DOI:
10.1039/D1RA02785A
(Paper)
RSC Adv., 2021,
11, 26110-26119
Coal fly ash driven zeolites for the adsorptive removal of the ceftazidime drug†
Received
9th April 2021
, Accepted 12th July 2021
First published on 29th July 2021
Abstract
The overall cost and efficiency of an adsorbent material is a major issue in deriving a sorbent into commercial markets. In this study, efforts have been directed to produce adsorption-capable zeolites from the dispensable product of coal power plants, i.e., coal fly ash (CFA). In addition, coal mining water (CW) was used as a direct hydrothermal solvent. The mine water from China's coal mines was used in this experiment to substitute tap water (TP) for synthesizing zeolite from C-type fly ashes with different crystallization temperatures (45 to 95 °C). Here, CW led to the formation of X-type and A-type zeolites of comparable size. Regarding the proper utilization of waste products, i.e., coal fly ash and mine water, the study paves a simple yet extremely cost-effective approach to synthesize workable zeolitic materials for adsorption purposes. The detailed characterization justified the use of CW as a better solvent than TP to prepare zeolites based on their better granular size and fewer carbon impurities. The prepared zeolites were later used as an adsorbent for the trace removal of ceftazidime (CAZ), taken as a model pharmaceutical pollutant. The zeolites prepared using CW realised a higher adsorption capacity of 80 mg g−1 during 20 min of agitation time. The pH, concentration, and external salt effects were also studied to achieve maximum removal efficiency. In general, the proposed approach enables the production of affordable yet efficient zeolite-based adsorbent materials without consuming any toxic and expensive reagents for practical application in environmental remediations.
1 Introduction
The growing use of pharmaceuticals has raised a significant environmental concern based on their proportionally increasing levels in aquatic bodies. Among many, the release of antibiotics in the form of hospital waste effluent is highly alarming based on the posed ecological and topological risk. The residual antibiotics have been associated with promoting drug-resistant bacteria, which eventually contributes to deteriorating human health via water consumption or the food cycle. The persistent nature, let alone the difficulties of a practical system for the efficient removal of antibiotics, requires material scientists' urgent attention to develop a feasible, environmentally friendly, yet economically viable approach on removing such drugs. Although conventional strategies, such as advanced oxidation, hydrolysis, and photo-degradation, are promising routes towards the efficient removal of many water pollutants, using such strategies to remove antibiotics is not practical based on the secondary byproduct production that might compromise the water quality.1,2 Among the most practical and preparative scale approaches is the adsorption technology, which effectively provides an economic benefit, besides the need for any renewability or large infrastructural requirements.3,4 The recent advancement in material science has led to developing various efficient adsorbents, such as activated carbon, nanomaterials, clays, molecular sieves, MOF, and their hybrid composites.5,6 However, the precursor material's added preparation cost to prepare such adsorbents restrains their practical viability for real-time, large-volume applications, i.e., hospital effluents or sewage.7,8 Here, the use of zeolites (adsorbent) driven directly from coal fly-ash (CFA), a leftover product of burned coal, has attracted significant research attention due to its economic viability, easy preparation method, and wide availability of cheap precursor ingredients.4,9 Zeolites, based on their thermal stability, large surface area, extremely high porosity, and high adsorption capacity, are widely considered in the area of gas-separation, water purification, and remediation.10–12 Zeolites have useful applications in separation, filtration, ion exchange, catalysis, and adsorption processes due to their negatively charged surface and internal pores, chemical structure, and interesting properties.13 Among many, the silica-based zeolites are also used for the adsorption of organic micropollutant, i.e., 2,4,6-trichlorophenol (TCP). The theoretical and experimental evidence supported the excellent adsorption capacity, besides revealing the corresponding adsorption mechanism. The wide variety of precursor materials, such as rice husk, kaolin, and coal fly ash, are recognized as universal adsorbents, which could be obtained from locally available ingredients.4 In the context of fly ash, China is one of the biggest coal consumers and producers, with