DOI:
10.1039/D1RA03538J
(Paper)
RSC Adv., 2021,
11, 25284-25295
Highly porous copper-supported magnetic nanocatalysts: made of volcanic pumice textured by cellulose and applied for the reduction of nitrobenzene derivatives†
Received
6th May 2021
, Accepted 4th July 2021
First published on 21st July 2021
Abstract
Herein, a novel designed heterogeneous catalytic system constructed of volcanic pumice magnetic particles (VPMPs), cellulose (CLS) as a natural polymeric matrix, and copper nanoparticles (Cu NPs) is presented. Also, to enhance the inherent magnetic property of VPMP, iron oxide (Fe3O4) nanoparticles have been prepared and incorporated in the structure via an in situ process. As its first and foremost excellent property, the designed composite is in great accordance with green chemistry principles because it contains natural ingredients. Another brilliant point in the architecture of the designed composite is the noticeable porosity of VPMP as the core of the composite structure (surface area: 84.473 m2 g−1). This great porosity leads to the use of a small amount (0.05 g) of the particles for catalytic purposes. However, the main characterization methods, such as Fourier-transform infrared and energy-dispersive X-ray spectroscopy, thermogravimetric analysis, and electron microscopy, revealed that the spherical metallic particles (Fe and Cu oxides) were successfully distributed onto the surface of the VPMP and CLS matrices. Further, vibrating-sample magnetometer analysis confirmed the enhancement of the magnetic property (1.5 emu g−1) of the composite through the addition of Fe3O4 nanoparticles. Further, the prepared (Fe3O4@VPMP/CLS–Cu) nanocomposite has been applied to facilitate the reduction reaction of hazardous nitrobenzene derivatives (NBDs) to their aniline analogs, with 98% conversion efficiency in eight minutes under mild conditions. Moreover, the good reusability of the catalytic system has been verified after recycling it ten times without any significant decrease in the performance.
1. Introduction
As time goes on, microscale and nanoscale heterogeneous catalytic systems are gaining increasing attention for a variety of reasons, of which one of the most important is that they are able to create a high surface area for chemical reactions between the involved reactants and the catalytic substrate.1–3 In this regard, heterogeneous catalytic systems based on iron oxide nanoparticles have become more important due to the possibility of their easy separation by only holding an external magnet at the bottom of the reaction flask and decanting the content.4–11 Heterogeneous catalytic composites are modified by various components, such as organic structures, polymers, inorganic particles, biological structures, copper nanoparticles, and palladium nanoparticles, so that the majority of the catalytic sites are available.12–20 In recent years, more attention has been paid to green chemistry due to environmental concerns.20,21 That is why researchers are constantly trying to design novel natural heterogeneous catalytic systems with a high degree of biocompatibility. Undoubtedly, volcanic pumice benefits from a very porous structure that can lead to a high surface area, and it possesses properties such as high magnetic property, biocompatibility, and great surface functionalization capability; thus, it can inherently act as an eco-friendly substrate to create a heterogeneous catalytic composite.21–25
The use of cellulose (CLS) in this work, because it is natural, has been a strong indication of how important green chemistry was to us in this work.26,27 There are many reasons why cellulose, as a substantial polymeric substrate with a biocompatible origin, is used in this work; one of the most important of these is that cellulose, due to its large number of hydroxyl (–OH) functional groups, can form physicochemical hydrogen bonds with the –OH groups of pumice, which can lead to integration in the composite. On the other hand, the rest of the hydroxyl functional groups of cellulose, which are free of hydrogen bonds with the hydroxyl functional groups of pumice, are suitable for chelation by cationic metals such as copper and palladium and can form heterogeneous catalytic composites from natural components; this is one of the most important properties of this composite.28 The synthesized composite is notable even in terms of mechanical properties because it is a stable hybrid structure.29,30 As mentioned earlier, the synthetic heterogeneous catalytic composite in this work is suitable for scaling up and industrial applications because of its high biocompatibility and because it is made from components found in abundance in nature. In this work, after pumice, as an inorganic base with –OH groups functions as a suitable host for cellulose, as an organic base, Cu2+ ions are added to the system to act as catalytic sites to reduce the nitro functional groups of different compounds to amines after their conversion to Cu.31,32
Herein, an attempt was made to introduce a novel and convenient method for the synthesis of amine derivatives from the corresponding nitro compounds using Fe3O4@VPMP/CLS–Cu catalyst, which was synthesized with natural VPMP, CLS, and also Cu NPs. Then, the magnetic behavior and other critical characteristic properties of the prepared catalytic system, such as its average size, porosity, present chemical state, metallic elements, and thermal stability, were carefully investigated using different analytical methods. Then, the ability of this catalyst to reduce nitrobenzene derivatives (NBDs) was carefully examined. In summary, it was found that using the Fe3O4@VPMP/CLS–Cu catalytic system at 70 °C led to a 98% reaction yield in just 8 minutes. Also, the catalytic system under study can be reused for 10 successive runs due to its magnetic property, which leads to easy magnetic separation of this catalyst from the reaction medium. Also, in this study, water solvent was used as an eco-friendly solvent to evaluate the performance of the synthesized catalytic composite; this easily confirms the importance of green chemistry in this study.
2. Results and discussion
2.1. Preparation of the Fe3O4@VPMP/CLS–Cu nanocatalyst
As shown in Scheme 1, several steps are taken to prepare the Fe3O4@VPMP/CLS–Cu composite. Initially, the pumice is ground by a ball-mill to form uniform particles.33 After that, because the pumice is very porous and there may be useless fillers in its pores, it should be calcinated at a high temperature in a furnace.34 Then, if electron microscopy (EM) confirms that the calcinated pumice has uniformity and the useless fillers have been successfully removed from its pores, the magnetic property of the pumice is increased by Fe3O4 in order to separate it from the solvent on a laboratory scale, although the pumice itself has an inherent magnetic property. Next, it is it is dispersed and mixed in a concentrated solution of CLS under mild conditions. At the end of this step, the formed composite is magnetically separated and washed to remove the unbound CLS. Herein, a composite called Fe3O4@VPMP/CLS was prepared that contains a large number of hydroxyl functional groups in its VPMP and CLS structures and can be used several times. In another flask, an aqueous solution of CuCl2·H2O was prepared, which was added to a solution of dispersed Fe3O4@VPMP/CLS in which the hydroxyl functional groups were activated by an alkaline aqueous solution. After completion of the reaction, the resulting composite, Fe3O4@VPMP/CLS–Cu(II), which was now brown and no longer black like magnetic pumice, was magnetically separated and washed to remove excess salts and ions trapped inside the pores and silicate network of the pumice. Ultimately, Cu(II) in the composite of Fe3O4@VPMP/CLS–Cu(II) was reduced to Cu(0) by sodium borohydride under alkaline conditions.35 Herein, we intend to monitor the catalytic ability of the Fe3O4@VPMP/CLS–Cu nanocatalyst in the reduction reactions of NBDs, and the results obtained from the mentioned experiments are reported in Table 1, in the optimization section.
