energy density than ordinary dielectric capacitors.7 Based on the mechanism of energy storage, supercapacitors can be divided into three categories: double layer capacitors, Faraday quasi-capacitors and battery-super capacitor hybrid devices (BSHDs) (Fig. 1).8 Among them, BSHDs attract more attention because they combine the high-energy-density feature of batteries and the high-power-density properties of supercapacitors. This should be attributed to the special structure where battery-type and capacitor-type electrode materials are applied in the cathode and anode, corresponding to the energy storage mechanism of the redox reaction and double layer, respectively (Fig. 2). Obviously, battery-type cathode materials are the key to achieving high-performance BSHDs.9,10
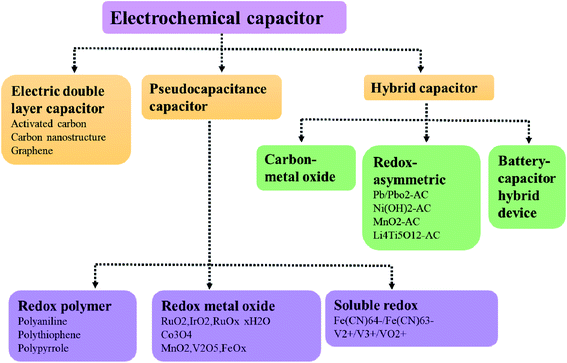 |
| Fig. 1 Classification of electrochemical capacitors. | |
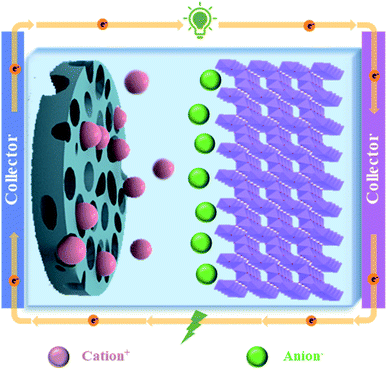 |
| Fig. 2 Schematic diagram of the working mechanism in BSHDs. | |
Battery-type cathodes mainly rely on transition metal compounds, such as metal oxides, hydroxides, sulfides, phosphides, etc., which are capable of providing high specific capacity due to their rich redox reactions.11 The electrochemical properties of different transition metal compounds are summarized in Table 1. Nickel oxide (NiO) has received much attention among transition metal oxides because of its excellent redox reversibility, high theoretical specific capacity (2584 F g−1),12 wide potential window and low cost.13 But NiO has the drawbacks of poor electrical conductivity, slow ion diffusion rates and the change of volume during charge and discharge, inducing impaired rate performance and cycling stability.14,15 Transition metal hydroxides are challenged by similar problems.16 In contrast, transition metal sulfides are a new generation of active materials for supercapacitors. For example, cobalt sulfide has excellent electrochemical properties, high theoretical capacity, structural diversity and multiple valence states and is widely applied in electrochemistry in electrocatalysts, lithium-ion batteries, and supercapacitors.17–19 Compared to oxygen or sulfur, phosphorus has lower electronegativity. Thus, transition metal phosphides show quasi-metallic structures and good electrical conductivity,20 exhibiting better electrochemical response than transition metal oxides/sulfides.21–23 However, due to the poor-electrical conductivity and slow ion transport kinetics of these materials, the poor-rate performance causes the trade-off of high power density and high energy density.
Table 1 Electrochemical properties of different types of transition metal-based compounds
Type |
Electrode materials |
Specific capacity (F g−1) at 1 A g−1 |
Specific capacity (F g−1) at 10 A g−1 |
Rate performance |
Stability |
Ref. |
Oxide |
NiO |
473 |
332.8 |
70% |
94%, n = 3000 |
24
|
CoO |
352 |
280 |
79.5% |
92.9%, n = 5000 |
25
|
Co3O4 |
1121 |
1023 |
91% |
98.2%, n = 6000 |
26
|
NiCo2O4 |
1516 |
1436 |
94.7% |
93%, n = 2000 |
27
|
Hydroxide |
Ni(OH)2 |
2110 |
1171 |
55.5% |
53%, n = 2000 |
28
|
Ni Co-LDH |
986.3 |
537.5 |
54.5% |
92.3%, n = 10 000 |
29
|
α-Co(OH)2 |
1310 |
960 |
73.3% |
83.9, n = 4000 |
30
|
β-Ni(OH)2 |
1065.7 |
812.5 |
76.2% |
91%, n = 10 000 |
31
|
Sulfide |
NiS |
1315.4 |
677.1 |
51.5% |
89.2%, n = 5000 |
32
|
CoS |
335 |
128 |
38% |
87.3%, n = 2000 |
33
|
CoS2 |
936 |
746 |
79.7% |
83%, n = 5000 |
34
|
Co9S8 |
1852 |
1228 |
66.3% |
86%, n = 5000 |
35
|
NiCoS |
1653 |
1344 |
81.3% |
84%, n = 3000 |
36
|
NiCo2S4 |
2161.7 |
1660 |
76.8% |
92.4%, n = 10 000 |
37
|
Selenide |
Ni0.85Se |
3150 |
1460 |
46% |
90.1, n = 5000 |
38
|
Co0.85Se |
1528 |
894.4 |
58.5% |
92, n = 5000 |
39
|
Ni0.6Co0.4Se2 |
1580 |
1320 |
83.5% |
90, n = 20 000 |
40
|
Ni0.67Co0.33Se2 |
784.2 |
674.4 |
86% |
97%, n = 2000 |
41
|
Phosphide |
Ni2P |
404.2 |
304.3 |
75.3% |
81%, n = 2000 |
42
|
Ni12P5 |
1414.4 |
963.4 |
68% |
53%, n = 1000 |
43
|
CoP |
558 |
462 |
82.8% |
98%, n = 5000 |
44
|
NiCoP |
1258 |
1056 |
83.9% |
90.1, n = 10 000 |
45
|
Rate performance is an important index that characterizes the electrochemical properties of materials and devices, depending on the reversibility of redox reactions occurring on the surface and the structural stability of electrode materials.46,47 Thus, the enhancement of rate performance is beneficial to improve the electrochemical performance of BSHDs and effectively promote their practical applications. In order to improve the rate performance of electrode materials, firstly with respect to kinetics and thermodynamics, they need to achieve high electrical conductivity and high surface activity. Secondly, some strategies such as doping, inserting defects, coupling with conducting materials, and building core–shell heterostructures can effectively improve the electrochemical activity of electrode materials and accelerate the kinetics of electrochemical reactions, thus leading to high-rate performance of electrode materials. For instance, Yu et al. reported urchin-like nickel–cobalt phosphide hollow spheres with polymetallic redox centers and excellent electrical conductivity, exhibiting a specific capacity of 761 C g−1 at a current density of 1 A g−1 and a capacity retention of 91.1% at 20 A g−1.48 Liu et al. reported composites achieved by integrating nickel–cobalt bimetallic hydroxide nanosheets with functionalized graphite.49 The fast electron/ion transport channel enabled excellent rate performance of the composite electrode, that is, specific capacities of 2442 F g−1 and 2039 F g−1 were achieved at current densities of 1 A g−1 and 50 A g−1, respectively, accompanied by a capacity retention of 83.5%. Cao et al. fabricated oxygen-rich defective Co3O4/graphene composites, whose oxygen vacancies on the surface can promote electrochemical charge transfer by generating another defect level in the band gap, thus significantly enhancing the rate performance of the electrode material.50 The corresponding specific capacity was 978.1 F g−1 at 1 A g−1, and a capacity retention of 93.7% was achieved even at 10 A g−1. Although many studies have been carried out based on high-rate transition metal compound-based electrodes, they usually focus on one individual material (e.g. transition metal oxides), or one single property (e.g. porous materials), or one structure (e.g. hierarchically structured oxides). Nevertheless, some reviews have discussed the strategies of how to enhance the stability of transition metal compounds. Since these previous reviews have mainly focused on partial discussions, there is a need for a systematic and comprehensive review.
The purpose of this review is to provide our perspective on improving the rate performance of transition metal compound-based cathodes in BSHDs, and offer some concluding remarks and suggestions for future development, which may prove to be a reference for further research work.
2. Energy storage mechanism of high-rate electrode materials
Low electrical conductivity and ion diffusion kinetics of transition metal compounds induce a poor rate performance, which is unable to meet the requirement for high energy density. To overcome this barrier, some efficient methods of enhancing the rate performance have been established recently, including (1) finding intrinsic materials exhibiting fast electron/ion transport, (2) modifying intrinsic materials (i.e. inserting defects or doping), (3) building composite structures, (4) synthesizing three-dimensional (3D) designed nano-array structures, (5) interface engineering and (6) utilizing the catalytic effects of transition metal compounds (Fig. 3).
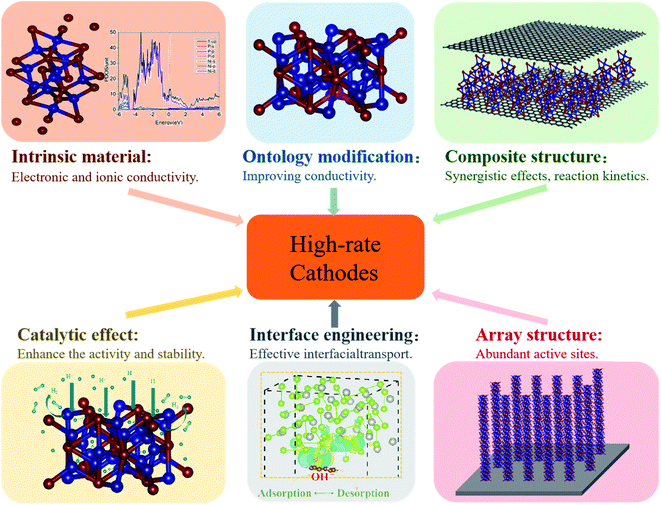 |
| Fig. 3 Methods of enhancing the rate performance of transition metal compounds. | |
Fast electron/ion transport in intrinsic materials boosts charge transport and ion diffusion, enabling fast and reversible Faraday reactions at large current density, and thus enhancing electrochemical energy storage.51,52 In recent years, spinel-type transition metal compound AB2M4 (where M is O, S) has been found to possess higher electrical conductivity and electrochemical activity than single metal oxides/sulfides, and is therefore considered a promising material for high-rate cathodes in BSHDs.18,53–56 Specifically, high conductivity would enable rapid electron transfer, and the synergistic effect of A and B ions can provide a richer Faraday redox reaction during the charging and discharging process.57–61 Besides the enhancement of electron transfer, the achievement of fast ion transport in the entire system is also another effective approach to improve the rate performance of electrode materials. One of the corresponding methods is to synthesize porous hollow nanostructures, which are able to exhibit superior performance to their bulk structure.48,62 Because porous hollow nanostructures have more active sites than their bulk counterpart, a larger specific surface area would be used in charge storage;48,63–65 the contact area between the electrolyte and active material would be increased and electrolyte penetration would be accelerated;66,67 shortening the ion diffusion path, promoting the transfer efficiency of ions,18,68,69 reducing the internal resistance, and consequently inducing higher rate performance.62,70,71 However, most transition metal compounds are limited by slow electron and ion transport.