an annual CFA production of 7.8 × 108 metric tons.14 The large quantity of annually produced CFA is primarily utilized for construction purposes, such as road sub-base material. However, the utilization efficacy remains low based on CFA's granular inconsistency. The conversion of fly ash into a value-added product, such as zeolites (which could later be considered for practical application), would not only contribute to waste management, but also to the ecological and economic growth of coal-consuming nations, such as China.15–17 Although numerous efforts have been taken to produce high-quality zeolites from coal fly ash, the quality of the final product depends on multiple factors ranging from the composition of CFA, synthesis route, temperature, pH, the solvent's nature, and alkalinity of the system.18,19
The coal mining process results in acidic or circumneutral mine water, as defined by the coal mine bedrock geology. The acid mine drainage (AMD) is produced when the sulfide-bearing material is exposed to oxygen and water. Here, the acidophilic bacteria accelerate AMD development and risk environmental toxicity when released in rivers and other groundwater flows. In other cases when AMD passes through dolomite-rich minerals, it transforms to the partially neutralized, circumneutral mine water, which is categorized as either Ca–Mg or Na-rich. Since coal mines and coal-fired power stations are typically close to each other, developing a comprehensive strategy to eliminate their byproducts by leveraging economies of scale would be useful.20
Coal-mine water is a rich source of various ion species that could facilitate or regulate zeolite growth.21–23 Furthermore, as a secondary waste product, the efficient utilization of mine water to produce efficient zeolite would eventually reduce the overall product cost, leading to rapid commercialization.24 In this study, we explore the potential effect of the solvent on the hydrothermal growth of zeolite from CFA using the alkali-dissolution approach. Here, the C-type coal fly ashes with varying Si/Al ratios were collected from the Beijing thermal power station and the Beilun power station in Zhejiang to synthesize zeolite-X and zeolite A using simple hydrothermal treatment. In addition, the morphology variation of zeolite in reference to the hydrothermal solvent's nature, i.e., coal mine water (CW) or tap water (TP) were studied. Their compositional alteration against the solvation temperature was varied in the range of 45–95 °C. As a proof-of-concept, the synthesized zeolites were also utilized as an adsorbent to remove trace quantities of ceftazidime (CAZ), a broad-spectrum antibiotic drug for bacterial infections. The proposed strategy to synthesize zeolites from CFA using mine water as a solvent system and its effective use as a sorbent to remove ceftazidime anticipate the viability route of the materials towards practical environmental remediation of hospital waste effluent.
2 Experimental
2.1. Materials and methods
Two coal fly ash samples denoted as CFA1 and CFA2 obtained from Beijing thermal power station (880 MW), and Beilun power station, Zhejiang China (5000 MW) were used as a precursor to the zeolites, respectively. Ceftazidime, NaOH, and HCl were purchased from Beijing chemical reagent Co., Ltd. These reagents are analytically pure, and no further purification is required. The TP was collected from the laboratory, whereas the CW was obtained from coal mines in Henan province, Xiang Sheng City, in China.
2.2. Synthesis of zeolites
The coal fly ashes, i.e., CFA1 and CFA2, were converted into zeolites using a simple hydrothermal approach. The experiments were carried with both TP and CW as a hydrothermal solvent for each CFA. In a typical experiment, 10.0 g of CFA1 and CFA2, previously passed through a 325-mesh sieve, were grounded with solid NaOH in a 1
:
1.2 ratio. The sodium hydroxide (NaOH) present in the mixture acts as an activator during the pre-fusion process to form soluble substances, silicate and aluminate, besides participating in zeolite formation. The Na+ also plays an essential role in zeolization, besides stabilizing its framework's sub-building unit, which is vital in zeolite formation under hydrothermal conditions. The obtained alkali-integrated mixtures were first heat-fused at 550 °C in ceramic crucibles to complete the fusion process. The materials were later dispersed in TP and CW in a ratio of 1
:
5 following ultrasonic treatment for 2 h before their hydrothermal treatment in Teflon reactors at different temperatures of 45, 65, 80, and 95 °C for 9 h. The final material was thoroughly washed with de-ionized water until the supernatant's pH reached <10, followed by overnight drying at 90 °C and filtering through mesh-100 before adsorption studies.