 |
| Scheme 1 Preparation route of the Fe3O4@VPMP/CLS–Cu(0) nanocomposite. | |
Table 1 Optimization of the reduction reaction of nitrobenzene under various catalytic conditions
Entry |
Cat. |
Cat. (mg) |
Cat. (mmol%) |
NaBH4 (mmol) |
Temp. (°C) |
Time (min) |
Yield (%) |
Optimum condition using the Fe3O4@VPMP/CLS–Cu nanocomposite (50.0 mg), nitrobenzene (1.0 mmol), NaBH4 (2.0 mol), and at 70 °C. Calculations related to mmol% of catalyst has been given in the ESI file. R.t. stands for room temperature. |
1 |
— |
— |
— |
— |
80 |
180 |
N.R. |
2 |
— |
— |
— |
2 |
80 |
180 |
Trace |
3 |
Fe3O4@VPMP/CLS |
30 |
12 |
2 |
80 |
90 |
Trace |
4 |
Fe3O4@VPMP/CLS–Cu |
10 |
4 |
2 |
70 |
8 |
85 |
5 |
Fe3O4@VPMP/CLS–Cu |
30 |
12 |
2 |
70 |
8 |
90 |
6 |
Fe3O4@VPMP/CLS–Cu |
50 |
20 |
2 |
70 |
8 |
98a |
7 |
Fe3O4@VPMP/CLS–Cu |
60 |
24 |
2 |
70 |
8 |
98 |
8 |
Fe3O4@VPMP/CLS–Cu |
50 |
20 |
3 |
70 |
8 |
94 |
9 |
Fe3O4@VPMP/CLS–Cu |
50 |
20 |
1 |
70 |
8 |
90 |
10 |
CLS–Cu |
50 |
20 |
2 |
70 |
8 |
92 |
11 |
Fe3O4@VPMP/CLS–Cu |
50 |
20 |
2 |
R.t. |
8 |
81 |
12 |
Fe3O4@VPMP/CLS–Cu |
50 |
20 |
2 |
R.t. |
30 |
97 |
2.2. Characterization of Fe3O4@VPMP/CLS–Cu nanocatalyst
2.2.1. FTIR spectroscopy. To examine the functional groups of the produced materials, FTIR spectra were obtained for the neat VPMP, Fe3O4@VPMP, Fe3O4@VPMP/CLS and Fe3O4@VPMP/CLS–Cu, as shown in Fig. 1. The results indicated that the existence of the peaks in all the materials spectra appearing at ca. 575–590 cm−1, 1000 cm−1 and 3450 cm−1 are related to the stretching vibrations of the metal oxide bonds (Fe–O), bending vibrations of the Si–O–Si bands of VPMP and stretching vibrations of the O–H bonds, respectively.36 Furthermore, the presence of Si–OH and SiO–H bonds was confirmed by the peaks that appeared at 950 cm−1 and 870 cm−1, respectively; these peaks are present in the spectra of all three samples.37 Finally, the peak that appeared at ca. 635 cm−1 well confirms the formation of Cu–O bonds in the structure of the Fe3O4@VPMP/CLS–Cu nanocomposite.38 The peak at 2300 cm−1 can also be related to CO2 in the atmosphere, and it is also visible in the spectra of all three samples.39
 |
| Fig. 1 The FTIR spectra of (a) neat VPMP, (b) Fe3O4@VPMP nanoparticles, (c) Fe3O4@VPMP/CLS nanocomposite, and (d) Fe3O4@VPMP/CLS–Cu nanocomposite. | |
2.2.2. EDX analysis. Energy-dispersive X-ray (EDX) spectroscopy should be used to further confirm the presence of elements that are predicted to be present at various stages of composite preparation. As shown in Fig. 2, all the composition elements for the three materials in the current study, Fe3O4@VPMP, Fe3O4@VPMP/CLS and Fe3O4@VPMP/CLS–Cu, were detected and affirmed through the EDX peaks with different intensities. Furthermore, the peak intensity of carbon element in the EDS of the fabricated Fe3O4@VPMP/CLS–Cu (Fig. 2a) increased significantly compared to that of the neat VPMP (Fig. 2b) and VPMP@CLS (Fig. 2c) samples, which is due to the good composition of CLS with VPMP in the presence of Cu nanoparticles in the magnetic nanocomposite structure. In addition, it has been clearly demonstrated that 10.1 wt% of the total weight of the fabricated Fe3O4@VPMP/CLS–Cu belongs to the Cu NPs.