Modification of intrinsic materials can improve the quality of the interface between the electrode and electrolyte, and provides additional Faraday pseudocapacitance as well, thus enabling high capacity storage.72–74 The modification methods include building defects and doping. Building defects is able to effectively break the periodic structure inside the crystal and alter the charge distribution in the surrounding, further changing the physicochemical properties of the electrode material.75–77 Element doping will modulate the band gap and the conductivity of electrode materials, thus reinforcing the rate performance.78–81 In addition, modification can reconfigure the crystalline structure inside the electrode material, which would work as a buffer, avoiding the capacity loss caused by volume expansion of electrode materials during a fast charging and discharging process.31
Composite structures can effectively combine the advantages of different materials to meet the demand of high rate performance. For transition metal compounds, many previous research studies have demonstrated an efficient approach of improving rate performance via coupling carbon-based materials. Among such carbon-based materials, graphene is one of the most widely applied, owing to its excellent electrical conductivity and huge specific surface area. Such composites would take their advantages (such as the synergistic effect from components and fast electron transport) to accelerate the speed of charge transfer and ion diffusion,19,47,82,83 mitigating the volume expansion during the redox reaction.56,84–86 Therefore, they are able to greatly enhance the rate performance of electrode materials with the improvement of cycling stability.87,88 Another approach of optimizing energy storage performance is to build heterojunctions using different transition metal compounds (such as Co3O4–RuO2,89 and MoSe2–Ni(OH)2 (ref. 70)), which will provide a built-in electric field to facilitate the transfer of electrons by an electrostatic force, finally improving the kinetics of the redox reaction during charging and discharging, and thus achieving high rate performance.90
3D nano-array structures can utilize active materials as much as possible and provide rich redox reaction sites, further increasing the rate performance. As the quality of the electron transporting channel is crucial to the performance of electrode materials, the morphologies of 3D nanostructures would play an important role in achieving high-performance electrode materials.91 It has been demonstrated that 3D nano-array structures consisting of 1D nanorods and 2D nanosheets have huge potential in enhancing the electrochemical properties of electrode materials. 2D nanosheets exhibit an enormous surface area, which will provide abundant active sites for redox reactions, whereas 1D nanorods have a large contact area with electrolyte ions during the electrochemical reactions. Besides, 1D nanorods not only act as an electronic highway to transfer electrons from the active material to the external circuit, but also have the ability of mitigating volume expansion.
The interface is an important position where electrochemical reactions occur in energy storage devices, and the performance of BSHD electrode materials strongly relies on effective electron and ion transport on the surface. The construction of high-quality interfaces inside composite electrodes or between the electrode/electrolyte is a key step of enhancing the electrochemical energy storage performance.92 In addition, catalyst materials play a crucial role in redox reactions that occur during the storage and conversion of electrochemical energy. The activity and stability of catalyst materials determine the electrochemical performance of energy storage devices, more or less. Therefore, it is important to survey the catalytic characteristics of electrode materials improving the rate performance and cycling stability.
Here, we will carry out a more detailed discussion with respect to individual strategies from the above arguments. Fig. 4 summarizes the rate performance of some transition metal compound cathodes based on different strategies.
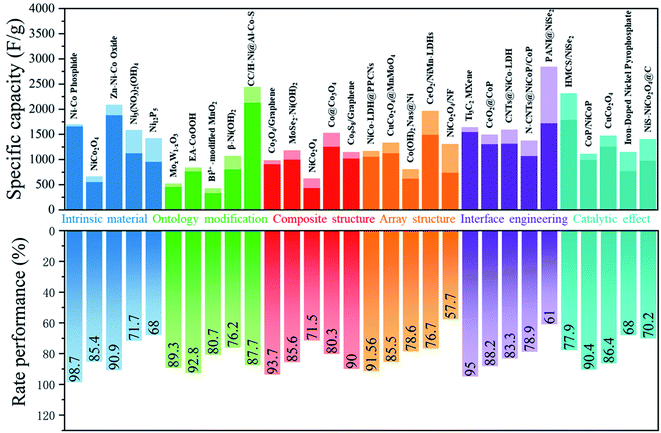 |
| Fig. 4 Effective methods used in increasing the rate performance of transition metal based cathodes in BSHDs. | |
3. Strategies of enhancing the rate performance of transition metal compound-based cathodes
3.1 Intrinsic materials
3.1.1 High-conductivity electrode materials.
Common battery-type transition metal compounds, such as nickel oxide,93 cobalt oxide,25,94 nickel sulfide,95,96 and cobalt phosphide,97 used as cathode materials usually have poor electrical conductivity, slow ion diffusion, and bad cycling stability, thus inducing low rate performance. Such transition metal compounds with low rate performance are not able to meet the needs and greatly limit practical applications.98 Therefore, researchers have dedicated themselves to find strategies of synthesizing high conductivity electrode materials, which can make electrons transfer from the collector to the surface of the electrode material faster, consequently reducing the charge transfer resistance.99 Among a lot of bimetallic compounds, nickel–cobalt bimetallic oxides are one of the most promising materials for high-performance pseudocapacitive electrodes. Compared to monometallic oxides, such as nickel oxide and cobalt oxide, spinel structure-based nickel–cobalt bimetallic oxides are able to offer more abundant redox active centers due to the synergistic effect, and thus higher specific capacity.54 Jiang et al. prepared NiCo2O4 and used it as an electrode material, which also showed high conductivity enabling excellent rate performance and cycling stability. It has a specific capacity of 658 F g−1 at a current density of 1 A g−1, and still kept 78% capacity retention even when the current density was increased 20 times.61 Lin et al. prepared a NiCo2S4 electrode material effectively improving the interaction between the electrolyte and active material, accelerating electron transfer during charge and discharge, and thus exhibiting impressive capacity and rate performance (i.e. a capacity of 82.6 mA h g−1 at 1 A g−1 and even a capacity of 46.2 mA h g−1 at 16 A g−1).18
With the electronegativity of the atom P in transition metal compounds being lower than that of the atoms O and S, transition metal phosphides have faster electron transfer and more active redox reactions enabling better electrochemical properties.98 Further, larger ionic gaps in the atomic structure of transition metal phosphides would enable more efficient electron/ion transport and better electrical conductivity, and thus transition metal phosphides would have good prospects as cathode materials in BSHDs. Wang et al. successfully synthesized high conductivity Ni12P5 nanowires by a simple one-step hydrothermal method. Such Ni12P5 nanowires can provide abundant electrochemical active centers and excellent electron transport paths.43 The electrode material showed a reversible specific capacity of 707.2 C g−1 at 1 A g−1 and a specific capacity of 481.7 C g−1 at 10 A g−1 with good capacity retention. Fig. 5a illustrates the crystal structure of Ni12P5, wherein the high porosity enables a high conductivity of 10 S cm−1. Fig. 5b demonstrates the density of states of Ni and P, suggesting that the energy bands of Ni12P5 are mainly attributed to Ni2p and P2p. The partial overlap of electron densities on the Fermi energy level further confirms the high conductivity of Ni12P5, which is the reason for high-rate performance. Fig. 5c shows the mechanism of electron transport in Ni12P5 nanowires in which the adsorption/desorption of OH− on the surface of the Ni12P5 nanowires promotes electron transfer; the corresponding redox reaction on the surface of the Ni12P5 nanowires follows eqn (1):
| Ni12P5 + xOH− ↔ Ni12P5(OH)x + xe− | (1) |
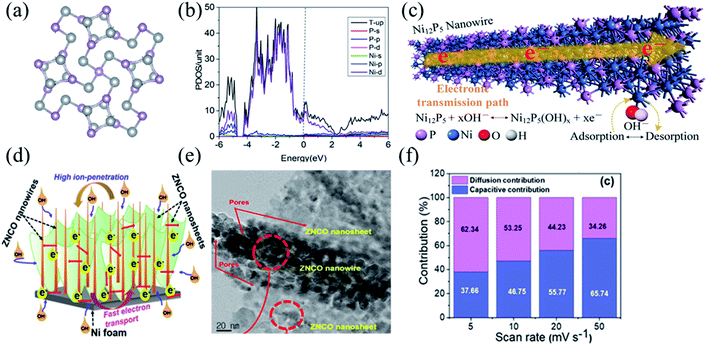 |
| Fig. 5 (a) The crystal structure of Ni12P5. (b) The projected density of states of the Ni12P5 bulk counterpart. (c) Electron transporting mechanism of Ni12P5 nanowires. Panel a–c adapted with permission from ref. 43, copyright 2019, Elsevier. (d) Electron transporting mechanism of ZNCO nanostructures. (e) The HRTEM image of the ZNCO. (f) Contribution of the capacitive- and diffusion-controlled process for the ZNCO electrode at different scanning rates. Panels d–f adapted with permission from ref. 112, copyright 2020, American Chemical Society. | |
3.1.2 Highly-active-site electrode materials.
To improve the rate performance of transition metal compound-based cathodes in BSHDs, another effective strategy is to prepare nanostructures with highly active sites. One of the simple approaches is to transform the bulk into porous nano-hollow structures, which would enable superior physical and chemical properties to the bulk materials.48,62 Hollow nanostructures can facilitate penetration of the electrolyte into the interior of electrode materials, increasing the amount of electrochemically active sites, and providing a large specific surface area for charge storage.60,61,100 Further, the large specific surface area would shorten the transport paths of ions and electrons, reducing the internal resistance, and thus enhancing the rate performance of the electrode material.91,101,102 The pores in electrode materials can increase the contact area between the electrolyte and electrode, accelerating the kinetics of electrochemical reactions, and finally ensuring rapid and effective charge storage reactions.103
Among battery-type cathode materials, Co3O4 is considered a promising electrode material due to its high ideal specific capacity, good electrochemical stability and redox activity.104,105 However, the rapid redox reaction causes severe attenuation of specific capacity during charging and discharging at large current density. To solve this problem, Sun et al. synthesized ultrathin Co3O4 nanosheets with high electrochemical activity and stability based on Co-MOFs as precursors.26 The corresponding specific capacities were 1121 F g−1 at 1 A g−1 and 873 F g−1 at 25 A g−1 with a capacity retention of 77.9%. The Co3O4 nanosheets increase the contact area with the electrolyte, promoting the diffusion of ions in the electrode material, accelerating the reaction kinetics, and resulting in good specific capacity performance at high current densities.106,107 In addition, the unique structure of Co3O4 nanosheets benefits the mitigation of structural collapse caused by volume changes during redox cycling, providing better reversible capacity and cycling stability.
Compared to monometallic/bimetallic compounds, ternary metal compounds have been widely used in energy storage systems because of higher electrochemical properties from the synergistic effect of multiple metal ions.108–111 Kim et al. reported a unique 3D hierarchical nanostructure of zinc–nickel–cobalt ternary oxide (ZNCO) (Fig. 5e).112 The synergistic effect between nanowires and nanosheets would provide abundant active sites for redox electrochemical reactions and reduce the volume expansion and mechanical strain of electrode materials during long-term charge/discharge cycles (Fig. 5d). Fig. 5f illustrates the contribution from diffusion in the ZNCO electrode at different scanning rates. The ZNCO electrode exhibited ultra-high-rate performance with specific capacities of 259.8 mA h g−1 at 1 A g−1, and 218 mA h g−1 at 50 A g−1 and a capacity retention of 83.9%. Qu et al. successfully synthesized a novel 3D-layered FeCoNi double hydroxide (FeCoNi-LDH) nanocage with excellent rate performance, grown from a cation exchange reaction with a metal–organic backbone as a template. Its corresponding specific capacity was 980 F g−1 at 1 A g−1 and the capacity maintains 93% even at a large current density of 20 A g−1, indicating that FeCoNi-LDH has promising applications in energy conversion and storage.113
3.2 Modification
3.2.1 Vacancy defects.
Most of the transition metal compounds are challenged by slow electron and ion transport. Therefore, excluding the strategies mentioned before, some other technical means have been investigated to effectively improve the rate performance of electrode materials. It has been proved that vacancy defects can promote electrochemical charge transfer achieving good conductivity and rate performance, because another additional defect level would be generated in the bandgap.114–116 A number of fascinating state-of-the-art studies have been reported. For example, Cao et al. reported ultra-small oxygen vacancy-rich Co3O4/graphene composites with ultra-high-rate performance. The specific capacity is able to reach 978.1 F g−1 at a current density of 1 A g−1 and the capacity retention exceeded 93.7% even at 10 A g−1.50 Zou et al. prepared oxygen vacancy-rich NiMn-LDH based on in situ oxidation by an electrodeposition method, reaching a specific capacity of 2150 F g−1 at a current density of 1 A g−1 and 1518 F g−1 at 10 A g−1, and a capacity retention of 70.6%, and thus achieving high rate performance.117 Feng et al. also used electrodeposition to obtain oxygen vacancy-rich NiCo-LDH, which exhibited a specific capacity of 1563 F g−1 at a current density of 1 A g−1. Particularly, a capacity retention of 67% can be maintained even when applied current density was increased by a factor of 20, suggesting excellent rate performance.118
Qiu et al. activated the intrinsic electrochemical properties of Co(OH)2via a reverse voltage method that would trigger the phase transition from Co(OH)2 to CoOOH. This resulting composition of lattice disorder and continuous cavity molecular structures would greatly facilitate the kinetics. With an abundance of defects, the reactivity of CoOOH would be higher than that of Co(OH)2. The electrode material showed excellent rate performance with a specific capacity of 832 F g−1 at 1 A g−1 and a capacity retention of 78% at 200 A g−1.2 In addition, they created a special lattice vacancy β-Ni(OH)2-based electrode with a unique and distinctive local lattice geometry, as shown in Fig. 6a and b. The tensile strain in the corrugated nanosheets provides an appropriate buffer for the repeated redox reactions, prolonging the lifetime of the electrode at high current densities. The corresponding specific capacity was 746 C g−1 at a current density of 1 A g−1. Even at 30 A g−1, it still had a specific capacity of 457 C g−1 with a capacity retention of 61%.31Eqn (2) explains the mechanism of this process, where oxygen vacancies and vanadium vacancies generated in the electrodes exhibit superior redox energy barriers, benefitting redox activity and reversible charge storage.