2.3. Characterization
Scanning Electron Microscopy (SEM) (Mdtf-6200) was used for the morphological characterization, whereas laser granulometry (Malvern Mastersizer 3000E) was considered for the evaluation of the CFA particle size. X-ray fluorescence (XRF) Axios FAST was utilized for major oxides and trace elements, and X-ray diffraction (XRD) Rigaku Smart Lab (X-ray 40 kV/100 mA) was used for compositional characteristics of the synthesized zeolites. The samples were verified for inorganic compounds through JCPDS (Joint Committee on Powder Diffraction Standards) documents. The BET (Brunauer, Emmett, and Teller) device used in the particle analyzer (Micromeritics Gemini 2375 and Gemini V) determines the specific surface area (m2 g−1). The pH of mine water was examined using a PHSJ-4F PH Meter, whereas the elemental analysis was obtained using ICP-MS (inductively-coupled plasma mass spectrometry).
3 Results and discussion
3.1. Characterization of collected coal fly ashes
The compositional characterization of the CFAs was obtained using XRF analysis. The major oxides are shown in Table 1, respectively. The Si, Al, and Fe oxide contents are approximately 56.4% and 61% in CFA1 and CFA2, respectively. Therefore, the fly ash were classified as type-C, as referenced against the ASTM standard C618. Such types of fly ashes are usually produced by burning low-rank (lignite or sub-bituminous) coal. The low amount of Ca in both types of fly ashes indicates their suitability as a precursor material for zeolite. In general, a high calcium environment has been linked to structural brittleness, and excessive Fe (magnetite) has also been proven harmful to zeolite synthesis. In this case, the low Fe content in CFA1 and CFA2 (less than 4%) suggests their suitability for zeolite synthesis. In addition, the ratio of SiO2/Al2O3, which is regarded as an indicator of the chemical ion-exchange capability, was determined to be 1.01 and 1.21, respectively (Nicholas M. Musyoka 2013;24 Ameh et al., 2017).28
Table 1 XRF based elemental composition of CFA1 and CFA2
Major constituents (oxides) |
Content (wt%) |
CFA1 |
CFA2 |
Al2O3 |
27 |
26.6 |
SiO2 |
27.4 |
32.4 |
Fe2O3 |
2 |
2.1 |
CO2 |
38.2 |
26.7 |
MgO |
0.2 |
2.5 |
CaO |
2.1 |
6.3 |
LOI |
0.10 |
0.12 |
SiO2/Al2O3 |
1.01 |
1.21 |
Others |
3.3 |
3.4 |
Fig. 1 and 2 shows the SEM images of CFA1 and CFA2, along with their corresponding EDX spectra. Although most CFA particles have a consistent spherical shape, certain forms are uneven and are coated by smaller particles and lumps of unburned carbon. The average size of these particles were determined to be 20 to 250 μm. The physical properties of fly ash depend on the feed coal size and the type of combustion. Fig. 1 and 2(c) shows the EDX spectra of the CFA1 and CFA2, where Al, C, O, and Si were identified as major elements. The corresponding particle size distribution and XRD pattern are further shown in Fig. S1.† A bell-shaped curved with a particulate distribution in the range of 0.5 to 200 μm is evident in each case. However, the distribution curve for CFA1 indicates a relatively smaller grain size compared to CFA2. The recorded XRD patterns are shown in Fig. S1(b),† with typical peaks related to quartz and mullite as the dominant components, and mullite < quartz in CFA1 and CFA2 (JCPDS card 46-1045 and 15-0776).