 |
| Fig. 2 EDX spectra of (a) Fe3O4@VPMP, (b) Fe3O4@VPMP/CLS, and (c) Fe3O4@VPMP/CLS–Cu. | |
2.2.3. Electron microscopy. In order to investigate the size, morphology, and dispersion state of the prepared Fe3O4@VPMP/CLS–Cu nanocomposite, scanning-electron microscopy (SEM) and transmission-electron microscopy (TEM) were used. As can be observed in Fig. 3a, the ground VPMP was obtained from the pumice mass, but there was no uniformity in size or shape. Also, the size of the ground particles is in the range of 500–1100 nm, which is not appropriate. Fig. 3b illustrates the powdered VPMP (obtained by ball-milling), which has high uniformity of its size and morphology. As can be seen, good dispersion of the spherical-shaped VPMP particles with the average sizes of ca. 64 nm have been obtained. Also, with a more accurate look at the image (b), it is recognized that the rough structure of the VPMP nanoparticles is quite porous. Fig. 3c exhibits the composition state of the iron oxide (Fe3O4) nanoparticles with the VPMP nanoparticles. It can be clearly observed that the in situ preparation and incorporation of Fe3O4 were successfully performed, as the Fe3O4 seeds with a mean size of ca. 27 nm are finely distributed on the VPMP surfaces. Moreover, the Fig. 3g-series demonstrates the SEM energy-mapping images of the Fe3O4@VPMP nanoparticles that are related to image (e). Fig. 3d shows that the Fe3O4@VPMP/CLS particles are slightly agglomerated due to the integration of the CLS polymeric matrix. In this stage, good coating of Fe3O4@VPMP by the CLS occurred, and the particle agglomeration is temporary because the Fe3O4@VPMP/CLS particles were further redispersed in an alkaline medium (NaOH, 0.5 M) and also washed several times. As can be observed in Fig. 3e, good dispersion of the Fe3O4@VPMP/CLS–Cu nanocomposite was obtained through the washing of the particles and functionalization with the copper ions. Actually, the excess CLS matrix was removed through re-dispersion via the ultrasonication and additional washing. As can be seen in image (e), the uniformity of the particles (in size and shape) was preserved during the copper-functionalization process. Furthermore, the mean size of the Fe3O4@VPMP/CLS–Cu particles was estimated to be ca. 81 nm, which is good for catalytic applications. Ultimately, Fig. 3f illustrates the TEM image of the Fe3O4@VPMP/CLS–Cu composite, in which the dark spots are attributed to the Fe3O4 and Cu nanoparticles on the surface of the VPMP/CLS substrate. The energy-mapping images of the Fe3O4@VPMP/CLS–Cu composite related to image (e) have been illustrated as the “g series”, demonstrating the presence of Cu element on the surfaces. Generally, there are two justifications for incorporation of the Cu nanoparticles into the VPMP/CLS matrix; first, there are strong metal–oxide (M–O) electronic interactions between the Cu nanoparticles and abundant hydroxyl groups in the structure of CLS.40 Second, the Cu nanoparticles are incorporated into the voids of the VPMP, which is a highly porous substrate.41
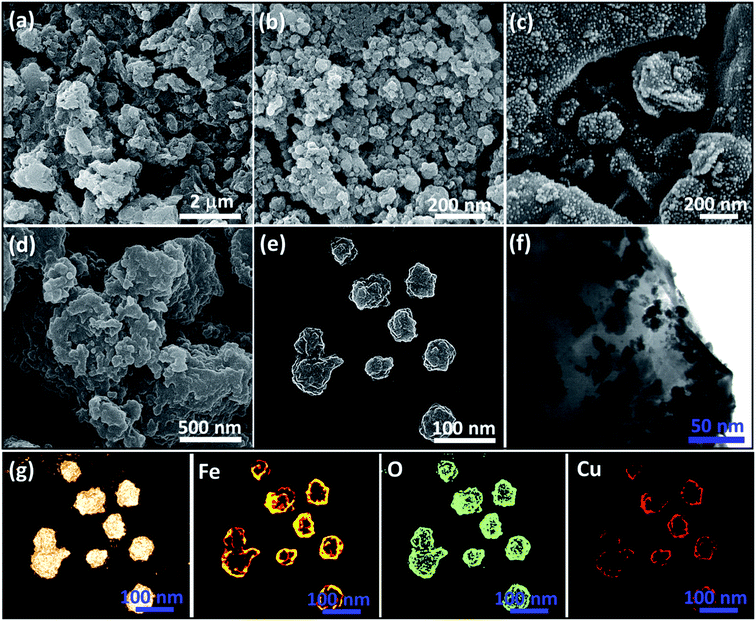 |
| Fig. 3 The SEM images of (a) ground pumice mass, (b) powdered VPMP, (c) Fe3O4@VPMP nanoparticles, (d) the integrated Fe3O4@VPMP/CLS composite, and (e) the dispersed Fe3O4@VPMP/CLS–Cu nanocomposite; (f) the TEM image of the Fe3O4@VPMP/CLS–Cu nanocomposite; and (g-series) SEM energy-mapping images of the Fe3O4@VPMP/CLS–Cu nanocomposite, related to image (e). | |
2.2.4. VSM analysis. The vibrating-sample magnetometer (VSM) technique was applied to detect the intrinsic magnetic performance of the arranged Fe3O4@VPMP and Fe3O4@VPMP/CLS–Cu nanocomposite materials. The hysteresis curves of the Fe3O4@VPMP nanocatalyst exhibit about a ca. 10.0 emu g−1 decrease in magnetic saturation, which is related to the phenomenon in which not all of the nanocatalysts were found to present magnetic features (Fig. 4). As is perceived from the magnetic–hysteresis curves, the magnetic behavior of the Fe3O4@VPMP nanocomposite has not been considerably reduced after addition of the CLS–Cu particles to form Fe3O4@VPMP/CLS–Cu nanocomposite materials. Additionally, the Fe3O4@VPMP/CLS–Cu nanocomposite materials could be collected, through this excellent magnetic property, without difficulty via using a magnet, and they could be reused several times.
2.2.5. TGA/DTA analysis. In this section, the thermal decomposition of the neat VPMP and the fabricated Fe3O4@VPMP/CLS–Cu system is investigated by thermogravimetric analysis (TGA) and differential thermal analysis (DTA). As shown in Fig. 5, in the temperate range of 150–370 °C, about 10% of the mass of Fe3O4@VPMP/CLS–Cu (black curve) was lost, while this reduction in mass for the neat VPMP from 300 °C to 500 °C is about 5%. This mass reduction in the TGA curve of Fe3O4@VPMP/CLS–Cu is related to the removal of –OH groups in the CLS structure. According to the literature, the –OH groups of polymers leave the structure during the dehydration process at this thermal range. Also, this change of mass due to the removal of the –OH groups of CLS in the DTA curve shows itself as an endotherm. Above 400 °C, both the Cu nanoparticles and VPMP NPs begin to decompose, where the reduction in mass of the prepared composite is very slow. This mass reduction in the DTA curve is shown as an endotherm. The silicate network has a high ability and capacity to trap various molecules, including water molecules, in its structure; therefore, it seems that the 5% reduction in the neat VPMP mass is probably related to the removal of water molecules trapped in the silicate structure of the VPMP structure.42 In addition, the first shoulder in the TGA curve of neat VPMP is about 1 wt%, and it is related to the separation of physically adsorbed moisture onto the surfaces. However, this shoulder is not in the TGA curve of Fe3O4@VPMP/CLS–Cu, which seems to be due to the good drying of the Fe3O4@VPMP/CLS–Cu sample under N2 before TGA. According to the DTA curve, the studied nanocomposite maintains its structure up to 600 °C, and no melting or crystallization action occurs up to the mentioned temperature in its structure (Fig. 5).