| 4Ni0.75V0.25(CO32−)0.125(OH)2H2O + 2OH− → 3Ni(OH)2 + VO2 + 6H2O + 0.5CO32− + e− | (2) |
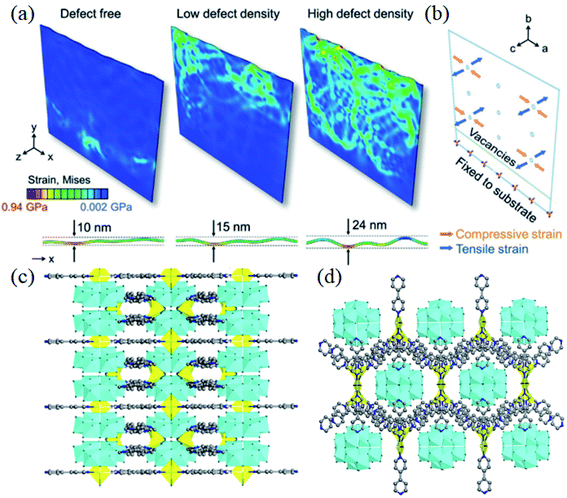 |
| Fig. 6 (a) von Mises strain and c-axis displacement in nanosheets depicting the corrugation formation process for 0%, 8%, and 18% disordered regions. (b) Schematic of the strain direction on nanosheets during the phase change from α-Ni(OH)2 to β-Ni(OH)2. Panels a and b adapted with permission from ref. 31, copyright 2020, Wiley-VCH. (c and d) Schematic diagram of the Mo doped Ni-MOF nanosheet structure along the a-axis and c-axis. Panels c and d adapted with permission from ref. 132, copyright 2020, Elsevier. | |
3.2.2 Doping.
Doping can improve the capacity performance of electrode materials by modulating their conductivity.119–121 A lot of research studies report that metal atom doping can increase the conductivity of transition metal oxides by generating additional oxygen vacancies. For example, Chen et al. doped Al into cobalt sulfide nanosheets by an electrodeposition method. The appropriate amount of Al doping is able to increase conductivity and enhance the electrochemical activity of cobalt sulfide, resulting in good electrochemical performance. The electrode material had a specific capacity of 2434 F g−1 at 1 A g−1. It still had 72.3% capacity retention when current density was increased by 100 times.122 Ni doped cobalt–cobalt nitride was prepared by Wang et al. which showed a specific capacity of 450 F g−1 at a current density of 2 mA cm−2 and a capacity retention of 82.5% at a current density of 50 mA cm−2.123 Wei et al. doped Mn into Ni–Co layered double hydroxide nanosheets coated by polyaniline-derived carbon. The Mn doping enabled a rich redox reaction (i.e. Mn2+ ↔ Mn3+ ↔ Mn4+), which effectively improved the specific capacity and rate performance. A high specific capacity of 1282.06 C g−1 and excellent rate stability were observed at a current density of 1 A g−1, and the capacity retention was 74.99% when the specific current was increased to 10 A g−1.124
In addition to the doping of metallic elements into transition metal compounds, the doping of non-metallic elements (O, N, S, F, and P) is also able to increase conductivity.125–127 Further, it can enable some other features, including adding the functional groups in the electrodes, improving their hydrophilicity/oil properties, and promoting the transporting efficiency of electrolyte ions.71,78,79,81,128 Wang et al. doped nitrogen into cobalt phosphide nanowire arrays, which increased the conductivity of cobalt phosphide, improving charge transfer, and giving rise to the high-rate performance of cobalt phosphide. In addition, the doping of N elements increased the number of active sites of the redox reaction in cobalt phosphide, thus increasing the specific capacity. It provides a specific capacity of 232.4 mA h g−1 at a current density of 2 mA cm−2, and maintains a capacity retention of 52% when the current density is increased to 50 mA cm−2.129 Meng et al. homogeneously doped P into Co–Ni–S nanosheet arrays by an electrodeposition method, which showed an ultra-high specific capacity of 3677 F g−1 at 1 A g−1 with excellent rate performance (i.e. a capacity retention of 63% at 20 A g−1).130 Wang et al. performed sulfur doping by heat treatment and obtained S-doped CoP nanotube arrays with a capacity of 610 F g−1 at a current density of 1.0 A g−1 and capacity retention of 56% at 20 A g−1.131 Yang et al. encapsulated Mo clusters in the holes of the Ni-MOF frame structure to improve the conductivity and stability of the Ni-MOF (Fig. 6c and d). The nanosheet structure of the Mo-doped Ni-MOF acts as a highway of charge transport, which enables faster charge transportation and the higher conductivity of the electrode material, and thus achieves excellent rate performance. The prepared Mo-doped Ni-MOF electrode exhibits a high specific capacity of 802 C g−1 at 1 A g−1, and even a specific capacity of 480 C g−1 at 10 A g−1.132
3.3 Composite structure
3.3.1 Carbon-based composite structure.
Among battery-type electrode materials, NiO is widely used because of its excellent redox and charge storage properties, low cost, and environmental friendliness.133–135 However, NiO is also challenged by poor electrical conductivity and cycling stability, which would limit practical applications. To solve this problem, an effective strategy is coupling NiO with other highly porous and conductive materials, such as graphene, activated carbon, and carbon nanotubes because such composite structures can significantly increase the conductivity and improve electrochemical properties. Graphene is a typical 2D material with in-plane carbon atoms arranged in a honeycomb pattern via the sp2-bond, enabling high electrical conductivity,136 a large specific surface area and high theoretical specific capacity.137 In addition, its ultrathin 2D structure makes fast charge transfer possible in the plane, whereas its high porosity from the intra- and inter-layer enables fast ion transport.138,139 Therefore, the combination of graphene with NiO forming some unique structures is expected to be a desired approach of enhancing the electrochemical performance of electrode materials based on the synergistic effect.140 Wang et al. synthesized reduced graphene oxide@NiO (rGO@NiO) composites where NiO nanoparticles were uniformly distributed on rGO, and confirmed their ability to strengthen the accessibility from the rGO@NiO composites to the electrolyte.141 In addition, the special structure of rGO promotes the fast electron/ion transport.46,135 The synergistic effect of rGO and NiO endows the composite electrode with excellent rate performance with a specific capacity of 1093 F g−1 at a current density of 1 A g−1, and 875 F g−1 at 10 A g−1 and a capacity retention of 80%.
Besides NiO, other transition metal compounds can also be coupled with carbon materials achieving high rate performance, such as Ni(OH)2/RGO (1795 F g−1 at 1 A g−1, 85.68% capacity retention at 40 A g−1),142 PEG/NiCo-DH (2442 F g−1 at 1 A g−1, a capacity retention of 83.5% at 50 A g−1),49 NiCo2S4/PCF (1169 F g−1 at 1 A g−1, a capacity retention of 81.3% at 20 A g−1),56 Co9S8/RGO (1140 F g−1 at 4 A g−1, a capacity retention of 74.5% at 30 A g−1),19 and (Ni, Mo)S2/RGO (2379 F g−1 at 1 A g−1, a capacity retention of 60.5% at 100 A g−1).64 Zheng et al. prepared ultrathin, highly crinkled CoP/RGO nanosheet arrays via a hydrothermal phosphorylation method (Fig. 7a).143 In such CoP/RGO composites, the pores in the nanosheets can serve as active sites for electrolyte diffusion and charge migration, facilitating the redox reaction process, and thus excellent electrochemical properties. Fig. 7b illustrates the partial density of states of the CoP/RGO composite determined by first principles calculations. The strong hybridization between the O atom of RGO and the Co atom of CoP suggests the existence of C–O–Co bonds between the interface of RGO and CoP.128Fig. 7c shows the structural model of OH− on the surface CoP (201) and the interface CoP (201)/RGO (001), and the corresponding adsorption energy. The existence of RGO can greatly reduce the adsorption energy of OH− on CoP, thus enhancing the electrochemical performance. The CoP/RGO electrode shows a specific capacity of 1438.0 C g−1 at 1 A g−1, and 1198.9 C g−1 at 10 A g−1 and a capacity retention of 83.4%. Moosavifard et al. created graphene coated Ni3S2 nanocube (RGO/Ni3S2) composites, which can be applied in high-performance and low-cost BSHDs electrodes. RGO/Ni3S2 electrodes exhibit high rate performance, that is, an ultra-high specific capacity of 616 C g−1 at 1 A g−1 and a high specific capacity of 377 C g−1 at 10 A g−1.144
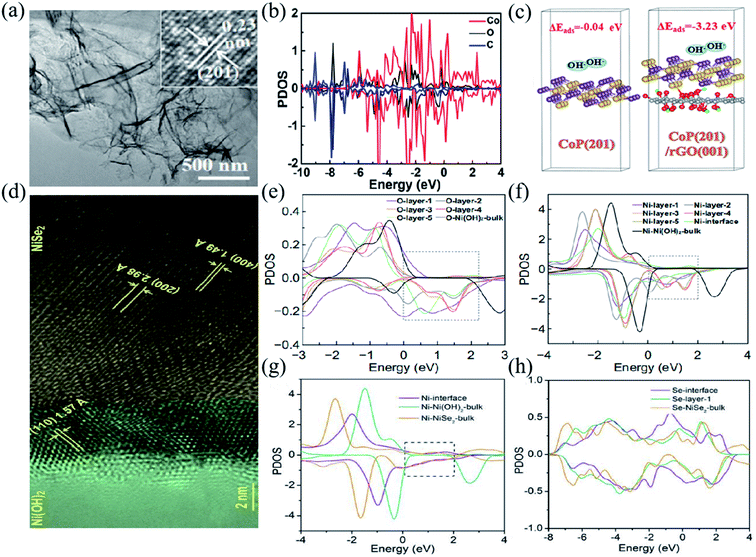 |
| Fig. 7 (a) TEM images of the CoP/rGO nanosheets. (b) PDOS of Co, O, and C atoms in CoP (201)/rGO (001). (c) The structure models and the corresponding adsorption energies of OH− for the CoP (201) surface and CoP (201)/rGO (001) interface. Panels a–c adapted with permission from ref. 143, copyright 2021, American Chemical Society. (d) HRTEM images of the NiSe2/Ni(OH)2 heterojunction. (e and f) PDOS of O and Ni atoms at different layers, respectively. (g) The PDOS of Ni atoms at the Ni(OH)2/NiSe2 interface, in bulk NiSe2, and in bulk Ni(OH)2. (h) The PDOS of Se atoms at and near the interface, as well as in the bulk. Panels d–h adapted with permission from ref. 16, copyright 2020, Springer Nature. | |