 |
| Fig. 1 (a and b) SEM images for CFA1; (c) the corresponding EDX spectra with elemental mapping indicating Al and O as major elements besides unburned carbon residues. | |
 |
| Fig. 2 (a and b) SEM images for CFA2; (c) the corresponding EDX spectra; the inset shows the elemental mapping with O and Al as major elements and relatively lower carbon content than CFA1. | |
3.2. Compositional analysis of the hydrothermal solvents
In the case of synthetic zeolite, the nature of the hydrothermal solvent directly influences the growth of zeolites. In this study, we have considered coal mine water (CW), a cheap mineral-rich end-product of coal mining, to produce zeolites. In addition, simple TP was utilized as a standard solvent system for zeolite growth. The compositional constituents of CW and TP are shown in Table 2. As evident, the rich elemental constituents present in CW were compared to TP. These ionic species could significantly lower the nucleation energy and serve as nucleation sites for the zeolites' growth. Moreover, the CW is relatively alkaline (pH = 8.3) compared to TP (pH = 7.0), which further contributes to the dissolution of ionic species and contributes to zeolite formation. Table 2 indicates that the content of Ca, Mg, Si, and Al is relatively lower in CW than TP, demonstrating the suitability of the former solvent for zeolite growth. The high Mg, Ca, Na, and Cl content in TP is ascribed to the conventional pre-treatment for palatable purposes.
Table 2 ICP-based chemical analysis of tap water and coal mine water
Cationic species |
Tap water (mg l−1) |
Coal mine water (mg l−1) |
Ag |
1.2 |
15 |
Al |
6.2 |
5.8 |
Ca |
13 000 |
1500 |
Cl |
7500 |
7500 |
Fe |
1.1 |
11 |
K |
950 |
8.3 |
Mg |
5900 |
620 |
Na |
5700 |
370 |
Si |
740 |
640 |
Sr |
820 |
5.5 |
Ti |
32 |
32 |
P |
15 |
15 |
As |
0.93 |
0.096 |
Cd |
0.026 |
0.026 |
Cr |
0.057 |
0.057 |
Hg |
0.021 |
0.021 |
Pb |
0.02 |
0.036 |
Zn |
0.62 |
1 |
Cu |
1.2 |
1.2 |
Pd |
3.3 |
3.3 |
3.3. Synthesis of zeolites from CFA
The zeolites were prepared from CFA using a simple hydrothermal approach following the procedure illustrated in Fig. 3. In general, obtained fly ashes, i.e., CFA1 and CFA2, were initially fused with alkali (NaOH) at 550 °C in ceramic crucibles, followed by dissolution of the material in TP or CW. The mixtures were then stirred for 2 h, resulting in a thick gel-like substance that was later transferred to a Teflon-reactor for hydrothermal treatment at different temperatures in the range of 45 to 95 °C for 9 h. The prepared zeolites were later washed and dried overnight at 90 °C. The CFA1 and CFA2 were systematically converted into zeolites using TP and CW as hydrothermal solvents, respectively. Fig. 4 shows the SEM images and corresponding XRD patterns for zeolites synthesized using CFA1 and CW at temperatures of 45 °C, 65 °C, 80 °C, and 95 °C. Unlike its TP counterpart (Fig. 5), the zeolite prepared using CW possesses better granular quality with less aggregation between the individual cube-shaped units. The corresponding XRD pattern also confirms the presence of peaks at 7, 10, 12, 24, 30, 32, and 35° attributed to type 4A of the zeolite (JCPDS card 43-0142). It is clear that at lower temperatures, i.e., 45 °C and 65 °C, the growth of the zeolite is incomplete with intense aggregation between the formed particles. Thus, the optimum temperature in the case of CFA1 using CW was determined to be 95 °C. The SEM images show that the application of CW may successfully assist zeolite development with a cubic-shaped morphology and homogeneous size distribution starting at 80 °C (Fig. 4(c)), as opposed to TP, which requires a high temperature of 95 °C to achieve correct cubic shape morphology (Fig. 5(d)). The aggregation between the cube-like zeolites is evident in TP (Fig. 5(d)). In contrast, the zeolites obtained using CW are highly dispersive and aggregation-free, making them ideal for adsorption applications. The XRD pattern for the TP-treated zeolite consists of additional peaks