 |
| Fig. 4 The VSM curves of Fe3O4@VPMP and Fe3O4@VPMP/CLS–Cu. | |
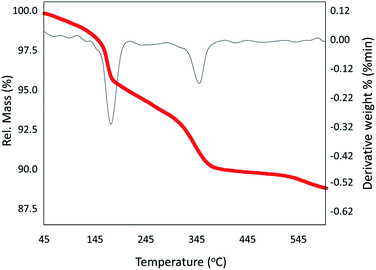 |
| Fig. 5 The TGA (red) and DTA (gray) curves of the fabricated Fe3O4@VPMP/CLS–Cu nanocomposite. | |
2.2.6. XRD analysis. The X-ray diffraction pattern (XRD) for the Fe3O4@VPMP/CLS–Cu compound is shown in Fig. 6. In this regard, the pattern of this nanocomposite was compared with the separate patterns of Fe3O4 and CuO based on the JCPDS database (PDF # 892531 and PDF # 190629). According to the results, the peaks found at 2θ = ∼30.7°, 36.2°, 43.8°, 52.2°, 57.7°, and 63.4°, which are respectively assigned to the green Miller indices (2 2 0), (3 1 1), (4 0 0), (4 2 2), (5 1 1), and (4 4 0), are related to the XRD patterns of Fe3O4 magnetic nanoparticles (MNPs). Also, the peaks that appeared at 2θ = ∼33.1°, 38.8°, 49.3°, 53.8°, 61.7°, 68.7°, and 69°, which were respectively assigned to the yellow Miller indices (1 1 0), (0 0 2), (2 0 0), (2 0 2), (0 2 0), (1 1 3), (0 2 2) and (2 2 0), in Fig. 6 are related to the diffraction pattern of the CuO structure in the composite of Fe3O4@VPMP/CLS–Cu.43 Also, the new peaks appearing at 2θ = ∼22.3°, 23.6°, 44.6°, 74.2°, and 79.6° are related to the amorphous structure of the VPMP structure.
 |
| Fig. 6 The XRD pattern of the fabricated Fe3O4@VPMP/CLS–Cu nanocomposite in comparison with the reference patterns of CuO and Fe3O4 NPs. | |
2.2.7. BET analysis. Due to the highly porous structure of the pumice used in the synthesis of the Fe3O4@VPMP/CLS–Cu nanocomposite, adsorption/desorption of N2 gas Brunauer–Emmett–Teller (BET) surface area analysis was used to confirm the porosity of the synthesized composite, as shown in Fig. 7. According to the obtained results, the pumice structure and Fe3O4@VPMP/CLS–Cu nanocomposite indicate the type IV isotherm of mesoporous materials. According to the obtained curves, all the pores of Fe3O4@VPMP/CLS–Cu were filled by liquid N2 at P/P0=0.99; therefore, for our sample, according to the amount adsorbed at P/P0 = 0.99 (72.2 cm3 g−1 STP) and its conversion to liquid volume (gas per liquid volume ratio is 647 for N2 at 77 K), we can estimate that the total volume of the composite pores is 0.5164 cm3 g−1. Also, according to the results, the reduction of the average pore size from 40 nm for pumice powder to 24.452 nm in the Fe3O4@VPMP/CLS–Cu nanocomposite along with the total surface area of the nanocomposite, which is 84.473 m2 g−1, confirms that although a large number of pumice pores are filled with Fe3O4 and CLS–Cu magnetic nanoparticles, large internal pores are still available for the catalytic performance of the nanocomposite.
 |
| Fig. 7 (a) The BET curves of the neat VPMP and the fabricated Fe3O4@VPMP/CLS–Cu nanocomposite and (b) the mean pore volumes of the neat VPMP and the fabricated Fe3O4@VPMP/CLS–Cu nanocomposite, via adsorption/desorption of N2 under ambient conditions. | |
2.2.8. XPS analysis. In order to evaluate the chemical state of the copper nanoparticles (Cu0, Cu+ or Cu2+) in the structure of the composite, X-ray photoelectron spectroscopy (XPS) was used. As demonstrated in Fig. 8a, the presence of Al/Si, Fe, and Cu elements in the structure of the Fe3O4@VPMP/CLS–Cu nanocomposite was confirmed; these elements originate from the VPMP, Fe3O4 and Cu nanoparticles, respectively. In the expanded spectrum of the copper element related to Cu 2p (Fig. 8b), there are two peaks at ca. 933 and 936 eV marked by Cu+ and Cu2+, respectively, confirming the formation of Cu2O and CuO nanoparticles in the structure of the catalyst.44 Therefore, it is concluded that the stage of reduction with sodium borohydride is required before beginning the catalytic process for the nitrobenzene derivatives. Also, the chemical state of the copper particles after the reduction process by sodium borohydride in alkaline conditions was investigated by this method. As can be observed in Fig. 8c and d, the peak of the copper element (Cu 2p) appeared at ca. 953 eV, confirming the chemical state Cu0 after the reduction process.45
 |
| Fig. 8 The XPS spectra of the prepared Fe3O4@VPMP/CLS–Cu nanocomposite: (a and b) before and (c and d) after reduction by NaBH4; (a and c) standard form and (b and d) expanded form of a specific area. | |
2.3. Application of Fe3O4@VPMP/CLS–Cu nanocatalyst in the reduction reactions of nitrobenzene derivatives (NBDs)
2.3.1. Optimization of the catalytic system in the reduction of nitrobenzene. In order to determine the optimized conditions for the use of the Fe3O4@VPMP/CLS–Cu catalytic system, the catalytic amount of the nanocomposite, amount of NaBH4, medium, temperature and reaction time used in the reduction reaction of nitrobenzene (NB) must be carefully monitored. Details of this investigation are reported in the table below. As shown in the table, in order to prove the important role of pumice porosity in the catalytic activity of Fe3O4@VPMP/CLS–Cu, CLS–Cu alone was applied under the same conditions during the reduction reaction, which showed a reduction in the reaction yield. This confirms the role of the pumice porosity in the catalytic activity of Fe3O4@VPMP/CLS–Cu. Also, the role of copper as the main catalytic site was investigated, which, as predicted, showed that the non-use of copper in the catalytic system leads to a sharp decrease in the yield of the reaction. From the table, it has been revealed that the optimum conditions were provided by using 0.05 g of the Fe3O4@VPMP/CLS–Cu catalyst during 8 min of stirring at 70 °C.