3.3.2 Heterojunction composite structure.
Building a heterojunction structure based on different electrode materials has been a hot research topic in nano/microstructure engineering, and is able to further optimize the energy storage performance.145–147 With built-in fields caused by the mismatch of energy bands from different materials, electron transfer at the interface of the heterojunction would be promoted by an electrostatic force, thus improving the kinetics of redox reactions during charging and discharging.90,148,149 Wang et al. prepared MgCo2O4@MnO2 core–shell structures by growing MnO2 nanostructures on MgCo2O4 nanoflakes, which showed excellent rate performance (i.e. 852.5 F g−1 at 1 A g−1, and 573.3 F g−1 at 40 A g−1 and a capacity retention of 67.2%).53 Sha et al. uniformly deposited Ni(OH)2 on silicon carbide nanowires, which promoted its interaction with the electrolyte shortening the ion diffusion distance.82 The SiC NWS@Ni(OH)2 electrode material showed excellent rate performance, that is, 1724 F g−1 at 2 A g−1, and 1412 F g−1 at 100 A g−1 and a capacity retention of 81.9%. Angaiah et al. synthesized molybdenum diselenide-nickel hydroxide nanohybrids with molybdenum diselenide grown on nickel hydroxide nanosheets, which was confirmed to have higher conductivity than nickel hydroxide. The rapid electron transfer that occurred at high current densities suggests improved rate performance (i.e. 1175 F g−1 at 1 A g−1, and 1006 F g−1 at 10 A g−1 and a capacity retention of 85.6%).70
Sun et al. prepared (100)-NiSe2/(110)-Ni(OH)2 heterojunction composites using an epitaxial-like growth strategy (Fig. 7d).16 Owing to the large specific surface area and suitable microporous structure of the NiSe2/Ni(OH)2 heterojunction, abundant electrochemically active centers would enable easy access of electrons to the electrolyte and rapid migration of ions inside the electrode. Fig. 7e–h illustrate the electronic density of states of the atoms on the NiSe2/Ni(OH)2 interface. The NiSe2/Ni(OH)2 electrode material exhibits excellent electrochemical properties with specific capacities of 909 C g−1 at 1 A g−1, and 597 C g−1 at 20 A g−1 and a capacity retention of 63.7%. Zeng et al. successfully prepared ZnCo2O4@MnCo2O4 heterojunction structure nanosheets with several advantages, including a large specific surface area, good structural stability and good electrical conductivity, exhibiting high-rate performance. The corresponding specific capacity is 254 F g−1 at 1 A g−1, and it can remains 186 F g−1 even at 10 A g−1.150 Li et al. fabricated the α-Ni(OH)2/NiS1.97 heterojunction by an ion-exchange based epitaxial growth method. Heterojunctions allow the components to provide ion/electron transport paths for each other, increasing the utilization rate of active materials, and thus achieving high specific capacity and rate performance. The corresponding specific capacity is as high as 2375.8 F g−1 at 1 mV s−1 and 939.5 F g−1 at 10 mV s−1.151
3.4 Array structure
Since the quality of the electron transport channel is crucial to the performance of electrode materials, different morphologies of nanomaterials usually alter electron transporting properties by directly affecting the specific surface area and density of electrode materials.55,91,152,153 Therefore, a reasonable design of the electrode structure plays an important role in the development of advanced electrode materials for high-performance BSHDs.99,129,154 3D array structures are found to increase the specific surface area and density of electrode materials, which would provide abundant electrochemical activity centers, facilitating charge transport, and consequently strengthening their electrochemical performance.54,154–157 Therefore 3D array structures are considered attractive for maximizing the use of active materials.158–160 Wang et al. prepared high-performance electrode materials by depositing arrays of copper hydroxide nanosheets on nickel grids via electrodeposition.157 They have a specific capacity of 798.2 F g−1 at 1 A g−1 and a specific capacity of 556.4 F g−1 at 20 A g−1 with a capacity retention of 70%. As copper hydroxide nanosheets have a large specific surface area which can sufficiently contact the electrolyte during the charging and discharging process, the length of the ion diffusion path would be shortened and the “dead volume” in the electrode would greatly reduce. In addition, the in situ growth method avoids the use of polymer binders, which significantly improves electron transfer and ion diffusion.48,68,103 Chen et al. reported a composite electrode consisting of a vertical, ordered arrangement of NiCo2S4 nanoflakes covered by elongated nickel columns (Fig. 8a).161 The array structure enabled fast charge storage/transfer and promoted reaction kinetics, allowing the active materials to react efficiently. The transmission electron microscopy (TEM) image in Fig. 8b shows intersecting ultrathin NiCo2S4 sheets forming a sparse nanostructure. The contribution rate of the NiCo2S4@NC array electrode at different scan rates is shown in Fig. 8c. With the increment of the scan rate, the contribution from diffusion decreases. The shorter ion diffusion time at high scan rates results in inadequate redox reactions. In this case, the capacitive control occurring on the material surface would dominate. Due to the good charge transfer kinetics and fast electron transfer, the NiCo2S4@NC array electrode has an ultra-high specific capacity of 486.9 mA h g−1 at 1 A g−1 and 150 mA h g−1 even at a very high current density of 100 A g−1.
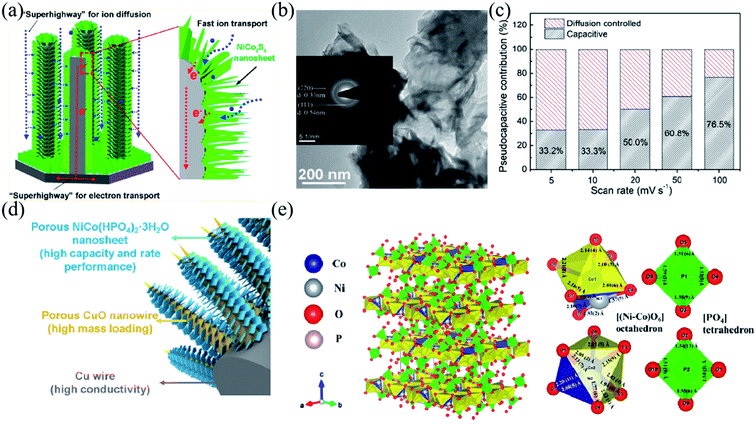 |
| Fig. 8 (a) Schematic illustration of ion diffusion and electron transport in the vertically aligned NiCo2S4@NC-array. (b) Transmission electron microscopy image of NiCo2S4 Nanoflakes. (c) Ratio of pseudocapacitive contribution at different scan rates. Panels a–c adapted with permission from ref. 161, copyright 2020, American Chemical Society. (d) Structure advantages of the Cu/p-CuO/NiCo-P hybrid material. (e) 3D atomic configuration of a NiCo(HPO4)2–3H2O unit cell and the local coordination of the strongly distorted [(Ni–Co)O6] octahedron and [PO4] tetrahedron. Panels d and e adapted with permission from ref. 163, copyright 2020, American Chemical Society. | |
Transition metal phosphides have excellent electrical conductivity and redox activity due to the lower electronegativity of phosphorus, as mentioned before.42,44,45,162 Chen et al. in situ grew dense NiCo(HPO4)2–3H2O nanosheet arrays on porous CuO nanowires, referred to as Cu/p-CuO/NiCo-P, and the corresponding schematic diagram is shown in Fig. 8d.163Fig. 8e suggests that the single layer of NiCo(HPO4)2–3H2O consists of octahedra [(Ni–Co)O6] and tetrahedra [PO4]. Cu/p-CuO nanowires would increase the conductivity of the whole electrode materials as the conducting frame and provide a large specific surface area for high-quality loaded active substances. The synergistic effect of Ni and Co effectively improves the electrical conductivity and capacitive properties of NiCo-P. The abundant pores and defects of ultrathin NiCo-P nanosheets can effectively expose the active centers promoting ion diffusion and charge transfer. The Cu/p-CuO/NiCo-P electrode exhibits ultra-high specific capacity (i.e. 1768.5 C g−1 at 1 A g−1) and excellent rate performance (i.e. 1144.8 C g−1 at 100 A g−1, 64.7% capacity retention).
3.5 Interface engineering
Since the interface of electrode materials is an important region where electrochemical reactions occur, the capacitive performance of BSHD electrode materials strongly depends on effective electron and ion transport at the interface. Therefore, building effective interfaces inside composite electrodes or between the electrode/electrolyte is key to improving the electrochemical energy storage performance.92 Interfaces between a metalloid/semiconductor would form Schottky contact, which can facilitate electron transfer from the free-electron-rich metalloid to the semiconductor and leave holes in the metalloid, thus enhancing OH− adsorption.164 In addition, the interface will release additional electrons during charging and discharging, ultimately improving the electrochemical performance of the electrode.165,166 Such interface engineering has been verified as an effective approach of improving the conductivity and structural stability of electrodes in SBHs by many previous studies.167–169 For example, Du et al. reported a NiCo2O4 nanowires/reduced graphene oxide (RGO) electrode material, which is able to combine the energy storage mechanisms of capacitive and Faraday materials.165 With the interconnected porous skeleton of the RGO/NiCo2O4 nanocomposite and the polarization of the interface caused by the difference of work function, the kinetics of the electronic and ionic reactions are enhanced, the structural stability is improved, and the rate performance of the RGO/NiCo2O4 nanostructure is greatly enhanced, that is, 4.37 F cm−2 at 2 mA cm−2 and 2.59 F cm−2 at 10 mA cm−2 with 67.5% capacity retention. Gao et al. proposed a simple interface engineering strategy where 2D MoS2 nanosheets were in situ integrated into a 3D polypyrrole framework via a DBS-anion intermediate linkage, consequently forming a novel MoS2-DBS-PPy film.168 As such the MoS2-DBS-PPy film combined the excellent conductivity of PPy chains and the high specific surface area of MoS2 nanosheets, and exhibited excellent rate performance (i.e. 1.2 F cm−2 at 0.5 mA cm−2, and 0.6 F cm−2 at 10 mA cm−2 with 50% capacity retention).
With the capability of strengthening the conductivity and stability of electrode materials by forming a highly conductive layer,170,171 polyaniline is widely implemented in energy devices by coupling with pseudocapacitive electrode materials.172–174 Cao et al. synthesized V2O5/PANI nanomaterials via in situ one-step oxidative polymerization of aniline monomers, which will insert vanadium vacancies and PANI on the surface of V2O5 (Fig. 9a).175 With the tilting of vanadium atoms, an unbalanced charge distribution generates in the plane, thus forming a local electric field which would provide the Coulomb force facilitating ion diffusion (Fig. 9b). Vanadium vacancies enable fast electron transfer by providing vacancy sites for electron adsorption/desorption, and also catalyze redox reactions on the surface. In addition, as an external percolation charge-transporting channel in the nanostructure, the high conductivity of the porous polyphenylene shell layer accelerates electron transport (Fig. 9c). Therefore, with vanadium vacancies and the interface modification of PANI, the charge transfer kinetics of the V2O5/PANI electrode would be enhanced, resulting in excellent electrochemical performance. It exhibited a specific capacity of 353.8 F g−1 at 1 A g−1 and a capacity retention of 50% at 10 A g−1. Yang et al. fabricated a PANI/SeNi2 core–shell nanotube electrode with different electron concentrations (Fig. 9d).176 The strong interaction between PANI and SeNi2 through the CNI–Se bond can induce electron accumulation at the Ni ion, which not only promotes electron transfer within the electrode, but also increases the theoretical Faraday capacity of the electrode. The Faraday redox reaction occurring at the electrode follows eqn (3):
| PANI@NiSe2 + (1 + x)OH− ↔ NiSe2(OH)1+x + (1 + x)e− | (3) |
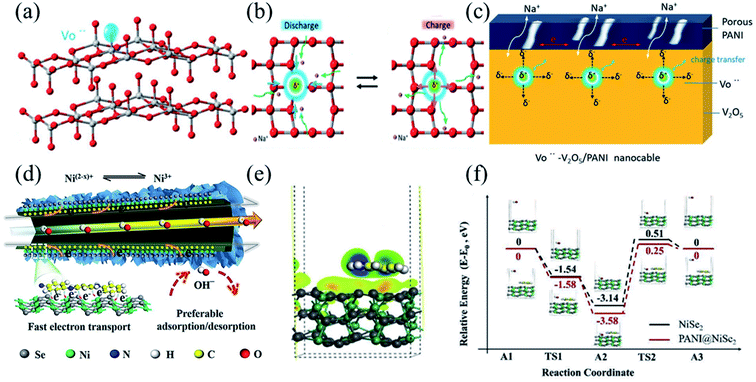 |
| Fig. 9 (a) The vacancy site in the V2O5 structure. (b) Schematic illustration of charge transfer behavior around the Vö region by forming a local electric field (E). (c) The enhanced charge transfer kinetics mechanism of Vö–V2O5/PANI due to the synergy of Vö and PANI. Panels a–c adapted with permission from ref. 175, copyright 2019, WILEY-VCH. (d) The electron transport mechanism of PANI@NiSe2. (e) The electronic density difference of PANI@NiSe2. (f) The DFT calculations of the transition-state energy of adsorbed hydroxyl (ΔGOH−). Panels d–f adapted with permission from ref. 176, copyright 2019, Elsevier. | |
Fig. 9e illustrates the transition state energy of the adsorbed hydroxyl group (ΔGOH−) calculated by DFT. Compared to NiSe2, the strong interaction through the CNI–Se bridge bond at the interface of PANI/NiSe2 promoted the electron transfer and the adsorption/desorption of ions on the surface, as shown in Fig. 9f. The combination of NiSe2 and PANI induced electron accumulation from lower valence states or a wide range of valence changes of Ni ions, which improved the specific capacity and rate performance of the electrode material. The electrode had a specific capacity of 275.6 mA h g−1 at 1 A g−1 and a capacity retention of 61% at 10 A g−1.