attributed to the sodalite phase, besides type 4A reflecting the compositional inconsistencies obtained after using TP as solvent. The SEM images and XRD pattern of the zeolites produced from CFA2 using CW and TP are shown in Fig. 6 and 7. In comparison to TP-produced zeolites, CW-produced zeolites have somewhat better morphological characteristics. The cube-like morphology started to form at 65 °C, compared to the TP-assisted zeolites, where such formation was attained at 80 °C. The XRD pattern confirms this growth process, where major peaks were attributed to X-type zeolite and gradually intensified with the rise of temperature from 45 °C to 95 °C. The crystal shape of the X-type zeolite is a typical octahedron belonging to the faujasite group. This difference in the obtained nature of zeolite using CFA1 and CFA2 could be directly attributed to the distinctive chemical composition of the utilized coal fly ashes. Fig. 8 shows the energy-dispersive X-ray spectroscopy (EDX) analysis of the zeolite samples prepared from CFA1 and CFA2 with TP and CW solvents at 95 °C, respectively. Here, Si, Al, and Na are the main components of the zeolites, indicating their complete formation without any structural impurities. Table 3 further shows the specific surface area obtained using BET analysis. The TP-assisted zeolites have a lower specific surface area than CW-assisted zeolites, indicating the latter's suitability for adsorption experiments. Based on the SEM, EDX, BET, and XRD observation, it is safe to conclude that the preparation of the zeolite using CFA with coal mine water could relatively improve the zeolite compositional quality compared to TP as dissolution during the hydrothermal treatment.
 |
| Fig. 3 Diagram showing a systematic approach to preparing zeolites using the hydrothermal approach with the coal mine water and tap water as dissolution solvents. | |
 |
| Fig. 4 (a–d) SEM images for zeolite synthesized from CFA1 using CW at different temperatures of 45, 65, 80 and 95 °C respectively; (e) the corresponding XRD patterns with major peaks attributed to type-4A zeolite. | |
 |
| Fig. 5 (a–d) SEM images for zeolite synthesized from CFA1 using TP at different temperatures of 45, 65, 80 and 95 °C, respectively; (e) the corresponding XRD patterns with major peaks attributed to type-4A zeolite in the presence of sodalite phase. | |
 |
| Fig. 6 (a–d) SEM images of zeolites synthesized from CFA2 using CW at different temperatures of 45, 65, 80, and 95 °C, respectively; (e) the corresponding XRD patterns with major peaks attributed to type-X zeolite. | |
 |
| Fig. 7 (a–d) SEM images for zeolite synthesized from CFA2 using TP at different temperatures of 45, 65, 80, and 95 °C, respectively; (e) the corresponding XRD patterns with major peaks attributed to type-X zeolite. | |
 |
| Fig. 8 EDX spectra of analysis of respective zeolite samples prepared at 95 °C from (a and b) CFA1 and (c and d) CFA2 using CW and TP as hydrothermal dissolution solvents. | |
Table 3 Specific surface area of the synthesized zeolites using CFA1 and CFA2 obtained from BET analysis
Zeolites |
Specific surface area (m2 g−1) |
Zeolite 4A (CMW) |
18.32 |
Zeolite 4A (DW) |
13.66 |
Zeolite X (CMW) |
15.02 |
Zeolite X (DW) |
11.32 |
3.4. Adsorption performance of the prepared zeolites for the removal of CAZ drug
The zeolites are known for their high adsorptive characteristics. In this case, superior morphologies of zeolites prepared at 95 °C using CFA1 and CFA2 using only CW were primarily selected for the adsorption of the CAZ drug. The said zeolites are denoted as ZE-1 and ZE-2 for adsorption purposes. In a bath experiment, fixed 0.01 g of prepared zeolites, i.e., ZE-1 and ZE-2 powders, were allowed to agitate with 1 mg mL−1 of the CAZ drug for 20 min of reaction time. The change in the CAZ concentration was measured using LC with a UV detector set at a fixed wavelength of 254 nm. Fig. 9 compares the different zeolites' adsorptive performance of ZE-1 and ZE-2 against the reaction time.