2.3.3. Suggested mechanism. As shown in Scheme 2, a plausible mechanism can be suggested for the reduction process of the NBDs under catalytic conditions provided by the Fe3O4@VPMP/CLS–Cu nanocomposite. At the first stage, the Cu2+ ions as the main catalytic sites are reduced to Cu0 by sodium borohydride (NaBH4) under the alkaline conditions provided by potassium carbonate (K2CO3).54 In stage 2, both the NB and borohydride (BH4−) structures are attracted onto the catalyst surface through electronic and hydrogen bond interactions.55 In third stage, hydridation of the NB structure is performed by the borohydride in the vicinity of the NB on the surface of the Fe3O4@VPMP/CLS–Cu particle. In the alkaline conditions, sodium metaborate (NaB(OH)4) is produced after completion of the reduction reaction of the NB. Finally, in stage 4, the produced aniline structure leaves the surface of the catalyst, and the particles are magnetically separated from the mixture, washed, and reused several times.
 |
| Scheme 2 A plausible multi-stage mechanism for the reduction of the NBDs catalyzed by the fabricated Fe3O4@VPMP/CLS–Cu catalytic system. | |
2.3.4. Recyclability effect of the nanocomposite catalytic system. In order to evaluate the reusability of the prepared Fe3O4@VPMP/CLS–Cu catalytic system, a reasonable investigation was performed on the model reduction reaction of nitrobenzene (NB). Firstly, the half-life of the reaction was estimated in five successive runs of the reaction. The details of the experiment and the obtained results are reported in Table S1 and Fig. S21, ESI file.† As reported in Table S2 (in the ESI file†), the time of the half-life of the reduction reaction of the NB changed to higher values after each cycle of separation and re-preparation of the catalyst particles. Based on the obtained results, it can be concluded that the catalytic efficiency of the Fe3O4@VPMP/CLS–Cu system is gradually lost during the recycling and reusing processes. To investigate the possible reasons, probable leaching of the copper particles from the Fe3O4@VPMP/CLS–Cu system as the main catalytic site was checked by inductively coupled plasma mass spectrometry (ICP-MS) analysis of the supernatant after the separation of the magnetic particles after running each recycling process. As can be seen in Table S3 (in the ESI file†), a small amount of leaching of the copper particles occurred during the separation, rinsing, drying and reusing of the Fe3O4@VPMP/CLS–Cu particles in five successive runs. Most likely, the copper leaching occurred during the ultrasonication process that is performed for dispersion of the particles before each run. The resulting reaction yields during five-time reuse of the Fe3O4@VPMP/CLS–Cu particles are given in the bar chart in Fig. 9a. As can be seen, it can be concluded that the Fe3O4@VPMP/CLS–Cu particles can be recovered and reused at least five successive times after magnetic separation, rinsing, and drying of the particles. Obviously, this has economic benefits, particularly in large scale applications. In order to investigate any possible change in the structure of the Fe3O4@VPMP/CLS–Cu nanocatalyst after five-time recycling, SEM and TEM imaging of the recovered particles were carried out. As illustrated in Fig. 9b and c, the uniformity and integrity of the VPMP, Fe3O4 and Cu nanoparticles in the CLS matrix have been suitably maintained, which confirms the good physicomechanical stability of the Fe3O4@VPMP/CLS–Cu composite. Also, the crystalline structure of the recovered Fe3O4@VPMP/CLS–Cu composite was studied by XRD spectroscopy. As can be observed in Fig. 9d, the same pattern with the fresh catalyst (Fig. 6) was obtained after recycling five times; only the intensity of the peaks related to the CuO nanoparticles (marked with Miller indices) decreased slightly due to the copper leaching. The content of Cu in the recovered structure was evaluated by inductively coupled plasma optical emission spectrometry (ICP-OES) analysis, and the obtained results, which have been given in Table S4 (in the ESI†), confirm the Cu-leaching from the catalytic system during the recycling. Besides, the graph of the optimization stages of reduction reaction of nitrobenzene under various catalytic conditions (related to Table 1) is illustrated in Fig. S22, ESI file.†
 |
| Fig. 9 (a) Recyclability diagram of the Fe3O4@VPMP/CLS–Cu catalytic system in the reduction reaction of NB to aniline; (b) SEM image, (c) TEM image, and (d) XRD pattern of the recovered Fe3O4@VPMP/CLS–Cu particles after recycling five times. | |
2.3.5. Comparison of the prepared Fe3O4@VPMP/CLS–Cu with other catalytic systems. In this section, we attempt to make a quick comparison between our presented nanocatalyst and a number of other previously reported systems that, like the Fe3O4@VPMP/CLS–Cu catalyst, have the ability to convert NBDs to their aniline analogues. Fe3O4@VPMP/CLS–Cu has advantages over the other catalysts discussed in the table below: (1) in general, heterogeneous catalytic systems are preferred to homogeneous catalytic systems due to their convenient separation process. The VPMP, which is used in our presented nanocatalyst, has a magnetic property itself due to the presence of iron in its structure; however, to increase this property, Fe3O4 was added to the synthetic composite, which leads to easier separation of this catalytic composite from the reaction medium. Significant conversion (98%) of different NB derivatives occurred in a short time (often less than 10 minutes), while in most cases (entries 1, 3, 4 and 5), the reaction time exceeded 90 minutes. In the design and preparation phase, it is very important to use materials that, in addition to benefiting from high degrees of biocompatibility, are inexpensive; therefore, the Fe3O4@VPMP/CLS–Cu composite, due to the use of abundant natural materials (such as VP rock), which has many economic advantages, can be considered superior to the systems reported in the table below (entry 2), although the results obtained by the reported catalytic systems are excellent. In addition to the mentioned advantages, other advantages of this catalytic system are easy preparation of the composite in question and use of lightweight substrates with a porous structure, which leads to good dispersion of the catalyst particles in the reaction medium and an overall increase in performance (Table 3).
Table 3 Catalytic systems previously reported for reduction of NB derivatives to aniline analogues
Entry |
Catalyst |
Conditions |
Cat. (mg) |
Time (min) |
Conversion (%) |
Ref. |
Poly-triallylamine (MPTA-1). SBA-15 is a mesoporous silica. Cobalt nanoparticles. Reduced graphene oxide. Copper nanoparticles. The present work. |
1 |
Ag–MPTA-1a |
80 °C/NaOH/N2 |
250 |
600 |
97 |
56 |
2 |
Ag–SBA-15b |
R.t./NaBH4 |
10 |
6 |
95 |
57 |
3 |
Nano Coc |
R.t./N2H4·H2O |
5.6 |
30 |
50 |
58 |
4 |
PhNO2,Pd NPs/RGOd |
50 °C/NaBH4 |
6.0 |
90 |
98 |
59 |
5 |
Cu NPse |
50 °C |
6.0 |
120 |
95 |
60 |
6 |
Fe3O4@VPMP/CLS–Cuf |
70 °C |
5.0 |
8 |
98 |
— |
3. Experimental
3.1. Chemicals and instruments
All the chemicals, reagents, and equipment used in this study are listed in Table 4.