3.6 Catalytic effect
As catalyst materials play a crucial role in redox reactions during electrochemical energy conversion and storage,177–179 their activity and stability would determine the electrochemical performance of energy storage devices. Thus, it makes sense to study the catalytic effect of electrode materials, further enhancing the rate performance and cycling stability of electrode materials.180,181 Transition metal sulfides have received great attention in the application of energy conversion and storage devices due to their high specific capacity and rate performance.182–184 Guo et al. prepared 3D Ni9S8/O–MoS2 nanostructures used in supercapacitors and hydrogen precipitation catalysts. Ni9S8 nanorods acted as conducting channels of electrons in the Ni9S8/O–MoS2 nanocomposites, enhancing electron transport throughout the electrodes, and thus achieved high electrochemical performance. It exhibited a specific capacity of 907 F g−1 at 2 A g−1 and retained a specific capacity of 430 F g−1 at 7 A g−1, enabling good rate performance. In addition, the oxygen doping of MoS2 would offer more active sites, which would participate in the catalytic process of the hydrogen precipitation reaction. Therefore, the Ni9S8/O–MoS2 composites also had highly electrocatalytic properties, and can be applied for hydrogen production.185
Transition metal phosphides are considered a kind of stable and effective catalyst material because of their unique catalytic and electronic properties. Owing to the electron-rich metallic surfaces of transition metal phosphides, their activity is better than that of other counterparts, such as carbides, nitrides, and sulfides.186–188 Thus, transition metal phosphides are widely used in water decomposition, fuel cells, batteries, and supercapacitors.189,190 Pang et al. prepared ultrathin and homogeneous 2D nickel–cobalt phosphate composite nanosheets, which are ultrathin enough to provide maximum mechanical flexibility and sufficient electroactive sites facilitating their electrochemical performance. The electrode shows a high specific capacity of 1132.5 F g−1 at 1 A g−1 and high rate performance with 63% capacity retention at 1 A g−1.191 Chen et al. built a nanoscale tadpole-like CoP/NiCoP heterojunction interface modulating the catalyst structure and thus strengthening the hydrogen precipitation and energy storage performance, as shown in Fig. 10a. Fig. 10b and c demonstrate linear sweeping in different directions, further revealing the elementary distribution of CoP/NiCoP. Density functional theory (DFT) explains the synergistic effect between NiCoP and CoP, confirming the effective proton adsorption/desorption ability of CoP/NiCoP (Fig. 10d). The d-band center of the H+ capture site would shift upward from the Fermi energy level after the elimination of the terminal P atoms (Fig. 10e). After CoP loading, the coordination number of the Co–Ni shell layer in NiCoP would decrease, and some of the Ni atoms would be replaced by Co atoms on the surface. The magnitude of ΔGH+ remains almost constant with the increased substitution of Ni atoms (Fig. 10f). In addition, the adsorption energy of H2O (ΔEH2O) was calculated and is illustrated in Fig. 10g, which indicates that in the alkaline HER process the adsorption of H2O would be improved and the dissociation is accelerated. The theoretical results show that the formation of the NiCoP/CoP heterojunction interface optimizes proton chemisorption and H2O dissociation. The optimized phosphide crystal keeps the balance of the proton chemisorption and H2O dissociation, thus accelerating the HER kinetics over a broad pH range. In addition, because of the unique properties, CoP/NiCoP had been proved as an excellent cathode material for SBHs with ultra-high rate performance, which was a specific capacity of 1106.2 F g−1 at 1 A g−1 and a specific capacity of 600 F g−1 at 100 A g−1.192
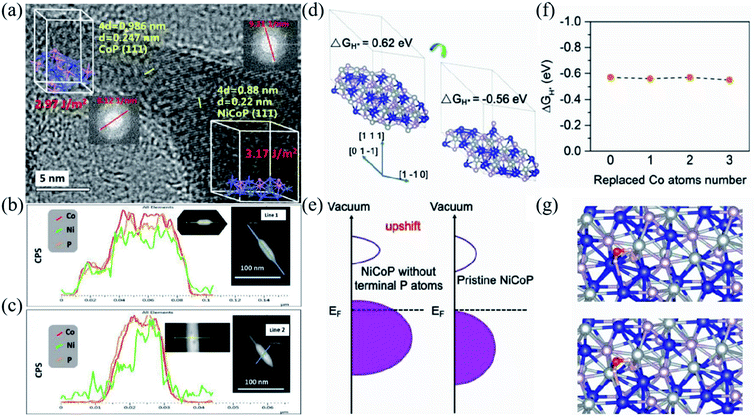 |
| Fig. 10 (a) HRTEM image of CoP and NiCoP; the inset shows the calculated surface energies and fast Fourier transform. (b and c) Line scanning in different directions of CoP/NiCoP. (d) The optimized hydrogen atom adsorption structure. (e) The schematic on the projected density of states. (f) The ΔGH+ values as the replaced Ni atoms increased. (g) The optimized hydrogen H2O adsorption structure. Panels a–g adapted with permission from ref. 192, copyright 2019, WILEY-VCH. | |
4. Conclusion and outlook
As a new generation of energy storage devices, BSHDs with high energy density, power density, and cycling stability have a wide application prospect. Due to the poor conductivity and structural stability, and the slow ion diffusion kinetics, the rate performance of transition metal compound-based cathodes cannot meet the demand, limiting the practical application of BSHDs. To solve this problem, this review introduces the energy storage mechanism of BSHDs and summarizes some efficient strategies of reinforcing the rate performance of transition metal compound-based cathodes. It may put forward a reference for developing new strategies to further improve the rate performance of transition metal compound-based cathodes in BSHDs.
With respect to the future design and fabrication of BSHDs, a number of points are still worth considering; the corresponding outlooks are listed below:
4.1 Optimizing the experimental method
In the preparation of transition metal sulfide/selenide/phosphate, toxic gases such as H2S, H2Se and PH3 may be produced, which are hazardous to human health. In addition, phosphorus-containing waste solution produced from the synthesis process needs to be carefully handled; otherwise it would cause environmental pollution. Therefore, the optimization of the preparation method is necessary.
4.2 Developing biomass-derived carbon materials
The complex synthesis process and high cost of graphene limit the wide application of transition metal compounds and graphene composites. Therefore, developing transition metal compound coupled biomass-derived carbon materials could be an effective strategy.
4.3 Amorphizing the surface
Amorphization is a process of making order crystals structurally amorphous. For electrode materials in SBHs, surface amorphization modulates the physicochemical properties, resulting in better electrochemical performance. Currently, most electrode materials are based on crystalline or layered compounds with good orderly crystallinity. However, a disorder part of the surface will be able to enhance the specific capacity of the material, and greatly increase the diffusion efficiency of ions, thus greatly improving the rate performance.193
4.4 Optimizing the electrolyte
Electrolyte is an important part of supercapacitors, whose interaction with the electrode would determine the electrode–electrolyte interface state, further having an impact on the rate performance. For example, aqueous electrolytes have high ionic conductivity, but are limited by low energy density and poor cycling stability. Organic electrolytes and ionic liquids usually have low ionic conductivity, although they can expand the potential window of electrode materials. Although water-in-salt electrolytes have a wide electrochemical window, making them promising electrolytes, their low conductivity and high viscosity limit their further application in SBHs. Therefore, there is a need for the design and development of more efficient electrolytes for SBHs.194
Author contributions
Cong Wang and Zehao Song wrote this manuscript; Pei Shi, Lin Lv, Houzhao Wan, Li Tao, Jun Zhang, Hanbin Wang, and Hao Wang supervised the work and revised the manuscript.
Conflicts of interest
We declare that we do not have any commercial or associative interest that represents a conflict of interest in connection with the work submitted.
Acknowledgements
This work was supported by the National Natural Science Foundation of China (No. 52002122), the Science and Technology Department of Hubei Province (No. 2019AAA038), the Project funded by the China Postdoctoral Science Foundation (No. 2021M690947) and the Wuhan Yellow Crane Talent Program (No. 2017-02).
References
- W. Xie, X. Jiang, T. Qin, H. Yang, D. Liu and D. He, Electrochim. Acta, 2017, 258, 1064–1071 CrossRef CAS.
- W. Guo, C. Yu, S. Li, X. Song, H. Huang, X. Han, Z. Wang, Z. Liu, J. Yu, X. Tan and J. Qiu, Adv. Mater., 2019, 31, e1901241 CrossRef PubMed.
- Y. Zhu, L. Peng, D. Chen and G. Yu, Nano Lett., 2016, 16, 742–747 CrossRef CAS PubMed.
- P. Xiong, R. Ma, N. Sakai, X. Bai, S. Li and T. Sasaki, ACS Appl. Mater. Interfaces, 2017, 9, 6282–6291 CrossRef CAS PubMed.
- K. Ghosh, S. Ng, C. Iffelsberger and M. Pumera, ACS Appl. Energy Mater., 2020, 3, 10261–10269 CrossRef CAS.
- F. Wu, J. Chen, L. Li, T. Zhao and R. Chen, J. Phys. Chem. C, 2011, 115, 24411–24417 CrossRef CAS.
- H. Nakanishi, I. Kikuta, H. Segawa, Y. Kawabata, R. Kishida, T. Norisuye and Q. Tran-Cong-Miyata, ChemSusChem, 2017, 10, 701–710 CrossRef CAS PubMed.
- P. Cai, K. Zou, X. Deng, B. Wang, M. Zheng, L. Li, H. Hou, G. Zou and X. Ji, Adv. Energy Mater., 2021, 11, 2003804 CrossRef CAS.
- H. Qian, B. Wu, Z. Nie, T. Liu, P. Liu, H. He, J. Wu, Z. Chen and S. Chen, Chem. Eng. J., 2021, 420, 127646 CrossRef CAS.
- M. Akhtar, J.-K. Chang and S. B. Majumder, J. Electrochem. Soc., 2020, 167, 110546 CrossRef CAS.
- T. Nguyen and M. F. Montemor, Adv. Sci., 2019, 6, 1801797 CrossRef PubMed.
- X. Zhang, W. Shi, J. Zhu, W. Zhao, J. Ma, S. Mhaisalkar, T. L. Maria, Y. Yang, H. Zhang, H. H. Hng and Q. Yan, Nano Res., 2010, 3, 643–652 CrossRef CAS.
- M. R. Das, A. Roy, S. Mpelane, A. Mukherjee, P. Mitra and S. Das, Electrochim. Acta, 2018, 273, 105–114 CrossRef CAS.