 |
| Fig. 9 (a) The adsorption capacity performance measured for ZE-1 and ZE-2 against standard CAZ solution (1 mg mL−1) measured for 20 min of reaction time; (b–d) the influence of pH, external salt (NaCl), and CAZ concentration on the adsorption capacity of ZE-1; (e) the reusability cycles of ZE-1 for the adsorption of the CAZ drug. | |
The data obtained from the adsorption tests were used to determine the removal capacity, qe (mg g−1) of the different adsorbents using the following eqn (i):25–27
|
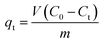 | (i) |
where
qt is the adsorption capacity (mg g
−1),
C0 is the initial, and
Ct is the final CAZ concentration.
V is the volume of the solution (L), and
m is the mass of the adsorbent (g).
Although the prepared zeolites are active towards the drug's adsorption, the adsorption capacity (qe) of the two zeolites differentiates significantly. In the case of ZE-2, the adsorption capability is relatively low, which might be explained based on compositional impurities that block the active sorbent sites. Simultaneously, the relatively superior adsorption capacity of ZE-1 (80 mg g−1) is directly attributed to the better gradual quality and lesser carbon impurities. Thus, ZE-1 proved to be a superior adsorbent for CAZ drugs. The maximum adsorption capacity of ZE-1 was achieved after optimizing the experimental conditions, i.e., pH, ionic tolerance and CAZ concentration. Fig. 9(b–d) shows the variation of the adsorption capability against these parameters. The best adsorption was achieved in the pH range of 5–6, where the acidic environment allows the drug molecules to protonate, promoting interionic interaction between the adsorbent and the drug. The presence of an external salt (NaCl) shows no effect on the adsorption capability of the ZE-1, signifying its favorability towards the removal of pharmaceutical drugs (Fig. 9(c)). The concentration of the drug is an essential factor that directly influences the adsorption performance of the zeolites. Fig. 9(d) shows the bar graph representing the removal efficiency achieved at different CAZ concentrations in the range of 1 to 20 mg mL−1. As seen, the highest adsorption was achieved with the lowest concentration of CAZ (1 mg mL−1). The adsorbent's repeatability is an important component in determining the material's practical workability. Fig. 9(e) shows the bar graph data representing the reusability cycles of ZE-1 against the standard CAZ solution (1 mg mL−1). As seen, 80% of efficiency is retained even after 20 adsorption cycles. In general, these experimental results recommend the feasibility of the CFA-derived zeolites in the trace removal of pharmaceutical drugs from drinking or wastewater systems.
4 Conclusion
In conclusion, zeolites could be produced using coal fly ash as a precursor and coal mine water as a hydrothermal solvent. Here, two types of coal fly ash (CFA1 and CFA2) were utilized as a precursor source for zeolites, whereas the importance of coal mine water (CW) and tap water (TP) as hydrothermal solvent were studied. The zeolites were prepared using an alkaline-fusion approach following hydrothermal treatment at various temperatures ranging from 45 to 95 °C. The detailed characterization supported the use of CW as a better dissolution solvent than TP, with better granular size and fewer carbon impurities. The superiority of zeolites prepared using CW was evaluated by configuring it into an adsorbent material for ceftazidime (CAZ), taken as a model pollutant. The superior structural configuration and high surface area enabled a faster and higher adsorption capacity of 80 mg g−1 in 20 min of agitation time. The pH, concentration, and external salt effects were also studied to achieve maximum removal efficiency. The study provides a simple route to utilize inoperable byproduct (fly ash) with the additional advantage of consuming toxic coal mine water to produce highly efficient adsorbent material with practical application in environmental remediation.
Abbreviations
CFA1 | Coal fly ash (type one) |
CFA2 | Coal fly ash (type two) |
CW | Coal mine water |
TP | Tap water |
NaOH | Sodium hydroxide |
CAZ | Ceftazidime |
Funding
National Special Water Programs (No. 2017ZX07101002-002).