Table 4 Chemicals and equipment used in this study
Materials and equipment |
Purity and brand |
Pumice stone |
Granulated – Sigma Aldrich |
Cellulose |
Microcrystalline – Sigma Aldrich |
FeCl2·4H2O |
Sigma Aldrich (98%) |
FeCl3·6H2O |
Sigma Aldrich (≥98%) |
Ammonia |
Merck (25%) |
Sodium hydroxide |
Merck, 97% |
CuCl2·2H2O |
Sigma Aldrich (≥99%) |
Ethanol |
Sigma Aldrich – 97% |
Sodium borohydride |
Sigma Aldrich (≥96%) |
FT-IR analysis |
Shimadzu IR-470 spectrometer |
EDX analysis |
Numerix DXP-X10P |
SEM analysis |
Sigma-Zeiss microscope |
TEM analysis |
Philips Cm 12 Instrument |
VSM analysis |
Lakeshore 7407 |
TGA/DTA analysis |
STA504 device |
XRD analysis |
JEOL JDX-8030 (30 kV, 20 mA) |
BET analysis |
Micromeritics ASAP 2010 |
XPS analysis |
K-Alpha+ |
ICP-OES analysis |
DV 5300 |
ICP-MS analysis |
ELAN 6100 DRC-e |
NMR analysis |
Varian Unity Inova 500 MHz |
Ultrasound cleaning bath |
KQ-250 DE (40 kHz, 250 W) |
Melting point measurement |
Electrothermal 9100, made in UK |
3.2. Preparation methods
3.2.1. Preparation of magnetic Fe3O4@VPMP micro-plates. First, the purchased pumice was placed in a milling bowl and ground by ball-milling (20 Hz) for two hours. The ground pumice was then poured into a crucible and placed in a furnace until its temperature reached 400 °C within an hour, and then the temperature slowly reached the ambient temperature as it was inside the furnace and without any temperature shock. The pumice was then removed from the furnace and washed several times with HCl (1 M). Then, 2.2 g of the prepared pumice was dispersed with 5.0 mmol of FeCl3, 5.0 mmol of FeCl2 and 50.0 mL of deionized water in a 100.0 mL balloon for 30 minutes at 45 °C via ultrasonication using a cleaner bath. It was then placed on a stirrer at 85 °C and stirred vigorously under N2 atmosphere for two hours. After this time, 7.5 mL of 25% ammonia was added dropwise in one hour. After this process, ultimately, the product was magnetically separated from the water, washed with deionized water several times, and then dried in an oven.
3.2.2. Preparation of the Fe3O4@VPMP/CLS composite. At this stage, 0.11 g of cellulose powder was initially dispersed in 20.0 mL of deionized water at room temperature. Then, 1.0 g of Fe3O4@VPMP particles were added with vigorous stirring to the prepared cellulose solution. After 6 hours, the Fe3O4@VPMP/CLS composite was magnetically separated and washed several times with deionized water.
3.2.3. Preparation of the Fe3O4@VPMP/CLS–Cu(II) composite. At this stage, in order to prepare the Fe3O4@VPMP/CLS–Cu(II) composite, initially, 75.0 mL of 0.04 M solution of CuCl2·3H2O was prepared. Then, in another flask, Fe3O4@VPMP/CLS particles (1.0 g) were dispersed in deionized water via ultrasonication, and the as-prepared solution of NaOH (0.5 M, 50.0 mL) was added dropwise during the ultrasonication at room temperature. Afterward, the pre-prepared solution of CuCl2·3H2O was slowly added to the flask of solution containing Fe3O4@VPMP/CLS particles and stirred vigorously. After 6 hours, the Fe3O4@VPMP/CLS–Cu(II) composite was magnetically separated and washed several times with deionized water.
3.3. A general procedure for reduction of nitroarenes with the Fe3O4@VPMP/CLS–Cu(0) system
To a round-bottom flask (25 mL) containing deionized water (5 mL), nitrobenzene (1 mmol, 0.123 g) and Fe3O4@VPMP/CLS–Cu(II) (0.05 g) were added. Then, the pH of the mixture was tuned to ca. 8.0 by addition of K2CO3 (0.04 g). Next, NaBH4 (2 mmol, 0.075 g) was added to the mixture, and the resulting mixture was stirred at 70 °C. After completion of the reaction, the catalyst was separated by an external magnet and the product was extracted with EtOAc. The organic layer was dried over anhydrous Na2SO4. Evaporation of the solvent under reduced pressure afforded the pure aniline in 98% yield.
3.4. Large scale experiment on the reduction of nitrobenzene by the Fe3O4@VPMP/CLS–Cu catalytic system
To evaluate the efficiency of the prepared Fe3O4@VPMP/CLS–Cu catalytic system in industrial applications, a gram scale model experiment was carried out. For this purpose, in a round bottom flask (500 mL), 40 mmol (4.9 g) of nitrobenzene was dissolved in 160 mL of water. Then, the pH of the mixture was tuned to ca. 8.0 by addition of K2CO3 (1.6 g), and the temperature of the flask was controlled with an ice bath. In a separate flask (100 mL), 2.0 g of Fe3O4@VPMP/CLS–Cu powder was well dispersed in 40 mL of water via ultrasonication by a cleaner bath (50 KHz, 100 W L−1) and finally added to the main flask (500 mL) containing the nitrobenzene solution. Then, NaBH4 (80 mmol, 3.0 g) was added to the mixture, and the resulting mixture was stirred in an ice bath. At this stage, the reaction temperature was maintained at around 20 °C. After completion of the reaction, the magnetic particles were separated with an external magnet several times. Next, the residue was divided into five 40 mL portions, and liquid–liquid extraction was performed using EtOAc (20 mL) (three times for each portion). Finally, the organic phase was dried over anhydrous Na2SO4 (5.0 g), and the solvent was evaporated under reduced pressure (pure aniline in 98% yield).