- K. Dai, C. Liang, J. Dai, L. Lu, G. Zhu, Z. Liu, Q. Liu and Y. Zhang, Mater. Chem. Phys., 2014, 143, 1344–1351 CrossRef CAS.
- A. Roy, A. Ray, S. Saha, M. Ghosh, T. Das, B. Satpati, M. Nandi and S. Das, Electrochim. Acta, 2018, 283, 327–337 CrossRef CAS.
- H. Mei, Z. Huang, B. Xu, Z. Xiao, Y. Mei, H. Zhang, S. Zhang, D. Li, W. Kang and D. F. Sun, Nano-Micro Lett., 2020, 12, 61 CrossRef CAS PubMed.
- S. Nandhini and G. Muralidharan, J. Solid State Electrochem., 2020, 25, 465–477 CrossRef.
- Y.-Y. Chen, P. Dhaiveegan, M. Michalska and J.-Y. Lin, Electrochim. Acta, 2018, 274, 208–216 CrossRef CAS.
- B. Xie, M. Yu, L. Lu, H. Feng, Y. Yang, Y. Chen, H. Cui, R. Xiao and J. Liu, Carbon, 2019, 141, 134–142 CrossRef CAS.
- X. Zhang, A. Wu, X. Wang, C. Tian, R. An and H. Fu, J. Mater. Chem. A, 2018, 6, 17905–17914 RSC.
- Y. Lu, J.-P. Tu, Q.-Q. Xiong, J.-Y. Xiang, Y.-J. Mai, J. Zhang, Y.-Q. Qiao, X.-L. Wang, C.-D. Gu and S. X. Mao, Adv. Funct. Mater., 2012, 22, 3927–3935 CrossRef CAS.
- D. Yang, Z. Lu, X. Rui, X. Huang, H. Li, J. Zhu, W. Zhang, Y. M. Lam, H. H. Hng, H. Zhang and Q. Yan, Angew. Chem., Int. Ed., 2014, 53, 9352–9355 CrossRef CAS PubMed.
- J. Tian, Q. Liu, A. M. Asiri and X. Sun, J. Am. Chem. Soc., 2014, 136, 7587–7590 CrossRef CAS PubMed.
- M. K. Wu, C. Chen, J. J. Zhou, F. Y. Yi, K. Tao and L. Han, J. Alloys Compd., 2018, 734, 1–8 CrossRef CAS.
- N. Tang, W. Wang, H. You, Z. Zhai, J. Hilario, L. Zeng and L. Zhang, Catal. Today, 2019, 330, 240–245 CrossRef CAS.
- Z. Xiao, L. Fan, B. Xu, S. Zhang, W. Kang, Z. Kang, H. Lin, X. Liu, S. Zhang and D. Sun, ACS Appl. Mater. Interfaces, 2017, 9, 41827–41836 CrossRef CAS PubMed.
- H. Huang, H. Zhang, Y. Fan, X. Deng, G. Li, X. Liang, W. Zhou, J. Guo and S. Tang, Appl. Surf. Sci., 2019, 481, 1220–1227 CrossRef CAS.
- F. Liu, X. Chu, H. Zhang, B. Zhang, H. Su, L. Jin, Z. Wang, H. Huang and W. Yang, Electrochim. Acta, 2018, 269, 102–110 CrossRef CAS.
- B. Huang, W. Wang, T. Pu, J. Li, J. Zhu, C. Zhao, L. Xie and L. Chen, J. Colloid Interface Sci., 2018, 532, 630–640 CrossRef CAS PubMed.
- M. Aghazadeh, A. Rashidi and M. R. Ganjali, Electron. Mater. Lett., 2017, 14, 37–45 CrossRef.
- S. Li, N. Sharma, C. Yu, Y. Zhang, G. Wan, R. Fu, H. Huang, X. Sun, S. J. Lee, J. S. Lee, D. Nordlund, P. Pianetta, K. Zhao, Y. Liu and J. Qiu, Adv. Mater., 2021, 33, e2006147 CrossRef PubMed.
- J. Zhao, B. Guan, B. Hu, Z. Xu, D. Wang and H. Zhang, Electrochim. Acta, 2017, 230, 428–437 CrossRef CAS.
- J. Zhu, L. Xiang, D. Xi, Y. Zhou and J. Yang, Bull. Mater. Sci., 2018, 41, 54 CrossRef.
- J. Ren, Q. Meng, Z. Xu, X. Zhang and J. Chen, J. Electroanal. Chem., 2019, 836, 30–37 CrossRef CAS.
- J. Li, Q. Li, J. Sun, Y. Ling, K. Tao and L. Han, Inorg. Chem., 2020, 59, 11174–11183 CrossRef CAS PubMed.
- T. Liu, J. Liu, L. Zhang, B. Cheng and J. Yu, J. Mater. Sci. Technol., 2020, 47, 113–121 CrossRef.
- Y. Cui, J. Zhang, C. Jin, Y. Liu, W. Luo and W. Zheng, Small, 2019, 15, e1804318 Search PubMed.
- L. Du, W. Du, H. Ren, N. Wang, Z. Yao, X. Shi, B. Zhang, J. Zai and X. Qian, J. Mater. Chem. A, 2017, 5, 22527–22535 RSC.
- J. Yang, Y. Yuan, W. Wang, H. Tang, Z. Ye and J. Lu, J. Power Sources, 2017, 340, 6–13 CrossRef CAS.
- S. Xie, J. Gou, B. Liu and C. Liu, J. Colloid Interface Sci., 2019, 540, 306–314 CrossRef CAS PubMed.
- Y. Hu, C. Huang, S. Jiang, Y. Qin and H. C. Chen, J. Colloid Interface Sci., 2020, 558, 291–300 CrossRef PubMed.
- P. Zhang, W. Wang, Z. Kou, J. Li, T. Wang and J. Guo, Ionics, 2021, 27, 801–810 CrossRef CAS.
- Y. Gan, C. Wang, X. Chen, P. Liang, H. Wan, X. Liu, Q. Tan, H. Wu, H. Rao, H. Wang, J. Zhang, Y. Wang, P. A. van Aken and H. Wang, Chem. Eng. J., 2020, 392, 123661 CrossRef CAS.
- Y. Jin, C. Zhao, Q. Jiang and C. Ji, Colloids Surf., A, 2018, 553, 58–65 CrossRef CAS.
- X. Zhang, L. Zhang, G. Xu, A. Zhao, S. Zhang and T. Zhao, J. Colloid Interface Sci., 2020, 561, 23–31 CrossRef CAS PubMed.
- J. Hei, L. Su, S. Chen, W. Ye, J. Zhan, L. Wang, Y. Gao, H. Wang and Y. Wang, Part. Part. Syst. Charact., 2019, 37, 1900344 CrossRef.
- P. Sun, Z. Li, L. Zhang, C. Dong, Z. Li, H. Yao, J. Wang and G. Li, J. Alloys Compd., 2018, 750, 607–616 CrossRef CAS.
- M. Gao, W.-K. Wang, X. Zhang, J. Jiang and H.-Q. Yu, J. Phys. Chem. C, 2018, 122, 25174–25182 CrossRef CAS.
- Y. Song, X. Cai, X. Xu and X.-X. Liu, J. Mater. Chem. A, 2015, 3, 14712–14720 RSC.
- S. Yang, Y. Liu, Y. Hao, X. Yang, W. A. Goddard, 3rd, X. L. Zhang and B. Cao, Adv. Sci., 2018, 5, 1700659 CrossRef PubMed.
- J. Chen, B. Luo, Q. Chen, F. Li, Y. Guo, T. Wu, P. Peng, X. Qin, G. Wu, M. Cui, L. Liu, L. Chu, B. Jiang, Y. Li, X. Gong, Y. Chai, Y. Yang, Y. Chen, W. Huang, X. Liu and M. Li, Adv. Mater., 2020, 32, e1905578 CrossRef PubMed.
- Y. Cheng, J. Shu, L. Xu, Y. Xia, L. Du, G. Zhang and L. Mai, Adv. Energy Mater., 2021, 11, 2100026 CrossRef CAS.
- J. Xu and L. Wang, Sci. Rep., 2019, 9, 12557 CrossRef PubMed.
- S. J. Arbaz, S. C. Sekhar, G. Nagaraju, B. Ramulu and J. S. Yu, Adv. Mater. Technol., 2020, 6, 2000793 CrossRef.
- M. M. Baig, E. Pervaiz, M. Azad, Z. Jahan, M. B. Khan Niazi and S. M. Baig, Ceram. Int., 2021, 47, 12557–12566 CrossRef CAS.
- Z. Ma, Z. Sun, H. Jiang, F. Li, Q. Wang and F. Qu, Appl. Surf. Sci., 2020, 533, 147521 CrossRef CAS.
- X. Wei, Y. Zhou, X. Shen, J. Di, X. Wang and Q. Li, Mater. Lett., 2021, 293, 129636 CrossRef CAS.
- N. Parveen, A. I. Al-Jaafari and J. I. Han, Electrochim. Acta, 2019, 293, 84–96 CrossRef CAS.
- Z. Tian, X. Wang, B. Li, H. Li and Y. Wu, Electrochim. Acta, 2019, 298, 321–329 CrossRef CAS.
- S. Yang, Z. Han, F. Zheng, J. Sun, Z. Qiao, X. Yang, L. Li, C. Li, X. Song and B. Cao, Carbon, 2018, 134, 15–21 CrossRef CAS.
- H. Chen, J. Jiang, L. Zhang, T. Qi, D. Xia and H. Wan, J. Power Sources, 2014, 248, 28–36 CrossRef CAS.
- C. Wang, J. Wang, W. Hu and D. Wang, Chem. Res. Chin. Univ., 2019, 36, 68–73 CrossRef.
- S. P. Gupta, M. A. More, D. J. Late and P. S. Walke, Electrochim. Acta, 2021, 366, 137389 CrossRef CAS.
- X. Yang, J. Mao, H. Niu, Q. Wang, K. Zhu, K. Ye, G. Wang, D. Cao and J. Yan, Chem. Eng. J., 2021, 406, 126713 CrossRef CAS.
- J. Qian, X. Wu, Y. Cao, X. Ai and H. Yang, Angew. Chem., Int. Ed., 2013, 52, 4633–4636 CrossRef CAS PubMed.
- C. V. V. M. Gopi, S. Sambasivam, K. V. G. Raghavendra, R. Vinodh, I. M. Obaidat and H.-J. Kim, Journal of Energy Storage, 2020, 30, 101550 CrossRef.
- M. Zhang, Y. Xu, H. Fan, N. Zhao, B. Yan, C. Wang, J. Ma, A. K. Yadav, W. Zhang, Z. Du, X. Zheng, M. Li, G. Dong and W. Wang, J. Alloys Compd., 2020, 826, 154115 CrossRef CAS.
- J.-G. Seong, T. H. Ko, D. Lei, W.-K. Choi, Y.-S. Kuk, M.-K. Seo and B.-S. Kim, Green Energy and Environment, 2021 DOI:10.1016/j.gee.2021.01.015.
- Z. Cai, L. Deng, Y. Song, D. Li, L. Hong and Z. Shen, Mater. Lett., 2020, 281, 128626 CrossRef.
- B. Kirubasankar, P. Palanisamy, S. Arunachalam, V. Murugadoss and S. Angaiah, Chem. Eng. J., 2019, 355, 881–890 CrossRef CAS.
- X. Wang, H. Yan, J. Zhang, X. Hong, S. Yang, C. Wang and Z. Li, J. Alloys Compd., 2019, 810, 151911 CrossRef CAS.
- Y. Lu, J. Liang, S. Deng, Q. He, S. Deng, Y. Hu and D. Wang, Nano Energy, 2019, 65, 103993 CrossRef CAS.
- Q. Meng, K. Qin, L. Ma, C. He, E. Liu, F. He, C. Shi, Q. Li, J. Li and N. Zhao, ACS Appl. Mater. Interfaces, 2017, 9, 30832–30839 CrossRef CAS PubMed.