Author contributions
S. H. Tumrani; analyzed and carried out experiments, R. A. Soomro; carried the adsorption studies and drafted the manuscript, X. Zhang; supported in the interpretation of data; D. Ali provided software analysis support and data interpretation; N. Bux; carried out supporting experiments; X. Dong supervised the study. All authors read and approved the final manuscript.
Conflicts of interest
The authors declare that they have no competing interests.
Acknowledgements
National Special Water Programs supported this work (No. 2017ZX07101002-002).
References
- W. C. Li, Occurrence, sources, and fate of pharmaceuticals in aquatic environment and soil, Environ. Pollut., 2014, 187, 193–201 CrossRef CAS PubMed
. - M. Jaseem, P. Kumar and R. M. John, An overview of waste management in pharmaceutical industry, Pharma Innovation, 2017, 6(3, part C), 158 Search PubMed
. - B. Renu, M. Agarwal and K. Singh, Methodologies for removal of heavy metal ions from wastewater: an overview, Interdiscipl. Environ. Rev., 2017, 18(2), 124–142 CrossRef
. - N. Jiang, R. Shang, S. G. Heijman and L. C. Rietveld, High-silica zeolites for adsorption of organic micro-pollutants in water treatment: A review, Water Res., 2018, 144, 145–161 CrossRef CAS PubMed
. - M. Agarwal and K. Singh, Heavy metal removal from wastewater using various adsorbents: a review, J. Water Reuse Desalin., 2017, 7(4), 387–419 CrossRef
. - A. Alsbaiee, B. J. Smith, L. Xiao, Y. Ling, D. E. Helbling and W. R. Dichtel, Rapid removal of organic micropollutants from water by a porous β-cyclodextrin polymer, nature, 2016, 529(7585), 190–194 CrossRef CAS
. - M. Suzuki, Activated carbon fiber: fundamentals and applications, Carbon, 1994, 32(4), 577–586 CrossRef CAS
. - R. Chakravarty and A. Dash, Nanomaterial-based adsorbents: the prospect of developing new generation radionuclide generators to meet future research and clinical demands, J. Radioanal. Nucl. Chem., 2014, 299(1), 741–757 CrossRef CAS
. - M. Ahmaruzzaman, A review on the utilization of fly ash, Prog. Energy Combust. Sci., 2010, 36(3), 327–363 CrossRef CAS
. - L. A. Oste, T. M. Lexmond and W. H. Van Riemsdijk, Metal immobilization in soils using synthetic zeolites, J. Environ. Qual., 2002, 31(3), 813–821 CrossRef CAS
. - J. Chen, H. Kong, D. Wu, Z. Hu, Z. Wang and Y. Wang, Removal of phosphate from aqueous solution by zeolite synthesized from fly ash, J. Colloid Interface Sci., 2006, 300(2), 491–497 CrossRef CAS PubMed
. - X. Ji, M. Zhang, Y. Wang, Y. Song, Y. Ke and Y. Wang, Immobilization of ammonium and phosphate in aqueous solution by zeolites synthesized from fly ashes with different compositions, J. Ind. Eng. Chem., 2015, 22, 1–7 CrossRef CAS
. - N. Jiang, M. Erdős, O. A. Moultos, R. Shang, T. J. Vlugt and S. G. Heijman, et al. The adsorption mechanisms of organic micropollutants on high-silica zeolites causing S-shaped adsorption isotherms: An experimental and Monte Carlo simulation study, Chem. Eng. J., 2020, 389, 123968 CrossRef CAS
. - N. Czuma, P. Baran, W. Franus, P. Zabierowski and K. Zarębska, Synthesis of zeolites from fly ash with the use of modified two-step hydrothermal method and preliminary SO2 sorption tests, Adsorpt. Sci. Technol., 2019, 37(1–2), 61–76 CrossRef CAS