4. Conclusion
In this study, a magnetic catalytic system using natural-based materials was presented that has the ability to reduce various derivatives of nitrobenzene (NB) in a very short time of 8 minutes. This efficient catalytic system was characterized by FT-IR spectroscopy, SEM, EDX spectroscopy, XRD spectroscopy, TGA, and VSM. This catalytic system has many advantages, such as (1) convenient separation, which is due to the superparamagnetic behavior of the nanoscale catalytic system, which was also proven by VSM analysis; (2) due to the high porosity of the pumice according to SEM, this catalytic system is able to provide a large active surface area; and (3) the use of low amounts of the heterogeneous catalyst (0.05 g) and many other advantages can introduce this composite as a suitable candidate for scaling up and industrial applications.
Author contributions
R. T. L. designed the project and led the hypothesis. M. S. and F. S. Q. carried out the experimental sections and provided the required analyses. R. T. L. and M. S. prepared the first draft of manuscript. All the authors helped in interpreting the obtained results, writing, editing and revising the manuscript. A. M. and A. E. S. managed and supervised all the work sections.
Conflicts of interest
The authors listed in this article have no conflict of interests.
Acknowledgements
The authors gratefully acknowledge the partial support from the Research Council of the Iran University of Science and Technology (IUST). Furthermore, AES thanks the National Research grants from MINECO, Spain, “Juan de la Cierva” [FJCI-2018-037717]. Also, the authors appreciate the kind accompaniment of Mr Seyed Masoud Seyed Ali Routeh from IAUSR.
References
- S. Bao, Y. Wang, Z. Wei, W. Yang, Y. Yu and Y. Sun, J. Hazard. Mater., 2021, 416, 125825 CrossRef CAS.
- R. Taheri-Ledari and A. Maleki, New J. Chem., 2021, 45, 4135–4146 RSC.
- B. Reddy, R. Dadigala, R. Bandi, K. Seku, G. Koteswararao, K. Mangatayaru and A. E. Shalan, RSC Adv., 2021, 11, 5139–5148 RSC.
- A. Maleki, R. Taheri-Ledari, J. Rahimi, M. Soroushnejad and Z. Hajizadeh, ACS omega, 2019, 4, 10629–10639 CrossRef CAS PubMed.
- V. Soltaninejad, M. R. Ahghari, R. Taheri-Ledari and A. Maleki, Langmuir, 2021, 37(15), 4700–4713 CrossRef CAS PubMed.
- R. Taheri-Ledari, A. Maleki, E. Zolfaghari, M. Radmanesh, H. Rabbani, A. Salimi and R. Fazel, Ultrason. Sonochem., 2020, 61, 104824 CrossRef CAS PubMed.
- X. Meng, Y. Liu, G. Han, W. Yang and Y. Yu, Carbon, 2020, 162, 356–364 CrossRef CAS.
- S. Bao, W. Yang, Y. Wang, Y. Yu and Y. Sun, J. Hazard. Mater., 2021, 409, 124470 CrossRef CAS PubMed.
- R. Taheri-Ledari, J. Rahimi and A. Maleki, Mater. Res. Express, 2020, 7(1), 015067 CrossRef CAS.
- S. Nabih, A. E. Shalan, E. S. A. Serea, M. A. Goda and M. F. Sanad, J. Mater. Sci.: Mater. Electron., 2019, 30, 9623–9633 CrossRef CAS.
- A. Maleki, R. Taheri-Ledari, R. Ghalavand and R. Firouzi-Haji, J. Phys. Chem. Solids, 2020, 136, 109200 CrossRef CAS.
- R. Taheri-Ledari, J. Rahimi, A. Maleki and A. E. Shalan, New J. Chem., 2020, 44, 19827–19835 RSC.
- A. Maleki, R. Taheri-Ledari and M. Soroushnejad, ChemistrySelect, 2018, 3, 13057–13062 CrossRef CAS.
- R. Taheri-Ledari, M. S. Esmaeili, Z. Varzi, R. Eivazzadeh-Keihan, A. Maleki and A. E. Shalan, RSC Adv., 2020, 10(66), 40055–40067 RSC.
- S. M. Abdellatif Soliman, M. F. Sanad and A. E. Shalan, RSC Adv., 2021, 11, 11541–11548 RSC.
- M. S. Esmaeili, Z. Varzi, R. Taheri-Ledari and A. Maleki, Res. Chem. Intermed., 2021, 47, 973–996 CrossRef CAS.
- R. Taheri-Ledari, S. S. Mirmohammadi, K. Valadi, A. Maleki and A. E. Shalan, RSC Adv., 2020, 10, 43670–43681 RSC.
- R. Taheri-Ledari and A. Maleki, J. Pept. Sci., 2020, 26, e3277 CrossRef CAS PubMed.
- A. E. Shalan, M. Afifi, M. M. El-Desoky and M. K. Ahmed, New J. Chem., 2021, 45, 9212–9220 RSC.
- S. Parvaz, R. Taheri-Ledari, M. S. Esmaeili, M. Rabbani and A. Maleki, Life Sci., 2020, 240, 117099 CrossRef CAS PubMed.
- Z. Varzi, M. S. Esmaeili, R. Taheri-Ledari and A. Maleki, Inorg. Chem. Commun., 2021, 125, 108465 CrossRef CAS.
- X. Zhang, Z. Chen, X. Liu, S. L. Hanna, X. Wang, R. Taheri-Ledari, A. Maleki, P. Li and O. K. Farha, Chem. Soc. Rev., 2020, 49, 7406–7427 RSC.
- R. Taheri-Ledari, K. Valadi, S. Gharibi and A. Maleki, Mater. Res. Bull., 2020, 130, 110946 CrossRef CAS.
- A. Maleki, S. Gharibi, K. Valadi and R. Taheri-Ledari, Phys. Chem. Solids., 2020, 142, 109443 CrossRef CAS.
- X. Meng, W. Lei, W. Yang, Y. Liu and Y. Yu, J. Colloid Inter. Sci., 2021, 600, 382–389 CrossRef CAS PubMed.
- M. H. Abu Elella, E. S. Goda, H. M. Abdallah, A. E. Shalan, H. Gamal and K. R. Yoon, Int. J. Biol. Macromol., 2021, 167, 1113–1125 CrossRef CAS PubMed.
- S. Karami, B. Zeynizadeh and Z. Shokri, Cellulose, 2018, 25, 3295–3305 CrossRef CAS.
- S. S. Soltani, R. Taheri-Ledari, S. M. F. Farnia, A. Maleki and A. Foroumadi, RSC Adv., 2020, 10, 23359–23371 RSC.