- P. Cai, R. Momen, M. Li, Y. Tian, L. Yang, K. Zou, X. Deng, B. Wang, H. Hou, G. Zou and X. Ji, Chem. Eng. J., 2021, 420, 129647 CrossRef CAS.
- P. Sun, R. Wang, Q. Wang, H. Wang and X. Wang, Appl. Surf. Sci., 2019, 475, 793–802 CrossRef CAS.
- Y. Zhang, Y. Hu, Z. Wang, T. Lin, X. Zhu, B. Luo, H. Hu, W. Xing, Z. Yan and L. Wang, Adv. Funct. Mater., 2020, 30, 2004172 CrossRef CAS.
- K. Xiang, Z. Xu, T. Qu, Z. Tian, Y. Zhang, Y. Wang, M. Xie, X. Guo, W. Ding and X. Guo, Chem. Commun., 2017, 53, 12410–12413 RSC.
- X. Wei, X. Jiang, J. Wei and S. Gao, Chem. Mater., 2016, 28, 445–458 CrossRef CAS.
- Z. Ge, Y. Zhang, D. Fu, L. He and M. Li, Nano Select, 2021, 1–10 Search PubMed.
- K. Liu, X. Zheng, K. Wang, C. Wang and M. Chen, Carbon, 2019, 153, 265–273 CrossRef CAS.
- J. Tian, H. Zhang, Z. Liu, G. Qin and Z. Li, Int. J. Hydrogen Energy, 2018, 43, 1596–1605 CrossRef CAS.
- L. Gu, Y. Wang, R. Lu, W. Wang, X. Peng and J. Sha, J. Power Sources, 2015, 273, 479–485 CrossRef CAS.
- L. Long, Y. Yao, M. Yan, H. Wang, G. Zhang, M. Kong, L. Yang, X. Liao, G. Yin and Z. Huang, J. Mater. Sci., 2016, 52, 3642–3656 CrossRef.
- F. Zhu, W. Liu, Y. Liu and W. Shi, Chem. Eng. J., 2020, 383, 123150 CrossRef CAS.
- S. Zhang, J. Wu, J. Wang, W. Qiao, D. Long and L. Ling, J. Power Sources, 2018, 396, 88–94 CrossRef CAS.
- X. Yang, Y.-Y. Wang, B.-H. Hou, H.-J. Liang, X.-X. Zhao, H. Fan, G. Wang and X.-L. Wu, Acta Metall. Sin., 2020, 34, 390–400 CrossRef.
- B. Dou, J. Yan, Q. Chen, X. Han, Q. Feng, X. Miao and P. Wang, Sens. Actuators, B, 2021, 328, 129082 CrossRef CAS.
- Z.-Y. Gu, J.-Z. Guo, Z.-H. Sun, X.-X. Zhao, W.-H. Li, X. Yang, H.-J. Liang, C.-D. Zhao and X.-L. Wu, Sci. Bull., 2020, 65, 702–710 CrossRef CAS.
- R. B. Rakhi, W. Chen, M. N. Hedhili, D. Cha and H. N. Alshareef, ACS Appl. Mater. Interfaces, 2014, 6, 4196–4206 CrossRef CAS PubMed.
- T. Dang, G. Zhang, Q. Li, Z. Cao, G. Zhang and H. Duan, J. Colloid Interface Sci., 2020, 577, 368–378 CrossRef CAS PubMed.
- P. Zhang, J. Zhou, W. Chen, Y. Zhao, X. Mu, Z. Zhang, X. Pan and E. Xie, Chem. Eng. J., 2017, 307, 687–695 CrossRef CAS.
- B. Tong, W. Wei, Z. Wu, L. Zhao, W. Ye, J. Wang, W. Chen, C. Soutis and L. Mi, ACS Appl. Energy Mater., 2021, 4, 3221–3230 CrossRef CAS.
- W. Sun, L. Xiao and X. Wu, J. Alloys Compd., 2019, 772, 465–471 CrossRef CAS.
- Y. Xiao, A. Dai, X. Zhao, S. Wu, D. Su, X. Wang and S. Fang, J. Alloys Compd., 2019, 781, 1006–1012 CrossRef CAS.
- B. Guan, Y. Li, B. Yin, K. Liu, D. Wang, H. Zhang and C. Cheng, Chem. Eng. J., 2017, 308, 1165–1173 CrossRef CAS.
- X. Ma, L. Zhang, G. Xu, C. Zhang, H. Song, Y. He, C. Zhang and D. Jia, Chem. Eng. J., 2017, 320, 22–28 CrossRef CAS.
- W. Wang, L. Zhang, G. Xu, H. Song, L. Yang, C. Zhang, J. Xu and D. Jia, Inorg. Chem., 2018, 57, 10287–10294 CrossRef CAS PubMed.
- X. Lei, S. Ge, Y. Tan, Z. Wang, J. Li, X. Li, G. Hu, X. Zhu, M. Huang, Y. Zhu and B. Xiang, ACS Appl. Mater. Interfaces, 2020, 12, 9158–9168 CrossRef CAS PubMed.
- A. Banerjee, S. Bhatnagar, K. K. Upadhyay, P. Yadav and S. Ogale, ACS Appl. Mater. Interfaces, 2014, 6, 18844–18852 CrossRef CAS PubMed.
- L. Zhang, K. N. Hui, K. S. Hui, X. Chen, R. Chen and H. Lee, Int. J. Hydrogen Energy, 2016, 41, 9443–9453 CrossRef CAS.
- L. Wang, X. Li, T. Guo, X. Yan and B. K. Tay, Int. J. Hydrogen Energy, 2014, 39, 7876–7884 CrossRef CAS.
- S. Ji, Y. Ma, H. Wang, J. Key, D. J. L. Brett and R. Wang, Electrochim. Acta, 2016, 219, 540–546 CrossRef CAS.
- M. Shi, M. Cui, L. Kang, T. Li, S. Yun, J. Du, S. Xu and Y. Liu, Appl. Surf. Sci., 2018, 427, 678–686 CrossRef CAS.
- Y. Tao, Y. Wu, H. Chen, W. Chen, J. Wang, Y. Tong, G. Pei, Z. Shen and C. Guan, Chem. Eng. J., 2020, 396, 125364 CrossRef CAS.
- J. Chen, Z. Xu, H. Zhu, R. Liu, X. Song, Q. Song, J. Wu, C. Zhang, L. Ding, J. Dong and H. Cui, Vacuum, 2020, 174, 109219 CrossRef CAS.
- D. Guo, X. Song, F. Li, L. Tan, H. Ma, L. Zhang and Y. Zhao, Colloids Surf., A, 2018, 546, 1–8 CrossRef CAS.
- Z. Liu, W. Zhou, S. Wang, W. Du, H. Zhang, C. Ding, Y. Du and L. Zhu, J. Alloys Compd., 2019, 774, 137–144 CrossRef CAS.
- Y.-Y. Huang and L.-Y. Lin, ACS Appl. Energy Mater., 2018, 1, 2979–2990 CrossRef CAS.
- S. C. Lee, S. Liu, P. A. Shinde, K. Y. Chung and S. Chan Jun, Electrochim. Acta, 2020, 353, 136578 CrossRef CAS.
- P. Sivakumar, M. Jana, M. G. Jung, A. Gedanken and H. S. Park, J. Mater. Chem. A, 2019, 7, 11362–11369 RSC.
- X. Gao, X. Liu, D. Wu, B. Qian, Z. Kou, Z. Pan, Y. Pang, L. Miao and J. Wang, Adv. Funct. Mater., 2019, 29, 1903879 CrossRef.
- J. Acharya, T. H. Ko, J.-G. Seong, M.-K. Seo, M.-S. Khil, H.-Y. Kim and B.-S. Kim, ACS Appl. Nano Mater., 2020, 3, 8679–8690 CrossRef.
- F. Li, Z. Sun, H. Jiang, Z. Ma, Q. Wang and F. Qu, Energy Fuels, 2020, 34, 11628–11636 CrossRef CAS.
- Z. Li, W. He, X. Wang, X. Wang, M. Song and J. Zhao, Int. J. Hydrogen Energy, 2020, 45, 112–122 CrossRef CAS.
- N. Joseph, P. Muhammed Shafi and A. Chandra Bose, New J. Chem., 2018, 42, 12082–12090 RSC.
- S. Kasap, I. I. Kaya, S. Repp and E. Erdem, Nanoscale Adv., 2019, 1, 2586–2597 RSC.
- Y. Tang, H. Shen, J. Cheng, Z. Liang, C. Qu, H. Tabassum and R. Zou, Adv. Funct. Mater., 2020, 30, 1908223 CrossRef CAS.
- H. Liang, H. Jia, T. Lin, Z. Wang, C. Li, S. Chen, J. Qi, J. Cao, W. Fei and J. Feng, J. Colloid Interface Sci., 2019, 554, 59–65 CrossRef CAS PubMed.
- T. Xiong, M. Zhu, Y. Zhang, W. S. V. Lee, Z. G. Yu and J. Xue, Batteries Supercaps, 2020, 3, 519–526 CrossRef CAS.
- Y. Guo, X. Hong, Y. Wang, Q. Li, J. Meng, R. Dai, X. Liu, L. He and L. Mai, Adv. Funct. Mater., 2019, 29, 1809004 CrossRef.
- Y. Chen, D. Ni, X. Yang, C. Liu, J. Yin and K. Cai, Electrochim. Acta, 2018, 278, 114–123 CrossRef CAS.
- J. Huang, J. Wei, Y. Xiao, Y. Xu, Y. Xiao, Y. Wang, L. Tan, K. Yuan and Y. Chen, ACS Nano, 2018, 12, 3030–3041 CrossRef CAS PubMed.
- X. Liu, W. Zang, C. Guan, L. Zhang, Y. Qian, A. M. Elshahawy, D. Zhao, S. J. Pennycook and J. Wang, ACS Energy Lett., 2018, 3, 2462–2469 CrossRef CAS.
- J. Cao, J. Li, L. Li, Y. Zhang, D. Cai, D. Chen and W. Han, ACS Sustainable Chem. Eng., 2019, 7, 10699–10707 CrossRef CAS.
- X. Deng, K. Zou, R. Momen, P. Cai, J. Chen, H. Hou, G. Zou and X. Ji, Sci. Bull., 2021 DOI:10.1016/j.scib.2021.04.042.
- D. H. Liu, W. H. Li, Y. P. Zheng, Z. Cui, X. Yan, D. S. Liu, J. Wang, Y. Zhang, H. Y. Lu, F. Y. Bai, J. Z. Guo and X. L. Wu, Adv. Mater., 2018, 30, e1706317 CrossRef PubMed.
- M. Yang, Q. Ning, C. Fan and X. Wu, Chin. Chem. Lett., 2021, 32, 895–899 CrossRef CAS.
- T. Liu, L. Zhang, W. You and J. Yu, Small, 2018, 14, e1702407 CrossRef PubMed.
- A. M. Elshahawy, C. Guan, W. Zang, S. Ding, Z. Kou, S. J. Pennycook, N. Yan and J. Wang, ACS Appl. Energy Mater., 2018, 2, 616–626 CrossRef.
- Y. Meng, P. Sun, W. He, B. Teng and X. Xu, Nanoscale, 2019, 11, 688–697 RSC.
- A. M. Elshahawy, C. Guan, X. Li, H. Zhang, Y. Hu, H. Wu, S. J. Pennycook and J. Wang, Nano Energy, 2017, 39, 162–171 CrossRef CAS.
- Q. Li, H. Guo, R. Xue, M. Wang, M. Xu, W. Yang, J. Zhang and W. Yang, Int. J. Hydrogen Energy, 2020, 45, 20820–20831 CrossRef CAS.
- P. Liu, M. Yang, S. Zhou, Y. Huang and Y. Zhu, Electrochim. Acta, 2019, 294, 383–390 CrossRef CAS.
- T. Liu, C. Jiang, B. Cheng, W. You and J. Yu, J. Power Sources, 2017, 359, 371–378 CrossRef CAS.