. - N. Murayama, H. Yamamoto and J. Shibata, Mechanism of zeolite synthesis from coal fly ash by alkali hydrothermal reaction, Int. J. Miner. Process., 2002, 64(1), 1–17 CrossRef CAS
. - C. Belviso, F. Cavalcante and S. Fiore, Synthesis of zeolite from Italian coal fly ash: differences in crystallization temperature using seawater instead of distilled water, Waste Manag., 2010, 30(5), 839–847 CrossRef CAS PubMed
. - Y. Luo, Y. Wu, S. Ma, S. Zheng, Y. Zhang and P. K. Chu, Utilization of coal fly ash in China: a mini-review on challenges and future directions, Environ. Sci. Pollut. Res., 2020, 1–14 Search PubMed
. - H. Kazemian, Z. Naghdali, T. G. Kashani and F. Farhadi, Conversion of high silicon fly ash to Na-P1 zeolite: alkaline fusion followed by hydrothermal crystallization, Adv. Powder Technol., 2010, 21(3), 279–283 CrossRef CAS
. - T. Aldahri, J. Behin, H. Kazemian and S. Rohani, Effect of microwave irradiation on crystal growth of zeolitized coal fly ash with different solid/liquid ratios, Adv. Powder Technol., 2017, 28(11), 2865–2874 CrossRef CAS
. - L. F. Silva, T. J. Crissien, C. Milanes and C. H. Sampaio, A three-dimensional nanoscale study in selected coal mine drainage, Chemosphere, 2020, 248, 125946 CrossRef CAS PubMed
. - A. Mittal, V. Thakur and V. Gajbe, Adsorptive removal of toxic azo dye Amido Black 10B by hen feather, Environ. Sci. Pollut. Res., 2013, 20(1), 260–269 CrossRef CAS
. - L. Zhao, C. Sun, P. Yan, Q. Zhang, S. Wang and S. Luo, et al. Dynamic changes of nitrogen and dissolved organic matter during the transport of mine water in a coal mine underground reservoir: Column experiments, J. Contam. Hydrol., 2019, 223, 103473 CrossRef CAS PubMed
. - G. Madzivire, R. M. Maleka, M. Tekere and L. F. Petrik, Cradle to cradle solution to problematic waste materials from mine and coal power station: Acid mine drainage, coal fly ash and carbon dioxide, J. Water Process. Eng., 2019, 30, 100474 CrossRef
. - N. M. Musyoka, L. F. Petrik, O. O. Fatoba and E. Hums, Synthesis of zeolites from coal fly ash using mine waters, Miner. Eng., 2013, 53, 9–15 CrossRef CAS
. - H. Karaer and I. Kaya, Synthesis, characterization of magnetic chitosan/active charcoal composite and using at the adsorption of methylene blue and reactive blue4, Microporous Mesoporous Mater., 2016, 232, 26–38 CrossRef CAS
. - S. Sivalingam, T. Kella, M. Maharana and S. Sen, Efficient sono-sorptive elimination of methylene blue by fly ash-derived nano-zeolite X: process optimization, isotherm and kinetic studies, J. Cleaner Prod., 2019, 208, 1241–1254 CrossRef CAS
. - G. Supelano, J. G. Cuaspud, L. C. Moreno-Aldana, C. Ortiz, C. Trujillo and C. Palacio, et al. Synthesis of magnetic zeolites from recycled fly ash for adsorption of methylene blue, Fuel, 2020, 263, 116800 CrossRef CAS
. - A. E. Ameh, O. O. Fatoba, N. M. Musyoka and L. F. Petrik, Influence of aluminium source on the crystal structure and framework coordination of Al and Si in fly ash-based zeolite NaA, Powder Technol., 2017, 306, 17–25 CrossRef CAS
.
Footnote |
† Electronic supplementary information (ESI) available. See DOI: 10.1039/d1ra02785a |
|
This journal is © The Royal Society of Chemistry 2021 |
Click here to see how this site uses Cookies. View our privacy policy here.