- X. Zhang, C. Shi, E. Liu, N. Zhao and C. He, ACS Appl. Mater. Interfaces, 2018, 10, 37586–37601 CrossRef CAS PubMed.
- K. Valadi, S. Gharibi, R. Taheri-Ledari and A. Maleki, Solid State Sci., 2020, 101, 106141 CrossRef CAS.
- T. B. Devi and M. Ahmaruzzaman, Mater. Today: proceedings, 2017, 5, 2098–2104 Search PubMed.
- M. Nasrollahzadeh, S. M. Sajadi, A. Rostami-Vartoonia, M. Bagherzadeh and R. Safari, J. Mol. Catal. A Chem., 2015, 400, 22–30 CrossRef CAS.
- S. P. K. Kohobhange, C. H. Manoratne, H. M. T. G. A. Pitawala and R. M. G. Rajapakse, Powder Technol., 2018, 330, 266–274 CrossRef CAS.
- B. Demirel and O. Keleştemur, Fire Saf. J., 2010, 45, 385–391 CrossRef CAS.
- K. Naseem, Z. H. Farooqi, R. Begum and A. Irfan, J. Clean. Prod., 2018, 187, 296–307 CrossRef CAS.
- Z. Hajizadeh, K. Valadi, R. Taheri-Ledari and A. Maleki, ChemistrySelect, 2020, 5, 2441–2448 CrossRef CAS.
- R. Taheri-Ledari, S. M. Hashemi and A. Maleki, RSC Adv., 2019, 9, 40348–40356 RSC.
- A. M. Youssef, F. M. Assem, H. S. El-Sayed, S. M. El-Sayed, M. Elaaser and M. H. Abd El-Salam, RSC Adv., 2020, 10(62), 37857–37870 RSC.
- R. Taheri-Ledari, K. Valadi and A. Maleki, Prog. Photovolt. Res. Appl., 2020, 28, 956–970 CrossRef CAS.
- Y. Sun, Y. Zhou, C. Zhu, W. Tu, H. Wang, H. Huang, Y. Liu, M. Shao, J. Zhong, S. T. Lee and Z. Kang, Appl. Catal. B, 2019, 244, 795–801 CrossRef CAS.
- P. Chang, H. Mei, Y. Zhao, W. Huang, S. Zhou and L. Cheng, Adv. Funct. Mater., 2019, 29(34), 1903588 CrossRef.
- R. Taheri-Ledari, W. Zhang, M. Radmanesh, S. S. Mirmohammadi, A. Maleki, N. Cathcart and V. Kitaev, Small, 2020, 16, 2002733 CrossRef CAS PubMed.
- S. Suresh, S. Karthikeyan and K. Jayamoorthy, J. Sci. Adv. Mater. Dev., 2016, 1, 343–350 Search PubMed.
- D. Ferrah, A. R. Haines, R. P. Galhenage, J. P. Bruce, A. D. Babore, A. Hunt, I. Waluyo and J. C. Hemminger, ACS Catal., 2019, 9(8), 6783–6802 CrossRef CAS.
- L. Guo, J. Cao, J. Zhang, Y. Hao and K. Bi, J. Mater. Sci., 2019, 54(14), 10379–10388 CrossRef CAS.
- V. Kandathil, T. S. Koley, K. Manjunatha, R. B. Dateer, R. S. Keri, B. S. Sasidhar and S. A. Patil, Inorg. Chim. Acta, 2018, 478, 195–210 CrossRef CAS.
- S. L. Arora, J. L. Fergason and A. Saupe, Mol. Cryst. Liq. Cryst., 1970, 3, 243–257 CrossRef.
- A. K. Shil, D. Sharma, N. R. Guha and P. Das, Tetrahedron Lett., 2012, 36, 4858–4861 CrossRef.
- S. Sobhani, F. O. Chahkamali and J. M. Sansano, RSC Adv., 2019, 3, 1362–1372 RSC.
- M. Rajabzadeh, H. Eshghi, R. Khalifeh and M. Bakavoli, RSC Adv., 2016, 23, 19331–19340 RSC.
- T. Maejima, Y. Shimoda, K. Nozaki, S. Mori, Y. Sawama, Y. Monguchi and H. Sajiki, Tetrahedron, 2012, 6, 1712–1722 CrossRef.
- J. Li, E. D. Inutan, B. Wang, C. B. Lietz, D. R. Green, C. D. Manly, A. L. Richards, D. D. Marshall, S. Lingenfelter, Y. Ren and S. Trimpin, J. Am. Soc. Mass Spectrom., 2012, 10, 1625–1643 CrossRef PubMed.
- R. Mirbagheri and D. Elhamifar, J. Alloys Compd., 2019, 790, 783–791 CrossRef CAS.
- J. Cai, Y. Zhuang, Y. Chen, L. Xiao, Y. Zhao, X. Jiang, L. Hou and Z. Li, ChemCatChem, 2020, 12(24), 6241–6247 CrossRef CAS.
- J. F. de Souza, G. T. da Silva and A. R. Fajardo, Carbohydr. Polym., 2017, 161, 187–196 CrossRef CAS PubMed.
- N. Salam, B. Banerjeec, A. S. Roy, P. Mondal, A. S. Roy, A. Bhaumik and S. M. Islam, APPL. Catal. A-Gen., 2014, 477, 184–194 CrossRef CAS.
- B. Naik, S. Hazra, V. S. Prasad and N. N. Ghosh, Catal. Commun., 2011, 12, 1104–1108 CrossRef CAS.
- R. K. Rai, A. Mahata, S. Mukhopadhyay, S. Gupta, P. Li, K. T. Nguyen, Y. Zhao, B. Pathak and S. K. Singh, Inorg. Chem., 2014, 53, 2904–2909 CrossRef CAS PubMed.
- M. Nasrollahzadeh, S. M. Sajadi, A. Rostami-Vartooni, M. Alizadeh and M. Bagherzadeh, J. Colloid Inter. Sci., 2015, 466, 360–368 CrossRef PubMed.
- Z. Duan, G. Ma and W. Zhang, Bull. Korean Chem. Soc., 2012, 33, 4003–4006 CrossRef CAS.
Footnotes |
† Electronic supplementary information (ESI) available. See DOI: 10.1039/d1ra03538j |
‡ Currently on leave from CMRDI. |
|
This journal is © The Royal Society of Chemistry 2021 |
Click here to see how this site uses Cookies. View our privacy policy here.