- T. Liu, L. Zhang, B. Cheng, W. You and J. Yu, Chem. Commun., 2018, 54, 3731–3734 RSC.
- D. Zhang, X. Zhang, Y. Chen, C. Wang, Y. Ma, H. Dong, L. Jiang, Q. Meng and W. Hu, Phys. Chem. Chem. Phys., 2012, 14, 10899–10903 RSC.
- S. Zhou, X. Jin, S. Zhu, Q. Luo, Z. Qiu, A. Wu and H. Huang, Chin. Chem. Lett., 2020, 31, 2353–2357 CrossRef CAS.
- C. Xiong, B. Li, X. Lin, H. Liu, Y. Xu, J. Mao, C. Duan, T. Li and Y. Ni, Composites, Part B, 2019, 165, 10–46 CrossRef CAS.
- H. Yang, S. Kannappan, A. S. Pandian, J. H. Jang, Y. S. Lee and W. Lu, Nanotechnology, 2017, 28, 445401 CrossRef PubMed.
- W. Liu, K. Feng, Y. Zhang, T. Yu, L. Han, G. Lui, M. Li, G. Chiu, P. Fung and A. Yu, Nano Energy, 2017, 34, 491–499 CrossRef CAS.
- Y. Zhang, Y. Shen, X. Xie, W. Du, L. Kang, Y. Wang, X. Sun, Z. Li and B. Wang, Mater. Des., 2020, 196, 109111 CrossRef CAS.
- U. Singh, A. Banerjee, D. Mhamane, A. Suryawanshi, K. K. Upadhyay and S. Ogale, RSC Adv., 2014, 4, 39875–39883 RSC.
- H. Xing, W. He, Y. Liu, G. Long, Y. Sun, J. Feng, W. Feng, Y. Zhou, Y. Zong, X. Li, X. Zhu and X. Zheng, ACS Appl. Mater. Interfaces, 2021, 13, 26373–26383 CrossRef CAS PubMed.
- A. Namdarian, A. G. Tabrizi, A. Maseleno, A. Mohammadi and S. E. Moosavifard, Int. J. Hydrogen Energy, 2018, 43, 17780–17787 CrossRef CAS.
- S. Zhou, W. Wei, Y. Zhang, S. Cui, W. Chen and L. Mi, Sci. Rep., 2019, 9, 12727 CrossRef PubMed.
- W. Luo, G. Zhang, Y. Cui, Y. Sun, Q. Qin, J. Zhang and W. Zheng, J. Mater. Chem. A, 2017, 5, 11278–11285 RSC.
- Y. Yan, K. Li, X. Chen, Y. Yang and J. M. Lee, Small, 2017, 13, 1701724 CrossRef PubMed.
- P. Ji, J. Wan, Y. Xi, Y. Guan, C. Zhang, X. Gu, J. Li, J. Lu and D. Zhang, Nanotechnology, 2019, 30, 335401 CrossRef CAS PubMed.
- K. Li, M. Liu, S. Li, F. Huang, L. Wang and H. Zhang, J. Alloys Compd., 2020, 817, 152712 CrossRef CAS.
- L. Wang, Y. Guan, X. Zhao, J. Mu, H. Che, H. Li and Z. Guo, J. Mater. Sci.: Mater. Electron., 2018, 29, 5782–5790 CrossRef CAS.
- W. Wei, J. Wu, S. Cui, Y. Zhao, W. Chen and L. Mi, Nanoscale, 2019, 11, 6243–6253 RSC.
- C. Wang, Z. Song, H. Wan, X. Chen, Q. Tan, Y. Gan, P. Liang, J. Zhang, H. Wang, Y. Wang, X. Peng, P. A. van Aken and H. Wang, Chem. Eng. J., 2020, 400, 125955 CrossRef CAS.
- N. Zhang, X. Li, T. Hou, J. Guo, A. Fan, S. Jin, X. Sun, S. Cai and C. Zheng, Chin. Chem. Lett., 2020, 31, 1221–1225 CrossRef CAS.
- S. Wu, H. Guo, K. S. Hui and K. N. Hui, Electrochim. Acta, 2019, 295, 759–768 CrossRef CAS.
- R. K. Pandey, Y. Totake, S. Soh and H. Nakanishi, ChemistrySelect, 2019, 4, 13543–13550 CrossRef CAS.
- J. M. Jeong, S. H. Park, H. J. Park, S. B. Jin, S. G. Son, J. M. Moon, H. Suh and B. G. Choi, Adv. Funct. Mater., 2021, 31, 2009632 CrossRef CAS.
- T. Peng, H. Wang, H. Yi, Y. Jing, P. Sun and X. Wang, Electrochim. Acta, 2015, 176, 77–85 CrossRef CAS.
- X. Feng, Y. Huang, M. Chen, X. Chen, C. Li, S. Zhou and X. Gao, J. Alloys Compd., 2018, 763, 801–807 CrossRef CAS.
- X. Guo, W. Zhang, C. Qian, H. Yang and T. Fan, Ceram. Int., 2018, 44, 9696–9702 CrossRef CAS.
- B. Wei, H. Liang, Z. Qi, D. Zhang, H. Shen, W. Hu and Z. Wang, Chem. Commun., 2019, 55, 1402–1405 RSC.
- Z. Hao, X. He, H. Li, D. Trefilov, Y. Song, Y. Li, X. Fu, Y. Cui, S. Tang, H. Ge and Y. Chen, ACS Nano, 2020, 14, 12719–12731 CrossRef CAS PubMed.
- Y.-Y. Wang, B.-H. Hou, J.-Z. Guo, Q.-L. Ning, W.-L. Pang, J. Wang, C.-L. Lü and X.-L. Wu, Adv. Energy Mater., 2018, 8, 1703252 CrossRef.
- J. Huang, Y. Xiong, Z. Peng, L. Chen, L. Wang, Y. Xu, L. Tan, K. Yuan and Y. Chen, ACS Nano, 2020, 14, 14201–14211 CrossRef CAS PubMed.
- H. Xing, G. Long, J. Zheng, H. Zhao, Y. Zong, X. Li, Y. Wang, X. Zhu, M. Zhang and X. Zheng, Electrochim. Acta, 2020, 337, 135817 CrossRef CAS.
- C. Zhang, C. Lei, C. Cen, S. Tang, M. Deng, Y. Li and Y. Du, Electrochim. Acta, 2018, 260, 814–822 CrossRef CAS.
- X. Zheng, Y. Sun, S. Jin, K. Zhang, Y. Li, J. Yan, H. Qin and H. Ni, Int. J. Electrochem. Sci., 2020, 15, 6249–6256 CrossRef CAS.
- C. Lu, A. Li, T. Zhai, C. Niu, H. Duan, L. Guo and W. Zhou, Energy Storage Mater., 2020, 26, 472–482 CrossRef.
- Y. Tian, J. Liu, X. Song, L. Zhao, P. Zhang and L. Gao, Compos. Sci. Technol., 2020, 197, 108263 CrossRef CAS.
- J. Ye, B. Hu, Y. Jin, Z. Wang, Y. Xi, L. Fang and Q. Pan, Electrochim. Acta, 2020, 349, 136372 CrossRef CAS.
- Y. Ma, C. Hou, H. Zhang, Q. Zhang, H. Liu, S. Wu and Z. Guo, Electrochim. Acta, 2019, 315, 114–123 CrossRef CAS.
- S. Mondal, U. Rana and S. Malik, J. Phys. Chem. C, 2017, 121, 7573–7583 CrossRef.
- J. Fu, J. Yun, S. Wu, L. Li, L. Yu and K. H. Kim, ACS Appl. Mater. Interfaces, 2018, 10, 34212–34221 CrossRef CAS PubMed.
- I. Chakraborty, N. Chakrabarty, A. Senapati and A. K. Chakraborty, J. Phys. Chem. C, 2018, 122, 27180–27190 CrossRef CAS.
- C. Pan, Z. Liu, W. Li, Y. Zhuang, Q. Wang and S. Chen, J. Phys. Chem. C, 2019, 123, 25549–25558 CrossRef CAS.
- W. Bi, J. Wang, E. P. Jahrman, G. T. Seidler, G. Gao, G. Wu and G. Cao, Small, 2019, 15, e1901747 CrossRef PubMed.
- T. Hao, Y. Liu, G. Liu, C. Peng, B. Chen, Y. Feng, J. Ru and J. Yang, Energy Storage Mater., 2019, 23, 225–232 CrossRef.
- Z. Gao, L. Zhang, J. Chang, Z. Wang, D. Wu, F. Xu, Y. Guo and K. Jiang, Chem. Eng. J., 2018, 335, 590–599 CrossRef CAS.
- Z. Gao, X. Liu, J. Chang, D. Wu, F. Xu, L. Zhang, W. Du and K. Jiang, J. Power Sources, 2017, 337, 25–35 CrossRef CAS.
- K. Seevakan, A. Manikandan, P. Devendran, A. Baykal and T. Alagesan, Ceram. Int., 2018, 44, 17735–17742 CrossRef CAS.
- X. Long, Z. Zeng, E. Guo, X. Shi, H. Zhou and X. Wang, J. Power Sources, 2016, 325, 264–272 CrossRef CAS.
- X. Zhao, H. Wan, P. Liang, N. Wang, C. Wang, Y. Gan, X. Chen, Q. Tan, X. Liu, J. Zhang, Y. Wang, H. Wang and H. Wang, Nano Res., 2021, 14, 2574–2583 CrossRef CAS.
- Y. Song, X. Zhao and Z.-H. Liu, Electrochim. Acta, 2021, 374, 137962 CrossRef CAS.
- S. B. Kale, A. C. Lokhande, R. B. Pujari and C. D. Lokhande, J. Colloid Interface Sci., 2018, 532, 491–499 CrossRef CAS PubMed.
- N. Karthik, T. N. J. I. Edison, R. Atchudan, D. Xiong and Y. R. Lee, J. Electroanal. Chem., 2019, 833, 105–112 CrossRef CAS.
- S. Li, T. Chen, J. Wen, P. Gui and G. Fang, Nanotechnology, 2017, 28, 445407 CrossRef PubMed.
- F. Yang, J. Wang, S. Gao, S. Zhou and Y. Kong, Mol. Catal., 2020, 486, 110873 CrossRef CAS.
- X. Li, X. Xiao, Q. Li, J. Wei, H. Xue and H. Pang, Inorg. Chem. Front., 2018, 5, 11–28 RSC.
- N. L. W. Septiani, Y. V. Kaneti, K. B. Fathoni, K. Kani, A. E. Allah, B. Yuliarto, Nugraha, H. K. Dipojono, Z. A. Alothman, D. Golberg and Y. Yamauchi, Chem. Mater., 2020, 32, 7005–7018 CrossRef CAS.
- P. Tian, Y. Wang, W. Li, S. Song, S. Zhou, H. Gao, H. Xu, X. Tian and J. Zang, J. Catal., 2020, 382, 109–120 CrossRef CAS.
- S. Ahmad, C. Yang, W. Xie, Z. Deng, H. Zhang, Y. Zhao and X. Su, Carbon, 2020, 158, 912–921 CrossRef CAS.
- B. Li, P. Gu, Y. Feng, G. Zhang, K. Huang, H. Xue and H. Pang, Adv. Funct. Mater., 2017, 27, 1605784 CrossRef.
- Y. Lin, K. Sun, S. Liu, X. Chen, Y. Cheng, W. C. Cheong, Z. Chen, L. Zheng, J. Zhang, X. Li, Y. Pan and C. Chen, Adv. Energy Mater., 2019, 9, 1901213 CrossRef.
- T. Zhou, Y. Zheng, H. Gao, S. Min, S. Li, H. K. Liu and Z. Guo, Adv. Sci., 2015, 2, 1500027 CrossRef PubMed.
- H. Liu, X. Liu, S. Wang, H.-K. Liu and L. Li, Energy Storage Mater., 2020, 28, 122–145 CrossRef.
Footnote |
† These authors have contributed equally to this work. |
|
This journal is © The Royal Society of Chemistry 2021 |
Click here to see how this site uses Cookies. View our privacy policy here.